GE IFD User manual

GEK
-
34069
CONTENTS
PAGE
3
DESCRIPTION
APPLICATION
RATINGS
.
...
3
3
3
CURRENT
CIRCUITS
CONTACT
RATINGS
CHARACTERISTICS
OPERATING
CHARACTERISTICS
-
INDUCTION
UNIT
OPERATING
CHARACTERISTICS
CURVES
HINGED
ARMATURE
FAULT
DETECTOR
OPERATING
PRINCIPLES
.
.
.
TORQUE
EQUATION
AND
INDUCTION
UNIT
PICKUP
.
TORQUE
BALANCE
EQUATION
OPERATING
CURRENT
EQUATION
4
4
4
4
4
5
5
5
5
5
BURDENS
CONSTRUCTION
INDUCTION
DISK
UNIT
HINGED
ARMATURE
FAULT
DETECTOR
TARGET
/
SEAL
-
IN
UNIT
RECEIVING
,
HANDLING
AND
STORAGE
ACCEPTANCE
TEST
VISUAL
INSPECTION
MECHANICAL
INSPECTION
DRAWOUT
RELAYS
GENERAL
..
.
.
.
POWER
REQUIREMENTS
GENERAL
ELECTRICAL
TESTS
INDUCTION
UNIT
PICKUP
TEST
..
..
.
OPERATING
CURRENTS
RESTRAINT
CURRENT
INSTANTANEOUS
UNIT
FAULT
DETECTOR
.
.
.
SETTING
THE
INSTANTANEOUS
UNIT
TARGET
AND
SEAL
-
IN
UNIT
PICK
-
UP
AND
DROP
OUT
TEST
INSTALLATION
ELECTRICAL
TESTS
6
6
6
6
7
7
7
7
7
8
8
8
8
8
8
8
9
9
9
9
LOCATION
MOUNTING
CONNECTIONS
TARGET
AND
SEAL
-
IN
ELEMENT
SETTING
Q
9
9
10
SERVICING
10
INDUCTION
UNIT
ADJUSTMENT
RENEWAL
PARTS
11
2
Courtesy of NationalSwitchgear.com

GEK
-
34069
PERCENTAGE
DIFFERENTIAL
RELAY
TYPE
IFD
MODEL
12
IFD
51
D
(
-
)
A
DESCRIPTION
The
IFD
51
D
relay
is
an
induction
disk
ground
differential
relay
.
It
was
designed
specifically
to
provide
differential
protection
for
single
phase
-
to
-
ground
faults
in
the
wye
connected
winding
of
a
power
transformer
and
the
leads
to
its
associated
circuit
breaker
.
The
IFD
51
D
relay
is
shock
resistant
and
is
supplied
complete
with
target
in
a
standard
M
2
drawout
case
.
The
internal
connections
and
the
outline
and
dimensions
are
illustrated
in
Figures
1
and
2
respectively
.
APPLICATION
The
IFD
51
D
was
specifically
designed
to
provide
differential
protection
for
single
-
phase
-
to
-
ground
faults
in
the
zone
from
the
wye
connected
winding
and
its
associated
circuit
breaker
.
This
zone
includes
the
transformer
wye
winding
itself
.
The
IFD
is
principally
intended
for
application
on
transformers
where
the
neutral
is
grounded
through
a
resistor
which
limits
the
single
phase
-
to
-
ground
fault
currents
to
a
range
of
200
-
2000
amperes
.
However
,
it
may
also
be
applied
to
solidly
grounded
transformers
if
the
neutral
CT
is
of
good
quality
and
has
the
same
ratio
as
the
circuit
breaker
CT
'
s
so
that
no
auxiliary
CT
is
required
.
The
power
transformer
winding
with
which
the
relay
is
associated
must
have
its
own
neutral
lead
as
illustrated
in
the
external
connection
of
Figure
5
.
That
is
to
say
,
that
the
power
transformer
cannot
be
an
auto
-
transformer
nor
can
it
be
a
wye
-
delta
-
wye
bank
with
a
common
neutral
terminal
for
both
windings
.
An
auxiliary
CT
is
normally
required
to
match
the
ratio
between
the
circuit
breaker
CT
'
s
and
the
transformer
neutral
CT
.
The
ratio
of
this
auxiliary
CT
can
be
evaluated
by
dividing
the
ratio
of
the
circuit
breaker
CT
‘
s
(
on
the
tap
used
)
by
the
ratio
of
the
neutral
CT
.
The
purpose
of
the
instantaneous
unit
in
the
IFD
51
D
is
to
make
the
relay
shock
resistant
The
pick
-
up
setting
of
the
instantaneous
unit
should
be
set
so
that
it
does
not
reduce
the
sensitivity
of
the
protection
.
Since
the
basic
sensitivity
of
the
main
unit
of
the
relay
is
0.5
or
1.0
amperes
,
it
is
suggested
that
the
setting
of
the
instantaneous
unit
be
in
the
range
of
0.5
to
1.0
amperes
.
As
indicated
in
the
section
under
CHARACTERISTICS
,
the
IFD
51
D
may
be
set
for
12.5
or
25
percent
slope
.
With
the
12.5
percent
slope
setting
,
the
main
unit
will
pick
up
at
about
0.5
amperes
in
the
operating
coil
with
no
current
in
any
restraint
coil
.
With
the
25
percent
slope
,
the
current
required
to
produce
operation
increases
to
about
1
ampere
.
The
higher
slope
setting
will
provide
security
against
improper
operation
in
the
event
of
circuit
breaxer
CT
saturation
during
external
multi
-
phase
faults
.
As
indicated
in
the
external
connections
of
Figure
5
,
only
one
IFD
51
D
relay
is
required
for
the
protection
described
.
Also
,
a
source
of
d
-
c
is
required
in
order
for
the
relay
to
trip
the
breaker
.
This
may
either
be
a
station
battery
or
a
capacitor
trip
device
.
RATINGS
CURRENT
CIRCUITS
Table
A
below
gives
the
current
circuit
ratings
.
These
instructions
do
not
purport
to
cover
all
details
or
variations
in
equipment
nor
to
provide
for
every
possible
contingency
to
be
met
in
connection
with
installation
,
operation
or
maintenance
.
further
information
be
desired
or
should
particular
problems
arise
which
are
not
covered
sufficiently
for
the
purchaser
'
s
purposes
,
the
matter
should
be
referred
to
the
.
-
General
Electric
Company
.
Should
To
the
extent
required
the
products
described
herein
meet
applicable
ANSI
,
IEEE
and
NEMA
standards
;
but
no
such
assurance
is
given
with
respect
to
local
codes
and
ordinances
because
they
vary
greatly
.
3
Courtesy of NationalSwitchgear.com

