bihl+Wiedemann 1062 User manual

AS-i/CANopen Gateway
User Manual


AS-i/CANopen Gateway Table of Contents
Subject to reasonable modifications due to technical advances.Copyright Bihl+Wiedemann, Printed in Germany
Bihl+Wiedemann GmbH · D-68199 Mannheim · Tel. +49-621-339960 · Fax +49-621-3392239 · Internet http://www.bihl-wiedemann.de
issue date 4.11.1999
3
Table of Contents
1The Used Symbols ...................................................................................7
2Safety ........................................................................................................9
2.1 Intended Use ...........................................................................................................9
2.2 General Safety Information ....................................................................................9
3General Information ...............................................................................11
4Connectors, Displays and Operating Keys .........................................13
4.1 Power Supply Concepts and AS-i Connection Techniques .............................13
4.1.1 Masters with power supply A ..................................................................................13
4.1.2 Masters with power supply N ..................................................................................14
4.2 The fieldbus interface ...........................................................................................17
4.3 Display and Operating Elements ......................................................................... 17
5Operating the AS-i/Gateway ..................................................................19
5.1 Master Start-Up ..................................................................................................... 19
5.2 Configuration Mode .............................................................................................. 19
5.3 Protected Operating Mode ...................................................................................20
5.3.1 Switching to Protected Operating Mode .................................................................20
5.3.2 Configuration Errors in Protected Operating Mode .................................................20
5.4 Assigning an AS-i Address in Configuration Mode ..........................................21
5.4.1 Assigning a Slave Address .....................................................................................21
5.4.2 Erasing the Slave Address ..................................................................................... 21
5.5 Programming the Address in Case of Configuration Errors ............................ 21
5.5.1 Automatic Address Assignment ..............................................................................21
5.5.2 Manual Address Assignment ..................................................................................22
5.6 Adjusting the CANopen node address and baud rate ...................................... 22
5.6.1 CANopen node address ......................................................................................... 22
5.6.2 Baud Rate ...............................................................................................................23
5.7 Error Messages .....................................................................................................23
6Operation As CANopen Node ...............................................................25
6.1 CANopen Parameter Communication ................................................................. 26
6.1.1 Object Directory ......................................................................................................26
6.1.2 Bit Assignment in Object 1001 ................................................................................27
6.1.3 Bit Assignment in Object 1002 ................................................................................27
6.2 Process Data Communication .............................................................................27
6.2.1 Mapping AS-i Data in CANopen PDOs ................................................................... 27
7CANopen telegrams ...............................................................................29
7.1 Representation of a CAN Message .....................................................................29
7.2 Default Identifier Distribution ..............................................................................30
7.2.1 Simplified Boot-up According to CANopen (NMT=0, DBT=0) ................................31
7.2.2 Examples for data exchange ..................................................................................33

AS-i/CANopen Gateway Table of Contents
Subject to reasonable modifications due to technical advances.Copyright Bihl+Wiedemann, Printed in Germany
Bihl+Wiedemann GmbH · D-68199 Mannheim · Tel. +49-621-339960 · Fax +49-621-3392239 · Internet http://www.bihl-wiedemann.de
issue date 4.11.1999
4
8Appendix: Displays of the Figure Display ........................................... 35
9Appendix: Settings of the 80C200 bus timing register ...................... 37
10 Appendix: The First Commissioning of AS-i ...................................... 39

AS-i/CANopen Gateway Declaration of Conformity
Subject to reasonable modifications due to technical advances.Copyright Bihl+Wiedemann, Printed in Germany
Bihl+Wiedemann GmbH · D-68199 Mannheim · Tel. +49-621-339960 · Fax +49-621-3392239 · Internet http://www.bihl-wiedemann.de
issue date 4.11.1999
5
Declaration of Conformity
according to EN 45014:1989
Bihl+Wiedemann GmbH, Mannheim, hereby declares under its sole responsibility
that the products mentioned below are according to the listed harmonized standards
or normative documents and (where neccessary) a component body has been re-
leased.
Specification: AS-i/CANopen Gateway
Article-no.: 1062, 1063
Applied harmonized Standards:
EN 50081-2
EN 50082-2
Applied national standards or normative documents:
AS-i Complete Specification
Prüfungsordnung für AS-i Master
Manufacturer: Bihl+Wiedemann GmbH
Date: 4.11.1999 Bernhard Wiedemann

