Graco Horizon Fluid Management Systems User manual

Important Safety Instructions.
Read all warnings and instructions in this manual.
Save these instructions.
Instructions
FLUID MANAGEMENT SYSTEMS
Used for bulk dispensing of petroleum and synthetic- based oils and antifreeze
to multiple service bays.
NOTE: These instructions are for software version 1.05
308607J
EN
t

2 308607
Table of Contents
Terms 3........................................
Symbols 4......................................
Warning 4......................................
Symboles 5.....................................
Attention 5.....................................
Pre-installation Checklist 6......................
Installation Checklist 8..........................
Hardware Installation 8........................
Cable Routing and Connection 8...............
System Startup 9.............................
Test the System 9............................
Hardware Installation 10.........................
Flush System 10.............................
Install Solenoids and Meters 10................
Set Control Module Addresses
and Label Boxes 10.......................
Change 110 VAC to 220 VAC 11................
Mount Control Module
and Keypad Bracket 13....................
Cable Routing and Connection 14................
Connect AC Electrical Power 14................
Route Solenoid and Meter Cables 15............
Connect Solenoid and Meter 15................
Connect Control Modules to CAN 16............
Connect Keypad Cable 17.....................
Connect Printer or Computer 17................
Visually Check Wire Connections 17............
System Setup
-- S t a r t u p 19....................................
Startup Screen 19............................
Mode Selection (HOME) 19....................
Enter Password 19...........................
Types of Setup 20............................
-- Enable/Disable CAN Option 22.................
-- Modify or New Setup Options 22................
NOTE: Setup instructions for individual options
begins on page 29, with Time and Date Setup.
-- Clear Setup Options 23........................
-- Print Setup Options 24.........................
-- Update Tables Options 25......................
-- Diagnostics 26................................
ABOUT Screen 26............................
POWER UP Screen 26........................
SOLENOIDS Screen 26.......................
METERS Screens 27
.........................
Monitor Meters 27.........................
Zero Meter Counters 27....................
KEYPAD Screen 27...........................
DIP SWITCHES Screen 27....................
CLEAR PRINTER BUFFER Screen 28...........
CAN Screens 28.............................
MANUALLY TEST CAN 28....................
CAN LEDs 28................................
TRANSACTION Screens 28...................
Setup - Modify or New Setup Options
-- Time and Date 29..............................
-- Operator Access 29...........................
-- Save Setup 29.................................
-- Important! 31..................................
-- Control Modules 31............................
Name Master Control Module 31...............
Name Slave Control Modules 31................
-- Fluids 32......................................
-- Dispense Areas 33............................
-- Connection Assignments 34...................
-- Meter Calibration 35...........................
-- Inventory 36..................................
-- Comm. on CM #1 37...........................
-- Run Options 38...............................
-- System Time-outs 39..........................
Printer and Computer Output 40..................
Computer: Receiving Horizon Data 43............
Windows 3.1 Setup 43........................
Windows 95 Setup 44.........................
Run Mode 48...................................
-- N e w J o b 49...................................
Select New Job 49............................
Enter Vehicle Data 49.........................
Dispense Request 50.........................
Preset Dispense 51...........................
Free Flow Dispense 51........................
Dispense Confirmation 51.....................
Dispense 52.................................
-- View Current Jobs 54..........................
-- Report Jobs 55................................

308607 3
Table of Contents
Inventory Mode 56..............................
-- Tank Levels 57................................
-- History Totals 58..............................
-- Report Inventory 59...........................
-- Save Inventory 60.............................
Installation and
Troubleshooting Tips 61.....................
-- General Precautions 61........................
-- System Components and
Installation Overview 61......................
Control Module 61............................
Programming Off-site 61.......................
Keypad 62...................................
Cabling 62...................................
New Installation Startup 62....................
Controller Area Network (CAN) 62..............
Control Module Address 62....................
Installing and Troubleshooting a
New Operating System Version 63..............
Reboot After Setup or
System Changes 63..........................
Printing Configuration 63......................
-- Troubleshooting System
Components 64.............................
Controller Area Network (CAN) 64..............
Solenoids 64.................................
Meters 65...................................
Printer 65....................................
-- Possible Problems and Solutions 66............
Maintenance 69.................................
Shutdown Procedure 69.......................
Pulse Meter Service 70........................
To Clean the Solenoid Valve 71.................
Power Failure 71.............................
Control Module 71............................
Clean The Keypad 71.........................
Install New Software 71.......................
Horizon System Components 72.................
Control Modules 72...........................
Keypads 74..................................
Keypad Wall-mount Bracket 75.................
Fluid Solenoid Valves 76......................
Air Solenoid Valves 76........................
Pulse Meters 77..............................
System Cables 77............................
Pressure Relief Kit 80.........................
Fluid Check Valve 80..........................
40 Column Thermal Printer 80
..................
Appendix 81....................................
Horizon Software Features 82.....................
System Configuration 83..........................
Installation Considerations 83..................
Steps For Configuring A System 83.............
System Design Suggestions 83.................
System Configuration Examples 84.............
Horizon Forms 85................................
Examples 86.................................
Blank Forms 97..............................
System Dynamics And Design Factors 104..........
Pressure Relief Kit 104........................
Ability to Dispense Fluid During
System Failure 104...........................
Avoiding Pulsation When
Simultaneous Dispensing Fluid 106.............
Selecting a Supply Pump 106..................
Technical Data 107..............................
Graco Standard Warranty 108....................
Graco Information 108...........................
Terms
CAN: Controller Area Network; network that
interconnects the control modules in the system.
Dispense Point: The combined designation of the
dispense area and fluid number (usually specifies a
hose reel with a dispense valve).
Fluid Zone: The groups of reels that share a pulse
meter.
Keypad: Hand-held device with display screen and
keys that communicates with the control module it is
connected to.
Master Control Module: In addition to the functions of
aSlave Control Module, it controls activity over the
CAN, has additional memory, provides printer or
computer interface, and continuously tracks the time
and date.
Non-volatile Memory: Data is retained when the
power is shut off.
Simultaneous Dispensing: The ability for more than
one hose reel in the Horizon system to be dispensing
fluid at the same time. The Horizon allows up to 12
dispenses to take place at a time.
Slave Control Module: Drives air and fluid solenoids
and counts pulses of the meters that are connected
to it.
Tables: Configuration information that is input during
installation to customize the system.