GEK
-
34069
TABLE
A
CONTINUOUS
RATING
AMPS
ONE
SECOND
RATING
AMPS
CIRCUIT
Operating
Coil
260
5
Restraint
Coils
10
260
Hinged
Armature
Fault
Detector
0.5
-
2
Amp
Range
0.75
10
CONTACT
RATINGS
The
current
-
closing
rating
of
the
contacts
is
30
amperes
for
voltages
not
exceeding
250
volts
.
The
current
-
carrying
ratings
are
offected
by
the
selection
of
the
tap
on
the
target
and
seal
-
in
coil
as
indicated
in
the
following
table
:
Amperes
,
a
-
c
or
d
-
c
Function
2
-
Amp
Tap
0.2
Amp
Tap
Tripping
Duty
Carry
Continuously
Operating
Range
Resistance
Impedance
at
60
cy
30
5
3
0.3
2
-
30
0.2
-
2
0.13
7
0.53
52
If
the
tripping
current
exceeds
30
amperes
an
auxiliary
relay
should
be
used
,
the
connections
being
such
that
the
tripping
current
does
not
pass
through
the
contacts
or
the
target
and
seal
in
coils
of
the
protective
relay
.
CHARACTERISTICS
OPERATING
CHARACTERISTICS
-
INDUCTION
UNIT
The
IFD
51
D
relay
has
an
operating
coil
with
taps
available
for
selecting
either
a
12.5
or
25
percent
slope
.
Percent
slope
is
defined
as
operating
coil
current
required
to
close
contacts
divided
by
restraint
current
flowing
in
two
restraint
coils
multiplied
by
100
percent
.
For
the
purpose
of
this
definition
the
currents
in
the
two
restraint
coils
are
equal
.
With
equal
currents
flowing
in
all
three
restraint
coils
,
the
operating
current
required
to
close
contacts
will
be
approximately
1.23
times
that
required
with
the
same
current
flowing
in
only
two
restraint
coils
.
With
the
operating
coil
set
on
the
12.5
percent
tap
,
the
induction
unit
will
close
its
contacts
at
0.5
amps
with
zero
restraint
current
.
On
the
25
percent
tap
,
operating
current
required
to
close
contacts
with
zero
restraint
is
approximately
twice
that
required
on
the
12.5
percent
tap
or
approximately
1
ampere
.
OPERATING
CHARACTERISTIC
CURVES
Figure
3
shows
the
operating
current
vs
restraining
current
characteristic
curve
'
for
the
IFD
51
D
.
Figure
4
shows
the
time
current
curve
for
this
relay
.
These
times
apply
only
for
the
1
/
2
time
dial
setting
.
Times
may
be
increased
by
increasing
the
time
dial
setting
,
but
the
time
dial
should
never
be
set
below
the
1
/
4
position
.
HINGED
ARMATURE
FAULT
DETECTOR
The
IFD
51
D
relay
includes
a
shock
resistant
hinged
armature
type
overcurrent
unit
.
The
contact
of
this
overcurrent
unit
is
connected
in
series
with
the
induction
disk
unit
contact
so
that
both
must
be
picked
up
to
initiate
a
tripping
output
.
This
checks
that
fault
current
is
flowing
and
guards
against
false
tripping
by
the
induction
disk
unit
if
it
should
close
its
contact
due
to
shock
.
k
Courtesy of NationalSwitchgear.com

GEK
-
34069
The
hinged
armature
overcurrent
unit
is
adjustable
over
a
pickup
current
range
of
0
,
5
-
2
amps
by
means
of
an
adjustable
core
.
This
unit
should
be
set
to
pickup
for
any
fault
condition
for
which
the
induction
disk
unit
is
expected
to
operate
.
OPERATING
PRINCIPLES
The
IFD
51
D
relay
induction
unit
has
four
U
-
magnets
operating
on
two
disks
mounted
on
a
common
shaft
.
Three
of
the
U
-
Magnets
have
restraining
coils
which
drive
the
disk
in
the
contact
opening
direction
.
The
fourth
U
-
Magnet
has
an
operating
coil
which
drives
the
disk
in
the
contact
closing
direction
.
The
induction
unit
will
close
its
contacts
when
the
torque
produced
by
the
operating
coil
exceeds
the
sum
of
the
torques
produced
by
the
control
spring
and
the
three
restraining
coils
.
TORQUE
EQUATION
AND
INDUCTION
UNIT
PICKUP
Each
of
the
four
U
-
Magnets
produces
a
torque
proportional
to
the
square
of
the
current
flowing
in
its
operating
coil
,
the
operating
coil
in
the
contact
closing
direction
and
the
restraining
coils
in
the
contact
opening
direction
.
Using
this
fact
plus
the
basic
torque
balance
equation
,
we
can
write
an
equation
for
operating
current
in
terms
of
currents
in
the
three
restraining
coils
and
control
spring
setting
.
Torque
Balance
Equation
To
=
TR
1
+
TR
2
+
TR
3
+
TS
where
T
0
=
operating
coil
torque
Tftl
®
TR
2
>
TR
3
=
tor
9
ue
produced
by
each
of
the
three
restraining
coils
respectively
T
$
=
Spring
torque
Operating
Current
Equation
:
I
oI
2
=
K
1
^
Rl
2
+
+
JR
32
)
+
!
S
2
where
I
0
=
operating
current
required
to
close
contacts
IRI
,
IR
2
*
*
R
3
=
current
in
each
of
the
three
restraining
coils
respectively
.
1
^
=
Operating
coil
current
to
overcome
spring
force
(
Close
contacts
with
zero
restraining
current
)
,
and
=
Design
constant
of
relay
,
may
be
determined
by
working
operating
current
equation
with
point
on
operating
current
vs
restraint
curve
.
Note
Ki
and
1
$
are
a
function
of
operating
coil
tap
setting
.
An
example
of
the
way
the
operating
current
equation
may
be
used
is
as
follows
.
With
the
operating
coil
set
on
the
12.5
percent
tap
the
induction
unit
will
close
its
contacts
with
0
,
5
amps
in
the
operating
coil
and
zero
restraint
current
(
I
<
.
=
0.5
)
.
The
operating
characteristic
curves
give
an
operating
current
of
about
0.9
amps
with
5
amps
in
three
restraints
.
Plugging
these
values
into
the
operating
current
equation
and
solving
for
Kj
,
we
get
=
7.47
X
10
“
3
.
Using
these
values
of
and
1
$
,
we
can
calculate
the
operating
current
required
to
close
contacts
for
different
conditions
of
restraint
current
.
For
instance
,
using
=
7.47
X
10
~
3
and
1
$
=
0.5
,
the
operating
current
equation
reveals
that
the
induction
unit
will
just
close
its
contacts
with
1.32
amps
in
the
operating
coil
and
10
amps
in
two
restraint
coils
.
BURDENS
Table
A
below
gives
the
impedances
of
the
coils
in
these
relays
.
These
impedances
are
measured
with
5
amperes
flowing
through
the
specified
coil
.
The
operating
coil
impedance
given
is
for
the
12.5
percent
tap
.
COIL
IMPEDANCE
Z
OHMS
Operating
Coil
Restraininq
Coi
~
1
~
s
.
43
+
j
.
99
1.08
6.065
+
j
6.52
0
VOb
8
Hinged
Armature
Unit
10.3
+
j
8.1
12.9
5
Courtesy of NationalSwitchgear.com

