Edco MAGNA-TRAP TMC-7 Assembly instructions

Operator’s Instruction Manual
TMC-7
EDGE/GRINDER
GASOLINE/ELECTRIC
TMC-7-I-0615
E-SPTS-I-0809
EQUIPMENTDEVELOPMENTCO.,INC.
To order go to Discount-Equipment.com

We sell worldwide for the brands: Genie, Terex, JLG, MultiQuip, Mikasa, Essick, Whiteman,
Mayco, Toro Stone, Diamond Products, Generac Magnum, Airman, Haulotte, Barreto, Power
Blanket, Nifty Lift, Atlas Copco, Chicago Pneumatic, Allmand, Miller Curber, Skyjack, Lull,
Skytrak, Tsurumi, Husquvarna Target, Stow, Wacker, Sakai, Mi-T-M, Sullair, Basic, Dynapac,
MBW, Weber, Bartell, Bennar Newman, Haulotte, Ditch Runner, Menegotti, Morrison, Contec,
Buddy, Crown, Edco, Wyco, Bomag, Laymor, EZ Trench, Bil-Jax, F.S. Curtis, Gehl Pavers, Heli,
Honda, ICS/PowerGrit, IHI, Partner, Imer, Clipper, MMD, Koshin, Rice, CH&E, General Equip-
ment ,Amida, Coleman, NAC, Gradall, Square Shooter, Kent, Stanley, Tamco, Toku, Hatz,
Kohler, Robin, Wisconsin, Northrock, Oztec, Toker TK, Rol-Air, APT, Wylie, Ingersoll Rand /
Doosan, Innovatech, Con X, Ammann, Mecalac, Makinex, Smith Surface Prep,Small Line,
Wanco, Yanmar
Discount-Equipment.com is your online resource for
commercial and industrial quality parts and equipment sales.
561-964-4949
visit us on line @ www.discount-equipment.com
TO PURCHASE THIS PRODUCT PLEASE CONTACT US
Select an option below to find your Equipment
Equipment Financing and
Extended Warranties Available

Page 2
TMC-7-I-0615
EQUIPMENTDEVELOPMENTCO.,INC.
READ AND UNDERSTAND THE OPERATORS INSTRUCTION MANUAL THOROUGHLY
BEFORE ATTEMPTING TO OPERATE THIS EQUIPMENT.
Death or serious injury could occur if this machine is used improperly.
Extreme care must be taken when operating electric
modelswithwaterpresent: Ensurepowercordisprop-
erlygrounded,isattachedtoaGround-Fault-Interrupter
(GFI) outlet, and is undamaged.
•Check all electrical cables - be sure connections are tight and
cable is continuous and in good condition. Be sure cable is
correctly rated for both the operating current and voltage of
this equipment.
•Improperconnection of theequipment-groundingconductor can
result in a risk of electric shock. Check with qualified electri-
cian or service person if there is any doubt as to whether the
outlet is properly grounded. Adhere to all local codes and
ordinances.
• NOTE: In the event of a malfunction or breakdown, grounding
provides a path of least resistance for the electric current to
dissipate. The machine is equipped with a grounded plug
and must be connected to an outlet that is properly installed
and properly grounded. DO NOT modify the plug provided on
the motor. If the plug does not fit the outlet have a qualified
electrician install the proper receptacle.
•Switch motor OFF before disconnecting power.
•Engine exhaust from this product contains
chemicals known to the State of California to
causecancer, birth defectsorotherreproductive
harm.
•Gasoline is extremely flammable and poisonous. It
should only be dispensed in well ventilated areas,
and with a cool engine.
•Small gasoline engines produce high concentrations of car-
bon monoxide (CO) example: a 5 HP 4 cycle engine opera-
tion in an enclosed 100,000 cu. ft. area with only one change
of air per hour is capable of providing deadly concentrations
of CO in less than fifteen minutes. Five changes of air in the
same area will produce noxious fumes in less than 30 min-
utes. Gasoline or propane powered equipment should not be
used in enclosed or partially enclosed areas. Symptoms of
CO poisoning include, headache, nausea, weakness, dizzi-
ness, visual problems and loss of consciousness. If symp-
toms occur - get into fresh air and seek medical attention
immediately.
SAFETY
MESSAGES SAFETY MESSAGES
Indicatesan imminent hazardwhich,ifnot avoid-
ed, will result in death or serious injury.
Indicatesanimminenthazardwhich,ifnotavoid-
ed, can result in death or serious injury.
Indicates hazards which, if not avoided, could
result in serious injury and or damage to the
equipment.
•Safety Instructions are proceeded by a graphic alert symbol
of DANGER, WARNING, or CAUTION.
ELECTRICAL POWERED EQUIPMENT
GASOLINE/PROPANE POWERED EQUIPMENT
•Equipment should only be operated by trained personnel in
good physical condition and mental health (not fatigued). The
operator and maintenance personnel must be physically able
to handle the bulk weight and power of this equipment.
•This is a one person tool. Maintain a safe operating distance
to other personnel. It is the operators’responsibility to keep
other people (workers, pedestrians, bystanders, etc.) away
during operation. Block off the work area in all directions with
roping, safety netting, etc. for a safe distance. Failure to do so
may result in others being injured by flying debris or exposing
them to harmful dust and noise.
