GE CL 5 User manual

CL 5
Operating Manual
Ident-Nr. 021-002-296
Issue 01
CL 5
Operating Manual
Ident-Nr. 021-002-296
Issue 01

Issue 01, 04/2005 applies to software version XX.04.XX
Issue 01, 04/2005 applies to software version XX.04.XX

CL 5 Issue 01, 04/05 0-1
Contents
1 General Information........................... 1-1
1.1 Supplyin Power to the CL 5................. 1-2
1.2 Powerin On and Off the Instrument .... 1-4
1.3 Key Features of the CL 5........................ 1-4
CL 5 Precision Thickness
Measurement Base Instrument .............. 1-5
Instrument Options .................................. 1-
1.4 Whats in this Manual ............................ 1-6
2 Understandin the Keypad,
Menu System, and Displays ............. 2-1
2.1 Keypad Features .................................... 2-2
2.2 Interpretin Display Screens ................. 2-2
2.3 Workin with the Confi uration
Display .................................................2-10
3 Settin Up the CL 5 ........................... 3-1
3.1 Connectin a Probe and Loadin a
Setup File ............................................. 3-3
3.2 Confi urin the Instrument ................... 3-6
3.2.1 Setting Instrument Gain ................ 3-8
3.2.2 Setting Update Rate ..................... 3-8
3.2.3 Setting Nominal Thickness ........... 3-8
3.3 Instrument Calibration ........................... 3-9
3.4 Settin the Maximum and Minimum
Alarms .................................................. 3-9
3.5 Creatin and Erasin Custom Setup
Files .....................................................3-11
3.6 Lockin and Unlockin Instrument
Settin s ...............................................3-14
4 Measurin Thickness ........................ 4-1
4.1 Selectin the Displayed View ................ 4-2
4.2 Normal Measurement Mode
(No A-Scan) .......................................... 4-3
4.3 Min Scan and Max Scan Measurement
Mode ..................................................... 4-6
CL 5 Issue 01, 04/05 0-1
Contents
1 General Information........................... 1-1
1.1 Supplyin Power to the CL 5................. 1-2
1.2 Powerin On and Off the Instrument .... 1-4
1.3 Key Features of the CL 5........................ 1-4
CL 5 Precision Thickness
Measurement Base Instrument .............. 1-5
Instrument Options .................................. 1-
1.4 Whats in this Manual ............................ 1-6
2 Understandin the Keypad,
Menu System, and Displays ............. 2-1
2.1 Keypad Features .................................... 2-2
2.2 Interpretin Display Screens ................. 2-2
2.3 Workin with the Confi uration
Display .................................................2-10
3 Settin Up the CL 5 ........................... 3-1
3.1 Connectin a Probe and Loadin a
Setup File ............................................. 3-3
3.2 Confi urin the Instrument ................... 3-6
3.2.1 Setting Instrument Gain ................ 3-8
3.2.2 Setting Update Rate ..................... 3-8
3.2.3 Setting Nominal Thickness ........... 3-8
3.3 Instrument Calibration ........................... 3-9
3.4 Settin the Maximum and Minimum
Alarms .................................................. 3-9
3.5 Creatin and Erasin Custom Setup
Files .....................................................3-11
3.6 Lockin and Unlockin Instrument
Settin s ...............................................3-14
4 Measurin Thickness ........................ 4-1
4.1 Selectin the Displayed View ................ 4-2
4.2 Normal Measurement Mode
(No A-Scan) .......................................... 4-3
4.3 Min Scan and Max Scan Measurement
Mode ..................................................... 4-6

0-2 Issue 01, 04/05 CL 5
Contents
4.4 Differential/Rate-of-Reduction
Measurement Mode ............................. 4-8
4.5 Thickness + A-Scan Measurement
Mode (Optional) ..................................4-10
4.6 Velocity Measurement Mode
(Optional) ............................................. 4-8
5 Usin the Optional Data Recorder ... 5-1
5.1 Creatin a New Data Recorder File ....... 5-2
5.2 Recallin and Erasin Stored Data
Recorder Files ...................................... 5-4
5.3 Recordin Thickness and Velocity
Measurements in Data Recorder
Files ...................................................... 5-5
5.3.1 Recording A-Scans in Data
Recorder Files .............................. 5-
5.3.2 Navigating Through Data
Recorder Files .............................. 5-
5.4 Printin a Report.................................... 5-6
6 I/O Features ........................................ 6-1
6.1 Transmittin Data to an External
Device ..................................................... 6-2
6.2 Settin Communication Speed
(Baud Rate) and Connectin to a PC... 6-4
6.3 Remote Commands ............................... 6-4
7 Specifications
7.1 Instrument Specifications ..................... 7-2
7.2 A-Scan Option Features......................... 7-5
7.3 Velocity Measurement Option
Features ................................................ 7-5
7.4 Data Recorder Option Features ............. 7-6
7.5 CL 5 Probe/Transducer
Specifications....................................... 7-6
0-2 Issue 01, 04/05 CL 5
Contents
4.4 Differential/Rate-of-Reduction
Measurement Mode ............................. 4-8
4.5 Thickness + A-Scan Measurement
Mode (Optional) ..................................4-10
4.6 Velocity Measurement Mode
(Optional) ............................................. 4-8
5 Usin the Optional Data Recorder ... 5-1
5.1 Creatin a New Data Recorder File ....... 5-2
5.2 Recallin and Erasin Stored Data
Recorder Files ...................................... 5-4
5.3 Recordin Thickness and Velocity
Measurements in Data Recorder
Files ...................................................... 5-5
5.3.1 Recording A-Scans in Data
Recorder Files .............................. 5-
5.3.2 Navigating Through Data
Recorder Files .............................. 5-
5.4 Printin a Report.................................... 5-6
6 I/O Features ........................................ 6-1
6.1 Transmittin Data to an External
Device ..................................................... 6-2
6.2 Settin Communication Speed
(Baud Rate) and Connectin to a PC... 6-4
6.3 Remote Commands ............................... 6-4
7 Specifications
7.1 Instrument Specifications ..................... 7-2
7.2 A-Scan Option Features......................... 7-5
7.3 Velocity Measurement Option
Features ................................................ 7-5
7.4 Data Recorder Option Features ............. 7-6
7.5 CL 5 Probe/Transducer
Specifications....................................... 7-6

CL 5 Issue 01, 04/05 0-3
Contents
8 Maintenance
Care of the Instrument .................................... 8-2
9 Appendix............................................ 9-1
9.1 Resettin the Operatin Software ......... 9-2
9.2 Up radin the Operatin Software ....... 9-2
9.3 EMC Documentation .............................. 9-3
9.4 Manufacturer/Service Addresses .......... 9-5
10 Index ................................................. 10-1
CL 5 Issue 01, 04/05 0-3
Contents
8 Maintenance
Care of the Instrument .................................... 8-2
9 Appendix............................................ 9-1
9.1 Resettin the Operatin Software ......... 9-2
9.2 Up radin the Operatin Software ....... 9-2
9.3 EMC Documentation .............................. 9-3
9.4 Manufacturer/Service Addresses .......... 9-5
10 Index ................................................. 10-1

