Makita BFH040 Manual

Models No.
Description
PRODUCT
CONCEPTION AND MAIN APPLICATIONS
Specification
Standard equipment
Optional accessories
< Note > The standard equipment for the tool shown may differ from country to country.
P 1 / 17
TECHNICAL INFORMATION
Dimensions (mm [inch])
Height (H)
Length (L) 190 [7-1/2]
266 [10-1/2]With BH1220
With BH1233 289 [11-3/8]
Width (W) 71 [2-13/16]
BFH040, BFH040F, BFH090, BFH090F, BFH120F
12V Cordless Screwdrivers
The above cordless screwdriver series enable you to work
also in the hazardous location which is defined by
UL1604, Class I, Division 2.
The conformation to UL1604, Class I, Division 2 has been achieved by using
1. Brush-less DC motor for spark-free armature rotation.
2. Battery inter lock system
In addition to the above features, they have the following features.
* Soft start for suppressing starting shock
* Delayed restarter for avoiding unintentional over fastening
* Indication lamp, informing operator of the result of
fastening
* Battery BH1220 ...................................................... 2 pcs.
* Charger DC14SA .................................................... 1 pc.
* Torque adjust tool ................................................. 1 pc.
* Accessory case ........................................................ 1 pc.
* Steel carrying case .................................................... 1 pc.
* Battery BH1220
* Battery BH1233
* Charger DC14SA
* Charger DC24SA
* Adjust grip
* ADP 03 Automatic Refreshing Adapter
Model No.
No load speed : min-1 = rpm
Fastening torque
: N.m
(in.lbs)
Battery
Electric brake
Driving shank
LED Job Light
Torque adjustment
Soft starter
Reverse switch
Over load protector
Net weight
: Kg (lbs)
Type of cell
Voltage : V
Capacity : Ah
Ni-MH
12
Hex 6.35mm (1/4")
2.0 Ah with battery BH1220
3.3 Ah with battery BH1233
400
1.5 (3.3)
1.8 (4.0)
Yes
Yes
Yes
Yes
Yes (Adjust grip is required.)
BFH040FBFH040 BFH090 BFH090F BFH120F
0.8 - 4.5
(7 - 40) 3.4 - 9.0
(30 - 80) 5 - 12
(44 - 106)
0.8 - 4.5
(7 - 40) 3.4 - 9.0
(30 - 80) 5 - 12
(44 - 106)
w/ 2.0Ah battery
w/ 3.3Ah battery
Hard joint
Soft joint
YesNo No YesYes
They come to market wit the following model name and the specification.
BFH040 BFH040SAE
BFH040F BFH040FSAE
BFH090 BFH090SAE
BFH090F BFH090FSAE
BFH120F BFH120FSAE
* Battery 1220 x 2pcs.
* Charger DC14SA
* Torque adjsut grip
* Accessory case
* Steel carrying case
with
H
L
W

Repair P 2 / 17
< 1 > Lubrication
Apply MAKITA grease N. No.2 to the following portions designated by black triangle to protect
parts and product from unusual abrasion. See Fig. 1.
44
44
47
47
48
48
49
49
50
50 54
54
Position
No. Parts item
Shaft portion which accept 47: spur gear 18.
Shaft portion which accept 49: spur gear 19.
Teeth portion of spur gear 9
Teeth portion
Teeth portion
Teeth portion where 47: spur gear 18 and 49: spur gear 19 roll.
Teeth portion
Spur gear 18
Spur gear 19
Rotor
Internal gear 47
Spur gear 9
complete
Carrier
complete B
Portion
to be lubricated Amount : g
( oz )
Ball bearing
6805LLB Gear case Lock washer
Motor bracket
Approx. 2
(0.08)
in total
Fig. 2
Fig. 1
< 2 > Disassembling bit holder section
( 1 ) Remove ring spring 10. Then, flat washer 11, compression spring 13, sleeve and 2 pcs of steel 3 can be removed
from spindle. See Fig. 2.
1R291
Retaining Ring S and R Pliers
Spindle
Flat washer 11
Sleeve
Steel ball 3
Steel ball 3
Compression spring 13
Head of clutch case
Ring spring 10
< 3 > Assembling bit holder section
( 1 ) Mount 2 pcs. of steel ball 3.
( 2 ) Mount sleeve.
( 3 ) Mount compression spring 13.
( 4 ) Mount flat washer 11.
( 5 ) Secure the above parts with ring spring 10 to spindle.
See Fig. 2.

Repair P 3 / 17
Fig. 3 Fig. 4
Fig. 5
Fig. 6
Fig. 7
< 4 > Disassembling spindle (as a bit holder) and clutch case
( 1 ) After removing bit holder section, remove ring 38 by unscrewing pan head screw M4x4, and clutch case cover
by unscrewing pan head screw M4x8. And then, remove compression spring 2 and switch lever. See Fig. 3.
( 2 ) Remove clutch case by unscrewing 4 pcs. of pan head screw M4x22. See Fig. 4.
( 3 ) Remove retaining ring R-21 from clutch case. And then, knock the edge of clutch case with plastic hammer.
So, spindle (as a bit holder) can be removed from clutch case. See Fig. 5.
( 4 ) Remove ring spring 11 from spindle. And then remove ball bearing 6801LLB on the ring spring 11 side.
See Fig. 6.
( 5 ) After removing ring 12, remove the another ball bearing 6801lLB. See Fig. 7.
< Note > Compression spring 5 can easily fall off clutch section. Be careful, not to lose compression spring 5
in this step.
Pan head screw M4x8
(black)
Clutch case cover
Clutch case
Compression
spring 2
Clutch case
Clutch section
Switch lever
Pan head
screw M4x22
Compression
spring 5
No.1R311
Retaining Ring Pliers
with Long Bent Nails
Retaining ring R-21
Spindle
Ring 12 Ball bearing
6801LLB
Ring spring 11 1R269
Bearing Extractor
Ball bearing 6801lLB
Ball bearing 6801lLB
Ring 12
Spindle
1R004
Retaining ring S plier
Pan head
screw M4x4 (silver)
Ring 38

