Jireh Rotix User manual

ROTIX
3-Axis Nozzle Scanner
CE0160 Rev 00

PAGE i of iv Rev. CE0160 Rev 00
SAFETY WARNINGS / PRECAUTIONS
DANGER! The ROTIX is designed for a specic use. Using the
ROTIX outside of its intended use could cause damage to the product.
Read and understand this manual before using.
KEEP THIS MANUAL – DO NOT LOSE
THIS MANUAL IS PART OF THE ROTIX AND MUST BE RETAINED FOR THE LIFE OF
THE PRODUCT. PASS ON TO SUBSEQUENT OWNERS.
Ensure any amendments are incorporated with this document.
WARNING! Do NOT operate scanner in an explosive environment.
Do NOT operate scanner in the presence of volatile substances.
The WEEE symbol indicates that the product must not be disposed of as
unsorted municipal waste, but should be collected separately.
(see Disposal on page 31)
Jireh Industries Ltd.
53158 Range Road 224
Ardrossan, Alberta, Canada
T8E 2K4
Phone: 780.922.4534
Fax: 780.922.5766
jireh.com
DISTRIBUTOR: MANUFACTURER:

PAGE ii of iv
Chapter1 Introduction 1
1.1. Product information 1
1.1.1. Intended use 1
1.1.2. Performance specifications 1
1.1.3. Operating environment 1
1.1.4. Environmental Sealing 1
1.2. Definition of symbols 1
1.3. Hardware 2
1.3.1. Included tools 2
1.3.2. Maintenance 2
1.4. Chain Configuration Setup Chart 3
1.5. Scanner Component Identification 4
Chapter2 Configurations 7
2.1. Nozzle Scanner 7
Chapter3 Operation 8
3.1. Setup of ROTIX on Scanning Surface 8
3.2. Using a Slider Probe Positioning System 12
Chapter4 System Components 13
4.1. Low Profile Link 13
4.1.1. Brake 13
4.1.2. Frame Bar Attachment 14
4.1.3. Encoder Connections 15
4.1.4. Cable Clip 15
4.2. Frame Bar with Ruler 15
4.2.1. Encoded Skew Vertical Probe Holder 16
4.2.2. Probe Holder Setup 17
4.2.3. Encoded Skew Vertical Probe Holder Adjustment 19
4.2.4. Skew Angle Adjustment 21
4.2.5. Pivot Buttons 22
4.3. Slider PPS 23
TABLE OF CONTENTS

PAGE iii of iv Rev. CE0160 Rev 00
4.3.1. Slider PPS Encoder 25
4.4. Chain Components 26
4.4.1. Chain Connection 26
4.5. Cable Management System 27
4.5.1. Cable Management Dovetail Mount 27
4.5.2. Cable Management Setup 28
4.5.3. Clamp Setup 29
4.6. Cable Clip 30
Chapter5 Service and Support 31
5.1. Troubleshooting 31
5.2. Technical Support 31
5.3. Disposal 31
Chapter6 Spare Parts 32
6.1. Low Profile Link 32
6.2. Kit Components 33
6.2.1. Encoder Connector Type 34
6.2.2. Probe Positioning 35
6.2.3. Slider Probe Positioning System (Slider PPS) 35
6.2.4. Slider PPS Encoded Leadscrew 35
6.3. Encoded Skew Vertical Probe Holder 36
6.4. Probe Holder Components 37
6.4.1. Pivot Button Style 37
6.5. Variable Components 37
6.5.1. Frame Bar with Ruler 37
6.6. Accessories 38
6.6.1. Cable Management 38
Chapter7 Limited Warranty 39

