heatco DF Series Installation and user guide

1
OPERATION, SERVICE AND
MAINTENANCE INSTRUCTION
ANSI Z83.25 (2017) –CSA 3.19 (2017)
Direct gas-fired process air heaters
!
WARNING:
FIRE OR EXPLOSION HAZARD
Failure to follow safety warnings exactly could result in serious injury,
death or property damage.
Be sure to read and understand the installation, operation and service
instructions in this manual.
Improper installation, adjustment, alteration, service or maintenance can
cause serious injury, death or property damage.
Do not store or use gasoline or other flammable vapors and liquids in the
vicinity of this or any other appliance.
WHAT TO DO IF YOU SMELL GAS
· Do not try to light any appliance
· Do not touch any electrical switch; do not use any phone in your building
· Leave the building immediately
· Immediately call your gas supplier from a phone remote from the
building. Follow the gas supplier’s instructions.
· If you cannot reach your gas supplier, call the fire department.
Installation must be performed by a qualified installer, service agency or gas
supplier.
This manual must be kept with the appliance for future reference.
Manufactured by:
Heatco Inc
50 Heatco Court
Cartersville, Ga. 30120DF-USM-MAN-LIST-Z83.25-1
DF Series
Direct Gas-Fired Heater Modules

2
The information provided in this manual applies to the furnace module installed as part of a
manufactured package system and to its operation, maintenance, and service. Refer to the
system manufacturer’s instructions for information related to all other components.
Table of Contents
I. Installation Requirements. . . . . . . . . 3
II. Installation. . . . . . . . . . . 3 - 4
III. Direct-Fired Heat Module Application. . . . . . . 4
IV. Paint Booth Application. . . . . . . . . 5
V. Installation in a Duct. . . . . . . . . 5
VI. Temperature Limit and Airflow Proving Switch. . . . . . 5
VII. Circulating Air Supply. . . . . . . . . 6
VIII. Burner Air Pressure Differential Adjustment . . . . . . 6
IX. Maximum / Minimum Airflow (VAV). . . . . . . . 6 - 7
X. Gas Supply, Piping and Connections. . . . . . . 8 - 9
XI. Direct Gas-Fired Heat Module Controls. . . . . . . 9
XII. Operation and Adjustment. . . . . . . . . 9 - 13
XIII. Burner Trouble Shooting. . . . . . . . . 13
XIV. Manifold Pressure Adjustment. . . . . . . . 14 –15
XV. Electrical Controls & Wiring.. . . . . . . . 15
XVI. Burner Maintenance. . . . . . . . . 16 –17
XVII. Filter Maintenance. . . . . . . . . . 17

3
I. Installation Requirements
All heater installations must be in accordance with the National Fuel Gas Code ANSI Z223.1 (NFPA 54) in the
United States and Can/CGA-B149 Installation Code in Canada, and all other applicable local codes and ordinances.
These requirements include but are not limited to:
·Gas supply, piping and connections
·Unit Location and clearances
All electrical equipment must be grounded and wired be in accordance with the National Electric Code (ANSI/NFPA
70) in the United States, and the Canadian Electric Code (CSA C22.1), in Canada
II. Installation
Verify the following before placing the equipment into service:
1. Electrical supply matches the voltage marked on the heater module Rating Plate.
2. Gas supply provided matches the Gas Type marked on the heater module Rating Plate.
3. Heater module is installed in orientation marked on vestibule. Orientation is specific to airflow direction
through the heating section of the unit.
4. The proper circulating/combustion airflow is traversing the burner at the designed airside burner air pressure
drop according to the heater module Rating Plate.
5. Furnace module is installed in a non-combustible duct or cabinet on the negative pressure side of the
circulating air blower.
6. An air flow proving switch is installed and wired to prove operation of the system circulating air blower.
7. A Manual Reset Limit is installed to shut-off furnace module in the event of low airflow conditions due to
filter blockage, coil blockage and or damper failure.
8. Removable access panels in duct immediately upstream and downstream of the heating appliance
cabinet to allow for inspection of the heat exchanger.
9. Electrical control panels mounted away from heated surfaces.
10. Completed electrical connections from direct gas-fired heater module to the control panel.
11. Properly supported wiring in vestibule area. Wiring should not contact metal surfaces which may be hot
during direct gas-fired heater module operation.
12. Pipe sealant resistant to LP gases on all thread gas connections.
13. For gas regulators located indoors and not equipped with vent limiters, a properly sized vent to the outdoors.
WARNING !
Gas-fired furnaces are not designed for use in hazardous atmospheres
containing flammable vapors or combustible dust, in atmospheres
containing chlorinated or halogenated hydrocarbons, or in applications
with airborne substances containing silicone.
WARNING !
The presence of chlorine vapors in the combustion air supplied to gas-
fired heaters presents a substantial corrosion hazard.

4
III. Direct-Fired Heat Module Application
Figure 1 –Typical Pull-Thru Installation
When the heater is operated as a process air heater in a paint booth application or other
applications with airborne particulate matter that could be detrimental to the operation of the
heater in the recirculating mode, the recirculated air must be filtered to remove particulates from
the air.
Filters must be installed in the return air duct system and have the means to facilitate inspection,
maintenance, cleaning, and access to fire protection devices.
Filters are required upstream of the direct gas-fired burner assembly. Particulate removal filters are not
provided by Heatco and must be approved by the authority having jurisdiction.
Minimum distance between the burner and blower should ensure proper stratification of the combustion
air. Uniform airflow MUST be directed over the profile plate opening.
The direct gas-fired heater module must be installed to fire with, and parallel to, the air flow.
The burner performance is dependent on its application and installation in the air handler.
Manufacturer does not guarantee combustion results prior to performing actual combustion tests. The
supply fan is positioned to draw air across the burner. Airflow across the burner must be laminar and
velocity must be within the specified range to insure desired capacity and turndown.
The direct gas-fired heater module profile plate mounting rails and profile plate sheet metal must be
securely fastened in the ductwork or cabinet. Provisions should be made so that downstream materials
within 48” to 60” are rated for at least 300oF.
WARNING !
Do not use burners, gas train, or manifold pipe as load bearing support during handling or
installation of direct gas-fired heater module in cabinet. Severe damage may result to burners,
profile plate, gas train, or pilot line assembly that result in unsafe operation, severe personal
Injury, death or significant property damage.