Repair P 4 / 17
Fig. 8 Fig. 9 Fig. 10
Fig. 11
Fig. 12
Fig. 13
Fig. 14
Ring spring 11
1R004
Retaining ring S plier
( 5 ) Mount the spindle section to clutch case as illustrated in Fig. 12.
( 6 ) Secure the spindle section in the clutch case with retaining ring R-21. See Fig. 13.
( 7 ) Mount clutch section to motor housing. Mount
compression spring 5 to the clutch section. Fasten
the clutch case to the motor housing with 4 pcs.of
pan head screw M4x22 See Fig. 13.
1R035
Bearing setting plate
1R036
Bearing setting plate
Ball bearing
6801LLB Ball bearing
6801LLB
Spindle
Ring 12
1R237
Round bar for arbor
Clutch case No.1R311
Retaining Ring Pliers
with Long Bent Nails
Retaining ring R-21
Clutch case
Clutch section
Pan head
screw M4x22
Compression
spring 5
< 6 > Assembling spindle (as a bit holder) and clutch case
( 1 ) Set ball bearing 6801LLB on 1R035 "Bearing setting plate". Mount spindle to ball bearing 6801LLB by pressing
with arbor press. See Fig. 8
( 2 ) Mount ring 12 to spindle. See Fig. 9.
( 3 ) Set another ball bearing 6801LLB on 1R035 "Bearing setting plate". Mount spindle to the ball bearing 6801LLB
by pressing with arbor press. See Fig. 10.
( 4 ) Secure 2 pcs. of ball bearing 6801LLB and ring 12 with ring spring 11. See Fig. 11.
< Note > Do not use the used ring spring 11. It has to be always replaced with the fresh one.

Repair P 5 / 17
Fig. 15 Fig. 16
Fig. 17
Fig. 18
Fig. 19 Fig. 20
( 8 ) Mount compression spring 2 and switch lever. And secure clutch case cover
with pan head screw M4x8 (black). See Fig. 15.
( 9 ) Secure ring 38 to clutch case with pan head screw M4x4 (silver). See Fig. 16.
Pan head
screw M4x8 (black)
Clutch case cover
Clutch case
Compression spring 2
Switch lever
Pan head
screw M4x4 (silver)
Ring 38
< 6 > Disassembling clutch section
( 1 ) Remove ring 38 and clutch case cover referring to "< 4 > Disassembling spindle (as a bit holder) and clutch case".
( 2 ) Remove clutch section from motor housing. See Fig. 17.
Clutch section
Compression
spring 5
( 4 ) Remove adjust ring complete, flat washer 18 and
compression spring 19 from spindle. See Fig.20.
( 3 ) Insert torque adjust tool into the hole of adjust ring complete.
Turn torque adjust tool anti-clockwise, until adjust ring complete
is free from the compression spring 19. See Fig. 18.
Then, lock nut M12 can be separated from adjust ring complete
by turning clockwise with your hand. See Fig. 19.
Lock nut M12
Lock nut M12
Adjust ring
complete
Compression
spring 19
Torque adjust tool
(Standard equipment)
Adjust ring
complete
Compression
spring 19
Flat washer 18
Spindle

Repair P 6 / 17
(5) Insert hex wrench into the hole of spindle and hold the hex wrench with vise. Insert torx wrench T25 into
the hole of torx counter sunk head screw M5x10. And turn torx wrench T25 anti-clockwise. See Fig. 21.
(6) After removing torx counter sunk head screw M5x10, the clutch section can be disassembled in the order of
flat washer 7, steel balls 3.0, cam A and steel balls 4. See Fig. 22.
Remove steel balls 5. Then, cam B can be removed from spindle. See Fig. 23.
Torx counter sunk
head screw M5x10.
Torx counter sunk
head screw M5x10.
Hex wrench Torx wrench T25
6mm
Steel balls 3.0
(13 pcs.)
Flat washer 7
Cam A
<Note>
Pay attention, not to lose steel
balls, when disassembling.
Use the hex wrench with the
following size.
Steel ball 4
(3 pcs.)
Cam D
Steel ball 5
(3 pcs.)
Cam B
Spindle
Fig. 24
< 7 > Assembling clutch section
(1) Before mounting, take the following steps. See Fig. 24.
1. Apply MAKITA grease N. No.2 to 3 pcs. of steel ball 5 and 3 pcs. of steel ball 4.
2. For effective adhesion, clean the screw hole of spindle and torx counter head sunk screw M5x10 with petrol.
Spindle Torx counter sunk
head screw M5x10
Screw hole for
torx counter sunk head
screw M5x10
Fig. 21
Fig. 22 Fig. 23

Repair P 7 / 17
Fig. 25 Fig. 26 Fig. 27 Fig. 28
Fig. 29 Fig. 30 Fig. 31
Fig. 32
(2) Mount steel balls and cam B and cam A in the order of Fig. 25, Fig. 26, Fig. 27 and Fig.28.
(3) Before mounting, apply MAKITA grease N. No.2 to 13 pcs. of steel balls 3.0.
Assemble steel balls 3.0, flat washer 7 and torx counter sunk head screw M5x10 as illustrated in Fig. 29, Fig.30
and Fig. 31.
(4) Before mounting, apply MAKITA grease N. No.2 to threaded portion of spindle.
Assemble compression spring 19, flat washer 18 and adjust ring complete and lock nut 12
in the order of Fig. 31 and Fig. 32.
Steel balls 5
(3 pcs.)
Mount steel balls 5
to spindle. Mount cam D to spindle
with aligning its 3 grooves
with steel balls 5. Mount steel balls 4
to cam B. Mount cam A.
Cam B Steel balls 4
(3 pcs.)
Steel balls 3.0
(13 pcs.)
Mount steel balls 3.0
to cam A. Mount flat washer 7
to cam A.
Pay attention, not to spot
the screw hole of spindle
with the grease, when
assembling steel balls.
Flat washer 7
Torx counter sunk
head screw M5x10
Apply here the
adhesive by 0.1CC,
before screwing.
After applying 0.1cc (3 drops) of
adhesive, "Lock tight 603" in the
screw hole, fasten flat washer 7
with torx counter sunk head
screw M5x10.
The fastening torque for the
screw is 8 - 10 N.m.
Compression
spring 19
Adjust ring
complete
Fig. 31 Lock nut 12
While pressing lock nut 12 strongly, turn torque adjust tool
clockwise. Then, lock nut M12 turns anti-clockwise
and fastened to spindle.
Cam A
Flat
washer 18

Repair P 8 / 17
Fig. 33
< 8 > Disassembling motor section and gear section
Fig. 34 Fig. 35
Fig. 36
( 1 ) Remove ring 38, and clutch cover from housing referring to "< 4 > Disassembling spindle (as a bit holder)
and clutch case".
( 2 ) After removing clutch section, separate housing L from housing R by unscrewing 8 pcs.
of pan head screw M3x20. See Fig. 33.
( 3 ) Remove gear section with motor section from housing R .
( 4 ) Turn motor bracket anti-clockwise. So gear section can be separated from motor section. See Fig. 35.
( 5 ) Pull off rotor from motor control unit and remove motor bracket. See Fig. 36.
Clutch
section
Compression spring 5
Pan head
screws M3x20
Housing L Housing R
Plate
Lens
Gear section
Motor section
See Fig. 34.
Motor bracket
Motor bracket
<Note>
Be careful, not to be pinched your finger
between motor control unit and rotor.
Because, rotor is pulled toward motor
control unit by the strong magnetic force.
Motor control unit
Rotor

