KIESELMANN 6125 User manual

Operating instruction
Translation of the original
Aseptic - sampling valve
Type 6125
pneumatical
manual
GB
ENGLISHPDF • ak • 22/11/2021

KIESELMANN GmbH
Paul-Kieselmann-Str. 4-10
D - 75438 Knittlingen
( +49(0) 7043 371-0 • 7 +49(0) 7043 371-125
www.kieselmann.de • [email protected]
Copyright: © KIESELMANN FLUID PROCESS GROUP

KIESELMANN GmbH Table of contents
6125_APNV_EN 3
Table of contents
1 General informations ....................................................................................................................................................4
1.1 Informations for your safety ...............................................................................................................................................4
1.2 Marking of security instructions.........................................................................................................................................4
1.3 General designated use ......................................................................................................................................................4
1.4 Personnel .............................................................................................................................................................................4
1.5 Modifications, spare parts, accessories ............................................................................................................................5
1.6 General instructions ............................................................................................................................................................5
2 Safety instructions........................................................................................................................................................6
2.1 Intended use ........................................................................................................................................................................6
2.2 General notes.......................................................................................................................................................................6
2.3 General safety instructions.................................................................................................................................................6
3 Delivery, transport and storage .....................................................................................................................................7
3.1 Delivery.................................................................................................................................................................................7
3.2 Transport..............................................................................................................................................................................7
3.3 Storage.................................................................................................................................................................................7
4 Specification.................................................................................................................................................................8
4.1 Modular system...................................................................................................................................................................8
5 Function and operation .................................................................................................................................................9
5.1 Description of function........................................................................................................................................................9
5.2 Control system and position indicator...............................................................................................................................9
6 Commissioning, service and maintenance ..................................................................................................................10
6.1 Commissioning..................................................................................................................................................................10
6.1.1 Installation instructions....................................................................................................................................... 10
6.1.2 General welding guidelines ................................................................................................................................. 10
6.1.3 ATEX - Guidelines ................................................................................................................................................ 10
6.2 Service................................................................................................................................................................................11
6.3 Cleaning .............................................................................................................................................................................11
6.4 Sterilization ........................................................................................................................................................................11
7 Technical data ............................................................................................................................................................13
8 Disassembly and assembly .........................................................................................................................................14
8.1 Disassembly - sampling valve ..........................................................................................................................................14
8.2 Assemble - sampling valve ...............................................................................................................................................18
8.3 Dismantle - steam valve DV..............................................................................................................................................19
8.4 Assemble - steam valve ....................................................................................................................................................20
9 Drawings and dimensions ...........................................................................................................................................21
9.1 Drawings ............................................................................................................................................................................21
9.2 Dimensions ........................................................................................................................................................................26
10 Wearing parts .............................................................................................................................................................27
10.1 Wear parts kit.....................................................................................................................................................................27
10.2 Spare parts list...................................................................................................................................................................27
11 Classification..............................................................................................................................................................29
11.1 Structure of Order Number ...............................................................................................................................................29
12 Appendix ....................................................................................................................................................................32
12.1 Declaration of incorporation.............................................................................................................................................32

Operating instruction | KIESELMANN GmbH1 | General informations
4 / 32 6125_APNV_EN
1 General informations
1.1 Informations for your safety
We are pleased that you have decided for a high-classKIESELMANN product. With correct applica-
tion and adequate maintenance, our products provide long time and reliable operation.
Before installation and initiation, please carefully read this instruction manual and the security ad-
vices contained in it. This guarantees reliable and safe operation of this product and your plant re-
spectively. Please note that an incorrect application of the process components may lead to great
material damages and personal injury.
In case of damages caused by non observance of this instruction manual, incorrect initiation, hand-
ling or external interference, guarantee and warranty will lapse!
Our products are produced, mounted and tested with high diligence. However, if there is still a
reason for complaint, we will naturally try to give you entire satisfaction within the scope of our war-
ranty. We will be at your disposal also after expiration of the warranty. In addition, you will also find
all necessary instructions and spare part data for maintenance in this instruction manual. If you
don't want to carry out the maintenance by yourself, ourKIESELMANN - service team will naturally
be at your disposal.
1.2 Marking of security instructions
Hints are available in the chapter "safety instructions" or directly before the respective operation in-
struction. The hints are highlighted with a danger symbol and a signal word. Texts beside these
symbols have to be read and adhered to by all means. Please continue with the text and with the
handling at the valve only afterwards.
Symbol Signal word Meaning
DANGER Imminent danger which will result severe personal injury or
death.
WARNING Imminent danger which may result severe personal injury or
death.
CAUTION Dangerous situation which may cause slight personal injury or
material damages.
NOTICE An harmful situation which may result in damages of the product
itself or of adjacent vicinity.
INFORMATION Marks application hints and other information which is particu-
larly useful.
1.3 General designated use
The fitting is designed exclusively for the purposes described below. Using the fitting for purposes
other than those mentioned is considered contrary to its designated use.KIESELMANNcannot be
held liable for any damage resulting from such use. The risk of such misuse lies entirely with the
user. The prerequisite for the reliable and safe operation of the fitting is proper transportation and
storage as well as competent installation and assembly. Operating the fitting within the limits of its
designated use also involves observing the operating, inspection and maintenance instructions.
1.4 Personnel
Personnel entrusted with the operation and maintenance of the tank safety system must have the
suitable qualification to carry out their tasks. They must be informed about possible dangers and
must understand and observe the safety instructions given in the relevant manual. Only allow quali-
fied personnel to make electrical connections.