AS-i/CANopen Gateway Declaration of Conformity
Subject to reasonable modifications due to technical advances.Copyright Bihl+Wiedemann, Printed in Germany
Bihl+Wiedemann GmbH · D-68199 Mannheim · Tel. +49-621-339960 · Fax +49-621-3392239 · Internet http://www.bihl-wiedemann.de
issue date 4.11.1999
6

AS-i/CANopen Gateway The Used Symbols
Subject to reasonable modifications due to technical advances Copyright Bihl+Wiedemann, Printed in Germany
Bihl+Wiedemann GmbH · D-68199 Mannheim · Tel. +49-621-339960 · Fax +49-621-3392239 · Internet http://www.bihl-wiedemann.de
issue date 4.11.1999
7
1The Used Symbols
This symbol warns the user of possible danger. Failure to heed this
warning can lead to personal injury or death and/or damage to equip-
ment.
This symbol warns the user of a possible failure. Failure to heed this
warning can lead to total failure of the equipment or any other con-
nected equipment.
This symbol gives the user important hints.

AS-i/CANopen Gateway The Used Symbols
Subject to reasonable modifications due to technical advance.Copyright Bihl+Wiedemann, Printed in Germany
Bihl+Wiedemann GmbH · D-68199 Mannheim · Tel. +49-621-339960 · Fax +49-621-3392239 · Internet http://www.bihl-wiedemann.de
issue date 4.11.1999
8

AS-i/CANopen Gateway Safety
Subject to reasonable modifications due to technical advances Copyright Bihl+Wiedemann, Printed in Germany
Bihl+Wiedemann GmbH · D-68199 Mannheim · Tel. +49-621-339960 · Fax +49-621-3392239 · Internet http://www.bihl-wiedemann.de
issue date 4.11.1999
9
2Safety
2.1 Intended Use
2.2 General Safety Information
The protection of operating personnel and the system against possible
danger is not guaranteed if the control interface unit is not operated in
accordance with its intended use.
The device may only be operated by appropriately qualified personnel
in accordance with this operating manual.
Safety and correct functioning of the device cannot be guaranteed if any
operation other than that described in this operation manual is per-
formed.
The connecting of the equipment and any maintenance work to be car-
ried out with voltage applied to the equipment must only be performed
by appropriately qualified electrotechnical personnel.
In the case that a failure cannot be repaired, the device must be taken
out of operation and kept from inadvertently put back into operation.
Repair work is to be carried out by the manufacturer only. Additions or
modifications to the equipment are not allowed and void the warranty.
The operator is responsible for the observance of local safety stan-
dards.

AS-i/CANopen Gateway Safety
Subject to reasonable modifications due to technical advance.Copyright Bihl+Wiedemann, Printed in Germany
Bihl+Wiedemann GmbH · D-68199 Mannheim · Tel. +49-621-339960 · Fax +49-621-3392239 · Internet http://www.bihl-wiedemann.de
issue date 4.11.1999
10

AS-i/CANopen Gateway General Information
Subject to reasonable modifications due to technical advances Copyright Bihl+Wiedemann, Printed in Germany
Bihl+Wiedemann GmbH · D-68199 Mannheim · Tel. +49-621-339960 · Fax +49-621-3392239 · Internet http://www.bihl-wiedemann.de
issue date 4.11.1999
11
3General Information
This operating instruction is for use with the following devices of the Bihl+Wiedemann
GmbH:
•AS-i/CANopen Gateway power supply A article-no. 1062
•AS-i/CANopen Gateway power supply N article-no. 1063
The AS-i/CANopen Gateway serves to connect the Actuator-Sensor-Interface to a hi-
erarchically higher CANopen system. The gateway acts as a complete master for the
AS-Interface and as a 128 Bit digital I/O module for CANopen. All basic functions as
well as interrupts, 8 bit groups, etc. are implemented. In case of AS-i configuration er-
rors an emergency message can be released.
As with all Masters of Bihl+Wiedemann, commissioning, debugging and setting up of
the AS-i parameters can be accomplished with the use of two push-buttons, the LCD
display and the LEDs directly on the system, but it can also be handled via CANopen.

