Fluidwell F131-P User manual

F131-P
BATCH CONTROLLER
with two-stage control, analog and pulse outputs
Signal input flowmeter: pulse, Namur and coil
External controls: start and stop
Digital outputs: two control outputs for two stage control, or
one control output and pulse output ref. total
Analog outputs: (0)4-20mA / 0-10V ref. flow rate
Options: Intrinsically safe, Modbus communication
F-Series - Field mounted indicators for safe and hazardous areas.
More info: www.fluidwell.com/fseries

FW_F131P_v1702_02_EN.docx
Page 2

FW_F131P_v1702_02_EN.docx
Page 3
SAFETY INSTRUCTIONS
▪Any responsibility is lapsed if the instructions and procedures as described in this
manual are not followed.
▪LIFE SUPPORT APPLICATIONS: The F131-P is not designed for use in life support
appliances, devices, or systems where malfunction of the product can reasonably be
expected to result in a personal injury. Customers using or selling these products for
use in such applications do so at their own risk and agree to fully indemnify the
manufacturer and supplier for any damages resulting from such improper use or sale.
▪Electro static discharge does inflict irreparable damage to electronics! Before installing
or opening the unit, the installer has to discharge himself by touching a well-grounded
object.
▪This unit must be installed in accordance with the EMC guidelines (Electro Magnetic
Compatibility).
▪Do connect a proper grounding to the metal enclosure as indicated if the F131-P has an
incoming power line which carries a 115-230V AC. The Protective Earth (PE) wire may
never be disconnected or removed.
▪Intrinsically safe applications: follow the instructions as mentioned in Chapter 5 and
consult “Fluidwell F1..-..-XI - Documentation for Intrinsic safety”.
DISPOSAL OF ELECTRONIC WASTE
▪The WEEE Directive requires the recycling of disposed electrical and electronic equipment in the European
Union. When the WEEE Directive does not apply to your region, we support its policy and ask you to be
aware on how to dispose of this product.
▪The crossed out wheelie bin symbol as illustrated and found on our products tells that this product shall not
be disposed of into the general waste system or into a landfill.
▪At the end of its life, equipment shall be disposed of according to the local regulations regarding waste of
the electrical and the electronic equipment.
▪Please contact your local dealer, national distributor or the manufacturer’s Technical helpdesk for
information on the product disposal.
SAFETY RULES AND PRECAUTIONARY MEASURES
▪The manufacturer accepts no responsibility whatsoever if the following safety rules and precautions
instructions and the procedures as described in this manual are not followed.
▪Modifications of the F131-P implemented without preceding written consent from the manufacturer, will
result in the immediate termination of product liability and warranty period.
▪Mounting, electrical installation, start-up and maintenance of this device may only be carried out by trained
persons authorized by the operator of the facility. Persons must read and understand this manual before
carrying out its instructions.
▪This device may only be operated by persons who are authorized and trained by the operator of the facility.
All instructions in this manual are to be observed.
▪Check the mains voltage and information on the manufacturer's plate before installing the unit.
▪Check all connections, settings and technical specifications of the various peripheral devices with the
F131-P supplied.
▪Open the enclosure only if all leads are free of potential.
▪Never touch the electronic components (ESD sensitivity).
▪Never expose the system to heavier conditions than allowed according the classification of the enclosure
(see manufacture's plate and chapter 4).
▪If the operator detects errors or dangers, or disagrees with the safety precautions taken, then inform the
owner or principal responsible.
▪The local labor and safety laws and regulations must be adhered to.

FW_F131P_v1702_02_EN.docx
Page 4
ABOUT THE MANUAL
This manual is divided into two main sections:
▪The daily use of the unit is described in chapter 2 "Operation". These instructions are meant for
users.
▪The following chapters and appendices are exclusively meant for electricians/technicians. These
provide a detailed description of all software settings and hardware installation guidance.
This manual describes the standard unit as well as the available options. For additional information,
please contact your supplier.
A hazardous situation may occur if the F131-P is not used for the purpose it was designed for
or is used incorrectly. Please carefully note the information in this manual indicated by the
pictograms:
A "warning !" indicates actions or procedures which, if not performed correctly, may lead to
personal injury, a safety hazard or damage of the F131-P or connected instruments.
A "caution !" indicates actions or procedures which, if not performed correctly, may lead to
personal injury or incorrect functioning of the F131-P or connected instruments.
A "note !" indicates actions or procedures which, if not performed correctly, may indirectly
affect operation or may lead to an instrument response which is not planned.
WARRANTY AND TECHNICAL SUPPORT
For warranty and technical support for your Fluidwell products,
Hardware version : 03.01.xx
Software version : 03.01.xx
Manual : FW_F131P_v1702_02_EN.docx
© Copyright 2017 : Fluidwell B.V. - the Netherlands
Information in this manual is subject to change without prior notice. The
manufacturer is not responsible for mistakes in this material or for incidental
damage caused as a direct or indirect result of the delivery, performance or
use of this material.
© All rights reserved. No parts of this publication may be reproduced or used
in any form or by any means without written permission of your supplier.

FW_F131P_v1702_02_EN.docx
Page 5
CONTENTS MANUAL
Safety instructions............................................................................................................ 3
Disposal of electronic waste............................................................................................ 3
Safety rules and precautionary measures.......................................................................3
About the manual.............................................................................................................. 4
Warranty and technical support....................................................................................... 4
Contents manual............................................................................................................... 5
1. Introduction.............................................................................................................. 6
1.1. System description 6
2. Operational............................................................................................................... 8
2.1. Control panel 8
2.2. Operator information and functions 8
3. Configuration ......................................................................................................... 11
3.1. How to program the F131-P 11
3.2. Setup menu - Settings 13
3.2.1. Explanation of Setup menu 1 - Preset 14
3.2.2. Explanation of Setup menu 2 - Flow rate 14
3.2.3. Explanation of Setup menu 3 - Overrun 15
3.2.4. Explanation of Setup menu 4 - Alarm 15
3.2.5. Explanation of Setup menu 5 - Display 15
3.2.6. Explanation of Setup menu 6 - Power management 16
3.2.7. Explanation of Setup menu 7 - Flowmeter 16
3.2.8. Explanation of Setup menu 8 - Analog output 17
3.2.9. Explanation of Setup menu 9 - Relays 18
3.2.10. Explanation of Setup menu A - Communication (option) 18
3.2.11. Explanation of Setup menu B - Others 19
4. Installation.............................................................................................................. 19
4.1. General directions 19
4.2. Installation / surrounding conditions 19
4.3. Dimensions - Enclosure 20
4.4. Installing the hardware 22
4.4.1. General installation guidelines 22
4.4.2. Aluminum enclosure - Field mounted 23
4.4.3. Aluminum enclosure - Panel mounted 23
4.4.4. Plastic (GRP) enclosure 24
4.4.3. Terminal connectors 25
4.4.6. Sensor supply 25
5. Intrinsically safe applications ............................................................................... 33
5.1. General information and instructions 33
5.2. Terminal connectors Intrinsically safe applications 35
5.3 Configuration Examples 37
5.4 Battery replacement instructions 39
5.4.1. Safety instructions 39
5.4.2. Replace the battery 39
5.4.3. Disposal of batteries 39
6. Maintenance........................................................................................................... 40
6.1. General directions 40
6.2. Repair 40
6.3. Repair policy 40
Appendix A.Technical specification.............................................................................. 41
Appendix B.Problem solving.......................................................................................... 44
Appendix C.Communication variables.......................................................................... 45
Appendix D. Declaration of Conformity......................................................................... 49
Index of this manual ....................................................................................................... 50
List of figures in this manual.......................................................................................... 50