4 308607
Symbols
Warning Symbol
WARNING
This symbol alerts you to the possibility of serious
injury or death if you do not follow the instructions.
Caution Symbol
CAUTION
This symbol alerts you to the possibility of damage to
or destruction of equipment if you do not follow the
instructions.
WARNING
FIRE, EXPLOSION, AND ELECTRIC SHOCK HAZARD
Improper grounding, poor air ventilation, open flames, or sparks can cause a hazardous condition and
result in fire or explosion and serious injury.
DGround the equipment. See Connect AC Electrical Power to the Control Module, page 14.
DKeep the dispense area free of debris, including solvent, rags, and gasoline.
DDo not smoke in the dispense area.
DIf there is any static sparking while using the equipment, stop dispensing immediately. Identify
and correct the problem.
DKeep liquids away from the electrical components.
DDisconnect electrical power at the main switch before servicing the equipment.
INSTRUCTIONS
EQUIPMENT MISUSE HAZARD
Equipment misuse can cause the equipment to rupture, malfunction, or start unexpectedly and result
in serious injury.
DThis equipment is for professional use only.
DRead all instruction manuals, tags, and labels before operating the equipment.
DUse the equipment only for its intended purpose. If you are uncertain about usage, call your Graco
distributor.
DDo not alter or modify this equipment. Use only genuine Graco parts and accessories.
DCheck the equipment daily. Repair or replace worn or damaged parts immediately.
DDo not exceed the maximum working pressure of the lowest rated system component. See the in-
struction manuals of the individual system components for their maximum working pressures.
DDo not stop or deflect fluid leaks with your hand, body, glove, or rag.
DFollow the Shutdown Procedure on page 69 whenever you stop dispensing; or clean, check, or
service the equipment.
DUse fluids or solvents that are compatible with the equipment wetted parts. See the Technical Data
section of all the equipment manuals. Read the fluid and solvent manufacturer’s warnings.
DComply with all applicable local, state and national fire, electrical and other safety regulations.

308607 5
Symboles
Symboledemiseengarde
ATTENTION
Ce symbole vous met en garde contre les risques de
blessure grave ou de mort en cas de non-respect des
consignes.
Symbole d’avertissement
MISE EN GARDE
Ce symbole avertit l’opérateur du risque de dégât ou
de destruction du matériel en cas de non-respect des
instructions.
ATTENTION
DANGER D’INCENDIE, D’EXPLOSION ET DE DÉCHARGE ÉLECTRIQUE
Si l’équipement n’est pas convenablement relié à la terre et si les locaux sont mal ventilés, des flam-
mes ou des étincelles peuvent générer des situations dangereuses et provoquer un incendie ou une
explosion avec risque de blessure grave.
DRelier l’équipement à la terre. Voir Branchement de l’alimentation sur le module de
commande CA, page 14.
DTenir la zone de distribution propre et exempte de tout résidu, p. ex: solvant, chiffons et essence.
DNe pas fumer dans la zone de distribution.
DS’il se produit de l’électricité statique en utilisant le matériel, arrêter la distribution immédiate-
ment. Identifier la cause et remédier à l’incident.
DMaintenir tout liquide à l’écart des composants électriques.
DCouper l’alimentation électrique à l’interrupteur principal avant de mettre l’équipement en marche.
INSTRUCTIONS
DANGER DE MAUVAISE UTILISATION DU MATÉRIEL
Toute mauvaise utilisation de l’équipement peut occasionner la rupture, un dysfonctionnement ou un
démarrage inopiné et provoquer des blessures graves.
DCe matériel est destiné à un usage uniquement professionnel.
DLire tous les manuels d’instruction, panneaux et étiquettes avant de mettre le matériel en service.
DUtilisez ce matériel seulement pour l’usage auquel il est destiné. En cas de doute, appelez votre
distributeur Graco.
DNe pas altérer ou modifier ce matériel. N’utiliser que des pièces et accessoires Graco.
DVérifier le matériel quotidiennement. Réparer ou remplacer les pièces usagées ou endommagées
immédiatement.
DNe pas dépasser la pression de service maximum de l’élément le plus faible du système. Voir les
instructions figurant dans les manuels des éléments individuels du système pour connaître leurs
pressions maximum de service.
DNe pas arrêter ni dévier les fuites de produit avec la main, le corps, un gant ou un chiffon.
DSuivre la procédure d’arrêt, page 69 lors de chaque arrêt de pulvérisation, netoyage, vérification
ou entretien de l’équipement.
DS’assurer que les produits utilisés sont compatibles avec les pièces en contact avec le produit. Se
reporter aux Caractéristiques techniques de tous les manuels du matériel. Lire les mises en
garde du fabricant de produit.
DToujours respecter les législations locales, fédérales, et nationales applicables en matière
d’incendie, d’électricité, et de sécurité.