GEK
-
34069
The
operating
coil
impedance
rises
to
approximately
1.4
ohms
at
pickup
or
at
0.5
amps
,
when
set
on
the
12
,
5
percent
tap
.
T
^
e
operating
coil
impedance
on
the
25
percent
tap
is
approximately
one
quarter
the
impedance
given
for
the
12.5
percent
tap
.
CONSTRUCTION
The
IFD
51
D
relay
consists
of
an
induction
disk
unit
,
a
target
/
seal
-
in
unit
,
and
a
hinged
armature
overcurrent
unit
mounted
in
a
medium
size
double
ended
drawout
M
2
case
.
The
internal
connections
diagram
is
shown
in
Figure
1
,
the
outline
and
panel
drilling
is
shown
in
Figure
2
.
INDUCTION
DISK
UNIT
The
induction
disk
unit
consists
of
two
disks
mounted
on
a
common
shaft
driven
by
four
U
-
Magnet
and
coil
assemblies
.
The
lower
left
U
-
Magnet
and
coil
is
the
operating
coil
,
this
element
drives
the
disks
in
the
contact
closing
direction
.
The
operating
coil
is
tapped
so
that
the
relay
may
be
set
for
either
a
12.5
or
25
percent
slope
.
The
operating
coil
tap
may
be
selected
by
setting
the
tap
plug
in
the
tap
block
position
indicated
by
the
engraved
tap
plate
.
The
tap
block
is
mounted
above
the
induction
disk
unit
.
The
operating
coil
U
-
Magnet
is
provided
with
fixed
shading
rings
which
provide
the
phase
shift
in
flux
necessary
to
drive
the
disk
.
The
other
three
U
-
Magnets
mount
the
restraint
coils
.
These
three
elements
drive
the
disk
in
the
contact
opening
direction
.
The
restraint
U
-
magnets
and
coils
are
similar
to
the
operating
U
-
Magnet
and
coil
except
the
restraint
coils
are
untrapped
and
the
restraint
U
-
Magnets
use
wound
shading
coils
instead
of
shading
rings
to
produce
the
phase
shifted
flux
necessary
to
drive
the
disk
.
The
wound
shading
coils
of
the
restraint
elements
are
wired
to
three
separate
slide
wire
resistors
mounted
in
the
back
of
the
relay
.
These
resistors
are
used
to
adjust
the
basic
torque
characteristic
of
the
restraint
elements
.
As
indicated
by
the
internal
connections
diagram
(
Fig
.
1
)
the
bottom
resistor
adjusts
the
lower
right
restraint
element
,
the
middle
resistor
adjusts
the
upper
right
,
and
the
top
resistor
adjusts
the
upper
left
restraint
.
The
control
spring
mounted
at
the
top
of
induction
disk
unit
is
used
to
adjust
the
operating
coil
current
required
to
close
contacts
with
no
current
in
the
restraints
.
This
control
spring
may
be
adjusted
by
turning
the
notched
adjusting
ring
.
The
time
dial
is
above
the
control
spring
.
The
time
dial
is
used
to
increase
the
travel
on
the
disk
and
this
increase
operating
time
.
The
time
dial
on
the
IFD
51
D
is
locked
by
two
locking
screws
through
the
top
of
the
frame
.
These
locking
screws
prevent
restraint
torque
from
turning
the
time
dial
and
changing
the
operating
time
setting
.
The
relay
time
dial
is
normally
set
and
locked
in
the
1
/
2
position
.
The
induction
disk
unit
is
provided
with
a
drag
magnet
which
serves
to
retard
the
motion
of
the
disk
to
give
the
correct
time
delay
.
HINGED
ARMATURE
FAULT
DETECTOR
The
IFD
51
D
relay
is
provided
with
a
small
hinged
armature
overcurrent
unit
.
This
unit
is
used
to
make
the
relay
more
shock
resistant
.
The
operating
coil
of
this
unit
is
wired
to
studs
4
-
5
and
the
contacts
are
in
series
with
the
induction
unit
contacts
.
The
pickup
current
of
this
unit
is
adjustable
over
a
4
-
1
range
range
by
means
of
an
adjustable
core
.
The
core
is
provided
with
a
locknut
which
must
be
loosened
before
the
core
may
be
turned
to
change
pick
-
up
.
The
fault
detector
unit
is
mounted
on
the
upper
right
hand
side
of
the
relay
.
TARGET
/
SEAL
-
IN
UNIT
The
target
seal
-
in
unit
is
mounted
in
the
top
of
the
case
on
the
left
hand
side
.
The
seal
-
in
unit
has
its
coil
in
series
and
its
contacts
in
parallel
with
the
contacts
of
the
induction
disk
unit
and
the
instantaneous
overcurrent
unit
such
that
when
the
instantaneous
unit
and
induction
disk
unit
contacts
close
the
seal
-
in
picks
up
and
seals
in
.
When
the
seal
in
unit
picks
up
,
it
raises
a
target
into
view
which
latches
up
and
remains
exposed
until
it
is
released
by
pressing
a
button
beneath
the
lower
left
corner
of
the
cover
.
The
components
of
the
IFD
51
D
relay
are
mounted
in
a
M
2
case
whose
outline
and
drilling
plan
is
shown
in
Figure
2
.
The
relay
^
components
are
mounted
in
a
cradle
assembly
which
is
latched
into
a
drawout
case
when
the
relay
is
in
operation
but
it
can
be
easily
removed
when
desired
.
To
do
this
,
the
relay
is
first
disconnected
by
removing
the
connection
plug
which
completes
the
electrical
connections
between
the
6
Courtesy of NationalSwitchgear.com