•This equipment is intended for commercial use only.
•For the operator’s safety and the safety of others, always keep
all guards in place during operation.
•Never let equipment run unattended.
•Personal Protection Equipment and proper safety attire must
be worn when operating this machinery. The operator must
wear approved safety equipment appropriate for the job such
as hard hat and safety shoes when conditions require. Hear-
ing protection MUST be used (operational noise levels of this
equipment may exceed 85db). Eye protection MUST be worn
at all times.
Keep body parts and loose clothing away from moving
parts. Failure to do so could result in dismemberment
or death.
•Do not modify the machine.
•Stopmotor/enginewhen adjusting or servicing this equipment.
Maintain a safe operating distance from flammable
materials. Sparksfromthecutting-actionofthis machine
can ignite flammable materials or vapors.
GENERAL INSTRUCTIONS
DUST WARNING
Some dust created by power sanding, sawing,
grinding, drilling, and other construction activi-
tiescontainschemicalsknowntocause cancer,
birthdefects,or other reproductive harm. Some
examples of these chemicals are:
•Lead from lead-based paints, and
•Crystalline silica from bricks and concrete and other
masonry products.
Your risk of exposure to these chemicals varies depending
on how often you do this type of work. To reduce your risk:
workin a well ventilatedarea,useadust control system,such
as an industrial-style vacuum, and wear approved personal
safetyequipment,such as a dust/particle respirator designed
to filter out microscopic particles.
•Donot disconnect power by pulling cord. Todisconnect,grasp
the plug, not the cord.
•Unplug power cord at the machine when not in use and before
servicing.
To order go to Discount-Equipment.com

Page 3
TMC-7-I-0615
E-SPTS-I-0809
EQUIPMENTDEVELOPMENTCO.,INC.
Operator’s Instruction Manual
TMC-7
Table of Contents
Figure 1
Specifications ................................................................................................................ 3
How to Order Repair Parts............................................................................................ 3
Safety Guideline........................................................................................................ 2, 4
Operating Instructions ..............................................................................................5 - 7
Maintenance Instructions and Schedule........................................................................ 8
SMI Dust and Silica Warning......................................................................................... 9
Notes........................................................................................................................... 10
Limited Equipment Warranty............................................................... Inside Back Page
NOTE: Due to improvements your machine may not appear the same as the pictures in this manual.
Specifications & dimensions are for
reference only and subject to change.
Length (L) 40” 102 cm
Width (W) 24” 61 cm
Height (H) 38.5” 98 cm
Total Weight 120 lbs. 54.4 kg
Noise level lwa - 99 dB(A)
Noise level leq - 87 dB(A)
L
H
W
To order go to Discount-Equipment.com

Page 4
TMC-7-I-0615
EQUIPMENTDEVELOPMENTCO.,INC.
Read and understand all operating instructions
before operating this equipment.
Death or serious injury can result if this machine is used improperly.
Eye and ear protection must be worn at all times while the grinder is in use. During normal operation,
sound pressure levels may exceed 85dBA. Use onlyANSI approved safety glasses to help prevent
eye injury. Everyday eyeglasses have only impact resistant lenses; they are NOT safety glasses.
Operator must wear appropriate clothing and footwear. Do not wear loose clothing or jewelry that
can get tangled in moving parts. Footwear should provide sure footing and protection.
Materials being removed can be toxic or hazardous. A breathing respirator is required to help protect the oper-
ator from inhaling the airborne material when operating this machine.
• Inspect the work surface for cracks, uneven joints and foreign objects such as nails, screws and pipes. Damage
to the disc and/or equipment may result which can also cause serious injury to the operator. Hazardous areas
should be properly identified and clearly marked.
• The TMC-7 is designed to be controlled by a single operator .
• Inspect the discs carefully before installing. Do not use any questionable disc since serious personal injury and/
or damage to property can result.
• Never operate this grinder while under the influence of drugs, alcohol or when taking medications that impair the
senses or reactions, or when excessively tired or under stress.
• Be sure decals on the machine can be clearly read and understood. Replace worn or missing decals immediately,
Safety Guidelines
Safety warnings and guidelines do not by themselves eliminate danger.
They are not given as substitutes for proper accident prevention procedures and good judgement.
To order go to Discount-Equipment.com

Page 5
TMC-7-I-0615
E-SPTS-I-0809
EQUIPMENTDEVELOPMENTCO.,INC.
Operating Controls
About the TMC-7:
• The EDCO edge grinder is designed to be used in conjunction with other EDCO surface preparation products. It’s
small, lightweight construction allows the operator to grind close to obstacles.
These units are equipped with a single 7” diameter Diamond Segmented Disc that is an aggressive surface material
grinder for removing excess concrete, epoxy mortar, urethane coatings and overlays, and non-skid abrasive coatings on
steel, concrete, or polymer slab floors. A scarifier disc is optional. This machine is capable of either wet or dry grinding.
Before Starting:
• Before starting, perform a visual inspection of the entire machine. Be sure all fasteners are tight and
secure, check for signs of metal cracking or fatigue, inspect for damage. Be sure guards are in place, secure and
undamaged.