6 308607
Pre-installation Checklist
C
A
UTION
Accurately and thoroughly document the Control Module port connections and dispense areas. If the Software
Map does not exactly match the way the cables are connected, the system will not operate properly. Errors that
could occur include: inability to turn on a fluid at a given dispense area; the wrong fluid or dispense point is acti-
vated; or a fluid dispense point is properly activated, but the wrong meter is monitored so the dispense job will not
shut off properly.
This process is not difficult, but it is detailed and precise. Follow all steps and document them according to this
manual to ensure a successful installation.
NOTE:
DFollow these steps before beginning to install the Horizon system.
DRefer also to Installation and Troubleshooting Tips, beginning on page 61, for information that will help you
avoid installation problems and correct any problems that may occur.
nPre-installation Steps Reference
1. Locate the Floor Plan, System Map (diagram of component locations), and all
other documentation used to specify the system prior to ordering it.
If this information cannot be located, recreate it from the packing slip that
came with the system.
Packing slip and
Appendix, pages
81--106
2. Verify that all the parts on the Floor Plan match the parts shipped to you. Floor Plan, purchase
order, and packing
slip
3. Verify that all Horizon system components are marked in their proper loca-
tions on the Floor Plan.
Floor Plan
4. Assign a name and number to all the control modules in the system. Record
the control module numbers on the Floor Plan.
DThe Master Control Module (which the Administrative Keypad and printer
or computer connect to) is always assigned number 1.
DAdditional Slave Control Modules are numbered in sequence as 2, 3, etc.
DThe control modules do not have to be in numerical order along the
network cable.
Floor Plan
5. Assign a name and number to each dispense area. Record the names and
numbers on the Floor Plan.
DThe dispense area usually consists of banks of hose reels, but may also
consist of oil bars or individual hoses.
DThe names should make sense to the shop personnel who will use the
system. For example: Fast Lube, Service Bay 3, etc.
Floor Plan
6. Within each dispense area, verify that the Floor Plan shows the fluid that
each reel or hose should dispense.
Floor Plan

308607 7
Pre-installation Checklist
nPre-installation Steps Reference
7. Repeat the following steps for each control module:
a. For each solenoid attached to the control module, assign one port num-
ber, from 1 to 6. Record the port number and whether it is an air or fluid
solenoid on the Floor Plan. NOTE: Air and fluid solenoids can be inter-
mixedontheHorizonports.
b. For each meter attached to the control module, assign one port number,
from 7 to 12. Record the port number on the Floor Plan. NOTE: More
than one dispense point (reel, oil bar, hose, etc.) can share a meter.
CAUTION: Record all the information carefully as it must be accu-
rately entered during software setup.
Floor Plan
8. Record the system data from the Floor Plan to the corresponding Pre-instal-
lation Forms. The completed forms will ease system setup by placing the
information in the order the software will request the input. To ease software
setup, keep the items in numerical order.
Pre-installation Forms
Form #1: User Name, PIN Number, and Access Level
Form #2: Control Module and Fluid: Names and Numbers
Form #3: Dispense Area Names and Numbers
Form #4: Connection Assignments
Form #5: Meter Calibration Chart
Form #6: Warranty Registration and Checkout Form
Floor Plan and Forms
1--6; see examples of
forms on pages 86--96
9. Make sure the following tools are available for the system installation:
DDrill, drill bit, and anchors to mount the control modules and keypad
brackets on the walls or beams
DWire cutter
DWire stripper (wire gauge ranges between 18 and 22 AWG)
DSmall, slotted screwdriver
DVOM (volt-ohmmeter) or multimeter to check cable continuity, input
voltage, etc.
10. You are now ready to install the system. See the Installation Checklist on
page 8.

8 308607
Installation Checklist
NOTE:
DAfter completing the Pre-installation Checklist on page 6, use the following installation checklist to guide you
through the steps of the system installation.
DRefer also to Installation and Troubleshooting Tips, beginning on page 61, for information that will help you
avoid installation problems and correct any problems that may occur.
Hardware Installation
nInstallation Steps Reference
1. Flush all fluid lines to remove the debris and avoid clogs in the meters.
2. Install the solenoids and meters in the fluid and air systems. Floor plan, Appendix
(pages 104--106), and
solenoid and meter
manuals
3. Set the control module addresses with the DIP switches and label each
control module.
Floor plan and
page 10
4. If the electrical input is 220 VAC, rewire the transformer. Page 11
5. Mount each control module and keypad bracket in its assigned location. Floor plan and
page 13
Cable Routing and Connection
nInstallation Steps Reference
6. Route and connect the AC power to each control module. Do not turn on
the power yet!
Floor plan and
page 14
7. Route the solenoid and meter cables to their assigned control module. Floor plan
8. Connect each solenoid and meter cable to the proper connector/port in the
assigned control module.
CAUTION: Observe the proper polarity of meter connections or the meter
will be damaged.
Floor plan and
page 15
9. Route the CAN network cable between the control modules. Connect the
cable to the proper control module connectors. Remove the terminating
resistor from the connectors of the control modules that are in the middle of
the network chain.
Floor plan and
page 16
10. Route and connect the keypad cables between the keypads and the control
modules.
Floor plan and
page 17
11. Route and connect the printer or computer cable between the Master Control
Module and the printer or computer.
Page 18
12. Visually check that all wiring is connected correctly. Compare the wiring to the
diagrams in this manual.
Pages 14--17

