Geco G-201-P00 Series Parts list manual

P.P.U.H. „Geco” spółka z o. o.
30-134 Kraków, ul. Zarzecze 112A
tel. +48 (12) 6369811,6361290
fax. +48 (12) 6362002
e-mail: [email protected]
http://www.geco.pl
SERVICE OPERATING MANUAL
FOR INDEPENDENT CONTROL
UNIT
G-201-P00…
VERSION FOR COOLING APPLIANCES
For software version 01,02
You are kindly asked to study instructions carefully before connecting and starting up each of
our appliances. If you have any doubts, please contact us from 8.00 till 16.00. Any remarks
sent to us by e-mail shall be a valuable help.
Notice !!! At the bottom of the following pages the date of the latest updating is given
and at the end of page XVI there is information on the changes in program versions and
the mode of operation that followed.
You are asked to use always the newest version of operating manual which can be received
free of charge by mail after submission of an order.

page 2 SERVICE MANUAL FOR PRODUCERS SBR TYPE G-201-P00
PPUH „GECO” - G-201-P00 01,02 PRINTOUT DATE 05-01-24
I. GENERAL CHARACTERISTICS.
Independent Control Unit called further G-201 is a modern, comfortable and easy to operate
appliance. It was produced using microprocessor technology and automatic surface assembly.
G-201 was provided with two temperature sensors and two outlets which allow to connect it
directly to appliances operating under voltage 230 V with load capacity as stated in table 1.
G-201 stabilises temperature and controls automatic defrosting whose period can be adjusted to
specific conditions of the environment and has also a button for manual defrosting of the evaporator.
This thermostat does not require special maintenance; the keyboard was made from a special type
of foil resistant to high temperature and most chemicals. It is not permitted to clean it with sharp objects.
It is sufficient to clean the front plate with a wet cloth from time to time.
II. METHOD OF MARKING AND TECHNICAL DATA
Model: G- 201 –P 00K X X – M XX00 0
Position: 1 2 3 4 5 6 7 8 9 10 11 12
1- ‘Geco’ thermostat.
2- Use in: refrigeration
3- Casing: 01 –minipanel
4- The beginning of symbols related to panel configuration (keyboard).
5- Version 00.
6- Temperature setting from: К- keyboard.
7- Light button: L – yes, 0 – no.
8- Sound signalling: В– yes, 0 – no
9- The beginning of symbols related to performing module configuration.
10- What transformers are installed. Detailed description below.
11- In this thermostat the option is not available.
12- In this thermostat the option is not available.
Additional information on marking of transformers.
Digits mean that there is a transformer, 0- no transformer:
1 – compressor transformer - H – high-voltage version
2 – light, ventilator or heater or valve transformer (version 02)
Examples of marks:
•M10000 – compressor
•MH0000 – compressor with higher power
•M12000 – compressor and ventilator
•M12000 – compressor and heater
•M12000 – compressor, light
Working voltage - 230V +10% -15%
Air temperature - from +5°C to +40°C
humidity - from 20% to 80% RH
Protection level - IP65 on the front side of the control panel
Table 1:Marking of transformers and carrying capacity of outlets
current-carrying capacity
outlet Ia Ib P

Page 3
version G-201-P00Kxx-M1x000
P1 – compressor R16A 6A
cos φ> 0,85 1HP 750W
P2 – Universal R16A 4A - 800W
version G-201-P00K0x-MH0000
P1 – compressor R30A 12A
cos φ> 0,85 2HP 1500W
Ia – transformer rated current.
Ib – load rated current
P – load rated power.
Notice !!!
•Total power consumed at once by appliances may not exceed 10A !!!
III. HOW TO ORDER
In the order you have to give the full name of the controller in accordance with the marking defined in
item II and the length of temperature sensors.
The following types of thermostats are available:
G - 201 –P00K00 – M1000 0
Thermostat that controls operation of the compressor
G - 201 –P00KL0 – M1200 0
Thermostat that controls operation of the compressor and lighting
G - 201 –P00K00 – M1200 0
Thermostat that controls operation of the compressor and of an additional appliance (a ventilator,
a heater or a valve (version 02))
G - 201 –P00K0B – M1000 0
Thermostat that controls operation of the compressor, provided with sound signalling
G - 201 –P00KLB – M1200 0
Thermostat that controls operation of the compressor and lighting, provided with sound
signalling
G - 201 –P00K0B – M1200 0
Thermostat that controls operation of the compressor and an additional appliance (a ventilator, a
heater or a valve (version 02)), provided with sound signalling
G - 201 –P00K00 – MH000 0
Thermostat that controls operation of the compressor with higher power
G - 201 –P00K0B – MH000 0
Thermostat that controls operation of the compressor with higher power, provided with sound signalling