PAGE iv of iv

PAGE 1 of 40 Rev. CE0160 Rev 00
Chapter 1
INTRODUCTION
1.1. Product information
1.1.1. Intended use
The ROTIX nozzle scanner is a manually operated chain scanning system. Its primary
purpose is to move an ultrasonic probe circumferentially around pipe nozzles and to
provide encoded positional information, encoded probe positional information and
encoded skew information.
1.1.2. Performance specifications
Minimum Maximum
Nozzle Range 7.6 cm (3 in) 60 cm (24 in)
Umbilical Length (Standard Kit) 5 m (16.4 in)
X-Axis Encoder Resolution 16.3 counts/mm (414.5 counts/inch)
Y-Axis Encoder Resolution (Slider PPS) 161.3 counts/mm (4096.0 counts/inch)
Skew Encoder Resolution 2.84 counts/deg
1.1.3. Operating environment
The ROTIX chain scanner is designed for use in an industrial environment that is
between -20° C (-4° F) and 50° C (122° F).
1.1.4. Environmental Sealing
Dust-tight, watertight (not submersible).
1.2. Definition of symbols
Instructions to ‘look here’ or to ‘see this part’
Denotes movement. Instructing user to carry out action
in a specified direction.
Indicates alignment axis
Alerts user that view has changed to a reverse angle

PAGE 2 of 40
1.3. Hardware
1.3.1. Included tools
The 3 mm hex driver (Fig. 1) is sucient for all typical operations and adjustments
of the ROTIX. The 3/8 in wrench (Fig. 2) is used to remove and install pivot
buttons on the probe holders.
1.3.2. Maintenance
General cleaning of components is important to keep your system working
well. All components that have no wiring or cables are completely waterproof.
Components can be washed with warm water, dish soap and a medium bristle
brush.
After washing your system, use a light oil to lubricate the slide and the
adjustment screw on the buckle component (Fig. 11). Before using the scanner,
ensure all connectors are free of water and moisture.
NOTE: All components with wiring, cables or electrical connections are splash
proof. However, these components are NOT submersible.
NOTE: Never use strong solvents or abrasive materials to clean your scanner
components.
Fig. 1 - 3 mm hex driver Fig. 2 - 3/8 in wrench

PAGE 3 of 40 Rev. CE0160 Rev 00
1.4. Chain Configuration Setup Chart
NOZZLE SCANNER: Setup Chart
MIN
(in)
MAX
(in)
MIN
(mm)
MAX
(mm)
SHORT*
LONG
CE0165 Rev 00
PIPE SIZE LINKS
*Short includes: Short Link, Dovetail Link, Red Catch Link.
Max of 10.2-30.5 cm
(4-12 in)
KitMax of 10.2-60 cm
(4-24 in)
Kit
NOZZLE SCANNER: Setup Chart
MIN
(in)
MAX
(in)
MIN
(mm)
MAX
(mm)
SHORT*
LONG
CE0165 Rev 00
PIPE SIZE LINKS
*Short includes: Short Link, Dovetail Link, Red Catch Link.
Max of 10.2-30.5 cm
(4-12 in)
KitMax of 10.2-60 cm
(4-24 in)
Kit
3 03.8 974.7 119
4 04.8 1225.7 145
2 03 713.8 97
5 05.7 1456.6 168
6 06.6 1687.5 191
7 07.4 1888.3 211
8 08.3 2119.2 234
9 09.1 23110.0 254
6 19.4 23910.2 259
7 110.2 25911.0 279
8 110.9 27711.8 300
9 111.7 29712.6 320
7 212.6 32013.5 343
5 313.5 34314.4 366
3 414.4 36615.2 386
4 415.1 38416.0 406
5 415.9 40416.8 427
6 416.7 42417.5 445
4 517.5 44518.4 467
5 518.3 46519.1 485
6 519.0 48319.9 505
4 619.9 50520.8 528
5 620.7 52621.5 546
6 621.4 54422.3 566
7 622.2 56423.1 587
8 623.0 58423.9 607
9 623.7 602
24.6 625
3 03.8 974.7 119
4 04.8 1225.7 145
2 03 713.8 97
5 05.7 1456.6 168
6 06.6 1687.5 191
7 07.4 1888.3 211
8 08.3 2119.2 234
9 09.1 23110.0 254
6 19.4 23910.2 259
7 110.2 25911.0 279
8 110.9 27711.8 300
9 111.7 29712.6 320
7 212.6 32013.5 343
5 313.5 34314.4 366
3 414.4 36615.2 386
4 415.1 38416.0 406
5 415.9 40416.8 427
6 416.7 42417.5 445
4 517.5 44518.4 467
5 518.3 46519.1 485
6 519.0 48319.9 505
4 619.9 50520.8 528
5 620.7 52621.5 546
6 621.4 54422.3 566
7 622.2 56423.1 587
8 623.0 58423.9 607
9 6
23.7 60224.6 625

