PERCo IRP-01 Installation manual


Reader Post
IRP-01
Certificate and Operation Manual
TC RU C-RU.МЛ02.В.00274
ТУ 4372-050-88226999-2014

CONTENTS
1General information.....................................................................................................3
2Technical specifications ..............................................................................................4
3Delivery set..................................................................................................................4
4Product description......................................................................................................5
4.1 Design ...................................................................................................................5
4.2 Operating principle ................................................................................................6
4.3 Data transmitting via Wiegand interface................................................................7
5Configuration...............................................................................................................8
5.1 Operation of reader in RS-485 mode.....................................................................8
5.1.1 Selection of reader number............................................................................8
5.1.2 Indication........................................................................................................9
5.2 Operation of reader in Wiegand mode.................................................................10
5.2.1 Indication setting ..........................................................................................10
5.2.2 Changing the format of output data..............................................................10
6Safety requirements ..................................................................................................11
6.1 Safe installation...................................................................................................11
6.2 Safe operation.....................................................................................................11
7Installation procedure................................................................................................12
7.1 Features of installation ........................................................................................12
7.2 Tools and equipment required for installation......................................................12
7.3 Required cables...................................................................................................12
7.4 Assembly sequence ............................................................................................13
8Troubleshooting.........................................................................................................15
9Perco warranty..........................................................................................................15

IRP-01 Reader Post
3
1 GENERAL INFORMATION
IRP-01 reader post is designed for reading and interpretation of proximity card identifier
and for transferring of identifier to ACS controller. The reader post is made in the form of
stainless steel cylindrical post equipped with proximity card reader and LCD indicating
operation modes of ACS controller.
IRP-01 reader post is designed as an up-market model to fit the highest requirements for
design and comfort (governmental offices, banks, administrative buildings, sport centers,
airports, etc.).
The reader post, with regard to resistance to environmental exposure, conforms to
category NF4 (operation in premises with climate control) according to GOST 15150-69.
Operation of the reader is allowed at ambient air temperature from +1°Сto +40°Сand at
relative air humidity of up to 80% at +25°С.
The reader has the marking on the inner side of the housing. The marking contains the
product name, the model abbreviation, the date of manufacture, the serial number.
The reader is packed in a cardboard box that protects it from being damaged during
transportation and storage.
Overall dimensions of the box (L × W × H)............................................1120×140×130, mm
Weight of the box................................................................................................... max. 7 kg
The reader in the original package should be transported in closed freight containers or
other closed type cargo transport units.
Storage of the reader is allowed in dry indoor facilities at the ambient air temperature from
+1°Сto +40°Сand relative air humidity of up to 80% at +25°С.
During storage and transportation the boxes can be stacked no more than 5 layers high.
After transportation or storage at temperatures below zero or at high air humidity, prior to
installation the reader must be kept in the original package for no less than 24 hours
indoors under normal climate conditions prior to installation.
Due to continuous improvement of products the Manufacturer reserves the right to modify,
without notice, the product design not aggravating its technical specifications.

Certificate & Operation Manual
4
2 TECHNICAL SPECIFICATIONS
Rated operating voltage1
Operating voltage limits .................................................................................. 10.8–14VDC
......................................................................................... 12VDC
Consumption current ...................................................................................... max. 150 mA
Power consumption .............................................................................................. max. 2 W
Card reading distance at the rated operating voltage for different card types:
HID ProxCard II cards ................................................................................. min. 6 cm
EM-Marin cards ........................................................................................... min. 7 cm
Controller connection interface2
Distance between reader and controller ............................................................. max. 40 m
............................................................... RS-485, Wiegand
Reader post weight .............................................................................................. max. 5 kg
Reader post dimensions (see Fig. 1) .................................................... 1025×107×107 mm
Mean lifetime ........................................................................................................... 8 years
Electric shock protection class ........................................... III under GOST R IEC 335-1-94
3 DELIVERY SET
Reader post ....................................................................................................................... 1
Mounting base ................................................................................................................... 1
S2 allen key ....................................................................................................................... 1
Package ............................................................................................................................. 1
Certificate and Operation Manual ...................................................................................... 1
Additional mounting tools:
The following equipment can be supplied optionally on request:
PFG IR 8-20 anchor («SORMAT», Finland) ...................................................................... 4
1As a power supply it is recommended to use DC source with linear voltage stabilization and
output pulsation amplitude max. 50 mV.
2Depends on position of switch №1 SA1.