KIESELMANN GmbH | Operating instruction General informations | 1
6125_APNV_EN 5 / 32
1.5 Modifications, spare parts, accessories
Unauthorized modifications, additions or conversions which affect the safety of the fitting are not
permitted. Safety devices must not be bypassed, removed or made inactive. Only use original spare
parts and accessories recommended by the manufacturer.
1.6 General instructions
The user is obliged to operate the fitting only when it is in good working order. In addition to the in-
structions given in the operating manual, please observe the relevant accident prevention regula-
tions, generally accepted safety regulations, regulations effective in the country of installation,
working and safety instructions effective in the user's plant.

Operating instruction | KIESELMANN GmbH2 | Safety instructions
6 / 32 6125_APNV_EN
2 Safety instructions
2.1 Intended use
The sampling valve is used to remove or vent liquid or gaseous media from tanks or pipe system in
plants of the food and drink industry, pharmaceutical and chemical industries as well as in biotech-
nology.
2.2 General notes
NOTICE - observe the operating instructions
To avoid danger and damage, the fitting must be used in accordance with the safety instructions
and technical data contained in the operating instructions.
NOTICE
All data are in line with the current state of development. Subject to change as a result of tech-
nical progress.
2.3 General safety instructions
WARNING
Risk of injury by outflowing medium
Dismantling the valve or valve assemblies from the plant can cause injuries.
– Medias flowing through the leakage drain outlet are to be drained off without splashing
into a discharge arrangement.
– Carry the disassembling only if when the plant has been rendered pressure-less and free
of liquid and gas.
CAUTION
Risk of burning whilst flaming the valve!
There is a risk from burns of parts of the body.
ØThe valve gets very hot under flaming. When flaming the valve,
– wear suitable protective gloves and protective clothing
– local fire safety regulations must be followed.
CAUTION
Destroy of the valve seal when flaming the valve!
The valve seal can be destroyed by excessive heat supply.
ØThe valve must be flamed generally by trained personnel.
– The instructions in the chapter “Sterilization” must be observed.

KIESELMANN GmbH | Operating instruction Delivery, transport and storage | 3
6125_APNV_EN 7 / 32
3 Delivery, transport and storage
3.1 Delivery
• Immediately after receipt check the delivery for completeness and transport damages.
• Remove the packaging from the product.
• Retain packaging material, or expose of according to local regulations.
3.2 Transport
CAUTION
Risk of injury and damage to the product
During the transport the generally acknowledged rules of technology, the national accident preven-
tion regulationsand company internal work and safety regulations must be observed.
3.3 Storage
NOTICE
Damage to the product due to improper storage!
Observe storage instructions
avoid a prolonged storage
INFORMATION
Recommendation for longer storage
We recommend regularly checking the product and the prevailing storage conditions during long
storage times.
• To avoid damage to seals and bearings,
– products up to DN 125 / OD 5 inch should be stored horizontally for maximum 6 months.
– products larger than DN 125 / 5 inch, should be stored in the upright position with the actu-
ator on top.
• Don't store any objects on the products.
• Protect the products for wetness, dust and dirt.
• The product should be stored in a dry and well ventilated room at a constant temperature (op-
timal indoor temperature: 25 C ±5; indoor humidity data 70% ±5%).
• Protect seals, bearings and plastic parts for UV light and ozone.

