BIRO Mini-32 Service manual

IMPORTANT NOTICE
This Manual contains important
safety instructions which must
be strictly followed when using
this equipment. Item No. 32313-299
Form No. Mini-32-3-19-9 B
Model MINI-32
AUTOMATIC FEED MIXER GRINDER
Operating and Service Manual


TABLE OF CONTENTS:
NOTICE TO OWNERS AND OPERATORS . . . . . . . . . . . . . . . . . . . . . . . . . . . . . . . . . . . . . . . . . . . . . .
PAGE
SAFETY TIPS . . . . . . . . . . . . . . . . . . . . . . . . . . . . . . . . . . . . . . . . . . . . . . . . . . . . . . . . . . . . . . . . . . . . . .
INSTALLATION . . . . . . . . . . . . . . . . . . . . . . . . . . . . . . . . . . . . . . . . . . . . . . . . . . . . . . . . . . . . . . . . . . . .
CLEANING . . . . . . . . . . . . . . . . . . . . . . . . . . . . . . . . . . . . . . . . . . . . . . . . . . . . . . . . . . . . . . . . . . . . . . . .
1
2
3
7
OPERATION . . . . . . . . . . . . . . . . . . . . . . . . . . . . . . . . . . . . . . . . . . . . . . . . . . . . . . . . . . . . . . . . . . . . . . .
8
MOTOR WIRING AND ELECTRICAL REQUIREMENTS . . . . . . . . . . . . . . . . . . . . . . . . . . . . . . . . . .
4
PRE-OPERATION . . . . . . . . . . . . . . . . . . . . . . . . . . . . . . . . . . . . . . . . . . . . . . . . . . . . . . . . . . . . . . . . . . .
5
PARTS LOCATION . . . . . . . . . . . . . . . . . . . . . . . . . . . . . . . . . . . . . . . . . . . . . . . . . . . . . . . . . . . . . . . . . . 6
REMOVAL & INSTALLATION INSTRUCTIONS . . . . . . . . . . . . . . . . . . . . . . . . . . . . . . . . . . . . . . . . .
9
MAINTENANCE & LUBRICATION . . . . . . . . . . . . . . . . . . . . . . . . . . . . . . . . . . . . . . . . . . . . . . .
10 - 12
PARTS LIST DIAGRAMS . . . . . . . . . . . . . . . . . . . . . . . . . . . . . . . . . . . . . . . . . . . . . . . . . . . . . . .
13 - 18
FASTENERS & LOCATIONS . . . . . . . . . . . . . . . . . . . . . . . . . . . . . . . . . . . . . . . . . . . . . . . . . . . . . . . . .
19
27
ELECTRICAL SCHEMATICS . . . . . . . . . . . . . . . . . . . . . . . . . . . . . . . . . . . . . . . . . . . . . . . . . . . .
20 - 24
FOOTSWITCHES, PNEUMATIC & ELECTRIC . . . . . . . . . . . . . . . . . . . . . . . . . . . . . . . . . . . . . 25 - 26
SAFETY LABEL LOCATIONS . . . . . . . . . . . . . . . . . . . . . . . . . . . . . . . . . . . . . . . . . . . . . . . . . . . . . . .
28
OPERATOR SIGNATURE PAGE . . . . . . . . . . . . . . . . . . . . . . . . . . . . . . . . . . . . . . . . . . . . . . . . . . . . . .
29
LIMITED WARRANTY . . . . . . . . . . . . . . . . . . . . . . . . . . . . . . . . . . . . . . . . . . . . . . . . . . . . . . . . . . . . .

NOTICE TO OWNERS AND OPERATORS
BIRO’s products are designed to process food products safely and efciently. Unless the opera-
tor is properly trained and supervised, however, there is the possibility of a serious injury. It is the
responsibility of the owner to assure that this machine is used properly and safely, strictly following
the instructions contained in this Manual and any requirements of local law.
Warnings related to possible damage are indicated by:
BIRO also has provided warning labels on the equipment. If any warning label, instruction label
or Manual becomes misplaced, damaged, or illegible, please contact your nearest Distributor or
BIRO directly for a replacement.
Remember, however, this Manual or the warning labels do not replace the need to be alert and to
use your common sense when using this equipment.
- NOTE -
A copy of this manual is included with each MODEL MINI-32 MIXER GRINDER.
The descriptions and illustrations contained in this manual are not binding.
The manufacturer reserves the right to introduce any modication without updating
the manual.
1
No one should use or service this machine without proper training and supervision. All operators
should be thoroughly familiar with the procedures contained in this Manual. Even so, BIRO cannot
anticipate every circumstance or environment in which its products will be used. You, the owner
and operator, must remain alert to the hazards posed by the function of this equipment
particularly the ROTATING GRINDING AUGER and the ROTATING MIXING PADDLE, which
can severely injure an inattentive operator amputating ngers and limbs. No one under eighteen
(18) years of age should operate this equipment. If you are uncertain about a particular task, ask
your supervisor.
This Manual contains a number of safe practices in the SAFETY TIPS section. Additional warn-
ings are placed throughout the Manual. Warnings relate to your personal safety are indicated by:
or

2
SAFETY TIPS
ROTATING GRINDING AUGER & ROTATING MIXING PADDLE
TO AVOID SERIOUS PERSONAL INJURY
• NEVER Touch This Machine without Training and Authorization by Your Supervisor.
• NEVER Place Hands into Machine Input or Output Openings.
• NEVER Open Machine During Operation.
• ONLY Use a Qualied Electrician to Install According to Local Building Codes: Machine MUST
Be Properly Grounded.
• ALWAYS Connect to PROPER Voltage & Phase.
• ONLY Install on Level, Non-Skid Surface in a Clean, Well-Lighted Work Area Away from
Children and Visitors.
• ALWAYS Lock Machine Castors After Moving This Machine.
• NEVER Use This Machine For Non-Food Products.
• NEVER Operate Machine With Product Mixer Safety Cover Open or Removed or Magnetic
Interlock Switch By-Passed.
• ALWAYS Turn Off, Unplug Machine From Power Source and Perform Lockout/Tagout Procedure
to this Machine BEFORE Attempting to Unjam or Unclog, Cleaning or Servicing.
• NEVER Leave Machine Unattended While Grinder is Running.
• NEVER Alter This Machine From its Original Form as Shipped From Factory. DO NOT Operate
Machine With Missing Parts.
• PROMPTLY REPLACE Any Worn or Illegible Warning Labels.
• ALWAYS Read Operation and Service Manual BEFORE Operating, Cleaning, or Servicing.
• USE ONLY BIRO Parts and Accessories Properly Installed.