IRP-01 Reader Post
5
4 PRODUCT DESCRIPTION
4.1 Design
Reader post consists of stainless steel tube with reader board and LCD. Delivery set also
contains mounting base that the reader post housing is attached to.
The reader is equipped with integrated sound indicator. Code reading is confirmed by a
short sound signal.
Figure 1. IRP-01 overall view and dimensions

Certificate & Operation Manual
6
The board of the reader is shown on Fig. 2.
Figure 2. The board of the reader
The board contains:
ХТ1 –connectors for power cables.
ХТ3 – connector for connection via RS-485 interface.
ХТ4and ХТ5 –connectors for connection via Wiegand interface.
ХР5– “disconnection of EOL resistor” connector for RS-485.
SA1 – DIP-switch for reader setting.
4.2 Operating principle
Readers provide code reading from Proximity identifiers with operation frequency 125 kHz
(hereinafter – the identifier) produced by HID Corporation, type: ProxCard II, ISOProx II
(standard formats HID: 26 bit (H10301), 37 bit (H10302, H10304)), and also IL-05ELR
and ЕM4100/4102 identifiers produced by EM-Microelectronic-Marin SA.
Code reading is performed when the identifier is presented to the reader. Maximum
operating distance between the identifier and the reader depends on the type of the
identifier. The identifier can be placed inside pocket, wallet or any other radio transparent
container (cover).
Figure 3. Reader operation
When switched on the reader radiates low frequency (125 kHz) electromagnetic field.
Caught in this field the identifier is activated and starts transmitting individual encoded
signal that is received by the reader.

IRP-01 Reader Post
7
Reader transforms the received signal in accordance with an external device interface and
sends it to controller of external device via RS-485 or Wiegand interfaces.
Data is transmitted to the external controller at one time, asynchronously, at the moment of
first positive signal receipt from identifier. Repeated data transfer is possible not earlier
than 200 ms after identifier leaves stable reception zone.
4.3 Data transmitting via Wiegand interface
Two wires are used for transmission: «data 0» and «data 1». When logic level «0» occurs
on one of the wires it signals the presence of bit with appropriate value in coded mark.
Time response characteristics of output data format:
Duration of data pulse................................................................................... 100 mcs
Pulse-time...........................................................................................................1 ms
All bytes are transmitted with high-order bits forward.
Figure 4. Formation of output reader signals and their diagrams
The length of the coded mark depends on the output data format set at assembly and can
be either fixed or specified by data dimension received from identifier.
Following rules are applied when there is difference between coded mark received from
identifier and the output coded mark:
- If the input coded mark from identifier is longer than output mark the excessive high-
order bits are truncated.
- If the input coded mark from identifier is shorter than output mark the missing high-
order bits are padded with zeros.
The structure of coded mark and order of parities in it for fixed length formats are
presented in the following Figures:
•The identifier encoded signal includes the even number of bits (N/2 – integer):

Certificate & Operation Manual
8
•The identifier encoded signal includes the uneven number of bits (N/2 – non
integer):
The structure of output coded mark in Wiegand 26 (H10301) format is presented in Figure:
1 – Control bit (corresponds with the even parity for the next 12 bit data)
2 – Byte code
3 – High-order byte of card number
4 – Low-order byte of card number
5 – Control bit (corresponds with the odd parity for the previous 12 bit data).
5 CONFIGURATION
The interface of the reader is chosen with the use of switch №1 of DIP-switch SA1, located
on the board of the reader (see Fig. 2):
•ON – connection to RS-485 interface,
•OFF – connection Wiegand interface.
5.1 Operation of reader in RS-485 mode
To operate the reader in RS-485 mode the switch №1 of DIP-switch SA1, located on the
board of the reader (see Fig. 2), shall be set in ON position. When the reader is connected
via RS-485 interface, it can be used as an external reader for PERCo Web controllers.
5.1.1 Selection of reader number
When readers are connected to RS-485 interface, they need to have different numbers
(switch 2) to determine the direction of passage. Binding of reader number to passage
direction is made by computer software.
The number is selected with the use of switch 2 of DIP-switch SA1, located on the board of
controller (see Fig. 2), in such case switch 1 shall be set in ON position. Number of reader
is determined according to Table 1.
Table 1. Setting of reader number on DIP-switch SA1
Reader number
Switch
1
2
Reader 1
ON
ON
Reader 2
ON
OFF

IRP-01 Reader Post
9
5.1.2 Indication
When operated with PERCo Web controllers, LCD of the reader show the following
indication of controller operation modes:
“Control” mode indication – general
background and an appearing hand with
a card, showing that it is necessary to
present a card
“Open” mode indication, and also the
response to the presentation of
authorized card – moving green arrow.
“Closed” mode indication, and also the
response to the presentation of non-
authorized card –
STOP inscription with changing color of
letters.
Indication of waiting for verification –
hourglass.

