John Bean EHP System I User manual

EHP System I, II and III
High Performance Tire Changers
Operation Instructions
Form 5843
For Reference Only
For Current Info See Equiserv.com

(BLANK PAGE)
For Reference Only
For Current Info See Equiserv.com

COPYRIGHT NOTICE
The information contained in this document is property of John Bean,
division of Snap-on Incorporated. It or any of the information contained
within shall not be used, copied, or reproduced without express written
consent of John Bean or its holding company.
TRADEMARK NOTICE
John Bean is a trademark of Snap-on Incorporated.
For Reference Only
For Current Info See Equiserv.com

(BLANK PAGE)
For Reference Only
For Current Info See Equiserv.com

- Page 5 -
EHP Series Operation Instructions
SAFETY INFORMATION
For your safety, read this manual thoroughly
before operating the EHP Series Tire Changer
The EHP Series Tire Changers are intended for use by properly trained automotive
technicians. Thesafetymessagespresentedinthissectionandthroughoutthemanual
are reminders to the operator to exercise extreme care when changing tires with these
products.
There are many variations in procedures, techniques, tools, and parts for changing
tires, as well as the skill of the individual doing the work. Because of the vast number of
wheel and tire applications and potential uses of the product, the manufacturer cannot
possibly anticipate or provide advice or safety messages to cover every situation. It is
the automotive technician's responsibility to be knowledgeable of the wheels and tires
being changed. It is essential to use proper service methods and change tires in an
appropriate and acceptable manner that does not endanger your safety, the safety of
others in the work area or the equipment or vehicle being serviced.
It is assumed that, prior to using the EHP Series Tire Changers, the
operator has a
thorough understanding of the wheels and tires being changed. In addition, it is as-
sumed he has a thorough knowledge of the operation and safety features of the rack,
lift, or floor jack being utilized, and has the proper hand and power tools necessary to
service the vehicle in a safe manner.
Before using the EHP SeriesTire Changers, always refer to and follow the safety mes-
sages and service procedures provided by the manufacturers of the equipment being
used and the vehicle being serviced.
IMPORTANT !! SAVE THESE INSTRUCTIONS -- DO NOT DISCARD !!
For Reference Only
For Current Info See Equiserv.com

- Page 6 -
Overinflated tires or rims mounted on the wrong sized rims can explode
producing hazardous flying debris.
••
••
•Read Operator’s Manual before using this Tire Changer.
••
••
•Never mount tire on rim with different sized diameter.
••
••
•Never exceed maximum inflation pressure listed on tire sidewall.
••
••
•Always use safety restraint arm to hold wheel in place while
inflating.
••
••
•Always use attached air hose to inflate tires.
Exploding tires can cause death or serious injury.
Risk of electrical shock.
••
••
•Do not operate equipment with a damaged power cord or if the
equipment has been dropped or damaged, until it has been
examined by a qualified service person.
••
••
•If an extension cord is necessary, a cord with a current rating equal
to or greater than that of the equipment should be used. Cords
rated for less current than the equipment can overheat.
••
••
•Unplug equipment from electrical outlet when not in use. Never
use the cord to pull the plug from the outlet. Grasp plug and pull to
disconnect.
••
••
•Do not expose the equipment to rain. Do not use on wet surfaces.
••
••
•Plug unit into correct power supply.
••
••
•Do not remove or bypass grounding pin.
Contact with high voltages can cause death or serious injury.
Risk of electrical shock. High voltages are present within the base unit.
••
••
•There are no user serviceable items within the unit.
••
••
•Service on the unit must be performed by qualified personnel.
••
••
•Do not open any part of the base cabinet.
••
••
•Turn power switch off and unplug the unit before servicing.
Contact with high voltages can cause death or serious injury.
SAFETY INSTRUCTIONS
IMPORTANT!! SAVE THESE INSTRUCTIONS
For Reference Only
For Current Info See Equiserv.com

- Page 7 -
EHP Series Operation Instructions
Risk of crushing. Stand clear of bead breaker arm during operation.
••
••
•Read and understand the operation instructions before using this
tire changer.
••
••
•Become familiar with all controls before proceeding with operation.
••
••
•Stand away from the bead breaker arm when in operation.
••
••
•Apply air to breaker in bursts if necessary to control arm depth.
••
••
•Keep all persons clear of tire changer.
Contact with moving parts could cause injury.
Risk of pinching or crushing hands and fingers when mounting and demounting.
••
••
•Read and understand the operation instructions before using this
tire changer.
••
••
•Keep hands and fingers clear of rim edge during demounting and
mounting process.
••
••
•Keep hands and fingers clear of mount/demount head during opera-
tion.
••
••
•Keep hands and other body parts away from moving surfaces.
••
••
•Do not use tools other than those supplied with tire changer.
••
••
•Do not bypass any safety features.
••
••
•Use proper tire lubricate to prevent tire binding.
Contact with moving parts could cause injury.
Risk of eye injury. Flying debris, dirt, and fluids may be discharged during bead
seating and inflation process.
••
••
•Remove any debris from tire tread, wheel surfaces.
••
••
•Remove excess tire lubricant before inflating.
••
••
•Wear approved safety glasses during mount and demount
procedures.
Debris, dirt, and fluids can cause serious eye injury.
Risk of injury. Tools may break or slip if improperly used or maintained.
••
••
•Read and understand the operation instructions before using this
tire changer.
••
••
•Use only the mount-demount tire tool supplied with the tire changer.
••
••
•Frequently inspect, clean, and lubricate (if recommended) where desig
nated.
••
••
•Follow procedures when as instructed in this manual.
Tools that break or slip can cause injury.
IMPORTANT !! SAVE THESE INSTRUCTIONS -- DO NOT DISCARD !!
Warning !
Warning !
For Reference Only
For Current Info See Equiserv.com

