GDS 3 Manual

1
Installation and Maintenance
Manual
Light Industrial
Swing Gate Operators
Model: GDS 3
A.B.N. 62 059 806 405
March 2017 V1.01

2
CONTENTS
Page
Standard Installation 3
Side-Mount Installation 5
Restricted Side Room
Outswing Installation 6
Circuit Board Settings 6
Options 7
Transmitter – Poor Range 8
Specifications
Emergency Release
Maintenance
Warranty 9

3
STANDARD INSTALLATION
A standard installation is one where the gates open by swinging inward toward the operator. The gate hinge
should be no more than 200mm from the rear of the pillar or post and side room of 350mm is required to
accommodate the swing of the arms (see Figure 1)
Figure 1: Standard Installation * Restricted side room installation
1. Ensure that the gates swing freely and that all existing latches, drop bolts etc are disabled or removed.
2. The master operator (the one containing the circuit board) should be fitted to the gate pillar or post
nearest the power supply. Remove the covers from the operators to access the slotted fixing holes in the
rear of the chassis. Bend the tabs out and back against the rear of the chassis. In this position they act as
spacers allowing clearance for the cover.
3. Position each unit on the gate pillars or posts approximately 50mm from the edge of the pillar. The
vertical position is found by locating the gate bracket. This is best placed where there is adequate fixing
on the gate and movement of the arms is unrestricted (Figure 2). The units may now be bolted in place.
PLEASE NOTE: The chassis has laser cut tabs on the back (top and bottom) for standard mounting. These
tabs should be bent back. This eliminates the need to use spacers and ensures the chassis is spaced correctly
to ensure correct positioning of metal cover.
Figure 2: Position of Operator

4
Connect the slave to the master unit with 2 core flex (maximum load 8Amp at 12volts) (Figure 3)
Figure 3: Master/Slave connections
The units are set in the factory for a standard installation with the master placed on the left hand side
(from inside looking out). If the master is to be located on the right then the motor wires need to be
reversed. To do this, locate the connection blocks for each motor on the circuit board. Swap the brown
and blue wires for motor one. Do the same for motor two (Figure 3)
4. The gate bracket should be positioned so that the arms are almost in a straight line when the gates are
closed (Figure 4) To check the location of the gate brackets, first disengage the main arm from the drive
shaft (using the spanner provided), unscrew the bolt until the arm swings freely. Clamp the gate bracket
in position. Open and close the gate to ensure the gate bracket is appropriately located.
Pillar
Figure 4: Arm position when gate closed
5. Connect Receiver Board
6. Connect power to the master operator.
7. The limit switches may now be adjusted (Figure 5). Each unit has its own pair of cams, one to set the
open position and one to set the closed position. Loosen the screw holding the cams. Operate the
operator with the transmitter and note which cam controls the opening/closing motion (the cam lobe
activates a limit switch to turn off the motor). Reposition each cam and operate the operator again.
Repeat until the gates open and close to the required positions.
Figure 5: Limit Switches

5
SIDE MOUNT INSTALLATION
The Light Industrial Operators may be mounted sideways, with the long side against the pillar or post for
extra flexibility. This feature is very useful when:-
•The gate must swing further than 90°
•The gate swing outwards
•The gate swings outward and it is positioned at least 400mm forward of the back of the pillar
NOTE: See also section on Outswing Installation
Figure 6: Side Mount Installations
Each unit should be fitted to the pillar with output shaft close to the gate hinge. With this in mind the
standard installation instructions may now be followed.
NOTE: Special Side mount covers to suit are supplied for this installation.
RESTRICTED SIDE ROOM
This term is applied to the situation where the movement of the standard arms cannot be accommodated
within the side room available. In most situations this problem can be overcome by cutting down the
Secondary arm (the link joining the gate bracket to the Primary arm). The new length can be approximated
by the following procedure:
1. Move the Primary arm to a position suitable for the close gate. Remembering that in the closed position
the Primary and Secondary arms must stop short of straight line alignment (Figure 7)
Pillar
Figure 7: Measure Length of Secondary arm
2. Mark a point on the gate suitable for the gate bracket. Holding the gate bracket in position, measure the
distance between the hole centres on the gate bracket and Primary arm.
3. Move the Primary arm to its maximum open position. Open the gate and measure the distance again
(Figure 8). If the length has changed then the gate bracket must be repositioned and the process repeated
until the dimension remains the same for both positions. Be careful that the Secondary arm does not
conflict with the drive shaft of the Primary arm.