Certificate & Operation Manual
10
5.2 Operation of reader in Wiegand mode
To operate the reader in Wiegand mode the switch 1 of DIP-switch SA1, located on the
board of the reader (see Fig. 2), shall be set in OFF position.If the reader is connected to
Wiegand interface, it can be used an external reader for ACS controllers.
5.2.1 Indication setting
During the operation of ACS controllers LCD shows the same indication as depicted in
Section 5.1.2. There are two possible options to control indication: «single line» and
«double line». The option is selected with the use of switch 2 of DIP-switch SA1, located
on the board of the reader (see Fig. 2), in such case switch 1 shall be set in OFF position.
Indication control option is determined according to Table 2.
Table 2. Indication setting on DIP-switch SA1
Indication option
Option
1
2
«double line»
OFF
ON
«single line»
OFF
OFF
Control signals in case of «single line» mode are transmitted via the line that is connected
to Led R contact (see Fig. 7) of XT5 connector on the reader board (see Fig. 2). In case of
«double line» mode control signals are transmitted via two lines connected to Led R, Led
Gcontacts of XT5 connector on the reader board. To control sound indication of the
reader with ACS controller it is necessary to connect the wire that is connected to Beep
contact of XT5 connector with the negative terminal of power supply unit. Indication of
reader is given in 3 according to control signals received by the reader.
Table 3. Indication of reader
Signal level on
control line
Indication of reader
Led R
Led G
«double line»
«single line»
0
0
Waiting for card presentation (hand with card)
Access granted
(moving green arrow)
0
HZ
Access granted (moving green arrow)
HZ
0
Access restricted (STOP inscription)
Access restricted
(STOP inscription)
HZ
HZ
Waiting for card presentation (hand with card)
0 – control line is connected to negative terminal of power supply unit;
HZ – high resistance on the control line (the line is not connected to negative
terminal of power supply unit)
5.2.2 Changing the format of output data
Attention!
Switching o
ver the reader into Wiegand formats does not prevent it from reading
cards of other formats and delivering read code to an output of a reader in the set
format.
Wiegand output data format is selected with the use of switches 3 and 4 of DIP-switch
SA1, located on the board of the reader (see Fig. 2), in such case switch 1 shall be set in
OFF position. Wiegand format of the reader is determined according to Table 4.

IRP-01 Reader Post
11
Table 4. Selection of output data format of the reader on DIP-switch SA1
Output data format
Switch
1
3
4
Wiegand 26
OFF
ON
ON
Wiegand 37
OFF
ON
OFF
Wiegand 42
OFF
OFF
ON
Wiegand
OFF
OFF
OFF
6 SAFETY REQUIREMENTS
6.1 Safe installation
Attention!
•
All work should be carried out only when the power is off and power supply is
disconnected from the mains.
•Study the Operation manual thoroughly before beginning the installation work.
•Reader installation must be carried out by a professional circuit installer.
•Only serviceable tools should be used.
•Observe general safety requirements for use of electrical equipment when laying
cables.
6.2 Safe operation
It is forbidden!
•To use the reader post if the supply voltage differs from the one given
in Section
“Technical specifications” of the Operation manual.
•To use the reader post
operation in conditions that don't conform to those given
in Section “General information”.
•
To use substances for cleaning of the device that may cause mechanical
damage or corrosion of the surfaces.
•To
hit any elements of the device so as to prevent their mechanical
deformation.

