Megger HVB 10 User manual

1
HVB 10
High Voltage Measuring Bridge
USER GUIDE
Issue: 04 (01/2019) - EN
Article number: 83041

2

Consultation with Megger
3
Consultation with Megger
The present system manual has been designed as an operating guide and for
reference. It is meant to answer your questions and solve your problems in as fast and
easy a way as possible. Please start with referring to this manual should any trouble
occur.
In doing so, make use of the table of contents and read the relevant paragraph with
great attention. Furthermore, check all terminals and connections of the instruments
involved.
Should any question remain unanswered or should you need the help of an authorized
service station, please contact:
Megger Limited Seba Dynatronic
Mess- und Ortungstechnik GmbH
Archcliffe Road
Kent CT17 9EN
T: +44 1304 502100
F: +44 1304 207342
E: uksales@megger.com
Dr.-Herbert-Iann-Str. 6
D - 96148 Baunach
T: +49 9544 68 – 0
F: +49 9544 22 73
E: team.dach@megger.com
Hagenuk KMT
Kabelmesstechnik GmbH
Megger USA
Röderaue 41
D - 01471 Radeburg / Dresden
T: +49 35208 84 – 0
F: +49 35208 84 249
E: team.dach@megger.com
Valley Forge Corporate Centre
2621 Van Buren Avenue
Norristown, PA 19403 USA
T: +1 610 676 8500
F: +1 610 676 8610
Megger
All rights reserved. No part of this handbook may be copied by photographic or other means unless Megger
have before-hand declared their consent in writing. The content of this handbook is subject to change without
notice. Megger cannot be made liable for technical or printing errors or shortcomings of this handbook.
Megger also disclaims all responsibility for damage resulting directly or indirectly from the delivery, supply, or
use of this matter.

Terms of Warranty
4
Terms of Warranty
Megger accept responsibility for a claim under warranty brought forward by a customer
for a product sold by Megger under the terms stated below.
Megger warrant that at the time of delivery Megger products are free from manufacturing
or material defects which might considerably reduce their value or usability. This
warranty does not apply to faults in the software supplied. During the period of warranty,
Megger agree to repair faulty parts or replace them with new parts or parts as new (with
the same usability and life as new parts) according to their choice.
This warranty does not cover wear parts, lamps, fuses, batteries and accumulators.
Megger reject all further claims under warranty, in particular those from consequential
damage. Each component and product replaced in accordance with this warranty
becomes the property of Megger.
All warranty claims versus Megger are hereby limited to a period of 12 months from the
date of delivery. Each component supplied by Megger within the context of warranty will
also be covered by this warranty for the remaining period of time but for 90 days at
least.
Each measure to remedy a claim under warranty shall exclusively be carried out by
Megger or an authorized service station.
This warranty does not apply to any fault or damage caused by exposing a product to
conditions not in accordance with this specification, by storing, transporting, or using it
improperly, or having it serviced or installed by a workshop not authorized by Megger.
All responsibility is disclaimed for damage due to wear, will of God, or connection to
foreign components.
For damage resulting from a violation of their duty to repair or re-supply items, Megger
can be made liable only in case of severe negligence or intention. Any liability for slight
negligence is disclaimed.
Since some states do not allow the exclusion or limitation of an implied warranty or of
consequential damage, the limitations of liability described above perhaps may not
apply to you.

Contents
5
Contents
Consultation with Megger...............................................................................................3
Terms of Warranty ...........................................................................................................4
Contents ...........................................................................................................................5
1Safety Instructions ...........................................................................................7
1.1 Basic Notes ........................................................................................................7
1.2 General Safety Instructions and Warnings.........................................................8
2Technical Description ....................................................................................10
2.1 System Description ..........................................................................................10
2.2 Technical Data .................................................................................................12
2.3 Connections, Controls and Display ..................................................................14
3Commissioning ..............................................................................................15
3.1 Electrical Connection in Fault Prelocation Mode .............................................16
3.2 Electrical Connection in Testing, Burning and Pinpointing Mode ....................18
3.3 Electrical Connection: Special Applications .....................................................19
3.4 Use of an External Safety Device (Optional)....................................................21
4Operation ........................................................................................................22
4.1 Switching On the System .................................................................................22
4.2 General Operation............................................................................................22
4.3 Security Mechanisms .......................................................................................24
4.4 System Settings ...............................................................................................25
4.5 Operating Modes..............................................................................................26
4.5.1 Testing the Insulation - ..............................................................................26
4.5.2 Prelocating a Fault - / ........................................................................28
4.5.3 Pinpointing a Sheath Fault - ......................................................................30
4.5.4 Burning - .....................................................................................................32
4.6 Concluding the Test .........................................................................................33
5Processing Log Data......................................................................................34
6Updating the Firmware ..................................................................................35
7Maintenance and Care ...................................................................................36


