GE GSY51A User manual

GEK
-
45441
DESCRIPTION
3
APPLICATION
OPERATION
OF
SCHEME
APPLICATION
CONSIDERATIONS
3
4
5
6
RATINGS
7
CURRENT
CIRCUIT
POTENTIAL
CIRCUIT
.
.
.
AMBIENT
TEMPERATURES
DC
RATINGS
TARGET
/
SEAL
-
IN
MHO
UNIT
CONTACTS
.
.
.
7
7
7
7
8
8
OPERATING
PRINCIPLES
9
CHARACTERISTICS
9
BURDENS
9
CURRENT
CIRCUITS
.
.
POTENTIAL
CIRCUITS
9
10
CALCULATION
OF
SETTINGS
GRAPHICAL
PROCEDURE
BLINDER
SETTINGS
MHO
UNIT
SETTING
VERIFICATION
OF
SETTINGS
10
10
10
11
12
CONSTRUCTION
13
GENERAL
13
DRAWOUT
RELAYS
.
.
.
POWER
REQUIREMENTS
13
13
ACCEPTANCE
TESTS
VISUAL
INSPECTION
MECHANICAL
INSPECTION
ELECTRICAL
TESTS
MHO
UNIT
-
ACCEPTANCE
TESTS
(
STANDARD
FACTORY
CALIBRATION
)
MHO
UNIT
-
ACCEPTANCE
TESTS
(
FACTORY
ADJUSTED
PER
CUSTOMER
'
S
SETTINGS
)
13
14
14
15
18
20
INSTALLATION
PROCEDURE
.
.
.
.
INSPECTION
LOCATION
MOUNTING
CONNECTIONS
MECHANICAL
INSPECTION
20
20
20
20
21
21
PERIODIC
CHECKS
AND
ROUTINE
MAINTENANCE
CONTACT
CLEANING
SERVICING
(
STANDARD
FACTORY
CALIBRATION
)
SERVICING
(
FACTORY
ADJUSTED
PER
CUSTOMER
'
S
SETTINGS
)
21
21
22
24
RENEWAL
PARTS
-
2
-
Courtesy of NationalSwitchgear.com

GEK
-
45441
MHO
AND
AUXILIARY
RELAY
FOR
OUT
-
OF
-
STEP
PROTECTION
TYPE
GSY
51
A
DESCRIPTION
The
Type
GSY
51
A
relay
is
designed
specifically
for
use
in
conjunction
with
the
Type
CEX
57
E
angle
-
impedance
relay
to
detect
an
out
-
of
-
step
condition
on
a
power
system
.
The
relay
includes
a
mho
-
type
distance
unit
with
provision
for
offsetting
its
characteristics
,
six
telephone
-
type
auxiliary
units
with
the
necessary
series
resistors
,
and
a
target
seal
-
in
unit
,
all
mounted
in
an
L
2
size
case
.
The
outline
and
panel
drilling
dimensions
are
shown
in
Figure
9
,
and
the
internal
connections
in
Figure
3
.
APPLICATION
The
usual
application
of
the
Type
GSY
51
A
relay
and
its
associated
Type
CEX
57
E
angle
-
impedance
relay
is
at
the
terminals
of
a
generator
to
provide
out
-
of
-
step
protection
of
the
machine
,
resulting
high
current
peaks
and
off
-
frequency
operation
may
cause
winding
stresses
,
pulsation
torques
and
mechanical
resonances
that
have
the
potential
of
damaging
the
turbine
-
generator
.
Therefore
,
to
minimize
the
possibility
of
damage
,
it
is
generally
accepted
that
the
machine
should
be
tripped
without
delay
,
preferably
during
the
first
half
-
slip
cycle
of
the
loss
of
synchronism
condition
.
When
a
generator
loses
synchronism
,
the
Formerly
the
generator
,
transformer
and
system
impedance
characteristics
were
such
that
the
electrical
center
during
loss
-
of
-
synchronism
conditions
generally
occurred
out
in
the
transmission
system
.
Hence
the
resulting
swing
impedance
locus
intersected
transmission
lines
and
would
be
detected
by
line
relaying
or
by
out
-
of
-
step
detection
schemes
located
at
line
terminals
,
and
in
most
instances
the
system
could
be
separated
without
the
need
for
tripping
generators
.
With
the
advent
of
EHV
systems
,
larger
generators
and
the
general
expansion
of
transmission
systems
,
the
impedances
involved
have
changed
significantly
.
Generator
and
step
-
up
transformer
impedances
have
increased
in
magnitude
,
while
system
impedances
have
decreased
.
As
a
result
,
on
many
systems
today
the
electrical
center
during
loss
-
of
-
synchronism
conditions
can
,
and
frequently
does
,
occur
in
the
generator
or
in
the
step
-
up
transformer
.
In
general
,
the
protection
normally
applied
in
the
generator
zone
,
such
as
differential
relaying
,
time
-
delay
system
back
-
up
,
etc
generator
during
a
loss
of
synchronism
.
will
not
protect
a
The
loss
of
excitation
relay
may
•
J
These
instructions
do
not
purport
to
cover
all
details
or
variations
in
equipment
nor
to
provide
for
every
possible
contingency
to
be
met
in
connection
with
installation
,
operation
or
maintenance
.
further
information
be
desired
or
should
particular
problems
arise
which
are
not
covered
sufficiently
for
the
purchaser
'
s
purposes
,
the
matter
should
be
referred
to
the
General
Electric
Company
.
To
the
extent
required
the
products
described
herein
meet
applicable
ANSI
,
IEEE
and
NEftA
standards
/
but
no
such
assurance
is
given
with
respect
to
local
codes
and
ordinances
because
they
vary
greatly
.
Should
-
3
-
Courtesy of NationalSwitchgear.com

GEK
-
45441
provide
some
degree
of
protection
,
but
cannot
be
relied
on
to
detect
generator
loss
of
synchronism
under
all
system
conditions
.
Therefore
,
if
during
a
loss
of
synchronism
the
electrical
center
is
located
in
the
region
from
the
high
voltage
terminals
of
the
generator
step
-
up
transformer
down
into
the
generator
,
separate
out
-
of
-
step
relaying
should
be
considered
to
protect
the
machine
.
The
combination
of
the
GSY
51
A
and
CEX
57
E
relays
,
located
at
the
generator
terminals
,
is
intended
locus
passes
through
the
machine
or
step
-
up
transformer
impedance
,
scheme
utilizes
three
impedance
measuring
units
and
the
logic
circuitry
provided
by
the
auxiliary
units
in
the
GSY
to
evaluate
the
progressive
change
in
impedance
during
a
loss
of
synchronism
condition
,
and
to
initiate
tripping
when
the
angle
between
generator
and
system
voltages
is
900
or
less
,
typical
application
of
the
GS
51
A
and
CEX
57
E
relays
at
the
terminals
of
a
generator
is
covered
by
the
external
connection
diagram
in
Figure
10
A
.
contact
circuit
logic
is
shown
in
Figure
10
B
.
to
detect
an
out
-
of
-
step
condition
when
the
swing
This
This
The
Although
the
CEX
-
GSY
scheme
is
normally
applied
at
the
terminals
of
the
generator
,
there
are
some
applications
where
it
will
be
more
advantageous
to
apply
these
relays
at
the
high
voltage
terminals
of
the
step
-
up
transformer
.
This
is
discussed
further
in
the
section
on
CALCULATION
OF
SETTINGS
.
The
occurrence
of
a
single
-
phase
-
to
-
ground
fault
that
evolves
into
a
double
-
phase
-
to
-
ground
fault
may
,
under
certain
conditions
,
appear
as
an
impedance
swing
to
the
CEX
-
GSY
scheme
,
misoperation
during
the
clearing
of
such
a
fault
on
the
system
,
it
is
suggested
that
an
instantaneous
ground
overcurrent
relay
be
connected
to
supervise
the
CEX
-
GSY
contact
circuit
,
as
shown
in
Figure
10
B
.
To
avoid
this
remote
possibility
of
a
OPERATION
OF
THE
SCHEME
The
operating
principles
of
the
scheme
can
be
explained
with
the
aid
of
the
R
-
X
diagram
and
contact
circuit
in
Figure
10
B
.
This
diagram
shows
the
angle
-
impedance
,
or
blinder
,
unit
contacts
(
21
ST
/
A
1
,
21
ST
/
A
2
,
21
ST
/
B
1
and
21
ST
/
B
2
)
,
the
offset
mho
unit
contacts
(
21
M
/
a
and
21
M
/
b
)
,
and
the
contacts
of
the
six
auxiliary
units
(
X
,
XI
,
X
2
,
X
3
,
X
4
,
and
X
5
)
.
The
angle
impedance
units
and
their
associated
auxiliary
units
(
XI
,
X
2
,
X
4
,
and
X
5
)
operate
independently
to
determine
a
loss
of
synchronism
,
but
their
trip
output
unit
,
X
3
,
is
supervised
by
the
21
M
/
a
contact
via
21
M
/
X
.
This
assures
that
tripping
is
initiated
only
for
an
impedance
swing
that
traverses
the
mho
unit
characteristic
(
21
M
of
the
R
-
X
diagram
in
Figure
10
B
)
.
Final
tripping
is
permitted
by
21
M
/
b
when
the
impedance
swing
leaves
the
mho
characteristic
,
causing
the
mho
unit
to
reset
.
The
R
-
X
diagram
in
Figure
10
B
shows
the
are
of
closure
of
the
21
ST
/
A
and
21
ST
/
B
blinder
unit
contacts
A
1
,
A
2
,
Bl
,
and
B
2
.
impedance
phasor
terminates
to
the
right
of
blinder
B
,
21
ST
/
A
2
and
21
ST
/
B
2
will
be
closed
.
21
ST
/
B
1
will
be
closed
,
and
when
the
impedance
is
to
the
left
of
blinder
A
,
21
STA
1
and
21
ST
/
B
1
will
be
closed
,
steady
-
state
conditions
,
load
impedance
will
fall
somewhere
near
the
R
axis
,
For
example
,
when
an
When
the
impedance
is
between
the
blinders
,
21
ST
/
A
2
and
It
should
be
noted
that
for
normal
-
4
-
Courtesy of NationalSwitchgear.com