Certificate & Operation Manual
12
7 INSTALLATION PROCEDURE
7.1 Features of installation
The following factors must be considered:
•Readers shall be installed close to the operating device;
•Close electric interference sources shorten card reading distance, therefore reader
must be installed at min. 1 m whilst its cable laid at min. 30 cm distance from
computer monitors, electric generators and motors, ac relays, thyristor light
regulators, ac lines, computer and telephone signals;
•The reader shall be provided with reliable electrical grounding;
•Distance between two readers should be min. 30 cm.
It is recommended:
•to mount the device on steady and level concrete (grade 400 or higher,
strength class B22,5), stone or similar foundations at least 150 mm thick;
•to apply reinforcing elements (300×300×150 mm) for installation on less
steady foundation;
•to control vertical and flatness alignment of the device with a level during
installation; maximum allowable flatness deviation is 1,5 mm;
•to use anchors produced by «SORMAT» for installation.
7.2 Tools and equipment required for installation
•1.2÷1.5kW hammer drill;
•Ø16 mm hard-alloy drill bits;
•Ø 5 mm hard-alloy drill bits;
•S6 allen key;
•S5 allen key;
•S2 allen key (included in the delivery set);
•hobby knife;
•level;
•2 m measuring tape.
7.3 Required cables
The reader is connected to a controller via RS-485 interface with a twisted pair cable (type
F/UTP2-Cat5e); A and B signal lines shall be in the same pair.
The reader is connected to a controller via Wiegand interface with a shielded cable (type
CABS8/EC, 8C.SEC-SC, cross-section 24AWG – 18AWG (0,2 - 0,8 mm2)). Do not use
twisted pair cables.
Power source unit is connected to the reader with PVC-insulated cable 2×0,75.
Note:
Maximum distance between the reader and the controller depends on the cross-
section of the cable you use. In case of use of standard cables given here the
flawless operation of the reader is guaranteed at the maximum distance of 40 m.

IRP-01 Reader Post
13
7.4 Assembly sequence
Follow this sequence during installation of the reader:
1. Unpack the box with equipment, check carefully the delivery set.
2. Choose the place for installation in accordance with recommendations given in
Section 7.1.
3. Mark the mounting holes in the floor as per 5, and also mark electrical conduit for
the cable from ACS controller to the reader post.
Note:
Material, section shape, dimensions, laying method (on surface, und
er surface,
combined), location at the entrance and other specifications of the electrical conduit
are defined by the user
according to features of the entrance, equipment location
and other factors.
4. Prepare electrical conduit and mounting holes for the reader post. Insert anchors,
so that their shells would not obtrude out of the floor surface.
5. Remove carefully “glass-LCD-board” unit. To do this use S2 allen key (included in
the delivery set), unscrew two countersunk screws located on the upper part of the
housing that fix “glass-LCD-board” unit to the metal tube of the housing (see Fig. 1).
6. Select reader interface with the use of switch №1 of the DIP-switch SA1, located on
the board of the reader (see Fig. 2). ON position – RS-485 interface, OFF position –
Wiegand interface.
6.1.RS-485 interface.
•Set the reader number with the use of switch №2 DIP-switch SA1, located
on the board of the reader (see Fig. 2). ON position – reader №1, OFF
position – reader №2 (see Section 5.1.1).
•If there are several devices connected to the controller the communication
line is connected to all devices consistently. If the reader is not used as a
final device on the line, it is necessary to disconnect the end-of-line resistor
– to do it remove the jumper from XP5 connector block on the board (see
Fig. 2). Please note that in this case it will be necessary to connect end-of-
line resistors on the ends of communication line of RS-485 interface.
6.2.Wiegand interface.
•Set the indication control variant with the use of switch №2 of DIP-switch
SA1, located on the board of the reader (see Fig. 2). ON position – «double
line», OFF position - «single line» (see Section 5.2.1).
•Select the output data format with the use of switches №3 and №4 of DIP-
switch SA1, located on the board of the reader (see Fig. 2). The position of
switches is determined in accordance with Table 4 (see Section 5.2.2).
7. Disassemble the mounting base from the post housing. To do so use S5 allen key
turn two screws clockwise that fix the mounting base to the post housing. The
screws are accessed through the holes located in the lower part of the housing (see
Fig. 1).
8. Drag the cable through the central hole in the mounting base with 16 mm diameter
(see Fig. 5).
9. Fix the mounting base on the installation surface with anchor bolts. Control vertical
alignment with the level during the installation. (Use S6 allen key to fix the mounting
base in case you are using PFG IR 8-20 anchor bolts produced by «SORMAT»).
10.Lay the connecting cable in the electrical conduit and inside the reader post.

