BIFFI HLA User manual

Installation, Operation and Maintenance Manual
MAN 646 Rev. 5
March 2022
Bif HLA
Double-Acting Hydraulic Linear Actuator
Copyright © Bif. The information in this document is subject to change without notice. Updated data sheets can be obtained from our website www.bif.it or from your nearest Bif Center:
Bif Italia s.r.l. - Strada Bif 165, 29017 Fiorenzuola d'Arda (PC) – Italy PH: +39 0523 944 411 – bif_italia@bif.it

March 2022
Installation, Operation and Maintenance Manual
MAN 646 Rev. 5
Revision Details
Revision Details
Revision Details
Rev. Date Description Prepared Checked Approved
5 March 2022 General update (Migration to new template)
4February 2019 Updated data plate Sassi Oreci Vigliano
3April 2016 Updated applicable regulation (chapter 1.1.1) Ermanni Oreci Vigliano
2July 2012 General update Ermanni Stoto Vigliano
1 June 2010 General update Ermanni Stoto Vigliano
0May 1999 Document release Lazzarini Aliani Ziveri

i
Table of Contents
Installation, Operation and Maintenance Manual
MAN 646 Rev. 5 March 2022
Table of Contents
Table of Contents
Section 1: General Warnings
1.1 Generalities................................................................................................... 1
1.1.1 Applicable Regulation ........................................................................ 1
1.1.2 Terms and Conditions......................................................................... 1
1.2 Identication Plate ........................................................................................ 2
1.3 Introducing the Actuator............................................................................... 2
1.4 Data Sheet .................................................................................................... 3
Section 2: Installation
2.1 Checks upon Actuator Receipt.......................................................................... 4
2.2 Actuator Handling......................................................................................... 4
2.3 Storage ......................................................................................................... 6
2.4 Actuator Assembly on the Valve.................................................................... 6
2.4.1 Types of Assembly.............................................................................. 6
2.4.2 Assembly Procedure........................................................................... 6
2.5 Hydraulic Connections................................................................................ 10
2.6 Electrical Connections (If Any)..................................................................... 11
2.7 Commissioning........................................................................................... 11
Section 3: Operation and Use
3.1 Operation Description................................................................................. 12
3.2 Residual Risks.............................................................................................. 13
3.3 Operations.................................................................................................. 13
3.3.1 Emergency Manual Operation (MHP) ............................................... 13
3.3.2 Remote Control Operations ............................................................ 14
3.4 Calibration of the Angular Stroke ................................................................ 16
3.5 Calibration of Microswitches (Bif Limit Switch Box Only)............................ 19
3.6 Calibration of the Operation Time............................................................... 21
Section 4: Operational Tests and Inspections
Operational Tests and Inspections......................................................................... 22
Section 5: Maintenance
5.1 Periodic Maintenance.................................................................................. 23
5.1.1 Check and Restore Oil Level in the Hydraulic Manual Handpump...... 24
5.2 Extraordinary Maintenance ......................................................................... 26
5.2.1 Lubrication of Mechanism ................................................................ 26
5.2.2 Replacement of Cylinder Seals ......................................................... 27
5.3 Dismantling and Demolition ....................................................................... 30

ii
March 2022
Installation, Operation and Maintenance Manual
MAN 646 Rev. 5
Table of Contents
Table of Contents
Section 6: Troubleshooting
6.1 Failure or Breakdown Research.................................................................... 31
Section 7: Layouts
7.1 Spare Parts Order........................................................................................ 32
7.2 Parts List for Maintenance and Replacing Procedure ................................... 33
Section 8: Date Report for Maintenance Operations
Date Report for Maintenance Operations .............................................................. 39

1
Installation, Operation and Maintenance Manual
MAN 646 Rev. 5
General Warnings
Section 1: General Warnings
March 2022
Section 1: General Warnings
NOTICE
The manual is an integral part of the machine, it should be carefully read before carrying
out any operation and it should be kept for future references.
1.1 Generalities
Bif Italia s.r.l. actuators are conceived, manufactured and controlled according to the
Quality Control System in compliance with EN-ISO 9001 international regulation.
1.1.1 Applicable Regulation
EN ISO 12100:2010: Safety of machinery – General principles for design – Risk
assessment and risk reduction
2006/42/EC: Machine directive
2014/68/EU: Directive for pressure PED equipment
2014/35/EU: Directive for low voltage equipment
2014/30/EU: Directive for the electromagnetic compatibility
2014/34/EU: Directive and safety instructions for use in hazardous area
NOTICE
Bif Italia s.r.l. pays the highest attention to collecting and verifying the documentation
contained in this Installation, Operation and Maintenance Manual. However, Bif Italia
s.r.l. is not liable for any mistakes contained in this manual, and for damage or accidents
due to the use of the latter. The information contained is of exclusive reserved ownership
of Bif Italia s.r.l. and may be modied without prior notice. All rights reserved.
1.1.2 Terms and Conditions
Bif Italia s.r.l. guarantees that all the items produced are free of defects in workmanship
and manufacturing materials and meet relevant current specications, provided they
are installed, used and serviced according to the instructions contained in the present
manual. The warranty can last either one year from the date of installation by the initial
user of the product, or eighteen months from the date of shipment to the initial user,
depending on which event occurs rst. All detailed warranty conditions are specied in
the documentation forwarded together with the product. This warranty does not cover
special products or components not warranted by subcontractors, or materials that were
used or installed improperly or were modied or repaired by unauthorized staff. In the
event that a fault condition be caused by improper installation, maintenance or use, or by
irregular working conditions, the repairs will be charged according to applicable fees.
The warranty and Bif Italia s.r.l. liability shall lapse in the event that any
modication or tampering whatsoever be performed on the actuator.

