NI 9157 User manual

Artisan Technology Group is your source for quality
new and certied-used/pre-owned equipment
• FAST SHIPPING AND
DELIVERY
• TENS OF THOUSANDS OF
IN-STOCK ITEMS
• EQUIPMENT DEMOS
• HUNDREDS OF
MANUFACTURERS
SUPPORTED
• LEASING/MONTHLY
RENTALS
• ITAR CERTIFIED
SECURE ASSET SOLUTIONS
SERVICE CENTER REPAIRS
Experienced engineers and technicians on staff
at our full-service, in-house repair center
WE BUY USED EQUIPMENT
Sell your excess, underutilized, and idle used equipment
We also offer credit for buy-backs and trade-ins
www.artisantg.com/WeBuyEquipment
REMOTE INSPECTION
Remotely inspect equipment before purchasing with
our interactive website at www.instraview.com
LOOKING FOR MORE INFORMATION?
Visit us on the web at www.artisantg.com for more
information on price quotations, drivers, technical
specications, manuals, and documentation
Contact us: (888) 88-SOURCE | sales@artisantg.com | www.artisantg.com
SM
View
Instra

USER MANUAL AND SPECIFICATIONS
NI 9157/9159
Reconfigurable Embedded Chassis with Integrated MXI-Express (x1)
Figure 1. NI 9157/9159 Front Panel
4
6
2
5
1
C
C
V2
V1
INPUT
9-30 V
35W MAX
NO FPGA APP
USER FPGA1
USER FPGA2
USER FPGA3
P
USER FPGA1
USER FPGA2
USER FPGA3
POWER
USER FPGA1
USER FPGA2
USER FPGA3
LINK LINK
UPSTREAM
DOWNSTREAM
MXI-Express RIO
NI 915X
3
OFF
1. LEDs
2. Upstream Port
3. MXI-Express LINK LEDs
4. Downstream Port
5. Power Connector
6. DIP Switches
This document describes how to connect the NI 9157/9159 to a MXI-Express host and one or
more other chassis, and how to use the features of the NI 9157/9159. This document also
contains specifications for the NI 9157/9159.
Safety Guidelines
Operate the NI 9157/9159 only as described in this document.
Caution Do not operate the NI 9157/9159 in a manner not specified in this
document. Product misuse can result in a hazard. You can compromise the safety
protection built into the product if the product is damaged in any way. If the product
is damaged, return it to NI for repair.

Safety Guidelines for Hazardous Locations
The NI 9157/9159 is suitable for use in Class I, Division 2, Groups A, B, C, D, T4 hazardous
locations; Class I, Zone 2, AEx nA IIC T4 and Ex nA IIC T4 hazardous locations; and
nonhazardous locations only. Follow these guidelines if you are installing the NI 9157/9159 in
a potentially explosive environment. Not following these guidelines may result in serious
injury or death.
Caution Do not disconnect the power supply wires and connectors from the
controller unless power has been switched off.
Caution Do not disconnect I/O-side wires or connectors unless power has been
switched off or the area is known to be nonhazardous.
Caution Do not remove modules unless power has been switched off or the area is
known to be nonhazardous.
Caution Substitution of components may impair suitability for Class I, Division 2.
Caution For Division 2 and Zone 2 applications, install the system in an enclosure
rated to at least IP54 as defined by IEC/EN 60079-15.
Special Conditions for Hazardous Locations Use in Europe and
Internationally
The NI 9157/9159 has been evaluated as Ex nA IIC T4 Gc equipment under DEMKO
Certificate No. 07 ATEX 0626664X and is IECEx UL 14.0089X certified. Each device is
marked II 3G and is suitable for use in Zone 2 hazardous locations, in ambient temperatures
of 0 °C ≤ Ta ≤ 55 °C.
Caution You must make sure that transient disturbances do not exceed 140% of
the rated voltage.
Caution The system shall only be used in an area of not more than Pollution
Degree 2, as defined in IEC 60664-1.
Caution The system shall be mounted in an ATEX/IECEx-certified enclosure with
a minimum ingress protection rating of at least IP54 as defined in IEC/EN 60079-15.
Caution The enclosure must have a door or cover accessible only by the use of a
tool.
Electromagnetic Compatibility Guidelines
This product was tested and complies with the regulatory requirements and limits for
electromagnetic compatibility (EMC) stated in the product specifications. These requirements
and limits provide reasonable protection against harmful interference when the product is
operated in the intended operational electromagnetic environment.
2| ni.com | NI 9157/9159 User Manual and Specifications

