EMRI 3TX20 User manual

3TX20
Voltage regulator for generators
Instruction Manual V1.3.2
Product version V2.3.2.0

Manual V1.3.2 Page 2 of 20
Warnings And Commissioning information
-Check the isolation of the generator windings before installation.
Poor isolation will cause damage to the AVR and dangerous situations for persons.
- The system should not be installed, operated, serviced or modified except by qualified personnel who
understand the danger of electric shock hazards and have read and understood the user instructions.
- Never work on a LIVE generator. Unless there is another person present who can switch off the power
supply or stop the engine.
- Dangerous voltages are present at the voltage regulator board. Accidental contact with live conductors
could result in serious electrical shock or electrocution.
- Disconnect the power source before making repairs, connecting test instruments, or removing or
making connections to the voltage regulator or generator.
- Defects in the generator or AVR may cause consequential loss. Precautions must be taken to prevent
this from occurring.
- The unit should be installed with respect to the environmental specifications as well as the rules
mentioned in the General installation information.
- For safety reasons the voltage level potentiometers are best turned completely counter clockwise in
order to start at the lowest possible voltage.
- Never change the rotary switch or dipswitch settings during operation.
- Never apply supply voltage when generator is not running, unless exciter field is disconnected.
HAZARDOUS VOLTAGES.
DO NOT OPERATE WHEN NOT FAMILIAR WITH GENERATORS.
Revision history
Version Change
Product Hardware Manual
V2.0 2.0 First release
V2.1 2.0.1 1.1 Minor hardware update
The table provides a historical summary of the changes made to the AVR.
Revisions are listed in chronological order.
1.1
V2.2.0.0 2.1 1.2 New manual layout. Changed sensing range.
V2.3.0.0 2.2 1.3 Minor hardware improvement.
V2.3.1.0 2.2 1.3.1 Manual improved and added new dealer
V2.3.2.0 2.3 1.3.2 Minor hardware improvement.
The manual does not cover all technical details of the product. Specifications may be modified by
the manufacturer without notice. For further information, the manufacturer should be contacted.

Manual V1.3.2 Page 3 of 20
Table of contents
3
Absolute maximum ratings 4
Modes of control 8
Commissioning set up 10Quick reference
13Wiring diagrams 12
General installation information 19
Contact 20
…………………………………………………………………………………………General description …………………………………………………………………………………
...……………………..……………………………………………………………………
..…………..………....….…………..………………………………………………
……………………………….......…...……………………………………………………
………………………..…………………………………………………………………...
……………………………………………………………………………
……...……………..…………………………………………………………………………………
Protections 18……………………....….…………..……………………………………………………………
Tips and Suggestions 6………….……………………………………………………………………………
General description
The 3TX20 is designed for use in brushless generators and can be used as a cost effective
universal replacement for a great variety original manufacturers AVR’s.
The 3TX20 can be used for parallel operation with other generators that also control voltage droop
by means of Quadrature Droop Compensation (QDC).
Parallel operation is possible with an additional droop CT.
Installation, maintenance and adjustment don’t require special application software.
The AVR is protected from the environment by a PUR coating.
Mode of control
Contstant voltage control
Quadrature voltage droop for parallel operation
Generator phase loss Protection
User adjustable underspeed knee Communication
Underspeed LED

Manual V1.3.2 Page 4 of 20
Absolute maximum rating I
Symbol Min. UnitParameter Condition Max.
(1) Always mount with heatsink fins aligned vertically and allow for sufficient airflow.
(2) See formula for calculating minimum field resistance
(3) See page 5 for safe operation area of the AVR.
U, V, W Voltage sensing input
200Volt
50-60Hz, continuous. - 250 VAC
Voltage sensing input
300Volt
50-60Hz, continuous. - 400 VAC
50Hz, continuous.
50Hz, Intermitted < 10s.
60Hz, continuous.
60Hz, Intermitted < 10s.
-
-
-
-
450
480
500
520
VAC
VAC
VAC
VAC
400Volt
Voltage sensing input
+, - AVR field current - 25 ADC
Ω
(1) (3)
Field resistance -6.9
(2) (3)
12
@ 115VAC supply
@ 230VAC supply Ω-3.5
Intermitted < 10s.
@ 400VAC supply - Ω
5 - VAC
LH1, LH2 Supply input 13030 VAC
14030 VAC
26050 VAC
60Hz
50Hz
Minimum supply for self excitation
115V
28050 VAC
450110 VAC
480110 VAC
TAMB 95% RHD non condensingOperating temperature 0 +50 °C
TSTG 95% RHD non condensingStorage temperature 0 +70 %Static control accuracy 1 %
(1)
°C
X1, X2 Isolated CT < 30s.Droop CT 0.5A - 1 AAC
230V
400V
50Hz
50Hz
60Hz
60Hz
1 2 3 4 5
1 2 3 4 5
1 2 3 4 5
ON
1234
dip
5678
ON
1234
dip
5678
ON
1234
dip
5678
Field resistance (Ω) ≥Supply input x 0.9 (VDC)
30
Stresses above “Absolute Maximum Ratings” may cause permanent damage to the device.
This is a stress rating only, the functional operation of the device or any other conditions
indicated in the “operation area” of this specification is not implied. Exposure to maximum
rating conditions for extended periods may affect device reliability and lifetime.

Manual V1.3.2 Page 5 of 20
Absolute maximum rating II
Operating Area : Supply input 115V
Exciter Field Voltage = Supply input x 0.9 (VDC)
Exciter
Field
Voltage
(VDC)
Exciter Field Resistance Ω
20A
50V
0V
62.5V
25A
Safe operating area
5Ω
30A
6.3Ω
4.2Ω2.5Ω∞Ω
125V
75V
104V
3.5Ω
Field forcing < 1s.
Intermitted < 10s.
Operating Area : Supply input 230V
Exciter Field Voltage = Supply input x 0.9 (VDC)
Exciter
Field
Voltage
(VDC)
Exciter Field Resistance Ω
20A
100V
0V
125V
25A
Safe operating area
10Ω
30A
12.5Ω
8.4Ω5Ω∞Ω
250V
150V
207V
6.9Ω
Field forcing < 1s.
Intermitted < 10s.
Operating Area : Supply input 400V
Exciter Field Voltage = Supply input x 0.9 (VDC)
Exciter
Field
Voltage
(VDC)
Exciter Field Resistance Ω
20A
200V
0V
250V
25A
Safe operating area
18Ω
30A
22.5Ω
15Ω10Ω∞Ω
450V
300V
360V
12Ω
Field forcing < 1s.
Intermitted < 10s.