Operating instruction | KIESELMANN GmbH4 | Specification
8 / 32 6125_APNV_EN
4 Specification
4.1 Modular system
Mounted on top /
Automation
Cover ring Sensor assembly*
(Sensor with thread M12)
Control head assembly*
Actuator
Type 6125 xxx00x-xxx
manual
(spring closing)
Type 6125 xxx01x-xxx
manual
(self-locking) **
Type 6125 xxx03x-xxx
pneumatical & manual
(spring closing)
Type 6125 xxx02x-xxx
pneumatical
Housing connec-
tions
INLINE Module t-piece
(DN 25-150 / OD 1½-4)
Tank welding socket Welding neck
(DN 25)
Outlet
Screw socket
(G 3/8)
Tube end
(DN 10)
Screw socket with blind nut
(G 3/8)
Clip-on
Rinsing connection
without connecting
piece
Screw socket
(G 3/8)
Tube end
(DN 10)
Screw socket with
blind nut (G 3/8)
Clip-on
Steam valve
Manual
Steam valve
Pneumatic
Steam valve
Pneumatic
with sensor assembly
Steam valve
Pneumatic
with control head
* can be adapted only with pneumatic actuator
** may not be combined with pneumatic actuator

KIESELMANN GmbH | Operating instruction Function and operation | 5
6125_APNV_EN 9 / 32
5 Function and operation
5.1 Description of function
Description of function
The function of the aseptic sampling valve is to remove sampling
from the systems and pipes under hygienic conditions. The valve
is opened pneumatically over the air connections (LA) or manually
operated over the lever clockwise opened and closed with spring
tension. Valves with a self-locking spindle are opened with a lever
clockwise and closed anti-clockwise.
At open valve, the product flows out through the outlet pipe (B).
Leaks will be discharged through the leakage hole (L).
5.2 Control system and position indicator
Feedback unit -optional-
Optionally, modular valve control head systems can be installed to the actuator for reading and ac-
tuating valve positions. The standard version is a closed system with SPS or ASI-bus switch-on
electronics, and integrated 3/2-way solenoid valves. For tough operating conditions we recommend
employing a high-grade steel cover.
Feedback unit with finger guard -optional-
For the acquisition of the valve positions over inductive initiators (Sensors), a feedback unit is
mounted on the actuation. The enquiry takes place over the position of the piston rod.

Operating instruction | KIESELMANN GmbH6 | Commissioning, service and maintenance
10 / 32 6125_APNV_EN
6 Commissioning, service and maintenance
6.1 Commissioning
6.1.1 Installation instructions
Installation Position
The valve must be installed so that the product can run out of the outlet spigot leaving no residue.
6.1.2 General welding guidelines
Sealing elements integrated in weld components must generally be removed prior to welding. To
prevent damage, welding should be undertaken by certified personnel (EN ISO 9606-1). Use the TIG
(Tungsten Inert Gas) welding process.
CAUTION
Damage and injuries due to high temperature supply
To avoid a distortion of the components, all welding parts must be welded to stress-relieved.
Allow all components to cool before assembling.
NOTICE
Damage due to impurities
Impurities can cause damage to the seals and seals area.
Clean inside areas prior to assembly.
6.1.3 ATEX - Guidelines
For valves or plants/installations that are operated in the ATEX area, sufficient bonding (grounding)
must be ensured (see valid ATEX Guidelines EG).

KIESELMANN GmbH | Operating instruction Commissioning, service and maintenance | 6
6125_APNV_EN 11 / 32
6.2 Service
RECOMMENDATION
Replacement of seals
To achieve optimal maintenance cycles, the following points must be observed!
– When replacement of seals, all product-contacting seals should be replaced.
– Only original spare parts may be installed.
Maintenance interval
The maintenance intervals depend on the operating conditions "temperature, temperature-intervals,
medium, cleaning medium, pressure and opening frequency". We recommend replacing the seals 3-
year cycle.The user, however should establish appropriate maintenance intervals according to the
condition of the seals.
Lubricant recommendation
EPDM; HNBR; NBR; FKM; k-flex - Klüber Paraliq GTE703*
Silicone - Klüber Sintheso pro AA2*
Thread - Interflon Food*
*) It is only permitted to use approved lubricants, if the respective fitting is used for the produc-
tion of food or drink. Please observe the relevant safety data sheets of the manufacturers of lub-
ricants.
6.3 Cleaning
SP
L
B
The cleaning of the valve occurs in the closed state over con-
nection (B), whereat with concurrent cleaning of the tank or
pipe system the valve can be opened. For valves with rinsing
connection the cleaning occurred via connection (SP).
6.4 Sterilization
The valve can be sterilized with flame, steam or liquid.
Steam - and liquid sterilization
D
LB
The steam or liquid sterilization proceeds though the outlet
pipe (B) or during tank or pipe cleaning.
For valves with rinsing connection the sterilization occurred
via connection (SP).
Optional the valve can be equipped with a steam valve (DV).
The steam or liquid sterilization occurred via the connection
(D).

