BONFIGLIOLI C Series User manual

INDUSTRY PROCESS
AND AUTOMATION SOLUTIONS
C, A, F, S, VF, W
ATEX
INCLUDED
Installation, use and service manual


1
INSTALLATION, USE AND SERVICE MANUAL
1.0 - GENERAL INFORMATION 2
1.1 - PURPOSE OF THE MANUAL ...................................................................................................................2
1.2 - EQUIPMENT IDENTIFICATION ................................................................................................................3
1.3 - GLOSSARY AND TERMINOLOGY ............................................................................................................4
1.4 - REQUESTING TECHNICAL ASSISTANCE .................................................................................................4
1.5 - MANUFACTURER’S LIABILITY ................................................................................................................4
2.0 - TECHNICAL INFORMATION 5
2.1 - GEAR UNIT DESCRIPTION .....................................................................................................................5
2.2 - CONFORMITY TO STANDARDS ..............................................................................................................5
2.3 - OPERATING LIMITS AND CONDITIONS ...................................................................................................6
3.0 - SAFETY INFORMATION 7
3.1 - SAFETY STANDARDS ............................................................................................................................7
4.0 - HANDLING AND TRANSPORT 8
4.1 - PACKAGING .........................................................................................................................................
4.2 - HANDLING INSTRUCTIONS ....................................................................................................................9
4.2.1 - Moving packages ..........................................................................................................................9
4.2.2 - Moving the equipment....................................................................................................................9
4.3 - STORAGE ..........................................................................................................................................10
5.0 - INSTALLATION 11
5.1 - INSTALLING THE GEAR UNIT ...............................................................................................................11
5.1.1 - Gear units with solid output shaft....................................................................................................14
5.1.2 - Gear units with hollow output shaft .................................................................................................14
5.1.3 - Gear units with shrink disk ............................................................................................................15
5.1.4 - Shaft mounted gear units series F ..................................................................................................15
5.2 - INSTALLING AN IEC-STANDARD FLANGED MOTOR...............................................................................16
6.0 - TESTING THE GEAR UNIT 17
7.0 - USING THE E UIPMENT 19
8.0 - MAINTENANCE 20
.1 - ROUTINE MAINTENANCE .....................................................................................................................21
.2 - LUBRICANTS ......................................................................................................................................23
.3 - OIL CHANGE .......................................................................................................................................23
.4 - RECOMMENDED/PERMITTED OILS.......................................................................................................24
.5 - CHECKING EFFICIENCY.......................................................................................................................26
.6 - CLEANING ..........................................................................................................................................26
.7 - PAINT.................................................................................................................................................26
9.0 - REPLACING PARTS 27
9.1 - TAKING APART OF THE IEC-STANDARD FLANGED MOTOR ....................................................................27
9.2 - SCRAPPING THE GEAR UNIT ...............................................................................................................27
10.0 - TROUBLESHOOTING 28
ANNEX 1 - CHECKING OIL LEVEL ON ATEX-SPECIFIED GEAR UNITS 29
ANNEX 2 - LUBRICANT CHARGE UANTITY 32
Helical in-line gear units, series C ...................................................................................................................32
Bevel helical gear units, series A.....................................................................................................................33
Shaft-mounted gear units, series F ..................................................................................................................34
Worm gear units, series V..............................................................................................................................35
Worm gear units, series W.............................................................................................................................36
Single-stage helical gear units, series S ...........................................................................................................36
ANNEX 3 - CUSTOMER'S SHAFT 37
Series A .....................................................................................................................................................37
Series F .....................................................................................................................................................3
Series VF and W..........................................................................................................................................39
ANNEX 4 - LIFTING 40
ANNEX 5 - INSTALLING THE MOTOR ON TYPE VFR WORM GEAR UNITS 47
ANNEX 6 - CALIBRATING THE TOR UE LIMITER SLIP TOR UE 48
Revisions
Refer to page 50 for the catalogue revision index. Visit www.bonfiglioli.com to search for catalogues with up-to-date revisions.

2
1.0 - GENERAL INFORMATION
1.1 - PURPOSE OF THE MANUAL
This manual has been compiled by the Manufacturer to provide information on the safe transport, handling,
installation, maintenance, repair, disassembly and dismantling of the gear units.
All purchasing and design criteria is provided in the Sales Catalogue. Apart from adhering to establi-
shed engineering practices, the information given in this manual must be carefully read and applied
rigorously.
The information regarding the electric motor that can be found matching the speed reducer is sup-
plied with the owner’s manual relevant to the specific electric motor.
Failure to adhere to the information provided herein may result in risk to personal health and safety, and may
incur economic damages.
This information, provided in the original language (Italian) of the Manufacturer, may also be made available
in other languages to meet legal and/or commercial requirements.
The documentation must be stored by a person with the correct authority and must always be made availa-
ble for consultation.
In case of loss or damage, replacement documentation must be requested directly from the Manufacturer,
quoting the code of this manual.
The manual reflects the state of the art at the time of commercialisation of the gear unit.
The Manufacturer reserves the right to modify, supplement and improve the manual, without the present pu-
blication being for that reason considered inadequate.
Particularly significant sections of the manual and important specifications are highlighted by symbols whose
meanings are given below.
SYMBOLS:
DANGER - WARNING
This symbol indicates situations of serious danger which, if ignored, may result in serious
risks to the health and safety of personnel.
CAUTION - ATTENTION
This symbol indicates the need to adopt specific precautions to avoid risks to the health
and safety of personnel and possible economic damages.
IMPORTANT
This symbol indicates important technical information.
The instructions indicated on a yellow background next to these symbols refer exclusively to
equipment conforming to the “ATEX“ Directive 94/9/EC.
The operations highlighted by these symbols must be carried out by qualified professionals spe-
cially trained in the safety requirements for zones characterised by potentially explosive atmo-
spheres.
Failure to observe these instructions may result in serious risks to personal and environmental
safety

3
1.2 - E UIPMENT IDENTIFICATION
The gear unit bears the following nameplate. The nameplate bears all references and indispensable safety
instructions. The gear unit’s identifying code is explained in the Sales Catalogue.
If the gear unit is supplied complete with electric motor (gearmotor), all information regarding the motor itself
is supplied in the motor manual.
Gear unit type.
Product code.
Month / Year of manufacture.
Mounting position.
Gear ratio.
Nameplate for ATEX-specified gear units:
Gear unit type.
Gear ratio.
Product code.
Transmissible torque at n1=1400 rpm [Nm].
Mounting position.
Month / Year of manufacture.
Maximum drive speed.
Certification Nr.
Temperature class, or maximum surface
temperature.
Maximum surface temperature.
CE - Mark
•Environmental limits (ambient temperature range between - 20°C and + 40°C).
•Maximum surface temperature: temperature class T4 for 2G and 130°C for 2D.
Some types of gear unit, shown in the catalogue, are exceptions to this rule and are marked
temperature class T3 for 2G or 160°C for 2G and 2D.
•Certifying agency with whom the technical file has been deposited.
Readability of the nameplate
The nameplate and the information thereon must be readable at all times and consequently cleaned from
time to time.
Should the nameplate wear and/or become damaged so as to affect its readability or that of even one of the
items of information thereon, the User must request a new nameplate from the Manufacturer, quoting the in-
formation given in this manual, and replace the old one.
Nameplate data