Manual V1.3.2 Page 6 of 20
Tips and Suggestions I
Precautions for large, slow running generators
In general large (>1000kVA), slow running (<900RPM) generators tend to have more inductive exciter
field windings. When the 3TX20 is used to control such a generator, the switched excitation current in
combination with the increased inductivity can cause voltage spikes on the field excitation output.
This can cause excessive AVR heating and damage to the AVR’s output stage. To reduce voltage
spikes it is recommended to fit RC-snubber in parallel and as close as possible to the exciter field.
Generator insulation- / polarization index test
As a rule of thumb the testing voltage used during an insulation test is two times the nominal voltage of
the winding under test. This exceeds the AVR ratings and may cause permanent damage to the AVR.
Therefore the AVR must be disconnected completely from the generator. When performing an
insulation test on the generator rotor disconnect the rotating rectifiers and any other components from
the windings under test. This will prevent damage should the testing voltage exceed the rectifiers
blocking voltage.
Field flashing
In case of a self excited generator it could be that the residual voltage level is too low to build up.
Causes for a low residual voltage can be a prolonged period of stand still, excessive heating or
mechanical shock and vibration.
To restore the residual voltage the generator can be manual field flashed. In order to perform this safely
the AVR must be completely disconnected from the generator. Next a potential free voltage
(e.g. a 9V battery block) source is connected to the exciter field of the generator, while it’s rotating.
This will cause the generator voltage to rise and restore the residual voltage level.
If the residual voltage of the generator is permanently low, an automatic field flash unit can be used or a
potential free voltage source which is automatically switched off when the generator voltage is within
normal range. The generator voltage should not exceed nominal voltage when field flash is active, to
prevent damage to the AVR. When using “Automatic field flash” there should always be a rectifier
bridge in the output of the source/unit.

Manual V1.3.2 Page 7 of 20
Tips and Suggestions II
Field flash with isolated battery
-
+
+
-
~
~
Disconnect @ Ugen > 50 Volt
ISOLATED
BATTERY
Voltage ≥ 1200V
Current ≥ Iexc.
RECTIFIER
Current limiting resistance
Choose the value to reach
50Vac generator voltage.
Exciter
Field
Stator
Rotor
-+
See wiring diagram
2 1
UVWN
400-450V / 50-60Hz 1
2
>450V / 60Hz
Options
VVPIFD FineCoarse
Dipswitch
LED
1 2 3 4 5
V
UX1W S TX2
LH2 - + LH1
ON
1234
dip
5678

Manual V1.3.2 Page 8 of 20
Modes of control I
Buildup (SE on/off)
Time à
Sensing voltage à
0V
Generator starting Voltage buildup Stable
Unom
Field
flash
Dip 1
Residual
voltage SE
Active
5V
Dipswitch 1 on : Self excited enabled.
ON
1234
dip
5678
Underspeed trip
Generator frequency à
Generator voltage à
0V
25Hz 45Hz
Unom
Dipswitch 8 on : Underspeed protection enabled.
Dip 8
F(Underspeed)
LED on
28%
Too low Underspeed setpoint or disabling protection may cause damage
to the generator or the AVR due to incorrect voltage / frequency ratio.
ON
1234
dip
5678
P/I control
Time à
Generator voltage à
Overshoot
Recovery time
prevent damage to the AVR and generator.
Turning the P/I control must be performed by a control specialist to
P(Prop. gain)
I(Integral time)
Generator Load à
Sensing voltage à
Unom
Droop
Inominal
D
more
capacitive
more
inductive
Voltage droop
0V0A
Droop range is Unom –3.5% @ cosphi 0,85 inductive.
(Droop)

Manual V1.3.2 Page 9 of 20
Modes of control II
Potentiometer S-T à
Sensing voltage à
0% (0Ω)
200V
-2.5%
0%
Remote adjust (Ω)
100%
1kΩ
0V
5kΩ-9%
Dip 2, 3 & 5
Maximum value at terminal S-T is 10kΩ.
Dipswitch 5 off : Remote adjust enabled.
Dipswitch 2 on and 3 off : 200V sensing voltage.
10kΩ-13%
Potentiometer S-T à
Sensing voltage à
0% (0Ω)
300V
-2.8%
0%
Remote adjust (Ω)
100%
1kΩ
0V
5kΩ-10%
Dip 2, 3 & 5
Maximum value at terminal S-T is 10kΩ.
Dipswitch 5 off : Remote adjust enabled.
Dipswitch 2 off and 3 on : 300V sensing voltage.
10kΩ-14%
ON
1234
dip
5678
ON
1234
dip
5678
Potentiometer S-T à
Sensing voltage à
0% (0Ω)
400V
-3.3%
0%
Remote adjust (Ω)
100%
1kΩ
0V
5kΩ-11%
Dip 2, 3 & 5
Maximum value at terminal S-T is 10kΩ.
Dipswitch 5 off : Remote adjust enabled.
Dipswitch 2 off and 3 off : 400V sensing voltage.
10kΩ-15.5%
ON
1234
dip
5678
Isolated supply voltage à
Sensing voltage à
-10V 0V +10V
Unom
Rx = 100kΩ
Rx = 10kΩ
Remote adjust (Vdc) Dip 2, 3 & 5
0%
Dipswitch 5 off : Remote adjust enabled.
Select sensing voltage with dipswitch 2 and 3.
1kΩ
+
-
S T
Isolated supply
(-10V .. +10V)
Rx
Range
Rx Unom = 200V Unom = 300V Unom = 400V
10kΩ
20kΩ
47kΩ
100kΩ
11.5%
6.2%
2.7%
1.5%
13.3%
6.6%
3.0%
1.3%
14.0%
7.5%
3.5%
1.7%
ON
1234
dip
5678