Certificate & Operation Manual
14
11.Install the reader post on the mounting base and fix it. To do so use S5 allen key
turn two screws counterclockwise that fix the mounting base to the metal tube of
the post (see Fig. 1). The screws are accessed through the holes located in the
lower part of the housing.
12.Lay the cable inside the reader post, fix it and connect it to the board of the reader
according to connection layouts shown on Fig. 6 or Fig. 7.
13.Install carefully “glass-LCD-board” unit back and fix it with two M4 screws, located in
the upper part of the housing (see Fig. 1). S2 allen key is included in the delivery
set, screws shall screwed inside so that that they would not obtrude out of the
housing.
14.Connect the cable to the PERCo Web controller or ACS according to layout given
on Fig. 6 or Fig. 7.
Figure 5. Mounting hole pattern for IRP-01 installation
Figure 6. Connection layout for RS-485 interface of PERCo Web controller

IRP-01 Reader Post
15
Figure 7. Connection layout for Wiegand interface of ACS
8 TROUBLESHOOTING
Possible faults to be corrected by the user themselves are listed in Table 5:
Table 5. Troubleshooting guide
Fault
Most plausible cause
Remedy
When powered-up, the reader does not
respond to a presented card
No supply voltage on the
reader
Check connection of the
reader to the power source
The reader responds to the presented
card, but there are no events and
indication on this reader
No connection with the
controller via RS-485 or
Wiegand
Check connection and
distribution of RS-485
In an unlikely event of other faults please consult the PERCo Technical Support
Department.
9 PERCO WARRANTY
PERCo (the Manufacturer) warrants that the IRP-01 reader post complies with applicable
statutory safety requirements and electromagnetic compatibility provided that the
instructions on storage, installation and operation, given in the Certificate & Operation
Manual, are observed.
The warranty period is 5 (five) years commencing from the date of sale. Should there be
no date of sale on the warranty card, the warranty period shall commence from the date of
manufacture specified in the Certificate and on the Product label.
In the post-warranty period the replacement parts/components are warranted to be free
from defects in material or workmanship for a period of 3 (three) months from the date of
shipment of the repaired/replaced Product to the Customer.

Certificate & Operation Manual
16
All claims with regard to quantity, completeness and defects to appearance of the Product
delivered are accepted by the Manufacturer in writing within no more than 5 (five) working
days after the products are received by the Customer. In case of failure to meet the
abovementioned deadline no claims are accepted.
The Warranty does not cover:
•products, parts and components with:
- external mechanical damages resulting in the Product’s fault;
- defects resulting from Customer's improper testing, operation, installation,
maintenance, modification, alteration, or adjustment;
- damages due to force majeure circumstances (natural disasters, vandalism etc.)
or defects as a result of external circumstances (power surges, electric discharge,
etc);
•fuses, accumulators, galvanic elements and other components, replacement of which
is performed by the Customer in accordance with the Product’s in-line
documentation.
To the maximum extent permitted by the acting law, the Manufacturer does not incur a
liability for any direct or indirect losses of the Customer, including but not limited to loss of
profit or data, losses caused by idle period, missed profit, and etc related to use or
impossibility to use products and software, including possible software errors and failures.
Within the warranty period the products are repaired free of charge at the Manufacturer’s
site. The Manufacturer reserves the right to repair failed product or replace it with an
operational one. Time of repair is specified at the moment the Product is accepted for
repair. Transportation cost to and back from the place of repair shall be borne by the
Customer.
In order to shorten the repair time the Customer must inform the Manufacturer’s Technical
Support Department (the TSD) of the problem with the Product’s operation and/or about
the origin of the fault by submitting a filled-in Technical Support Form by e-mail, fax or via
the Manufacturer’s website or communicate directly a specialist of the TSD.
The Manufacturer reserves the right not to accept the Product for repair from the Customer
who failed to submit the Technical Support Form.
The Manufacturer’s warranty obligations don’t cover attendance by the experts of a
Customer and maintenance of any Product on site
If in the course of the examination taken by the Manufacturer of the Product or its
parts/components believed to be faulty, no faults have been detected, the Customer is
responsible for compensation of the Manufacturer’s expenses related to the examination.
Apart from the warranties mentioned above the Manufacturer does not provide any other
warranties with regard to compatibility of a Product purchased with software or products
produced by other manufacturers as well as any warranties that this Product will fit for the
purposes not stipulated in the Product’s in-line documentation.
The warranty does not provide for any claims with regard to the technical specifications of
the Product in case they are in compliance with those stated by the Manufacturer. The
Manufacturer does not guarantee that the Product purchased will meet Customer’s
requirements and expectations.
PLEASE NOTE THAT PERCo PRODUCES TECHNICALLY
SOPHISTICATED PRODUCTS THAT, IF NOT FAULTY,
CANNOT BE RETURNED BACK IF BY SOME REASON
THE CUSTOMER DEEMS THEM UNSATISFACTORY