Repair P 9 / 17
( 6 ) Turn lock washer, and pull off it. See Fig. 37.
( 7 ) Then, gear section can be disassembled as illustrated in Fig. 38 and Fig. 39.
Fig. 37 Fig. 38 Fig. 39
Spur gear 9
complete
Spur gear 19 x 3 pcs.
Spur gear 18 x 3 pcs.
Carrier
complete B
Internal gear 47
Gear case
Ball bearing
6805LLB
Lock washer
< 9 > Assembling motor section and gear section
( 1 ) Referring to "< 1 > Lubrication", apply MAKITA grease N No.2 to the gears and shaft portions of spur gear 9
and carrier complete B.
( 2 ) Mount ball bearing 6805LLB and carrier complete B to gear case. See Fig. 40
( 3 ) Mount internal gear 47 to the gear case. See Fig. 41.
( 4 ) Engaging internal gear 47, mount 3 pcs. of spur gear 18 to the shaft portion of carrier complete B. See Fig. 42.
( 5 ) Engaging spur gears 18, mount spur gear 9 complete. See Fig. 43.
( 6 ) Engaging internal gear 47, mount 3 pcs. of spur gears 19 to the shaft portion of spur gear 9 complete.
See Fig. 44.
( 7 ) Mount lock washer to the gear case by turning. See Fig. 45.
( 8 ) Mount motor bracket to the gear case by turning clockwise. The assembling of gear section has been completed
in this step. See Fig. 46.
Fig. 40 Fig. 41 Fig. 42 Fig. 43
Fig. 44 Fig. 45 Fig. 46
Ball bearing
6805LLB
Carrier
complete B
Gear case
Gear case
Internal
gear 47
Spur gear 18 Spur gear 9
complete
Spur gear 19 Lock washer
Motor bracket

Repair P 10 / 17
( 9) Insert armature into motor control unit. See Fig. 47. The assembling of motor section has been completed
in this step.
(10) Join the motor section to the gear section. See Fig. 48.
Fig. 49
Fig. 50
<Note>
Be careful, not to be pinched
your finger between motor control
unit and rotor.
Because, rotor is pulled toward
motor control unit by the strong
magnetic force.
Motor control unit
Rotor
Fig. 47 Fig. 48
Gear section
(11) Facing switch unit to the plate installing side, mount the motor and gear section to housing R.
and mount trigger switch section, LED circuit to housing R. See Fig. 49.
(12) Mount plate and lens. And secure housing L with 8 pcs. of pan head screw M3x20. See Fig. 50.
Pan head
screws M3x20
Housing L Housing R
Plate
Lens
Switch unit
Plate installing side
Spacer
Terminal
Lever guide
Trigger switch
section
Buzzer
circuit
(for BFH...F series)
LED circuit
(for BFH...F series)
Switch
lever B
As for buzzer circuit, lever guide, switch lever B and interlock switch, mount as illustrated in Fig. 49A
and Fig. 49B.
Interlock
switch
Hooks of Switch lever B
Lever guide
Fig. 49A
Press switch lever B toward lever guide
through housing R. Then hooks of switch
lever B are interlocked in the assembling
hole of lever guide.
Interlock
switch unit
Buzzer circuit
Boss for protecting
interlock switch unit
Bosses on Housing R
Housing R
Lever guide
Fig. 49B

P 11 / 17
(1) Remove Clutch case section and Housing L from Housing R.
(2) Remove Switch unit of trigger section by carefully extending hooks. See Fig. 51
(3) And then, by removing Tapping bind screw PT3x16 and Cover, you can disassemble Switch section as illustrated
in Fig. 52;
<10> Disassembling Switch Section
Hook
Switch unit of
trigger section
(1) Set Leaf spring in place on Change lever, and install Compression spring 4 on Switch leverA.
And then, set the following parts in place on Switch base;
Compression spring 4
Switch lever A
Change lever
Leaf spring
Switch unit for rotational direction change
Switch base
Switch unit of trigger section
Tapping bind screw PT3x16
Cover
Switch unit for rotational direction change
Switch unit of trigger section
(2) While pushing Change lever with Cover, assemble the parts in Fig. 52 with PT3x16 Tapping bind screw. (Fig. 53)
Take care not to allow Compression spring 4 and protruding portion of Change lever to get out of place.
Protruding portion of Change lever
Install the protruding portion of the Change lever
in the Switch lever A.
Switch lever A
Fig. 51
Fig. 52
Fig. 53
<11> Assembling:

P 12 / 17
Switch lever B and Lever guide can be removed by carefully expanding hooks of Switch lever B in Interlock section
with slotted driver, etc. (Fig. 54)
Hooks of Switch lever B
Lever guide
Slotted driver
Fig. 54
Fig. 55
<12> Disassembling Interlock Section
<13> Caution fort handling rotor
Keep the following minimum distances, when put or store the plural rotors. Failure to keep the minimum distances
will be cause of breakage. See Fig. 55.
10.0 mm (3/8")
15.0 mm
(9/16")
20.0 mm
(13/16")
Lever guide
Switch
lever B

Circuit diagram P 13 / 17
ON/OFF switch
Switch Section
Motor control unit
Terminal
Stator of
DC brushless
motor
Color index of lead wires' sheath
Black
White
Red
Orange
Blue
Yellow
Purple
Gray
Buzzer
circuit Switch unit
(clutch)
Switch unit
(interlock) LED
circuit
Reverse switch
Controller
Connector
Wiring diagram
When connecting Connectors, be sure to connect together two Connectors that have lead wires of the same colors.
(1) Wiring in the rotor fan side of housing
Set Motor section in place on Housing R, and then as illustrated in Fig. A, route the lead wires which connects
Motor section and Controller section.
Housing R
Lead wire (blue)
Lead wire (white)
Lead wire (orange)
(1) First, route the three lead wires:
blue, white and orange.
(2) And then put the other wires
under the three lead wires.
Motor section of
Motor control unit
Controller section of
Motor control unit
Fig. A