GEK
-
34069
case
block
and
the
cradle
block
.
To
test
the
relay
in
its
case
this
connection
block
can
be
replaced
by
a
test
plug
.
The
cover
,
which
is
attached
to
front
of
the
relay
case
,
contains
the
target
reset
mechanism
and
an
interlock
arm
which
prevents
the
cover
from
being
replaced
until
the
connection
plugs
have
been
inserted
.
The
relay
case
is
suitable
for
either
semi
flush
or
surface
mounting
on
all
panels
up
to
2
inches
thick
and
appropriate
hardware
is
available
.
However
,
panel
thickness
must
be
indicated
on
the
relay
order
to
insure
that
proper
hardware
will
be
included
.
Every
circuit
in
the
drawout
case
has
an
auxiliary
brush
,
as
shown
in
Fig
.
6
,
to
provide
adequate
overlap
when
the
connecting
plug
is
withdrawn
or
inserted
.
Some
circuits
are
equipped
with
shorting
bars
(
see
Figure
1
)
and
on
these
circuits
it
is
especially
important
that
the
auxiliary
brush
makes
contact
as
indicated
in
Fig
.
6
.
with
adequate
pressure
to
prevent
the
opening
of
C
.
T
.
secondary
circuits
.
RECEIVING
,
HANDLING
AND
STORAGE
These
relays
,
when
not
included
as
a
part
of
a
control
panel
,
will
be
shipped
in
cartons
designed
to
protect
them
against
damage
.
Immediately
upon
receipt
of
a
relay
,
examine
it
for
any
damage
sustained
in
transit
.
If
injury
or
damage
resulting
from
rough
handling
is
evident
,
file
a
damage
claim
at
once
with
the
transportation
company
and
promptly
notify
the
hearest
General
Electric
Apparatus
Sales
Office
.
Reasonable
care
should
be
exercised
in
unpacking
the
relay
in
order
that
none
of
the
parts
are
in
-
jured
or
the
adjustments
disturbed
.
If
the
relays
are
not
to
be
installed
immediately
,
they
should
be
stored
in
their
original
cartons
in
a
place
that
is
free
from
moisture
,
dust
and
metallic
chips
.
Foreign
matter
collected
on
the
outside
of
the
case
may
find
its
way
inside
when
the
cover
is
removed
and
cause
trouble
in
the
operation
of
the
relay
.
ACCEPTANCE
TEST
Immediately
upon
receipt
of
the
relay
,
an
inspection
and
acceptance
test
should
be
made
to
insure
that
no
damage
has
been
sustained
in
shipment
and
that
the
relay
calibrations
have
not
been
disturbed
.
VISUAL
INSPECTION
Check
the
nameplate
stamping
to
insure
that
the
model
number
and
rating
of
the
relay
agree
with
the
requisition
.
Remove
the
relay
from
its
case
and
check
that
there
are
no
broken
or
cracked
molded
parts
or
othc
signs
of
physical
damage
,
and
that
all
the
screws
are
tight
.
MECHANICAL
INSPECTION
1
.
There
should
be
no
noticable
friction
when
the
disk
is
rotated
slowly
clockwise
.
The
disk
should
return
by
itself
to
its
rest
position
.
2
.
Make
sure
the
control
spring
is
not
deformed
nor
its
convolutions
tangled
^
or
touching
.
3
.
The
armature
and
contacts
of
the
seal
-
in
unit
as
well
as
the
armature
and
contacts
of
the
instantaneous
unit
should
move
freely
when
operated
by
hand
,
there
should
be
at
least
1
/
32
"
wipe
on
the
seal
in
and
instantaneous
unit
contacts
.
4
.
The
targets
in
the
seal
-
in
unit
and
in
the
instantaneous
unit
must
come
into
view
and
latch
when
the
armature
are
operated
by
hand
and
should
unlatch
when
the
target
release
level
is
operated
.
5
.
Make
sure
that
the
fingers
and
shorting
bars
agree
with
the
internal
connections
diagram
.
6
.
The
time
dial
locking
screws
should
be
observed
to
lock
the
time
dial
so
that
it
can
not
be
turned
.
CAUTION
:
EVERY
CIRCUIT
IN
THE
DRAWOUT
CASE
HAS
AN
AUXILIARY
BRUSH
.
IT
IS
ESPECIALLY
IMPORTANT
ON
CURRENT
CIRCUITS
AND
OTHER
CIRCUITS
WITH
SHORTING
BARS
THAT
THE
AUXILIARY
BRUSH
BE
BENT
HIGH
ENOUGH
TO
ENGAGE
THE
CONNECTING
PLUG
OR
TEST
PLUG
BEFORE
THE
MAIN
BRUSHES
DO
.
THIS
WILL
PREVENT
CT
SECONDARY
CIRCUITS
FROM
BEING
OPENED
.
DRAWOUT
RELAYS
GENERAL
Since
all
drawout
relays
in
service
operate
in
their
case
,
it
is
recommended
that
they
be
tested
ir
their
case
or
an
equivalent
steel
case
.
In
this
way
any
magnetic
effects
of
the
enclosure
will
be
7
Courtesy of NationalSwitchgear.com

GE
K
-
34069
accurately
duplicated
during
testing
,
using
a
12
XLA
13
A
test
plug
,
shorting
bars
in
the
case
.
plug
allows
greater
testing
flexibility
,
it
also
requires
C
.
T
.
shorting
jumpers
and
the
'
exercise
of
greater
care
since
connections
are
made
to
both
the
relay
and
the
external
circuitry
.
POWER
REQUIREMENTS
GENERAL
A
relay
may
be
tested
without
removing
it
from
the
panel
by
This
plug
makes
connections
only
with
the
relay
and
does
not
disturb
any
Of
course
,
the
12
XLA
12
A
test
plug
may
also
be
used
.
Although
this
test
All
alternating
current
operated
devices
are
affected
by
frequency
.
Since
non
sinusoidal
waveforms
can
be
analyzed
as
a
fundamental
frequency
plus
harmonics
of
the
fundamental
frequency
,
it
follows
that
alternating
current
devices
(
relays
)
will
be
affected
by
the
applied
waveform
.
Therefore
,
in
order
to
properly
test
alternating
current
relays
it
is
essential
to
use
a
sine
wave
of
current
and
/
or
voltage
.
The
purity
of
the
sine
wave
(
i
.
e
.
its
freedom
from
harmonics
)
cannot
be
expressed
as
a
finite
number
for
any
particular
relay
,
however
,
any
relay
using
tuned
circuit
,
R
-
L
or
C
networks
,
or
saturating
electromagnets
(
such
as
induction
disk
relays
)
would
be
essentially
affected
by
non
-
sinusoidal
wave
forms
.
ELECTRICAL
TESTS
The
IFD
51
D
relay
may
be
satisfactorily
tested
on
a
single
phase
basis
,
in
that
its
performance
with
single
phase
currents
is
not
significantly
different
than
with
three
phase
currents
.
The
electrical
tests
needed
to
determine
that
the
relay
adjustments
have
not
been
disturbed
are
as
follows
:
NOTE
:
It
is
recommended
that
a
voltage
source
of
115
volts
or
more
of
rated
frequency
with
resistive
loading
be
used
to
perform
these
tests
.
INDUCTION
UNIT
PICKUP
TEST
Apply
gradually
increasing
current
to
operating
coil
circuit
(
studs
2
-
3
)
.
With
the
operating
coil
set
on
the
0.5
amp
tap
,
the
relay
should
just
hold
its
contacts
closed
with
a
current
of
0.48
-
0.52
amps
flowing
.
The
contact
circuit
is
between
studs
1
-
11
and
the
instantaneous
unit
contacts
must
be
jumpered
for
this
circuit
to
show
continuity
when
the
induction
disk
unit
contacts
close
.
Set
on
the
25
percent
tap
the
contact
closing
current
should
be
approximately
0.9
amps
.
OPERATING
CURRENTS
RESTRAINT
CURRENT
See
Figure
7
for
test
connections
and
Figure
1
for
relay
internal
connections
.
With
the
three
restraint
currents
wired
in
series
(
jumper
stud
7
to
8
,
9
-
16
)
apply
5
amps
to
the
three
restraints
(
be
-
tween
studs
6
-
17
)
.
With
the
operating
coil
set
on
the
12.5
percent
tap
the
relay
should
just
close
its
contacts
with
0.75
-
0.95
amps
flowing
in
the
operating
coil
.
For
information
on
adjusting
the
restraint
current
vs
operating
current
,
refer
to
the
section
on
Servicing
.
INSTANTANEOUS
UNIT
FAULT
DETECTOR
The
pickup
current
of
the
fault
detector
may
be
checked
by
applying
current
to
studs
4
-
5
.
unit
is
adjustable
over
a
range
of
pickup
currents
from
0.5
-
2
amps
by
turning
the
adjustable
core
,
unit
is
set
at
the
factory
to
pickup
at
0.45
-
0.55
amps
,
this
adjustment
may
be
changed
if
desired
.
This
The
SETTING
THE
INSTANTANEOUS
UNIT
Loosen
the
locknut
and
turn
pole
piece
toward
che
desired
setting
.
Turning
the
pole
piece
up
increases
the
pick
up
,
turning
the
pole
piece
down
decreases
the
pick
up
.
Bring
up
the
current
slowly
until
unit
picks
up
.
It
may
be
necessary
to
repeat
this
operation
until
the
desired
pick
up
value
is
obtained
.
Once
the
desired
pick
up
value
is
reached
,
tighten
the
locknut
.
CAUTION
:
THE
INSTANTANEOUS
UNIT
IS
RATED
1.5
TIMES
MINIMUM
PICK
UP
.
DO
NOT
LEAVE
THE
TEST
CURRENT
ON
ttiOTONG
AS
IT
MAY
DAMAGE
THE
UNIT
.
TARGET
AND
SEAL
-
IN
UNIT
The
target
and
seal
-
in
unit
has
an
operating
coil
tapped
at
0.2
and
2.0
amperes
.
The
relay
is
shipped
from
the
factory
with
the
tap
screw
in
the
lover
ampere
position
.
The
tap
screw
is
the
screw
holding
the
right
hand
stationary
contact
.
To
change
the
tap
setting
,
first
remove
one
screw
from
the
left
hand
stationary
contact
and
place
it
in
the
desired
tap
.
Next
remove
the
screw
from
the
undesired
tap
and
place
it
on
the
left
hand
stationary
contact
where
the
first
screw
was
removed
.
This
procedure
necessary
to
prevent
the
right
hand
stationary
contact
from
getting
out
of
adjustment
.
Screws
should
not
be
in
both
taps
at
the
same
time
.
8
Courtesy of NationalSwitchgear.com