Safety Instructions
7
1Safety Instructions
1.1 Basic Notes
This handbook contains basic instructions for the commissioning and operation of the
HVB 10. For this reason, it is important to ensure that the manual is always available to
authorised and trained personnel. Operating personnel should read the manual
thoroughly. The manufacturer will not be held liable for any injury or damage to
personnel or property through failure to observe the safety precautions contained in this
handbook.
The specific standards and regulations in each country must also be observed.
Important instructions concerning personnel, operational and technical safety are
marked in the text as follows:
Symbol Description
WARNING
Indicates a potential danger of an electric shock that may result in
fatal or
serious injury.
CAUTION
Indicates a potential danger that may lead to slight or moderate injury.
The notes contain important information and useful tips for using the
system. Failure to observe them can render the measurement results
useless.
It is important to observe the generally applicable electrical regulations of the country in
which the device will be installed and operated, as well as the current national accident
prevention regulations and internal company directives (work, operating and safety
regulations).
After working on the system, it must be voltage-free and secured against reconnection
as well as having been discharged, earthed and short-circuited.
Use genuine accessories to ensure system safety and reliable operation. The use of
other parts is not permitted and invalidates the warranty.
This system and its peripheral equipment may only be operated by trained or instructed
personnel. Anyone else must be kept away.
The system may only be installed by an authorised electrician. DIN VDE 0104 (EN
50191), DIN VDE 0105 (EN 50110) and the German accident prevention regulations
(UVV) define an electrician as someone whose knowledge, experience and familiarity
with the applicable regulations enables him to recognise potential hazards.
Repair and maintenance work may only be performed by Megger or authorised service
partners. Megger recommends having the system tested and maintained at a Megger
service centre once a year.
Megger also offers its customers on-site service. Please contact your service centre as
needed.
Safety precautions
Labelling of safety
instructions
Working with products
from Megger
Operating staff
Repair and
maintenance

Safety Instructions
8
This device is designed for industrial use according to EN 55011. When used at home it
could cause interference to other equipment, such as the radio or television.
The interference level from the line complies with the limit curve B (living area), the
radiation level complies with the limit curve A (industrial area). Once the living area is
sufficiently far away from the planned area of operation (industrial area), equipment
there will not be impaired.
The device must only be lifted and carried using the handles provided on the top and
side. Other parts of the device, such as the accessory bag or connecting cables, cannot
withstand the forces caused by lifting the device and could break or tear off as a result.
1.2 General Safety Instructions and Warnings
The operating safety is only guaranteed if the delivered system is used as intended.
Incorrect use may result in danger to the operator, to the system and the connected
equipment.
The thresholds listed in the technical data may not be exceeded under any
circumstances. Condensation during the operation of Megger products may result in
danger to persons and devices through voltage arc-over. Prevent condensation before
and during the measuring mode by cooling the measuring systems sufficiently. The
operation of Megger products in direct contact with water, aggressive substances and
inflammatory gases and vapours is prohibited.
The HVB 10 is built to be robust and can withstand the stresses it can expect to be
subjected to in demanding everyday use. Nevertheless, it is a precision measuring
device which needs to be treated with the appropriate care. This applies in particular to
the connection cable and the clamps, which play an important role in ensuring the
device remains safe while the results of measurements remain precise.
The system may only be operated whilst it is in perfect working condition. In the event of
damage, irregularities or malfunctions that cannot be resolved with the assistance of the
operating instructions, the system must be shut down immediately and labeled
accordingly. In such an event, the relevant management must be informed. Please
contact Megger Service immediately, to eliminate the malfunction. The system may only
be started up again once the malfunction has been eliminated.
Five safety rules
The five safety rules must always be followed when working with HV (High Voltage):
1. De-energise
2. Protect against re-energising
3. Confirm absence of voltage
4. Earth and short-circuit
5. Cover up or bar-off neighbouring energised parts
Using cardiac pacemaker
Physical processes during operation of high voltage may endanger persons
wearing a cardiac pacemaker when near these high voltage facilities.
Electromagnetic
radiation
Lifting and carrying
Use only as intended
Procedure in the event
that the device
malfunctions

Safety Instructions
9
Fire fighting in electrical installations
•According to regulations, carbon dioxide (CO2) is required to be
used as extinguishing agent for fighting fire in electrical
installations.
•Carbon dioxide is electrically non conductive and does not leave
residues. It is safe to be used in energized facilities as long as the
minimum distances are maintained. A CO2fire exti
nguisher must be
always available within electrical installations.
•If, contrary to the regulations, any other extinguishing agent is used
for fire fighting, this may lead to damage at the electrical
installation. Megger disclaims any liability for consequential
damage. Furthermore, when using a powder extinguisher near
high-voltage installations, there is a danger that the operator of the
fire extinguisher will get an electrical shock from a voltage arc-over
(due to the powder dust created).
•It is essential to observe the safety instruction on the extinguishing
agent.
•Applicable is DIN VDE 0132.
WARNING
Be careful when working with high voltage
Working on high voltage systems and equipment – especially in non-
stationary operation – requires particular care and safety-
conscious action
on the part of test personnel. VDE regulations 0104 on setting up and
operating electrical test systems, as well as EN 50191 and national
standards and regulations must be strictly adhered to.
•The System generates a dangerous voltage of up to 10 kV. This is
supplied via a HV connection cable to the test object.
•The test system may not be operated without supervision.
•Never fail to use safety equipment or put it out of operation.
•To prevent dangerous charge accumulation, earth all metal parts in the
vicinity of the high voltage equipment.
•When high voltage is shut off, the cable under test is discharged by an
internal discharge device. This discharge device is designed for a
maximum test object capacity in compliance with the technical data.
This value must not be exceeded. The discharge device may otherwise
become damaged and charge may remain in the test object. The cable
must therefore always be discharged in accordance with the applicable
safety regulations, e.g. discharged using a discharge rod and then be
shorted before the danger zone is accessed.