2
March 2022
Installation, Operation and Maintenance Manual
MAN 646 Rev. 5
Section 1: General Warnings
General Warnings
1.2 Identication Plate
! WARNING
It is forbidden to modify the information and the marks without previous written
authorization by Bif Italia s.r.l.
The plate fastened on the actuator contains the following information (Figure 1).
Figure 1 Data plate
1.3 Introducing the Actuator
HLA double-acting hydraulic linear actuators are suitable for the operation of linear
valves (wedge gate valves, through conduit gate valves) for ON-OFF and modulating
heavy-duty service.
The actuator is made up of a hydraulic cylinder and a mounting pedestal complete with a
joint for the coupling to the valve stem of actuator output stem. The valve is actuated in
opening and in closing position by the actuator hydraulic cylinder that is pressurized in one
or in the other direction.
The linear stroke of the valve is adjustable by means of the external mechanical stop for
upward position and by the adjustment of the coupling of valve stem to actuator joint for
the downward position.
The actuator pedestal has a ange with threaded holes to x the actuator to the valve.
Bif can supply different types of control system following customer’s requirements.
The expected lifetime of actuator is approximately 25 years.

3
Installation, Operation and Maintenance Manual
MAN 646 Rev. 5
General Warnings General Warnings
Section 1: General Warnings
March 2022
Figure 2 Identication of actuator parts
Lifting eyelets
Manual handpump
MHP (optional)
Valve coupling
Hydraulic cylinder
Valve position
indicator
1.4 Data Sheet
Supply uid Mineral oil or synthetic uids
Operating temperature Standard: from –30 °C to +100 °C
Optional: from –60 °C to +140 °C
Applications Gate, Globe valves
Max. allowable thrust (N)
HLA 250 k 135 300 MHP
Cylinder diameter (mm)
Stroke (mm)
Double-acting actuator
Manual override

4
March 2022
Installation, Operation and Maintenance Manual
MAN 646 Rev. 5
Section 2: Installation
Installation
Section 2: Installation
2.1
Checks upon Actuator Receipt
• Check that the model, the serial number of the actuator, and the technical
data reported on the identication plate correspond with those of order
conrmation (Section 1.2).
• Check that the actuator is equipped with the ttings as provided for by
order conrmation.
• Check that the actuator was not damaged during transportation; if necessary,
renovate the painting according to the specication reported on the
order conrmation.
• If the actuator is received already assembled with the valve, its settings have
already been made at the factory.
• If the actuator is delivered separately from the valve, it is necessary to check, and,
if required, to adjust, the settings of the mechanical stops (Section 3.4) and of
microswitches (if any) (Section 3.5).
2.2 Actuator Handling
Figure 3 Lifting points for HLA actuators
! WARNING
The fastening points are appropriate for the lifting of the actuator alone and not for the
valve + actuator assembly. Avoid that during the handling, the actuator passes above the
staff. The actuator should be handled with appropriate lifting means. The weight of the
actuator is reported on the delivery bill.
NOTICE
The lifting and handling should be made by qualied staff and in compliance with the laws
and provisions in force.
1 = Lifting points (obligatory)

5
Installation, Operation and Maintenance Manual
MAN 646 Rev. 5
Section 2: Installation
Installation
March 2022
Figure 4 Positioning by chains
1 = point of support
! WARNING
2 = don’t lay the actuator on tie rods of cylinder
3 = don’t lay the actuator on accessories (manual handpump, hydraulic control system, etc.)
Figure 5 Positioning by slings

6
March 2022
Installation, Operation and Maintenance Manual
MAN 646 Rev. 5
Section 2: Installation
Installation
2.3 Storage
If the actuator needs storage before installation, follow these steps:
• Place it on a wood surface in order not to deteriorate the area of valve coupling.
• Make sure that plastic plugs are present on the hydraulic and electrical
connections (if present).
• Check that the cover of the control group and of the limit switch box (if any) are
properly closed.
If the storage is long-term or outdoor:
• Keep the actuator protected from direct weather conditions.
• Replace plastic plugs of hydraulic and electrical connections (if any) with metal
plugs that guarantee perfect tightness.
• Coat the valve coupling area with oil, grease or protection disc.
• Periodically operate the actuator (Section 3.3).
2.4 Actuator Assembly on the Valve
2.4.1 Types of Assembly
The adapter pedestal in fabricated carbon steel is specically designed for adaptation to
any type of valve with provision for local indicator, limit switches and other accessories
(on request).
Lift the actuator by safety hook for chains using the lifting points (see Section 2.2) on
the top of actuator for handling, transporting and assembling in vertical position (see
Figure 3). For handling, transporting and assembling the actuator in horizontal position
by safety hook for chains use the lifting points on the top of cylinder head ange and on
coupling ange (see Figures 4 and 5).
2.4.2 Assembly Procedure
! WARNING
Failure to comply with the following procedures may impair product warranty. Installation,
commissioning and maintenance and repair works should be carried out by qualied staff.
A non-conforming assembly could be the source of serious accidents.
For actuator assembly on the valve:
NOTICE
Check that the assembly position, as shown on the documentation, complies with system’s
geometry. Check the consistency of the parts of actuator-valve coupling.