- Page 8 -
Tires and Rims that are not the same diameter are mismatched.
••
••
•NEVER attempt to mount or inflate any tire and rim that are mismatched.
••
••
•ALWAYS check to see that tire and rim diameters are the same.
A mismatched tire and rim will explode causing death or serious personal injury
Over-pressurizedtires canexplode causingflying debris.
••
••
•Read and understand Operator’s Manual before operating.
••
••
•Keep bystanders away from work area.
••
••
•ALWAYS wear Safety Goggles.
••
••
•ALWAYS check to see that Tire and Rim diameters are the same.
••
••
•NEVER attempt to mount or inflate any Tire and Rim with different
diameters.
••
••
•Inspect tires, NEVER inflate tires that are damaged, rotten or worn.
••
••
•NEVER inflate ‘Split Rim Wheels’ on this tire changer, remove them and
use only an approved safety inflation cage designed for this purpose.
••
••
•Lock turntable Clamp on inside of rim before attempting to inflate tire.
••
••
•Use approved tire bead lubricant before removing or installing tire on
rim.
••
••
•ALWAYS position the “Safety Restraint Arm” over the wheel to hold it
to the turntable while inflating if so equipped.
••
••
•If a tire explodes on this tire changer, STOP using it until the "Safety
Restraint Arm" has been replaced, which must be done even if no
damage is seen.
••
••
•NEVER place head or body over a tire during inflation process.
••
••
•Use short bursts of air to seat tire beads, check tire air pressure
frequently. NEVER exceed tire manufacturer’s pressure limits.
••
••
•NEVER attempt to bypass or alter the built in air pressure limiter. Only
inflate tire with air hose supplied with tire changer. NEVER use shop
inflation hose to inflate a tire.
••
••
•Tire Changer must be anchored to concrete floor if equipped with a
“Safety Restraint Arm”
ExplodingTires cancauseseriousinjury.
For Reference Only
For Current Info See Equiserv.com

- Page 9 -
EHP Series Operation Instructions
TABLE OF CONTENTS
Safety Statements Page 5-8
Table of Contents Page 9
1.0 Introduction Page 10
1.1 Specifications and Features Page 10
1.2 Nomenclature Page 12
1.3 Dimensions of the Machine Page 12
1.4 StandardAccessories Page 12
1.5 OptionalAccessories Page 13
1.6 General Precautions Page 14
2.0 Installation Page 14
2.1 Electric Installation Page 15
2.2 Air Installation Page 15
3.0 Controls Page 16
4.0 Mounting and Demounting-precautions Page 17
4.1 DemountingTubelessTires Page 17
4.2 MountingTubeless Tires Page 20
4.3 InflatingTubelessTires Page 21
5.0 DemountingTubeTypeTires Page 23
5.1 MountingTubeTypeTires Page 23
5.2 InflatingTubeTypeTires Page 24
6.0 Mounting/Demounting Motorcycle Tires Page 24
7.0 Maintenance Page 25
For Reference Only
For Current Info See Equiserv.com

- Page 10 -
1.0 INTRODUCTION
Congratulations on purchasing the JBC EHP Series elec-
tric/air tire changer. This tire changer is designed for
ease of operation, safe handling of rims, reliability and
speed. This combination of features means more profit
and added versatility for your shop, enabling you to work
with aluminum or magnesium alloy wheels without dam-
aging customer’s rims. With a minimum of maintenance
and care your JBC EHP Series Tire Changer will provide
many years of trouble-free operation.
Please read this manual thoroughly before operating
the unit. Instructions on use, maintenance and opera-
tional requirements of the machine are covered in this
manual.
1.1 SPECIFICATIONS
Operation temperature range +41/+122 F (+5/50 C)
Electric-air tire changers for car, light commercial ve-
hicle and motorcycle tires designed for one-piece rims.
System I
Weight 400 lbs (181 kg)
Air pressure required 110-170 psi (8-12 bar)
Bead breaker force 3300 lbs (kN 15)
Motor 110 VAC 60Hz 1 Hp (kW 0.75)
Max. turntable torque 740 ft-lb (Nm 1000)
Max. wheel diameter 40" (mm 1016)
Max. wheel width 12" (305mm)
Rim diameter outside locking 10"-18"(254-457mm)
Rim diameter inside locking 12"-20"(305-508mm)
Motorcycle wheels with adapters 15"-23"(381-584mm)
System II and III
Weight
System II 530 lbs (240 kg)
System III 572 lbs (260 kg)
Air pressure required 110-170 psi (8-12 bar)
Bead breaker force 3300 lbs (kN 15)
Motor 110 VAC 60Hz 1 Hp (kW 0.75)
Max. turntable torque 740 ft-lb (Nm 1000)
Max. wheel diameter 50" (mm 1270)
Max. wheel width
System II 12"(305.0mm)
System III 17"(431.8mm)
Max. Bead Breaker rim width
System II 13"(330.0mm)
System III 16.5"(419.1mm)
Rim diameter outside locking 10"-18"(254-457mm)
Rim diameter inside locking 12"-20"(305-508mm)
Motorcycle wheels with adapters 15"-23"(381-584mm)
Swing Arm
Detail
Jaw and Air
JetDetail
78
15
546a
Figure 1
21
1.2 NOMENCLATURE
Before installing and using the JBC EHP Series Tire
Changer it is suggested that you become familiar with
the nomenclature of the machine’s components.
1 Vertical slide
2 Swing arm
3 Swing Arm Adjustment knob
4 Lock lever
5 Mount/demount head
6 Tower or column
7 Turntable
8 Clamping Jaws
9 Bead breaker arm
10 Bead breaker blade
11 Bead breaker pads
12 Foot pedal controls
13 Inflation gauge
14 Bead seater/inflator pedal
15 Inflation jets
16 Safety restraint arm (Optional)
17 Safety restraint positioning knob (Optional)
18 Inflation hose
19 Lube bottle
20 Mount/Demount Tool
21 Safety Restraint Arm Anti-rotation Lock
For Reference Only
For Current Info See Equiserv.com