4
1.3 - GLOSSARY AND TERMINOLOGY
Some of the frequently occurring terms used in this manual are described below so as to unequivocally defi-
ne their meaning.
Routine maintenance: the set of operations required for maintaining the functionality and efficiency of the
gear unit. These operations are usually scheduled by the Manufacturer, who defines the qualifications requi-
red and tasks in question.
Non-routine maintenance: the set of operations required for maintaining the functionality and efficiency of
the gear unit. These operations are not scheduled by the Manufacturer and must be done by an expert main-
tenance technician.
Expert maintenance technician: an authorised technician selected by means of having the qualifications,
skills and mechanical and electrical training to do repairs and non-routine maintenance work on the gear unit.
Overhaul: an overhaul consists in the replacement of bearings and/or other mechanical components which
have worn to such an extent as to compromise the operation of the gear unit. The overhaul also includes ve-
rification of the condition of all gear unit components (keys, seals, gaskets, vents, etc.). If any such compo-
nents are damaged they must be replaced and the reason for the damage identified.
1.4 - RE UESTING TECHNICAL ASSISTANCE
For any technical service needs, contact the Manufacturer’s sales network, quoting the information on the
unit’s nameplate, the approximate hours of service and the type of defect.
1.5 - MANUFACTURER’S LIABILITY
The Manufacturer declines all liability for cases of:
•use of the gear unit in violation of local laws on safety and accident prevention at work.
•incorrect installation, disregard or incorrect application of the instructions provided in this manual.
•incorrect or defective power supply (gearmotors).
•modifications or tampering.
•work done on the unit by unqualified or unsuitable persons.
The safety of the gear unit also depends on scrupulous observance of the instructions given in this manual,
in particular:
•always operate the unit within its operating limits.
•diligently observe the routine maintenance schedule.
•only authorise trained operators to inspect and service the unit.
•use only original spare parts.
•the configurations given in the gear unit catalogue are the only ones permitted.
•do not attempt to use the unit contrary to the instructions supplied.
•the instructions given in this manual do not substitute but summarise the provisions of applicable
safety legislation.

5
2.0 - TECHNICAL INFORMATION
2.1 - GEAR UNIT DESCRIPTION
The gear unit has been designed and constructed for integration, if required, driven by an electric motor, into
an assembly of interlocking parts or mechanisms as part of a specific application.
Depending on the requirements of the application, the gear unit can be supplied in a variety of executions
and configurations. It is capable of satisfying a range of specific requirements in the mechanical, chemical,
agricultural and food industries, etc.
BONFIGLIOLI RIDUTTORI supplies a range of accessories and optionals to make their products as versatile
as possible. For further technical information and descriptions, refer to the Sales Catalogue.
The User is responsible for using the products recommended for installation and maintenance of
BONFIGLIOLI gear units in an appropriate manner and in accordance with instructions.
SAFETY SPECIFICATIONS FOR ATEX SPECIFIED GEAR UNITS
•use of synthetic lubricants only (oil and grease)
•VITON®seal rings
•thread locker on all external bolts
•vent caps with anti-intrusion valve
•double oil seals on series C gear units, and oil seals with dust traps on all other types
•components and products operable at above the maximum rated operating temperature
•no metal moving parts external to the gear unit
•no plastic parts capable of building up electrostatic charge
•irreversible temperature indicator supplied along with each unit
•for installations in zones 21 and 22 the User must schedule and implement a regular cleaning
programme of all surfaces and recesses to avoid a build up of dust of more than 5 mm in depth
•to prevent dust build-ups in difficult to access areas, the units are equipped with a variety of se-
als in proximity to the couplings of moving parts, mounting flanges and external threaded holes.
2.2 - CONFORMITY TO STANDARDS
All gear units or gearmotors (when supplied complete with electric motor) are designed in compliance with
the provisions of all applicable Essential Health and Safety Requirements, “Machinery Directive” 9 /37/EC
and, if requested, can be supplied complete with Manufacturer’s Declaration – Annex IIB as provided by said
directive.
The electric motors of all BONFIGLIOLI RIDUTTORI gearmotors conform to the provisions of Low Voltage
Directive 73/23/EEC and Electromagnetic Compatibility Directive 9/336/EEC.
Furthermore, if specified for use in potentially explosive atmospheres, the gear units are desi-
gned and constructed to conform with the Essential Health and Safety Requirements (EHSR) of
Annex II of ATEX Directive 94/9/EC and conform to the following classification:
•Equipment group: II.
•Calass: Gas 2G – Dust 2D.
•Zone: Gas 1– Dust 21.
•Maximum surface temperature: temperature class T4 for 2G and 130°C for 2D.
Some types of gear units, given in the catalogue, are exceptions to this rule and are marked
temperature class T3 for 2G or 160°C for 2G and 2D.

6
2.3 - OPERATING LIMITS AND CONDITIONS
Ambient conditions
•Ambient temperature: min. - 20°C; max. + 40°C.
•Do not use the gear unit, if not explicitly intended for the purpose, in a potentially explosive atmosphere or
where the use of explosion-proof equipment is specified.
•Lighting
If the unit is to be serviced in a poorly lit area, use additional lamps and ensure that the work is
done in compliance with applicable safety legislation.
•Noise - Vibration
During operational testing at the Manufacturer’s premises, the acoustic pressure measured under full load at
a distance of 1 m from the unit and 1.6 m above ground level without vibration was less than 5 dB(A).
The vibrations produced by the gear unit do not constitute a health risk for personnel. Excessive vibration
may be the result of a fault and should be immediately reported and eliminated.
Modification of the gearbox configuration or mounting position is only permitted if previously aut-
horised by the BONFIGLIOLI RIDUTTORI technical service.
Failure to obtain said authorisation voids the ATEX certification.
The nameplate data on the maximum surface temperature, refer to measurements made in nor-
mal ambient and installation conditions. Even minimal variations to said conditions (e.g. smaller
mounting cabinet) could have a significant impact on the build up of heat.