7
Installation, Operation and Maintenance Manual
MAN 646 Rev. 5
Section 2: Installation
Installation
March 2022
A. To assemble the actuator onto the valve by bracket with threaded joint, proceed
as follows:
Figure 6 Pedestal with threaded coupling joint
Table 1. Parts list
Item Description
1Nut
2Stud bolt
3Support joint
4Index
5Screw
6Connecting joint
7Screw
8Bushing
9Flange
1. Check that the coupling dimensions of the valve ange and stem, or of the
relevant extension, meet the actuator coupling dimensions (valve stem and
ange). Lubricate the valve stem with grease in order to make the assembly easier.
2. Connect a sling to the support point of the actuator and lift it. To make the
assembly easier, the valve stem has to be in perfect vertical position.
NOTICE
The eyebolt is sized for the lifting of the actuator only (NOT ACTUATOR+VALVE). Proper
lifting points have to be foreseen for the valve.
3. Screw the actuator coupling joint onto the valve by rotating the actuator, or screw
down the valve stem stroke-ring with Red Loctite 542 and x the half-bearings.
When the threaded holes of the actuator ange are in correspondence with the
holes on the valve ange screw the proper stud bolts. Screw the nuts on the stud
bolts and tighten up the valve ange is in contact with the actuator ange.
4. Tighten the nuts of the connecting stud bolts evenly with the torque prescribed in
the table. The stud bolts must be made of ASTM A320 L7 steel, the nuts must be
made of ASTM A194 grade 2 steel as minimum.

8
March 2022
Installation, Operation and Maintenance Manual
MAN 646 Rev. 5
Section 2: Installation
Installation
B. To assemble the actuator onto the valve by bracket with shell joint, perform the
following operations:
Figure 7 Pedestal with shell coupling joint
Item Description
1Stud bolt
2Nut
3Nut
4Screw
5Pedestal
6Actuator joint
7Stem valve joint
8Shell joint
9Spacer
10 Screw
Table 2. Parts list

9
Installation, Operation and Maintenance Manual
MAN 646 Rev. 5
Section 2: Installation
Installation
March 2022
1. Check that the coupling dimensions of the valve ange and stem, or of the
relevant extension, meet the actuator coupling dimensions (valve stem and
ange). Lubricate the valve stem with grease in order to make the assembly easier.
2. To make the assembly easier, the valve stem has to be in perfect vertical position.
3. Disassemble the two halves of actuator pedestal shell joint (item 8) by unscrewing
the retaining screws (item 4), therefore, disassemble the valve stem joint (item 7).
4. Lift the actuator by utilizing the proper lifting eyelets and unscrew the nuts and
the stud bolts from the actuator pedestal.
5. Assemble the actuator onto the valve and arrange it in its correct vertical position
proper to connection between valve stem and actuator cylinder rod.
6. Screw the valve stem joint (item 7) on valve stem up to reach the proper position
which allow the reassembly of the two halves of shell joint (item 8), tighten the
joint fastening screws (item 4).
7. Screw the stud bolts (item 1) into the actuator pedestal ange and screw the nuts
on the stud bolts.
8. Tighten according to the nut (item 2) size torque requirements.
NOTICE
To operate, refer to following table:
Threading Tightening torque (Nm)
M8 20
M10 40
M12 70
M14 110
M16 160
M20 320
M22 420
M24 550
M27 800
M30 1100
M33 1400
M36 1700
Table 3. Nuts tightening torque
The screwing values in Table 3 were calculated considering the materials ASTM A320 L7 for
screws or tie rods and ASTM A194 gr. 2H for the nuts.

10
March 2022
Installation, Operation and Maintenance Manual
MAN 646 Rev. 5
Section 2: Installation
Installation
2.5 Hydraulic Connections
! WARNING
Check that the values of hydraulic supply available are compatible with those reported on
the identication plate of the actuator.
NOTICE
The connections should be made by qualied staff.
Use pipes and connections appropriate as for type, material and dimensions.
! WARNING
Use motor uid with purity degree ISO 4406 17/14 or NAS 1638 Class 8 (AS4059 Class
4B-F). For special applications, the lower contamination degree is required. Please refer to
the documentation supplied.
• Properly deburr the ends of rigid pipes.
• Properly clean the interior of pipes sending through them plenty of the supply uid
used in the system.
• Mold and fasten the connection pipes so that no irregular strains at entries or
loosening of threaded connections occur.
• Make the connections according to the operating diagram.
• Check the absence of leakages from hydraulic connections. If necessary, tighten
the nuts of the pipe-ttings.

11
Installation, Operation and Maintenance Manual
MAN 646 Rev. 5
Section 2: Installation
Installation
March 2022
2.6 Electrical Connections (if Any)
! WARNING
Use components appropriate as for type, material and dimensions.
The connections should be made by qualied staff.
Before carrying out any operation, cut line power off.
Safety provisions as per CEI 64-8 regulation should be complied with (same as IEC 60364).
Remove plastic plugs from cable entries.
• Screw the cable glands rmly.
• Introduce connection cables.
• Make the connections in compliance with applicable wiring diagrams on the
documentation supplied.
• Screw the cable gland.
• Replace the plastic plugs of unused entries with metal plugs.
2.7 Commissioning
Upon actuator commissioning, please carry out the following checks:
• Check that paint is not damaged during transport; if necessary, repair the damages
to paint coat.
• Check that the values of hydraulic supply available in the system are compatible
with those reported on the identication plate of the actuator (Figure 1) and on
the documentation supplied.
• Check that the feed voltage values of the electric components (solenoid valve
coils, microswitches, pressure switches, etc.) are compatible with those reported
on the identication plate of the actuator (Figure 1).
• Check that the setting of the components of the actuator control unit
(pressure regulator, pressure switches, ow control valves, etc.) meet the
plant requirements.
• Carry out all kinds of operations and check their proper execution (Section 3.3).
• Check the absence of leakages in the hydraulic connections. If necessary, tighten
the nuts of the pipe-ttings.
• Check proper operation of all the due signalling (valve position, hydraulic supply
pressure, etc.).
• Make a complete functional test in order to verify all the operations are executed
according to operating schematic diagram supplied.
! WARNING
Installation, commissioning and maintenance and repair works should be made by
qualied staff.