0-4 Issue 01, 04/05 CL 5
Important Notice
Important Notice
The following information must be read and understood
by any user of a GE Inspection Technologies ultrasonic
thickness gauge. Failure to follow these instructions
can lead to errors in thickness measurements or other
test results. Decisions based on erroneous results can,
in turn, lead to property damage, personal injury or
death.
General Warnin s
Proper use of ultrasonic test equipment requires three
essential elements:
Selection of the correct test equipment.
Knowledge of the specific test application
requirements.
Training on the part of the instrument operator.
This operating manual provides instruction in the basic
set up and operation of the thickness gauge. There are,
however, additional factors which affect the use of
ultrasonic test equipment. Specific information
regarding these additional factors is beyond the scope
of this manual. The operator should refer to textbooks
on the subject of ultrasonic testing for more detailed
information.
Operator Trainin
Operators must receive adequate training before using
ultrasonic test equipment. Operators must be trained in
general ultrasonic testing procedures and in the set up
and performance required by a particular test.
Operators must understand:
Soundwave propagation theory.
Effects of the velocity of sound of the test material.
Behavior of the sound wave where two different
materials are in contact.
Areas covered by the sound beam.
More specific information about operator training, quali-
fication, certification, and test specifications is avail-
able from various technical societies, industry groups,
and government agencies.
0-4 Issue 01, 04/05 CL 5
Important Notice
Important Notice
The following information must be read and understood
by any user of a GE Inspection Technologies ultrasonic
thickness gauge. Failure to follow these instructions
can lead to errors in thickness measurements or other
test results. Decisions based on erroneous results can,
in turn, lead to property damage, personal injury or
death.
General Warnin s
Proper use of ultrasonic test equipment requires three
essential elements:
Selection of the correct test equipment.
Knowledge of the specific test application
requirements.
Training on the part of the instrument operator.
This operating manual provides instruction in the basic
set up and operation of the thickness gauge. There are,
however, additional factors which affect the use of
ultrasonic test equipment. Specific information
regarding these additional factors is beyond the scope
of this manual. The operator should refer to textbooks
on the subject of ultrasonic testing for more detailed
information.
Operator Trainin
Operators must receive adequate training before using
ultrasonic test equipment. Operators must be trained in
general ultrasonic testing procedures and in the set up
and performance required by a particular test.
Operators must understand:
Soundwave propagation theory.
Effects of the velocity of sound of the test material.
Behavior of the sound wave where two different
materials are in contact.
Areas covered by the sound beam.
More specific information about operator training, quali-
fication, certification, and test specifications is avail-
able from various technical societies, industry groups,
and government agencies.

CL 5 Issue 01, 04/05 0-5
Important Notice
Testin Limitations
In ultrasonic testing, information is obtained only from
within the limits of the sound beam. Operators must
exercise great caution in making inferences about the
test material outside the limits of the sound beam. For
example, when testing large materials it may be
impossible or impractical to inspect the entire test
piece.
When a less-than-complete inspection is to be
performed, the operator must be shown the specific
areas to inspect. Inferences about the condition of
areas not inspected, based on data from the evaluated
areas, should only be attempted by personnel fully
trained in applicable statistical and probability
techniques. In particular, materials subject to erosion
or corrosion, in which conditions can vary significantly
in any given area, should only be evaluated by fully
trained and experienced operators.
Sound beams reflect from the first interior surface
encountered. Because of part geometry and over-
lapped flaws or overlapped surfaces, thickness gauges
may measure the distance to an internal flaw rather
than to the back wall of the material. Operators must
take steps to ensure that the entire thickness of the
test material is being examined.
Ultrasonic Thickness Measurement Critical
Operatin Procedures
The following operating procedures must be observed
by all users of ultrasonic thickness gauges in order to
minimize errors in test results.
1. Calibration of Sound Velocity
The principle of operation of an ultrasonic thickness
gauge is that the instrument measures the time of flight
of an ultrasonic pulse through the test piece and
multiplies this time by the velocity of sound in the
material. Thickness measuring error is minimized by
ensuring that the sound velocity to which the instru-
ment is calibrated is the sound velocity of the material
being tested. Actual sound velocities in materials often
vary significantly from the values found in published
tables. In all cases, best results are obtained if the
instrument is calibrated on a velocity reference block
made from the same material as the test piece; this
block should be flat and smooth and as thick as the
maximum thickness of the test piece.
CL 5 Issue 01, 04/05 0-5
Important Notice
Testin Limitations
In ultrasonic testing, information is obtained only from
within the limits of the sound beam. Operators must
exercise great caution in making inferences about the
test material outside the limits of the sound beam. For
example, when testing large materials it may be
impossible or impractical to inspect the entire test
piece.
When a less-than-complete inspection is to be
performed, the operator must be shown the specific
areas to inspect. Inferences about the condition of
areas not inspected, based on data from the evaluated
areas, should only be attempted by personnel fully
trained in applicable statistical and probability
techniques. In particular, materials subject to erosion
or corrosion, in which conditions can vary significantly
in any given area, should only be evaluated by fully
trained and experienced operators.
Sound beams reflect from the first interior surface
encountered. Because of part geometry and over-
lapped flaws or overlapped surfaces, thickness gauges
may measure the distance to an internal flaw rather
than to the back wall of the material. Operators must
take steps to ensure that the entire thickness of the
test material is being examined.
Ultrasonic Thickness Measurement Critical
Operatin Procedures
The following operating procedures must be observed
by all users of ultrasonic thickness gauges in order to
minimize errors in test results.
1. Calibration of Sound Velocity
The principle of operation of an ultrasonic thickness
gauge is that the instrument measures the time of flight
of an ultrasonic pulse through the test piece and
multiplies this time by the velocity of sound in the
material. Thickness measuring error is minimized by
ensuring that the sound velocity to which the instru-
ment is calibrated is the sound velocity of the material
being tested. Actual sound velocities in materials often
vary significantly from the values found in published
tables. In all cases, best results are obtained if the
instrument is calibrated on a velocity reference block
made from the same material as the test piece; this
block should be flat and smooth and as thick as the
maximum thickness of the test piece.