GEK
-
45441
to
the
right
of
21
ST
/
B
and
outside
the
21
M
mho
characteristic
,
condition
21
ST
/
A
2
and
21
ST
/
B
2
will
be
closed
,
21
M
/
X
1
will
be
picked
up
,
21
M
/
b
will
be
closed
,
and
21
M
/
a
will
be
open
.
For
this
Referring
to
the
contact
circuitry
and
the
R
-
X
diagram
in
Figure
10
B
,
the
step
-
by
-
step
operation
of
the
scheme
during
an
impedance
swing
will
be
as
follows
:
Step
1
-
Assume
that
a
swing
impedance
locus
traverses
the
relay
characteristics
from
C
to
K
.
Before
the
swing
reaches
point
D
the
mho
unit
(
21
M
)
will
be
dropped
out
,
the
21
ST
/
A
2
and
21
ST
/
B
2
contacts
are
closed
,
and
the
two
21
M
/
X
1
contacts
are
closed
.
The
21
ST
/
A
1
and
21
ST
/
B
1
contacts
are
both
open
.
Step
2
-
When
the
swing
locus
enters
the
mho
unit
characteristic
at
point
D
,
the
21
M
/
b
contact
in
the
trip
circuit
opens
and
21
M
/
a
closes
,
picking
up
unit
21
M
/
X
,
which
closes
its
contact
in
the
X
3
coil
circuit
.
Step
3
-
The
impedance
swing
next
enters
the
area
,
G
,
between
the
two
blinder
characteristics
,
closing
21
ST
/
B
1
and
opening
21
ST
/
B
2
,
which
in
turn
de
-
energizes
the
XI
unit
.
Closure
of
the
B
1
contact
picks
up
X
2
through
the
A
2
contact
,
which
is
still
closed
,
and
the
XI
contact
,
which
has
a
12
-
cycle
time
-
delay
dropout
.
Unit
X
2
seals
in
around
the
XI
contact
.
Step
4
-
When
the
impedance
locus
enters
region
H
,
to
the
left
of
blinder
A
,
21
ST
/
A
2
opens
,
21
ST
/
A
1
closes
,
and
21
ST
/
B
1
remains
closed
,
opening
of
A
2
de
-
energizes
the
X
2
unit
and
the
closure
of
A
1
picks
up
unit
X
4
.
The
12
-
cycle
dropout
time
of
the
X
2
unit
provides
time
for
X
3
to
pick
up
through
the
X
2
and
X
4
contacts
,
and
the
X
unit
contact
which
has
previously
closed
.
these
contacts
,
and
the
X
3
contact
in
the
trip
circuit
closes
.
The
The
X
3
unit
seals
in
around
Step
5
-
When
the
impedance
locus
enters
region
K
,
the
mho
unit
resets
,
opening
21
M
/
a
and
closing
21
M
/
b
.
The
closure
of
21
M
/
b
completes
the
trip
coil
circuit
through
the
21
M
/
X
3
contact
which
closed
in
Step
4
.
The
previous
description
assumes
an
impedance
swing
from
right
to
left
(
C
to
K
)
,
which
will
be
the
case
for
generator
loss
of
synchronism
.
However
,
the
scheme
will
perform
correctly
for
swings
in
either
direction
,
and
hence
is
applicable
for
out
-
of
-
step
protection
out
on
the
transmission
system
as
well
as
at
the
generator
terminals
.
APPLICATION
CONSIDERATIONS
The
application
of
out
-
of
-
step
relaying
schemes
at
a
generator
,
or
out
in
the
system
,
is
not
a
simple
procedure
.
In
general
,
the
proper
application
of
such
schemes
requires
extensive
stability
studies
to
determine
the
following
:
Loss
-
of
-
synchronism
characteristics
(
i
.
e
.
,
impedance
loci
)
.
Maximum
expected
generator
slip
.
1
.
2
.
-
5
-
Courtesy of NationalSwitchgear.com

GEK
-
45441
Characteristics
of
expected
stable
swings
.
Expected
current
levels
.
The
relationship
between
this
information
and
the
application
of
the
CEX
-
GSY
scheme
is
covered
in
a
technical
paper
,
information
on
this
subject
,
he
should
request
it
from
the
nearest
General
Electric
Company
Sales
Office
.
3
.
4
.
If
the
user
desires
further
RATINGS
Refer
to
Figures
1
and
2
.
and
is
available
for
50
or
60
hertz
frequencies
.
The
GSY
51
A
relay
is
rated
for
120
volts
,
5
amperes
,
The
basic
minimum
reach
is
2
,
4
,
6
ohms
phase
-
to
-
neutral
at
90
o
lead
,
with
the
restraint
leads
connected
at
100
%
on
the
restraint
transformer
.
Each
basic
minimum
reach
can
be
selected
with
a
link
arrangement
located
behind
the
relay
.
There
are
two
sections
of
reach
on
one
tap
block
;
each
section
is
marked
A
-
B
and
2
,
0
,
4
.
By
connecting
both
sections
as
shown
in
Table
I
,
the
basic
minimum
ohmic
reach
of
the
relay
can
be
selected
.
TABLE
I
Minimum
Reach
Phase
-
to
-
Neutral
Links
"
A
"
"
B
"
2.0
ohms
4.0
ohms
6.0
ohms
2
0
0
4
4
2
The
basic
minimum
reach
can
be
extended
up
to
ten
times
the
basic
reach
by
reducing
the
restraint
circuit
setting
on
the
restraint
transformer
.
The
following
equation
can
be
used
for
increasing
the
basic
minimum
reach
of
the
relay
.
100
(
%
)
(
90
°
lead
)
Z
Relay
=
x
basic
minimum
reach
Transformer
setting
(
%
)
Ohmic
reach
settings
greater
than
the
basic
minimum
reach
can
be
set
within
1
%
increments
by
selecting
the
proper
taps
on
the
restraint
transformer
,
which
is
tapped
in
10
%
and
1
%
steps
.
The
relay
also
has
a
reverse
offset
transactor
with
a
phase
-
to
-
neutral
offset
reach
of
0
to
4
ohms
in
0.5
ohm
steps
.
The
taps
are
selected
with
the
"
H
"
and
"
L
"
leads
on
the
offset
tap
block
,
which
is
located
on
the
left
front
side
,
approximately
in
the
center
of
the
relay
.
The
transactor
angle
can
be
adjusted
with
the
R
63
rheostat
,
located
just
to
the
right
of
the
offset
tap
block
.
-
6
-
Courtesy of NationalSwitchgear.com

