Hanbay RD-DT-10.31 Series User manual

User Manual RDx-xxxDT-10.31
Page 1 of 8 www.hanbayinc.com | 1 800 315 4461
Rev.2020.4 hanbaysales@hanbayinc.com
RDx-xxxDT- 10.31
Contents
Installation pg. 1-3
Mounting pg 1
Wiring pg 2
Connecting power and signal pg 3
Manual override pg 3
Operation pg. 4-6
DIP Switch settings pg 4
Functionality pg 5
Torque Settings pg 6
Appendix pg. 6-7
Calibration pg 6
Trouble shooting pg 6
Dimensions pg 7
Factory Presets pg. 8
Installation
Mounting:
Holes for a mounting bracket. Holes are
threaded for ¼-20 and are approximately
.275” deep.
For dimensions see page 7.

User Manual RDx-xxxDT-10.31
Page 2 of 8 www.hanbayinc.com | 1 800 315 4461
Rev.2020.4 hanbaysales@hanbayinc.com
Turck connector not included
in the Class 1, Div 1 Groups
B, C & D rated explosion
proof enclosures.
Appropriate rated cable
glands or conduit should be
installed by qualified
personnel in accordance with
site requirements.
Wiring:
The actuator comes standard with a Turck 6 position connector and a 20’ cable with plug. Cut the cable to the
length required and then connect according to the following wire color schematic:
Wire color schematic for “Turck 6” cable:
Pin
Color
DC power supply only
6
White
+24VDC
5
Black
Power Gnd
4
Pink
Output TTL2
3
Grey
Output TTL1
2
Blue
Input TTL2
1
Brown
Input TTL1
Connect the power:
The RDx-xxxDT may be connected to voltages ranging from:
12 –24 VDC.
The power consumption will range from max. 3.0A to approx. min.100mA
when the actuator is active. When not moving, the actuator draws around
50mA.
Terminal
123456
GND
V+
DC Voltages
1 2 3 4 5 6
P1
*For non-explosion proof R-Series
Turck connector/cable pinout

User Manual RDx-xxxDT-10.31
Page 3 of 8 www.hanbayinc.com | 1 800 315 4461
Rev.2020.4 hanbaysales@hanbayinc.com
Connect the signal:
Locate the correct connection terminals as shown on the previous page, then connect your input signal on
pos. 1 and 2 as shown below. Feedback, if applicable is connected to positions 3 and 4.
.
1 2 3 4 5 6
P1
Input #1
TTL I/O Signals
Input #2
Output #2
Output #1
USER SUPPLIED
GND
GND
2
1
1
2
RL
(max drive
current
2mA)
External
I/O device
supplied
by user
< 1mA
RDx
RDx series with manual override
The actuator is certified for hazardous
locations.
The additional manual override gear case
and handle do not require a certification.
Operation of the manual override when
power is applied will be difficult as the
actuator will try to maintain the valve in
the position it has been commanded to.
Power should be removed if the valve is
to be moved manually.

User Manual RDx-xxxDT-10.31
Page 4 of 8 www.hanbayinc.com | 1 800 315 4461
Rev.2020.4 hanbaysales@hanbayinc.com
Operation
DIP switches:
The DIP switches allow you to change the
settings on your actuator. To flip a switch,
gently use a small flat-head screwdriver.
See chart below for DIP switch functionality.
Switches 1 and 2 set the actuator position control parameters. High settling speed settings are suitable for fast
positioning of light valves. Longer settling times will allow heavier valves to reach their target positions; trying to
use a fast settling setting on a high torque valve will increase current consumption when holding position, and
cause heating of the motor.
DIP 3
Reserved for custom function.
DIP 4
Sets direction of offset.(Offset only available in RDH, RDFand RDUseries)
DIP 5
Sets the highest amount of offset, typically 12°. NOTE: To set maximum offset DIP’s 5,6 and 7 will
need to be high for a total of 21°. The max. offset can also be set differently upon customer request.
