National Instruments NI 9512 User manual

OPERATING INSTRUCTIONS AND
SPECIFICATIONS
NI 9512
Stepper Drive Interface Module with Feedback
ni.com/manuals
DeutschFrançais

2|ni.com |NI 9512 Operating Instructions and Specifications
This document describes how to use the National Instruments 9512
module and includes specifications and pin assignments for the
NI 9512.
Note The safety guidelines and specifications in this
document are specific to the NI 9512. The other
components in the system may not meet the same safety
ratings and specifications. Refer to the documentation for
each component in the system to determine the safety
ratings and specifications for the entire system.
Related Information
Safety Guidelines
Operate the NI 9512 only as described in these operating
instructions.

NI 9512 Operating Instructions and Specifications |© National Instruments |3
Safety Guidelines for Hazardous Locations
The NI 9505 is suitable for use in Class I, Division 2, Groups A, B,
C, D, T4 hazardous locations; Class I, Zone 2, AEx nA IIC T4 and
Ex nA IIC T4 hazardous locations; and nonhazardous locations
only. Follow these guidelines if you are installing the NI 9505 in a
potentially explosive environment. Not following these guidelines
may result in serious injury or death.
Caution Do not disconnect I/O-side wires or connectors
unless power has been switched off or the area is known to
be nonhazardous.
Caution Do not remove modules unless power has been
switched off or the area is known to be nonhazardous.
Caution Substitution of components may impair
suitability for Class I, Division 2.
Caution For Division 2 and Zone 2 applications, install
the system in an enclosure rated to at least IP 54 as defined
by IEC/EN 60079-15.

4|ni.com |NI 9512 Operating Instructions and Specifications
Caution For Division 2 and Zone 2 applications, install a
protection device between the input signal and the Vsup
pin. The device must prevent the Vsup-to-channel voltage
from exceeding 42 V if there is a transient overvoltage
condition.
Special Conditions for Hazardous Locations Use in
Europe and Internationally
This equipment has been evaluated as Ex nA IIC T4 Gc equipment
under DEMKO Certificate No. 07 ATEX 0626664X and is IECEx
UL 14.0089X certified. Each module is marked II 3G and is
suitable for use in Zone 2 hazardous locations, in ambient
temperatures of – 40 °C Ta 70 °C. If you are using the NI 9512
in Gas Group IIC hazardous locations, you must use the device in
an NI chassis that has been evaluated as Ex nC IIC T4, Ex IIC T4,
Ex nA IIC T4, or Ex nL IIC T4 equipment.
Caution You must make sure that transient disturbances
do not exceed 140% of the rated voltage.
Caution The system shall only be used in an area of not
more than Pollution Degree 2, as defined in IEC 60664-1.

NI 9512 Operating Instructions and Specifications |© National Instruments |5
Caution The system shall be mounted in an
ATEX/IECEx-certified enclosure with a minimum ingress
protection rating of at least IP54 as defined in
IEC/EN 60079-15.
Caution The enclosure must have a door or cover
accessible only by the use of a tool.
Electromagnetic Compatibility Guidelines
This product was tested and complies with the regulatory
requirements and limits for electromagnetic compatibility (EMC)
as stated in the product specifications. These requirements and
limits are designed to provide reasonable protection against
harmful interference when the product is operated in its intended
operational electromagnetic environment.
This product is intended for use in industrial locations. As such,
there is no guarantee that harmful interference will not occur in
a particular installation, when the product is connected to a test
object, or if the product is used in residential areas. To minimize
the potential for the product to cause interference to radio and
television reception or to experience unacceptable performance

6|ni.com |NI 9512 Operating Instructions and Specifications
degradation, install and use this product in strict accordance with
the instructions in the product documentation.
Furthermore, any changes or modifications to the product not
expressly approved by National Instruments could void your
authority to operate it under your local regulatory rules.
Caution To ensure compliance with the applicable
regulatory requirements, product installation requires
either special considerations or user-installed, add-on
devices. See the product installation instructions for
further information.
Caution The inputs/outputs of this product can be
damaged if subjected to Electrostatic Discharge (ESD). To
prevent damage, industry-standard ESD prevention
measures must be employed during installation,
maintenance, and operation.
Special Conditions for Marine Applications
Some modules are Lloyd’s Register (LR) Type Approved for
marine applications. To verify Lloyd’s Register certification, go to
ni.com/certification and search for the LR certificate, or
look for the Lloyd’s Register mark on the module.

NI 9512 Operating Instructions and Specifications |© National Instruments |7
Caution To meet radio frequency emission requirements
for marine applications, use shielded cables and install the
system in a metal enclosure. Suppression ferrites must be
installed on power supply inputs near power entries to
modules and controllers. Power supply and module cables
must be separated on opposite sides of the enclosure and
must enter and exit through opposing enclosure walls.
Connecting the NI 9512
The NI 9512 stepper drive interface module is part of a family of
C Series motion modules. The module provides stepper drive
interface signals for a single axis, a full set of motion I/O including
inputs for a home switch and limit switches, incremental encoder
inputs for position feedback, and 0 to 30 V digital input and output
lines. The NI 9512 also includes a processor to run the spline
interpolation engine and patented NI step generation algorithm.
Working together they produce smoother motion resulting in
precise stepper motion control.
System Connection
The NI 9512 has two connectors, a 15-pin DSUB drive interface
connector and a 20-pin MDR feedback connector. The 15-pin