17
WARRANTY CARD
IRP-01 reader post
Serial number 5 1 7
Date of manufacture « » ________________201__
Quality control seal _____________________________________________
Date of sale « » ________________201__
____________________________________
(signature, seal)
Cutting line
Warranty repair coupon
IRP-01 reader post
Serial number 5 1 7
Date of manufacture « » ________________201__
Quality control seal ______________________________________________
Date of sale « » ________________201__
____________________________________
(signature, seal)


Table of contents
Other PERCo Card Reader manuals
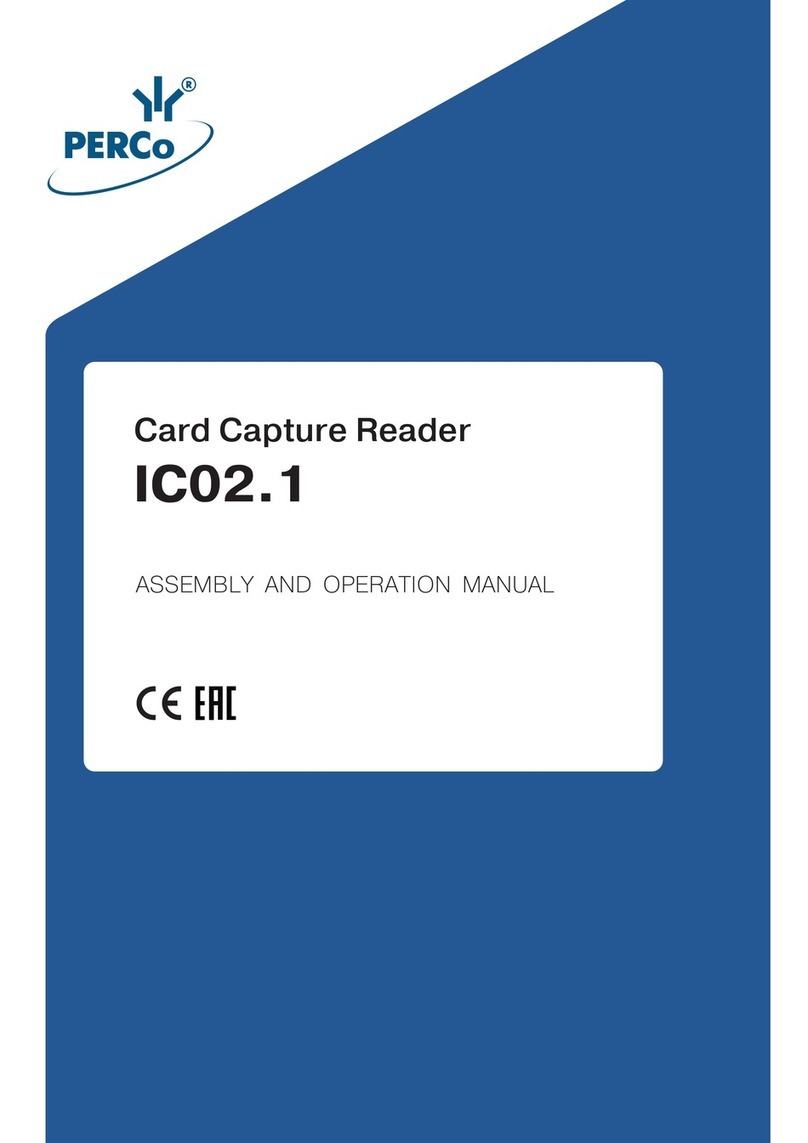
PERCo
PERCo IC02.1 Installation and operating instructions