5
IV. Paint Booth Application
In a paint booth application, an interlock shall be installed in the field to lock out the paint spraying
equipment unless the process heater is operated in the ventilation air mode. The customer safety
interlock should be wired in series with the heat enable signal. See supplied wiring diagram.
An interlock shall be installed in the field so that when the heater is operated in the ventilation air mode
for an minimum of three (3) minutes at the start of the bake or drying cycle with the paint spraying
equipment locked out. The purge period is field adjustable by setting the Time delay relay purge (TDRP)
on the heater module control.
An interlock shall be installed in the field to initiate the operation of the heater fan in conjunction with the
operation of the exhaust fan. This interlock is provided by others and may be validated by an air flow
proving switch. An air flow proving switch should be wired in series with the heat enable and other
customer safety interlocks.
V. Installation in a Duct
An air straightener and/or turning vanes may be used in the elbows to keep the circulating air uniform around a turn.
See Figure 5 for Duct dimensions upstream and downstream of the direct gas-fired gas heat module.
Figure 5 –Elbow/Bend Duct Considerations
VI. Temperature Limit and Airflow Proving Switch
An airflow proving switch and manual reset temperature limit must be installed in the duct or cabinet for direct
gas-fired heater module application.
The airflow proving switch prevents operation of the gas direct gas-fired heater module in the event of failure or
restriction of the circulating air fan. The airflow probe should be installed upstream of the heating section (See Fig.
1) to detect a negative pressure. The airflow switch would open the heat enable circuit to the flame safeguard
control if the correct minimum pressure is not detected by the switch. An airflow proving switch kit is available for this
module.
A manual reset temperature limit provides additional protection from overheating of the appliance or air handler in
the event of improper operation or a circulating air fan failure. Under such conditions the integral primary high limit
would cycle the heater resulting in heat build-up and possible damage to the module or appliance. A properly
located temperature limit is critical (See Fig. 1). The temperature limit will function to shut-off the gas supply to the
burners by opening the temperature safety circuit to the flame safeguard control.

6
VII. Circulating Air Supply
DF Series Direct gas-fired heater modules should ALWAYS be installed with burners in parallel with the
circulating airflow direction.
The circulating air is to be uniform across the full length of profile plate opening.
The direct gas-fired module is designed to operate with all circulating air passing over the burners.
VIII. Burner Air Pressure Differential Adjustment
The direct gas-fired heater modules have an ideal standard design airflow condition of 2850 fpm and a flame length
of 15” at high fire (full input capacity 550 MBtuh per foot of burner) with 70 oF air.
Proper air velocity over the burner is critical to satisfactory operation of direct gas-fired units. If air velocity is not
within specifications, the unit may not operate efficiently or maintain satisfactory combustion emissions levels. To
obtain the desired operating condition, the proper pressure differential across the burner should be set as follows:
·Natural Gas: 0.60 in. w.c. (+/- .02”)
·Propane Gas: 0.75” in. w.c. (+/- .02”)
Connect a manometer to the burner differential pressure sensing probes (See Fig. 7) to measure the pressure drop
across the burner.
Adjust circulating air fan RPM with adjustable motor sheaves or VFD (if equipped) to achieve proper pressure drop.
Be sure motor amp draw does not exceed motor nameplate Full Load amperage (FLA).
Burner profile plates come with manually adjustable air baffles. These baffles may be used in the field at final
installation to optimize the circulating air velocity and pressure drop across the burners. The profile plate baffles are
constructed such that the width is fixed, and adjustments are incorporated above and below the burner (typical
adjustment is +/- 2” per baffle). If fan RPM cannot be adjusted, evenly adjust the baffles above and below the
burner, keeping the burner centered in the opening until the required pressure is obtained. To increase the static
pressure, lessen the opening size. To decrease the static pressure, increase the opening size.
If the burner baffles have been adjusted, this process may need to be repeated until the proper pressure drop is
obtained. This adjustment will change the air quantity delivered by the unit, so recheck delivered air quantity.
IX. Maximum / Minimum Airflow (VAV)
A variable air volume (VAV) option is recommended when a building’s exhaust volume may vary. This option
enables the make-up air volume to track the exhaust volume, providing only the required volume of make-up air.
A burner bypass damper is required for proper operation of variable volume units. It functions to maintain proper
combustion by providing constant airflow over the burner as the air volume traversing the burner changes.
At design airflow, the bypass damper will be fully open and approximately 50% of the total airflow will pass through
damper area, while the remaining air will flow over the burner. As the supply air is reduced, the bypass damper will
begin to close. This reduces the amount of air passing through the damper area and maintains a constant volume of
air passing over the burner. At minimum airflow the bypass damper will be closed and all the air will flow through the
burner profile plate opening. Thus, airflow through the burner profile stays comparatively constant throughout the
range of operation.
A damper bypass with damper control monitoring burner pressure drop may be installed to ensure proper operating
burner pressures. A two-position damper with potentiometer or modulating damper with Photohelic control may be
used.
When providing a variable speed blower fan, the burners can operate normally at a 50% turndown without adding
dampers. Design burner pressure drop should be 1.0” w.c. When the blower is turned down 50% the burner pressure

7
drop will be close to 0.25” w.c. These operating parameters are within the combustion air switch high and low limits
(0.2” w.c. to 1.2” w.c.).
Figure 6 –Variable Profile Plate Damper Construction
Figure 7 –Component Locations (Typical)
Profile
Modulating
Dampers

