Hesai PandarQT User manual

Safety Notice
PLEASE READ AND FOLLOW ALL INSTRUCTIONS CAREFULLY AND CONSULT ALL RELEVANT NATIONAL AND INTERNATIONAL SAFETY REGULATIONS
FOR YOUR APPLICATION.
Caution
To avoid violating the warranty and to minimize the chances of getting electrically shocked, please do not disassemble the device on your own accord. The
device must not be tampered with and must not be changed in any way. There are no user-serviceable parts inside the device. For repairs and
maintenance inquiries, please contact an authorized Hesai Technology service provider.
Laser Safety Notice – Laser Class 1
This device satisfies the requirements of
•IEC 60825-1:2014
•21 CFR 1040.10 and 1040.11 except for conformance with IEC 60825-1 Ed.3, as described in Laser Notice No.56, dated May 8, 2019
NEVER LOOK INTO THE TRANSMITTING LASER THROUGH A MAGNIFYING DEVICE (MICROSCOPE, EYE LOUPE, MAGNIFYING GLASS, ETC.)

Safety Precautions
In all circumstances, if you suspect that the device malfunctions or is
damaged, stop using it immediately to avoid potential hazards and injuries.
Contact an authorized Hesai Technology service provider for more
information on device disposal.
Handling
This device contains metal, glass, plastic, as well as sensitive electronic
components. Improper handling such as dropping, burning, piercing, and
squeezing may cause damage to the device.
Enclosure
This device contains high-speed rotating parts. To avoid potential injuries,
DO NOT operate the device if the enclosure is loose or damaged.
Repair
DO NOT open and repair the device without direct guidance from Hesai
Technology. Disassembling the LiDAR may cause degraded performance,
failure in water resistance, or potential injuries to the operator.
Power Supply
Use only the cables and power adapters provided by Hesai Technology.
Only the power adapters that meet the device’s power requirements and
the applicable safety standards can be used. Using damaged
cables/adapters or supplying power in a humid environment can result in
fire, electric shock, personal injuries, product damage, or property loss.
Prolonged Exposure to Hot Surface
Prolonged exposure to the device’s hot surface may cause discomfort or
injury. If the device has been powered and operating for a long time, avoid
skin contact with the device or its power adapter.
Vibration
Strong vibration may cause damage to the device and should be avoided.
Radio Frequency Interference
Please observe the signs and notices on the device that prohibit or restrict
the use of electronic devices. Although the device is designed, tested, and
manufactured to comply with the regulations on RF radiation, the radiation
from the device may still influence other electronic devices.
Medical Device Interference
Some components in the device can emit electromagnetic fields, which
may interfere with medical devices such as cochlear implants, heart
pacemakers and defibrillators. Consult your physician and medical device
manufacturers for specific information regarding your medical device and
whether you need to keep a safe distance from the LiDAR. If you suspect
that the LiDAR is interfering with your medical device, stop using the LiDAR
immediately.
Explosive Atmosphere and Other Air Conditions
Do not use the device in any area where potentially explosive atmospheres
are present, such as high concentrations of flammable chemicals, vapors or
particulates (including particles, dust, and metal powder) in the air.
Exposing the device to high concentrations of industrial chemicals,
including liquefied gases that are easily vaporized (such as helium), can
damage or weaken the device’s function. Please observe all the signs and
instructions on the device.
Light Interference
Some precision optical instruments may be interfered by the laser light
emitted from the device.
Eye Safety
Although the device meets Class 1 eye safety standards, operators should
still avoid looking directly at the LiDAR for maximum self-protection.

Contents
1 Introduction............................................................................................................ 1
1.1 Operating Principle ................................................................................................. 1
1.2 LiDAR Structure ........................................................................................................2
1.3 Channel Distribution ...............................................................................................3
1.4 Specifications ............................................................................................................4
2 Setup......................................................................................................................... 5
2.1 Mechanical Installation...........................................................................................5
2.2 Interfaces ....................................................................................................................7
2.3 Connecting Box (Optional) ...................................................................................9
2.4 Use .............................................................................................................................12
3 Data Structure ...................................................................................................... 13
3.1 Point Cloud Data Packet......................................................................................14
3.2 GPS Data Packet.....................................................................................................18
4 Web Control ......................................................................................................... 23
4.1 Homepage...............................................................................................................23
4.2 Settings .....................................................................................................................24
4.3 Angle Range............................................................................................................25
4.4 Device Info...............................................................................................................27
4.5 Time Statistics .........................................................................................................28
4.6 Firmware Upgrade.................................................................................................29
5 PandarView ........................................................................................................... 30
5.1 Installation................................................................................................................30
5.2 Use .............................................................................................................................31
5.3 Features ....................................................................................................................33
6 Sensor Maintenance........................................................................................... 37
7 Troubleshooting.................................................................................................. 38
Appendix I PTP Protocol....................................................................................... 40
Appendix II FCC Statement.................................................................................. 42
Appendix III Support and Contact ..................................................................... 43