12
March 2022
Installation, Operation and Maintenance Manual
MAN 646 Rev. 5
Section 3: Operation and Use
Operation and Use
Section 3: Operation and Use
3.1 Operation Description
The supply uid pressurizes the hydraulic cylinder chamber relevant to the operation to
carry out (opening or closing) (see following pages).
This pressure starts the linear motion of the piston and the consequent motion of the valve
stem that is coupled.
Figure 8
For local or remote operations, please refer to technical documentation furnished
with actuators.
The power and control systems are supplied on specic customer demand.
NOTICE
For all the relevant information, please refer to the specic documentation supplied.

13
Installation, Operation and Maintenance Manual
MAN 646 Rev. 5
Section 3: Operation and Use
Operation and Use
March 2022
Figure 9 Double-acting function with jackscrew manual override MHP
3.2 Residual Risks
! WARNING
The actuator has parts under pressure.
Use due caution.
Use individual protections provided for by the laws and provisions in force.
3.3 Operations
(refer to specic document: operating diagram furnished)
3.3.1 Emergency Manual Operation (MHP)
! WARNING
Refer to applicable control schematic in supplied documentation.
The HLA actuators can have an emergency manual override in addition to the local
and/or remote control system which controls the oil supplied by a power pack for the
“normal” actuator operation.
The emergency manual override mounted on the actuator consists of a hydraulic manual
override and a hydraulic manual selector to choose the actuator “Normal operation” with
oil supply from a power pack, or the “Emergency manual operation”. For nominal pressure
until 105 bar, the manual override is similar to Section 7, Figure 23. For nominal pressure
upper to 105 bar, the manual override will be OMFB for carbon steel material, or dedicated
model engineered by Bif for stainless steel material.

14
TEST/RE-CHARGE POINT
ELECTRIC CONNECTION
TO MICROSWITCHES
CONNECTIONS AT
CUSTOMER CARE
PCS/PSD
OIL SUPPLY LINE
OIL RETURN LINE
March 2022
Installation, Operation and Maintenance Manual
MAN 646 Rev. 5
Section 3: Operation and Use
Operation and Use
3.3.2 Remote Control Operations
Figure 10 Example of control schematics for double-acting HLA actuator
Electric remote control to open
Energize permanently the solenoid
valve 424A.
The opening time is adjustable by the
ow regulator 528B.
Electric remote control to close
De-energize the solenoid valve 424A.
The closing time is adjustable by the ow
regulator 528A.
1 Double-acting hydraulic
linear actuator
34 Hydraulic accumulator (Piston type)
41 Electric microswitches
103 Needle valve with drain valve
282 Rupture disk
302 Panel
351 Stop valve
352 Needle valve
353 Needle valve with drain valve
358 Hydraulic lter with visual indicator
A - Filter
B - Clogging visual indicator
379 Check valve
395 Relief valve
424 5/2 Hydraulic pilot/spring-return
solenoid valve
A - 5/2 Hydraulic pilot/
spring-return valve
B - 3/2 N.C. Poppet type
solenoid valve
528 Undirectional ow regulator
(adjustable setting)
563 Piston position visual indicator
621 Pressure gauge
NOTE:
The diagram is drawn with solenoid valves coils not energized.
E.M.

15
Installation, Operation and Maintenance Manual
MAN 646 Rev. 5
Section 3: Operation and Use
Operation and Use
March 2022
Figure 11 Example of control schematics for double-acting HLA actuator
with power pack
1 Double-acting pneumatic actuator
33 Hydraulic accumulator (bladder type)
292 Electric position transmitter
302 Panel
351 Stop valve
352 Needle valve
354 Hydraulic lter
358 Hydraulic lter with visual indicator
A - Filter
B - Clogging visual indicator
379 Check valve
380 Pilot-operated check valve
384 Dual pilot-operated relief valve
with check valves
A - Pilot-operated relief valve
B - Check valve
395 Relief valve
442 3/2 N.C. Poppet type solenoid
valve (test push button)
519 Electric pressure switch (adjustable)
526 Bidirectional ow regulator
(adjustable setting)
528 Unidirectional ow regulator
(adjustable setting)
540 Handpump
542 Hydraulic rotating pump
553 Quick connector
555 Oil tank
559 Level gauge
561 Oil pouring plug with lter
621 Pressure gauge
954 Electric control panel
956 Electric motor
999 Electronic positioner
Electrohydraulic power unit operation
The operation of electric motor 956
which drives the hydraulic pump 542,
is controlled by the pressure switch 519A
through the electric control panel 954,
so as to maintain the oil pressure into the
accumulator 33 within the xed range.
Regulating service
The electronic positioner 999 energizes the
solenoid valve 442A or 442B in order to reach
the position required by the electric set signal.
Lock in position
When the solenoid valves 442 are not
energized, the actuator is locked in position
by valve 384.
Local control
In case of set signal failure, actuate the
manual override of valve 442B to open or
442A to close during all the valve stroke.
Emergency manual operation
In case of electric supply failure, actuate the
handpump 540A to close or 540B to open.
NOTE:
The diagram is drawn with solenoid valves coils
not energized.
HYDRAULIC CONNECTION ELECTRIC CONNECTION
_ _ _ _ _ _ _ _ _ _ _ _ _ _ _ _
PNEUMATIC CONNECTION
---------------------------------------
ELECTRIC CONNECTION
OF SET SIGNAL (4-20 mA)
ELECTRIC CONNECTIONS
OF POWER SUPPLY (220 V 60 Hz)
AND ALARM SIGNAL (PSL)