• Inspect diamond grinding disc. Check for loose or damaged diamond segments and replace if
necessary. Check that the diamond disc has been correctly mounted and be sure it is tight. Different
diamond/matrix discs wear at different rates. Be sure to use the correct diamond/matrix combination
for your specific application.
Figure 2
Switch Box
J
Electric Motor
Adjustable
Wheel Carriage Vacuum Port
Hood
Grease Fitting
Access Cap
Belt Lock Guard
Diamond Disc (Underneath)
Adjustable Handle
Gas Engine
Flat for Edge Grinding
Pivot Adjuster (head)
To order go to Discount-Equipment.com

Page 6
TMC-7-I-0615
EQUIPMENTDEVELOPMENTCO.,INC.
Operating Instructions
To Start Grinding:
• Operating the machine from the rear, push down, or if operating from the front,
lift the handle very slightly to shift some of the weight off of the disc, but do not
let the disc lift from the slab surface. The slight weight shift will aid in reaching
the operating speed without an excessive start-up power draw.
Once the unit reaches operating speed, allow the edger-grinder to settle
back down on the slab with the full weight on the disc.
• If the disc is out of balance, stop immediately and have the problem fixed or
damage to the equipment will result.
For Wet Grinding:
• Water is not necessary as a coolant but rather as a means of controlling dust. Lightly dampen the floor or use a
fine mist.
Do not use an excessive amount of water . Excess water on the surface will create a dangerous, slip-
pery surface and more work during cleanup.
• Sprinkle a small amount of sand on the slab to create a slurry during grinding. The slurry tends to keep the dia-
monds free from build up and the cutting edge exposed. If a squeaking sound is heard or the machine tends to
pull to one side, the diamond segments may have filled and are no longer grinding effectively. Discontinue use of
machine. Make sure the throttle is completely closed (full stop position) to insure the engine will not accidently fire
(kick back) when removing the disc which could cause bodily injury and/or damage to the machine. Then follow
the directions for replacing the diamond disc or optional scarifier disc.
For Dry Grinding:
Check materials being removed to determine if they are listed on an EPA hazardous substance list. A
breathing respirator is required to help protect the operator.
• The EDCO industrial VAC’s have available optional HEPA filter kits designed to be used when removing
hazardous materials. Standard, shop-vac style vacuums are not capable of extended operation. In addition,
these standard vacs use paper bag filters that can clog and overload the vacuum motor.
• Dry grinding creates a large volume of airborne dust. The edgers are equipped with a 1-1/2” vacuum port for
attaching a high volume industrial vacuum capable of removing particles to three microns. If the materials
involved are hazardous, or unknown and assumed hazardous, the operator must assume responsibility for the
proper handling and disposal of the hazardous material.
Note: Hazardous debris, including vacuum filters, must be disposed of properly according to OSHA and
government standards.
Figure 1
To order go to Discount-Equipment.com

Page 7
TMC-7-I-0615
E-SPTS-I-0809
EQUIPMENTDEVELOPMENTCO.,INC.
Figure 4Figure 3
Figure 6 Figure 7
Figure 2
Figure 5
Operating Instructions
For Edge Grinding:
• Loosenhandle lock knob and lifthandle until clear ofslots and pivotto desired position. Lockknob. Pull pin inrear deck
and turn deck to desired position. Release pin into locking hole.
Replacing the Diamond Grinding Disc:
• Disconnect from power source.
• To gain access to the disc, push down on the handle in the rear optional position and pivot the unit back on
the wheels until it comes to rest on the handle. (Figures 5)
• Remove plastic cap from belt cover (Figure 4). Place 9/16” socket on top of shaft. While holding ratchet on top, place 1 1/8”
socket on nut and remove. (Figure 3)
• Replace with a new disc and reverse the procedure. (Figure 3)
Inspect drive belt:
• Remove belt cover by removing 2 bolts. (Figure 6)
• Check belt tension. On new equipment, and after installing a new belt, the belt should be re-tensioned after the first
four hours of use. A damaged, stretched, or worn belt should be replaced with a new one.
(Figures 7 - Shown with belt cover removed.) Loosen motor mount bolts and push down slightly to tension belts.
Re-tighten motor mount bolts. Replace belt cover.
To order go to Discount-Equipment.com

Page 8
TMC-7-I-0615
EQUIPMENTDEVELOPMENTCO.,INC.
Maintenance
Make sure the the engine or motor are turned off before
performing any maintenance.
• All maintenance should be performed regularly and by qualified personnel only.
• Never work under equipment without first properly securing the equipment to prevent
it from moving or falling. Always work on a flat and level surface.
• Grease disc bearings every 4 hours of use. To access grease the fitting on the TMC-7 refer to (Figure 8).
These bearings are tapered roller bearings lubricated with High Temp Lubriplate No. 930-AA, or equivalent
bearing grease. Do not over lubricate. Be sure to clean up any excess grease after lubricating the
bearings. These bearings can occassionally require adjustment. If it is evident that these bearings need
adjustment they can be accessed by removing the belt over.
• Lubricate the wheel bearings from time to time with an occasional drop or two of oil to prevent binding.
• Proper belt tension must be maintained to transmit the motor power to the grinding disc.
Damage to the motor will occur and disc life shortened if belts are not kept at the
proper tension.