GEK
-
45441
CURRENT
CIRCUIT
The
current
circuit
is
continuously
rated
at
5
amperes
,
with
a
one
-
second
rating
of
250
amperes
.
Higher
magnitudes
of
current
above
5
amperes
can
be
applied
for
shorter
periods
of
time
,
according
to
the
following
equation
.
K
=
I
2
T
I
=
the
applied
current
in
amperes
T
=
time
in
seconds
K
=
Constant
=
(
2502
)
=
62500
t
seconds
=
—
where
:
Therefore
:
12
POTENTIAL
CIRCUIT
The
potential
circuit
is
continuously
rated
at
120
volts
at
rated
frequency
.
AMBIENT
TEMPERATURES
The
relays
are
designed
to
operate
continuously
at
rated
voltage
,
current
and
frequency
in
an
ambient
temperature
not
to
exceed
40
Oc
.
DC
RATINGS
The
DC
voltage
circuits
are
available
at
48
/
110
-
125
/
220
-
250
volts
DC
.
circuits
consist
of
telephone
relays
whose
contacts
,
when
closed
,
can
carry
30
amperes
for
one
second
,
with
a
continuous
rating
of
3
amperes
.
The
The
interrupting
rating
of
these
contacts
is
listed
in
Table
II
.
TABLE
II
Volts
Interrupting
Rating
in
Amperes
DC
Inductive
Non
-
Inductive
125
0.50
1.5
TARGET
/
SEAL
-
IN
The
combination
target
and
seal
-
in
unit
has
a
dual
rating
of
0.6
or
2.0
amperes
.
The
tap
setting
selected
on
the
target
/
seal
-
in
unit
is
determined
by
the
current
drawn
by
the
breaker
trip
coil
.
The
0.6
ampere
tap
is
used
with
trip
coils
which
operate
on
currents
ranging
from
0.6
ampere
to
2.0
amperes
at
the
maximum
control
voltage
.
The
0.6
ampere
tap
can
be
used
also
with
trip
coils
drawing
as
much
as
30
amperes
,
provided
that
the
voltage
drop
across
the
coil
with
trip
current
flowing
is
not
excessive
.
The
2.0
ampere
tap
can
be
used
with
all
trip
coils
that
draw
more
than
2.0
amperes
at
the
maximum
control
voltage
.
-
7
-
Courtesy of NationalSwitchgear.com

GEK
-
45441
The
ratings
of
the
target
/
seal
-
in
unit
are
shown
in
TABLE
III
.
TABLE
III
HI
-
G
TARGET
/
SEAL
-
IN
UNIT
2.0
Amp
Tap
0.6
Amp
Tap
2.0
amps
2.6
amps
3.5
secs
.
30
secs
.
0.18
ohm
0.65
ohm
0.54
ohm
Minimum
operating
Carry
continuously
Carry
30
amps
for
Carry
10
amps
for
DC
Resistance
60
cycle
impedance
50
cycle
impedance
0.6
amp
1.8
amps
0.5
sec
.
5
secs
0.78
ohm
6.2
ohms
5.1
ohms
MHO
UNIT
CONTACTS
The
mho
unit
contacts
,
when
closed
,
will
carry
30
amperes
momentarily
up
to
a
250
volt
DC
control
voltage
.
However
,
the
contacts
do
not
have
an
interrupting
rating
;
therefore
some
other
suitable
method
must
be
used
to
open
the
trip
circuit
after
a
trip
condition
.
OPERATING
PRINCIPLES
The
mho
unit
of
the
GSY
51
A
relay
is
of
the
four
-
pole
induction
cylinder
construction
,
where
the
torque
is
produced
by
the
interaction
between
the
polarizing
flux
and
the
fluxes
which
are
proportional
to
the
restraining
and
/
or
operating
quantities
.
The
torque
at
the
balance
point
of
the
mho
unit
can
be
expressed
by
the
following
equation
.
Torque
=
0
=
Ei
Cos
(
0
-
0
)
-
KE
2
-
Ks
Where
:
Phase
-
to
-
phase
voltage
Delta
currents
(
Il
-
l
2
)
Angle
of
maximum
torque
Power
factor
angle
of
the
fault
impedance
Design
constant
Ks
=
Control
spring
constant
E
I
9
0
K
To
prove
that
the
equation
defines
an
mho
characteristic
,
divide
both
sides
by
E
^
and
transpose
.
The
equation
reduces
to
:
^
Cos
(
0
-
0
)
=
K
Z
Y
Cos
(
0
-
0
)
=
K
Thus
,
the
unit
will
pick
up
at
a
constant
component
of
admittance
at
a
fixed
angle
,
depending
on
the
angle
of
maximum
torque
.
Hence
the
name
mho
unit
.
When
the
offset
is
used
,
the
transactor
is
energized
with
line
current
which
produces
a
voltage
proportional
to
the
current
and
added
to
the
line
-
to
-
line
voltage
in
the
unit
'
s
potential
circuit
.
or
This
voltage
will
offset
the
-
8
-
Courtesy of NationalSwitchgear.com

GEK
-
45441
circular
characteristic
of
the
mho
unit
as
shown
in
the
R
-
X
diagram
,
Figure
4
.
Although
not
shown
in
Figure
4
,
the
offset
can
be
set
between
0
and
4
ohms
in
0
,
5
ohm
steps
.
CHARACTERISTICS
The
mho
unit
produces
a
circular
impedance
characteristic
as
shown
in
Figure
4
.
The
diameter
of
the
characteriStic
can
be
increased
as
shown
in
Figure
5
,
by
reducing
the
restraint
tap
leads
on
the
restraint
transformer
,
recommended
that
the
restraint
leads
be
set
below
10
%
on
the
restraint
transformer
.
It
is
not
BURDENS
CURRENT
CIRCUITS
The
burden
imposed
on
each
current
transformer
at
5
amperes
by
the
current
circuits
of
the
GSY
51
A
relay
is
listed
in
Table
IV
for
each
basic
minimum
reach
tap
at
60
hertz
.
TABLE
IV
Basic
Reach
Tap
,
0
-
N
R
X
V
.
A
.
U
P
.
F
.
2.0
0.142
0.110
0.081
0.054
0.065
0.170
3.55
3.30
0.930
0.860
0.430
4.0
2.75
2.365
0.870
6.0
2.025
The
burden
at
50
hertz
will
be
slightly
lower
.
POTENTIAL
CIRCUITS
The
maximum
burden
imposed
on
each
potential
transformer
,
with
120
volts
60
hertz
applied
,
is
shown
in
Table
V
.
TABLE
V
FTT
:
Offset
Tap
,
0
-
N
R
X
W
V
7
A
7
0
705
451
12.53
12.84
13.10
13.06
12.93
14.87
14.82
14.66
14.28
13.67
0.840
0.866
0.893
0.914
0.945
0.5
725
417
1.0
752
377
2.5
785
348
4.0
855
297
The
50
hertz
burden
will
be
slightly
lower
.
-
9
-
Courtesy of NationalSwitchgear.com

GEK
-
45441
CALCULATION
OF
SETTINGS
The
determination
of
relay
settings
for
the
CEX
-
GSY
scheme
need
not
be
a
complicated
procedure
.
Preliminary
settings
of
the
blinder
and
mho
units
can
be
obtained
by
means
of
a
simplified
graphical
approach
on
an
R
-
X
diagram
,
and
then
the
validity
of
these
settings
can
be
checked
with
the
results
of
the
stability
study
.
GRAPHICAL
PROCEDURE
In
the
simplified
graphical
procedure
,
the
generator
is
represented
by
its
transient
reactance
(
X
1
d
)
.
reactance
(
Xj
)
and
the
system
impedance
(
Zs
)
is
plotted
to
scale
on
an
R
-
X
diagram
,
the
origin
of
which
is
at
the
terminals
of
the
generator
,
as
shown
in
Figure
18
.
If
the
system
impedance
is
variable
,
the
smallest
system
impedance
should
be
used
,
since
this
will
ensure
that
the
subsequent
blinder
settings
will
be
able
to
detect
the
smaller
swing
impedance
locus
associated
with
low
system
impedances
.
This
reactance
,
along
with
the
transformer
The
angle
of
The
total
impedance
line
is
then
drawn
between
points
C
and
D
.
this
line
with
respect
to
the
horizontal
axis
represents
the
system
angle
.
With
the
system
characteristic
thus
established
,
settings
for
the
blinders
can
now
be
determined
.
BLINDER
SETTINGS
Referring
to
Figure
18
,
the
distance
,
N
,
from
the
origin
to
the
blinder
,
and
angle
B
between
the
blinder
and
the
horizontal
axis
,
can
be
adjusted
separately
for
each
blinder
.
The
angle
,
B
,
is
normally
selected
so
that
both
blinders
are
approximately
parallel
to
the
total
impedance
line
,
CD
.
The
spacing
between
blinders
is
generally
selected
so
that
at
the
point
in
an
impedance
swing
where
the
blinders
operate
,
the
angular
separation
,
S
,
between
generator
and
system
is
1200
.
This
angular
separation
can
be
determined
by
drawing
construction
lines
at
points
C
and
D
that
are
30
°
from
the
total
impedance
line
,
CD
.
The
blinders
are
then
plotted
to
pass
through
the
120
°
points
E
and
F
at
an
angle
,
B
,
with
respect
to
the
R
axis
,
as
shown
in
Figure
18
.
It
should
be
noted
that
the
dashed
line
,
which
is
the
bisector
of
the
1200
angles
,
passes
through
the
impedance
center
of
the
system
and
would
represent
the
locus
of
the
impedance
swing
for
the
case
where
the
ratio
of
the
generator
internal
voltage
to
the
system
voltage
equals
one
(
1
)
.
MHO
UNIT
SETTING
The
mho
unit
is
set
so
that
it
will
permit
tripping
for
all
impedance
loci
that
will
appear
in
the
region
from
the
high
voltage
terminals
of
the
step
-
up
transformer
down
into
the
generator
,
generally
connected
with
its
forward
reach
looking
into
the
generator
and
with
its
offset
adjusted
to
encompass
the
transformer
reactance
with
some
margin
.
To
accomplish
this
,
the
mho
unit
is
The
forward
reach
of
the
unit
should
be
set
so
that
it
will
detect
all
impedance
loci
that
can
go
through
the
generator
but
not
operate
for
stable
transient
swings
.
A
forward
reach
setting
which
is
equal
to
2
to
3
times
generator
transient
reactance
(
X
'
^
)
would
meet
this
criterion
.
-
10
-
Courtesy of NationalSwitchgear.com

