Fagor CNC 8065elite T User manual

Ref. 2107
8058/8060
8065/8070
CNCelite
Remote modules.
RIO5, RIOW and RIOR series.

BLANK PAGE
ꞏ2ꞏ
MACHINE SAFETY
It is up to the machine manufacturer to make sure that the safety of the machine
is enabled in order to prevent personal injury and damage to the CNC or to the
products connected to it. On start-up and while validating CNC parameters, it
checks the status of the following safety elements. If any of them is disabled, the
CNC shows the following warning message.
• Feedback alarm for analog axes.
• Software limits for analog and sercos linear axes.
• Following error monitoring for analog and sercos axes (except the spindle)
both at the CNC and at the drives.
• Tendency test on analog axes.
FAGOR AUTOMATION shall not be held responsible for any personal injuries or
physical damage caused or suffered by the CNC resulting from any of the safety
elements being disabled.
DUAL-USE PRODUCTS
Products manufactured by FAGOR AUTOMATION since April 1st 2014 will
include "-MDU" in their identification if they are included on the list of dual-use
products according to regulation UE 428/2009 and require an export license
depending on destination.
TRANSLATION OF THE ORIGINAL MANUAL
This manual is a translation of the original manual. This manual, as well as the
documents derived from it, have been drafted in Spanish. In the event of any
contradictions between the document in Spanish and its translations, the wording
in the Spanish version shall prevail. The original manual will be labeled with the
text "ORIGINAL MANUAL".
HARDWARE EXPANSIONS
FAGOR AUTOMATION shall not be held responsible for any personal injuries or
physical damage caused or suffered by the CNC resulting from any hardware
manipulation by personnel unauthorized by Fagor Automation.
If the CNC hardware is modified by personnel unauthorized by Fagor
Automation, it will no longer be under warranty.
COMPUTER VIRUSES
FAGOR AUTOMATION guarantees that the software installed contains no
computer viruses. It is up to the user to keep the unit virus free in order to
guarantee its proper operation. Computer viruses at the CNC may cause it to
malfunction.
FAGOR AUTOMATION shall not be held responsible for any personal injuries or
physical damage caused or suffered by the CNC due a computer virus in the
system.
If a computer virus is found in the system, the unit will no longer be under warranty.
All rights reserved. No part of this documentation may be transmitted,
transcribed, stored in a backup device or translated into another language
without Fagor Automation’s consent. Unauthorized copying or distributing of this
software is prohibited.
The information described in this manual may be subject to changes due to
technical modifications. Fagor Automation reserves the right to change the
contents of this manual without prior notice.
All the trade marks appearing in the manual belong to the corresponding owners.
The use of these marks by third parties for their own purpose could violate the
rights of the owners.
It is possible that CNC can execute more functions than those described in its
associated documentation; however, Fagor Automation does not guarantee the
validity of those applications. Therefore, except under the express permission
from Fagor Automation, any CNC application that is not described in the
documentation must be considered as "impossible". In any case, Fagor
Automation shall not be held responsible for any personal injuries or physical
damage caused or suffered by the CNC if it is used in any way other than as
explained in the related documentation.
The content of this manual and its validity for the product described here has been
verified. Even so, involuntary errors are possible, hence no absolute match is
guaranteed. However, the contents of this document are regularly checked and
updated implementing the necessary corrections in a later edition. We appreciate
your suggestions for improvement.
The examples described in this manual are for learning purposes. Before using
them in industrial applications, they must be properly adapted making sure that
the safety regulations are fully met.