FW_F131P_v1702_02_EN.docx
Page 6
1. INTRODUCTION
1.1. SYSTEM DESCRIPTION
Functions and features
The batch controller model F131-P is a microprocessor driven instrument designed for batching and
filling of small up to large quantities as well as displaying the flow rate, the batched total and the
accumulated total.
This product has been designed with a focus on:
▪ultra-low power consumption to allow long-life battery powered applications (type PB/PC);
▪intrinsic safety for use in hazardous applications (type XI),
▪ability to process all types of flowmeter signals;
▪transmitting possibilities with analog, pulse and communication outputs;
▪several mounting possibilities with GRP or aluminum enclosures for industrial surroundings.
Flowmeter input
This manual describes the unit with a pulse input from the flowmeter. Other versions are available to
process (0)4-20mA signals.
One flowmeter with a passive or active pulse, Namur or sine wave (coil) signal output can be
connected to the F131-P. To power the sensor, several options are available.
Standard outputs
▪Two passive transistor or relay outputs: for two- or one stage control with pulse output.
▪Pulse output to transmit a pulse that represents a totalized quantity as programmed.
▪Linear (0)4-20mA or 0-10V analog output to represent the actual flow rate as programmed. The
(0)4-20mA or 0-10V signal limits can be tuned.
Fig. 1: Typical application

FW_F131P_v1702_02_EN.docx
Page 7
Configuration of the unit
The F131-P is designed for use in many types of applications. For that reason, a setup menu is
available to program the F131-P according to your specific requirements.
The setup includes several important features, such as K-Factors, engineering units, signal
selection, power management (to extend battery life-time), etc. All settings are stored in a non-
volatile memory and therefore kept in the event of a power failure or an exhausted battery.
Display information
The unit has a LCD with (optional) backlight to show the process information, status and alarm messages.
The display refresh rate is programmed in the setup menu.
At a key press, the display refresh rate will switch to FAST for 30 seconds. When 'OFF' is selected,
the display goes off after 30 seconds after the last key press. The display temporarily comes on after
a key press.
A backup of the total and accumulated total in EEPROM memory is made every minute.
Options
The following options are available: isolated or active (0)4-20mA / 0-10V analog output, full Modbus
communication RS232/485/TTL (also battery powered), intrinsic safety, mechanical relay or active
output, power- and sensor-supply options, panel -mount, wall-mount and weather-proof enclosures,
flame proof enclosure and LED backlight.

FW_F131P_v1702_02_EN.docx
Page 8
2. OPERATIONAL
•This device may only be operated by persons who are authorized and trained by the
operator of the facility. All instructions in this manual are to be observed.
•Take careful notice of the "Safety rules, instructions and precautionary measures" in the
front of this manual.
This chapter describes the daily use of the F131-P . This instruction is meant for users / operators.
2.1. CONTROL PANEL
The control panel has three keys. The available keys are:
Fig. 2: Control Panel
Functions of the keys
This key is used to program and save new values or settings.
The PROG/ENTER key is also used to gain access to the setup menu (read
chapter 3).
This key is used to START the batch process.
The START/key is also used to increase a value after the PROG/ENTER key has
been pressed (read chapter 3).
This key is used to pause or stop the batch process. When the batch process is
stopped, it cannot be continued. The STOP/key is also used to select the total and
the accumulated total.
The STOP/key is also used to select a digit or an option after the PROG/ENTER
key has been pressed (read chapter 3).
2.2. OPERATOR INFORMATION AND FUNCTIONS
In general, the F131-P operates in the operator
mode. The shown information depends on the
settings which are made in the setup menu.
The signal from the connected sensor is processed
by the F131-P in the background, independent from
the selected display refresh rate.
Fig. 3: Process information (typical)
▪To enter a batch quantity (change the preset)
You can only change the preset when the READY
indicator is on.
1. Press the PROG/ENTER key until the
PROGRAM indictor starts to blink.
2. Use the START/and STOP/key to change
the value.
3. Momentarily, press the PROG/ENTER key to
confirm the new preset.
Fig. 4: Program preset value (typical)
If you do not press the PROG/ENTER key to confirm, your selection is not saved.
The PRESET value can be used time after time till a new value is programmed.
Changes are only saved when you press the PROG/ENTER key.

FW_F131P_v1702_02_EN.docx
Page 9
▪Leading zero
The amount of leading zeros is dependent on the batch maximum setting. In the program mode
the leading zeros will show. When you confirm the selection with the PROG/ENTER key, the
F131-P will hide the leading zeros in the operational preset menu.
It is not possible to enter a preset value which exceeds the batch maximum setting.
E.g. if the batch maximum is set to 20000, it will not be possible to program a preset
21000. If you want to program a preset 21000, you must change the batch maximum
setting.
Fig. 5: Leading zero (typical)
▪Batch maximum/minimum
When you program a new value which is not valid, the decrease-sign ▼(batch too big, program
a smaller batch) or the increase-sign ▲ (batch to small, program a bigger batch) will show.
▪To start the batch process
The batch process can only be started when "READY" is shown. The batch process is started
by pressing the START/key. Depending on the SETUP-settings, one or two relays will be
switched. The arrows at the display indicate if the ACTUAL-value is counting up or down.
▪To interrupt or to stop the batch process
When the STOP/key is pressed once, the batch
process is paused; the actual values are not lost. At
the display, the word "PAUSE" blinks. In this case
the, the batch process can be resumed with the
START/key.
When the STOP/key is pressed two times, the
batch process is stopped completely. In this case the
actual values are "lost" and the system returns to
steady state: the batch process cannot be resumed.
Fig. 6: Process paused (typical)
▪Flow rate indication
This function might not be available: it depends on the configuration of the unit.
During batching, the actual flow rate will be shown on the bottom-line of the display.
It depends on the configuration settings if flow rate is shown continuously or alternating with the
preset value.
▪Clear batch total
The value for total can be reset. To do so, select Total and press PROG followed by STOP -
STOP. After pressing the STOP/key once, the flashing text "PUSH STOP" is shown. To
avoid a reset at this stage, press another key than the STOP/key or wait for 20 seconds.
The reset of total DOES NOT influence the accumulated total.
▪Display accumulated total
When the STOP/key is pressed, total and accumulated total are shown. The accumulated
total cannot be reset. The value will count up to 99,999,999,999. The unit and number of
decimals are shown according to the configuration settings for total.
▪Low-battery alarm
Only use original batteries. Original batteries can be ordered at the manufacturer.
The use of unapproved batteries will void the warranty.
•
At the end of the battery’s life-time, the
voltage starts to drop. When the voltage
becomes too low, the battery indicator comes
on. When the battery indicator is on, install a
new and fresh battery as soon as possible.
Fig. 7: Low-battery alarm (typical)

FW_F131P_v1702_02_EN.docx
Page 10
▪No-flow alarm
The F131-P offers a no-flow monitoring feature: When the flowmeter does not generate a signal
during a certain (preset) time period, the F131-P will shut-off the control output(s) and bring the
batch controller in alarm status.
The “PAUSE” and “ALARM” indicators come on and NO FLOW is shown. Press the STOP/key to
confirm the alarm status and note that the “PAUSE” indicator stays on. Now you can cancel or
continue the batch (after you have solved the possible problem).
▪Alarm
When the alarm indicator is shown, refer to Appendix B: Problem Solving.