GEK
-
34069
PICK
UP
AND
DROP
OUT
TEST
1
.
Connect
relay
studs
1
and
2
to
a
D
.
C
.
source
,
ammeter
and
load
box
so
that
the
current
can
be
controlled
over
a
range
of
0.1
to
2.0
amperes
.
2
.
Jumper
the
induction
disk
and
instantaneous
unit
contacts
.
3
.
Increase
the
current
slowly
until
the
seal
-
in
unit
picks
up
.
See
Table
XI
below
.
4
.
Remove
the
jumper
from
the
instantaneous
unit
contacts
,
the
seal
-
in
unit
should
remain
in
the
pick
up
position
.
5
.
Decrease
the
current
slowly
until
the
seal
-
in
unit
drops
out
.
See
Table
XI
.
TABLE
XI
PICK
-
UP
CURRENT
DROPOUT
CURRENT
TAP
0.2
0.15
-
0.195
.
05
OR
MORE
2.0
1.50
-
1.95
.
55
OR
MORE
INSTALLATION
If
after
the
acceptance
tests
the
relay
is
held
in
storage
before
shipment
to
the
job
site
,
it
is
recommended
that
the
visual
and
mechanical
inspection
described
under
the
section
on
ACCEPTANCE
TESTS
be
repeated
before
installation
.
The
relay
must
be
mounted
on
a
vertical
surface
and
must
be
level
for
correct
operation
.
ELECTRICAL
TESTS
It
is
recommended
that
the
electrical
tests
outlined
under
acceptance
tests
be
repeated
at
the
time
of
installation
.
If
desired
,
the
induction
disk
unit
may
be
checked
at
several
operating
points
using
a
method
similar
to
that
outlined
in
acceptance
tests
.
The
fault
detector
and
target
seal
in
units
should
be
set
at
their
desired
operating
points
and
these
settings
should
be
electrically
tested
.
LOCATION
The
location
should
be
clean
and
dry
,
free
from
dust
and
excessive
vibration
,
and
well
lighted
to
facilitate
inspection
and
testing
.
MOUNTING
The
relay
should
be
mounted
on
a
vertical
surface
.
The
outline
and
panel
diagram
is
shown
in
Figure
2
.
CONNECTIONS
Internal
connection
diagram
is
shown
in
Figure
1
.
A
typical
wiring
diagram
is
given
in
Figure
5
.
One
of
the
mounting
studs
or
screws
should
be
permanently
grounded
by
a
conductor
not
less
than
No
.
12
B
&
S
gage
copper
wire
or
its
equivalent
.
TARGET
AND
SEAL
-
IN
ELEMENT
SETTING
For
trip
coils
operating
on
currents
ranging
from
0.2
up
to
2.0
amperes
at
the
minimum
control
voltage
,
set
the
target
and
seal
-
in
tap
plug
in
the
0.2
ampere
tap
.
For
trip
coils
operating
on
currents
ranging
from
2
to
30
amperes
at
the
minimum
control
voltage
place
the
tap
plug
in
the
2
ampere
tcip
.
The
tap
plug
is
the
screw
holding
the
right
-
hand
stationary
contact
of
the
seal
-
in
element
.
To
change
the
tap
setting
,
first
remove
the
connecting
plug
.
Then
,
take
a
screw
from
the
left
-
hand
stationary
contact
and
place
it
in
the
desired
tap
.
Next
remove
the
screw
from
the
other
tap
,
and
place
it
in
the
left
-
hand
contact
.
This
procedure
is
necessary
to
prevent
the
right
-
hand
stationary
contact
from
getting
out
of
adjustment
.
Screws
should
not
be
in
both
taps
at
the
same
time
as
pickup
for
d
-
c
will
9
Courtesy of NationalSwitchgear.com