DIP 6
Sets medium offset, typically 6°.
DIP 7
Sets the lowest amount of offset, typically 3°.
DIP 8
With DIP switch 8 in the ON position, the actuator will move to 4 positions. It will also alter the
function of the output signals. In the OFF position, the actuator is limited to three positions.
DIP 9
Run / Calibrate
Putting DIP switch 9 into the OFF position will disable the actuator positioning control, and the motor
will not move regardless of the input signals.
When DIP 9 is moved back into the ON position, the actuator will perform its homing routine, and
then move to the position commanded by the input signals.
DIP 10
DIP 11
Description
Approximate stall current
Off
Off
Low torque
0.75A
Off
On
Medium-low
1A
On
Off
Medium-high
2A
On
On
High torque
3A
Approximate stall torque
DIP 10
DIP 11
RDL
RDM
RDH
RDF
RDU (M-Train)
Off
Off
40 in-lbs.
120 in-lbs.
405 in-lbs.
756 in-lbs.
3348 in-lbs.
Off
On
53 in-lbs.
160 in-lbs.
540 in-lbs.
1008 in-lbs.
4464 in-lbs.
On
Off
60 in-lbs.
180 in-lbs.
608 in-lbs.
1134 in-lbs.
5022 in-lbs.
On
On
65 in-lbs.
195 in-lbs.
657 in-lbs.
1241 in-lbs.
5440 in-lbs.
DIP 12
DIP 12 sets the direction of rotation
DiP 1
DiP 2
Off
Off
Fastest settling
Use only for low torque valves
Off
On
Medium-fast
Typical setting
On
Off
Medium-slow
Typical setting
On
On
Slowest settling
Use for high torque valves
DIP switches. In this example DIPs 1, 2, 6 and 12 are on.

User Manual RDx-xxxDT-10.31
Page 5 of 8 www.hanbayinc.com | 1 800 315 4461
Rev.2020.4 hanbaysales@hanbayinc.com
Functionality of the RDx-xxxDT:
The RDx can operate as a 3-position or 4-position actuator. The 4th position is enabled by turning Dip 8 ON.
3-pos Functionality (Dip 8 OFF)
Input#1
(Pin 1)
Input#2
(Pin 2)
Action taken
High
High
Moves to or remains in center position
Low
High
Moves to or remains in right position
High
Low
Moves to or remains in left position
Low
Low
Moves to or remains in right position (Input#1 has
precedence over Input #2)
The feedback from the RDx-xxxDT is as follows:
Output#1
(Pin 3)
Output#2
(Pin 4)
Meaning High = 4.5vDC Low = 0.8vDC
High
High
Actuator output is in center position
High
Low
In Right position
Low
High
In Left position
Low
Low
Actuator is moving, or has stalled and given up trying to
reach a requested position.
You may retry to reach any position by cycling alternate
inputs and trying the original again. Repeated failures to
reach the position will require troubleshooting.
4-pos Functionality (Dip 8 ON)
Input#1
(Pin 1)
Input#2
(Pin 2)
Action taken
High
High
Moves to or remains in center position
Low
High
Moves to or remains in right position
High
Low
Moves to or remains in left position
Low
Low
Moves to or remains in back position
The feedback from the RDx-xxxDT is as follows:
Output#1
(Pin 3)
Output#2
(Pin 4)
Meaning High = 4.5vDC Low = 0.8vDC
Low
Low
Actuator is at requested position
High
Low
Actuator is moving
Low
High
Actuator has stalled. The stall can be cleared by making
the actuator turn in the other direction.
Direction of rotation and using Input 1
To change the direction of rotation on the actuator change the setting on Dip12 and power up the actuator again.
VERY IMPORTANT: Input 1 must always be used if only one input is used to operate the valve.
When the actuator is operated using input 1 an automatic calibration is done every time the valve
is actuated. This does not happen on input 2.