FW_F131P_v1702_02_EN.docx
Page 11
3. CONFIGURATION
This and the following chapters are exclusively meant for electricians and non-operators. In these,
an extensive description of all software settings and hardware connections are provided.
•Mounting, electrical installation, start-up and maintenance of this device may only be
carried out by trained persons authorized by the operator of the facility. Persons must
read and understand this manual before carrying out its instructions.
•This device may only be operated by persons who are authorized and trained by the
operator of the facility. All instructions in this manual are to be observed.
•Make sure, the measuring system is correctly wired up according to the wiring diagrams.
Protection against accidental contact is no longer assured when the housing cover is
removed or the panel cabinet has been opened (danger from electrical shock). The
housing may only be opened by trained persons authorized by the operator of the facility.
•Take careful notice of the "Safety rules, instructions and precautionary measures" in the
front of this manual.
The setup menu is used to program the F131-P.
The setup menu is accessible at all times while the F131-P remains fully operational. Be aware that
in this case any change to the settings may have an influence on the operation.
It is possible to prevent access to the setup menu with a password. A password may be
required to enter the setup menu. Without this password, access is denied.
3.1. HOW TO PROGRAM THE F131-P
The setup menu has different
submenus. Each submenu has an
unique number which is shown in
front of the menu name.
Each setting has an unique two-
digit number which is shown in
front of the setting. The first digit
refers to the submenu and the
second digit refers to the setting.
Note that sometimes the name of
the setting is shown on the upper
line of the display.
How to enter the setup menu
When the setup menu is protected by a password, the F131-P asks for a password to access the
setup menu. When in the operator mode, press and hold the PROG/ENTER key for 7 seconds to
access the setup menu.
How to navigate in the setup menu
The setup menu has different submenus to program the F131-P. For navigation, the submenus
and the settings are identified with numbers (for the submenu: e.g. 1; for the setting: e.g. 12.).
The STOP/► key and the PROG/ENTER key are used for navigation. The explanation assumes
that you are in the submenu PRESET.
Action
Result
Remark
1
Press the STOP/► key
to select the next
submenu.
•The submenu FLOW
RATE shows
-
2
Press again to go to the
next submenu.
•The submenu OVERRUN
shows.
-
3
Momentarily, press the
PROG/ENTER key to
select the previous
submenu.
•The submenu FLOW
RATE shows
-
4
Press again to go to the
previous submenu.
•The submenu PRESET
shows
-

FW_F131P_v1702_02_EN.docx
Page 12
The START/▲ key and the STOP/► key are used for navigation.
The explanation assumes that you are in the submenu PRESET. When you are:
•in the first setting and you navigate to the previous setting, the F131-P goes back to the related
main menu.
•in the last setting and you navigate to the next setting, the F131-P goes to the related main
menu.
Action
Result
Remark
1
Press the START/▲ key to
select the first setting.
•The setting UNIT shows.
-
2
Press the START/▲ key
again to go to the next
setting.
•The setting DECIMALS
shows.
-
3
Press the STOP/► key to
select the previous setting.
•The setting UNIT shows.
-
4
Press the STOP/►key
again to go to the previous
setting.
•The submenu PRESET
shows
This is normal behavior because
the setting UNIT is the first
setting of the submenu
PRESET.
How to make a setting
Changes are only saved when you press the PROG/ENTER key.
The explanation assumes that you are in the submenu PRESET and the setting UNIT. When you do
not want to save the change, wait for approximately 20 seconds or press and hold the
PROG/ENTER key for approximately 3 seconds.
Action
Result
Remark
1
Momentarily, press the
PROG/ENTER key.
•The PROG indicator blinks.
•The engineering unit L shows.
To access the setting.
2
Press the START /▲ key to
select the next engineering
unit.
•The PROG indicator blinks.
•The engineering unit m3shows.
If you wait too long, the
program mode goes off and
changes are not saved, this is
normal behavior.
3
Press the START /▲ key to
select the next engineering
unit.
•The PROG indicator blinks.
•The engineering unit US GAL
shows.
-
4
Press the STOP /► key to
select the previous
engineering unit
•The PROG indicator blinks.
•The engineering unit m3shows.
-
5
To confirm the changes:
Momentarily, press the
PROG/ENTER key.
•The PROG indicator goes off.
•The change is saved.
•The engineering unit m3shows.
If you do not press the
PROG/ENTER key to confirm,
your selection is not saved.
To discard the changes:
Press and hold the
PROG/ENTER key for
approximately 3 seconds.
•The PROG indicator goes off.
•The change is discarded.
•The engineering unit L shows.
-

FW_F131P_v1702_02_EN.docx
Page 13
3.2. SETUP MENU - SETTINGS
1
PRESET
11
unit
L; m3; kg; lb; GAL; USGAL; bbl; no unit
12
decimals
0000000; 111111.1; 22222.22; 3333.333
13
K-factor:
0.000010 - 9999999
14
decimals K-factor
0 - 6
15
batch-min
0000000 - 9999999
16
batch-max
0000000 - 9999999
2
FLOW RATE
21
unit
mL; L; m3; mg; g; kg; ton; gal; bbl; lb; cf; rev; - - - - (no unit);
scf; nm3; nL; p
22
time
/sec; /min; /hour; /day
23
decimals
0000000; 111111.1; 22222.22; 3333.333
24
K-factor
0.000010 - 9,999,999
25
decimals K-factor
0 - 6
26
calculation
per 1 - 255 pulses
27
cut-off
0.1 - 999.9 seconds
3
OVERRUN
31
overrun
disable; enable
32
time
0.1 - 999.9 seconds
4
ALARM
41
no flow
disable; enable
42
time
0.1 - 999.9 seconds
5
DISPLAY
51
display
increase; decrease
52
flow rate
off; batch; toggle
53
light
0% (off); 20%; 40%; 60%;- 80%; 100% (full brightness)
6
POWER MANAGEMENT
61
LCD new
fast; 1 sec; 3 sec; 15 sec; 30 sec; off
62
battery mode
operational; shelf
7
FLOWMETER
71
signal
npn; npn-lp; reed; reed-lp; pnp; pnp-lp; namur; coil-hi; coil-lo;
8-1 DC; 12 DC; 24 DC
8
ANALOG
81
output
disable; enable
82
rate-min
0000.000 - 9999999
83
rate-max
0000.000 - 9999999
84
cut-off
0.0 - 9.9%
85
tune-min
0 - 9999
86
tune-max
0 - 9999
87
filter
01 - 99
9
RELAYS
91
relays
1-step; 2-step
92
preclose
0000.000 - 9999999
93
width
0.001 - 9.999
94
decimals
0000000; 111111.1; 22222.22; 3333.333
95
amount
0000.001 –9999999
96
pulse
total; batch
A
COMMUNIC(ATION)
A1
speed
1200; 2400; 4800; 9600
A2
address
1 - 247
A3
mode
bus-rtu; bus-asc; off
B
OTHERS
B1
model
F131-P
B2
software version
nn:nn:nn
B3
serial no.
nnnnnnn
B4
password
0000 - 9999
B5
tag-nr
0000000 - 9999999