INSTALLATION
TO AVOID SERIOUS PERSONAL INJURY, PROPERLY INSTALL
EQUIPMENT IN ADEQUATE WORK AREA
3
• ALWAYS Connect to Proper Voltage & Phase.
• NEVER Operate Machine With Product Mixer Safety Cover Open or Removed or Magnetic
Interlock Switch By-Passed.
• ALWAYS Use Qualied Technician and Electrician for Installation.
• ALWAYS Install Equipment in Work Area with Adequate Light and Space Away From Children
and Visitors.
• ONLY Operate on a Solid, Level, Non-Skid Surface.
• ALWAYS Lock Machine Castors After Moving Machine.
• NEVER Bypass, Alter, or Modify This Equipment in Any Way From Its Original Condition.
• NEVER Operate Without all Warning Labels Attached and Owner/Operator Manual Available to
the Operator.
• USE ONLY BIRO Parts and Accessories Properly Installed.
UNCRATING AND SET UP
1. Read this Manual thoroughly before installation and operation. Do not proceed with installation and
operation if you have any questions or do not understand anything in this Manual. Contact your local
Distributor, or BIRO rst.
2. Remove all banding, shipping carton, and all equipment from inside the tub. Then take machine off
shipping pallet.
3. Install machine on a level, non-skid surface in a well-lighted work area away from children and visitors.
4. This machine is complete except for knife and plate. There is a bowl shipping plug (cardboard)
placed in the output end of the grinding bowl to retain the grinding auger during shipment. REMOVE
THE BOWL SHIPPING PLUG AND THE GRINDING AUGER.
5. After checking and making sure the power supply is correct, plug in your machine. NEVER OPERATE
MACHINE WITH PRODUCT MIXER SAFETY COVER OPEN OR HOPPER REMOVED.
(Machine will not run with cover open.)
6. Machine must be properly grounded. Use qualied electrician to install according to local building codes.

MOTOR WIRING AND ELECTRICAL REQUIREMENTS
1. Interchange of motor current is made in motor outlet box. Leads are properly marked. Changing
instructions are on the motor plate or inside junction box cover.
NOTE TO OWNER AND ELECTRICIAN: IF THIS MACHINE IS NOT CORD
AND PLUG CONNECTED TO THE ELECTRICAL SUPPLY SOURCE, THEN IT
SHOULD BE EQUIPPED WITH, OR CONNECTED TO, A LOCKABLE,
MANUALLY-OPERATED DISCONNECT SWITCH (OSHA 1010.147)
4
2. All grinders are wired 208-230 volts unless otherwise specied. Be sure motor specications (voltage,
cycle, phase) match power supply line. Be sure line voltage is up to specication.
3. Connect leads to machine in a manner that will be approved by local electrical inspectors.
4. Rated voltage of the unit shall be identical with full supply voltage.
5. Voltage drop on the supply line shall not exceed 10% of full supply voltage.
7. The feederline conductor shall only be used for the supply of one unit of the relevant horsepower. For
connections of more than one unit on the same feederline, a local electrician will have to be consulted to
determine the proper conductor size.
6. The feederline conductor size in the raceway from the branch circuit to the unit must be correct to assure
adequate voltage under heavy starting and short overload conditions.
8. The size of the electrical wiring required from the power source to the mixer grinder/chopper is a
MINIMUM OF No. 12 WIRE.
9. The BIRO Manufacturing Company is not responsible for permanent wiring, connection or installation.
MOTOR SPECIFICATIONS
HP KW VOLTS HZ PH AMPS
3 2.2 208/230 60 3 9.7/9.4
3 2.2 208/230 60 1 24/21
3 2.2 460 60 3 4.6
2.5 1.9 380/415 50 3 5.3/4.9

5
11. Turn the toggle hand/foot selector switch to the hand position and move the Auger Engage Lever to
“Grind”to activate the grinding drive shaft. Push the green start button. CHECK THE ROTATION OF
THE AUGER DRIVE SHAFT; ROTATION MUST BE COUNTER-CLOCKWISE as indicated by
the rotation decal afxed to the grinding bowl.
ONLY HAND TIGHTEN END RETAINING RING
15. Check placement of all warning labels and be sure anyone who is to operate this MINI-32 MIXER
GRINDER has read and fully understands the manual. Machine is now ready for trained operators to
process product.
16. Use meat deector attached to grinding bowl to eliminate meat splatter.
17. Contact your local distributor if you have any questions or problems with the installation or operation of
this machine.
12. If machine runs clockwise(backwards), it must be rewired to correct rotation, otherwise serious
irreparable damage may occur to the grinding components.
PRE-OPERATION AND AUGER ROTATION CHECK
ROTATION MUST ONLY BE CHECKED WITH THE
GRINDING AUGER REMOVED, otherwise serious irreparable
damage may occur to grinding components.
13. Check operation of optional footswitch if equipped. Plug footswitch cord into tting on control panel.
Turn selector to foot. The machine will operate with pressure on the footswitch treadle. Releasing the
treadle stops the machine.
14. Insert auger assembly into the grinding bowl and fully engage the auger into the drive shaft. Place knife
rst (sharp edges out) then grinding plate into end of grinding bowl. The grinding plate slides over the
knife drive pin, and is held from rotating during operation by three pins in the grinding bowl. Install the
end retaining ring.
For best results, use knife and plate as a set. Do not operate machine
for any period of time without product in the grinding bowl. This will
cause heating and dulling of the knife and plate.
10. The start/stop switches and the grind engage lever are located on the right side of the machine when facing
the grinding bowl. The start switch will activate the mixer paddles. The start switch will also activate the
grinding auger, only when the grind lever is in the engaged, or in the grind position. The stop switch will
stop operation. To deactivate the grinding operation move the grind lever to the disengaged, or to the mix
position. The tank and hopper cover interlock switches are located in the motor compartment. When the
safety cover is raised the machine will stop operation.

PARTS LOCATION
6
AUGER DRIVE ENGAGE LEVER
ENGAGED DISENGAGED

OPERATION
• NEVER Place Hands into Machine Input or Output Openings.
• ONLY Properly Trained Personnel Should Use This Equipment.
7
• NEVER Open Machine During Operation.
• NEVER Operate Machine With Product Mixer Safety Cover Opened or Hopper Removed or Magnetic
Interlock Switch By-Passed.
• ALWAYS Turn Off and Unplug Machine from Power Source and Perform Lockout/Tagout
Procedure to This Machine BEFORE Unjamming, Unclogging, Cleaning or Servicing or When Not in Use.
• NEVER Operate Without All Warning Labels Attached and Owner/Operator Manual Available to
the Operator.
• DO NOT Wear Gloves While Operating.
• DO NOT Tamper With, Bypass, Alter, or Modify This Equipment in Any Way From Its Original Condition.
• NEVER Leave Machine Unattended While the Grinder is Running.
A. TO PROCESS PRODUCT
1. Before starting the mixer grinder, have a container for receiving ground product at the output end of the
grinding bowl.
2. FIRST GRIND
3. SECOND GRIND
4. Unplug machine from power source and perform lockout/tagout procedures.
a. Fill Product Hopper (Maximum 60 Pounds), and close Product Mixer Safety Cover.
b. With the Auger Engage Lever disengaged, in the “Mix” postion and the selector switch in hand postion,
push the green start button. During this mix operation, seasonings may be added through the sight holes
in the Product Mixer Safety Cover.
c. After the desired mix, engage the Auger Engage Lever by moving it into the “Grind” position to operate
the grinding auger and grind out the product.
b. Push the green start button with the selector switch in hand position and engage the Auger Engage
Lever by moving it to the “Grind” position to feed rst grind. It is recommended to use a breaker plate
with a ⅜” diameter or larger holes.
c. Push the red stop button and disengage the Auger by moving the Auger Engage Lever to the “Mix”
position when all product has been ground out.
a. Fill Product Hopper (Maximum 60 Pounds), and close Product Mixer Safety Cover.
d. Push the red stop button and disengage the grinder by moving the Auger Engage Lever to “Mix” when
all product has been ground out.
ROTATING GRINDING AUGER & ROTATING MIXING PADDLE
TO AVOID SERIOUS PERSONAL INJURY

