KIOUR MACON HP User manual

Control device CHILLER / heat pump for 1 or 2 circuits with 2 or 4 compressors,
with analog outputs 0-10 Volt in compressors and fans.
Models: MACON_HP (panel), MACON_HPR (rail) (1st circuit) and MACON_HPB (rail), (2nd circuit) V.2.1
DESCRIPTION
MACON_HP controller is suitable for controlling a chiller or 2-circuit heat pump. Available in 28x70mm box or in 70mm rail box. The second circuit (MACON_HPB) is
available in a 70mm rail box and is connected to the main unit via three cables.
MACON_HP (1st circuit) has the following specifications:
MACON_HPB (2nd circuit) has the following specifications:
3 analog inputs for measuring temperature with range -50 ÷ +150°C
1 analog high pressure input (HP1) 4-20 mA for transmitter
2 analog inputs for measuring temperature with range -50 ÷ +150°C
1 analog high pressure input (HP1) 4-20 mA for transmitter
SENsor 1. Water input circuit 1. Operation thermostat HEATING - COOLING
SENsor 4. Water output 2nd circuit. Safety thermostat Νo2. Resistance Νo2
SENsor 2. Water output. Safety thermostat Νo1. Resistance Νo1
SENsor 5. Defrost C2 control (2nd circuit.)
SENsor 3. Defrost control C1 (Compressor 1st )
6 digital inputs:
3 digital outputs:
1st input Terminal block 15. ΟΝ-OFF device from a remote switch
7th input Terminal block 23 HΡ2. High pressure 2nd circuit
2nd input Terminal block 16 HEAT-COOL from a remote switch
8th input Terminal block 22 LP2. Low pressure 2nd circuit
3rd input Terminal block 17 HP1. High pressure 1st circuit
9th input Terminal block 21 C2. Thermal of 2nd circuit compressor
4th input Terminal block 18 LP1. Low pressure 1st circuit
5th input Terminal block 19 C1. Thermal of 1st circuit compressor
6th input Terminal block 20 FLOW SWITCH.
7 relay outputs 250VAC 5Amp: pump relay, compressor C1, valve V1,
resistance R1, fan FAN 1, alarm, compressor C1b Tadem or capacitive.
2 analog output 0-10 Volt Compressor C1 (Terminal blocks 25, 28), and
for the fan FAN1 (Terminal blocks 25, 27).
5 relay outputs 250VAC 5Amp: compressor relay C2, valve V2, resistance R2, fan
FAN 2, compressor C2b Tadem or capacitive.
2 analog output 0-10 Volt Compressor C2 (Terminal blocks 7, 8) and for the
fan FAN2 (Terminal blocks 6, 8).
CONNECT TO NETWORK
The device can connect to a PC via network RS485 or to a Remote Control via four cables.
Connect to a PC: CAMIN software can monitor all temperatures, compressors relays, alarms, parameters, while sending SMS and emails in case of an alarm.
More than 250 devices can connect to this network.
Connect to a Remote Control device: it displays on screen whatever is displayed on the main device and it has full access from the keyboard to the main device.
It can be installed up to 500 meters away from the main device.
PARAMETERS
Parameters are separated in two groups: 120 main parameters and 16 secondary parameters (A1-A16). Two of the main and 16 of the secondary parameters are easy
accessible. For the rest we have to enter in the parameter Cod = 22 to have access to all the parameters.Check relevant table on page 2.
TECHNICAL SPECIFICATIONS
Power supply: 24 VAC/DC 50/60 Hz 10W
Connection with terminal blocks 28-16 AWG 1.5 mm2
7 relays 250VAC 5A/3A Resistive Load in MACON_HP
5 relays 250VAC 5A Resistive Load in MACON_HPΒ
Operation temperature: -10 ÷+50 °C
Storage temperature: -20 ÷+80 °C
MACON_HP is mounted on a panel / Dimensions 28x70x75mm
MACON_HPΒis mounted on a Ωrail / Dimensions 70x90x65mm
It is suggested using a safety switch 1Α(not included)
Maximum consumption for each device 10 Watt
ON/OFF DEVICE
Press for 4 seconds to toggle the device between ON/OFF state if the parameter is set to Grc=0.
If ON-OFF input No 15 is activated or if the parameters are under programming, this function is canceled.
HEATING –COOLING OPERATION
Press for 4 seconds to toggle the operation between heating and cooling or cooling and heating mode if parameter is set to GrH=0.
If the input No 16 Heating-Cooling is activated or the parameters are under programming, this operation is cancelled.
dFrost
Pressing the SET button for 5 sec starts dFrost on both circuits. The display shows the message dF1 and dF2 every 2 sec, for a fraction of a second, which means that
circuits 1 and 2 do dFrost.
RESET ALARMS
Pressing to reset the alarms: this feature is active even during programming the parameters.
PROGRAMMING PARAMETERS
Press to enter or exit the parameters menu.
The first parameter “SCo” is displayed and with the , we scroll into the parameters menu.
Press SET to display the parameters value and adjust it with the , .
Press to confirm the new value and display the parameters name.
Press SET to cancel the new value and revert to the parameters name.
NOTE: for safety reasons all parameters as presented to the parameters table are not displayed. We must enter parameter Cod=22 to access full parameters menu.

DISPLAY AND RESET OPERATION HOUR OF COMPRESSORS
Press to display the first parameter SCo. By pressing up arrow button parameters from A16 to A1 are displayed. From A10-A14 are the operating hours of
compressors and pump. When the parameter name is displayed, for eg. h P and press SET the pump operating hours are displayed and by pressing simultaneously
+ resets the hours. Then, press to confirm the nihilism. When the operating hours indicator flashes, it means that the hours are 100.
DISPLAY TEMPERATURE and 4-20 mA
Parameters from A1 to A9: by pressing SET displays the temperature of the corresponding sensor or 4-20 mA as described in the parameter table.
LED OPERATION
ON The system is activated.
C1 ON when the compressor C1 operates. When it starts blinking then the compressor is set to ON but a timer is active and waits to elapsed.
C1bON when the compressor C1boperates. When it starts blinking then the compressor is set to ON but a timer is active and waits to elapsed.