• Keep the Grinders clean. Be sure the safety decals are readable and properly maintained on the machine.
2 pumps every 2 months
Repairs are to be done
by authorized EDCO
Dealers only.
Read and follow
instructions in the engine
owner’s manual.
Quick Reference
For Maintaining
Grinders
Before
Each
Operation Daily After
Each
Use
As
Required
Engine Air FIlter (Gas) X
Visual Inspection of
Entire Machine X
Inspect Diamond Disc X
Grease Bearings X
Clean dust and dirt off
Machine X
Inspect Belt and Belt
tensioning XFigure 8
Grease Fittings
To order go to Discount-Equipment.com

Page 9
TMC-7-I-0615
E-SPTS-I-0809
EQUIPMENTDEVELOPMENTCO.,INC.
Grinding/cutting/drillingofmasonry,concrete,metalandothermaterials can generate dust, mists and fumescontaining chem-
icals known to cause serious or fatal injury or illness, such as respiratory disease, cancer, birth defects or other reproductive
harm. If you are unfamiliar with the risks associated with the particular process and/or material being cut or the composition
of the tool being used, review the material safety data sheets and/or consult your employer, the manufacturers/suppliers,
governmental agencies such as OSHA and NIOSH and other sources on hazardous materials. California and some other
authorities, for instance, have published lists of substances known to cause cancer, reproductive toxicity, or other harmful
effects.
Control dust, mist and fumes at the source where possible. In this regard use good work practices and follow the recom-
mendationsof the manufacturers/suppliers,OSHA/NIOSH, andoccupational andtrade associations. Watershould beused
for dust suppression when wet grinding/cutting/drilling is feasible. When the hazards from inhalation of dust, mists and
fumes cannot be eliminated, the operator and any bystanders should always wear a respirator approved by NIOSH/MSHA
for the material being used.
Grinding/cutting/drilling of masonry, concrete and other materials with silica in their composition may give off dust or mists
containingcrystalline silica. Silica isa basic componentof sand,quartz, brickclay, granite andnumerous other mineralsand
rocks. Repeated and/or substantial inhalation of airborne crystalline silica can cause serious or fatal respiratory diseases,
including silicosis. In addition, California and some other authorities have listed respirable crystalline silica as a substance
known to cause cancer. When grinding/cutting/drilling such materials, always follow the respiratory precautions mentioned
above.
SMI Dust and Silica Warning
To order go to Discount-Equipment.com

We sell worldwide for the brands: Genie, Terex, JLG, MultiQuip, Mikasa, Essick, Whiteman,
Mayco, Toro Stone, Diamond Products, Generac Magnum, Airman, Haulotte, Barreto, Power
Blanket, Nifty Lift, Atlas Copco, Chicago Pneumatic, Allmand, Miller Curber, Skyjack, Lull,
Skytrak, Tsurumi, Husquvarna Target, Stow, Wacker, Sakai, Mi-T-M, Sullair, Basic, Dynapac,
MBW, Weber, Bartell, Bennar Newman, Haulotte, Ditch Runner, Menegotti, Morrison, Contec,
Buddy, Crown, Edco, Wyco, Bomag, Laymor, EZ Trench, Bil-Jax, F.S. Curtis, Gehl Pavers, Heli,
Honda, ICS/PowerGrit, IHI, Partner, Imer, Clipper, MMD, Koshin, Rice, CH&E, General Equip-
ment ,Amida, Coleman, NAC, Gradall, Square Shooter, Kent, Stanley, Tamco, Toku, Hatz,
Kohler, Robin, Wisconsin, Northrock, Oztec, Toker TK, Rol-Air, APT, Wylie, Ingersoll Rand /
Doosan, Innovatech, Con X, Ammann, Mecalac, Makinex, Smith Surface Prep,Small Line,
Wanco, Yanmar
Discount-Equipment.com is your online resource for
commercial and industrial quality parts and equipment sales.
