Monitor FCX Manual

1www.monitorproducts.com
Fully Condensing Oil Fired Heating System Efficiency, Up to 95% efficient
MONITOR PRODUCTS, INC.
www.monitorproducts.com
MONITOR FCX
INSTALLATION AND SERVICE MANUAL
As part of its policy of continuous product improvement,
Monitor Products, Inc. reserves the right to make changes without notice
Revised7/07
“The availability of these manuals and instructions is not to be construed or interpreted as MPI’s approval, consent, or
authorizationforany third partytoinstall,repair,oradviseon any actions taken on or with the MPIproductsdescribedtherein.”
PARTNO.1130COPYRIGHT©2007MONITORPRODUCTS,INC

2
FCX INSTALLATION AND SERVICE MANUAL
FCX INSTALLATION AND SERVICE MANUAL
TABLE OF CONTENTS
I. INTRODUCTION
1 - PRODUCT DESCRIPTION
Model FCX oil fired heating system utilizes a sealed combustion
systemthatoperates at a temperature at which the flue products
willcondense.Howmuchtheunitcondensesdependsonreturn
watertemperatures.Thelowerthetemperaturethemoretheunit
condenses and the high the efficiency. The flue products
temperature is so low that the unit is suitable for use with PVC
intake / Polypropylene exhaust flue pipes, which are offered as
standardoptionsforinstallation.TheFCXisapprovedforinstallation
with zero clearance to combustible materials by Intertek Testing
Services to the UL Standard for Oil Fired Storage Tank Water
Heaters(UL 732).
The FCX is completely assembled and provides standard parts
as follows:
• An enameled steel cabinet with thick insulation
• A completely unitized, thick shelled heating system with
combustion chamber and a heat exchanger with a system of
removablebaffles
• A stainless steel condenser, with condensate drain
• A high efficiency, low emission, gun type oil burner with
combustion air fan, integral oil pump, oil heater and primary
control
• A control panel assembly and all electrical controls for
operation of the heating system, including a water
temperature thermometer in circuit 1
• Amanualwater-mixingvalvethatcan bemotorized ifdesired
• Asafetypressurereliefvalve
• An expansion tank
• A water circulating pump
• Completeinternalwaterpiping terminatinginconnectionsfor
two independent water heating circuits.
• Complete internal air piping terminating in a connection to a
coaxial flue/combustion air intake system.
Front
View
Side
View
Rear
View
I-INTRODUCTION ..............................................................2
1-PRODUCTDESCRIPTION ...........................................2
2-DESIGNATIONOFCOMPONENTS.............................3
3-HEATING SYSTEM OPERATION ................................3
4-PRODUCTSTANDARDRATINGS. ..............................4
5-DIAMETEROF PIPE CONNECTIONS.........................4
II - INSTALLATION.............................................................4
1-OPENING THE UNIT .................................................4
2-LOCATION OFTHE UNIT ..........................................4
3- FLUECONNECTIONSANDROUTING ......................5
4-ALTERNATIVEFLUECONNECTIONS .......................8
5- CONDENSATEDRAINCONNECTION.....................10
6- WATER CIRCUITCONNECTIONS...........................10
7- ELECTRICALCONNECTIONS ................................13
8- FUELOILSUPPLYCONNECTIONS .......................13
III - START-UPAND OPERATION ....................................13
1- PRE-STARTFINALSYSTEM CHECK.....................13
2-START-UPANDOPERATION ..................................13
3-ADJUSTINGTHEOILBURNER...............................14
4- CHECKING THE SAFETY DEVICES ......................14
IV - MAINTENANCE .........................................................14
1- CLEANING THE SYSTEMSHELL ..........................15
2-CLEANINGTHECONDENSER ...............................15
3-BURNER MAINTENANCE .......................................15
4-ADDITIONALCOMPONENTMAINTENANCE ........ 15
5-EXPANSIONTANK PRE-INFLATIONPRESSURE.
CHECK .........................................................................15
6-COMBUSTION PRODUCT FLUE.............................16
7-CHANGINGATHERMOSTATORTHE ..................
THERMOMETER ...................................................16
V - OPERATING ...............................................................16
VI - MONITOR PRODUCTS, INC. (“MPI”) LIMITED .....
WARRANTIES ...........................................................17
VI - FCX PARTS BREAKDOWN. .....................................18
VIII - HEAT WISE BURNER ..............................................21
1-BURNERWARRANTY ............................................21
2-OPERATINGINSTRUCTIONS .................................22
3-SERVICINGTHE BURNER .....................................24
4-WIRINGDIAGRAM..................................................26
5 - PARTS BREAKDOWN ............................................28
6-HONEYWELLCONTROLS......................................30
7- SUNTEC PUMP ......................................................44
8-BS INDIRECTSTORAGETANK ..............................45
Standardoptions available from Monitor include:
• Coaxial balanced flue system components for connection to
theheatingsystemtoprovideventingoftheflueproductsand
combustion air intake.

3www.monitorproducts.com
Rear View
INTRODUCTION
Front View
2 - DESIGNATION OF COMPONENTS 1) Control Panel
2) Control Panel Cover
3) Safety Pressure Relief
Valve
4) Condenser
5) Manual Mixing Valve
6) Combustion Product
Pressure Test Point
7) Condenser Inspection Port
8) Condensate Drain
View from above
9) Drain Cock
10)Burner Air Inlet Pipe
11)Oil Burner
12)Safety Light and Reset Button
13)SightGlass
14)HeatingSystemShell
15)Pockets for Water Overheating
Safety and Thermostat Bulbs
Thermostat
16)Heating Output Sensor
17)Bleed Connection
18)First Circuit Heating Output
19)SecondCircuit heating output
20)Combustion Products Flue
21)First Circuit Heating Return
22)Second Circuit Heating Return
23)Well for Combustion Product
Overheating Thermostat Bulb
24)Protection Plate for Electrical
Connections Box
25)Circulating pump
26)Expansion vessel
3 - HEATING SYSTEM OPERATION
Circuit
heating
return 1or 2
2nd circuit
heating
output
Combustion air is drawn into the oil
burner by the burner fan through the
air intake hose connected to the
coaxial flue/combustion air intake/
exhaust separator. Heated air from
combustionof the oil burnercools as it
passesthroughtheheatingsystemheat
exchanger, then the secondary heat exchanger
condenser.Cooledflueproductsexittheunitthrough
thecenteroftheflue/combustionairseparator tube
assembly. Condensate from the flue products is
drained from the bottom of the condenser into the
condensatedrain tube, exitingthe unit throughthe
condensatedrain system.
Wateriscirculatedthrough the heating system heat
exchangerand condensercircuitswhereit isheated
bythecombustionoftheoilburner.Twoindependent
water-heatingcircuitscanbe connected to the unit:
• The first circuit passes through a three way
mixing valve incorporated into the heating
system. This valve can either be used manually
as supplied or driven by a motorized controller
(option).
• The second circuit can supply another heating
circuit and/or a domestic hot water indirect
storage tank such as BS DHW tanks.

4
FCX INSTALLATION AND SERVICE MANUAL
INTRODUCTION - INSTALLATION
II. INSTALLATION
4 - PRODUCT STANDARD RATINGS
Ratings for Model FCX are provided in the following table:
Performance Product
Parameter Units Rating
Rated Input BTUH 81,250
Rated Output BTUH 76,000
Combustion Chamber Length Inches 8.98
Combustion Chamber Diameter Inches 11.5
Combustion Chamber Volume Cu. Inches 915
Combustion Prod. Circuit Volume Cu. Inches 3051
Flue Pressure Drop Inches H2O 0.10
Max Heating Service Pressure Psig 43.5
Max Heating circuit water temp Deg. F 176
Water Overheating Safety
Thermostat Setting Deg. F 230
Combustion Prod. Overheating
Safety Thermostat Setting Deg. F 248
Heating Circuit Water Capacity Gallons 4.23
Primary Water Flow Rate
(60/80 deg. C) Gal/hr 254
Water Pressure Drop
(at nominal flow rate) MCE 1.4
PowerAbsorbed(withburner,
without circulator) KW 0.2
Packaged Weight Lb. 267
Ratingsarefor the heatingsystem when connectedtostandard
option coaxial flue system components.
Electrical Power Supply 115 volts, single phase, 60 Hz
Full Load Current 2.0 Amps FLA
Max Fuse/ Circuit Breaker Size 15 Amps
5 - DIAMETER OF PIPE CONNECTIONS
Connection Diameter Units
Combustion Products 3.15 / 4.92 Inch
Water Heating Supply/Return 1 Inch
Domestic Hot Water or
Second Heating Circuit 1 Inch
Condensate Drain 1 -1/2 Inch
Heating Water Drain 1/2 Inch
Air Bleed 3/8 Inch
Safety Pressure Relief Valve 3/4 inch
• Remove the control panel
escutcheonmolding (2) by
grasping it on both sides
and pulling it outward
towards you and up. The
escutcheon will come free
of the attachment clips
leaving the control panel
exposed.
1 - OPENING THE UNIT
To open ModelFCX to access forinstallation,and/or service,
•Removethetopcoveroftheunit(A) by lifting the cover at the
front and rear to free the attachment clips, and then simply
liftthe cover straightup and off.
•Removethe front panel attachment screws (P),thenpullthe
frontpanel (J) outward towardsyou at the topto free it from
the attachment clips. Lift the panel up to free it from the
lower attachment pins, and simply lift the panel off.
follow these
steps :
Fig. 4
2 - LOCATION OF THE UNIT
ModelFCXisafreestanding(floormounted)appliancesuitable
for installation on combustible flooring. It is approved for
installation with zero clearance to combustible walls, ceiling,
doors, etc from the cabinet. Standard option coaxial flue
components are suitable for installation with zero clearance
to combustible materials.
These are operating clearances and it is recommended that
additionalclearancesbe considered:
• Sufficientclearanceshouldbe provided in back of the unit to
facilitate installation and maintenance of water, electrical,
flueand condensate drain connectionsand components.
• Sufficientclearanceoverthetopoftheunitshouldbeprovided
toallow the topto be removedfor service.
• Sufficientclearancefrom the front of the unitshouldalsobe
providedto facilitate adjustments and service.
There is no need for additional clearance to either side of the
unit since there is no access to the unit from either side.
Alternative access measures such as doors, removable wall
panels, etc. may be provided if desired.
Choosing the location should also take into account the total
fluelength totheoutdoors(SeeFlue ConnectionandRouting).
Inaddition,thechoice of location should consider the location
of utilities such as electrical supply and sewer access for
condensate drainage. Location and routing of water lines is, of
course,asignificantpartofthechoice.WhileModelFCXcanbe
installed in an enclosure such as a closet, ventilation or other
meansmustbeprovidedsothattheenclosuretemperaturedoes
not exceed 113 deg. F (45 deg. C).