Technical Description
10
2Technical Description
2.1 System Description
Due to its high measurement resolution and accuracy, the high voltage measuring
bridge HVB 10 is supposed to be used to prelocate faults of the primary insulation that
are difficult or impossible to locate using other methods like a pulse reflection
measurements. Typical examples are high-resistive conductor faults in paper insulated
(PILC) cables, faults in very long cables (long fault distance) and faults in cross-bonded
cable systems.
Furthermore, the system permits in the easiest way the testing of cable sheaths and
prelocation and pinpointing of cable sheath faults.
To test the integrity of the inner cable insulation or the sheath, the HVB 10 works in test
mode with a voltage of up to 10 kV kV (negative polarity).
The prelocation of a detected fault takes place using the voltage drop method, in which
the current, voltage and resistance before and after the fault location are determined
and considered in relation to the cable length. The necessary measuring and calculation
steps take place automatically and, after a few seconds, the distance to the fault is
displayed. Due to the bipolar measurement, falsifying thermoelectric and galvanic
influences can be detected and mathematically eliminated.
For sheath fault pinpointing, the device provides several possibilities. One of these is a
pulsed DC output voltage, which is used in combination with an earth fault locator as the
ESG to locate the sheath fault by the step voltage method. A second method is to
pinpoint the fault with a so-called A-Frame while the HVB 10 transmits a low frequency
(3 or 4.8 Hz) signal.
If the device is equipped with the “AF” option it simultaneously transmits a 8.44 kHz
audio frequency signal into the cable when working in pinpointing mode.
Intended use
Function

Technical Description
11
The HVB 10 combines the following features in a single device:
•Easy and comfortable operation via rotary encoder (EasyGo) and touch screen
•Bipolar measurement
•Two prelocation modes to cope with the different (fault type dependant)
accuracy requirements
•Burning mode with manual control of the output voltage, selectable current limit
and up to 200 mA of continuous output current (max. 5 minutes)
•Pinpointing with pulsed DC voltage
•Fully automatic measurement
•Independent from the resistance of supplementary wires and test leads
•Detection of incorrect hook-up to cable under test
•Fault locating of high resistive faults inside cables
•Detection, storage and data recording of fast processes (wipers, breakdowns)
•Logging and log data export to Easyprot software via USB
•Integrated discharge with active overload protection
•High-performance battery for power supply independent of the mains
•Robust IP53 trolley case with extendable handle
•Wide range input for the voltage supply
The scope of delivery of the system includes the following:
•HVB 10
•HV connection cable (incl. aligator clips), 4 m
•Mains connection lead, 2.5 m
•Earthing lead, 5 m
•2 x Kelvin clip for HV cable terminations, red
•4 x aligator clip for HV cable terminations, black
•2 x measuring leads (incl. aligator clips), 0.5 m
•12 V vehicle charging cable, 3.5 m
•Accessory bag
•USB flash drive with Easyprot software
•Manual
Check the contents of the package for completeness and visible damage right after
receipt. In the case of visible damage, the device must under no circumstances be taken
into operation. If something is missing or damaged, please contact your local sales
representative.
Features
Scope of delivery
Check contents

Technical Description
12
The following optional accessories can also be ordered from Megger Sales:
Accessory Description Item number
Connection set for HV
cable terminations
Connection set with 8 larger connection
clamps (e.g. for HV
cable terminations) and
connection cables 2 m in length (for the
wiring at the far end of the cable)
1003344
External safety device Safety device for norm-compliant signaling
and Emergency Stop according to DIN EN
50191 / VDE 0104.
893024147
Connection cable VK 67 Connection cable for connection of the
external safety device.
820003129
2.2 Technical Data
The HVB 10 has the following parameters:
Parameter Value
Output voltage 0 … 10 kV DC, bipolar
Output current 200 mA at 0.5 … 1.5 kV,
60 mA at 5 kV,
30 mA at 10 kV
Maximum permitted capacity of
the test object
25 µF
Test voltage 0 … −10 kV
Prelocation
•Method
•Measuring accuracy
Voltage drop method (fully automatic)
±0,1%
Pinpointing
•Voltage
•Duty cycle
•Pulse rates
•
Audio frequency (devices with
“AF” option only)
0 … -10 kV DC, pulsed
selectable
0.5:1 / 1:2 / 1.5:0.5 / 1.5:3.5
4,8 Hz („vLoc“ A-frame of VivaxMetrotech)
3 Hz („SFL2“ A-frame of Metrotech)
f = 8.44 kHz, Uo = 100 VRMS, P = 7 Wpeak (at 500 Ω)
Power supply (rated voltage) 88 V … 264 V, 50 / 60 Hz
DC supply (for charging only) 12/24 V DC
Battery Built-in NiMH battery (340 Wh)
Operating time whilst
battery powered
approx. 2 hours1
Power consumption max. 500 VA
Display 320 x 240 pixel LCD, LED backlight
Interfaces USB port
1The value depends largely on the operating conditions. The value specified applies to
continuous pinpointing with a rate of 1:3 at an output of 300 W.
Optional accessories