- Page 11 -
EHP Series Operation Instructions
TURNTABLE & CABINET FEATURES
TURNTABLE PLATFORM - Provides easier access to tires
lower bead during the tire changing process.
INTEGRATED BEAD SEATING JETS -Airinflationjets are
integrated into the turntable clamping jaws to insure full bead seating
force directly into the tire cavity regardless of tire diameter.
ADJUSTABLE BEAD BREAKER OPENING-Simple two
position bead breaker pin adjustment allows for readjusting breaker
to fit larger OD tires. (System III only)
TWIN CYLINDER CLAMPING POWER - Two cylinders provide
uniform clamping pressure throughout the stroke (regardless of rim
sizes) as well as providing 25% more clamping power than most
single clamping cylinder tire changers. Additionally two samller
cylinders reduce the critical turntable to cabinet distance, reducing
the stress on the transmission.
WHEEL CLAMPS
UNIQUE SIX POINT CONTACT CLAMPS
Provide better gripping capability regardless of dirt and
moisture.
REDUCEDANGLECLAMPS
Increases clamping contact area with rim insuring no slippage.
NYLON INSERT SOFT TOUCH CLAMPS
Single sided nylon insert in the clamping jaws provides non-
metal touch in critical customer visible areas.
VALVE CORE/TIRE TOOLSTORAGE
On tire changer storage area for valves, tools, caulk, etc.
IN-COMINGAIRPRESSUREGAUGE
Ergonomically located air gauge allows easy monitoring of incoming
air pressure.
INTEGRATEDPRESSURELIMITER
Integrated safety pressure limiter stops air flow once tire pressure
has reached approx. 55 PSI preventing accidential tire over-inflation.
MOUNT/DEMOUNT ARM ASSEMBLY
SURGE TANK IN THE TOWER - Space saving design integrates
the air storage surge tank in the tower allowing for flush to wall tire
changer installation
ADJUSTABLE SLIDEWAY - Unique adjustable mount/demount
shaft slideway allows for easy operator adjustment to compensate
for any cumulative wear in the slideway causing mount/demount
head movement.
NON-SCRATCH NYLON INSERT - Integrated into the mount/
demounthead is a replaceable scratch resistent nylon insert
protecting against accidental rim contact.
SAFETY RESTRAINT ARM (Optional)
TIRE/RIM ASSEMBLYRESTRAINT - Safety Restraint Arm
positively restrains tire and rim assembly to the tire machine during
the inflation process reducing potential for injury caused by the
unlikely event of castrophic tire or rim failure.
SIMPLE SWING ARM DESIGN - SRA arm easily swings to the
left when not in use allowing the technician to quickly and safely
perform the inflation process without disrupting the tire changing
procedure.
GRAVITY LOCK - SRA lock mechanism operates without any
mechanical cam system eliminating the possibility of system
deterioration or misadjustment from mechanical wear.
POSITIONING SAFETY INTERLOCK SWITCH - Integrated
switch insures that SRA arm is centered on the tire/rim assembly
before the inflation process can begin.
ANTI-ROTATION LOCK - Prevents SRA from rotating during
inflation process.
CONSTRUCTIONDESIGNEDFORDURABILITY
RUST PROOF VALVES AND CYLINDERS - Critical bead
breaking cylinder is lined with rust-proof polyfiber liner for years of
rust free operation. Non-lined cylinders will pit causing bead
breaker power loss.
LIFETIME LUBRICATED POLYMER VALVES - Critical
footvalves fabricated from glass/fiber self lubricating material
providing years of maintenance free operation.
WATER SEPARATOR ANDAUTOMATIC OILER - Lubricates
all air used for machine operation, does not lubricate air used for tire
inflation, as do some competitive models.
HIGH TORQUE 1HP MOTOR - Industrial strength high torque
turntable drive motor eliminates tire remount stalling on low profile
high performance tires (UL/CSA approved ).
5 YEAR TRANSMISSION WARRANTY - Designed for
extremely heavy use the critical motor to turntable transmission
linkage carries a full five (5) year replacement warranty.
For Reference Only
For Current Info See Equiserv.com

- Page 12 -
1.3 MACHINE DIMENSIONS - System I
MACHINE DIMENSIONS - System II and III
547
Figure 2
1.4 STANDARDACCESSORIES
87111 - Mount /Demount Tool (Fig.3)
294
Figure 3
Inflation Guage is mounted on the Inflation Tank Col-
umn. (Not shown)
Air Filter andAir Lubricator, (Fig.4)
539
Figure 4
Incoming Air Pressure Gauge
Located on the air filter and the air lubricator
Lubrication Bottle
Lubrication Applicator
Replacement Mount/Demount Head Inserts (4)
For Reference Only
For Current Info See Equiserv.com

- Page 13 -
EHP Series Operation Instructions
1.5 OPTIONALACCESSORIES
87435 - Motorcycle Adapter (Fig.5)
320
Figure 5
87436 - 8" Wheel Adapter (Fig.5)
316
Figure 6
66735 - Bead Holding Clamp (Fig.7)
315
Figure 7
For Reference Only
For Current Info See Equiserv.com
EAA0332G84A
ST4028566 or
EAA0304G23A

