Dobot MG400 User manual

Issue: V1.5
Date: 2023-02-20
Shenzhen Yuejiang Technology Co.,Ltd.|China

Dobot MG400 User Guide
Issue V1.5 (2023-03-20)User Guide Copyright © Yuejiang Technology Co., Ltd
i
Copyright © Shenzhen Yuejiang Technology Co., Ltd 2023. All rights reserved.
No part of this document may be reproduced or transmitted in any form or by any means
without the prior written consent of Yuejiang Technology Co., Ltd.
Disclaimer
To the maximum extent permitted by applicable law, the products described (including its
hardware, software, and firmware, etc.) in this document are provided AS IS, which may have flaws,
errors or faults. Dobot makes no warranties of any kind, express or implied, including but not limited
to, merchantability, satisfaction of quality, fitness for a particular purpose and non-infringement of
third party rights. In no event will Dobot be liable for any special, incidental, consequential or
indirect damages resulting from the use of our products and documents.
Before using our product, please thoroughly read and understand the contents of this document
and related technical documents that are published online, to ensure that the robot is used on the
premise of fully understanding the robot and related knowledge. Please use this document with
technical guidance from professionals. Even if follow this document or any other related
instructions, damages or losses will be happening in the using process. Dobot shall not be considered
as a guarantee regarding all security information contained in this document.
The user has the responsibility to make sure of following the relevant practical laws and
regulations of the country, in order that there is no significant danger in the use of the robot.
Shenzhen Yuejiang Technology Co., Ltd
Address: Room 1003, Building 2, Chongwen Garden, Nanshan iPark, Liuxian Blvd, Nanshan
District, Shenzhen, Guangdong Province, China
Website: www.dobot-robots.com

Dobot MG400 User Guide
Issue V1.5 (2023-03-20)User Guide Copyright © Yuejiang Technology Co., Ltd
ii
Preface
Purpose
This document describes the functions, technical specifications and installation procedure of
Dobot MG400 robot, which is convenient for users to understand and use the robot.
Intended Audience
This document is intended for:
Customer
Sales Engineer
Installation and Commissioning Engineer
Technical Support Engineer
Change History
Date
Change Description
2023/03/20
Reconstruct and update the document
2022/03/03
Update the sequence of 3. Electrical Specifications, and modify the motion
range of J4 joint
2021/08/23
Update the end-effector size, and add description on reserved mounting hole
2021/07/26
Add input and output circuit examples in different application scenarios
2021/04/06
Add description on hand-guiding button and diameter of the air interface
2021/02/06
The first releases
Symbol Conventions
The symbols that may be found in this document are defined as follows.
Symbol
Description
DANGER
Indicates a hazard with a high level of risk which, if not avoided, could result
in death or serious injury
WARNING
Indicates a hazard with a medium level or low level of risk which, if not
avoided, could result in minor or moderate injury, robot damage
NOTICE
Indicates a potentially hazardous situation which, if not avoided, can result
in equipment damage, data loss, or unanticipated result
NOTE
Provides additional information to emphasize or supplement important
points in the main text

Dobot MG400 User Guide
Issue V1.5 (2023-03-20)User Guide Copyright © Yuejiang Technology Co., Ltd
iii
Contents
Security Precautions................................................................................................1
Liability.............................................................................................................................1
Validity and Responsibility..................................................................................1
Limitation of Liability .........................................................................................1
Intended Use........................................................................................................1
Safety warning signs.........................................................................................................2
General safety ...................................................................................................................2
Personal safety ..................................................................................................................5
Emergency ........................................................................................................................6
Emergency stop switch........................................................................................6
Emergency recovery............................................................................................6
Forced joint movement........................................................................................6
Transportation .........................................................................................................7
Product Introduction...............................................................................................8
Overview...........................................................................................................................8
Robot base.........................................................................................................................8
End button and interface ...................................................................................................9
Operation terminal ............................................................................................................9
Product Features....................................................................................................10
Coordinate system...........................................................................................................10
Joint coordinate system .....................................................................................10
User coordinate system......................................................................................10
Tool coordinate system......................................................................................11
Home posture..................................................................................................................11
Braking time and braking angle......................................................................................12
Mechanical Specifications .....................................................................................13
Dimensions .....................................................................................................................13
Base installation dimensions...........................................................................................13
End dimensions...............................................................................................................14
Workspace.......................................................................................................................15
Load curve ......................................................................................................................16
Electrical Specifications.........................................................................................18
Base Interface .................................................................................................................18
Interface overview.............................................................................................18
Base I/O interface..............................................................................................19
Tool I/O interface............................................................................................................21
Installation..............................................................................................................22
Installation Environment.................................................................................................22
Unpacking.......................................................................................................................22
Robot Installation............................................................................................................22
Wiring and powering on..................................................................................................23
Maintenance and Repair.......................................................................................25

Dobot MG400 User Guide
Issue V1.5 (2023-03-20)User Guide Copyright © Yuejiang Technology Co., Ltd
iv
Safety Instructions ..........................................................................................................25
Body Maintenance ..........................................................................................................25
Certification............................................................................................................27
Collaborative robot certification .....................................................................................27
Robot reliability certification..........................................................................................28
FCC SDoC certification....................................................................................................1
CE-MD certification .........................................................................................................2
CE-EMC certification .......................................................................................................3
RoHS.................................................................................................................................4
RCM certification .............................................................................................................5
KCs certification ...............................................................................................................6
Warranty ................................................................................................................7
Product warranty...............................................................................................................7
Disclaimer.........................................................................................................................7
Appendix A Technical Specifications......................................................................8
Appendix B I/O Simple Circuit .............................................................................10

Dobot MG400 User Guide
Issue V1.5 (2023-03-20)User Guide Copyright © Yuejiang Technology Co., Ltd
1
Security Precautions
Liability
Validity and Responsibility
The information in this document does not cover designing, installing and operating a complete
robot system, nor does it cover all peripheral equipment that can affect the safety of the complete
system. The complete system must be designed and installed in accordance with the safety
requirements set forth in the standards and regulations of the country where the robot is installed.
The integrators of Dobot are responsible for ensuring that the applicable safety laws and
regulations in the country concerned are observed and that any significant hazards in the complete
robot application are eliminated. This includes, but is not limited to:
• Performing a risk assessment for the complete robot system.
• Adding safety machines and mechanisms based on the risk assessment.
• Setting up the appropriate safety settings in the software.
• Ensuring that the user will not modify any safety measures.
• Validating that the total robot system is designed and installed correctly.
• Specifying instructions for use.
• Marking relevant signs and contact information of the integrators on the robot.
• Archiving relevant technical files.
Limitation of Liability
Any safety information provided in this document should not be construed as a warranty by
Dobot. The robot may cause injury or damage even if all safety instructions are observed.
Intended Use
Dobot MG400 is a collaborative robot only for general industrial use, such as processing or
delivering products or parts through end tools.
Dobot MG400 is equipped with special safety mechanisms including collision detection. These
mechanisms are purposely designed for human-robot collaborative operation, but only intended for
non-hazardous applications after risk assessment, where tools, commodities, environments and
other machines have been demonstrated to be incapable of significant risk through application-
specific risk assessments.
Any use or application deviating from intended use is deemed to be impermissible misuse,
including, but is not limited to:
• Use in potentially explosive environments.
• Use in life critical applications.
• Use before performing a risk assessment.
• Use over-stated specifications.