This product is intended for use in industrial locations. However, harmful interference may
occur in some installations, when the product is connected to a peripheral device or test object,
or if the product is used in residential or commercial areas. To minimize interference with
radio and television reception and prevent unacceptable performance degradation, install and
use this product in strict accordance with the instructions in the product documentation.
Furthermore, any changes or modifications to the product not expressly approved by National
Instruments could void your authority to operate it under your local regulatory rules.
Special Conditions for Marine Applications
Some products are Lloyd’s Register (LR) Type Approved for marine (shipboard) applications.
To verify Lloyd’s Register certification for a product, visit ni.com/certification and search for
the LR certificate, or look for the Lloyd’s Register mark on the product.
Caution In order to meet the EMC requirements for marine applications, install the
product in a shielded enclosure with shielded and/or filtered power and input/output
ports. In addition, take precautions when designing, selecting, and installing
measurement probes and cables to ensure that the desired EMC performance is
attained.
What You Need to Install the NI 9157/9159
• NI 9157/9159 reconfigurable embedded chassis with integrated MXI-Express (x1)
• One of the following MXI-Express (x1) host systems:
– PXI system with MXI-Express device installed
– PC with MXI-Express PCI or PCIe device installed
– NI Industrial Controller
Note
The NI 9157/9159 requires a host system with a PCI Express clock that
complies with the PCI Express Specification. The NI 9157/9159 may not be
compatible with systems using noncompliant clocks, particularly clocks with
peak frequencies higher than 100 MHz. For more information about PCI
Express clock compatibility with the NI 9157/9159, go to ni.com/info and enter
the Info Code 915xclock.
• C Series I/O modules
• MXI-Express (x1) cable(s) up to 7 m long
• DIN rail mount kit (for DIN rail mounting only)
• Panel mount kit (for panel mounting only)
• Three M4 or number 8 panhead screws (for mounting the chassis without one of the listed
mounting kits)
• Number 2 Phillips screwdriver
NI 9157/9159 User Manual and Specifications | © National Instruments | 3

• Power supply
•MXI-Express (x1) Series User Manual
Note Visit ni.com/info and enter the Info Code rdsoftwareversion to
determine which software you need to use the NI 9157/9159.
Mounting the NI 9157/9159
You can mount the chassis horizontally on a 35 mm DIN rail or on a flat, vertical, metallic
surface such as a panel or wall. The maximum allowable ambient temperature for operation is
55 °C. Mounting the chassis in a different orientation or on a nonmetallic surface can reduce
the maximum allowable ambient temperature and can affect the typical accuracy of modules in
the chassis. The following figure shows the chassis mounted horizontally.
Figure 2. NI 9157/9159 Mounted Horizontally
Up
Measure the ambient temperature at each side of the chassis, 63.5 mm (2.5 in.) from the side
and 50.8 mm (2 in.) forward from the rear of the chassis.
Note For more information about typical accuracy specification for modules, go to
ni.com/info and enter the Info Code criotypical.
4| ni.com | NI 9157/9159 User Manual and Specifications

Caution Your installation must meet the following requirements for space and
cabling clearance:
• Allow 50.8 mm (2 in.) on the top and the bottom of the chassis for air
circulation.
• Allow 50.8 mm (2 in.) in front of modules for cabling clearance for common
connectors, such as the 10-terminal, detachable screw terminal connector.
Figure 3. NI 9157/9159, Bottom View with Dimensions
63.5 mm
(2.50 in.)
50.8 mm
(2 in.) 406.3 mm
(16 in.)
50.8 mm
(2 in.)
48.4 mm
(1.91 in.)
1
1
89.4 mm
(3.52 in.)
63.5 mm
(2.50 in.)
29 mm
(1.14 in.)
Cabling Clearance
50.8 mm (2 in.)
1. Measure ambient temperature here.
Figure 4. NI 9157/9159, Front View with Dimensions
51.7 mm
(2.04 in.)
28.0 mm
(1.10 in.)
4.1 mm
(0.16 in.)
Cooling Outline
50.8 mm (2 in.)
88.1 mm
(3.47 in.)
Cooling Outline
50.8 mm (2 in.)
36.4 mm
(1.43 in.)
132.6 mm
(5.22 in.)
165.1 mm
(6.50 in.)
NI 9157/9159 User Manual and Specifications | © National Instruments | 5

Figure 5. NI 9157/9159, Side View with Dimensions
18.7 mm
(0.74 in.)
44.1 mm
(1.74 in.)
69.5 mm
(2.74 in.)
51.4 mm
(2.02 in.)
68.2 mm
(2.68 in.)
The following sections contain instructions for the mounting methods. Before using any of
these mounting methods, record the serial number from the back of the chassis. You will be
unable to read the serial number after you have mounted the chassis.
Caution Make sure that no I/O modules are in the chassis before mounting it.
Mounting the Chassis on a DIN Rail
Use the DIN rail mounting method if you already have a DIN rail configuration or if you need
to be able to remove the chassis quickly. You can order the NI 9916 DIN rail mount kit if you
want to mount the chassis on a DIN rail. You need one clip for mounting the chassis on a
standard 35 mm DIN rail. Complete the following steps to mount the chassis on a DIN rail.
1. Fasten the DIN rail clip to the chassis using a number 2 Phillips screwdriver and three
M4 x 50 screws. NI provides these screws with the DIN rail mount kit. Tighten the
screws to a maximum torque of 1.3 N · m (11.5 lb · in.).
6| ni.com | NI 9157/9159 User Manual and Specifications

