controlair 550 Series Manual

Shaded areas and associated dimensions apply to the zero based unit only.
(Drawing downloads available at http://www.controlair.com)
Contents
Section Description Page
1.0 Installation 3
2.0 Operation 5
3.0 Approvals 6
4.0 Maintenance & Repairs 7
5.0 Troubleshooting 8
6.0 Warranty 8
Type 550X
Miniature I/P, E/P Transducer
Installation, Operation and
Maintenance Instructions
8 Columbia Drive, Amherst, New Hampshire 03031 USA
Phone: (603) 886-9400 Fax: (603) 889-1844
18

Type 550X Page 2
WARNING
CAUTION
DANGER
ALL DANGER, WARNING, AND CAUTION NOTICES MUST BE COMPLIED WITH IN FULL.
Functional Specifications
Standard Range High Output Zero-Based
INPUT 4-20 MA, 0-5 VDC, 0-10 VDC, 1-5 VDC, 1-9 VDC
Outputs
psig
(BAR)
Supply Pressure
psig
(BAR)
3-15
(0.2-1.0)
20-100
(1.4-6.9)
3-27
(0.2-1.8)
32-100
(2.2-6.9)
6-30
(0.4-2.0)
35-100
(2.4-6.9)
2-60
(0.14-4.0)
65-150
(4.5-10.0)
3-120
(0.2-8.0)
125-150
(8.6-10.0)
0-30
(0.0-2.0)
35-100
(2.4-6.9)
0-60
(0.0-4.0)
65-150
(4.5-10)
0-120
(0.0-8.0)
125-150
(8.6-10)
Air Consumption 1.8 scfh (0.9 NL/min) at mid range typical 4.2 scfh (2.1 NL/min) at mid range
typical
6.0 scfh (3 NL/min) at mid range typical
Flow Capacity 4.5 scfm (127.4 NL/min)
at 25 psig (1.7 BAR) supply pressure
12.0 scfm (340 NL/min)
at 100 psig (6.9 BAR) supply pressure
12.0 scfm
(340 NL/min)
at 100 psig
(6.9 BAR)
supply
20.0 scfm
(566 NL/min)
at 150 psig (10.0
BAR) supply
12.0 scfm (340 NL/min)
at 100 psig (6.9 BAR) supply
20.0 scfm
(566 NL/min)
at 150 psig
(10.0 BAR)
supply
Temperature Limits -400F to 1580F (-400C to +700C)
Impedance 4-20 mA
180 Ohms
0-5 VDC
615 Ohms
0-10 VDC
1230 Ohms
1-5 VDC
495 Ohms
1-9 VDC
985 Ohms
4-20 mA
240 Ohms
0-5 VDC
550 Ohms
0-10 VDC
1100 Ohms
1-5 VDC
440 Ohms
1-9 VDC
880 Ohms
4-20 mA
240 Ohms
0-5 VDC
550 Ohms
0-10 VDC
1100 Ohms
1-5 VDC
440 Ohms
1-9 VDC
880 Ohms
4-20 mA
245 Ohms
0-5 VDC
520 Ohms
0-10 VDC
1040 Ohms
1-5 VDC
495 Ohms
1-9 VDC
900 Ohms
4-20 mA
280 Ohms
0-5 VDC
500 Ohms
0-10 VDC
1000 Ohms
1-5 VDC
475 Ohms
1-9 VDC
880 Ohms
4-20 mA
290 Ohms
0-5 VDC
450 Ohms
0-10 VDC
900 Ohms
1-5 VDC
410 Ohms
1-9 VDC
830 Ohms
4-20 mA
300 Ohms
0-5 VDC
480 Ohms
0-10 VDC
960 Ohms
1-5 VDC
460 Ohms
1-9 VDC
800 Ohms
4-20 mA
315 Ohms
0-5 VDC
495 Ohms
0-10 VDC
990 Ohms
1-5 VDC
455 Ohms
1-9 VDC
785 Ohms
Performance Specifications
Linearity
(Independent)
<± 0.5% of span <± 2.0% of span <± 1.5% of span
Hysteresis, and
Repeatability
< 0.5% of span < 0.5% of span < 1.0% of span
Supply Pressure
Sensitivity
< 0.1% of span per 1.0 psig (0.07 BAR) < 0.4% of span per 1.0 psig
(0.07 BAR)
< 0.02% of span per 1.0 psig (0.07 BAR)
Physical Specifications
Port Sizes Pneumatic: 1/4” NPT
Media Clean, dry, oil-free, instrument air, filtered to 40 micron
Electrical
Connections
Conduit 1/2” NPT, Terminal Block, DIN 43650, M12
Mounting Direct wall, panel, 1 1/2" pipe, DIN rail or Manifold
Materials Housing: Chromate-treated aluminum with epoxy paint. NEMA 4X (IP65)
Elastomers: Buna-N
Trim: Stainless steel; brass; zinc-plated steel
Weight 1.3 lbs (0.59 kg) 1.7 lbs (0.77 kg)
DANGER, WARNING, CAUTION and NOTE statements
DANGER
NOTE
Refers to conditions or hazards which could result in serious personal injury or death.