PAGE 4 of 40
1.5. Scanner Component Identification
The ROTIX system may contain or utilize the following components (see System
Components on page 13).
Fig. 3 - Low profile link
CEA024
1
mm
Fig. 4 - Frame bar with ruler
BG0090-
Fig. 5 - Slider probe positing system
CJA002- Fig. 6 - Encoded skew vertical probe holder
PHA024-
Fig. 7 - PPS Encoder
CJS017-
Fig. 8 - Short link
CES002

PAGE 5 of 40 Rev. CE0160 Rev 00
Fig. 9 - Short link with dovetail
CES024 Fig. 10 - Long link
CES009
Fig. 11 - Buckle
CES005
Fig. 12 - Catch link
CES003
Fig. 13 - 3 mm hex driver
EA414
Fig. 14 - 3/8 in wrench
EA470

PAGE 6 of 40
Fig. 15 - Irrigation kit
CMG007
Fig. 16 - Carrying case
CEA025
Fig. 17 - J400 Encoder Cable
UMA036-
Fig. 18 - Cable management, dovetail mount
CES044-

PAGE 7 of 40 Rev. CE0160 Rev 00
Chapter 2
CONFIGURATIONS
2.1. Nozzle Scanner
Fig. 19 - Nozzle scanner configuration
Fig. 20 - Nozzle scanner configuration

PAGE 8 of 40
Chapter 3
OPERATION
3.1. Setup of ROTIX on Scanning Surface
1. Determine the diameter of the nozzle to be scanned. Included in the ROTIX kit
is a setup chart which will indicate the number of links required based on the
diameter of the pipe or tubing (Fig. 21).
2. Assemble the appropriate configuration to the low profile link (Fig. 22). Install the
wedge and probe to be used (see Probe Holder Setup on page 17).
TIP: Route cables and hoses though the cable clips as a means of cable
management (see Cable Management System on page 27).
TIP: This example displays a conguration for a 30.5 cm (12 in) nozzle diameter.
ø
Fig. 21 - Refer to setup chart Fig. 22 - Assemble configuration
Fig. 23 - Place system on nozzle

PAGE 9 of 40 Rev. CE0160 Rev 00
3. On a flat surface, connect the appropriate amount of links as indicated on the
ROTIX setup chart. Arrange the link setup so the buckle and catch link will be
180° opposite of the low profile link (Fig. 24).
TIP: Place the dovetail link 2nd in the chain behind the low prole
link (Fig. 76 on page 27).
4. Ensure the brake of
the low profile link is
activated to prevent
scanner movement during
installation (see Brake on
page 13).
5. Place the configured
assembly around the
nozzle to be inspected
(Fig. 24).
Fig. 24 - Place system on nozzle

