Plum ecoMAX920P1-S TOUCH User manual

CONTROLLER
ecoMAX920P1-S TOUCH
FOR AUTOMATIC SOLID FUEL FIRED BOILERS
INSTALLATION AND OPERATING MANUAL
ISSUE: 1.0_EN
Functions available in
additional module B
ecoSTER TOUCH**
ecoNET300**
ecoNET.apk
ecoNET.app
www.econet24.com
** Devices are not standard equipment of the controller.
11-2020
eSTER_x80**
eSTER_x40**
Functions available in
additional module C

ELECTRIC DEVICE UNDER VOLTAGE!
Before any action related to the power supply (cables connection,
device installation etc.) check if the controller is not connected to the
mains!.
Installation should be done by a person with appropriate electrical
qualifications. Improper cables connection could result in the controller
damage.
Due to fire hazard it is forbidden to use the controller in explosive gas
and dust atmospheres.
The controller cannot be used in steam condensation conditions and
cannot be exposed to water.
MAIN PRINCIPLES OF PROPER BOILER OPERATION WITH
INDIVIDUAL FUZZY LOGIC.
The controller must be programmed individually for a given boiler and
fuel type.
It is not allowed to change the type of gear motor, type of fan and
make other changes in boiler equipment affecting the combustion
process. The equipment should correspond to the factory components
installed by the boiler manufacturer.
It is recommended to operate with fan shutter maximally open.
Enabling Fuzzy Logic mode does not exempt from obligation to adjust
the SUPERVISION parameters.
Fuzzy Logic mode may require additional adjustment.

3
TABLE OF CONTENTS
1RECOMMENDATIONS REGARDING SAFETY ........ 4
2GENERAL INFORMATION .................................... 5
3INFORMATION ABOUT DOCUMENTATION......... 5
4STORAGE OF DOCUMENTATION......................... 5
5APPLIED SYMBOLS .............................................. 5
6DIRECTIVE WEEE 2012/19/EU............................. 5
USER SETTINGS ............................................ 7
7USER MENU - STRUCTURE .................................. 8
8CONTROLLER OPERATION................................... 9
8.1 DESCRIPTION OF THE MAIN WINDOW....................... 9
8.1 SWITCHING THE BOILER ON AND OFF...................... 10
8.2 PRESET TEMPERATURE SETTING ............................ 10
8.3 FIRE UP MODE................................................. 10
8.5 STABILIZATION MODE ..................................... 10
8.6 OPERATION MODE .......................................... 11
8.7 REGULATION MODES .......................................... 11
8.8 SUPERVISION MODE ....................................... 11
8.9 BURNING OUT/BURNING OFF MODE.............. 12
8.10 STOP MODE..................................................... 12
8.11 GRATE MODE/CLEANING ................................ 12
8.12 HUW SETTINGS................................................. 13
8.13 HUW PRESET TEMPERATURE SETTING.................... 13
8.14 HYSTERESIS OF HUW CONTAINER......................... 13
8.15 ACTIVATION OF THE SUMMER FUNCTION ............. 13
8.16 HUW CONTAINER DISINFECTION........................... 13
8.17 MIXER CIRCUIT SETTINGS..................................... 13
8.18 WEATHER CONTROL ........................................... 14
8.19 NIGHT DECREASE SETTINGS .................................. 15
8.20 CIRCULATION PUMP CONTROL .............................. 15
8.21 FUEL LEVEL CONFIGURATION ................................ 15
8.22 INFORMATION................................................... 16
8.23 MANUAL CONTROL ............................................ 16
8.24 MENU FAVORITES .............................................. 16
8.25 COOPERATION WITH ROOM THERMOSTAT AND ROOM
PANEL.............................................................. 16
8.26 COOPERATION WITH INTERNET MODULE................. 17
INSTALLATION AND SERVICE SETTINGS....... 19
9HYDRAULIC SCHEMES ....................................... 20
10 TECHNICAL DATA .............................................. 23
11 STORAGE AND TRANSPORT CONDITIONS......... 23
12 CONTROLLER INSTALLATION ............................ 23
12.1 ENVIRONMENTAL CONDITIONS ............................. 23
12.2 INSTALLATION REQUIREMENTS.............................. 23
12.3 MODULE INSTALLATION ...................................... 23
12.4 IP PROTECTION LEVEL ......................................... 24
12.5 ELECTRIC CONNECTION........................................ 24
12.6 ELECTRIC SCHEME .............................................. 26
12.7 CONNECTION OF TEMPERATURE SENSORS ............... 28
12.8 CONNECTING THE WEATHER TEMP.SENSOR ............ 28
12.9 CONNECTING THE EXHAUST TEMPERATURE SENSOR .. 28
12.10 TEMPERATURE SENSORS CHECKING........................ 29
12.11 OPTICAL SENSOR CONNECTION ............................. 29
12.12 MIXERS ROOM THERMOSTAT CONNECTION ............. 29
12.13 BOILER ROOM THERMOSTAT CONNECTION .............. 30
12.14 CONNECTING AUXILIARY BOILER.............................30
12.15 ALARMS SIGNALING CONNECTION..........................31
12.16 MIXER SERVOMOTOR CONNECTION........................31
12.17 CIRCULATION PUMP CONNECTION..........................32
12.18 CONNECTING STB TEMPERATURE LIMITER...............32
12.19 CONNECTING ROOM PANEL ..................................32
12.20 WIRELESS ROOM PANEL CONNECTION ....................33
13 SERVICE MENU - STRUCTURE............................34
14 DESCRIPTION OF SERVICE PARAMETERS...........36
14.1 BURNER ...........................................................36
14.2 BOILER .............................................................37
14.3 CH AND HUW ..................................................38
14.4 BUFFER ............................................................39
14.5 MIXER..............................................................39
14.6 OTHER PARAMETERS...........................................40
15 ALARMS DESCRIPTION ......................................41
15.1 MAXIMUM BOILER TEMPERATURE EXCEEDED ...........41
15.2 MAXIMUM FEEDER TEMPERATURE EXCEEDED...........41
15.3 BOILER TEMPERATURE SENSOR DAMAGE .................41
15.4 EXHAUST TEMPERATURE SENSOR DAMAGE ..............41
15.5 FEEDER TEMPERATURE SENSOR DAMAGE.................41
15.6 FAN DAMAGED ..................................................41
15.7 NO COMMUNICATION .........................................42
15.8 NO SUPPLY........................................................42
15.9 UNSUCCESSFUL BOILER FIRING-UP ATTEMPT ............42
16 FIRMWARE UPDATE ..........................................42
17 OTHER CONTROLLER FUNCTIONS .....................42
17.1 POWER FAILURE.................................................42
17.2 ANTI-FREEZE PROTECTION....................................42
17.3 PUMPS STANDSTILL PROTECTION FUNCTION.............42
18 LAMBDA PROBE.................................................42
19 REPLACEMENT OF PARTS AND COMPONENTS .43
19.1 REPLACEMENT OF CONTROL PANEL ........................43
19.2 REPLACEMENT OF MODULE CONTROLLER.................43
19.3 MAINS FUSE REPLACEMENT ..................................43
20 DESCRIPTION OF POSSIBLE MALFUNCTIONS ....44