6
Open Gate Leaf
Pillar
OUTSIDE
INSIDE
Plan View
Open Gate
Figure 8: Re-measure length of Secondary arm
4. Once the dimension is consistent, a new hole can be drilled in the Secondary arm and the arm trimmed to
suit. The gate bracket and Secondary arm should now be fitted.
OUTSWING INSTALLATION
In this type of installation the gate swings outward or away from the operators to the open position (Figure
6). Several factors must be considered to determine the most suitable arm length. These include the drive
through width required, the placement of the operators and the location of the gate. Direct support from the
supplier is always available in these situations.
NOTE: The polarity of the motor connections may need to be reversed on out-swing operation. See the
‘Overloads’ section.
SETTINGS
AUTO CLOSE
The gates can be set to automatically close after a specific period.
This feature is activated by fitting a ‘jumper’ across the appropriate connection block (Figure 9) and
adjusting the Auto Close dial to the required time delay. Turning the dial anticlockwise increases the time
until the gates automatically close.
Figure 9: Settings
OVERLOAD
The overloads (Figure 9) are preset to maximum sensitivity i.e. slight pressure on the gate during operation
will cause the operator to stop if it is opening or stop and automatically reverse if it is closed.
NOTE: If these functions are reversed i.e. the gate stops when closing and stops and automatically reversed
when opening, then the polarity of the motor connections must be reversed, and the limit switch cams
adjusted.
There is one overload for each gate, as indicated on the circuit board. To reduce the sensitivity, turn the
overload dials in the anticlockwise direction.
Be Careful! Large reductions in sensitivity may allow the gates to exert excessive pressure on people or
vehicles trapped in the path of the gates.

7
On Board Version 2.3 or later, there is a Travel Timer – yellow L.E.D. trimpot. This should be set
approximately 5 to 10 seconds after full operation after gates reach full travel on limits in open and closed
position.
Travel times can be adjusted by turning trimpot anticlockwise to extend travel time and vice versa.
Green LED – Open Position (located above relay 4)
Red LED – Close Position
ANTI-CLASH LEAF DELAY
To avoid jamming, there is a time delay between the movement of each gate. This delay may be
independently adjusted for the opening sequence and the closing sequence.
Dial R24 changes the closing delay and dial R27 changes the opening delay. In situations where the master
unit is on the right hand side from inside looking out, R24 sets the opening delay and R27 sets the closing
delay.
Turning the dials anticlockwise gives the minimum delay.
OPTIONS
PUSH BUTTON,KEY PAD ETC
A variety of hard wired input devices can be used to operate the Light Industrial Operators. Input should be
in the form of a momentary closed circuit.
Warning: Voltage must not be applied to these terminals or damage to the circuitry will result. Devices that
send a voltage pulse (as some intercoms do) must be connected to the circuit board through a relay.
Figure 10: Push-button connection
ELECTRIC LOCK
Connections for an electric lock are provided on the circuit board (Figure 11) This connection block will
supply 12 volts to energise and lock at the beginning of the opening and closing cycles.
Figure 11: Electric Lock Connection

8
PHOTO ELECTRIC CELL
A photo electric cell may be fitted to detect obstructions in the path of the Gate. The Light Industrial
Operators will check for obstructions during the closing cycle only. If an obstruction is encountered the
gates will reverse to the open position.
If the Automatic Close mode is set the gates will remain open or return to the open position until the
obstruction is cleared.
Wires for the photo electric cell should be attached to the appropriate connection block (Figure 12)
Figure 12: Photo electric Cell connections
TROUBLE SHOOTING RANGE
POOR TRANSMITTER RANGE -This may occur for several reasons:-
•The first thing to check is the battery in the transmitter. Power may be low even if the transmitter light
or buzzer is functioning.
•The antenna wire may be damaged or not fully extended.
•Another cause is interference from external radio sources (electric fences, baby monitors, other local
transmitters). Here the best solution is to remove the external source. If this is not possible, the problem
may sometimes be solved by using special frequency transmitters and a matching receiver. These may
be ordered through your supplier.
OTHER FAULTS
Other faults may be due to incorrect settings. Refer to the ‘Settings’ and ‘Options’ sections of this manual to
ensure the settings are correct.
SPECIFICATIONS
Dimensions
Case: ............................................................................................ 245mm high x 140mm wide x 335mm deep
Primary arm:.................................................................................................................... pivot centres 550mm
Secondary arm:................................................................................................................ pivot centres 570mm
Weight
Master Unit including battery....................................................................................................................21kg
Slave Unit ..................................................................................................................................................17kg
Power Requirements
Standard...............................................................................................................................240volts 50Hz AC
Solar.....................................................................................................................................10watt Solar Panel
Battery (Solar/Battery backup) .....................................................................................................12volt 6.5Ah
EMERGENCY RELEASE
A spanner is provided to disconnect the operators and allow manual operation of the gates. The spanner is
used to unscrew the bolt on the output shaft of the unit. There is no need to fully remove the bolt as it is
loosened the arm will drop away and allow the gate to swing freely.
MAINTENANCE
ANTS AND OTHER INSECTS
The Light Industrial Operators have been designed to minimise infestation by insects. Additional protection
is recommended by spraying of a Surface Spray to the area surrounding the unit every 3 months.
LUBRICATION
The gears and shafts are greased on assembly. They should not require further lubrication during their
service life.