GEK
-
34069
be
the
higher
tap
value
and
a
-
c
pickup
will
be
increased
.
SERVICING
I f
it
is
found
that
the
relay
calibrations
are
out
of
adjustment
then
proceed
as
follows
:
1
.
If
there
are
indications
of
excessive
friction
the
lower
jewel
may
be
tested
for
cracks
by
exploring
its
surface
with
the
point
of
a
fine
needle
.
It
it
is
necessary
to
replace
the
jewel
a
new
pivot
should
be
screwed
into
the
bottom
of
the
shaft
at
the
same
time
.
The
jewel
should
be
turned
up
until
the
disk
is
centered
in
the
air
gaps
,
after
which
it
should
be
locked
in
this
position
by
the
set
screw
provided
for
this
purpose
.
The
upper
bearing
end
play
can
be
felt
;
about
0
,
015
inch
is
correct
.
2
.
The
differential
unit
pick
up
can
be
adjusted
by
turning
the
control
spring
adjusting
ring
.
3
.
To
change
target
seal
-
in
tap
settings
,
proceed
as
follows
:
The
tap
plug
is
the
screw
holding
the
right
-
hand
stationary
contact
of
the
seal
-
in
unit
.
To
change
the
tap
setting
,
first
remove
the
connection
plug
.
Then
,
take
a
screw
from
the
left
-
hand
stationary
contact
and
place
it
in
the
desired
tap
.
Next
remove
the
screw
from
the
other
tap
,
and
place
it
in
the
left
-
hand
contact
.
This
procedure
is
necessary
to
prevent
the
right
hand
stationary
contact
from
getting
out
of
adjustment
.
Screws
should
not
be
in
both
taps
at
the
same
time
as
pickup
for
d
-
c
will
be
the
higher
tap
value
and
a
-
c
pickup
will
be
increased
.
4
.
For
cleaning
relay
contacts
a
flexible
burnishing
tool
should
be
used
.
This
consists
of
an
etched
roughened
strip
of
flexible
metal
resembling
a
superfine
file
which
removes
corroded
material
quickly
without
scratching
the
surface
.
The
flexibility
of
the
tool
insures
the
cleaning
of
the
actual
points
of
contact
.
Never
use
knives
,
files
,
abrasive
paper
or
cloth
to
clean
relay
contacts
.
A
burnishing
tool
as
described
above
can
be
obtained
from
the
factory
.
5
.
Instantaneous
overcurrent
unit
adjustment
.
Select
the
current
above
which
it
is
desired
to
have
the
instantaneous
unit
operate
and
set
the
adjustable
pole
piece
so
that
the
top
of
hexagon
head
is
even
with
the
desired
calibration
on
the
scale
.
To
raise
or
lower
the
pole
piece
,
loosen
the
locknut
and
turn
it
up
or
down
and
then
tighten
in
position
.
INDUCTION
UNIT
ADJUSTMENT
Should
it
become
necessary
the
induction
disk
unit
may
be
restored
to
the
factory
calibration
as
follows
:
1
.
Pickup
Setting
-
The
pickup
current
with
no
restraint
current
flowing
should
be
set
to
be
0.48
-
0.52
amps
with
the
operating
coil
set
on
the
12.5
percent
tap
by
adjusting
the
control
spring
.
2
.
Preliminary
Restraint
Adjustment
.
Using
test
connections
similar
to
figure
7
but
with
jumpers
removed
energize
one
restraint
coil
at
a
time
and
adjust
the
slide
band
resistors
in
the
back
of
the
case
.
Do
not
change
control
spring
setting
.
With
relay
on
12.5
%
tap
,
adjust
as
follows
:
Set
10
amps
through
studs
6
and
7
and
adjust
bottom
resistor
until
contacts
just
close
with
1.0
amps
in
studs
2
-
3
.
Set
10
amps
through
studs
8
and
9
and
adjust
middle
resistor
until
contacts
just
close
with
1.0
amps
in
studs
2
-
3
.
Set
10
amps
through
studs
16
and
17
and
adjust
tap
resistor
until
contacts
just
close
with
1.0
amps
in
studs
2
-
3
.
3
.
Restraint
Test
Using
test
connections
similar
to
those
shown
in
Figure
7
except
with
jumpers
installed
tying
studs
6
,
8
and
16
together
instead
of
the
jumpers
shown
in
Figure
7
,
test
the
restraint
coils
in
pairs
as
follows
.
Relay
set
ON
tap
indicated
in
table
below
check
combinations
of
restraint
coils
per
table
below
.
Do
not
change
control
spring
setting
.
10
Courtesy of NationalSwitchgear.com

GEK
-
34069
RESTRAINT
COILS
CONNECT
TO
STUDS
NUMBERS
A
1
A
2
AO
Both
Upper
Upper
left
,
Lower
right
Upper
right
,
lower
left
Check
IFD
51
D
relays
to
the
following
limits
and
adjust
resistors
as
needed
.
9
17
2
-
3
7
17
2
-
3
7
2
-
3
9
PERCENT
SLOPE
12.5
%
25
%
*
R
I
I
OP
OP
0.49
-
0.51
1.25
-
1.35
2.5
-
2.65
4.5
-
5.30
0
10
2.30
-
2.60
4.5
-
5.5
20
8
-
11
40
When
the
adjustments
have
been
restored
per
3
above
,
the
relay
should
pass
the
three
restraint
test
given
under
Acceptance
Tests
.
RENEWAL
PARTS
It
is
recommended
that
sufficient
quantities
of
renewal
parts
be
carred
in
stock
to
enable
the
prompt
replacement
of
any
that
are
worn
,
broken
,
or
damaged
.
When
ordering
renewal
parts
,
address
the
nearest
Sales
Office
of
the
General
Electric
Company
,
specify
quantity
required
,
name
of
the
part
wanted
,
and
give
complete
nameplate
data
.
If
possible
,
give
the
General
Electric
requisition
number
on
which
the
relay
was
furnished
.
11
Courtesy of NationalSwitchgear.com

GEK
-
34069
PANEL
LOCATION
SEMI
-
FLUSH
MTG
.
(
4
)
5
/
16
-
18
STUDS
FDR
SURFACE
MTG
.
SURFACE
MTG
.
10
-
32
STUDS
,
6.625
168
MM
\
-
O
19
17
15
13
11
o
o
o
o
o
o
o
o
o
o
20
18
16
14
12
|
C
r
/
:
KD
=
^
15.875
403
MM
STUD
NUMBERING
16.312
414
MM
(
6
)
10
-
32
X
3
/
8
MTG
.
SCREWS
9
7
5
3
1
oo
o o o
o
o
o
o
o
108642
-
10
-
32
STUDS
GLASS
_
i
L
1
.
125
29
MM
.
75
BACK
VIEW
CUTDUT
MAY
REPLACE
DRILLED
HDLES
-
^
"
19
MM
1
/
4
DRILL
6
HDLES
6.187
157
MM
3
.
0
76
MM
6
MM
i
>
ii
1
III
4
HOLE
1
^
G
0
C
30
%
C
30
%
5
/
8
7.875
200
MM
,
000
2
03
MM
5.781
147
MM
I
A
r
4
•
75
I
y
~
^
121
MM
^
t
L
I
9
5
Q
,
(
f
F
%
242
HM
375
~
QQ
~
7
^
~
50
~
\
l
~
.
718
J
/
~
.
250
18
MM
/
|
6
M M
i
-
t
-
i
-
9
CUTbUT
I
f
I
15.75
4
0
0
MM
11.562
294
MM
16.000
406
MM
19
7
.
1
4
1
,
468
37
MM
V
I
J
2.843
72
MM
-
.
500
12
MM
(
TYPICAL
)
.
218
.
218
5.25
5
MM
5
MM
133
MM
5.687
3
/
4
DRILL
20
HDLES
19
MM
PANEL
144
MM
:
JiliTit
PANEL
DRILLING
FDR
SURFACE
MOUNTING
FRONT
VIEW
PANEL
DRILLING
FDR
SEMI
-
FLUSH
MDUNTING
FRDNT
VIEW
CASE
i
5
/
16
-
18
STUD
'
3.0
^
76
MM
VIEW
SHDWING
ASSEMBLY
DF
HARDWARE
FDR
SURFACE
MTG
.
DN
STEEL
PANELS
TYPICAL
DIM
.
INCHES
MM
FIG
.
2
(
K
-
06209274
|
6
]
)
Outline
and
Panel
Drilling
Diagram
for
the
M
2
Case
13
Courtesy of NationalSwitchgear.com