Dobot MG400 User Guide
Issue V1.5 (2023-03-20)User Guide Copyright © Yuejiang Technology Co., Ltd
2
Safety warning signs
The following safety warning signs may appear in this document, and their meanings are
described as follows.
Sign
Description
DANGER
Indicates a high degree of potential danger, which, if not avoided, will result in death
or serious injury.
ELECTRICITY
May cause dangerous power consumption soon, which, if not avoided, will cause
personal injury or serious damage to the equipment.
HOT
May cause dangerous hot surfaces, which, if touched, may cause personal injury.
WARNING
Indicates a moderate or low potential hazard, which, if not avoided, may cause
minor personal injury and damage to the equipment.
ATTENTION
Indicates a potential risk, which, if ignored, may result in damage to the robot arm,
loss of data or unpredictable results
NOTICE
A situation that, if not avoided, can cause personal injury or damage to the
equipment.
For items marked with such signs, depending on the specific situation, there is
sometimes a possibility of significant consequences
General safety
Follow the safety instructions below when starting and using the robot for the first time.
DANGER
The robot system is electrical equipment. Non-professional technicians should not
modify the circuit, otherwise, it may cause damage to devices or personal injury.
Comply with the local laws and regulations when operating the robot. The security
precautions in this document are only supplemental to the local laws and
regulations.
Use the robot in the specified environment scope. Exceeding the specifications or
load conditions will shorten the service life of the robot, even damage it.
Ensure that the robot is operated under the security conditions and there is no
harmful object around the robot.
Turning on or off the power continually may result in degraded performance of the
main circuit components inside the controller. If turning on or off the power
continually is required, please keep the frequency less than once per minute.

Dobot MG400 User Guide
Issue V1.5 (2023-03-20)User Guide Copyright © Yuejiang Technology Co., Ltd
3
NOTICE
The personnel responsible for installation, operation and maintenance of equipment
must first receive strict training, understand various safety precautions, and master
correct operation and maintenance methods before they can operate and maintain
equipment.
Personnel without professional training shall not disassemble and repair the
equipment without authorization. If the device fails, please contact Dobot technical
support engineer in time.
Be sure to carry out daily inspections and regular maintenance, and replace faulty
components in time to ensure the safe operation of the equipment.
If the equipment is scrapped, please comply with relevant laws to properly handle
industrial waste and protect the environment.
In order to prevent personnel from accidentally entering the working space of the
robot arm, be sure to set up safety fence to prevent personnel from entering the
hazardous area.
Before operating the robot, make sure that no one is inside the safety fence. When
operating the robot, be sure to operate outside the safety fence.
Do not expose the robot to permanent magnetic fields all the time. Strong magnetic
fields can cause damage to the robot.
Dobot assumes no responsibility for robot damage or personal injury caused by
failure to follow product instructions or other improper operations.
Use appropriate and reliable lifting equipment during handling operations such as
lifting rings and bridge crane. According to the relevant regulations of various
countries, it must be carried out by personnel with operating qualification
certificates or personnel authorized by the company.
Make sure that there are no obstacles within 2 meters of the robot during
transportation. Relevant personnel should stay away from the suspended robot.
Dobot is not responsible for any damage caused during the transportation and
handling of equipment.
Make sure that the robot is in the packing posture before packaging, and the brakes
on each axis are normal.
Make sure that there are no obstacles around the packing area, so that the staff can
leave in a timely manner in case of an emergency.
When the robot is transported, the packaging needs to be fixed to ensure that the
robot is stable.
After removing the outer packaging, make sure that the robot maintains the original
packing posture and the brakes of each axis are normal.
During the commissioning process, make sure that no relevant personnel and
equipment (include computer used for debugging) stay in the dangerous area of the
machine.

Dobot MG400 User Guide
Issue V1.5 (2023-03-20)User Guide Copyright © Yuejiang Technology Co., Ltd
4
If necessary, wear corresponding safety protective equipment, such as safety
helmets, safety shoes (with non-slip soles), face shields, protective glasses and
gloves. Inappropriate clothing may cause personal injury.
In order to prevent personnel from entering the working space of the robot arm by
mistake, please set up safety barriers to prevent personnel from entering the
hazardous area.
Do not enter the working space of the manipulator at will during operating the robot,
otherwise cause injury to the robot or yourself.
The personnel responsible for installation, operation, and maintenance of the
equipment must first undergo strict training, understand various safety precautions,
and master the correct operation and maintenance methods before operating and
maintaining the equipment.
When an abnormality occurs in the mechanical arm, it is necessary to ensure that
the machine is stopped and then checked.
After the commissioning of the operator is completed, the test needs to be performed
in the Manual mode first, and then it is automatically run after it is confirmed to be
correct.
If the controller needs to be restarted due to power failure, when restarting, the robot
must be manually returned to the initial position of the automatic operation program
before restarting the automatic operation.
Before maintenance and wiring work, the power supply must be cut off, and the
sign No power supply must be put on. Otherwise, electric shock and personal injury
may result.
Please observe the ESD regulations when disassembling the robot or controller.
Avoid dismantling the power supply system in the controller. After the controller is
turned off, its power supply system may still have high voltage for several hours.
Please contact our technical support staff for the disassembly and repair of the robot.
Maintenance and repair work must be carried out by designated personnel,
otherwise electric shock and personal injury may result.
If the brake is manually released, the robot may move because of the action of
gravity. So, when manually releasing the brake, please ensure that the robot body
and the tools or workpieces installed on the robot are effectively supported.
In order to prevent electric shock, when replacing parts, please turn off the circuit
breaker in advance and cut off the main power before proceeding.
Turn off the main power supply for 5 minutes before replacing parts.
The replacement operation must be performed by the specified operator.
The robot is designed and tested according to the group I class A engineering
medical robot standard. In order to reduce the radio interference in in light industry
or family environment, please take protective measures.
It is prohibited to operate the robot in strong radiation environment (such as RF
source without shielding), otherwise, it could interference robot work.