5www.monitorproducts.com
OPERATION
3 - FLUE CONNECTIONS AND ROUTING
Connection of the coaxial flue/combustion air piping system
is in the back of the unit to the separator tube assembly. The
combustion products are vented from the heating system and
condenser through the center of the coaxial tube, while the
combustion air is supplied through the outside ring of the
coaxial tube. Since the FCX is a condensing heating system,
flue products exiting the unit are relatively low temperature,
typically from 120 -212 ° F (49 -100 ° C), and saturated with
humidity. Consequently, an airtight, corrosion resistant flue
systemmust be provided.
Variousstandardoption flue pipingcomponentsand packages
with which to create the flue system are available.
0.98 m Straight Horizontal Flue Kit
Fig. 5
Reference No Length
MPIPart2201(N40.28399) 38.6” (980 mm)
Useful length after assy. - 34.6” (0.88 m)
3 m Angled Horizontal Flue Kit
Fig. 6
Reference No MPIPart2209 (V72.28414)
3 m angled horizontal balanced flue -straight
Fig. 7
Reference only
PP/PVC Concentric Vertical Terminal - For Flat or Sloping
Roof
Fig. 8
Reference No Color Length I.D. O.D.
MPI Part 2206 Black 51.9” 3.15” 4.92”
(1320mm) (80mm) (125mm)
Usefullength under roof flashing -29.5” (0.75 m)
PP/PVC Concentric Horizontal Extension
- joint fitting -
Fig. 9
Reference No Length I.D. O.D.
MPI Part 2202 19.7” 3.15” 4.92”
(N40.28397) (500 mm) (80mm) (125mm)
MPI Part 2203 39.4” 3.15” 4.92”
(N40.28398) (1000 mm) (80mm) (125mm)
Useful length after assy. - 17.7” (0.45 m) or 37.4” (0.95 m)
Roof Flange with Adaptable Coupling
Fig. 10
Reference No Slope Covering type Color
9031 25 - 45 deg Tile/Shingle Red
9032 25 - 45 deg Slate - Shingle Black
Fig. 6 Contains
2 80 mm/1 meter lengths
2elbows
1horizontaltermination
1flexible hose clampand adapter.
NOTE:If the vertical length ismorethen 1 meter a
45 degree concentric elbow, #2204 or 1/2 meter
extension,#2202, canbeused comingoutthe back
of the unit. This kit must be properly supported.

6
FCX INSTALLATION AND SERVICE MANUAL
INSTALLATION
PP/PVC Concentric Elbow
- joint fitting -
Fig. 11
Reference No Bend I.D. O.D.
MPI Part 2204 45 deg 3.15” 4.92”
(N40.28395) (80mm) (125mm)
MPI Part 2205 90 deg 3.15” 4.92”
(N40.28396) (80mm) (125mm)
Fastening collar (option)
Fig. 12
Reference No Number Ø mm
MPI Part 2208 3 125
(B00.29727)
Collars are essential to bear the weight of the vertical
extensionsso that theheatingsystemdoesnot bear theweight,
as well as horizontal runs preventing sagging and pooling of
condensate.
Polypropylene Roof Plate
Fig. 13
Reference No Color
MPI Part 2207 Black
(A90.12172)
45° bend 90° bend
TYPICAL INSTALLATION EXAMPLES:
Theflue/combustion airsystempipingmay be eitherhorizontal
orvertical or a combinationofboth, observing the following:
• Themaximumunrestrictedhorizontalorverticalflue length
shall not be more than 16.4 ft (5 m), if using the HeatWise
burner.
• Foreach90-degree elbow used in the flue system, subtract
3.28 ft (1m) from the total allowable length.
• For each 45-degree elbow used in the flue systems,
subtract 1.64 ft (0.5m) from the total allowable length.
• Horizontalruns of the fluesystem must pitch back3/4 inch
peryard (2 cm per m) of length towards the heatingsystem
toensureproper flue products condensate drainage.
• Termination of a horizontal flue system shall not be less
than 2 ft above grade or 1 ft above average snow level as
shown in fig. 15 and 16 or as dictated by local codes.
• Do not place the flue terminal less than 6.56 ft. (2 m) from
aventilationholeoropeninginabuilding.NOTE:Thisisan
importantconciderationifunitis used year round (domestic
hotwater production) where windows maybe open.
• Terminationofaverticalflue must provide atleast12inches
(30cm) above the roof jack to the combustion air intake
collar.
• If there are two units in the installation with vertical flue
systems,theterminationofthesystemsmustbeseparated
by 24 inches (60cm).
Fig. 14
Allflue-pipingcomponents must be assembled and supported
to provide an airtight flue/ combustion air system.
Application of liquid soap over the flue pipes to be joined will
aid in assembly of the parts.
Typical installation examples appear in the illustration that
follow.
Straight Balanced Flue Configuration
Fig. 15
Option: Straight Horizontal Flue Kit
2ft minimum

7www.monitorproducts.com
INSTALLATION
Fig. 17
Options:
CondensateTee
Concentric extensions
1 concentric vertical terminal
1 sleeve tile roof flange
1roof plate
Adjustablesupports as needed
max L = L1 + 3.28 ft (1m) < 16.4 ft (5m)_
Fig. 18
Options:
CondensateTee
3 Concentric extensions
2 45 deg concentric elbows
1 concentric vertical terminal
1 sleeve tile roof flange
1roof plate
Adjustablesupports as needed
_
Fig. 19
Options:
1 45 deg concentric elbow
CondensateTee
Concentric extensions
1 concentric vertical terminal
1 sleeve tile roof flange
1 roof plate
max L = L1 + 1.64 ft (0.5 m) + 3.28 ft (1m) < 16.4 ft (5m)_
Note: Use fastening collars as needed. Support leg can consist of a fastening collar attached to a support such as a 2X6 joist.
Angled Balanced Flue Configuration
Fig. 16
Option:Angled Horizontal Flue Kit
max L = L1 + 1.64 ft (0.5m) + L2 + 1.64 ft (0.5m) + L3 +
3.28 ft (1m) < 16.4 ft (5m)
condensate tee
To provide
clearance
around water
connections a
45 degree
elbow can be
used.
To provide clearance
around water
connections a 1/2
meter concentric
extension can be
used
1ft minimum
above max.
snow level
IMPORTANT: Total
lengths longer then 6 ft
(2 meters) should use a
concentric condensate
Tee, #2255, instead of the
concentric 90° elbow to
eliminate condensate
before draining back to
the unit. Condensate tee
must drain properly. It
can be tied into conden-
sate drain of the unit.
Use Condensate Tee
for lengths over 6ft