Remote modules. RIO5, RIOW and RIOR series.
CNCelite
8058 8060
8065 8070
ꞏ3ꞏ
REF. 2107
INDEX
About this manual. ........................................................................................................................ 5
About the product. ........................................................................................................................ 7
Declaration of CE conformity and warranty conditions. .............................................................. 13
Safety conditions. ....................................................................................................................... 15
Returning conditions. .................................................................................................................. 19
CNC maintenance. ..................................................................................................................... 21
New features............................................................................................................................... 23
CHAPTER 1 PREVIOUS INFORMATION.
CHAPTER 2 HARDWARE STRUCTURE.
CHAPTER 3 RIO5 REMOTE MODULES. (CANOPEN PROTOCOL).
3.1 Dimensions and mounting of the modules..................................................................... 31
3.2 Power supply. ................................................................................................................ 32
3.2.1 Elements (connectors). .............................................................................................. 34
3.3 Digital inputs and digital outputs (single module)........................................................... 38
3.3.1 Elements (connectors). .............................................................................................. 39
3.4 Digital inputs and digital outputs (double module). ........................................................ 40
3.4.1 Elements (connectors). .............................................................................................. 41
3.5 Electrical characteristics of the inputs and outputs. ....................................................... 42
3.6 Numbering of the digital inputs and outputs................................................................... 43
3.7 Numbering of the analog inputs and outputs and of the temperature sensor inputs. .... 45
CHAPTER 4 RIOW REMOTE MODULES. (CANOPEN PROTOCOL).
4.1 Dimensions of the modules............................................................................................ 48
4.2 Technical and electrical characteristics. ........................................................................ 49
4.2.1 Technical characteristics............................................................................................ 49
4.2.2 Electrical characteristics of the inputs and outputs. ................................................... 51
4.3 Sizing of the remote groups. .......................................................................................... 53
4.4 Installation of the modules. ........................................................................................... 55
4.5 RIOW-CANOPEN-STAND module. Leading (first) module. .......................................... 58
4.5.1 Elements (connectors). .............................................................................................. 59
4.5.2 Voltage supply for the module.................................................................................... 61
4.5.3 Node configuration. .................................................................................................... 62
4.5.4 Meaning of the LED's. ................................................................................................ 64
4.6 RIOW-PS24 module. ..................................................................................................... 68
4.6.1 Elements (connectors). .............................................................................................. 69
4.7 RIOW-8DI module. Module of 8 digital inputs................................................................ 70
4.7.1 Elements (connectors). .............................................................................................. 71
4.8 RIOW-8DO module. Module of 8 digital outputs............................................................ 72
4.8.1 Elements (connectors). .............................................................................................. 73
4.9 RIOW-4AI module. Module of 4 analog inputs............................................................... 74
4.9.1 Elements (connectors). .............................................................................................. 75
4.10 RIOW-4AO module. Module of 4 analog outputs........................................................... 76
4.10.1 Elements (connectors). .............................................................................................. 77
4.11 RIOW-2AI-PT100 module. Module of 2 inputs for PT100 temperature sensors............ 78
4.11.1 Elements (connectors). .............................................................................................. 79
4.12 RIOW-END module. Last module of the group.............................................................. 80
4.13 Numbering of the digital inputs and outputs................................................................... 81
4.14 Numbering of the analog inputs and outputs and of the temperature sensor inputs. .... 83
CHAPTER 5 RIOR-E-48I32O / RIOR-E-48I32O-ANALOG (CANOPEN).
5.1 Dimensions and mounting of the module....................................................................... 87
5.2 Powering the modules. .................................................................................................. 89
5.3 Electrical characteristics of the inputs and outputs. ....................................................... 90
5.4 Description of connectors. ............................................................................................. 92
5.5 CAN bus connection. ..................................................................................................... 97
5.6 Connection of the digital inputs and outputs. ................................................................. 98
5.7 Connection of the analog inputs/outputs and the PT100 inputs. ................................... 99

Remote modules. RIO5, RIOW and RIOR series.
CNCelite
8058 8060
8065 8070
ꞏ4ꞏ
REF. 2107
CHAPTER 6 RIOR-E-48I32O / RIOR-E-48I32O-ANALOG (ETHERCAT).
6.1 Specifications............................................................................................................... 102
6.1.1 Conditions of acceptabity for NRTL certification. ..................................................... 104
6.2 Dimensions. ................................................................................................................. 105
6.3 Enclosure and securing of the modules....................................................................... 106
6.3.1 Ambient characteristics of the cabinet. .................................................................... 106
6.3.2 Cabinet design. ........................................................................................................ 106
6.3.3 Securing the module. ............................................................................................... 106
6.4 Power supply for the module. ................................................................................... 107
6.4.1 Voltage supply at 24 V DC....................................................................................... 107
6.4.2 Protection against over-voltage and reverse voltage............................................... 107
6.4.3 External power supply requirements........................................................................ 108
6.5 Hardware functionality. Connectors............................................................................. 109
6.6 Technical/electrical characteristics of the inputs and outputs...................................... 113
6.7 Connections. ............................................................................................................... 115
6.7.1 Ground connection................................................................................................... 115
6.7.2 EtherCAT bus connection. ....................................................................................... 115
6.7.3 Connection of the digital inputs and outputs. ........................................................... 117
6.7.4 Connection of the analog inputs/outputs and the PT100 inputs. ............................. 118
CHAPTER 7 CAN BUS (CANOPEN PROTOCOL).
7.1 Identification of the modules at the bus. ...................................................................... 121
7.2 Selecting the baudrate for the CANopen bus. ............................................................. 123

Remote modules. RIO5, RIOW and RIOR series.
CNCelite
8058 8060
8065 8070
ꞏ5ꞏ
REF. 2107
ABOUT THIS MANUAL.
Title. Remote modules.
Models. CNCelite
8058 8060
8065 8070
Type of documentation. OEM manual. This manual describes the available remote modules;
models, dimensions, connectors, etc.
Remarks.
Always use the manual reference associated with the software version
or a later manual reference. You can download the latest manual
reference from the download section on our website.
Limitations.
The availability of some of the features described in this manual are
dependent on the acquired software options. Moreover, the machine
manufacturer (OEM) customizes the CNC performance of each
machine using the machine parameters and the PLC. Because of this,
the manual may describe features that are not available for the CNC
or the machine. Consult the machine manufacturer for the available
features.
Electronic document. man_elite_58_60_65_70_rios.pdf. Manual available from the
download section of our website.
Language. English [EN]. Refer to our website, download area, the languages
available for each manual.
Date of publication. July, 2021
Manual reference Ref. 2107
Associated version. v2.00.01
Responsibility exemption. The information described in this manual may be subject to changes
due to technical modifications. Fagor Automation reserves the right to
change the contents of this manual without prior notice.
Trademarks. This manual may contain third-party trademarks or trade names,
however, they do not have them associated ® or ™ symbols. All the
trade marks appearing in the manual belong to the corresponding
owners. The use of these marks by third parties for their own purpose
could violate the rights of the owners.
Website / Email. http://www.fagorautomation.com
Email: [email protected]

Remote modules. RIO5, RIOW and RIOR series.
CNCelite
8058 8060
8065 8070
ꞏ6ꞏ
REF. 2107