- Page 14 -
1.6 GENERALCAUTIONS
A. DURING THE USE AND MAINTENANCE OF THE MA-
CHINE IT IS MANDATORY TO COMPLY WITHALLLAWS
ANDREGULATIONS FORACCIDENT PREVENTION.
B. THE ELECTRICAL POWER SOURCE MUST HAVE A
GROUND CABLE AND THE GROUND CABLE OF THE
MACHINE MUST BE CONNECTED TO THE GROUND
CABLE OF THE POWER SOURCE.
C. BEFOREANY MAINTENANCE OR REPAIRS AREAC-
COMPLISHEDTHE MACHINEMUST BEDISCONNECTED
FROM THEAIRAND ELECTRICAL SUPPLY.
D. NEVER WEAR TIES, CHAINS OR OTHER LOOSE AR-
TICLESWHEN USING, MAINTAINING OR REPAIRINGTHE
MACHINE. LONG HAIR IS ALSO DANGEROUS AND
SHOULD BE KEPT UNDER A HAT. THE USER MUST
WEAR PROPER SAFETY ATTIRE - GLOVES, SAFETY
SHOES AND GLASSES.
2.0 INSTALLATION
Your new JBC EHP SeriesTire Changer requires a
simple installation procedure requiring only a few mo-
ments. Follow these instructions carefully to insure
proper and safe operation.
The Tire Changer is delivered mounted to a wooden
skid. Remove tire changer from its mounts carefully,
taking care to avoid any back strain.
Place Changer where proper operation will be unob-
structed to all sides. Install the machine in a covered
and dry place.
2.0.1 Models with SRA attached
Once placed in the desired location the tire changer
must be bolted to the floor using only the rear two mount-
ing holes. Mounting anchors are provided with those
machines with a Safety Restraint Arm.
Tire Changer must be anchored to concrete floor
if equipped with a “Safety Restraint Arm”
2.1 ELECTRICAL INSTALLATION
BUILDING ELECTRICAL INSTALLATION MUST BE
MADE BY A LICENSED ELECTRICIAN.
Check that the electrical specifications of the power
source are the same of the machine. The machine uses
110v, 60 hz, single phase 20 amp source. Electric
specifications are clearly marked on a label at the rear
of the machine.
FAILURE TO PROVIDE PROPER ELECTRICAL
SUPPLY AND GROUNDING WILL CREATE A
SHOCK HAZARD TO THE OPERATOR.
540
For Reference Only
For Current Info See Equiserv.com

- Page 15 -
EHP Series Operation Instructions
2.2 BEAD BREAKER INSTALLATION
The side mounted Bead Breaker is shipped from the
factory dismounted for a more compact shipping pack-
age.
A. Cut the plastic tie strap which secures the Breaker
Arm to the cabinet pivot.
B. Remove the “C” clip from the top of the pivot pin, slip
the pin out of the hole.
C. Place the Breaker Arm into position and insert the
pivot pin through the top and bottom holes.
D. Replace the “C” clip retainer onto the pivot pin.
E. Locate the spring located at the rear of the pivot
mount. Place the free end of the spring onto the “ear”
located on the Breaker Arm just forward of the pivot.
HINT: You may tie a small rope or cord onto the free end
of the spring, run the cord through the hole. Pull the
spring end toward the ear and loop free end over.
2.3 AIR INSTALLATION
THE AIR INSTALLATION MUST BE MADE ONLY
BY QUALIFIED PERSONNEL.
EXCESSIVEAIR PRESSURE CAN SERIOUSLY IN-
JURE PERSONNEL AND DAMAGE THE MACHINE.
Ensure that the line pressure is within the limits re-
quired by the machine. If the pressure exceeds 170 psi
(12 bar) it is mandatory to install a pressure regulator
before the air inlet of the machine.
If the air pressure is lower than the minimum required
of 110 psi (8 bar) the clamping power of the turntable
and the bead breaker power may be insufficient for cer-
tain tires and substantially reduces tire changer perfor-
mance.
It is suggested that the air supply be equipped with a
water separator/dryer type modification for maximum
performance.
After ensuring all the above proceed as follows:
A. Connect the machine to the air supply with a rubber
hose (rated for the pressure) with an internal diameter
of no less than 1/2" (12.5mm).
WARNING!
BEFORE CONNECTING THE
MACHINE TO THE AIR SUP-
PLY BE SURE ALL PERSON-
NEL ARE CLEAR OF THE MA-
CHINE AND NO ITEMS ARE
LEFT ON THE TURNTABLE.
B. It is recommended that an air valve shut-off be in-
stalled between the shop air supply and the tire changer
in case of air line or filter failure.
C. Should you install any optional accessories, please
refer to the relevant instructions.
D. Ensure the functional ability of the air lubricator by
ensuring that the glass site bowl is filled with air lubri-
cant.
For Reference Only
For Current Info See Equiserv.com

- Page 16 -
3.0 CONTROLS
549
Figure 8
Before operating the machine, take the time to familiar-
ize yourself with the operation and function of all the
controls.
APress down and release the first pedal (1) from the
left: the jaws of the turntable will retract. Do it again:
the jaws will expand. If you press the pedal prior to
the end of the stroke and release, the jaws may be
stopped in any position.
BOpen the bead breaker arm. Press down and hold
the second pedal (2) from the left: by doing this you
operate the bead breaker blade and the arm will
move towards the machine. Release the pedal:
the bead breaker blade will retract.
WARNING!
WATCH YOUR FINGERSANDLEGS!
541a 542a
CPress down the first pedal (3) from the right: the
turntable turns clockwise. Placing your foot under
the pedal and lift, the turntable turns counterclock-
wise.
DLower the Lock Lever (4 ) to unlock the vertical slide,
lift the Lock Lever to lock.
ETurn Swing Arm Adjustment Knob (5) for position-
ing mount/demount head slightly away from rim di-
ameter
FPress bead-seater pedal on left side of the ma-
chine (6 ) half way down: air will come out from
inflation hose end.
GPress bead-seater pedal (6) all the way down swiftly
to get air blast from the inflator jets in the clamping
jaws. Air simultaneously comes out of inflator hose.
ATTENTION!
WHEN OPERATING THE BEAD SEATER IT IS MANDA-
TORYTO WEAR SAFETY GLASSES TOPROTECT EYES.
Models with SRA attached
HSafety RestraintArm (7) swings to center of the turn-
table.
ILift upward on the restraint positioning knob (8) to
position over tire/wheel assembly for inflation, at
the same time push down on the Anti-rotation Lock
Arm to release lock. (9) You may now swing the
safety restraint arm to position on the center of the
wheel. Lower the restraint until the rubber pad on
the restraint disc is resting on the rim center. The
SRA is a gravity lock which will automatically lock if
any force other than the restraint position knob is
lifted. You are now ready for the inflation process.
NOTE: the air supply will not function until the safety
arm is centered over the turntable.
9
For Reference Only
For Current Info See Equiserv.com