8
DO’s DON’Ts
• Always keep knife & plate as matched set.
• Always keep the knife & plate sharp.
• Always install the knife & plate in correct
sequence, knife 1st, then plate.
• Always inspect the plates making sure all holes
are clear - that there are no cracks.
• Always keep knives & plates lubricated in storage
and when starting machine.
• Always check for straightness by laying the knife
on the plate before inserting in machine.
• Always use coolant when sharpening plates.
• Never, never mix different knives to different plates.
• Never, never over tighten the bowl retaining ring
on the machine.
• Never, never hit the plate against anything to
clean the holes.
• Never, never run the grinder without product.
Product is a natural lubricant. Heat can build up so
fast that cold product could crack the plate.
• Never, never throw the knives & plates.
CLEANING
• ALWAYS Turn Off, Unplug Machine From Power Source and Perform Lockout/Tagout
Procedure to this Machine BEFORE Cleaning or Servicing.
• ONLY Use Recommended Cleaning Equipment, Materials, and Procedures.
• NEVER Spray Water or Other Liquid Substances Directly at Motor, Power Switch or any Other
Electrical Components.
• ALWAYS Thoroughly Clean Equipment at Least Daily.
CLEANING THE MINI-32 MIXER-GRINDER
l. Disconnect mixer grinder from power-source and perform lockout/tagout procedures.
2. Remove grinding bowl end ring, breaker plate, knife and grinding auger.
3. Remove mixing paddle, hopper and grinding bowl assembly from machine (see instruction on page 9).
4. Machine is now ready to be cleaned using warm soapy water and rinsed with clean water. Machine may be
cleaned by power spray washing, taking care not to spray directly at any electrical controls.
5. After machine has been cleaned and allowed to air dry, all exposed metal surfaces should be coated with a
good food grade light oil or grease.
BEFORE CLEANING OR SERVICING
6. Never wash the clear hopper cover with abrasive cleaners. Use a soft cloth and warm soapy water only.

9
REMOVAL & INSTALLATION INSTRUCTIONS
PADDLE REMOVAL:
Remove mixing paddle by rst locating and lifting up on the hopper lock down clamps releasing them
from the hopper. Next loosen the paddle lock knob (four point knob located at the front of the hopper).
Then turn the locking lever clockwise approximately ¼ turn and remove to unlock the paddle shaft
from the hopper. Slide paddle shaft toward front of hopper and lift drive end up and out to remove
paddle.
PADDLE INSTALLATION:
Install paddle shaft by rst connecting the driven end of the paddle shaft to the driver hub.
Insert the locking lever and tighten the paddle lock knob.
HOPPER REMOVAL:
After the paddle shaft has been removed, be sure the hopper lock down clamps have been lifted and
lock down rods extracted from the hopper anchor releasing them from the hopper. The hopper is now
ready for removal.
HOPPER INSTALLATION:
Place the hopper on top of the grinding bowl assembly with the lock arm retainer facing toward the
front of the machine. Connect the hopper lock down rods to the hopper anchors and lower the lock
down handles to lock the hopper in place.
AUGER ASSEMBLY REMOVAL:
Loosen the retaining ring and remove knife and plate. Now the auger can be pulled out from grinding
bowl.
GRINDING BOWL ASSEMBLY REMOVAL:
After the paddle shaft, hopper, retaining ring and auger assembly have been extracted, the grinding
bowl can be removed by lifting the output end of the assembly and pushing toward the cabinet. Next
lift the bowl lock hooks and seperate the bowl assembly from the machine.

10
MAINTENANCE
LUBRICATION
1. MOTOR: The grinder motor has pre-lubricated, sealed motor bearings.
2. ROLLER CHAIN AND DRIVE SPROCKETS: The main drive chain has been pre-lubricated at the
factory to protect it against dirt and moisture. Chain life will vary appreciably depending upon its
lubrication. The better the lubrication, the longer the chain life.
• ALWAYS Turn Off, Unplug Machine From Power Source and Perform Lockout/Tagout
Procedure to this Machine BEFORE Servicing.
• NEVER Touch This Machine without Training and Authorization by Your Supervisor.
• NEVER Place Hands into Machine Input or Output Openings.
• NEVER Bypass, Alter, or Modify This Equipment in Any Way From Its Original Condition.
• PROMPTLY REPLACE Any Worn or Illegible Warning Labels.
• USE ONLY GENUINE BIRO Parts and Accessories Properly Installed.
ROTATING GRINDING AUGER & ROTATING MIXING PADDLE
TO AVOID SERIOUS PERSONAL INJURY
Lubrication effectiveness will vary with the amount of lubricant and frequency of application. Ideally, a
lubricant lm should always be present between the working parts. Manually lubricate the chain as often
as is needed (possibly once a week). NEVER exceed three months without lubricating.
Lubricating just the outside of the chain does little good. Apply lubrication on the inside of the chain span
so that it will work through the moving parts and joints by centrifugal force as the chain rotates and
reaches the area where one surface “scrubs” another.
Recommended types of chain lubricant are those with Molybdenum Disulphide or Graphite added. Also
bonded lubricants such as Dow Corning Molykote 321R or equivalent are excellent for open chains. The
lubricant should be of a viscosity whereby it will “ow” somewhat and penetrate the internal working
sufaces. Thick stiff greases are of little value because they cannot work into moving parts of the chain.
a. Unplug mixer/grinder from power source and perform lockout/tagout procedures.
b. Remove rear drive or access cover.
c. Spray or brush lubricant on inside of chain, slowly and carefully turning the large sprocket by hand.
d. Reinstall rear drive cover.
3. THRUST BEARING: The thrust bearing is housed in an enclosed and sealed cover. The lubrication
effectiveness will vary with the amount of lubricant and frequency of application. Ideally, a lubricant lm
should always be present between working parts. Manually lubricate the thrust bearing with a good grade
of bearing grease as often as is needed (possibly once a week). Never exceed 3 months without
lubricating.