Manual V1.3.2 Page 10 of 20
Quick reference I
Minimum Rfield
Formula
Minimum field resistance
Factory settings
Sensing voltage
Underspeed frequency
Droop
Stability P-action
Stability I-action
Dipswitch 1
Dipswitch 2
Dipswitch 3
Dipswitch 4
Dipswitch 5
Dipswitch 6
Dipswitch 7
Dipswitch 8
: 400V
: 47Hz
: 100%
: 50%
: 50 %
: On
: Off
: Off
: Off
: On
: Off
: Off
: On
AVR field current.
Max. rating: Intermitted 25A < 10s.
Max. rating: Field forcing 30A < 1s.
Dipswitch
Self excited disabled.
DIP Off On
Self excited enabled.1
2
3
4
5
6
7
8
Phase loss protection disabled.
Remote adjust enabled.
Not used.
Not used.
Underspeed protection disabled.
Phase loss protection enabled.
Not used.
Not used.
S-T internally shorted.
Underspeed protection enabled.
(Page 8, 9)
Droop
(Page 8)
D
0% 100%
Underspeed
(Page 8)
F
LED
+ -
Stability
(Page 8)
I P
- + - +
I-action
(Integral time) P-action
(Proportional gain)
Voltage
V V
- + - +
FineCoarse
Trip @
Higher –RPM - Lower
+/- 65Hz +/- 33Hz
Field resistance (Ω) ≥Supply input x 0.9 (VDC)
30
See : Sensing range
When potentiometers in mid position.
Voltage is +/- 195V @ sensing range 200V
Voltage is +/- 305V @ sensing range 300V
Voltage is +/- 390V @ sensing range 400V
Sensing range
Dip 2 on & Dip3 on
Range +/- 95 .. 140V
115V
200V
300V
400V
Dip 2 on & Dip3 off
Range +/- 160 .. 250V
Dip 2 off & Dip3 on
Range +/- 250 .. 400V
Dip 2 off & Dip3 off
Range +/- 315 .. 510V
ON
1234
dip
5678
ON
1234
dip
5678
ON
1234
dip
5678
ON
1234
dip
5678
ON
1234
dip
5678

Manual V1.3.2 Page 11 of 20
Quick reference II
Sensing
U-V-W clockwise
Remote adjust
1kΩ
+
-
Max. value : 10K Max. : -10V..+10V
S T
Isolated supply
(-10V .. +10V)
Rx (10kΩ ..100kΩ)
Dipswitch 5 off Dipswitch 5 off
S T
0..10kΩ
Gnd
Rx
Current sensing
X1 X2
Input X1-X2
CT 0.5A
(Droopkit)
Max. rating :
Continuous : 0.5Aac
Intermitted : 1Aac < 10s.
Exciter
0 .. 20Adc
Check
Formula
Minimum
Field Resistance
(Page 4, 10)
Max. rating:
Intermitted 25A < 10s.
Field forcing 30A <1s.
Exciter Field
+_
- +
V phase
0.5A
200V 300V 400V
AVR supply configuration (Page 13..17)
Supply 115V Supply 230V Supply 400V
W
V
U
N
W
V
U
N
W
V
U
N
1 2 3 4 5
LH2 - + LH1
LH2 - + LH1
LH2 - + LH1
1 2 3 4 5
1 2 3 4 5
Supply range :
110..450V @ 50Hz
110..480V @ 60Hz
Field resistance:
@ 400V ≥ 12.0Ω
@ 450V ≥ 13.5Ω
@ 480V ≥ 14.5Ω
Supply range :
50..260V @ 50Hz
50..280V @ 60Hz
Field resistance:
@ 230V ≥ 7.0Ω
@ 260V ≥ 8.0Ω
@ 280V ≥ 8.5Ω
Field resistance:
@ 115V ≥ 3.5Ω
@ 130V ≥ 4.0Ω
@ 140V ≥ 4.5Ω
Supply range :
30..130V @ 50Hz
30..140V @ 60Hz
ON
1234
dip
5678
ON
1234
dip
5678
ON
1234
dip
5678
Fuse 20AT/500V
(10.3x38.1mm)
Ø5,5
6.5 6.5130
10
10
140
ON
1234
dip
5678
Options
VVPIFD FineCoarse
Dipswitch
LED
1 2 3 4 5
V
UX1W S TX2
LH2 - + LH1
20
- Measurements in mm.
- Size is 143mm x 180mm.
- Height is +/- 115mm.
- Weight is +/- 2.1Kg.
Product information

Manual V1.3.2 Page 12 of 20
Commissioning set up
Commissioning set up
Start (AVR Active / Generator running ! )
Underspeed protection
Done
Threshold underspeed
FSlowly
Until led on
Setpoint underspeed
FVery slowly
Until led off
Led not red flickering!
Nominal speed
GM
Note:
It is recommended to turn
the potentiometer a little
further clockwise,
to allow for short
frequency dips.
Indication setpoints
+/- 56Hz
O
O
+/- 47Hz

Manual V1.3.2 Page 13 of 20
Wiring diagram I
AVR with 115V supply : Transformer
RC-NETWERK
400-450V / 50-60Hz
Phase sequence:
U,V,W
Exciter
Field
Stator
Rotor
Droopkit
UVW
S1 P1
-+
N
Gnd
0..10kΩ
Recommended
1
2
Ugen 400-450V / 50-60Hz
1 2 3 4 5
Supply selection
1Ugen > 450V / 60Hz
1 2 3 4 5
Supply selection
2
>450V / 60Hz
12
xxxV
115V
Options
VVPIFD FineCoarse
Dipswitch
LED
1 2 3 4 5
V
UX1W S TX2
LH2 - + LH1
ON
1234
dip
5678

Manual V1.3.2 Page 14 of 20
Wiring diagram II
AVR with 115V supply : ½ phase –neutral
400-450V / 50-60Hz
Phase sequence:
U,V,W
Exciter
Field
Stator
Rotor
Droopkit
UVW
S1 P1
-+
N
Gnd
0..10kΩ
½ ~
½ ~
½ ~
½ ~
½ ~
½ ~
1
2
Ugen 400-450V / 50-60Hz
1 2 3 4 5
Supply selection
1Ugen > 450V / 60Hz
1 2 3 4 5
Supply selection
2
>450V / 60Hz
12
RC-NETWERK
Recommended
Options
VVPIFD FineCoarse
Dipswitch
LED
1 2 3 4 5
V
UX1W S TX2
LH2 - + LH1
ON
1234
dip
5678

Manual V1.3.2 Page 15 of 20
Wiring diagram III
AVR with 200V supply : ½ phase –½ phase
400-450V / 50-60Hz
Phase sequence:
U,V,W
Exciter
Field
Stator
Rotor
Droopkit
UVW
S1 P1
-+
N
Gnd
0..10kΩ
½ ~
½ ~
½ ~
½ ~
½ ~
½ ~
>450V / 60Hz
RC-NETWERK
Recommended
Options
VVPIFD FineCoarse
Dipswitch
LED
1 2 3 4 5
V
UX1W S TX2
LH2 - + LH1
ON
1234
dip
5678

Manual V1.3.2 Page 16 of 20
Wiring diagram IV
AVR with 230 supply : phase –neutral
400-450V / 50-60Hz
Phase sequence:
U,V,W
Exciter
Field
Stator
Rotor
Droopkit
UVW
S1 P1
-+
N
Gnd
0..10kΩ
1
2
Ugen 400-450V / 50-60Hz
1 2 3 4 5
Supply selection
1Ugen > 450V / 60Hz
1 2 3 4 5
Supply selection
2
>450V / 60Hz
12
RC-NETWERK
Recommended
Options
VVPIFD FineCoarse
Dipswitch
LED
1 2 3 4 5
V
UX1W S TX2
LH2 - + LH1
ON
1234
dip
5678