1
1 Introduction
This manual describes the specifications, installation, and data output format of PandarQT, a 64-channel mechanical LiDAR.
This manual is under constant revision. Please contact Hesai for the latest version.
1.1 Operating Principle
Distance Measurement: Time of Flight (ToF)
1) A laser diode emits a beam of ultrashort laser pulses onto the object.
2) Diffuse reflection of the laser occurs upon contact with the target object. The beams are detected by the optical sensor.
3) Distance to object can be accurately measured by calculating the time between emission and receipt by the sensor.
Figure 1.1 ToF Formula

2
1.2 LiDAR Structure
64 pairs of laser emitters and receivers are attached to a motor that rotates horizontally.
Figure 1.2 Partial Cross-Sectional Diagram Figure 1.3 Coordinate System (Isometric View) Figure 1.4 Rotation Direction (Top View)
The LiDAR’s coordinate system is shown above. The Z-axis is the axis of rotation.
The origin is shown as a red dot in Figure 1.6 on the next page. After geometric transform, all the measurements are relative to the origin.
Each laser channel has an intrinsic horizontal angle offset. When Channel 18 passes the zero degree position illustrated in Figure 1.4, the azimuth data in
the corresponding UDP data block will be 0°.

3
1.3 Channel Distribution
The vertical resolution is unevenly distributed across all channels.
Figure 1.5 Channel Vertical Distribution Figure 1.6 Laser Firing Position

4
1.4 Specifications
NOTE Specifications are subject to change without notice.
NOTE Range accuracy as the average range error across all channels may vary with range, temperature and target reflectivity.
SENSOR
MECHANICAL/ELECTRICAL/OPERATIONAL
Scanning Method
Mechanical Rotation
Laser Class
Class 1 Eye Safe
Channel
64
Waterproof Grade
IPX7
Range
0.1 to 20 m (at 10% reflectivity)
Weight
0.4 kg
Range Accuracy
±5 cm (0.1 to 0.5 m)
±2.5 cm (0.5 to 15 m)
±10 cm (15 to 30 m)
Dimensions Height: 75.0 mm
Diameter: 80.2 mm
FOV (Horizontal)
360°
Operating Voltage
9~65 VDC
Resolution (Horizontal)
0.6°
Power Consumption
7 W
FOV (Vertical)
104.6° (-52.3° to +52.3°)
Operating Temperature
-20℃ to 65℃
Resolution (Vertical)
Finest at 1.4°
Frame Rate
10 Hz
DATA I/O
Returns
Single/Dual
Data Transmission
UDP/IP Ethernet (100BASE-T1 Slave Mode)
Data Outputs
Distance, Azimuth Angle, Background
Illumination
Data Points Generated
Single Return Mode: 384,000 pts/s
Dual Return Mode: 768,000 pts/s
Clock Source
GPS / PTP
PTP Clock Accuracy
≤1 μs
PTP Clock Drift
≤1 μs/s

5
2 Setup
2.1 Mechanical Installation
Figure 2.1 Isometric View Figure 2.2 Mounting Base

6
Installation
Figure 2.3 Installation Diagram

7
2.2 Interfaces
PandarQT by default uses a 4-pin M8 male socket (with needles inside), which includes power wires and 100BASE-T1 twist-pairs. Another option is an 8-
pin male socket with the same size. The use of 4-pin M8 sockets is strongly recommended.
Figure 2.4 Connector Dimensions
Connector 4-pin 8-pin
Figure 2.5 PandarQT Connector Options (Male socket, on the LiDAR)

8
The 4-pin male socket (recommended):
Pin # Description
1 VIN
2 GND
3 Ethernet_TRX+
4 Ethernet_TRX-
The 8-pin male socket (optional, not recommended):
Pin # Description
1 VIN
2 Ethernet_TRX-
3 Ethernet_TRX+
4
GPS_RX
5 GPS_PPS
6 Sync_N
7 Sync_P
8 GND
Cables
The optional cable for connecting QT to the connection box is 2 m in length.
Contact Hesai if you need customized cables for connecting the LiDARs to your control units directly. The maximum allowable diameter of power wires is
0.511 mm, 24 AWG.
When choosing cables, please check their voltage drop and power consumption to ensure a minimum of 9 V DC input to the LiDARs.
TYPE Diameter
(mm)
Resistance/meter
(Ohm)
Max Voltage Drop
over 1 m cable (V)
Max Voltage Drop
over 6 m cable (V)
Average Power Consumption
over 1 m cable (W)
Average Power Consumption
over 6 m cable (W)
24AWG 0.511 0.0894 0.1788 1.0728 0.064368 0.386208

9
2.3 Connecting Box (Optional)
This device converts automotive 100BASE-T1 to 100BASE-TX typical Ethernet, as well as providing a power port with 5.5 mm X 2.1 mm socket and a GPS
port.
Users may connect the LiDAR directly or use the connecting box.
The cable length from the connector to the connecting box is 2 m by default.
NOTE The GPS port only supports 8-pin cables.
Figure 2.6 Connecting Box