Refers to conditions or hazards which could result in personal injury.
Refers to conditions or hazards which could result in equipment or property damage.
Alerts you to facts or special instructions.
SPECIFICATIONS

Type 550X Page 3
2” PIPE
1.1 Pre-Installation Requirements
1.1.1 Environment: Suitable for installation in the following locations:
Intrinsically safe operation in hazardous locations outdoors (NEMA 4X, CSA.ENC.4 & IP65)
See section 3.1, 3.2 and 3.3 for Factory Mutual (FM), Canadian Standards (CSA), ATEX and EU
approvals.
All wiring must be made to all local and national codes appropriate to the area of
installation.
1.1.2 Electrical Input: 4-20 mAdc current source or 0-5, 0-10, 1-5, 1-9 VDC voltage source depending on
model.
1.1.3 Air supply: Clean, dry, oil free instrument air filtered to 40 micron.
Clean all pipe lines to remove dirt and scale prior to installation. Failures attributable to
instrument air supply contamination are not covered by the warranty.
This instrument vents to atmosphere. The use of supply gas other than air can create a
hazardous environment.
1.2 Mounting
1.2.1 The Type 550X comes with a standard mounting kit that enables panel or wall mounting of the
unit. An accessory mount kit (P/N: 448-542-005) allows 1 ½” or 2” pipe mounting.
1.2.2 With access to the rear of a panel, attach transducer using two 10-32 screws and the two threaded
mounting screws on the back of the unit. With no access to the back of the panel, attach the bracket to
the transducer using the two 10-32 holes on the back of unit and mount bracket to panel using four 10-
32 screws (see figure 2).
1.2.3 To mount unit to a 1 ½” or 2” pipe, use two 10-32 holes on the back of the unit to attach bracket to
transducer. Then place U-bolt around pipe and through bracket. Place nuts on U-bolt and tighten (see
figure 1) (Accessory mount kit P/N: 448-542-005).
1.2.4 Due to its light weight, the Type 550X can also be mounted in line with support provided by the supply
and output piping.
1.2.5 Because of it’s small size, the Type 550X can easily be mounted to a manifold. ControlAir’s Type 925
multifunction supply manifold is designed for this purpose.
Shaded areas and associated dimensions apply to the zero based unit only.
1. INSTALLATION
DANGER
NOTE
CAUTION
1.14
29.0
1 1/2”
PIPE
1.39
35.3
3.50
88.9
4.74
120.3
3.30
83.7
2” PIPE

Type 550X Page 4
1.2.6 The Type 550X can be mounted to DIN-rail using the optional kit, ControlAir part number
445-766-024. This will allow the transducer to mount to DIN 50045, 50035, 50022 rails (see figure 3).
Shaded areas and associated dimensions apply to the zero based unit only.
1.3 Pneumatic Connections
1.3.1 Clean all pipe lines to remove dirt and scale prior to installation.
1.3.2 Supply air must be filtered to 40 microns and free of moisture and lubricants.
1.3.3 Two (2) 1/4" NPT ports labeled IN are provided for supply air connections. Either port may be used.
The unused port must be plugged with the pipe plug included with the unit.
1.3.4 Two (2) 1/4" NPT ports labeled OUT are provided for pneumatic output connections. Either port may
be used and one may be used for the mounting of an output gauge. If no gauge is installed, the
unused port must be plugged with the pipe plug included with the unit.
1.4 Electrical Connections
1.4.1 Both the I/P and E/P versions of the Type 550X are two wire devices (do not require a separate power
source), plus a safety ground. The I/P unit requires a variable input current of 4-20 mA. The E/P
version requires a DC voltage input signal such as 0-10 VDC.