Dobot MG400 User Guide
Issue V1.5 (2023-03-20)User Guide Copyright © Yuejiang Technology Co., Ltd
5
WARNING
Before the operation, please wear protective clothing, such as antistatic uniform,
protective gloves, and protective shoes.
It is prohibited to modify or remove the nameplates, instructions, icons and marks
on the robot and the related equipment.
Before operating the equipment, please find and be familiar with the operation
method of the emergency stop function to ensure that the robot arm can be stopped
urgently in the case of sudden stress. The emergency stop function is Stop Category
1.
Be careful when carrying or installing the robot. Please follow the instructions on
the packing box to put down the robot gently and place it correctly in the direction
of the arrow.
Please use the matched cables when connecting a robot to internal or external
equipment for personal security and equipment protection.
Please ensure that the robot and tools are installed correctly.
Please ensure that the robot has enough space to move freely.
If the robot is damaged, do not continue to use it.
Any impact will release a lot of kinetic energy, which is much higher than that under
high speed and high load.
Personal safety
When operating the robot system, please strictly follow the general precautions listed below to
ensure the personal safety of the operator.
WARNING
Please comply with local laws or regulations with regard to the maximum weight
one person is permitted to carry.
Do not touch the terminal blocks or disassemble the equipment with the power ON.
Otherwise, it may result in an electric shock.
Please confirm that the equipment is well grounded, otherwise it will endanger
personal safety.
Do not touch the terminal blocks or remove the interval circuit components within
10 minutes after the power is shut off, so as to avoid an electric shock since there is
residual capacitance inside the controller.

Dobot MG400 User Guide
Issue V1.5 (2023-03-20)User Guide Copyright © Yuejiang Technology Co., Ltd
6
Even if the power switch of the controller is already in the OFF status, touching the
terminal blocks or removing the interval circuit components is not allowed, so as to
avoid an electric shock since there is residual capacitance inside the controller.
When working with robots, do not wear loose clothing or jewelry. When operating
the robot, make sure that you have bundle your hair behind your head.
If the robot appears to have stopped during the operation of the equipment, it may
be because the robot is waiting for the start signal and is in the state of being about
to move. In this case, the robot should also be considered to be in motion. Do not
approach the robot.
Emergency
Emergency stop switch
After you press the emergency stop switch in emergencies, the robot will immediately stop all
motions and be locked.
The emergency stop switch is not a safeguard. It is a complimentary protective measure and
are not intended to prevent injury.
Emergency recovery
The emergency stop switch will be locked after you press it. To unlock the switch, you need to
rotate the switch according to the mark on the switch.
WARNING
Please operate the robot to recover from the emergency only after the danger of the robot
system is completely removed.
Forced joint movement
In the unlikely event of an emergency, you may need to move the robot joint(s) when the
robot power is either impossible or unwanted. In this case, you must push or pull the robot arm
hard to move the joint(s).
WARNING
Moving the locked joints forcefully may cause joint damage. Please operate only in
emergencies.

Dobot MG400 User Guide
Issue V1.5 (2023-03-20)User Guide Copyright © Yuejiang Technology Co., Ltd
7
Transportation
The robot should be restored to its packaging posture during transportation, as shown below,
and transported with its original packaging. The robot arm has four joints: J1, J2, J3 and J4, and the
corresponding joint angles of the factory posture are: J1= 0°, J2= 0°, J3= 60°, J4= 0°. You can adjust
the joint angles through jogging or programming. See the corresponding software guide for details.
Figure 2.1 Packaging posture
During transportation, ensure that the robot arm is stable and fixed by corresponding measures.
During transportation and long-term storage, ensure that the ambient temperature ranges from
-20 °C to +55 °C, and the ambient humidity is no more than 95% without condensation.
When moving the robot from its packaging to the installation space, hold the robot arm in place
until all mounting bolts are securely tightened at the base of the robot.
After transportation, store the original package in a dry place for repacking and transporting it
in the future.
WARNING
Ensure that the operator is not unduly stressed on their back or other parts of body
when lifting the equipment, and use appropriate lifting equipment if necessary.
Dobot shall not be held responsible for any damage caused by transportation of the
equipment.
Be sure to follow all installation instructions when installing the robot.

Dobot MG400 User Guide
Issue V1.5 (2023-03-20)User Guide Copyright © Yuejiang Technology Co., Ltd
8
Product Introduction
Overview
MG400 is an ultra-compact desktop robot arm. It is designed integrating the controller and the
robot arm body. The controller is installed in the base. MG400 robot arm includes 4 rotating joints,
and two connecting rods (upper arm and forearm), as shown in Figure 3.1.
Figure 3.1 MG400
Robot base
The base is equipped with core computing and electrical components of MG400. The electrical
interface board is on the back of the base, and a circular indicator light button is on the base, as
described below.
Table 3.1 Indicator light
Color
Status
Definition
White light
Flash
System is starting
Blue light
Steady on
The robot arm has been started but not enabled
Flash
Hand-guiding status
Green light
Steady on
The robot arm is enabled (not running projects)
Flash
Automatic running (project is running)
Red light
Steady on
General alarm

Dobot MG400 User Guide
Issue V1.5 (2023-03-20)User Guide Copyright © Yuejiang Technology Co., Ltd
9
Flash
Position limit alarm
End button and interface
MG400 is equipped with a button and two interfaces on its forearm.
Hand-guiding button: When the robot arm is enabled and not running a program, long
press the button and then you can drag the joints for teaching. After dragging the robot
arm to the teaching point, press the end button again and the joints will be locked (cannot
be dragged). In addition, when the machine is powered normally, this button can also
release the motor brake in emergency stop or other alarm states to rescue trapped people.
NOTE
During the dragging process, you need to hold the robot arm with your hands, otherwise
it may lift or fall slowly.
Tool I/O interface: Aerial socket, which is used to connect the end tool. See 6.2Tool I/O
interface for details.
Air pipe interface: It is connected to the air source interface on the back of the base for
supplying air for the tool. The corresponding diameter of the air pipe is 4mm.
Operation terminal
MG400 robot supports control through PC and App, as shown in Table 3.2. If you need to use
WiFi for control, you need to plug the WiFi module into the controller.
Table 3.2 Operation terminal parameters
Terminal type
PC
Tablet (Android)
iPad
Operation system
Windows7/10/11
Android 10 and above
iOS 10 and above
Control software
DobotStudio Pro
Dobot CRStudio
Dobot CRStudio
Minimum
configuration
CPU: Intel Core i3
Memory: 4GB
Storage space: 256GB
CPU: 4-core
Running memory: 2G
Storage space: 32G
Storage space: 32G
Communication mode
LAN/WiFi
WiFi
WiFi