C2 ON when the compressor C2 operates. When it starts blinking then the compressor is set to ON but a timer is active and waits to elapsed.
C2bON when the compressor C2b operates. When it starts blinking then the compressor is set to ON but a timer is active and waits to elapsed.
CCool –indication that system operates in cooling mode.
HHeat –indication that system operated in heating mode.
Blinks if an alarm is active.
RESET TO FACTORY DEFAULT SETTINGS
Enter the parameter Cod = 31 and press it twice to enter the factory values of the parameters (see in the following table the column default values).
TABLE 1
No
PARAMETERS
DESCRIPTION
min
max
DEFAULT
UoM.
Α1
t1
Temperature sensor Νo 1 (Input)
-
-
-
°C
Α2
t2
Temperature sensor Νo 2 (Water output 1)
-
-
-
°C
Α3
t3
Temperature sensor Νο 3 (deFrost C1)
-
-
-
°C
Α4
HP1
High pressure, circuit 1. HP1
-
-
-
pressure
Α5
LP1
out of order
-
-
-
pressure
Α6
t4
Temperature sensor Νο 4 (Water output 2)
-
-
-
°C
Α7
t5
Temperature sensor Νο 5 (deFrost C2 )
-
-
-
°C
Α8
HP2
High pressure, circuit 2. HP2
-
-
-
pressure
A9
LP2
out of order
-
-
-
pressure
A10
h P
Pump operation hours
Operation hours: When the symbol x100is ON, the
operation hours are x100.
To reset the timer, press simultaneously +and
then .
-
-
-
hours
A11
h 1
Compressor C1 operation hours
-
-
-
hours
A12
h1b
Compressor C1b operation hours
-
-
-
hours
A13
h2
Compressor C2 operation hours
-
-
-
hours
A14
h2b
Compressor C2b operation hours
-
-
-
hours
A15
Hs1
out of order
-
-
-
-
A16
Hs2
out of order
-
-
-
-
1
SCo
SET POINT of compressor in Cooling mode
LCL
LCH
10
°C
2
SHt
SET POINT of compressor in Heating mode
LHL
LHH
20
°C
3
Cod
Access code: with Cod=22 we access all the following parameters
0
255
0
-
4
diS
Adjust which sensor is displayed on screen, where 1 = sensor 1, etc.
1
5
1
-
5
rCo
Differential of SET POINT in Cooling mode
0.1
25
1
°C
6
rHt
Differential of SET POINT in Heating mode
0.1
25
1
°C
7
rS2
Differential of the second SET POINT
The differential is divided into 4 parts. E.g. for rS2 = 4 and SCo = 10. In the 1st circuit the 1st ON at
10°C the second ON at 11°C (TADEM). The 3rd of the 2nd circuit, ON at 12°C and the 4th ON at
13°C (TADEM). In circuits with a compressor / circuit, the 1st of the 1st ON circuit at 10°C and the
2nd of the 2nd ON circuit at 12°C.
0.1
25,0
2,0
°C
8
LCL
minimum temperature limit of SCo in Cooling mode
-50
150
-10,0
°C
9
LCH
maximum temperature limit of SCo in Cooling mode
-50
150
40,0
°C
10
LHL
minimum temperature limit of SHt in Heating mode
-50
150
10,0
°C
11
LHH
maximum temperature limit of SHt in Heating mode
-50
150
60,0
°C
12
FoP
Fan operation
0 = Fans are always OFF
1 = Fans are ΟΝ when the device is ΟΝ.
2 = Fan is ON when the corresponding compressor is ON
3 = The fans operate on the basis of SET POINT. FSC in cooling and FSH in heating.
The fan is controlled by the defrost temperature/pressure. The fan is ON when the temperature /
pressure of the defrost sensor commands the fan to ON (in normal operation and not in defrost
process). When OFF the OFF compressor and the fan
0
3
1
units
13
FSC
SET POINT of fan in Cooling mode. Operates when parameter FoP=3.
The differential is constant equal to 1,0 °C.
-50
150
15,7
°C
14
FSH
SET POINT of fan in Heating mode. Operates when parameter FoP=3.
The differential is constant equal to 1,0 °C.
-50
150
15,7
°C
15
doP
Defrost operation, where 0 = defrost operation is deactivated and 1 = defrost operation is activated
0
1
1
units
16
dto
0 =defrost ends based only on parameter timer dt3
1 =defrost ends when the temperature reaches temperature end deFrost. In the meantime, if timer
dt3 elapses, defrost ends and an indication dF appears on screen for a few seconds.
0
1
1
units
17
dbE
Temperature starting defrost
When the temperature is below the dbE limit continuously for a time longer than the dt1 time and with
the compressor ON, then a defrost process starts.
With the parameter t3E = 1 it works as a SET POINT for safety thermostat of temperature
SEn3, SE55
-50
150
3.6
°C

No
PARAMETERS
DESCRIPTION
min
max
DEFAULT
UoM
18
dEn
Temperature ending defrost
With the parameter dto = 1 the defrost ends when it reaches this temperature in less than the
maximum duration of the defrost. With the parameter t3E = 1 it functions as a differential
(differential = dEn - dbE) safety thermostat of the temperature SEn3, SE55
-50
150
15.6
°C
19
dFA
Over this temperature, the fan is ON during defrost. Differential is 1 °C.
-50
150
16.4
°C
20
dt1
Time frame in which all defrost requirements must occur in order to start defrost
1
200
1
min
21
dt2
Minimum time defrost duration, where 1 unit = 10 sec
1
200
1
10sec
22
dt3
Maximum time defrost duration
1
200
1
min
23
dt4
Minimum time between two successive defrosts of the same circuit
1
200
1
min
24
dt5
Minimum time between two successive defrost of the two circuits
0
200
0
min
25
dt6
ON or OFF time of the valve at the start and end of dFrost.
If this function is enabled by the dFS parameter.
0
20
1
min
26
dFS
dFrost value, where:
0 = At the start and at the end of deFrost the compressors stop in order to rotate the valves with
time dt6
1 = The valve rotates without stopping the compressor.