0- Issue 01, 04/05 CL 5
Important Notice
Operators should also be aware that the sound velocity
may not be constant in the material being tested; heat
treating, for example, can cause significant changes in
sound velocity. This must be considered when eval-
uating the accuracy of the thickness provided by this
instrument. Instruments should always be calibrated
before testing, and the calibration should be checked
after testing, to minimize testing errors.
2. Probe Zero Procedure
When performing a one-point calibration with a contact
probe, the probe zero procedure must be performed as
described in this manual. The probe zero block should
be clean, in good condition, and without noticeable
wear. Failure to properly perform the probe zero
procedure will cause inaccurate thickness readings.
3. Effects of Temperature on Calibration
Temperature variations change the sound velocity of
materials and transducer delay lines and, therefore,
calibrations. All calibrations should be performed on-
site, and with test blocks at the same temperature as
the test piece, to minimize errors due to temperature
variations.
4. Transducer Selection
The transducer used in testing must be in good
condition without noticeable wear of the front surface.
Badly worn transducers will have a reduced effective
measuring range. The specified range of the transducer
must include the complete range of thicknesses to be
tested. The temperature of the material to be tested
must be within the transducers temperature range.
5. Use of Couplants
Operators must be familiar with the use of ultrasonic
couplants. Testing skills must be developed so that
couplant is used and applied in a consistent manner to
minimize variations in couplant layer thickness and
errors in test results. Calibration and actual testing
should be performed under similar coupling conditions,
using a minimum amount of couplant and applying
consistent pressure on the transducer.
. Doubling
Ultrasonic thickness gauges will, under certain
conditions, display readings which are twice (or, in
some cases, three times) the actual material thickness
0- Issue 01, 04/05 CL 5
Important Notice
Operators should also be aware that the sound velocity
may not be constant in the material being tested; heat
treating, for example, can cause significant changes in
sound velocity. This must be considered when eval-
uating the accuracy of the thickness provided by this
instrument. Instruments should always be calibrated
before testing, and the calibration should be checked
after testing, to minimize testing errors.
2. Probe Zero Procedure
When performing a one-point calibration with a contact
probe, the probe zero procedure must be performed as
described in this manual. The probe zero block should
be clean, in good condition, and without noticeable
wear. Failure to properly perform the probe zero
procedure will cause inaccurate thickness readings.
3. Effects of Temperature on Calibration
Temperature variations change the sound velocity of
materials and transducer delay lines and, therefore,
calibrations. All calibrations should be performed on-
site, and with test blocks at the same temperature as
the test piece, to minimize errors due to temperature
variations.
4. Transducer Selection
The transducer used in testing must be in good
condition without noticeable wear of the front surface.
Badly worn transducers will have a reduced effective
measuring range. The specified range of the transducer
must include the complete range of thicknesses to be
tested. The temperature of the material to be tested
must be within the transducers temperature range.
5. Use of Couplants
Operators must be familiar with the use of ultrasonic
couplants. Testing skills must be developed so that
couplant is used and applied in a consistent manner to
minimize variations in couplant layer thickness and
errors in test results. Calibration and actual testing
should be performed under similar coupling conditions,
using a minimum amount of couplant and applying
consistent pressure on the transducer.
. Doubling
Ultrasonic thickness gauges will, under certain
conditions, display readings which are twice (or, in
some cases, three times) the actual material thickness

CL 5 Issue 01, 04/05 0-7
Important Notice
being measured. This effect, commonly known as
doubling, can occur below the minimum specified
range of the transducer. If the transducer being used is
worn, doubling is possible at a thickness greater than
the minimum of the specified range.
When using a new transducer, any reading which is
less than twice the minimum specified range of the
transducer may be a doubled reading, and the
thickness of the material being tested should be
verified by the use of other methods. If the transducer
shows any sign of wear, doubling may occur at a
second echo or other echo signal combinations may
produce a readable signal. The instrument reading and
apparent thickness are up to about twice the actual
value, resulting in a thickness greater than twice the
minimum of the specified range. This thickness should
be determined by calibrating the instrument/transducer
combination on reference blocks that represent the
complete range of possible thicknesses that may be
encountered in testing. This is particularly important
when the test piece is being ultrasonically measured for
the first time or in any case where the history of thick-
ness of the test specimen is unknown.
Safety Information
Attention:
The CL 5 is an instrument for materials testing. Any
use for medical applications or other purposes is not
allowed.
The CL 5 may only be used in industrial environments.
The CL 5 can be operated with batteries or while
plugged into an electrical outlet using the AC charger.
The power supply unit has the electrical safety class II.
Batteries:
For the battery operation of the CL 5, we recommend
the use of a lithium-polt battery pack provided.
Operation using alkaline batteries, NiMH or NiCAD
cells is possible. You should only use the products
recommended by us for the battery operation. Do not
attempt to use any lithium batteries that are not
provided with the instrument. Do not attempt to charge
the provided batteries on an outside charger.
CL 5 Issue 01, 04/05 0-7
Important Notice
being measured. This effect, commonly known as
doubling, can occur below the minimum specified
range of the transducer. If the transducer being used is
worn, doubling is possible at a thickness greater than
the minimum of the specified range.
When using a new transducer, any reading which is
less than twice the minimum specified range of the
transducer may be a doubled reading, and the
thickness of the material being tested should be
verified by the use of other methods. If the transducer
shows any sign of wear, doubling may occur at a
second echo or other echo signal combinations may
produce a readable signal. The instrument reading and
apparent thickness are up to about twice the actual
value, resulting in a thickness greater than twice the
minimum of the specified range. This thickness should
be determined by calibrating the instrument/transducer
combination on reference blocks that represent the
complete range of possible thicknesses that may be
encountered in testing. This is particularly important
when the test piece is being ultrasonically measured for
the first time or in any case where the history of thick-
ness of the test specimen is unknown.
Safety Information
Attention:
The CL 5 is an instrument for materials testing. Any
use for medical applications or other purposes is not
allowed.
The CL 5 may only be used in industrial environments.
The CL 5 can be operated with batteries or while
plugged into an electrical outlet using the AC charger.
The power supply unit has the electrical safety class II.
Batteries:
For the battery operation of the CL 5, we recommend
the use of a lithium-polt battery pack provided.
Operation using alkaline batteries, NiMH or NiCAD
cells is possible. You should only use the products
recommended by us for the battery operation. Do not
attempt to use any lithium batteries that are not
provided with the instrument. Do not attempt to charge
the provided batteries on an outside charger.

0-8 Issue 01, 04/05 CL 5
Important Notice
Software:
According to the current state of the art, software is
never completely free from errors. Before using any
software-controlled test equipment, please make sure
that the required functions operate perfectly in the
intended combination.
Defects/errors and exceptional stresses
If you have reason to believe that a safe operation of
your CL 5 is no longer possible, you have to disconnect
the instrument and secure it against unintentional
reconnection. Remove the batteries if necessary.
A safe operation is no longer possible e.g.:
The instrument shows visible damages
The instrument no longer operates perfectly
After prolonged storage under adverse conditions like
exceptional temperatures and/or especially high air
humidity, or corrosive environmental conditions.
Being subjected to heavy stresses during
transportation
Service
Every effort has been made to provide you with a
reliable product. However, should service become
necessary, GE Inspection Technologies, has estab-
lished a number of Factory Trained Service Centers.
For the location of the nearest facility refer to section
9.4 of this manual.
0-8 Issue 01, 04/05 CL 5
Important Notice
Software:
According to the current state of the art, software is
never completely free from errors. Before using any
software-controlled test equipment, please make sure
that the required functions operate perfectly in the
intended combination.
Defects/errors and exceptional stresses
If you have reason to believe that a safe operation of
your CL 5 is no longer possible, you have to disconnect
the instrument and secure it against unintentional
reconnection. Remove the batteries if necessary.
A safe operation is no longer possible e.g.:
The instrument shows visible damages
The instrument no longer operates perfectly
After prolonged storage under adverse conditions like
exceptional temperatures and/or especially high air
humidity, or corrosive environmental conditions.
Being subjected to heavy stresses during
transportation
Service
Every effort has been made to provide you with a
reliable product. However, should service become
necessary, GE Inspection Technologies, has estab-
lished a number of Factory Trained Service Centers.
For the location of the nearest facility refer to section
9.4 of this manual.

