Edco TG-10 Assembly instructions

E-TG10-I-0808
Printed in USA
TVW ©2008
Page 1
100 Thomas Johnson Drive, Frederick, MD 21702-4600 USA
Phone (301) 663-1600 • 1-800-638-3326
Fax (301) 663-1607 • 1-800-447-3326
Website: www.edcoinc.com
Email: [email protected]
Operator’s Instruction Manual
TG-10
Turbo Grinder
Available in Gasoline, Propane
and Electric Models

E-TG10-I-0808
Printed in USA
©2008 TVW
Page 2
100 Thomas Johnson Drive, Frederick, MD 21702-4600 USA
Phone (301) 663-1600 • 1-800-638-3326
Fax (301) 663-1607 • 1-800-447-3326
Website: www.edcoinc.com
Email: [email protected]
READ AND UNDERSTAND THE OPERATORS INSTRUCTION MANUAL THOROUGHLY
BEFORE ATTEMPTING TO OPERATE THIS EQUIPMENT.
Death or serious injury could occur if this machine is used improperly.
Extreme care must be taken when operating electric
modelswithwaterpresent: Ensurepowercordisprop-
erlygrounded,isattachedtoaGround-Fault-Interrupter
(GFI) outlet, and is undamaged.
•Check all electrical cables - be sure connections are tight and
cable is continuous and in good condition. Be sure cable is
correctly rated for both the operating current and voltage of
this equipment.
•Improperconnection oftheequipmentgrounding conductor can
result in a risk of electric shock. Check with qualified electri-
cian or service person if there is any doubt as to whether the
outlet is properly grounded. Adhere to all local codes and
ordinances.
•NOTE: In the event of a malfunction or breakdown, grounding
provides a path of least resistance for the electric current to
dissipate. The motor is equipped with a grounded plug and
must be connected to an outlet that is properly installed and
properly grounded. DO NOT modify the plug provided on the
motor. If the plug does not fit the outlet have a qualified electri-
cian install the proper receptacle.
•Switch motor OFF before disconnecting power.
•Engine exhaust from this product contains
chemicals known to the State of California to
cause cancer, birth defects or other reproduc-
tive harm.
•Gasoline is extremely flammable and poisonous.
It should only be dispensed in well ventilated areas,
and with a cool engine.
•Small gasoline engines produce high concentra-
tions of carbon monoxide (CO) example: a 5 HP 4 cycle
engine operation in an enclosed 100,000 cu. ft. area with
only one change of air per hour is capable of providing
deadly concentrations of CO in less than fifteen minutes.
Five changes of air in the same area will produce noxious
fumes in less than 30 minutes. Gasoline or propane pow-
ered equipment should not be used in enclosed or partially
enclosed areas. Symptoms of CO poisoning include, head-
ache, nausea, weakness, dizziness, visual problems and
loss of consciousness. If symptoms occur get into fresh air
and seek medical attention immediately.
SAFETY
MESSAGES SAFETY MESSAGES
Indicates an imminent hazard which, if not
avoided, will result in death or serious injury.
Indicates an imminent hazard which, if not
avoided, can result in death or serious injury.
Indicates hazards which, if not avoided, could
result in serious injury and or damage to the
equipment.
•Safety Instructions are proceeded by a graphic alert symbol
of DANGER, WARNING, or CAUTION.
ELECTRICAL POWERED EQUIPMENT
GASOLINE/PROPANE POWERED EQUIPMENT
•Equipment should only be operated by trained personnel in
good physical condition and mental health (not fatigued). The
operator and maintenance personnel must be physically able
to handle the bulk weight and power of this equipment.
•This is a one person tool. Maintain a safe operating distance
to other personnel. It is the operators’responsibility to keep
other people (workers, pedestrians, bystanders, etc.) away
during operation. Block off the work area in all directions with
roping, safety netting, etc. for a safe distance. Failure to do so
may result in others being injured by flying debris or exposing
them to harmful dust and noise.
•This equipment is intended for commercial use only.
•For the operator’s safety and the safety of others, always keep
all guards in place during operation.
•Never let equipment run unattended.
•Personal Protection Equipment and proper safety attire must
be worn when operating this machinery. The operator must
wear approved safety equipment appropriate for the job such
as hard hat and safety shoes when conditions require. Hear-
ing protection MUST be used (operational noise levels of this
equipment may exceed 90db). Eye protection MUST be worn
at all times.
Keep body parts and loose clothing away from moving
parts. Failure to do so could result in dismemberment
or death.
•Do not modify the machine.
•Stopmotor/enginewhenadjusting or servicing this equipment.
Maintain a safe operating distance from flammable
materials. Sparksfrom the cutting-action of this machine
can ignite flammable materials or vapors.
GENERAL INSTRUCTIONS
DUST WARNING
Some dust created by power sanding, sawing,
grinding, drilling, and other construction activi-
tiescontainschemicalsknownto cause cancer,
birthdefects,or other reproductive harm. Some
examples of these chemicals are:
•Lead from lead-based paints, and
•Crystalline silica from bricks and concrete and other
masonry products.
Your risk of exposure to these chemicals varies depending
on how often you do this type of work. To reduce your risk
workin a wellventilatedarea, use adustcontrolsystem, such
as an industrial-style vacuum, and wear approved personal
safetyequipment, such as a dust/particlerespiratordesigned
to filter out microscopic particles.
•Donotdisconnect power by pulling cord. To disconnect, grasp
the plug, not the cord.
•Unplug power cord at the machine when not in use and before
servicing.