Operating instruction | KIESELMANN GmbH6 | Commissioning, service and maintenance
12 / 32 6125_APNV_EN
Air sterilization by flaming
The valve can be sterilized by flaming. This process may take
up to 15 seconds for the entire valve. To avoid high temperat-
ures at certain points the flame has to be moved constantly.
CAUTION
Risk of burning whilst flaming the valve!
There is a risk from burns of parts of the body.
ØThe valve gets very hot under flaming. When flaming the valve,
– wear suitable protective gloves and protective clothing
– local fire safety regulations must be followed.
CAUTION
Destroy of sealing materials due to high heat supply!
When flaming attention must be paid so that the valve is not exposed to short-time temperature ex-
ceeding 130°C, otherwise the sealing material will be destroyed.
– The valve must be flamed generally by trained personnel.

KIESELMANN GmbH | Operating instruction Technical data | 7
6125_APNV_EN 13 / 32
7 Technical data
Model Aseptic - sampling valve
Valve size - Product line: DN 25 - DN 150DN 1½“ - DN 4“
- Tank fitting
Variations of actu-
ation
• manual (spring close)
• manual (self locking)
• pneumatical
• pneumatically & manual
Housing variants • Inline - housing
• Housing with welding connection DN 25
• Housing with T-pipe piece DN 25 - DN 150, DN 1½“ - DN 4“
• Housing with tank welding connection
Outlet connections • G3/8
• G3/8 with blind nut
• DN10
• Clip-on
Rinsing - and steam
connections
• G3/8
• G3/8 with blind nut
• DN10
• Clip-on
• Connection for manual or pneumatically steam valve
Temperature range Ambient (air): +4° to +45°C
Operating (medium dependent): +0° to +95°C
Sterilization (SIP 30 min): EPDM +140°C
PTFE +130°C
NBR +100°C
Operating pressure max. 10 bar for liquids
Leak rate A (DIN EN 12266-1)
Control air Control air pressure: Quality of control air::
4,0 - 8,0 bar ISO 8573-1 : 2001 quality class 3
Material:
(in product contact)
stainless steel: AISI 316L
Surface: Ra ≤ 0,8µm metallic bright;
e-polished
Sealing material: PTFE-FTM

Operating instruction | KIESELMANN GmbH8 | Disassembly and assembly
14 / 32 6125_APNV_EN
8 Disassembly and assembly
8.1 Disassembly - sampling valve
NOTICE
All threaded joint have right-hand thread.
Unscrew and remove control air, steam resp. cleaning lines and electrical lines, complete feedback
unit or control head.
aseptic sampling valve - modules
IG
DV
FA MA
R
PA
IG Inline-housing DV Steam valve
FA Spring module MA Manual actuator
R End ring PA Pneumatic actuator

KIESELMANN GmbH | Operating instruction Disassembly and assembly | 8
6125_APNV_EN 15 / 32
Assembly - valve insert (VE)
NOTICE
Spring-loaded valve insert
For valves with spring-loaded valve insert, before unscrewing the clamp coupling the valve must be
actuated pneumatically or manually.
pneumatically - charge the actuator with compressed air at connection LA.
VE
• The piston retracts and the bellow lift up from valve seat.
• Unscrew the screw connection (F12) / (F13). Remove the clamp coupling (F11) and dismount
the valve insert from the housing (IG).
• Disconnect the compressed air at connection (LA).
LA
LA P1
IG F12
F13
F11
manually - open the actuator via Allen key
• Remove cap (K).
• Place a nut (M12) and a washer (A6.4) on the shaft (P1) and screw in a Allen screw (M6x10) in
the shaft till metallic stop by hand.
• Then turn further with al Allen key to the limit stop (approx. 3 turns).
• The piston retracts and the bellow lift up from valve seat.
• Unscrew the screw connection (F12) / (F13).
• Remove the clamp coupling (F11) and dismount the valve insert from the housing (IG). Un-
screw the screw (M6x10) from shaft (P1).
M12 A6.4 M6x10
~ 3x
K
LA
VE
IG F12
F13
F11