11
LUBRICATION CONTINUED FOR GEAR REDUCERS
1. Factory Filling
The speed reducer is lled with Mobil Glygoyle 460 polyglycol (PAG), to the proper level for the standard mounting
position. The oil level should be checked and adjusted (if necessary) prior to operation, using the oil level plug
provided and while the unit is oriented in its operating position.
2. Oil Changing
OIL SHOULD BE CHANGED MORE OFTEN IF THE
REDUCER IS USED IN A SEVERE ENVIRONMENT
(i.e., DUSTY, HUMID)
Therefore, if changing to a different oil, it is recommended that the housing be completely drained and thoroughly
ushed with a light ushing oil prior to relling with the appropriate lubricant. The oil level should be rechecked
after a short period of operation and adjusted, if necessary.
A. Initial Oil Change
The oil in a new speed reducer should be changed at the end of 100 hours of operation.
B. Subsequent Oil Changes
Under normal conditions, after the initial oil change, the oil should be changed after every 2500 hours of operation,
or every six months, whichever occurs rst. Under severe conditions (rapid temperature changes, moist, dirty, or
corrosive environment) it may be necessary to change oil at intervals of one to three months. Periodic examination
of oil samples taken from the unit will help establish the appropriate interval.
C. Synthetic Oils (NOTE: Gearbox comes standard with Synthetic Oil).
3. Overlling or Underlling
If a speed reducer is overlled with oil, the energy in churning the excessive oil can result in overheating. If this occurs,
shut down the drive, remove the oil level plug and allow oil to drain until oil ceases to drain from the level hole,
reinstall the oil level plug and restart the drive. If the speed reducer is underlled, the resultant friction can cause
overheating and possible damage. If this occurs, ll the speed reducer to the oil level plug hole and check the gearing
for excessive wear. NOTE: Oil capacity is approximately 40 ounces.
4. Oil Seals
A. When installing a new seal, cover the keyway and any other surface discontinuity with smooth tape to protect the
seal lip from being damaged.
B. A sealant should be used between the O.D. of the seal and the I.D. of the bore into which the seal is installed. The
seal bore should also be free of any burrs, nicks, or scratches.
C. Be sure that the seal is not cocked in the bore. The outer face of the seal should be ush with the surface into which
it is mounted.
WHEN CHANGING OIL FOR ANY REASON,
DO NOT MIX DIFFERENT OILS IN THE REDUCER.
OILS SHOULD BE COMPATIBLE WITH
VITON SEAL MATERIAL.
®
Synthetic lubricants can be advantageous over mineral oils in that they generally are more stable, have a longer life,
and operate over a wider temperature range. These oils are appropriate for any application but are especially useful
when units are subjected to low start-up temperatures or high operating temperatures. For continuous duty
we recommend the use of Mobil Glygoyle 460 polyglycol (PAG).
Although the speed reducer uses high quality oil seals and precision ground shafts to provide a superior seal contact
surface, it is possible that circumstances beyond the speed reducer’s control can cause oil seal leakage (damage during
shipment or installation, etc.) When replacing a shaft oil seal, using the following suggestions will help to insure leak-
free operation and long seal life:

12
GEAR REDUCERS
(Item No. 63070, up to Serial No. 560) (Item No. 63070G, Serial No. 561 and up)
LUBRICATION AND MAINTENANCE
LUBRICANTS FOR 63070/63070G GEAR WORM REDUCERS
The precision-made gears and bearings in gear speed reducers require high-grade lubricants
of the proper viscosity to maintain trouble-free performance. For best results, use lubricants on the
following chart for worm gear reducers.
Standard factory-installed lubricant is Mobil Glygoyle 460.
Manufacturer
Kluber Klubersynth UH 6-460
Castrol Alphasyn PG 460
BP Enersyn SG-XP 460
Lotos Transmil Synthetic Extra PG 460
Shell Tivela S 460
Texaco Synlube CLP 460
Within -10° to 120°F
Ambient Temperature

1
2
3
4
5
6
7
8
9
10
11
18
20
17
13
16
12
pulled out for clarity 15
19
4
21
22
23
14
Description
Item No.
63035S Stn Stl hopper cover & arm assembly
63035 Hopper cover & arm assembly
63082 Lid safety arm weldment
62182 Sleeve bushing, hinge
EMG92032 Washer, outside lid hinge arm
HHS083S Hex head cap screw, ⅜-16 x 1¾”, SS
56337 Shroud, selector switch
56105 Selector switch, hand/foot
Fig.
1
2
3
4
5
6
7
8
EMG62181 Washer, inside lid hinge
63096 Lid arm pivot weldment
HNNL25S Hex nut, ⅜-16, SS nylok, jam
62182 Sleeve bushing, hinge
21
22
23
4
MOTOR DRIVE COVER
AND HOPPER COVER
13
24
42MC-Y73 Start button, Green
56125 Legend plate (controls)
42MC-Y74 Stop button, Red
63044 Hood wrap weldment
56301G Watertight cord connector, 90°
241-LN Locknut, ½” conduit, metal
9
10
11
12
13
14
15
16
56302I Plastic tubing, ¼ O.D. x ⅛ I.D. x 18”
56300J-CPB Female coupling body w/ nut,
Quick disconnect, metal
50024-1 Oil seal, auger shaft
63021 Bearing cover
360A1 Angle grease tting
17
18
19
20 RHS070S Round head screw, 10-24 x 1, SS
24 HHS035S Hex head screw, ¼-20 x ⅝, SS

7
1
2
3
4
19 17
15
18
16 17
9
11 1012
14
1
9
23
24
20
14
21
22
5 6
13
8
25
Description
Item No.
63169 Sleeve bushing washer
62182 Sleeve bushing, hinge
EMG92032 Washer, outside hinge lid arm
HHS083S Hex head cap screw, ⅜-16 x 1¾”, SS
311-1 Rubber bumper
AN05S Acorn nut, 8-32, high crown, SS
63035S-PX Hopper cover & arm assembly, SS
Fig.
1
2
3
4
5
6
7
MOTOR DRIVE COVER
AND HOPPER COVER
63082 Lid safety arm weldment
HNNL25S Hex nut, ⅜-16, SS nylok, jam
PC084 South pole magnet (green)
RHS074S Round head screw, 8-32 x ⅝, SS
LW03S Lock washer, #8, SS
HN05S Hex nut, 8-32, SS
63031 Safety switch harness,
(2- PC166’s w/ quick disconnect plug)
8
9
10
11
12
13
PC166K Safety switch (1- PC166 w/ butt connectors)14
14
EMG62190-1 Retaining clip, gas spring, internal
EMG62190 Gas spring, internal
63175 Ball stud, 10mm ball, 5/16-18 x 5/32”
56105 Selector switch, hand/foot
42MC-Y73 Start button, Green
42MC-Y74 Stop button, Red
56301D Air switch w/ nut, momentary, SPDT
56302I Plastic tubing, ¼ O.D. x ⅛ I.D. x 18”
17
18
19
20
21
22
23
24
25 63044-HEB Hood wrap weldment w/damper boss
63174 Ball stud, 10mm ball, 5/16-18 x ⅜”
16
63173 Damper arm, lid15