7
3.0 - SAFETY INFORMATION
3.1 - SAFETY STANDARDS
•Carefully read the instructions given in this manual and those posted directly on the gear unit, especially
those regarding safety.
•Persons charged with working on the gear unit at any time in its service life must be trained specifically for
the purpose with special abilities and experience in this area as well as being equipped with the appropria-
te tools and individual safety equipment (as per Legislative Decree 626/94). Failure to meet these require-
ments constitutes a risk to personal health and safety.
•Use the gear unit only for the applications envisaged by the Manufacturer. Improper use can result in risks
to personal health and safety and economic damages.
The applications defined by the Manufacturer are those industrial applications for which the
gear unit has been developed.
•Keep the gear unit at its maximum efficiency by following the routine maintenance schedule. Good mainte-
nance enables the unit to operate at maximum performance over a long service life in compliance with sa-
fety regulations.
•When working on the unit in areas which are difficult to access or hazardous, ensure that adequate safety
precautions have been taken for the operator and others in compliance with the provisions of law on health
and safety at work.
•All maintenance, inspection and repairs must only be done by an expert maintenance technician fully fami-
liar with the attendant hazards. It is, therefore, essential to implement operating procedures which address
potential hazards and their prevention for the entire machine. The expert maintenance technician must al-
ways work with extreme caution in full compliance with applicable safety standards.
•During operation wear only the apparel and safety equipment indicated in the User instructions provided
by the Manufacturer or laid down by applicable laws on safety at work.
•Replace worn components with original spare parts. Use the lubricants (oil and grease) recommended by
the Manufacturer.
•Do not dump polluting materials into the environment. Dispose of all such materials as stipulated by appli-
cable legislation.
•After replacing lubricants clean the gear unit’s surfaces and the walk-on surfaces around the work area.
If the gear unit is to be serviced in a potentially explosive atmosphere, the operator must first
switch off power to the gear unit and ensure that it is out of service, as well as taking all neces-
sary precautions against it being accidentally switched on again or its parts moving without war-
ning.
Furthermore, all additional environmental safety precautions must be taken (e.g. elimination of
residual gas or dust, etc.).

4.0 - HANDLING AND TRANSPORT
4.1 - PACKAGING
The standard packaging, when supplied and unless otherwise agreed, is not proofed against rainfall and is
intended for shipping by ground and not sea, and for environments which are under cover and not humid.
The material can be stored in suitable conditions for a period of two years under cover at a temperature bet-
ween –15 °C and +50 °C at a relative humidity not in excess of 0%. Storage in all other conditions requires
specific packaging.
In order to facilitate handling, heavy packages can be loaded on pallets.
The most frequent types of packaging are shown in the figures below.
- Wooden crate for miscellaneous products shipped by sea.
- Carton pallet packaging for single products and kits.
On receipt of the gear unit, check that the delivery item corresponds to the purchase order
and that it is not damaged or faulty in any way. Refer any nonconformity to your BONFIGLIOLI
RIDUTTORI dealer.
Dispose of packaging materials as laid down by the provisions of law.
Horizontal packaging Vertical packaging

9
4.2 - HANDLING INSTRUCTIONS
Handle packages as per the Manufacturer’s instructions and those marked on the packages themselves.
Since the weight and shape of packages may make manual handling unfeasible, special equipment must be
used to avoid damage and injury. Persons authorised for this purpose must be trained and experienced in
the work in question to safeguard his safety and that of all other persons involved.
The person authorised to handle the product must take all necessary precautions to safe-
guard his safety and that of all other persons involved.
4.2.1 - Moving packages
•Prepare a suitable, delimited area with a level floor or surface for unloading the packages.
•Prepare the equipment required for handling the package. The lifting and handling equipment used (e.g.
crane or lift truck) must have adequate capacity for the weight and size of the load, taking into account its
attachment points and centre of gravity. If required, this information is indicated on the package itself. Har-
ness heavy packages with chains, belts and steel ropes after checking that they are capable of sustaining
the weight of the load, which is generally specified.
•When handling the load keep it level to avoid instability and/or tipping.
4.2.2 - Moving the equipment
All the following operations must be done with due care and caution and without sudden mo-
vements.
•Identify the attachment points for lifting the gear unit. Refer to Annex 4 of this manual for this information.
•Prepare the gear unit for lifting by attaching straps, hooks, shackles etc. to its attachment points, or alternati-
vely, use a pallet for moving the load. If using a crane, first lift the gear unit vertically out of its packaging.
•If using a lift truck or pallet truck, remove the packaging and fit the truck’s forks at the indicated positions.
•First lift the load very slowly to check that it is stable.
•Move the gear unit to the unloading area and lower it gently into position, taking care not to cause sudden
oscillations while moving it.
If the gear unit is coupled to an electric motor, do not use the eyebolts on the motor for lifting
the entire load, unless this is expressly indicated.

10
4.3 - STORAGE
Some recommendations for storing the gear unit are indicated below.
1. Do not store the unit in excessively humid conditions or where it is exposed to the weather (do not store
outdoors).
2. Do not place the gear unit directly on the ground.
3. Place the gear unit on a stable base and make sure that it is not subjected to accidental displacement.
4. Store the packaged gear unit (if allowed) in accordance with the instructions on the packaging itself.
If the gear unit is stored for more than 6 months, the following additional precautions must be taken:
5. Cover all machined external surfaces with a rustproofing product such as Shell Ensis or equivalent pro-
duct with similar properties and application range.
6. Fill the unit with lubricating oil.
SAFETY PRECAUTIONS to be taken when returning the gear unit to service after storage.
The output shafts and external surfaces must be thoroughly cleaned of all rustproofing product,
contaminants and other impurities (use a standard commercial solvent).
Do this outside any explosion hazard area.
The solvent must not touch the seal rings as this can damage them and render them ineffective.
If the oil or protective material used during storage is not compatible with the synthetic oil used
during the machine’s operation, the interior of the unit must be thoroughly cleaned before filling
with the operating oil.
The service life of bearing grease is reduced if the unit is stored for more than 1 year.
The bearing grease must be synthetic.