Operating instruction | KIESELMANN GmbH8 | Disassembly and assembly
16 / 32 6125_APNV_EN
Dismantle - pneumatic actuator PA
• Unscrew air connection (LA) and hand lever (M4). Unsrew ring (R) and housing (P8). Remove
plain bearing (P6).
PA
LA
M4
• Dismantle circlip ring (P2) and pull off piston (P4). Dismount O-rings (P3) and (P5). Unscrew
shaft (P1) from shaft (F4).
Dismantle - manual actuator MA
• Pull off cover (M12). Remove O-rings (M7) and (M11). Unscrew housing (M10). Remove disc
(M6), dog (M3) with pins (M2).
MA
• Unscrew with a hook wrench the worm (M5) from shaft (F4). The spring (F7) is completely re-
laxed. Remove disc (M1). Remove plain bearing (M8) and O-Ring (M9) from housing (M10).

KIESELMANN GmbH | Operating instruction Disassembly and assembly | 8
6125_APNV_EN 17 / 32
Dismantle - spring module FA
• Pull off the housing (F10), spring (F7) and guidance (F6) from shaft (F4). Clamp shaft (F4)
between soft jaws in a vice and unscrew the bellow (F1) with a pliers.
FA
• Remove the guidance (F2) and the plate spring (F3). Dismount de plain bearing (F9) and O-ring
(F8) from housing (F10).

Operating instruction | KIESELMANN GmbH8 | Disassembly and assembly
18 / 32 6125_APNV_EN
8.2 Assemble - sampling valve
• Before installation, thoroughly clean and slightly lubricate mounting areas and running sur-
faces.
• Lightly grease and mounting the O-rings.
CAUTION
ØThread connection (G1) from bellow (F1) and shaft (F4) is secured with a screw retention. After
unscrewing the bellows (F1) it must always be replaced.
– Remove all adhesive residue on the threaded connection (G1) and degrease thoroughly.
During assembly secure the new bellows again with a Screw retention detachable (e.g.
Loctite 243).
Insert spring module (FA)
At first open the valve manually. See fig. A, gap (SP) = 1mm.
Fig. A • Place a nut (M) and a washer (U) on the shaft (F4).
• Screw a nut (S) in the shaft till metallic stop by hand.
• Then turn further with a flat wrench to the limit stop (approx. 3 turns). Insert the spring module
(FA) into the housing (IG).
Fig. B • Mount clamp coupling (F11) and tighten the screw connections (F12) / (F13) evenly.
• Unscrew nut (M6) again. Remove disc (A6.4) and nut (12).
• Check the valve function.
Fig. A Fig. B

KIESELMANN GmbH | Operating instruction Disassembly and assembly | 8
6125_APNV_EN 19 / 32
8.3 Dismantle - steam valve DV
Dismantle - pneumatic steam valve pDV
• Actuate the actuator with a Allen key.
• Place a nut (M) [M12] and a washer (U) [A6.4] on the shaft and screw in a screw (S) [M6x10] in
the shaft till metallic stop by hand. Then turn further with al Allen key to the limit stop (approx.
3 turns). The piston retracts and the bellow lift up from valve seat.
• Use a flat wrench (SW 32) to unscrew the steam valve from the housing.
pDV
D1 S
U
M
3x
SW32
• Unscrew the screw (S) and remove nut (M) and disc (U).
CAUTION
Risk of injury by jumping out components
Spring-preloaded valve!
When unscrewing the cover (D15) components can jump out.
• Unscrew cover (D15). Remove all components from housing (D5). Dismount circlip ring (D16)
and pull piston (D10) from shaft (D8). Remove the wearing parts.
LA1 D5 D15 R
SW32
D4
D7
D6 D5
D8
D10 D16 D12 D14
D13
D15
D16
• Unscrew piston (D1) from shaft (D3). Remove the wearing parts.
D1
D3
D1 D2 D3 D16 D9 D10 D11
D8
G2