8
FCX INSTALLATION AND SERVICE MANUAL
INSTALLATION
4 -ALTERNATIVE FLUE CONNECTIONS
All combustion appliances consume a quantity of air
proportionaltotheircapacity.If unit is installed using inside
make up air, ventilation louvers must be installed in
confined areas according to code. Toavoid corrosion, the
combustion air must not contain any harmful agents.
Halogenated hydrocarbons, containing combinations of
chlorine or fluorine that are found in solvents, paints, glues,
propellants,household cleaning products,etc.
TheFCXheatingsystem is acondensing heatingsystem,which
means that the combustion products from the appliance are
discharged at low temperature(120° to 212°F) and saturated
with humidity. Consequently, an airtight, corrosion-resistant
fluesystem must be provided.It is possible touse an existing
flueas long as it is lined. Thelining must beinserted so that it
doesnot retain any condensateandso that any condensates
are transferred to a drain located at the foot of the flue or
directly back to the heating system condensate trap. The
materialfor the lining must bechosen specifically for use with
a condensing heating system. Suitable materials certified for
use in such combustion product systems are 904 L stainless
steel,PPSpolypropylene, and PVDF.Specializedcompanies
market these systems and indicate the tubing assembly
proceduresto be applied.
Some flue components available from Monitor Products are
as follows:
Flue Connection Adapter -
Adapterisa4.33to3.15inch(110to80mm)offcenterreducer.
Fig. 22
Reference No 9103
Rigid Polypropylene Tubes
Fig. 23
Reference No Length inch (m) Ø inch (mm)
2256 39.37(1) 3.15 (80)
9049 39.37(1) 4.33(110)
9102
78.7 (2) 4.33(110)
Polypropylene Elbows
Fig. 24
Reference No Type Elbow Ø inch (mm)
2259 90° 3.15(80)
9048 90° 4.33(110)
Leaf Guard
Fig. 25
Reference No
2210 4.33”(110)
Should be used on the end of 110 mm piping run
Fig. 27
Roofevacuation above the ridge
Flue components:
Flueconnection kit withoff-center reducer (item1)
4.33in (110mm) polypropylene tube, 1m long (item 3),
4.33 in (110mm) polypropylene tube, 2m long (item 4),
4.33 in (110mm) 90° polypropylene elbow, (item 5)
L1 < 32.8 ft (10m)
Note:
•With this arrangement, the burner air inlet hose (10) is
disconnected from the burner. The burner draws air directly
intothe unit from the premises in whichtheheatingsystem is
installed. Combustion air must be supplied to the premises
withavent(11)or alternativemeans.Condensatedrainsdown
the inside of the flue into the heat exchanger and out the
condensate drain tube.
•If you must deflect the flue system, use 45° degree elbows.
Use45degreeelbowsinsteadof90°tolessenfluerestrictions.
Use Condensate Tee
_
Rigid tubes can be run inside
a building, or inside an existing
negative pressure conduit.

9www.monitorproducts.com
INSTALLATION
PPtl/PVC Condensate Tee-Joint
- joint fitting -
Fig. 28
Reference No Length I.D. O.D.
2255 10” 3.15” 4.92”
Length does not include drain spicket
Useful length after assy. 2”
PPtl/PVC Parallel Concentric Adapter (Male/Top)
- joint fitting -
Fig. 29
Reference No Length I.D. O.D.
2253 3.5” 3.15” 4.92”
PPtl/PVC Parallel Concentric Adapter (Female/Bottom)
- joint fitting -
Fig. 30
Reference No Length I.D. O.D.
2254 7” 3.15” 4.92”
45 degree Polypropylene Elbows
Fig. 31
Reference No Type Elbow Diameter
2258 45 degree 3.15”/80mm
2260 45 degree 4.33”/110mm
Typical Installation examples
Fig. 32
Options:
1 90 deg concentric
condensateT#2255
Rigidtube extentions # 2256
1concentric vertical terminal #2206
1sleevetile roof flange
#9031⍈
1roofplate#2207
1adjustable support #2208
1parallel concentric adapter
#2253 (male top)
1parallel concentric
adapter#2254
(femalebottom)
Note: This is using the
BeckettNXBurner
Max L1= 32LF
Each 90* = 3.28lf
Each 45* = 1.64lf
LongerVenting Options:
Longer exhaust lengths can be achieved by using a Beckett
NX burner specifically modified and set up for use with the
FCX. When using the Beckett NX burner the maximum
unrestrictedhorizontal or vertical fluelengthshall be no more
then 36 feet if using an 80mm parallel piping system with
PPTL/PVC parallel concentric adapters on each end, or no
more then 30 feet if using concentric PPTL/PVC end to end.
Thesubtractionof3.28 feet for 90 degree elbows and1.6feet
for 45 degree elbows still applies and must be taken into
account when figuring what the overall length is. It is
recommended that the Heatwise burner be used on overall
lengths of less then 16.4 feet and the Beckett be used on
lengths of 15 to a maximum of 36 feet.
TheBeckettNXburner adapted for use on the FCXmusthave
thefollowing specifications:
The oil line heater is standard with the burner.
The oil pressure is set to (150-155) PSI.
Theoil nozzle used is a Danfoss .5-60 degree-AH.
NOTE:Donotuseanylargersizeorsupply nozzle with higher
pressure
Combustion readings should be CO 11 - 12.5, smoke 0 - .5

10
FCX INSTALLATION AND SERVICE MANUAL
6 - WATER CIRCUIT CONNECTIONS
Water circuit connections are made in the back of the unit
utilizing the four 1" male pipe thread couplings provided or
usingother adapters provided. The FCXcanbe connected to
variouscomfort heatingwatersystemsas wellasto adomestic
hotwater heating system if desired, observing that:
•Watercirculatingpumpsprovidedinthevariouscircuits must
belarge enough foreach circuit includingthe pressure drop
of the heating system/condenser in the unit. For optimum
soundleveland power consumption, set thecirculatorto the
speed that is appropriate for the installation flow rate and
pressuredrop.
•Isolationvalvesmaybeused inthevariouscircuitstofacilitate
heating system maintenance without having to completely
drain each circuit. NEVERplace an isolationvalve between
apressure relief deviceand a watertank.
•Thewaterpressuregauge(notsupplied)hastobefittedoutside
theunit.
INSTALLATION
TheFCXcomesequippedwiththefollowingstandardequipment:
1)8LexpansionTank(Approx.2.11 USGallonwithacceptance
value of approx. 0.9 gallons) Please refer to expansion tank
manufacturerstablestodeterminetanksthatmeetyoursystems
requirements. Someradiantsystemsmayrequirespecialtanks
tomeettubingoxygenrequirements.
2) Grundfos UPS1542 Circulator. (see Fig. 35 on page 11 for
pump capacities.) Additional pumps or a primary secondary
system may need to be set up to meet individual system
requirements
3)Safetyreliefvalve. Mustbepipedawayfromheating system
aspercodeusingrigidpipethatisthesamediameteroftherelief
valveoutletapprovedforthetemperatureofthesystem. Discharge
pipemustnotcauseahazardor apotentialcause ofdamageto
equipmernt.
CAUTION:
Ifthepressurereliefvalveisnotpipeddownanditopens,damage
can occur to the burner.
Fig. 34
1.expansiontank
2.circulatingpump
3.safetypressurereliefvalve
Note: Installed expansion tank is good for up to 25 gallons of
systemwater.Anadditionalexpansiontankisrequiredformore
than 25 gallons. Size accordingly.
5 - CONDENSATE DRAIN CONNECTION
Connection of the condensate drain piping system is to the
condensatedrain tube in therear of the unit beneath the flue/
combustionairseparatortubeassembly.The condensatedrain
tube provided in the unit is 1-19/32 inches (40 mm) outside
diameter over which standard 1-1/2 inch trade size schedule
40 PVC pipe can be connected to begin the rest of the drain
system. A trap must be provided to prevent leakage of
combustion products into the drain. The drain system must
pitch downward towards the sewer.
Note: The condensate will not likely require any specific water
treatmentbecauseofcondensatedilutionbynormalwastewater
use.If,however,localregulationsrequirewastewater tohavea
neutralpH condensatetreatmenttankcanbeinstalledbetween
the trap and the sewer. PH level must be neutralized before
entering a septic tank or cesspool.
Fig. 33
NOTE:Makethetrapaccessibleandremovableforcleaningand
donotdownsizethecondensatedraintubeuntilafterthetrap,if
necessary.Ifusingacondensatepumpchooseapumpthatcan
holduptothecorrosiveeffectsofthecondensate.

11 www.monitorproducts.com
INSTALLATION
C1 C Heatingsystem
M Pressure gauge
C1 = Radiator circuit,
Baseboards,Radiant Panels
or Fancoils
VM1 1st circuit mixer valve
Dc1 1st circuit heating outlet
Rc1 1st circuit heating return
C1 C Heating system
M Pressure gauge
C1 = Radiator circuit,
Baseboards,Radiant Panels
or Fancoils
VM1 1st circuit mixer valve
Dc1 1st circuit heating outlet
Rc1 1st circuit heating return
C3 = Domestic hot water
preparation circuit
P3 Domestic hot water pump
C3 B Domestic hot water
production system
Ss Domestic hot water sensor
C Heatingsystem
M Pressure gauge
Low Temp
C1 = Radiator circuit
C1 VM1 1st circuit mixer valve
Dc1 1st circuit heating output
Rc1 1st circuit heating return
C2 = Underfloor heating circuit
C2 P2 2nd circuit heating circulator
VM2 2nd circuit mixer valve
Dc2 2nd circuit heating output
Rc2 2nd circuit heating return
Sd Heating output sensor
Connection to a heating circuit with
a domestic hot water production
system
Connection to a double heating circuit
Fig. 37
Various typical water circuits are
illustrated below :
Connection to a single heating circuit
Fig. 35
Connection to a double
heating circuit with a
domestic hot water
production system
C Heatingsystem
M Pressure gauge
C1 C1 = Radiator circuit
VM1 1st circuit mixer valve
Dc1 1st circuit heating output
Rc1 1st circuit heating return
C2 C2 = Underfloor heating circuit
P2 2nd circuit heating circulator
VM2 2nd circuit mixer valve
Dc2 2nd circuit heating output
Rc2 2nd circuit heating return
Sd Heating output sensor
C3 = Domestic hot water production circuit
C3 P3 Domestic hot water pump
B Domestic hot water production system
Ss Domestic hot water sensor
Fig. 36
Fig. 38
Note: If the radiator circuit is high temperature baseboard then the connections at the heating system should be reversed with
the baseboard loop using the DC2 circuit and circulator and the underfloor loop using the DC1 circuit which eliminates the need
for VM2 since DC1 has one built in. This applies to figs 37 and 38.