0
1
0
units
27
d07
Start of dFrost with 2 circuits.
0 = Regardless
1 = When both reach dFrost conditions
2 = When 1 of 2 reaches dFrost conditions
0
2
2
units
28
d08
0 =. DFrost ends independently.
1 = If one is finished, then the compressor turn OFF and waits for the other to finish.
In any case, both of them, end from the time pass.
2 =. If one ends, the other ends.
0
2
0
units
29
drE
State of resistance during dFrost.
0 = OFF , 1 = ON
0
1
0
units
30
dF1
FAN status in dFrost.
0 = OFF , 1 = works as in cooling with SP = FSC
0
1
0
units
31
dF2
FAN. Evaporator drying after dFrost.
0 = OFF , 1-250 sec = FAN is ON with maximum drying speed.
0
255
0
sec
32
ASP
SET POINT ALARM Antifreeze, Safety tthermostat
-50
60
4
°C
33
Adi
Differential , Safety Thermostat
0,1
20,0
1.5
°C
34
t3E
0 = this function is disabled.
1 =. (for water coolers) activates the temperature SEn3 and SEn5 as a safety thermostat.
DFrost is not needed and we turn it off. (doP = 0)
0
1
0
units
35
rSH
Resistance SET POINT Heating. Below Set Point, resistance is ON. (Works with T2 , T4).
-50
60
3.6
°C
36
Adr
Differential resistance thermostat.
0,1
20,0
1,0
°C
37
rOF
Value =0 => resistances OFF with whole system OFF. - frost conditions - .
0
1
1
units
38
rH1
activation / deactivation of the heating resistance. ON based on Set Point rH1.
Below Set Point, resistance is ON.
0
1
1
units
39
rC1
activation / deactivation of the cooling resistance. ON based on Set Point rSC.
Below Set Point, resistance is ON (5°C).
0
1
1
units
40
rSC
Resistance Set Point Cooling. Below Set Point, resistance is ON (5°C). (Works with T2 , T4).
-50
+150
15,0
°C
41
SE1
out of order
0
1
1
units
42
SE2
Sensor activation Νο 2, where 0 = sensor deactivated, 1 = sensor activated
0
1
1
units
43
SE3
Sensor activation Νο 3, where 0 = sensor deactivated, 1 = sensor activated
0
1
1
units
44
SE4
Sensor activation Νο 4, where 0 = sensor deactivated, 1 = sensor activated
0
1
1
units
45
SE5
Sensor activation Νο 5, where 0 = sensor deactivated, 1 = sensor activated
0
1
1
units
46
SH1
Value = 0 => disables the input. Value = 1 => Activates the 4-20 mA input of the high pressure of the
1st circuit. (Transmitter HP1) (when there is transmitter failure the analog voltage of the FAN is at the
maximum value). When transmitter is activated, the Set Point of the FSC and FSI parameters and the
0-10 Volt output work based on the transmitter signal. DeFrost operation is run by temperature only.
0
1
0
units
47
SH2
Value = 0 => disables the input. Value = 1 => Activates the 4-20 mA input of the high pressure of the
2nd circuit. (Transmitter HP2) (when there is transmitter failure the analog voltage of the FAN is at the
maximum value). When transmitter is activated, the Set Point of the FSC and FSHparameters and
the 0-10 Volt output work based on the transmitter signal.
DeFrost operation is run by temperature only.
0
1
0
units
48
SL1
out of order
0
1
0
units
49
SL2
out of order
0
1
0
units
50
rH1
Adjustment of the mA scale. 1st circuit high pressure inlet (HP1). Display the correct transmitter
pressure range, for example instead of 0 –100 units show 0 - 30,0 Bar.
10
99,9
100
%
51
rH2
Adjustment of the mA scale. 2nd circuit high pressure inlet (HP2). Display the correct transmitter
pressure range, for example instead of 0 –100 units show 0 - 30,0 Bar.
10
99,9
100
%
52
rL1
Adjustment of the mA scale. 1st circuit low pressure inlet (LP1). Display the correct transmitter
pressure range, for example instead of 0 –100 units show 0 - 30,0 Bar.
10
99,9
100
%
53
rL2
Adjustment of the mA scale. 2nd circuit low pressure inlet (LP2). Display the correct transmitter
pressure range, for example instead of 0 –100units show 0 - 30,0 Bar.
10
99,9
100
%
54
AJ1
Sensor No 1 offset
-9,0
15,0
0
°C
55
AJ2
Sensor No 2 offset
-9,0
15,0
0
°C
AJ3
Sensor No 3 offset
-9,0
15,0
0
°C
56
AJ4
Sensor No 4 offset
-9,0
15,0
0
°C
57
AJ5
Sensor No 5 offset
-9,0
15,0
0
°C
58
AJ6
out of order
-
-
-
-
59
AJ7
out of order
-
-
-
-
60
AJ8
out of order
-
-
-
-
61
AJ9
out of order
-
-
-
-

No
PARAMETERS
DESCRIPTION
min
max
DEFAULT
UoM
62
tPC
Pump-Compressor Time. Compressor start time after pump.
0
200
3
sec
63
tCP
Compressor-Pump Time. OFF time of the pump after OFF of the compressor.
0
200
0
min
64
tPO
Intermittent operation of the pump when the compressor is OFF. The tPO parameter works in
conjunction with the GFr parameter. GFr = 0 deactivates the function of the tPO parameter.
If GFr = 1 and tPO = 1-100 min, the pump restarts after the time specified by the parameter (OFF
time) and remains ON at the time specified by the parameter tPd, (time ON).