561-964-4949
visit us on line @ www.discount-equipment.com
TO PURCHASE THIS PRODUCT PLEASE CONTACT US
Select an option below to find your Equipment
Equipment Financing and
Extended Warranties Available
Other manuals for MAGNA-TRAP TMC-7
3
Other Edco Grinder manuals
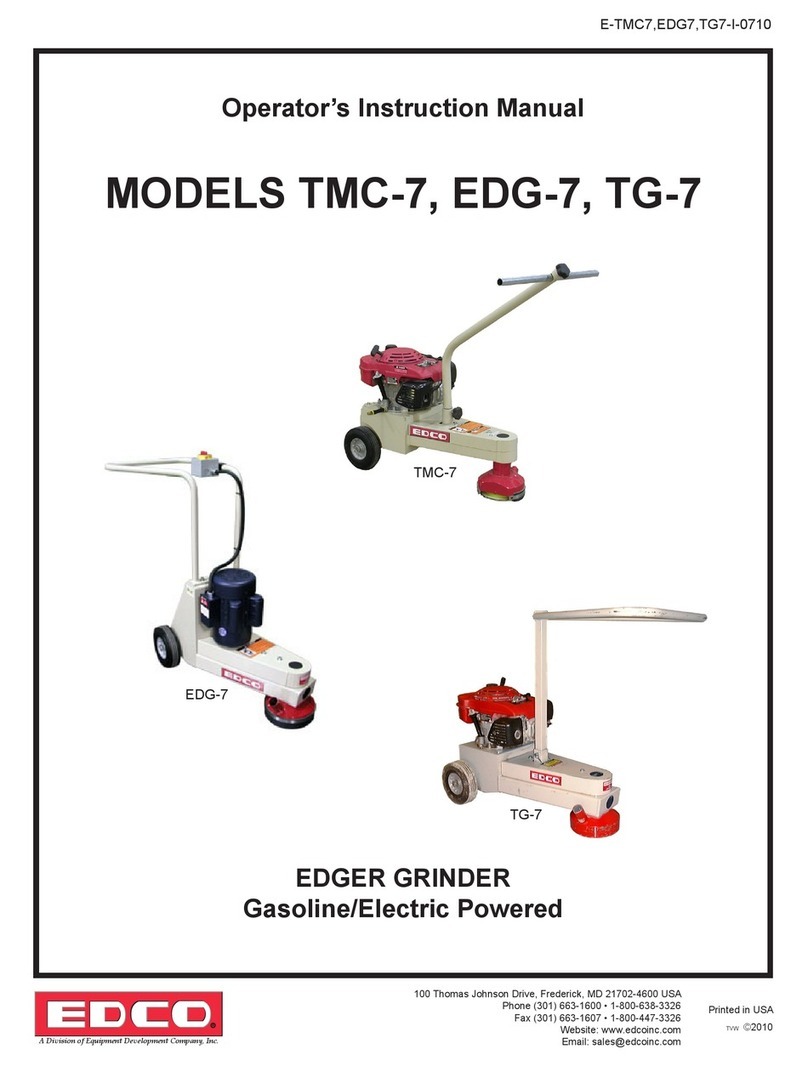
Edco
Edco MAGNA-TRAP TMC-7 Assembly instructions
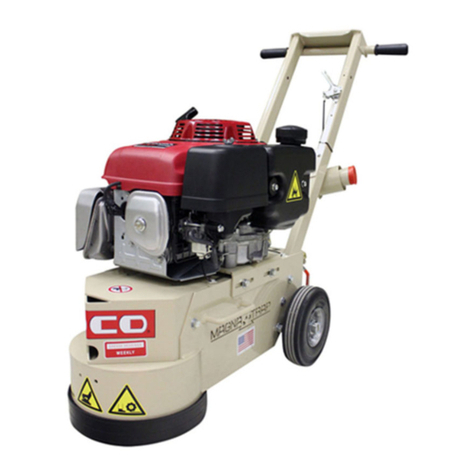
Edco
Edco TG-10 Assembly instructions
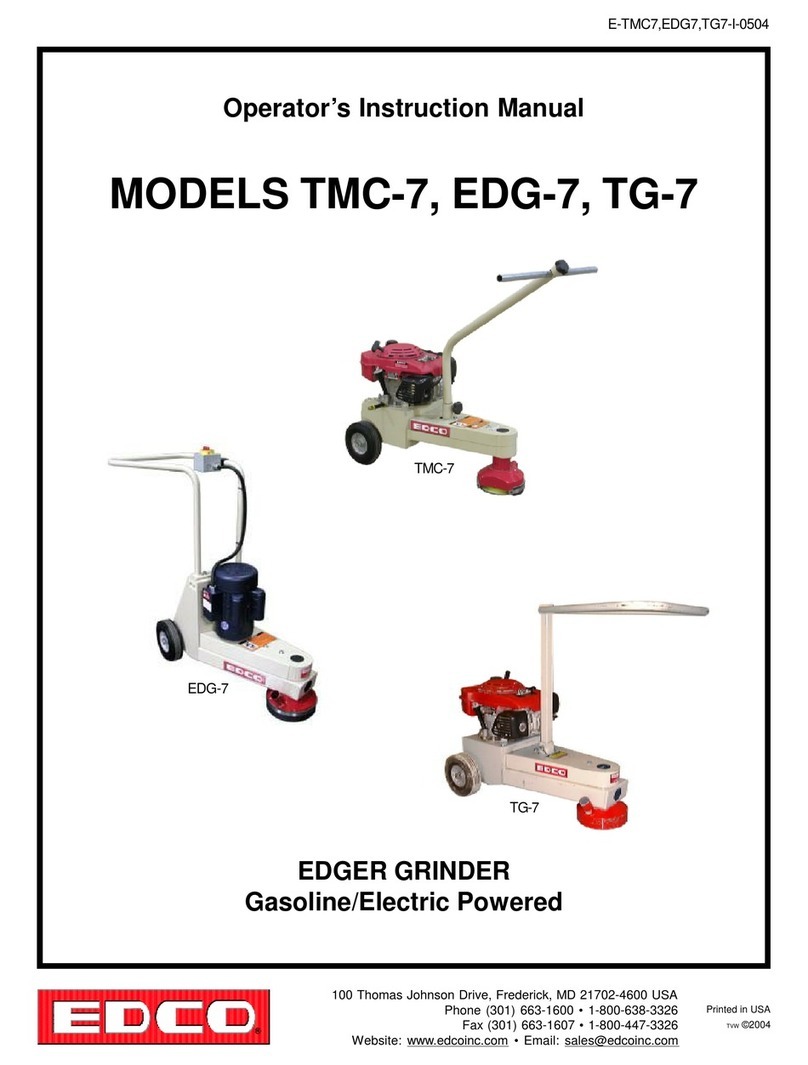
Edco
Edco MAGNA-TRAP TMC-7 Assembly instructions