Remote modules. RIO5, RIOW and RIOR series.
CNCelite
8058 8060
8065 8070
ꞏ7ꞏ
REF. 2107
SOFTWARE OPTIONS.
Some of the features described in this manual are dependent on the acquired software options. The active
software options for the CNC can be consulted in the diagnostics mode (accessible from the task window
by pressing [CTRL] [A]), under software options. Consult Fagor Automation regarding the software options
available for your model.
About the product.
Software option Description.
SOFT ADDIT AXES Option to add axes to the default configuration.
SOFT ADDIT SPINDLES Option to add spindles to the default configuration.
SOFT ADDIT TOOL MAGAZ Option to add magazines to the default configuration.
SOFT ADDIT CHANNELS Option to add channels to the default configuration.
SOFT 4 AXES INTERPOLATION LIMIT Limited to 4 interpolated axes.
SOFT DIGITAL SERCOS Option for a Sercos digital bus.
SOFT THIRD PARTY DRIVES Option to use EtherCAT third party drives.
SOFT THIRD PARTY I/Os Option to use third party I/O modules.
SOFT OPEN SYSTEM Option for open systems. The CNC is a closed system that
offers all the features needed to machine parts.
Nevertheless, at times there are some customers who use
third-party applications to take measurements, perform
statistics or other tasks apart from machining a part.
This feature must be active when installing this type of
application, even if they are Office files. Once the
application has been installed, it is recommended to close
the CNC in order to prevent the operators from installing
other kinds of applications that could slow the system
down and affect the machining operations.

Remote modules. RIO5, RIOW and RIOR series.
CNCelite
8058 8060
8065 8070
ꞏ8ꞏ
REF. 2107
SOFT i4.0 CONNECTIVITY PACK Options for Industry 4.0 connectivity. This option provides
various data exchange standards (for example, OPC UA),
which allows the CNC (and therefore the machine tool) to
be integrated into a data acquisition network or into a MES
or SCADA system.
SOFT EDIT/SIMUL Option to enable edisimu mode (edition and simulation)
on the CNC, which can edit, modify and simulate part
programs.
SOFT DUAL-PURPOSE (M-T) Option to enable the dual-purpose machine, which allows
milling and turning cycles. On Y-axis lathes, this option
allows for pockets, bosses and even irregular pockets with
islands to be made during milling cycles. On a C-axis mill,
this option allows turning cycles to be used.
SOFT TOOL RADIUS COMP Option to enable radius compensation. This
compensation programs the contour to be machined
based on part dimensions without taking into account the
dimensions of the tool that will be used later on. This
avoids having to calculate and define the tool paths based
on the tool radius.
SOFT PROFILE EDITOR Option to enable the profile editor in edisimu mode and in
the cycle editor. This editor can graphically, and in a
guided way, define rectangular, circular profiles or any
profile made up of straight and circular sections an it can
also import dxf files. After defining the profile, the CNC
generates the required blocks and add them to the
program.
SOFT HD GRAPHICS
In a multi-channel system, this feature requires the MP-
PLUS (83700201) processor.
High definition solid 3D graphics for the execution and
simulation of part-programs and canned cycles of the
editor. During machining, the HD graphics display, in real
time, the tool removing the material from the part, allowing
the condition of the part to be seen at all times. These
graphics are required for the collision control (FCAS).
SOFT IIP CONVERSATIONAL The IIP (Interactive Icon-based Pages) mode, or
conversational mode, works with the CNC in a graphical
and guided way based on predefined cycles.
There is no
need to work with part programs, have any previous
programming knowledge or be familiar with Fagor CNCs.
Working in conversational mode is easier than in ISO
mode, as it ensures proper data entry and minimizes the
number of operations to be defined.
SOFT RTCP
This feature requires the MP-PLUS (83700201)
processor.
Option to enable dynamic RTCP (Rotating Tool Center
Point) required to machine with 4, 5 and 6 axis kinematics;
for example, angular and orthogonal spindles, tilting
tables, etc. The RTCP orientation of the tool may be
changed without modifying the position occupied by the
tool tip on the part.
SOFT C AXIS Option to enable C-axis kinematics and associated
canned cycles. The machine parameters of each axis or
spindle indicate whether it can operate as a C axis or not.
For this reason, it is not necessary to add specific axes to
the configuration.
SOFT Y AXIS Option to enable lathe Y-axis kinematics and associated
canned cycles.
SOFT TANDEM AXES Option to enable tandem axle control. A tandem axis
consists of two motors mechanically coupled to each
other forming a single transmission system (axis or
spindle). A tandem axis helps provide the necessary
torque to move an axis when a single motor is not capable
of supplying enough torque to do it.
When activating this feature, it should be kept in mind that
for each tandem axis of the machine, another axis must
be added to the entire configuration. For example, on a
large 3-axis lathe (X Z and tailstock), if the tailstock is a
tandem axis, the final purchase order for the machine
must indicate 4 axes.
Software option Description.