308607 9
Installation Checklist
System Startup
nInstallation Steps Reference
13. Turn on the printer or computer.
14. Turn on the AC power to each control module. All the keypads should briefly
display a revision screen and then the HOME screen. The printer should print
“WELCOME TO HORIZON...” If the HOME screen is not displayed and/or
there is no print-out, see Troubleshooting, page 68.
Page 19
15. Using the Administrative Keypad, which is connected to the Master Control
Module, access the Setup screens. The Password is 1111 for a new system
installation.
Page 19
16. If your system has one control module only, disable the CAN network. Page 21
17. Select CLEAR SETUP to initialize the system. Be sure to enter a new pass-
word for setup access before exiting Setup.
Page 23
18. Using the administrative keypad, connected to the Master Control Module,
complete the System Setup. Use the six forms that were filled out in the
Pre-installation Procedure (refer to step 8, page 7) to enter the System
Map information into the Setup screens.
Pre-installation Forms
and Appendix, pages
86--95, or page 22,
New Setup Options
19. After entering all the setup data, reboot the system (turn the main power off
then on) to initialize the software.
Test the System
nInstallation Steps Reference
20. Request a dispense job for each fluid to each location. If any problems occur,
see Diagnostics, page 26, and troubleshooting information on page 61.
Pages 48 -- 52
21. Select SETUP!PRINT SETUP!ALLMEMORYtoprintarecordofallthe
data entered during Setup. Send a copy of this record and all other required
documents as instructed in Pre-installation Form 6, Warranty Registration &
Checkout Form.
Pages 24 and 96
System Installation Complete

10 308607
Hardware Installation
CAUTION
It is important to follow the floor plan or note any
deviations as the software addresses will be setup
according to what the floor plan shows. If addresses
and physical connections do not match, the system
will not operate properly.
1. Flush the System
Flush the fluid lines thoroughly to remove any particles
that could clog the meters.
2. Install Solenoids and Meters
WARNING
A Pressure Relief Kit is required in the
Horizon system to reduce the risk of
serious injury, caused by splashing fluid
in the eyes or on the skin resulting from component
rupture from over-pressurization. See Fig. 20,
page 104. See page 80 to order the kit.
Install the fluid system with the meters and solenoids in
their designated locations. Install pressure relief kits,
check valves, ball valves, fluid filters and other acces-
sories that are shown in the floor plan. Refer to Appen-
dix, pages 104 to 106.
3. Set Control Module Addresses and
Label the Boxes
CAUTION
Each control module must have a unique binary
number address, set by the DIP switches Once the
dip switch values are set, they must match the values
entered for each control module during setup.
Each packet of information sent through the network
contains the unique address of the control module
the information is intended for. If the DIP switches
are not set to the correct address, the control module
will not receive its information. If two control modules
have the same address, both of them will receive the
information and try to act on it, resulting in system
errors and incorrectly dispensed jobs.
NOTE:
DRefer to the Detail drawing of the DIP switches in
Fig. 1.
DSee page 73 for the location of the DIP switches in
the control module.
1. The Master Control Module is always number 1; do
not change its address.
2. All Slave Control Modules are shipped with their
address set to 0. Set the DIP switches for each
Slave Control Module to an address from 2 to 40.
DIP switches 1 to 6 are used to set the control
module addresses; see the chart on page 11.
3. Place a number label on the box that matches its
address number.
4. DIP switch 7 is used to tell the control module
whether a basic keypad or enhanced or adminis-
trative keypad is connected to it. The OFF position
indicates a basic keypad is connected. The ON
position indicates an enhanced or administrative
keypad is connected.
5. DIP switch 8 should be in the ON position for
normal system operation. The OFF position turns
on all six solenoid drivers in the control module.
This option can be used when there is a system
failure and fluids need to be dispensed. The moni-
toring and controlling of dispensed fluids is dis-
abled when the switch is in the OFF position.
Fig. 1 06651
Basic Keypad
Connected
Automatic
Operation
Control
Control Module
Addresses

308607 11
Hardware Installation
3. Set Control Module Addresses and
Label the Boxes (continued)
DIP
Switch
No.
123456Address
Setting OFF OFF OFF OFF OFF OFF 0*
g
ON OFF OFF OFF OFF OFF 1
OFF ON OFF OFF OFF OFF 2
ON ON OFF OFF OFF OFF 3
OFF OFF ON OFF OFF OFF 4
ON OFF ON OFF OFF OFF 5
OFF ON ON OFF OFF OFF 6
ON ON ON OFF OFF OFF 7
OFF OFF OFF ON OFF OFF 8
ON OFF OFF ON OFF OFF 9
OFF ON OFF ON OFF OFF 10
ON ON OFF ON OFF OFF 11
OFF OFF ON ON OFF OFF 12
ON OFF ON ON OFF OFF 13
OFF ON ON ON OFF OFF 14
ON ON ON ON OFF OFF 15
OFF OFF OFF OFF ON OFF 16
ON OFF OFF OFF ON OFF 17
OFF ON OFF OFF ON OFF 18
ON ON OFF OFF ON OFF 19
OFF OFF ON OFF ON OFF 20
ON OFF ON OFF ON OFF 21
OFF ON ON OFF ON OFF 22
ON ON ON OFF ON OFF 23
OFF OFF OFF ON ON OFF 24
ON OFF OFF ON ON OFF 25
OFF ON OFF ON ON OFF 26
ON ON OFF ON ON OFF 27
OFF OFF ON ON ON OFF 28
ON OFF ON ON ON OFF 29
OFF ON ON ON ON OFF 30
ON ON ON ON ON OFF 31
OFF OFF OFF OFF OFF ON 32
ON OFF OFF OFF OFF ON 33
OFF ON OFF OFF OFF ON 34
ON ON OFF OFF OFF ON 35
OFF OFF ON OFF OFF ON 36
ON OFF ON OFF OFF ON 37
OFF ON ON OFF OFF ON 38
ON ON ON OFF OFF ON 39
OFF OFF OFF ON OFF ON 40
* Slave Control Modules are shipped with their address set
to 0.
4. To Change from 110 VAC to 220 VAC
WARNING
FIRE, EXPLOSION, AND ELECTRIC
SHOCK HAZARD
To reduce the risk of fire, explosion, and
electric shock all wiring must be done by
a qualified electrician.
a. Power should not be connected at this point of
installation if the procedure is being followed
properly. Make sure there is no power to the
control module(s).
b. See Fig. 2 wire connections for 110 VAC. Cut
the white wire connecting transformer termi-
nals 2 to 6 at the terminal 2 connector.
c. Cut the black wire connecting transformer
terminals 1 to 5 at the terminal 1 connector.
d. Switch the connectors on terminals 2 and 6.
See Fig. 2 wire connections for 220 VAC.
e. Strip 0.25 in. (6.4 mm) of insulation from the
wires connected to terminals 2 and 5. Connect
the wires together with a wire nut.