page 4 SERVICE MANUAL FOR PRODUCERS SBR TYPE G-201-P00
PPUH „GECO” - G-201-P00 01,02 PRINTOUT DATE 05-01-24
IV. INSTALLATION AND CONNECTION OF G-201
1. Cut a hole with dimensions 28x70 mm in the appliance in the place marked accordingly.
2. All metal elements through which G-201 or its cables are put should be filed or protected
otherwise. I is not permitted to fix G-201 in a way which allows direct contact with water (e.g.
condensing water on the lower cover of the display), touching of evaporator outlet pipe etc. and
causes considerable changes of its temperature in comparison with air temperature (e.g. fixing
in direct vicinity of the compressor and its accessories, cooling and heated elements).
3. When G-201 is fixed, power cables should be connected in accordance with the description on
the casing. Depending on the version of G-201 some outlets may be out of use: they will not be
described on the label with description and in type description there will be ‘0’ digit: one may
not connect any cables to those outlets!!!
4. Connectors have certification for permanent load 16A !!! They are provided with fine thread and
special plates preventing cutting of cables, therefore, when lightly screwed together they will
have maximally good contact and if more force is applied, it may damage the thread. In result
the socket may be melted and there might be a short circuit!!!
5. The whole unnecessary length of cables is shortened by cutting or winding and clipping together
by special plastic bands. Cable have to be well-fastened along their whole length and may not
touch the compressor and its accessories.
6. When the appliance is connected to mains, there might be voltage in light cable regardless
whether it is switched on or off with the button therefore, the starter or the fluorescent
lamp may be replaced only when the power cable is unplugged from the socket!!!
THE SAME CONDITION IS VALID FOR ANY OTHER REPAIRS!!!
8. If there are heaters, their voltage has to be chosen in such a way that if there is a breakdown of G-
201 or of an external contactor and they are switched off permanently, there will be no
possibility of fire or destruction of the appliance. If high power heaters are used, safety
thermostat must be used on the evaporator unconditionally. This thermostat should operate on a
different basis, e.g. a mechanical thermostat.

Page 5
V. INSTALLATION OF SENSORS.
1. For every type of the cooling unit the place of fixing of chamber and evaporator sensor and setting
of system parameters G-201 should be chosen through experimentation. It is absolutely forbidden
to change the location or the method of fixing of sensors and settings of G-201 without doing new
tests related to temperature stabilisation and to the course of defrosting of the unit!!!
2. The chamber sensor must be fixed in such a way that it does not touch foods and is not exposed to
damage during cleaning of the unit. A special plastic handle can be used to fix this sensor. Such
solution causes quick (time delay on/off see V, item 4) the reaction of the sensor and of the whole
thermostat to a change of air temperature in the unit. If it is recommended or necessary to slow
down and ‘smooth out’ reaction time of the sensor to temperature changes, it is advisable to screw it
to a metal element of the unit.
3. Evaporator sensor should be fixed in the way which assures maximally good and sure contact with
the evaporator slat and in the place where ice keeps longest during defrosting. Its fixing should
prevent its pushing out by growing ice. If possible, sensors should be fixed vertically so that the
cable goes out of a sensor at its bottom.
4. Sensor cables can be shortened or lengthened in any way according to the following rules:
-Cable sensor should not be cut at a distance below 0.5 m from the shell
-It is not recommended to lengthen sensor cable above 20 m.
-SENSOR CABLES CAN BE CONNECTED TO SENSOR CLAMPS IN THE OPERATING
UNIT IN ANY WAY!!!
(similarly to the method of plugging of the plug in the socket ~230V)
-cable OMY 2x0.5 mm is recommended for cable lengthening,
-if cables are lengthened their connection should be done very carefully, every pair of veins
should be soldered and heat-shrinking sheaths should be put on them. Then the place of
connection should be filled with water-resistant silicone and one more heat-shrinking sheath
should be put on..
-endings of cable connected to the independent control unit should be tinned.