Technical Description
13
Parameter Value
Memory 2 GB flash memory for system and user data
Data logging with a USB stick
Operating temperature −25 °C ... +55 °C
Storage temperature −40 °C ... +70 °C
Operating humidity max. 93% relative humidity
Dimensions (W x H x D) 500 x 457 x 305 mm
Weight 25 kg
Protection class (according to
IEC 61140 (DIN VDE 0140-1))
I (protective earthing)
Protection rating (according to
IEC 60529 (DIN VDE 0470-1))
IP53 (with closed lid)

Technical Description
14
2.3 Connections, Controls and Display
The HVB 10 has the following connections, controls and display:
Element Description
Touch-screen display
USB port
On/off push-button
HV “interlock” key switch
“HV ON” push-button
“HV OFF” push-button
Rotary encoder
Protective earthing connection
HV output
WARNING
The HVB 10 generates a dangerous voltage of up to 10 kV
during HV operation. This is induced into the HV connection
cable through the HV output.
Power supply socket with fuses F1 / F2 (2 x M6.3/250)
12 … 24 V DC charging socket
Emergency off button
Socket to connect the external safety device (see page 17)

Commissioning
15
3Commissioning
WARNING
Safety instructions for commissioning
•The safety guidelines for the operation of mobile testing systems often
differ from one network operator to another and are frequently subject
to national regulations (such as the German BGI 5191). Before the
measurement session, find out what the applicable guidelines are and
follow the rules set out therein precisely, in respect of the organisation
of work and the commissioning of the mobile test system.
•Before connecting the test object, always follow the general safety
instructions and the five safety rules in particular (see page 8).
•Select a location that is sufficient for the weight and size of the system
and which ensures that it stands securely.
•The air inlet and outlet vents on both sides of the device may not be
covered during operation.
•When setting up and connecting the device, make sure that it does not
impair the function of any other systems or components. If other
systems and components have to be modified in order to set up and
operate the device, be sure to reverse these actions when the work is
finished. Always take the special requirements of these systems and
components into account and only carry out work on them after
consulting and obtaining approval from whoever is in charge of them.
•All cables which are out of operation and not tested must be shorted
and earthed.
•The protective earth connection must always be connected to a
suitable earthing point (e.g. station earth). Inadequate protective earth,
especially when operating the HVB 10 by battery, can raise the
potential of the device, and the hazardous voltages produced make it
unsafe to handle.
•Since the voltage applied to the test object can assume values that
pose a risk of incidental contact, the cable ends must be shielded in
accordance with VDE 0104 to avoid this. When doing so, be sure to
take all cable branchings into account.

Commissioning
16
3.1 Electrical Connection in Fault Prelocation Mode
The following figure shows the simplified connection diagram:
Connection diagram
88 V … 264 V,
50 / 60 Hz Connecting method for sheath fault location
Connecting method for a fault between inner conductor and shield
Connecting method for a fault between two adjacent conductors of a multicore cable
Observe position / order

Commissioning
17
Connect the system in the following order:
Step Description
1 Using the earthing cable, the protective earthing connection of the HVB 10
is connected to a suitable point on the protective earth system (station earth).
2 Plug in and tighten the HV connection cable to the HV output on the device,
in compliance with the alignment specified by the guide grooves.
CAUTION
To protect the HV connector from damage
, the protective caps on
both jack and plug have to be reinstalled as soon as the cable is
disconnected from the device.
3 Depending on the applied connecting method (see figure on previous page),
connect the yellow connection lead either directly to a suitable earth point of
the cable system under test or to one of the faulty inner conductors (which in
turn needs to be earthed).
4 Connect the red and the brown connection leads to the conductor to be tested
(see figure on previous page).
To achieve optimal results during prelocation, you should use separate
connection clamps or the supplied red Kelvin clip!
5 Connect the black and the green connection leads to separate healthy
conductors (auxiliary conductors) of the same cable system.
6 At the far end of the cable, connect both auxiliary conductors to the conductor
to be tested (the one to which the red and the brown connection leads are
connected to).
To achieve optimal results during prelocation, you should use separate
connection clamps or the supplied red Kelvin clip to connect the
auxiliary conductors to the conductor under test.
Make sure the contact is of good quality (remove or clean any dirt or
corroded surfaces).
7 In case of a sheath test or a sheath fault location, the earthing of the shields
and the auxiliary conductors must be removed!
If there are any voltage transformers, they must be separated from the test
object. Make also sure that there is no indirect contact to earth, e.g. through
joints.
8 If the unit is to be powered through the mains, connect the supplied mains
power cable to the power supply socket of the HVB 10 and a mains socket.
Otherwise, the device on being switched on is automatically powered by the
internal battery. In which event, ensure that the battery has a sufficient charge.
If necessary, charge the battery (see page 36).
Procedure