AS-i/CANopen Gateway General Information
Subject to reasonable modifications due to technical advance.Copyright Bihl+Wiedemann, Printed in Germany
Bihl+Wiedemann GmbH · D-68199 Mannheim · Tel. +49-621-339960 · Fax +49-621-3392239 · Internet http://www.bihl-wiedemann.de
issue date 4.11.1999
12

AS-i/CANopen Gateway Connectors, Displays and Operating Keys
Subject to reasonable modifications due to technical advances.Copyright Bihl+Wiedemann, Printed in Germany
Bihl+Wiedemann GmbH · D-68199 Mannheim · Tel. +49-621-339960 · Fax +49-621-3392239 · Internet http://www.bihl-wiedemann.de
issue date 4.11.1999
13
4Connectors, Displays and Operating Keys
On the front panel of the AS-i/CANopen Gateways are:
•terminals to connect the power supply and the AS-i circuit
•a interface connector to the hierarchically higher fieldbus
•7 LEDs
•a two-digit seven-segment display
•2 push-buttons to configure the gateway
4.1 Power Supply Concepts and AS-i Connection Techniques
4.1.1 Masters with power supply A
The terminals have the following functions:
•+"AS-i +", Actuator Sensor Interface, positive terminal
•-"AS-i -", Actuator Sensor Interface, negative terminal
•GND,Ground terminal, usedfor better EMC.Should be connectedwith a shortwire
to machine GND.
The AS-i masters with master power supply A do not need a voltage
supply of their own. They can be powered completely out of the AS-i
line (the power consumption is about 200 mA from AS-i). An additional
24 V voltage source is not necessary. The AS-i master merely requires
the connection to the AS-i line. When the AS-i power supply is switched
on, the master starts to operate.
Connection samples for the AS-i power supply:
AS-i master
AS-i power
GND
+
-
+-

AS-i/CANopen Gateway Connectors, Displays and Operating Keys
Subject to reasonable modifications due to technical advances.Copyright Bihl+Wiedemann, Printed in Germany
Bihl+Wiedemann GmbH · D-68199 Mannheim · Tel. +49-621-339960 · Fax +49-621-3392239 · Internet http://www.bihl-wiedemann.de
issue date 4.11.1999
14
4.1.2 Masters with power supply N
At the bottom of the unit there are 10 terminals for the power supply and the AS-i net-
work. The jumper settings (J+, J-) decide whether AS-i is powered by a separate AS-i
power supply or by the power supply that also provides the AS-i Master.
The terminals have the following functions:
+"AS-i +", Actuator Sensor Interface, positive terminal
This terminal is connected internally with the center contact of jumper "J+".
-"AS-i -", Actuator Sensor Interface, negative terminal
This terminal is connected internally with the center contact of jumper "J-".
24V Master power supply, positive terminal (18 - 31.6 V DC)
0V Master power supply, negative terminal
GND Ground terminal, used for better EMC.
Should be connected with a short wire to machine GND.
J+, J- Jumpers for selecting the power supply of AS-i
"int pwr" position (closed):
AS-i is powered by the master power supply.
Master power supply and AS-i network are then decoupled with coils.
"ext pwr" position (open):
With the jumper open (or missing), the AS-i network must be powered by
a separate AS-i power supply.
In the wiring schemes above the current through the AS-i master
must not exceed 5 A.
AS-i Master
max. 10 A
PELV according to EN 60950
(Protective extra low voltage)
AS-i
power
supply
-
+
AS-i Slave
-
+
AS-i Slave
-
+
AS-i Master
max. 5 A
PELV according to EN
60950 (Protective extra
low voltage)
AS-i
power
supply
-
+
AS-i Slave
-
+
AS-i Slave
-
+
AS-i Master
AS-i power
GND24V 0V+-J+ J-