8
X. Gas Supply, Piping and Connections
1. Installation and sizing of piping must conform with local building codes and ordinances, or with ANSI Z223.1 the
National Fuel Gas Code. In Canada, installation must be in accordance with CAN/CGA –B149.1 Installation
Codes.
2. Use a pipe sealant resistant to LP gases on Gas supply connections to heater.
3. Properly support gas train components with back-up wrench, during supply pipe installation to prevent
loosening valve or damage to burner assembly or manifold.
4. Gas piping must be sized for the total Btu input of all units (heaters) serviced by a single supply.
5. Be sure that gas regulators servicing more than one heater have the proper pipe and internal orifice size for the
total input of all heating units serviced by the regulator. (See Figure 8)
6. Direct Gas-Fired modules require a minimum inlet gas pressure. These pressure values are specific to the job
site location. See burner module ratings plate.
7. Connect a fitting suitable for connection to a pressure gauge capable of measuring gas pressure to 1/8” NPT tap
provided on the inlet side of the gas valve or manual shut-off valve tapping (See Figure 7). Measure inlet
pressure to each module serviced by a single regulator with all modules in operation. (See Figure 8)
Figure 8
8. A drip leg (sediment trap) and a manual shut off valve must be provided immediately upstream of the gas control
on the heating unit. To facilitate servicing of unit, installation of a union is recommended. (See Figure 9)
Figure 9
9. The burner module gas piping was leak tested prior to shipping. However, during shipping and installation
connections may have loosened. Check for leaks using a soap solution and correct any leaks before placing
direct gas-fired heater module in operation.
10. Vent valves (when used) must be piped to the outdoors and outside the vestibule cabinet and in accordance with
applicable codes.
WARNING !
1. All field gas piping must be pressure /
leak tested prior to operation. NEVER use
an open flame to check for leaks. Use a
soap solution or other leak detecting
solution.
2. Gas pressure to appliance controls must
never exceed what is found on the rating
label.
WARNING !
1. When pressure testing at ½ PSI or less,
close the manual shut-off valve on the
appliance before testing.
2. When pressure testing gas supply line at ½
PSI or higher, close manual gas valve and
disconnect heater from supply line to be
tested. Cap or plug the supply line.

9
Inlet Gas Supply Pipe Connection Sizes
Gas supply pipe connection sizes are based on definitive job site specifications. The gas train design is based on
fuel type, full rate capacity, design inlet gas supply pressure, pressure drop, valve arrangement, and local or national
gas piping codes.
Each direct gas-fired heater module is supplied with a gas train piping diagram showing arrangement, sizing,
and selection.
XI. Direct Gas-Fired Heat Module Controls
Customer Air Control:
CA (Customer Provided Modulating Signal): The integral Maxitrol SC11 converts a building controller’s DC output
signal of 4-20 mA or 0-10 VDC to a 0-20 VDC signal to control the Maxitrol Selectra modulating valve. See Figure
10A.
Discharge Air Controls:
DA (Discharge Air): The integral Maxitrol A1014R references a desired set point temperature (either set on the
A1014R or an optional remote dial selector) to the measured discharge air duct temperature, The A1014R outputs
the 0-20 VDC signal to the Modulating valve to modulate the gas input of the gas burner. See Figure 10B.
DR (Discharge Air w/ Room Override): Provides space temperature control by raising the discharge air
temperature to a pre-selected point –when used in conjunction with the remote temperature selector.
DI (Discharge Air w/ Inlet Air Sensor): Provides inverse change in discharge air temperature for each degree change
in inlet air –when installed in a convenient duct location upstream of the burner.
Room Air Controls:
RA (Room Air w/ Selectrostat): The integral Maxitrol A1044R references a desired set point temperature set by
the Selectrostat in the heated space, to the measured room air temperature and then outputs a 0-20 VDC signal to
the Modulating valve to modulate the gas input of the gas burner. See Figure 10C.
RR (Room Air w/ Remote Sensing &Temperature Selector): The Maxitrol A1044R references a desired set point
temperature set by a remote temperature selector (does not have to be in the heated space), to the measured room
air temperature and outputs the 0-20 VDC signal to the Modulating valve to modulate the gas input of the gas
burner.
XII.Operation and Adjustment
SEE Heatco website for information and start-up procedure videos.
1. Most direct gas-fired heater module modules come with a pilot. If the module is < 400 MBH it is equipped with a direct spark
ignition device that automatically lights the gas burner. DO NOT try to light burners by hand.
2. BEFORE OPERATING, leak test all gas piping up to and including heater gas valve train. Smell around the unit area for gas.
If odor of gas is detected, DO NOT attempt to place heater in operation until source of gas leak is identified and corrected.
3. Use tools with only hand force. If regulator adjustments do not operate by hand force, replace gas valve prior to starting the
unit. Forcing or attempting to adjust or repair the gas valve may result in fire or explosion.
4. Each DF module comes with a Time Purge Delay Relay. This Time delay relay pauses the call for heat signal to the ignition
control for aset time. This time is factory set during operation tests. In the field this Purge Time Delay Relay may be adjusted
to satisfy the standard listing of (4) four complete air changeovers in the heater cabinet section and attached discharge duct
work. This time can change based on job specific installations.

10
Start-up
1. A pressure tap is used to measure the differential at the burner and to set high fire gas pressure (See Manifold Pressure
Adjustment on Page 17-18). The manifold pressure tap is 1/8” and located between modulating valve and the burner(s).
2. Close the inlet manual shut off valve and open the manual shut off located between the modulating valve and the burner.
Turn the circulating blower on to full operating CFM and record the negative pressure on a u-tube manometer or gas
pressure gauge. This reading is used for high fire burner pressure adjustment during operation.
3. After recording the negative burner manifold pressure, temporarily leave the manometer attached to the 1/8"tap. It will be
used later to check high fire gas pressure. Close the manual shut off valve located between the modulating valve and the
burner.
4. Open the inlet manual shut off valve. Verify supply inlet pressure does not exceed maximum rated gas pressure as
stated on the rating plate. See Figure 8 for measuring location.
5. Set the supply gas pressure at the stepdown regulator (normally outside of the enclosure if one is installed),
according to the nameplate rating inlet gas pressure specifications.
6. Before proceeding, check Start-up wiring changes for the corresponding installed heater control (Step 12). Make
necessary wiring changes only when the module is powered OFF.
Only perform Steps 7 - 10 if a pilot is installed.
7. Place a u-tube manometer or gas pressure gauge on the tee at the downstream side of the pilot pressure regulator. Open
the inlet manual gas valve and close the manual gas valve downstream of the modulating valve.
8. Supply correct source voltage to heater control. Give a call for heat (close contacts between T1 and T2), Once
flame safeguard lights the pilot, adjust the differential pilot pressure regulator to 3.5 in w.c. for natural gas or 2.0 in w.c. for
LPG.
9. Verify that the burner flame control has a flame signal of 2-5 UA or 2-5 VDC.
10. Remove the call for heat (open contacts between T1 and T2), and open the manual gas valve downstream of the
modulating valve.
11. Give a call for heat (close contacts between T1 and T2). Allow flame safeguard to ignite the pilot (if installed), open
main gas valve(s), and prove the main flame.
12. Depending on which Burner Control is installed follow subsequent steps for each controller type to check full input
range of the gas modulation.
CA: Provide 10 VDC to terminals 5 & 6 on the SC11 (See Figure 10A) signal conditioner control. Polarity is sensitive
(Positive to Terminal 6, Negative to Terminal 5). After a 15 second warm up period the unit will run at high fire. Check
that manifold pressure is manifold pressure recorded on Ratings Label. If high fire manifold pressure adjustment is needed
(See Manifold Pressure Adjustment) and a MR212 modulating valve is installed, see Figure 11 for adjustment location.
If a M 411, 511, 611 modulating valve is installed, adjust high fire manifold pressure by adjusting the combination
gas valve (See Figure 13 or 14), or the Regulator Valve upstream of main gas valve(s).
Provide 0 VDC to terminals 5 & 6 on the SC11 signal conditioner control. Heat module will run at low fire. Manifold
pressure will be negative. Check to make sure that there is not a loss of flame. If manifold pressure
adjustment is needed see Figure 11 or 12 for low fire bypass adjustment location. View flame through viewport
to ensure there is a steady even flame across the full length of the throat of the burner (See Figure 17).
DA / DI / DR: If using a remote Temperature selector Remove the wire lead from terminal 4 on the Maxitrol A1014R controller
to run unit at full high fire. Check that manifold pressure correlates to the differential manifold pressure recorded on Ratings
Label. If high fire manifold pressure adjustment is needed (See Manifold Pressure Adjustment) and a MR212 Modulating
valve is installed, see Figure 11 for adjustment pot location. If a M 411, 511, 611 Modulating valve is installed, adjust high
fire manifold pressure by adjusting the Regulator Valve upstream of on/off valves, or the combination gas valve (See Figure
13 or 14).
Remove the wire lead from terminal 6 on the Maxitrol A1014R controller to run unit at low fire. The manifold pressure will be
negative. Check to make sure that there is not a loss of flame. If manifold pressure adjustment is needed
see Figure 11 & 12 for low fire bypass adjustment location. View flame through viewport to ensure there is a
steady even flame across the full length of the throat of the burner (See Figure 17).
After checking both high and low fire, power down module, correct dip switch setting if needed, replace remote
temperature selector if needed, and select correct temperature setting either using onboard pot or remote selector.