page 6 SERVICE MANUAL FOR PRODUCERS SBR TYPE G-201-P00
PPUH „GECO” - G-201-P00 01,02 PRINTOUT DATE 05-01-24
VI. OPERATION METHOD
A - General information
1. Start after connection to mains
When the unit is connected to mains a 3-second start procedure takes place during which two dots
appear on the display for a second, controller program version appears for another second and then
two dots appear again. At that time none of controlled units is switched on.
If the unit was on when power was disconnected, at the end of start procedure it will be on and the
value of temperature in chamber sensor appears on the display.
If it was off, two horizontal lines will appear on the display.
2. Functions of buttons
- When pressed, thermostat is switched on/ off. When it is off, two horizontal lines appear on
the display.
- When pressed, light is switched on/ off. This is signalled by a green diode at the button.
Button works independently from thermostat switch - .
- Used for manual defrosting.
- used to program settings and to end programming.
- used to increase temperature set during programming and to switch on monitoring of
evaporator temperature.
- used to decrease temperature set during programming and to switch on monitoring of chamber
temperature during defrosting.
If G-201 was provided with sound signalling, pressing of any button is signalled by a short sound.
3. Programming of temperature:
When is pressed, programming mode begins, the value of a parameter appears on the display and
a diode at the button switches on.
When are pressed, the value of a parameter changes within the range ‘d0’ – ‘d1’.
When is pressed, settings are memorised and normal operation of the controller follows.
If G201 is switched off during programming, it will not memorise the new value of temperature.
4. Signalling of compressor operation
When the compressor is on, small red diode (dot) in the right bottom corner of temperature display is
on. This facilitates checking of possible defects of the system.
If the compressor should be switched on and it is not because one of protections has been switched
on (see item 5), the dot which signals operation of the compressor will flash. When the set time of
protection ends, the dot will be lit permanently and the compressor will be switched on.
5. Compressor protection
•A delay in switching on of the compressor when the temperature at which it should be on is
reached (temperature set by the user minus the lower value of hysteresis) is 30 seconds. If during
that time temperature falls, condition of excess of 30 seconds is checked again. This is to protect
the compressor against unneeded switching on caused by e.g. placement of goods, drafts, etc.
•From the moment when the compressor is switched off for time defined by parameter ‘c2’, G-201
will prevent compressor from switching on.

Page 7
•After every break in electricity supply or voltage fall below 175V, G-201 will prevent compressor
from switching on for time defined by parameter ‘c2’. However, if ‘c2’=0min, protection will last
60 seconds.
•When the unit is connected by the button there is a 5-seconds delay before the compressor is
switched on. It should be emphasised that in this way all other protections are cancelled. Thanks
to that, operation of the compressor can be checked quicker.
6. Alarms of sensors – A1 and A2
The controller is provided with alarms which inform of defects of sensors. A defect of a sensor is
signalled by appearance of a corresponding symbol on the display.
A1 – damage of chamber temperature sensor. G-201 will connect the compressor in a time cycle (so
called: clock control) according to time defined in parameters ‘c8’ and ‘c9’. Defrosting will function
normally.
A2 – damage of evaporator sensor. Manual and automatic defrosting is blocked !!! The unit may
be defrosted only when it is switched off by the button and ice melts down in time.
Breakdown of two sensors simultaneously – only symbol A1 is displayed. When chamber sensor
is repaired, A2 will appear.
7. Overheating alarm - A4: refers to program version 02
If temperature in the chamber is higher than the parameter D6, alarm A4 and temperature appear on
the display alternately and a sound alarm is generated (if G-201 is provided with sound signalling).
When any button is pressed, the sound alarm stops.
8. Temperature monitoring
When is pressed for 0.5 second, the display will begin to flash and show evaporator temperature,
after the following 5 seconds G-201 will show chamber temperature again. Notice!!! This function
works also during defrosting when ‘dF’ appears on the display. Chamber sensor temperature can be
seen also when is pressed for 0.5 second, the display will show (without flashing) chamber
temperature, after the following 5 seconds ‘dF’ will be displayed again.
B - Defrosting
1. If additional defrosting is necessary in result of difficult conditions of operation, the button
should be pressed. Then the green diode will light permanently on the button and ‘dF’ will appear
on the display instead of measurement of temperature. This moment the unit will begin a defrosting
cycle.
2. If defrosting takes place and temperature on evaporator is higher than temperature set in parameter
‘d2’, after about 10 seconds the unit will begin the end phase of defrosting and after its end it will
start further operation.
If defrosting takes place and temperature on evaporator is lower than temperature set in parameter
‘d2’, G202 will switch on defrosting and when temperature in parameter ‘d2’ is reached, the
procedure of the end of defrosting will begin (signalled by a flash of the green diode on the button
) consisting of one dripping phase in which the compressor is off for time defined by parameter
‘c3’.
3. Defrosting will end when evaporator will reach temperature set in parameter ‘d2’ or when time set
in parameter ‘c1’ is exceeded.
4. When ‘dF’ disappears and defrosting is finished, the display shows the temperature that was
memorised just before the beginning of defrosting for the whole time defined in parameter ‘c7’: this
is to prevent complaints because of ‘sudden changes of temperature in the unit’.