12
FCX INSTALLATION AND SERVICE MANUAL
INSTALLATION
6.1 - CIRCULATING PUMP CHARACTERISTICS
Fig. 39
7 - ELECTRICAL CONNECTIONS
WARNING - ELECTRICAL SHOCK HAZARD!
DISCONNECT THE POWER SUPPLY
BEFORE ATTEMPTING ELECTRICAL
INSTALLATION OF THE UNIT.
Electrical power and control connections are made to pigtail
leadsthatexitthrough holes in the right rear oftheunit(facing
the front of the unit).
The power connections must be made in a Listed junction
Total Head in Feet
Capacity in U.S. GPM
HP range 1/25, 1/12, 1/6
Fluid temp 230°F Maximum
50°F Minimum
Flow Range 10-46 GPM
box that is not provided with the unit. All wiring should
conform to the National Electrical Code and any applicable
local codes and standards. To minimize the likelihood of a
heating system shutdown caused by an unrelated electrical
circuit fault, the unit and any related electrical components
should be connected to a separate branch circuit specifically
dedicated for that purpose.
The control circuit connections can be in-air splices made to
pigtail leads provided. Control circuit connections are NEC
Class2,intended for connection to a typicalroomthermostat.
Fig. 40
LEGEND
L: Phase
N: Neutral
M/A: On/Off switch
E/H: Summer/Winter switch
TSE: Overheat safety cutout aquestat
TRC: Adjustable thermostat
TSF: Flue gas safety cutout thermostat
V1: On light
V2: Burner safety shutdown light
C: Burner connector
F: Fuse (6,3 A)
R: Relay
T: Main transformer 120/24 volts
CC: Circulating pump
Notes:
A. Electric power leads factory provided at
right rear of unit. Permanently field splice
120-1-60fieldprovidedpowercircuitleads
in NEC junction box.
B. Control circuit leads factory provided at
rightrearof the unit are 24volt,NEC class
2 for connection to a room thermostat.
C.Do not use the internal transformer to
power any external system components
such as a zone valve.

13 www.monitorproducts.com
INSTALLATION - START UP AND OPERATION
1) Junction box
2) Main Power Pigtail Leads
3) Unit Upper Back Panel
4) Control circuit Pigtail Leads
8 - FUEL OILSUPPLY CONNECTIONS
The buner supplied with the unit is connected to the heating
system.Lines are terminatedwith3/8-inchreverse flarefittings
for connection of the supply from the fuel oil tank. When
connecting the line, a 10-micron spinon type oil filter must be
installedin theoilsupply linetominimizeburner contamination.
UPPER LEFT REAR CORNER OF UNIT (Facing rear of
unit)
Fig. 41
Therearethree 7/8" holes in therightrear of the unit. Mount a
Listed2 x 4inch, “HandiBox” type junction box vertically over
the lower left hole (facing the rear of the unit) in such manner
that the lower right hole is open. When installing the junction
box,centertheboxverticallyoverthe hole by using the center
knockout in the box. Install a 1/2-inch trade size cable
connector or insulating bushing through the hole in the unit
and through the knockout in the box. Secure the box with
screwsas required.
Route the factory supplied main power pigtail leads through
the connector into the junction box from inside the unit and
secure the connector clamp on the wires. Install a second
cable or conduit connector in another knockout in the box for
thepowerwiring system as required. Connectthepowerwires
andgroundingconductors to the pigtail leadsinthe box using
Listed wire connectors and install a cover.
Routethe factory supplied control circuitpigtailleads through
the lower right hole from inside the unit. Connect the room
thermostatwires to thecon-circuitpigtailleadsusing a suitable
Class2 wiring connection method.
III. START UP AND OPERATION
1 - PRE-START FINAL SYSTEM CHECK
Beforestartingnormaloperation oftheheatingsystem,perform
thefollowing final installation procedures:
• Leak-checktheflue/combustionairsystem to minimize the
likelihoodofleakage.
• Leak-check the entire water system, repairing any leaks
that may be found.
• Fill the entire water system with water, treated as desired
for the application, including anti-freeze solution if
appropriate. Open any shut-off valves in the system
• Fill the condensate drain trap with water
• Leak-check the fuel oil supply system and open any fuel
shut-off valves.
• Recheck the power and control circuit connections THEN
replace all cabinet access panels
• Energize the electrical power circuit to the unit.
2 - START-UP AND OPERATION
Aftercompleting thepre-startfinal system checks, the system
can be started and run through start-up checks and
adjustments as required.
1) Start/Stop Switch
2) Summer/Winter Switch
Circulator control inside the heating system
3) Heating System Temperature Control Thermostat
HeatingSystem Temperature adjusted between 140 -176
deg. F (60 - 80C)
4) Water Outlet Temperature Thermometer (Circuit 1)
5) Water Overheating Safety Thermostat
BurnerCutout
6) Combustion Product Overheating Safety Thermostat
HeatingSystemShutdown
7) Burner Safety Device Light
8) Slot for Additional Control
Note: overheat thermostats may not physically pop up if
tripped. Press the red center with a pointy object such
as a pen and listen for an audible click.
Fig. 42

14
FCX INSTALLATION AND SERVICE MANUAL
START UP AND OPERATION - MAINTENANCE
Tostartthe heatingsystem,firstmakesuretheroomthermostat
is set at a high enough temperature to be closed so that any
externalwatercirculating pumps are running. Turntheheating
systemOn-offswitchtothe“ON”position,andsettheHeating
System Temperature Control thermostat to its maximum
temperaturesetting.
Turn the Summer-winter switch to “WINTER”. This will start
the internal circulating pump.After the start time delay set on
the oil burner (for the oil heater) has expired, the burner will
start. Reduce the Heating System Temperature Control
thermostat setting to make sure the heating system stops
properlywhen controlledbythatthermostat. Increasetheroom
temperaturethermostatsettingto makesurethatthecirculating
pump(s)stopproperly.
3 - ADJUSTING THE OIL BURNER
Whilethe oil burnerleavesthefactoryset at therecommended
settings, safe operation requires that the burner be checked
and adjusted by a qualified, licensed if required, oil service
technician using properly calibrated combustion test
equipment, vacuum and pressure gages.Run the unit long
enough at the burner maximum firing rate to make sure the
burnerhas reached a stablemaximumoperatingtemperature.
THEN, check the burner and adjust as follows:
Check to determine that the smoke spot number does not
exceed 0.5 with a Bacharach or equipment tester control.
Adjust the burner as required to be below this maximum.
Checktodeterminethatthe CO2 rate is from 11.5 - 13 percent
andthatthereisnoCOproduction.Adjusttheburnerasrequired
to achieve this operating characteristic.
Measure the temperature of the flue gas exiting the unit to
determine that it does not exceed 250 degrees F (120 C).
Combustioninspection can be carriedouton the unit through
the hole (item N) provided in the inspection port (item 7). Be
sure to replace the washer (item M) and the test point screw
(item6) properly after inspection.
4 - CHECKING THE SAFETY DEVICES
At the time of start-up, check the safety and control devices
as follows:
Thermostats:
• Check to see that the thermostat bulbs are correctly
positioned in their housings. This is essential to provide
temperature sensing to facilitate burner shutdown in the
event of overheating,
Flame monitoring:
• Check to make sure that the burner shuts down properly
upon the deactivation or disconnection of the flame
monitoring device or interruption of the flow of fuel,
Safety Pressure Relief valve:
• Checkthe safety pressure relief valvein the heating circuit
for proper operation.
Factory Settings for the Burner
Burner PIONEER - 1
Oil pump pressure psig 165-170
Nozzle 0.50 80° AS
FiringHeadAdjustment 1.75
Air shutterAdjustment 6-8
Fig. 43
IV. MAINTENANCE
Itisrecommend that the heating systemandflue/combustion
airsystem beinspectedandmaintainedannuallybya qualified
technician.
DISCONNECT ALL ELECTRICAL CIRCUITS
BEFORE SERVICING THE UNIT CLOSE ANY
ISOLATION VALVES THAT MAY BE IN THE
WATER SYSTEM SHUT OFF THE FUEL OIL
SUPPLY IF SERVICING THE BURNER
To gain access to the inside of the unit, first remove the
control panel cover by grasping it on both sides and pulling
directlyoutwardtowards you and up. Remove any frontpanel
screw(s) and remove the front panel by pulling the top out
towards you and then lifting up to free the bottom from the
mounting pins. Remove the top cover by simply pulling it
up. Remove the electrical terminal block protection plate by
removing the screws in the rear and lifting. Remove the
control panel cover screws and remove the control panel
cover. The water can be bled from the unit by opening the
drain-cock on the base of the heating system shell using the
valvecapsasthevalvehandle.
For more detailed burner instructions refer to the Heatwise or the Beckett
NX burner manual