CL 5 Issue 01, 04/05 1-1
General Information 1
CL 5 Issue 01, 04/05 1-1
General Information 1

1-2 Issue 01, 04/05 CL 5
General Information Supplying Power to the CL 5
The CL 5 is an ultrasonic precision thickness
measurement device. Its available with optional live
A-Scan display, acoustic velocity measurement
capability, and a data recorder in which as many
10,000 thickness measurements per file can be stored.
This chapter of your manual introduces the key
features of the CL 5 and the contents of this operating
manual. The next chapter explains the keypad
functions and display-menu contents. Closely
reviewing the material in these two chapters will help
you make better use of the more detailed information
found throughout the rest of this manual.
In this chapter, youll learn
How to install batteries or connect the AC power
adapter to the instrument (Section 1.1)
How to Power on and off the instrument
(Section 1.2)
The features of the instrument and base instrument
package contents (Section 1.3)
The general content of each chapter in this manual
(Section 1.4)
1.1 Supplyin Power to the
CL 5
The instrument is powered by a Lithium (Li) battery
pack.
It will also accept three AA size Alkaline, NiCAD,
or NiMH (nickel metal hydride) battery types.
The Lithium battery, which is recommended, will
provide up to approximately 25 hours of service life.
This pack (and only this pack) may be recharged in
the instrument using the charger provided with your
instrument.
When other types of rechargeable batteries are
used, they must be removed from the instrument for
charging.
To install batteries, remove the battery-compartment
cover as shown in Figure 1-1. After inserting the Li
pack or three AA batteries according to the polarity
indicated in the battery compartment, replace the
compartment cover. Instructions on specifying battery
type are found in Section 3.2.
1-2 Issue 01, 04/05 CL 5
General Information Supplying Power to the CL 5
The CL 5 is an ultrasonic precision thickness
measurement device. Its available with optional live
A-Scan display, acoustic velocity measurement
capability, and a data recorder in which as many
10,000 thickness measurements per file can be stored.
This chapter of your manual introduces the key
features of the CL 5 and the contents of this operating
manual. The next chapter explains the keypad
functions and display-menu contents. Closely
reviewing the material in these two chapters will help
you make better use of the more detailed information
found throughout the rest of this manual.
In this chapter, youll learn
How to install batteries or connect the AC power
adapter to the instrument (Section 1.1)
How to Power on and off the instrument
(Section 1.2)
The features of the instrument and base instrument
package contents (Section 1.3)
The general content of each chapter in this manual
(Section 1.4)
1.1 Supplyin Power to the
CL 5
The instrument is powered by a Lithium (Li) battery
pack.
It will also accept three AA size Alkaline, NiCAD,
or NiMH (nickel metal hydride) battery types.
The Lithium battery, which is recommended, will
provide up to approximately 25 hours of service life.
This pack (and only this pack) may be recharged in
the instrument using the charger provided with your
instrument.
When other types of rechargeable batteries are
used, they must be removed from the instrument for
charging.
To install batteries, remove the battery-compartment
cover as shown in Figure 1-1. After inserting the Li
pack or three AA batteries according to the polarity
indicated in the battery compartment, replace the
compartment cover. Instructions on specifying battery
type are found in Section 3.2.

CL 5 Issue 01, 04/05 1-3
Supplying Power to the CL 5 General Information
FIGURE 1-1Insert batteries as shown here. Notice the location of the External Power onnector to which the
instruments Li battery packs charger be connected.
CL 5 Issue 01, 04/05 1-3
Supplying Power to the CL 5 General Information
FIGURE 1-1Insert batteries as shown here. Notice the location of the External Power onnector to which the
instruments Li battery packs charger be connected.

1-4 Issue 01, 04/05 CL 5
. Note:
When the battery indicator is in the last quarter as
indicated by the display screen symbol , replace
the batteries as soon as possible. The CL 5
automatically shuts off when batteries are too weak for
reliable operation. However, settings are saved and
restored when the instrument is turned on again. When
testing in remote locations, always carry spare
batteries.
. Note:
The instrument can be operated while the Li battery
packs charger is connected. This charger is connected
to the instrument though the connector shown in
Figure 1 1. When the charger is powering the
instrument, appears on the display screen. The
charger may only be connected when the GE
Inspection Technologies Li battery pack is installed in
the instrument.
1.2 Powerin On and Off the
Instrument
After a power source has been provided, power on the
instrument by pressing and holding until the
instrument turns on. Press and hold when the
instrument is on to turn if off.
1.3 Key Features of the CL 5
Large Hollow/filled thickness digits
Alarm Bar Graph
Standard and Custom parameter setups
Supports delay and contact probes
Alphanumeric naming of data locations
Lockout feature with password access
Lightweight .75 lbs (.34 Kg)
Large LCD Display with Backlight and Adjustable
Contrast
General Information Powering On and Off the Instrument
1-4 Issue 01, 04/05 CL 5
. Note:
When the battery indicator is in the last quarter as
indicated by the display screen symbol , replace
the batteries as soon as possible. The CL 5
automatically shuts off when batteries are too weak for
reliable operation. However, settings are saved and
restored when the instrument is turned on again. When
testing in remote locations, always carry spare
batteries.
. Note:
The instrument can be operated while the Li battery
packs charger is connected. This charger is connected
to the instrument though the connector shown in
Figure 1 1. When the charger is powering the
instrument, appears on the display screen. The
charger may only be connected when the GE
Inspection Technologies Li battery pack is installed in
the instrument.
1.2 Powerin On and Off the
Instrument
After a power source has been provided, power on the
instrument by pressing and holding until the
instrument turns on. Press and hold when the
instrument is on to turn if off.
1.3 Key Features of the CL 5
Large Hollow/filled thickness digits
Alarm Bar Graph
Standard and Custom parameter setups
Supports delay and contact probes
Alphanumeric naming of data locations
Lockout feature with password access
Lightweight .75 lbs (.34 Kg)
Large LCD Display with Backlight and Adjustable
Contrast
General Information Powering On and Off the Instrument