PAGE 10 of 40
6. Bring the buckle arm
(Fig. 25-1) towards the
catch link (Fig. 25-2). Hook
the buckle’s arm to the
middle axle of the catch
link. The buckle
adjustment knob (Fig.
26-A) may have to be
loosened to allow arm to
reach catch link.
7. Rotate the knob until the
buckle’s lever can be
pushed down locking the
buckle in place (Fig. 26-3).
The tightness of the
ROTIX on the pipe can
be adjusted using the
buckle adjustment knob
(Fig. 26-A).
TIP: If additional
clearance is
needed, the
handle on the
buckle can be
pulled out and
rotated to various
positions (see
Ratchet Lever on
page 22).
2
1
Fig. 25 - Hook buckle to catch link
A
3
Fig. 26 - Adjust pressure of buckle
Fig. 27 - Buckle locked
Fig. 28 - Lower probe holder to scan surface
A

PAGE 11 of 40 Rev. CE0160 Rev 00
8. Pull the probe holder latch pin (Fig. 28-A) to release the probe holder from the
locked position (see Latch Pin on page 20 for more information).
9. Lower the probe to the scan surface (see Encoded Skew Vertical Probe Holder
Adjustment on page 19).
NOTE: To maintain optimal scanner performance, the manufacturer recommends the
user does not position the probe holder beyond 45° from the axis of the scan
surface’s centre point (Fig. 29).
45°
Fig. 29 - Do not scan beyond 45° from the axis of scan surface
6. Bring the buckle arm
(Fig. 25-1) towards the
catch link (Fig. 25-2). Hook
the buckle’s arm to the
middle axle of the catch
link. The buckle
adjustment knob (Fig.
26-A) may have to be
loosened to allow arm to
reach catch link.
7. Rotate the knob until the
buckle’s lever can be
pushed down locking the
buckle in place (Fig. 26-3).
The tightness of the
ROTIX on the pipe can
be adjusted using the
buckle adjustment knob
(Fig. 26-A).
TIP: If additional
clearance is
needed, the
handle on the
buckle can be
pulled out and
rotated to various
positions (see
Ratchet Lever on
page 22).
2
1
Fig. 25 - Hook buckle to catch link
A
3
Fig. 26 - Adjust pressure of buckle
Fig. 27 - Buckle locked
Fig. 28 - Lower probe holder to scan surface
A

PAGE 12 of 40
3.2. Using a Slider Probe Positioning System (Slider PPS)
To setup and install a slider probe positioning system (see Slider PPS on page 23).
1. Ensure the slider
lock knob (Fig. 30-A)
is tight and rotate
the main knob to
position the slider
(Fig. 30).
A
Fig. 30 - Slider positioning

PAGE 13 of 40 Rev. CE0160 Rev 00
Chapter 4
SYSTEM COMPONENTS
4.1. Low Profile Link
The low profile link contains the main positional encoder and a mounting point
for a frame bar. Two encoder inputs are located at the rear of the link along with
the output to the user’s instrument (Fig. 31).
4.1.1. Brake
The red lever operates the brake. Lower
the lever to activate the brake and prevent
scanner movment. Raise the lever to
disengage the brake (Fig. 32).
Fig. 31 - ROTIX - Low profile link
Fig. 32 - Brake lever

PAGE 14 of 40
4.1.2. Frame Bar Attachment
1. Rotate the two knobs at the front
of the low profile link to align the
dovetail jaws (Fig. 33).
2. Slide the frame bar over the two
dovetails of the low profile link
(Fig. 34).
3. Tighten the two knobs to secure
the frame bar in place (Fig. 35).
4. The 3 mm hex driver may be used
to tighten and loosen the knobs
should additional strength be
required.
Fig. 33 - Attach frame bar to dovetail
Fig. 34 - Attach frame bar to dovetail Fig. 35 - Tighten knobs
Fig. 36 - Use 3 mm hex driver