15 www.monitorproducts.com
MAINTENANCE
1 - CLEANING THE HEATING SYSTEM SHELL
• Remove the screws (B) from the cast-iron heating system
shellcover(C)
• Remove the flue outlet baffle (D)
Note:If vacuuming becareful not todamage insulator, check
for deterrieration and replace if needed
• Remove the combustion baffles (E) clean, inspect and
replaceifdeteriorated
• Clean the inner walls of the heating system shell, remove
anydebriethatmayhavefallento thebottomofthechamber
• Reassemble all the parts the way they were removed,
positioning the flue outlet (D) with its centering screw (P)
towardsthe frontofthe heating system, thenpositioningthe
heating system shell cover (C) arrow marker opposite the
centeringscrew(P)
• Replace the screws (B) in the heating system shell cover.
Fig. 44
2- CLEANING THE CONDENSER
• Remove the wing nut (F) from the condenser top cover
(G) and remove the cover
• Remove the condenser access plug (7)
• Clean the condenser tubes (H) using a bottle brush or
similar tool
• Pour tap water through the condenser tubs to ensure
combustion products can flow freely
• Visually inspect vent house tee at condenser outlet for
integrity
• Replace the condenser access plug (7) and the top cover
(G), making sure that the seal (I) is properly positioned
when replacing the cover
• Make sure that the seal (I) on the cover and the access
plug is in good condition.
• Inspect and clean the condensate trap(external)
NOTE: If after cleaning the condenser, the temperature of
the flue gasses still exceeds 250°F, perform a burner check.
Fig. 41
3- BURNERMAINTENANCE
Onceadjustedproperly, regular maintenance oftheoilburner
is not generally required.Aroutine examination of the burner
shouldinclude examination ofthe burner fanand housing for
dirtand the sparkelectrodesforproper clearances.Thenozzle
shouldbe replaced after every1000 gallons of fuel used,due
to wear. Replace the fuel filter if necessary. Cleaning and
adjustmentisalwaysappropriateduringperiodicinspection.If
burnerfiring rate adjustment is required,follow instructions in
“Adjusting the Oil Burner”.
ALWAYS CHECK FOR ANDCORRECTANY FUELLEAKS
4- ADDITIONAL COMPONENT MAINTENANCE
Check to see that the safety and regulation devices (safety
reliefvalve,air bleed valve, control box components,etc.)are
operating properly. Check that the condensate drain trap is
clean. If necessary, remove the bottom of the trap, clean it,
replace it and then refill the trap it with water. Also check to
see that neither the installation nor the heating system have
any water or fuel leaks (leaks may produce a risk for safety
andshortenthe life-span). If it becomesfrequentlynecessary
to add water to maintain pressure in the installation, even
thoughnoleakshavebeendiscovered, perform an expansion
tank check or if the pressure releif valve drips or pops
occasionally.
5- EXPANSION TANKPRE-INFLATION PRESSURECHECK
Reducethepressureintheheatinginstallationbyopeningthe
draincockorthe safety valve until the pressure gauge reading
is less than 7 - 8 psig (0.5 bar)
Check the pressure in the expansion tank and if necessary
bringitbackup to pressure. Replace the tank if the membrane
ispunctured(water present in the inflatingvalve)
To optimize the efficiency of the expansion tank:
• Adjustits pre-inflation pressure in line with theinstallation.
The pressure must correspond to the static height of the
installation(H), the height betweenthe highest point ofthe
installation and the expansion tank, as expressed in psi
where 2.41Ft in height = 1 psi
• Adjustthefillingpressure oftheinstallationtoavaluegreater
than 3 psi (0.2 bar) above the pre-inflation pressure of the
tank after totally bleeding any air from the installation.
Water inlet
Dilated
water
volume
Pressure
rises as
the air is
compressed
Max
vessel
volume
Membrane
Inflating
valve
H

16
FCX INSTALLATION AND SERVICE MANUAL
MAINTENANCE - OPERATING FAULTS
V. OPERATING FAULTS
Fig. 42
6 - COMBUSTION PRODUCT FLUE
Examine the flue/combustion air system for leaks and
obstructions. Leaks can generally be detected by the
appearanceof condensate stains ontheoutside of the pipes.
Replaceany damagedsealsifnecessary.Theflue/combustion
air pipe can be cleaned with running water, if necessary,
providing that the water flow is not too great to be drained
throughthecondensate drain system. Leavetheexcesswater
in the condensate trap when cleaning is completed.
7 - CHANGINGA THERMOSTAT OR THE THERMOMETER
Replacementof the thermostatsor the thermometer requires
removal of the bulb from its location and the control from the
control box.
• Thebulb fortheHeatingSystemTemperatureThermometer
is located on the first circuit heating output tube. Remove
the bulb from the tube, remove the thermometer mounting
screws in the control box and remove the thermometer.
Replace the thermometer with another, routing the bulb
capillary the same way as the original, replacing the bulb
on the tube properly and as securely as possible.
• The bulbs for the Heating System Temperature Control
Thermostatandthe Water Overheating Safety Thermostat
areboth locatedinpocketson thesideof theheatingsystem
shell. To change either, remove the bulb from the pocket,
removethe thermostat mounting screwsin the control box
and remove the thermostat. Replace the thermostat with
another, routing the bulb capillary the same way as the
original, replacing the bulb properly into the pocket as far
as possible.
• The bulb for the Combustion Product Overheating
Thermostat is located in a well provided in the condenser
access plug/inspection port. Remove the combustion test
point plug and washer from the inspection port to free the
thermostatbulb,andremovethebulbfrom thewell.Remove
the thermostat mounting screws in the control box and
removethethermostat.Replacethethermostatwithanother,
routingthe bulb capillarythe same way as the original and
replacingthe bulb properly into the well as far as possible.
Replace the combustion test point plug and washer in the
inspection port, securing the bulb in place.
Fig. 43
During the course of seemingly normal operation, there may
be operating faults experienced in the system. Some of the
more common faults that may be encountered are:
BURNERFAULTSHUT-DOWN
Theburner may shutdownforany ofseveralreasons,atwhich
point the burner safety device light (red) on the control panel
will be ON and the there will be a green fault indicator light lit
ontheoilburner. This may be caused by a loss offueloil(tank
empty?), a fouled oil spray nozzle in the burner, or perhaps a
fouledorfaultyflamesensor.Toattemptarestartaftercorrecting
any burner problem and the fuel supply is assured, push the
resetbutton on the burner.The burner shouldrestartafterthe
preset time delay period expires.
OVERHEATINGSAFETYTHERMOSTATSHUT-DOWN
Openingof either theWaterOverheatingSafetyThermostat or
theCombustionProductOverheatingThermostatwillresultin
anoil burnershutdown.Ineither case, theburnersafetydevice
light (red) on the control panel WILL REMAIN OFF, and the
green fault indicator light on the oil burner will REMAIN OFF.
The only way to tell if either device has opened is to check
electrically or check the position of the reset button, located
underthescrew cap over each device.
• TheWater Overheating SafetyThermostat may open if the
water temperature exceeds 230°F (110°C) in the heating
system. This can occur if the water temperature control is
near its maximum setting, and or the three way valve is
drawingitsmajorityofwater outofthesecondarycondenser.
This can be prevented if the water temperature control is
turned to a lower temperature, the three way valve is
readjustedclockwiseortheburnerisrewiredforapostpurge.
Afaultywatertemperaturecontrolcanalsocauseashutdown.
Aftercorrecting any fault, either thermostatmustbe manually
reset by removing the screw cap on top and depressing the
reset button.
Note:Actuationoftheresetbuttonmaynotbe physicallyvisible.
Iftrippedabuttonwillhaveanaudibleclickwhentryingtoreset.
INLINEOILHEATER ORTHERMOSTATSHUTDOWN
The heatwise Pioneer Burner is equipped with an inline oil
heater, thisheatsupandclosesa thermostatfor the burner to
get power. If the heater or the thermostat malfunction (one
complete unit) it will not allow the burner to start. If the fuel is
extremely cold the inline heater may not be able to keep up
and may momentarily shut off the burner until the oil gets
back to a temperature of 125-130° F.
PHONE (732) 329-0900 • FAX (732) 329-0904
MPI offers technical support to qualified licensed heating
contractors during normal business hours. (Monday-Friday
8:30 A.M. to 4:30 P.M. Eastern Time)
To help us serve you properly our technicians will require
the following information:
Nozzle manufacturer, G.P.H., angle and pattern.
Pump pressure in PSI Pump vacuum in inchs of Hg
Head Setting and Air Setting
Oil delivery system: 1 pipe or 2 pipe.
Oil Tank: Indoor, outdoor. Above or below pump level.
Smoke reading CO reading in PPM CO 2 reading in %
Flue Outlet Temperature °F
Water Outlet temperature °F Water Return temperature °F
System load: Radiant, high temperature, DHW. Total BTU
requirement