- Page 17 -
EHP Series Operation Instructions
4.0 MOUNTING AND DEMOUNTING PRECAUTIONS
IMPORTANT!
BEFORE MOUNTINGATIRE ONA RIM, PAYATTENTION
TOTHE FOLLOWING:
A.THE RIM MUST BE CLEANAND IN GOOD CONDITION:
IF NECESSARY CLEAN IT AFTER REMOVING ALL
WHEEL-WEIGHTS INCLUDING ‘TAPE WEIGHTS’INSIDE
THE RIM.
B. THE TIRE MUST BE CLEANAND DRY, WITHOUT ANY
DAMAGETO THE BEAD.
C. REPLACE THE RUBBER VALVE STEM WITH ANEW
ONE OR REPLACE THE ‘O’RING IF THE VALVE STEM IS
MADEOF METAL.
D. IF THE TIRE REQUIRES A TUBE, MAKE SURE THE
TUBE IS DRY AND IN GOOD CONDITION.
E. LUBRICATION IS NECESSARY TO MOUNT THE TIRE
CORRECTLYAND GETAPROPERCENTERING.BE SURE
YOUARE USINGAPPROVED LUBRICANT ONLY.
F. MAKE SURE THE TIRE IS THE CORRECT SIZE FOR
THE RIM.
4.1 DEMOUNTING TUBELESS TIRES
A. Remove all wheel-weights from the rim. Remove the
valve stem or valve stem core and deflate the tire (Fig.11).
535a
Fig.11
B. Break both beads.
Hold open the Bead Breaker, roll the tire/rim into the
Breaker area (Fig. 12). Ensure that the Tire/rim assem-
bly is against the rubber breaker pads on the side of the
machine. Make certain that the bead breaker blade is
not over the top of any portion of the rim. Now activate
the bead breaker pedal. As soon as the bead dislodges
from the rim, release the breaker foot pedal. It may be
necessary to rotate the tire 90 degrees and repeat the
above procedure to dislodge all beads.
Pay extra attention during this operation as it easy to
mistakenly keep your foot on the bead breaking pedal
too long. This could potentially result in bead or rim
damage
(Fig.12)
536
Fig.12
NOTICE!
ON “RUN FLAT”TYPE WHEELS WITH THE OPTIONAL
LOW PRESSURE SENSOR INSTALLED, BREAK THE
BEADAT 90DEGREES OFFSET FROMTHE VALVESTEM.
DAMAGE TO THE WHEEL AND/OR SENSOR WILL RE-
SULT IF THE BEAD IS BROKEN ATANY OTHER POINT
ON THE RIM.
C. Set the rim clamps to the proper position: retract
clamps to clamp the wheel from the outside and ex-
pand clamps to clamp from the inside.
When clamping small wheels (14" or smaller) from the
outside, set the clamps at a diameter nearly equal to
the rim diameter, before placing the wheel on the
clamps. This will help avoid the possibility of pinching
the tire as the clamps retract.
NOTICE!
TO MINIMIZE THE RISK OF SCRATCHING ALLOY OR
CLEAR COATED RIMS, THESE RIMS SHOULD BE
CLAMPED FROM THE OUTSIDE.
For Reference Only
For Current Info See Equiserv.com

- Page 18 -
D. Liberally lubricate both beads. Place the wheel WITH
DROP CENTER UP (Fig.13a) on the turntable, and clamp
in position. Hold the tire and wheel down while clamping.
331
Fig.13 Fig. 13a
E. Gently position the mount/demount head in contact
with rim edge, now manually push the lock lever up and
lock it into place. The tool automatically moves verti-
cally up and away from the rim edge. Turn the swing
arm adjustment knob until the mount/demount head
moves horizontally away from the rim flange by approxi-
mately 1/16" (2mm): this is necessary to avoid any rim
contact during the changing process. (Fig.14).
332
Fig.14
NOTE:
EVERY MACHINE IS EQUIPPED WITH SEVERAL RE-
PLACEMENT PLASTIC INSERTS (INSIDE STANDARD
EQUIPMENTPACK). THE PLASTIC INSERTS WILLHELP
AVOID DAMAGE FROM ACCIDENTAL CONTACT BE-
TWEEN THE MOUNT/DEMOUNT HEAD AND THE RIM.
THE PLASTIC INSERTS WILL NEED TO BE PERIODI-
CALLYREPLACED.
MAINTENANCENOTE:
IF THE MOUNT/DEMOUNT HEAD NYLON INSERTS ARE
WEARING OUT PREMATURELY, THE CAUSE IS THE OP-
ERATORS FAILURE TO CORRECTLY SET THE SWING
ARM ADJUSTMENT KNOB, CAUSING THE INSERT TO
INCORRECTLY CONTACT THE RIM.
NOTE:
ONCE THE MOUNT/DEMOUNT HEAD IS POSITIONED
PROPERLY, IDENTICAL WHEELS MAY BE CHANGED
WITHOUT HAVING TO RESET THE HEAD.
F. Insert the mount/demount tool under the bead and
over the support of the mount/demount head. Lift the
bead onto the mount/demount head. To make this op-
eration easier, insure that the bead of the tire, directly
across from the mount/demount head, is in the drop
center of the wheel. Push the tire into the drop center
with your hand or bead depressor tool if necessary.
If desired, the mount/demount tool can be removed af-
ter lifting the bead onto the mount/demount head
(Fig.15), or you may remove the tool after the bead has
been removed.
1/16”
For Reference Only
For Current Info See Equiserv.com

- Page 19 -
EHP Series Operation Instructions
333
Fig.15
G. Rotate the turntable clockwise (pedal down) and, at
the same time, push down on the tire sidewall to move
the bead into the drop center of the rim (Fig.16).
334
Fig.16
H. Repeat the process for removing the lower bead.
This time, lift the bead opposite to the mount/demount
head to keep it in the drop center (Fig.17).
Move the swing arm aside and remove the tire.
335
Fig.17
For Reference Only
For Current Info See Equiserv.com