16
March 2022
Installation, Operation and Maintenance Manual
MAN 646 Rev. 5
Section 3: Operation and Use
Operation and Use
3.4 Calibration of the Angular Stroke
It is important that the mechanical stops of the actuator (and not those of the valve) stop
the linear stroke at both extreme valve position (fully open and fully closed), except when
this is required by the valve operation.
The setting of the open/closed valve position (upward position) is performed by adjusting
the travel stop screw into the end ange of the hydraulic cylinder and by the adjustment of
the coupling of valve stem to actuator joint for the downward position.
Figure 12 Mechanical stop
Table of contents
Other BIFFI Controllers manuals
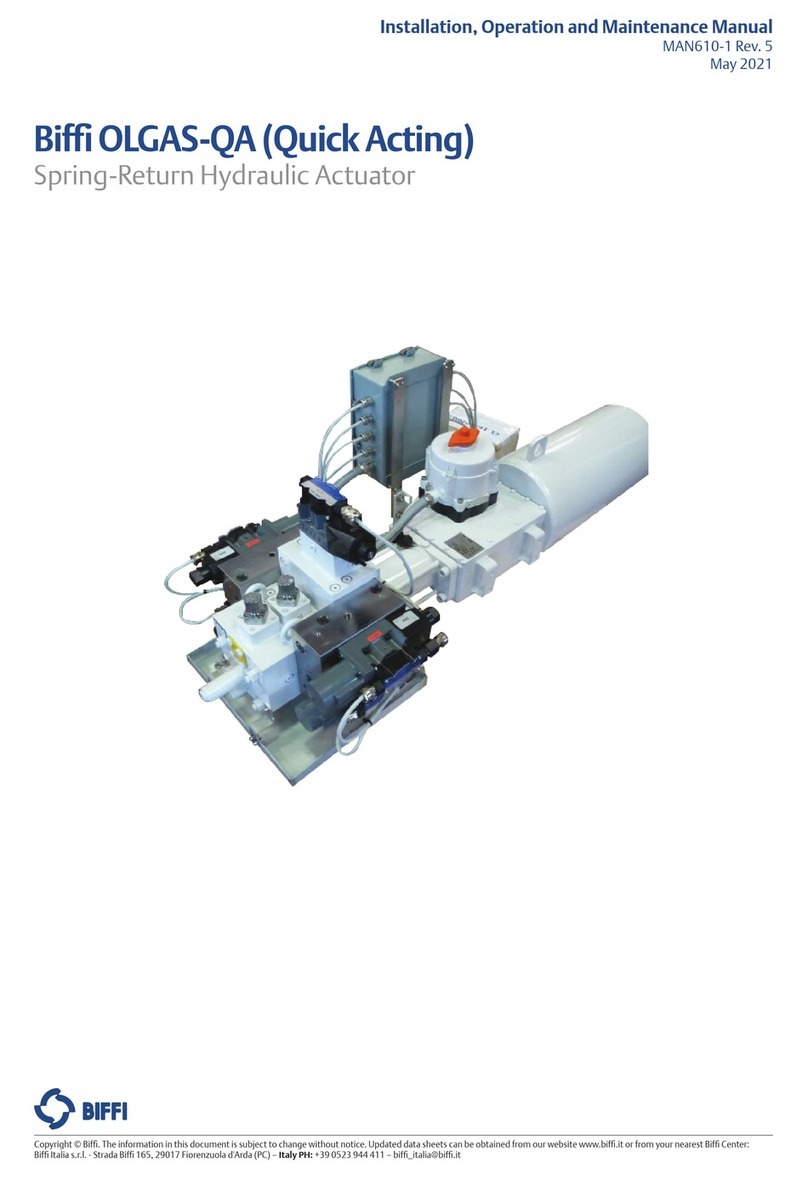
BIFFI
BIFFI OLGAS-QA User manual
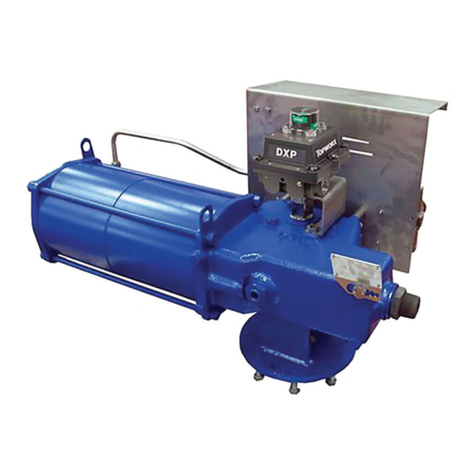
BIFFI
BIFFI RPS Series User manual
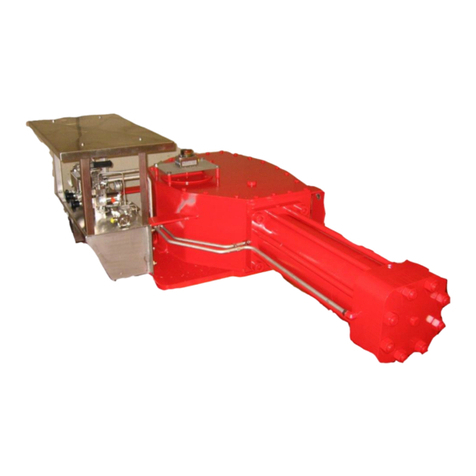
BIFFI
BIFFI OLGA-H User manual
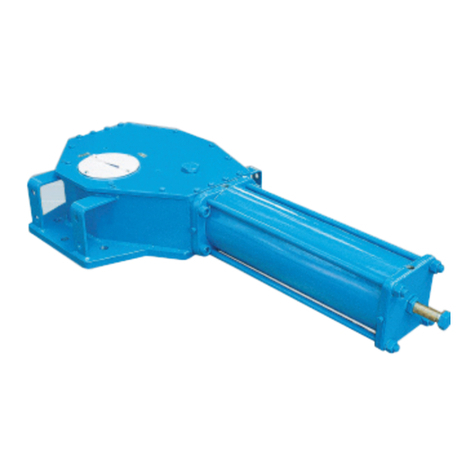
BIFFI
BIFFI OLGA Series User manual