0
100
0
min
65
tPd
It works in conjunction with the tPO parameter and sets the operating time of the pump
1
100
1
min
66
tF1
Bypass time of FLOW SWITCH at pump start
0
200
5
sec
67
tF2
Bypass time of FLOW SWITCH during operation
0
200
5
sec
68
too
Time from ON to ON of the same compressor, where 1 unit = 10 sec
0
200
1
10sec
69
tFo
Time from OFF to ON of the same compressor, where 1 unit = 10 sec
0
200
1
10sec
70
tdC
Time from ON to ON between the two compressors
0
200
5
sec
72
tFC
Time from OFF to OFF between the two compressors
0
200
2
sec
73
ton
Minimum compressor operating time
0
200
2
sec
74
tLP
Bypass time of low compressor pressure (LP1, LP2) at start-up
0
200
3
sec
75
tLo
Bypass time of low compressor pressure (LP1, LP2) during operation
0
200
3
sec
76
tAF
Safety thermostat bypass time at startup
0
200
30
sec
77
ttA
In TANDEM mode. Switch compressors if only one works for time > ttA
2
100
30
min
78
Grc
ON-OFF Remote Control of the system.
Value = 1 Input enabled. Value = 0 the keyboard of the device is activated.
0
1
1
units
79
GrH
Remote Control of HEAT-COOL selection of the system.
Value = 1 Input enabled. Value = 0 the device keyboard is activated.
0
1
1
units
80
itY
Instrument Type: 1 = TADEM, 2 = CAPACITIVE, 3 = one compressor / circuit.
1
3
1
units
81
C12
Common circuit (condenser).
Value = 1=> 1st condenser, Value = 2 => 2nd condenser. With a common condenser, if FAN1 is ON
then the FAN2 is ON. If FAN2 is ON then the FAN1 is ON. The parameter only affects the fans.
0
1
2
units
82
GAL
Alarm function, automatic or manual,
Value: 0 = alarms manual Reset: HP1, LP1, PH1, Safety Thermostat 1, FLOW
SWITCH, HP2, LP2, PH2, Safety Thermostat 2
1 = automatic Reset
0
1
1
units
83
GSu
Valve Inversion Parameter
Value: 0 = In Cooling the valve relays are OFF and in heating ON
1 = In Heating the valve relays are OFF and in Cooling ON
0
1
0
units
84
GFr
Value: 0= The pump is running continuously.
1= The pump starts and stops with the compressors, based on the tPC and tCP times.
0
1
0
units
85
Gnc
Number of circuits, Values: 1 = One circuit, 2 = Two circuits
1
2
2
units
86
GLE
out of order
0
255
0
-
87
GPo
Compressor boot time in Power Up
0
200
0
sec
88
GLC
Value: 0= gives priority to the compressor with the fewest hours
1= gives constant priority to the compressor 1
2= gives constant priority to the compressor 2
0
2
0
units
89
GFP
Pump operation with ALARM safety thermostat in OFF machine condition.
0 = the pump is deactivated when safety thermostat is activated
1 = the pump is activated when safety thermostat is activated
0
1
1
-
90
trE
Time response of the device on network
30
100
30
units
91
Add
0 = network is deactivated. 1= Remote Control operation is activated.
Address of the device on network from 1 –255
0
255
1
units
92
nCo
0 = SLAVE: PC operation
1 = MASTER: REMOTE CONTROL operation and parameter Add = 1
0
1
0
units
93
C1d
Lower analog output voltage. Compressor C1 of the 1st circuit. The analog signal 0-10 Volt
corresponds consistently to C1. Values from 0 to 4.0 Volt. The analog output will be between C1U -
C1d in a temperature range defined by parameter C1H or C1C.
For example, C1U - C1d = 7 and C1H = 3 and SHt = 45°C, the voltage will change 10-3 Volt from 42
÷ 45°C on heating (see figure 5B).
0
5
3,0
Volt
94
C1U
C1. Compressor C1 of the 1st circuit Higher voltage at the analog output.
6
10
10,0
Volt
95
C1H
C1. Compressor C1 of the 1st circuit.
In the heating: Temperature range to which the proportional voltage at the output corresponds.
1.0
25.0
3.0
°C
96
C1C
C1. Compressor C1 of the 1st circuit.
In the cooling: Temperature range to which the proportional voltage at the output corresponds.
1.0
25.0
3.0
°C
97
C1i
C1. Reverse analog signal at the output
0
1
0
units
98
C1A
C1. Compressor C1 of the 1st circuit Increasing the value reduces the oscillation of the signal 0-10
Volt.
1
40
5
units
99
F1d
FAN 1. Lower analog output voltage. 1st circuit. Values from 0 to 4.0 Volt. The analog output will be
between F1U - F1d in a temperature range defined by parameter F1H or F1C. For, example F1U -
F1d = 7 and F1H = 3 and SHt = 45 °C, the voltage will change 10-3 Volts from 42 ÷ 45 °C on heating
(see figure 6B). When the relays C1, C1b are OFF then the analog output is zero
In the DRIPING_TIME phase it produces the maximum voltage
0
5
3,0
Volt
100
F1U
FAN 1. Higher voltage at the analog output.
When the relay of FAN 1 is OFF then the analog output is 0 Volt
6
10
10,0
Volt
101
F1H
FAN 1. In the heating.
Temperature / pressure range to which the analog output voltage corresponds.
1.0
25.0
3.0
°C
102
F1C
FAN 1. In the cooling.
Temperature / pressure range to which the analog output voltage corresponds.
1.0
25.0
3.0
°C
103
F1i
FAN 1. Reverse analog signal at the output
0
1
0
units
104
F1A
FAN 1. Increasing the value reduces the oscillation of the 0-10 Volt signal
1
40
5
units

No
PARAMETERS
DESCRIPTION
min
max
DEFAULT
UoM
105
C2d
C2. Lower analog output voltage. Compressor C2 of the 2nd circuit. The analog signal 0-10 Volt
corresponds consistently to C2. Values from 0 to 4.0 Volts. The analog output will be between C2U -
C2d in a temperature range defined by the parameter C2H or C2C. For example, C2U - C2d = 7 and
C2H = 3 and SHt =45°C, the voltage will change 10-3Volt from 42 ÷ 45°Con heating (see figure 5B).
0
5
3,0
Volt
106
C2U
C2. Higher voltage at the analog output.
6
10
10,0
Volt
107
C2H
C2. In the heating. Temperature / pressure range to which the analog output voltage corresponds.
1.0
25.0
3.0
°C
108
C2C
C2. In the cooling. Temperature / pressure range to which the analog output voltage corresponds.