Wiring diagram P 14 / 17
(3) Wiring near the trigger switch section
Place Switch section in place on Housing R. See Fig. C for the wiring.
The lead wires to Switch unit of Trigger section must be placed between Pin 1 and Pin 2.
Also do not fail to place the lead wire to Switch unit for rotational direction change between Pin 2 and Pin 3.
(2) Wiring near the LED circuit and clutch switch unit
Put Controller section in place on Housing R, and install LED circuit on Housing R. And then as illustrated in
Fig. B, pull the following parts out of Housing R: Lead wires and Connectors from LED circuit, Clutch switch unit.
1. Clutch switch unit
2. Lead wire to Motor control unit (yellow)
3. Lead wire to Motor control unit (purple)
4. Lead wire from LED circuit (gray)
5. Lead wire from LED circuit (blue)
6. Lead wire to Motor control unit (gray)
7. Lead wire to Motor control unit (blue)
These parts must be
placed out of Housing R.
Fig. B
LED circuit
Fig. C
Controller section of
Motor control unit
Housing R
Pin1
Pin2
Pin3
Switch unit of trigger section
Lead wire to Switch unit for
rotational direction change
(yellow)
Lead wire to switch unit of
trigger section (white)
Lead wire to switch unit of
trigger section (yellow)
Lead wire to Switch unit for
rotational direction change
(blue)
Lead wire to Switch unit for
rotational direction change
(yellow)
Lead wire to Switch unit for
rotational direction change
(blue)
Lead wire from
Motor control unit (yellow) Lead wire from
Motor control unit (blue)
1
2345
67

(5) Wiring near the terminal
1. Connect Terminal to Motor control unit as follows.
There is a flag receptacle on each of the two lead wires (black one and red one) from Motor
control unit.
Connect these receptacles with Terminal as illustrated in Fig. F.
Be sure to connect the flag receptacle on the red lead wire to the (+) terminal, and connect
the other one on the black lead wire to the (-) terminal.
(4) Wiring near the buzzer circuit and interlock switch
Place the lead wires from Buzzer between the boss and the wall of Housing R as illustrated in Fig. D.
And then fix Interlock switch unit to Housing R by fitting the through holes of the Switch unit to the bosses
on Housing R as illustrated in Fig. E.
Lead wire from Buzzer (white)
Boss of Housing R for holding Buzzer
Wall of Housing R
Lead wire from Buzzer (red)
Buzzer
Fig. D
Fig. E
Fig. F
Interlock switch unit
Boss for protecting Interlock switch unit
Bosses on Housing R
Housing R
Lead wire from Interlock switch unit (red)
Lead wire from Interlock switch unit (yellow)
Flag receptacle on
black lead wire Flag receptacle
on red lead wire
Terminal
P 15 / 17

P 16 / 17
2. After connecting flag receptacles, set Terminal in place on Housing R, and put the lead wires
(black one and red one), which connect Terminal to Motor control unit, on the lead wires from
Interlock switch unit illustrated in Fig. G.
And then apply gentle pressure to lead wires (black one and red one) in order to hold down the lead wires which
is laid under them.
Fig. G
Fig. H
Red lead wire which connects Terminal
to Motor control unit
And black one
Terminal
< Note >
Make sure that spacer has been mounted
to housing R, before setting terminal.
Refer to Fig. 49 in page 10.
Top view of clutch switch unit
Clutch switch unit
Pass the lead wires, covered by shrink tube,
through the pin.
And hold them with lead holders at clutch case.
Clutch case
Lead holder
Contain the slack portion
of lead wires and connectors
into this pace.
Pin
(5) Wiring around clutch case
Put the lead wire of clutch switch unit as illustrated in Fig. H

Wiring diagram P 17 / 17
(7) Handling connectors
You can disconnect the connectors which connects up the 6 units/circuits listed below by pulling the connectors to
the directions designated by the arrows as illustrated in Figs. H, I and J:
Buzzer circuit, Interlock switch unit, Switch unit of Trigger section,
Switch unit for rotational direction change, Clutch switch unit, LED circuit
Note: Never hold the wires when separating the connectors, because they are very thin and fragile.
Therefore, always hold the connectors when disconnecting the connectors.
Fig. H Fig. JFig. I
Buzzer circuit Interlock
switch unit Switch unit of Trigger section
Switch unit for rotational
direction change
LED circuit
Clutch switch unit
Other manuals for BFH040
1
This manual suits for next models
4
Table of contents
Other Makita Power Screwdriver manuals
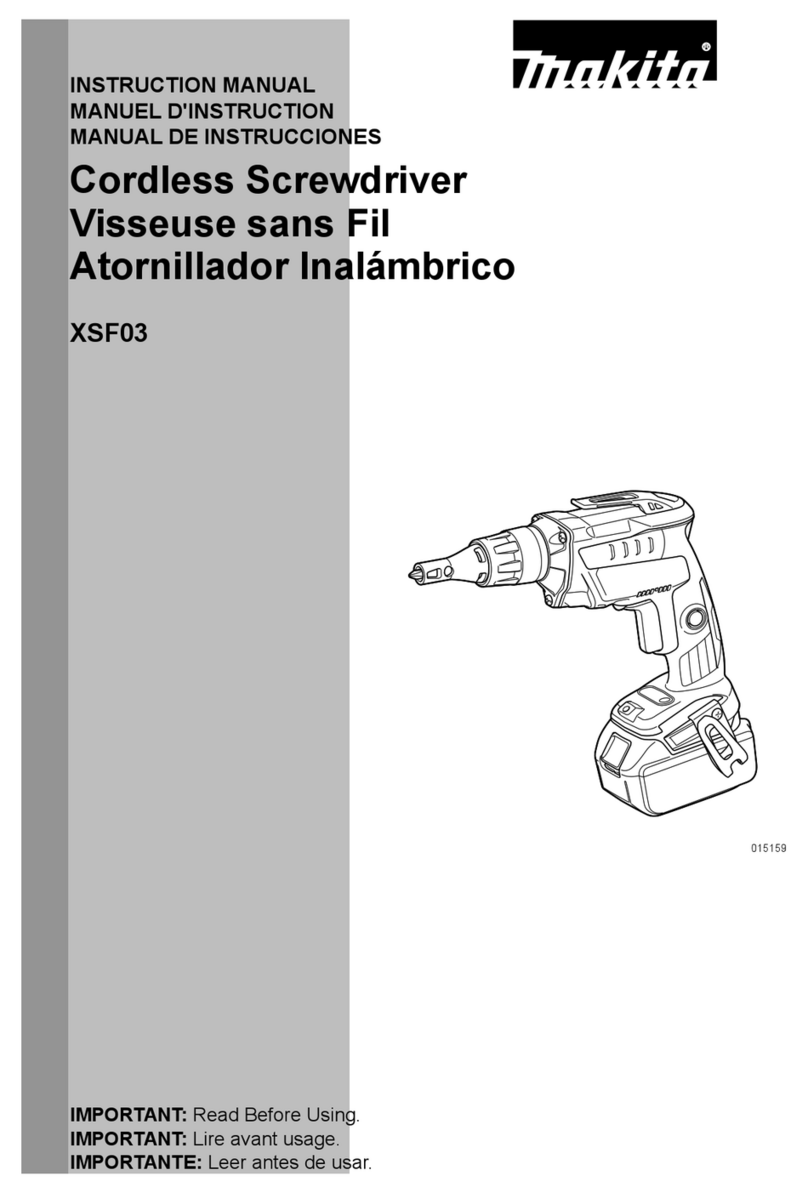
Makita
Makita XT255R User manual