GEK
-
45441
The
offset
must
be
adjusted
so
that
it
will
detect
an
impedance
locus
that
will
go
through
the
high
voltage
terminals
of
the
step
-
up
transformer
.
A
setting
which
is
equal
to
1.5
to
2
times
transformer
reactance
will
usually
accomplish
this
purpose
.
With
the
proper
setting
,
the
offset
circle
should
be
outside
the
blinders
for
swings
going
through
the
high
voltage
terminals
of
the
transformer
,
as
shown
in
Figure
18
.
This
spacing
assures
that
there
will
be
proper
coordination
between
the
mho
unit
and
the
blinders
for
this
extreme
swing
.
It
may
be
difficult
to
achieve
this
adjustment
where
the
system
impedance
is
large
.
This
will
be
illustrated
shortly
.
It
should
be
noted
that
,
in
order
to
detect
swings
at
the
transformer
high
voltage
terminals
,
the
offset
setting
reaches
out
into
the
system
,
and
therefore
the
scheme
may
detect
a
swing
which
is
outside
the
generator
zone
.
While
this
is
a
possibility
,
the
probability
of
this
happening
is
small
,
since
the
impedance
locus
will
be
near
the
balance
point
of
the
relay
,
where
relay
operation
is
slow
.
The
chances
are
that
system
relaying
will
operate
before
the
out
-
of
-
step
relaying
scheme
.
If
the
scheme
does
operate
for
such
swings
,
this
is
generally
accepted
as
a
desired
option
.
VERIFICATION
OF
SETTINGS
Once
the
settings
have
been
determined
,
they
should
be
checked
with
the
actual
impedance
loci
as
determined
from
the
stability
studies
.
Figures
19
,
20
,
21
and
22
compare
the
calculated
settings
with
expected
impedance
loci
for
system
impedances
of
0.05
,
0.09
,
0.2
and
0.4
per
unit
on
the
generator
base
.
To
facilitate
comparison
with
the
relay
characteristics
,
the
examples
in
these
figures
are
presented
in
terms
of
secondary
ohms
.
Figure
19
is
intended
to
represent
the
impedance
locus
that
would
occur
with
a
system
impedance
of
0.05
per
unit
and
the
voltage
regulator
out
of
service
.
For
this
situation
,
the
impedance
locus
tends
to
be
small
in
diameter
and
thus
more
difficult
to
detect
.
With
the
blinders
set
for
1200
angle
separation
between
generator
and
system
(
solid
lines
in
Figure
19
)
,
the
impedance
locus
just
barely
crosses
the
left
blinder
.
To
provide
additional
operating
margin
for
this
situation
,
both
blinders
can
be
shifted
to
the
right
as
indicated
by
the
dashed
lines
.
In
addition
,
the
forward
reach
of
the
mho
unit
should
be
held
to
twice
the
generator
transient
reactance
(
X
'
j
)
,
as
shown
,
to
assure
that
the
impedance
locus
will
leave
the
area
of
the
mho
characteristic
,
thereby
permitting
tripping
.
Figure
20
typifies
an
application
of
the
CEX
-
GSY
scheme
where
the
system
impedance
equals
0.09
per
unit
.
In
this
case
,
the
blinder
and
mho
settings
as
previously
described
would
be
satisfactory
and
would
not
require
modification
.
This
figure
also
shows
that
there
is
ample
margin
between
the
assumed
stable
impedance
locus
and
the
forward
reach
of
the
mho
unit
,
which
in
this
case
is
set
for
3
times
the
transient
reactance
(
X
'
d
)
.
Figure
21
typifies
the
application
of
the
scheme
where
the
system
impedance
equals
0.2
per
unit
.
calculations
would
be
satisfactory
and
would
require
no
modification
.
In
this
example
,
the
settings
based
on
the
previous
-
11
-
Courtesy of NationalSwitchgear.com

GEK
-
45441
Figure
22
shows
the
application
of
the
CEX
-
GSY
scheme
where
the
system
impedance
equals
0.4
per
unit
,
would
be
adequate
,
but
the
spacing
between
the
mho
unit
and
the
blinder
for
swings
near
the
high
voltage
terminals
of
the
transformer
might
be
considered
marginal
.
The
mho
unit
is
at
its
maximum
offset
reach
of
4
ohms
and
therefore
cannot
be
increased
further
.
In
this
instance
,
the
calculated
settings
If
additional
margin
is
desired
,
the
relays
can
be
shifted
to
the
high
voltage
terminals
of
the
transformer
,
as
shown
in
Figure
23
.
offset
,
there
is
more
margin
available
betwen
the
CEX
and
mho
unit
settings
.
This
problem
of
spacing
between
the
blinders
and
the
mho
unit
at
the
extreme
limits
of
possible
swings
will
only
arise
for
high
system
impedances
.
Now
,
with
a
3
-
ohm
It
was
noted
earlier
that
when
system
impedance
is
variable
,
the
smallest
impedance
should
be
used
to
determine
the
settings
.
In
general
,
if
the
resulting
settings
are
adequate
with
the
small
system
impedance
,
they
will
also
be
adequate
with
the
higher
system
impedance
.
For
example
,
if
the
system
impedance
can
be
0.05
and
0.2
per
unit
,
it
should
be
readily
apparent
that
the
settings
for
the
0.05
system
would
be
able
to
detect
the
larger
impedance
locus
of
the
0.2
system
.
On
the
other
hand
,
if
the
relays
had
been
set
for
the
0.2
system
impedance
(
Figure
21
)
,
these
settings
would
not
have
detected
the
smaller
impedance
locus
shown
in
Figure
19
.
As
a
final
point
of
interest
,
it
should
be
noted
that
while
the
simple
graphical
approach
is
an
approximate
procedure
,
it
does
give
a
fairly
good
indication
as
to
where
the
actual
impedance
locus
will
go
.
As
noted
earlier
,
the
bisector
of
the
1200
angle
between
generator
and
system
will
go
through
the
impedance
locus
for
Eg
/
ESyS
=
1
.
As
can
be
seen
in
Figures
19
,
20
,
21
and
22
,
the
actual
impedance
loci
are
only
slightly
below
this
impedance
center
.
It
should
be
emphasized
that
the
guidelines
and
data
presented
here
are
the
results
of
generalized
studies
that
do
not
consider
the
effects
of
all
types
and
designs
of
generators
and
system
parameters
,
or
the
interaction
effect
of
other
generators
.
These
effects
can
only
be
completely
determined
by
the
study
of
a
generator
connected
to
a
specific
system
.
Therefore
,
it
is
recommended
that
the
user
determine
the
actual
loss
-
of
-
synchronism
characteristic
for
each
generator
,
considering
the
overall
effects
of
the
system
.
CONSTRUCTION
The
type
GSY
51
A
relay
is
assembled
in
a
large
size
,
double
ended
(
L
2
)
drawout
case
.
external
connections
.
There
are
stud
connections
at
both
ends
at
the
rear
of
the
case
for
The
electrical
connections
between
the
relay
units
and
the
case
studs
are
made
with
a
removable
connection
plug
.
Every
circuit
in
the
drawout
case
has
an
auxiliary
brush
,
as
shown
in
Figure
6
,
to
provide
adequate
overlap
between
the
auxiliary
brush
,
relay
fingers
and
shorting
bar
.
-
12
-
Courtesy of NationalSwitchgear.com