12 308607
Fig. 2
06652
110 VAC Connection
220 VAC Connection
transformer
wire nut
06897
transformer
Wire
Connector Color
1black
2white
5black
6white
Wire
Connector Color
1black
2white
5black
6white

308607 13
Hardware Installation
5. Mount the Control Module and Keypad
Bracket
Control Module
DThe control module(s) should be mounted near the
hose reels. Control modules can be mounted on the
wall or at ceiling level.
DLocate the control module(s) as directed in the floor
plan, being sure to follow the cable length and other
configuration requirements.
DThe mounting surface must be able to support the
weight of the control module, 14 lbs. (6.3 kg). Use
wall anchors if necessary.
DSee Fig. 3 for the mounting hole layout.
¡6 in. (152.4 mm)
©8.75 in. (222.3 mm)
Fig. 3 06799
©
¡
Keypad Bracket
See Fig. 4 for the mounting hole layout.
¡3.44 in. (87.4 mm)
©3.66 in. (93.0 mm)
¢1.97 in. (50.0 mm)
£1.77 in. (45.0 mm)
¤0.62 in. (15.7 mm)
Fig. 4
¡
©
¢
£
¤

14 308607
Cable Routing and Connection
6. Connect the AC Electrical Power to the
Control Module
WARNING
FIRE, EXPLOSION, AND ELECTRIC
SHOCK HAZARD
To reduce the risk of fire, explosion, and
electric shock:
DAll wiring must be done by a qualified electri-
cian.
DGround the Horizon system by connecting the
electrical power cable to a true earth ground.
Wire the control module(s) into the facility’s electrical
system. It is recommended that the system be wired to
a separate circuit breaker. This will help prevent acci-
dental shutdown of the system and make it easier to
power off the system when necessary. The system is
designed to remain powered-up continuously during
normal operation.
To ease system maintenance, install a switch for
turning off the power at each control module. Locate
the switches near each control module, but out of
reach from the floor to prevent accidental shutoff of
power to the control module.
Connect the power cable to the control module as
showninFig.5.
Fig. 5 06650
¡
ground
AC
¥
£
¡AC power supply, 110 VAC or 220 VAC
NOTE: 220 VAC operation requires modification of transformer
connections inside control module. See page 11.
©Power cable must be 12--22 AWG with a minimum of 6 in. (152
mm) of the wire jacket removed.
¢Leave ground wire 2 inches (50.8 mm) longer than the two AC
wires. NOTE: Ground wire is green with yellow stripe.
£Strip 0.25 in. (6.4 mm) of insulation from wires, insert wires into
terminal block, and tighten screws to hold wire.
¤To transformer
¥To chassis ground
¤
©
©¢

308607 15
Cable Routing and Connection
7. Route the Solenoid and Meter Cables
to their Assigned Control Module
8. Connect the Solenoid and Meter
Cables
f. Connect the solenoid cables as shown in Fig.
6. The cables connect at the solenoid end with
wire nuts.
g. Connect the Ready Light as shown in Fig. 6.
h. Connect the pulse meter cables. The cables
connect at the pulse meter end with wire nuts.
DConnect an oil meter as shown in Fig. 7.
DConnect an anti-freeze meter as shown in
Fig. 8. Be sure to install the RC Filter. Fig. 6 06577
P8 or P9
Solenoid Connection
¡
¢
©
¡Use bulk Cable P/N 113557 (500 ft. [152.5 m]) or 113558
(1000 ft. [305 m)]); 50 ft. (15.3 m) maximum length
©Ready Light Kit 238996
NOTE: If existing Ready Light is used, the bulb and lens must
be replaced with bulb P/N 113859 and lens 113857
¢Fluid Solenoid P/N 218588 (includes Ready Light), 215487 or
512927; Air Solenoid P/N 215407 or 512926
NOTE: See Fig. 9, page 16, for connector locations.
Fig. 7 06579
J5
P5
Pulse Meter P/N 238618 Connection
ground
signal
+12V
black
white
red
©
¡Connector J5 in this drawing; can be J5, J6, or J7
©Use bulk Cable P/N 113555 (500 ft. [152.5 m]) or
113556 (1000 ft. [305 m)]); 50 ft. (15.3 m) maxi-
mum length
¢Pulse Meter P/N 238618
¢
ground
signal
signal
ground
+12V
shield
+12V
shield
black
white
red
Circuit Board
¡
Fig. 8 06580
Pulse Meter P/N 215474 Connection ¡
P5
shield
black
red
©
¡Connector J5 in this drawing; can be J5, J6, or J7
©RC Filter P/N 113837; included with meter
¢Pulse Meter P/N 215474
NC=No Connection
¢
N/C
N/C
black
red
ground
signal
N/C
ground
signal