15
32
4
789
16 17
1
18
19
13
14
13
14
15
11 12
10
6
5
14 19
20 21
63027-A Bushing, multi hole, .25 DIA
63027-B Cord grip, 90°, ½”
224-11 Cord grip connector, 90°, ½”, .25-.375
224-5 Cord grip connector, 90°, ½”, .50-.625
241-LN Locknut, ½” conduit, metal
LW10S Lock washer, ¼”, SS
HN15S Hex nut, ¼-20, SS
2
3
4
5
6
7
8
9
10 226EE-GO11K Contactor, LS11K, 24 V Coil
63094-1 Electrical box weldment, s/n 500 on
1
Description
Item No.
Fig.
11 226EE-OL12M Overload, B18K-M, 8-12 A
63028 Din rail, 2⅜” long
RHS060S Round head screw, 10-24 x ⅜”, SS
63026-1 Transformer, 100VA, 208-460/24 SEC
EMG92014 Fuse block, din rail type
EMG90552 Fuse, 3A, time delay
PC162-1 Central control unit, 24 VDC
BLK323 End barrier
PC148 Bridge rectier, AC-DC volts
13
14
15
16
17
18
19
20
21 RHS062S Round head screw, 10-24 x ⅝”, SS
H281EE-51 Overload, B18K-K, 4-6.3 A
12
Description
Item No.
Fig.
ELECTRICAL BOX
HHS035S Hex head screw, ¼-20 x ⅝”, SS
Note: Refer to Wiring Diagram Serial No. 2133 on

16
MOTOR-DRIVE UNIT
AND
COMPONENTS
DescriptionItem No.
15026-02 Double roller chain, 49”
15029 Double chain master link
20050-10 #40 Roller chain, 80 pitch
20050-01 #40 Roller chain master link, #40-C/L
Fig.
1
2
3
4
53568 Mixer paddle lock wing bolt
53852 Lock arm assembly w/ bushings
53517-1 Thrust bearing
53594 Radial bearing
11
12
12A
12B
56304 Footswitch assembly w/ 6’ tubing
63036 Hopper assembly, up to s/n: 489
63036-1-HEB Hopper assembly, HEB style
63041 Sprocket, D40B35
13
29
29A
31
63043 Sprocket, D40B15F-01
63045 Back access panel
63047 Timing pulley, 48H100SK
63048-01 Taper lock, SK, 1” (Winsmith reducer)
33
34
35
36
63048-03 Taper lock, SK, ¾” (Grove reducer)36A
63049 Timing belt37
63055 Cart assembly w/ casters38
DescriptionItem No.
63057 Table top leg, (Optional)
63070 Gear reducer, Winsmith up to s/n 560
63070G Gear reducer, Grove s/n 561 on
63073 Mixer paddle, round blade
Fig.
39
45
45A
46
63073-2 Mixer paddle, curved blade
63099-4 Motor, 3HP, 208-230/460V-60Hz-3PH
46A
54
63136 Paddle spacer
H340 Ring Wrench
PC175-1 Caster w/ swivel lock
PC175S-1 SS Caster w/ swivel lock
72
115
124
124A
14688 4-point knob, ⅜-16 thread
WS077S Weld stud, ⅜-16 x 1½”
63048 Timing pulley, 18H100QD, 18 tooth
63048-02 Taper lock bushing, SH ⅞”
135
136
137
138

17
Fig. Item No. Description
5
6
8
10
14
15
16
17
18
19
20
21
22
24
25
28
30
32
40
41
42
43
44
TRANSMISSION
MOUNTING
ASSEMBLY
117
116
114
113
108
107
106
76
75
74
73
71
70
68
67
66
65
64
59
58
57
56
55
49
48
Fig. Item No. Description
20665 Key, 1/4 x 1/4 x 1-1/8 S.S.
20665-01 Key, 1/4 x 1/4 x 1-3/4 S.S.
O-Ring, 1.25 I.D.
30315
50029 Washer, brass (used up to s/n 499)
Base plate (used up to s/n 499)
63005
14A 63005-1 Base plate (used on s/n 500-on)
63007 Shaft bearing retainer, front
63008 Shaft bearing retainer, rear
(used up to s/n 499)
16A 63008-1 Shaft bearing retainer, rear
(used on s/n 500-on)
63009 Frame side plate
63010 Bowl lock side spacer
63011 Gear box top plate
63014 Auger drive shaft
63015 Main drive shaft
63016 Bearing retainer, main shaft
Spacer, mixer drive shaft63019
63020 Spacer, plastic, mixer drive shaft
25A 63020-1 Spacer, sealed, mixer drive shaft
Mixer drive shaft
63033
63040 72T sprocket #40B72-01
22T sprocket #D40B22
63042
63062 Linkage pivot arm
Linkage arm
63063
63065 Spacer, thrust bearing
63066 Thrust bearing
63067 Spacer, main drive shaft
(used up to s/n 499)
47
(used on s/n 646-on)
63081-01 Bowl support bracket, LH
63081-02 Bowl support bracket, RH
63084 Hopper latch rod
Drive clutch, squire drive
56064
56065 Driving clutch, motor output
56211-1 Engagement lever bushing
56214 Clutch engagement lever, LH
63104 Link engagement handle
56215 Clutch engagement lever, RH
63119 Clutch engagement shaft
56127-1 Woodruff key
MC-21R2 Lock handle groove pin
Shoulder bolt, 3/8-16 x 1/2
SSB50PS
Chain tensioner63126
63127 Tensioner block
63139-01 Bowl lock hook, LH
Bowl lock hook, RH
63139-02
63140 Hopper latch
Bowl adjusting pin63141
Bearing
83017
Bearing
83032
Key, 3/8 x 3/8 x 1-1/2 lg.
83080-07
Pivot arm knob90509
PCM570 V-Ring seal
FW07S Flat washer, 3/8
Light jam nut, 3/8-16
HN30S
HN35S Heavy jam nut, 3/8-16
118
119 Set screw, 5/16-18 X 5/16 lg., knurled cup pointSSS17KL
SSS20 Set screw, 3/8-16 X 3/8 lg., knurled cup point
120
63063-1 Spring, clutch linkage arm
41A
DescriptionItem No.
20665 Key, ¼ x ¼ x 1⅛”
20665-01 Key, ¼ x ¼ x 1¾”
30315 O-Ring, 1.25 I.D.
50029 Washer, brass (up to s/n: 499)
Fig.
5
6
8
10
63005 Base plate (up to s/n: 499)
63005-1 Base plate (used s/n: 500 on)
63007 Shaft bearing retainer, front
63008 Shaft bearing retainer, rear (up to s/n 499)
14
14A
15
16
63008-1 Shaft bearing retainer, rear (s/n 500 on)
63009 Frame side plate
16A
17
63010 Bowl lock mount spacer, sides
63011 Gear box mount plate, top
63014 Grinder socket shaft
63015-1 Auger drive shaft w/ shoulder
18
19
20
21
63016 Bearing mount, auger drive shaft22
63019 Spacer, mixer drive shaft24
63020 Spacer, mixer drive shaft (up to s/n 645)
63020-1 Spacer, mixer drive shaft (s/n 646 on)
25
25A
63033 Mixer drive shaft
63040 Sprocket, 72 tooth, #40B72-01
63042 Sprocket, 22 tooth, #D40B22
28
30
32
63062 Linkage pivot arm40
63063 Linkage arm41
63063-1 Spring, clutch linkage arm
63065 Spacer, thrust bearing
41A
42
63066 Thrust bearing, auger drive shaft43
63067 Spacer, auger drive shaft44
DescriptionItem No.
63081-01 Bowl support bracket, LH
63081-02 Bowl support bracket, RH
63084 Hold down rod
56064 Driven clutch, square drive
Fig.
47
48
49
55
56065 Driving clutch, motor output
56211-1 Driven clutch engagment lever bushing
56214 Clutch engagement lever, LH
63104 Link engagement handle
56
57
58
59
56215 Clutch engagement lever, RH
63119 Clutch engagement shaft
56127-1 Woodruff key
MC-21R2 Lock handle groove pin
64
65
66
67
SSB50PS Shoulder bolt, ⅜-16 x ½”
63126 Bracket, chain tensioner
63127 Tension block
63185-01 Bowl lock hook, LH
68
70
71
73
63185-02 Bowl lock hook, RH74
63140 Hopper latch75
63141 Bowl adjusting pin
83017 Bearing, auger drive shaft
76
106
83032 Bearing, mixer shaft
83080-07 Key, ⅜ x ⅜ x 1½”
90509 Plastic ball knob
PCM570 V-Ring seal
107
108
113
114
FW07S Flat washer, ⅜”116
HN30S Hex nut, light jam, ⅜-16, SS117
HN31S Hex nut, ⅜-16, SS
SSS17KL Set screw, knurled cup point, 5/16-16 x ⅜”
118
119
SSS20 Set screw, knurled cup point, ⅜-16 x ⅜”120
TRANSMISSION
MOUNTING
ASSEMBLY
Other manuals for Mini-32
2
Table of contents
Other BIRO Grinder manuals