Makita
Makita BFT043F User manual
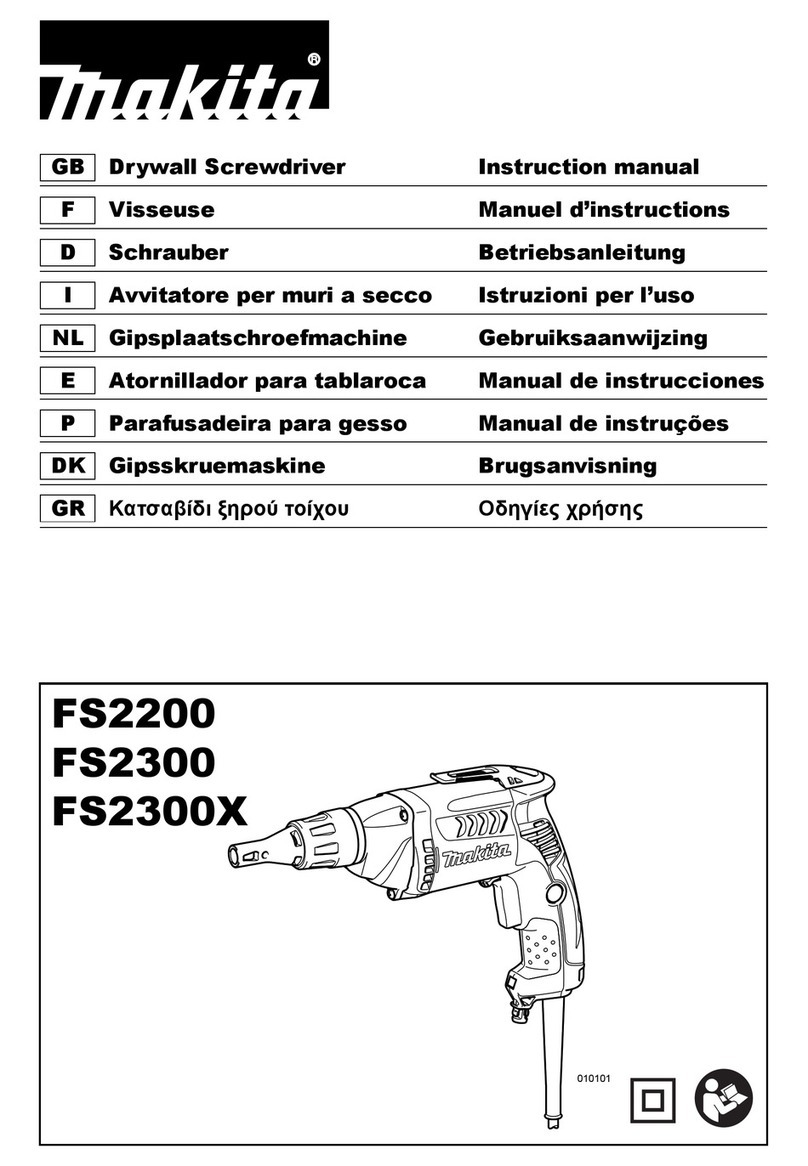
Makita
Makita FS2200 User manual

Makita
Makita DFL123F User manual
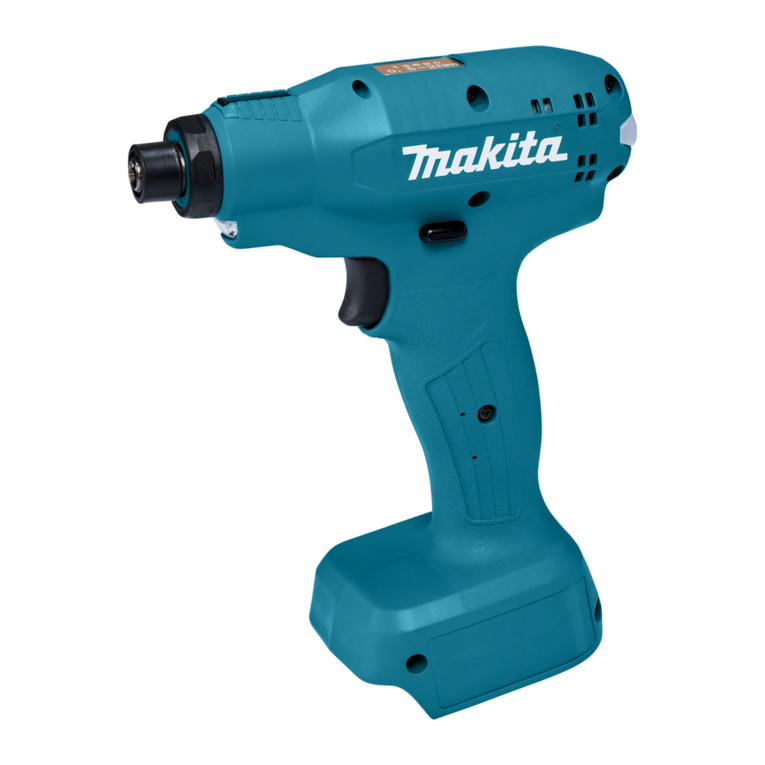
Makita
Makita DFT024F User manual

Makita
Makita AD03 User manual
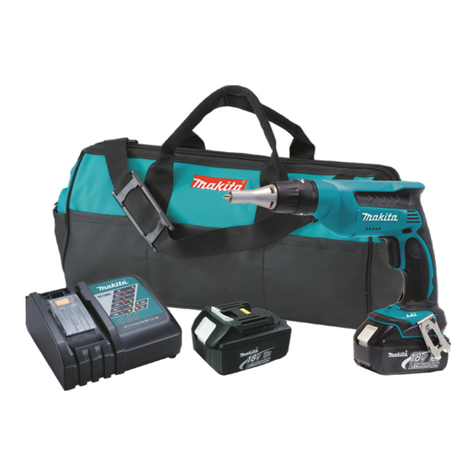
Makita
Makita LXSF02 User manual