16 308607
Cable Routing and Connection
9. Connect the Control Modules to the
CAN (Controller Area Network)
WARNING
FIRE, EXPLOSION, AND ELECTRIC
SHOCK HAZARD
To reduce the risk of fire, explosion, and
electric shock all wiring must be done by
a qualified electrician.
The cables are connected at each control module by
stripping the wires and connecting the wires as shown
in Fig. 10. Refer to Fig. 9 for the placement of the
control module connectors.
Each control module ships with a terminating resistor
on the connector for the CAN network. When the cable
is connected to the control module, the resistor must
be removed from the control modules located in the
middle of the network chain, leaving only the resistors
at each end of the network. The end resistors are
necessary for the control modules to be able to com-
municate properly with each other across the network.
DConnect the control module(s) in the middle of the
network chain as shown in Fig. 10, with the termi-
nating resistor removed.
DConnect the control modules at the end of the
network chain as shown in Fig. 10, with the termi-
nating resistor in place.
Fig. 9 06581
Control Module Connectors
1
2
3
4
5
6
1
2
3
4
5
6
1
2
3
4
5
6
1
2
3
4
5
6
1
2
3
4
5
6
123456
DConnect the shield at both ends of each cable
section (pins 2 or 5).
Fig. 10 06578
black
clear
shield
black black
clear clear
shield shield shieldshieldshield
P4 P4 P4 P4
End of Chain Middle of Chain
(resistor removed)
Middle of Chain
(resistor removed)
End of Chain
Controller Area Network (4 con
t
r
o
l
modu
l
e
s
s
ho
w
n
)
Use Bulk Cable P/N 113559 (500 ft. [152.5 m]) or 113560 (1000 ft. [305 m)])
NOTE: No distance requirement between control modules provided the overall length of the network cables does not exceed 2000 ft. (610 m).

308607 17
Cable Routing and Connection
10.Connect the Keypad Cable
Route and connect the keypad cables (P/N 191393 (25
ft. [7.6 m]) or 191394 (50 ft. [15.3 m)]) between the
keypads and control module connectors. If using the
Administrative or Enhanced Keypad, be sure to con-
nect the cable to the top keypad connector. The bottom
connector is for the bar code reader.
11. Connect the Printer or Computer Cable
Printer
New Style Printer: Program the DIP switches with the
printer software. See instruction sheet 308818,
included with the printer. Route and connect the printer
cable between the printer and the Master Control
Module connectors. Use the same cables that are used
with the keypads. See Fig. 11.
Old Style Printer: Set the DIP switches on the bottom
of the printer as shown in Fig. 12. Route and connect
the printer cable between the printer and the Master
Control Module connectors. Use the printer cables
shown in Fig. 12.
Computer
Route and connect the computer cable (P/N 192873
(25 ft. [7.6 m]) or 192874 (50 ft. [15.3 m)]) between the
computer and the Master Control Module connectors.
See Fig. 13.
See page 40 to set up your computer to receive Hori-
zon system data.
12.Visually Check the Wire Connections
The Horizon hardware installation is now complete.
The Checklist Steps 1 to 12, page 8, should be
checked off.
Connecting to New Style Printer P/N 113774
54132
9876
New Style Printer P/N 113774
9 Pin D--Sub Male Pin Connector
Master Control Module
9 Pin D--Sub Male Pin Connector
©
¡Printer cable with connector, P/N 191393 (25 ft. [7.6 m]) or 191394 (50 ft. [15.3 m)])
Fig. 11
green
white
red
ground
receive
transmit
ground
receive
transmit
shield
shield
54132
9876
Black power
power

18 308607
Cable Routing and Connection
Connecting to Old Style Printer P/N 113774
252423222120191817161514
13 12 11 10 9 8 7 6 5 4 132
25 24 23 22 21 20 19 18 17 16 15 14
13121110987654132 54132
9876
87654132654132
Old Style Printer P/N 113774
25 Pin D--Sub Male Pin Connector
(Jumper 6 to 20)
Master Control Module
9 Pin D--Sub Male Pin Connector
ON
OFF
Standard DIP Switch Settings for O
l
d
S
t
y
l
ePrinter 113774
©
¡Printer serial port
©Printer cable with connector, P/N 191395 (25 ft. [7.6 m])
or 191396 (50 ft. [15.3 m)])
¡
Fig. 12
green
white
red
ground
receive
transmit
ground
receive
transmit
shield
Communication Settings
D9600 Baud Rate
DNo Parity
D1StopBit
D8DataBits
DNo Software Handshaking
Connecting to a Computer
54132
9876
Computer
9 Pin D--Sub Female Pin Connector
Master Control Module
9 Pin D--Sub Male Pin Connector
©
¡Printer cable with connector, P/N 192873 (25 ft. [7.6 m]) or 192874 (50 ft. [15.3 m)])
Fig. 13
green
white
red
ground
receive
transmit
ground
receive
transmit
shield
54132
9876