E-TG10-I-0808
Printed in USA
TVW ©2008
Page 3
100 Thomas Johnson Drive, Frederick, MD 21702-4600 USA
Phone (301) 663-1600 • 1-800-638-3326
Fax (301) 663-1607 • 1-800-447-3326
Website: www.edcoinc.com
Email: [email protected]
Figure 1
EDCO Model TG-10 TURBO GRINDER
Operator’s Instruction Manual
Dimensions and specifications are approximate
and subject to change.
TG10-5B
41”/104cm
24”/61cm
38”/97cm
175 lbs.
Weights include 10” Diamond Disc (20 segments)
TG10-11H
41”/104cm
24”/61cm
38”/97cm
180 lbs.
TG10-11P
41”/104cm
24”/61cm
38”/97cm
220 lbs.
Model
Length
Width
Height
Weight
Table of Contents
Section Page Number
Safety Information................................................................................................................ 2
Table of Contents and Specifications................................................................................... 3
Safety Guidelines.................................................................................................................. 4
SMI Dust and Silica Warning................................................................................................. 4
Operation Instructions...........................................................................................................5-8
Maintenance Instructions......................................................................................................9-10
Maintenance Schedule...........................................................................................................11
Limited Equipment Warranty............................................................................................ back cover
HOW TO ORDER REPAIR PARTS
To insure product safety and reliability, always use genuine
EDCO replacement parts when making repairs to the equip-
ment.
When ordering parts, please specify the MODEL and SERIAL
NUMBER of the machine as given on the NAMEPLATE. In
addition, give part number, description and quantity as listed
on the parts list.
Please note: Due to improvements and changes in the equip-
ment the illustrations shown may be different from the actual
machine.
Toll Free: Phone 1-800-638-3326 • Fax 1-800-447-3326
NOTE: Due to improvements in design your machine may not look
exactly like the ones in this manual. All function the same.
Width
Length Height

E-TG10-I-0808
Printed in USA
©2008 TVW
Page 4
100 Thomas Johnson Drive, Frederick, MD 21702-4600 USA
Phone (301) 663-1600 • 1-800-638-3326
Fax (301) 663-1607 • 1-800-447-3326
Website: www.edcoinc.com
Email: [email protected]
Eye and ear protection must be worn at all times when this machine is in use. During normal use,
sound levels exceed 92dB. Use onlyANSI approved safety glasses to help prevent eye injury.
Operator must wear appropriate clothing and footwear. Do not wear loose clothing or jewelry that can
get tangled in moving parts.
Grinding creates a large volume of airborne dust. The operator must wear an applicable respirator and use a
heavy duty vacuum, such as the EDCO VAC-290. The dust may contain chemicals known to cause serious ill-
nesses. The vacuum unit should be capable of filtering particles to less than 1 micron and have the capability
to be equipped with a HEPA filter. Check the chemical properties of the material to be removed and follow all
EPA/OSHA regulations. FAILURE TO COMPLY COULD LEAD TO SERIOUS ILLNESS.
• Keep a safe operating distance from other personnel and never leave the machine running unattended.
• Maintain the machine in safe operating condition with all guards in place and secure, all mechanical fasteners
tight, all controls in working order and the grinder configured for the job application.
• The TG-10 Turbo Grinder is to be operated by a properly trained and qualified operator from a position at the rear
of the machine.
• Inspect the disc carefully before installing. Do not use any damaged disc since serious personal injury and/or
damage to the equipment can result.
• Never operate the TG-10 Turbo Grinder if under the influence of drugs, alcohol or when taking medications that
impair the senses or reactions, or when excessively tired or under stress.
• Be sure all safety decals on the machine can be clearly read and understood. Replace damaged or missing
decals immediately.
Safety Guidelines
Read and understand the Operator’s Manual,
and the Engine Manufacturer’s Owner’s Manual
before operating this equipment.
Death or serious injury can result if this machine is used improperly.
Grinding/cutting/drilling of masonry, concrete, metal and other materials can generate dust, mists and fumes containing
chemicals known to cause serious or fatal injury or illness, such as respiratory disease, cancer, birth defects or other
reproductive harm. If you are unfamiliar with the risks associated with the particular process and/or material being
cut or the composition of the tool being used, review the material safety data sheets and/or consult your employer,
the manufacturers/suppliers, governmental agencies such as OSHA and NIOSH and other sources on hazardous
materials. California and some other authorities, for instance, have published lists of substances known to cause
cancer, reproductive toxicity, or other harmful effects.
Control dust, mist and fumes at the source where possible. In this regard use good work practices and follow the recom-
mendations of the manufacturers/suppliers, OSHA/NIOSH, and occupational and trade associations. Water should
beused for dustsuppression when wetgrinding/cutting/drilling is feasible. Whenthe hazards frominhalationof dust,
mists and fumes cannot be eliminated, the operator and any bystanders should always wear a respirator approved
by NIOSH/MSHA for the material being used.
Grinding/cutting/drilling of masonry, concrete and other materials with silica in their composition may give off dust or
mists containing crystalline silica. Silica is a basic component of sand, quartz, brick clay, granite and numerous
other minerals and rocks. Repeated and/or substantial inhalation of airborne crystalline silica can cause serious or
fatalrespiratorydiseases, including silicosis. Inaddition, California and someother authorities have listedrespirable
crystalline silica as a substance known to cause cancer. When grinding/cutting/drilling such materials, always follow
the respiratory precautions mentioned above.
SMI Dust and Silica Warning

E-TG10-I-0808
Printed in USA
TVW ©2008
Page 5
100 Thomas Johnson Drive, Frederick, MD 21702-4600 USA
Phone (301) 663-1600 • 1-800-638-3326
Fax (301) 663-1607 • 1-800-447-3326
Website: www.edcoinc.com
Email: [email protected]
Figure 2
Before Operating:
• Visually inspect machine:
- Verify all guards are in place and fasteners are tight.
- Check engine oil level (gasoline/propane models).
- Inspect power cord for damage and check for proper grounding (electric models).
• Inspect disc assembly:
- Check discs for damage or wear.
- Check mounting hardware.
- Check belt tension after first 4 hours of use with factory new equipment or after installing new belts.
• Inspect the work area:
Inspect work area carefully before starting to grind. EDCO will not be held responsible for damage to the discs
caused by striking protruding slab inserts, nails, screws, pipe extensions, machinery bases, or other objects that
transmit sudden shocks.
Safety warnings and guidelines do not by themselves eliminate danger.
They are not given as substitutes for proper accident prevention and good judgement.
Operating Instructions
Exhaust from this engine contains Carbon Monoxide, an invisible,
odorless gas that can kill. In addition, it contains chemicals known, in cer-
tain quantities, to cause cancer, birth defects or other reproductive harm.
Important Reminder!
A water mist system or an industrial vacuum must be used while operating this equipment and the
operator must wear a respirator. Failure to comply could lead to serious illness and possible death.
• If dry grinding:
- Hook up heavy-duty vacuum.
• If wet grinding:
- Attach hose to water supply.
- NOTE: Do not use dry vacuum when wet
grinding.