GEK
-
45441
GENERAL
DRAWOUT
RELAYS
Since
all
drawout
relays
in
service
operate
in
their
cases
,
it
is
recommended
that
they
be
tested
in
their
cases
or
an
equivalent
steel
case
.
In
this
way
,
any
magnetic
effects
of
the
enclosure
will
be
accurately
duplicated
during
testing
.
A
relay
may
be
tested
without
removing
it
from
the
panel
,
by
using
a
12
XLA
13
A
test
plug
.
This
plug
makes
connections
only
with
the
relay
,
and
does
not
disturb
any
shorting
bars
in
the
case
.
Of
course
,
the
12
XLA
12
A
test
plug
may
aos
be
used
.
Although
this
test
plug
allows
greater
testing
flexibility
,
it
also
requires
CT
shorting
jumpers
and
the
exercise
of
greater
care
,
since
connections
are
made
to
both
the
relay
and
the
external
circuitry
.
Refer
to
GEI
-
25372
for
further
information
on
the
XLA
test
plugs
.
POWER
REQUIREMENTS
All
AC
(
alternating
-
current
)
-
operated
devices
are
affected
by
frequency
.
Since
non
-
sinusoidal
waveforms
can
be
analyzed
as
a
fundamental
frequency
plus
harmonics
of
the
fundamental
frequency
,
it
follows
that
AC
devices
(
relays
)
will
be
affected
by
the
applied
waveform
.
Therefore
,
in
order
to
test
AC
relays
properly
it
is
essential
to
use
a
sine
wave
of
current
and
/
or
voltage
.
The
purity
of
the
sine
wave
(
i
.
e
.
its
freedom
from
harmonics
)
cannot
be
expressed
as
a
finite
number
for
any
particular
relay
;
however
,
any
relay
using
tuned
circuits
,
R
-
L
or
RC
networks
,
or
saturating
electromagnets
(
such
as
time
-
overcurrent
relays
)
would
be
essentially
affected
by
non
-
sinusoidal
waveforms
.
Similarly
,
relays
requiring
DC
control
power
should
be
tested
using
DC
and
not
full
-
wave
rectified
power
.
Unless
the
rectified
supply
is
well
filtered
many
relays
will
not
operate
properly
,
due
to
the
dips
in
the
rectified
power
.
Zener
diodes
,
for
example
,
can
turn
off
during
these
dips
.
As
a
general
rule
,
the
DC
source
should
not
contain
more
than
5
%
ripple
.
ACCEPTANCE
TESTS
Immediately
upon
receipt
of
the
relay
,
an
inspection
and
acceptance
test
should
be
made
to
insure
that
no
damage
has
been
sustained
in
shipment
and
that
the
relay
calibration
was
not
disturbed
.
VISUAL
INSPECTION
Check
the
nameplate
stamping
to
insure
that
the
model
number
and
ratings
of
the
relay
agree
with
the
requisition
.
Remove
the
cover
,
connection
plugs
and
the
relay
from
its
case
and
check
that
there
are
no
broken
or
cracked
molded
parts
or
other
indications
of
physical
damage
.
-
13
-
Courtesy of NationalSwitchgear.com

GEK
-
45441
MECHANICAL
INSPECTION
Check
the
mechanical
adjustments
as
listed
in
Table
VI
.
1
.
TABLE
VI
MHO
unit
Mechanical
Parameters
Rotating
Shaft
End
Play
Contact
Gap
Contact
Wipe
0.005
inch
to
O
.
O
08
inch
0.055
inch
to
0.065
inch
0.003
inch
to
0.005
inch
Move
the
mho
unit
contact
manually
to
determine
if
the
rotating
member
has
any
friction
.
2
.
Check
that
the
control
spring
is
not
deformed
and
that
the
other
turn
is
not
hooked
behind
the
spring
soldering
post
.
3
.
4
.
Check
the
telephone
relays
manually
to
determine
if
they
are
free
and
have
not
been
damaged
.
Check
that
the
target
/
seal
-
in
unit
is
not
damaged
,
and
that
it
is
free
of
mechanical
binds
.
5
.
Check
the
contact
fingers
and
shorting
bars
in
the
case
and
relay
against
the
internal
connection
diagram
for
the
relay
(
Figure
3
)
.
6
.
ELECTRICAL
TESTS
All
electrical
tests
must
be
performed
with
the
relay
in
its
own
case
or
an
equivalent
steel
test
case
.
Connect
the
relay
per
the
test
circuit
diagram
of
Figure
7
and
Table
VII
.
Note
:
TABLE
VII
Connect
lead
A
to
stud
17
.
Connect
lead
B
to
stud
18
.
Connect
lead
C
to
stud
7
.
Connect
lead
D
to
stud
10
.
Jumper
stud
8
to
stud
9
.
Connect
a
contact
light
to
the
normally
-
open
contact
of
the
mho
unit
,
the
contact
on
the
left
side
of
the
unit
,
front
view
.
This
is
ihere
are
two
conditions
that
exist
which
must
be
taken
into
consideration
before
any
attempt
is
made
to
check
the
calibration
of
the
mho
unit
.
Either
:
1
.
The
relay
was
calibrated
for
a
standard
factory
test
;
or
The
relay
was
calibrated
per
the
customer
'
s
recommended
settings
,
disturb
the
settings
if
this
was
the
case
.
2
.
Do
not
-
14
-
Courtesy of NationalSwitchgear.com

GEK
-
45441
MHO
UNIT
-
ACCEPTANCE
TESTS
(
STANDARD
FACTORY
CALIBRATION
)
The
relay
should
be
leveled
in
its
own
case
or
a
test
case
,
in
the
upright
position
.
Set
the
following
conditions
.
Restraint
circuit
taps
set
at
100
%
on
the
restraint
transformer
.
1
.
Set
both
reach
taps
at
4
ohms
0
-
N
.
2
.
2
A
links
to
0
2
B
links
to
4
Set
the
offset
transactor
tap
leads
(
H
and
L
)
to
0
on
the
offset
block
.
3
.
Before
applying
power
to
the
circuit
,
check
that
the
moving
contact
of
the
mho
unit
is
closed
to
the
right
side
,
front
view
.
Directional
Tests
Apply
120
volts
,
rated
frequency
and
5
amperes
to
the
relay
.
Adjust
the
phase
shifter
to
set
the
phase
angle
meter
for
90
o
lead
.
Reduce
the
voltage
to
3
volts
and
the
current
to
0
amperes
.
Gradually
increase
the
current
;
the
left
contact
should
close
between
1.5
and
2.0
amperes
.
Increase
the
current
from
the
pickup
to
60
amperes
very
quickly
and
note
that
the
left
contact
remains
closed
.
period
of
tine
,
because
it
will
overheat
and
possibly
damage
the
unit
.
Do
not
apply
this
current
for
too
long
a
Reduce
the
current
to
0
and
remove
the
voltage
from
studs
17
and
18
.
Place
a
jumper
across
17
and
18
.
Note
that
left
contact
opens
.
Again
,
increase
the
current
from
0
to
60
amperes
and
note
that
the
left
contact
remains
open
.
Remove
the
short
from
studs
17
-
18
and
connect
the
potential
to
these
studs
according
to
the
test
connections
diagram
(
Figure
7
)
.
Reach
Apply
120
volts
and
increase
the
current
until
the
left
contact
closes
.
This
should
occur
at
14.80
to
15.15
amperes
.
Make
sure
that
the
phase
angle
meter
is
set
for
90
°
lead
during
this
test
.
Angle
of
Maximum
Torque
In
order
to
check
the
angle
of
maximum
torque
of
the
mho
unit
,
the
reach
should
be
checked
at
two
angles
which
are
30
o
on
either
side
of
the
angle
of
maximum
torque
.
Check
the
reach
at
60
o
and
at
120
o
by
setting
the
phase
angle
meter
for
these
angles
.
-
15
-
Courtesy of NationalSwitchgear.com