8|ni.com |NI 9512 Operating Instructions and Specifications
DSUB includes command signals for interfacing with stepper
drives, 0 to 30 V general-purpose digital input and output lines, and
a +19 to 30 V input for power connection. Refer to Table 2 for the
DSUB connector pin assignments.
The 20-pin MDR connector includes incremental encoder
feedback inputs, a +5 V output for encoder power, home, limit, and
position compare inputs, an output for position compare, an
additional +19 to 30 V input for power connection, and an
additional 0 to 30 V general-purpose digital input line. Refer to
Figure 2 for the MDR connector pin assignments.
Note The NI 9512 requires an external power supply.
You can connect the external power supply to the Vsup
input provided on the DSUB or MDR connector. Do not
connect more than one external power supply to the
module.
NI 9512 Connection Options
National Instruments offers several options for connecting the
NI 9512 to stepper or position command servo drives. Refer to
Table 1 for available NI 9512 connection options.

NI 9512 Operating Instructions and Specifications |© National Instruments |9
Table 1. NI 9512 Connection Options
Drive Connection Option
NI ISM-7400/7401/
7402
NI SMD-7610
NI SMD-7611/7612
NI SMD-7620/7621
Direct Connectivity to NI ISM and NI SMD
stepper drives
Go to ni.com/info and enter stepper for
installation and configuration information for
NI ISM and NI SMD stepper drives.
AKD Analog Servo NI 9512 to AKD Drive Cable
(NI part number 781525-01)
Refer to Getting Started with NI 9512 C Series
Drive Interface Modules and AKD Analog Servo
Drives for installation and configuration
information for AKD servo drives
Mitsubishi MR-J2
or MR-J3
NI 9930M Motion Control Accessory
(NI part number 781824-01)
Refer to NI 9930 Motion Control Accessories
User Guide for installation and configuration
information for connection to Mitsubishi,
p-command servo drives.

10 |ni.com |NI 9512 Operating Instructions and Specifications
Panasonic Minas-A
or Minas-A5
NI 9930P Motion Control Accessory
(NI part number 781823-01)
Refer to NI 9930 Motion Control Accessories
User Guide for installation and configuration
information for connection to Panasonic
p-command servo drives.
Yaskawa Sigma-II
or Sigma-V
NI 9930Y Motion Control Accessory
(NI part number 781822-01)
Refer to NI 9930 Motion Control Accessories
User Guide for installation and configuration
information for connection to Yaskawa
p-command servo drives.
Other third-party
stepper drive
NI 951x cable and terminal block bundle
(NI part number 780553-01)
Refer to the Getting Started with NI 951x C Series
Drive Interface Modules and LabVIEW for
information about using the NI 9512 with other
devices.
Table 1. NI 9512 Connection Options (Continued)
Drive Connection Option

NI 9512 Operating Instructions and Specifications |© National Instruments |11
How to Connect the NI 9512 to Drives and I/O
Complete the following steps to connect the NI 9512 stepper drive
interface module to drives and other I/O:
1. Install the module in the chassis as specified in the chassis
documentation.
Note Refer to the SoftMotion Module book of the
LabVIEW Help for information about chassis, slot, or
software restrictions.
2. Connect the module to a drive and other I/O using one of the
connection options in Table 1.
3. Connect the NI 9512 module to an external power supply.
Caution Do not connect anything to pins marked
Reserved.
Caution The 37-pin terminal block has separate Vsup
and COM terminals for each connector. Make sure you are
using the correct Vsup and COM terminals for the
connector you are using. All signals associated with the
DSUB connector in Figure 3 are marked with a dagger (†).
Figure 1 shows a simplified system connection diagram.

12 |ni.com |NI 9512 Operating Instructions and Specifications
Figure 1. NI 9512 Connection Example
Encoder (Optional)Stepper Motor
Step±/CW
Step±/CW
Direction±/CCW
Drive Fault
Drive Enable
DSUB Connector
Forward, Reverse Limit, Home
MDR Connector
NI 9512
Drive
Motor
Encoder 0 Phase A, B, Index
Limit and Home
Sensors
Power Supply
Vsup
NI Connection
Accessory/
Custom Cable
+5 V OUT
Direction±/CCW
Drive Fault
Drive Enable

NI 9512 Operating Instructions and Specifications |© National Instruments |13
Table 2. NI 9512 DSUB Connector Pin Assignments
Connector Pin Signal
1Reserved
2Drive Enable
3Digital Input 3
4Digital Input 2
5Digital Output 1
6Reserved
7COM
8Digital Input 1
9Direction (CCW)-
10 Step (CW)-
11 Digital Output 0
12 Vsup
13 Direction (CCW)+
14 COM
15 Step (CW)+
1
6
11
5
10
15

14 |ni.com |NI 9512 Operating Instructions and Specifications
Figure 2. NI 9512 MDR Connector Pin Assignments
10
9
8
7
6
5
4
3
2
1
11
20
19
18
17
16
15
14
13
12
+5 V OUT
COM
Encoder 0 Index–
Encoder 0 Index+
COM
Digital Input 0
COM
Home
Forward Limit
Position Compare
Encoder 0 Phase A+
Encoder 0 Phase B–
Encoder 0 Phase B+
COM
Reserved
Vsup
Reserved
Reverse Limit
Position Capture
Encoder 0 Phase A–