Dobot MG400 User Guide
Issue V1.5 (2023-03-20)User Guide Copyright © Yuejiang Technology Co., Ltd
10
Product Features
Coordinate system
Joint coordinate system
The joint coordinate system is determined based on all motion joints. All joints are rotating
joints, and the positive rotating direction is shown in Figure 4.1.
Figure 4.1 Joint coordinate system
User coordinate system
The user coordinate system is a movable coordinate system which is used for representing
equipment like fixtures, workbenches. The origin and the orientations of axes can be defined based
on the site requirements to measure point data within the workspace and arrange tasks conveniently.
The default user coordinate system is determined based on the robot base, as shown in Figure 4.2.
X-axis: perpendicular to the base (positive direction: forward).
Y-axis: perpendicular to the base (positive direction: left).
Z axis: vertical upward according to the right-hand rule.

Dobot MG400 User Guide
Issue V1.5 (2023-03-20)User Guide Copyright © Yuejiang Technology Co., Ltd
11
Figure 4.2 User coordinate system
Tool coordinate system
The tool coordinate system defines the tool center point (TCP) and tool posture, of which the
origin and orientations vary with the position and angle of the workpiece at the end of robot. The
default tool coordinate system is determined based on the end of the robot, as shown in Figure 4.3.
Figure 4.3 Tool coordinate system
Home posture
The posture when all joint angles of the robot are 0 degrees is called the home posture, as
shown in Figure 4.4.

Dobot MG400 User Guide
Issue V1.5 (2023-03-20)User Guide Copyright © Yuejiang Technology Co., Ltd
12
Figure 4.4 Home point sticker
If the home point of the robot arm changes due to the replacement of the transmission parts or
the collision, you can calibrate using the calibration block through the control software. See the
corresponding software guide for details.
Braking time and braking angle
When the J1~J4 axes triggers an emergency stop at maximum speed, maximum load and
maximum arm span, the maximum braking angle and braking time of each joint are shown in the
table below.
Table 4.1 Braking time and Braking distance
Axis
Maximum braking angle (°)
Maximum braking time (ms)
J1
63.391
427
J2
16.13
114
J3
17.951
123
J4
22.027
131

Dobot MG400 User Guide
Issue V1.5 (2023-03-20)User Guide Copyright © Yuejiang Technology Co., Ltd
13
Mechanical Specifications
Dimensions
Figure 5.1 MG400 Dimensions
Base installation dimensions

Dobot MG400 User Guide
Issue V1.5 (2023-03-20)User Guide Copyright © Yuejiang Technology Co., Ltd
14
Figure 5.2 Base installation dimensions
End dimensions
Figure 5.3 End flange dimensions