POWER
TRANSFORMER
WYE
CONNECTED
WINDING
(
+
)
1
TS
;
~
n
CD
OP
Q T
CD
w
dL
o
IX
)
4
^
CD
CO
CD
11
CD
CD
i
;
;
o
<
<
52
"
O
o
CD
a
CD
m
m
x
S
S
3
7
*
rt
l
NEUTRAL
RESISTOR
CD
CO
TC
CD
D
=
3
o
QJ
CD
OP
.
INST
.
yV
^
rA
/
V
-
o
CD
l
7
)
O
Z
3
CIRCUIT
BREAKER
xn
ZS
(
D
n
AA
-
AAJ
ri
-
AUX
.
CT
.
IF
REQUIRED
TO
MATCH
CT
RATIOS
X
o
rs
to
o
D
zr
n
>
~
n
>
o
<
'
CD
<
<
REST
.
O
PJ
11
1
QJ
'
<
REST
.
0
8
REST
.
17
16
Courtesy of NationalSwitchgear.com

GEK
-
34069
CONNECTING
PLUG
MAIN
BRUSH
CONNECTING
BLOCK
Ef
Cm
k
I
I
TERMINAL
BLOCK
\
SHORTiNG
BAR
NOTE
AFTER
ENGAGING
AUXILIARY
8
RUSH
,
CONNECTING
PLUG
TRAVELS
1
/
4
INCH
BEFORE
ENGAGING
THE
MAIN
BRUSH
ON
THE
TERMINAL
BLOCK
AUXILIARY
BRUSH
FIG
.
6
(
8025039
)
Cross
Section
Of
Drawout
Case
Showing
Position
Of
Auxiliary
Brush
And
Shorting
Bar
17
Courtesy of NationalSwitchgear.com

GEK
-
34069
115
VOLTS
MIN
AT
RATED
FREQ
.
9
9
RESISTIVE
RESISTIVE
LOAD LOAD
UP
TO
1
CH
-
INO
I
CAT
ING
LIGHT
FOR
A
1
AO
16
3
62
l
±
z
CHECKING
—
SI
PICKUP
0
-
1
O
-
i
-
I
op
<
£
:
SI
<
>
<
r
<
f
EXTERNAL
JUMPERS
A
2
AO
11
o
—
$
^
L
-
O
7
TO
ACCURATELY
REPRODUCE
KLAY
CHARACTERISTICS
ILL
TESTS
SHOULD
BE
MADE
WITH
RELAY
IN
CASE
.
WITH
CASE
.
LEVEL
BLOCK
INSTANTANEOUS
UNIT
(
I
)
CLOSED
FOR
LIGHT
TO
SHOW
INDUCTION
UNIT
PICKUP
TESTING
TWO
RESTRAINTS
AT
A
TIME
,
REMOVE
JUMPERS
SHOWN
AND
TIE
STUDS
6
,
8
,
16
TOGETHER
.
FOR
FIG
.
7
(
0246
A
3653
II
]
)
Test
Connections
for
Model
IFD
51
D
18
Courtesy of NationalSwitchgear.com
This manual suits for next models
2
Table of contents
Other GE Relay manuals
Popular Relay manuals by other brands
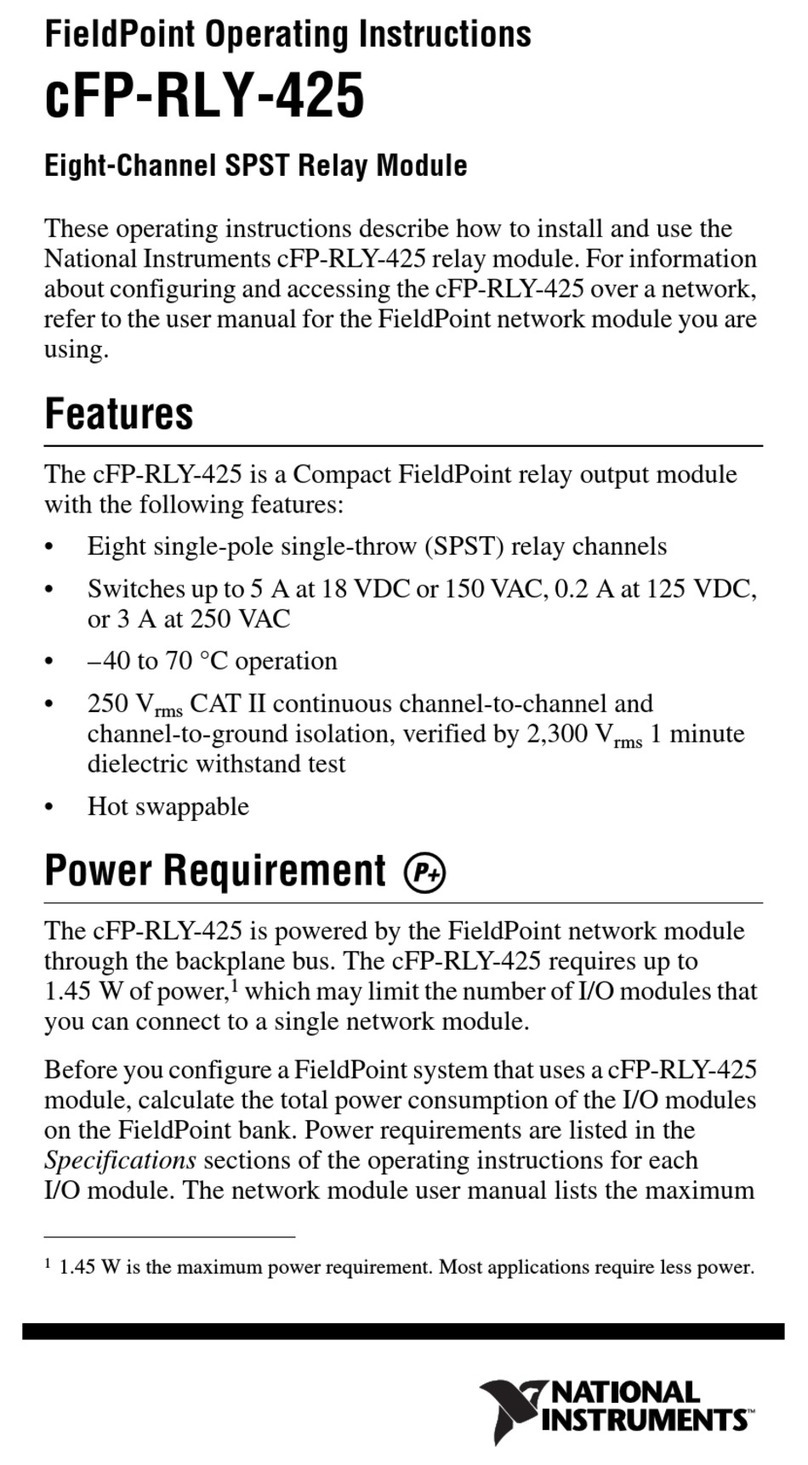
National Instruments
National Instruments FieldPoint cFP-RLY-425 operating instructions
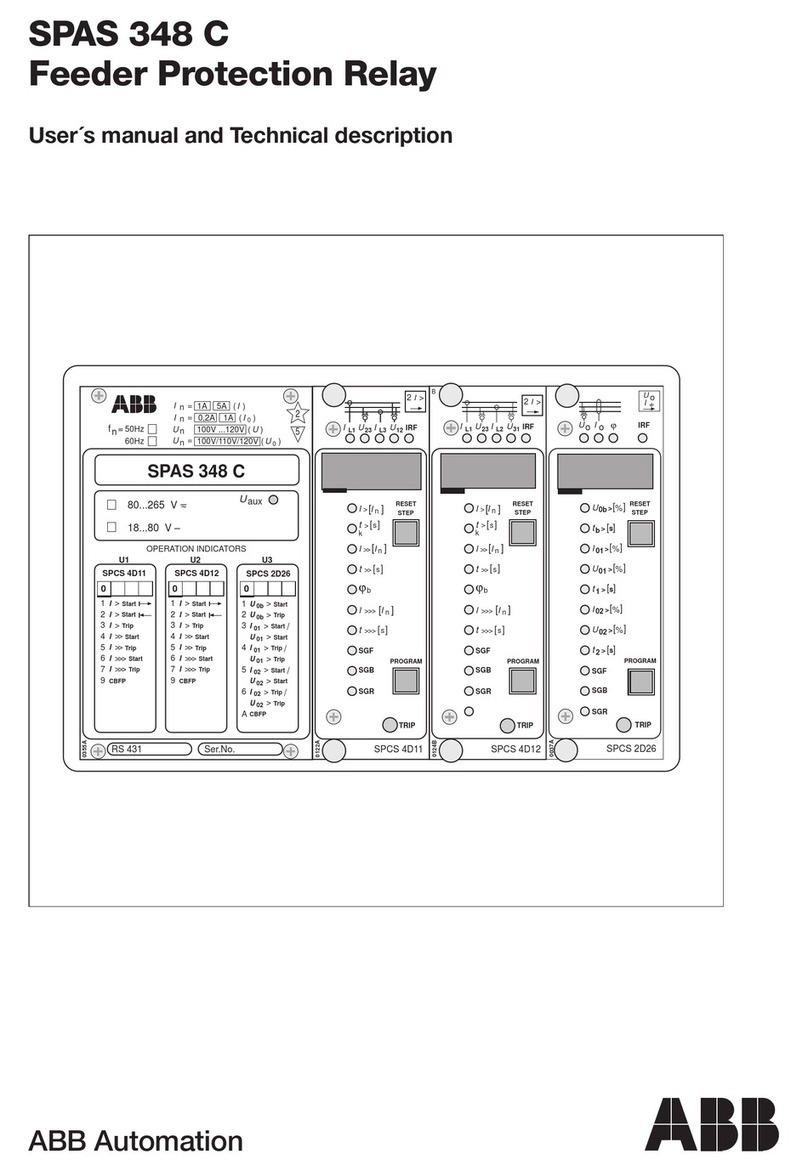
ABB
ABB SPAS 348 C User manual and technical description
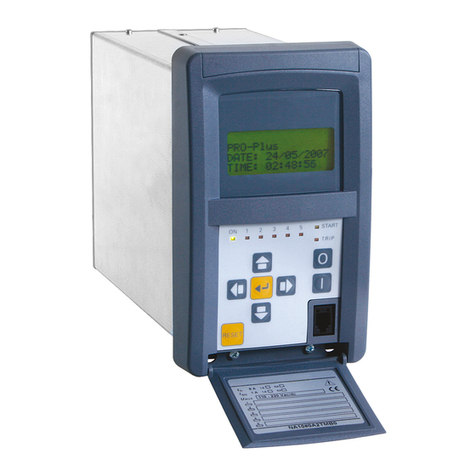
Thytronic
Thytronic NA30 manual