AS-i/CANopen Gateway Connectors, Displays and Operating Keys
Subject to reasonable modifications due to technical advances.Copyright Bihl+Wiedemann, Printed in Germany
Bihl+Wiedemann GmbH · D-68199 Mannheim · Tel. +49-621-339960 · Fax +49-621-3392239 · Internet http://www.bihl-wiedemann.de
issue date 4.11.1999
15
TheAS-ipowersupplycan be connected to the jumper ortotheAS-icable
in the field.
Operation without AS-i power supply
When the jumpers are in position "int pwr", the AS-i network is powered by the mas-
ter's power supply. For test purposes, it is possible to use a conventional 24 V DC
power supply to supply the AS-i network. You get optimum results with a 30 V DC volt-
age source.
This connection technique serves also for providing more than one AS-i Master out of
one master power supply because each AS-i circuit is decoupled with its own in the
AS-i Master integrated coils.
For the following wiring scheme the current through the AS-i mas-
ter must not exceed 2.8 A.
AS-i Master
-
+
Master
power
supply
max. 2.8 A
29.5 - 31.6 V DC
PELV according to EN 60950
(Protective extra low voltage)
AS-i Slave
-
+
AS-i Master N
-
+
Master
power
supply
max. N x 2.8 A
29.5 - 31.6 V DC
PELV according to
EN 60950
(Protective extra low
voltage)
Fuse
2.8 A T
Fuse
2.8 A T Fuse
2.8 A T
...
AS-i Slave
-
+
AS-i Master 2
AS-i Slave
-
+
AS-i Master 1
AS-i Slave
-
+

AS-i/CANopen Gateway Connectors, Displays and Operating Keys
Subject to reasonable modifications due to technical advances.Copyright Bihl+Wiedemann, Printed in Germany
Bihl+Wiedemann GmbH · D-68199 Mannheim · Tel. +49-621-339960 · Fax +49-621-3392239 · Internet http://www.bihl-wiedemann.de
issue date 4.11.1999
16
Operation with AS-i power supply
In the jumper position "ext pwr" the AS-i network needs an additional AS-i power sup-
ply.
Do not try to provide the AS-i Master with power supply N out of the AS-i power supply
of the AS-i circuit („backwards“), because the additional decoupling coils would bur-
den the AS-i line and cause erroneous AS-i telegrams.
AS-i Master
18 - 31.6 V
150 mA
PELV according to EN 60950
(Protective extra low voltage)
max. 10 A
PELV according to EN 60950
(Protective extra low voltage)
AS-i
powers
upply
-
+
AS-i Slave
-
+
-
+
master
powers
upply
AS-i Master
AS-i
powers
upply
-
+
AS-i Slave
-
+

AS-i/CANopen Gateway Connectors, Displays and Operating Keys
Subject to reasonable modifications due to technical advances.Copyright Bihl+Wiedemann, Printed in Germany
Bihl+Wiedemann GmbH · D-68199 Mannheim · Tel. +49-621-339960 · Fax +49-621-3392239 · Internet http://www.bihl-wiedemann.de
issue date 4.11.1999
17
4.2 The fieldbus interface
According to the CANopen specification the CANopen interface connector is de-
signed as a 5-pin COMBICON connector. It is located on the right hand side of the
front panel.
4.3 Display and Operating Elements
On the front panel of the AS-iCANopen Gateway are seven light-emitting diodes, a
two-digit display and two push buttons.
power The master's power supply is sufficient.
MNS Red LED flashes: no CAN communication in "Pre Operation-
al Mode"
Green LED flashes: CAN communication node in "Pre Opera-
tional Mode"
Green LED: CAN communication node in "Operational
Mode"
config err Configuration error
At least one configured slave is missing, or at least one detected
slave is not projected or for at least one projected and detected
slave the actual configuration data does not match the nominal
configuration data.
U ASI The AS-i circuit is sufficiently powered.
ASI active Normal operation active.
prg enable Automatic address programming enabled.
Exactly one slave is missing in protected operating mode. The
slave can be replaced by another slave of the same type with ad-
dress zero. The master addresses the new slave to the faulty ad-
dress and thus eliminates the configuration error.
prj mode The AS-i Master is in configuration mode.
5 V - (not used by the AS-i master)
4 CAN -
3 Shield
2 CAN+
1 V + (not used by the AS-i master)
nicht verwendet)
COMBICON connector

AS-i/CANopen Gateway Connectors, Displays and Operating Keys
Subject to reasonable modifications due to technical advances.Copyright Bihl+Wiedemann, Printed in Germany
Bihl+Wiedemann GmbH · D-68199 Mannheim · Tel. +49-621-339960 · Fax +49-621-3392239 · Internet http://www.bihl-wiedemann.de
issue date 4.11.1999
18