Manual V1.3.2 Page 17 of 20
Wiring diagram V
AVR with 400V supply : phase –phase
400-450V / 50-60Hz
Phase sequence:
U,V,W
Exciter
Field
Stator
Rotor
Droopkit
UVW
S1 P1
-+
N
Gnd
0..10kΩ
>450V / 60Hz
Use this connection diagram only upon
low current and/or higher voltage exciter value’s.
Ask the manufacturer when in doubt.
Recommended to use stepdown transformer
xxxV:115V or xxxV:230V for AVR supply.
RC-NETWERK
Required
Options
VVPIFD FineCoarse
Dipswitch
LED
1 2 3 4 5
V
UX1W S TX2
LH2 - + LH1
ON
1234
dip
5678

Manual V1.3.2 Page 18 of 20
Protections
Phase loss protection
Default the phase loss protection is disabled.
Dip 4
The phaseloss protection validates the presence of all three generator phases on the sensing
terminals U, V and W . When one of the three phases is not sensed anymore for more than 300ms
the AVR decreases the generator voltage setpoint to +/- 40% of Unom. If the error condition is
relieved for 5s, the generator voltage is ramped up again to nominal voltage.
Sensing
voltage
Generator
phase
U, V or W 0V
-Vpeak
Vpeak
Unom
40%
<0.3S >0.3S 5S
ON
1234
dip
5678
Fuse protection
When replacing the fuse, a 20A/500V slow type fuse with dimensions 10.3 x 38.1mm must be used.
To prevent consequential damage in case of an AVR or generator failure, the AVR supply is fused by
a 20A slow fuse.
Blowing the fuse will interrupt the field excitation output and causes the generator to de-excite.
Fuse
UVWX1X2ST

Manual V1.3.2 Page 19 of 20
General installation information
Absolute Maximum Ratings
- The Absolute Maximum Ratings are those limits for the device that, if exceeded, will likely damage the device. Exceeding the
absolute maximum ratings voids any warranty and/or guarantee.
Mounting
Mounting of the product should be done in such a way that:
-the absolute maximum ambient temperature rating of the product will never be exceeded.
-maximum cooling (direction of cooling ribs and direction of airflow) is achieved.
-Mounting no humid air can flow through the product or condensation occurs.
-dust or other materials or residue will not remain in or on the product.
-the maximum vibration is not exceeded.
-personal contact with persons is impossible.
Wiring
-Diameter size of the wiring should be enough to carry the expected current. Wire insulation should be enough to withstand
the expected operating voltages and temperatures.
-To improve EMC emission and immunity, care should be taken for the lay out of the wiring. This in respect to all wiring in the
installation.
-Keep current carrying wires as short as possible.
-Keep wires carrying a total sum of zero Ampere close to each other, or in one single cable, E.g. U, V, W, or X (+) and XX (-),
or Phase and neutral, or S and T.
-Avoid current carrying conductors next to sensing or control wiring. Especially current controlled by SCR’s or PWM controlled
transistors.
-If sensitive sensing signal cables need to be laid across distance along other cabling, shielded cable is preferred. Keep the
shield as long as possible and the wiring outside the shield as short as possible. Do not solder or shrink the shield to a
regular wire. Connect the original shield to ground at one side with an as large as possible contact surface.
Additional installation information
- When the product is supplied by means of a transformer, it should never be an auto-transformer. Auto-transformers react as
voltage sweep up coil and may cause high voltage peaks.
-Standard fit capacitors or over-voltage suppressers across X (+) and XX (-), or exciter field terminals inside the generator
should be removed.
-When the product is supplied by means of a transformer, it should be able to carry at least the maximum expected current.
Advisable is, to have a transformer which can carry twice the maximum expected current. Inductive loads make voltage sacks
and peeks into the secondary voltage of a transformer, from which the device may malfunction.
-It is not recommended to apply switches in dc outputs. It is preferred to use switches in the ac supply inputs of devices. In
case it is unavoidable to have switches in the dc output of a device, action must be taken to avoid over voltage damage to the
device due to contact arcing. Use a voltage suppressor across the output.
-It is not recommended to apply switches or fuses in the sensing lines. Defects can cause high voltage situations due to over-
excitation.
-When using a step down transformer in medium or high voltage generators, the transformer should be three phase (if three
phase sensing), and the transformer should be suitable for acting as a sensing transformer. If the transformer is unloaded,
connect a resistor to avoid voltage waveform distortion.
-The phase relation from the generator to the AVR is important. Also when voltage transformers and/ or current transformers
are installed.
-When using a step down or insulation transformer in the droop circuit, phase relation from the generator to the AVR is
important.
-CT’s wiring, connected to the AVR should never be grounded.
-Always disconnect electronic products, circuits and people before checking the insulation resistance (Megger check).
-Due to differences in generators impedance’s, EMC behavior is not predictable. Therefore the commissioner / installer should
be aware of proper and correct installation.
-Large, highly inductive, exciter stator windings can cause destructive high voltage peaks. Adding a resistor from 10 to 20
times the exciter stator field resistance reduces voltage spikes. If necessary filter can be fitted additionally. (e.g. snubber, RC-
network)
-Upon problems during commissioning, faulty behavior or defects in the generator, consult the fault finding manual at our web
site
-Some advises may be overdone or seem extraordinary, but since the electrical rules are the same everywhere, these advises
are given.