Operating instruction | KIESELMANN GmbH8 | Disassembly and assembly
20 / 32 6125_APNV_EN
Dismantle - manual steam valve mDV
• Open the valve with the hand wheel (mD5) completely. Dismount the circlip (mD7). Remove
disc (mD6) and hand wheel (mD5). Dismount the circlip (mD8). Pull the bolt (mD4) from the
housing. Unscrew the piston (mD1). Dismantle the O-ring (D2), (D7). Remove the wearing parts.
mDV
mD5
mD4
mD7
mD6
mD4 mD7 mD6
mD5
• Unscrew piston (mD1) from shaft (mD2). Remove the wearing parts.
mD1
mD3
mD4 mD7
mD6
mD5
mD8
mD3
mD2D7
mD1
8.4 Assemble - steam valve
• Before installation, thoroughly clean and slightly lubricate mounting areas and running sur-
faces.
• Lightly grease and mounting the O-rings.
CAUTION
ØThread connection (G2) is secured with a screw retention.
ØAfter unscrewing the piston (D1) e.g. (mD1) it must always be replaced.
– Remove all adhesive residue on the threaded connection (G1) and degrease thoroughly.
During assembly secure the new piston again with a Screw retention detachable (e.g. Loc-
tite 243).
Table of contents
Other KIESELMANN Control Unit manuals