4
1Recommendations regarding
safety
Requirements regarding safety are described
in detail in individual chapters of this manual.
Apart from them, the following requirements
should in particular be followed.
Before starting assembly, repairs or
maintenance, as well as during any
connection works, please make sure
that the mains power supply is
disconnected and that terminals and
electric wires are devoid of voltage.
After the controller is turned off,
dangerous voltage still can occur on
its terminals.
The controller cannot be used at
variance with its purpose.
The controller is designed for
development.
Additional automatics which protect
the boiler, central heating system,
and domestic hot water system
against results of malfunction of the
controller, or of errors in its software,
should be applied.
Choose the value of the programmed
parameters accordingly to the given
type of boiler and fuel, taking into
consideration all the operational
conditions of the system. Incorrect
selection of the parameters can cause
malfunction of the boiler (e.g.
overheating of the boiler, the flame
going back to the fuel feeder, etc.).
The controller is intended for boiler
manufacturers. Before applying the
controller, a boiler manufacturer
should check if the controller’s
matching with the given boiler type is
proper, and whether it can cause
danger.
The controller is not an intrinsically
safe device, which means that in the
case of malfunction it can be the
source of a spark or high
temperature, which in the presence of
flammable dusts or liquids can cause
fire or explosion. The controller’s
surroundings should be kept clean.
The controller must be installed by a
boiler manufacturer in accordance
with the applicable safety standards.
The programmed parameters should
only be altered by a person
familiarized with this manual.
The device should only be used in
heating systems in accordance with
the applicable regulations.
The electric system in which the
controller operates must be protected
by means of a fuse, selected
appropriately to the applied loads.
The controller cannot be used if its
casing is damaged.
In no circumstances can the design of
the controller be modified.
Electronic disconnection for connected
devices is applied in the controller
(type 2Y operation according to PN-EN
60730-1) and micro-disconnection
(type 2B operation according to PN-
EN 60730-1).
Prevent access to the controller of
people who do not know the content
of this manual, especially children.