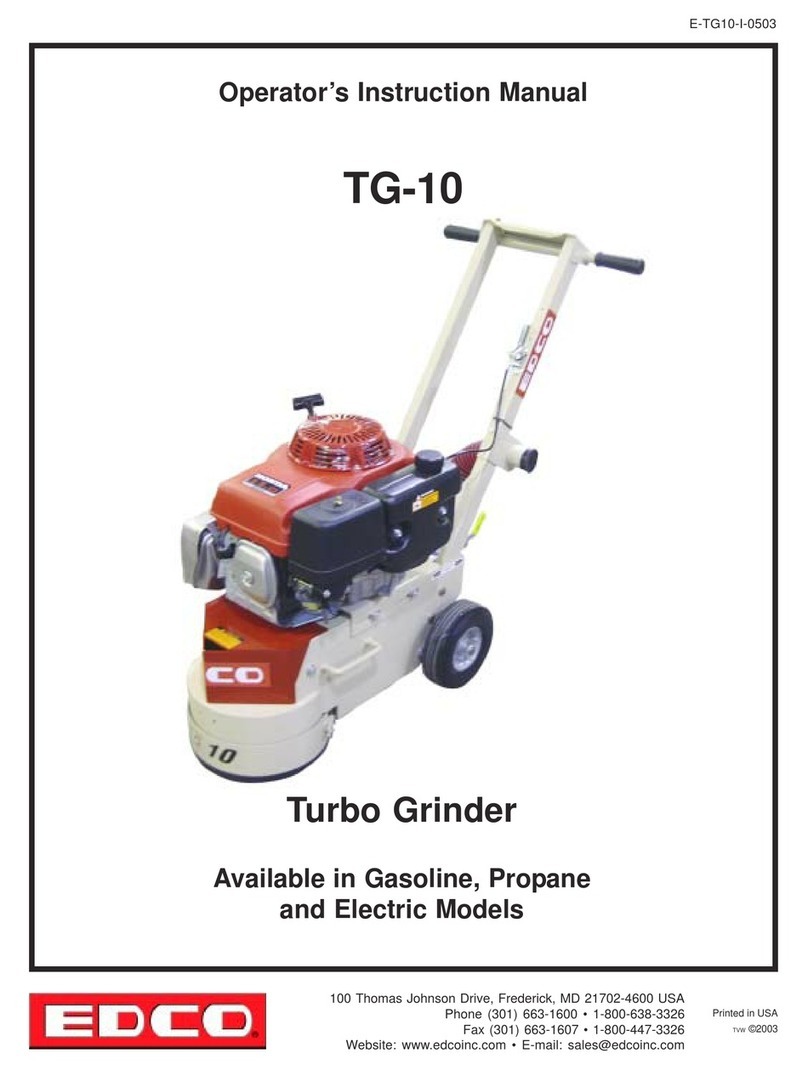
Edco
Edco TG-10 Assembly instructions
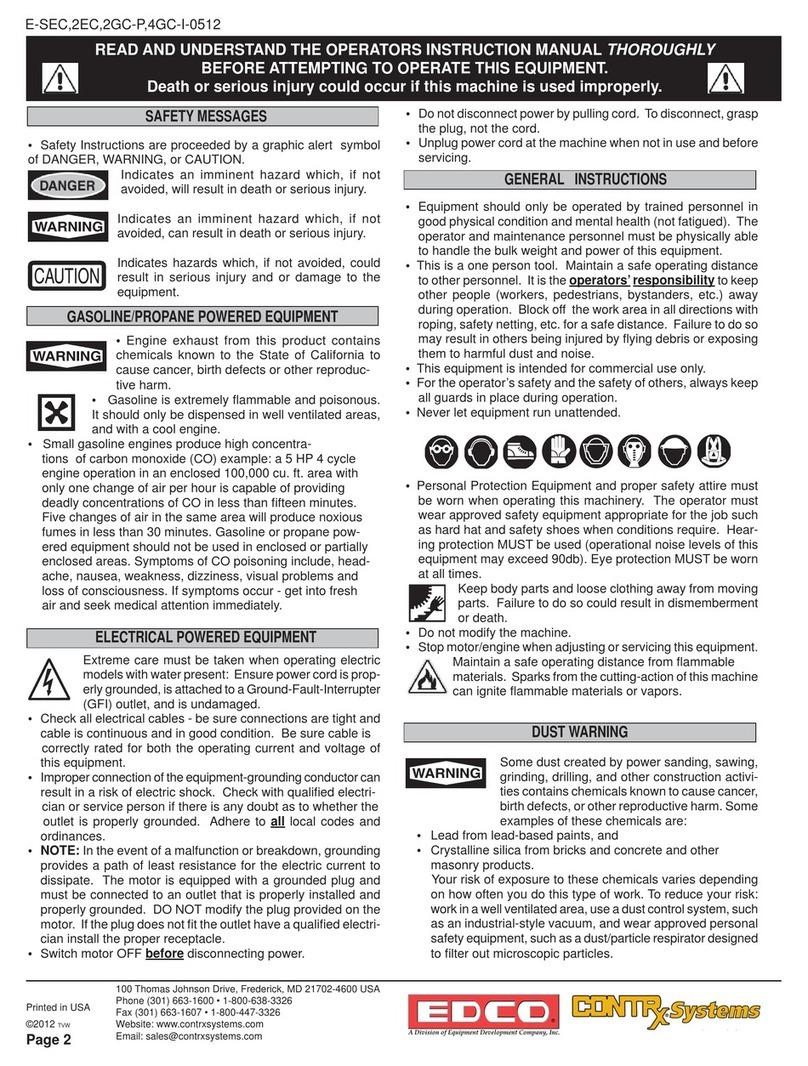
Edco
Edco 2-EC User manual
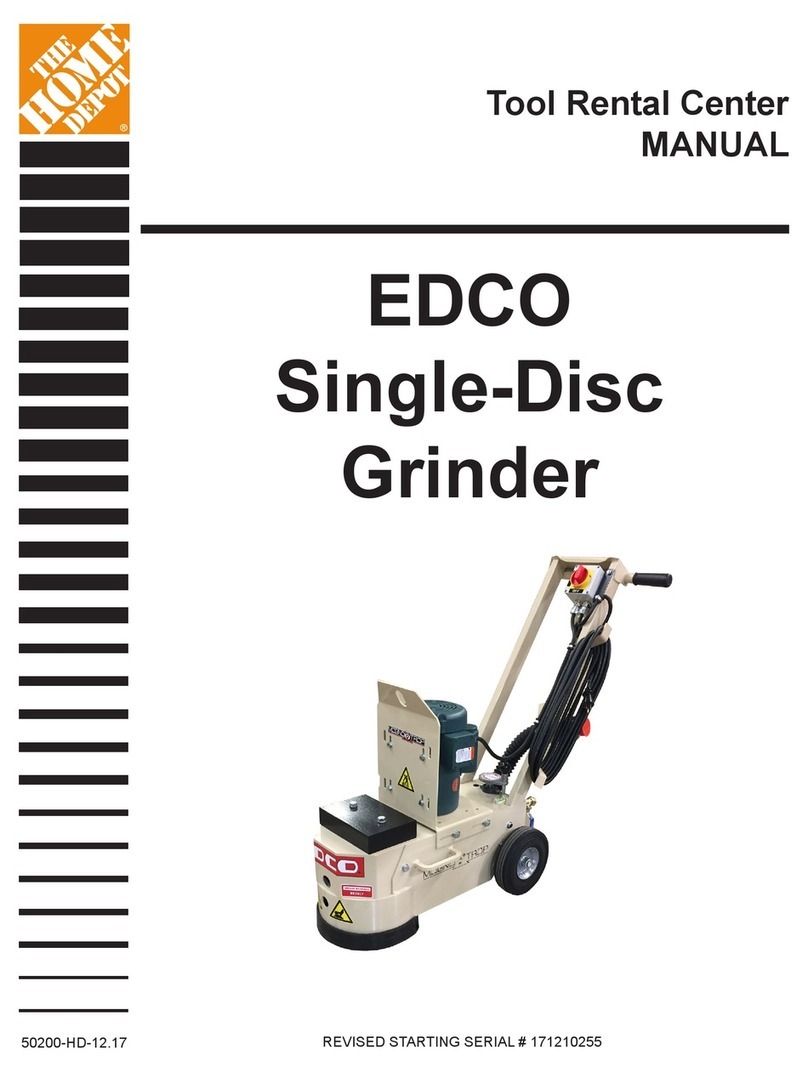
Edco
Edco SEC-HD User manual