NI 9512 Operating Instructions and Specifications |© National Instruments |15
Figure 3. NI 9512 37-Pin Terminal Block Pin Assignments
37
363534
333231
302928
27
262524
23
22212019
GND
18
17161514131211
10
98765
432
1
Forward Limit
Home
COM
Digital Input 0
COM
Encoder 0 Index+
Encoder 0 Index–
COM
+5V OUT
Position Compare
Reserved
Reserved
Digital Output 0†
V
sup
†
Digital Input 1†
Direction (CCW)+†
COM†
Step (CW)+†
Shield
Digital Output 1†
Reverse Limit
Reserved
Reserved
COM
Encoder 0 Phase A+
Encoder 0 Phase A–
Encoder 0 Phase B+
Position Capture
Encoder 0 Phase B–
Reserved
Reserved
COM†
Drive Enable†
Digital Input 3†
Digital Input 2†
Direction (CCW)–†
Step (CW)–†
V
sup
†
IndicatesDSUB connector signals.

16 |ni.com |NI 9512 Operating Instructions and Specifications
Signal Connections
Figure 4 shows the NI 9512 block diagram.
Figure 4. NI 9512 Block Diagram
Note This document provides a brief overview of the
module signal connections. Refer to the NI 951x User
Phase A± (0)
Phase B± (0)
Index± (0)
Home
Position
Capture
Position
Compare
Receiver
Circuitry
+5V Reg +5V OUT
Vsup
COM
Output
Circuitry
Input
Circuitry
Step ±
Drive
Enable
Forward
Reverse
Microprocessor
Digital
Output
(0-1)
Direction ±
Buffer
Buffer
Buffer
Buffer
Digital
Input
(0-3)

NI 9512 Operating Instructions and Specifications |© National Instruments |17
Manual, which you can download from ni.com/
manuals, for more information about signal connections.
Step and Direction Outputs
The NI 9512 module supports both industry standards for stepper
command signals—step and direction, or clockwise (CW) and
counterclockwise (CCW) pulse outputs. The step and direction
output circuits are software configurable for either single-ended or
differential output type.
When connecting to drives with differential receiver inputs,
configure the output type in software to differential and connect as
shown in Figure 5.
Figure 5. Differential Step and Direction Output Connection
NI 9512
Step– / Dir– Output
Step+ / Dir+ Output
Receiver
Drive

18 |ni.com |NI 9512 Operating Instructions and Specifications
Many stepper drive manufacturers offer opto-isolated inputs for
Step (CW)/Direction (CCW) signals. When connecting to
opto-isolated inputs, configure the Step output type to
single-ended, connect the NI 9512 Step+ output to the negative
(cathode) side of the optocoupler input, and leave the Step- output
on the NI 9512 disconnected. Connect the positive (anode) side of
the drive input to a supply as specified by the drive manufacturer.
Figure 6 shows a single-ended connection example.
Figure 6. Opto-Isolated Step and Direction Output Connection
Encoder Signals
The encoder channel consists of a Phase A, a Phase B, and an Index
input. The NI 9512 supports RS-422 differential and single-ended
inputs for Phase A, Phase B, and Index signals, and provides a
+5 V output for encoder power. National Instruments strongly
recommends you use encoders with differential line driver outputs
NI 9512
Step+/Dir+
Drive
Step+/Dir+
Step–/Dir–
+5 V
No Connection Step–/Dir–

NI 9512 Operating Instructions and Specifications |© National Instruments |19
for optimized noise immunity and improved accuracy in all
applications. Figures 7 and 8 show simplified schematic diagrams
of the encoder input circuit connected to differential and
single-ended encoder outputs.
Figure 7. Differential Encoder Input Circuit
Figure 8. Single-Ended Encoder Input Circuit
Receiver
Phase +
Phase –
Encoder NI 9512
+5 V
COM
Receiver
Phase+
Encoder NI 9512
No
Connection Phase–
+5 V
COM
+5 V
Com