FW_F131P_v1702_02_EN.docx
Page 14
3.2.1. EXPLANATION OF SETUP MENU 1 - PRESET
UNIT
11
This setting is used to select the engineering unit for the indication of the
batch total, the accumulated total and the pulse output.
When you change the engineering unit, you must recalculate and
reprogram the K-factor for the (accumulated) total. When you
recalculate and reprogram the K-Factor, the history for
(accumulated) batch total is not correct anymore, because the
(accumulated) batch total is not recalculated. For future reference,
best practice is to make a note of the accumulated total before you
program the recalculated K-Factor.
DECIMALS
12
This setting is used to set the amount of digits behind the decimal point
for the (accumulated) total indication.
K-FACTOR
13
This setting is used to set the K-Factor for the total. With the K-Factor, the
flowmeter pulse signals are converted to a quantity. The K-Factor is
based on the number of pulses generated by the flowmeter per selected
engineering unit, for example per m3. A more accurate K-Factor (more
decimals, as set in decimals K-Factor) allows for a more accurate
operation of the system.
Example 1: Calculating the K-Factor.
The flowmeter generates 2.4813 pulses per liter and the selected unit is
m3. A cubic meter consists of 1000 liter which gives 2.4813 pulses*1000
liter=2481.3 pulses per m3. So, the K-Factor is 2481.3. Enter for the
Flowmeter K-Factor: 24813 and for the flowmeter K-Factor decimals: 1.
Example 2: Calculating the K-Factor.
The flowmeter generates 6.5231 pulses per gallon and the selected
engineering unit is gallons. So, the K-Factor is 6.5231. Enter for the
Flowmeter K-Factor: 65231 and for the Flowmeter K-Factor decimals: 4.
When you recalculate and reprogram a new K-Factor, the history for
(accumulated) batch total is not correct anymore, because the
(accumulated) batch total is not recalculated. For future reference,
best practice is to make a note of the accumulated total before you
program the recalculated K-Factor.
DECIMALS K-FACTOR
14
This setting is used to set the amount of digits behind the decimal point
for the K-Factor.
BATCH MIN
15
This setting is used to set the lower limit for a batch volume. An operator
cannot set a batch volume which is beyond the lower limit.
BATCH MAX
16
This setting is used to set the upper limit for a batch volume. An operator
cannot set a batch volume which is beyond the upper limit.
3.2.2. EXPLANATION OF SETUP MENU 2 - FLOW RATE
The settings for total and flow rate are entirely separate. In this way, different engineering units can
be used for each e.g. cubic meters for total and liters for flow rate.
UNIT
21
This setting is used to select the engineering unit for the indication of the
flow rate.
Alteration of the engineering unit will have consequences for
operator and SETUP-level values, they will not be automatically
recalculated to the value of the new selected unit. The K-factor has
to be adapted as well; the calculation is not done automatically.
TIME
22
This setting is used to set the time unit for the flow rate calculation. Note
that the flow rate is given in engineering unit/time unit, e.g. liters/minute
(l/min).
When you change this setting, also recalculate and change the
settings for the analog rate-min and analog rate-max.
DECIMALS
23
This setting is used to set the amount of digits behind the decimal point
for the flow rate indication.
K-FACTOR
24
This setting is used to set the K-Factor for the flow rate. With the K-
Factor, the flowmeter pulse signals are converted to a quantity. The K-
Factor is based on the number of pulses generated by the flowmeter per
selected engineering unit, for example per m3. A more accurate K-Factor
(more decimals, as set in decimals K-Factor) allows for a more accurate
operation of the system.
DECIMALS K-FACTOR
25
This setting is used to set the amount of digits behind the decimal point
for the K-Factor.

FW_F131P_v1702_02_EN.docx
Page 15
CALCULATION
26
The flow rate is calculated by measuring the time between a number of
pulses, for example 10 pulses. The more pulses the more accurate the
flow rate will be. The maximum value is 255 pulses.
This setting does influence the update interval for the flow rate and
thus, indirectly the update interval of the analog output.. (maximum
update 10 times a second). If the output response is too slow, decrease
the number of pulses. For low frequency applications (< 10Hz): do not
program more than 10 pulses, else the update time will be very slow.
For high frequency applications (> 1kHz): do program 50 or more pulses.
CUT-OFF
27
This setting is used to set the threshold for a minimum flow. If during this
time less than XXX-pulses are generated (refer to Calculation), the flow
rate will be shown as zero. The cut-off has to be entered in seconds.
3.2.3. EXPLANATION OF SETUP MENU 3 - OVERRUN
Due to system parameters which are beyond the settings of the batch controller, an overrun can
occur at the end of a batch. The batch controller analyzes the overrun volume and automatically
corrects the volume each time after each batch (self learning).
OVERRUN
31
For an accurate overrun correction, it is necessary that the flowmeter
meets certain technical demands, such as "high resolution" and shows no
"false" overrun due to a slow update time. Do not enable this function if
the flow meter is not compatible to this function.
TIME
32
The overrun characteristic of the system will be analyzed during a certain
time after the batch relay has been de-energized. In this way, false signal
generated through leakage are eliminated. Enter here the expected time
needed by the system to stop a batch. It is advisable to provide extra time
in order to avoid an incorrect overrun correction or false leakage alarms.
The next batch can only be started after the overrun time is completed!
3.2.4. EXPLANATION OF SETUP MENU 4 - ALARM
The F131-P offers a no-flow monitoring feature: When the flowmeter does not generate a signal
during a certain (preset) time period, the F131-P will shut-off the control output(s) and bring the
batch controller in alarm status.
NO-FLOW
41
This setting is used to program the behavior of the no-flow alarm. When
the flow rate is zero, it is possible to ignore or disable the no-flow
monitoring.
TIME
42
This setting is used to set a delay time for the related alarm. When the
alarm condition is still valid after the delay time, an alarm is given.
3.2.5. EXPLANATION OF SETUP MENU 5 - DISPLAY
DISPLAY
51
This setting is used to set the behavior of the counter during a batch
process: count down (quantity to do) or count up (quantity done).
FLOW RATE
52
This setting is used to determine how the flow rate will be shown during a
batch process. The settings are:
▪off: flow rate will not be shown;
▪batch after the start, the flow rate will be shown till the end of the
batch. (advise: set the display to setting "decrease";
▪toggle: flow rate is shown alternating with the preset value.
LIGHT
53
The backlight brightness can be adjusted from 0% (off) to 100% (full
brightness) in steps of 20%.
When the F131-P is only loop powered, the backlight is disabled. An
external power supply is required to supply the backlight.