1.0
25.0
3.0
°C
109
C2i
C2. Reverse analog signal at the output
0
1
0
units
110
C2A
C2. Increasing the value reduces the oscillation of the 0-10 Volt signal.
1
40
5
units
111
F2d
FAN 2. Lower analog output voltage. 2nd circuit. Values from 0 to 4.0 Volt. The analog output will
range between F2U - F2d in a temperature range defined by parameter F2H or F2C. For example,
F2U - F1d = 7 and F2H = 3 and SHt = 45 °C, the voltage will change 10-3 Volt from 42 ÷ 45 °Con
heating (see figure 6B). When the relays C2, C2b are OFF then the analog output is zero.
In the DRIPING_TIME phase it produces the maximum voltage.
0
5
3,0
Volt
112
F2U
FAN 2. Higher voltage at the analog output.
When the relay of FAN 2 is OFF then the analog output is 0 Volt
6
10
10,0
Volt
113
F2H
FAN 2. In the heating.
Temperature / pressure range to which the analog output voltage corresponds.
1.0
25.0
3.0
°C
114
F2C
FAN 2. In the cooling.
Temperature / pressure range to which the analog output voltage corresponds.
1.0
25.0
3,0
°C
115
F2i
FAN2. Reverse analog signal at the output
0
1
0
units
116
F2A
FAN 2. Increasing the value reduces the oscillation of the 0-10 Volt signal
1
40
5
units
117
VtO
In case the machine is OFF. Time OFF of the valves after the minutes specified by the parameter
(See EOV parameter).
0
20
0
min
118
EOV
If EOV = 0 and the system is OFF, then the valves are OFF after the time specified by parameter VtO.
If EOV = 1 the valves remain in the state specified by the GSu parameter.
0
1
0
units
119
PrE
PREVENT. In case the pressure of circuit 1 becomes higher than the value of the parameter, the
ALARM PREVENT (Pr1) is activated and turns OFF the 2nd compressor or CAPACITIVE of the 1st
circuit. The same applies to the second circuit. (Pr2). Activated if PEn = 1 and with the parameters
SH1 = 1 and SH2 = 1 respectively for circuit 1 and 2. With itY = 3 (1 compressor / circuit) PREVENT
is deactivated. PrE Set Point works without differential.
5,0
99,9
40,0
units
120
HPA
In case the pressure of circuit 1 becomes higher than the value of the parameter, the high pressure
ALARM is activated by the transmitter (P1H), and turns OFF the compressors of the 1st circuit. The
same applies to the second circuit, called ALARM P2H. Activated if HEn = 1 and with the parameters
SH1 = 1 and SH2 = 1 respectively for circuit 1 and 2.
The SET POINT of HPA works without differential.
5,0
99,9
40,0
units
121
PEn
Value=0 Deactivate the parameter PrE. Value =1 activate the PrE parameter.
0
1
0
units
122
HEn
Value=0 Deactivate the parameter HPA. Value =1 activate the HPA parameter.
0
1
0
units
123
CAV
Reverse operation of CAPACITIVE, C1b and C2b relays. Value = 0 => ON the relay on the thermostat
ON. Value = 1 => OFF the relay on the thermostat ON.
0
1
0
units
124
LPA
ALARM Operation of Low Pressure when the compressor is OFF.
Value=0 => Blocks ALARM. Value = 1 => ALARM is free
0
1
1
units
ALARM TABLE Display flashes when the alarm messages are displayed
1
HP1
ALARM HIGH PRESSURE C1: Stops the operation of compressor C1. By adjusting parameter GAL = 0, alarm reset is manual.
2
LP1
ALARM LOW PRESSURE C1: Stops the operation of compressor C1. By adjusting parameter GAL = 0, alarm reset is manual.
3
C1
ALARM COMPRESSOR C1: Stops the operation of compressor C1. Alarm is only automatically deactivated when the cause of the alarm disappears.
4
FLS
ALARM FLOW SWITCH: ALARM from the FLOW SWITCH. By adjusting parameter GAL = 0, alarm reset is manual.
5
HP2
ALARM HIGH PRESSURE C2: Stops the operation of compressor C2. By adjusting parameter GAL = 0, alarm reset is manual.
6
LP2
ALARM LOW PRESSURE C2: Stops the operation of compressor C2. By adjusting parameter GAL = 0, alarm reset is manual.
7
C2
ALARM COMPRESSOR C2: Stops the operation of compressor C2. Alarm is only automatically deactivated when the cause of the alarm disappears.
8
Ar1
ALARM SENSOR 1: ALARM analog input Νο 1. Safety thermostat. (Water input). Sensor malfunction. Alarm is only automatically deactivated when the cause
of the alarm disappears.
9
Ar2
ALARM SENSOR 2: ALARM analog input Νο 2. Safety thermostat. (Water output). Circuit 1. Sensor malfunction. Alarm is only automatically deactivated
when the cause of the alarm disappears.
10
Ar3
ALARM SENSOR 3: ALARM analog input Νο 3. Defrost Sensor malfunction. Alarm is only automatically deactivated when the cause of the alarm disappears.
11
Ar4
ALARM SENSOR 4: ALARM analog input Νο 4. Safety thermostat. (Water output). Circuit 2. Sensor malfunction. Alarm is only automatically deactivated
when the cause of the alarm disappears.
12
Ar5
ALARM SENSOR 5: ALARM analog input Νο 5. Defrost. Sensor malfunction. Alarm is only automatically deactivated when the cause of the alarm disappears.
13
At1
ALARM FROST: ALARM from the Safety Thermostat Circuit 1. At compressor’s start-up, the thermostat is deactivated based on parameter timer tAF. By
adjusting GAL = 0, alarm reset is manual.
14
At2
ALARM FROST: ALARM from the Safety Thermostat Circuit 2. At compressor’s start-up, the thermostat is deactivated based on parameter timer tAF. By
adjusting GAL = 0, alarm reset is manual.