KIESELMANN
KIESELMANN 6164 User manual
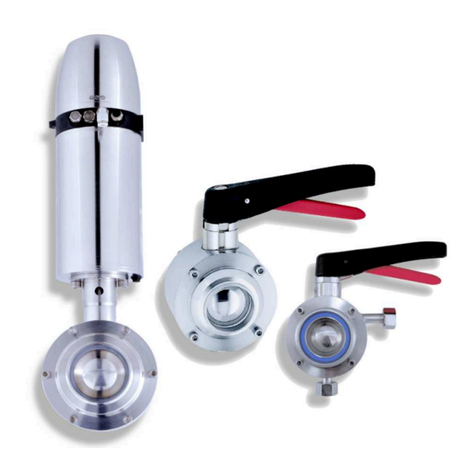
KIESELMANN
KIESELMANN 403 Series User manual
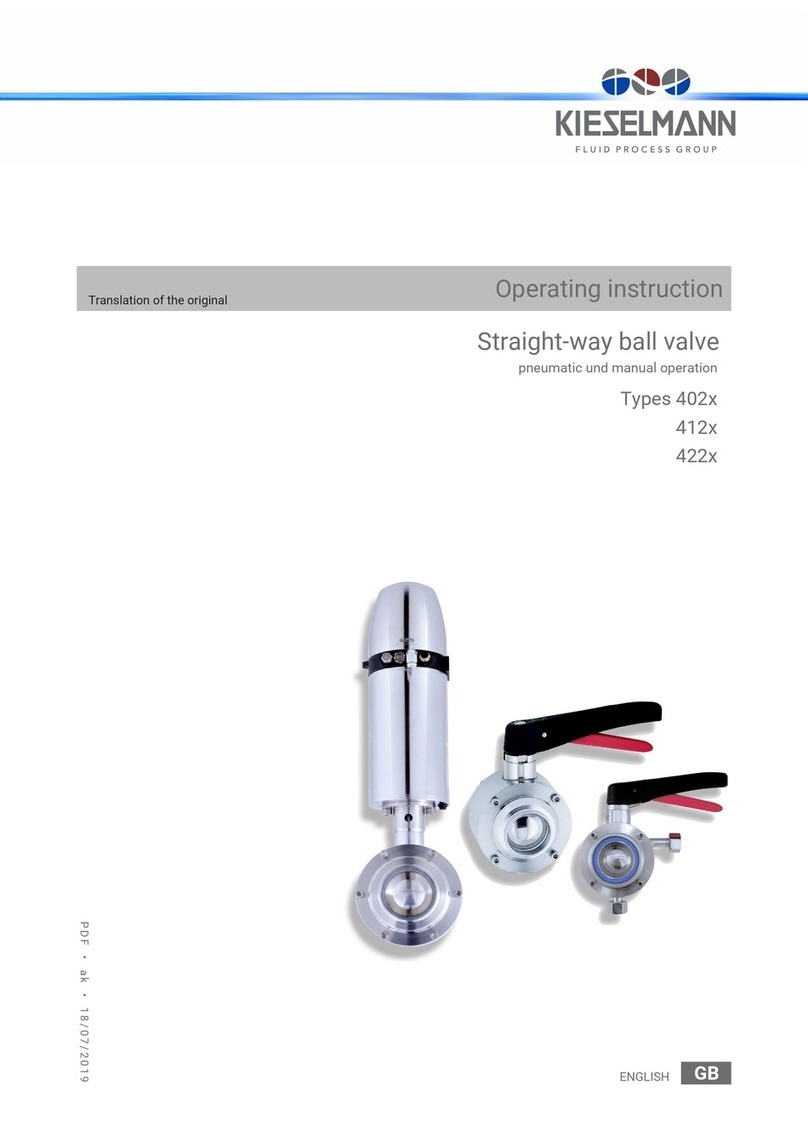
KIESELMANN
KIESELMANN 402 Series User manual
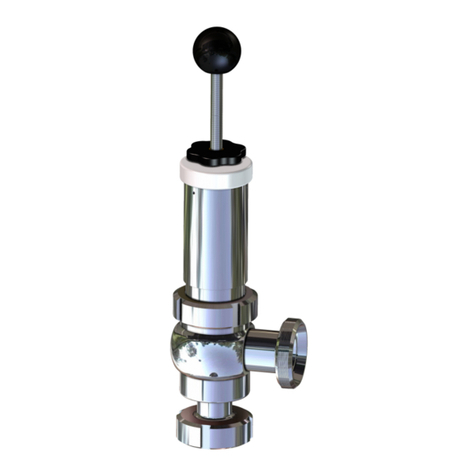
KIESELMANN
KIESELMANN 6268 User manual
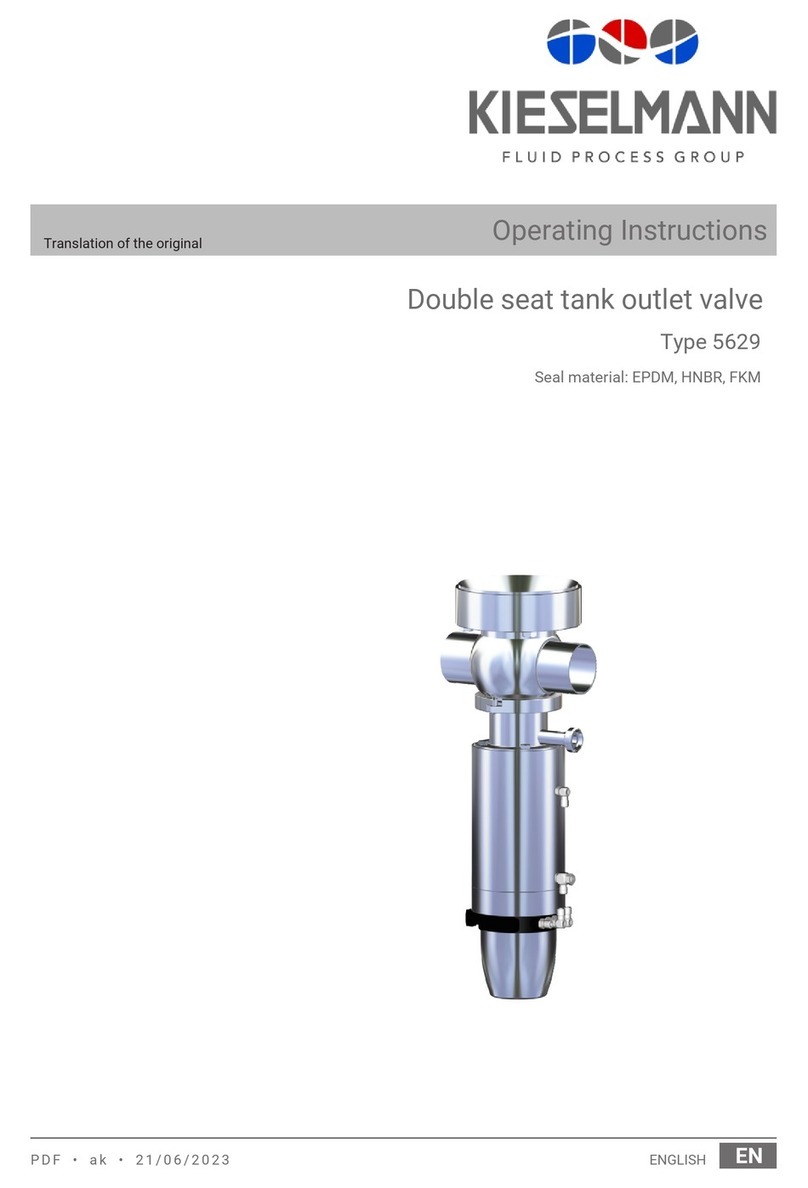
KIESELMANN
KIESELMANN 5629 Series User manual