Figure 6. Installing the DIN Rail Clip on the NI 9157/9159
2. Insert one edge of the DIN rail into the deeper opening of the DIN rail clip.
Figure 7. One Edge of the DIN Rail Inserted in a Clip
3
2
1
1. DIN Rail Clip
2. DIN Rail
3. DIN Rail Spring
3. Press down firmly on the chassis to compress the spring until the clip locks in place on
the DIN rail.
Caution Make sure that no I/O modules are in the chassis before removing it
from the DIN rail.
NI 9157/9159 User Manual and Specifications | © National Instruments | 7

Mounting the Chassis on a Flat Surface Using the
NI 9907 Panel Mount Kit
Panel or wall mounting is the best method for applications that are subject to high shock and
vibration. You can use the NI 9907 panel mount kit to mount the NI 9157/9159 on a flat
surface. Complete the following steps.
1. Fasten the chassis to the panel mount kit using a number 2 Phillips screwdriver and six
M4 x 50 screws. NI provides these screws with the panel mount kit. Tighten the screws to
a maximum torque of 1.3 N · m (11.5 lb · in.).
Figure 8. Installing the Panel Mount Plate on the NI 9157/9159
Figure 9. Dimensions of NI 9157/9159 with Panel Mounting Plate Installed
25.3 mm
(0.99 in.)
9.5 mm
(0.37 in.)
25.7 mm
(1.01 in.)
457.2 mm
(18.0 in.)
438.2 mm
(17.25 in.)
17.4 mm (0.69 in.)
31.8 mm
(1.25 in.) 63.5 mm
(2.50 in.) 88.1 mm
(3.47 in.)
8| ni.com | NI 9157/9159 User Manual and Specifications

2. Fasten the panel mounting plate to the surface using the screwdriver and screws that are
appropriate for the surface. The maximum screw size is M4 or number 8.
Caution Make sure that no I/O modules are in the chassis before removing it from
the panel.
Mounting the Chassis Directly on a Flat Surface Using
the Mounting Holes
Panel or wall mounting is the best method for high shock and vibration applications. If you do
not have the NI 9907 panel mount kit and do not require the portability that the NI 9907
affords, you can mount the NI 9157/9159 directly on a flat surface using the three mounting
holes. Complete the following steps.
1. Align the chassis on the surface.
2. Fasten the chassis to the surface using three M4 or number 8 screws. NI does not provide
these screws with the chassis.
Figure 10. Mounting the NI 9157/9159 Directly on a Flat Surface
Caution Make sure that no I/O modules are in the chassis before removing it from
the panel.
Installing C Series Modules
The following figure shows the mechanical dimensions of C Series I/O modules.
Figure 11. C Series I/O Module, Front and Side View with Dimensions
88.1 mm
(3.47 in.)
70.7 mm
(2.78 in.)
22.9 mm
(0.90 in.)
NI 9157/9159 User Manual and Specifications | © National Instruments | 9

Complete the following steps to install a C Series I/O module in the chassis.
1. Make sure that no I/O-side power is connected to the I/O module. If the system is in a
nonhazardous location, the chassis power can be on when you install I/O modules.
2. Align the I/O module with an I/O module slot in the chassis. The module slots are labeled
1 to 14, left to right.
Figure 12. Installing an I/O Module in the Chassis
2
1
1. Insertion Groove
2. Latch
3. Squeeze the latches and insert the I/O module into the module slot.
4. Press firmly on the connector side of the I/O module until the latches lock the I/O module
into place.
5. Repeat these steps to install additional I/O modules.
Removing C Series Modules
Complete the following steps to remove a C Series I/O module from the chassis.
1. Make sure that no I/O-side power is connected to the I/O module. If the system is in a
nonhazardous location, the chassis power can be on when you remove I/O modules.
2. Squeeze the latches on both sides of the module and pull the module out of the chassis.
10 | ni.com | NI 9157/9159 User Manual and Specifications

Wiring Power to the Chassis
The NI 9157/9159 requires an external power supply that meets the specifications. The
NI 9157/9159 filters and regulates the supplied power and provides power for all of the I/O
modules. You must connect a power supply to at least one pair of V and C terminals.
Optionally, you can connect a second power supply to the other pair of V and C terminals. The
chassis draws power from the power supply with the higher voltage. The NI 9157/9159 has
one layer of reverse-voltage protection. Complete the following steps to connect a power
supply to the chassis.
1. Connect the positive lead of the power supply to the V1 or V2 terminal of the
COMBICON connector shipped with the NI 9157/9159.
2. Connect the negative lead of the power supply to one of the C terminals of the
COMBICON connector.
3. Optionally you can connect the positive lead of another power supply to the other V
terminal and the negative lead to one of the C terminals.
4. Install the COMBICON connector on the front panel of the NI 9157/9159.
Note The chassis draws power from either V1 or V2 depending on which
terminal has a higher voltage. It does not draw power from both terminals. The
chassis switches between V1 and V2 without affecting operation.
Note If you prefer for the chassis to draw power from one power supply, you
must ensure that the voltage of that power supply, measured at the chassis
power connector, is at least 500 mV higher than the voltage of the other power
supply.
Caution The C terminals are internally connected to each other. If you use
two power supplies, make sure that they share a common ground.
Caution The C terminals are internally connected to the body of the chassis to
prevent a faulty ground connection from causing the chassis ground to float. If
you reverse the input voltage, the positive input voltage is connected directly to
the chassis. The chassis has built-in reversed-voltage protection, but reversed
voltage can damage connected peripherals if the chassis ground is not reliably
connected to earth ground.
Caution Do not tighten or loosen the terminal screws on the power connector
while the power connector is plugged into the chassis or while the power
supply is on.
Connecting One or More NI 9157/9159 Chassis
to the MXI-Express Host System or a Target
Complete the following steps to connect one or more NI 9157/9159 chassis to a MXI-Express
host system or a target.
NI 9157/9159 User Manual and Specifications | © National Instruments | 11