BIFFI
BIFFI ECU 1000 Manual
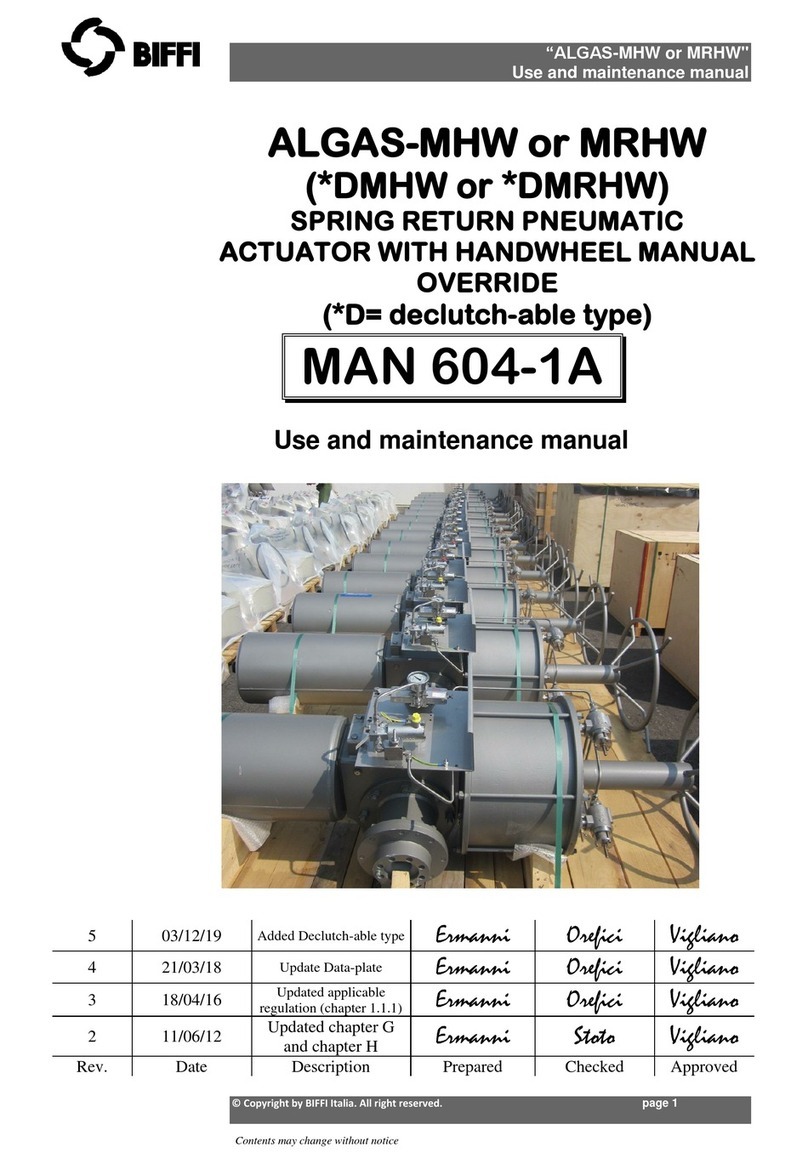
BIFFI
BIFFI ALGAS-MHW User manual
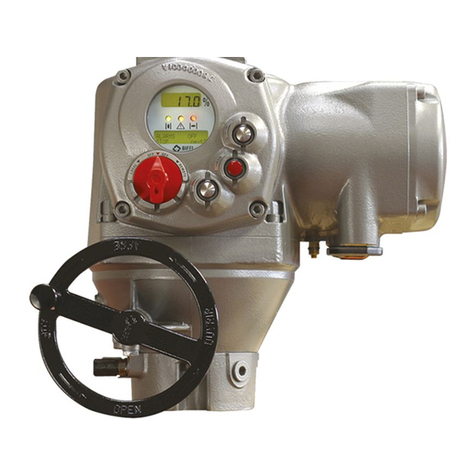
BIFFI
BIFFI F01-2000 User manual
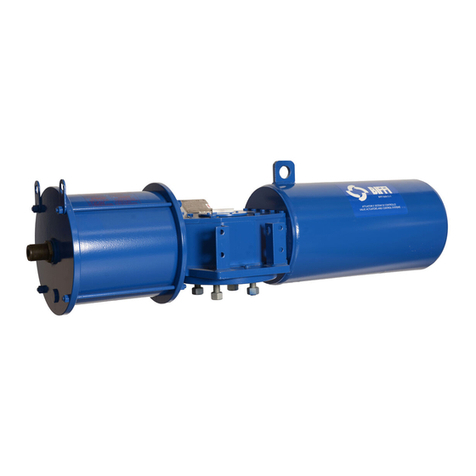
BIFFI
BIFFI ALGAS User manual