10
2.3.1 Connecting Box Interfaces
Table 2.2 Connecting Box Interfaces
Port #
Port Name
Description
a
Standard Ethernet Port
RJ45, 100BASE-TX Ethernet
b Power Port DC power adapter with voltage ranging from 12 V to 48 VDC and a minimum power output of 18 W is suggested
c GPS Port Connector type: JST SM06B-SRSS-TB
Recommended connector for the external GPS module: JST SHR-06V-S-B
Voltage standard: RS232
Baud rate: 9600 bps
The GPS port pin numbers are 1 to 6 from left to right, defined as follows:
Table 2.3 GPS Pin Description
Pin # Direction Pin Description Requirements
1 Input PPS (pulse-per-second) signal for synchronization TTL level 3.3 V/5 V
Pulse width: 1 ms or longer is recommended
Cycle: 1 s (from rising edge to rising edge)
2 Output Power for the external GPS module 5V
3
Output
Ground for the external GPS module
-
4 Input Receiving serial data from the external GPS module RS232 level
5 Output Ground for the external GPS module -
6 Output Transmitting serial data to the external GPS module RS232 level

11
2.3.2 Connection
Figure 2.7 LiDAR Connection When Using the Connecting Box
NOTE Refer to Appendix I when PTP protocol is used.

12
2.4 Use
The Pandar family LiDARs do not have a power switch. They start operating once wired and powered up.
•To receive data on your PC, set the PC’s IP address to 192.168.1.100 and subnet mask to 255.255.255.0
For Ubuntu-16.04: For Windows:
Use the ifconfig command in the terminal:
~$ sudo ifconfig enp0s20f0u2 192.168.1.100
(replace enp0s20f0u2 with the local network port name)
1)
Open the Network Sharing Center, click on “Ethernet”
2) In the “Ethernet Status” interface, click on “Properties”
3) Double-click on “Internet Protocol Version 4 (TCP/IPv4)”
4) Configure the IP address to 192.168.1.100 and subnet mask to 255.255.255.0
•To record and display point cloud data, see Chapter 5 PandarView
•To set parameters, check device info, and upgrade firmware, see Chapter 4 Web Control
•The SDK (Software Development Kits) download links can be found at www.hesaitech.com/en/download

13
3 Data Structure
Fast Ethernet UDP/IP is used for data output. The output data includes Point Cloud Data Packets and GPS Data Packets. Each data packet consists of an
Ethernet header and UDP data.
Figure 3.1 Data Structure with UDP Sequence OFF
The UDP sequence feature is OFF by default. When UDP sequence is ON, the Tail in the UDP data changes from 22 bytes to 26 bytes.

14
3.1 Point Cloud Data Packet
3.1.1 Ethernet Header
Each LiDAR has a unique MAC address.
The source IP is 192.168.1.201 by default. The destination IP address is 0xFF FF FF FF and in broadcast form.
Ethernet Header: 42 bytes
Ethernet II MAC 12 bytes Destination: broadcast (0xFF: 0xFF: 0xFF: 0xFF: 0xFF: 0xFF)
Source: (xx:xx:xx:xx:xx:xx)
Ethernet Data Packet Type 2 bytes 0x08, 0x00
Internet Protocol 20 bytes Shown in Figure 3.2
UDP Port Number 4 bytes UDP source port (0x2710, representing 10000)
Destination port (0x0940, representing 2368)
UDP Length 2 bytes 0x04b2 when UDP sequence is OFF, representing 1202 bytes (8 bytes more than the size of the Point Cloud
UDP Data, shown in Figure 3.1)
0x04b6 when UDP sequence is ON, representing 1206 bytes
UDP Checksum 2 bytes -
Table 3.1 Point Cloud Data Packet – Ethernet Header
Figure 3.2 Point Cloud Ethernet Header – Internet Protocol

15
3.1.2 UDP Data
All the multi-byte values are unsigned and in little endian format.
Header
Header: 8 bytes
0xEEFF 2 bytes SOP (start of packet), 0xEE first
Laser N 1 byte 0x40 (64 channels)
Block N 1 byte 0x6 (6 blocks per packet)
Reserved 1 byte -
Dis Unit 1 byte 4 mm
Reserved 1 byte -
Reserved 1 byte -
Table 3.4 Point Could UDP Data – Header
Body
Body: 1164 bytes (6 blocks)
Block 1
Block 2
Block 3
…
Block 6
Azimuth 1 Azimuth 2 Azimuth 3 … Azimuth 6
Channel 1 Channel 1 Channel 1 … Channel 1
Channel 2 Channel 2 Channel 2 … Channel 1
… … … … …
Channel 64 Channel 64 Channel 64 … Channel 64
Table 3.5 Point Could UDP Data – Body
Block size = 64 * Size of Channel XX + Size of Azimuth
NOTE Under the Dual Return mode, the ranging data from each firing is stored in two adjacent blocks: the odd number block is the last return, and the
even number block is the strongest return. If the last and strongest returns coincide, the second strongest return will be placed in the even number block.
The azimuth changes every two blocks.