GEK
-
45441
Apply
120
volts
;
left
contact
will
open
.
Increase
the
current
until
the
left
contact
of
the
unit
closes
.
This
should
occur
between
17.0
to
17.7
amperes
at
60
°
and
at
120
°
lead
.
Additional
Reach
Taps
For
a
check
on
the
additional
two
reach
taps
,
set
the
reach
taHs
,
phase
angle
,
and
voltage
as
listed
in
Table
VIII
and
check
the
current
necessary
to
operate
the
mho
unit
.
TABLE
VIII
Reach
Links
Reach
Phase
Angle
A
B
0
-
0
(
Lead
)
Voltage
Applied
Current
Pickup
2
0
4.0
900
60
V
14.55
-
15.45
9.7
-
10.3
120
V
2
4
12.0
900
Offset
Test
The
offset
is
in
the
reverse
direction
from
the
unit
,
therefore
its
angle
is
at
270
o
lead
.
Table
IX
is
a
listing
of
the
ohmic
reach
for
each
offset
tap
.
Apply
the
voltage
,
5
amperes
of
current
,
set
the
phase
angle
listed
,
then
increase
the
current
.
The
unit
should
operate
between
the
values
listed
under
Current
Pickup
.
TABLE
IX
Offset
Tap
Ohmic
Reach
Phase
Angle
(
Lead
)
Applied
Voltage
Current
Pickup
0
-
N
0
-
0
2700
20
V
18
-
22
18
-
22
18
-
22
14.5
-
16.5
0.5
£
2
1.0
£
2
2.5
n
4.0
£
2
1.0
£
2
2.0
£
2
5
.
0
£
2
8.0
£
2
40
V
270
°
100
V
120
V
2700
270
°
Refer
to
the
section
on
SERVICING
if
any
of
these
tests
do
not
function
properly
within
specifications
.
Target
/
Seal
-
in
Connect
the
following
studs
to
a
DC
current
circuit
consisting
of
a
125
volt
DC
source
with
a
rheostat
,
ammeter
and
target
coil
studs
connected
in
series
across
the
DC
source
,
ove
a
range
of
0.03
to
2.0
amperes
.
The
circuit
should
be
capable
of
varying
the
current
Connect
one
test
circuit
coil
lead
to
stud
11
.
Connect
the
other
test
circuit
coil
lead
to
stud
19
.
Put
an
external
jumper
between
studs
19
and
1
.
-
16
-
Courtesy of NationalSwitchgear.com

GEK
-
45441
The
external
jumper
is
used
to
determine
if
the
target
/
seal
-
in
circuit
is
functioning
properly
,
result
in
a
damaged
control
contact
.
Failure
to
put
the
jumper
on
the
proper
studs
will
spring
on
the
normally
-
closed
M
/
b
mho
unit
Reduce
the
current
to
approximately
0
.
Close
the
M
^
,
(
normally
-
closed
contact
)
on
the
mho
unit
;
gradually
increase
the
current
until
the
target
/
seal
-
in
unit
picks
up
.
that
the
target
remains
sealed
in
.
DC
current
and
check
the
dropout
current
of
the
unit
,
and
dropout
are
listed
in
Table
X
.
Open
the
Mb
contact
and
note
With
the
Mb
contact
held
open
,
reduce
the
The
values
for
pickup
TABLE
X
DC
Pickup
Current
DC
Dropout
Current
Target
Tap
0.60
A
2.00
A
0.36
-
0.60
A
1.20
-
2.00
A
0.15
or
higher
0.50
or
higher
In
order
to
change
taps
without
disturbing
the
mechanical
adjustments
of
the
contacts
,
proceed
as
follows
:
1
.
Remove
one
of
the
screws
on
the
left
-
hand
plate
,
front
view
.
Place
this
screw
into
the
desired
tap
on
the
right
-
hand
plate
(
tap
plate
)
,
front
view
.
Remove
the
screw
from
the
undesired
tap
and
put
it
in
the
left
-
hand
plate
.
Restraint
Transformer
2
.
3
.
The
offset
transactor
lead
(
H
-
L
)
should
be
connected
to
0
on
the
offset
block
.
Apply
100
volts
,
rated
frequency
,
to
studs
17
and
18
at
0
current
.
Read
the
voltage
on
each
tap
on
the
restraint
transformer
with
an
accurate
high
-
input
impedance
voltmeter
.
Connect
one
lead
of
the
voltmeter
to
0
on
the
restraint
transformer
block
and
the
other
lead
to
each
tap
.
The
reading
should
be
equal
to
tap
value
(
+
1
%
)
.
Telephone
Relays
There
are
six
telephone
relays
that
must
be
checked
for
pickup
voltage
,
pickup
time
and
dropout
time
.
Connect
the
relays
per
the
test
circuit
of
Figure
8
and
refer
to
the
test
parameters
listed
in
Table
XI
.
Always
connect
(
-
)
DC
to
terminal
2
for
testing
of
telephone
relays
.
-
17
-
Courtesy of NationalSwitchgear.com

GEK
-
45441
TABLE
XI
Telephone
Relays
Tests
Ref
.
Fig
.
8
Xl
X
2
X
3
XT
Xb
X
Studs
Studs
2
-
20
2
-
12
Studs
2
-
15
Connections
A
-
B
Studs
Studs
Studs
2
-
15
2
-
6
2
-
3
Connections
C
-
D
Studs Studs
13
-
14
4
-
5
Studs
Studs
Studs Studs
4
-
5
4
-
5
4
-
5
1
-
16
Operate
Manually
Mho
N
.
O
.
X
-
5
Contact
XI
X
2
XI
X
4
X
4
80
%
or
less
of
rated
voltage
80
%
or
less
of
ra
ted
voltage
80
%
or
80
%
or
less
of
less
of
rated
rated
voltage
voltage
80
%
or
less
of
rated
voltage
80
%
or
less
of
rated
voltage
Pickup
Voltage
0.008
Sec
.
or
less
0.008
Sec
.
or
1
ess
0.009
Sec
.
or
less
0.008
Sec
.
or
less
0.008
p
.
008
Sec
.
or
Sec
.
or
1
ess
Pickup
Time
less
0.200
0.220
0.200
0.220
0.200
0.220
0.100
0.110
0.200
0.220
0.200
0.220
Dropout
Time
(
Sec
.
)
Because
of
the
fast
pickup
times
involved
with
these
telephone
relays
,
it
is
recommended
that
the
pickup
times
be
checked
on
an
electronic
timer
and
an
initiating
switch
with
a
minimum
of
timing
error
between
the
two
poles
.
Pickup
voltage
is
defined
as
the
DC
voltage
,
gradually
applied
,
that
causes
the
telephone
relay
armature
to
pick
up
and
seal
in
against
the
pole
piece
.
Pickup
time
is
defined
as
the
time
interval
between
the
energization
of
the
telephone
relay
and
the
closing
of
an
"
a
"
(
normally
open
)
contact
,
as
rated
DC
voltage
is
suddenly
applied
.
Dropout
time
is
defined
as
the
time
interval
between
the
de
-
energization
of
the
telephone
relay
and
the
opening
of
an
"
a
"
contact
,
as
the
DC
voltage
is
suddenly
reduced
from
rated
DC
to
0
volts
.
MHO
UNIT
-
ACCEPTANCE
TESTS
(
FACTORY
ADJUSTED
PER
THE
CUSTOMER
'
S
SETTINGS
)
If
the
relay
was
calibrated
at
the
factory
per
the
customer
'
s
settings
that
were
listed
on
the
requisition
,
then
the
following
test
procedure
is
recommended
:
Visual
inspection
-
Same
as
before
.
1
.
Mechanical
inspection
-
Same
as
before
.
2
.
-
18
-
Courtesy of NationalSwitchgear.com

GEK
-
45441
Electrical
tests
(
mho
unit
)
-
New
procedure
;
see
below
,
beginning
with
Directional
Test
.
3
.
4
.
Target
/
Seal
-
in
-
Same
as
before
.
5
.
Restraint
Transformer
-
Same
as
before
.
Telephone
relays
-
Same
as
before
.
6
.
Relays
that
have
been
set
per
the
requisition
will
be
set
by
the
factory
and
shipped
with
those
settings
,
adjustments
.
Therefore
,
do
not
disturb
any
of
the
Directional
Test
With
the
relay
set
for
a
particular
application
,
the
directional
test
can
be
omitted
because
the
unit
will
be
set
for
both
a
forward
and
a
reverse
reach
.
After
the
relay
is
leveled
in
its
upright
position
in
its
own
case
or
in
a
similar
test
case
,
note
that
the
normally
-
closed
contact
is
closed
.
Reach
Check
the
requisition
for
the
reach
settings
,
both
in
the
forward
direction
(
90
o
lead
)
and
in
the
reverse
direction
(
2700
lead
)
,
ordinarily
stated
in
ohms
-
phase
-
to
-
neutral
,
but
the
test
circuit
will
test
for
a
phase
-
to
-
phase
ohmic
reach
.
This
will
be
equal
to
two
times
the
phase
-
to
-
neutral
ohmic
reach
.
These
values
are
Connect
the
relay
per
the
test
circuit
of
Figure
7
and
Table
VII
.
The
following
equation
will
determine
the
current
operating
pickup
.
Applied
Voltage
ohmic
reach
setting
(
0
-
0
)
Ipickup
~
(
900
lead
)
Apply
enough
voltage
,
up
to
the
relay
'
s
rated
voltage
,
to
provide
as
much
operating
current
as
possible
,
up
to
a
maximum
of
20
amperes
.
Angle
of
Maximum
Torque
Set
the
phase
angle
at
60
°
lead
.
The
current
operating
pickup
should
be
as
determined
in
the
following
equation
.
T
_
Applied
Voltage
;
P
1
C
|
<
L
|
P
ohmic
reach
setting
(
0
-
0
)
x
cos
30
°
(
600
lead
)
Set
the
phase
angle
at
120
°
lead
.
The
current
operating
pickup
should
be
the
same
as
determined
at
60
o
lead
(
1
3
%
0
f
each
other
)
.
-
19
-
Courtesy of NationalSwitchgear.com