- Page 20 -
4.2 MOUNTING TUBELESS TIRES
A. Clean entire rim surface (Fig.18).
336
Fig.18
Liberally lubricate both beads of the tire with approved
tire lubricant (Fig.19).
337
Fig.19
NOTICE!
THESE LUBRICATION OPERATIONSARE NECESSARY
TO MOUNT THE TIRE CORRECTLYAND GET APROPER
CENTERING ON THE RIM. BE SURE YOU ARE USING
APPROVED LUBRICANT ONLY.
DANGER!! Keep hands
and fingers clear of
mount-demount head
during operaton.
For Reference Only
For Current Info See Equiserv.com
This manual suits for next models
2
Table of contents
Other John Bean Tyre Changer manuals
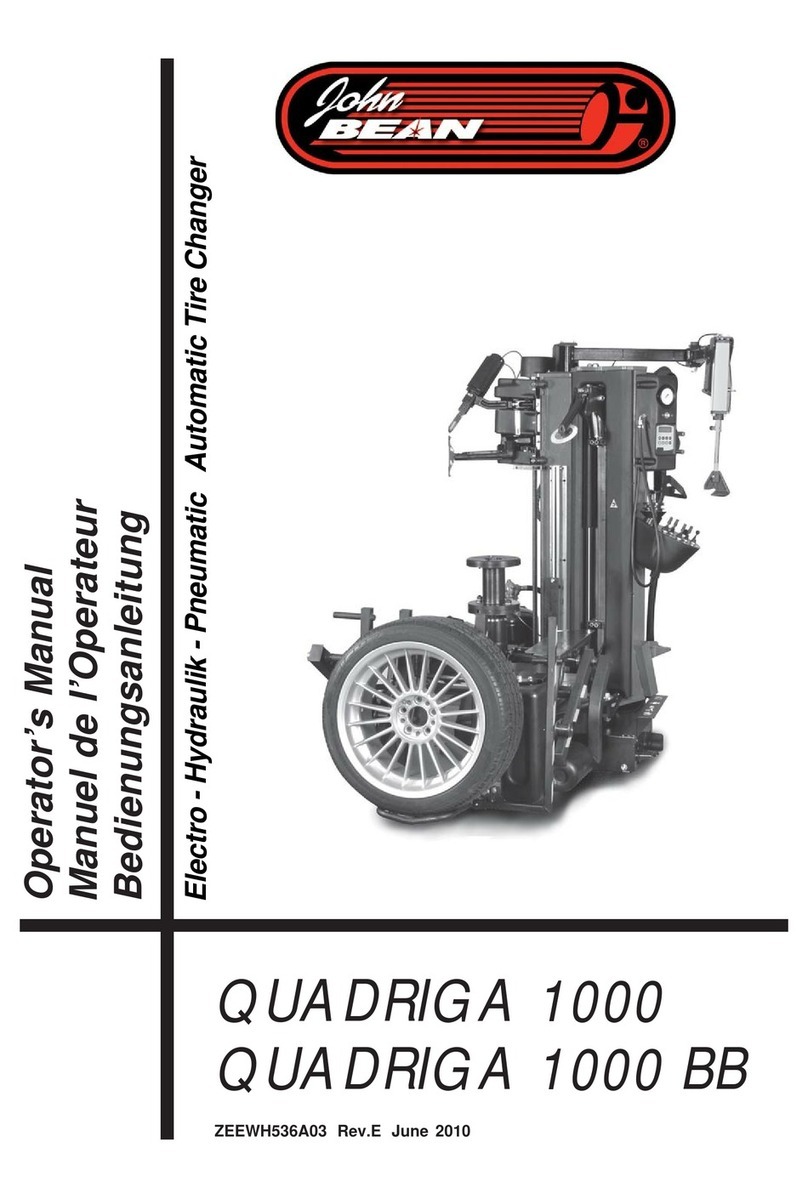
John Bean
John Bean QUADRIGA 1000 User manual
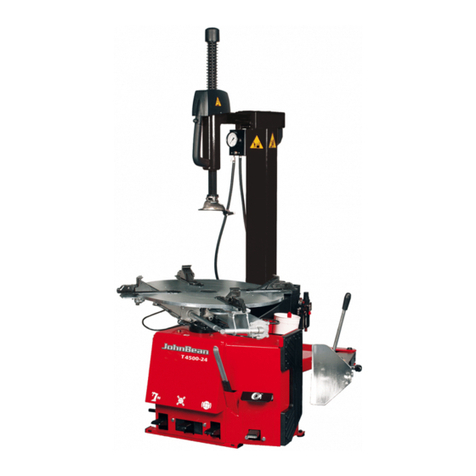
John Bean
John Bean T4500-24 User manual
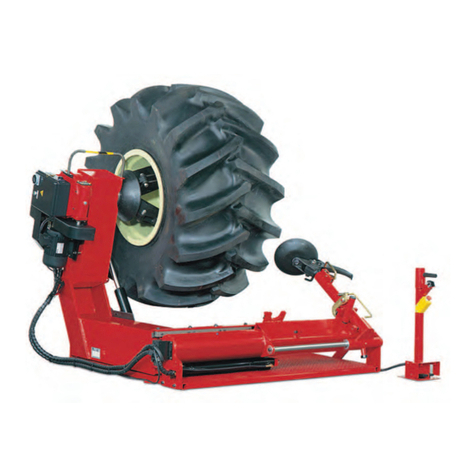
John Bean
John Bean T 8056 User manual
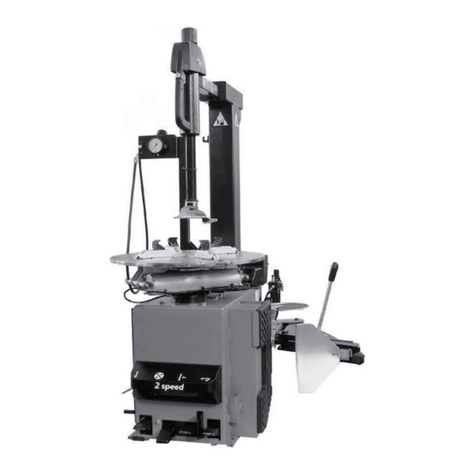
John Bean
John Bean T 3300-24 User manual
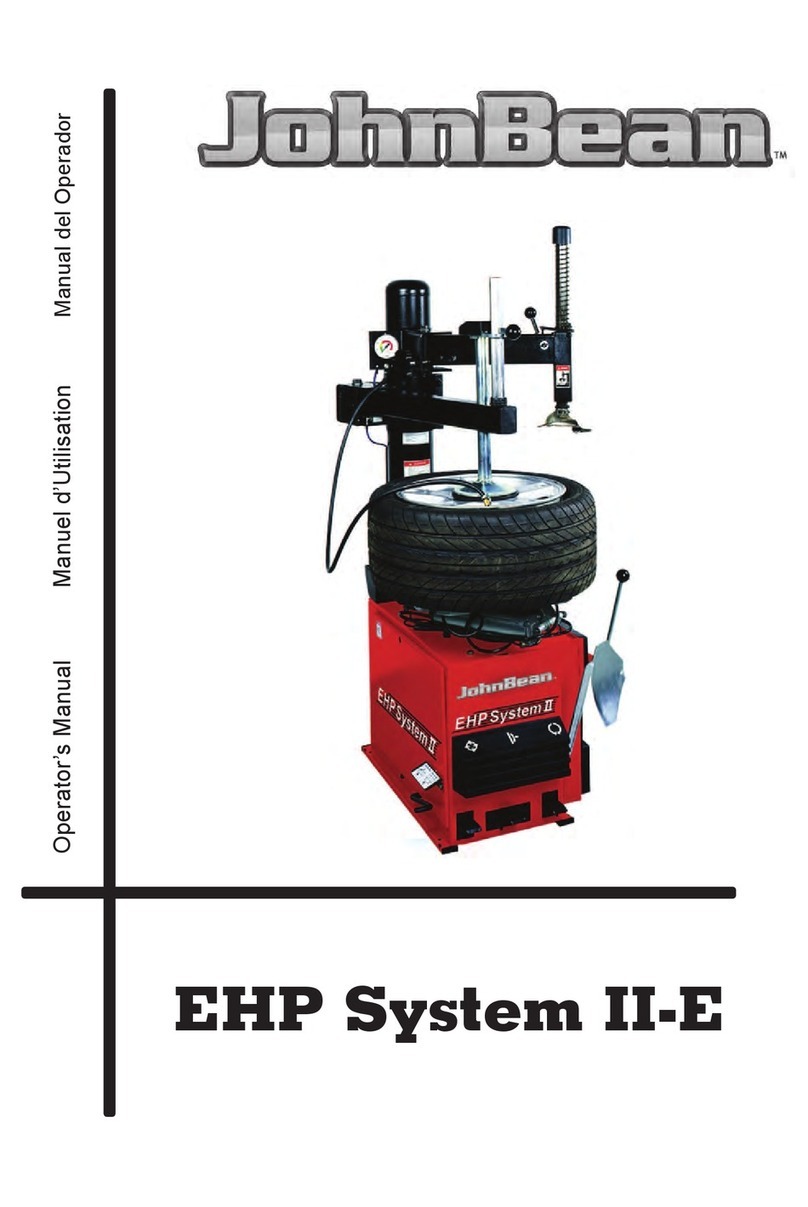