PERCo
PERCo IR-03.1 Installation and operating instructions

PERCo
PERCo IR-10 User manual
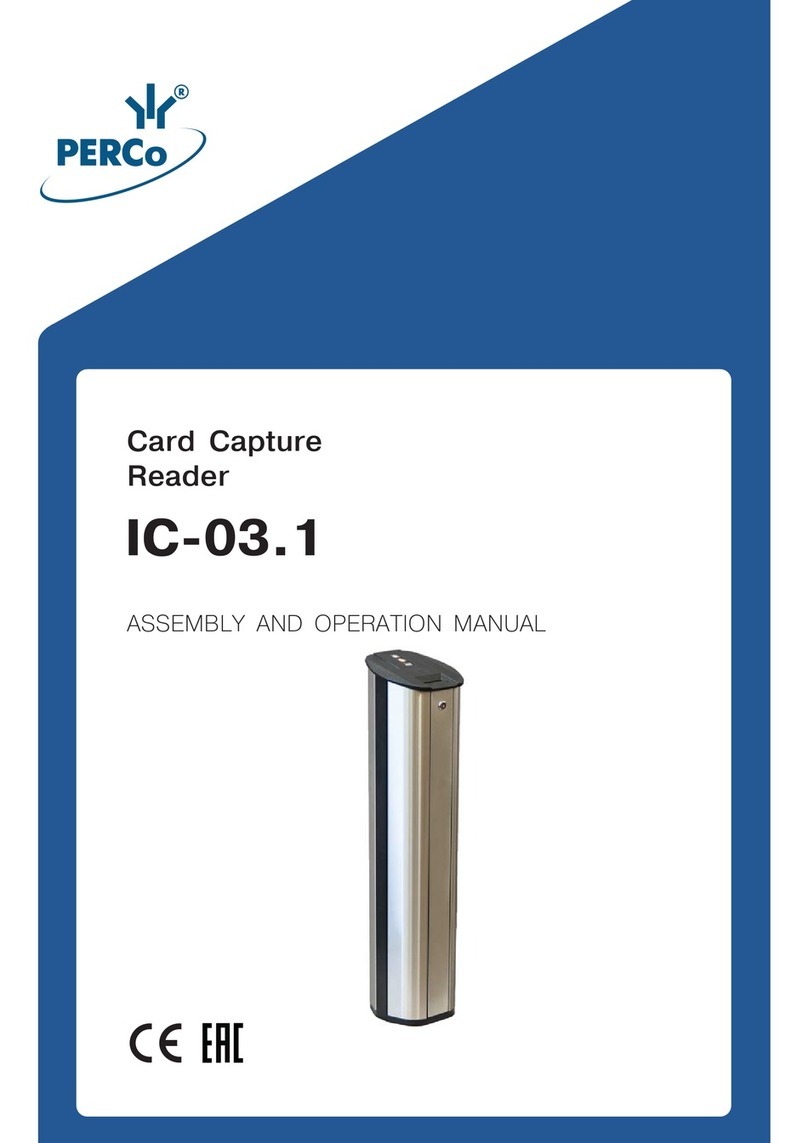
PERCo
PERCo IC-03.1 Installation and operating instructions
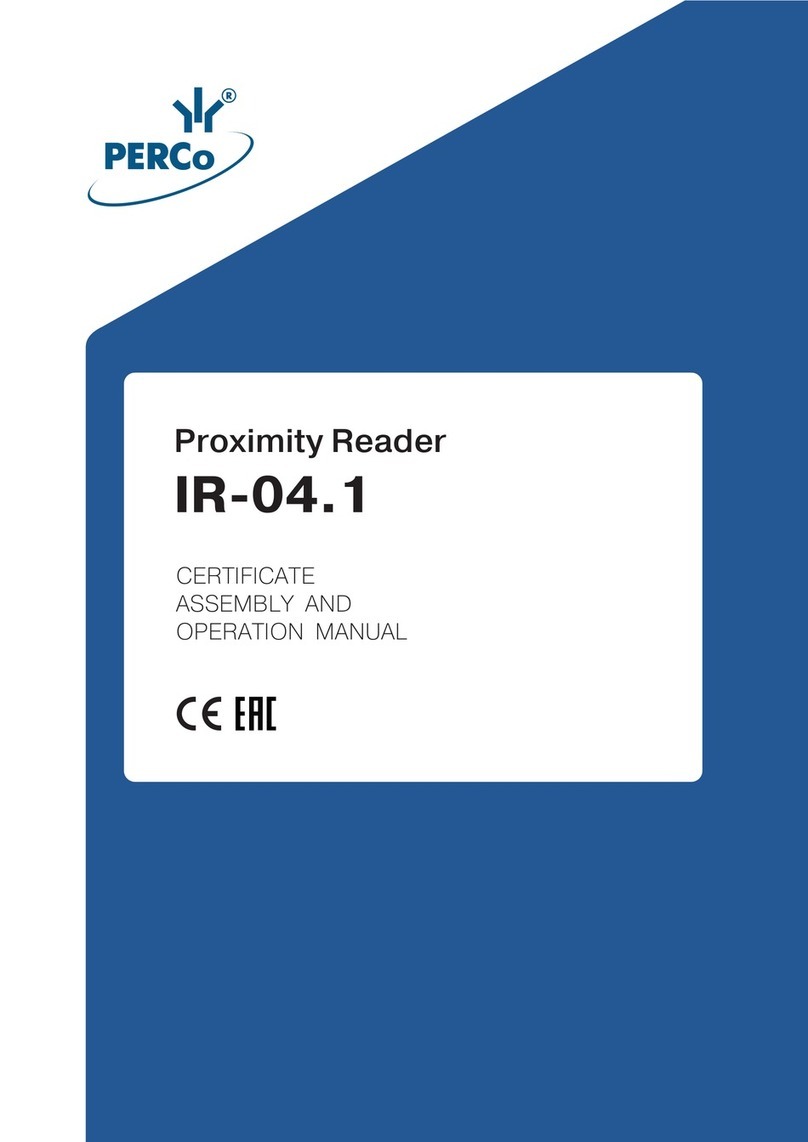
PERCo
PERCo IR-04.1 Installation and operating instructions