11
RA / RR: If using a remote Temperature selector, remove the leads off of Terminals 4 & 5 on the Maxitrol A1044R.
(See Figure 10C) Place the supplied 12,000 Ohm resistor across Terminals 4 & 5. Rotate the on board
temperature selector dial fully CW to run unit at full input high fire. Check that manifold pressure correlates to the differential
manifold pressure recorded on Ratings Label. If high fire manifold pressure adjustment is needed (See Manifold Pressure
Adjustment) and a MR212 Modulating valve is installed, see Figure 11 for adjustment location.
If a M 411, 511, 611 Modulating valve is installed, adjust high fire manifold pressure by adjusting the Regulator
Valve upstream off on/off valves, or the combination gas valve (See Figure 13 or 14).
Rotate the onboard temperature selector dial fully CCW to run unit at low fire. Manifold pressure will be negative.
Check to make sure that there is not a loss of flame. If manifold pressure adjustment is needed see
Figure 11 & 12 for low fire bypass adjustment location. Adjust modulating valve until there is a nice steady
even flame across the full length of the throat of the burner (See Figure 17), view flame through viewport.
After checking both high fire and low fire, power down heat module, replace remote Selectrostat wire leads, and
select correct temperature setting either using onboard pot or remote Selectrostat.
Figure 10A–SC11
Figure 10B –A1014R

12
Figure 10C–A1044R
Figure 11–MR 212 Modulating Regulator Valve
Figure 12 –M 411, 511, 611 Modulating Valve

13
Figure 13 –Robertshaw Regulator / Pilot Gas Valve
Figure 14 –Honeywell Regulator Valve
XIII. Burner Trouble Shooting
The Burner is only a component of the complete system. For trouble shooting of the equipment, contact the OEM
(Original Equipment Manufacturer) or the component manufacturer.
If the pilot fails to light: install a manometer on the pilot pressure tap. Check for 3.5″ W.C. for natural gas or 2″
W.C. for propane, using a natural gas pilot or 5″ to 7″ using a propane pilot with orifice # 58 drill (.042”). If no gas,
check for voltage to pilot solenoid valve. If no voltage check operating controls or primary flame safeguard. If voltage
to pilot solenoid valve is present and if there is 3.5″ W.C. gas pressure at pilot pressure tap then check for spark or
flame rod settings. See Figure 7. If there is no voltage to pilot solenoid valve, refer to Flame Safety control
specifications or contact the original equipment manufacturer.
If Main Burner fails: If no main flame, check manifold pressure. If no manifold pressure, check for voltage to the
gas solenoid valve and check if main manual fi ring valve is open. If no voltage to gas valve, refer to Flame Safety
control specifications or contact the original equipment manufacturer. If the pilot fails as main gas valves open, the
first adjacent gas port hole (next to the pilot) might need to be plugged with direct gas-fired heater module cement.
For high fire start units see Figure 7 - Pilot Configuration.

14
XIV. Manifold Pressure Adjustment
The correct input capacity of the direct gas-fired heater module is controlled by the burner gas differential manifold
pressure. A pressure tap is provided in each heat module gas train manifold. Manifold pressure must be checked at
start-up and during any service or maintenance. See Figures 11 through 14 for Gas Valve adjustment locations. Verify
proper low fire adjustments as outlined in the Sequence of Operation for the operating control system provided.
All direct gas-fired heat modules require the differential manifold pressure listed on the module ratings plate.
Differential Manifold Pressure is the difference between the negative pressure measured before start-up and the
set high fire pressure during operation.
Example: With -1.0”w.c. measured with the heat module off and a rated differential manifold pressure of 4.2”w.c., the set
manifold pressure at high fire should be 3.2”w.c.
Direct gas-fired heat modules are designed on 550M Btu/H/r./ft of burner. This rate corresponds to a 4.2” w.c. manifold
pressure for natural gas and 1.6” w.c. for propane (See Figure 15) with Midco HMA-2A Burners. Maxon NP1-LE Burners
operate at 3.9” w.c. manifold pressure for natural gas and 1.6” w.c. for propane (curves not shown).
Figure 15 –Btu/hr/ft vs. Manifold Pressure
Manifold pressure set at a specific Btu/ft. can be correlated to a flame length at high fire operation based on pressure drop
across the burner (See Figure 16).
Figure 16 –Flame Length vs. Pressure Drop