Makita
Makita 6802BV User manual
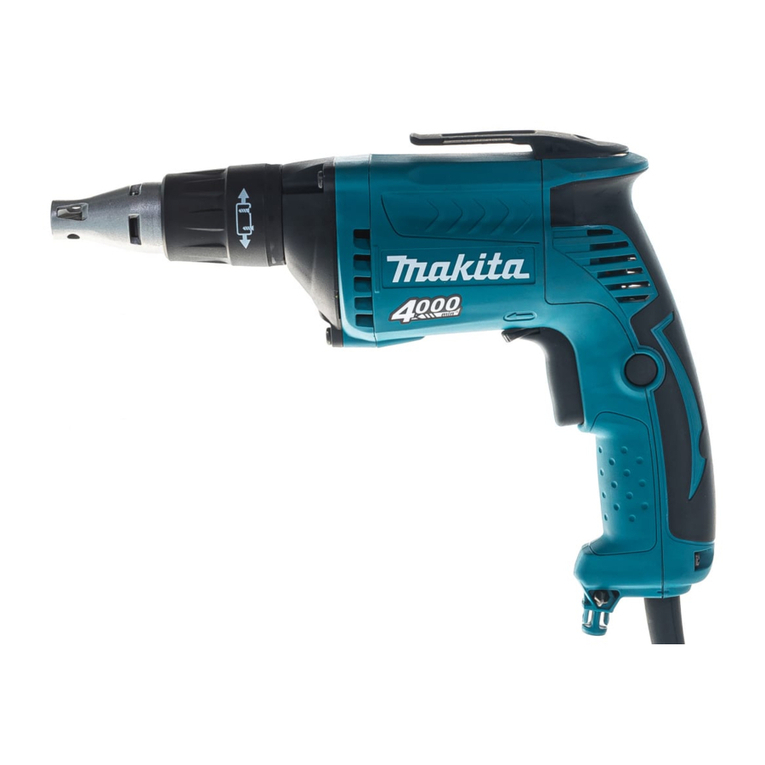
Makita
Makita FS4000 User manual
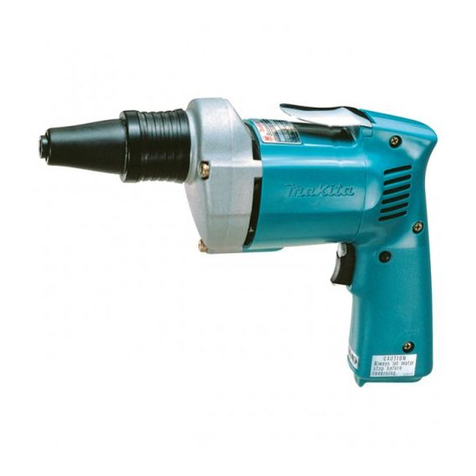
Makita
Makita 6802BV User manual
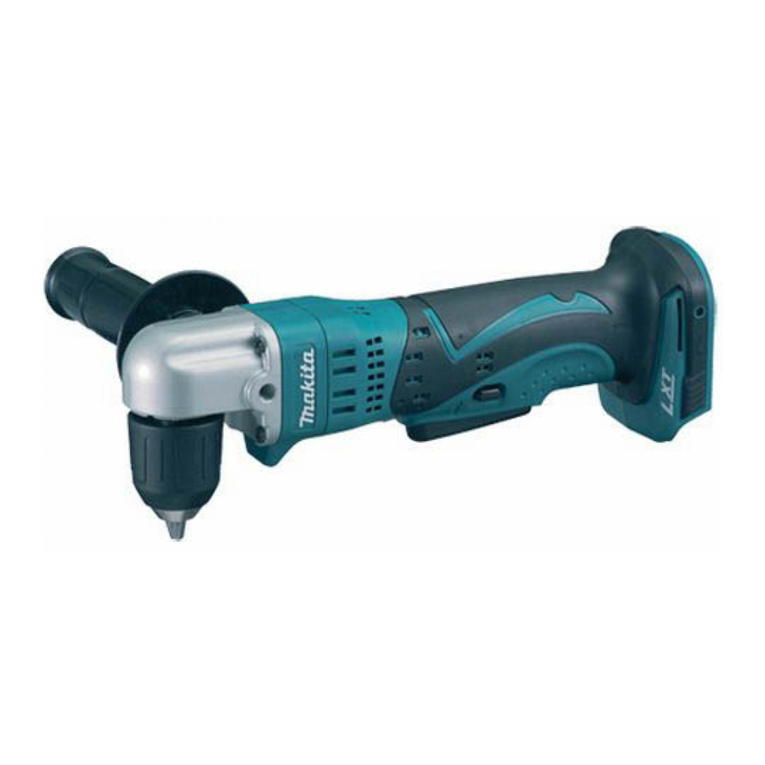
Makita
Makita DDA341 User manual