17 www.monitorproducts.com
First year - MPI warrants that its FCX heating systems are
free from defects in material and workmanship under normal
use and service for 1 year from the date of purchase with an
additional period of up to 3 months if the unit is not installed at
time of purchase.
First through tenth year - MPI warrants that the primary heat
exchanger is free from defects in material and workmanship for
10 years from date of purchase.
Parts covered: All product or parts of the FCX manufactured by
or for MPI except as provided for herein.
Parts not covered: The following parts are not covered by this
warranty: venting kits, fuses, and all parts subject to physical,
chemical or freeze damage. The FCX is designed to be fueled
with clean, dry, #2 grade or better, home-heating oil. Use of
substandardoilor otherfuels willvoid thiswarranty.Nozzle failure
due to water or contaminants in fuel will not be covered.
This warranty does not cover physical, chemical or freeze
damage or use of antifreeze other than that approved by MPI.
Water of strong acidic or alkaline composition can damage the
heatexchanger assembly and will void this warranty. In addition,
the ingestion of chlorine or chlorine contaminating fumes or
vapors,fluorine or florinecontainingfumes or vapors,fumes from
animal confinement, fumes from beauty parlors, fumes from
muriatic acid or other compounds used for cement cleaning,
fumesfrom mechanical parts’cleaning, fumes from dry-cleaning
establishments, fumes from laundry, fumes from manufacturing
or industrial activity into the combustion-air to the heating
system can damage the heat exchanger assembly and will
void this warranty of the heat exchanger assembly.
STANDARD PROVISIONS, TERMS AND CONDITIONS THAT
ARE COMMON TO ALL MPI INDIVIDUAL PRODUCT
WARRANTIES:
These warranties are subject to the condition that the MPI
product(s) must have been installed in accordance with
manufacturer’sinstructions.These warranties extend onlytothe
first retail purchaser of the products and only to a product that
has not been moved from its original installation site. These
warranties do not apply to commercial applications.
In addition to each product warranty listed, MPI warranties do
not cover:
1) Components that are part of the heating system but were
not furnished by MPI as part of the heating system.
2) The workmanship of any installer of MPI’s product(s). In
addition, this warranty does not assume any liability of any
nature for unsatisfactory performance caused by improper
installation.
3) Any costs for labor for removal and reinstallation of the
alleged defective part, the cost of shipping or transportation
toMPIandback to the consumer,if necessary, and any other
materials necessary to perform the exchange.
4) Replacement parts beyond the balance of the original
warranty period.
REMEDY: If within the applicable warranty period, any pro-
duct(s)orpart(s) included in this warranty proves tobedefective
in material and/or workmanship, then MPI shall repair or
replace, at its option, the defective product(s) or part(s) and
return it to the consumer.
PROCEDURE FOR OBTAINING PERFORMANCE UNDER
THIS WARRANTY: In order to obtain performance under this
warranty, the original purchaser must promptly (in no event later
than thirty (30) days after discovery of the defect) see to the
return of the product(s) or part(s) in question, accompanied by a
properly filled out MPI warranty claim form (Available from MPI
by mail or phone).Any claim made under this warranty must be
accompanied by proof of original purchase date, sales invoice
or cancelled check showing the serial number as satisfactory
evidence. Any replacements are made subject to validation by
MPI of in-warranty coverage. An item to be replaced must be
made available in exchange for the replacement.
SOLE REMEDY: The remedy and liability for any breach of
warranty, express or implied, set forth herein is the sole and
exclusive remedy and the limit of liability for any such breach.
EXCLUSIONS AND IMPLIED WARRANTIES: This warranty
does not extend to any defect due to the negligence of others.
Failureto install,operateor maintaintheproduct(s) inaccordance
with the installation, operation and maintenance instructions
furnished with each new product, unreasonable use, accidents,
actsofgod,fire, snow,floods,lightning, alteration, ordinary wear
and tear, or the use of unauthorized or non-standard parts.
ALL IMPLIED WARRANTIES, IF ANY,ARISING UNDER LAW
IN CONNECTION WITH THE SALES BY MPI OF ANY
PRODUCT(S)ARE LIMITED IN EXTENTAND DURATION TO
THE DURATION OF THIS WRITTEN WARRANTY. THERE
ARE NO WARRANTIES, EXPRESS OR IMPLIED, OF
MERCHANTABILITY, FITNESS FOR A PARTICULAR
PURPOSE OTHER THANAS EXPRESSLY STATED HEREIN.
MPI SHALL NOT BE RESPONSIBLE FORANY INCIDENTAL,
INDIRECT, PUNITIVE, OR CONSEQUENTIAL DAMAGES
WHETHER AS A RESULT OF BREACH OF WARRANTY,
NEGLIGENCE, STRICT LIABILITY IN TORT OR OTHERWISE.
Note:Some jurisdictions do not allow: (a)limitationsonhow long
an implied warranty lasts; or (b) the exclusion or limitation of
incidental, indirect, punitive or consequential damages, so the
above limitations or exclusions may not apply to you.
NOVARIATION OF TERMS:the partiesintend that this warranty
be the exclusive and final expression of their agreement.
No person has the authority to orally, in writing or in any other
way vary the terms, conditions or exclusions of this warranty, or
to make any express warranties other than those contained
herein.
LEGAL RIGHTS: This warranty gives you specific legal rights
and you may also have other rights which vary from jurisdiction
to jurisdiction.
VI - MONITOR PRODUCTS, INC. (“MPI”) LIMITED WARRANTIES
WARRANTIES
As part of its policy of continuous product improvement, Monitor Products, Inc. reserves the right to make changes without notice
COPYRIGHT © 2007 MONITOR PRODUCTS, INC.

18
FCX INSTALLATION AND SERVICE MANUAL
PARTS BREAKDOWN
VII - PARTS BREAKDOWN
FCX

19 www.monitorproducts.com
38 2363 ADAPTORFOR VENTOUSE D.80-125
39 2319 SILICONESEALINGD.162X85X4
40 2320 BLACKHANDLE (FOR H3MG VALVE)
41 2321 REDUCEDMESSINGNIPPLEM1-M3/4
42 2322 NUT
43 2323 BRASS VALVE
44 2324 NUTFOR FLANGE 1” (FORPIPED.22,5)
45 2325 STAINLESSSTEELWASHER
30,4X25,5X0,3
46 2326 SIGHTGLASSPYREXD.30X5
47 9012 EXPANSION TANK,VESSEL8LMALE
3/4
48 2327 SEALINGAFM34D24X17X3
49 2328 DRAIN VALVE WITH CAP M 1/2 - M 3/4
50 2383 HEATING FLOW BEFORE 1. CIRCUIT
51 2329 CONDENSATE DISCHARGE
52 2330 FRESHAIRINTAKEHOSE
53 2331 MINERALCARBOARDWASHER D.
25X8,5X3
54 2384 INSULATIONCONDENSERFCX
55 2385 HEATING SYSTEM SHELL COVER
EQUIPPED FORFCX
56 2332 VALVE STOP
57 2386 BASEFORFCX
58 2387 FLANGE
59 2333 SALMSONSEALING11/2DIA44X32X3
60 2388 CIRCULATING PUMPGRUNDFOSS 115
UPS15.42 F-9H
61 2389 BEND90°F3/4-F3/8
62 2334 AUTOMATIC DRAIN3/8WITH
ISOLATING VALVE
63 2335 FLOW/RETURN BEND F1-F22
64 2336 SAFETY VALVE 30 PSIG MAL/FEM.
3/4 NPT
65 2385 HEATINGSYSTEMSHELL;EQUIPED
* 2337 SEAL VITON D.80
* 2338 FIXING PIECE FOR THE COVER
(MALE)
* BOLT(PVC)
* BAFFLEPLATEF400-F E/FEA-FCX
(250X200X1,5)
* DISKFORISOLATION (KERLANE)
*NOT SHOWNON THEDRAWING
PARTS BREAKDOWN
MPI PARTS # DESCRIPTION
1 2300 FRONT COVEREQUIPPED
2 2301 INSULATIONFRONTCOVER
3 2302 RIGHT HAND SIDE COVER EQUIPPED
4 2303 INSULATIONRIGHTHANDSIDE
5 2367 FOLDED NECK
6 2368 INSULATION FOR SYSTEM SHELL
7 2304 PAINTEDCONNECTING FLANGE
8 2305 PAINTEDBACK COVER
9 2362 SWIRLERS
10 2369 COMBUSTIONCHAMBER
11 2366 MINERAL WOOL90 KG DISK
DIAMETER 262X20
12 2370 FASTENINGANGLE
13 2371 GLASSFIBER INSULATION LG 950-
CAST PLATE
14 2306 CERAMICFIBERINSULATIOND.280X20
(300°C)
15 2372 HEATING SYSTEM SHELL- CASTIRON
16 2307 TOPCOVER EQUIPPED
17 2308 PROTECTINGCOVER
18 2309 ABSPROTECTION
19 2359 ELECTR.CONTROL BOX + CABLE
20 2373 CONDENSERCOVER
21 2311 TOPRING CONDENSER
22 2312 FASTENINGFLANGE FOR
CONDENSER COVER
23 2374 CONDENSER(secondaryheatexchanger)
24 2313 SEALAFM34 D. 18,6 X 12 2 MM
THICKNESS
25 2360 BRASSCONNECTIONM1/2-F3/4 NPT
26 2314 LEFTHANDSIDECOVEREQUIPPED
27 2315 INSULATION LEFTHAND SIDE
28 2316 NITRILEO’RING D.50X470SHORE
29 2376 CLEANINGCAP FOR CONDENSER
EQUIPPED
30 2377S HEATING RETURN2.CIRCUITSHORT
31 2317 SEALINGAFM34D30X21X3
32 2377L HEATINGRETURN1.CIRCUITLONG
33 2378 HEATINGFLOW2.CIRCUIT
34 2318 SEALINGONCONDENSERFLANGE
35 2379 HEATINGFLOW
36 2380 HEATING SYSTEM SHELLRETURN
37 2381 MALECONNECTION 3/4