FW_F131P_v1702_02_EN.docx
Page 16
3.2.6. EXPLANATION OF SETUP MENU 6 - POWER MANAGEMENT
When used with the internal battery option (type PB/PC), the user can expect reliable measurement
over a long period of time. The F131-P has several smart power management functions to extend
the battery life time significantly. Two of these functions can be set.
LCD NEW
61
The calculation of the display-information influences the power
consumption significantly. When the application does not require a fast
display refresh rate, it is strongly advised to select a slow refresh rate.
Please understand that NO information will be lost; every pulse will be
counted and the output signals will be generated in the normal way.
At a key press, the display refresh rate will switch to FAST for 30
seconds. When 'OFF' is selected, the display goes off after 30 seconds
after the last key press. The display temporarily comes on after a key
press.
Example battery life-time with a coil pick-up:
•1kHz pulse and FAST update: about 2 years;
•1kHz pulse and 1 sec update: about 5 years.
BATTERY MODE
62
The F131-P has two modes: operational or shelf.
After "shelf" has been selected, the F131-P can be stored for several
years; it will not process the sensor signal; the display is switched off but
all settings and totals are stored. In this mode, power consumption is
extremely low.
To wake up the F131-P again, press the START/key two times.
3.2.7. EXPLANATION OF SETUP MENU 7 - FLOWMETER
SIGNAL
71
With this setting the type of flowmeter output is selected. The settings with
LP (low-pass) filter are used to apply a build-in noise reduction.
Selections "active pulse" offer a detection level of 50% of the supply
voltage.
TYPE OF SIGNAL
EXPLANATION
RESISTANCE
FREQ./MV
REMARK
NPN
NPN input
100 kΩ pull-up
max.6 kHz.
(open collector)
NPN - LP
NPN with low pass filter
100 kΩ pull-up
max.1.2 kHz.
(open collector)
less sensitive
REED
Reed-switch input
1 MΩ pull-up
max.1.2 kHz.
REED - LP
Reed-with low pass filter
1 MΩ pull-up
max.120 Hz.
Less sensitive
PNP
PNP input
100K pull-down
max.6 kHz.
PNP - LP
PNP with low pass filter
100K pull-down
max.1.2 kHz.
Less sensitive
NAMUR
NAMUR input
820 Ω pull-down
max.4 kHz.
External power
required
COIL-HI
High sensitive coil input
-
min. 20 mVpp
Sensitive for
interference!
COIL-HI
(option ZF)
min. 10 mVpp
COIL-HI
(option ZG)
min. 5 mVpp
COIL LO
Low sensitive coil input
-
min. 80 mVpp
Normal
sensitivity
8-1 DC
Active pulse input
detection level 8.2V DC
3K9
max.10KHz.
External power
required
12 DC
Active pulse input
detection level 12V DC
4K
max.10KHz.
External power
required
24 DC
Active pulse input
detection level 24V DC
3K
max.10KHz.
External power
required

FW_F131P_v1702_02_EN.docx
Page 17
3.2.8. EXPLANATION OF SETUP MENU 8 - ANALOG OUTPUT
A linear 4-20mA signal (option AB: 0-20mA or option AU: 0-10V) output signal is generated that
represents the flow rate. The settings for the flow rate influence the analog output directly. The
relationship between the flow rate and the analog output is set with the following settings.
OUTPUT
81
If the analog output is not used, select disable to minimize the power
consumption (e.g. save battery life-time).
Option AP: When a power supply is available but the output is disabled, a
3.5mA signal will be generated.
RATE-MIN
82
Enter here the flow rate at which the output should generate the minimum
signal (0)4mA or 0V - in most applications at zero flow. The number of
decimals shown depend upon setup 23. The engineering units/time (e.g.
L/min) are dependent upon setup 21 and 22.
RATE-MAX
83
Enter here the flow rate at which the output should generate the maximum
signal (20mA or 10V) - in most applications at maximum flow. The number
of decimals shown depend upon setup 23. The engineering units/time
(e.g. L/min) are dependent upon setup 21 and 22.
CUT-OFF
84
To ignore leakage of the flow for example, a low flow cut-off can be set as
a percentage of the full range of 16mA, 20mA or 10V.
When the flow is less than the required rate, the current will be the
minimum signal (0)4mA or 0V.
Example: Calculate the cut-off.
Rate-min: 0L/min [4mA], Rate-max: 100 L/min [16mA], Cut-off: 2%
Required rate [L/min]: (rate-max - rate-min)*cut-off: (100-0)*2%=2 L/min
Output [mA]: rate-min + (rate-max*cut-off): 4+(16*2%)=4.32mA
TUNE-MIN
85
The (0)4mA or 0V value can be tuned precisely with this setting. The
initial minimum analog output value is (0)4mA or 0V. However, this value
might differ slightly due to ambient influences such as temperature for
example.
Before tuning the signal, be sure that the analog signal is not being
used for any application!
After pressing PROG, the current will be about 4mA (0mA or 0V). The
current can be increased / decreased with the arrow keys and is directly
active. Press ENTER to store the new value.
If required, you can program the analog output 'up-side-down'. The
(0)4mA or 0V represents the maximum flow rate and the 20mA or 10V
represents the minimum flow rate.
TUNE-MAX
86
The 20mA or 10V value can be tuned precisely with this setting. The initial
maximum analog output value is 20mA or 10V However, this value might
differ slightly due to ambient influences such as temperature for example.
Before tuning the signal, be sure that the analog signal is not being
used for any application!
After pressing PROG, the current will be about 20mA or 10V. The current
can be increased / decreased with the arrow keys and is directly active.
Press ENTER to store the new value.
If required, you can program the analog output 'up-side-down'. The
(0)4mA or 0V represents the maximum flow rate and the 20mA or 10V
represents the minimum flow rate.
FILTER
87
This setting is used to stabilize the output signal. With the help of this
digital filter a more stable but less actual representation of the flow rate
can be obtained.
The filter principal is based on three input values: the filter level (01-99),
the last calculated flow rate and the last average value. The higher the
filter level, the longer the response time on a value change will be.