E-TG10-I-0808
Printed in USA
©2008 TVW
Page 6
100 Thomas Johnson Drive, Frederick, MD 21702-4600 USA
Phone (301) 663-1600 • 1-800-638-3326
Fax (301) 663-1607 • 1-800-447-3326
Website: www.edcoinc.com
Email: [email protected]
Propane Models: (11 HP Honda Motor with 115V Electric Start)
To Start the Engine:
• Turn on the main valve at the propane tank.
• Check all connections for tightness and inspect for leaks. If you detect a gas odor, immediately shut off the main
fuel valve and consult a qualified LP-gas service person or call EDCO directly. NEVER check for leaks using an
open flame; use a leak-testing solution. NEVER allow propane to escape in an enclosed area; propane is heavier
than air and will “settle”.
• Tilt the machine back slightly to allow the disc to clear the slab surface.
• Start the engine according to the directions in the engine manufacturer’s Owner’s Manual.
To Stop the Propane Model:
• Tilt the machine back slightly to allow the disc to clear the slab surface.
• Turn the engine off.
• Close the valve on the propane tank.
Gasoline Models: (11 HP Honda Engine)
To Start the Engine:
• Tilt the machine back slightly to allow the disc to clear the slab surface.
• Start the engine according to the directions in the engine manufacturer’s Owner’s Manual.
NOTE: If during operation refueling becomes necessary, allow the engine to cool down. NEVER refuel a hot engine.
To Stop the Gasoline Model:
• Tilt the machine back slightly to allow the disc to clear the slab surface.
• Turn the engine off.
Propane is extremely flammable.
To shut off the engine -
Press and hold the Emergency Stop Button
(Figure 3)
Figure 3

E-TG10-I-0808
Printed in USA
TVW ©2008
Page 7
100 Thomas Johnson Drive, Frederick, MD 21702-4600 USA
Phone (301) 663-1600 • 1-800-638-3326
Fax (301) 663-1607 • 1-800-447-3326
Website: www.edcoinc.com
Email: [email protected]
Dry Grinding:
Dry Grinding creates a large volume of airborne dust. For health reasons, the operator should wear an
applicable respirator. The dust may contain chemicals known to cause serious illnesses, including Silicosis
- a fatal disease of the lungs. Check the chemical properties of the material to be removed and follow all
EPA/OSHA regulations.
• An Industrial vacuum, capable of handling high volume of fine dust,such as the
VAC - 290 (Figure 5), should be used when dry grinding with this machine. If the
material being used is hazardous or contains Silica - the vacuum unit should be
capable of removing Respirable Silica and hazardous particles of less than 1
micron and if necessary, have the capability to be equipped with a HEPA filter.
Most standard vacuum drum type units use a paper bag filter. The dust created
during grinding is extremely fine and will clog the filter bag of these units and eventu-
ally damage the vacuums motor. In addition, damage to the TG-10 engine could
occur.
• The collected debris and filters should be disposed of according to procedures that
comply with current EPA/OSHA standards.
Electric Models:
(5 HP Baldor. Available in 1 Phase or 3 Phase)
Electric units must be connected to a properly grounded
electrical system using an approved electrical cable.
To Start the Machine:
• Tilt the machine back slightly, just enough for the disc to be clear of the slab surface.
• Press the ON button on the power box.
• Be sure to check motor for correct rotation.
• Gently set the machine back down until the disc touches the slab surface and begin moving the machine.
To Stop the Machine:
• Tilt the machine to allow the disc to clear the slab surface.
• Press OFF button on the power box.
Wet Grinding:
• In the wet grinding stage - water is fed from a standard garden hose into a
ball valve cut off, then into a nozzle that sprays over the disc assembly. (Figure 4)
Use the ball valve to regulate the flow of water to the disc.
Only use enough water flow to reduce dust. Excess water flow will
create clean up problems and could cause a hazardous walking area.
Always use dust control when using this product, vacuum or
water mist.
Figure 4
Figure 5

E-TG10-I-0808
Printed in USA
©2008 TVW
Page 8
100 Thomas Johnson Drive, Frederick, MD 21702-4600 USA
Phone (301) 663-1600 • 1-800-638-3326
Fax (301) 663-1607 • 1-800-447-3326
Website: www.edcoinc.com
Email: [email protected]
Discs:
• Inspect the disc (Figure 8) periodically to determine it’s wear characteristics, if signs of uneven wear appear the
cause should be determined and corrected. If repairs are needed contact EDCO or your EDCO representative.
• Rigid Head can be used on uneven expansion joints, high spots, joint curls and bridge decks, removing coatings
and grinding rough concrete surfaces. Use with a vacuum or water for dust control but not the same time.
• Flex Head can be used preparing a smooth, flat floor to receive a new coating, removing coatings, grind rough
concrete surfaces. Can be used with a vacuum or water for dust control but not the same time.
• Each new machine is shipped with a RIGID HEAD (FLEX HEAD OPTIONAL) 10”/255 mm factory balanced disk.
It is important to maintain the coupling to which the disk is attached. A worn coupling, damaged bearings or a bent
shaft will cause the grinding discs to wear unevenly. (Figure 9 rigid head assembly & 9A flex head assembly.) It is
important to note FLEX HEAD for smooth flat surfaces, RIGID HEAD for buckled, bumpy or rough surfaces.
Controlling the Grind:
• Grinding discs are extremely aggressive. It is important to KEEP THE GRINDER MOVING IN A SIDE-TO-SIDE
MOTION, do not let the grinder stay in one spot, even for a few seconds, or the surface will be damaged. When
grinding is completed, tilt the machine back and shut off the power.
• To achieve a smooth “polished” surface, complete the grinding operation with an EDCO dual disc unit using
grinding stones or dyma serts.
• To remove a light coating, move the grinder quickly. For heavier removal, move the grinder more slowly.
• Keep the grinding disc flat - do not attempt to grind against vertical surfaces. Be sure the machine is in the correct
operating position. (See Figure 6 below..)
Figure 9A
Flex
Optional FLEX HEAD
Figure 9
Standard RIGID HEAD
Fixed
Figure 6
Figure 8
Disc shown is for reference
only.