Remote modules. RIO5, RIOW and RIOR series.
CNCelite
8058 8060
8065 8070
ꞏ9ꞏ
REF. 2107
SOFT SYNCHRONISM Option to enable the synchronization of paired axes and
spindles, in speed or position, and through a given ratio.
SOFT KINEMATIC CALIBRATION Option to enable tool calibration. For the first time, this
kinematics calibration allows for the kinematics offsets to
be calculated using various approximate data and, also,
from time to time to correct any possible deviations
caused by day-to-day machining operations.
SOFT 60 HSSA I MACHINING SYSTEM Option to enable the HSSA-I (High Speed Surface
Accuracy) algorithm for high speed machining (HSC).
This new HSSA algorithm allows for high speed
machining optimization, where higher cutting speeds,
smoother contours, a better surface finishing and greater
precision are achieved.
SOFT HSSA II MACHINING SYSTEM Option to enable the HSSA-II (High Speed Surface
Accuracy) algorithm for high speed machining (HSC).
This new HSSA algorithm allows for high speed
machining optimization, where higher cutting speeds,
smoother contours, a better surface finishing and greater
precision are achieved. The HSSA-II algorithm has the
following advantages compared to the HSSA-I algorithm.
• Advanced algorithm for point preprocessing in real
time.
• Extended curvature algorithm with dynamic
limitations. Improved acceleration and jerk control.
• Greater number of pre-processed points.
• Filters to smooth out the dynamic machine behavior.
SOFT TANGENTIAL CONTROL Option to enable tangential control. "Tangential Control"
maintains a rotary axis always in the same orientation with
respect to the programmed tool path. The machining path
is defined on the axes of the active plane and the CNC
maintains the orientation of the rotary axis along the entire
tool path.
SOFT PROBE Option to enable functions G100, G103 and G104 (for
probe movements) and probe canned cycles (which help
to measure part surfaces and to calibrate tools). For the
laser model, it only activates the non-cycle function G100.
The CNC may have two probes; usually a tabletop probe
to calibrate tools and a measuring probe to measure the
part.
SOFT FVC STANDARD
SOFT FVC UP TO 10m3
SOFT FVC MORE TO 10m3
Options to enable volumetric compensation. The
precision of the parts is limited by the machine
manufacturing tolerances, wear, the effect of
temperature, etc., especially on 5-axis machines.
Volumetric compensation corrects these geometric errors
to a larger extent, thus improving the precision of the
positioning. The volume to be compensated is defined by
a point cloud and for each point the
error to be corrected is measured. When mapping the total
work volume of the machine, the CNC knows the exact
position of the tool at all times.
There are 3 options, which depend on the size of the
machine.
• FVC STANDARD: Compensation for 15625 points
(maximum 1000 points per axis). Quick calibration
(time), but less precise than the other two, but
sufficient for the desired tolerances.
• FVC UP TO 10m3: Volume compensation up to 10 m³.
More accurate than FVC STANDARD, but requires a
more accurate calibration using a Tracer or Tracker
laser).
• FVC MORE TO 10m3: Volume compensation greater
than 10 m³. More accurate than FVC STANDARD, but
requires a more accurate calibration using a Tracer or
Tracker laser.
Software option Description.

Remote modules. RIO5, RIOW and RIOR series.
CNCelite
8058 8060
8065 8070
ꞏ10ꞏ
REF. 2107
SOFT CONV USER CYCLES Option to enable user conversational cycles. The user and
the OEM can add their own canned cycles (user cycles)
using the FGUIM application that comes installed on the
CNC. The application offers a guided way to define a new
component and its softkey menu without having to be
familiar with script languages. User cycles work in a
similar way as Fagor canned cycles.
SOFT PROGTL3 Option to enable the ProGTL3 programming language
(ISO language extension), allowing profiles to be
programmed using a geometric language and without the
need to use an external CAD system. This language can
program lines and circles where the end point is defined
as the intersection of 2 other sections, pockets, ruled
surfaces, etc.
SOFT PPTRANS Option to enable the program translator, which can
convert programs written in other languages to Fagor ISO
code.
SOFT DMC Option to enable the DMC (Dynamic Machining Control).
DMC adapts the feedrate during machining to maintain
the cutting power as close as possible to ideal machining
conditions.
SOFT FMC Option to enable the FMC (Fagor Machining Calculator).
The FMC application consists of a database of materials
to be machined and machining operations, with an
interface to choose suitable cutting conditions for these
operations.
SOFT FFC Option to enable the FFC (Fagor Feed Control). During
the execution of a canned cycle of the editor, the FFC
function makes it possible to replace the feedrate and
speed programmed in the cycle with the active values of
the execution, which are acted upon by the feed override
and speed override.
SOFT 60/65/70 OPERATING TERMS Option to enable a temporary user license for the CNC,
which is valid until the date set by the OEM. While the
license is valid, the CNC will be fully operational
(according to the purchased software options).
SOFT FCAS Option to enable the FCAS (Fagor Collision Avoidance
System). The FCAS option, within the system limitations,
monitors the automatic, MDI/MDA, manual and tool
inspection movements in real time, so as to avoid
collisions between the tool and the machine. The FCAS
option requires that the HD graphics to be active and that
there is a defined a model configuration of the machine
adjusted to reality (.xca file), which includes all its moving
parts.
SOFT GENERATE ISO CODE ISO generation converts canned cycles, calls to
subroutines, loops, etc. into their equivalent ISO code (G,
F, S, etc functions), so the user can modify it and adapt it
to his needs (eliminate unwanted movements, etc.). The
CNC generates the new ISO code while simulating the
program, either from the DISIMU mode or from the
conversational mode.
SOFT PWM CONTROL Option to enable PWM (Pulse - Width Modulation) control
on laser machines. This feature is essential for cutting
very thick sheets, where the CNC must create a series of
PWM pulses to control laser power when drilling the initial
point.
This function is only available for Sercos bus control
systems and must also use one of the two fast digital
outputs available from the central unit.
SOFT GAP CONTROL Option to enable gap control, which makes it possible to
set a fixed distance between the laser nozzle and the
sheet surface with the use of a sensor. The CNC
compensates the difference between the distance
measured by the sensor and the programmed distance
with additional movements on the axis programmed for
the gap.
Software option Description.