FW_F131P_v1702_02_EN.docx
Page 18
3.2.9. EXPLANATION OF SETUP MENU 9 - RELAYS
Two control outputs are available to control relays or valves. Relay 2 can also be used as pulse
output according the batch total (actual) or accumulated total.
RELAYS
91
This submenu is used to set the function of related output.
1-Step: The F131-P is used for one-stage batch control while R2 is used
as a scaled pulse output.
2-Step: The F131-P is used for two-stage batch control.
PRECLOSE
92
According to the setting 91 - 2-step, relay two will be used to control a
second valve for the batch process. If the product is batched in two steps,
the switch-off-moment for relay 2 has to be set. The switch moment is
based on the remaining quantity before the end of batch.
If preclose is set to zero, relay 2 will switch simultaneously with relay 1.
The settings: width, decimals, amount and pulse are only valid when
relay 2 is used as a scaled pulse output. A scaled pulse output is used to
indicate that the batch or accumulated total has increased with the value
as set in the setup 95.
WIDTH
93
When relay 2 is used as a scaled pulse output:
The pulse width determines the time that the output will be active; in other
words the pulse duration. Value “zero” will disable the pulse output.
The pulse signal always has a 50% duty cycle, hence the minimum time
between the pulses is equal to the pulse width setting. If the frequency
should go out of range –when the flow rate increases for example –an
internal buffer will be used to “store the missed pulses”: As soon as the
flow rate slows down, the buffer will be “emptied”.
It might be that pulses will be missed due to a buffer-overflow, so it is
advised to program this setting within its range!
DECIMALS
94
This setting is used to set the amount of digits behind the decimal point for the
amount.
AMOUNT
95
A pulse will be generated every time a certain quantity is added to the
total. Enter this quantity here while taking the decimals for pulse into
account.
PULSE
96
The pulse generation is controlled by the batch total or the accumulated
total.
When set to “batch”, the buffer (setting: Width) will be emptied when a
new batch is started.
3.2.10. EXPLANATION OF SETUP MENU A - COMMUNICATION (OPTION)
This product is designed for the connection to a communication network. Products with a
communication option do not include cyber security functions. Fluidwell cannot take any
responsibility for the cyber security, omissions or errors in the communication safety. To maintain a
secure operation, automation and control, it is the sole responsibility of the owner to install and
manage the appropriate safety measures to protect the network, the product and the communication
against any kind of security breaches.
The functions described below deal with hardware that is not part of the standard delivery.
Programming of these functions does not have any effect if this hardware has not been installed.
Consult Appendix C and the Modbus communication protocol description for a detailed explanation.
SPEED
A1
This setting is used to set the Baudrate.
ADDRESS
A2
This setting is used to set the communication address for the F131-P.
MODE
A3
This setting is used to set the Modbus transmission mode. Select OFF to
disable the communication.

FW_F131P_v1702_02_EN.docx
Page 19
3.2.11. EXPLANATION OF SETUP MENU B - OTHERS
For support and maintenance it is important to have information about the characteristics of the
F131-P. Your supplier will ask for this information when support is required.
MODEL
B1
This setting shows the model name.
SOFTWARE VERSION
B2
This setting shows the version number of the firmware (software).
SERIAL NO
B3
This setting shows the serial number.
PASSWORD
B4
This setting is used to set a password (pin code) to limit the access for the
setup menu. Only persons who know the pin code can access the setup
menu. The pin code 0000 disables the pin code to allow for access by any
person.
TAG-NR
B5
This setting is used to set a tag number for the F131-P.
4. INSTALLATION
4.1. General directions
•Mounting, electrical installation, start-up and maintenance of this device may only be
carried out by trained persons authorized by the operator of the facility. Persons must
read and understand this manual before carrying out its instructions.
•This device may only be operated by persons who are authorized and trained by the
operator of the facility. All instructions in this manual are to be observed.
•Make sure, the measuring system is correctly wired up according to the wiring diagrams.
Protection against accidental contact is no longer assured when the housing cover is
removed or the panel cabinet has been opened (danger from electrical shock). The
housing may only be opened by trained persons authorized by the operator of the facility.
•Take careful notice of the "Safety rules, instructions and precautionary measures" at the
front of this manual.
4.2. INSTALLATION / SURROUNDING CONDITIONS
Take the relevant IP classification of the
enclosure into account (see identification plate).
Even an enclosure rated for IP67 / TYPE 4(X)
should NEVER be exposed to strongly varying
(weather) conditions.
When panel-mounted, the front panel of the
F131-P is rated for IP65 / TYPE 4(X)!
When used in very cold surroundings or varying
climatic conditions, inside the instrument case,
take the necessary precautions against
moisture.
Mount the F131-P onto a solid structure to
avoid vibrations.

FW_F131P_v1702_02_EN.docx
Page 20
4.3. DIMENSIONS - ENCLOSURE
Fig. 8: Aluminum enclosures - Dimensions
75 mm (2.95")
130 mm (5.12") 112 mm (4.40")
120mm(4.72”)
M20 x 1,5
PG9 PG9
30mm 30mm
M20 x 1,5
M16 x 1,5 M16 x 1,5
30mm 30mm
M20 x 1,5
M20 x 1,5 M20 x 1,5
25mm 25mm
1/2"NPT
0.9”
3x 1/2"NPT
0.12" 0.12"
HA
HM
HN
HO
HP
HT
HU
6 x M12
12mm 12mm
24mm24mm
36mm
36mm
14mm17mm
115 mm (4.53”)
HB
29.1 mm (1.15”)
31 mm
(1.22”)
HZ
4x M20 x 1,5
15 15
HV
2323
16
mm
1/2"NPT 1/2"NPT
25mm 25mm
22,5mm
HL
22,5mm22,5mm22,5mm22,5mm
0.9”
15
60mm(2.36”)
98mm(3.86”)
38 mm (1.50”)
Other manuals for F131-P
1
This manual suits for next models
1
Table of contents
Other Fluidwell Controllers manuals
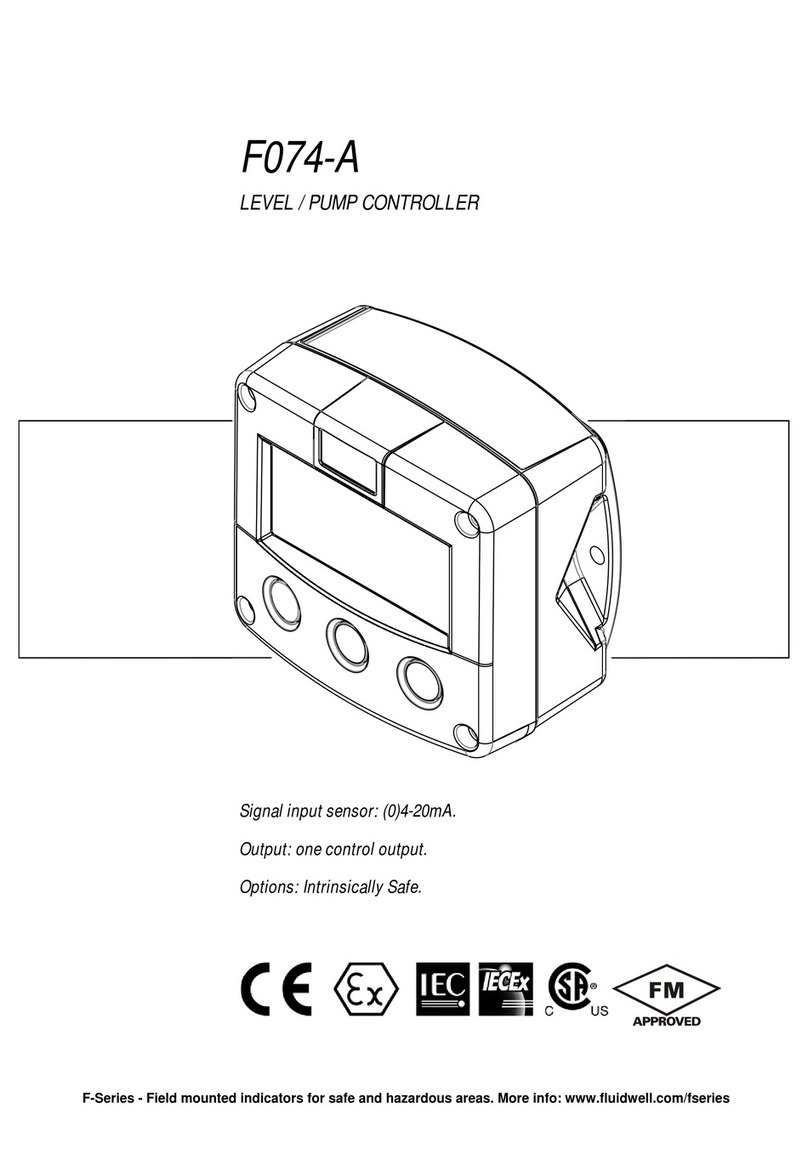
Fluidwell
Fluidwell F074-A User manual
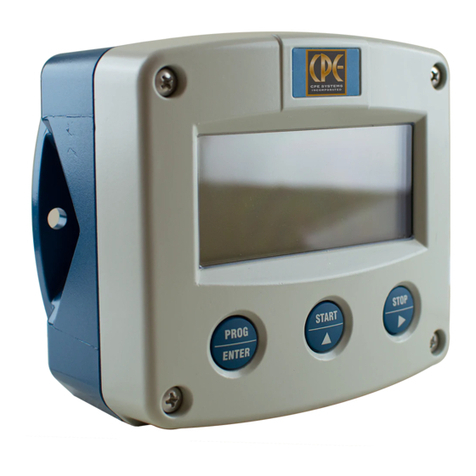
Fluidwell
Fluidwell F030-A User manual