E-TG10-I-0808
Printed in USA
TVW ©2008
Page 9
100 Thomas Johnson Drive, Frederick, MD 21702-4600 USA
Phone (301) 663-1600 • 1-800-638-3326
Fax (301) 663-1607 • 1-800-447-3326
Website: www.edcoinc.com
Email: [email protected]
Maintenance
Disconnect spark plug lead (Figure 10) before pre-
forming any maintenance on this machine! Or on the
electric model, unplug the electric cord at the machine
(instead of at the wall) to assure the machine will
remain un-plugged while you are working on it.
Inspect Every 8 Hours:
• Inspect the disc mounting screws. (Figure 11) The constant vibration
and heat generated, especially when grinding dry, could cause the
screws to loosen and the disc to become off balance.
Follow the engine manufacturer’s guidelines for regular maintenance.
Lubricate Every 50 Hours:
• Bearings (Figure 12) must be lubricated every 50 hours.
• Belt guard has to be removed to access bearing lubrication
fitting.
Figure 10
Figure 11
Disc Mount-
ing Screws
Figure 12

E-TG10-I-0808
Printed in USA
©2008 TVW
Page 10
100 Thomas Johnson Drive, Frederick, MD 21702-4600 USA
Phone (301) 663-1600 • 1-800-638-3326
Fax (301) 663-1607 • 1-800-447-3326
Website: www.edcoinc.com
Email: [email protected]
Belts:
To remove/replace belts:
• Remove belt cover to expose belts. (Figure 13)
• Loosen engine/motor mounting bolts (Figure 14) on both sides of the TG-10 and slide engine forward to allow
belts to slide off.
• Replace worn belts with a complete set of new belts - even if only one belt is showing wear.
• Slide engine back in place until belts are tight and retighten engine mounting bolts.
• Reinstall belt cover and tighten hardware.
• After four hours of use, retighten belts.
Figure 15
Engine Air Filter:
Inspect the air filters (Figure 15) for excess dust, dirt
or damage before the engine is operated. More often if
operating in a dusty environment.
Operating the engine with a damaged or dirty air filter,
or without an air filter, will allow dirt to enter the engine
causing rapid engine wear which would not be covered
under the engine manufacturer’s warranty.
Follow the engine manufacturer’s procedures for keep-
ing the filters in good condition.
Figure 13 Figure 14

E-TG10-I-0808
Printed in USA
TVW ©2008
Page 11
100 Thomas Johnson Drive, Frederick, MD 21702-4600 USA
Phone (301) 663-1600 • 1-800-638-3326
Fax (301) 663-1607 • 1-800-447-3326
Website: www.edcoinc.com
Email: [email protected]
Maintenance Schedule
Read and follow the
engine manufacturer’s
maintenance schedule.
Repairs are to be done by au-
thorized EDCO Dealers only.
* When applicable.
Before Operation
After First 4 Hours
Every 8 Hours
Every 50 Hours
As Necessary
Adjust Wheel
Height
X
X
X
X
X
X
X
Inspect Entire
Machine
* Check Oil & Fuel
Levels
* Inspect Propane
Connections
Inspect Disc
Inspect Belt Tension
Lubricate Shaft Bear-
ings
Inspect/Tighten
Disc Mounting Screws
* Inspect Vacuum
(empty bins, etc.)
XX
X
X
* Check Air Filter
(Clean if Necessary) X