Commissioning
18
3.2 Electrical Connection in Testing, Burning and Pinpointing
Mode
In testing, burning and pinpointing mode, all connecting leads except of the yellow one
have to be connected to the conductor to be testes or faulty conductor respectively.
Inner conductor testing / inner conductor fault burning
Sheath testing or sheath fault burning / pinpointing
When testing cable systems for which the probability of a fault is very low, all conductors
to be tested can be bridged and tested in a single step, without having to reconnect.
In this procedure, the capacity of the measured object is the sum of the capacities of all
the connected conductors and, of course, must not exceed the maximum capacity of 25
µF! If the test result indicates that one of the conductors is affected by leakage fault, the
electrical connection must be corrected and each conductor individually tested.

Commissioning
19
3.3 Electrical Connection: Special Applications
This method of prelocating a fault should only be used when absolutely unavoidable,
e.g. when no second, fault-free auxiliary conductor is available.
The precision will be impaired in the same way as the simple Murray loop bridge is
impaired by the effects of the contact resistances, but should remain comparatively
higher.
Furthermore, the auxiliary conductor must be fault-free. It is connected as follows:
For this type of prelocation, the double cable length must be entered!
If both conductors are not of the same type (cross section, conductor material,
length), they should be treated like a mixed cable with two sections (with the
faulty conductor being the first section) during prelocation.
Prelocation using one
auxiliary conductor only

Commissioning
20
Under certain circumstances, prelocation can also be performed on a spooled cable
which allows the HVB 10 to be connected directly to both ends of the cables.
To prelocate an inner conductor fault, the cables only have to be connected to the two
faulty conductors as shown in the following illustration (shield/inner conductor or inner
conductor/inner conductor):
Prelocating a sheath fault, in contrast, requires a conductive sheath with is used as a
return conductor for the fault current. The yellow connection cable must, in this case, be
connected to the earthed outer sheath. The contact for the conductive sheath must be
established very carefully (e.g. using copper mesh tape which is looped tightly around
the sheath several times and pressed securely in place using pipe clamps or cable ties).
The reference point for the measured fault distance is the end of the cable to
which the yellow line is connected.
For this application, the conductive outer sheath of the cable is used as a return path for
the fault current. Accordingly, the outer sheath must be earthed at as many places as
possible to ensure the fault current can flow out of the pipe and into the ground. An
earth point like this can e.g. be established with the aid of copper mesh tape (see
above).
Prelocation when there
is direct access to both
ends of the cable
Prelocation for cables
with a conductive outer
layer installed in pipes
Observe position / order
Table of contents
Other Megger Measuring Instrument manuals

Megger
Megger TDR2000/3 User manual
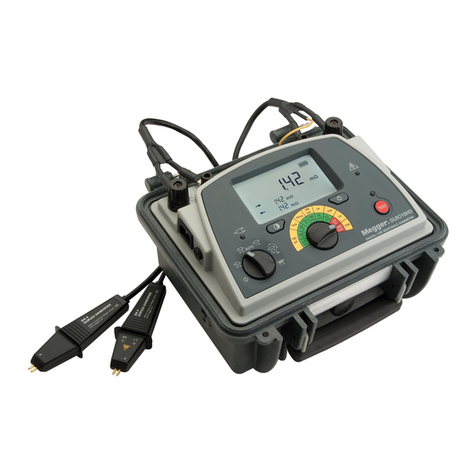
Megger
Megger DLRO10HD User manual
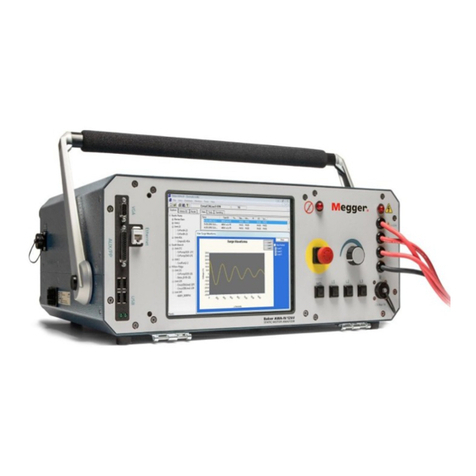
Megger
Megger Baker AWA-IV User manual