Manual V1.3.2 Page 20 of 20
Contact
EMRI Electronics B.V. Manufacturer
Morsestraat 10
6716 AH, Ede, Netherlands
Tel: +31 (0)318 620 427
Website: www.emri.nl
E-mail: [email protected]
ICELAND, Hafnarfjordur
Rafeining ehf
Tel: +354 565 3049
Fax: +354 565 3048
Website: www.rafeining.is
E-mail: [email protected]
POLAND, Gdynia
An-Elec Sp. z o.o.
Tel: +48 58 668 44 00
Fax: +48 58 668 44 66
Website: http://an-elec.pl
E-mail: [email protected]
INDIA, Faridabad
Power Solutions
Tel: +91 9868907903
Fax:: +91 129 2431216
Website: www.psolindia.com
E-mail: [email protected]
SOUTH AFRICA, Roodepoort
Yneldo Electronics
Tel: +27(0)117637053
Fax: +27(0)117634212
Website: www.yneldo.com
E-mail: [email protected]
POLAND, Szczecin-Mierzyn
Marel Serwis
Tel: +48 91 48 58 388
Fax: +48 91 48 79 948
Website: www.marel.szczecin.pl
E-mail: [email protected]
CHILE, Santiago
Lucio Vicencio y CIA.LTDA
Tel: +1-281-334-2904
Fax:: +1-832-221-5642
Website: www.luciovicencio.cl
E-mail: [email protected]
NORWAY, Bergen
Frydenbø Electric A/S
Tel: +47 55 34 91 00
Fax: +47 55 34 91 10
Website: www.frydenbo.no
E-mail: [email protected]
SINGAPORE, Singapore
Cyclect Electrical Engineering
Tel: +65 6868 6013
Fax: +65 6863 6260
Website: www.cyclect.com.sg
E-mail: [email protected]
THAILAND, Bang Lamung
Semtec Maritime/Genetech Co.Ltd
Tel: +66 38301262
Fax: +1-832-221-5642
Website: semtecmaritime.com/
Email: [email protected]
UNITED ARAB EMIRATES, Sharjah
KDU Technical Services
Tel: +971-6-5575480
Fax: +971-6-5575490
Website: www.kdutech.ae
E-mail: [email protected]
SWEDEN, Kungälv
Elektrisk Drivteknik EDT AB
Tel: +46-705-28 20 60
Tel: +46-709-50 47 90
Website: www.edtab.se