20
FCX INSTALLATION AND SERVICE MANUAL
PARTS BREAKDOWN
FCX CONTROL BOX
MPI PART # DESCRIPTION
1 2340 PAINTEDCONTROLBOX
2 2341 WIRECARRIER
3 2343 WIRE ROPE CLAMP PA6,6
4 2342 TRANSFORMER120V/24V
5 2344 PAINTED CASING /CONTROLBOX
6 2345 THERMOSTATRECTHORIZ69X14
LGCAPIL.1500MM
7 2346 THERMOSTAT50/70° C SINGLE
CONTACT
8 2347 WATERTEMP. CONTROLKNOB
9 2357 FUSEHOLDERWICKMANNREF
19820+19835
10 2349 RED LIGHT230V -120)FLATHEAD
11 2350 CONTROLPANEL+STICKER
12 2351 SAFETYTHERMOSTAT110CAP
1,5MTG400
13 2352 SAFETYTHERMOSTAT120 CAP
1,5M TG400
14 2353 UNIPOLAR SWITCH D. 23/ GREEN
LIGHT
15 2354 UNIPOLARREVERSIBLESWITCH
D. 23 BLACK
16 2355 OMRONRELAY
17 UPPERFASTENER FORTHERELAY
18 2356 FUSE 6.3AMP 5X20
* 2358 WIRINGFORFCX
* 2359 ELECTR.CONTROLBOX+CABLE
*NOT SHOWNON THEDRAWING
Table of contents
Other Monitor Heating System manuals
Popular Heating System manuals by other brands

Innova
Innova HRC 08 Instructions for installation, use and maintenance manual
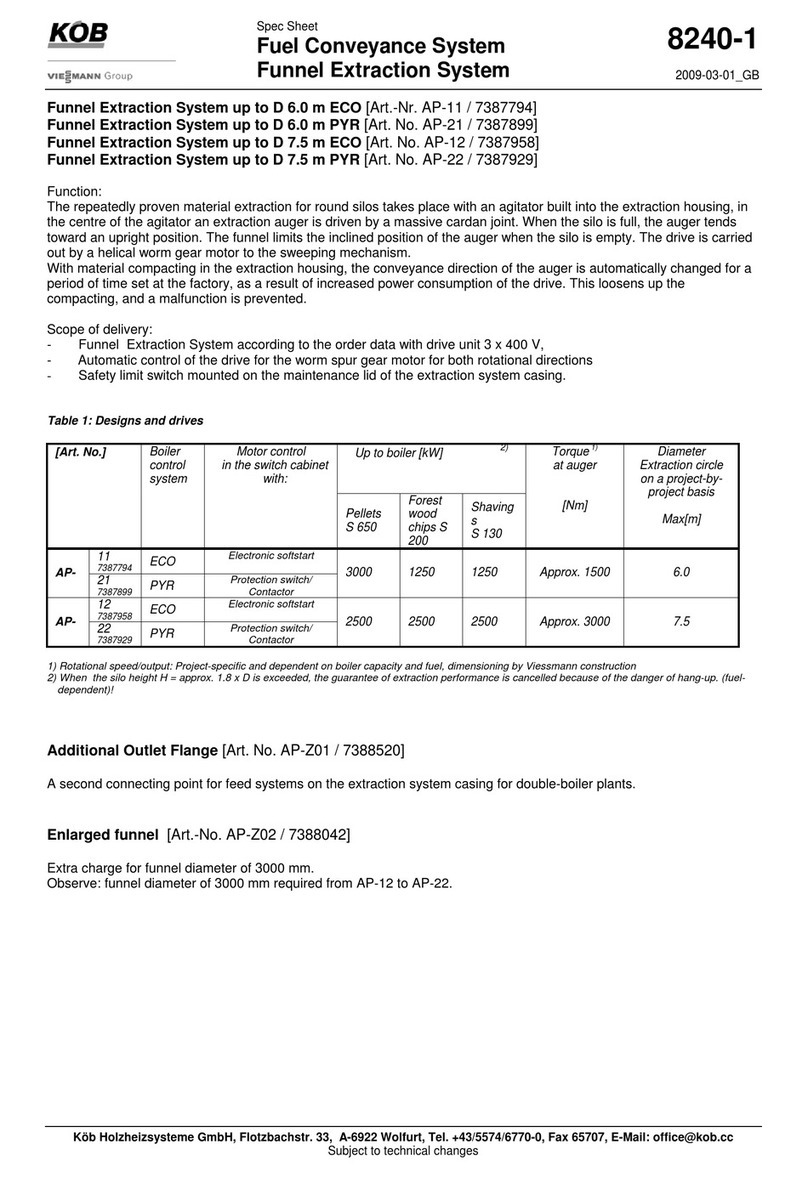
KOB
KOB KOB 8240-1 Spec sheet
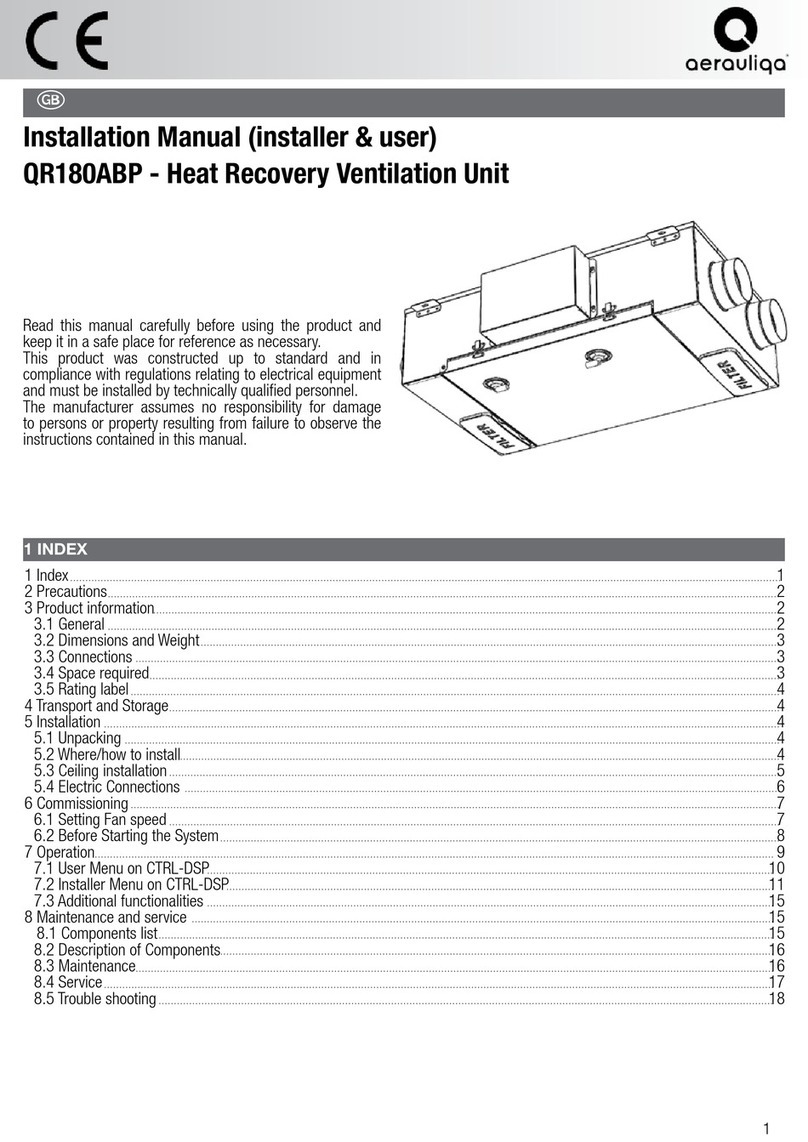
aerauliqa
aerauliqa QR180ABP installation manual

Vent-Axia
Vent-Axia Sentinel Kinetic 200ZH Installation & commissioning
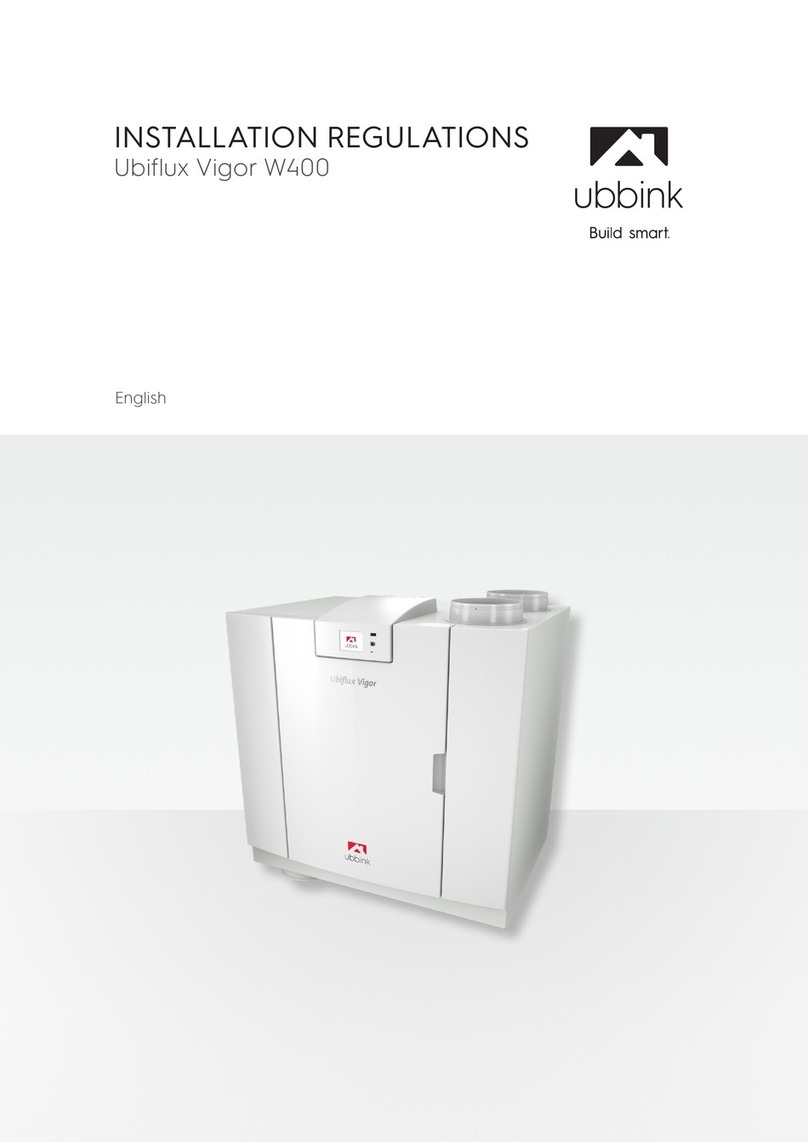
ubbink
ubbink Ubiflux W400 + Installation regulations
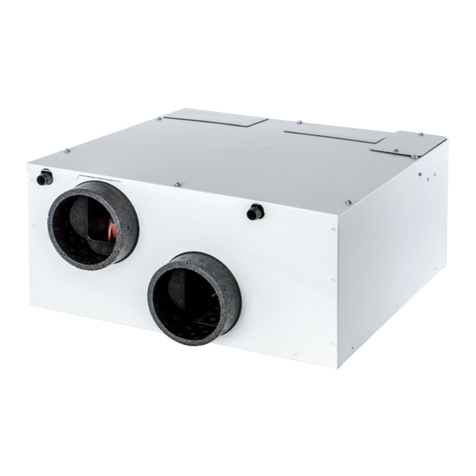
Vortice
Vortice VORT INVISIBLE MINI Instruction booklet