11
5.0 - INSTALLATION
5.1 - INSTALLING THE GEAR UNIT
The entire installation process must be planned based on the general design of the machine.
The person authorised to do the work must, if necessary, implement a safety plan to safe-
guard all persons directly involved and rigorously apply all applicable legislation.
If a gearmotor is going to be installed, please consult the owner’s manual of the electric motor on beforehand.
1. Thoroughly clean all packaging materials and protective product residue from the gear unit. Pay particu-
lar attention to the coupling surfaces.
2. Check that the data on the nameplate corresponds to that which is specified on the order.
3. Ensure that the structure to which the gear unit is to be mounted is sufficiently robust and rigid to support
its weight and operating stresses.
4. Check that the machine on which the gear unit is to be installed is switched off and cannot be acciden-
tally switched on again.
5. Check that all coupling surfaces are flat.
6. Check that the shaft/shaft or shaft/bore are perfectly aligned for coupling.
7. Fit suitable guards to protect against the external moving parts of the gear unit.
. If the work environment is corrosive for the gear unit or any of its parts, take the special precautions re-
quired for aggressive environments. In this case, contact the BONFIGLIOLI RIDUTTORI sales service.
9. We recommend applying a protective paste to all couplings between the gear unit/motor and other parts
(Klüberpaste 46 MR 401 or equivalent product with similar properties and application range) to ensure
optimal coupling and protection against fretting corrosion.
10. To ensure effective coupling, the driven shafts should be machined to the tolerances given in tables
(A16), (A17), (A1 ), (A19), (A20) and (A21) in Annex 3 of this Manual.
11. In case of installation outdoors and when fitted with an electric motor, protect the latter from direct sun-
light and the weather by means of guards or a casing. Also make sure that the assembly is properly ven-
tilated.
Now proceed with the installation as follows:
1. Place the gear unit in the vicinity of the installation area.
2. Mount the gear unit and secure it to the structure at the points provided. The gear unit should be secured
to the structure through all mounting points on the mount specified (feet or flange).
3. Locate the closed plug used for transportation (usually red) and replace it with the vented plug provided.
4. Tighten down the mounting bolts and check that the oil plugs are screwed down to the torque given in ta-
ble (A0).

12
5. Charge the gear unit with oil or top it up with reference to the method in which gear units of the type co-
vered by this manual are filled in the factory. The standard charge of synthetic life-time lubricant is as fol-
lows:
C 05 C 11 C 21 C 31 C 35 C 41 C 51 C 61 C 70 C 0 C 90 C 100
A 10 A 20 A 30 A 41 A 50 A 60 A 70 A 0 A 90
F10F20F30F40F50F60F70F0F90
S10 S20 S30 S40 S50
VF 27 VF 30 VF 44 VF 49 VF 130 VF 150 VF 1 5 VF 210 VF 250
W 63 W 75 W 6 W 110
(A1)
Life-time lubrication.
Life-time lubrication with ATEX-specified unit only.
Cap/vent thread Pitch Tightening torque
[Nm]
1/ " 2 5
1/4" 19 7
3/ " 19 7
1/2" 14 14
3/4" 14 14
1" 11 25
Bolt size
Tightening torque [Nm]
+5% /-10%
Bolt class
8.8 10.9
M4 3 3.
M5 5.9 .0
M6 10.3 13.0
M 25.5 32
M10 50 64
M12 7.3 110
M14 13 .3 1 0
M16 210.9 275
M1 306 390
M20 432 540
M22 592 720
M24 744 930
M27 1100 1400
M30 1500 1 50
(A0)

13
Helical in-line gear units C 11, C 21 and C 31 are not equipped with service plugs for direct
oil level checks.
Bevel helical gear units A 10, A 20 and A 30 are not equipped with service plugs for direct
oil level checks in mounting positions B6 and B7 only.
For these types of gear units, refer to Annex 1 of this Manual.
Before installing, check the unit as follows:
1. Place the gear unit in the mounting position indicated for the gear unit in question in Annex 1.
Wait 10 minutes for the oil level to stabilise inside the gear unit’s casing.
2. Insert a dipstick through the hole shown in drawing (S4) or (S5) and measure the distance betwe-
en the oil level and the exterior of the casing. This value must be compared with the values in
mm given in Annex 1, tables (A7) and (A ), depending on the mounting position for the gear
unit in question.
3. If the measurement gives a higher value than that prescribed, top up the oil to the correct level
as indicated in the catalogue.
For all other types of gear unit the oil level must be checked via the oil plug (spill type) using the
tool (out of scope for supply) described in Annex 1.
For the first charge and subsequent top ups, only use the recommended oils.
Installation of gear units classified under Directive 94/9/EC
•Category 2D gear units must be installed in compliance with the provisions of standards EN
1127-1 and EN 502 1-1-2. The installer must, therefore, be fully informed and trained for this
application.
•The installation technician must be aware of the ATEX class of the installation area, as well as
the risks associated with the presence of a potentially explosive atmosphere, with particular at-
tention to explosion and fire hazards, and thereby adopt the necessary safety precautions.
•All maintenance, assembly and disassembly work must be done outside the explosion ha-
zard area by trained personnel.
•Check that all accessory components (cables, joints, cable glands, cooling units, etc.) comply
with the Essential Health and Safety Requirements of the ATEX directives. Handle them with
extreme care to avoid altering their characteristics.
•Remove the bolts sealing the threaded holes if provided for securing the gear unit. Do not da-
mage the coupling surfaces.
•When assembling gear units with a torque arm, make sure that during operation, the metal
parts which move relative to each other do not come into contact. If necessary, insert non-me-
tal anti-friction elements in compliance with Directive 94/9/EC.
•Do not connect any object with electrical resistance greater than 109Wto the product.
•Install guards to prevent the hazardous accumulation of dust and liquids on the seals of the so-
lid shafts and to protect them mechanically.
•In case of installation of the gearmotor in a vertically downward orientation, the electric motor
must be equipped with a drip cover.
•The output shaft and any pulleys or other transmission components must be perfectly aligned.
•Only install the gear unit in the motor execution and mounting position specified on the order.
Shaft-mounted gear units can be installed with a tolerance relative to the theoretical plane of
installation of ± 5°.
•If the gear unit is supplied without lubricant it must be installed as such and only filled with lu-
bricant thereafter.
•Secure the gear unit to a flat, vibration-free surface capable of bearing the torsional stresses it
produces in operation. Make sure not to deform the contact surfaces, mounting feet and/or
flanges by overtightening the bolts.
•Use bolts of quality no lower than . for mounting the gear unit, and for heavy-duty installa-
tions use 10.9 bolts. For the tightening torque refer to table (A0). To prevent bolts from unscre-
wing, apply a thin film of Loctite 510, or equivalent, on threads of all bolts used to assemble the
gear unit onto the structure and/or to the electric motor.
•Make sure that the radial/thrust loads and operating torques do not exceed those specified for
the unit.
•The vent caps and oil level caps must be easy to access for inspection.
•Clean the gear unit thoroughly after installation.