15
Figure 17 –Flame Appearance
High Fire (550 MBH/ ft of burner) Low Fire (20 MBH/ ft of burner)
XV.Electrical Controls & Wiring
All electrical wiring must be done in accordance with the National Electric Code, ANSI/NFPA No. 70.
Operating electrical controls are mounted within the heat module vestibule or on the vestibule panel.
Controls locations should be selected to prevent exposing the controls to the following:
·Moisture, especially wind driven rain or snow
·High temperatures- surfaces or ambient conditions must be less than 160 oF
·Avoid mounting controls on or adjacent to surfaces that may be hot during heater operation.
Wiring connections are quick-connect type or screw-terminal to facilitate interconnection to the heat module gas
valves, pressure switches and limits.
Minimize length of high voltage spark lead(s) and route this wire independently of all control wiring to reduce
radio frequency interference (RFI) with the electronic controls.
Electrical Supply
The direct gas-fired heater module control system requires both line voltage and low voltage circuits with correct
polarity, and clean neutral and ground. Line voltage readings between L1 and Neutral as well as L1 and Ground
should be within +/- 3 volts.
Refer to electrical supply information on duct direct gas-fired heater module rating plate.
Instructions and Wiring Diagrams
Each heat module is shipped with its own wiring diagram, sequence of operation, and control diagnostic information
for the control system provided on the heat module as part of the OEM and User information package.
Interlocks for paint booth application are shown as customer safety interlocks on the supplied wiring diagram. All
customer safety interlocks should be wired in series with the heat enable signal.
The Time delay relay purge (TDRP) on the heater module control is preset at 32 seconds. The purge period is field
adjustable and should allow the heater to be operated in the ventilation air mode for an minimum of 3 minutes or a
minimum of four air changes of the paint booth volume, whichever is greater.
Each heater is test-fired at the factory and a copy of the Test and Inspection sheet is also included.
These documents should be retained by the air handling unit manufacturer for future reference.

16
XVI. Burner Maintenance
Annual maintenance of the burner is recommended to ensure trouble free operation.
1. Clean the burner plates
2. Clear the burner gas and air ports
3. Change the spark rod igniter
4. Insure the flame sensor is in good condition
Use a stiff wire brush to clean the burner plates. Scrub both sides of the stainless-steel burner plates to remove any
soot or other crud, which may be on the burner. All of the burner plate holes must be clear, so air can pass through
them unrestricted. The holes in the burner plate allow air to mix with the gas in increasing amounts, as the flame
gets longer. Scrub the rust, soot and other foreign material from the burner orifice area. After the burner plates are
cleaned inspect them for cracking. Cracks occurring between one or two holes are normal and should be of no
concern. If the cracking is more extensive, the affected plates should be replaced. Clean the burner gas and air
ports using a drill or piece of wire of the appropriate size in table below.
After the burner plates and orifices are cleaned inspect the spark rod. The tip should be clean and free of dirt and
carbon. The porcelain must be intact. If it is cracked, replace it. Pull the flame rod or ultraviolet scanner as well. If the
flame sensor is a scanner, clean the lens with a clean damp soft rag. The flame rod’s metal rod should be clean and
free of dirt and carbon. Like the spark rod igniter, the porcelain on the flame rod must be intact as well. Replace it if it
is cracked.
Safety Shut-off Valve Leak Test
Safety shut-off valves need to be checked annually for closure tightness using the following procedure. A small
amount of leakage is normal. However, leakage rates exceeding those in the table below require replacement of gas
valve. This test must only be performed by an experienced, qualified technician.
Figure 18 –Leak Test Apparatus

17
1.) De-energize the control system to make sure no power goes to SSOV (C). .
2.) Close upstream manual gas cock (A).
3.) Make sure manual test cock (F) on leak test tap assembly is closed.
4.) Remove leak test tap plug and connect test apparatus to leak test tap (D).
5.) Close the downstream manual gas cock (E).
6.) Open the upstream manual gas cock (A).
7.) Momentarily enable the SSOV (C) through the safety system.
8.) Immerse the ¼” tube into the water approximately ½” deep.
9.) Slowly open test cock (F) on the leak assembly.
10.)When the rate of bubbles coming through the water stabilizes, count the number of bubbles appearing during a
ten (10) second period. Each bubble represents approximately 0.001 cfh. Reference leakage rate chart below.
11.)Check each SSOV separately.
Chart 1 –Allowable Valve Leakage Rate
Following leak test
1.) Close upstream manual gas cock. (A)
2.) Close manual test cock (F), remove test apparatus, and close leak test tap (D).
3.) Make sure downstream manual gas cock (E) is closed.
4.) Open the upstream manual gas cock (A), and energize the SSOV through the safety system.
5.) With a soap solution leak test the tap connection (D) and pipe / valve mating points.
6.) De-energize the SSOV (C).
7.) Open downstream manual gas cock (E).
8.) Restore system to normal operation.
XVII. Filter Maintenance
Filters are required upstream of the direct gas-fired burner assembly. Particulate removal filters are not
provided by Heatco and must be approved by the authority having jurisdiction.
Filters must be installed in the return air duct system and have the means to facilitate inspection,
maintenance, cleaning, and access to fire protection devices.
Filters are required to have periodic inspection and cleaning. The use of a filter pressure drop gauge
(supplied by others) is recommended to verify adequate operation and performance of the recirculating
air duct system filters.
Heatco Inc.
50 Heatco Court
Cartersville, Ga. 30120
Other manuals for DF Series
1
Table of contents
Other heatco Control Unit manuals
Popular Control Unit manuals by other brands