GEK
-
45441
Other
Reach
Taps
The
other
reach
taps
should
not
be
checked
,
because
in
order
to
set
the
mho
unit
characteristic
per
the
customer
'
s
request
the
adjustments
were
changed
so
that
the
basic
minimum
reach
taps
are
not
at
the
nominal
values
as
shown
on
the
reach
tap
block
.
Offset
Tests
The
offset
should
be
checked
at
the
offset
tap
setting
that
was
made
per
the
customer
'
s
requisition
settings
.
Set
the
phase
ange
for
2700
lead
.
Calculate
the
current
pickup
with
the
following
equation
.
Applied
Voltage
ffset
ohmic
reach
(
0
-
0
)
Ipickup
_
g
(
2700
lead
)
Apply
enough
voltage
,
up
to
the
rated
voltage
of
the
unit
,
to
provide
as
much
operating
current
as
possible
,
to
a
maximum
of
20
amperes
.
INSTALLATION
PROCEDURE
INSPECTION
Inspect
all
parts
and
components
of
the
relay
as
described
under
ACCEPTANCE
TESTS
.
Check
the
nameplate
information
against
the
purchase
order
.
Check
the
fingers
and
shorting
bars
in
relay
and
relay
case
against
the
internal
connection
diagram
,
Figure
3
.
LOCATION
The
relay
should
be
installed
in
a
clean
and
dry
location
,
free
from
dust
and
excessive
vibration
,
and
in
a
well
lighted
area
in
order
to
facilitate
inspection
and
testing
.
MOUNTING
The
relay
should
be
mounted
on
a
vertical
surface
in
the
upright
position
,
and
as
level
as
possible
.
The
outline
and
panel
drilling
is
shown
in
Figure
9
.
CONNECTIONS
The
internal
connections
of
the
relay
are
shown
in
Figure
3
.
The
external
connections
are
shown
in
Figures
10
A
and
10
B
.
-
20
-
Courtesy of NationalSwitchgear.com
Other GE Relay manuals
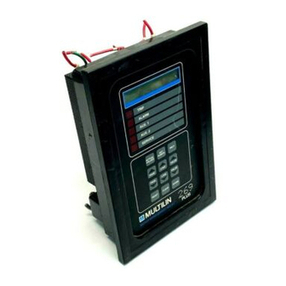
GE
GE MULTILIN 269 MOTOR MANAGEMENT RELAY Series User manual
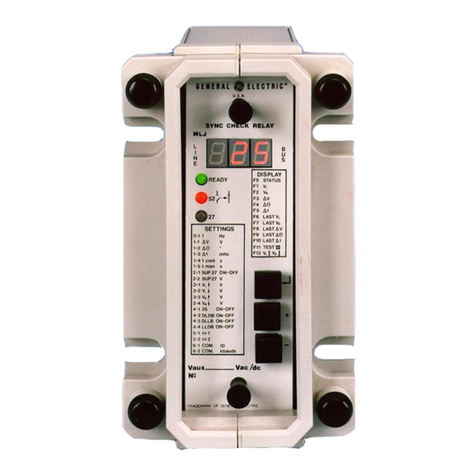
GE
GE MLJ1000 User manual
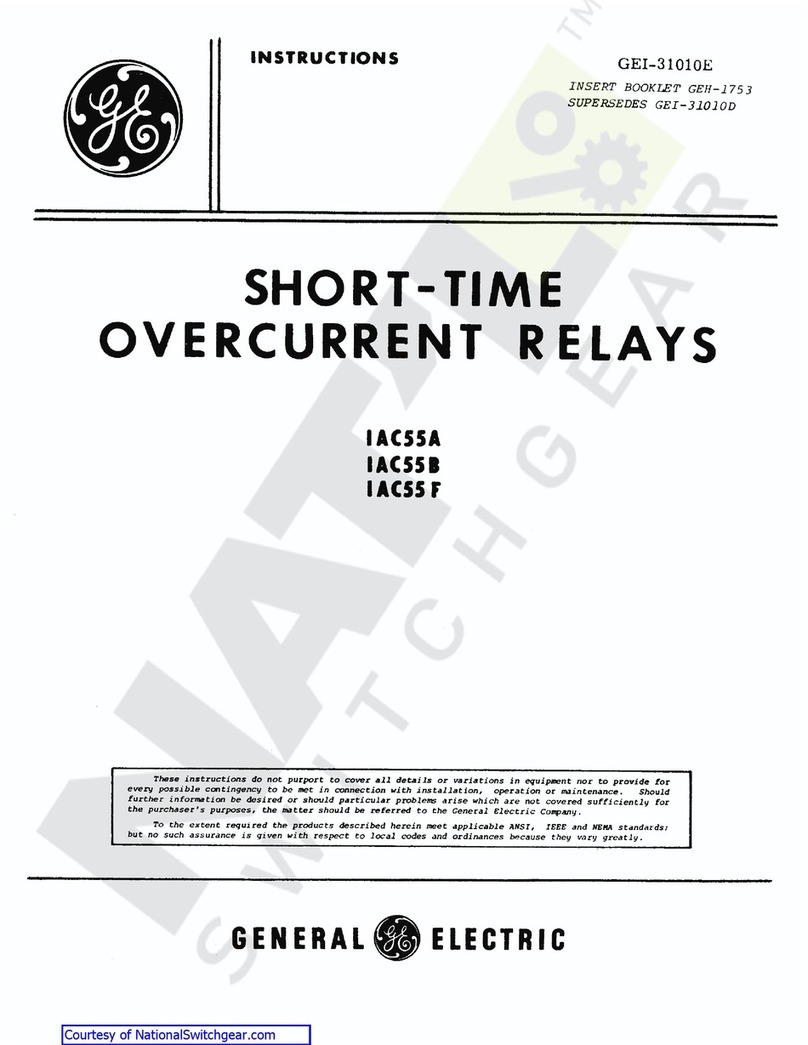
GE
GE IAC55A User manual
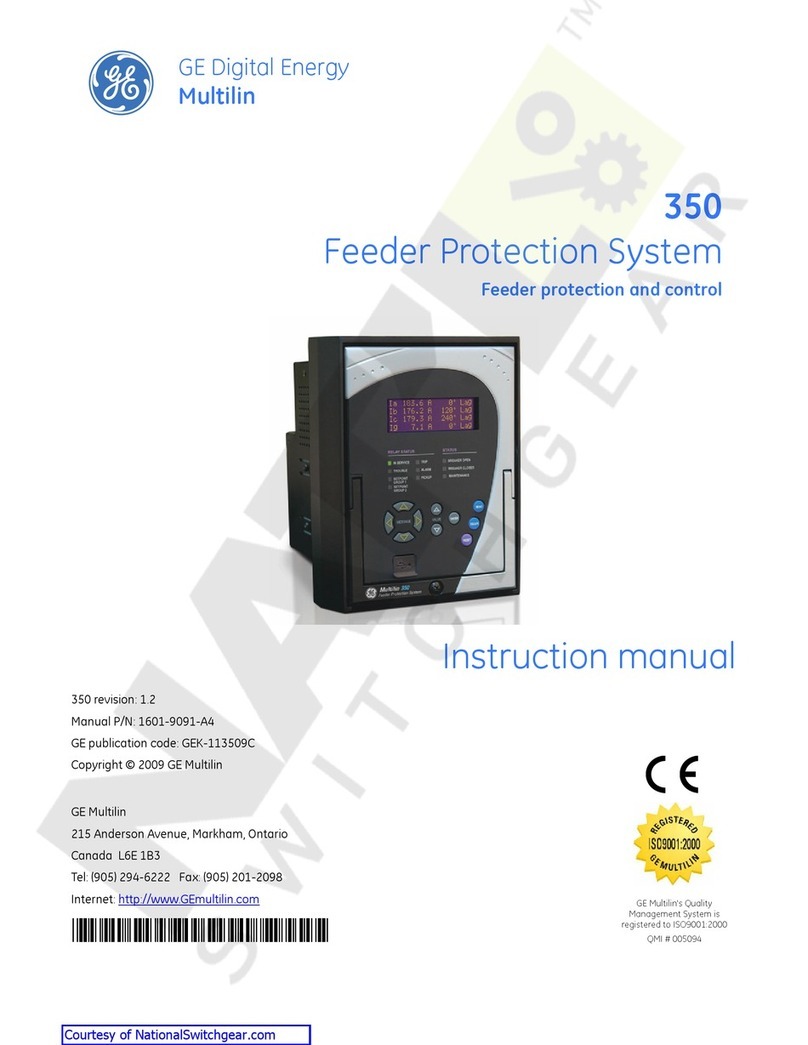
GE
GE ML Series 350 User manual