308607 19
System Setup -- Startup
CAUTION
The addresses in the software must match the
physical connections to the control modules or the
system will not operate properly.
Instructions Screens
Startup Screen
This screen is displayed for four seconds after the
system is turned on, then the Mode Selection screen
(or Home screen) appears.
STARTUP Screen
HORIZON
REV X.XX
GRACO INC
COPYRIGHT XXXX
Mode Selection (HOME)
This is the HOME screen. It is the destination any time
the HOME button on the keypad is pressed.
1. Cursor is initially on RUN.
2. Move the cursor to SETUP by pressing the "or #
key.
NOTE: The SETUP option can only be modified on
the administrator keypad.
3. Press ENTER on the keypad.
HOME Screen
__________"HOME A__________
RUN SETUP
INVNT
Enter Password
The password is determined by what is entered during
setup. The first time the system is started, the Pass-
word is 1111.
1. Cursor is in the PASSWORD field.
2. Type the password.
3. Press ENTER on the keypad.
PASSWORD Screen
ENTER PASSWORD
SETUP MENU
XXXX

20 308607
System Setup -- Startup
Instructions
Types of Setup
1. SETUP screen appears.
2. Cursor is on ENABLE/DISABLE CAN.
3. Move the cursor by pressing the "or #key.
4. Press ENTER on the keypad when the cursor is at
the desired selection.
ENABLE/DISABLE CAN: ENABLE CAN is the default
selection. It indicates that the system has more than
one control module. For normal operation, all control
modules should have CAN enabled. To change to
DISABLE CAN, which must be done for a system with
only one control module, follow page 21.
NOTE: When a controller’s CAN communication is
disabled, the controller will not send any CAN mes-
sages but it can still receive CAN messages.
MODIFY SETUP: to modify a current setup. See page
22.
NEW SETUP: to enter a completely new setup. See
page 22.
CLEAR SETUP: to clear particular setup options.
Choose CLEAR SETUP if this is the initial setup of a
new system. See page 23.
PRINT SETUP: to print out selected information about
the control module. If this is the initial setup of a new
system, print out ALL MEMORY after the system is
completely installed, for future reference. See page 24.
UPDATE TABLES: to send information from one
control module to all connected control modules. If the
Master Control Module was setup off-line, use this
feature to send information to all control modules after
they are connected. See page 25.
DIAGNOSTICS: to help troubleshoot the system. See
page 26.
Screens
SETUP Screens
__________"SETUP A__________
ENABLE/DISABLE CAN
MODIFY SETUP
NEW SETUP #
__________"SETUP A__________
CLEAR SETUP "
PRINT SETUP
UPDATE TABLES #
__________"SETUP A__________
PRINT SETUP "
UPDATE TABLES
DIAGNOSTICS
Table of contents
Other Graco Control System manuals
Popular Control System manuals by other brands
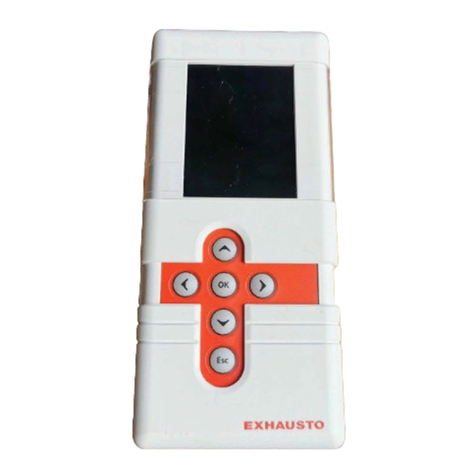
Exhausto
Exhausto EXact2 VEX240 series Basic instructions
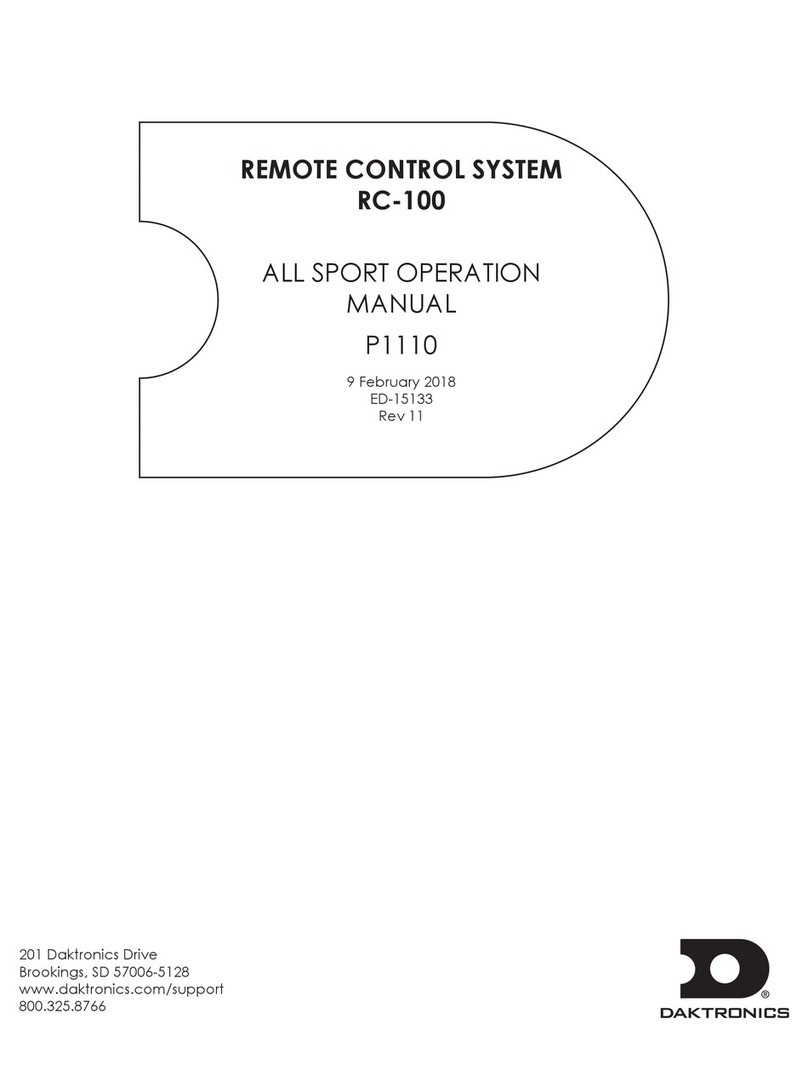
Daktronics
Daktronics RC-100 Operation manual
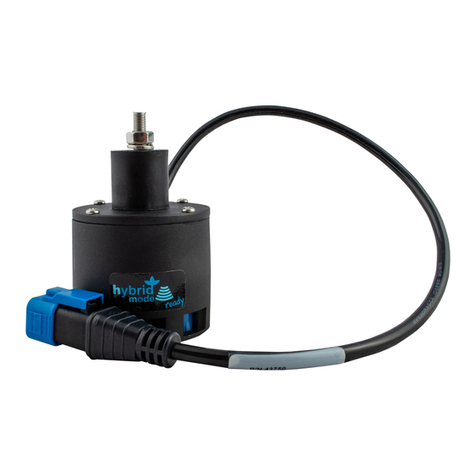
Norac
Norac UC5 Topcon X30 installation manual

