Grizzly G0656 User manual

COPYRIGHT © FEBRUARY, 2008 BY GRIZZLY INDUSTRIAL, INC.
WARNING: NO PORTION OF THIS MANUAL MAY BE REPRODUCED IN ANY SHAPE
OR FORM WITHOUT THE WRITTEN APPROVAL OF GRIZZLY INDUSTRIAL, INC.
#BL10444 PRINTED IN CHINA
Clean Up (See Page 13)
The following sliding surfaces must be cleaned:
• Fence carriage
• Fence bracket
Assembly (See Page 14)
Assembly of the fence bracket, fence carriage
assembly, and handwheels has changed. Steps
2-5 below replace Steps 15-17 on Page 15 of the
G0656 Owner's Manual.
1. Follow Steps 1-14 on Pages 14 & 15.
2. Align the mounting holes on the fence bracket
and jointer, and fasten with the M8-1.25 x 35
cap screws, flat washers and lock washers,
as shown in Figure 2. Do not fully tighten the
fasteners yet.
This update covers changes made to the machine after the owner's manual was printed. All page num-
ber references refer to the owner's manual for this machine. Keep this update with your owner's man-
ual for future reference. If you have questions, contact Tech Support at (570) 546-9663 or by email at
MODEL G0656
8" JOINTER w/BUILT-IN
MOBILE BASE
MANUAL UPDATE
The items below have been added to the original
list of included assembly fasteners:
Assembly Fasteners Qty
• Cap Screws M8-1.25 x 35 (Fence) ............ 4
• Lock Washers 8mm (Fence) ...................... 4
• Flat Washers 8mm (Fence) ........................ 4
• Key 4 x 4 x 12 (Right Handwheel) ............. 1
Machine Inventory (See Page 11)
The fence assembly and fence bracket are no
longer pre-installed on the jointer assembly by
the factory for shipping, as shown in Figure 3 on
G0656 Manual Page 11. These items have been
added to the machine inventory (Figure 1). Refer
to the owner's manual for the rest of the inven-
tory.
Wood Crate (Figure 1): Qty
A. Fence Bracket ........................................... 1
B. Fence Assembly ........................................ 1
B
A
Figure 1. New inventory items.
Fence
Bracket
Figure 2. Fence bracket installed.

5. Install the round-slotted handwheel onto the
right shaft with the 4 x 4 x 12 key, and install
the square-slotted handwheel onto the left
shaft, using the cap screws and flat washers
already mounted on the handwheel shafts.
Figure 5. Handwheels installed.
Round Slotted
Handwheel
Square Slotted
Handwheel
Figure 4. Fence installed.
Flat Washer
Fence Lock
Handle Bolt
4. Secure the fence lock handle bolt with the
locking nut and flat washer removed in Step
3, as shown in Figure 4, and final tighten the
fence bracket.
3. Remove the locking nut and flat washer
(Figure 3) from the fence lock handle bolt
(Figure 4), place the fence assembly over
the jointer tables and fence bracket, and
insert the bolt through the fence bracket slot,
making sure the carriage fits over the key
(Figure 3).
Figure 3. Fence locking nut and washer
removed.
Flat Washer
Locking Nut
Key Carriage
6. Perform Steps 18-26 on Pages 15 & 16.
Locking Nut

MODEL G0656
8" JOINTER w/BUILT-IN
MOBILE BASE
OWNER'S MANUAL
COPYRIGHT © NOVEMBER, 2007 BY GRIZZLY INDUSTRIAL, INC.
WARNING: NO PORTION OF THIS MANUAL MAY BE REPRODUCED IN ANY SHAPE
OR FORM WITHOUT THE WRITTEN APPROVAL OF GRIZZLY INDUSTRIAL, INC.
#BL10198 PRINTED IN CHINA


Table of Contents
INTRODUCTION ............................................... 2
Foreword ........................................................ 2
Contact Info ................................................... 2
Machine Data Sheet ...................................... 3
Identification ................................................... 5
SECTION 1: SAFETY ....................................... 6
Safety Instructions for Machinery .................. 6
Additional Safety Instructions for Jointers ..... 8
SECTION 2: CIRCUIT REQUIREMENTS ........ 9
220V Operation .............................................. 9
SECTION 3: SETUP ....................................... 10
Setup Safety ................................................ 10
Items Needed for Setup ............................... 10
Unpacking .................................................... 10
Inventory ...................................................... 11
Hardware Recognition Chart ....................... 12
Clean Up ...................................................... 13
Site Considerations ...................................... 13
Assembly ..................................................... 14
Dust Collection ............................................. 17
Setting Outfeed Table Height ...................... 17
Test Run ...................................................... 18
Recommended Adjustments ........................ 18
Tighten V-Belt .............................................. 18
SECTION 4: OPERATIONS ........................... 19
Operation Safety .......................................... 19
Jointer Overview .......................................... 19
Basic Controls .............................................. 20
Stock Inspection & Requirements ............... 21
Squaring Stock ............................................ 22
Surface Planing ........................................... 22
Edge Jointing ............................................... 23
Bevel Cutting ............................................... 24
Rabbet Cutting ............................................. 25
SECTION 5: ACCESSORIES ......................... 27
SECTION 6: MAINTENANCE ......................... 30
Schedule ...................................................... 30
Lubrication ................................................... 30
Cleaning ....................................................... 31
V-Belts ......................................................... 31
SECTION 7: SERVICE ................................... 32
Troubleshooting ........................................... 32
Inspecting Knives ......................................... 34
Setting/Replacing Knives ............................. 34
Setting Infeed Table ..................................... 36
Setting Fence Stops .................................... 37
Adjusting Gibs .............................................. 38
Wiring Diagram ............................................ 39
Table Parts Breakdown ............................... 40
Fence Parts Breakdown .............................. 42
Stand Parts Breakdown ............................... 44
Label Placement .......................................... 46
WARRANTY AND RETURNS ........................ 49

-2- G0656 8" Jointer with Built-In Mobile Base
INTRODUCTION
Foreword
We are proud to offer the Model G0656 8" Jointer
with Built-In Mobile Base. This machine is part
of a growing Grizzly family of fine woodworking
machinery. When used according to the guide-
lines set forth in this manual, you can expect
years of trouble-free, enjoyable operation and
proof of Grizzly’s commitment to customer satis-
faction.
The specifications, drawings, and photographs
illustrated in this manual represent the Model
G0656 when the manual was prepared. However,
owing to Grizzly’s policy of continuous improve-
ment, changes may be made at any time with no
obligation on the part of Grizzly.
For your convenience, we always keep current
Grizzly manuals available on our website at www.
grizzly.com. Any updates to your machine will be
reflected in these manuals as soon as they are
complete. Visit our site often to check for the lat-
est updates to this manual!
If you have any comments regarding this manual,
please write to us at the address below:
Grizzly Industrial, Inc.
C/O Technical Documentation Manager
P.O. Box 2069
Bellingham, WA 98227-2069
Email: [email protected]
We stand behind our machines. If you have any
service questions or parts requests, please call or
write us at the location listed below.
Grizzly Industrial, Inc.
1203 Lycoming Mall Circle
Muncy, PA 17756
Phone: (570) 546-9663
Fax: (800) 438-5901
E-Mail: [email protected]
Web Site: http://www.grizzly.com
Contact Info

G0656 8" Jointer with Built-In Mobile Base -3-
Machine Data Sheet

-4- G0656 8" Jointer with Built-In Mobile Base

G0656 8" Jointer with Built-In Mobile Base -5-
A. Outfeed Table
B. Fence
C. Cutterhead Guard
D. Fence Adjustment Wheel
E. Fence Tilt Handle
F. ON/OFF Switch
G. Infeed Table
H. Fence Tilt Lock
I. Outfeed Table Lock
J. Fence Lock
K. Depth Stop Lever
L. Infeed Table Lock
M. Infeed Table Handwheel
N. Depth Scale
O. Wheel Assembly
P. Dust Port
Q. Outfeed Table Handwheel
Identification
Figure 1. Model G0656 identification.
AB
C
D
E
F
G
K
M
N
O
D
E
H
I
J
P
L
Q