Remote modules. RIO5, RIOW and RIOR series.
CNCelite
8058 8060
8065 8070
ꞏ11ꞏ
REF. 2107
SOFT MANUAL NESTING Option to enable nesting in the automatic option. Nesting
consists of creating a pattern on the sheet material using
previously defined figures (in dxf, dwg or parametric files),
so as to use most of the sheet as possible. Once the
pattern has been defined, the CNC creates a program.
During manual nesting, the operator distributes the parts
on top of the sheet material.
SOFT AUTO NESTING Option to enable nesting in the automatic option. Nesting
consists of creating a pattern on the sheet material using
previously defined figures (in dxf, dwg or parametric files),
so as to use most of the sheet as possible. Once the
pattern has been defined, the CNC creates a program.
During automatic nesting, the application distributes the
figures on the sheet material and optimizes the spaces.
SOFT DRILL CYCL OL Option to enable ISO drilling cycles (G80, G81, G82,
G83).
Software option Description.

Remote modules. RIO5, RIOW and RIOR series.
CNCelite
8058 8060
8065 8070
ꞏ12ꞏ
REF. 2107

Remote modules. RIO5, RIOW and RIOR series.
CNCelite
8058 8060
8065 8070
ꞏ13ꞏ
REF. 2107
DECLARATION OF CONFORMITY
The declaration of conformity is available from the downloads section of the Fagor Automation corporate
website.
https://www.fagorautomation.com/en/downloads/
Type of file: Declaration of conformity.
WARRANTY TERMS
The sales and warranty conditions are available from the downloads section of the Fagor Automation
corporate website.
https://www.fagorautomation.com/en/downloads/
Type of file: General sales - warranty conditions.
DECLARATION OF CE CONFORMITY AND
WARRANTY CONDITIONS.

Remote modules. RIO5, RIOW and RIOR series.
CNCelite
8058 8060
8065 8070
ꞏ14ꞏ
REF. 2107

Remote modules. RIO5, RIOW and RIOR series.
CNCelite
8058 8060
8065 8070
ꞏ15ꞏ
REF. 2107
Read the following safety measures in order to prevent harming people or damage to this product and those
products connected to it. Fagor Automation shall not be held responsible of any physical or material damage
originated from not complying with these basic safety rules.
PRECAUTIONS BEFORE CLEANING THE UNIT
PRECAUTIONS DURING REPAIRS
In case of a malfunction or failure, disconnect it and call the technical service.
PRECAUTIONS AGAINST PERSONAL HARM
SAFETY CONDITIONS.
Before start-up, verify that the machine that integrates this CNC meets the 2006/42/EC Directive.
Do not get into the inside of the unit. Only personnel authorized by Fagor Automation may access the
interior of this unit.
Do not handle the connectors with the unit
connected to AC power.
Before handling these connectors (I/O, feedback, etc.), make sure
that the unit is not powered.
Do not get into the inside of the unit. Only personnel authorized by Fagor Automation may access the
interior of this unit.
Do not handle the connectors with the unit
connected to AC power.
Before handling these connectors (I/O, feedback, etc.), make sure
that the unit is not powered.
Interconnection of modules. Use the connection cables provided with the unit.
Use proper cables. To prevent risks, only use cables and Sercos fiber recommended for
this unit.
To prevent a risk of electrical shock at the central unit, use the proper
connector (supplied by Fagor); use a three-prong power cable (one
of them being ground).
Avoid electric shocks. To prevent electrical shock and fire risk, do not apply electrical voltage
out of the indicated range.
Ground connection. In order to avoid electrical discharges, connect the ground terminals
of all the modules to the main ground terminal. Also, before
connecting the inputs and outputs of this product, make sure that the
ground connection has been done.
In order to avoid electrical shock, before turning the unit on verify that
the ground connection is properly made.
Do not work in humid environments. In order to avoid electrical discharges, always work with a relative
humidity (non-condensing).
Do not work in explosive environments. In order to avoid risks, harm or damages, do not work in explosive
environments.