E-TG10-I-0808
Printed in USA
©2008 TVW
Page 12
100 Thomas Johnson Drive, Frederick, MD 21702-4600 USA
Phone (301) 663-1600 • 1-800-638-3326
Fax (301) 663-1607 • 1-800-447-3326
Website: www.edcoinc.com
Email: [email protected]
LIMITED EQUIPMENT WARRANTY OF SALE – TERMS & CONDITIONS
Equipment Development Company, Inc. herein referred to as EDCO (Seller) warrants that
eachnewunitmanufactured byEDCO tobe freefrom defectsin materialand workmanshipin
normal use and service for a period of (90) ninety days (except for the cutter drum assembly
on all model concrete/asphalt planes, in which case the warranty period shall be 90 days)
from date of shipment to the original retail or equipment rental center owner.
Accessories or equipment furnished and installed on the product by EDCO but manufactured by
others,including, butnot limitedto engines,motors,electrical components,transmissions etc., shall
carry the accessory manufacturers own warranty.
EDCO will, at its option, repair or replace, at the EDCO factory or at a point designated by
EDCO, any part which shall appear to the satisfaction of EDCO inspection to have been
defective in material or workmanship.
EDCO reserves the right to modify, alter and improve any part or parts
without incurring any obligation to replace any part or parts previously sold without such
modified, altered or improved part or parts.
This warranty is in lieu of and excludes all other warranties, expressed, implied, statutory, or
otherwisecreated underapplicable law including,but notlimited tothe warrantyof merchant-
abilityand the warranty of fitnessfor aparticular purpose inno eventshall selleror the manu-
facturer of the product be liable for special, incidental, or consequential damages, including
loss of profits, whether or not caused by or resulting from the negligence of seller and/or the
manufacturerof theproduct unlessspecifically provided herein.In addition,this warrantyshall
not apply to any products or portions there of which have been subjected to abuse, misuse,
improper installation, maintenance, or operation, electrical failure or abnormal conditions
and to products which have been tampered with, altered, modified, repaired, reworked by
anyone not approved by seller or used in any manner inconsistent with the provisions of the
above or any instructions or specifications provided with or for the product
FORCE MAJEURE
Seller’s obligation hereunder are subject to, and Seller shall not be held responsible for, any
delay or failure to make delivery of all or any part of the Product due to labor difficulties,
fires, casualties, accidents, acts of the elements, acts of God, transportation difficulties,
delays by a common carrier, inability to obtain Product, materials or components or qualified
labor sufficient to timely perform part of or all of the obligations contained in these terms
and conditions, governmental regulations or actions, strikes, damage to or destruction in
whole or part of manufacturing plant, riots, terrorist attacks or incidents, civil commotions,
warlike conditions, flood , tidal waves, typhoon, hurricane, earthquake, lightning, explosion
or any other causes, contingencies or circumstances within or without the United States not
subject to the Seller’s control which prevent or hinder the manufacture or delivery of the
Products or make the fulfillment of these terms and conditions impracticable. In the event
of the occurrence of any of the foregoing, at the option of Seller, Seller shall be excused
from the performance under these Terms and Conditions, or the performance of the Seller
shall be correspondingly extended.
This document sets forth the terms and conditions pursuant to which the purchaser (“Pur-
chaser”) will purchase and Equipment Development Co.Inc. (“Seller”)will sell the products,
accessories,attachments (collectivelythe Products“) orderedby thePurchaser.Theseterms
andconditions shallgovern andapplyto thesale ofSeller’sProductsto Purchaser, regardless
of any terms and conditions appearing on any purchase order or other forms submitted by
Purchaser to Seller, or the inconsistency of any terms therein and herein.
1. PRICE
All prices set forth on any purchase order or other document are F.O.B. Sellers facility or distribu-
tion point, as may be determined by Seller (F.O.B.Point). All prices are exclusive of any and all
taxes,including, butnot limitedto, excise,sales, use,property ortransportation taxesrelated tothe
sale or use of the Products, now or hereafter imposed, together with all penalties and expenses.
Purchaser shall be responsible for collecting and/or paying any and all such taxes, whether or
not they are stated in any invoice for the Products. Unless otherwise specified herein, all prices
are exclusive of inland transportation, freight, insurance and other costs and expenses relating
to the shipment of the Products from the F.O.B. point to Purchaser’s facility. Any prepayment by
Seller of freight insurance and other costs shall be for the account of Purchaser and shall be
repaid to Seller.
2. PAYMENT TERMS
Payment termsare asfollows. 2%10 days(to approvedand qualifiedaccounts). Net30 days.
This is a cash discount for invoices paid within 10 days after the invoice date, regardless of
date of receipt of shipment. This is not a trade discount and will not be granted to accounts
that do not adhere to stated terms.
*All past due accounts are subject to a late payment fee of 1.5% per month or a maximum
allowed by law if different, along with the expenses incidental to collection including reason-
able attorney’s fees and costs.
*Seller reserves the right to hold shipments against past due accounts.
*Seller reserves the right to alter payment terms.
3. FREIGHT TERMS
All shipments will be made F.O.B. shipping point as designated in these Terms and Condi-
tions, and title shall pass at the F.O.B. point. Delivery to the initial common carrier shall
constitute delivery to the Purchaser. Any claims for loss or damage during shipment are
to be filed with carrier by the Purchaser. Seller will not assume responsibility for the per-
formance of the carrier.
Back orders will be shipped in the most practical fashion with charges consistent with our
freight policy established with the original order. UPS, FED EX, MAIL or shipments by other
couriers are subject to the same terms and conditions as outlined in paragraph #3”Freight
Terms”.
4. DELIVERY, DAMAGES, SHORTAGES
Seller shall use reasonable efforts to attempt to cause the Products to be delivered as provided
for in these Terms & Conditions. Delivery to the initial common carrier shall constitute the delivery
to the Purchaser. Sellers responsibility, in so far as transportation risks are concerned ceases
upon the delivery of the Products in good condition to such carrier at the F.O.B. point and all the
Products shall be shipped at the Purchaser’s risk. Seller shall not be responsible or liable for
any loss of income and/or profits, or incidental, special, consequential damages resulting from
Seller’s delayed performance in shipment and delivery.
5. RETURN OF DEFECTIVE PRODUCTS
Defective or failed material shall be held at the Purchaser’s premises until authorization has
been granted by Seller to return or dispose of Products. Products that are to be returned
for final inspection must be returned Freight Prepaid in the most economical way. Credit
will be issued for material found to be defective upon Seller’s inspection based on prices
at time of purchase.
6. PRODUCTS ORDERED IN ERROR
Products may be returned, provided that claim is made and Seller is notified within 7 days
of receipt of Products, and the Products are in original buyer’s possession not more than
30 days prior to return, subject to Seller’s approval. If Products are accepted for return, they
must be Freight Prepaid and buyer will be charged a minimum of 15% rehandling charge,
plus a charge back for outbound freight charges if the original order was shipped prepaid.
Returns are not accepted for any Products that are specifically manufactured to meet the
buyer’s requirement of either specifications or quantity.
AGREEMENTS
These Terms and Conditions constitute the entire agreement between Seller and Purchaser as it
relatesto termsand conditionsof sale,andsupersedes anyand allprior oralor writtenagreements,
correspondence, quotations or understandings heretofore in force between the parties relating to
the subject matter hereof. There are no agreements between Seller and Purchaser with respect
to the Product herein except those specifically set forth in and made part of these terms and
conditions. Any additional terms, conditions and/or prices are rejected by Seller.
These terms and conditions may be modified, cancelled or rescinded only by a written
agreement of both parties executed by their duly authorized agents.
USE ONLY GENUINE EDCO PARTS &ACCESSORIES
For your own safety, the safety of others and the life of your machine.
Other manuals for TG-10
3
Table of contents
Other Edco Grinder manuals
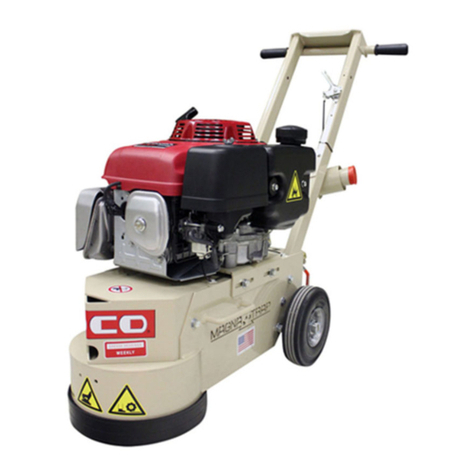
Edco
Edco TG-10 Assembly instructions
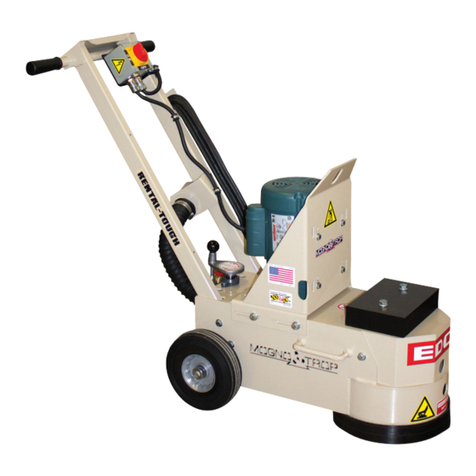
Edco
Edco SECNG-1.5L User manual