Mitsubishi Electric
Mitsubishi Electric MELPRO-A Series instruction manual

Broyce Control
Broyce Control P9680C quick start guide
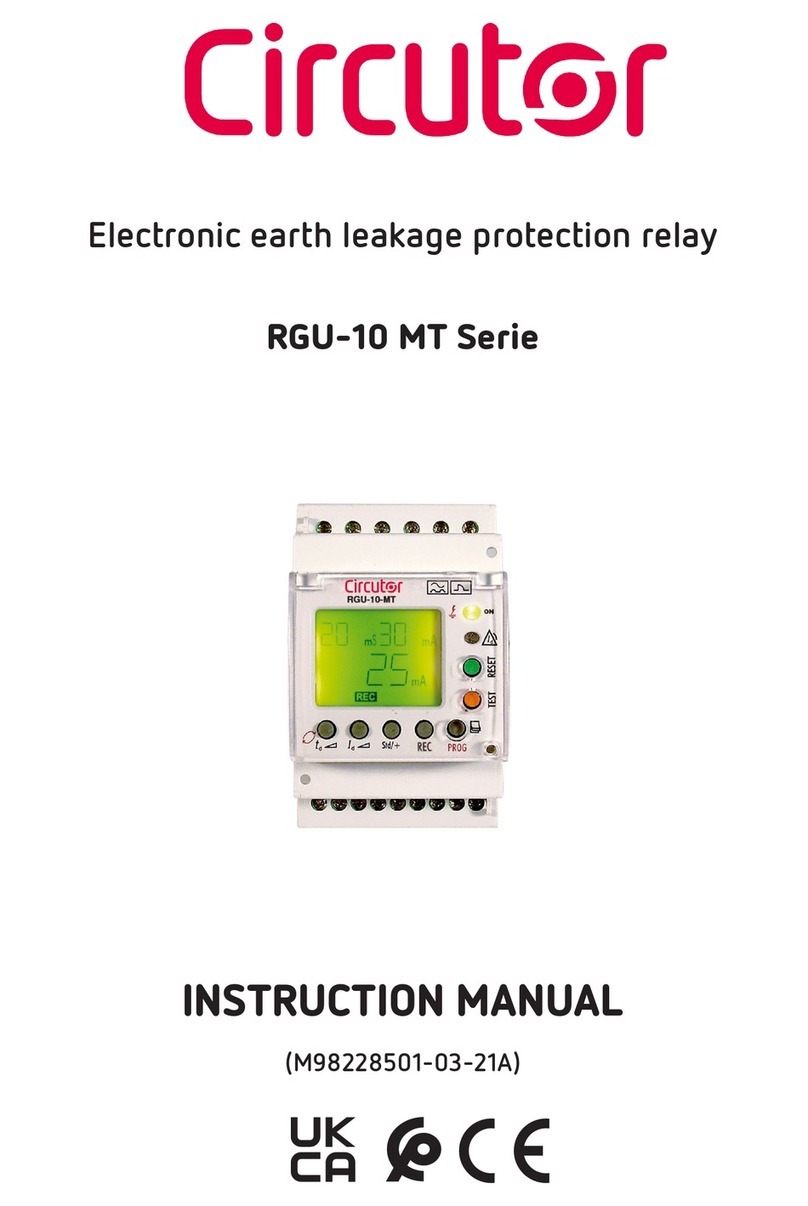
Circutor
Circutor RGU-10 MT instruction manual