9
WARRANTY
a. Gate Drive Systems Australia warrants that the goods manufactured by it shall be free from defect in
manufacture for a period of 12 months from the date of invoice. Should any fault occur within that
period as a result of faulty workmanship or materials, Gate Drive Systems Australia at its discretion,
replace the product at no charge to the Customer except for installation & freight. The appropriate
Serial Number must be quoted for all warranty claims.
b. For the goods not manufactured by Gate Drive Systems Australia, we shall pass on the manufacturers
warranty to the Customer from the date of invoice. It is the manufacturer`s discretion to repair or
replace goods deemed to be defective as a result of faulty workmanship or materials.
c. All goods must be returned to Gate Drive Systems Australia or its representative for inspection or
testing to assess if a claim is justified. It is the responsibility and at the cost of the Customer, to
remove & return the goods for inspection and freight costs are the responsibility of the Customer.
d. The warranty is negated and will not apply in the following circumstances:-
i. If no proof of date of purchase can be produced.
ii. If the product has been used in a manner beyond its design parameters.
iii. If the product is tampered with or repaired by personnel not authorised to do so.
iv. In respect of loss or damage caused by rough treatment.
v. If the product is not used and maintained in accordance with instructions or recommendations
listed in this Installation and Maintenance Manual.
vi. In respect of loss or damage caused by an Act of God or any other cause not within the
manufacturers control.
e. Goods returned under warranty for repair or testing will incur a charge to be fixed by the manufacturer
if no fault is found.
f. The Customer shall bear freight charges for removing & returning the goods for inspection and for the
delivery & installation of any replacement or repaired product from a justified warranty claim.
g. Save for the express conditions and warranties herein contained all other conditions or warranties
(whether as the quality, fitness for purpose or any other matter) expressed or implied by statute,
common law, equity, trade custom, usage or otherwise are hereby expressly excluded provided that
nothing in these terms and conditions shall exclude or limit any breach or condition implied by law,
the exclusion or limitation of which is not permitted by law.
Table of contents
Other GDS Gate Opener manuals
Popular Gate Opener manuals by other brands
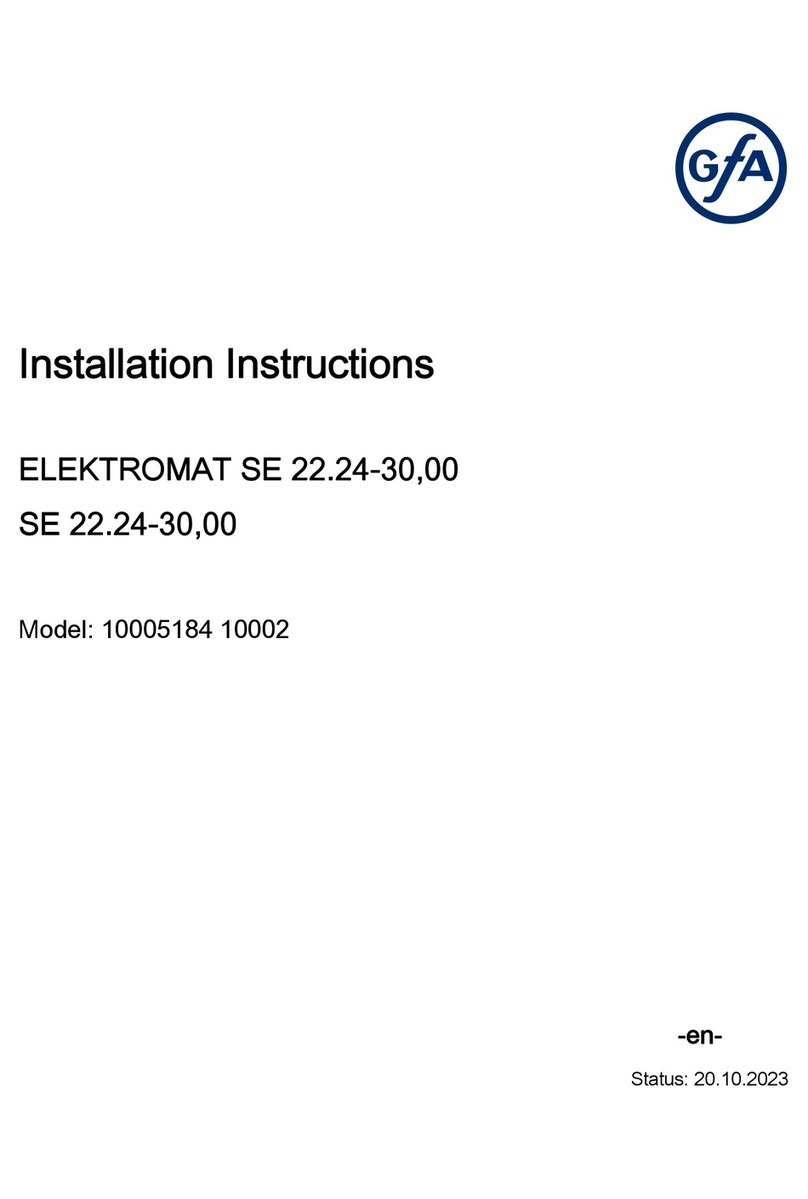
GFA
GFA ELEKTROMAT SE 22.24-30,00 installation instructions
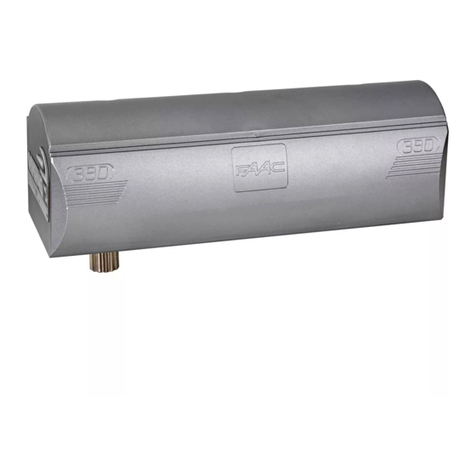
Viking Access Systems
Viking Access Systems X-390 Installation instructions and safety information
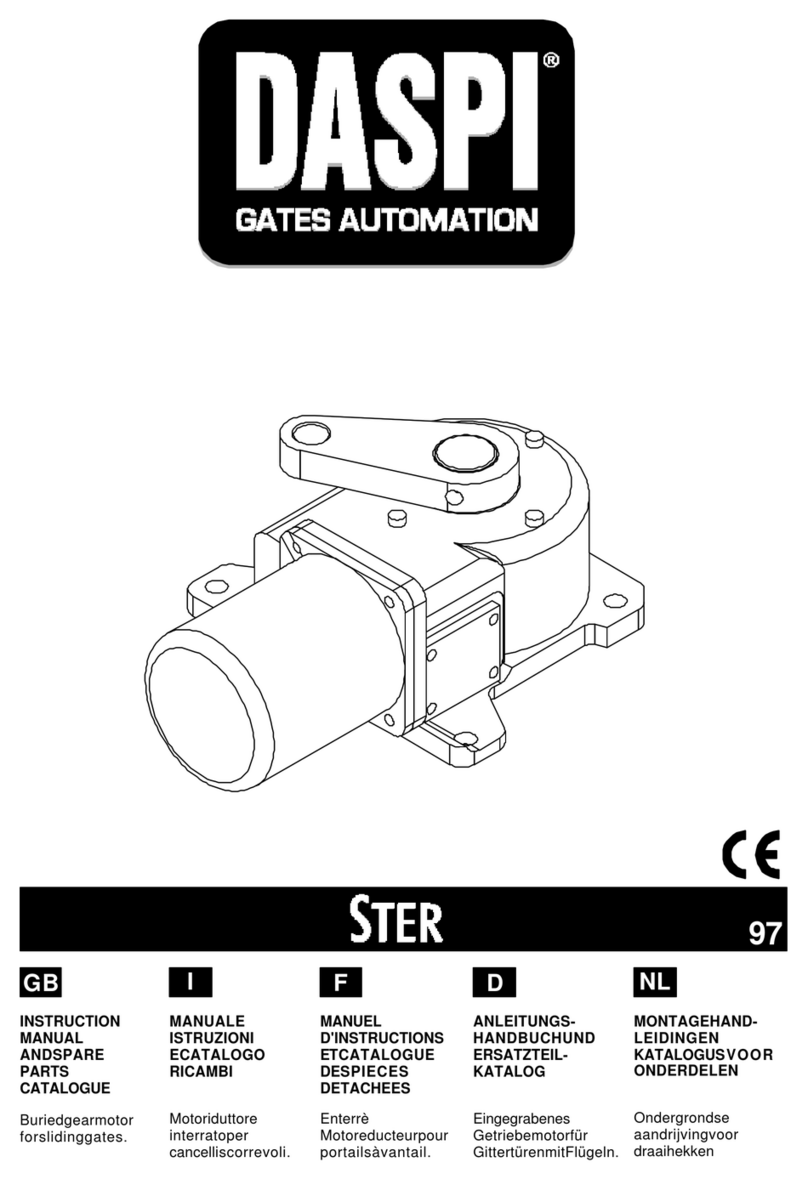
Daspi
Daspi STER instruction manual