page 8 SERVICE MANUAL FOR PRODUCERS SBR TYPE G-201-P00
PPUH „GECO” - G-201-P00 01,02 PRINTOUT DATE 05-01-24
5. The unit functions in the same way during manual and automatic defrosting.
C - Hysteresis
During programming of the parameter ‘d0’ and ‘d1’ (minimal and maximal temperature which can be
set by the client) one should remember that the value of hysteresis ‘d3’ causes additional lowering or
increasing of temperature beyond the temperature sent by the user.
This is particularly important for units with plus temperatures, which should always operate above 0ºC.
Example:
As a producer of cooling equipment, e.g. of a refrigerated display case (plus temperatures) I demand
that the unit allow operation within the range of values given below: off – min: 2ºC, on - max: 10ºC.
symmetrical hysteresis for even
values of‘d3’
asymmetrical hysteresis for odd
values ‘d3’
example 1.
Hysteresis of ‘d3’ is set as 2ºC
For the above setting of the hysteresis the
parameter ‘d0’ should be set as 3ºC and ‘d1’ as
9ºC
example 3.
Hysteresis of ‘d3’ is set as 3ºC
For the above setting of the hysteresis the
parameter ‘d0’ should be set as 3ºC and ‘d1’ as
8ºC
example 2.
Hysteresis of ‘d3’ is set as 4ºC
For the above setting of the hysteresis the
parameter ‘d0’ should be set as 4ºC and ‘d1’ as
8ºC
example 4.
Hysteresis of ‘d3’ is set as 5ºC
For the above setting of the hysteresis the
parameter ‘d0’ should be set as 4ºC and ‘d1’ as
7ºC
On
Temperature set
by the user
‘
d3
’
Off
‘
d3
½
‘d3’+0.5ºC
½
‘
d3
’-
½
‘
d3
’
½
‘d3’

Page 9
VII. CHARTS WHICH PRESENT OPERATION OF PARTICULAR
ELEMENTS OF THE UNIT
Thick line means that the unit is on and interrupted line means that the unit is off.
The square ‘stop’ means that the compressor is off and ‘operation’ that it is on because programmed
temperature has been exceeded, taking into account the value of programmed hysteresis parameter ‘d3’.
AN ERROR IN THE SETUP OF PARAMERS WILL CAUSE WRONG OPERATION OF THE UNIT!!!
1. ventilator which operates together with compressor ‘r1’=01
t=0 (c3 of no importance)
CO M PRE SSO R
VENTILATOR
stop operation D EFR O ST IN G E N D O F D E FRO ST IN G operation stop
2. ventilator which operates all the time ‘r1’=02, t=0 (c3 of no importance)
C O M PR E SSO R
V E N T IL A T O R
stop operation D E FR O ST IN G EN D O F D E FR O ST IN G operation stop
3. evaporator heater ‘r1’=03,
t=c3
C O M PR E SSO R
H E A T E R
stop operation D E FR O ST IN G E N D O F D E FR O ST IN G operation stop
4. tray heater ‘r1’=04, t= c3
C O M PR E SSO R
TRAY HEATER
stop operation D EFR O ST IN G EN D O F D E FR O ST IN G operation stop
5. valve ‘r1’=05, t=c3
C O M PR E SSO R
V A LV E
stop operation D EFR O ST IN G E N D O F D EFR O ST IN G operation stop
ª

page 10 SERVICE MANUAL FOR PRODUCERS SBR TYPE G-201-P00
PPUH „GECO” - G-201-P00 01,02 PRINTOUT DATE 05-01-24
VIII. PROGRAMMING OF SYSTEM PARAMETERS
When the unit is on and correctness of its operation has been checked (factory settings are standard
settings), setting of system parameters of G 201 begins.
In order to do that, the unit must be switched off with the button . Then buttons and
must be pressed and when they are being pressed, the button must be pressed. All three buttons
must be pressed together for 3 seconds. If any of the buttons is released at that time, programming will
be interrupted. When this activity is done, diodes on buttons and
will flash and symbol ‘c0’ will appear on the display for 1 second. Then the latest programmed value of
the parameter will appear. Now, using buttons the new values should be set; every longer
pressing of the button will cause quick winding of possible settings. Then should be pressed to
accept the set data and start programming of a new parameter.
It is possible to change some settings only; if you do not want to change a given parameter, press
and G201 will move to the next parameter.
Notice !!!
Producer of cooling equipment can block access to some or to all parameters of the
keyboard using a computer programmer. If so, when an attempt to change settings of a
blocked parameter is made, the symbol ‘bL’ will appear on the display for about 1
second.