CL 5 Issue 01, 04/05 1-5
Approximately 25 hours life with the Li battery
pack or 3 AA alkaline batteries
Easy-to-use, single-level menu system
Multiple display-screen languages
User-selectable measurement resolution to 0.0001
inch (0.001 mm)
Normal (thickness), Min-Scan, Max-Scan, and
Differential/Rate of Reduction Measurement Modes
are Standard
Optional A-Scan provides A-Scan plus Thickness
Optional Data Recorder stores up to 10,000 thick-
ness measurements with A-Scan images attached
in as many as 120 data recorder files
Optional Velocity Measurement Mode includes an
electronically connected digital caliper for exact
measurement and automatic input of nominal
thickness
Field upgrades available via the GE Inspection
Technologies web site
Compatible with UltraMATE© and UltraMATE LITE©
software programs
CL 5 Precision Thickness Measurement
Base Instrument
Contents of the CL 5 Base Instrument
CL 5 Instrument
Lithium Battery Pack
Lithium Battery Pack Recharger
Plastic Carrying Case
Wire Stand
Two-Point Check Block (uncertified)
Couplant Sample
Firmware Upgrade CD-ROM (requires Serial PC
cable)
Operating Manual
Operating Instruction Card
Certificate of Conformity
Key Features of the CL 5 General Information
CL 5 Issue 01, 04/05 1-5
Approximately 25 hours life with the Li battery
pack or 3 AA alkaline batteries
Easy-to-use, single-level menu system
Multiple display-screen languages
User-selectable measurement resolution to 0.0001
inch (0.001 mm)
Normal (thickness), Min-Scan, Max-Scan, and
Differential/Rate of Reduction Measurement Modes
are Standard
Optional A-Scan provides A-Scan plus Thickness
Optional Data Recorder stores up to 10,000 thick-
ness measurements with A-Scan images attached
in as many as 120 data recorder files
Optional Velocity Measurement Mode includes an
electronically connected digital caliper for exact
measurement and automatic input of nominal
thickness
Field upgrades available via the GE Inspection
Technologies web site
Compatible with UltraMATE© and UltraMATE LITE©
software programs
CL 5 Precision Thickness Measurement
Base Instrument
Contents of the CL 5 Base Instrument
CL 5 Instrument
Lithium Battery Pack
Lithium Battery Pack Recharger
Plastic Carrying Case
Wire Stand
Two-Point Check Block (uncertified)
Couplant Sample
Firmware Upgrade CD-ROM (requires Serial PC
cable)
Operating Manual
Operating Instruction Card
Certificate of Conformity
Key Features of the CL 5 General Information

1- Issue 01, 04/05 CL 5
Instrument Options
A-Scan Upgrade Option
Data Recorder Upgrade Option
Velocity Measurement Option
1.4 Whats in this Manual
The CL 5 Operating Manual is divided into ten
chapters. All chapters except 4 and 5 apply to all
instruments. The last two sections of Chapter 4 apply
only to instruments equipped with the A-Scan or
Velocity measurement options. Chapter 5 applies only
to instruments equipped with the Data Recorder option.
Note that any CL 5 can be retrofitted to incorporate
these options. Following is a summary of Chapters 1
through 10:
Chapter 1General Introduction
Supplying Power to the instrument
Powering on and off the instrument
Overview of instrument features
Explanation of the operating manual contents
Chapter 2Understandin the Keypad, Menu
System, and Displays
Operations performed by each key
Navigating the display screens
Overview of menu functions
Explanation of display features (base model, data
recorder, and A-Scan equipped instruments)
Definition of icons
Chapter 3Settin Up the CL 5
Install a probe and configure the instrument by
loading a setup file
Set up the instrument display appearance (for base
model and A-Scan equipped instruments) and make
other configuration settings
General Information Whats in the Manual
1- Issue 01, 04/05 CL 5
Instrument Options
A-Scan Upgrade Option
Data Recorder Upgrade Option
Velocity Measurement Option
1.4 Whats in this Manual
The CL 5 Operating Manual is divided into ten
chapters. All chapters except 4 and 5 apply to all
instruments. The last two sections of Chapter 4 apply
only to instruments equipped with the A-Scan or
Velocity measurement options. Chapter 5 applies only
to instruments equipped with the Data Recorder option.
Note that any CL 5 can be retrofitted to incorporate
these options. Following is a summary of Chapters 1
through 10:
Chapter 1General Introduction
Supplying Power to the instrument
Powering on and off the instrument
Overview of instrument features
Explanation of the operating manual contents
Chapter 2Understandin the Keypad, Menu
System, and Displays
Operations performed by each key
Navigating the display screens
Overview of menu functions
Explanation of display features (base model, data
recorder, and A-Scan equipped instruments)
Definition of icons
Chapter 3Settin Up the CL 5
Install a probe and configure the instrument by
loading a setup file
Set up the instrument display appearance (for base
model and A-Scan equipped instruments) and make
other configuration settings
General Information Whats in the Manual

CL 5 Issue 01, 04/05 1-7
Whats in this Manual General Information
Adjust the instrument gain setting
Specify the nominal material thickness
Calibrate and zero the instrument/probe combination
Set maximum and minimum alarm values
Create and erase custom setup files
Lock and unlock instrument controls
Chapter 4Measurin Thickness
Specify and use the Normal measurement mode (No
A-Scan)
Operate in Min-Scan and Max-Scan Measurement
mode
Operate in Differential/Rate of Reduction
measurement mode
Select and interpret the A-Scan plus Thickness
measurement mode (Optional)
Magnify the displayed A-Scan using the Zoom
control
Freeze the thickness reading and A-Scan
Connect the digital caliper and measure acoustic
velocity (Optional)
Chapter 5Usin the Optional Data Recorder
Create, recall, and delete data recorder files
Store A-Scan and thickness readings in data
recorder files
Navigate data recorder file locations
Attach notes to the data recorder file
Print reports
Chapter 6I/O Technical Details
Configure the instrument to communicate with PCs
and printers
Thickness value format
Remote control codes
CL 5 Issue 01, 04/05 1-7
Whats in this Manual General Information
Adjust the instrument gain setting
Specify the nominal material thickness
Calibrate and zero the instrument/probe combination
Set maximum and minimum alarm values
Create and erase custom setup files
Lock and unlock instrument controls
Chapter 4Measurin Thickness
Specify and use the Normal measurement mode (No
A-Scan)
Operate in Min-Scan and Max-Scan Measurement
mode
Operate in Differential/Rate of Reduction
measurement mode
Select and interpret the A-Scan plus Thickness
measurement mode (Optional)
Magnify the displayed A-Scan using the Zoom
control
Freeze the thickness reading and A-Scan
Connect the digital caliper and measure acoustic
velocity (Optional)
Chapter 5Usin the Optional Data Recorder
Create, recall, and delete data recorder files
Store A-Scan and thickness readings in data
recorder files
Navigate data recorder file locations
Attach notes to the data recorder file
Print reports
Chapter 6I/O Technical Details
Configure the instrument to communicate with PCs
and printers
Thickness value format
Remote control codes

1-8 Issue 01, 04/05 CL 5
Chapter 7Specifications
Chapter 8Maintenance
Chapter 9Appendix
Reset the operating software
Upgrade the operating software
EMC documentation
How to obtain service
Chapter 10Index
Whats in this Manual General Information
1-8 Issue 01, 04/05 CL 5
Chapter 7Specifications
Chapter 8Maintenance
Chapter 9Appendix
Reset the operating software
Upgrade the operating software
EMC documentation
How to obtain service
Chapter 10Index
Whats in this Manual General Information

CL 5 Issue 01, 04/05 2-1
Understandin the Keypad,
Menu System, and Displays 2
CL 5 Issue 01, 04/05 2-1
Understandin the Keypad,
Menu System, and Displays 2