AS-i/CANopen Gateway Operating the AS-i/Gateway
Subject to reasonable modifications due to technical advances Copyright Bihl+Wiedemann, Printed in Germany
Bihl+Wiedemann GmbH · D-68199 Mannheim · Tel. +49-621-339960 · Fax +49-621-3392239 · Internet http://www.bihl-wiedemann.de
issue date 4.11.1999
19
5Operating the AS-i/Gateway
5.1 Master Start-Up
After powering on, all segments of the figure display and all LEDs light up for approx-
imately one second (self-test). Afterwards, the LEDs display the condition of their re-
spective flags. The LCD displays the condition of the master:
40 Off-line Phase
The AS-i Master initializes - there is no data communication on the AS-i.
41 Detection Phase
Start of the start-up phase, where the system looks for slaves located on
the AS-i. The master remains in the detection phase until it finds at least
one slave.
42 Activation Phase
Condition at the end of the start-up operation where the parameters are
transmitted to all connected and recognized slaves. This enables access
to the AS-i slaves’ data connections.
431Start of Normal Operation
In normal operation the AS-i master can exchange data with all active
slaves. It transmits management messages and looks for and activates
newly connected slaves. During normal operation, the system keeps the
maximum cycle time of 5 milliseconds.
5.2 Configuration Mode
The configuration mode serves to configure the AS-i circuit.
Pressing the “mode” button for at least five seconds switches the master to configu-
ration mode. While in configuration mode, the yellow “prj mode” LED lights up.
The system then displays one after the other all detected slaves at a speed of two per
second. If the display is empty, no slaves were detached on the AS-i circuit.
In configuration mode, all recognized slaves are activated except of slave zero. The
AS-i Master is in normal operation. There is data exchange between the AS-i Master
If the AS-i circuit is insufficiently powered (“U ASI” does not
light up) or there is no communication relationship between
the CANopen master and the AS-i/CANopen Gateway, the
master remains in the off-line phase.
1. Activation phase and the start of normal operation maybe so short that the numbers can not be seen in the display.
In the configuration mode, all recognized slaves are activated even
when the desired and actual configurations do not match.

AS-i/CANopen Gateway Operating the AS-i/Gateway
Subject to reasonable modifications due to technical advance.Copyright Bihl+Wiedemann, Printed in Germany
Bihl+Wiedemann GmbH · D-68199 Mannheim · Tel. +49-621-339960 · Fax +49-621-3392239 · Internet http://www.bihl-wiedemann.de
issue date 4.11.1999
20
and all AS-i slaves detected by the master regardless of whether the detected AS-i
slaves were projected before.
When delivered the AS-i/Gateway is in configuration mode.
5.3 Protected Operating Mode
5.3.1 Switching to Protected Operating Mode
Pressing the button shortly:
Exits the configuration mode without projecting the current AS-i configuration.
Pressing the button for more than five seconds:
Exits the configuration mode and projects the actual AS-i configuration. Si-
multaneously the actual AS-i configuration is stored as nominal configuration
in the EEPROM.
In the protectedoperating mode, only AS-islaves that are projected and whose actual
configurations match the nominal configurations will be activated.
5.3.2 Configuration Errors in Protected Operating Mode
As long as there is no configuration error, the numeric display is turned off while in
protected operating mode. Otherwise, the that address a faulty assignment is dis-
played. A faulty assignment occurs when a slave has been recognized or projected
but cannot be activated.
If there are more than one faulty assignments the one that was first detected is dis-
played. Pressing the “set” button shortly displays the next higher faulty address.
Shortly appearing configuration errors are stored in the device (advanced AS-i diag-
nosis). The last error that occurred can be displayed by pressing the set button. If a
short AS-i power failure is responsible for the configuration error the display shows a
“39“.
In contrast with the configuration mode in the protected mode there is
only data exchange between the AS-i Master and the projected AS-i
slaves.
You leave the configuration mode by pressing the “mode” button.
If the system detects an AS-i slave with address zero on the AS-i, it can
not leave the configuration mode.
This manual suits for next models
1
Table of contents
Other bihl+Wiedemann Gateway manuals