16
Each Block in the Body: 194 bytes
Azimuth
2 bytes
Current reference angle of the rotor
Azimuth[15:0]: lower byte Azimuth_L[7:0], upper byte Azimuth_H[15:8].
Azimuth Angle = [Azimuth_H, Azimuth_L] / 100° = Azimuth / 100°
Channel XX 3 bytes 2-byte distance data Distance[15:0]: lower byte Distance_L[7:0], upper byte Distance_H[15:8]
Distance Value = [Distance_H, Distance_L] * 4 mm = Distance * 4
Maximum Distance Value = (2 ^ 16 – 1) * 4 mm = 262.14 m
1-byte background
illumination data
Relative brightness of the receiving FOV
Synchronized to the point cloud, but not related to the emitting laser pulse or distance
Table 3.6 Point Cloud UDP Data – Block Definition
Tail
Tail: 22 (+4) bytes
Reserved 5 bytes -
High Temperature Shutdown
Flag 1 byte
0x01 for high temperature; 0x00 for normal operation
When high temperature is detected, the shutdown flag will be set to 0x01, and the system will shut down
after 60 s. The flag remains 0x01 during the 60 s and the shutdown period
When the system is no longer in high temperature status, the shutdown flag will be reset to 0x00 and the
system will automatically return to normal operation
Reserved 2 bytes -
Motor Speed 2 bytes speed_2_bytes [15:0] = speed (RPM)
GPS Timestamp 4 bytes Packing time of this data packet, in units of 1 μs
Range: 0 to 1000000 μs (1 s)
Return Mode Information 1 byte 0x37 for Strongest Return mode, 0x38 for Last Return mode, and 0x39 for Dual Return mode
Factory Information 1 byte 0x42 (or 0x43)
UTC 6 bytes Year, month, date, hour, minute, second, decimal digit
UDP Sequence 4 bytes Added only when UDP sequence is ON
Label the sequence number of Point Cloud UDP packets, 1 to 0xFF FF FF FF in little endian format
Table 3.7 Point Cloud Data UDP Data – Tail