E-mail: [email protected]
GREECE, Piraeus
Stavros Kassidiaris S.A.
Tel: +30 210 4636000
Fax: +30 210 4624471
Website:www.kassidiaris.gr
E-mail: [email protected]
CANARY ISLANDS, Las Palmas
Zamakona Yards
Tel: +34 928467521
Fax: +34 928461233
Website: www.zamakonayards.com/
E-mail: [email protected]
UNITED KINGDOM, Stockton on Tees
MJR Controls
Tel: +44 1642 762 151
Fax: +44 1642 762 502
Website: www.mjrcontrols.com
Email: [email protected]
UNITED STATES, Kemah - Texas
Ramtec Marine Systems LLC
Tel: +1-281-334-2904
Fax: +1-832-221-5642
Website: www.ramtec-marine.com
Email: [email protected]
REPUBLIC OF PANAMA, Panama
PASRAS S.A.
Tel: +507 3140095
Fax: +507 3140094
Website: www.pasras.com
E-mail: [email protected]
ROMANIA, Constanta
SAMTEC SRL
Tel: +40 241 517 047
Fax: +40 241 517 047
Website: www.samtec.ro
E-mail: [email protected]
UNITED KINGDOM, Cheadle Hulme
TGS Total Generator Solutions Ltd
Tel: +44161 8188720
Fax: +447754677963
Website: http://totalgeneratorsolutions.com
Email: sales@totalgeneratorsolutions.com
POLAND, Szczecin
MARCONTREL
Tel: +48 91 4 888 474
Fax: +48 91 4 888 475
Website: www.marcontrel.com
E-mail: [email protected]
Other manuals for 3TX20
1
Table of contents
Other EMRI Controllers manuals
Popular Controllers manuals by other brands
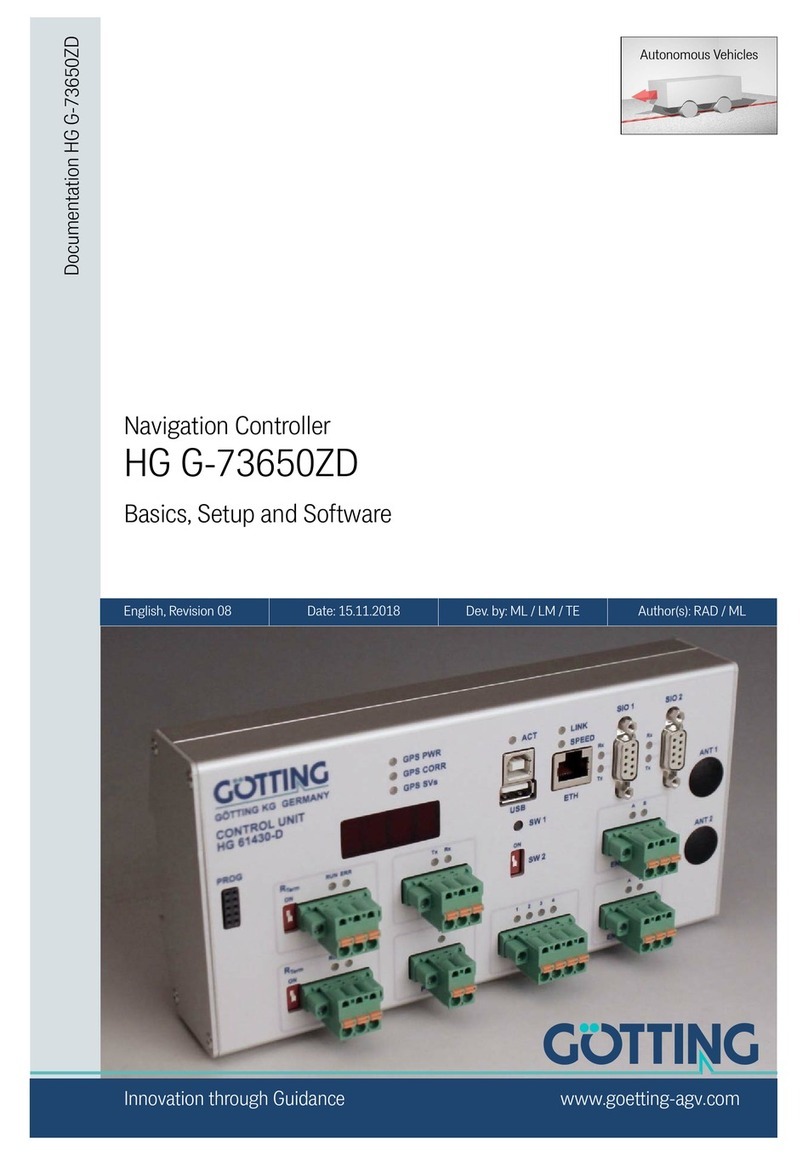
Gotting
Gotting HG G-73650ZD Basics, Setup and Software
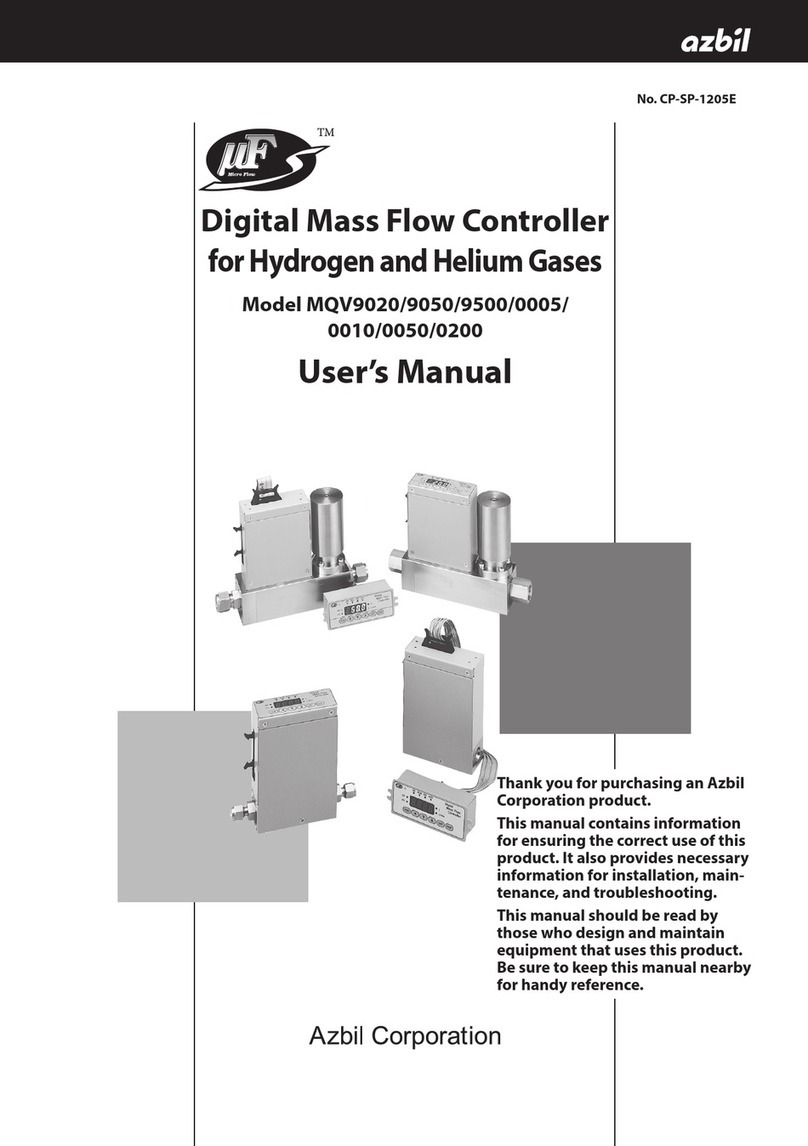
Azbil
Azbil Micro Flow MQV9020 user manual
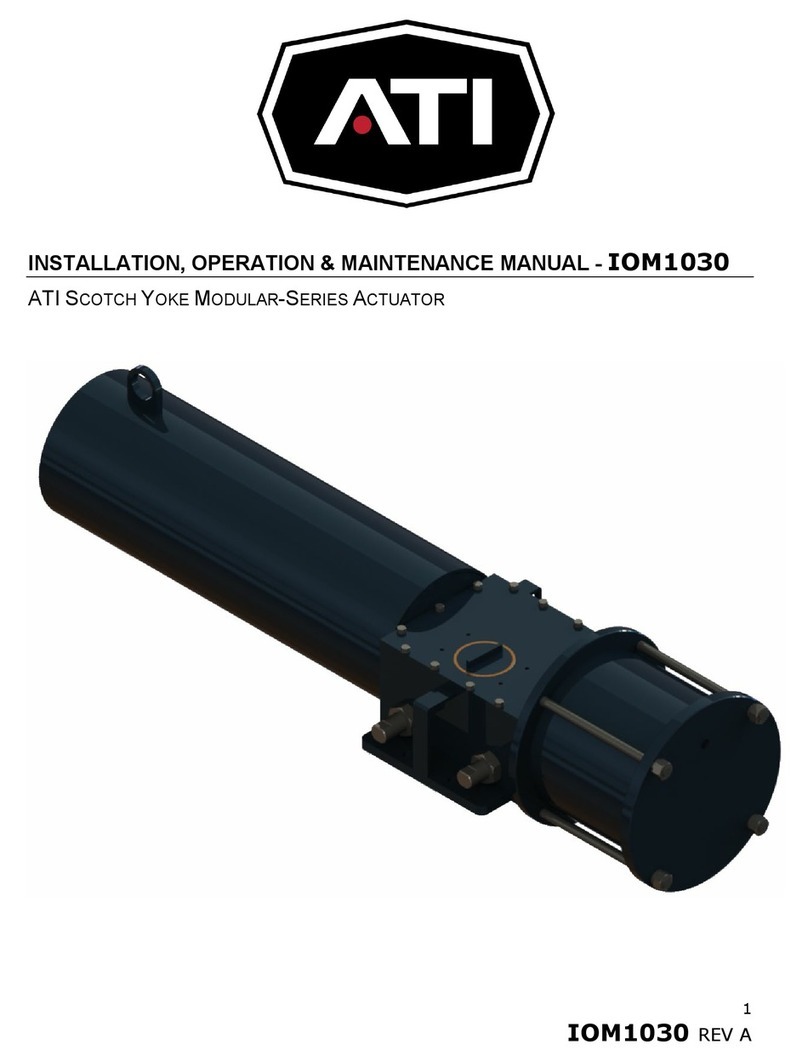
ATI Technologies
ATI Technologies IOM1030 Installation, operation & maintenance manual
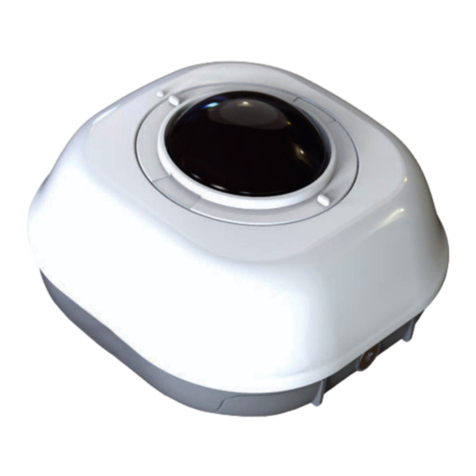
EVERSPRING
EVERSPRING AC134 user manual