Right
Top View
onto valve or
other
appliance
Center
Back
Left
Top View
onto valve or
other
appliance
Center
Right
Left

User Manual RDx-xxxDT-10.31
Page 6 of 8 www.hanbayinc.com | 1 800 315 4461
Rev.2020.4 hanbaysales@hanbayinc.com
Torque Settings:
Effect of power settings and speed settings:
To accommodate different valves and other applications with different torque requirements, the actuator can be
set to apply different torque on the valve stem when in the seating mode. Please see table on pg. 4 to select the
power setting that is right for your application.
The actuator will use 100% of available torque to try and reach maximum speed. Current drawn will be limited
proportionally to the DiP setting applied actuator will automatically slow down and deliver the maximum available
torque for a given “Permanent Power Setting”.
Appendix
Calibration
The center position calibration routine can be initiated by switching Dip9 momentarily “on” then “off”. This will
cause the actuator to go through a series of movements to determine the proper center position. This function is
useful if the actuators output gear gets manually rotated while the actuator is powered down and can’t properly
realign to the center by itself.
Troubleshooting:
Upon noticing a problem, your first step should almost always be to recalibrate the actuator by switching DIP 9 on
then off, all while the actuator is powered. This alone can solve basic problems. See section 3 on this page for
more details.
If the actuator does not move, try following these steps:
1) Re-calibrate the actuator. This will move the actuator regardless of what signal it is receiving.
2) A sticking valve may be the problem. Remove the valve from the actuator, and re-test the actuator.
3) Remove power. Re-check the wiring and the power/signal apparatus. Power actuator, and re-calibrate. If
the problem persists, please call Hanbay for technical support.
Note: 66% setting and 100% setting may alter duty cycle:
Supply voltage needs to be min 14 VDC for 66% setting
- Supply voltage needs to be 16 VDC for 100% setting
- When operating above 20VDC and 66% power, Duty cycle is reduced to 50% - 25%
maximum.
At these levels, the electronics produce more heat which must be dissipated (depending on
environmental temperature)

User Manual RDx-xxxDT-10.31
Page 7 of 8 www.hanbayinc.com | 1 800 315 4461
Rev.2020.4 hanbaysales@hanbayinc.com
Main Dimensions:
RxL/RxM RxH
Desiccant sticks:
These sticks change colour when exposed to
moisture. When they change from the original
color, blue, to pink, the actuator has been
exposed to an excess of moisture.
Table of contents
Other Hanbay Controllers manuals
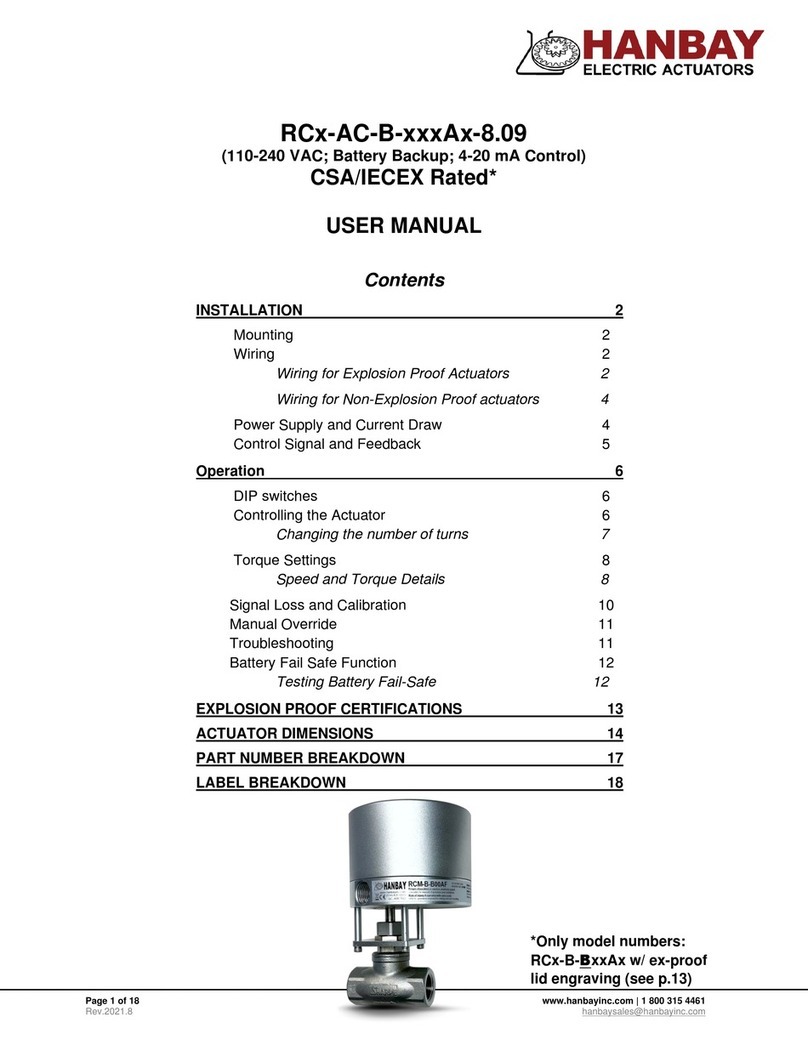
Hanbay
Hanbay RC Series User manual
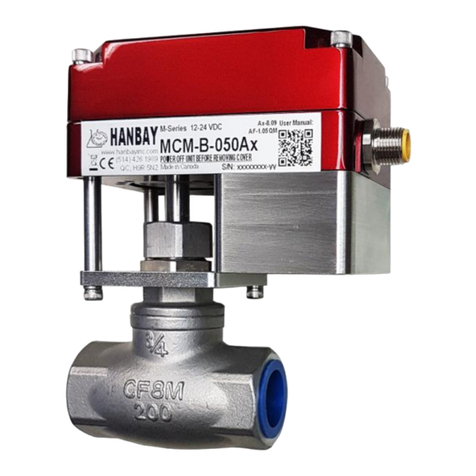
Hanbay
Hanbay MC-B-A-8.09 Series User manual

Hanbay
Hanbay M Series User manual
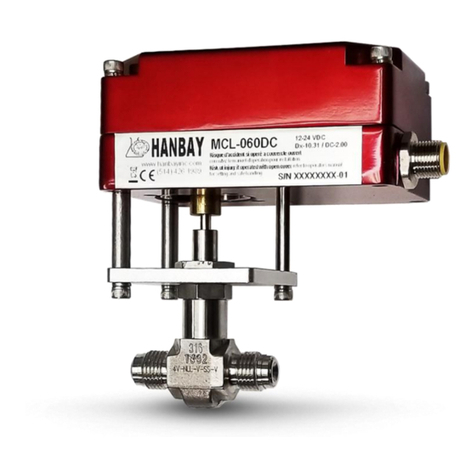
Hanbay
Hanbay MC DC-2.00 Series User manual
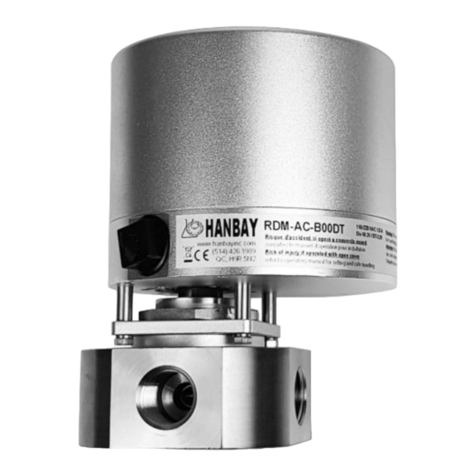
Hanbay
Hanbay RD-AC Series User manual
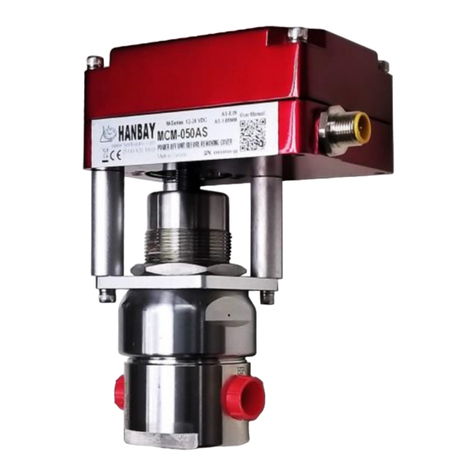
Hanbay
Hanbay MC-AS-1.05 Series User manual
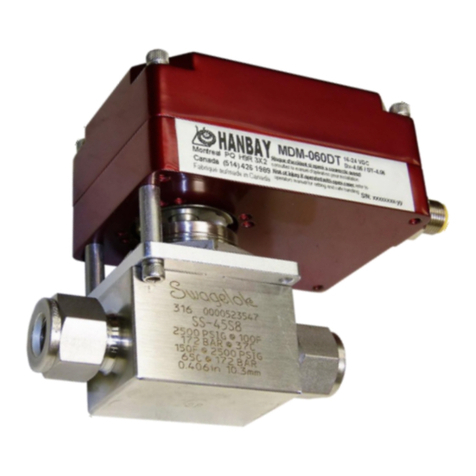
Hanbay
Hanbay MD DT-10.31 Series User manual
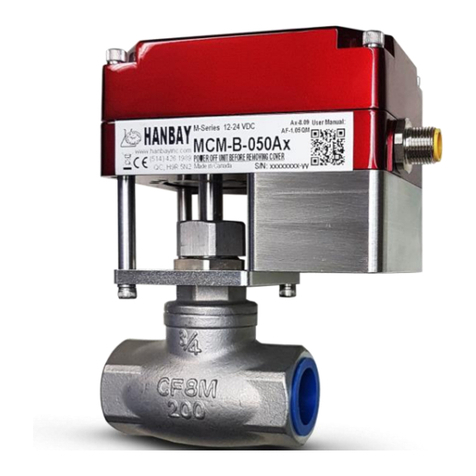
Hanbay
Hanbay MC A 8.09 Series User manual