bihl+Wiedemann
bihl+Wiedemann AS-i 2.1 User manual
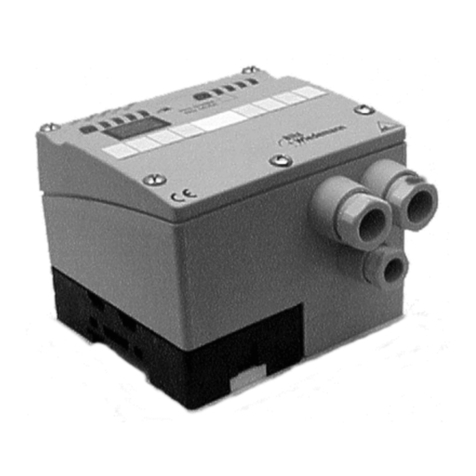
bihl+Wiedemann
bihl+Wiedemann 1435 User manual
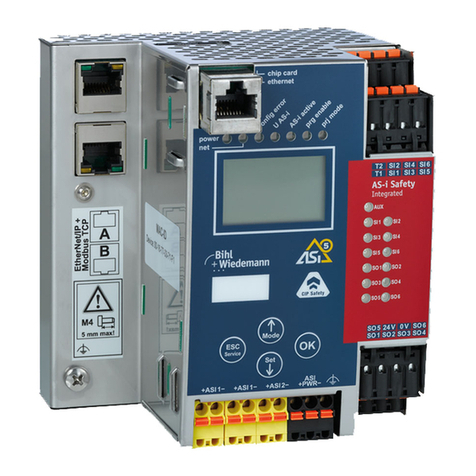
bihl+Wiedemann
bihl+Wiedemann BWU3857 User manual