Viconics
Viconics VTR8300 Series User Interface Guide
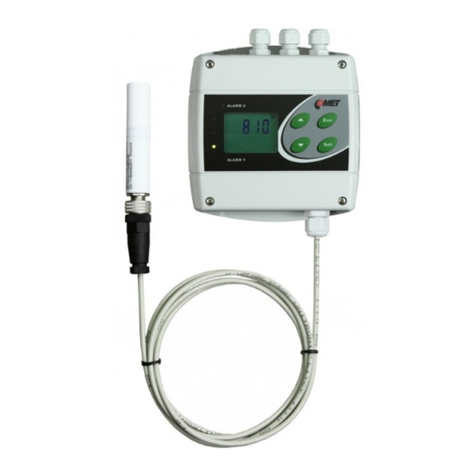
Comet
Comet H5021 instruction manual
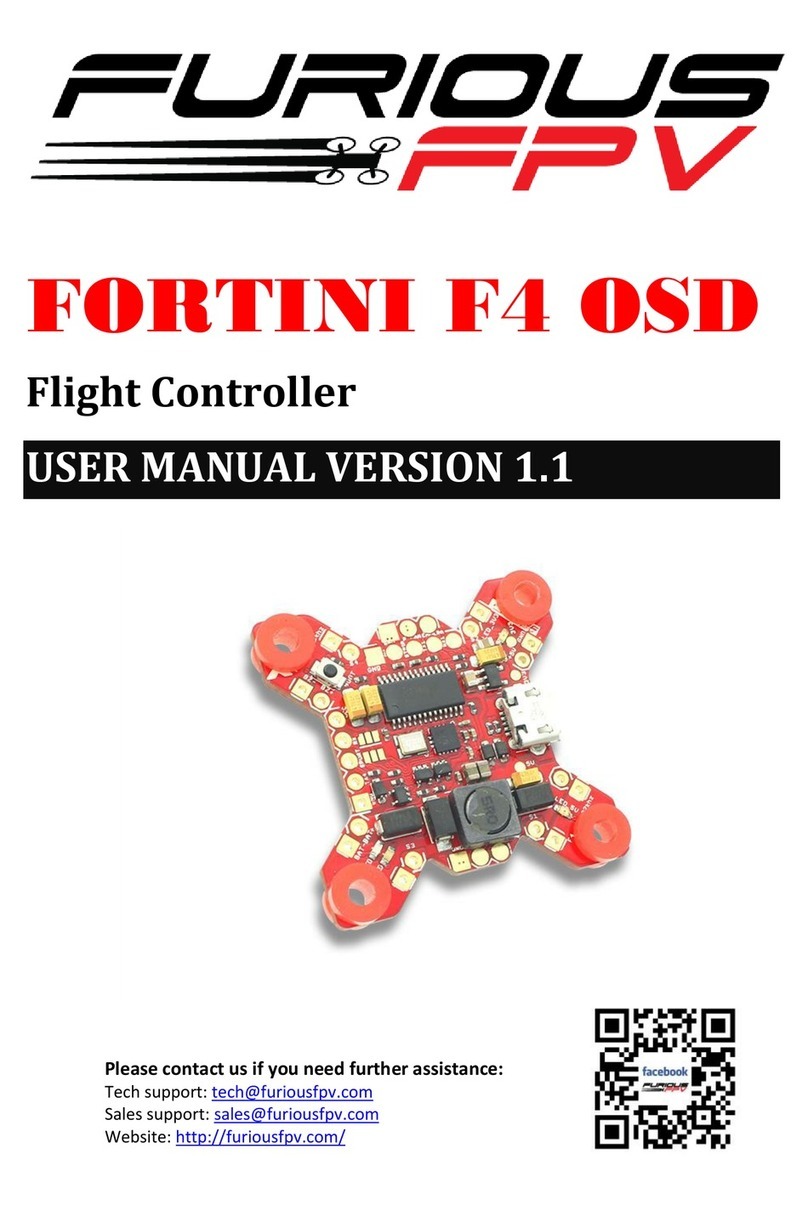
Furious FPV
Furious FPV Fortini F4 OSD user manual
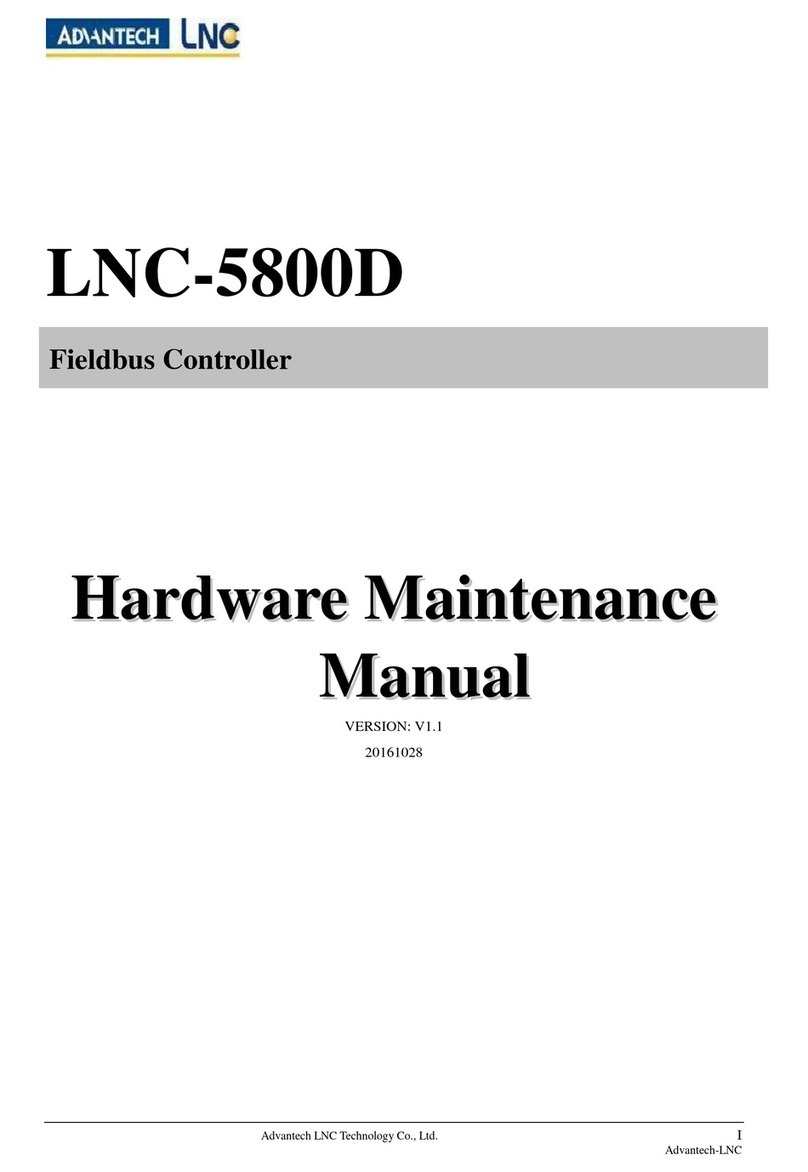
Advantech
Advantech LNC-5800D Hardware Maintenance Manual
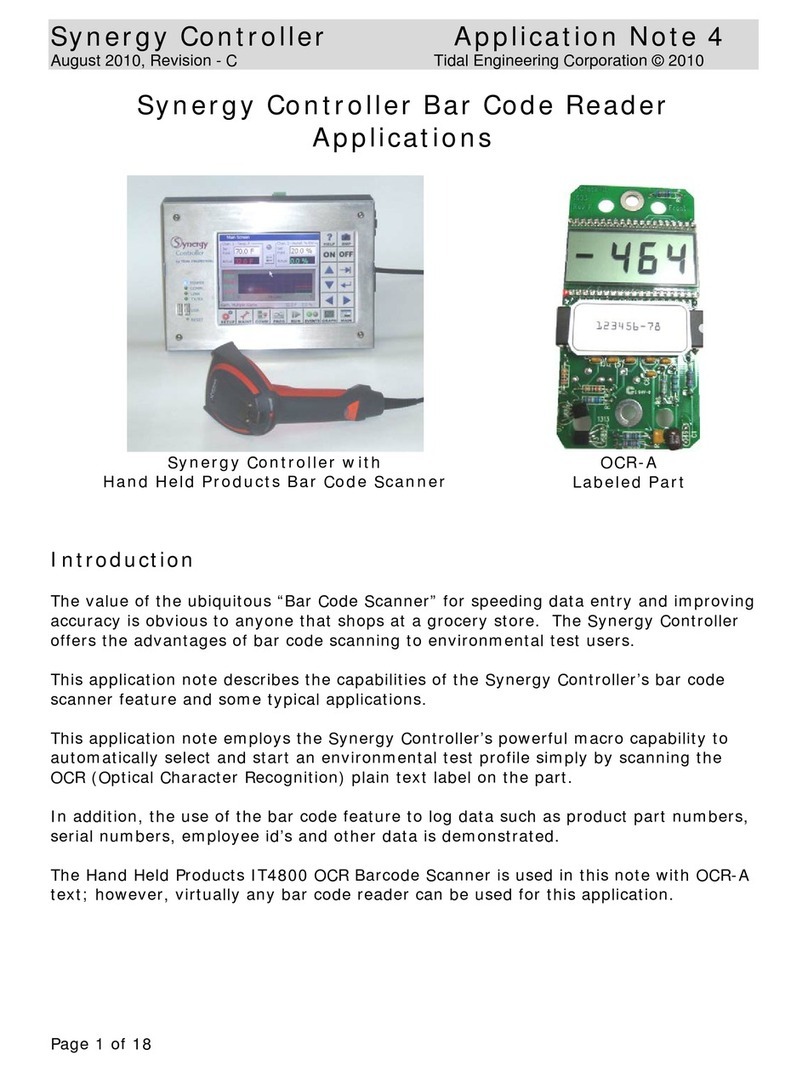