15
t31
ALARM Sensor No 3 - Sen3 (dFrost) –in Safety Thermostat mode. See parameter No 34 t3E
16
t32
ALARM Sensor No 5 –Sen5 (dFrost) –in Safety Thermostat mode. See parameter No 34 t3E
17
nH1
HP1 transmitter failure. HIGH PRESSURE circuit 1
18
nH2
HP2 transmitter failure. HIGH PRESSURE circuit 2
19
P1H
ALARM HP1 from the transmitter 4-20 mA of the 1st circuit. OFF the compressors. RESET manual optional.
20
P2H
ALARM HP2 from the transmitter 4-20 mA of the 1st circuit. OFF the compressors. RESET manual optional.
21
Pr1
ALARM PREVENT 4-20 mA high pressure sensor of the 1st circuit. When the circuit pressure becomes greater than the value of the PrE parameter the
ALARM PREVENT (Pr1) is activated and OFFs the second compressor or CAPACITIEVE of the 1st circuit
22
Pr2
ALARM PREVENT 4-20 mA high pressure sensor of the 2nd circuit. When the circuit pressure becomes greater than the value of the PrE parameter the
ALARM PREVENT (Pr2) is activated and OFFs the second compressor or CAPACITIEVE of the 2nd circuit
The alarms are automatically deactivated when the cause of the alarm disappears.

MESSAGE BOARD Display does not flash when displaying messages. Displays the message sequentially for 0.2 seconds and the temperature for 2 seconds.
1
dP1
Drainage procedure of the 1ST circuit after deFrost.
2
dP2
Drainage procedure of the 2nd circuit after deFrost.
3
dF1
dFrost is running on the 1st circuit.
4
dF2