1. Make sure the MXI-Express host system is set up and configured as described in the
MXI-Express (x1) Series User Manual.
2. If the MXI-Express host system is powered up, power it down.
3. If the NI 9157/9159 is powered up, power it down.
4. Use a MXI-Express (x1) cable to connect the MXI-Express host system to the Upstream
port of the first NI 9157/9159 in the chain.
5. Use a MXI-Express (x1) cable to connect the Downstream port of the first NI 9157/9159
to the Upstream port of the next NI 9157/9159 in the chain.
Note The maximum number of NI 9157/9159 chassis in a chain depends on
the system configuration. For example, a PXI system with an NI PXI-8196
controller can support four chassis per chain. Different types of systems may
support more or fewer chassis per chain. For more information about how
different system configurations can affect the maximum number of chassis in a
chain, go to ni.com/info and enter the Info Code 915xchain.
6. Power up all of the connected NI 9157/9159 chassis.
7. Power up the MXI-Express host system.
Note Refer to the MXI-Express (x1) Series User Manual for connectivity
options and supported host devices.
Caution All connected NI 9157/9159 chassis must have power connected
before the host system is powered up. The BIOS and OS of the host system
must detect all bus segments on the chassis side in order to configure the PCI
hierarchy. Powering connected chassis up or down while the host system is
running can cause system hangs and data corruption.
Caution Do not remove MXI-Express (x1) cables while power is connected.
Doing so can cause hangs or application errors. If a cable becomes unplugged,
plug it back in and reboot.
Chassis Powerup Options
The following table lists the reset options available for the NI 9157/9159. These options
determine how the chassis behaves when it is powered on in various conditions. Use the RIO
Device Setup utility to select reset options. Access the RIO Device Setup utility by selecting
Start»All Programs»National Instruments»NI-RIO»RIO Device Setup.
Table 1. Chassis Powerup Options
Powerup Option Behavior
Do Not Autoload VI Does not load the FPGA bit stream from flash memory.
Autoload VI on device powerup Loads the FPGA bit stream from flash memory to the
FPGA when the chassis powers on.
12 | ni.com | NI 9157/9159 User Manual and Specifications

If you want the NI 9157/9159 to autoload and run a VI at powerup, you must also configure
the VI to autoload before you compile it. For more information about autoloading VIs, refer to
the LabVIEW FPGA Module Help.
Checking MXI-Express LINK LEDs for Status
After powering on the chassis and host system, check the MXI-Express LINK LEDs to ensure
that all connected systems are linked and communicating properly. The MXI-Express LINK
LEDs of the NI 9157/9159 indicate the following:
Table 2. NI 9157/9159 MXI-Express LINK LED Indications
LINK LED Appearance Meaning
Off Chassis power is off.
Solid yellow Link is not established.
Solid green Link is established.
Blinking yellow PCI Express clock is incompatible with NI 9157/9159
Note For information about PCI Express clock compatibility with the
NI 9157/9159, go to ni.com/info and enter the Info Code 915xclock.
Powering Down the MXI-Express System
Always power down the host system before powering down any connected NI 9157/9159
chassis. When the host system is powered down, the order in which the NI 9157/9159 chassis
are powered down is not important.
Configuring DIP Switches
Figure 13. DIP Switches
NO FPGA APP
USER FPGA1
USER FPGA2
USER FPGA3
OFF
All of the DIP switches are in the OFF position when the chassis is shipped from National
Instruments.
NO FPGA APP Switch
Push the NO FPGA APP switch to the ON position to prevent a LabVIEW FPGA application
from loading at startup. The NO FPGA APP switch overrides the chassis powerup options
NI 9157/9159 User Manual and Specifications | © National Instruments | 13

described in the section on chassis powerup options. After startup you can download to the
FPGA from software regardless of switch position.
USER FPGA Switches
You can define the USER FPGA switches for your application. Use the LabVIEW FPGA
Module and NI-RIO software to define the USER FPGA switches to meet the needs of your
application. Refer to the LabVIEW Help for information about programming these switches.
Understanding LED Indications
Figure 14. NI 9157/9159 LEDs
P
USER FPGA1
USER FPGA2
USER FPGA3
POWER
USER FPGA1
USER FPGA2
USER FPGA3
POWER LED
The POWER LED is lit while the NI 9157/9159 is powered on. This LED is a bi-color LED.
When the chassis is powered from V1, the POWER LED is lit green. When the chassis is
powered from V2, the POWER LED is lit yellow.
USER FPGA LEDs
You can use the bi-color, yellow and green USER FPGA LEDs to help debug your application
or easily retrieve application status. Use the LabVIEW FPGA Module and NI-RIO software to
define the USER FPGA LEDs to meet the needs of your application. Refer to LabVIEW Help
for information about programming these LEDs.
NI 9157/9159 Specifications
The following specifications are typical for the range 0 °C to 55 °C unless otherwise noted.
Caution Do not operate the NI 9157/9159 in a manner not specified in this
document. Product misuse can result in a hazard. You can compromise the safety
protection built into the product if the product is damaged in any way. If the product
is damaged, return it to NI for repair.
MXI-Express
Maximum cable length 7 m
14 | ni.com | NI 9157/9159 User Manual and Specifications