1.4.2 1/2" NPT conduit connection (A) is made using 18” pigtail wire coming from unit. For I/P (current to
pressure) versions, electrical connections are made to the red (+) and black (-) leads. The green lead
is furnished for case ground. For E/P (voltage to pressure) versions, electrical connections are made
to the red (+) and black (-). The green lead is furnished for case ground (see figure 4).

Type 550X Page 5
Pin I/P-E/P Connection
4 Pin M12
Connector
3.01
76.5
3.08
78.2
4.52
114.9
1.4.3 DIN 43650 Connector (D) electrical connections are made as shown in figure 5.
Shaded areas and associated dimensions apply to the zero based unit only.
1.4.4 Terminal Block (T) Electrical connections are made to the positive (+) and negative (-) terminals. For
direct acting operation connect the positive side of the input signal to the (+) terminal
1.4.5 The use of shielded cable is recommended.
1.4.6 M12 (M) Electrical Connections are made to the positive (+) pin 2 and negative (-) pin 1. For direct
acting operation connect the positive side of the input signal to the (+) pin 2. Pin 4 is for case ground.
Pin 3 is not used.
NOTE No agency approvals apply for M12 connector.

Type 550X Page 6
2.1 Calibration
2.1.1 All units are shipped from the factory calibrated, direct acting.
Factory calibration is susceptible to shift due to handling during transit. ControlAir
recommends that all units be recalibrated prior to use.
2.1.2 Though the units are shipped fully calibrated it is suggested that the user check the calibration to
ensure that settings and operation match the application requirements.
2.2 Direct Acting Calibration
2.2.1 In direct acting operation the unit is calibrated so that minimum input signal corresponds to minimum
output pressure and increasing input signal results in increasing output pressure. Apply the minimum
input signal of the range being used (e.g. 4 mA for a 4-20 mA unit).
2.2.2 Observe the output pressure. If necessary, adjust the zero screw until reaching minimum output
pressure setting. Turn zero screw clockwise to increase and counter clockwise to decrease.
2.2.3 Apply the maximum input signal of the range being used (e.g. 20 mA for a 4-20 mA unit).
2.2.4 Observe the output pressure. If necessary, adjust the span screw until reaching maximum output
pressure setting.
2.2.5 After setting the span it will be necessary to recheck the zero. Repeat steps 1-4 until both end points
are at required values.
2. OPERATION
NOTE
The unit must be calibrated in the plane it is mounted in.
NOTE
NOTE
NOTE
If unable to achieve output during the calibration process, follow the steps
outlined in 4.1.4. to clean the orifice. Then turn the zero adjustment screw
clockwise slowly and carefully until output pressure begins to respond.
The unit must be calibrated in the plane it is mounted in.
For I/P (current) input models, turn span screw clockwise to increase pressure,
counter clockwise to decrease pressure. For E/P (voltage) input models, turn span
screw clockwise to decrease pressure, counter clockwise to increase pressure.
NOTE
NOTE Repeated cycling of supply pressure may cause increased leakage and
p
remature
p
roduct failure.

Type 550X Page 7
3.1 Factory Mutual Research Corporation (FM)
& Canadian Standards (CSA) Approvals
Intrinsically Safe (1/2” NPT Conduit): Intrinsically Safe (1/2” NPT Conduit):
Class I, II, III, Division 1, Class I, Division 2,
Groups C, D, E, F & G Groups A, B, C & D
Enclosure Nema 4X (IP 65) Temp. Code T4 Ta = 700 C
Temp. Code T4 Ta = 700 C
Rated 4-20 mA, 30 VDC Max. Suitable for (Conduit only)
Class II & III, Division 2
Intrinsically Safe (DIN & Terminal) Groups F & G
Class I, Division 1, Groups C & D Temp. Code T4 Ta = 700 C
Temp. Code T4 Ta=70 C
Rated 4-20 mA, 30 VDC Max. Entity Parameters
Ui (Vmax) = 30 VDC Ci = 0 uF
Ii (Imax) = 125 mA Li = 0 m H
Pi = .7 w Max.
3.2 ATEX Approvals (option K)
Ex ia IIB T4 Entity Parameters
Tamb = -400 C to +700 C Ui (Vmax) = 30 VDC Ci = 0 uF
FM09ATEX0012X Ii (Imax) = 125 mA Li = 0 mH
Pi = .7 w Max.