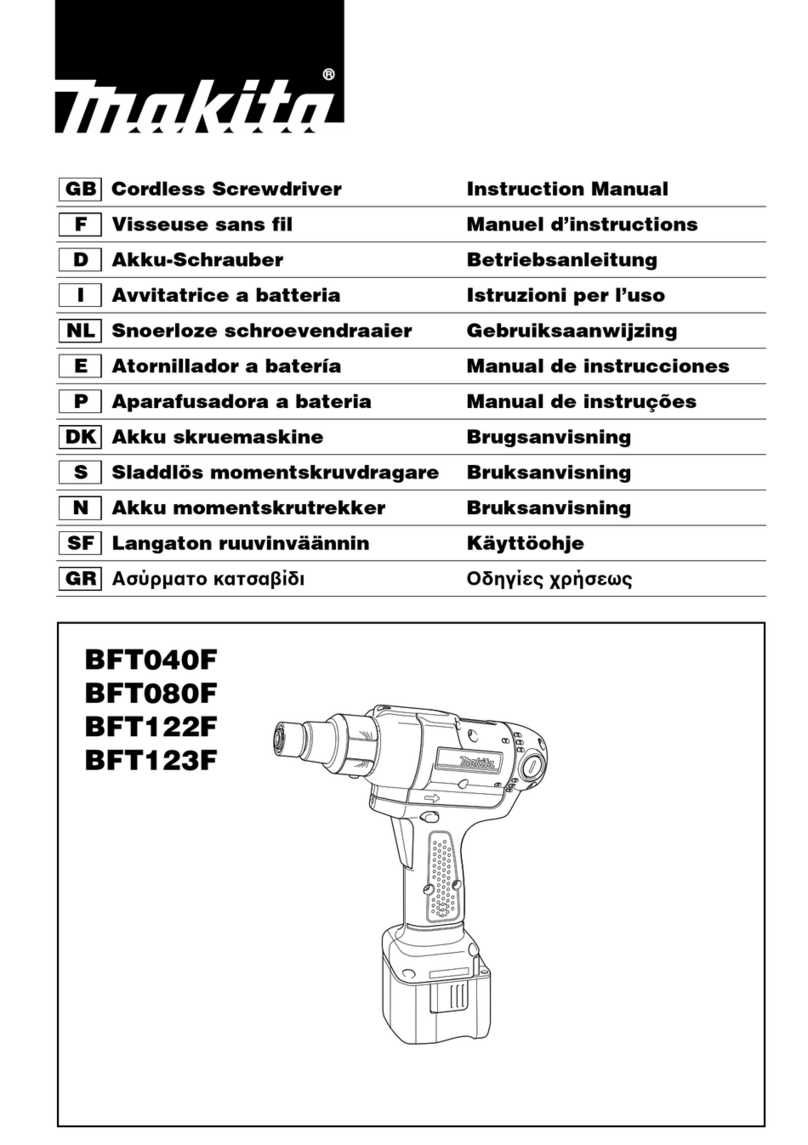
Makita
Makita BFT040F User manual
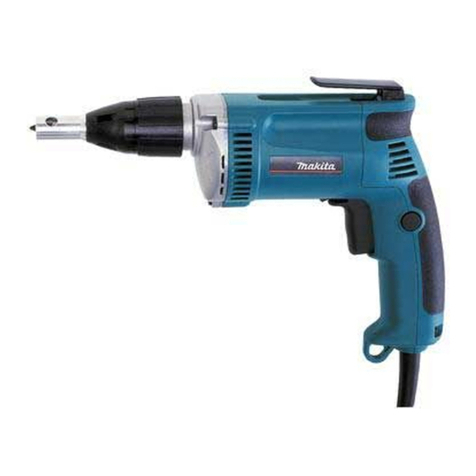
Makita
Makita 6823 User manual
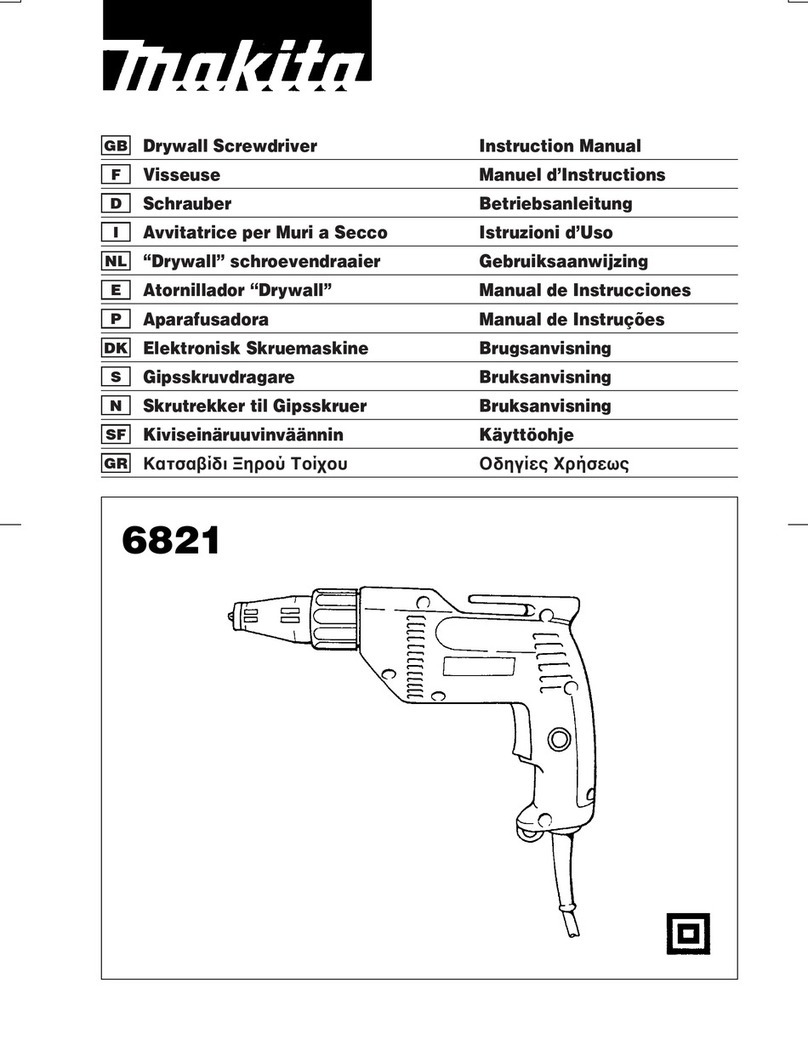
Makita
Makita 6821 User manual
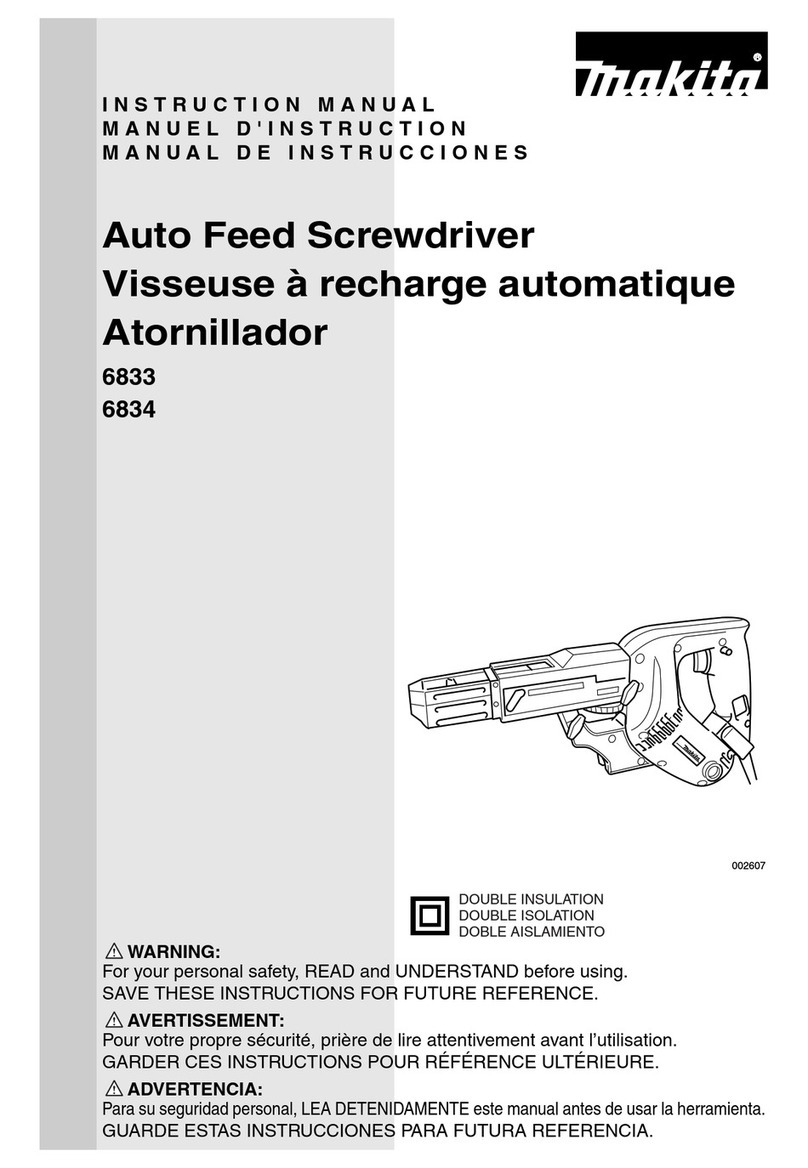
Makita
Makita 6833 User manual