Page 11
Table 2: Significance of parameters
Parameter description Min Max step factory
setting
c0 how often defrosting will take place
00 – there will be no automatic defrosting, only manual defrosting!!!
-01 there will be no automatic or manual defrosting!!!
-01 24 1h 6h
c1 Maximal time of defrosting, if the evaporator does not reach set
temperature (parameter d2) Note!!! If this parameter is set as ‘-01’
there will be no time limits
-01 99 1min 30min
c2 minimal time of compressor stoppage 0 15 1min 3min
c3 time of evaporator dripping 0 15 1min 2min
c5 Maximal time of operation of compressor
0 – no testing (this parameter is off)
0 99 1min 40min
c6 Time of compressor stoppage after switching on of protection from
parameter ‘c5’
0 99 1min 10min
c7 Time during which after the end of defrosting (parameter ‘c4’)
temperature measured just before the beginning of defrosting will be
displayed
0 60 1min 5min
c8 Compressor operation time with damage of control sensor 1 99 1min 25min
c9 Compressor stoppage time with damage of control sensor 1 60 1min 5min
d0 Minimal temperature for a client to set -40 20 1°C 1°C
d1 Maximal temperature for a client to set d0+1 40 1°C 10°C
d2 Evaporator temperature at which defrosting will stop 0 40 1°C 5°C
d3 Value of hysteresis 1 10 1°C 2°C
d4 Value of rescaling of chamber sensor in comparison with actually
measured temperature
-10 10 1°C 0°C
d6 Temperature in the chamber whose exceeding makes alarm A4
switch on.
only software version 02
-40 40 1°C 40°C
r0 Type of temperature sensor:
00 – NTC 2,2k
01 – NTC 10k
only software version 02
00 01 1 00
r1 Unit connected to other transformer:
00 – lighting
01 – ventilator operating with compressor
02 – ventilator operating all the time
03 – evaporator heater
04 – tray heater
and from software version 02
05 – valve
06 – compressor transformer with more power - ! equipment
replacement required ! ref. to G-201-P00K0x-MH0000
00 04 1 00
r5 Conditions of switching on of defrosting when the unit is switched
on:
00 – beginning of operation without defrosting
01 – if during defrosting power supply is disconnected, defrosting
will be switched on
02 – defrosting after every switching on of unit power supply
00 02 1 00

page 12 SERVICE MANUAL FOR PRODUCERS SBR TYPE G-201-P00
PPUH „GECO” - G-201-P00 01,02 PRINTOUT DATE 05-01-24
IX. PROBLEMS AND THEIR REMOVAL
defect symptoms check
1. Display is not lit
although G-201 is
connected to mains
Check:
- if there is voltage 220V on feeding clamps L and N
2. Compressor
does not switch on
although it is
signalled that it is
on: red diode
Check:
- if there is voltage 220V on clamps P2 and N – If there is voltage,
check the compressor
3. Defrosting heater
does not switch on Check:
- if there is voltage 220V on clamps as described on the casing of the
controller
- if there is, check the heater
4. Error of
temperature
indication
Check:
- connection of sensors to connectors
- the value of parameter ‘d4’
- the value of parameter ‘r0’
- if the sensor is fixed correctly
- the condition of the cable of the sensor: the cable can not have any
defects
- in detail the lookout of external surface of sensor shell to see whether
it has not been damaged mechanically.
5. impossible to set
the required
temperature
Check:
the value of parameters ‘d0’ and ‘d1’ (d0<d1)
6. dots on the
display flash, no
possibility to switch
it on
Check :
- the value of feeding voltage
- condition of feeding connectors
- whether feeding connectors are tightened up
7. ‘’abnormal’
‘strange’ operation
of the unit
Check:
- if there is voltage 230V on feeding clamps L and N
- condition of feeding connectors
- ‘zeroing’ of cooling unit
- condition of electric system and the number of units connected to
one phase
- if the type of thermostat is right (label with description of outlets) for
the unit
- whether the thermostat was not wetted by water or other liquid
- if thermostat is not exposed to humidity or sudden changes of
temperature

Page 13
8. Problems with
defrosting of the
appliance
Check:
- the value of parameters ‘d2’ and ‘c0’, ‘c1’
- the value of parameter ‘c1’. This is the maximal time of defrosting
of the appliance regardless whether the evaporator reached
programmed temperature of the end of defrosting or not (parameter
‘d2’). If this time is too short, the appliance will not defrost fully
- correct fixing of the sensor to the evaporator slats.
IT MUST BE FIXED FIRMLY AND ADHERE TO THE SLATS!!!
- is the evaporator sensor fixed in the place where ice stays the
longest? If not, check the temperature on the sensor at the moment
when last pieces of ice fall from the evaporator. THIS
TEMPERATURE SHOULD BE DEFINED THEN AS PARAMETER
‘d2’
9. The appliance
does not reach the
set temperature
and does not cool
Check:
- what temperature was programmed by the user
- set values of particular parameters, in particular ‘c2’, ‘c5’, ‘d0’, ‘d1’
- item 9 – Problems with defrosting of the unit. If the unit does not
defrost itself fully, it won’t reach the programmed temperature!!!
- the method and place of fixing of the chamber sensor
- whether side panes were not uninstalled from the rack or whether
moving panes were not uninstalled from the display
- WHETHER THE UNIT STANDS IN A DRAFT OR IN SUNLIGHT!!!
- whether ventilators or air conditioning are installed on the ceiling or
nearby - cleanliness of the condenser
- temperature in the shop (each producer defines maximal operating
temperature of an appliance)
- the quantity of gas, ventilators, evaporator heater, hose that carries
away water from the evaporator