Notes:
1. (North America) Control equipment connected to the Associated Apparatus must not use or generate more than 250 Vrms or Vdc.
2. The IS Barriers or Equipment (Associated Apparatus) must be FM Approved and the configuration of associated Apparatus must be
FM Approved and CSA certified under the Entity Concept. The Associated Apparatus may be installed within the Hazardous
(Classified) location for which it is approved. The Associated Apparatus and hazardous location loop apparatus manufacturer’s
control drawings must be followed when installing this equipment. An AEx [ib] Associated Apparatus is suitable only for connection
to Class I, Zone 1, Hazardous (Classified) Locations and is not suitable for Class I, Zone 0, or Class I, Division 1 Hazardous
(Classified) Locations.
(ATEX) The IS barriers or other Associated Apparatus shall comply with the ATEX directive 2014/34/EU. Control equipment
connected to the Associated Apparatus shall not use or generate more than the marked Um.
3. (US) Installation should be in accordance with ANSI / ISA RP12.6 “Installation of Intrinsically Safe Systems for Hazardous
(Classified) Locations” and Article 500 of the National Electrical Code (ANSI/NFPA 70).
(Canada) Installation should be in accordance with Section 18 of the Canadian Electrical Code.
(ATEX) Installations shall comply with EN 60079-14
4. (North America) The connection option “A” is suitable for Type 4X installations. All others must be mounted in a suitable enclosure.
2809
II 1G
3. APPROVALS

441-622-052 REV 04/23/19 Type 550X Page 8
5. The connection option “A” is suitable for Class I, II, and III, Division 2, Groups A, B, C, D, E, F, and G hazardous (classified)
locations. Dust--tight conduit seal must be used when installed in Class II and Class III environments.
The connection options “D” and “T” are suitable for Class I, Division 2, Groups A, B, C, and D hazardous
(classified) locations.
Transducers to be installed in accordance with the:
(US) National Electrical Code (ANSI--NFPA 70) Division 2 hazardous (classified) location wiring techniques. (Canada) Canadian
Electrical Code
6. The Intrinsic Safety Entity concept allows the interconnection of two FM Approved Intrinsically safe devices with. The linear barriers
parameters must meet the following requirements:
Ui or Vmax > Uo or Voc or Vt > 7.2 volts
Ii or lmax > lo or lsc or lt
Ca or Co > Ci + Ccable
La or Lo > Li + Lcable
Pi > Po.
Entity Parameters for: MODELS T550-A*%
Ui (Vmax) = 30 V
li (lmax) = 125 mA
Pi = 0.70 watts
Ci = 0 uF
Li = 0 mH
7. No revision to this drawing is permitted without prior FM Approvals notification.
8. The Intrinsic Safety Entity concept allows the interconnection of two EU-Type certified devices with entity parameters, not
specifically examined in a combination when: Ui > Uo
Ii > lo
Ca > Ci + Ccable
La > Li + Lcable
Pi > Po
9. Because the enclosure is made of aluminum, if it is mounted in an area where the use of category 1G apparatus is required, it must
be installed such that even in the event of rare incidents, ignition sources due to impact and friction sparks are excluded.
3.3 EU Declaration of Conformity
We,ControlAirLLC
8ColumbiaDrive
Amherst,NH03031
DeclarethattheType550XTransducerfamilytowhichthisdeclarationapplies,complywiththesestandards:
EN50082‐1:1998
EN55011:1999
EN61010‐1:1993includingAMD2:1995
FollowingtheprovisionsofEMCdirective89/336/EEC
EN60079‐0:2006
EN60079‐11:2007
FollowingtheprovisionsofATEXdirective2014/34/EU
Under normal circumstances, no maintenance should be required.
4.1 Instrument Air Filtration
4.1.1 Failures due to instrument supply air contamination are not covered by warranty.
4.1.2 Use of oil and/or water saturated instrument air can cause erratic operation.
4.1.3 Poor quality instrument air can result in unit failure. It is recommended that a filter regulator (such as
ControlAir Type 300) be placed upstream of each unit where oil and/or water laded instrument air is
suspected.
4.1.4 If clean, dry air is not used the orifice can become blocked. To clean, first turn off supply air, then
remove the screw located on the side of the unit above the “out” port. The orifice is a very small hole
on the side of the screw. Unplug the orifice using a wire that has a smaller diameter than 0.012”
(0.30mm). Replace screw tightly into unit.