Dobot MG400 User Guide
Issue V1.5 (2023-03-20)User Guide Copyright © Yuejiang Technology Co., Ltd
15
Figure 5.4 End reserved holes
DANGER
Make sure the tools are properly and safely installed in place.
Ensure the safe architecture of tools to prevent accidental fall of any parts.
Workspace
Figure 5.5 shows the workspace of MG400 robot.
NOTICE
When operating the robot, be sure to operate within the workspace.
Other manuals for MG400
1
Table of contents
Other Dobot Robotics manuals
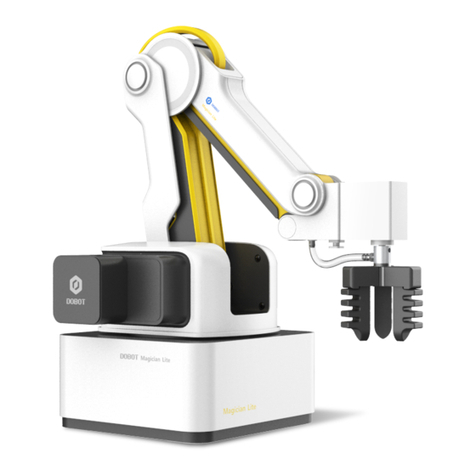
Dobot
Dobot Magician Lite User manual
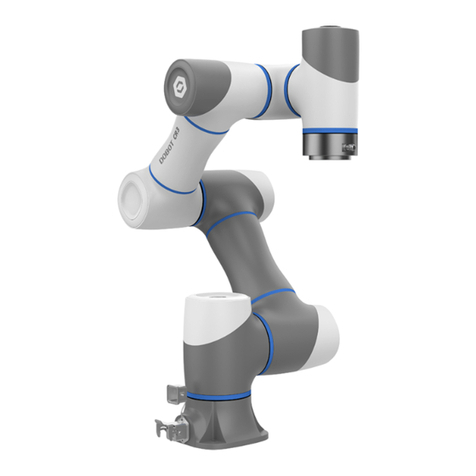
Dobot
Dobot CR3 Installation manual
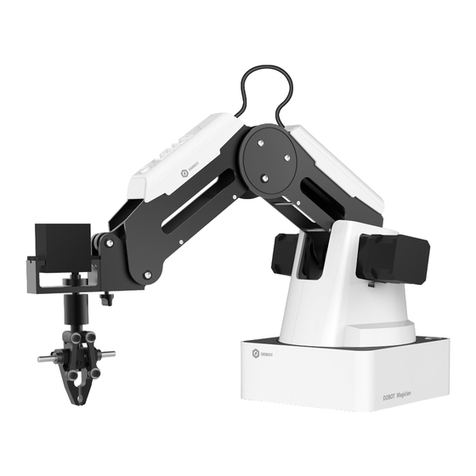
Dobot
Dobot Magician User manual
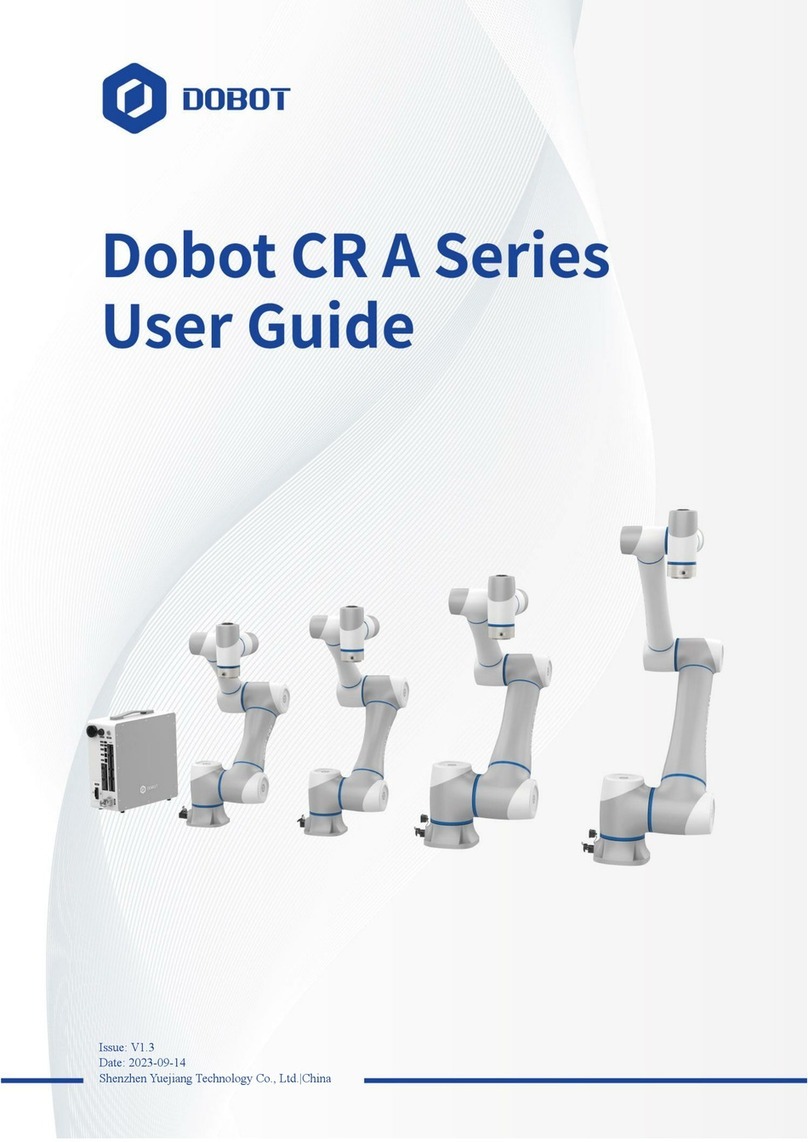
Dobot
Dobot CR A Series User manual
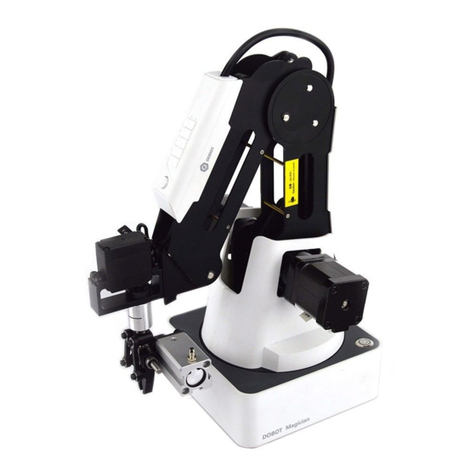
Dobot
Dobot Magician User manual
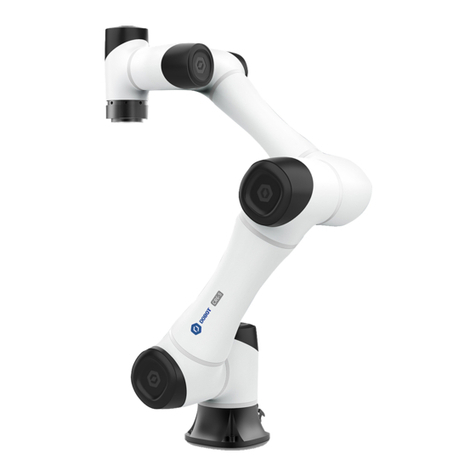
Dobot
Dobot CR5 Installation manual
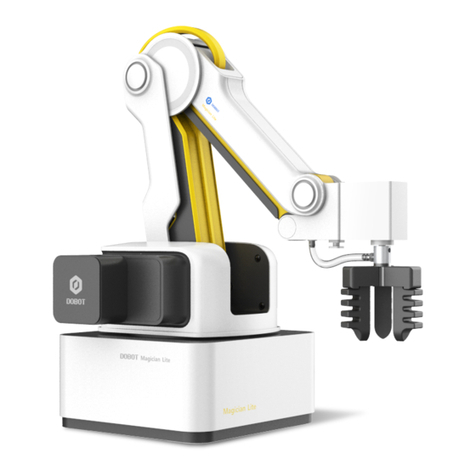
Dobot