Fluidwell
Fluidwell F131-P User manual
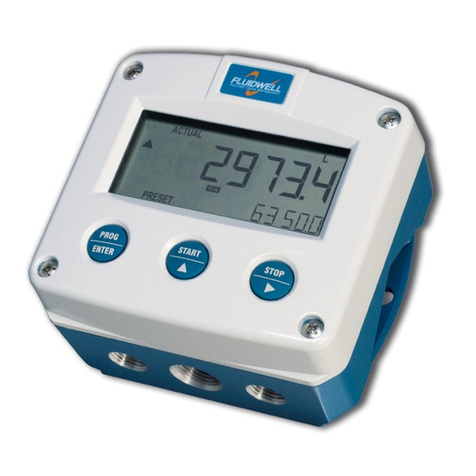
Fluidwell
Fluidwell F Series User manual
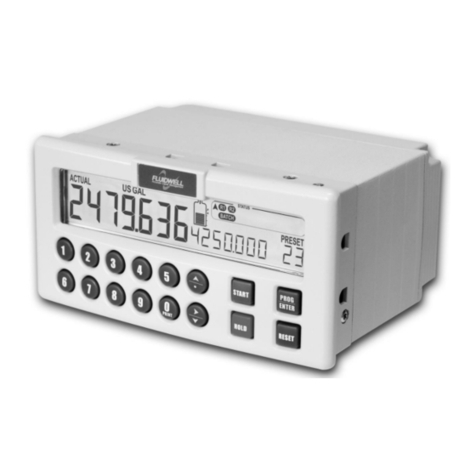
Fluidwell
Fluidwell N Series User manual
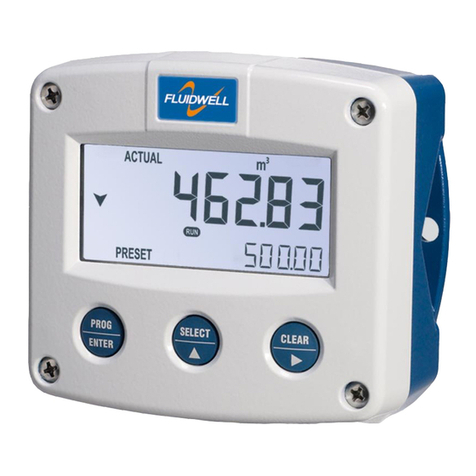
Fluidwell
Fluidwell F074-A User manual
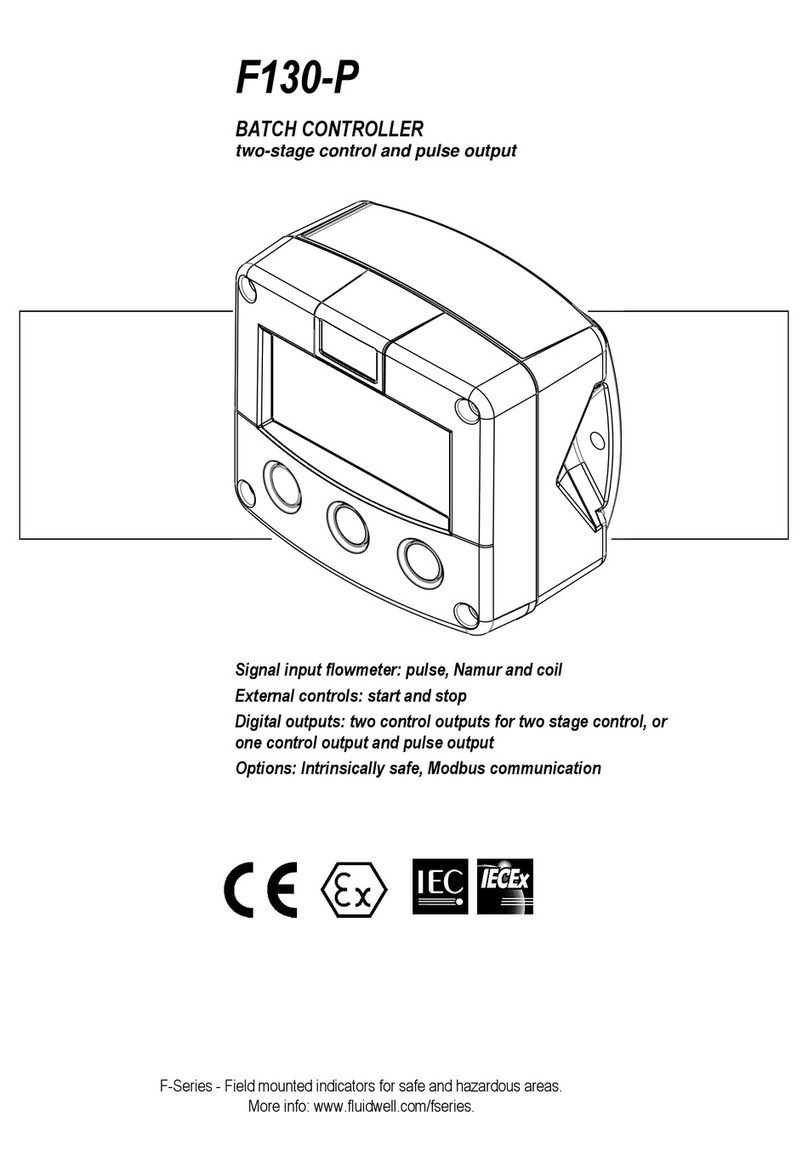