PAGE 15 of 40 Rev. CE0160 Rev 00
4.1.3. Encoder Connections
A. Labled ENC 1, the Y-axis encoder
(slider probe positioning system) plugs
into this terminal.
B. Labled ENC 2, plug the cable from
the skew encoder here.
C. The main output of all encoder
singals, including the low profile
link’s positional encoder, to the
user’s instrument.
4.1.4. Cable Clip
Locations for cable clips have been provided to assist with cable management (Fig. 38).
To route the cable or hose through the cable clips, place the cable clip around the
hose and then pinch the clip and press it into the dovetail groove (Fig. 39) located on
the low profile link.
4.2. Frame Bar with Ruler
Frame bars (Fig. 40) are used to mount
probe holders, probe positioning
systems and other accessories (see
Frame Bar with Ruler on page 37).
Frame bars are available in a variety
of lengths.
A
B
C
ENC
1
ENC
2
Fig. 37 - Connection identification
Fig. 38 - Cable clip mounting points Fig. 39 - Pinch clip and press into place
1
mm
Fig. 40 - Frame bar with ruler
Other manuals for Rotix
8
Table of contents
Other Jireh Scanner manuals
Popular Scanner manuals by other brands
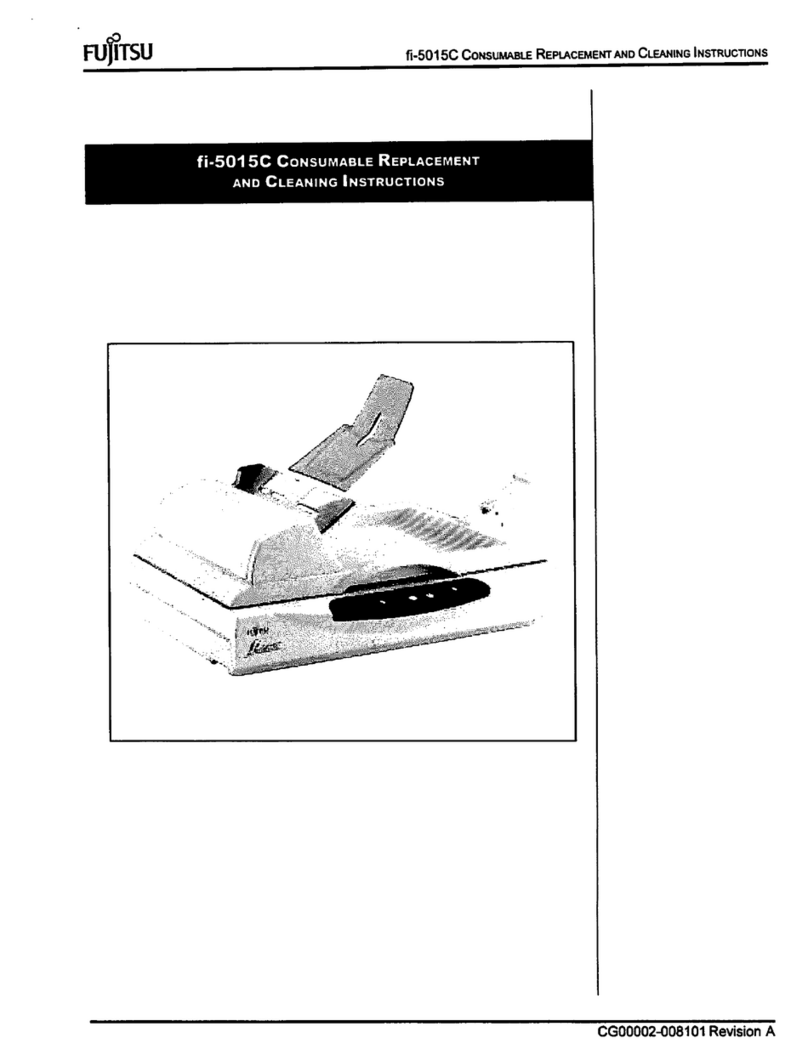
Fujitsu
Fujitsu FI-5015C Consumable replacement and cleaning instructionsmable replacement and cleaning instructions
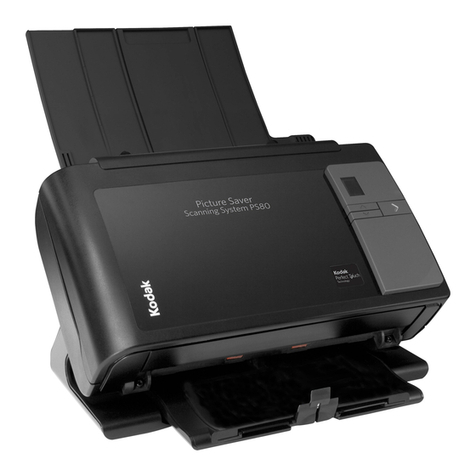
Kodak
Kodak PS80 Series user guide