Dobot Magician Lite User manual
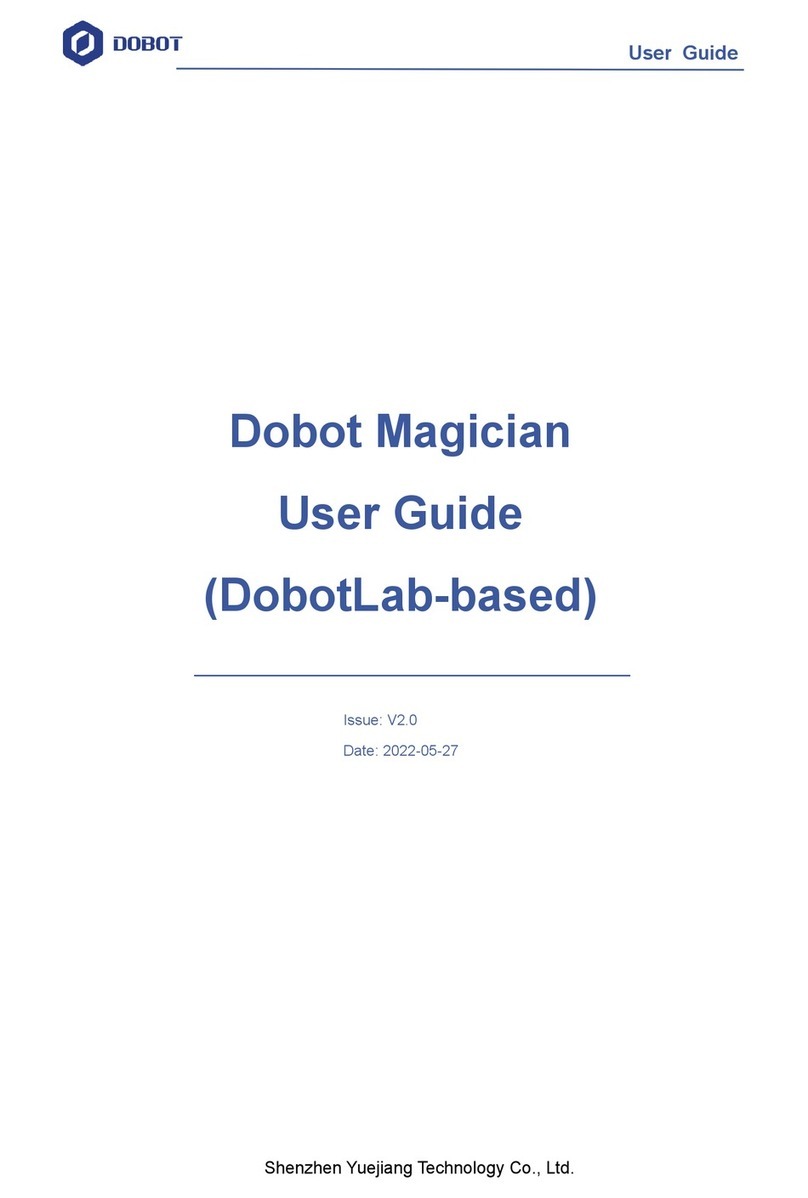
Dobot
Dobot Magician User manual
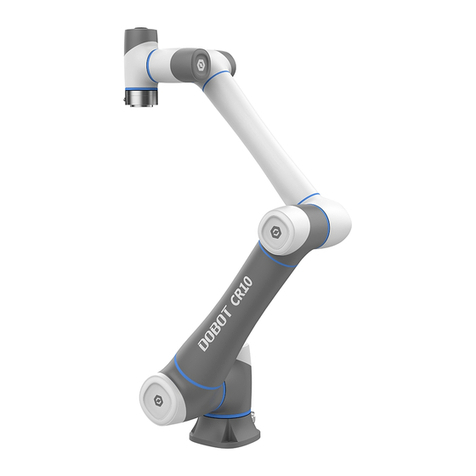
Dobot
Dobot CR 10 Installation manual
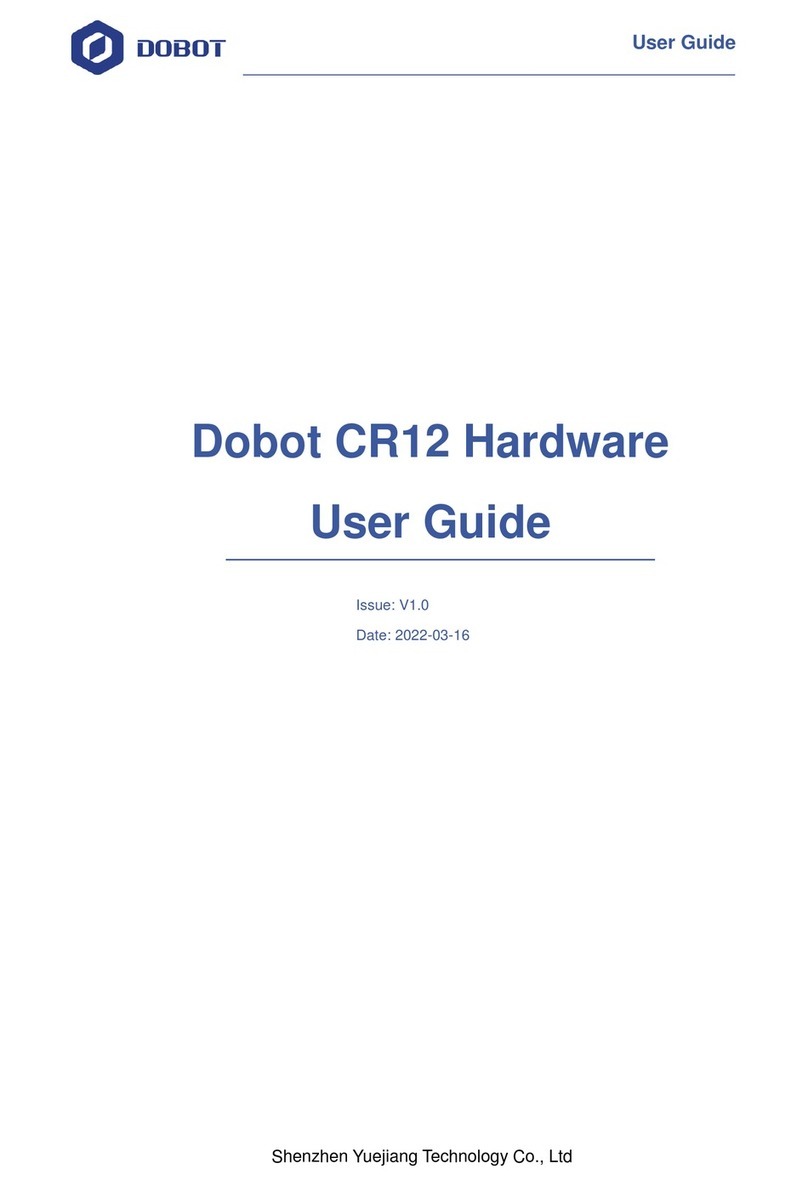
Dobot
Dobot CR12 Installation manual
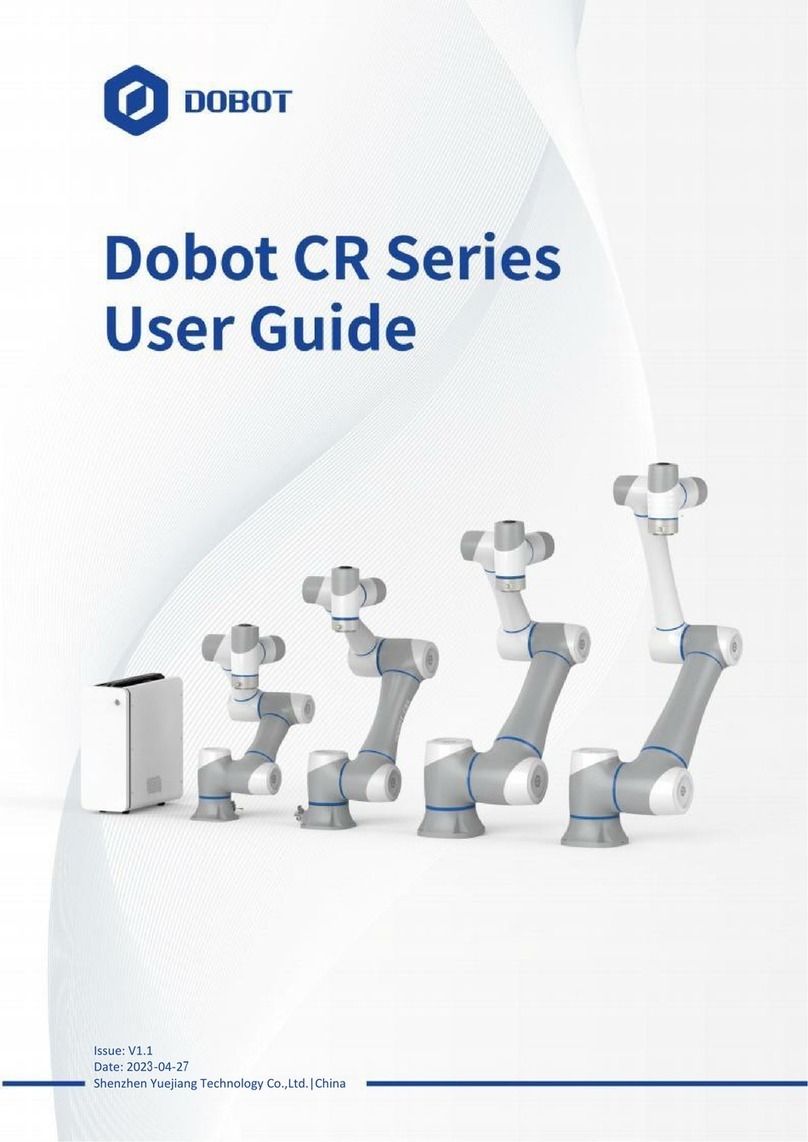
Dobot
Dobot CR Series User manual
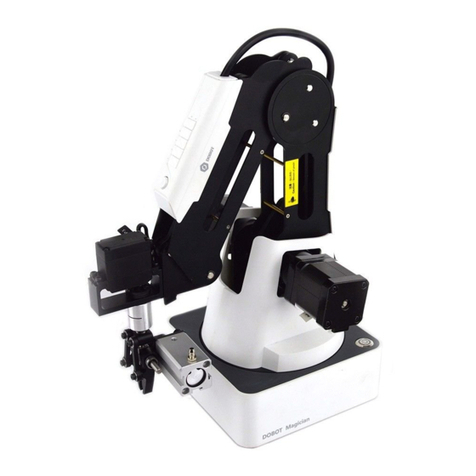
Dobot
Dobot Magician User manual
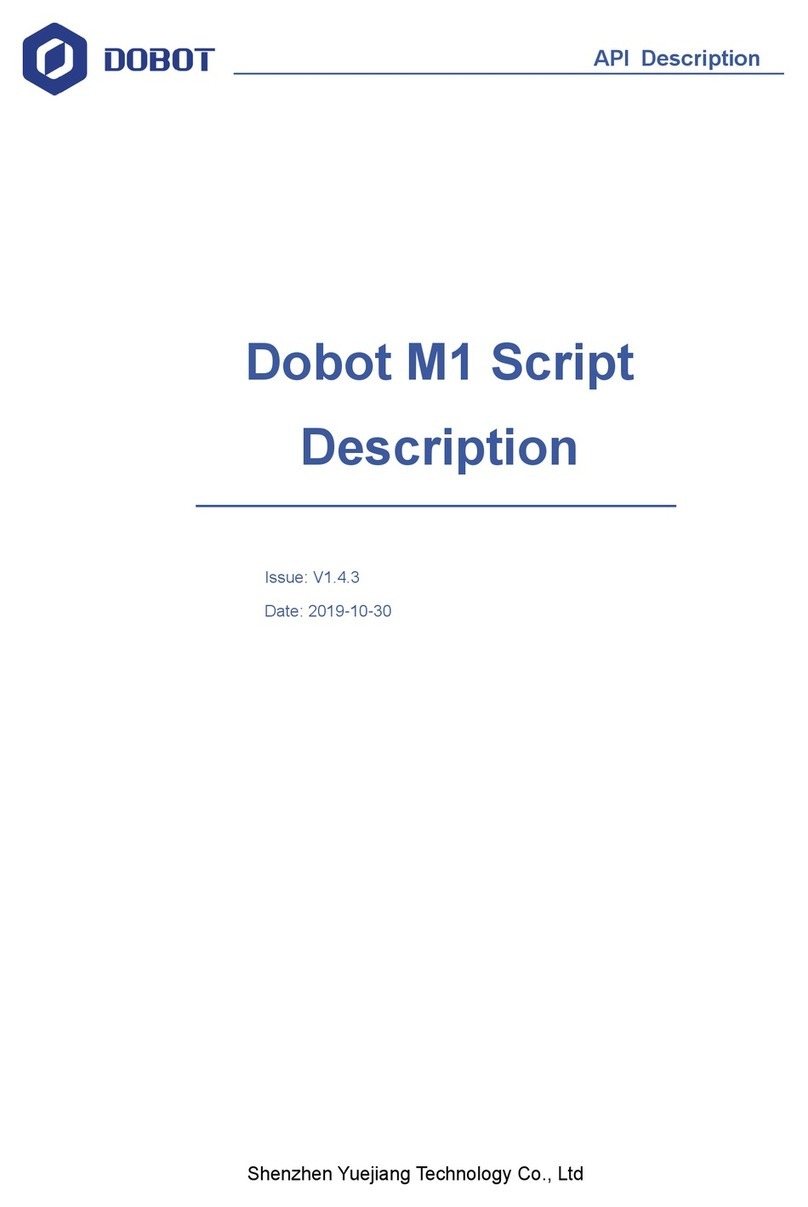
Dobot
Dobot M1 User manual
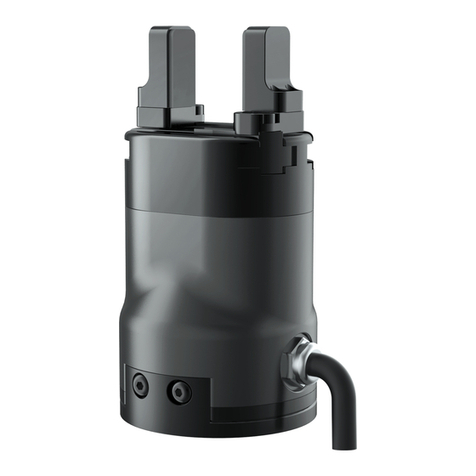