2-2 Issue 01, 04/05 CL 5
Understandin the Keypad, Menu System, and Displays Keypad Features
The CL 5s display, keypad, and functional commands
are easy to interpret and use. In this chapter youll find
a brief explanation of all display and keypad features.
Youll also find references to manual sections where
more detailed information is available.
Note that the CL 5s display screen contents vary
depending on the optional features installed and the
operational settings selected. Display screens shown
in this chapter represent those found in all instrument
configurations including:
Base Model
A-Scan Option Installed
Data Recorder Option Installed
A-Scan and Data Recorder Options Installed
2.1 Keypad Features
The instruments keypad includes dedicated keys
( and ), arrow keys ( , , , ), and three
virtual function keys ( ). Key functions are described
in Figure 2-1.
2.2 Interpretin Display Screens
This section of your manual describes the layout of the
CL 5s primary display modes including the:
Measurement Display Mode Indicates measured
thickness, contains status icons, displays data
recorder location and file name (when this option is
installed and activated), and the live A-Scan display
(when this option is installed and activated). Figure
2-2 shows four representative display screens.
2-2 Issue 01, 04/05 CL 5
Understandin the Keypad, Menu System, and Displays Keypad Features
The CL 5s display, keypad, and functional commands
are easy to interpret and use. In this chapter youll find
a brief explanation of all display and keypad features.
Youll also find references to manual sections where
more detailed information is available.
Note that the CL 5s display screen contents vary
depending on the optional features installed and the
operational settings selected. Display screens shown
in this chapter represent those found in all instrument
configurations including:
Base Model
A-Scan Option Installed
Data Recorder Option Installed
A-Scan and Data Recorder Options Installed
2.1 Keypad Features
The instruments keypad includes dedicated keys
( and ), arrow keys ( , , , ), and three
virtual function keys ( ). Key functions are described
in Figure 2-1.
2.2 Interpretin Display Screens
This section of your manual describes the layout of the
CL 5s primary display modes including the:
Measurement Display Mode Indicates measured
thickness, contains status icons, displays data
recorder location and file name (when this option is
installed and activated), and the live A-Scan display
(when this option is installed and activated). Figure
2-2 shows four representative display screens.
Other GE Measuring Instrument manuals
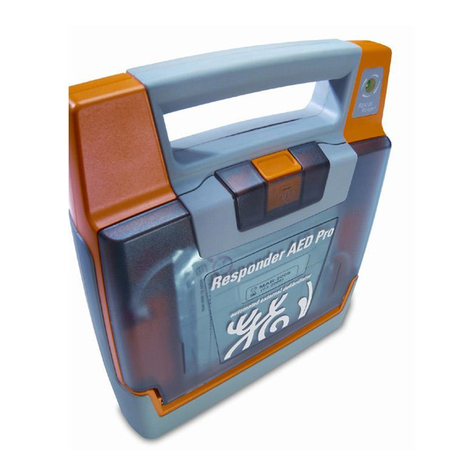
GE
GE AED Pro User manual
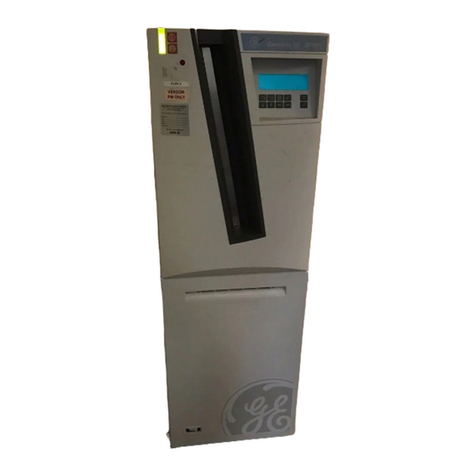
GE
GE Centricity SP1001 User manual
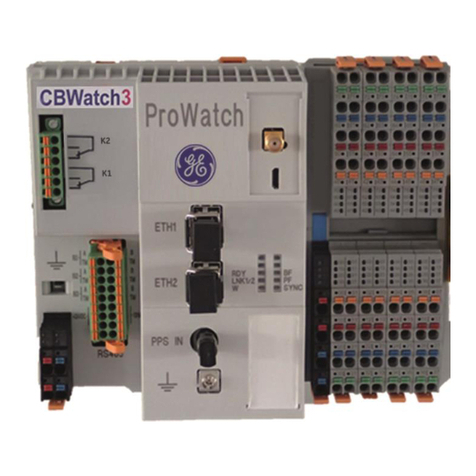
GE
GE CB Watch 3 User manual

GE
GE WiMAX WX-I210+c Installation guide
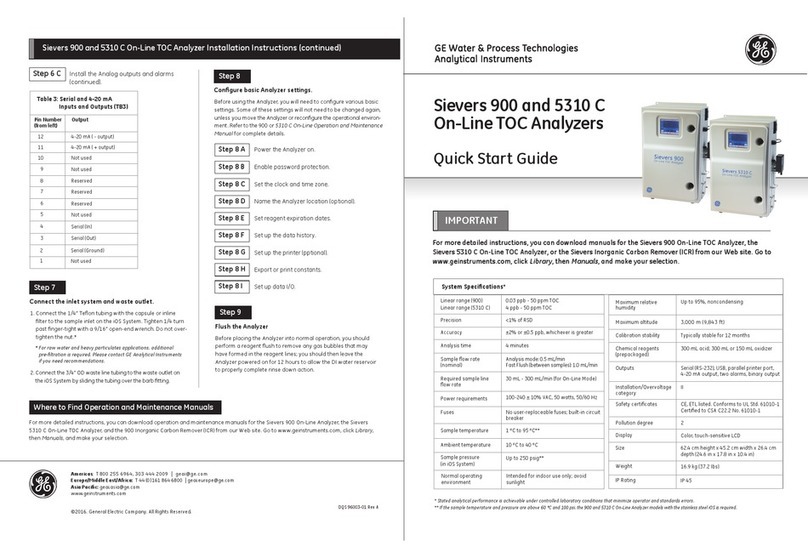
GE
GE Sievers 900 User manual