Tidal Engineering Corporation
Tidal Engineering Corporation Synergy Controller Application note
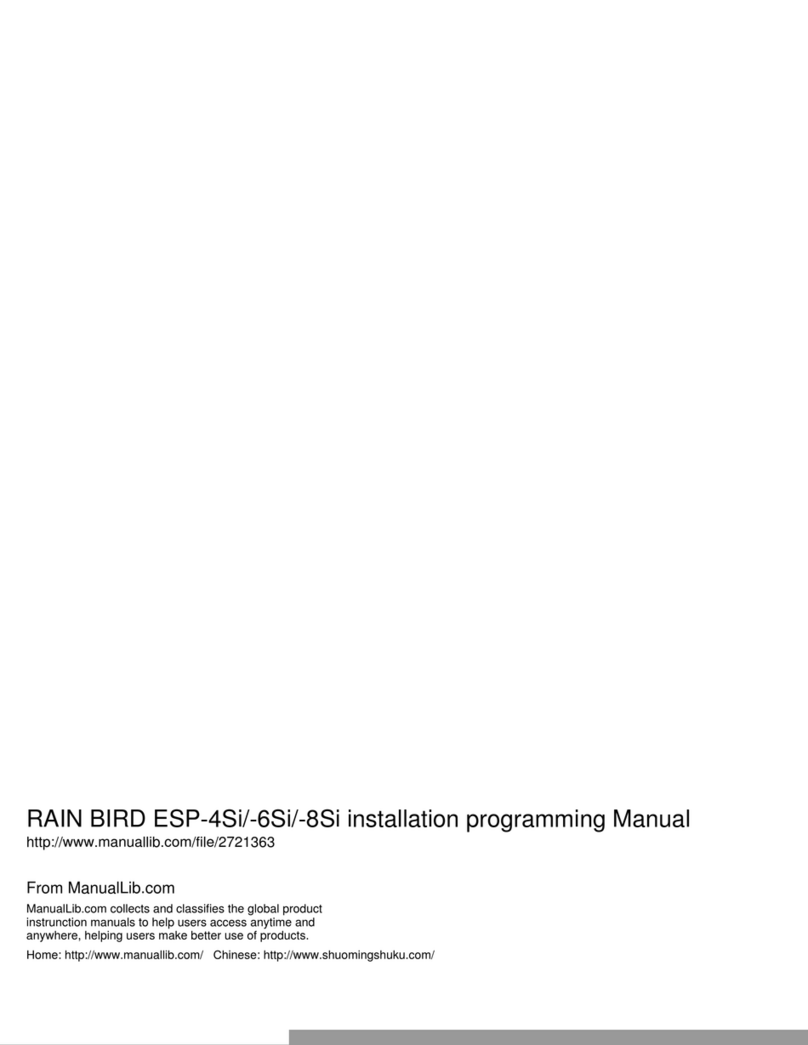
Rain Bird
Rain Bird ESP-4Si Installation & operation manual
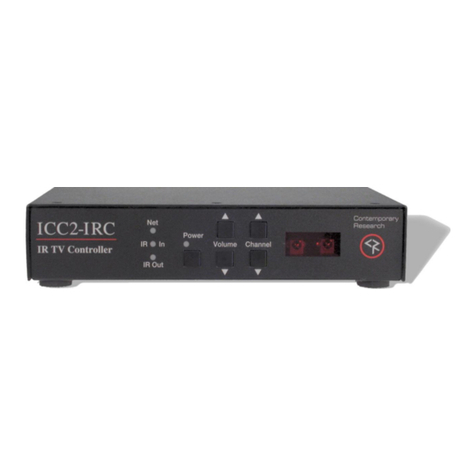
Contemporary Research
Contemporary Research ICC2-IRC product manual

LEGRAND
LEGRAND 0 261 19 manual