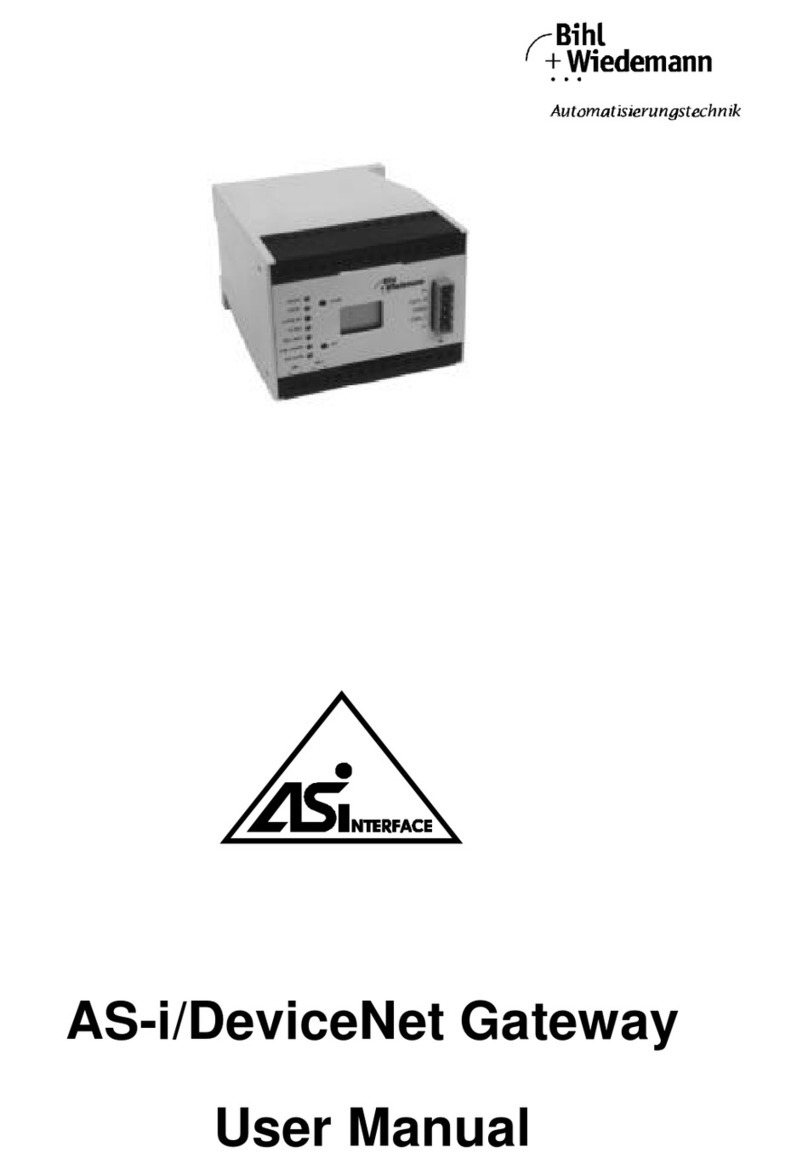
bihl+Wiedemann
bihl+Wiedemann 1116 User manual
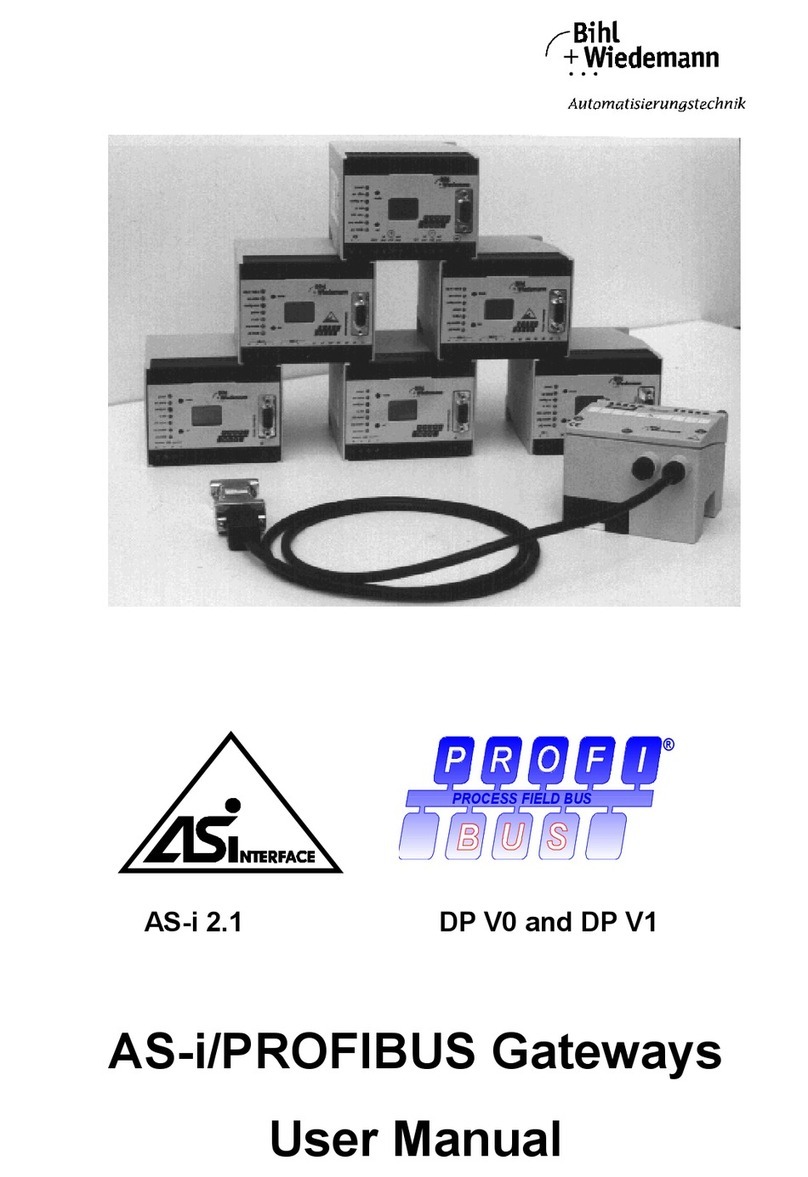
bihl+Wiedemann
bihl+Wiedemann 1249 User manual
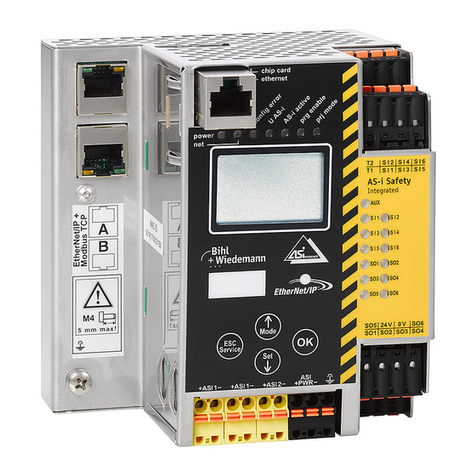
bihl+Wiedemann
bihl+Wiedemann BWU3543 User manual