GE
GE PM880 User manual
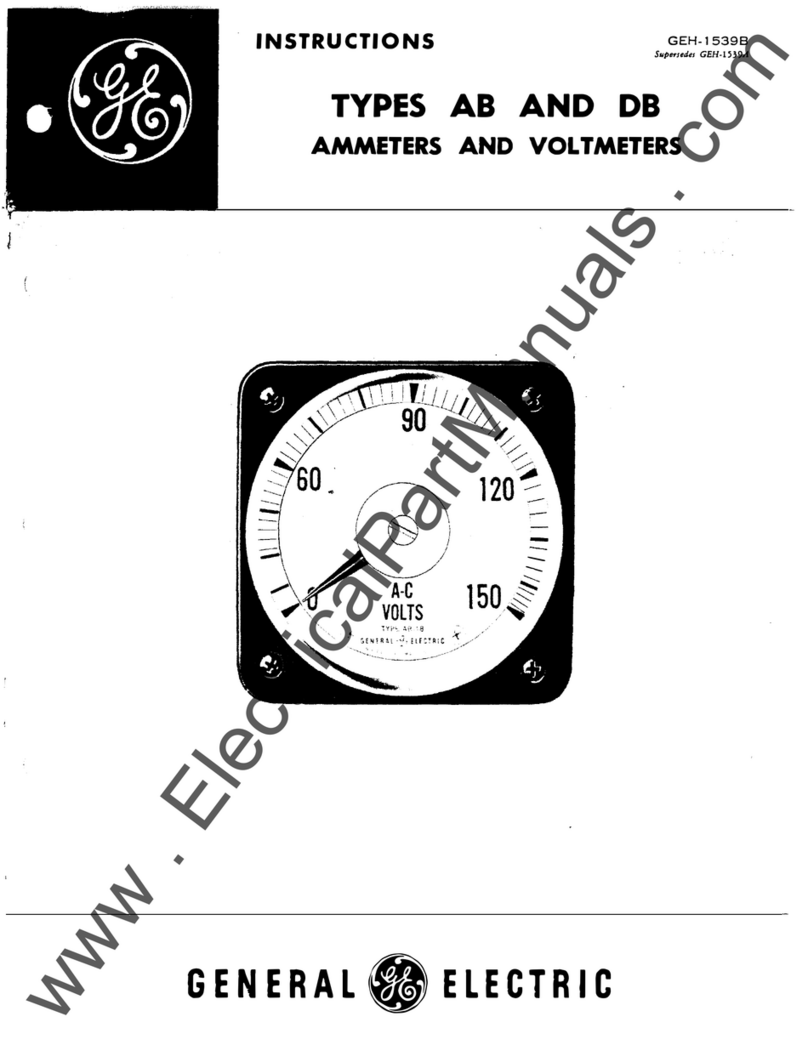
GE
GE AB Series User manual
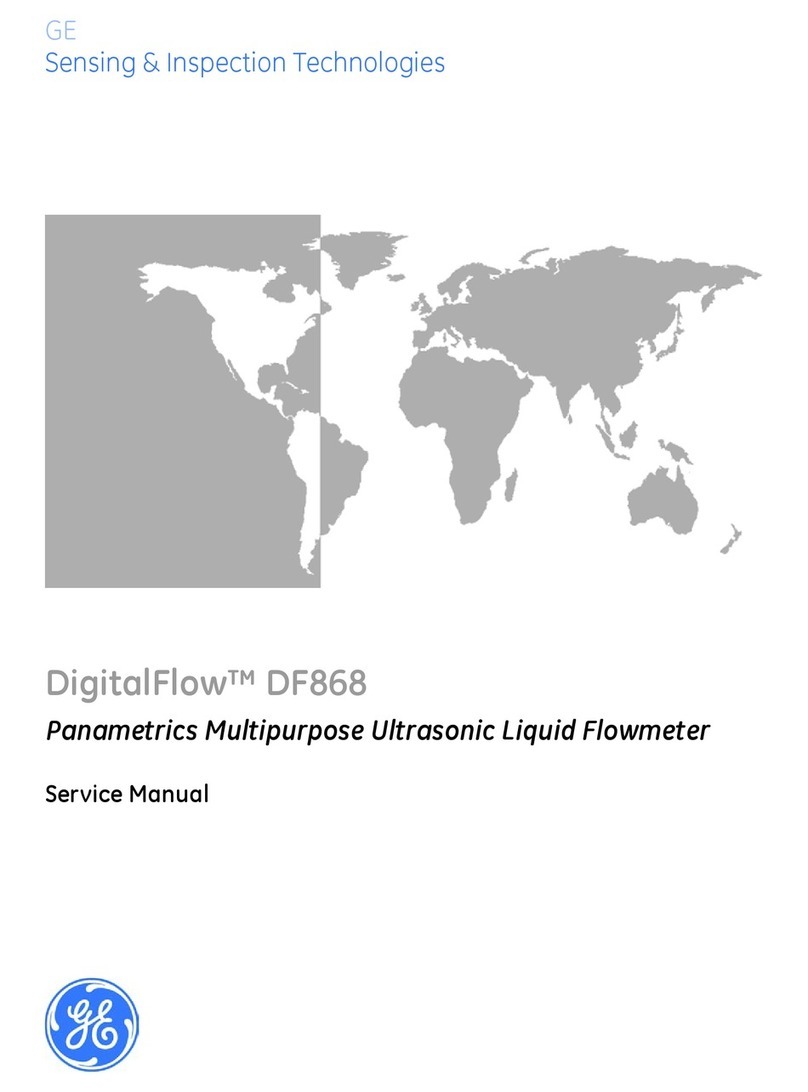
GE
GE DigitalFlow DF968 User manual

GE
GE Bently Nevada 3300/16 User manual
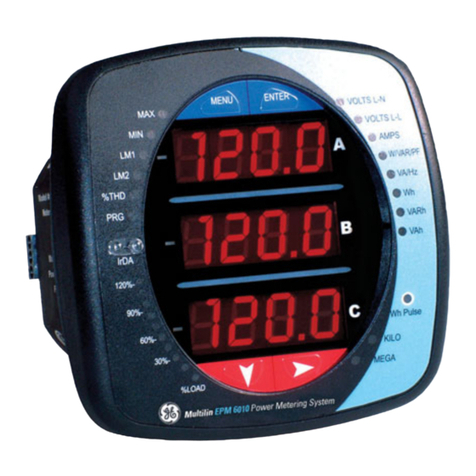
GE
GE Multilin EPM 6010 User manual
Popular Measuring Instrument manuals by other brands
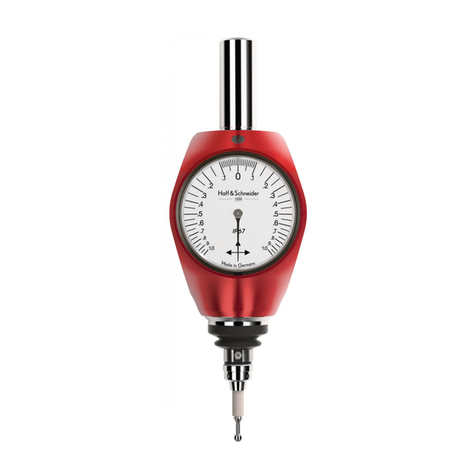
Haff & Schneider
Haff & Schneider 3D-Touch Probe 2007 Operation instructions
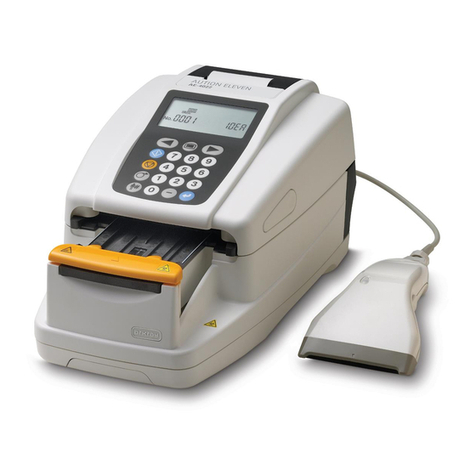
Arkray
Arkray AUTION ELEVEN AE-4022 Quick reference guide