Other manuals for PandarQT
6
Table of contents
Other Hesai Measuring Instrument manuals
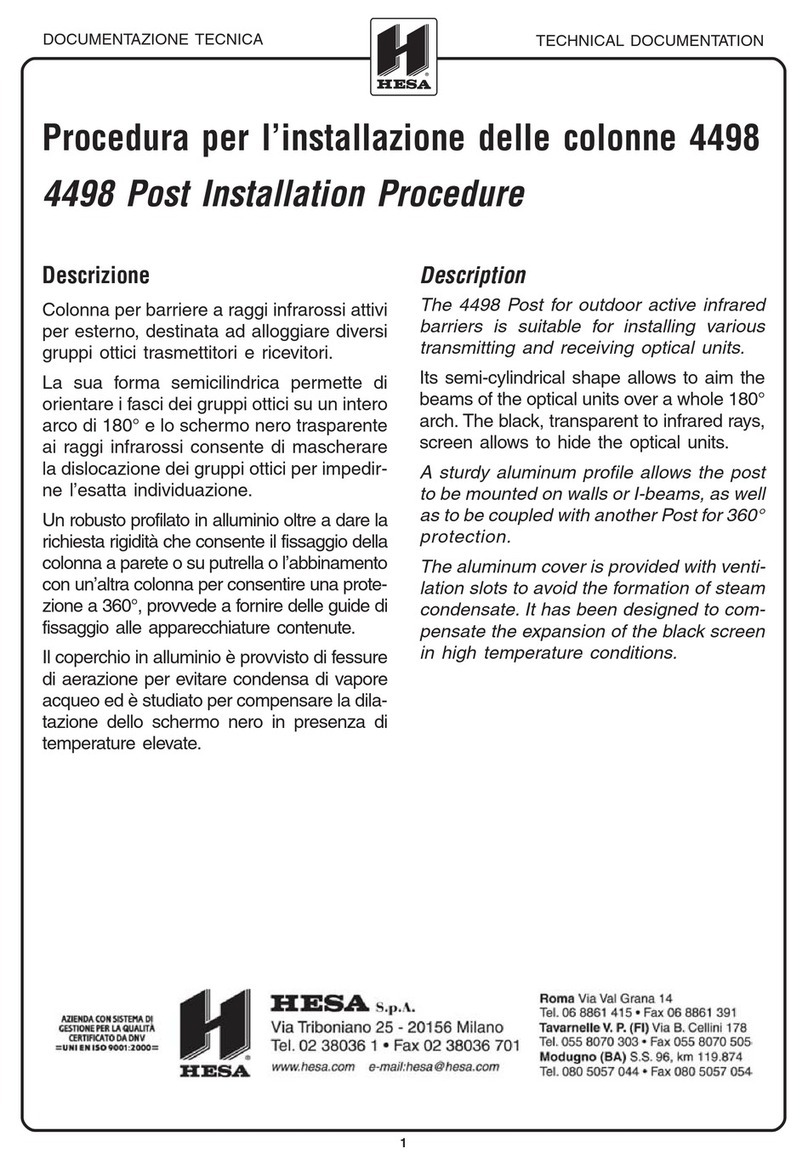
Hesai
Hesai 4498 Guide
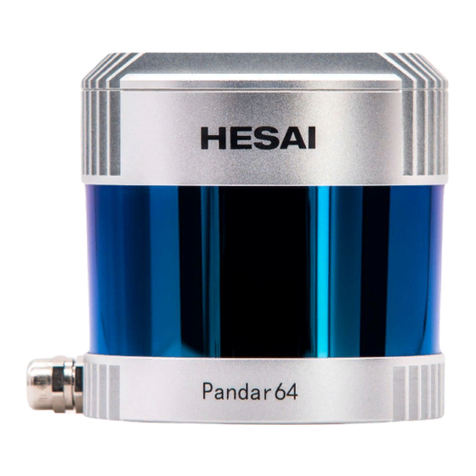
Hesai
Hesai Pandar64 User manual
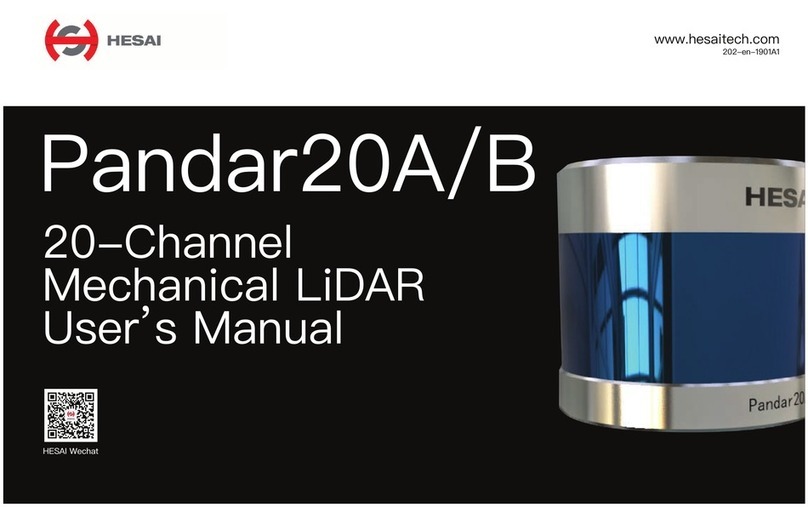
Hesai
Hesai Pandar20A User manual
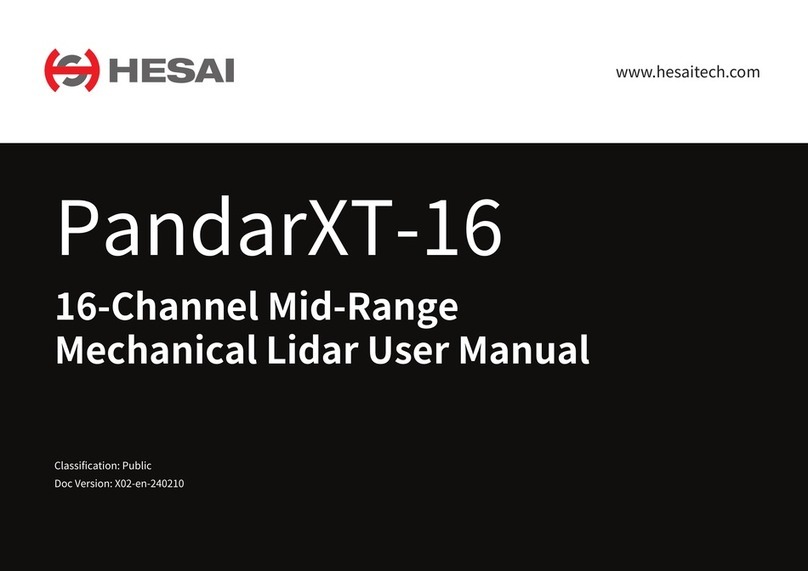
Hesai
Hesai PandarXT-16 User manual
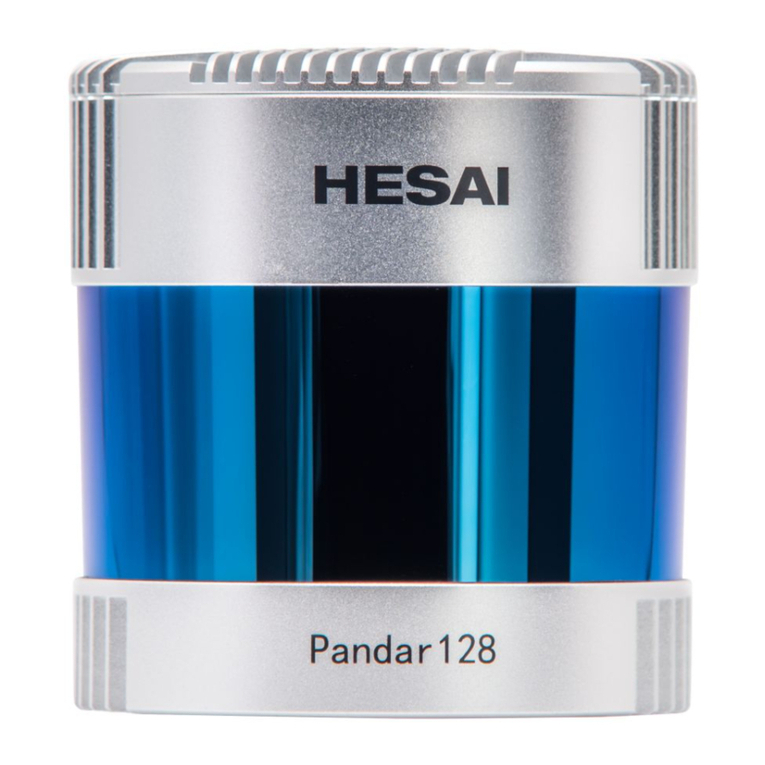
Hesai
Hesai Pandar128 User manual
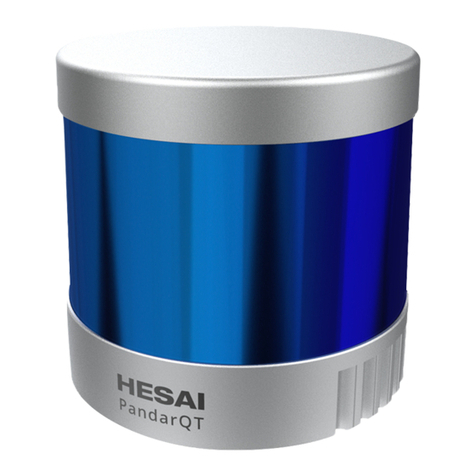
Hesai
Hesai PandarQT User manual
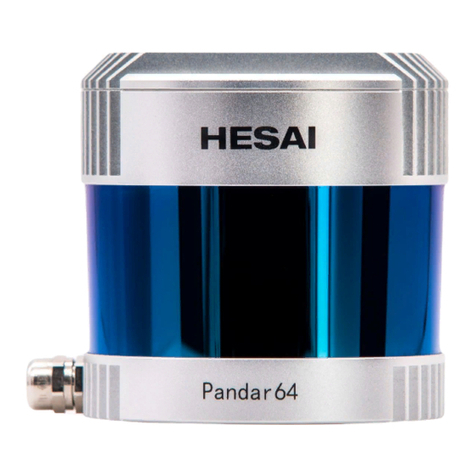
Hesai
Hesai Pandar64 User manual
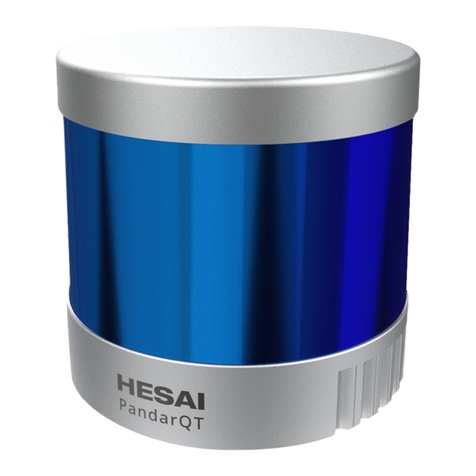
Hesai
Hesai PandarQT User manual
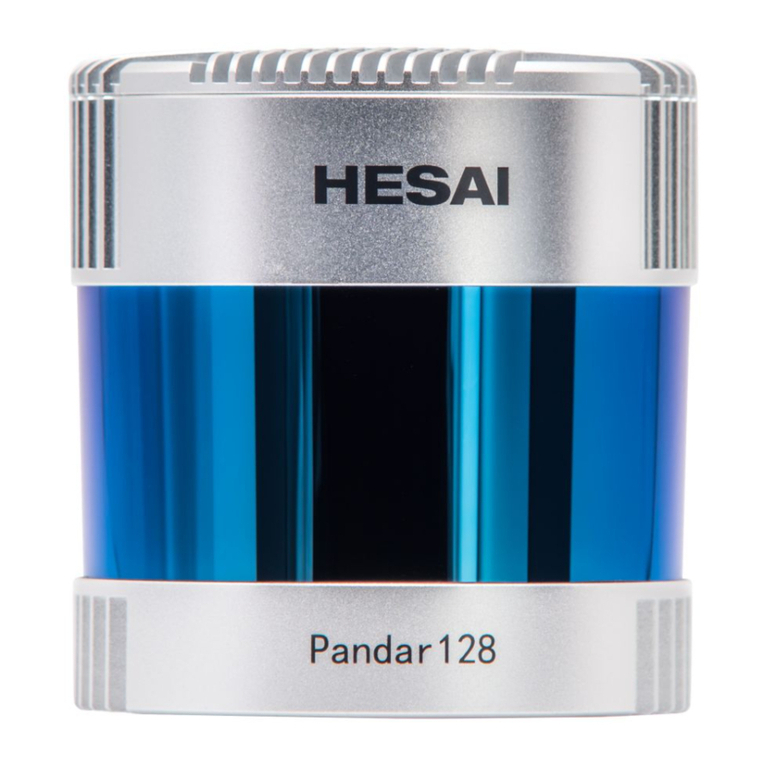
Hesai
Hesai Pandar128 User manual
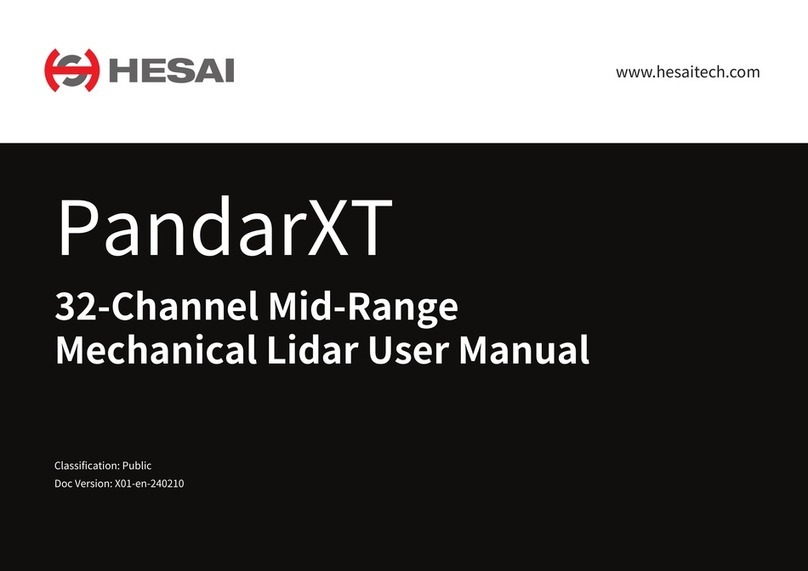
Hesai
Hesai PandarXT User manual
Popular Measuring Instrument manuals by other brands