SOMFY
SOMFY IXENGO J S 230V installation instructions

Beninca
Beninca VN.S40V manual
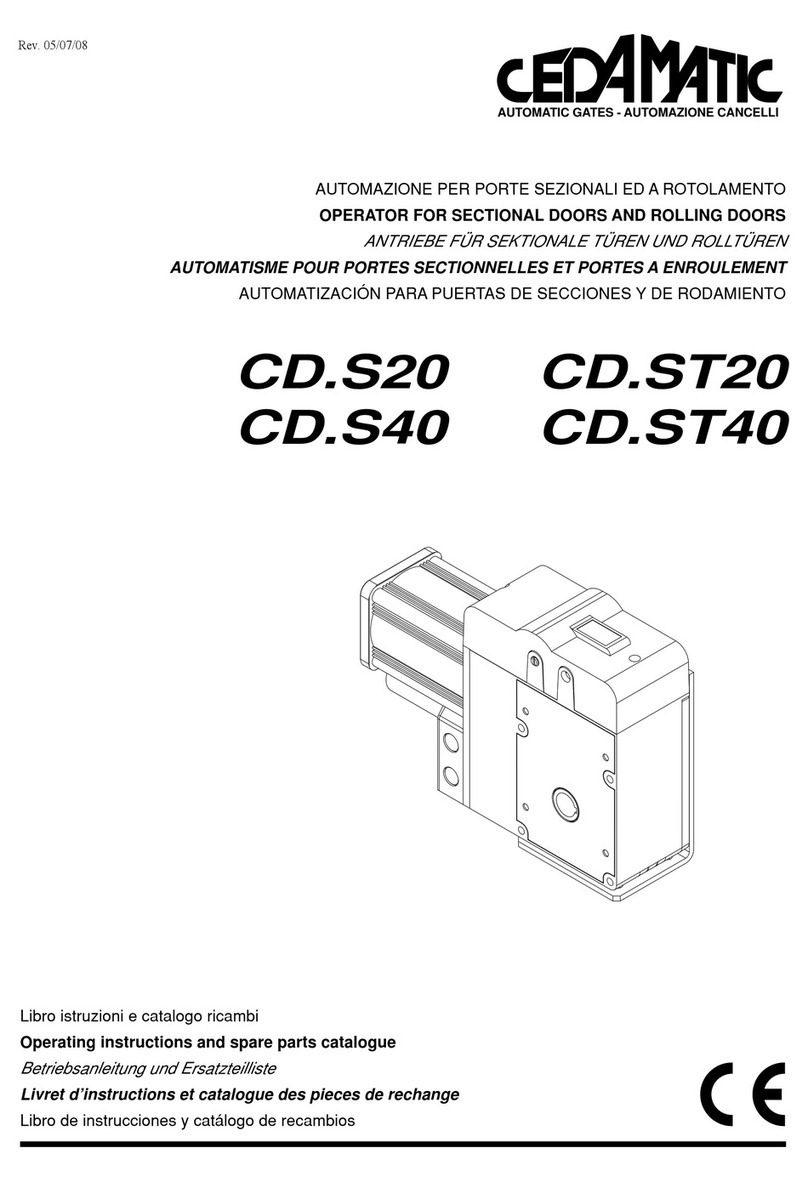
cedamatic
cedamatic CD.S20 operating instructions