Apera
Apera PH60 quick start guide
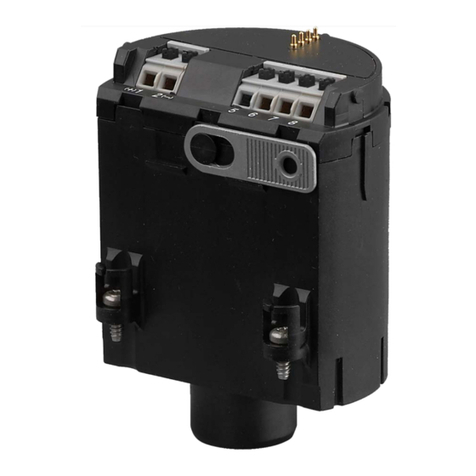
Vega
Vega VEGAFLEX FX-E.80H operating instructions
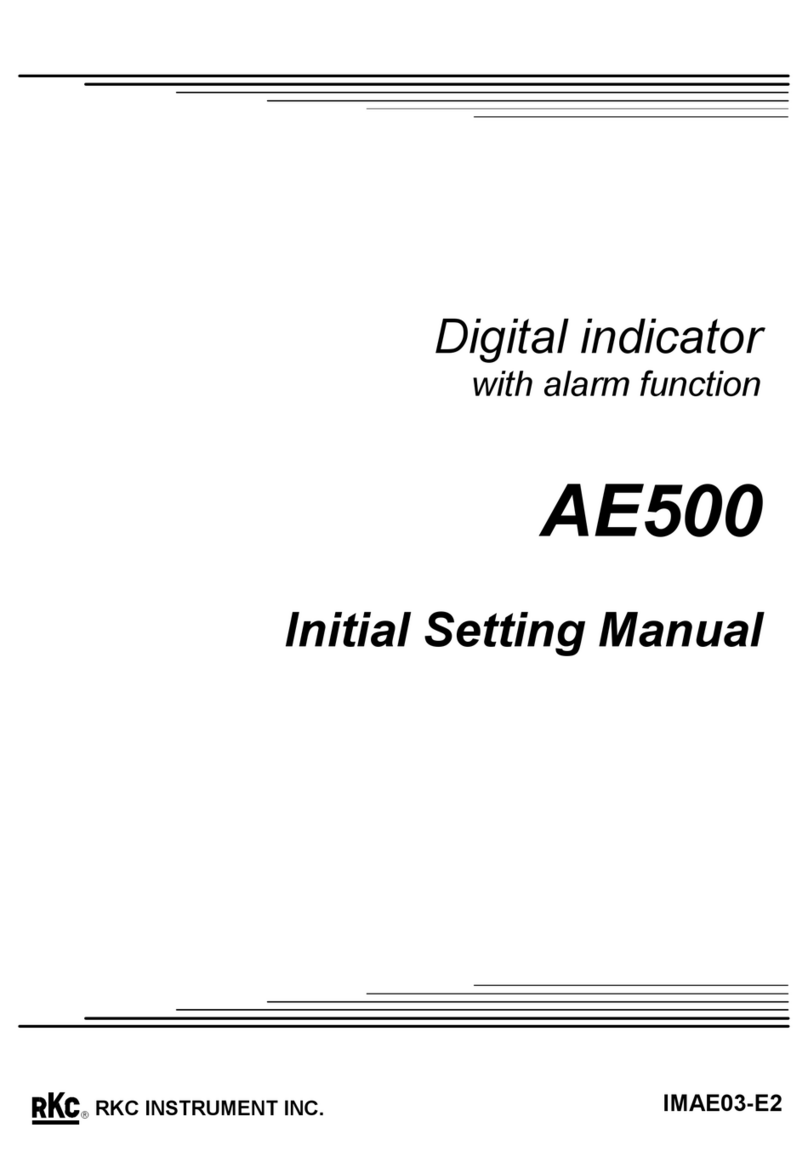
RKC INSTRUMENT
RKC INSTRUMENT AE500 INITIAL SETTING MANUAL
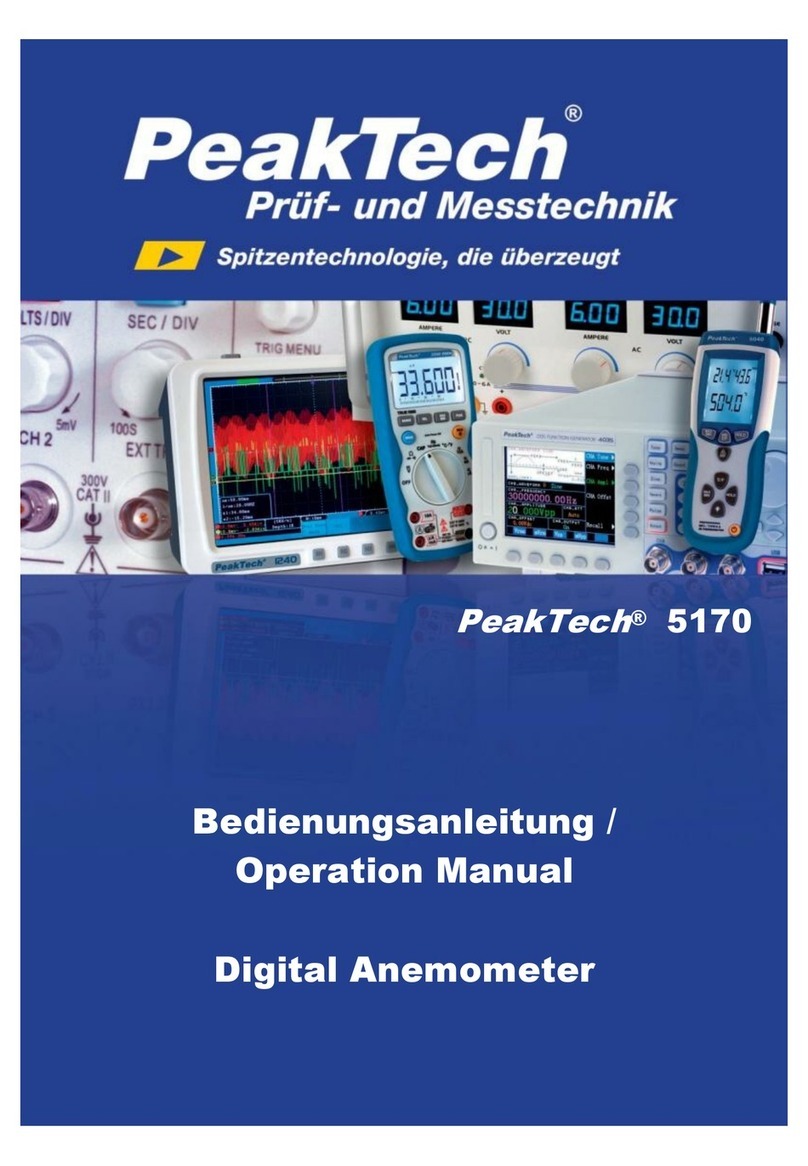
PeakTech
PeakTech 5170 Operation manual