BIFFI
BIFFI GIGS 0.3 User manual
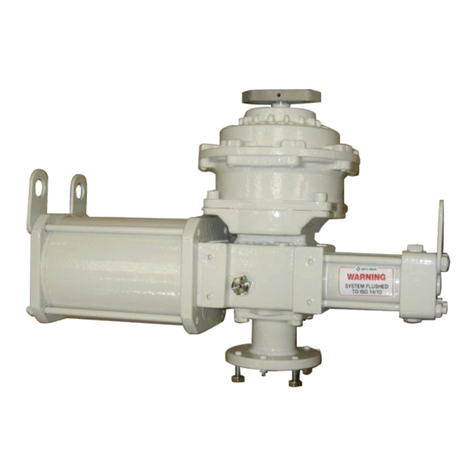
BIFFI
BIFFI RPHD-10 User manual
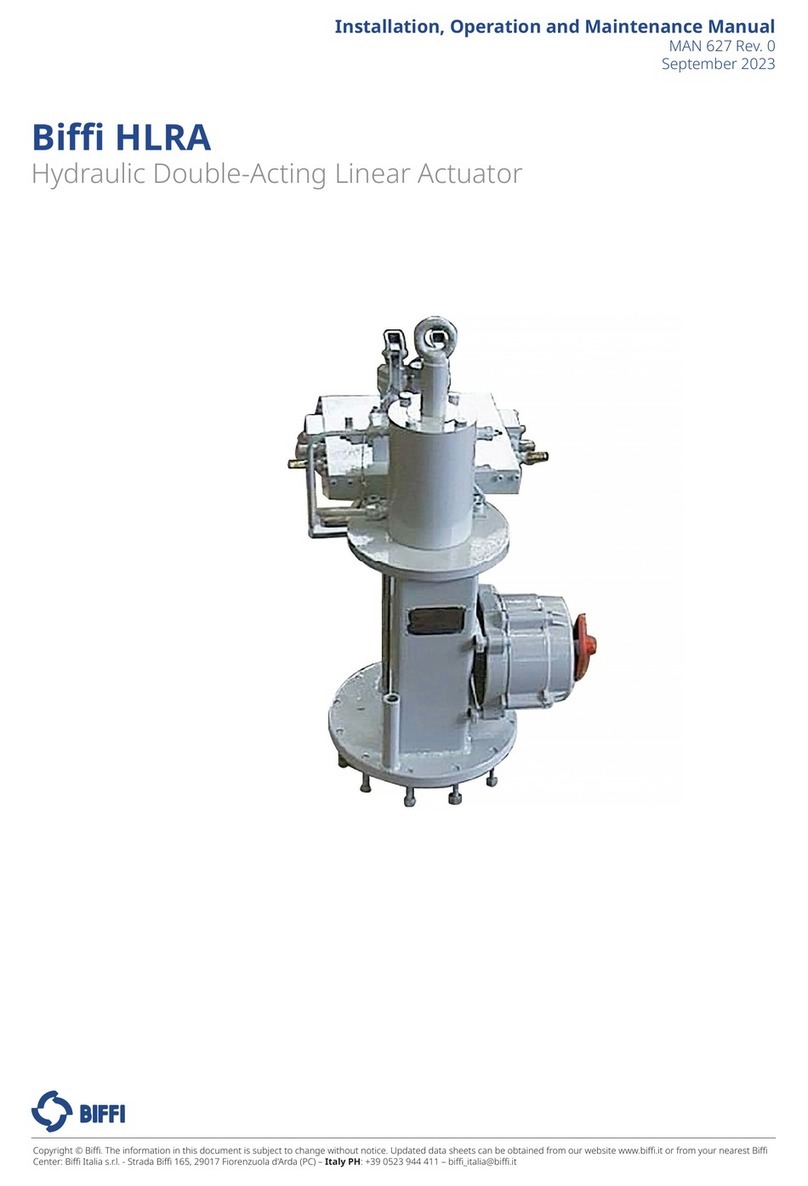
BIFFI
BIFFI HLRA User manual
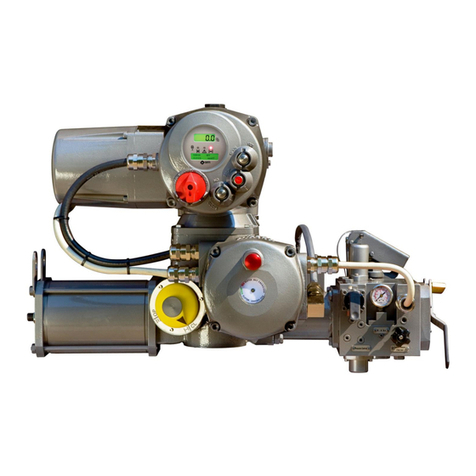
BIFFI
BIFFI EFS2000v4 Parts list manual
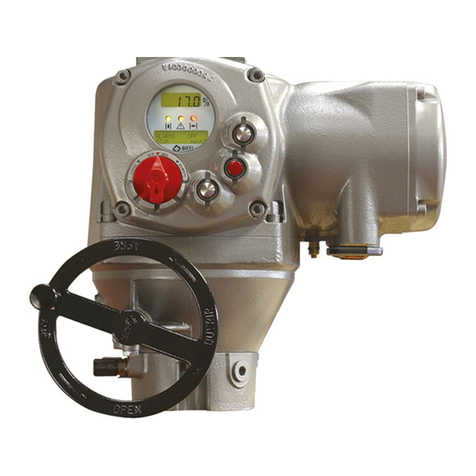
BIFFI
BIFFI F01-2000 Parts list manual
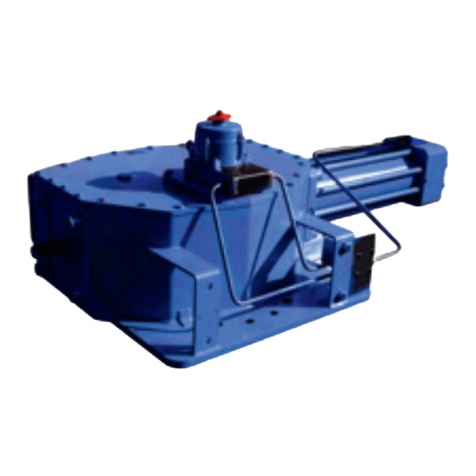
BIFFI
BIFFI OLGA-H User manual