Galcon
Galcon GalStar Instruction
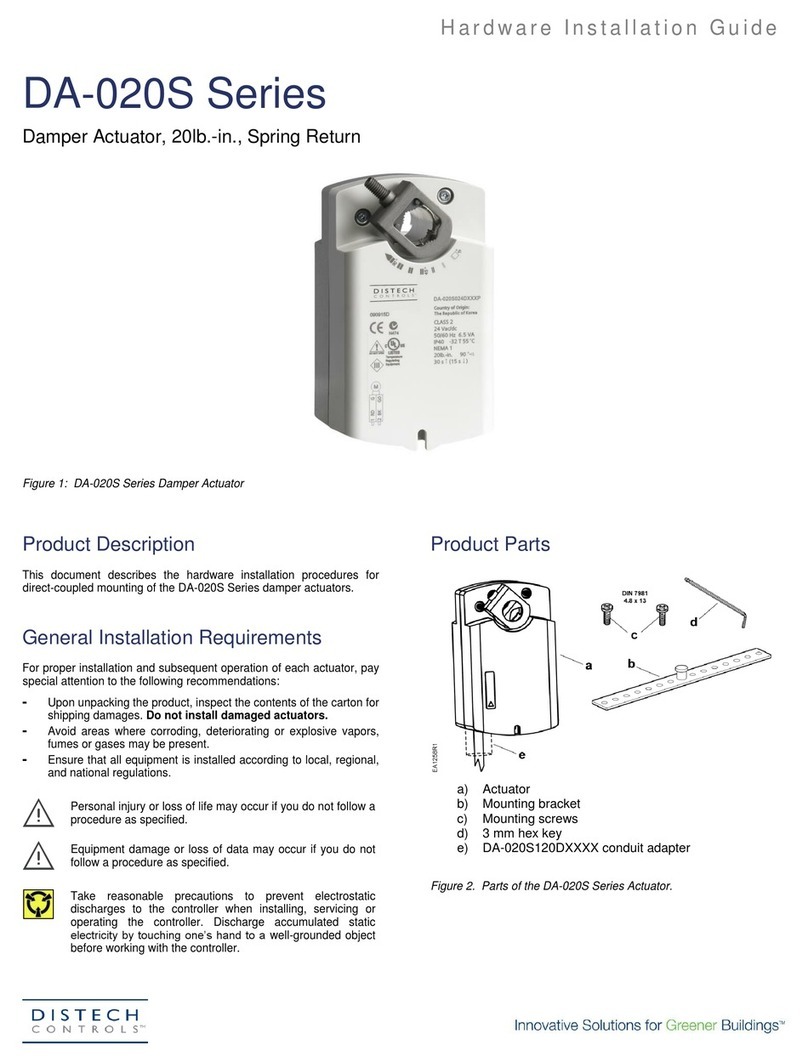
Distech Controls
Distech Controls DA-020S Series Hardware installation guide
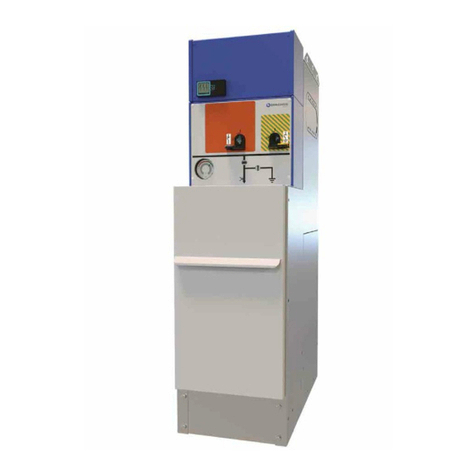
Ormazabal
Ormazabal cgmcosmos-l General instructions