page 14 SERVICE MANUAL FOR PRODUCERS SBR TYPE G-201-P00
PPUH „GECO” - G-201-P00 01,02 PRINTOUT DATE 05-01-24
X. RETURNS FOR REPAIR
If there is a breakdown and G-201 is returned for a repair, it is required
unconditionally that the replacement form whose sample is enclosed at the end of
the manual be filled in completely. It is recommended not cut out the form but to
photocopy it.
PPUH ‘GECO’ reserves the right to refuse a free repair of the unit, if
there is no form, the form is not filled in completely or the seals are
broken !!!
P.P.U.H. ‘Geco’ Sp. z o. o. is not responsible for loses and damages resulting
from provision of information on the method of making changes in the system
data of G-201 by the producer or its service to the final client, incorrect or
non-professional assembly and for loses caused by defective operation of the
appliance.
XI. CHANGES IN THE CONTROL
17.06.2004: introduction of version 2of the control. Added parameters:
- D6: overheating alarm,
- R0: operation of 2 types of temperature sensors
- R1 expanded: operation of the valve and higher power transformer.

Page 15
Un = 230V 50Hz Imax = 10A
P2 - KOMPRESOR 8A 2HP 1500W
P-P Czujnik PAROWNIKA - SZARY
K-K Czujnik KOMORY - BIAŁY
PPUH GECO Sp. z o.o.
30-134 Kraków ul. Zarzecze 112A
tel. +48 (12) 6369811 fax 6362002
www.geco.pl e-mail:geco@geco.pl
WIDOK Z GÓRY
WIDOK Z PRZODU
G-201-P00K00-M1000
Un = 230V 50Hz Imax = 10A
P1 - ŚWIAŁO 2A 750W
P2 - KOMPRESOR 8A 2HP 1500W
P-P Czujnik PAROWNIKA - SZARY
K-K Czujnik KOMORY - BIAŁY
PPUH GECO Sp. z o.o.
30-134 Kraków ul. Zarzecze 112A
tel. +48 (12) 6369811 fax 6362002
www.geco.pl e-mail:geco@geco.pl
WIDOK Z GÓRY
WIDOK Z PRZODU
G-201-P00KL0-M1200

page 16 SERVICE MANUAL FOR PRODUCERS SBR TYPE G-201-P00
PPUH „GECO” - G-201-P00 01,02 PRINTOUT DATE 05-01-24
widok z góry: view from above
w. z przodu: front view
czujnik komory: chamber sensor
cz. Parownika: evaporator sensor

Page 17
XII. OPERATION OF G-201: FOR USERS
1. When the unit is connected to mains, two dots will appear on the display for a second, then the
version of unit software and dots for another second. Then, on middle segments of the display two
horizontal lines which signal connection to mains appear. The unit is started when the button
is pressed. The value of temperature in the unit appears on the display (temperature reading from
the chamber sensor).
2. Setting a defined temperature .
When is pressed, programming is begun, the value of set temperature appears and a diode
appears at the button .
When are pressed, the set value can be changed within the range programmed by the
producer of the cooling unit.
When is pressed, newly set value will be memorised and the controller will return to its normal
operation.
If G201 is switched off during programming, it won’t memorise the new setting.
3. Switching on/off of lighting.
Pressing of the button causes switching on/ off of the light. It is signalled by a green diode at the
button. The button works independently of the thermostat switch - .
4. Switching on of manual defrosting.
Defrosting is switched on manually when the button is pressed. Then a green diode is switched
on on the button; the ‘dF’ symbol appears on the display.
Defrosting will end automatically after the required time or when the required temperature
programmed by the producer of cooling equipment is reached.
5. Alarms.
If one of the symbols below appears on the display:
A1
A2
it means a breakdown of the control and service should be called.
If the symbol
A4
is displayed alternately with temperature it means that the unit has too high temperature and it
should be checked what is the reason of the alarm (open door, sunlight) and the condition of
products should be checked.
If repairs are done on one’s own, guarantee will be lost and it might cause electric shock
and other dangers. Therefore, all repairs should be done by trained and authorised service
personnel!!!!