Honeywell
Honeywell 4219 Installation and setup guide
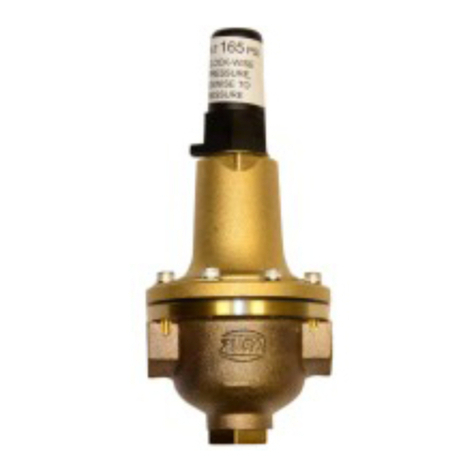
ZURN
ZURN WILKANS PV-PRD quick start guide
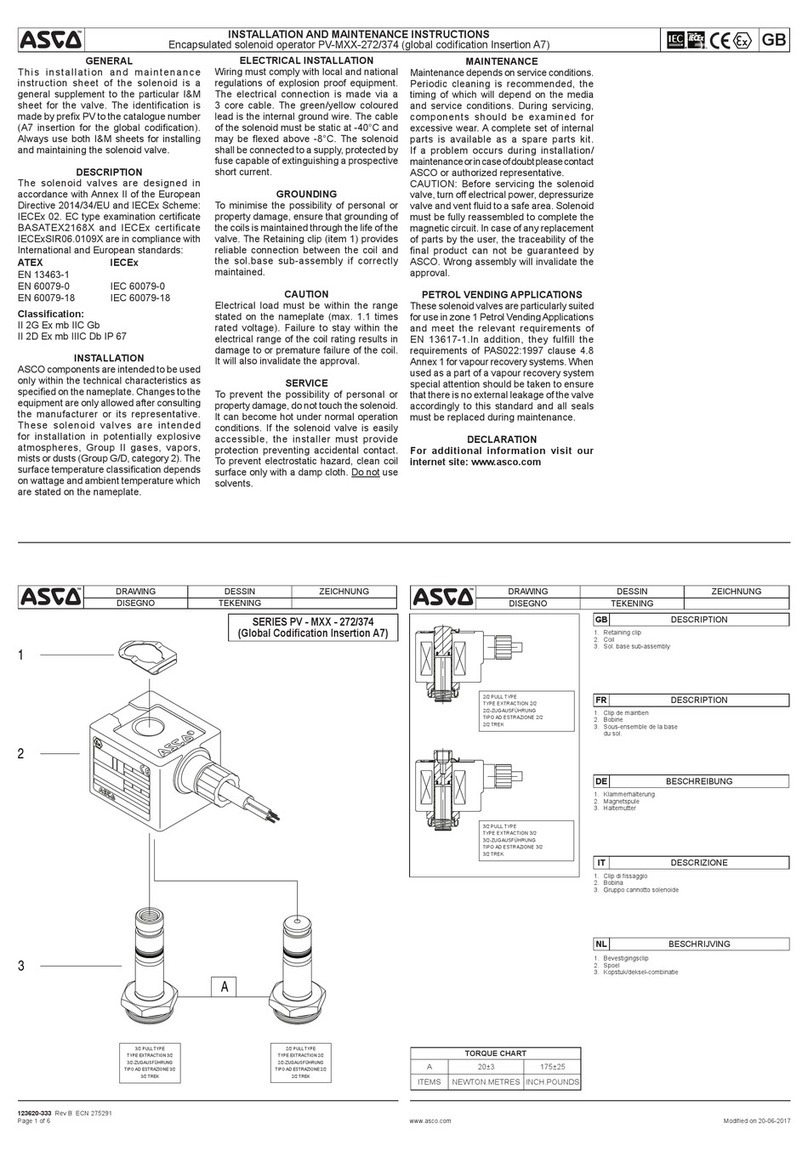
Emerson
Emerson Asco PV-MXX-272/374 Series Installation and maintenance instructions
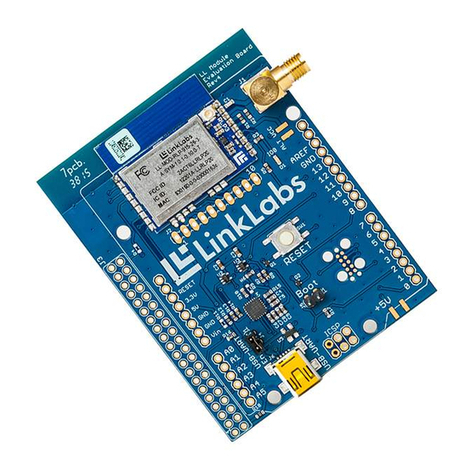
LINK LABS
LINK LABS LL-RLP-20 manual
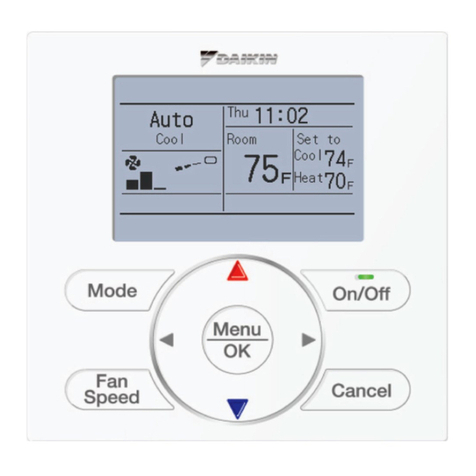
Daikin
Daikin BRC1E71 Engineeiring data
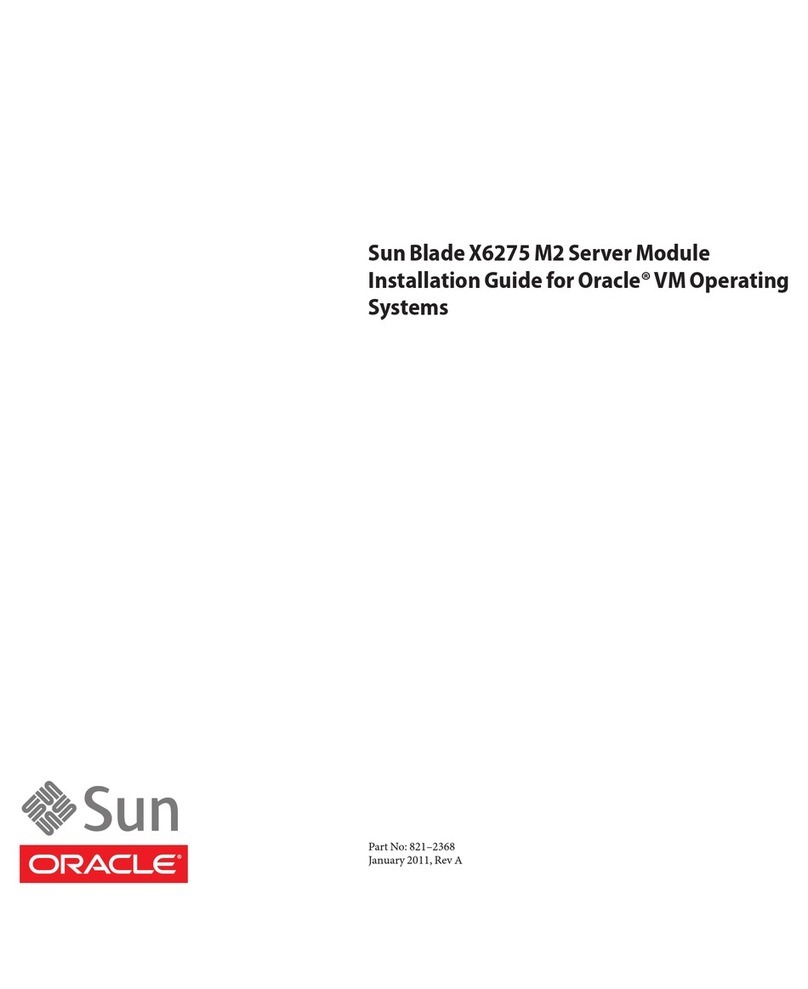
Sun Oracle
Sun Oracle Sun Blade X6275 M2 installation guide