Megger
Megger MWA300 Series User manual
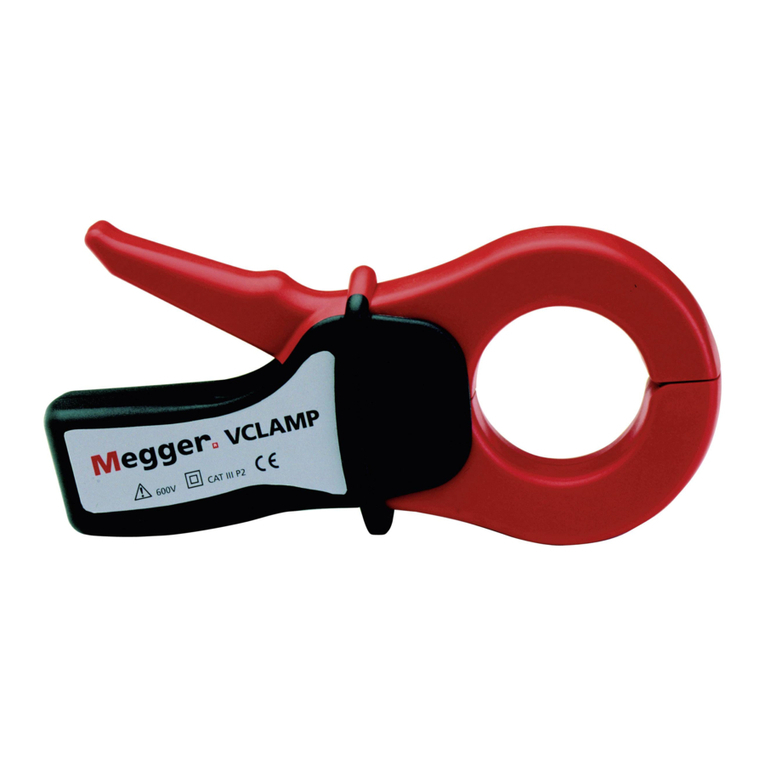
Megger
Megger VCLAMP User manual
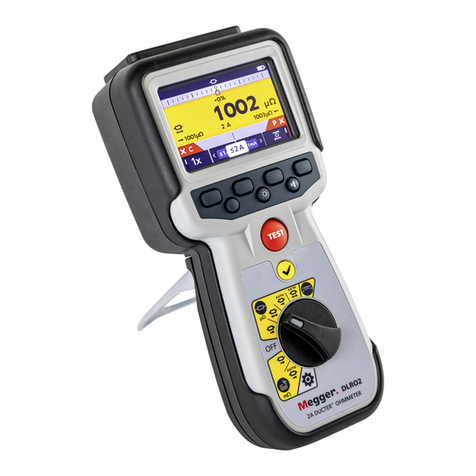
Megger
Megger Ducter DLRO2 User manual
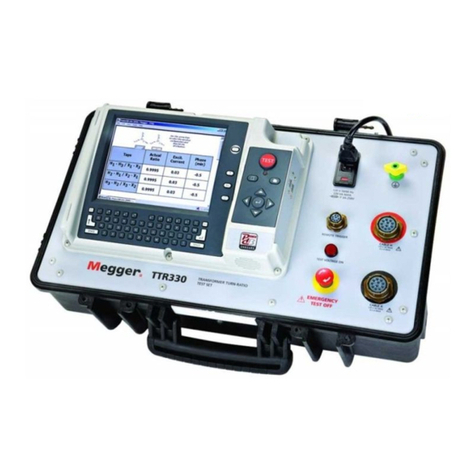
Megger
Megger Three-Phase TTR User manual
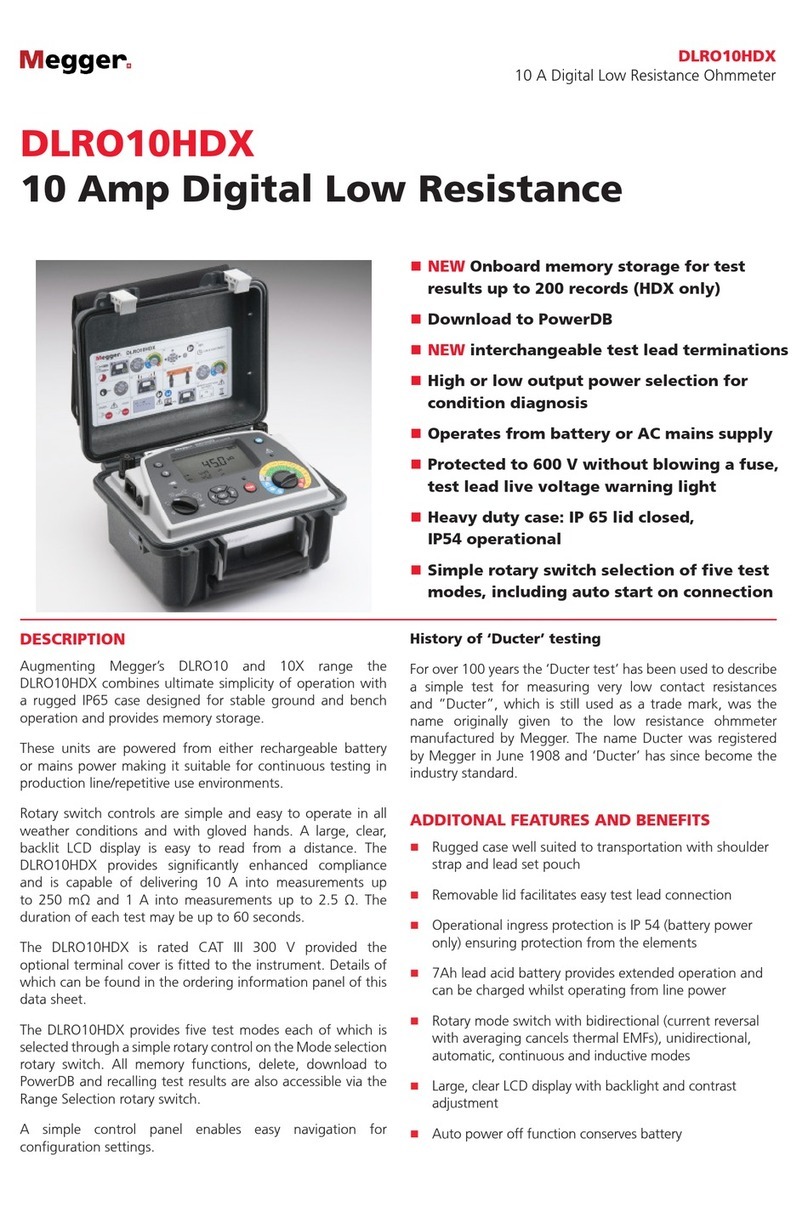
Megger
Megger DLRO10HDX User manual