dFrost is running on the 2nd circuit.
On the MACON_HPB, the flashing LED in position No. 2 indicates that the device is communicating with the main unit. The LED in position
of terminal No. 11 indicates that the device is under voltage.
The same applies to compressor C2, respectively with parameters C2d, C2U, C2H

The same applies to FAN 2, respectively with the parameters F2d, F2U, F2C

In case of using analog signals, the use of an isolation transformer in the power
supply is recommended.
Temperature sensor No 1. Water inlet, circuit 1.
Thermostat operation: HEATING-COOLING
Temperature sensor No 2. Water outlet.
Safety thermostat No. 1. Resistance No. 1.
Temperature sensor No 3. deFrost control.
Temperature sensor No 4. Water outlet, circuit 2.
Safety thermostat No 2. Resistance No 2.
Temperature sensor No 5. Defrost control C2

*!!* Versions: V2.1.060721. Parameters: 97C1i,103F1i, 109C2i,115F2i *!!*
Made in Greece
ATTENTION: according to safety standards, the device must be properly positioned and protected from any contact with electrical parts. The device must be fastened in such a way that it
cannot be removed without the use of tools. Disconnect the main safety switch of the installation before proceeding to any maintenance. Disconnect the power supply of the device before
proceeding to any maintenance. Do not place the device near heat sources, equipment containing strong magnets, in areas affected by direct sunlight or rain. Prevent electrostatic discharges