5
2General information
The controller ecoMAX920P1-S TOUCH is
designed to control the operation of a solid
fuel boiler using an optical flame brightness
sensor. The controller can control the
operation of direct central heating circuit,
HUW circuit and operation of five mixing
heating circuits. The preset temperature of
circuits can be set on the basis of weather
sensor indications. The possibility of
cooperation with room thermostats, separate
for each heating circuit is beneficial for
maintaining comfortable temperature in
heating rooms. Moreover, the device turns
on the auxiliary gas or oil boiler if necessary.
The controller may operate with additional
room panel or room thermostat placed in a
living room and λprobe module, additional
expansion modules B, C and internet module
ecoNET300 to operate the controller on-line.
The controller may be used in households
and other similar premises and in light
industry facilities.
3Information about documentation
The controller’s manual is a supplement for
the boiler manual. In particular, except for
this manual, the boiler manual should also be
observed. The controller’s manual is divided
into two parts: for user and fitter. Yet, both
parts contain important information,
significant for safety issues, hence the user
should read both parts of the manual.
We are not responsible for any damages
caused by failure to observe these
instructions.
4Storage of documentation
This assembly and operation manual, as well
as any other applicable documentation,
should be stored diligently, so that it was
available at any time. In the case of removal
or sale of the device, the attached
documentation should be handed over to the
new user / owner.
5Applied symbols
In this manual the following graphic symbols
are used:
- useful information and tips,
- important information, failure to
observe these can cause damage of
property, threat for human and
household animal health and life,
Caution: the symbols indicate important
information, in order to make the manual
more lucid. Yet, this does not exempt the
user from the obligation to comply with
requirements which are not marked with a
graphic symbol!
6Directive WEEE 2012/19/EU
Purchased product is designed and made of
materials of highest quality.
The product meets the requirements of the
Directive 2012/19/EU of 4 July 2012 on
waste electrical and electronic
equipment (WEEE), according to which it is
marked by the symbol of crossed-out
wheeled bin (like below), meaning that
product is subjected to separate collection.
Responsibilities after finishing a period of
using product:
dispose of the packaging and product at
the end of their period of use in an
appropriate recycling facility,
do not dispose of the product with other
unsorted waste,
do not burn the product.
By adhering obligations of waste electrical
and electronic equipment controlled disposal
mentioned above, you avoid harmful effects
on the natural environment and risks to
human health.

6

USER SETTINGS
ecoMAX920P1-S TOUCH

8
7User menu - structure
Boiler settings
CH preset temperature - grate**
Boiler weather control*
Boiler heating curve*
Heating curve paralel shift*
Room temp. factor*
Output modulation
Limitation of boiler power
Fan output correction
Fan output in grate mode*
Fan in grate mode*
Operation mode*
Pellet
Grate
Regulation mode
Standard
Fuzzy Logic
Fuel level
Alarm level
Fuel level calibration
Fuel calorific
Capacity of tank
Lambda probe calibration*
Night time boiler decrease
On
Decrease value
Schedule
HUW settings*
HUW preset temperature
HUW pump operation mode
Off
Priority
No priority
HUW container hysteresis
HUW disinfection
HUW night time decrease
On
Decrease value
Schedule
Night time circ. pump decrease*
Summer/Winter
SUMMER mode
Summer
Winter
Auto*
SUMMER mode activation temp.
SUMMER mode deactivation temp.
Mixer 1-5 settings*5
Preset mixer temperature
Mixer room thermostat
Mixer weather control*
Mixer heating curve
Parallel curve shift
Room temperature factor
Mixer night decrease
On
Decrease value
Schedule
General settings
Clock
Date
Screen brightness
Sound
Language
Firmware update
Wi-Fi settings*:
SSID, Securities, Select security type,
Password
* not available if proper sensor or
additional module not connected or the
parameter is hidden and available only
after selecting relevant setting.
** parameter available only after
activation in advanced menu.
Main menu
Information
Boiler settings
HUW settings*
Mixer 1-5 settings*
Summer/Winter
General settings
Alarms
Outputs test
Service settings