BIRO
BIRO AFMG-52 Service manual

BIRO
BIRO EMG-32 User manual

BIRO
BIRO Mini-32 Service manual

BIRO
BIRO Mini-32 Service manual
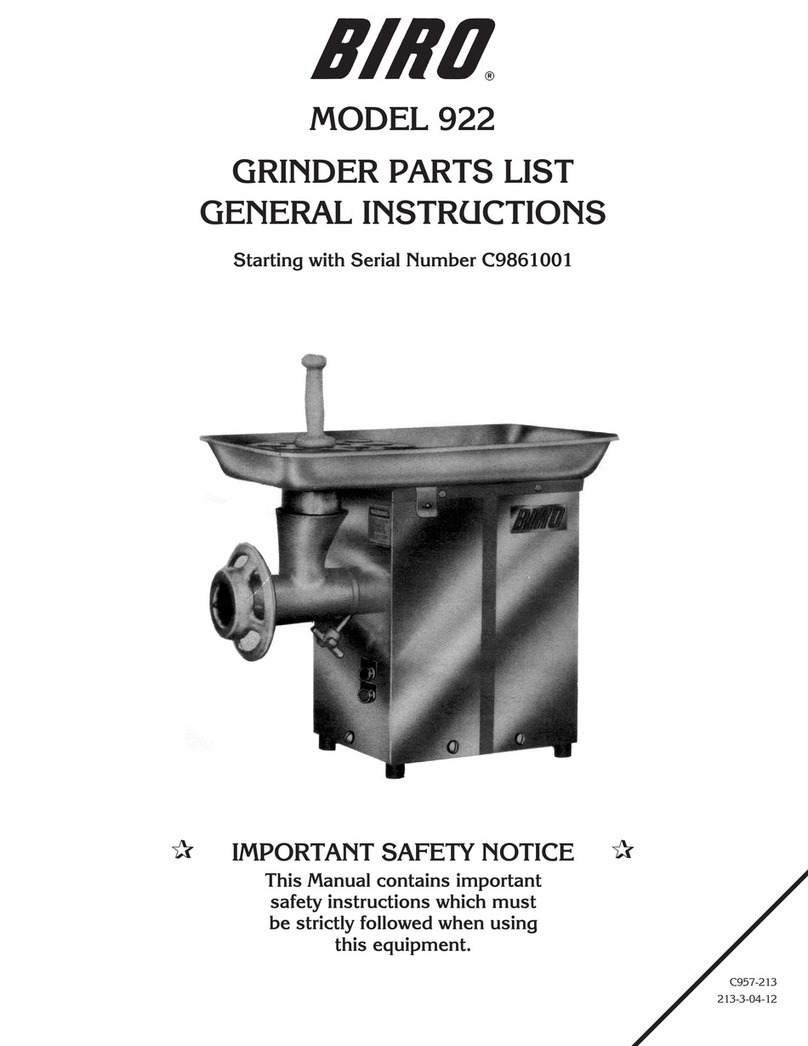
BIRO
BIRO 922 Instruction manual
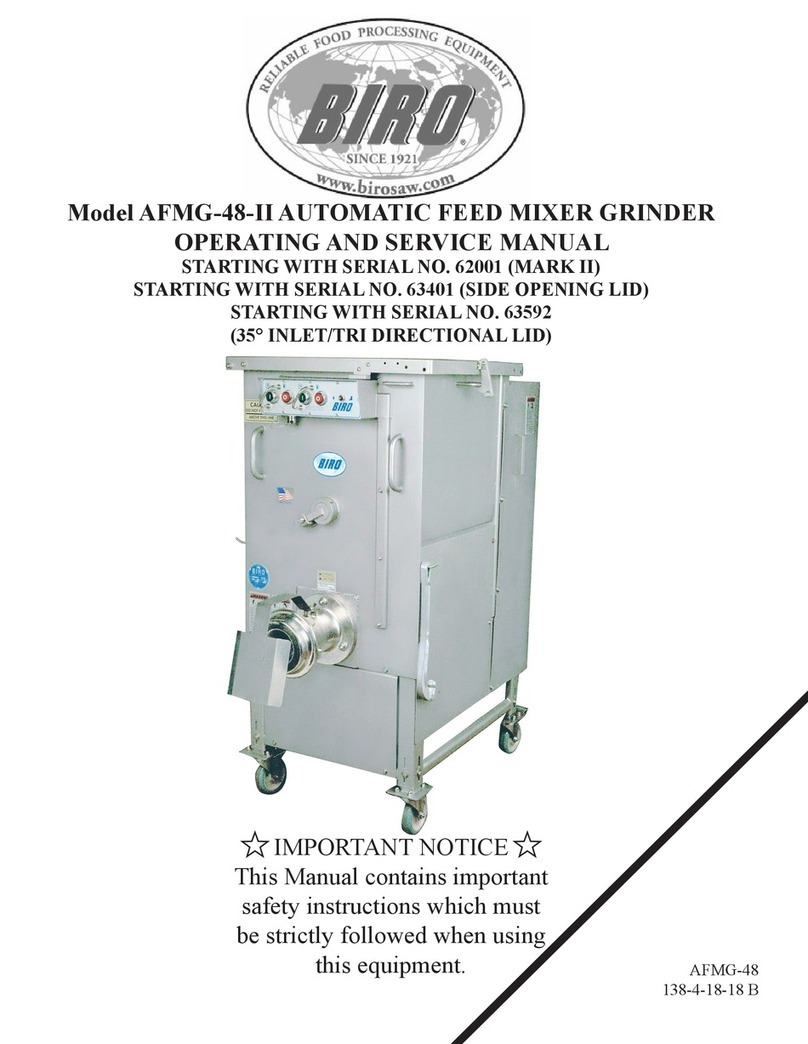
BIRO
BIRO AFMG-48-II Service manual
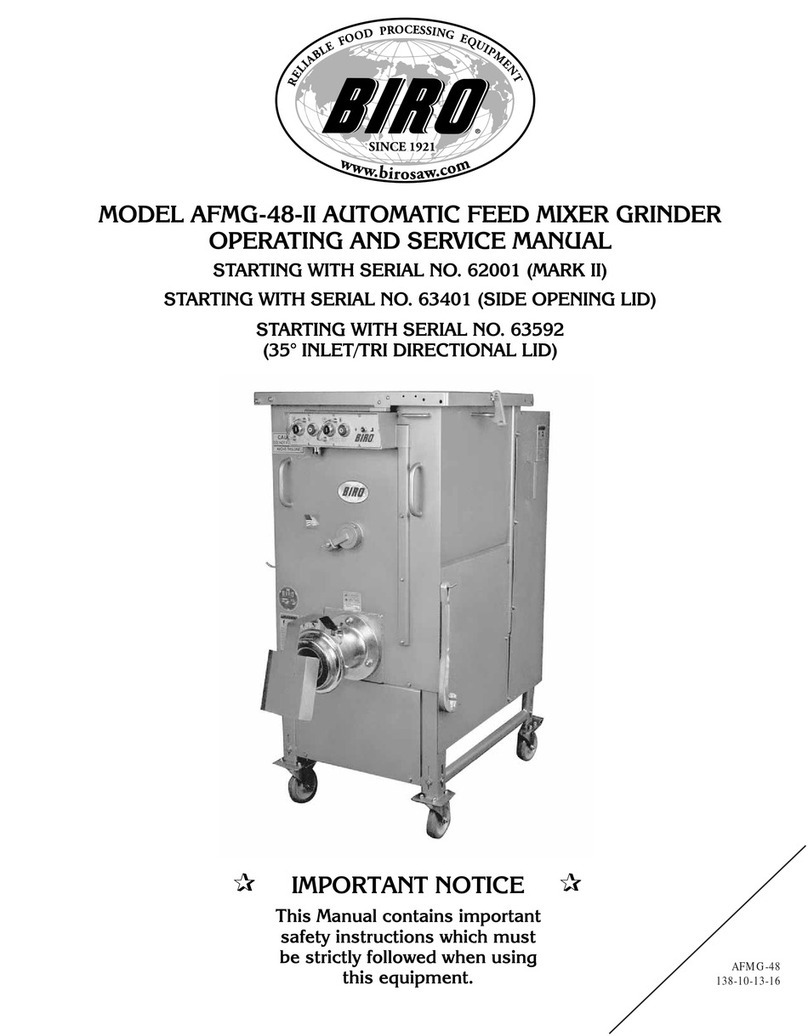
BIRO
BIRO AFMG-48-II Service manual