DS
DS POCKET CHECKER-PRO instructions
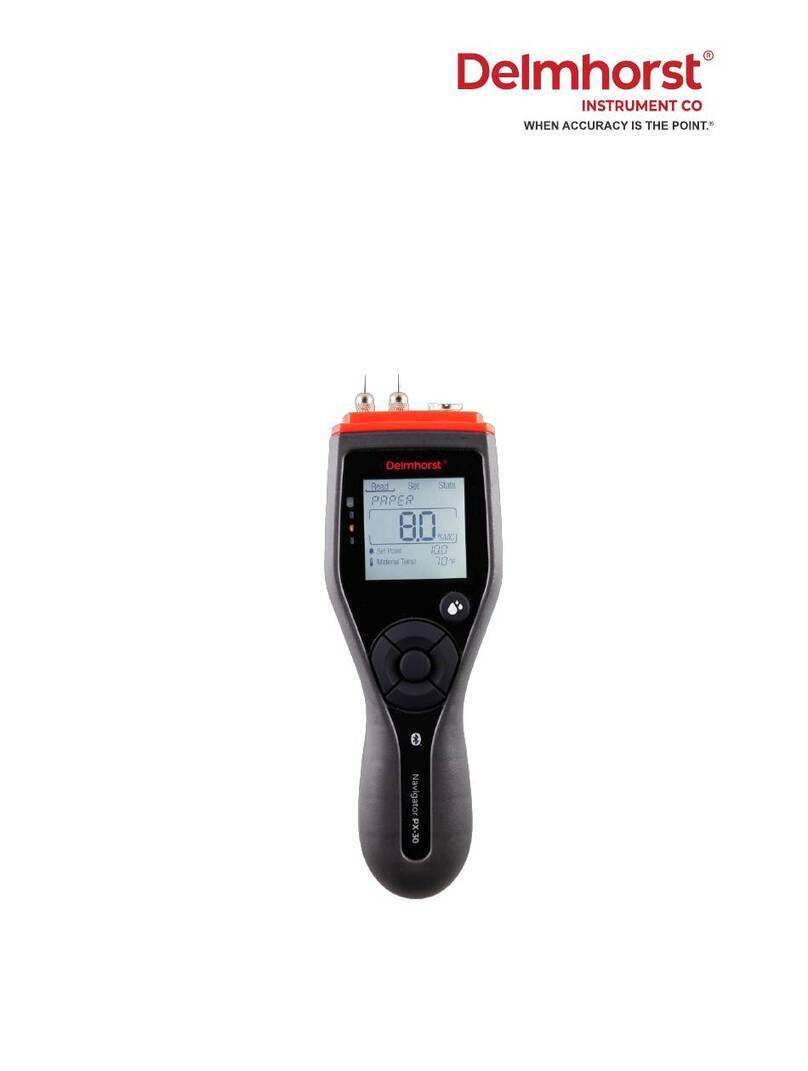
Delmhorst Instrument Co
Delmhorst Instrument Co PX-20 owner's manual
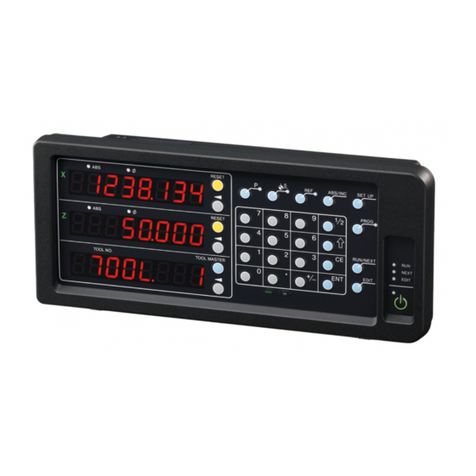
Magnescale
Magnescale LH72 Initial setup manual