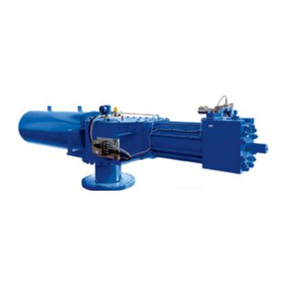
BIFFI
BIFFI OLGAS-H User manual
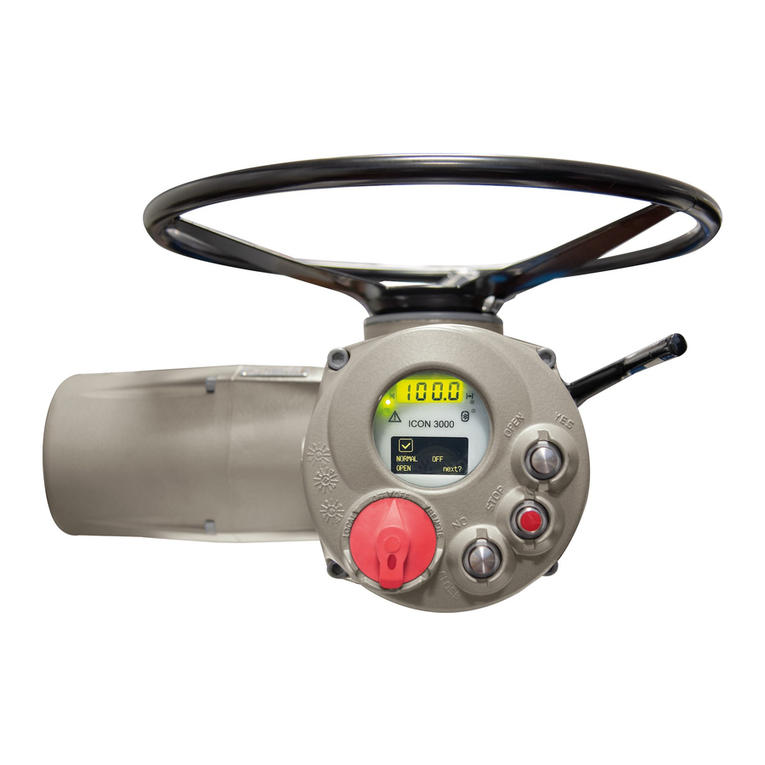
BIFFI
BIFFI ICON3000 Series User manual
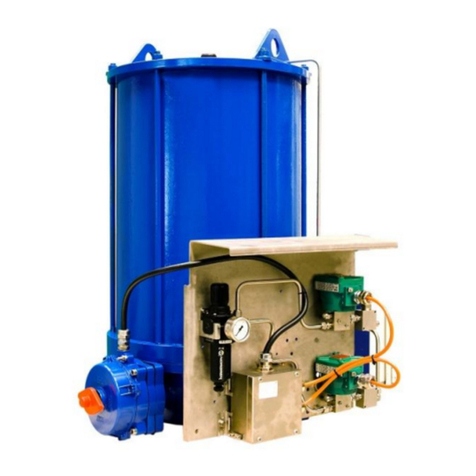
BIFFI
BIFFI TPS Series User manual
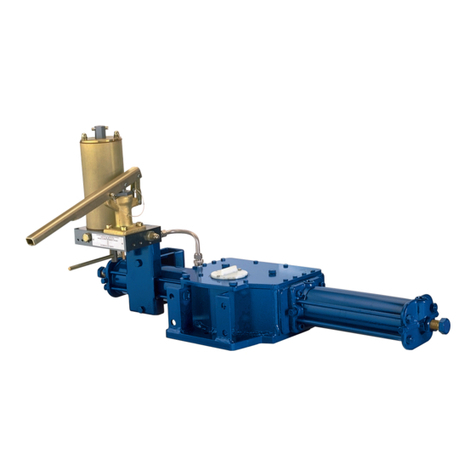
BIFFI
BIFFI GIG User manual
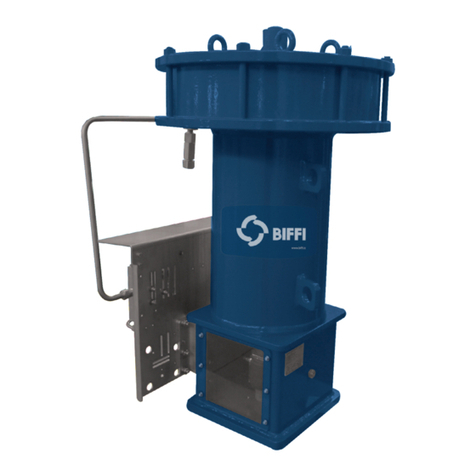
BIFFI
BIFFI PLAS Series User manual
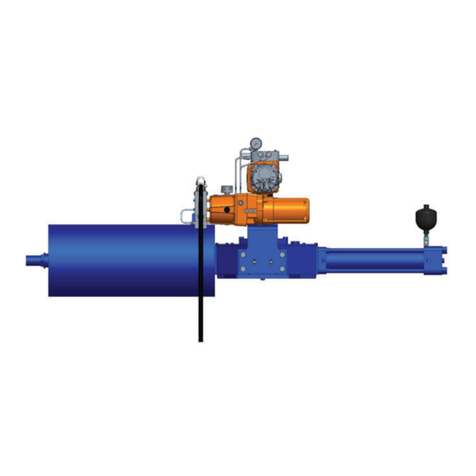
BIFFI
BIFFI EHO User manual