bihl+Wiedemann
bihl+Wiedemann BWU3683 User manual
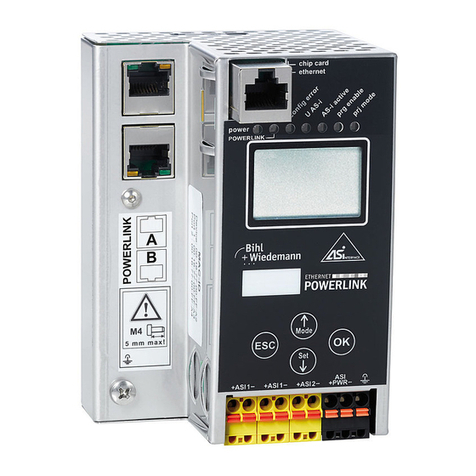
bihl+Wiedemann
bihl+Wiedemann BWU3593 User manual
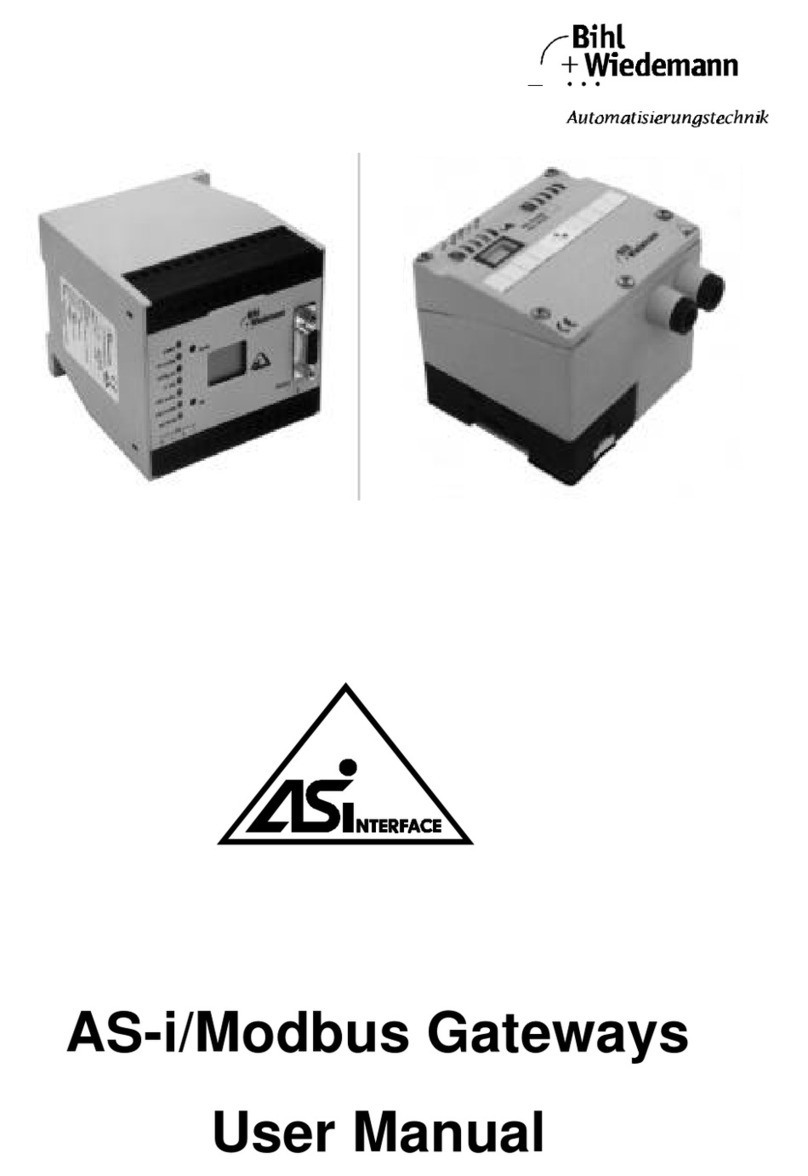
bihl+Wiedemann
bihl+Wiedemann AS-i/Modbus Gateway User manual