Megger
Megger DLRO-10 User manual

Megger
Megger DLRO10HD User manual
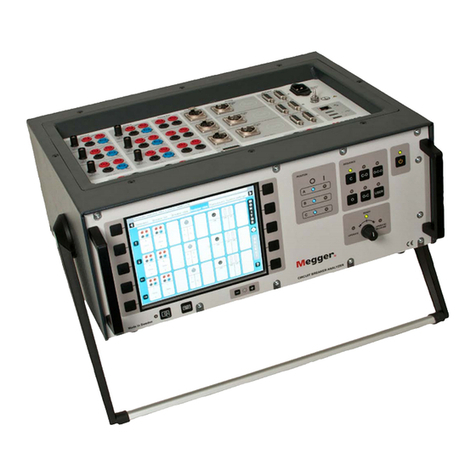
Megger
Megger TM1700 Series User manual
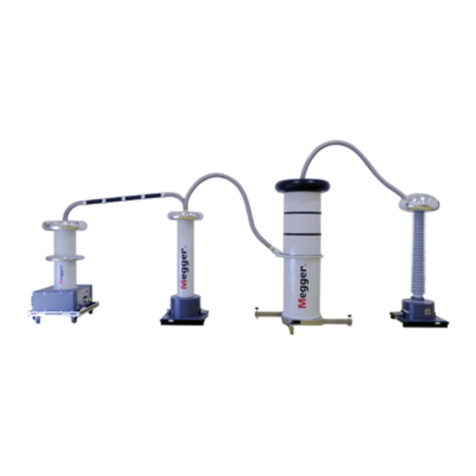
Megger
Megger HV DAC-300 User manual

Megger
Megger PDS 60 User manual
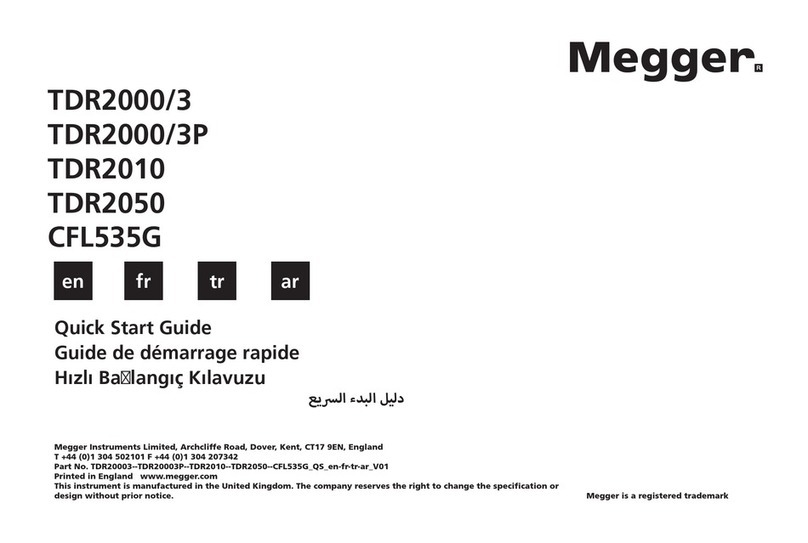
Megger
Megger TDR2000/3 User manual
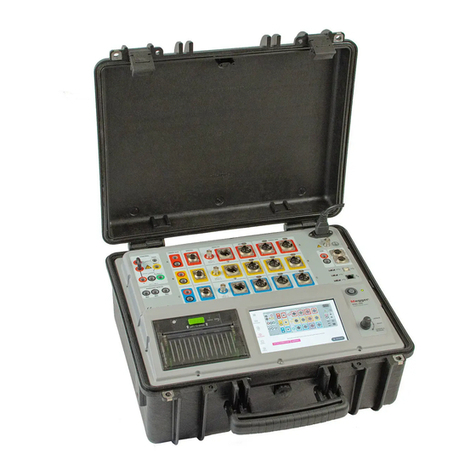
Megger
Megger EGIL200 Series User manual
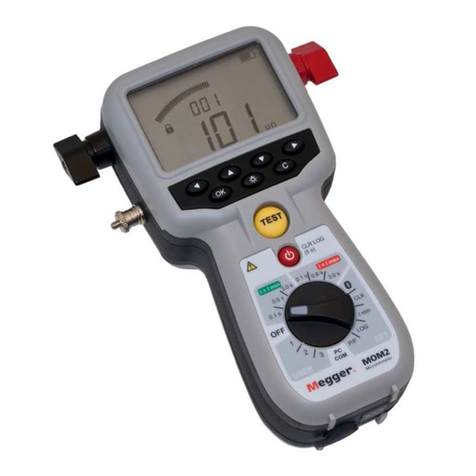
Megger
Megger MOM2 User manual
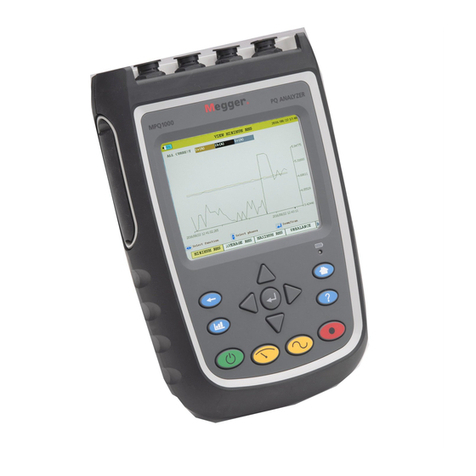
Megger
Megger MPQ1000 User manual
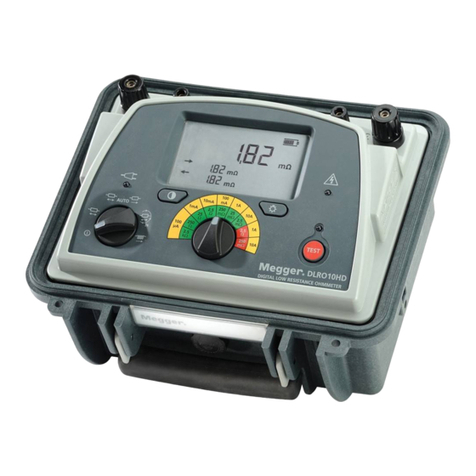
Megger
Megger 1006-603 User manual