Remote modules. RIO5, RIOW and RIOR series.
CNCelite
8058 8060
8065 8070
ꞏ16ꞏ
REF. 2107
PRECAUTIONS AGAINST DAMAGE TO THE PRODUCT
SAFETY SYMBOLS
Symbols that may appear in the manual.
Work environment. This unit is ready to be used in industrial environments complying with
the directives and regulations effective in the European Community.
Fagor Automation shall not be held responsible for any damage
suffered or caused by the CNC when installed in other environments
(residential, homes, etc.).
Install this unit in the proper place. It is recommended, whenever possible, to install the CNC away from
coolants, chemical product, blows, etc. that could damage it.
This unit meets the European directives on electromagnetic
compatibility. Nevertheless, it is recommended to keep it away from
sources of electromagnetic disturbance such as:
Powerful loads connected to the same mains as the unit.
Nearby portable transmitters (radio-telephones, Ham radio
transmitters).
Nearby radio / TC transmitters.
Nearby arc welding machines.
Nearby high voltage lines.
Enclosures. It is up to the manufacturer to guarantee that the enclosure where the
unit has been installed meets all the relevant directives of the
European Union.
Avoid disturbances coming from the
machine.
The machine must have all the interference generating elements
(relay coils, contactors, motors, etc.) uncoupled.
Use the proper power supply. Use an external regulated 24 Vdc power supply for the keyboard,
operator panel and the remote modules.
Connecting the power supply to ground. The zero Volt point of the external power supply must be connected
to the main ground point of the machine.
Analog inputs and outputs connection. Use shielded cables connecting all their meshes to the corresponding
pin.
Ambient conditions. Maintain the CNC within the recommended temperature range, both
when running and not running. See the corresponding chapter in the
hardware manual.
Central unit enclosure. To maintain the right ambient conditions in the enclosure of the central
unit, it must meet the requirements indicated by Fagor. See the
corresponding chapter in the hardware manual.
Power switch. This switch must be easy to access and at a distance between 0.7 and
1.7 m (2.3 and 5.6 ft) off the floor.
Danger or prohibition symbol.
This symbol indicates actions or operations that may hurt people or damage products.
Warning or caution symbol.
This symbol indicates situations that certain operations could cause and the suggested actions to prevent
them.
Obligation symbol.
This symbol indicates actions and operations that must be carried out.
Information symbol.
This symbol indicates notes, warnings and advises.
Symbol for additional documentation.
This symbol indicates that there is another document with more detailed and specific information.
i

Remote modules. RIO5, RIOW and RIOR series.
CNCelite
8058 8060
8065 8070
ꞏ17ꞏ
REF. 2107
Symbols that the product may carry.
Ground symbol.
This symbol indicates that that point must be under voltage.
ESD components.
This symbol identifies the cards as ESD components (sensitive to electrostatic discharges).

Remote modules. RIO5, RIOW and RIOR series.
CNCelite
8058 8060
8065 8070
ꞏ18ꞏ
REF. 2107

Remote modules. RIO5, RIOW and RIOR series.
CNCelite
8058 8060
8065 8070
ꞏ19ꞏ
REF. 2107
Pack it in its original package along with its original packaging material. If you do not have the original
packaging material, pack it as follows:
1Get a cardboard box whose 3 inside dimensions are at least 15 cm (6 inches) larger than those of the
unit itself. The cardboard being used to make the box must have a resistance of 170 Kg (375 lb.).
2Attach a label to the device indicating the owner of the device along with contact information (address,
telephone number, email, name of the person to contact, type of device, serial number, etc.). In case
of malfunction also indicate symptom and a brief description of the problem.
3Protect the unit wrapping it up with a roll of polyethylene or with similar material. When sending a central
unit with monitor, protect especially the screen.
4Pad the unit inside the cardboard box with polyurethane foam on all sides.
5Seal the cardboard box with packaging tape or with industrial staples.
RETURNING CONDITIONS.