Reconfigurable FPGA
NI 9157
FPGA type Virtex-5 LX85
Number of flip-flops 51,840
Number of 6-input LUTs 51,840
Number of DSP48 slices
(25 x 18 multipliers)
48
Embedded block RAM 3,456 kbits
NI 9159
FPGA type Virtex-5 LX110
Number of flip-flops 69,120
Number of 6-input LUTs 69,120
Number of DSP48 slices
(25 x 18 multipliers)
64
Embedded block RAM 4,608 kbits
Timebases 40 MHz, 80 MHz, 120 MHz, 160 MHz, or 200
MHz
Accuracy ±100 ppm (maximum)
Frequency dependent on jitter (peak-to-peak)
40 MHz 250 ps
80 MHz 422 ps
120 MHz 422 ps
160 MHz 402 ps
200 MHz 402 ps
Power Requirements
Caution You must use the NI 9157/9159 with a 9 VDC to 30 VDC output, UL
Listed limited power source (LPS) supply. The power supply must bear the UL
Listed and LPS marks. The power supply must also meet any safety and compliance
requirements for the country of use.
Recommended power supply 55 W, 30 VDC maximum
Voltage requirement 9 V to 30 V
NI 9157/9159 User Manual and Specifications | © National Instruments | 15

Chassis power consumption/dissipation
NI 9157
With no I/O modules 14.4 W (maximum)
With 14 I/O modules 30.7 W (maximum)
NI 9159
With no I/O modules 16.25 W (maximum)
With 14 I/O modules 32.7 W (maximum)
Note
The power consumption specifications in this document are maximum values for a
LabVIEW FPGA application compiled at 80 MHz. Your application power
requirements may be different. To calculate the power requirements of the
NI 9157/9159, add the power consumption/dissipation for the chassis and the I/O
modules you are using. Keep in mind that the resulting total power consumption is a
maximum value and that the NI 9157/9159 may require less power in your
application. For more information about the I/O module power requirements, refer to
the module operating instructions.
Physical Characteristics
Screw-terminal wiring
Gauge 0.2 mm 2 to 2.1 mm2 (24 AWG to 14 AWG)
copper conductor wire
Wire strip length 6 mm (0.24 in.) of insulation stripped from the
end
Temperature rating 85 °C
Torque for screw terminals 0.20 N · m to 0.25 N · m (1.8 lb · in. to
2.2 lb · in.)
Wires per screw terminal One wire per screw terminal
Connector securement
Securement type Screw flanges provided
Torque for screw flanges 0.3 N · m to 0.4 N · m (2.7 lb · in. to
3.5 lb · in.)
Weight 2,231 g (78.7 oz)
Safety Voltages
Connect only voltages that are within the following limits:
V terminal to C terminal 30 VDC maximum, Measurement Category I
16 | ni.com | NI 9157/9159 User Manual and Specifications

Measurement Category I is for measurements performed on circuits not directly connected to
the electrical distribution system referred to as MAINS voltage. MAINS is a hazardous live
electrical supply system that powers equipment. This category is for measurements of voltages
from specially protected secondary circuits. Such voltage measurements include signal levels,
special equipment, limited-energy parts of equipment, circuits powered by regulated low-
voltage sources, and electronics.
Caution Do not connect the NI 9157/9159 to signals or use for measurements
within Measurement Categories II, III, or IV.
Note Measurement Categories CAT I and CAT O are equivalent. These test and
measurement circuits are not intended for direct connection to the MAINS building
installations of Measurement Categories CAT II, CAT III, or CAT IV.
Hazardous Locations
U.S. (UL) Class I, Division 2, Groups A, B, C, D, T4;
Class I, Zone 2, AEx nA IIC T4
Canada (C-UL) Class I, Division 2, Groups A, B, C, D, T4;
Class I, Zone 2, Ex nA IIC T4
Europe (ATEX) and International (IECEx) Ex nA IIC T4 Gc
Safety and Hazardous Locations Standards
This product is designed to meet the requirements of the following electrical equipment safety
standards for measurement, control, and laboratory use:
• IEC 61010-1, EN 61010-1
• UL 61010-1, CSA 61010-1
• EN 60079-0:2012, EN 60079-15:2010
• IEC 60079-0: Ed 6, IEC 60079-15; Ed 4
• UL 60079-0; Ed 5, UL 60079-15; Ed 3
• CSA 60079-0:2011, CSA 60079-15:2012
Note For UL and other safety certifications, refer to the product label or the Online
Product Certification section.
Electromagnetic Compatibility
This product meets the requirements of the following EMC standards for electrical equipment
for measurement, control, and laboratory use:
• EN 61326 (IEC 61326): Class A emissions; Industrial immunity
• EN 55011 (CISPR 11): Group 1, Class A emissions
• AS/NZS CISPR 11: Group 1, Class A emissions
NI 9157/9159 User Manual and Specifications | © National Instruments | 17