-6- G0656 8" Jointer with Built-In Mobile Base
Safety Instructions for Machinery

G0656 8" Jointer with Built-In Mobile Base -7-

-8- G0656 8" Jointer with Built-In Mobile Base
Additional Safety Instructions for Jointers
Like all machines there is danger associated
with this machine. Accidents are frequently
caused by lack of familiarity or failure to pay
attention. Use this machine with respect
and caution to lessen the possibility of
operator injury. If normal safety precautions
are overlooked or ignored, serious personal
injury may occur.
1. JOINTER KICKBACK. "Kickback" is when
the workpiece is thrown off the jointer table
by the force of the cutterhead. Always use
push blocks and safety glasses to reduce
the likelihood of injury from “kickback.” If you
do not understand what kickback is, or how
it occurs, DO NOT operate this machine.
2. CUTTERHEAD ALIGNMENT. Keep the top
edge of the outfeed table aligned with the
cutterhead knife or insert at top dead center
(TDC) to avoid kickback and personal inju-
ries.
3. PUSH BLOCKS. Always use push blocks
whenever surface planing. Never pass your
hands directly over the cutterhead without a
push block.
4. WORKPIECE SUPPORT. Supporting the
workpiece adequately at all times while
cutting is crucial for making safe cuts and
avoiding injury. Never attempt to make a cut
with an unstable workpiece.
5. KICKBACK ZONE. The "kickback zone"
is the path directly through the end of the
infeed table. Never stand or allow others to
stand in this area during operation.
6. SAFE KNIFE PROJECTION. Knives that
project more than 0.125" from the cutterhead
may become loose or damaged during oper-
ation. Always make sure knives are properly
set and well tightened in the cutterhead.
7. MAXIMUM CUTTING DEPTH. The maxi-
mum cutting depth for one pass is 1⁄8".
To minimize kickback, never attempt any
single cut deeper than this!
8. JOINTING WITH THE GRAIN. Jointing
against the grain or jointing end grain is
dangerous and could produce chatter or
excessive chip out. Always joint with the
grain.
9. KEEPING GUARDS IN PLACE. With the
exception of rabbeting, all operations must
be performed with the cutterhead guard in
place. After rabbeting, be sure to replace
the guard, to reduce the risk of serious
injury.
10. PROPER CUTTING. When cutting, always
keep the workpiece moving toward the
outfeed table until the workpiece has passed
completely over the cutterhead. Never back
the work toward the infeed table, to reduce
the risk of kickback.
11. USING GOOD STOCK. Jointing safety
begins with your lumber. Inspect your
stock carefully before you feed it over the
cutterhead. Never joint a board that has
loose knots, nails, or staples. If you have
any doubts about the stability or structural
integrity of your stock, DO NOT joint it!
No list of safety guidelines can be complete.
Every shop environment is different. Always
consider safety first, as it applies to your
individual working conditions. Use this and
other machinery with caution and respect.
Failure to do so could result in serious per-
sonal injury, damage to equipment, or poor
work results.

G0656 8" Jointer with Built-In Mobile Base -9-
220V Operation
Full Load Amperage Draw
Motor Draw at 220V .............................. 15 Amps
Minimum Circuit Requirements
You MUST connect your machine to a grounded
circuit that is rated for the amperage given below.
Never replace a circuit breaker on an existing cir-
cuit with one of higher amperage without consult-
ing a qualified electrician to ensure compliance
with wiring codes. If you are unsure about the
wiring codes in your area or you plan to con-
nect your machine to a shared circuit, consult
a qualified electrician.
Minimum Circuit Size .............................20 Amps
Extension Cords
Using extension cords may reduce the life of the
motor. Instead, place the machine near a power
source. If you must use an extension cord:
• Use at least a 12 gauge cord that does not
exceed 50 feet in length!
• The extension cord must also have a ground
wire and plug pin.
• A qualified electrician MUST size cords over
50 feet long to prevent motor damage.
Figure 2. NEMA L6-20 plug and receptacle.
SECTION 2: CIRCUIT REQUIREMENTS
Serious personal injury could occur if you
connect the machine to power before com-
pleting the setup process. DO NOT connect
the machine to the power until instructed
later in this manual.
Electrocution or fire could
result if machine is not
grounded and installed in
compliance with electrical
codes. Compliance MUST
be verified by a qualified
electrician!
Power Connection Device
The type of plug required to connect your machine
to power depends on the type of service you cur-
rently have or plan to install. We recommend
using the plug shown in Figure 2.

-10- G0656 8" Jointer with Built-In Mobile Base
Wear safety glasses dur-
ing the entire setup pro-
cess!
This machine presents
serious injury hazards
to untrained users. Read
through this entire manu-
al to become familiar with
the controls and opera-
tions before starting the
machine!
Setup Safety
SECTION 3: SETUP
The following items are needed to complete the
setup process, but are not included with your
machine:
Description Qty
• Safety Glasses (for each person) .............. 1
• Wrench or Socket 17mm ............................ 2
• Wrench or Socket 13mm ............................ 2
• Extra Person for Lifting Help ...................... 1
• Straightedge (see Page 28) ....................... 1
• Phillips Head Screwdriver .......................... 1
• Dust Collection System .............................. 1
• 4" Dust Hose (length as needed) ............... 1
• 4" Hose Clamp ........................................... 1
Your machine was carefully packaged for safe
transportation. Remove the packaging materials
from around your machine and inspect it. If you
discover the machine is damaged, please imme-
diately call Customer Service at (570) 546-9663
for advice.
Save the containers and all packing materials for
possible inspection by the carrier or its agent.
Otherwise, filing a freight claim can be difficult.
When you are completely satisfied with the condi-
tion of your shipment, inventory the contents.
Unpacking
Items Needed for
Setup
This machine and its com-
ponents are very heavy.
Get lifting help or use
power lifting equipment
such as a forklift to move
heavy items.

G0656 8" Jointer with Built-In Mobile Base -11-
Inventory
The following is a description of the main compo-
nents shipped with your machine. Lay the compo-
nents out to inventory them.
Note: If you can't find an item on this list, check
the mounting location on the machine or examine
the packaging materials carefully. Occasionally
we pre-install certain components for shipping
purposes.
Wood Crate: (Figure 3) Qty
A. Jointer Assembly ........................................ 1
B. Cutterhead Guard ....................................... 1
C. Handwheels ................................................ 2
D. Handles ...................................................... 2
E. Fence Tilt Lever ......................................... 1
F. Push Blocks ................................................ 2
G. Knife Setting Gauge Hardware Bag
— Knife Setting Gauge Rod ........................ 1
— Knife Setting Gauge Foot ....................... 2
— E-Clip 8mm ............................................. 2
H. Tool Hardware Bag
— Hex Wrenches 2.5, 3, 4, 6mm ......1 Each
—Open-end Wrench 8/10, 12/14mm ......... 1
Cardboard Box: (Figure 4) Qty
I. Stand Assembly w/Motor and Door ........... 1
J. Pedestal Switch .......................................... 1
K. Wheel Assembly ......................................... 1
L. V-Belt .......................................................... 1
M. Dust Port ................................................... 1
Assembly Fasteners Qty
• Hex Bolt M8-1.25 x 50 (Wheel/Stand) ....... 1
• Flat Washer 8mm (Wheel/Stand) ............... 1
• Hex Bolts M10-1.5 x 55 (Wheel/Stand) ...... 2
• Flat Washers 10mm (Wheel/Stand) ........... 2
• Hex Nuts M10-1.5 (Wheel/Stand) .............. 2
• Cap Screws M8-1.25 x 50 (Jointer/Stand) . 3
• Flat Washers 8mm (Jointer/Stand) ............ 6
• Lock Washers 8mm (Jointer/Stand) ........... 3
• Hex Nuts M8-1.25 (Jointer/Stand) .............. 3
• Flat Washers 6mm (Handwheels) .............. 2
• Cap Screws M6-1 x 12 (Handwheels) ....... 2
• Set Screw M5-.8 x 12 (Cutterhead Guard) 1
• Cap Screws M8-1.25 x 25 (Pedestal) ........ 2
• Lock Washers (Pedestal) ........................... 2
• Flat Washers (Pedestal) ............................. 2
• Phillips Head Screws
M5-.8 x 16 (Dust Port) ................................ 4
• Flat Washers 5mm (Dust Port) .................. 4
• Cap Screws M8-1.25 x 25 (Fence Suppt.) . 4
• Flat Wshers 8mm (Fence Support) ............ 4
• Lock Washers 8mm (Fence Supptort) ....... 4
In the event that any nonproprietary parts are
missing (e.g. a nut or a washer), we would be
glad to replace them, or for the sake of expedi-
ency, replacements can be obtained at your local
hardware store.
Figure 3. Box 1 inventory contents.
A
B
C
D
E
F
G
H
Figure 4. Box 2 inventory contents.
J
K
L
M
SUFFOCATION HAZARD!
Immediately discard all plas-
tic bags and packing materi-
als to eliminate choking/suf-
focation hazards for children
and animals.
I