GE
GE B90 User manual
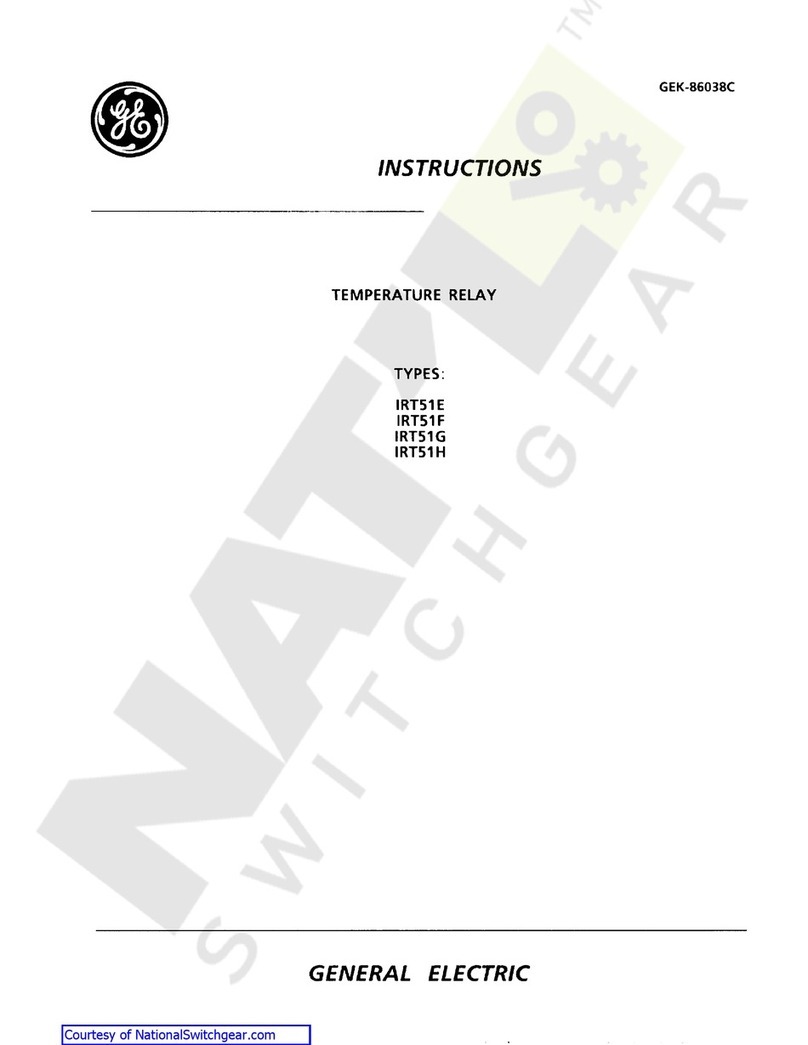
GE
GE IRT51E User manual
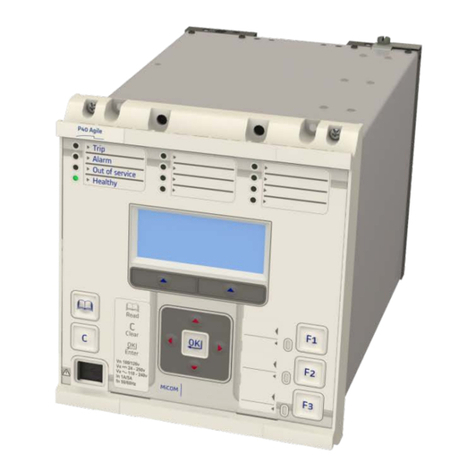
GE
GE MiCOM P40 Agile P14D User manual
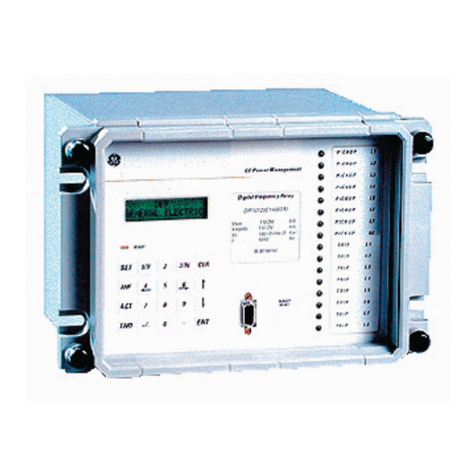
GE
GE Multilin DFF User manual
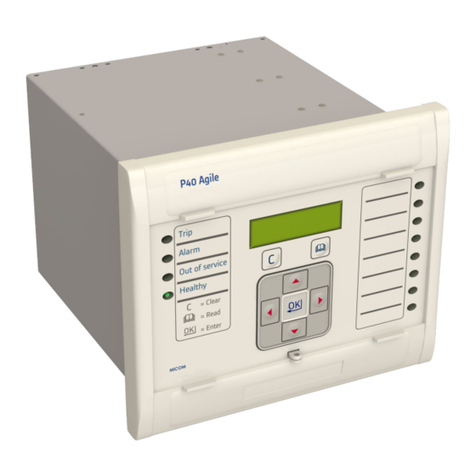
GE
GE MiCOM P40 Agile User manual
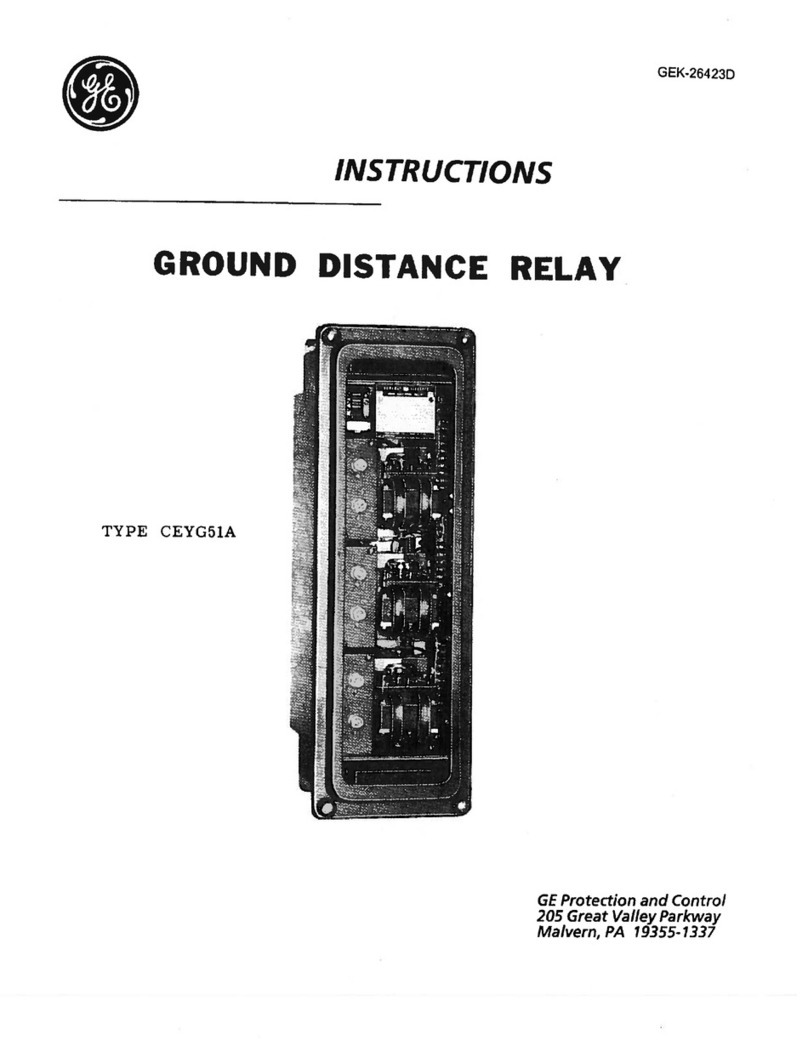
GE
GE CEYG51A User manual