BIRO
BIRO AFMG-48-II Service manual

BIRO
BIRO MINI-22 User manual
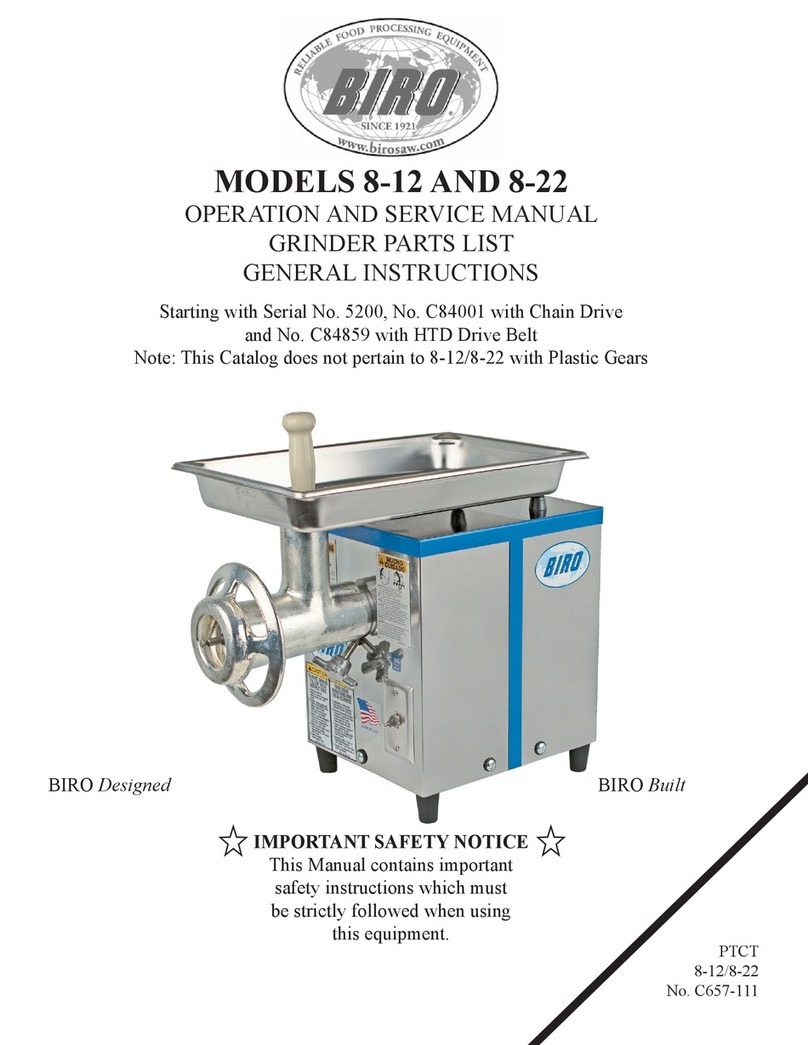
BIRO
BIRO 8-12 Operation manual
Popular Grinder manuals by other brands

Silverline
Silverline DIY 650W manual

Klutch
Klutch 100801 owner's manual
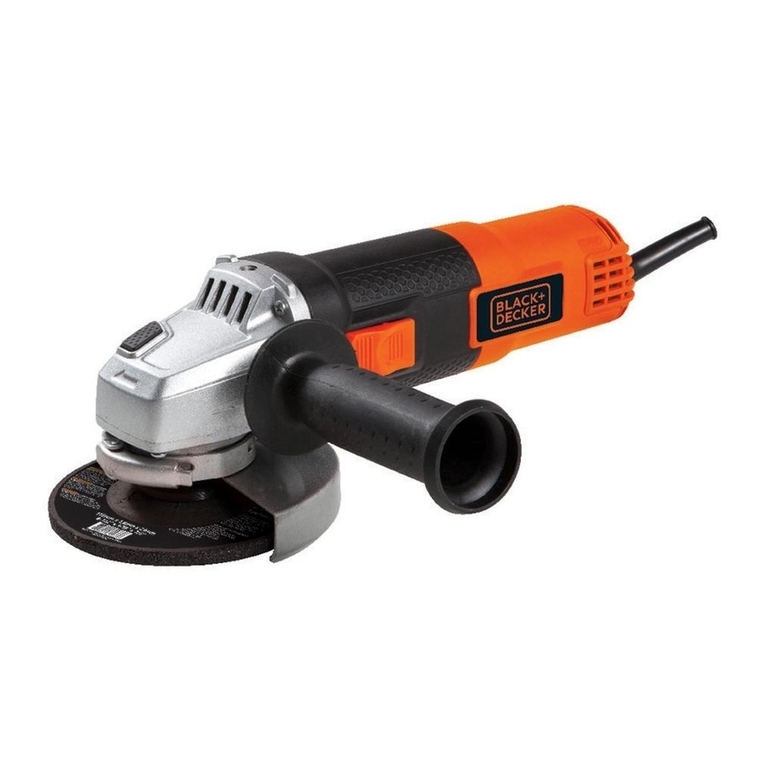
Black & Decker
Black & Decker Linea Pro G720 instruction manual