-12- G0656 8" Jointer with Built-In Mobile Base
Hardware Recognition Chart

G0656 8" Jointer with Built-In Mobile Base -13-
Floor Load
Refer to the Machine Data Sheet for the weight
and footprint specifications of your machine.
Some residential floors may require additional
reinforcement to support both the machine and
operator.
Placement Location
Consider existing and anticipated needs, size of
material to be processed through each machine,
and space for auxiliary stands, work tables or
other machinery when establishing a location for
your new machine. See Figure 6 for the minimum
working clearances.
Children and visitors may be
seriously injured if unsuper-
vised around this machine.
Lock entrances to the shop
or disable start switch or
power connection to prevent
unsupervised use.
The unpainted surfaces are coated with a waxy
oil to prevent corrosion during shipment. Remove
this protective coating with a solvent cleaner or
citrus-based degreaser such as Grizzly’s G7895
Citrus Degreaser. To clean thoroughly, some parts
must be removed. For optimum performance
from your machine, clean all moving parts or
sliding contact surfaces. Avoid chlorine-based
solvents, such as acetone or brake parts cleaner
that may damage painted surfaces. Always follow
the manufacturer’s instructions when using any
type of cleaning product.
To access the sliding surfaces, remove the lock
nut (Figure 5) and flat washer securing the fence
lock handle, and remove the fence from the jointer
unit.
Site ConsiderationsClean Up
Figure 6. Minimum working clearances.
Gasoline and petroleum
products have low flash
points and can explode
or cause fire if used to
clean machinery. DO
NOT use these products
to clean the machinery.
Figure 5. Removing the fence lock nut so the
sliding surfaces can be cleaned.
Once the sliding surfaces of the fence are clean,
reassemble the fence to the jointer and secure
the lock handle with the lock nut and washer.
Fence Lock
Handle
Fence Lock Nut

-14- G0656 8" Jointer with Built-In Mobile Base
Assembly
To assemble the jointer:
1. Carefully lay the stand on its side so you can
access the underside.
2. Bolt the wheel assembly to the stand with the
provided hardware, as shown in Figure 7.
Note: Refer to the Inventory List on Page
11 for a list of components needed for ass-
sembly.
Figure 7. Example of bolting the wheel assembly
to the stand.
3. Turn the stand rightside up.
5. With the help of an assistant, lift the jointer
onto the stand.
6. Align the mounting holes on the jointer and
stand.
7. Secure the jointer to the stand with the M8-
1.25 x 50 cap screws, washers, and hex nuts,
as shown in Figure 8.
The jointer is heavy. Seek
assistance when lifting it
onto the jointer stand.
Figure 8. Jointer secured to stand.
8. Using a 13mm wrench, loosen the motor
bracket fasteners shown in Figure 9.
Note: DO NOT completely remove the motor
mount bolts.
Figure 9. Motor bracket fasteners (black
arrows); motor mount fasteners (white arrows).
Hex Bolt M8-1.25 x 50
Flat Washer 8mm
Hex Nuts
M10-1.5
Hex Bolts M10-1.5 x 55
Flat Washers 10mm
4. Remove the rear access panel from the
jointer stand.

G0656 8" Jointer with Built-In Mobile Base -15-
9. Slide the motor upward, and place the V-belt
around the cutterhead pulley and the motor
pulley.
10. Slide the motor down to rest on the V-belt.
11. Place a straightedge against both pulleys
(Figure 10) and check the alignment of
the two pulleys to make sure that they are
aligned and that the V-belt is straight up and
down (see Figure 11).
— If the pulleys are aligned, tighten the motor
bracket fasteners and go to Step 15.
— If the pulleys are NOT aligned, perform
Steps 12–14.
12. Remove the V-belt and loosen the motor
mount fasteners (see Figure 9).
Figure 11. Pulleys aligned.
Cutterhead
Pulley
Motor
Pulley
Figure 13. Fence tilt lever installed.
18. Slide the cutterhead guard shaft down through
the mounting hole on the table.
Note: The guard may not fully seat in the hole
initially; however, rotating the guard will allow
the shaft to fully seat in the hole.
Figure 10. Checking belt alignment.
13. Shift the motor horizontally as needed to
align the motor pulley with the cutterhead pul-
ley, then replace the V-belt.
14. Tighten the motor mount fasteners.
15. Secure the infeed and outfeed handwheels
with the cap screws and flat washers already
mounted on the handwheel shafts, as shown
in Figure 12.
16. Secure the handwheel handles to each of the
the handwheels, as shown in Figure 12.
17. Install the fence tilt lever, as shown in Figure
13.
Figure 12. Securing the handwheel handle.
Straightedge