Lenze
Lenze EtherNet/IP E84AYCEO Mounting instructions
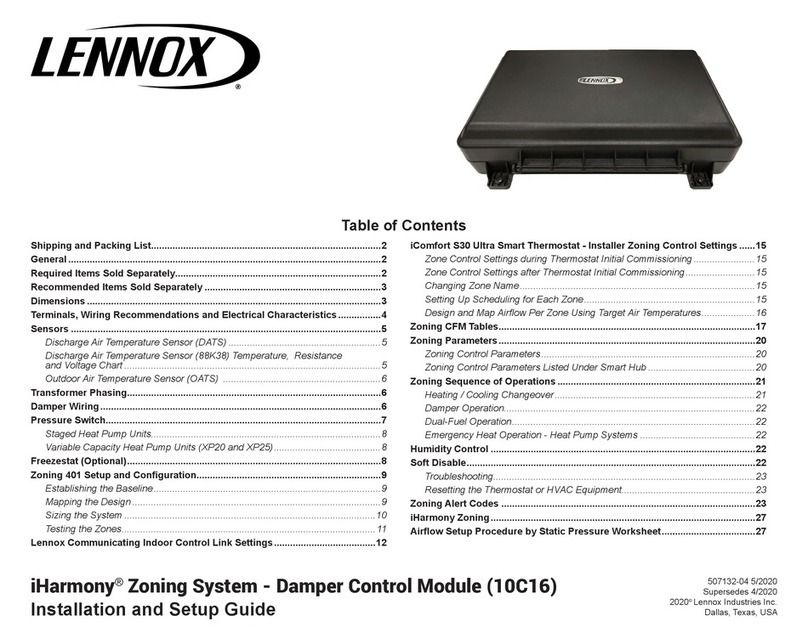
Lennox
Lennox iHarmony 10C16 Installation and setup guide
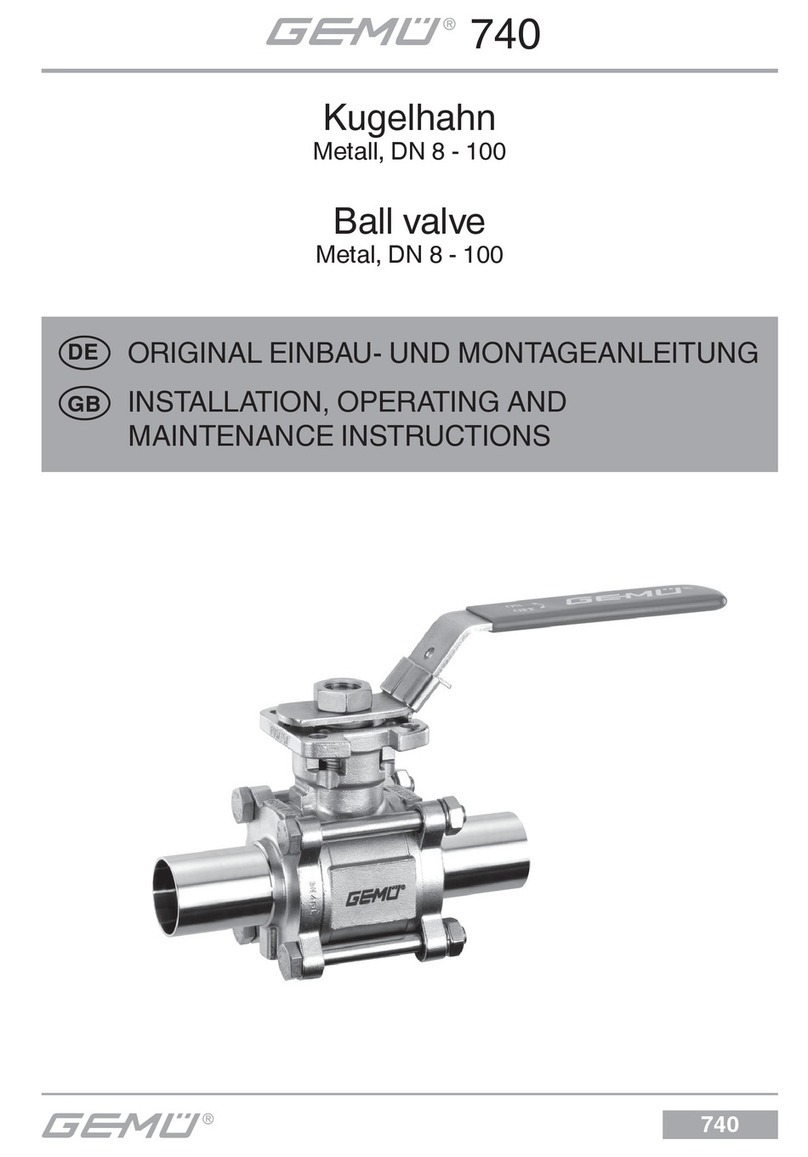
GEM
GEM 740 Installation, operating and maintenance instructions