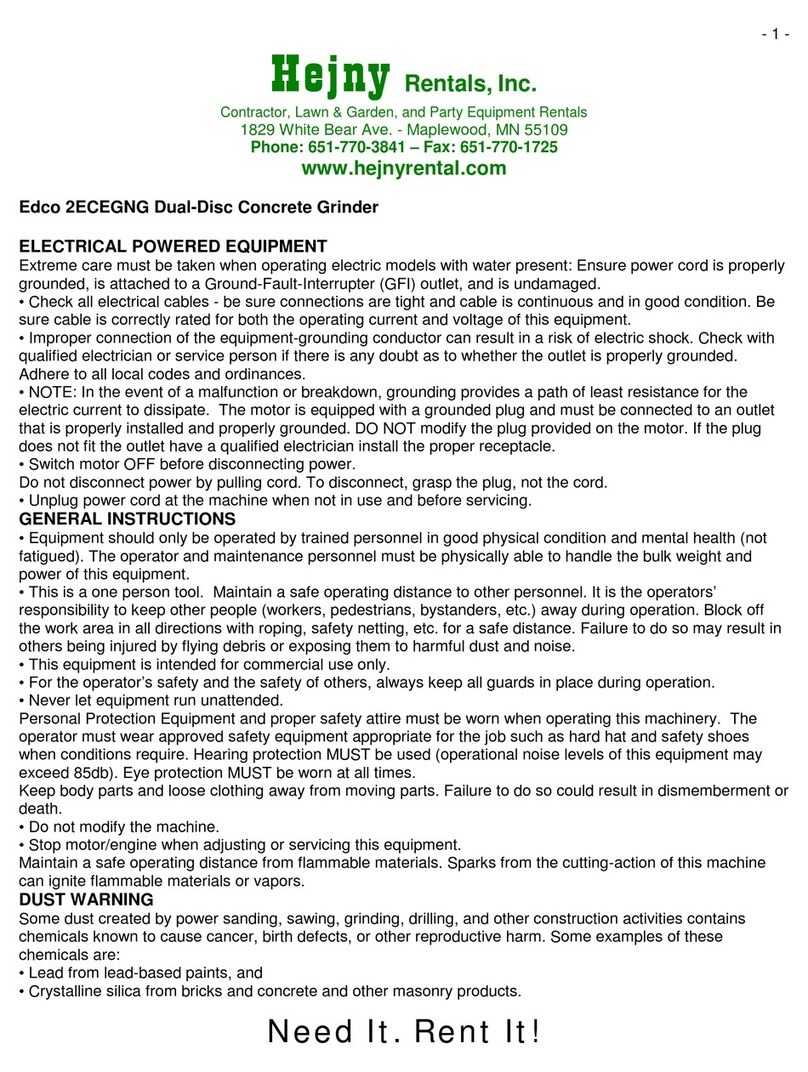
Edco
Edco 2ECEGNG User manual
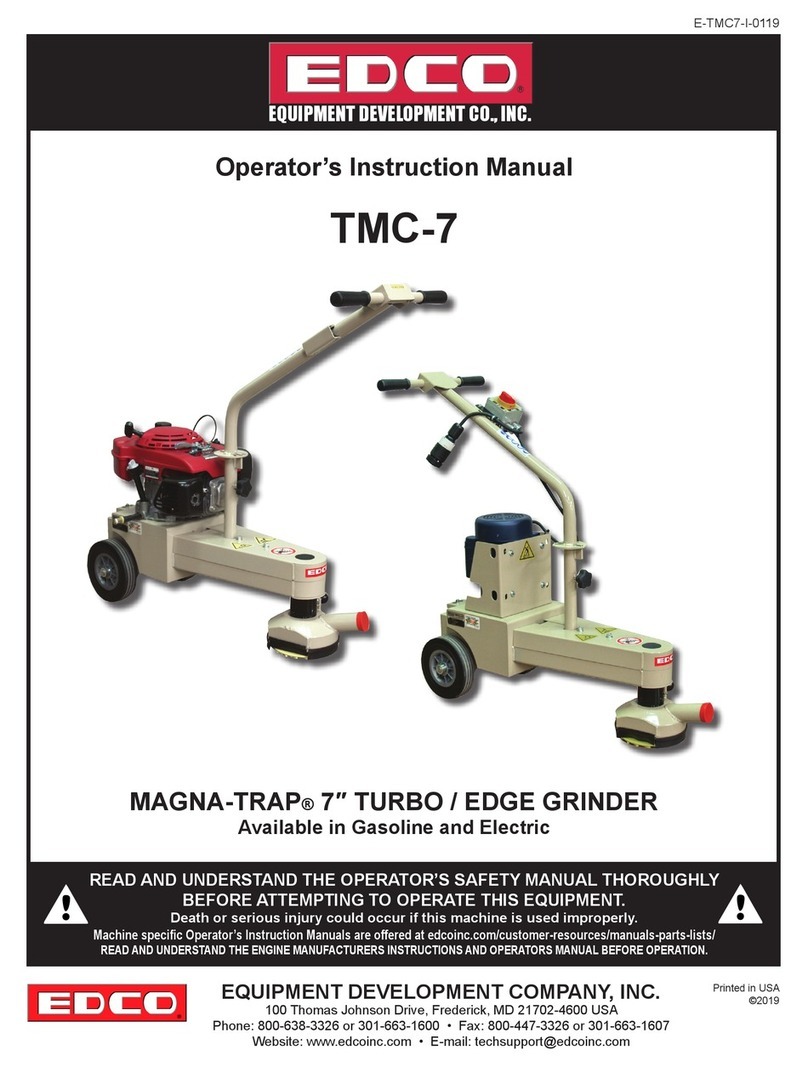
Edco
Edco MAGNA-TRAP TMC-7 Assembly instructions

Edco
Edco TG-10 Assembly instructions
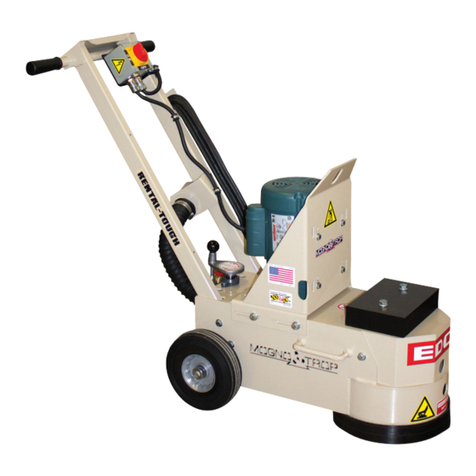
Edco
Edco SECNG-1.5L User manual