page 18 SERVICE MANUAL FOR PRODUCERS SBR TYPE G-201-P00
PPUH „GECO” - G-201-P00 01,02 PRINTOUT DATE 05-01-24

Page 19
SERVICE STAMP INDEPENDENT CONTROL UNIT
REPLACEMENT FORM
FIRST NAME AND SURNAME OF SERVICE
PERSON:
DATE OF REPLACEMENT:
INDEPENDENT CONTROL UNIT DATA:
damaged: PANEL MODEL
SERIES NUMBER:
TYPE: G-
COOLING UNIT DATA:
PRODUCER:
TYPE: COMPRESSOR TYPE:
SERIES NUMBER:
PRODUCTION DATE:
DETAILED DESCRIPTION OF DEFECT OF INDEPENDENT CONTROL UNIT:
DESCRIPTION OF COOLING UNIT DEFECT:
DAMAGED: COMPRESSOR VENTILATIR HEATERS LIGHT NO GAS/ EXCESSIVE GAS
ATMOSHERIC DISCHARGE SYSTEM
VOLTAGE
ELECTRICITY CUT OFF
VOLTAGE DROPS
DAMAGED ELECTRIC SYSTEM
NO ‘ZEROING’
SERVICE PERSON SIGNATURE:
Table of contents
Other Geco Control Unit manuals
Popular Control Unit manuals by other brands
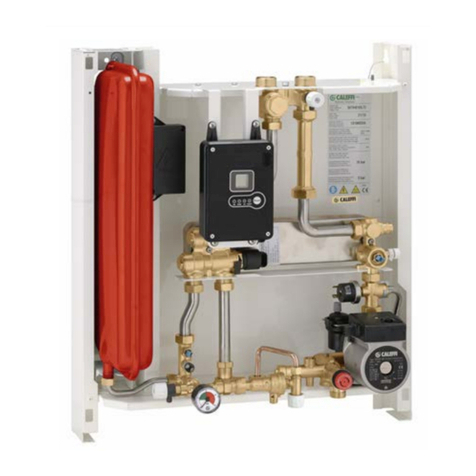
CALEFFI
CALEFFI SATK40 Series INSTRUCTIONS FOR INSTALLATION, COMMISSIONING AND MAINTENANCE
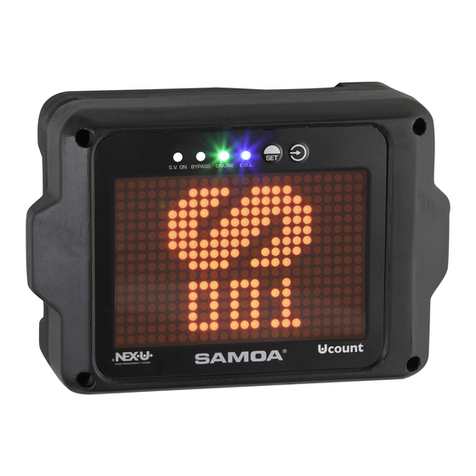
Samoa
Samoa 383750 Parts and technical service guide

GEM
GEM R693 Installation, operating and maintenance instructions
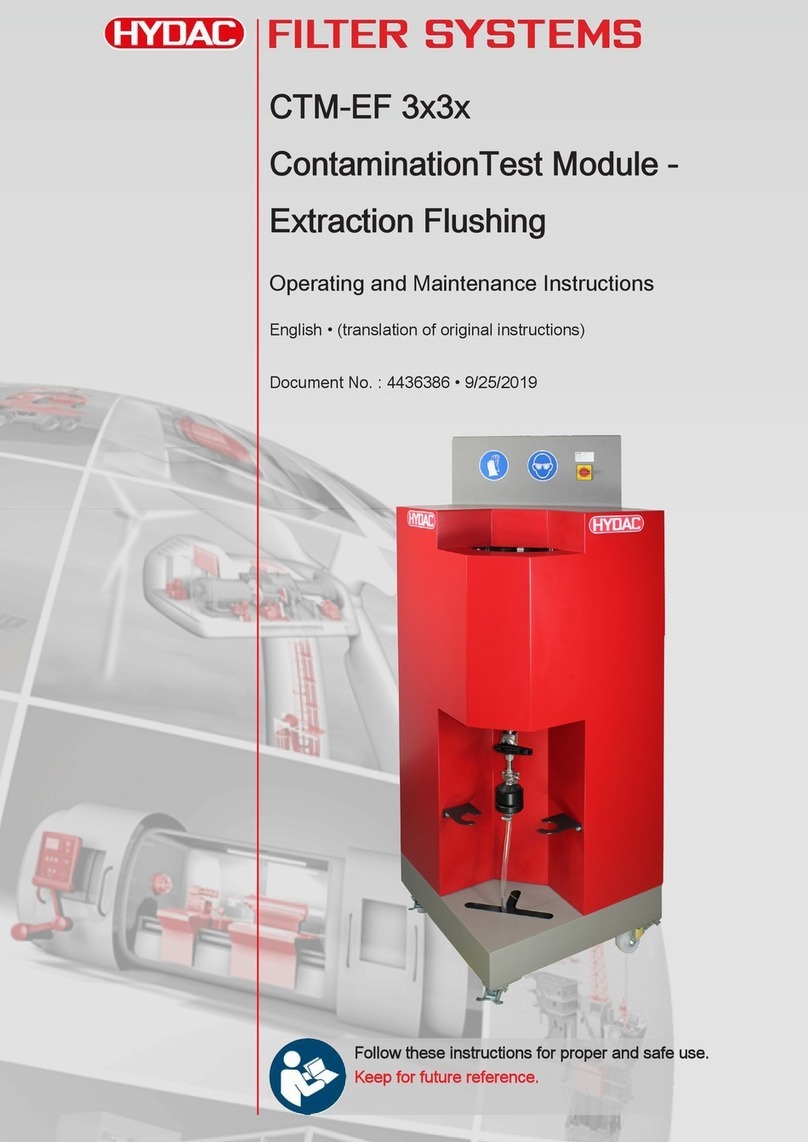
HYDAC FILTER SYSTEMS
HYDAC FILTER SYSTEMS CTM-EF 3 3 Series Operating and maintenance instructions