Edco
Edco TG-10 Assembly instructions
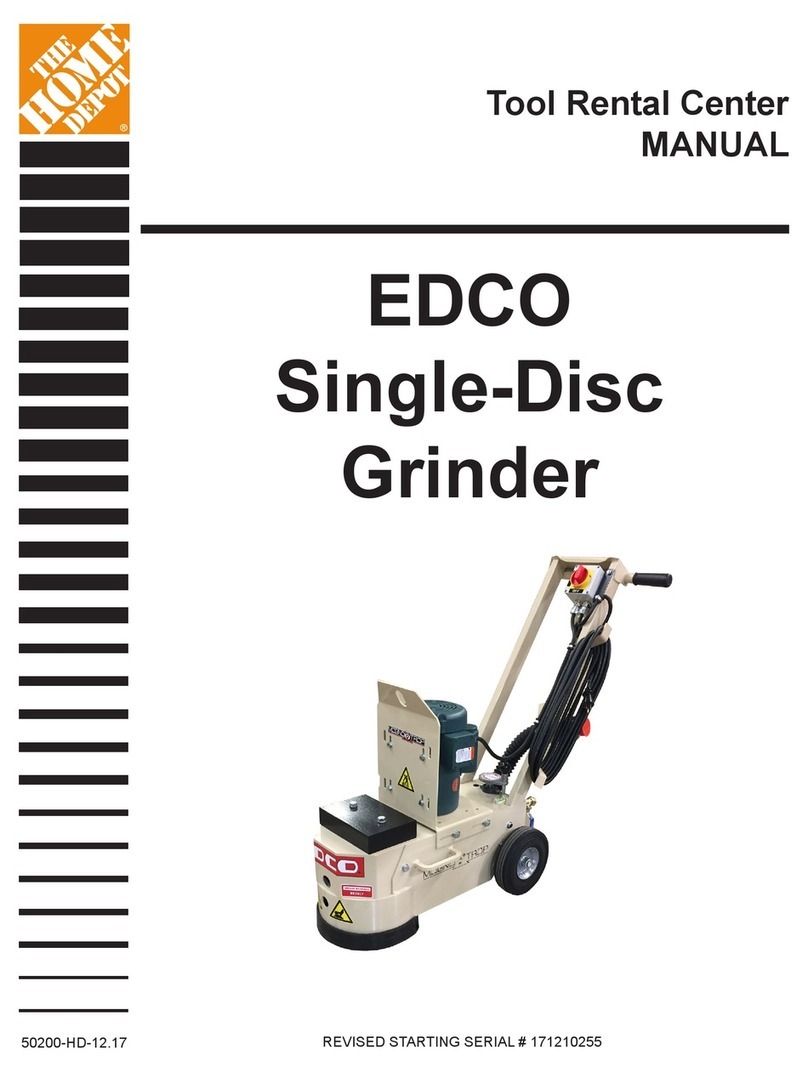
Edco
Edco SEC-HD User manual
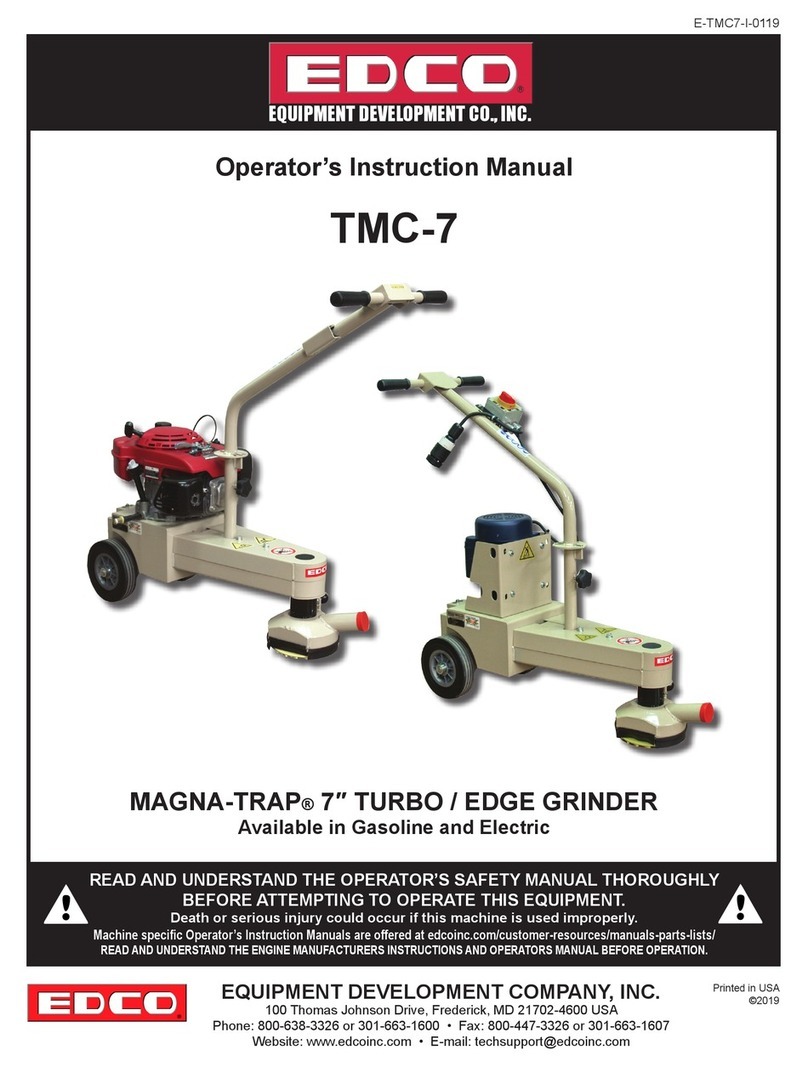
Edco
Edco MAGNA-TRAP TMC-7 Assembly instructions
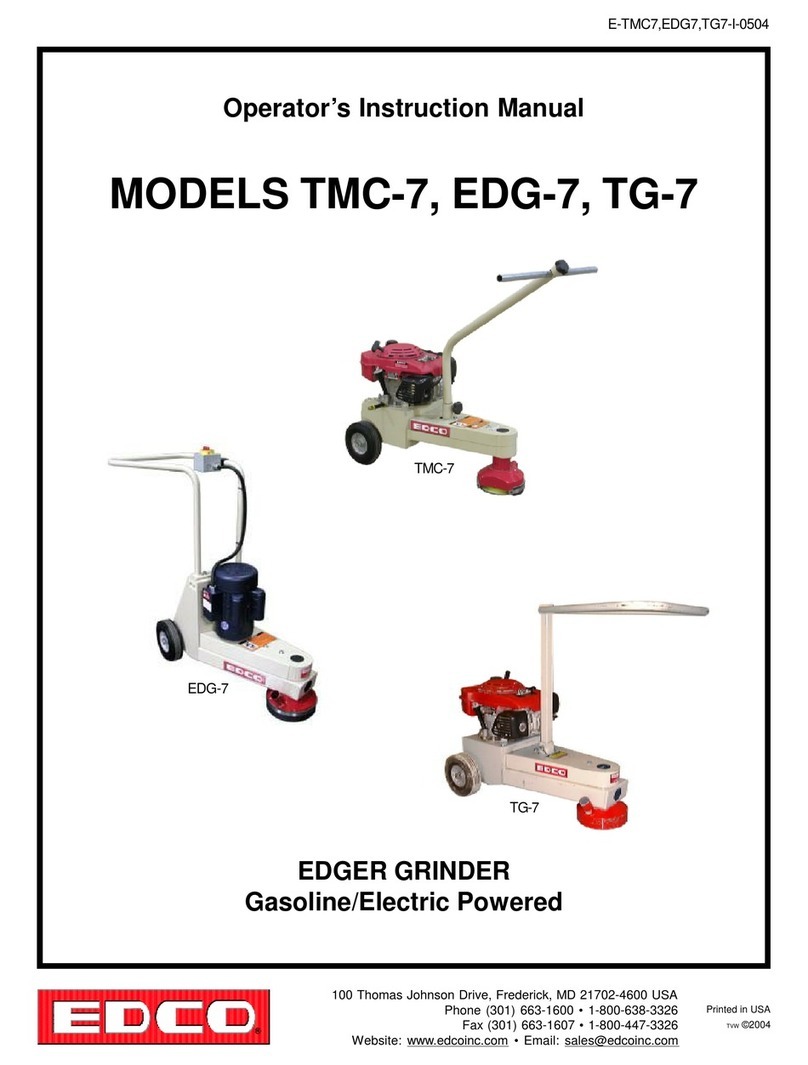
Edco
Edco MAGNA-TRAP TMC-7 Assembly instructions
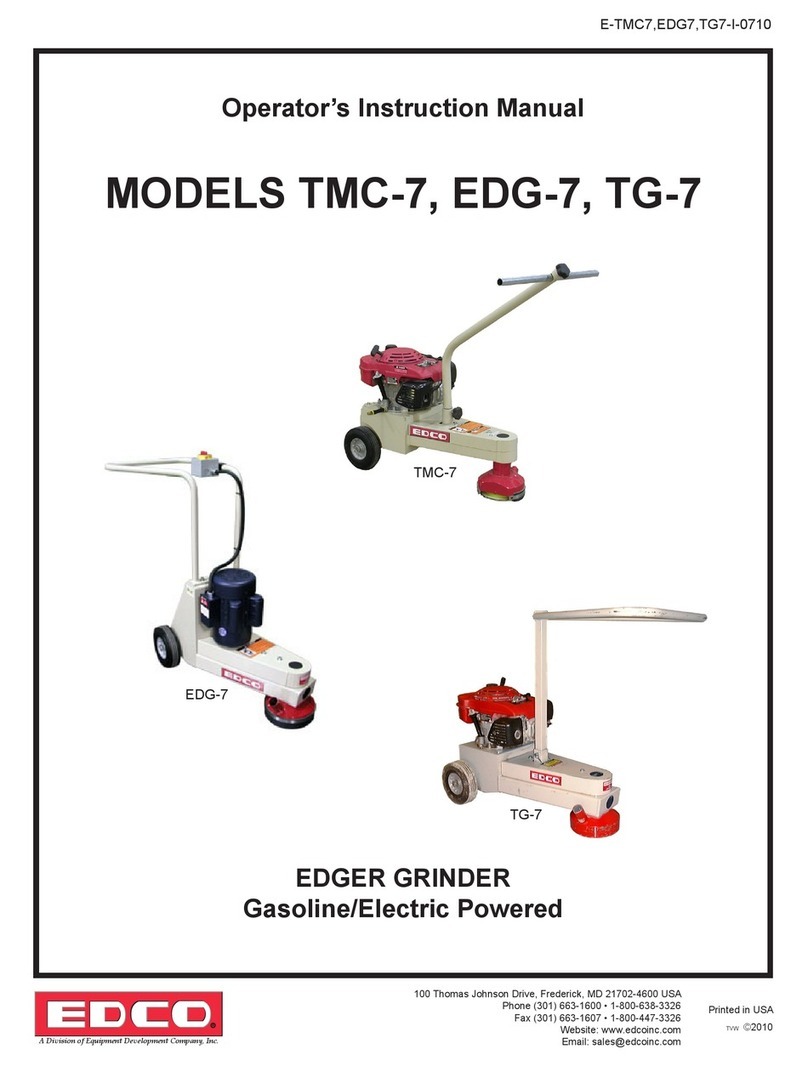
Edco