-16- G0656 8" Jointer with Built-In Mobile Base
25. Assemble the knife setting gauge using the
knife setting gauge rod, feet and 8mm e-
clips, as shown in Figure 16.
Figure 16. Knife setting gauge assembly.
Figure 15. Attaching pedestal switch to stand.
24. Thread the excess switch cord through the
access hole in the stand and connect it to the
motor cord.
22. Test the guard by pulling it back and letting it
go.
—The guard should snap back over the
cutterhead without dragging across the
table.
—If the guard drags across the table, loosen
the set screw, raise the guard until it won't
drag, then tighten the set screw.
—If the guard does not snap back, remove it
and repeat Steps 18–21.
23. Attach the pedestal switch with the cap
screws, lock washers, and flat washers, as
shown in Figure 15.
Figure 14. Example of installing cutterhead
guard set screw.
20. Raise the fence and rotate the guard one
revolution counter-clockwise as it appears
from the top. Hold the guard in position.
21. Lower the fence and allow the guard to swing
back against the fence.
NOTICE
The cutterhead guard must always return to
the closed position whenever it is moved.
19. Using a 2.5mm hex wrench, thread the set
screw through the hole in the forked end of
the cutterhead guard shaft (Figure 14).
Note: Thread the set screw far enough to
prevent the guard from being pulled out.
26. Replace the rear access panel on the stand.
Table of contents
Other Grizzly Power Tools manuals
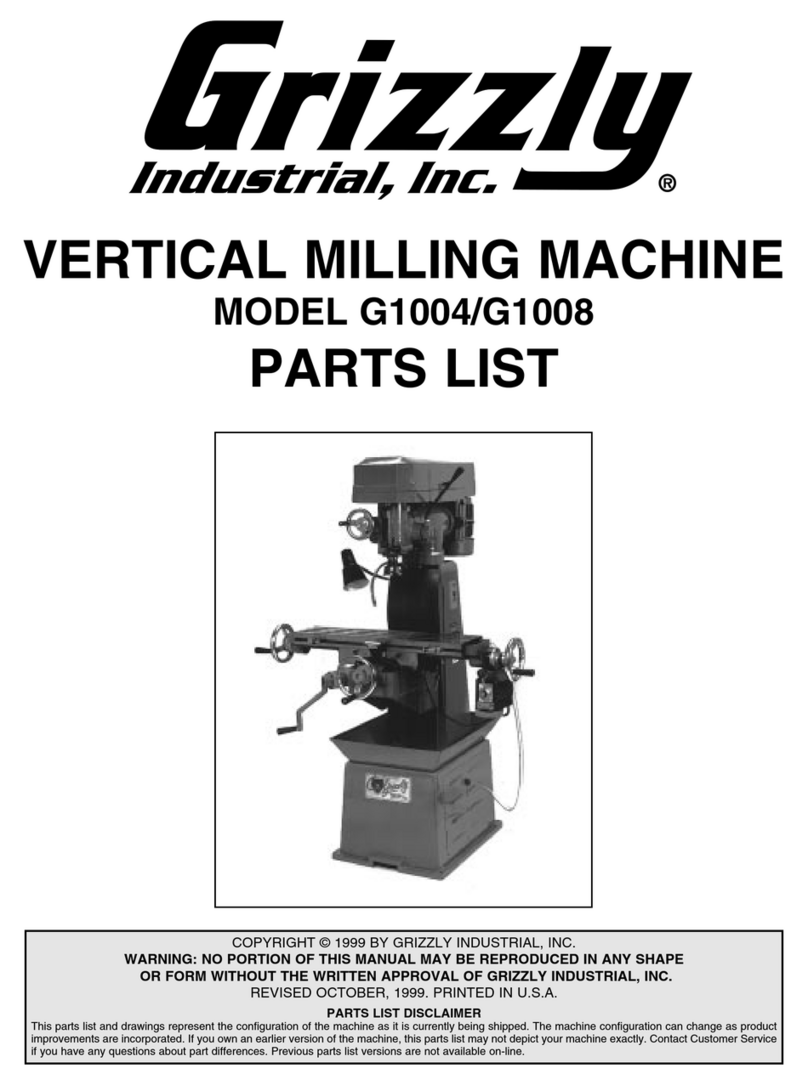
Grizzly
Grizzly G1004 User manual
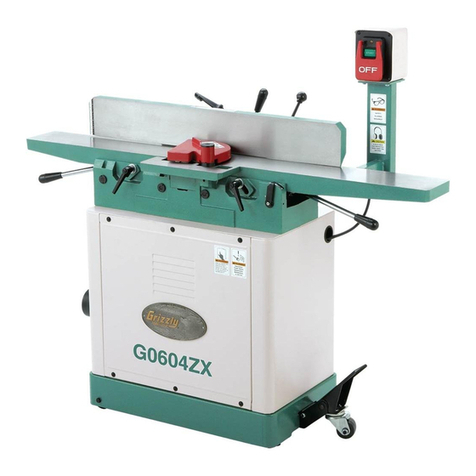
Grizzly
Grizzly G0604ZX User manual
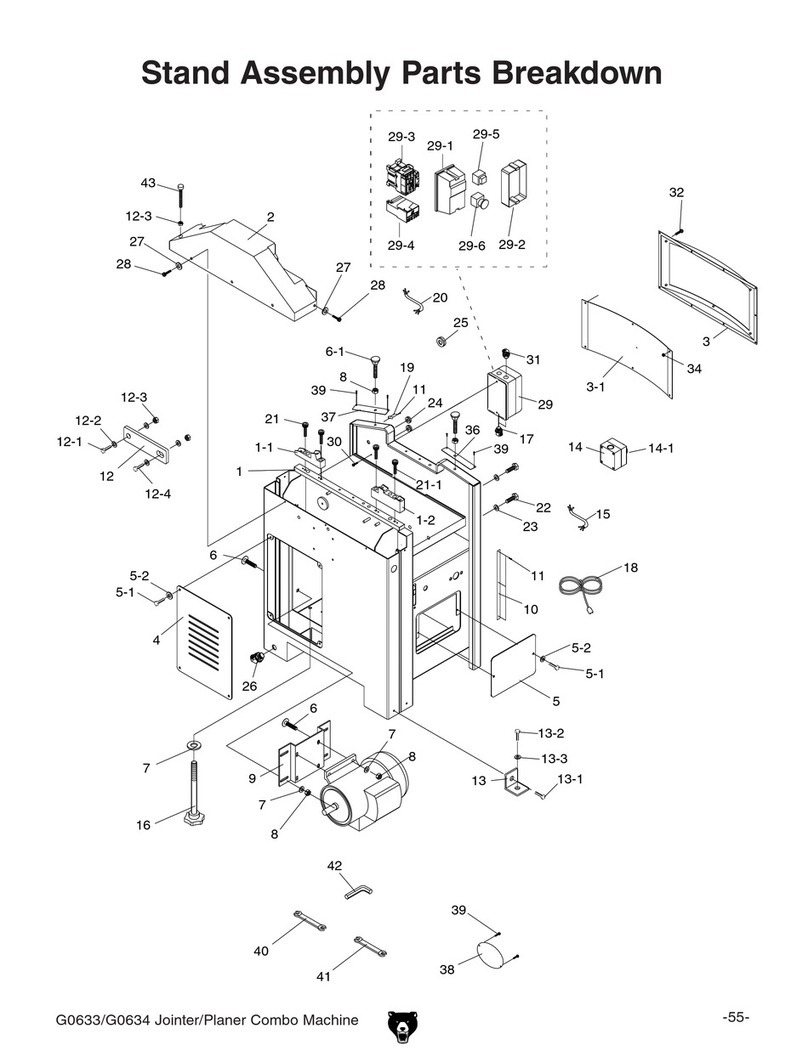
Grizzly
Grizzly G0634 Quick start guide
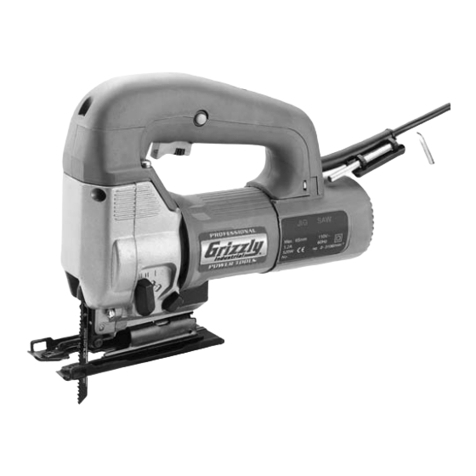
Grizzly
Grizzly G8994 User manual
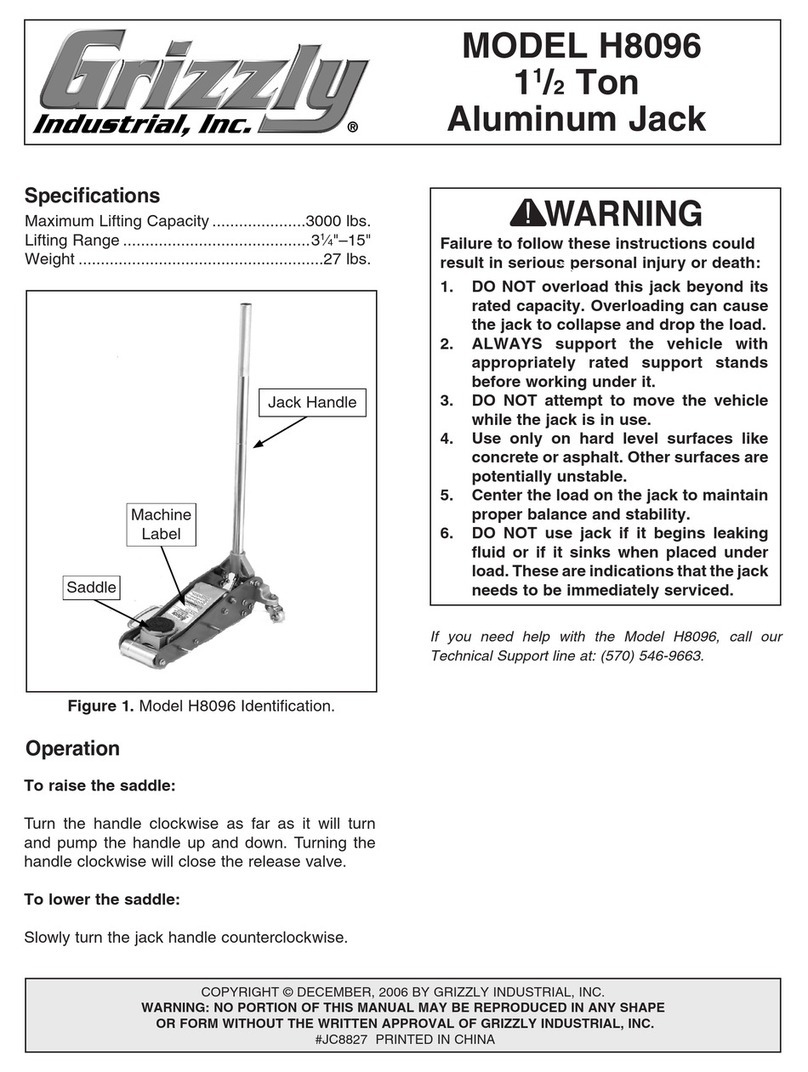