John Bean
John Bean EHP II-E User manual
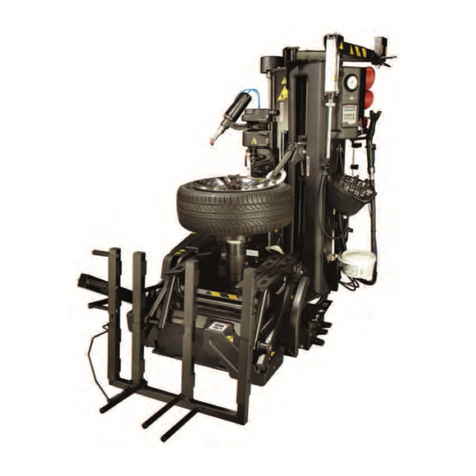
John Bean
John Bean QUADRIGA 1000 User manual
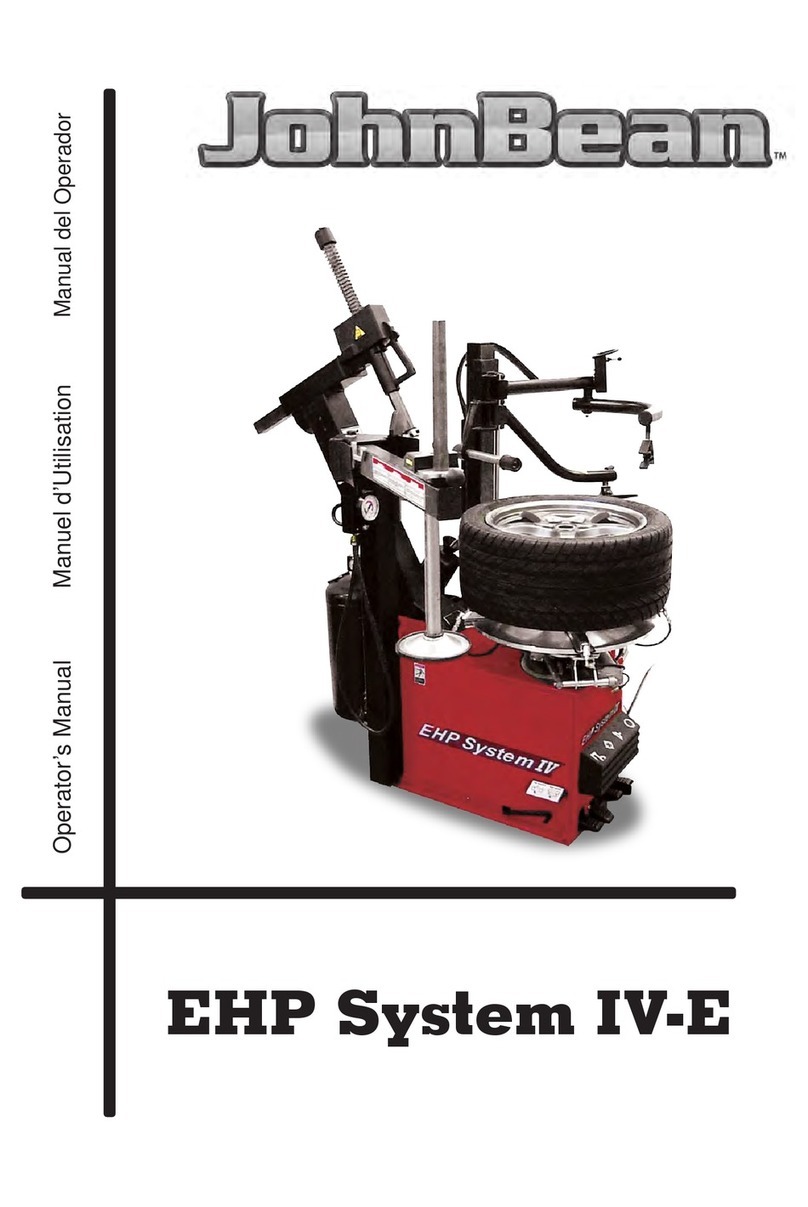
John Bean
John Bean EHP System IV-E User manual
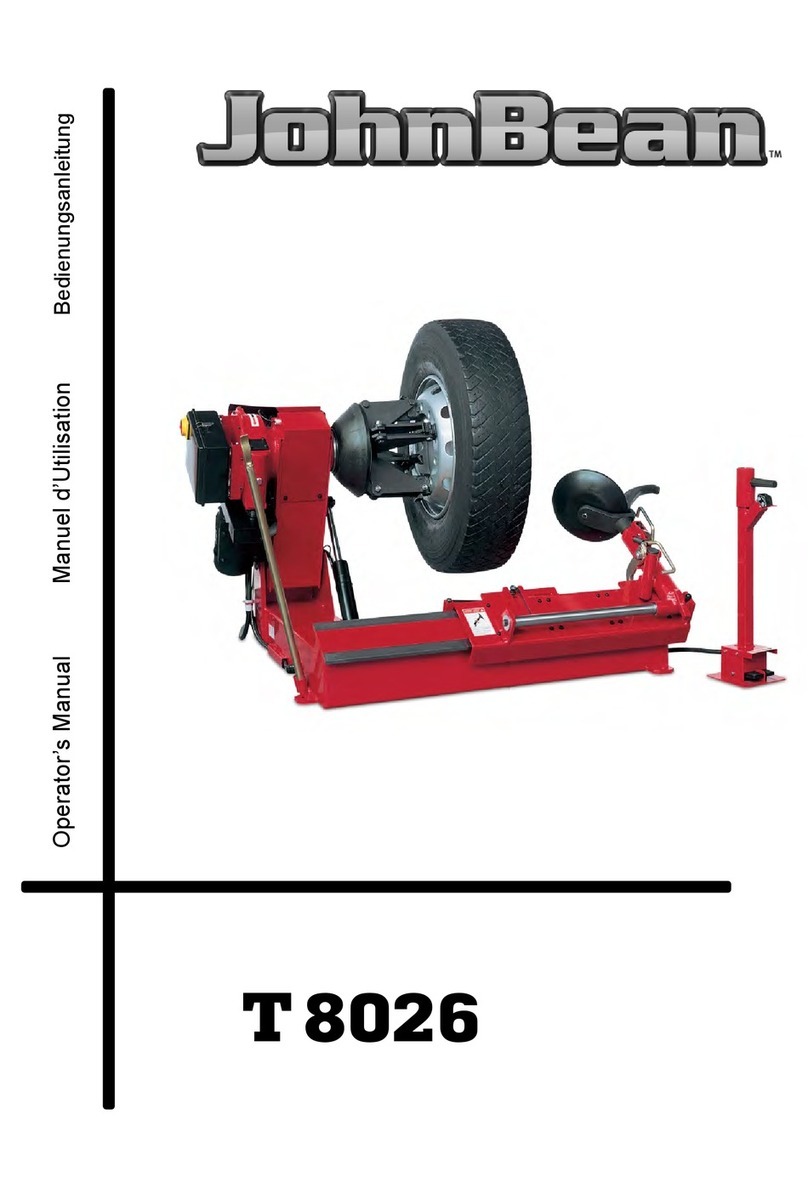
John Bean
John Bean T 8026 User manual
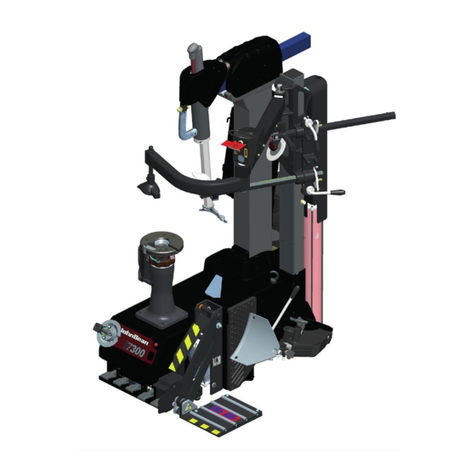
John Bean
John Bean T7300 User manual
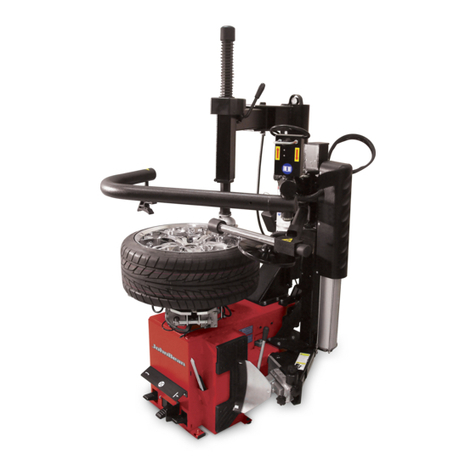
John Bean
John Bean EHP System III-E User manual