Makita
Makita DFL651F User manual

Makita
Makita FS2500K User manual
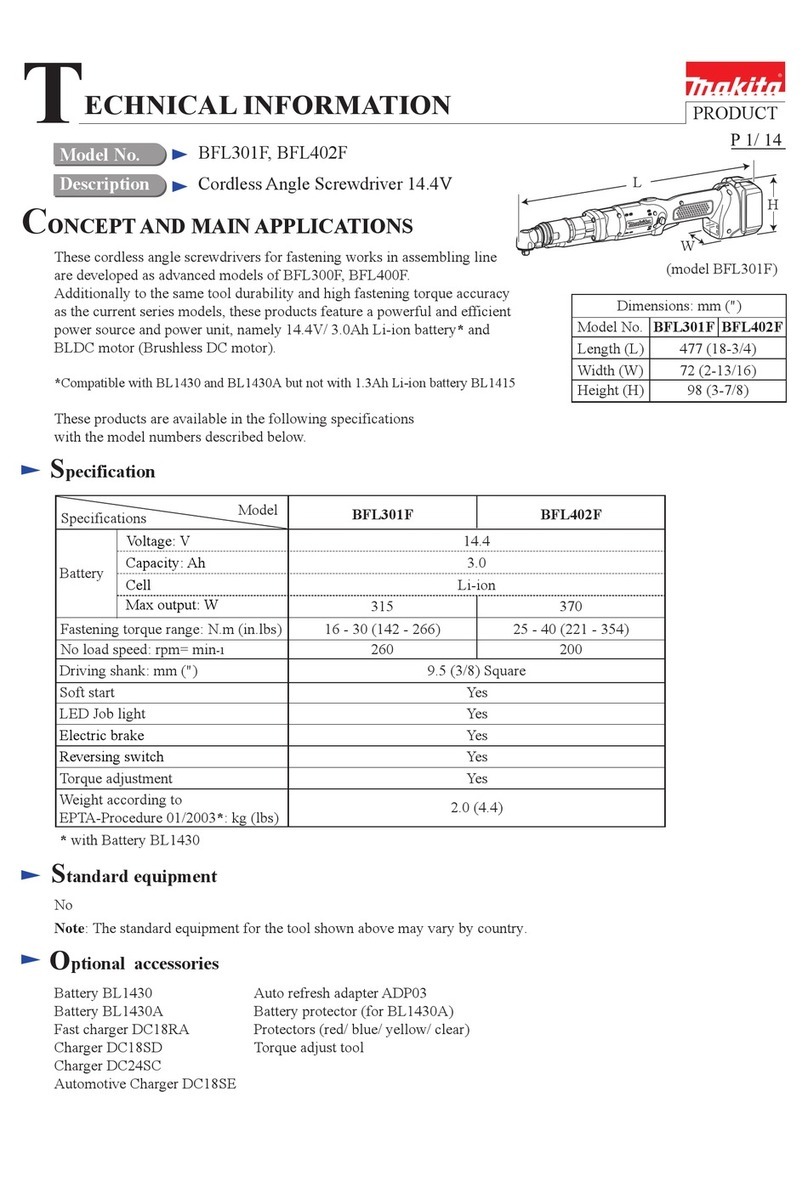
Makita
Makita BFL301F Manual
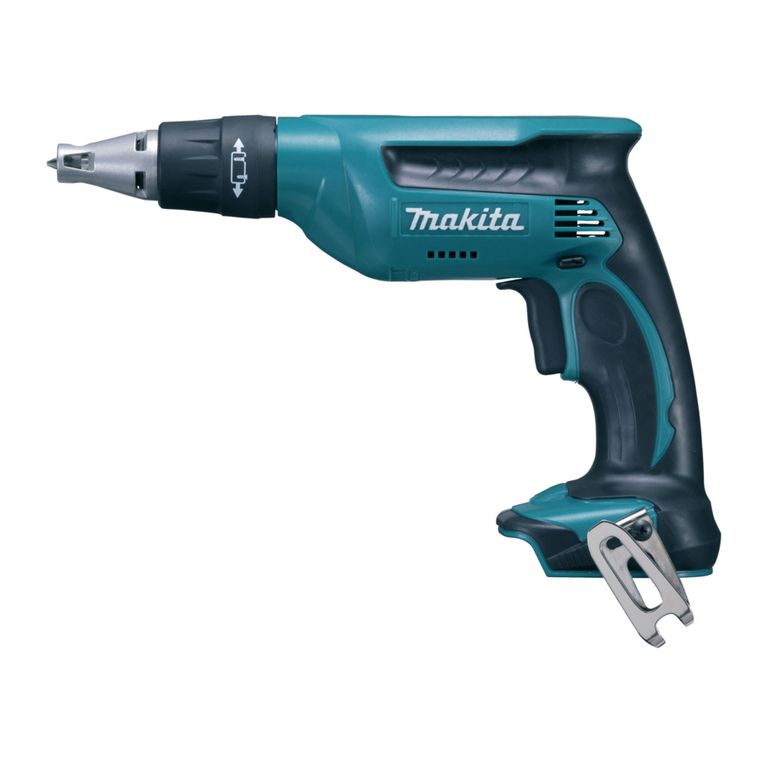
Makita
Makita DFS441 User manual

Makita
Makita 6800DB User manual