4. MAINTENANCE AND REPAIRS
NOTE

441-622-052 REV 03/24/20 Type 550X Page 9
4.2 Factory Repairs
3.2.1 In the event of unit failure, the Type 550X can be returned to the factory through point of purchase for
warranty repair if the warranty period has not expired.
3.2.2 All units returned for repair must be authorized prior to receipt at the factory. Contact a representative
at the point of purchase to receive a Return Authorization Number.
4.3 Field Repairs
3.3.1 Service kits for elastomer components in the Type 550X are available. Consult factory for kit numbers
and availability.
3.3.2 Replacement components for the Type 550X are available. Consult factory for part numbers and
availability.
PROBLEM LOOK FOR SOLUTION
No or low output Zero adjustment
Supply pressure too low
Reset zero (2.2.2 and 2.2.3)
Increase supply pressure (see specs)
Unstable / low output Electrical connection
Clogged orifice
Check connection/signal (1.4)
Clean orifice (4.1.3)
Erratic operation Liquid/contamination in air supply Clean air supply (1.1.3)
Works in reverse Pressure goes down when signal is
increased
Reverse input wires (1.4.2)
Output equals supply pressure Improper pneumatic connections Insure that supply is connected to “IN” port and
output is connected to “OUT” port (1.3.3, 1.3.4)
ControlAir LLC products are warranted to be free from defects in materials and workmanship for a period of
eighteen months from the date of sale, provided said products are used according to ControlAir LLC
recommended usages. ControlAir LLC’s liability is limited to the repair, purchase price refund, or replacement in
kind, at ControlAir LLC’s sole option, of any products proved defective. ControlAir LLC reserves the right to
discontinue manufacture of any products or change products materials, designs or specifications without notice.
Note: ControlAir does not assume responsibility for the selection, use, or maintenance of any product.
Responsibility for the proper selection, use, and maintenance of any ControlAir product remains solely with the
purchaser and end user.
Before using these products with fluids other than air, for non-industrial application, life-support systems, or other
applications not within published specifications, consult ControlAir LLC