emmeti
emmeti T3 Installation and commissioning instructions
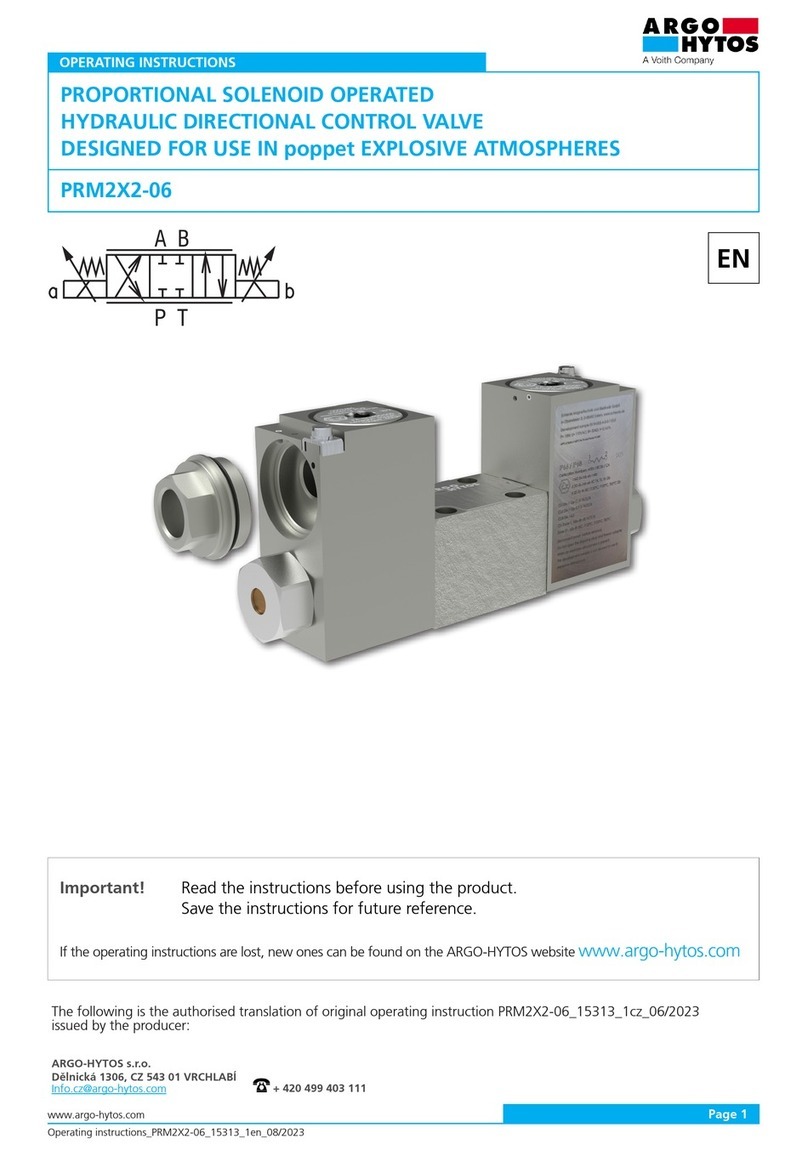
Volth
Volth ARGO HYTOS PRM2X2-06 operating instructions