• FCC 47 CFR Part 15B: Class A emissions
• ICES-001: Class A emissions
Note For EMC declarations and certifications, and additional information, refer to
the Online Product Certification section.
Note For EMC compliance, operate this product according to the documentation.
CE Compliance
This product meets the essential requirements of applicable European Directives, as follows:
• 2014/35/EU; Low-Voltage Directive (safety)
• 2014/30/EU; Electromagnetic Compatibility Directive (EMC)
• 94/9/EC; Potentially Explosive Atmospheres (ATEX)
Online Product Certification
Refer to the product Declaration of Conformity (DoC) for additional regulatory compliance
information. To obtain product certifications and the DoC for this product, visit ni.com/
certification, search by model number or product line, and click the appropriate link in the
Certification column.
Shock and Vibration
To meet these specifications, you must panel mount the system.
Operating vibration
Random (IEC 60068-2-64) 5 grms, 10 Hz to 500 Hz
Sinusoidal (IEC 60068-2-6) 5 g, 10 Hz to 500 Hz
Operating shock (IEC 60068-2-27) 30 g, 11 ms half sine; 50 g, 3 ms half sine;
18 shocks at 6 orientations
Environmental
Refer to the manual for the chassis you are using for more information about meeting these
specifications.
Note Refer to the mounting instructions in the Mounting the NI 9157/9159 section
of this document. Failure to follow the mounting instructions in that section can
cause temperature derating. For more information about mounting configurations
18 | ni.com | NI 9157/9159 User Manual and Specifications

and temperature derating, go to ni.com/info and enter the Info Code
criomounting.
Operating temperature (IEC 60068-2-1,
IEC 60068-2-2)
0 °C to 55 °C
Storage temperature
(IEC 60068-2-1, IEC 60068-2-2)
-40 °C to 85 °C
Ingress protection IP40
Operating humidity (IEC 60068-2-78) 10% RH to 90% RH, noncondensing
Storage humidity (IEC 60068-2-78) 5% RH to 95% RH, noncondensing
Pollution Degree 2
Maximum altitude 2,000 m
Indoor use only.
Environmental Management
NI is committed to designing and manufacturing products in an environmentally responsible
manner. NI recognizes that eliminating certain hazardous substances from our products is
beneficial to the environment and to NI customers.
For additional environmental information, refer to the Minimize Our Environmental Impact
web page at ni.com/environment. This page contains the environmental regulations and
directives with which NI complies, as well as other environmental information not included in
this document.
Waste Electrical and Electronic Equipment (WEEE)
EU Customers At the end of the product life cycle, all NI products must be
disposed of according to local laws and regulations. For more information about
how to recycle NI products in your region, visit ni.com/environment/weee.
电子信息产品污染控制管理办法(中国 RoHS)
中国客户 National Instruments 符合中国电子信息产品中限制使用某些有害物
质指令(RoHS)。关于 National Instruments 中国 RoHS 合规性信息,请登录
ni.com/environment/rohs_china。(For information about China RoHS
compliance, go to ni.com/environment/rohs_china.)
Worldwide Support and Services
The NI website is your complete resource for technical support. At ni.com/support, you have
access to everything from troubleshooting and application development self-help resources to
email and phone assistance from NI Application Engineers.
NI 9157/9159 User Manual and Specifications | © National Instruments | 19
This manual suits for next models
1
Table of contents
Other NI Chassis manuals
Popular Chassis manuals by other brands
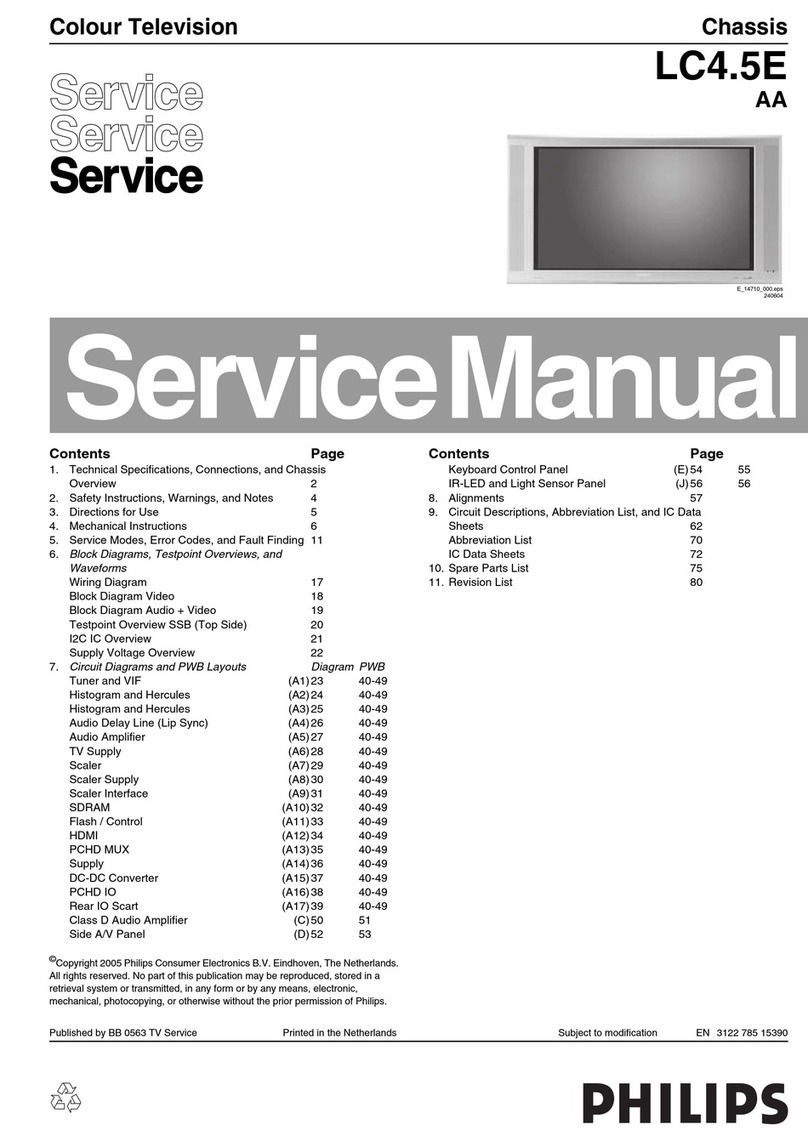
Philips
Philips LC4.5E Service manual