KIESELMANN
KIESELMANN 582x User manual
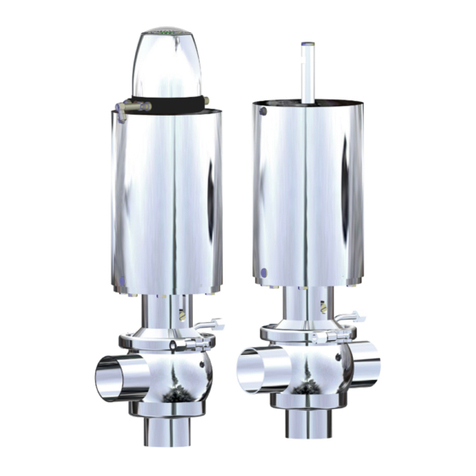
KIESELMANN
KIESELMANN GEMBRA 5836 User manual

KIESELMANN
KIESELMANN 5098 User manual
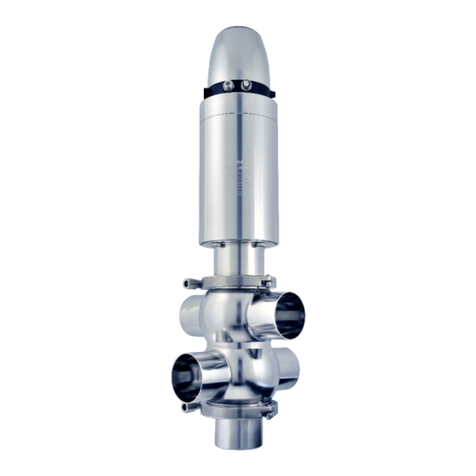
KIESELMANN
KIESELMANN 567 Series User manual
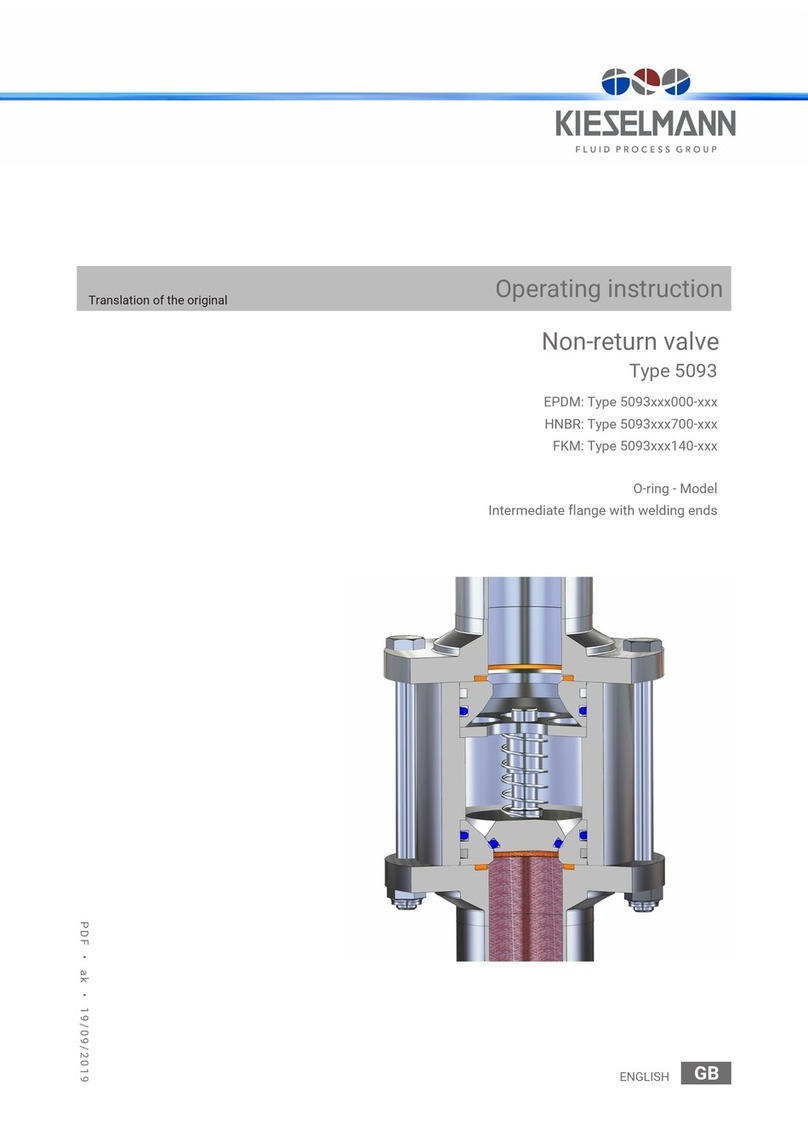
KIESELMANN
KIESELMANN 5093 Series User manual