Megger
Megger DCM330 User manual
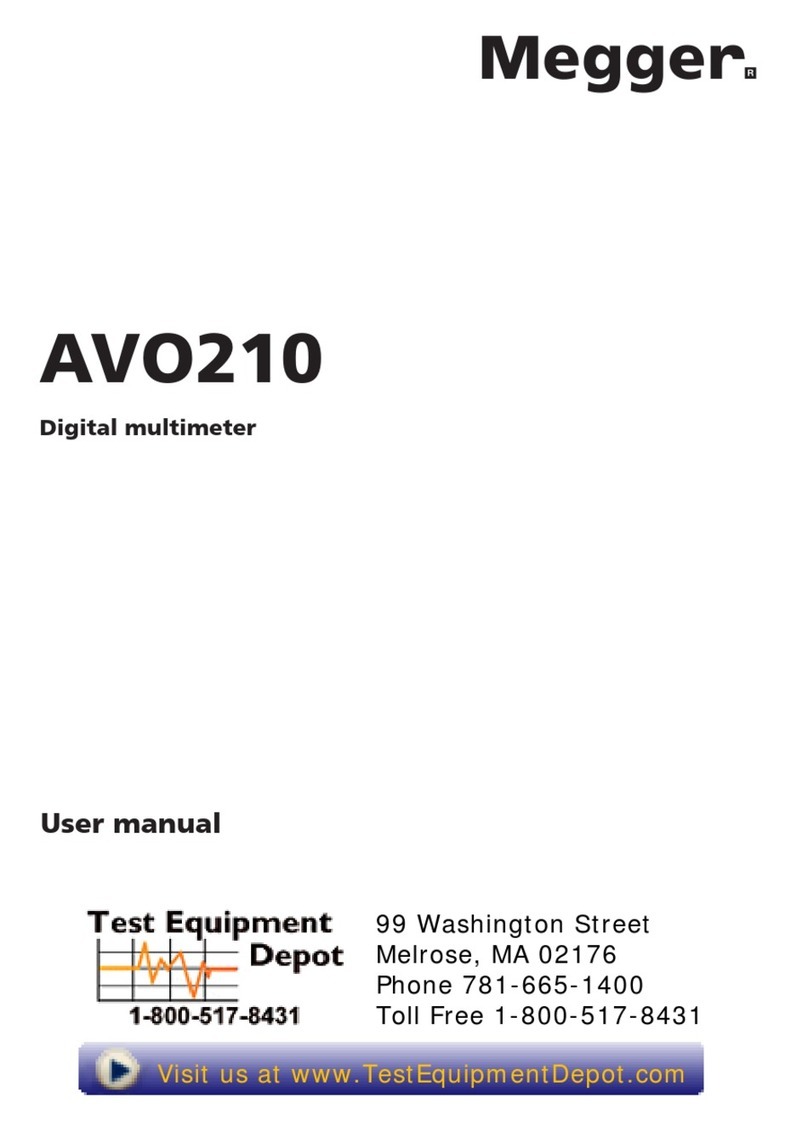
Megger
Megger AVO210 User manual