Remote modules. RIO5, RIOW and RIOR series.
CNCelite
8058 8060
8065 8070
ꞏ20ꞏ
REF. 2107
Other manuals for CNC 8065elite T
1
This manual suits for next models
26
Other Fagor Control Unit manuals
Popular Control Unit manuals by other brands
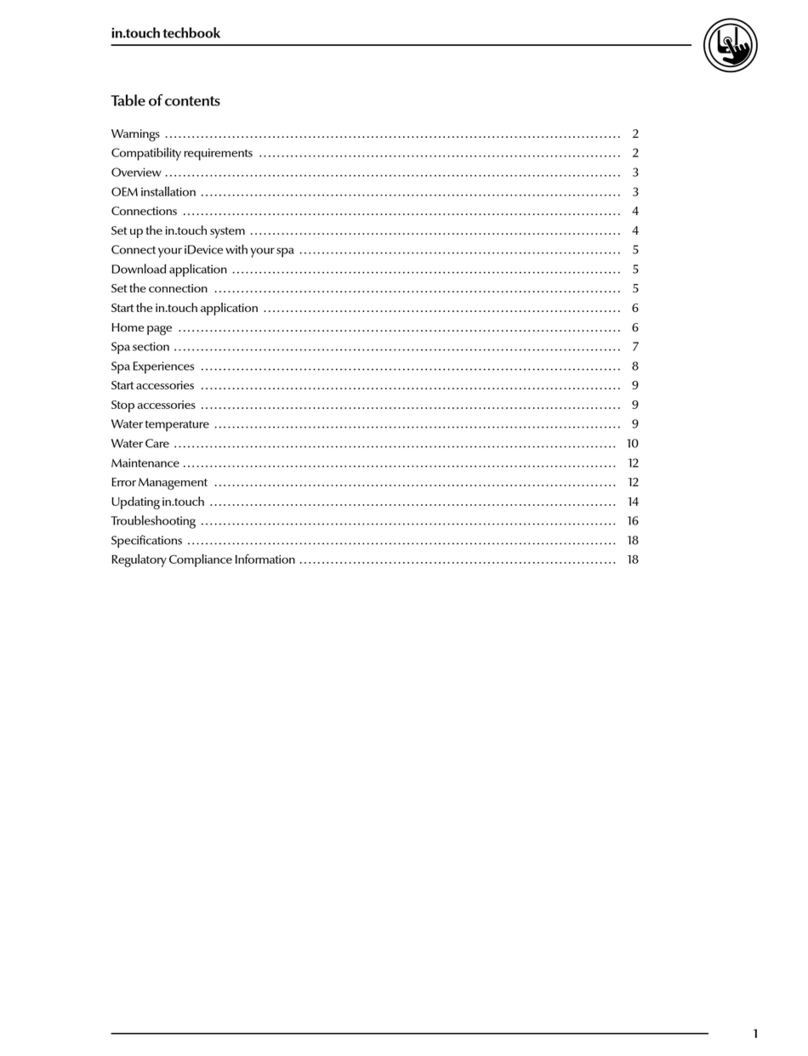
Gecko
Gecko In.Touch 0608-521012 Tech book
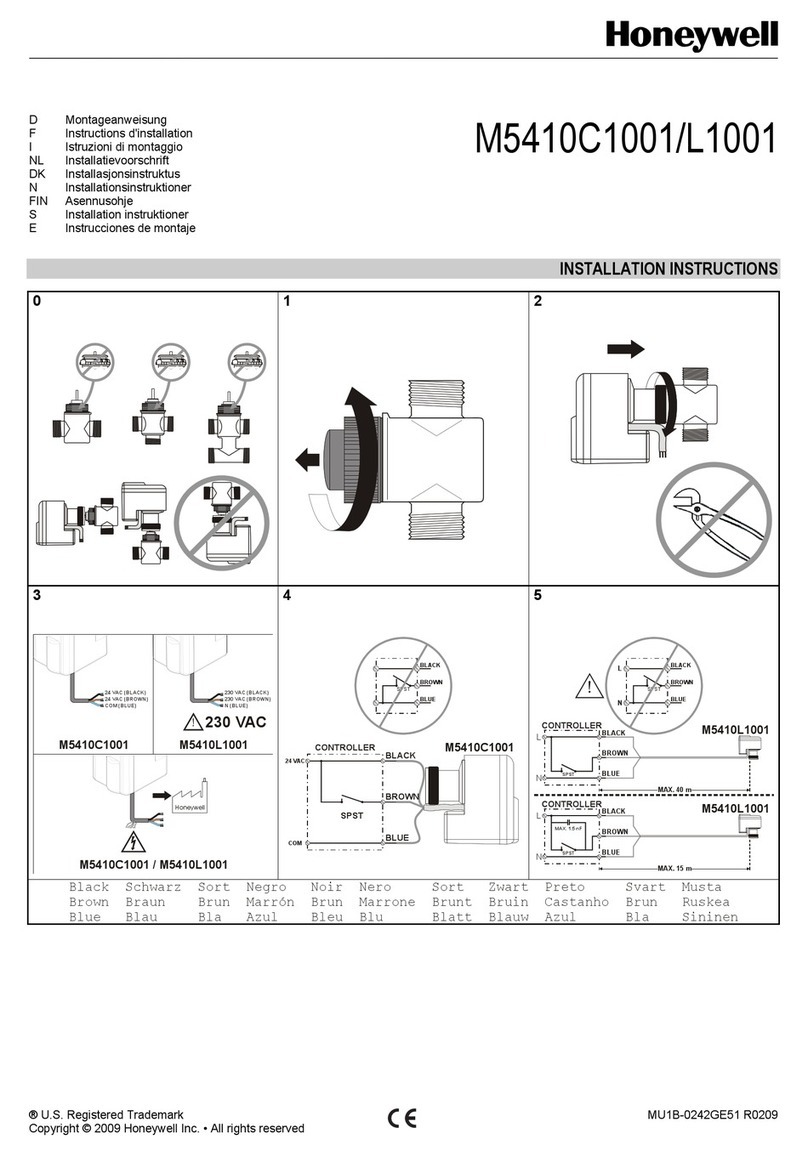
Honeywell
Honeywell M5410C1001 installation instructions
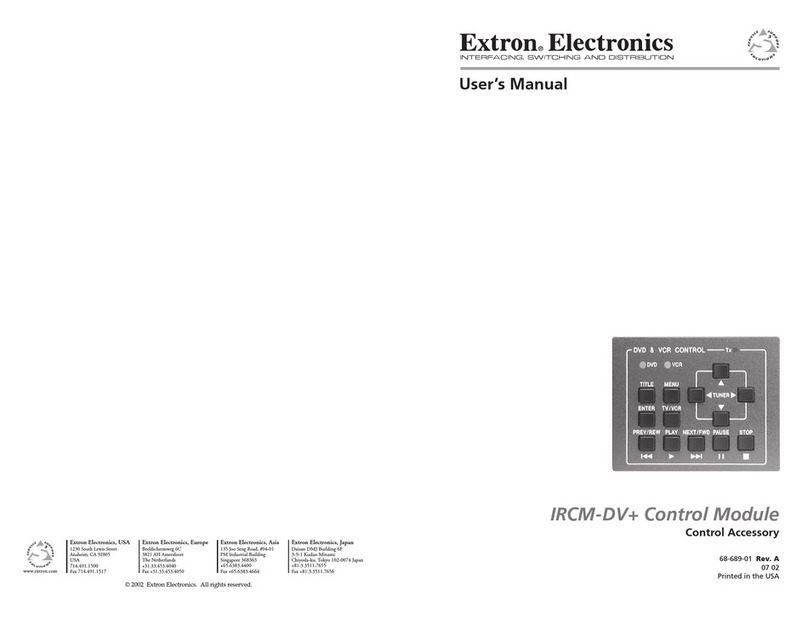
Extron electronics
Extron electronics IRCM-DVplus user manual
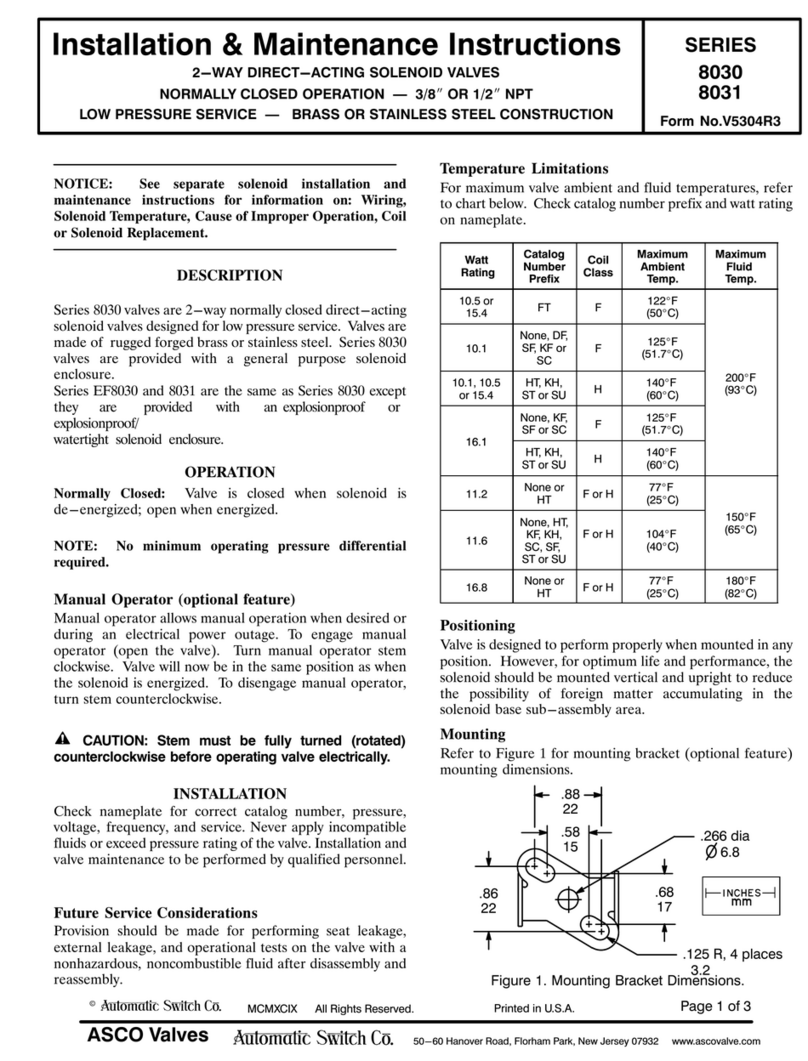
Asco
Asco 8030 Series Installation & maintenance instructions