20 |ni.com |NI 9512 Operating Instructions and Specifications
Limit and Digital Input Signals
You can configure the Forward Limit, Reverse Limit, Home, and
Digital Input <1..4> circuits in software for current sinking or
sourcing output devices and set the active state of the inputs in
software to on or off. To use the Drive Fault functionality
referenced in Figure 1, you can map an available digital input in
software. Figure 9 shows an example of wiring the inputs to a
sourcing output device.
Figure 9. Limit or Digital Input Circuit Configured for Sinking
PNP (Sourcing)
Output Device
COM
NI 9512
V–
V+
Out
Limit, Home,
or Digital Input
(Reference)
Limit, Home,
or Digital Input
Current
Limiting
Circuit
Other manuals for NI 9512
1
Table of contents
Other National Instruments DC Drive manuals
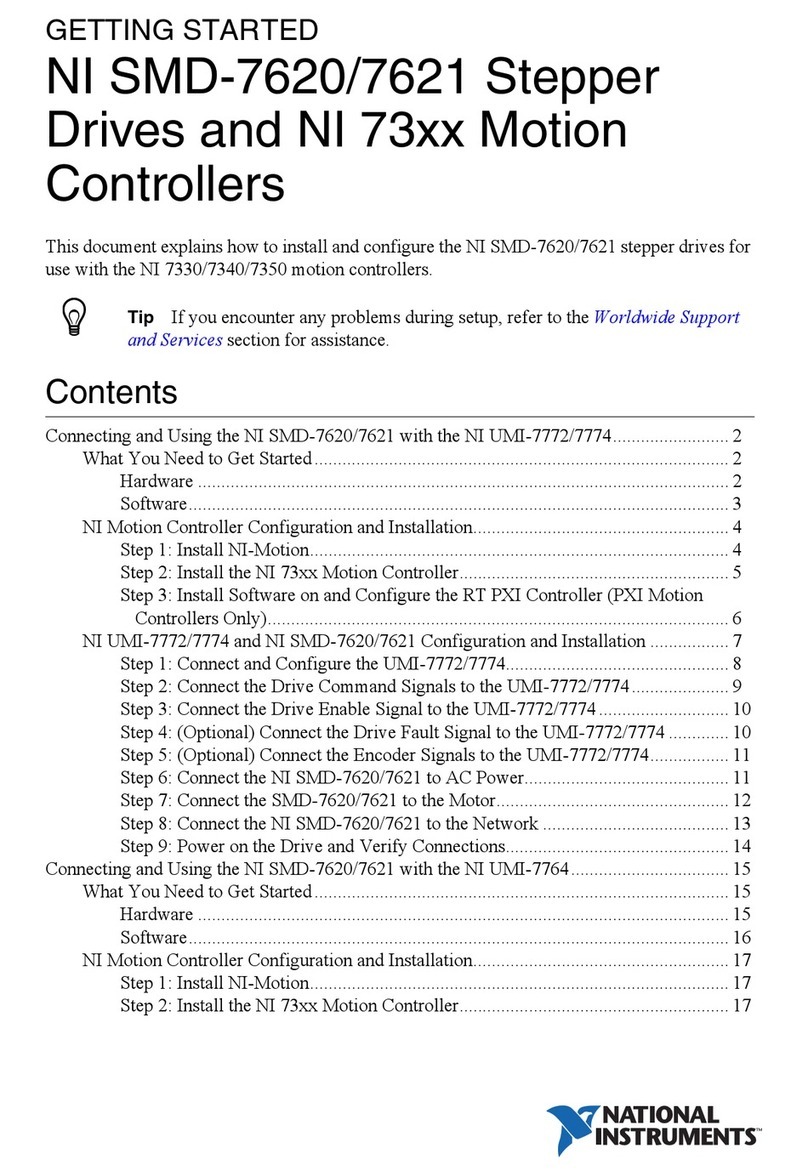
National Instruments
National Instruments NI 73 Series User manual
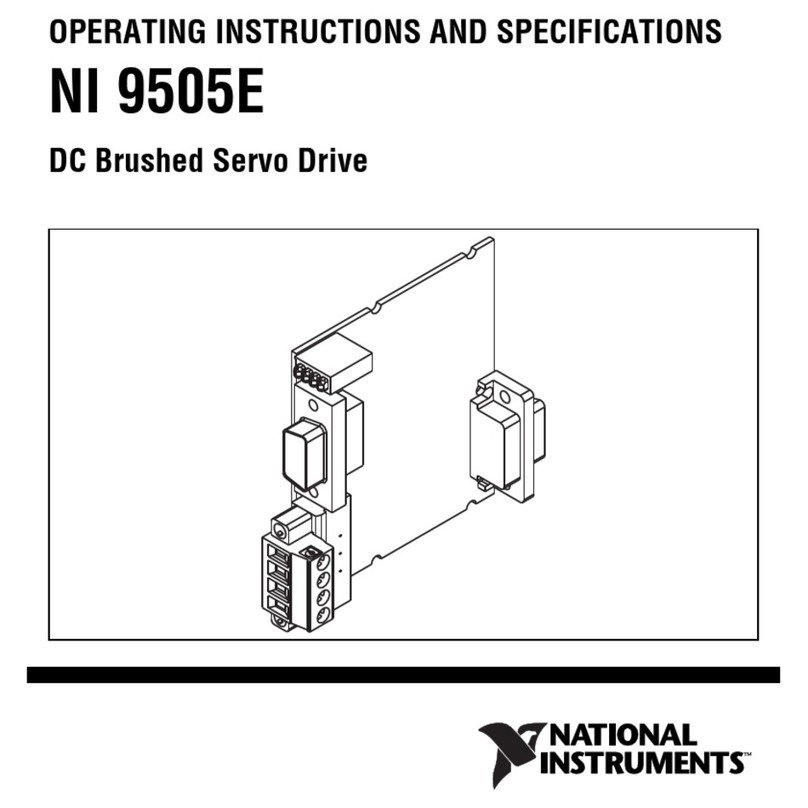
National Instruments
National Instruments 9505E User manual
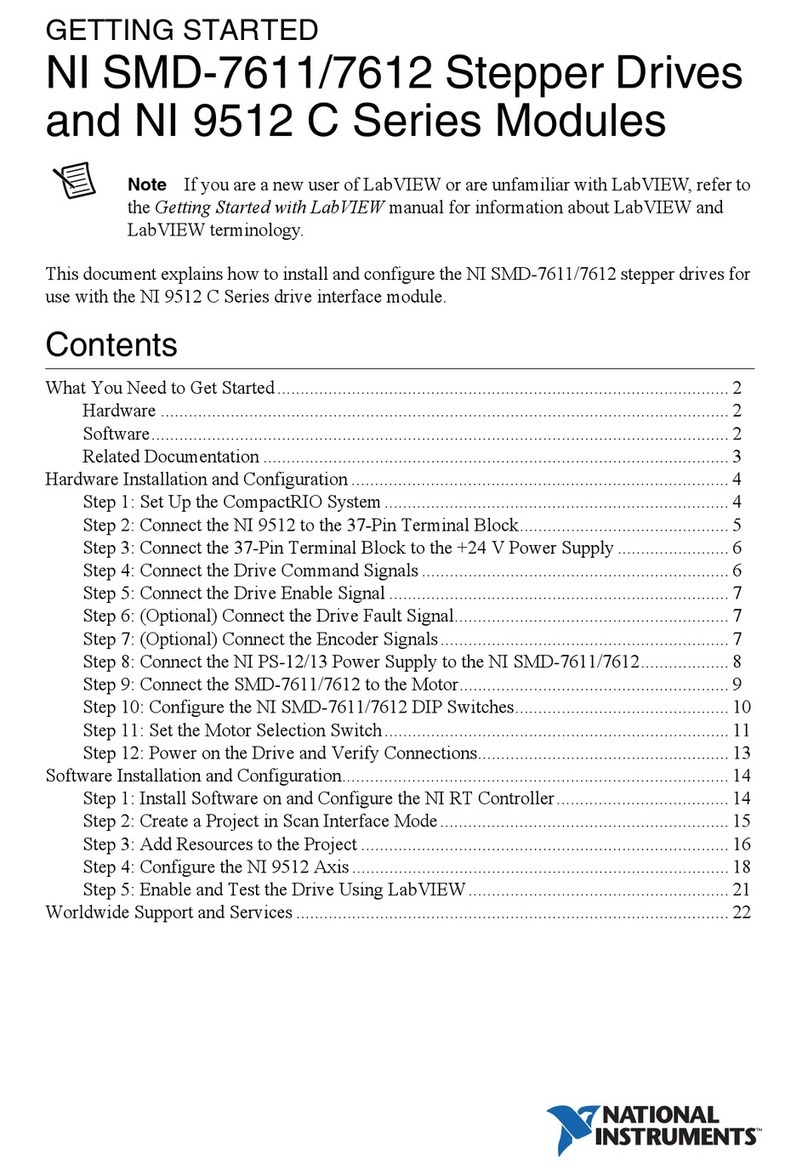
National Instruments
National Instruments 9512 C Series User manual