Marvin
Marvin Geotest GT7700 user guide
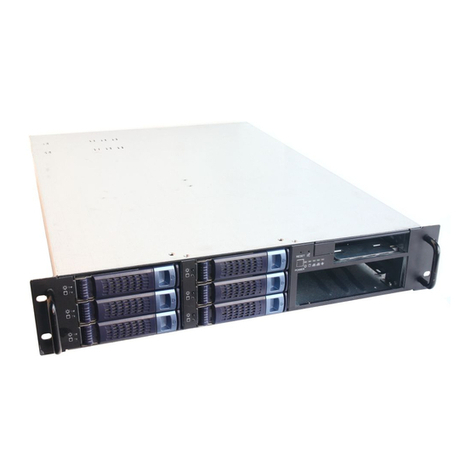
Chenbro
Chenbro Chassis RM21400 Installation reference guide
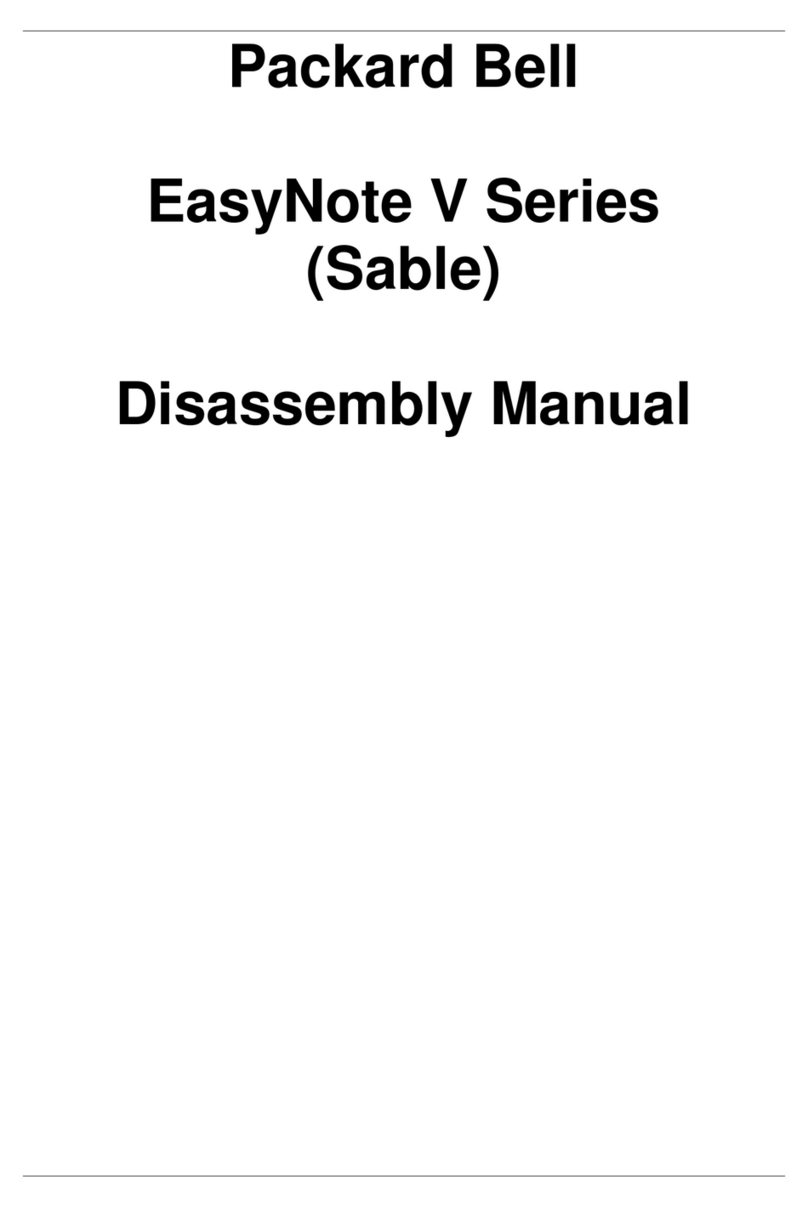
Packard Bell
Packard Bell EasyNote V Series Disassembly manual