14
5.1.1 - Gear units with solid output shaft
For mounting external parts do not use hammers or other tools which might damage the gear
unit’s shafts or bearings. Instead, proceed as indicated in the diagram below:
Bolt (1) and spacer (2) are to be supplied by customer.
To minimise the loads on the shaft bearings, when mounting transmission elements with asymmetrical hubs,
the preferred layout is shown in diagram (A) below:
5.1.2 - Gear units with hollow output shaft
To facilitate mounting hollow shaft gear units onto the machine’s driven shaft, proceed as indicated in the
diagram below. Also refer to Annex 3 of this Manual for dimension information on customer’s shaft.
The bolt (1) and spacer (2) are to be supplied by customer.
(A)

15
5.1.3 - Gear units with shrink disk
Series A and F gear units may be specified with a shrink disk for coupling onto the driven shaft. When instal-
ling a unit of this type, proceed as follows:
1. Loosen the locking bolts gradually and in sequence and remove the entire shrink disk.
2. Clean and carefully degrease the coupling surface between the gear unit’s output shaft and the customer
shaft.
Do not use molybdenum bisulphide or any other grease which would affect the friction coeffi-
cient of the coupling surfaces and reduce the performance of the shrink disk.
3. Fit the gear unit onto the machine sliding its output shaft onto the driven shaft.
4. Fit the shrink disk to the gear unit shaft.
5. Fully tighten down the shrink disk bolts gradually following a circular sequence using a torque wrench.
This operation usually must be repeated several times to reach the tightening torque Mt specified in the
table below:
A10 A20 A30 A41 A50 A60 A70 A80 A90
Mt [Nm] 14.5 14.5 14.5 14.5 35 35 35 69 69
F10 F20 F30 F40 F50 F60 F70 F80 F90
Mt [Nm] .5 14.5 14.5 14.5 14.5 35 35 69 69
(A2)
Mt.
5.1.4 - Shaft mounted gear units series F
Anchoring the torque arm
Use the original vibration-damping kit to ensure optimal operation of the assembly, as it is specifi-
cally designed and constructed, along with the gear unit, for operation in explosion hazard areas.
Failure to use the original accessory on gear units classified under 94/9/EC voids the ATEX certi-
fication.
The torque arm shown in the diagram is to be supplied by customer.
Mt
[Nm]
F10 10
F20 10
F30 20
F40 20
F50 50
F60 50

16
5.2 - INSTALLING AN IEC-STANDARD FLANGED MOTOR
Further to all the precautions indicated above, when installing a IEC-flange mount electric motor the following
precautions must also be observed:
•
Do not force the coupling and do not use inappropriate tools during assembly. Take care not to damage
the flat and/or cylindrical coupling surfaces.
•
Do not force the shaft with large radial and/or thrust loads.
•
To facilitate assembly, use a lubricating synthetic oil paste such as Klüberpaste 46 MR 401 or equivalent
product with similar properties and application range.
•
Tighten down all motor/gear unit mounting bolts to their prescribed torque. For the tightening torques, refer
to table (A0).
When the gear unit is mounted to an IEC electric motor, proceed as follows:
•
Apply a layer of sealant (Loctite 510 or equivalent product with similar properties and applica-
tion range) to the motor/gear unit mounting flanges, spigot and frontal coupling surfaces as
shown in diagram (S1).
(S1)
•
After mounting the motor, apply a layer of sealant (Loctite 5366 or equivalent product with simi-
lar properties and application range) around the edges of the flanges so as to close any gaps
between their surfaces.
•
If the gearbox is of the flanged type, the User must take similar precautions to prevent dust de-
posits forming in the gaps between the flanges or in the vicinity of the couplings.
1 - Apply “Loctite 510” to both the flange
surface and spigot.
2 - Apply “Klüberpaste 46MR401” to the
input shaft bore and motor shaft.
3 - Use “Loctite 5366” to seal the area
of contact between the gear unit and
motor, taking care to fill in any gaps
between the two flanges (e.g. disas-
sembly slots).

17
6.0 - TESTING THE GEAR UNIT
The gear unit has been factory tested by the Manufacturer.
Before starting the unit, check that:
•The machine incorporating the gear unit complies with the provisions of the “Machinery Directive”
9 /37/EC and any other applicable safety legislation.
•The gear unit’s mounting position in the installation corresponds to that prescribed and indicated on the
nameplate.
•The electrical power supply and control systems are suitable and operational as stipulated in standard EN
60204-1, and grounded as per standard EN 50014.
•The motor power supply corresponds to that prescribed and is within ± 5% of the rated value.
•The oil level is as prescribed and that there are no leaks from the caps or gaskets.
•The unit does not run noisily or with excessive vibration.
Before starting up the unit, check and ensure that:
•Assembly is not carried out in a potentially explosive atmosphere (oil, acid, gas, vapour or ra-
diation) and that there is no dust deposits thicker than 5 mm on the gear unit.
•During service the gear unit is sufficiently ventilated and that it is not subject to radiation from
external heat sources.
•During service the cooling air does not exceed 40 °C.
•The oil level, drain and vent plugs are all easily accessible.
•All accessories of any type mounted onto the gear unit are ATEX compliant.
•Gear units with hollow shafts, with or without shrink disk, have been correctly mounted.
•The gear unit is thoroughly cleaned after installation.
•All guards installed to prevent accidental contact between operators and the gear unit’s moving
parts or seals, are effective.