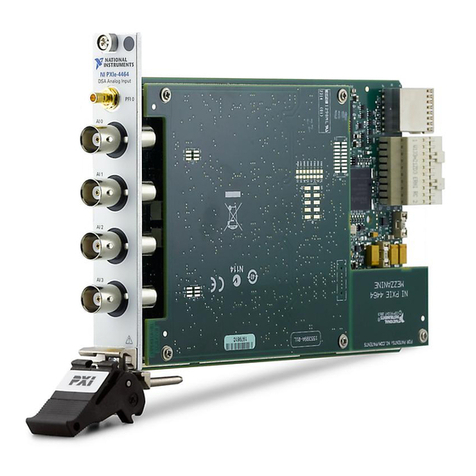
National Instruments
National Instruments NI PXIe-4464 Manual
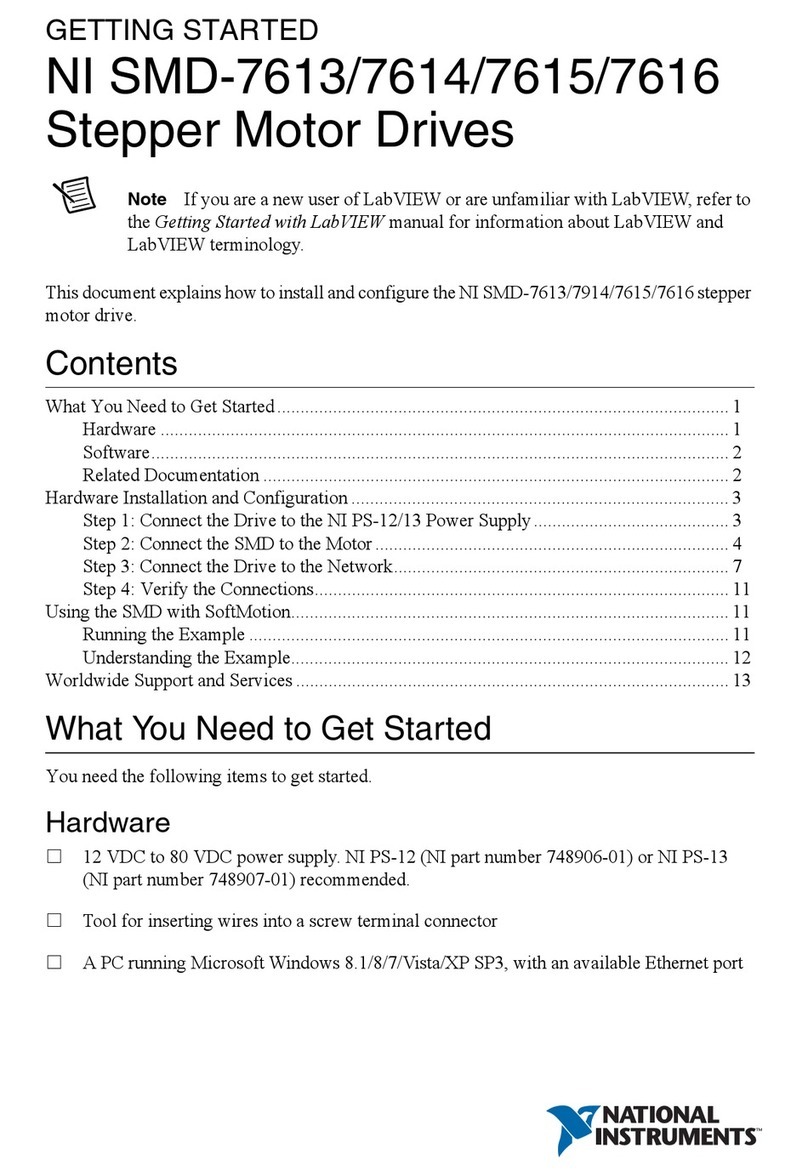
National Instruments
National Instruments NI SMD-7613 User manual
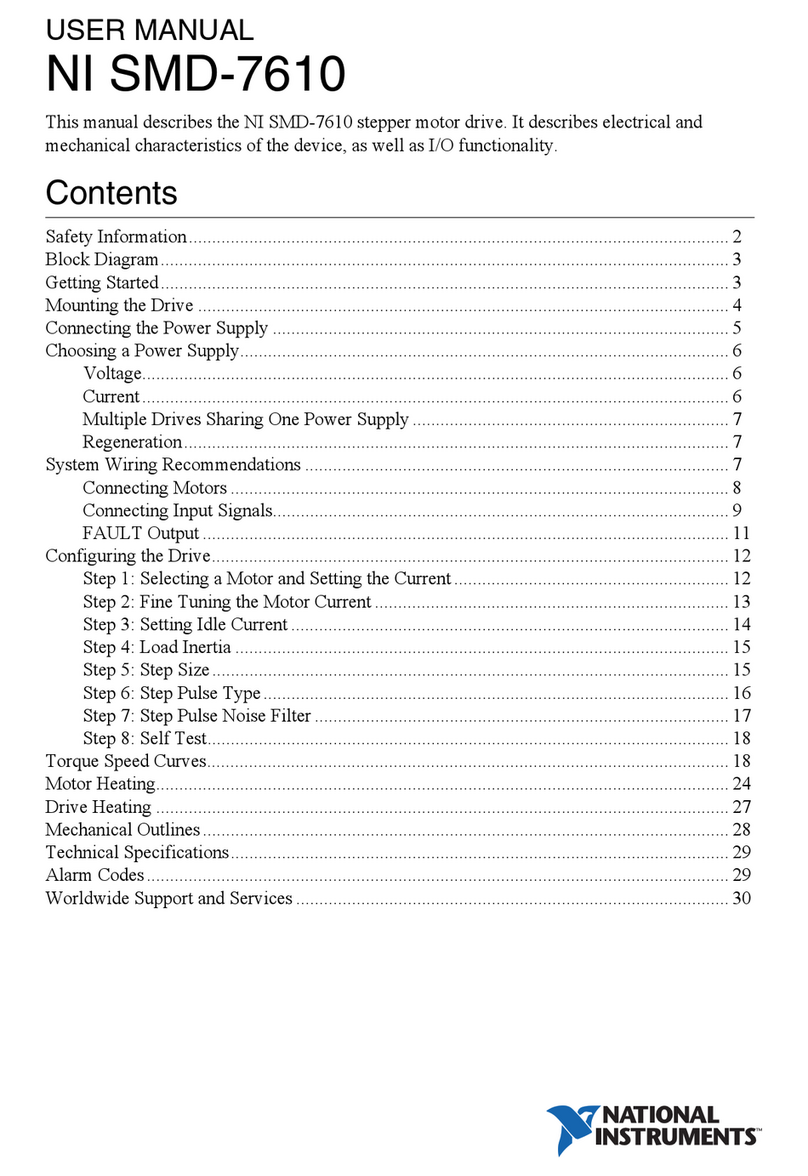
National Instruments
National Instruments SMD-7610 User manual
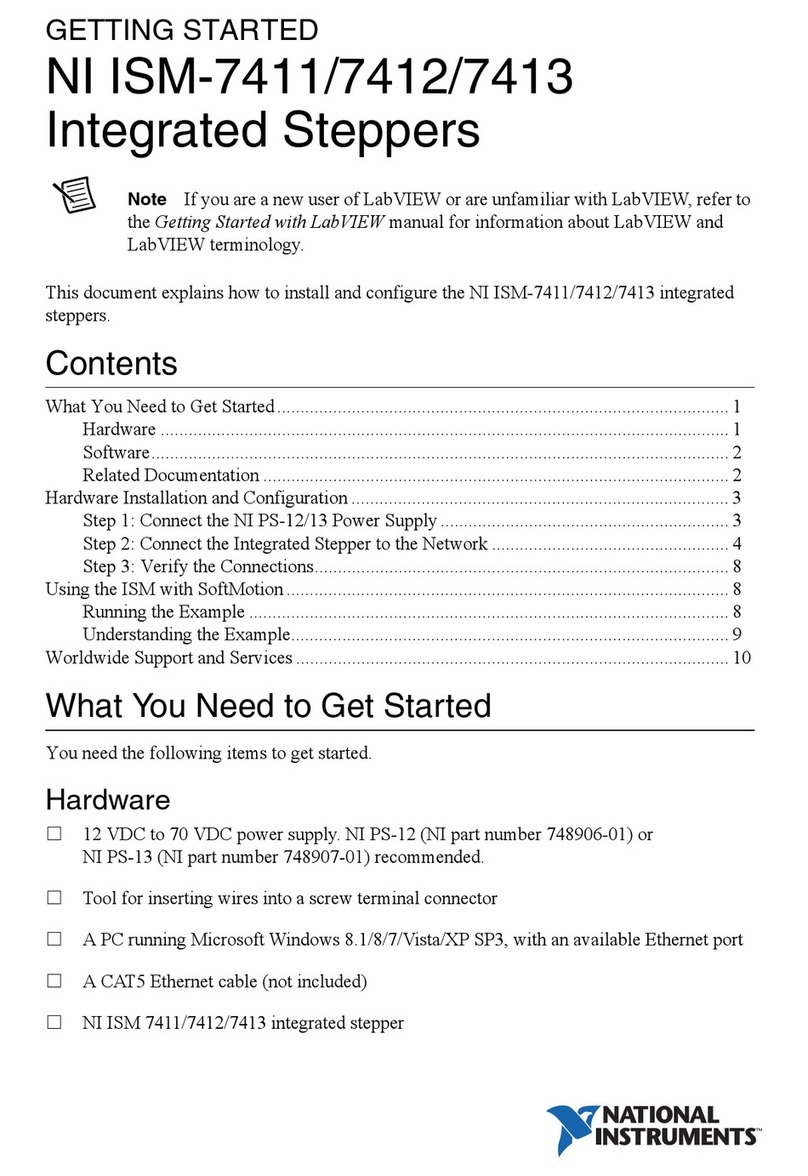
National Instruments