PERCo
PERCo IC-05 Installation and operating instructions
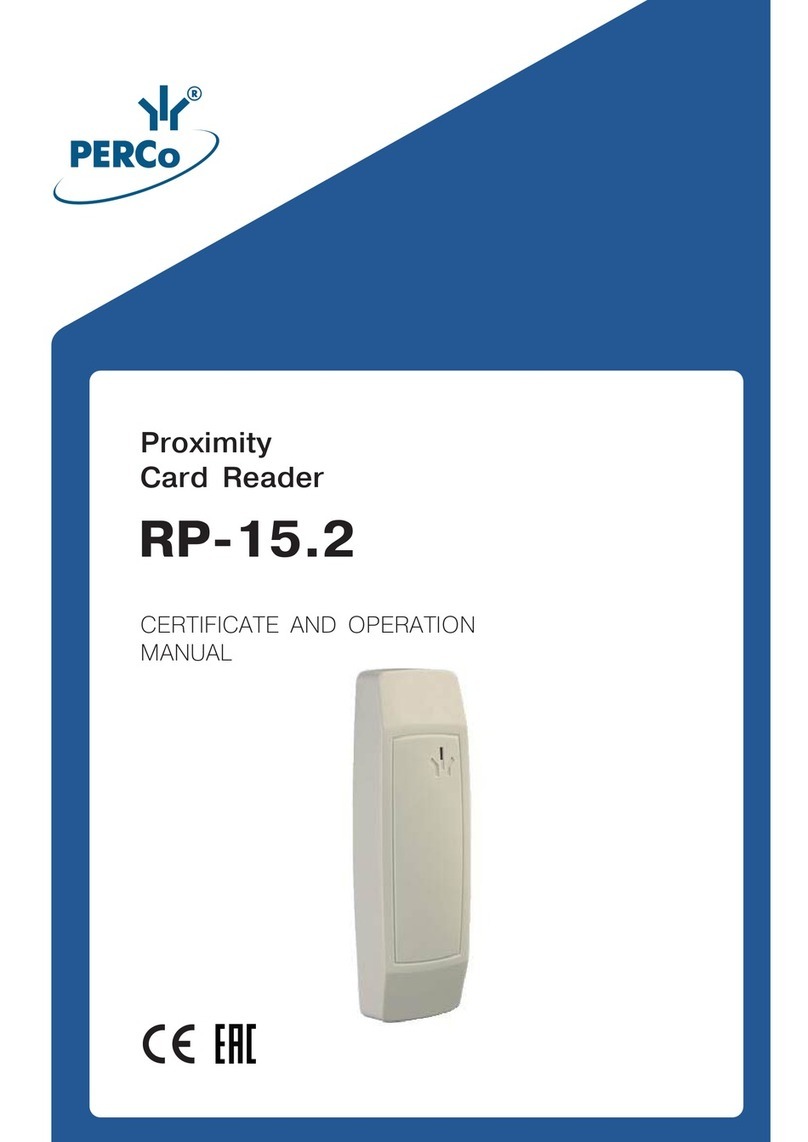
PERCo
PERCo RP-15.2 User manual