1
Measuring the gear unit’s surface temperature
•The gear unit’s maximum surface temperature depends on the motor speed, gear ratio and
motor execution and must never exceed 130 °C (160 °C if so specified on the nameplate).
•The nameplate specifications regarding the maximum surface temperature, refer to measure-
ments made in normal ambient and installation conditions. Even minimal variations to said
conditions (e.g. smaller mounting cabinet) could have a significant impact on the build up of
heat.
•When commissioning the gear unit, the surface temperature must be measured in the same
operating conditions as for the final application.
The surface temperature must be measured at the coupling between the gear unit and motor,
and at the points which are most shielded from the motor’s fan cooling.
(S2)
IMPORTANT:
The maximum surface temperature is reached after 3 hours’ operation at full load. The
temperature measured in these conditions must not differ (DT) from the ambient tempe-
rature by more than the following values:
Should the temperature differential exceed these values, stop the gear unit at once and
contact the BONFIGLIOLI RIDUTTORI technical service.
•If the temperature differential is within the above values, wait for the gear unit to cool down and
then install the temperature indicator supplied with the gear unit at the point of maximum tem-
perature.
Example:
•At the same time, check for excessive running noise and vibration.
DT[°C]
C 11...C 61 75
A 10...A 60 75
F 10...F 60 75
VF 44, VF 49 75
W 63...W 86 75
W 110 90
(A3)
2
6
6
°
F
1
3
0
°
C
This manual suits for next models
53
Table of contents
Other BONFIGLIOLI Engine manuals
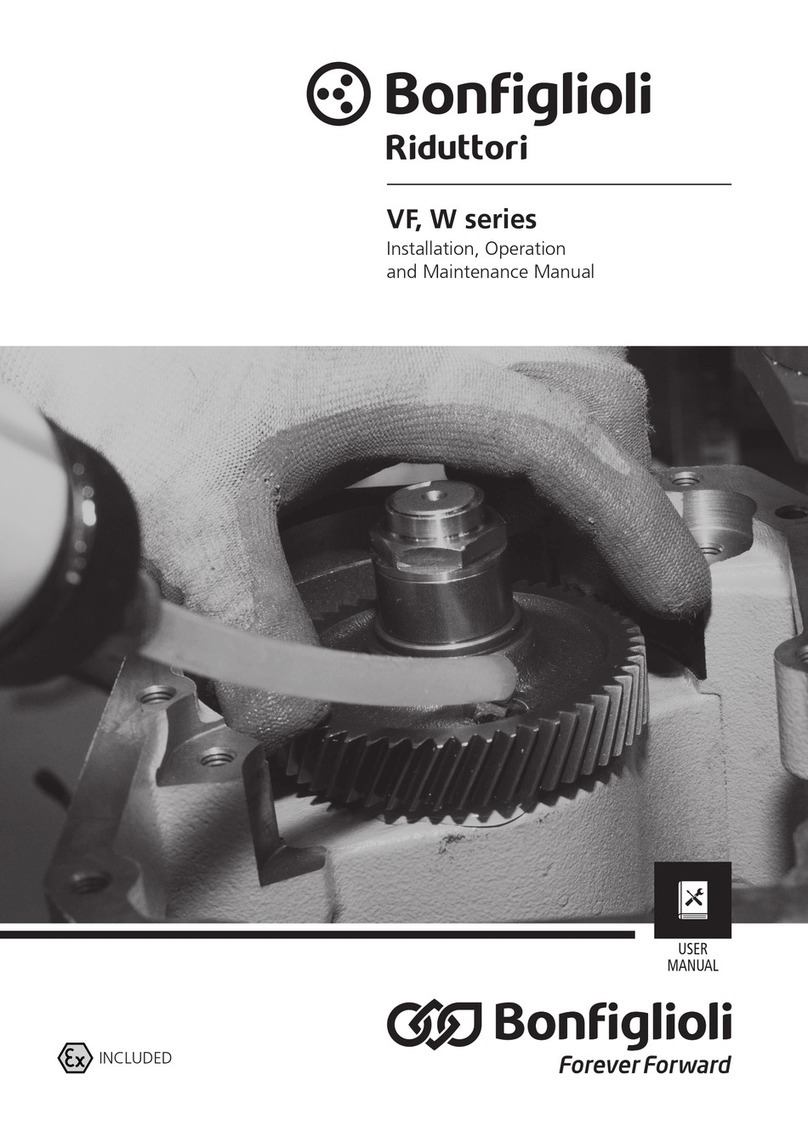
BONFIGLIOLI
BONFIGLIOLI VF Series User manual
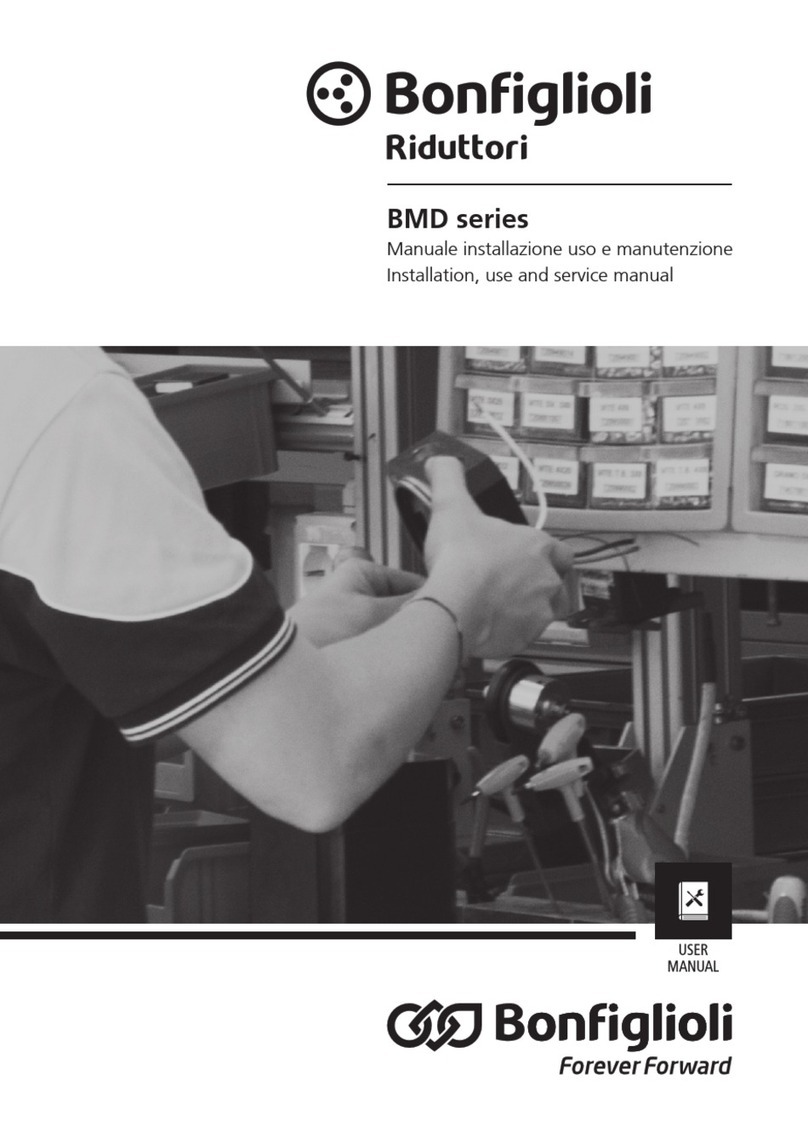
BONFIGLIOLI
BONFIGLIOLI BMD 65 User manual
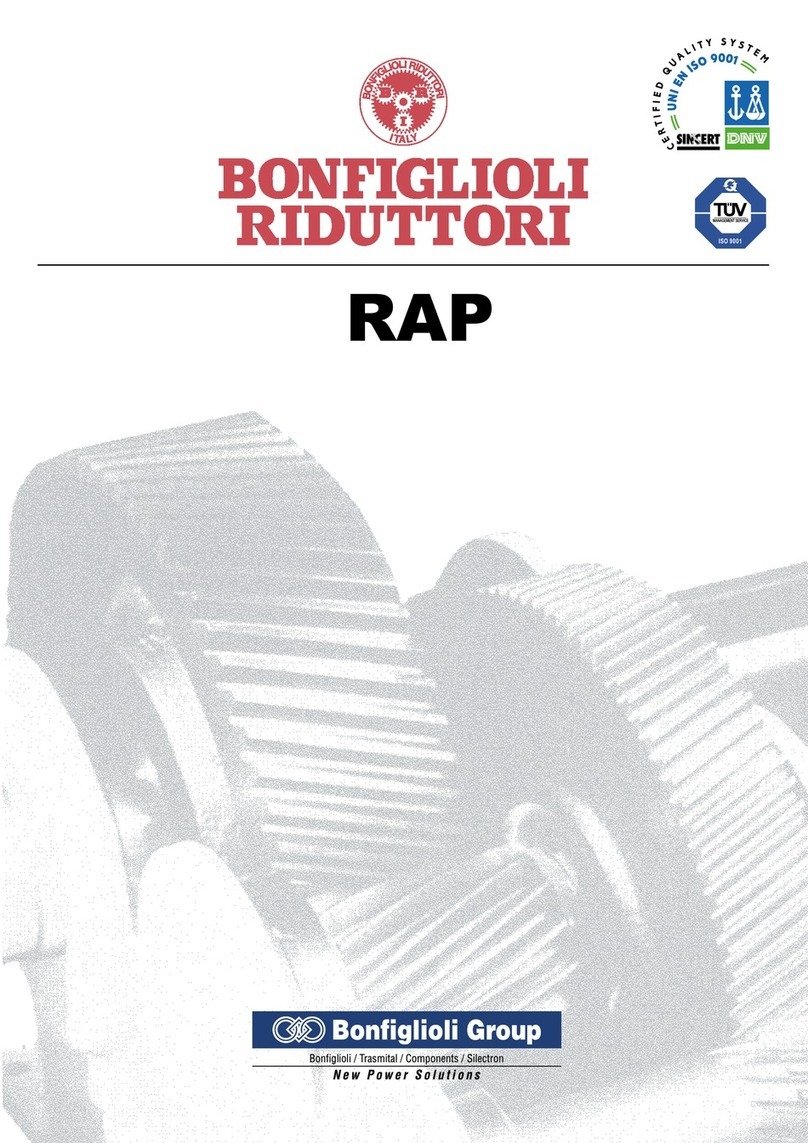
BONFIGLIOLI
BONFIGLIOLI C RAP Series User manual
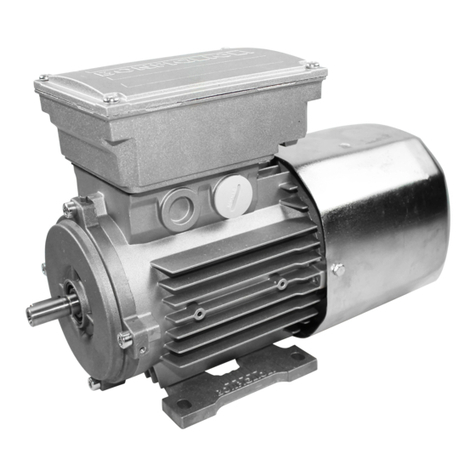
BONFIGLIOLI
BONFIGLIOLI BX Series Installation and operating instructions