Grizzly
Grizzly H8096 User manual
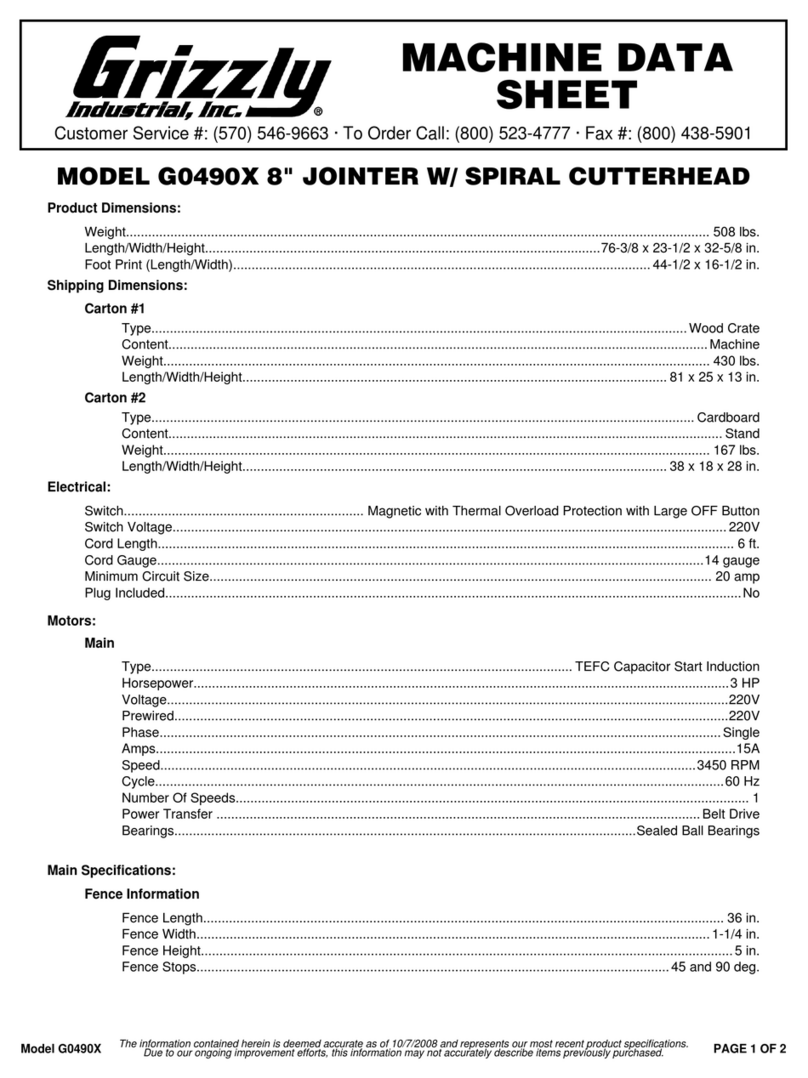
Grizzly
Grizzly G0490X Instruction Manual
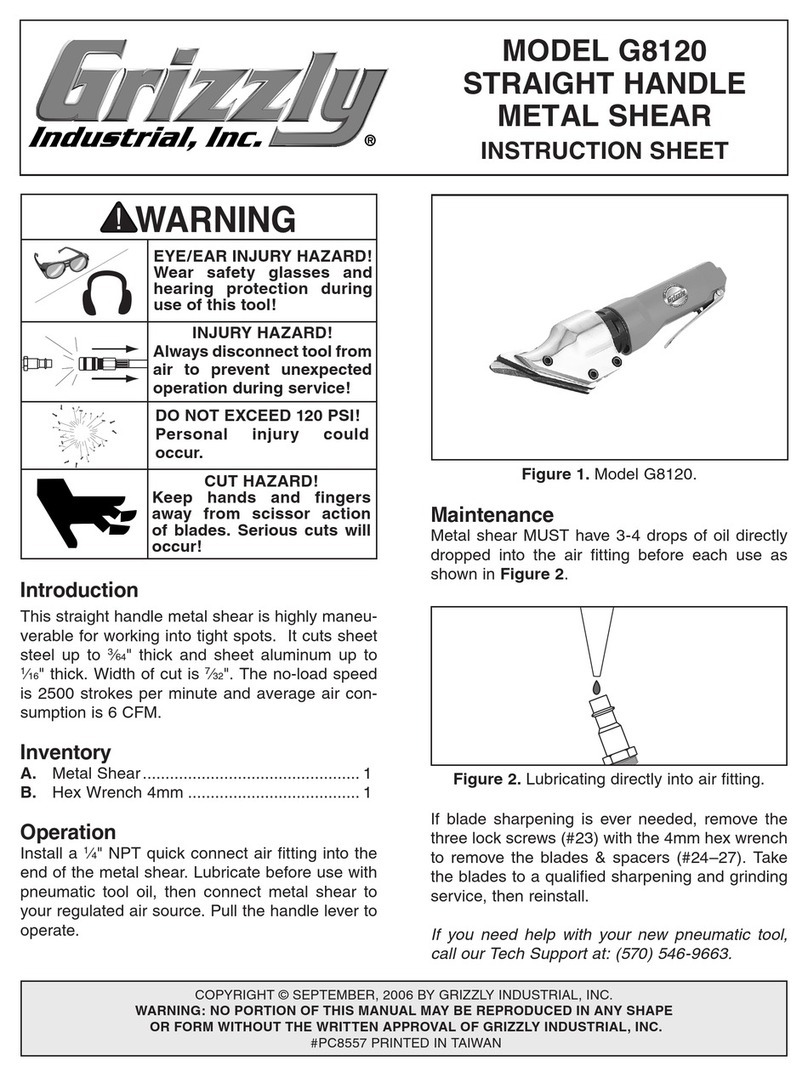
Grizzly
Grizzly G8120 User manual
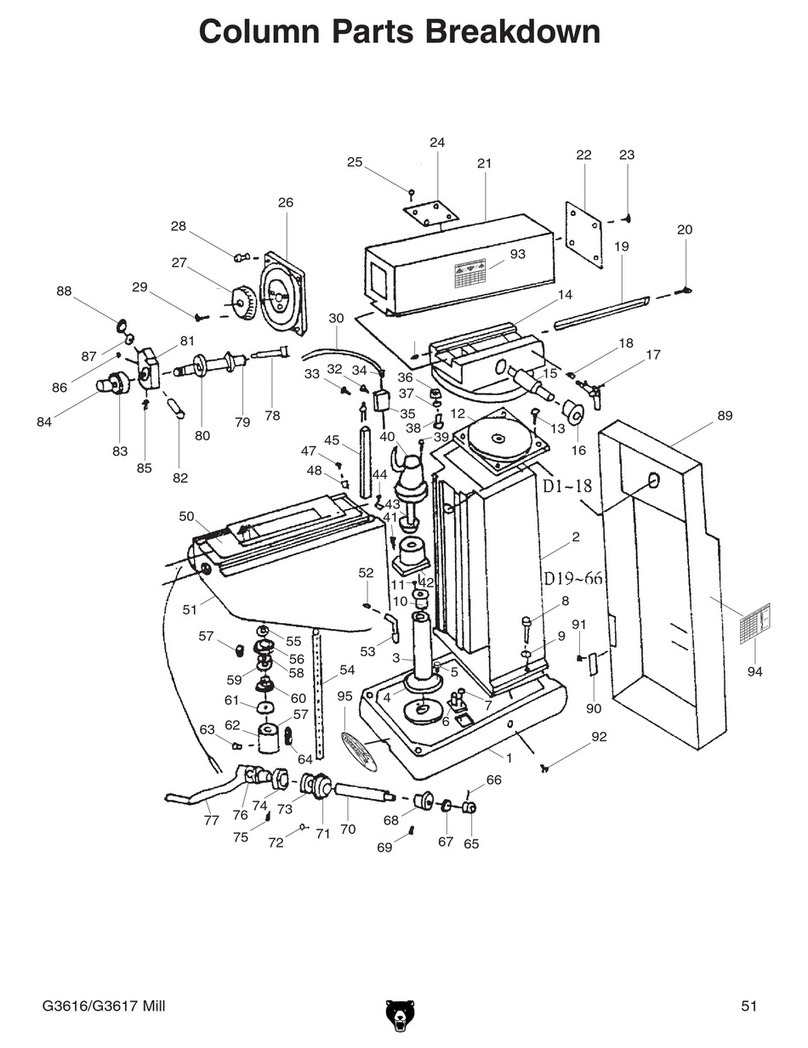
Grizzly
Grizzly G3617 Quick start guide
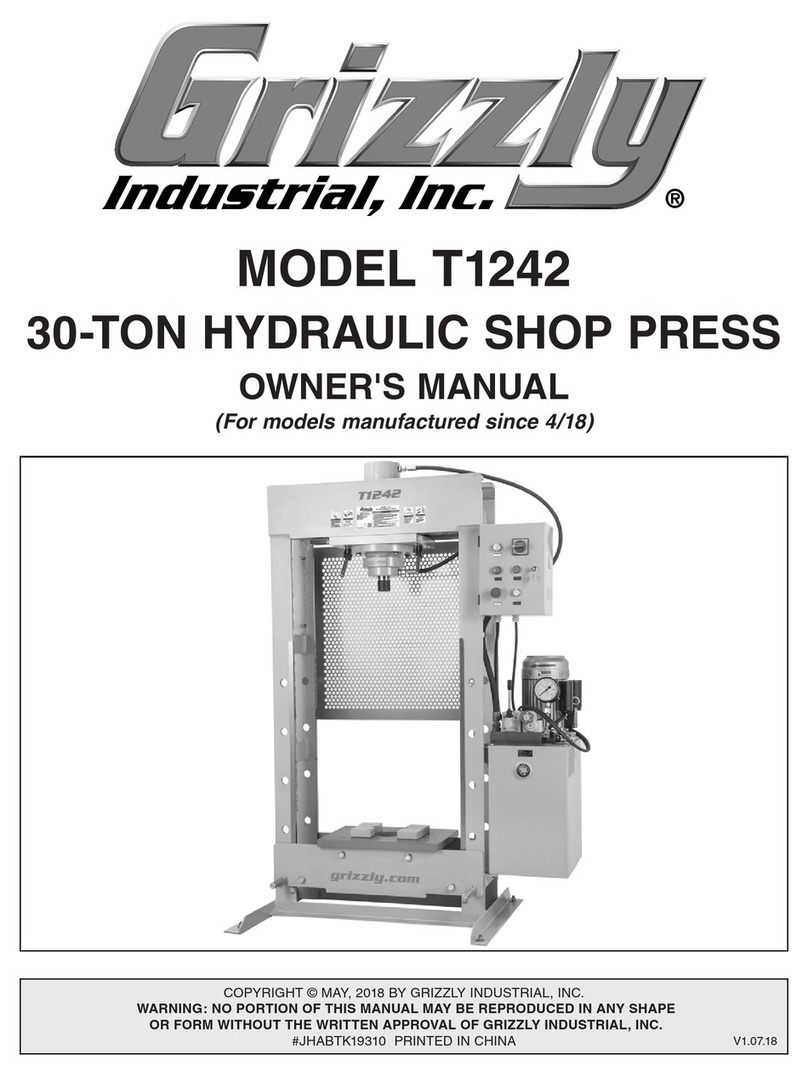
Grizzly
Grizzly T1242 User manual
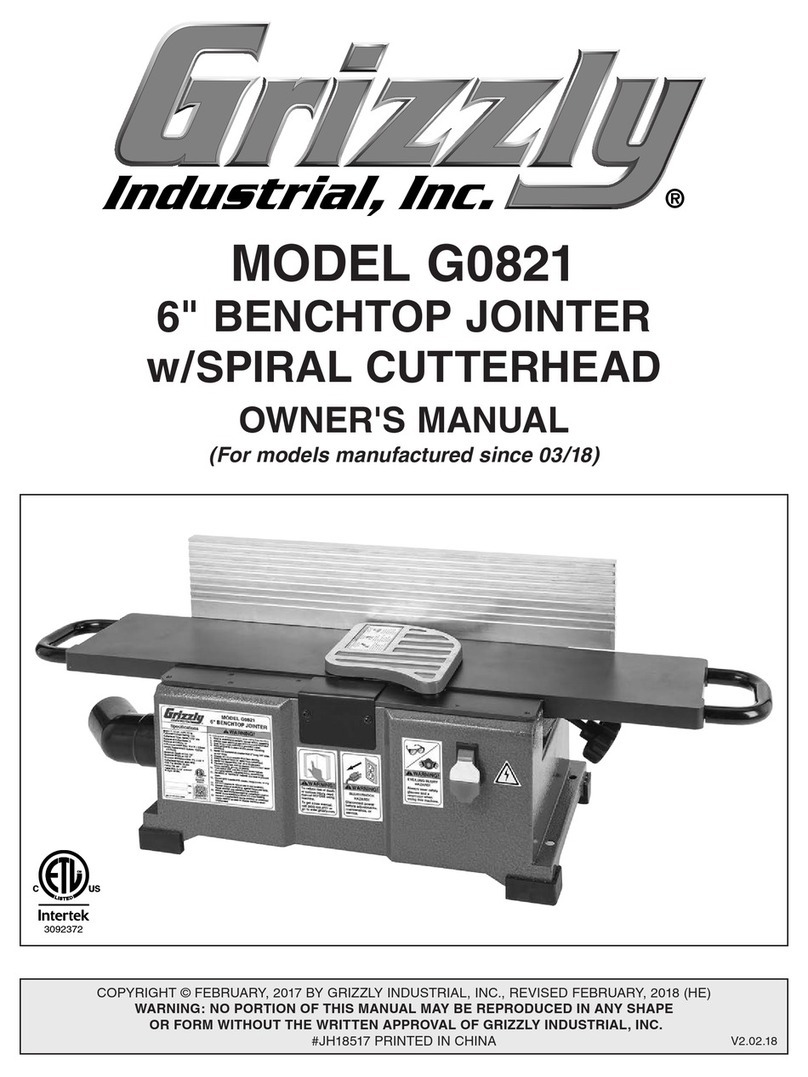
Grizzly
Grizzly G0821 User manual
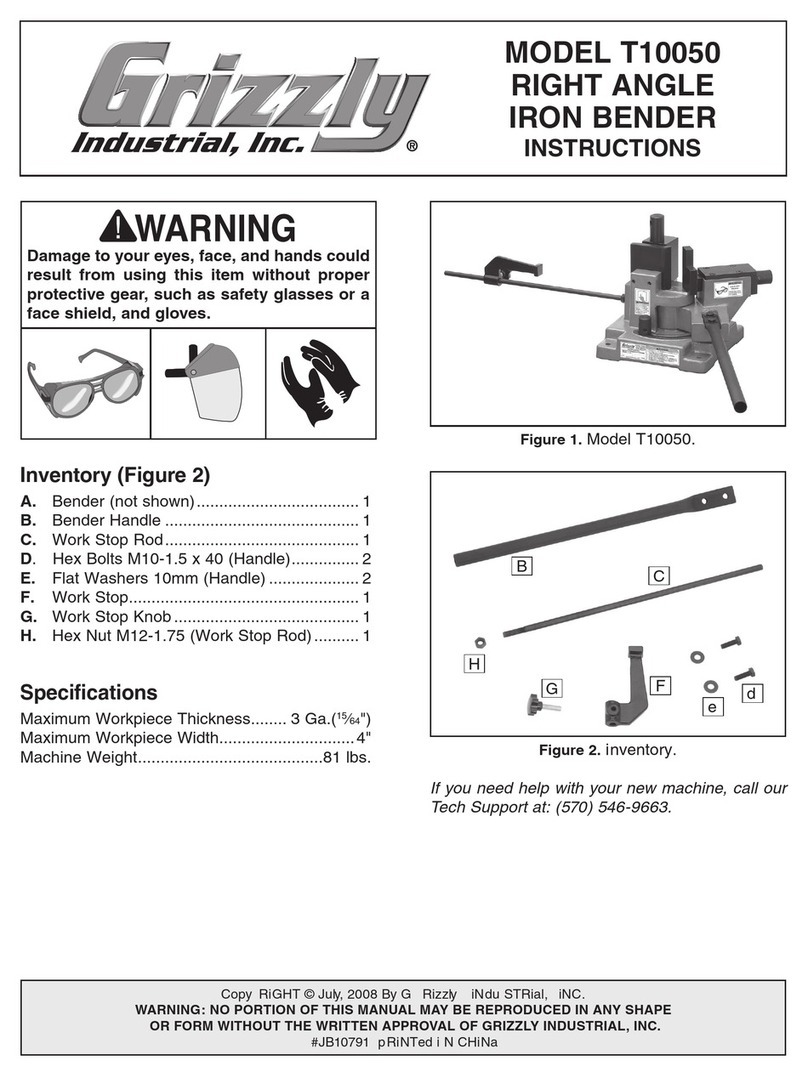
Grizzly
Grizzly T10050 User manual
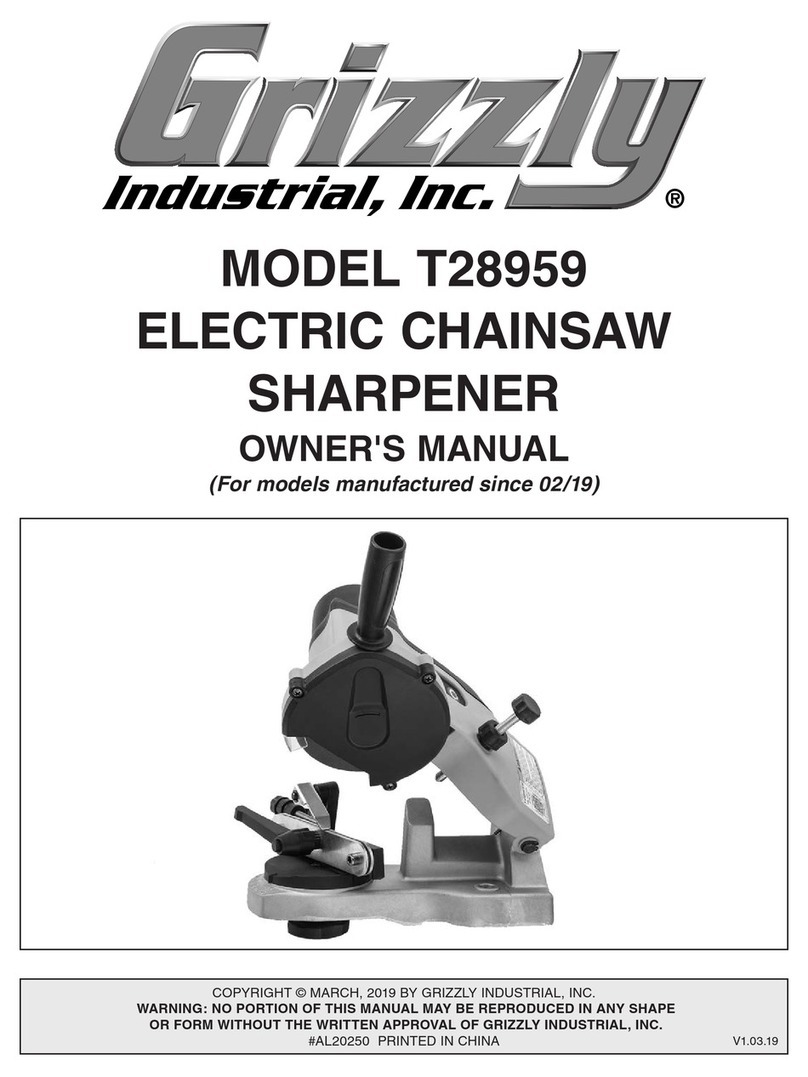
Grizzly
Grizzly T28959 User manual