Airflow
Airflow Uno hab Installation and operating instructions
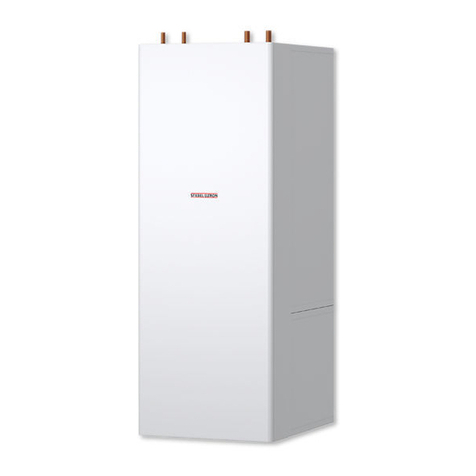
STIEBEL ELTRON
STIEBEL ELTRON HSBC 300 cool Operation and installation
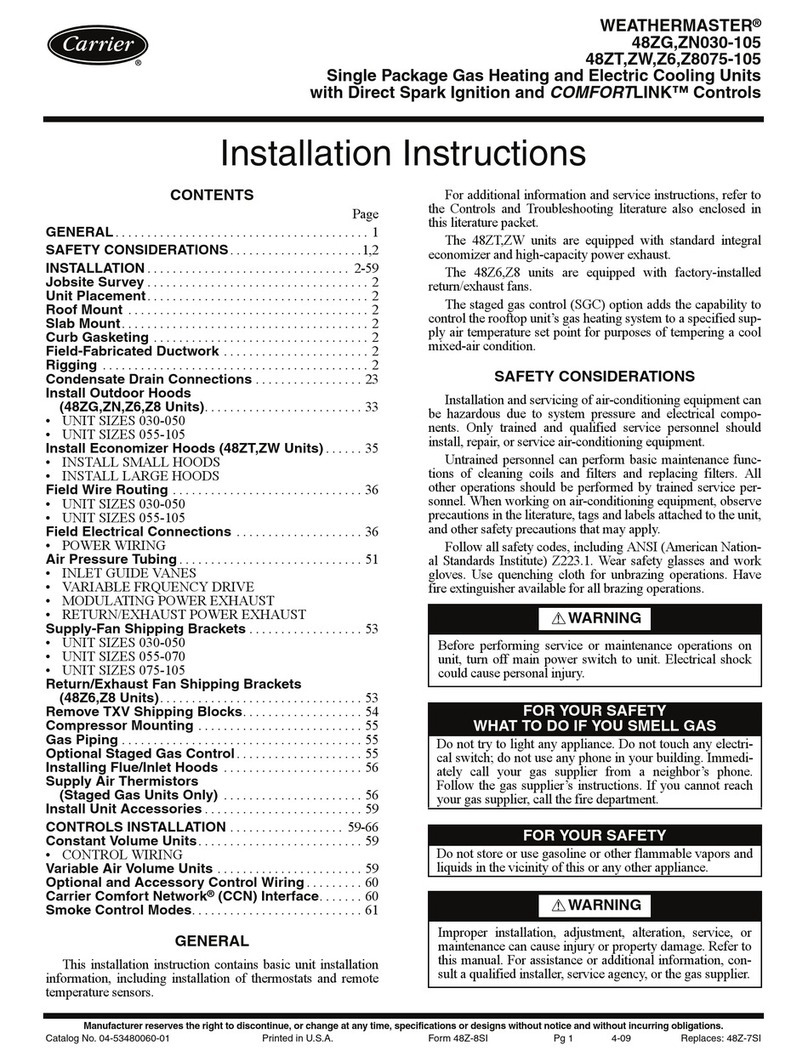
Carrier
Carrier Z6 user manual

SND
SND SND-1500-3 owner's manual
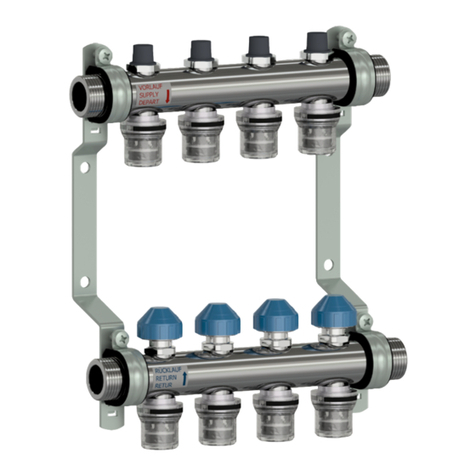
Watts
Watts Push'n'Go HKV-R Series Installation and operating manual
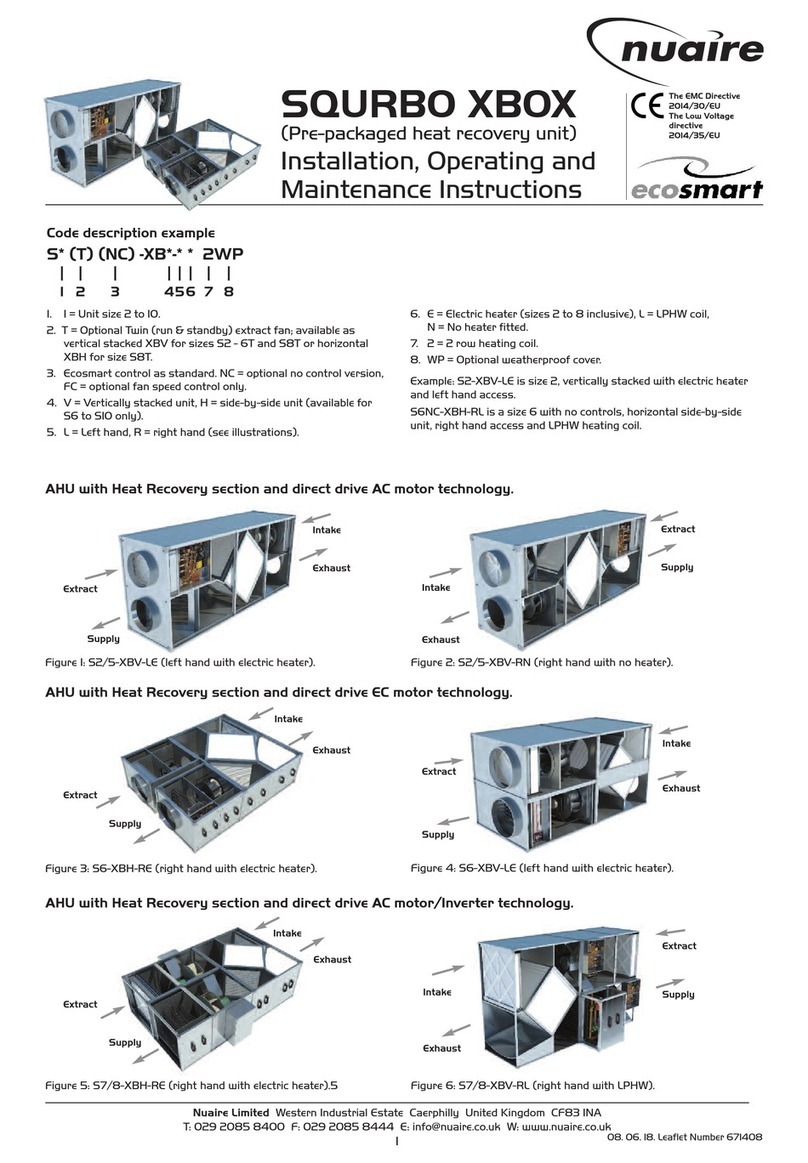
NuAire
NuAire ecosmart SQURBO XBOX Installation, operating and maintenance instructions