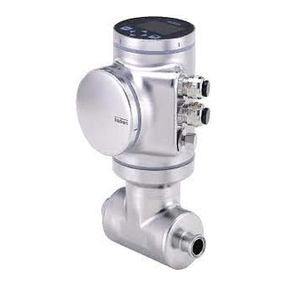
Burkert
Burkert Flowave 8098 operating instructions
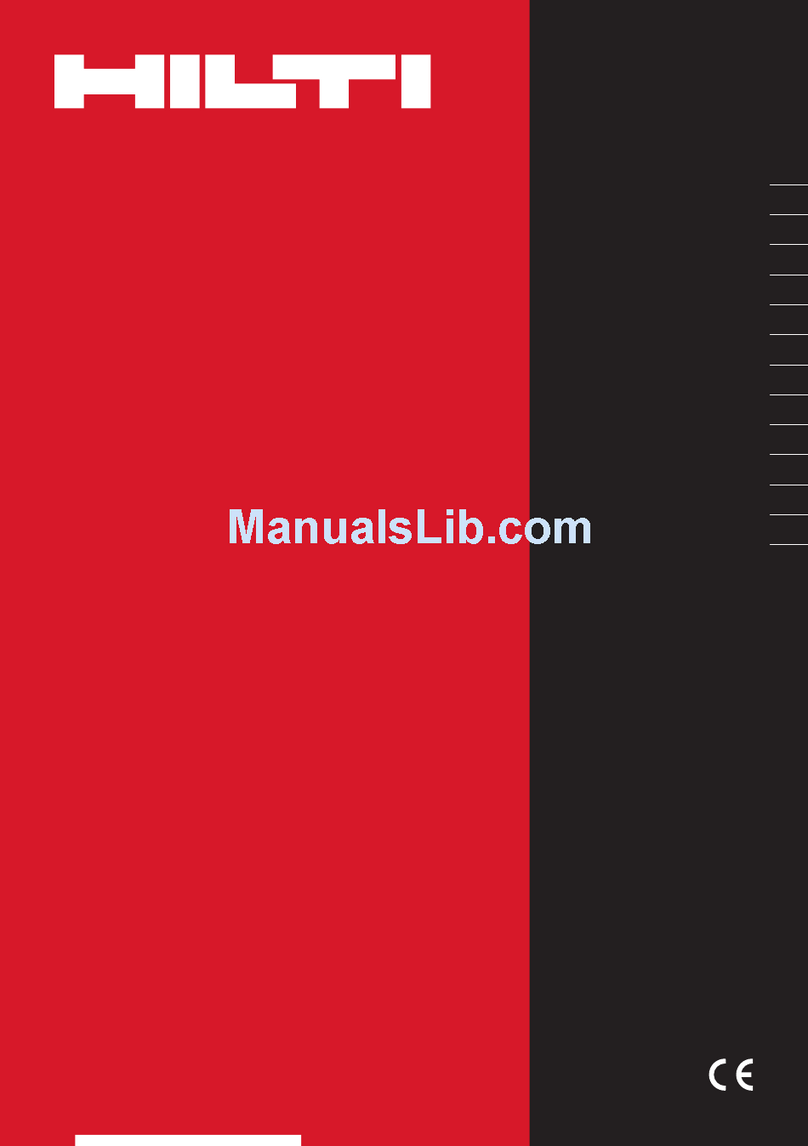
Hilti
Hilti pos 150 Original operating instructions

Konica Minolta
Konica Minolta VIVID 9i/VI instruction manual