Chauvet
Chauvet Stage Designer 50 TFX-48B user manual
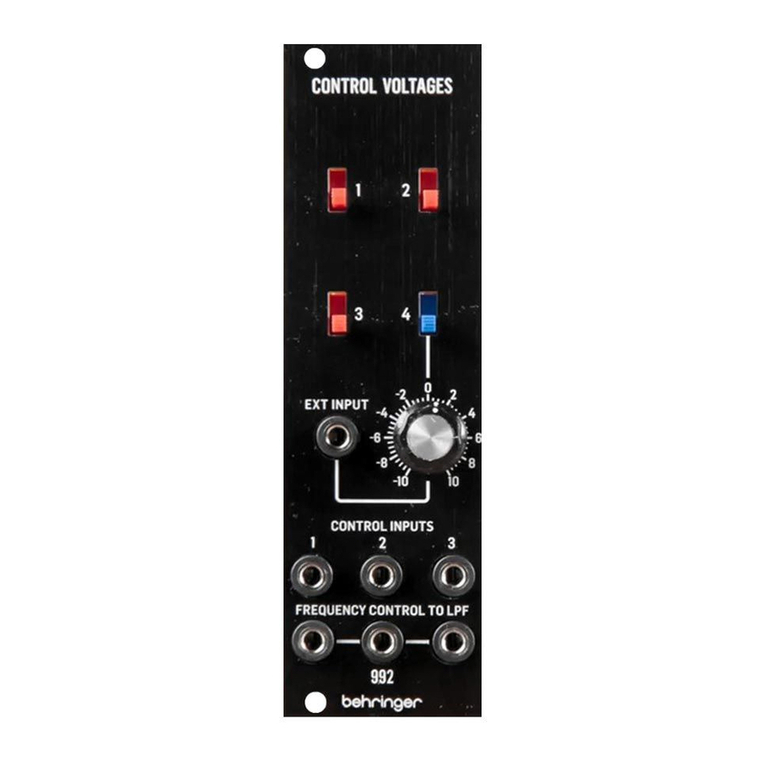
Behringer
Behringer 992 CONTROL VOLTAGES quick start guide