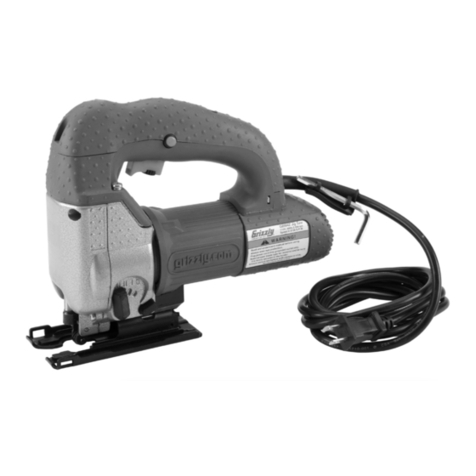
Grizzly
Grizzly G8994Z User manual
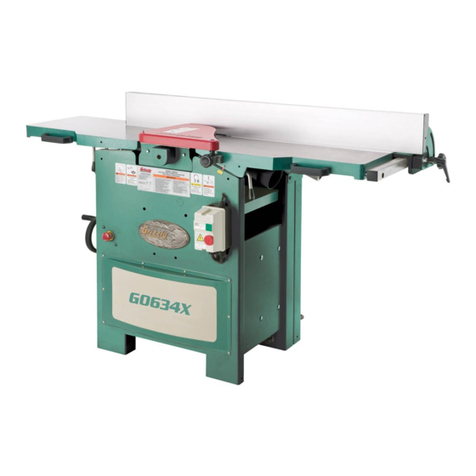
Grizzly
Grizzly G0634X User manual
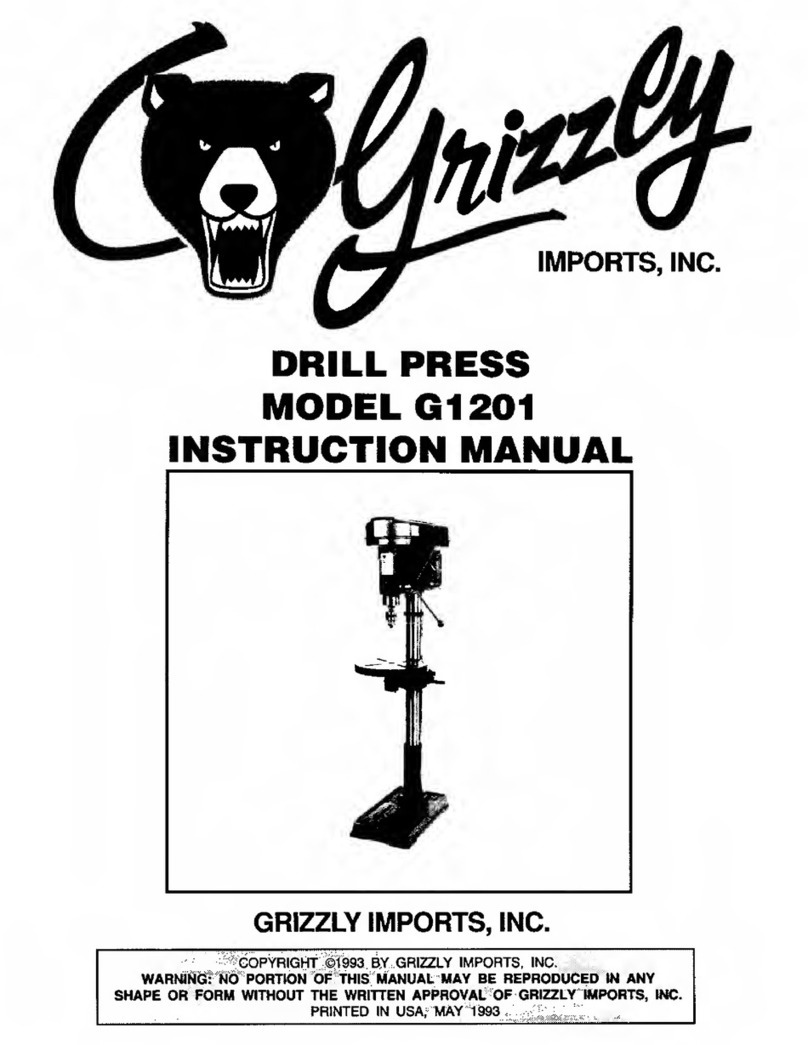
Grizzly
Grizzly G1201 User manual
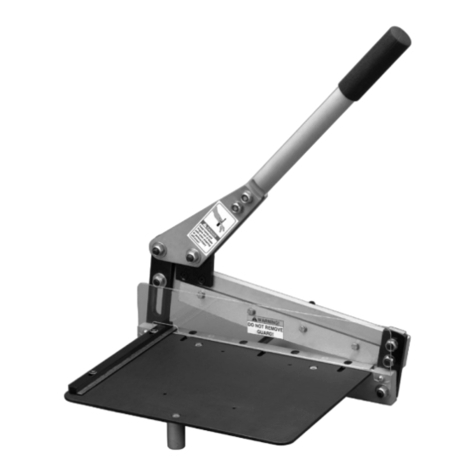
Grizzly
Grizzly T10051 User manual
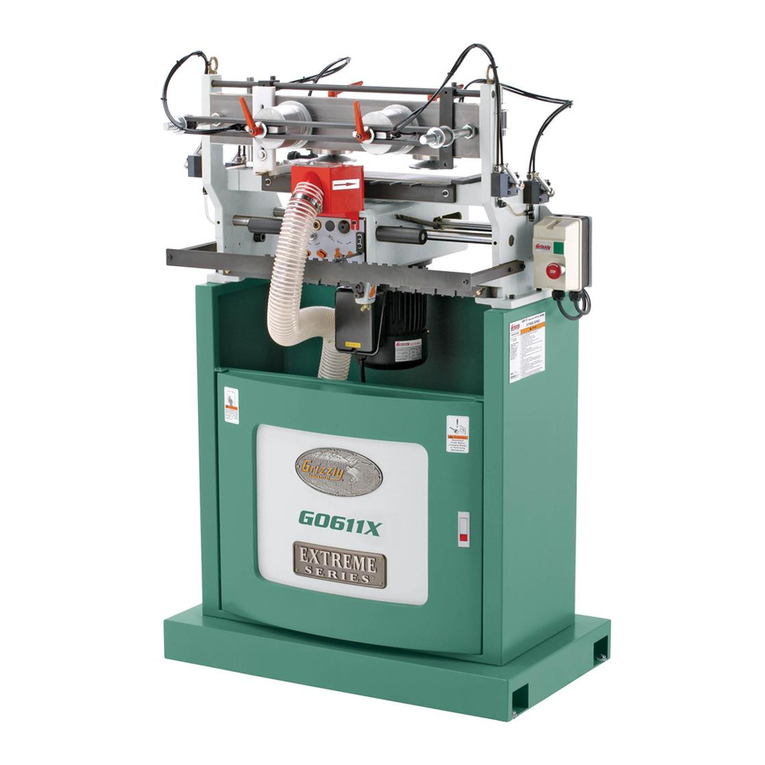
Grizzly
Grizzly G0611X User manual
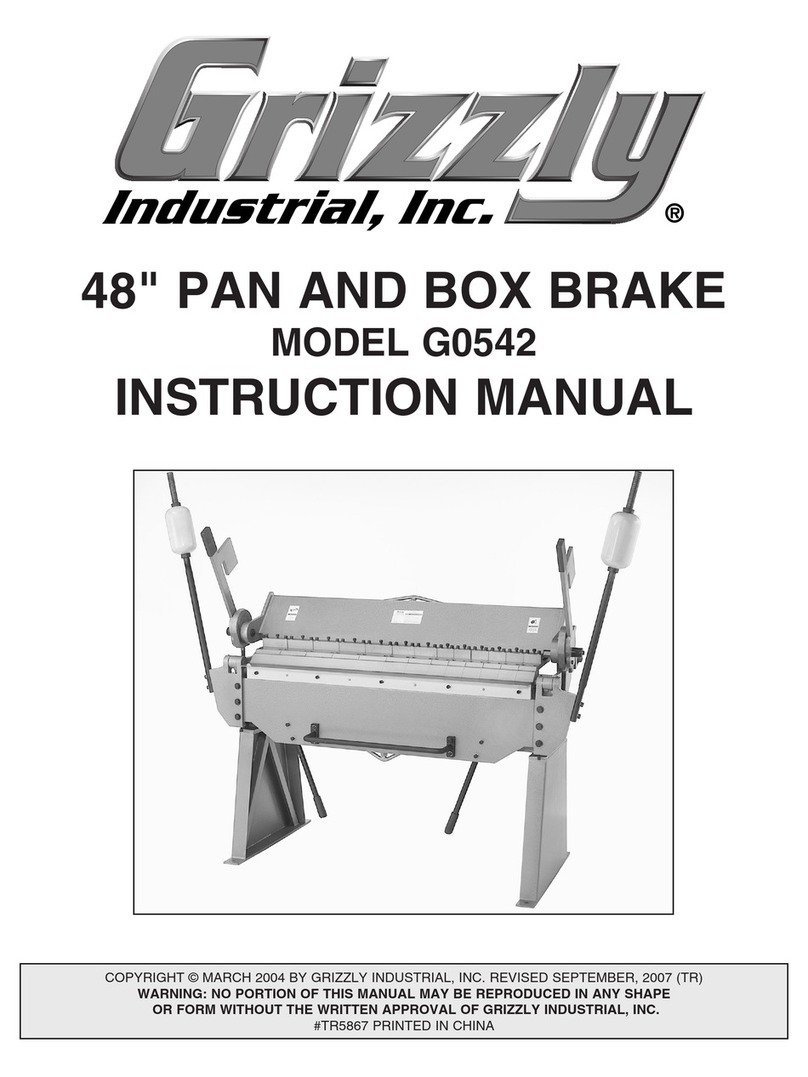
Grizzly
Grizzly G0542 User manual
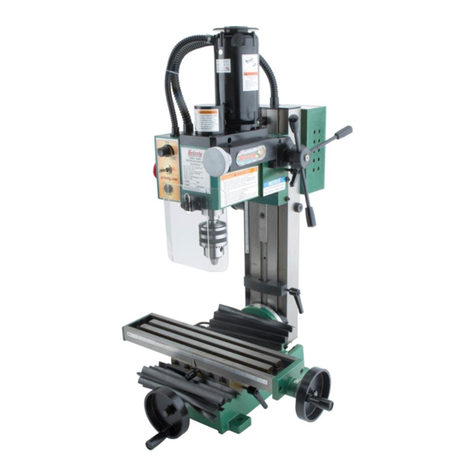
Grizzly
Grizzly G8689 User manual
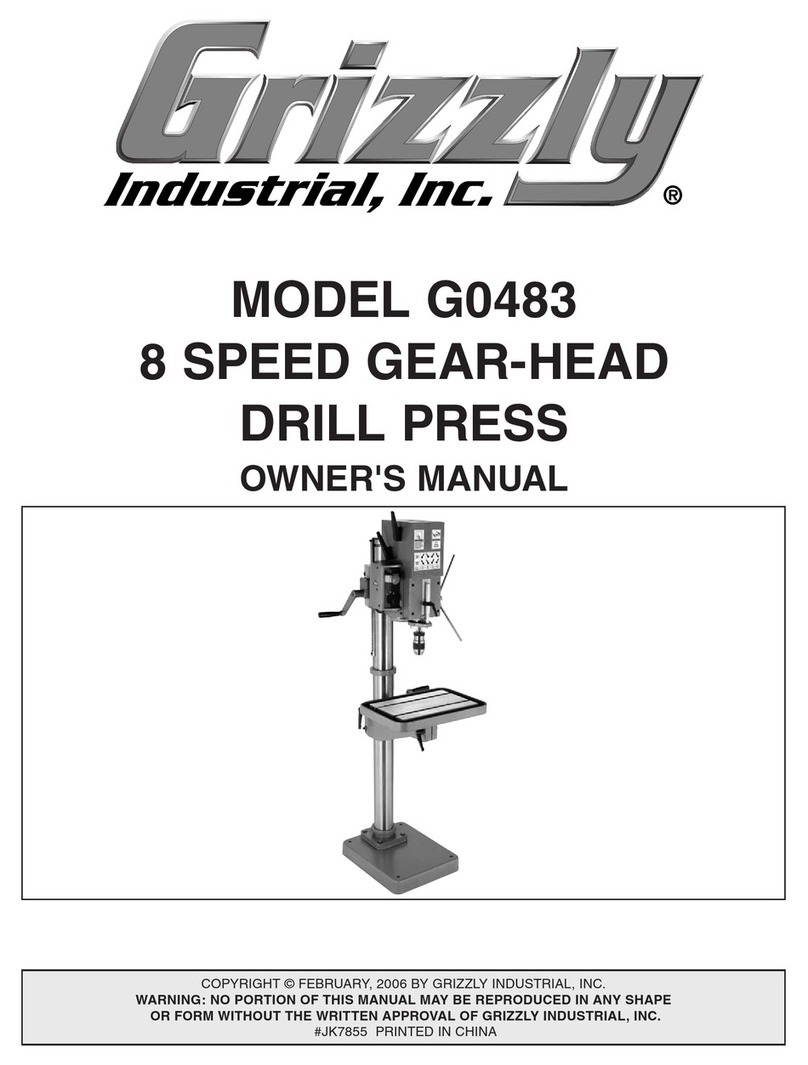
Grizzly
Grizzly G0483 User manual