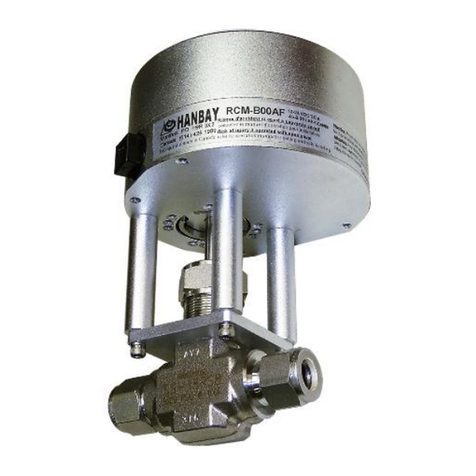
Hanbay
Hanbay RC AS-1.05 Series User manual
Popular Controllers manuals by other brands
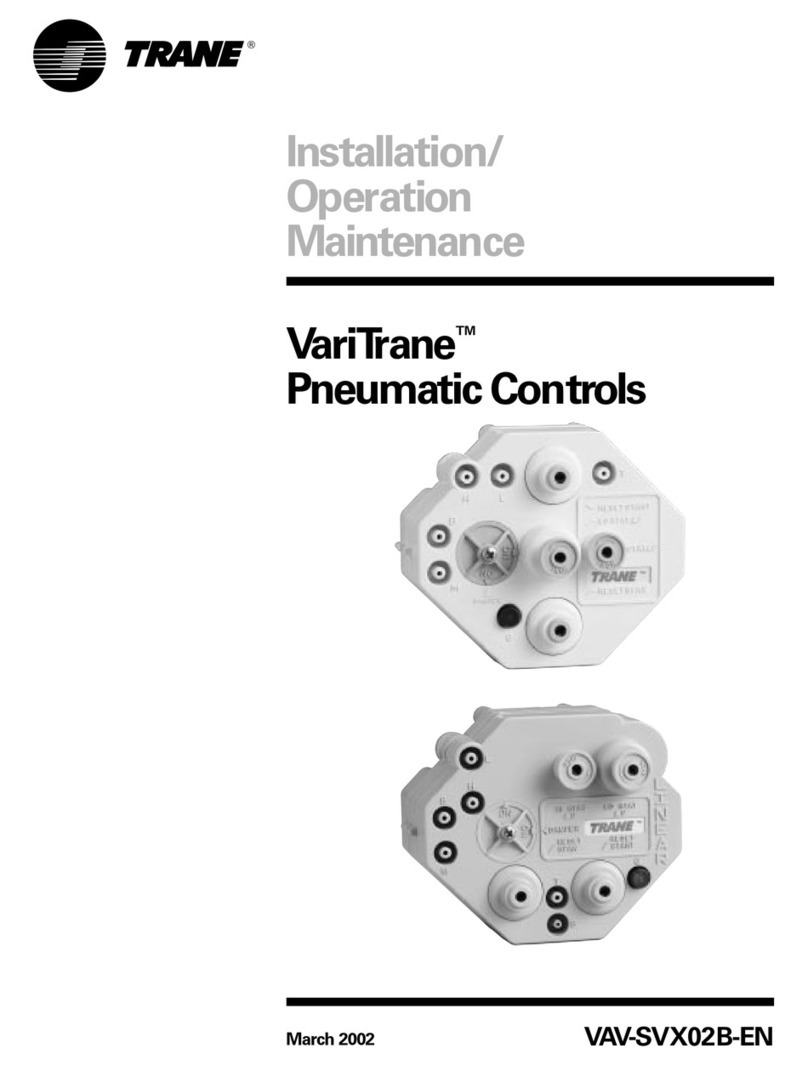
Trane
Trane VariTrane VAV-SVX02B-EN Installation operation & maintenance
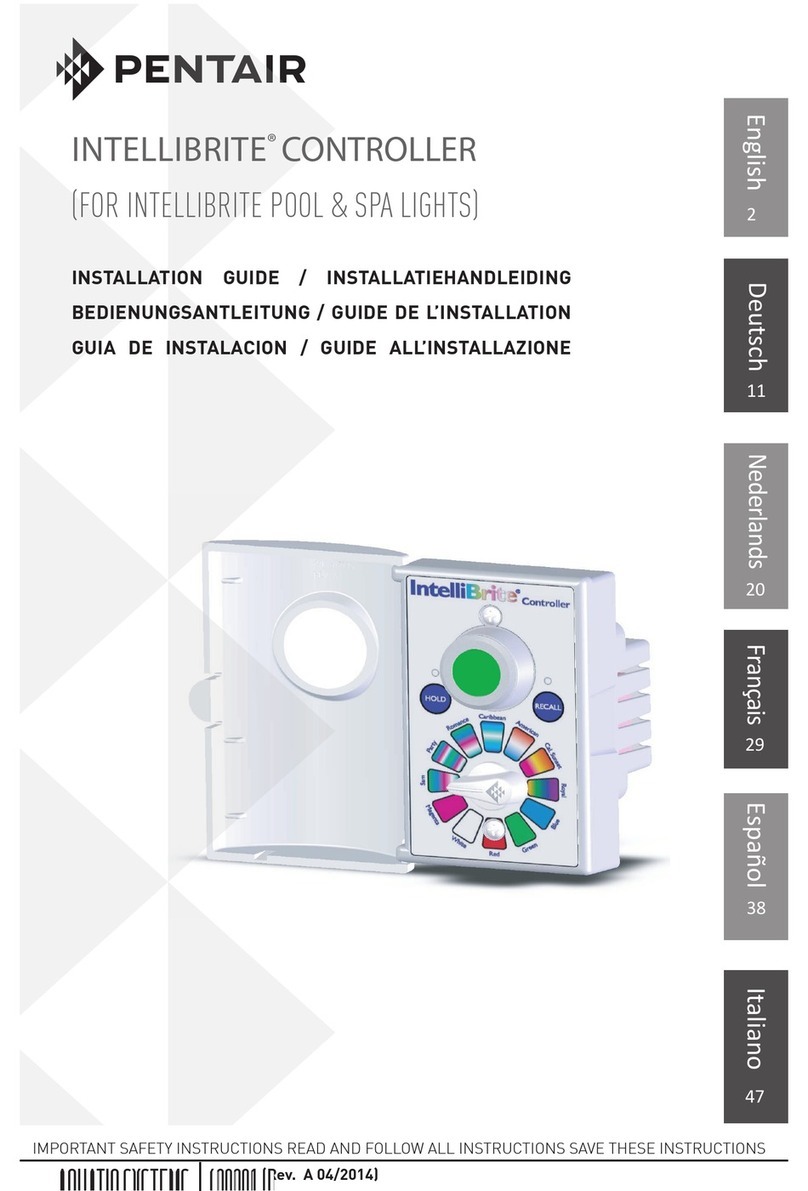
Pentair
Pentair IntelliBrite installation guide

ZyXEL Communications
ZyXEL Communications NXC2500 user guide
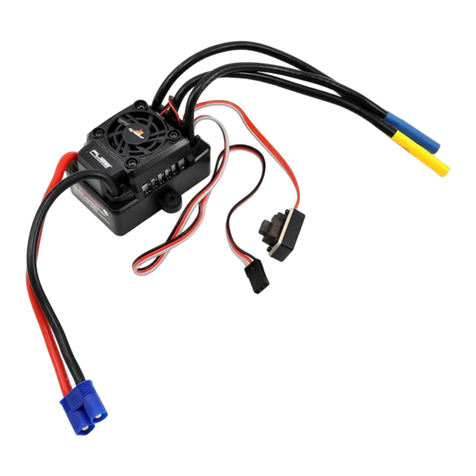
Dynamite
Dynamite FUSE DYN4955 instruction manual
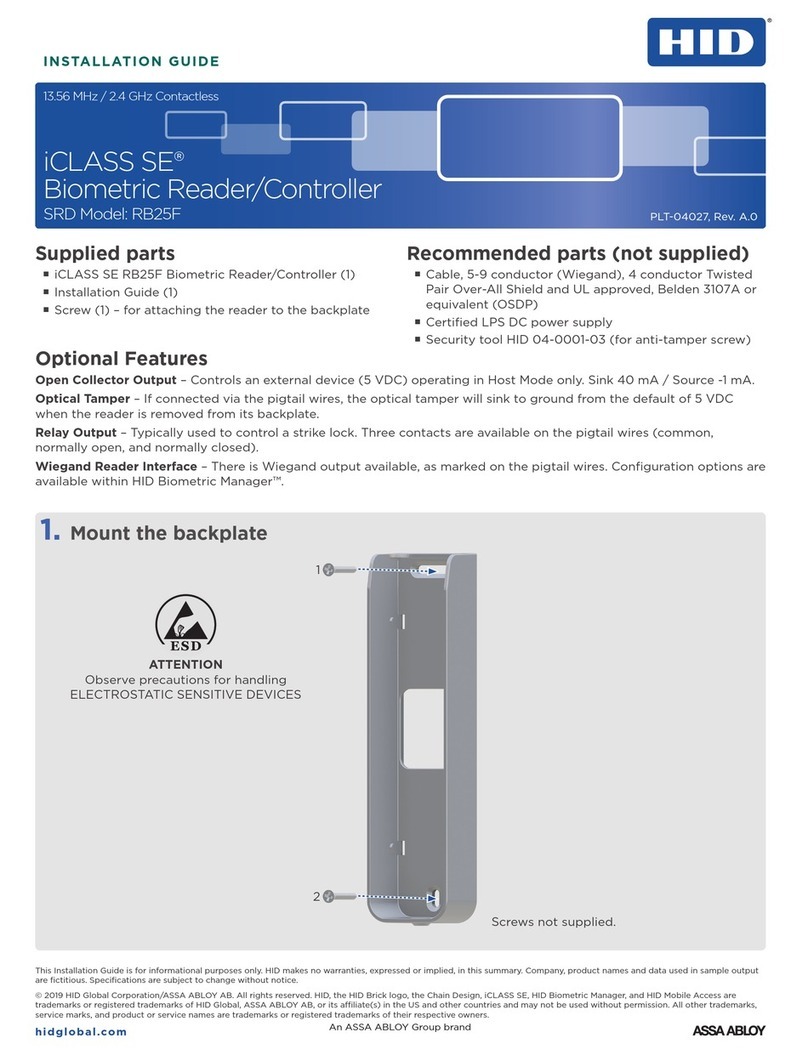
HID
HID iCLASS SE RB25F installation guide
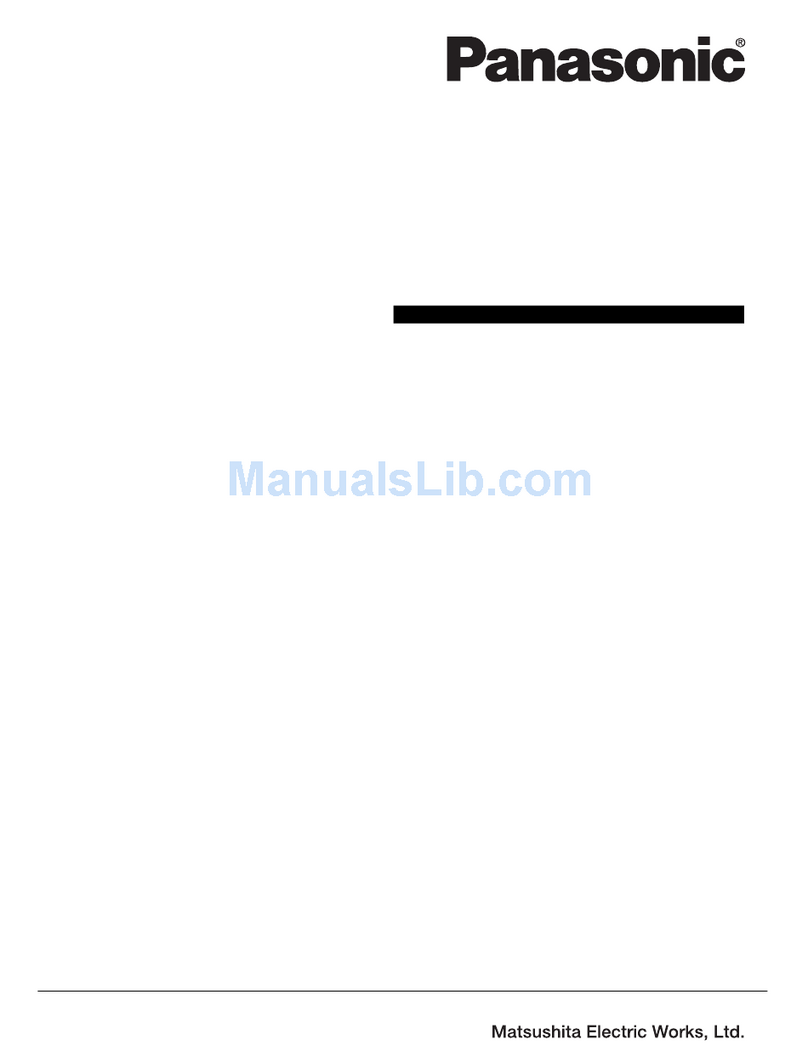
Panasonic
Panasonic FP3 Technical manual