Fluidwell
Fluidwell F130-P User manual
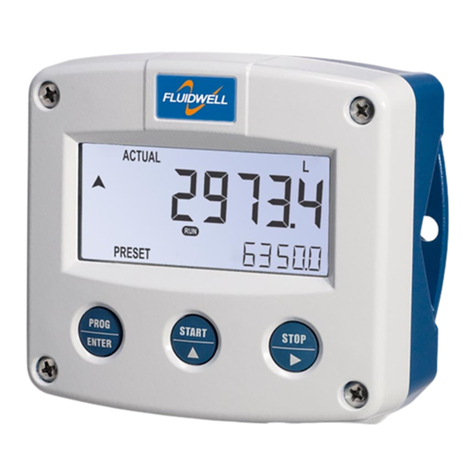
Fluidwell
Fluidwell F030-P User manual
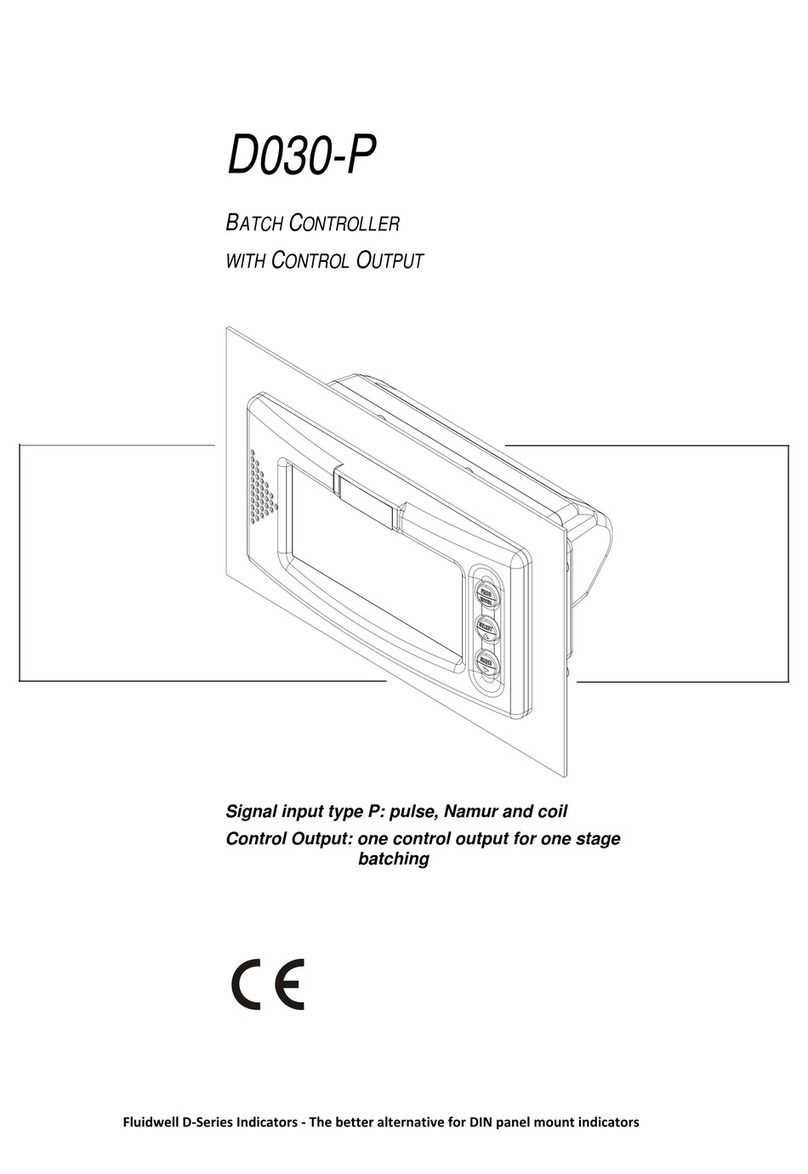
Fluidwell
Fluidwell D030-P Series User manual
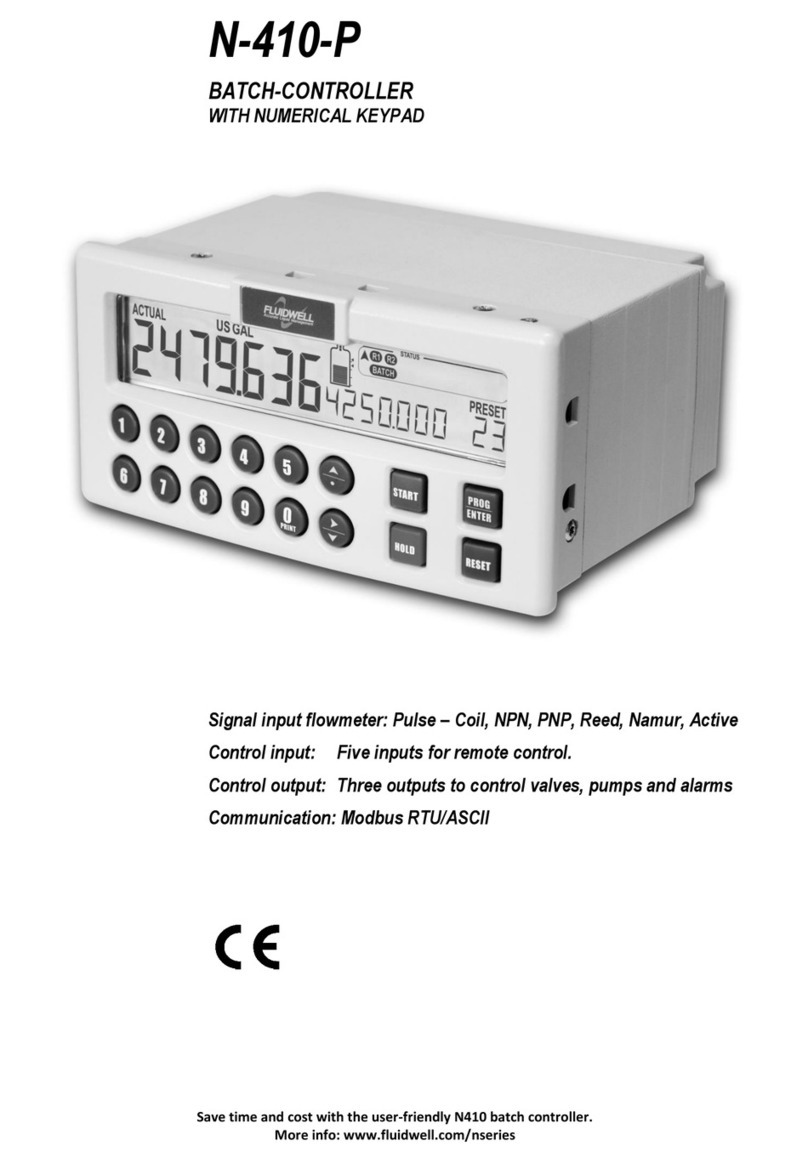
Fluidwell
Fluidwell N-410-P User manual