Edco MAGNA-TRAP TMC-7 Assembly instructions
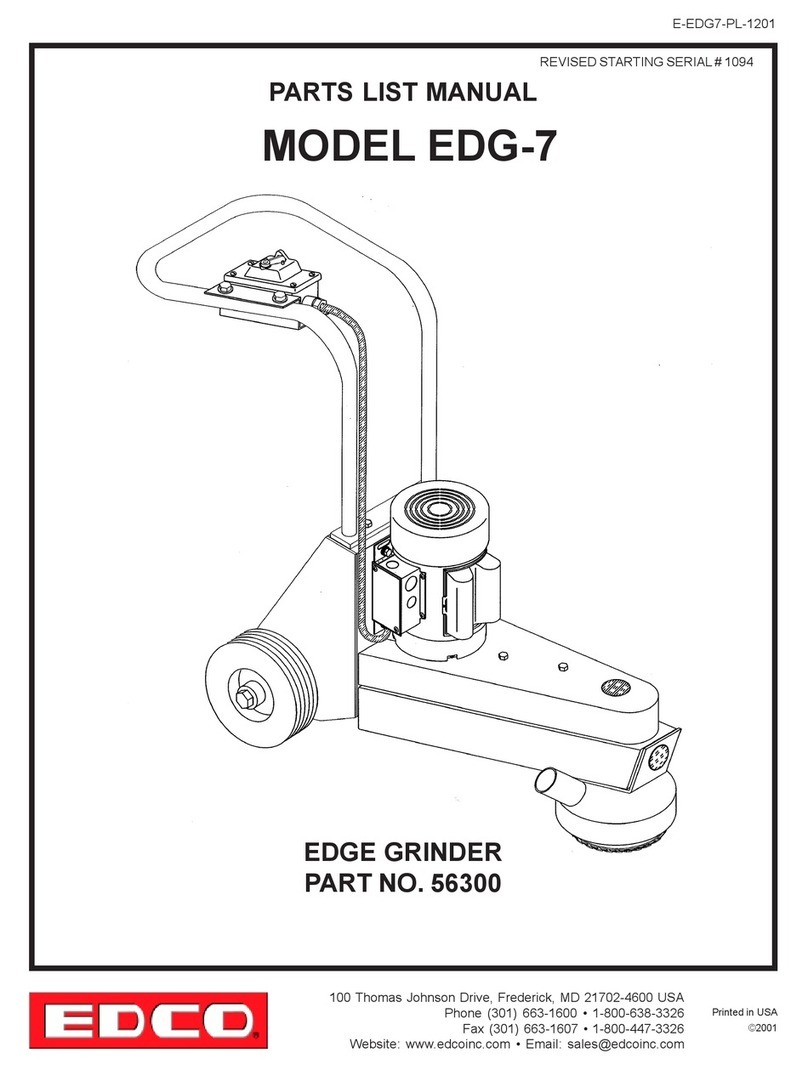
Edco
Edco EDG-7 Datasheet
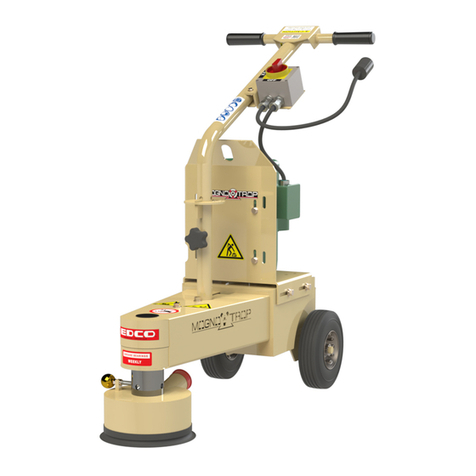
Edco
Edco MAGNA-TRAP TMC-7 Assembly instructions
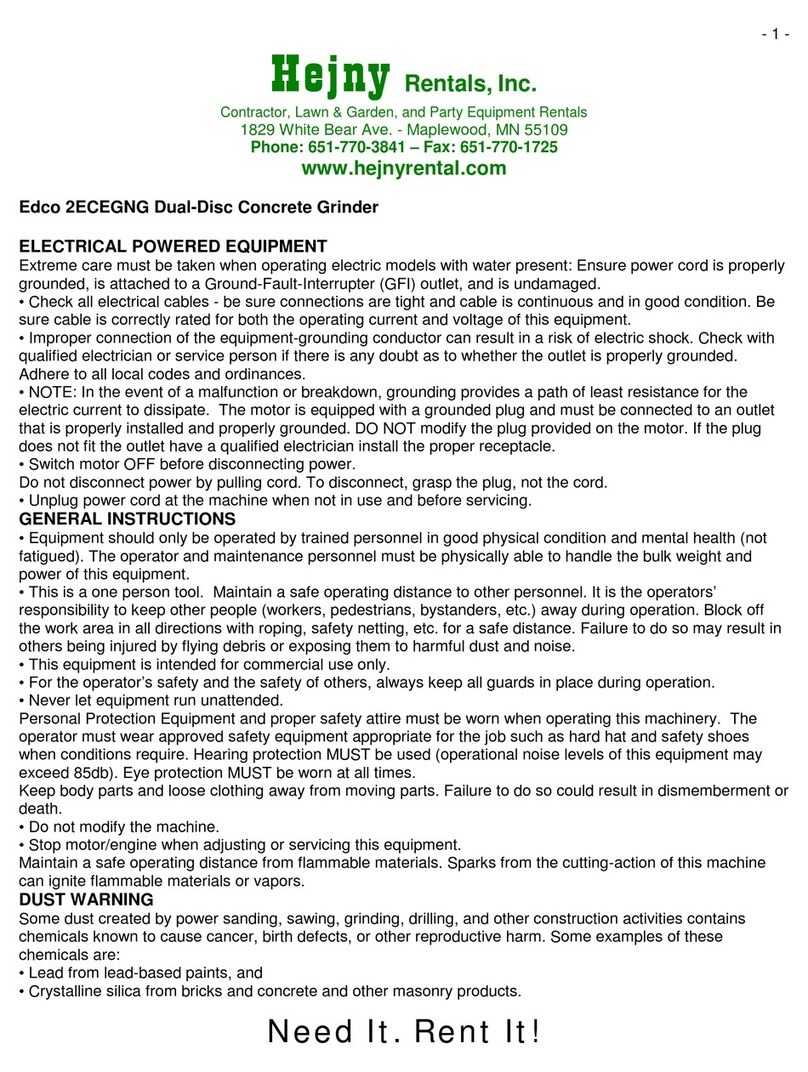
Edco
Edco 2ECEGNG User manual
Popular Grinder manuals by other brands
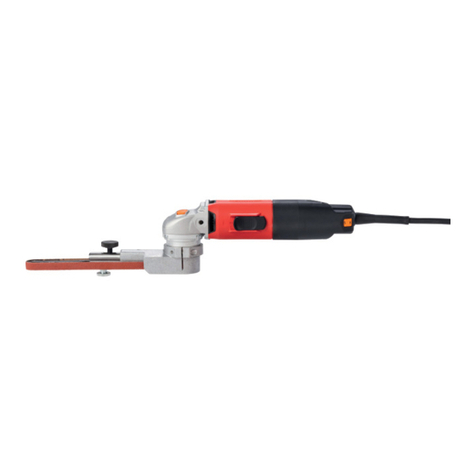
SUHNER ABRASIVE
SUHNER ABRASIVE UBC 9-R Technical document
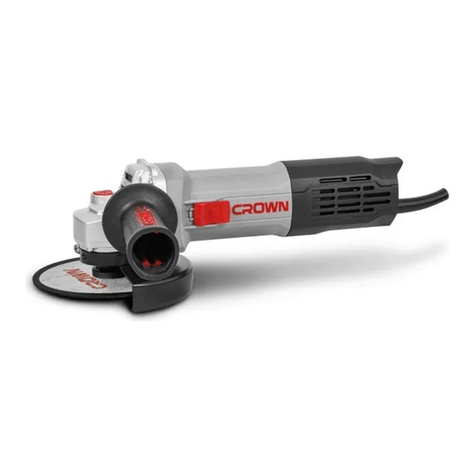
Crown
Crown CT13567-100 Original instructions

Erbauer
Erbauer EBS950 Original instructions

Dotco
Dotco 10LF Series product manual

Makita
Makita 9553B instruction manual

Silver Eagle
Silver Eagle SE350 Operating instructions, warning information, parts breakdown