Parkside
Parkside PMTS 180 A1 Translation of the original instructions
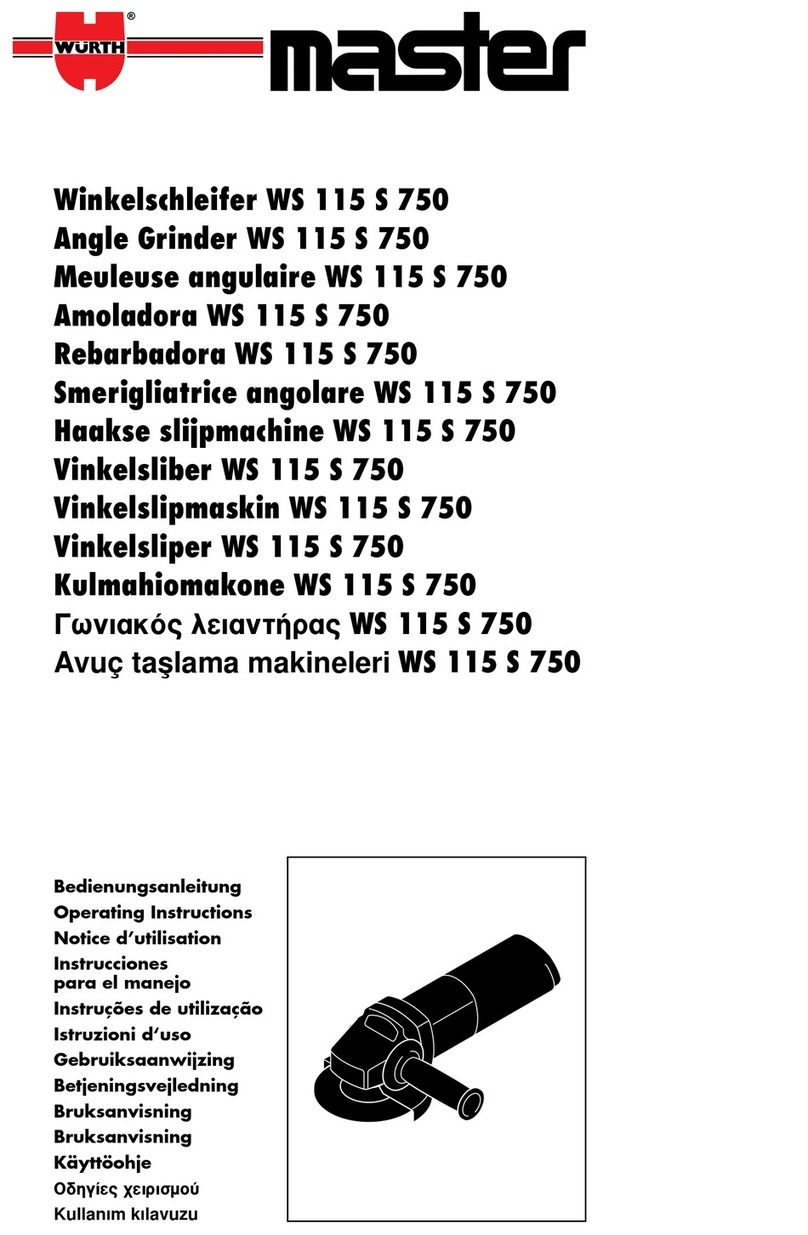
wurth
wurth WS 115 S 750 operating instructions
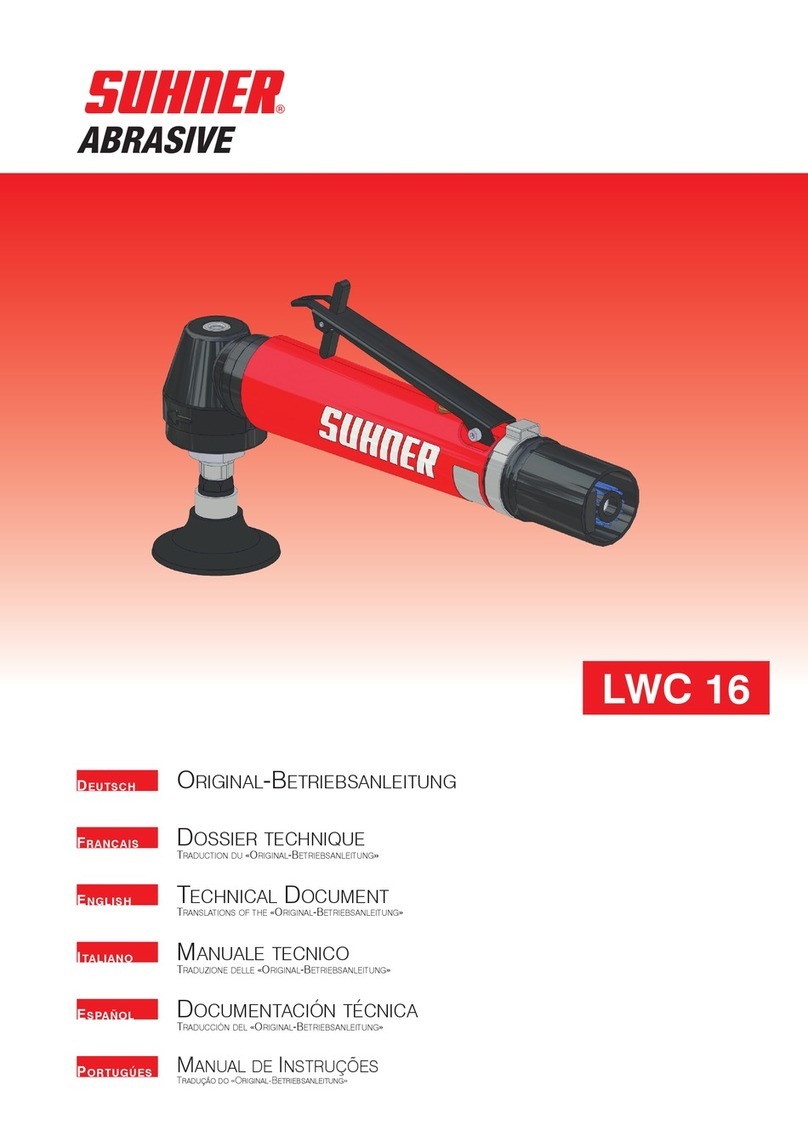
SUHNER ABRASIVE
SUHNER ABRASIVE LWC 16 Technical document