and sharp objects from been inserted to the device. Separate signal cables from power supply cables to prevent electromagnetic disorders. Signal cables must never be in the same pipe with
the power supply cables.
The device is under two year’s guarantee. The guarantee is valid only if the manual instructions have been applied. The control and service of the device must be done by an authorized
technician. The guarantee covers only the replacement or the service of the device. preserves the right to adjust its products without further notice.
392 Mesogeion Avenue Agia Paraskevi 153 41 Τ: 210 6533730 F: 210 6546331 [email protected] www.kiour.com
V2.1.080721
This manual suits for next models
2
Table of contents
Other KIOUR Controllers manuals
Popular Controllers manuals by other brands
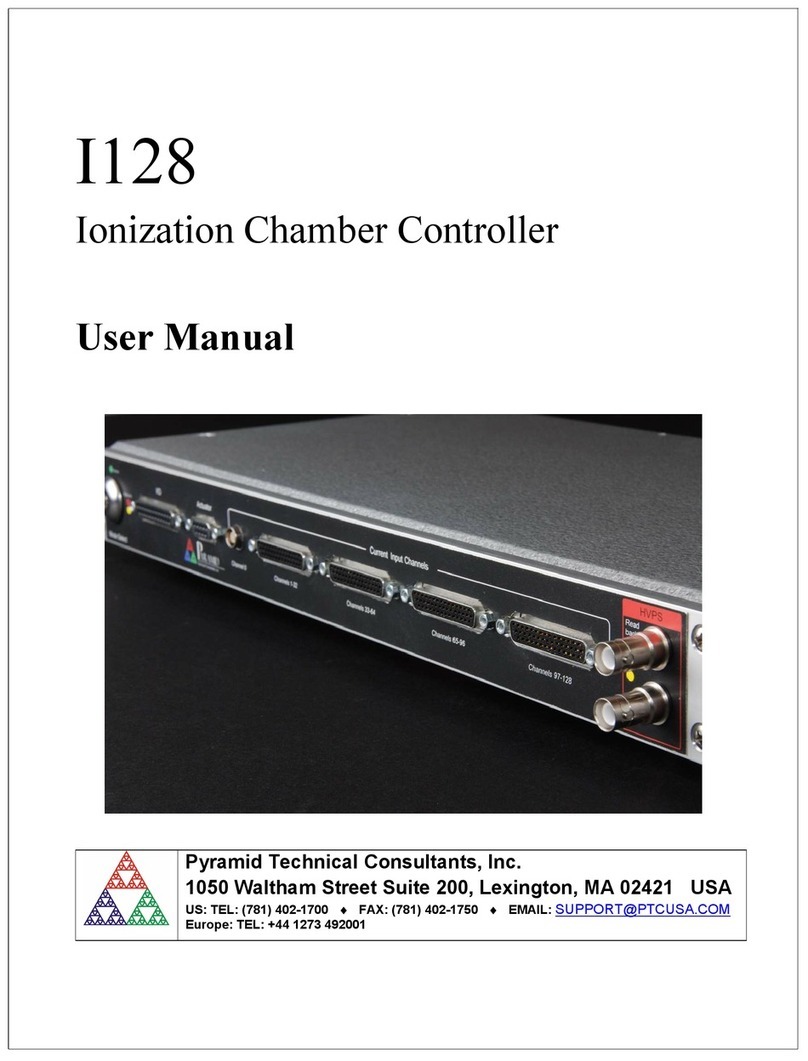
Pyramid Technical Consultants
Pyramid Technical Consultants I128 user manual
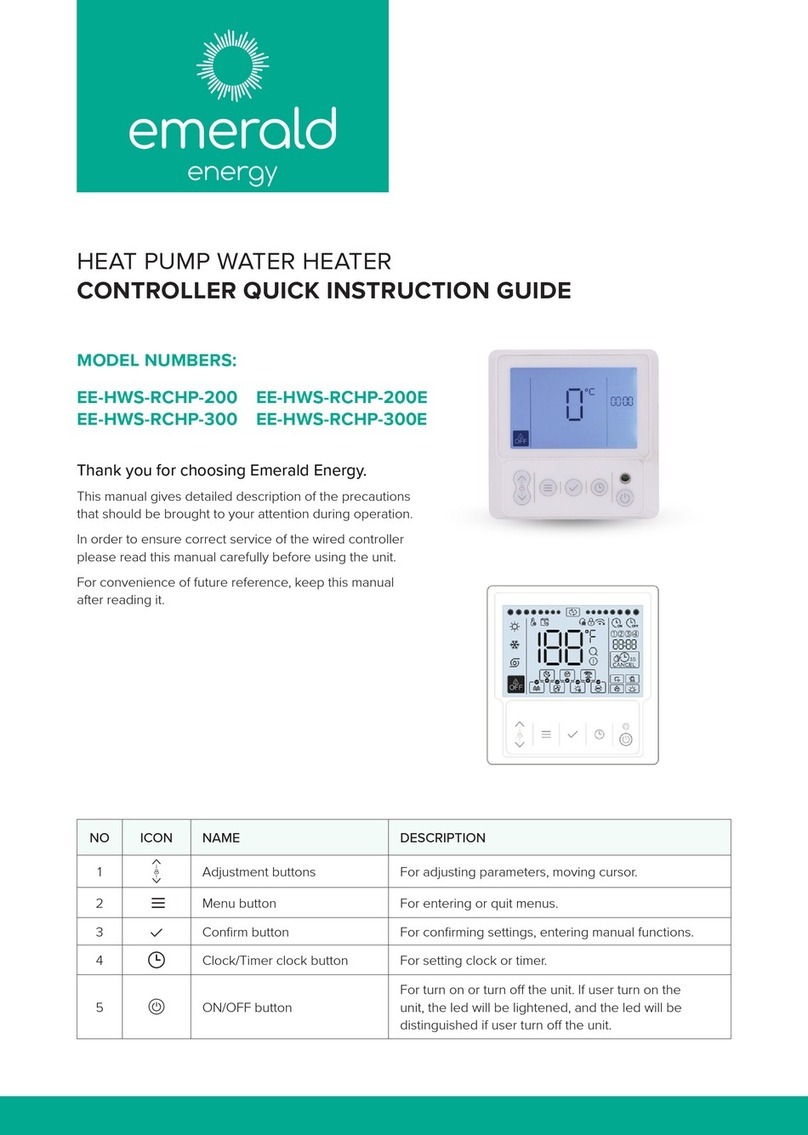
Emerald
Emerald EE-HWS-RCHP-200 Quick instruction guide
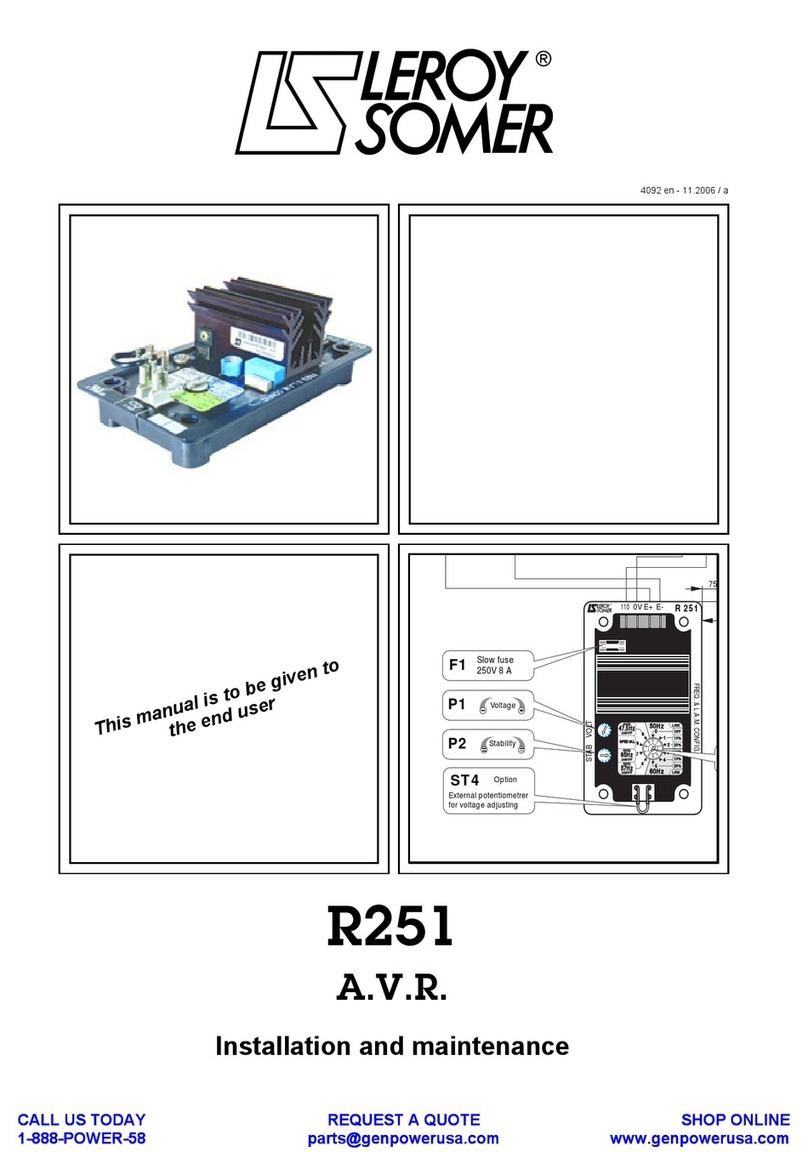
Leroy-Somer
Leroy-Somer R 251 Installation and Maintenance
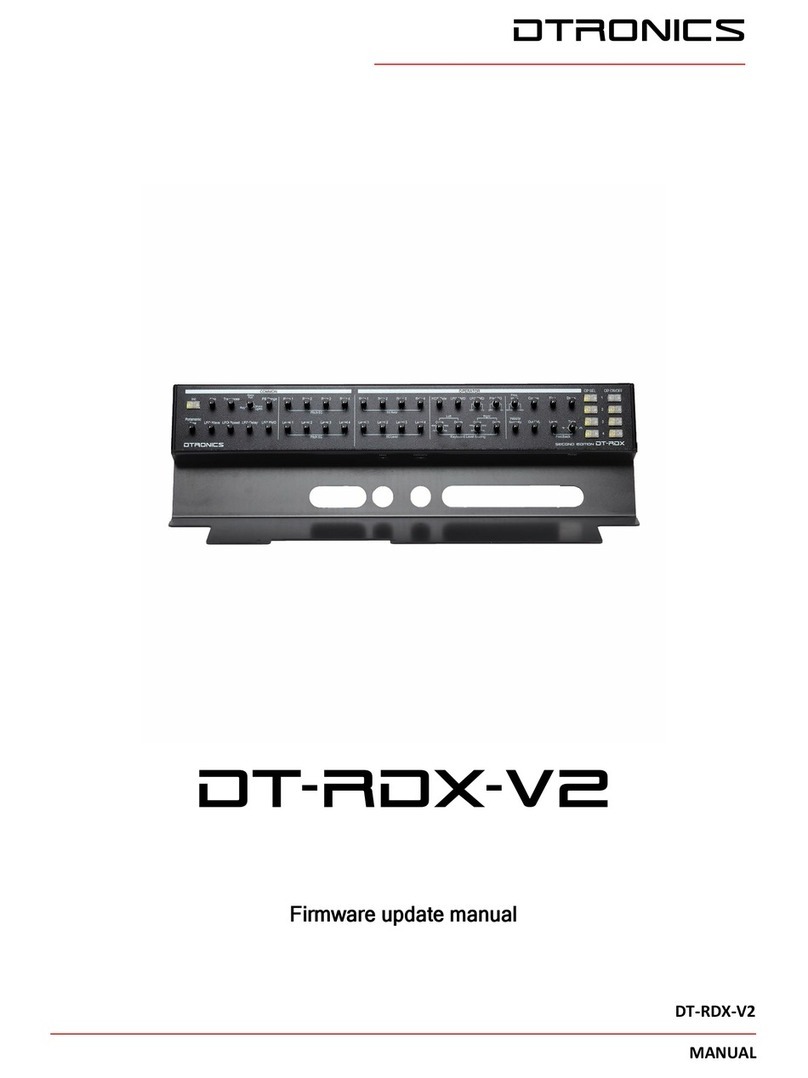
DTronics
DTronics DT-RDX-V2 manual

HORNER APG
HORNER APG HEXT240C115 Specifications and installation
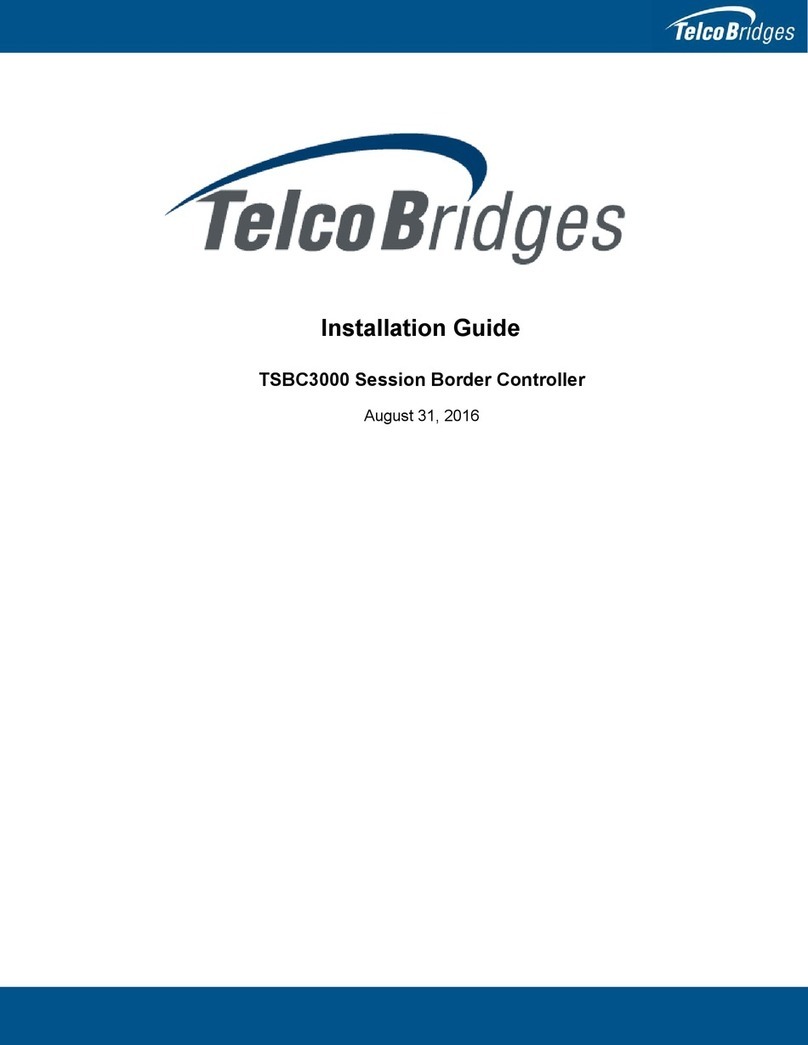
TelcoBridges
TelcoBridges TSBC3000 installation guide