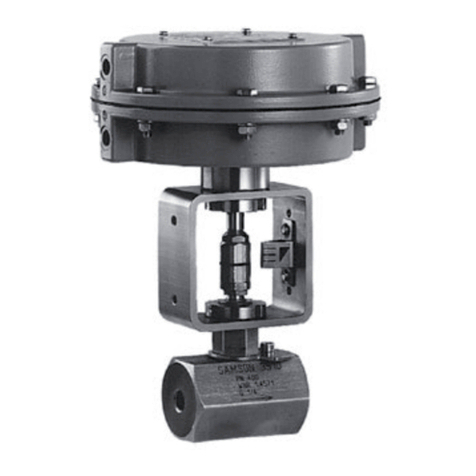
Samson
Samson 3510 Mounting and operating instructions
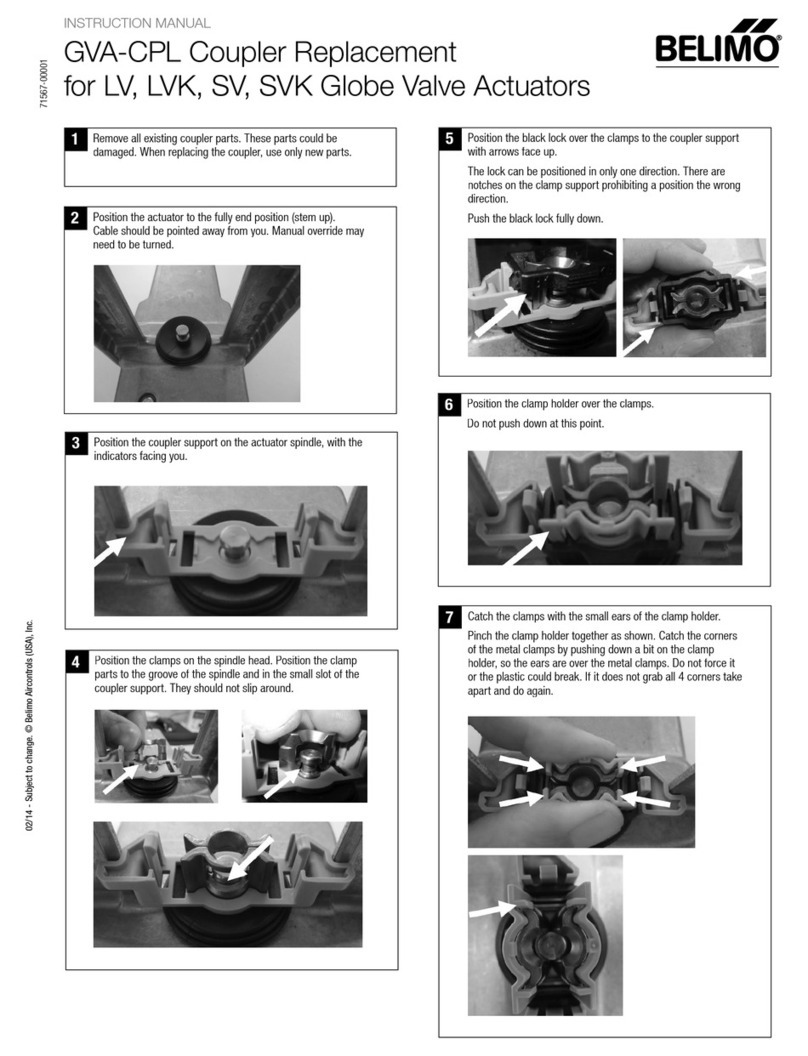
Belimo
Belimo GVA-CPL instruction manual
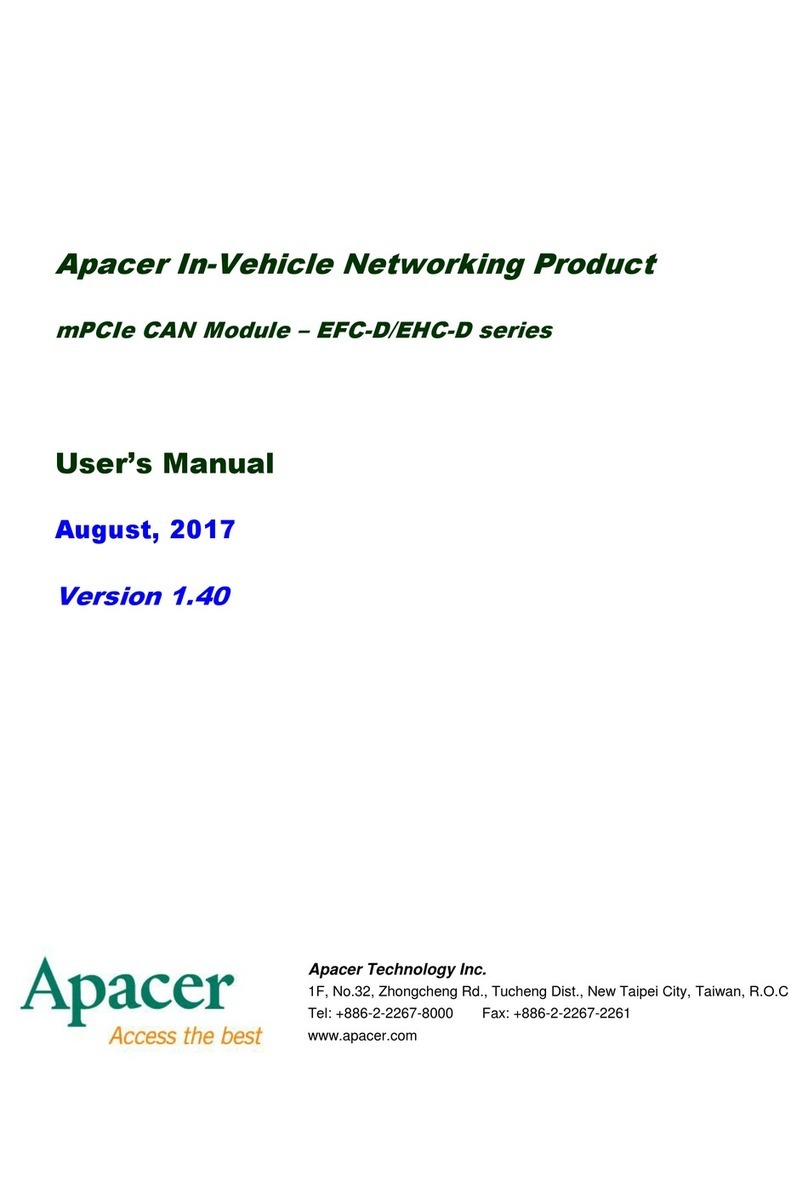
Apacer Technology
Apacer Technology EFC-D Series user manual