Dobot
Dobot PGC-50 User manual
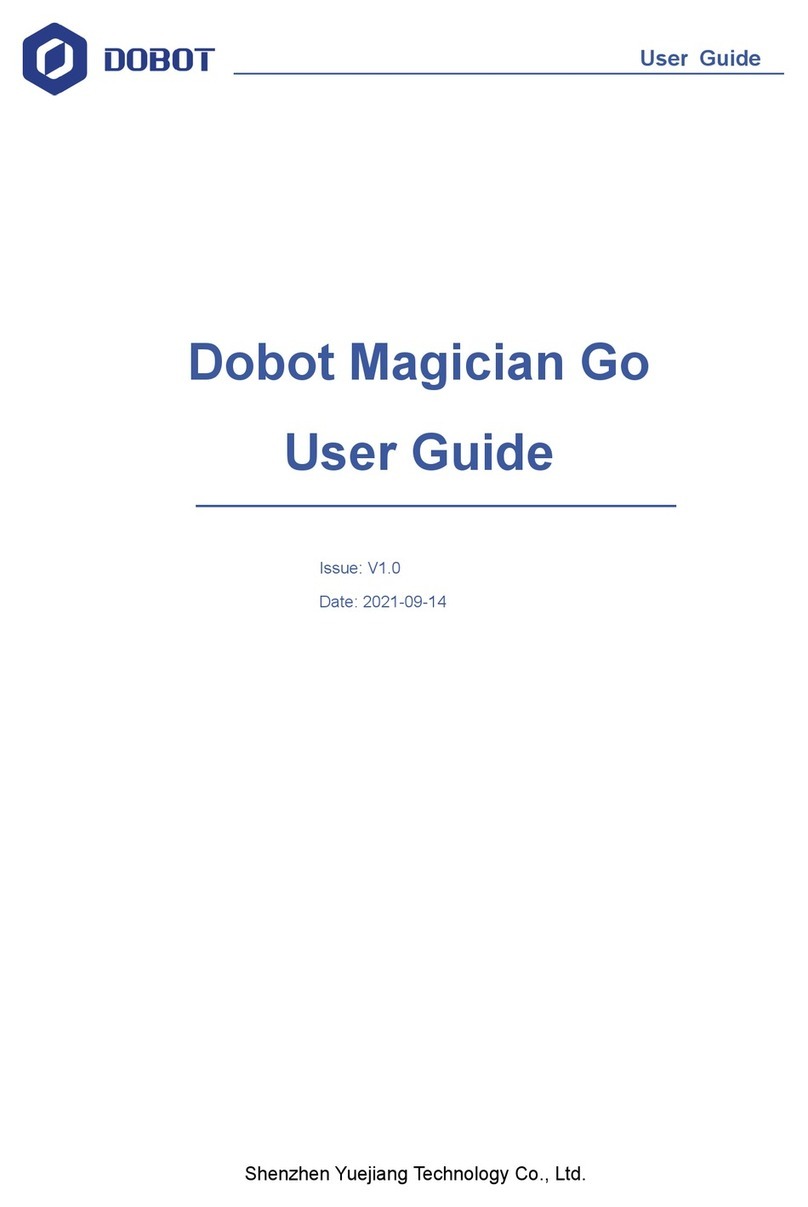
Dobot
Dobot Magician Go DT-AC-GO4WD-01E User manual
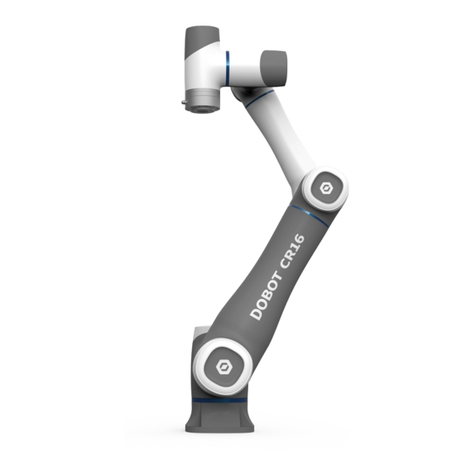
Dobot
Dobot CR16 Installation manual
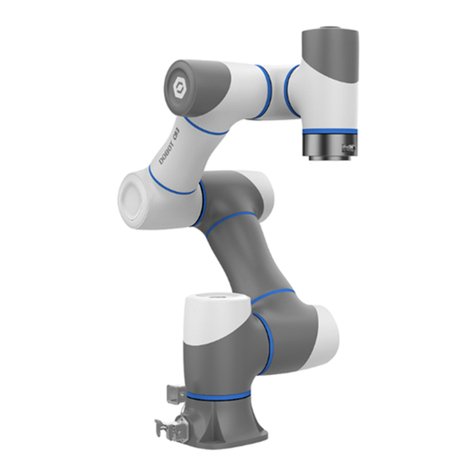
Dobot
Dobot CR Series User manual
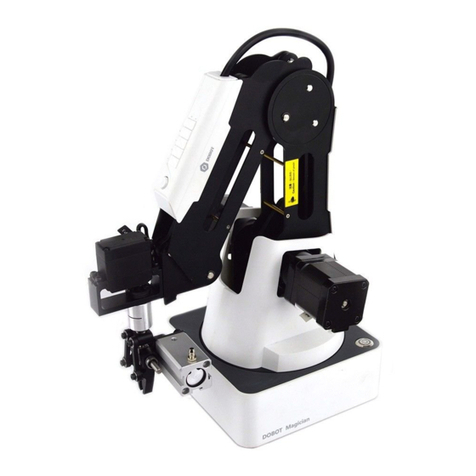
Dobot
Dobot Magician User manual
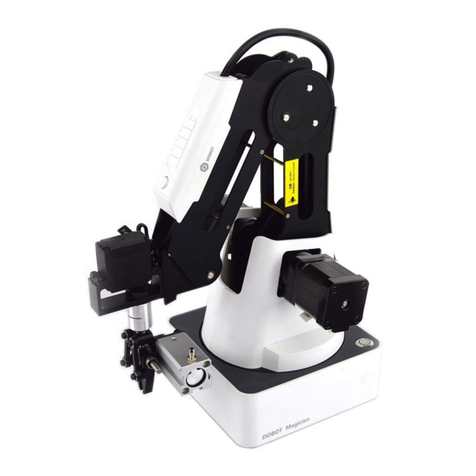
Dobot
Dobot Magician User manual
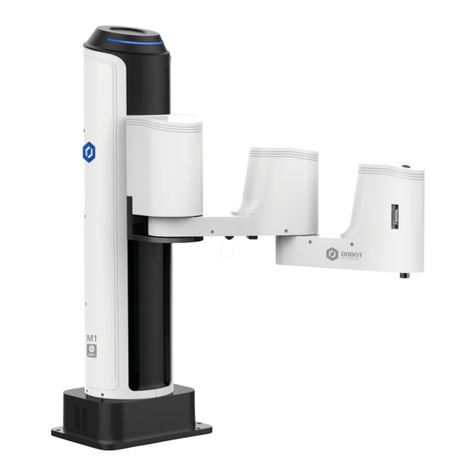
Dobot
Dobot M1 User manual