BONFIGLIOLI
BONFIGLIOLI AS Series User manual
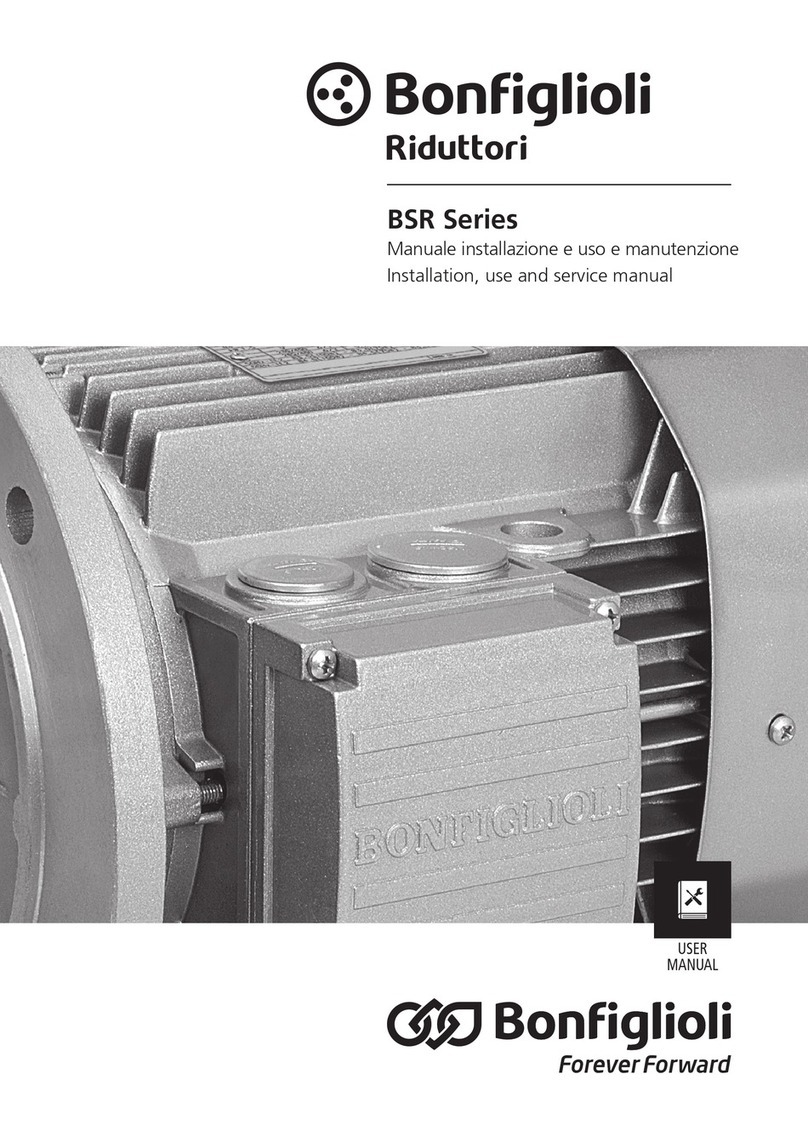
BONFIGLIOLI
BONFIGLIOLI bsr series User manual
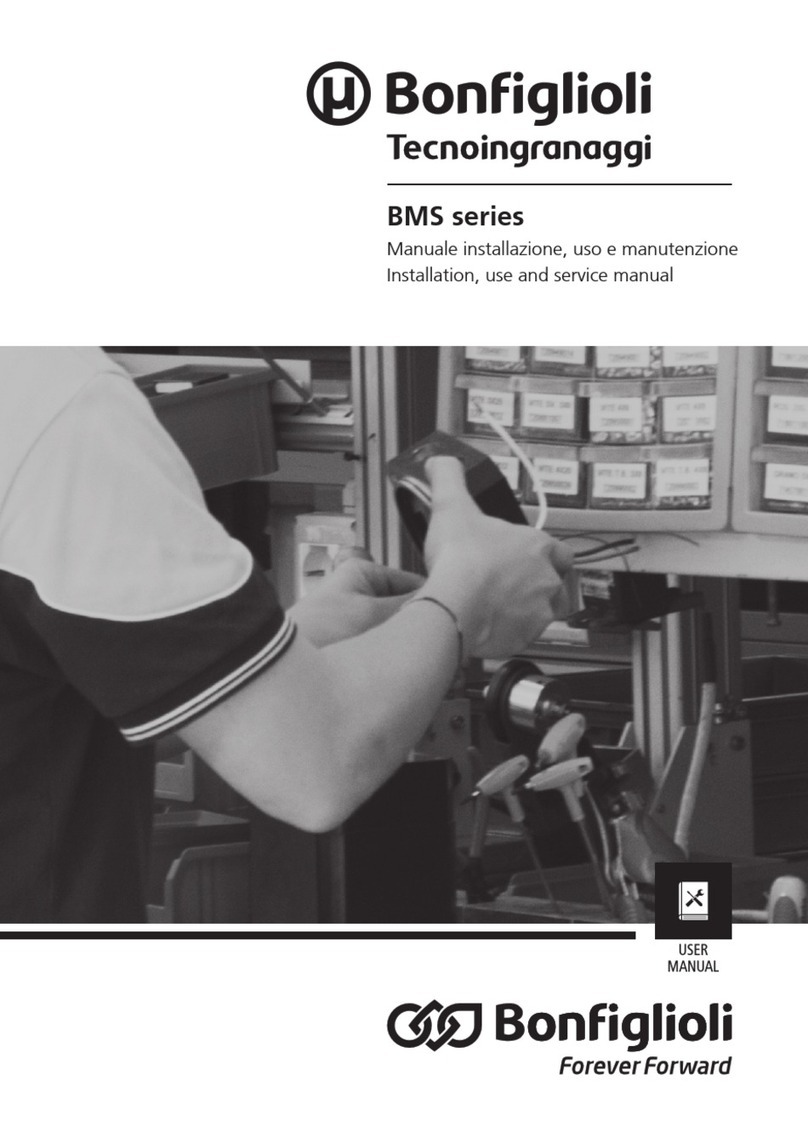
BONFIGLIOLI
BONFIGLIOLI BMS series User manual
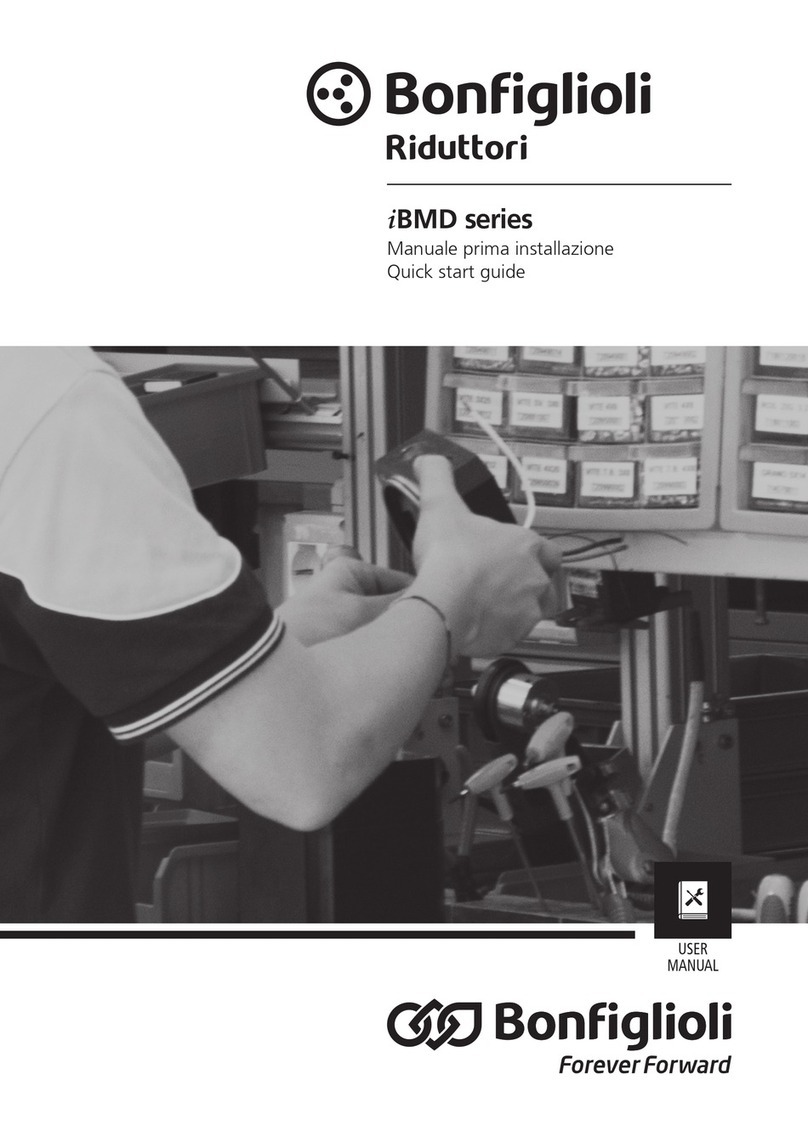
BONFIGLIOLI
BONFIGLIOLI iBMD Series User manual
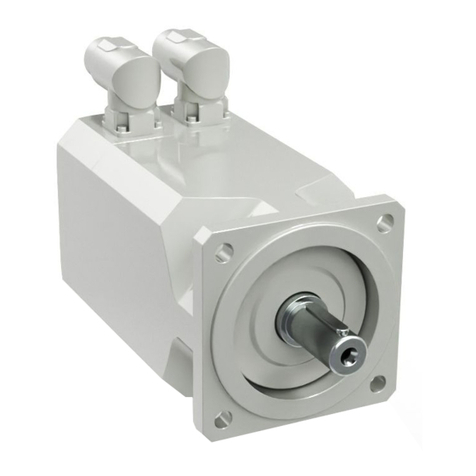
BONFIGLIOLI
BONFIGLIOLI bmd series User manual