Canon
Canon CR-180 Cleaning and maintenance
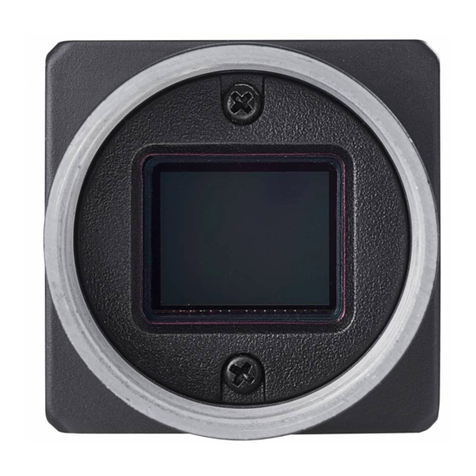
HikRobot
HikRobot CA Series user manual
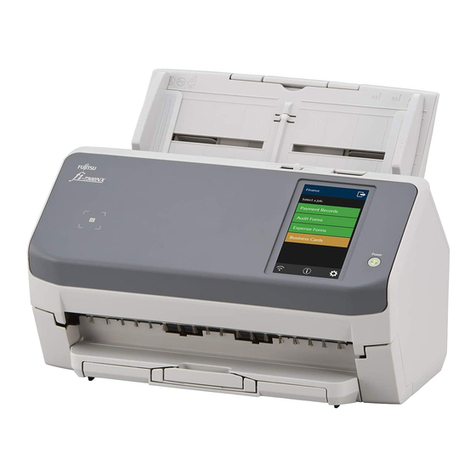
Fujitsu
Fujitsu fi-7300NX Operator's guide
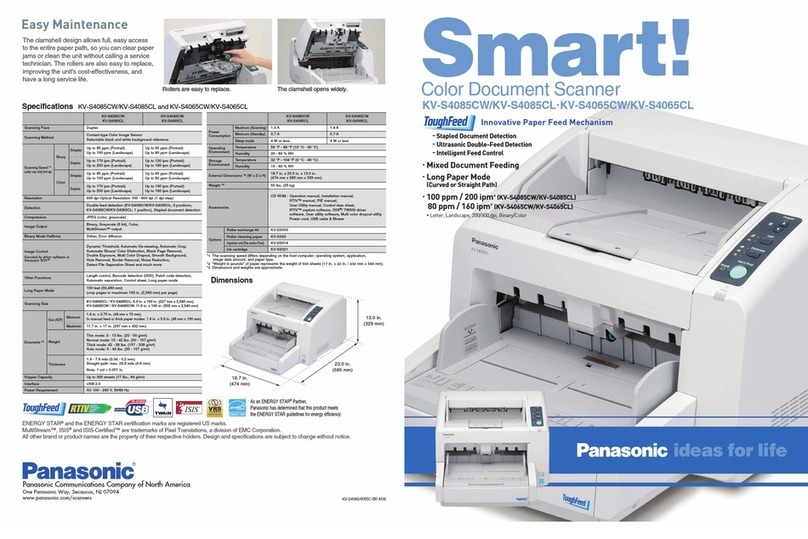
Panasonic
Panasonic KV-S4065CL - Sf Clr Duplex 65PPM USB 2.0 Lgl 300PG... Specifications