8 Columbia Drive, Amherst, NH 03031 USA
Phone: (603) 886-9400 Fax: (603) 889-1844
www.controlair.com [email protected]
5. TROUBLESHOOTING
NOTE
6. WARRANTY & DISCLAIMER
WARNING These products are intended for use in industrial compressed-air systems only. Do
not use these products where pressures and temperatures can exceed those listed
under Specification
If problems are not solved by troubleshooting procedures, contact a
factory applications engineer at (603) 886-9400 for further assistance.
An ISO-9001:2015 Certified Company
Table of contents
Other controlair Transducer manuals
Popular Transducer manuals by other brands
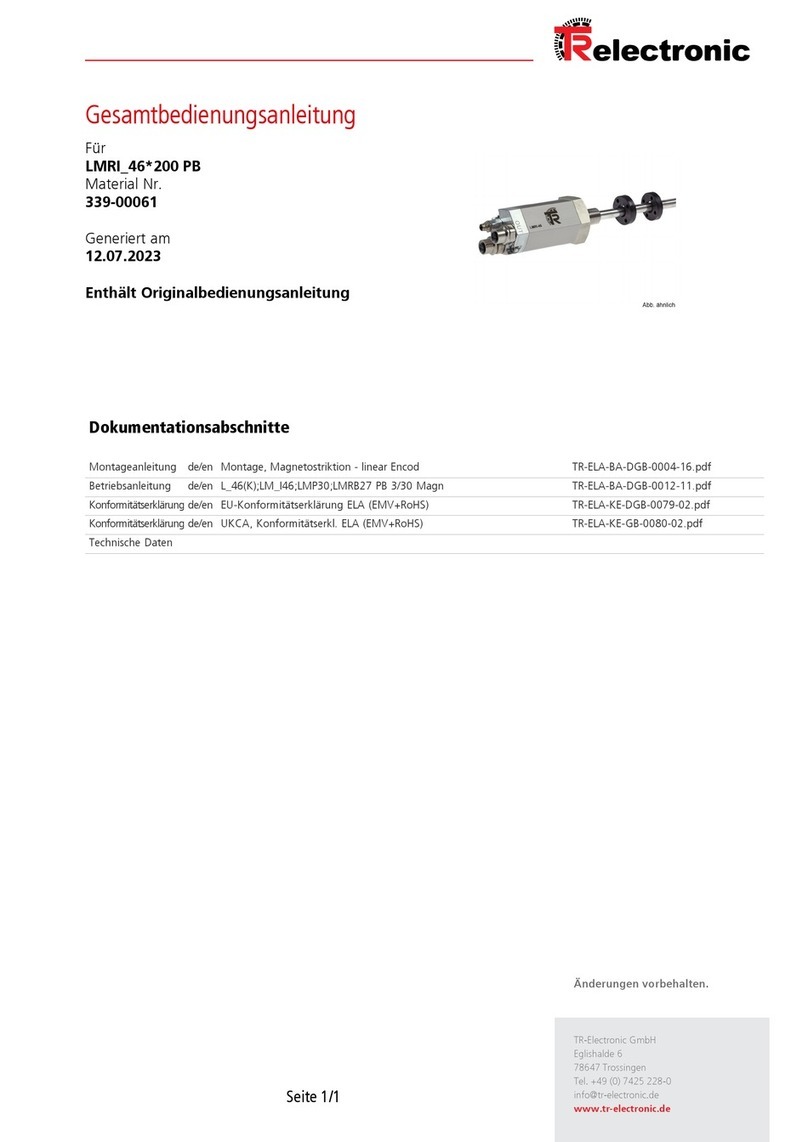
TR-Electronic
TR-Electronic LMRI-46 200 PB manual

HBM
HBM TOP Transfer Mounting instructions
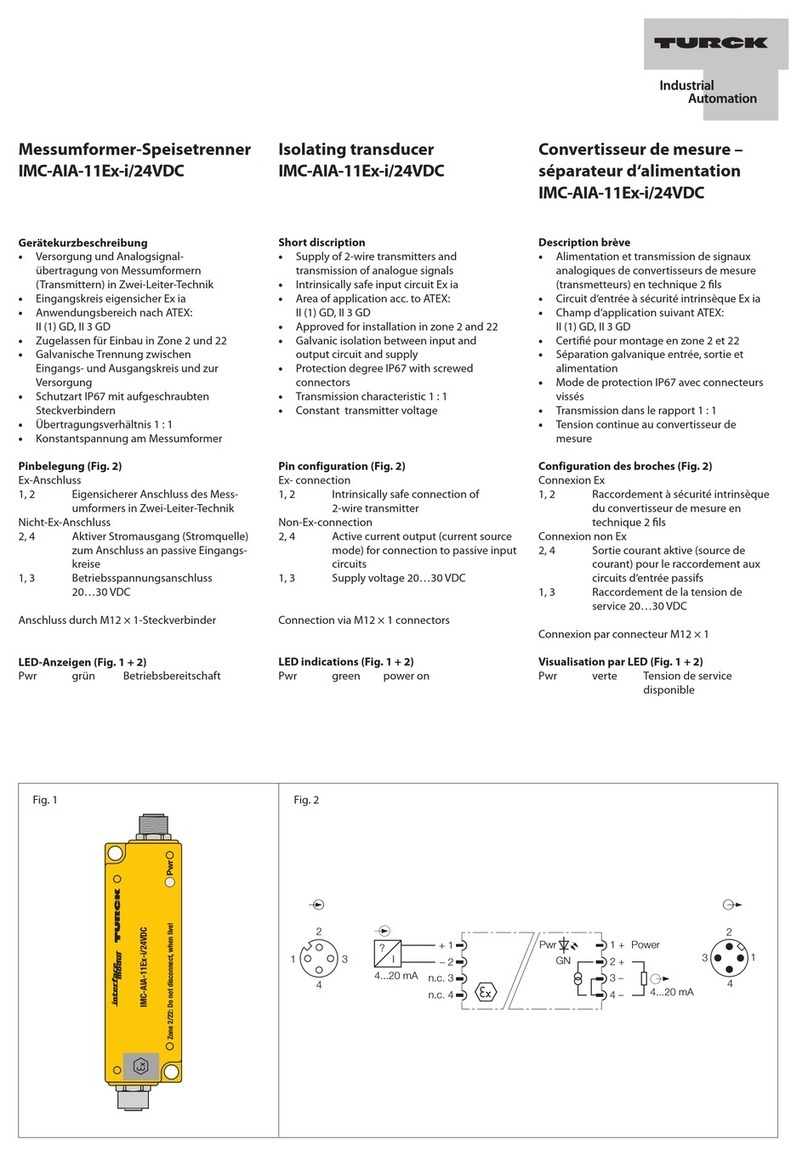
turck
turck interface modul IMC-AIA-11Ex-i/24VDC quick start guide
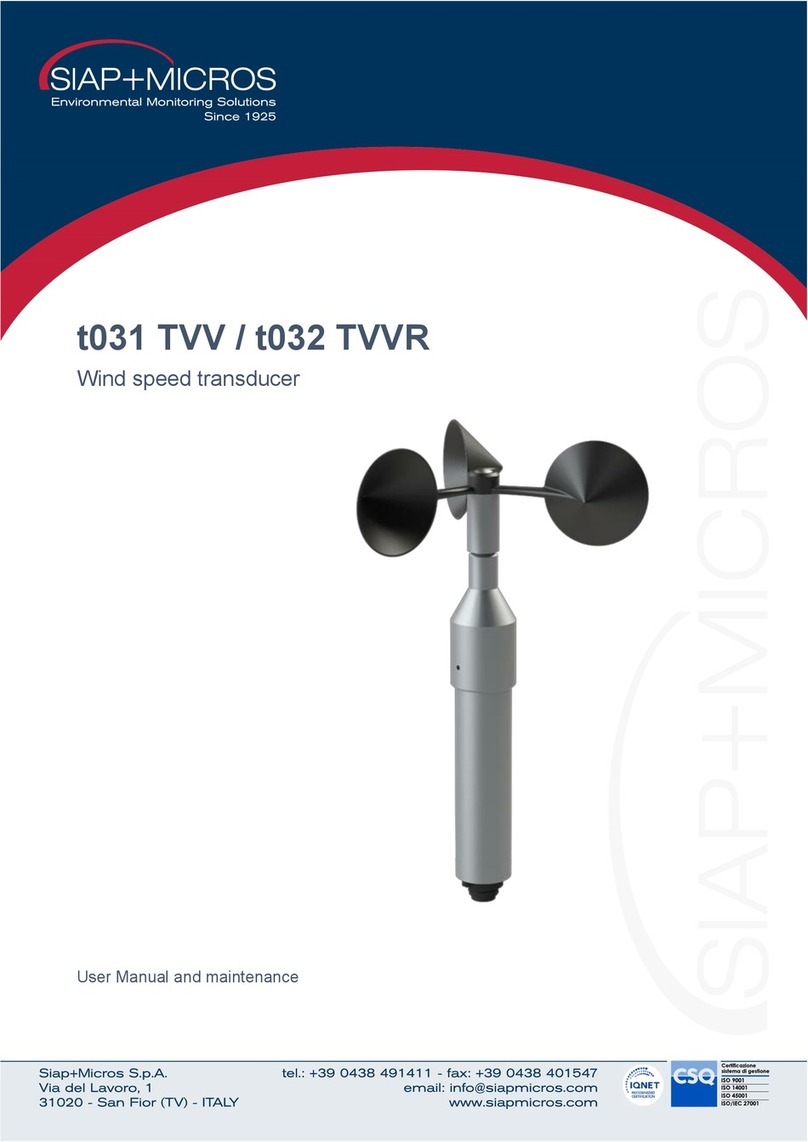
SIAP+MICROS
SIAP+MICROS t031 TVV User manual and maintenance

HBM
HBM Z30A Mounting instructions
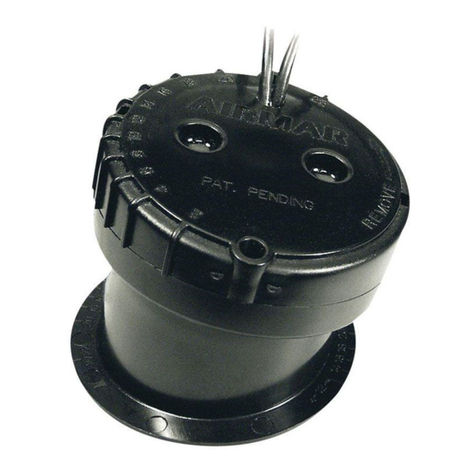
Airmar Technology Corporation
Airmar Technology Corporation P79 quick start guide