National Instruments ISM-7411 User manual
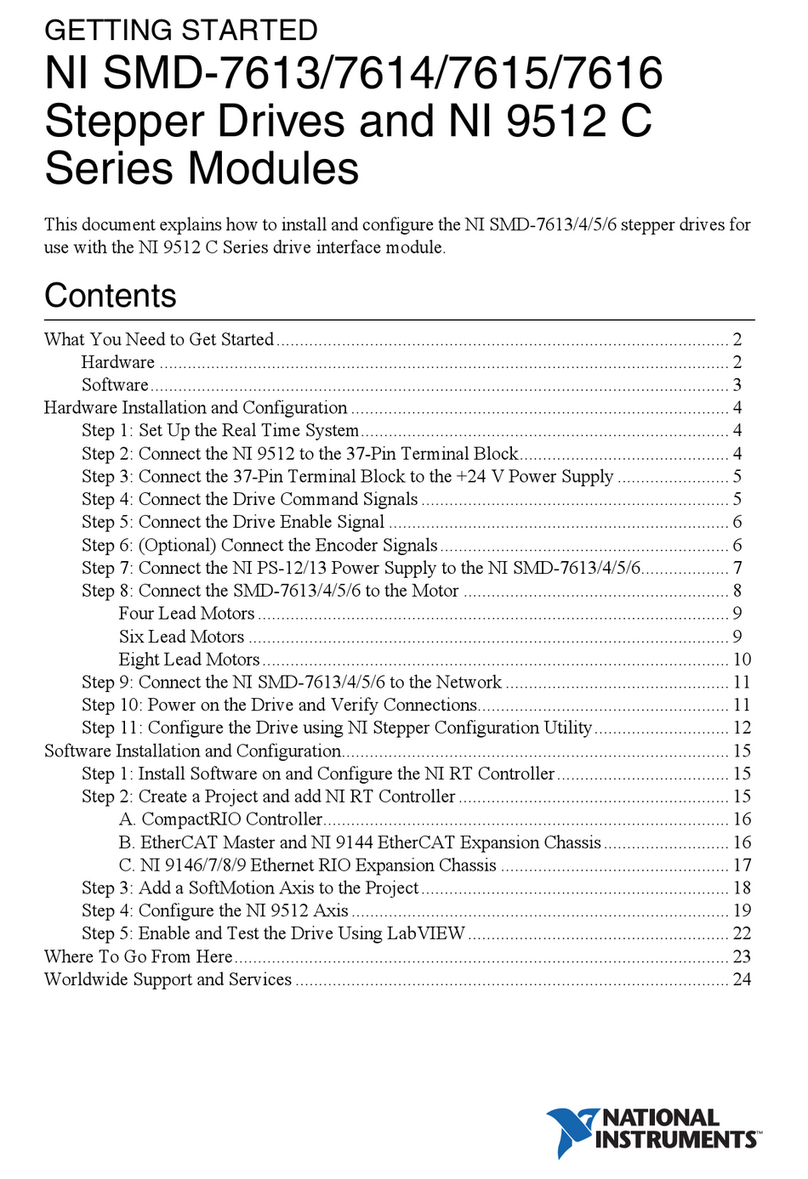
National Instruments
National Instruments NI SMD-7613 User manual
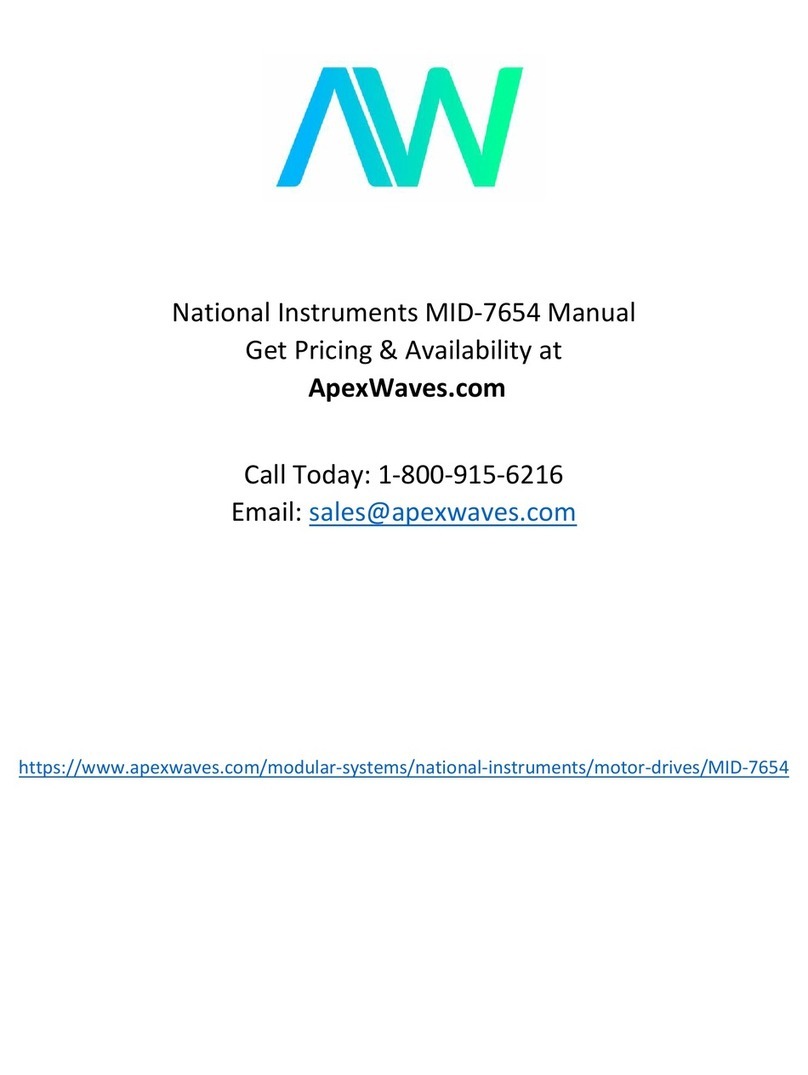
National Instruments
National Instruments NI MID-7654 User manual
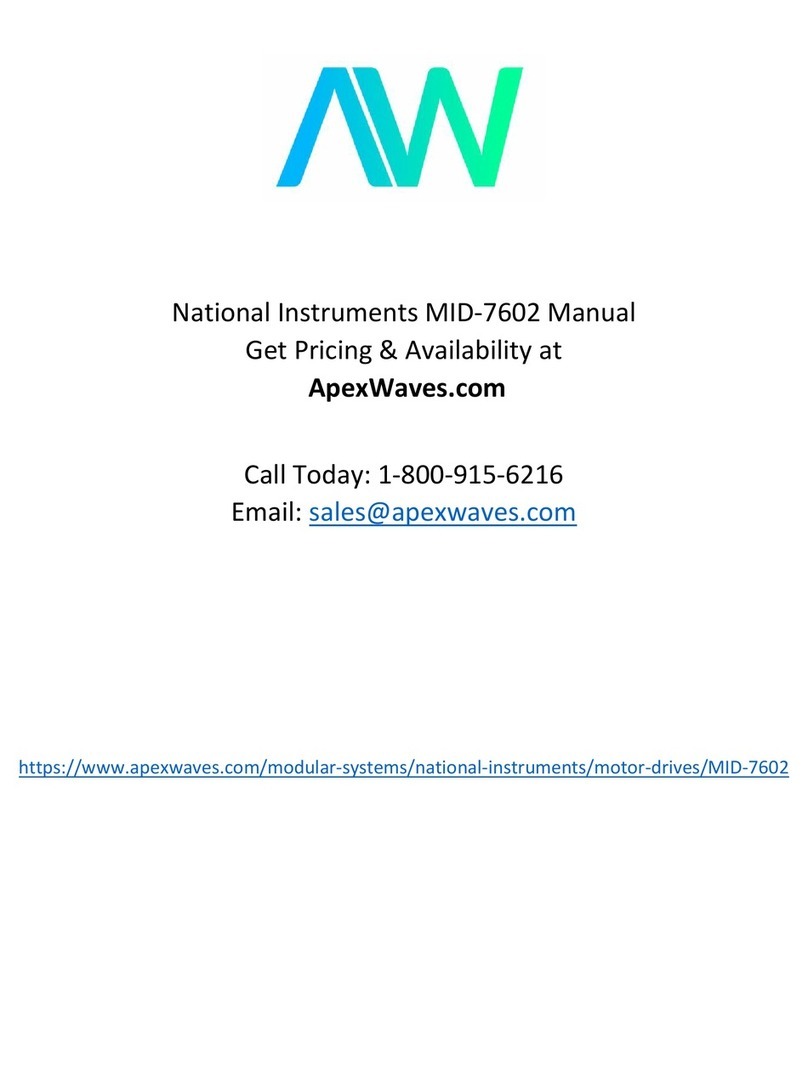
National Instruments
National Instruments NI MID-7602 User manual