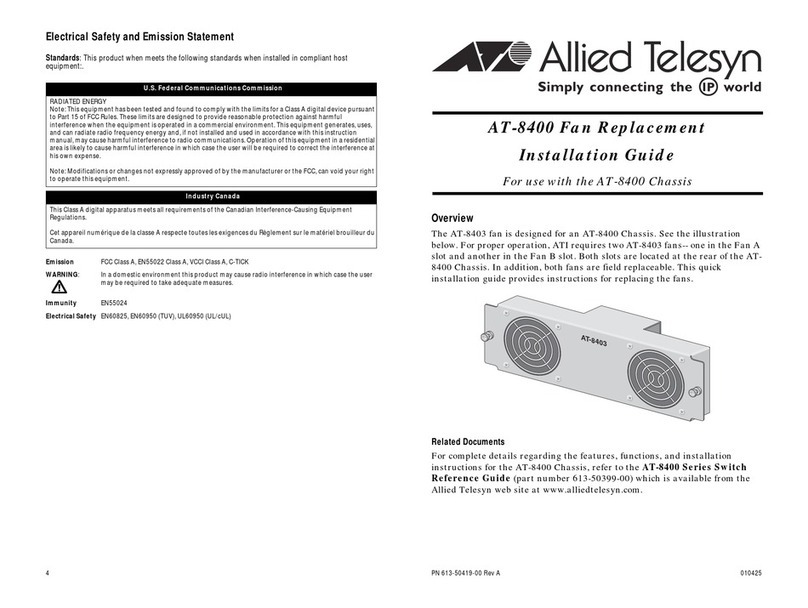
Allied Telesis
Allied Telesis AT-8400 Series installation guide
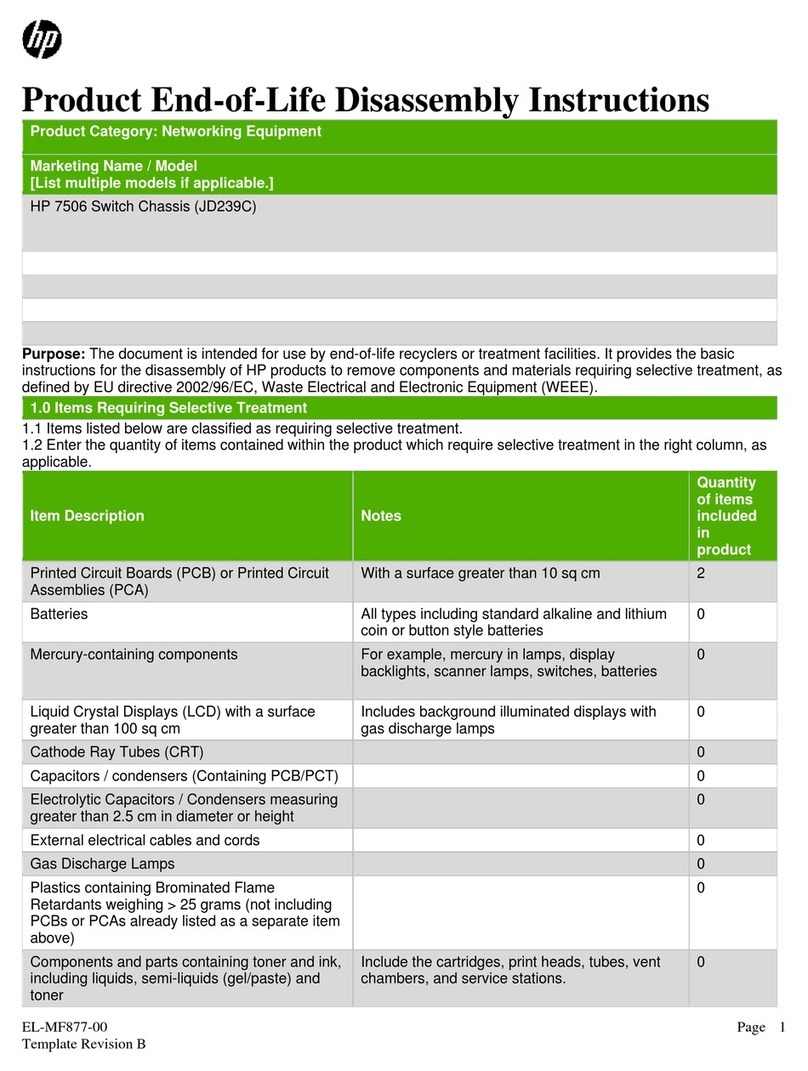
HP
HP 7506 Product End-of-Life Disassembly Instructions