9
8Controller operation
8.1 Description of the main window
Display main window.
Legend:
1. Controller operation modes: FIRE UP,
STABILIZATION, OPERATION,
SUPERVISION, BURNING OUT, BURNING
OFF, CLEANING, STOP
2. preset boiler temperature,
3. boiler measured temperature,
4. menu entering button
5. information field:
- airflow fan,
- fuel feeder
- burner feeder
- HUW and CH pump,
- lighter,
- grate.
6. Measured HUW container temperature,
7. Preset HUW container temperature value,
8. Clock and day of the week,
9. Outside temperature value (weather),
10. Functions affecting preset boiler
temperature. Following symbols signal
respectively:
- room thermostat contacts open –
preset room temperature reached,
- preset boiler temperature decrease
due to activated time spans,
- increasing preset boiler temperature
during loading of HUW container,
- boiler preset temperature increase
from mixer circuit,
- active return protection,
- preset temperature increase to load
the buffer.
Right and left window on the main screen
may represent different information, e.g.
mixer circuits, basic information about HUW,
fuel level, flame intensity, that can be
changed by touching the selected window.
Tip: fuel level may also be displayed in room
panel.
OPERATION
Mon.
Boiler temperature
HUW temperature

10
8.1 Switching the boiler on and off
Make sure fuel is present in the tank and
tank hatch is closed. Now boiler may be
switched on. To start the boiler, press “Boiler
Off” at any place on the screen. The message
“Active controller?” appears.
Screen with boiler off.
After accepting the boiler goes into Firing-up
phase. There is a second method of
integration of the boiler. Press the menu
button, then press in the menu button .
To turn off the boiler, press the menu button,
then press in the menu button , then
the controller will go to the process of
burning off. Only after burning off completion
will be information "Boiler Off".
8.2 Preset temperature setting
The preset boiler temperature, mixer circuits
temperature and grate preset temperature
can be set from the menu:
Boiler settings → CH preset temp. - grate
Mixer 1-5 settings →Preset mixer temp.
The parameter value: CH preset temp. -
grate, is bypassed by the controller when the
preset boiler temperature is controlled by
weather sensor. Regardless of that, the
preset boiler temp. is automatically increased
to load the hot user water tank and power
heating circuits of mixers.
8.3 FIRE UP mode
The FIRE UP mode is for automatic firing up
of furnace in boiler. Total time of firing up
process depends on controller’s settings and
on boiler’s condition before firing up. The
parameters affecting the firing up process
are in the menu:
Service settings →
Burner settings →Fire up
Firing up phase cycles:
Phase 1 is the ignition test time. It does not
appear on first fire up, only after e.g. boiler
inactivity period in STOP mode. Fan is
switched on with the power set by Firing up
airflow parameter. Small fuel dosage is
given, 20% of basic dosage. If during period
set by Ignition test time parameter, from
switching the fan on, the flame does not
reach the value from Flame detection
including No fuel detection time, firing up
process will end –the controller enters into
OPERATION mode. If the fire up detection
criteria are not met the controller will try to
clean and fire up the furnace.
Phase 2 is firing up. The furnace is cleaned
using fan with the power of Cleaning airflow
and operation of movable grate. In some
cases the controller extends the cleaning
time before firing up to make sure that there
are no smoldering fuel particles in the
burner, e.g. after power failure. This is to
minimize the risk of fuel gasification in the
boiler chamber and the possibility of ignition
of accumulated gases. Along with the furnace
the heat exchanger is also cleaned
mechanically.
In case of failed attempt of firing up the
furnace, another attempts are taken during
which amount of fuel is reduced to 10% of
first attempt’s dose. Further attempts of
firing up are signaled by numbers next to the
igniter . After three failed firing up
attempts an alarm “Unsuccessful boiler
firing-up attempt” is reported. Boiler’s
operation is then stopped. It is not possible
to automatically continue boiler’s operation.
Service intervention is required. After finding
and solving the cause of firing up failure the
boiler should be fired up again.
8.5 STABILIZATION mode
Additional indirect operation mode between
FIRE UP and OPERATION mode. In this mode
the controller tries to stabilize the flame,
Kocioł wyłączony
Boiler Off

11
thereby to fire up the furnace most
effectively.
Service parameter Stabilization time
determines the time to reach flame stability
during firing up by the controller. After
reaching flame stabilization the controller
enters OPERATION mode.
8.6 OPERATION mode
In the OPERATION mode the burner fan
operates constantly. Fuel feeder is engaged
periodically. Period consists of feeder
operating time and pause in fuel feeding
time.
Feeder and fan operation cycles.
The Feeding cycle time parameter is located
in the menu:
Service settings →Burner settings →
Fuel
Feeder operation time is calculated
automatically depending on the required
current power of the burner, Feed efficiency
and Calorific value of the fuel.
Parameters of blow-in are available in the
menu:
Service settings →Burner settings →
Airflow
8.7 Regulation modes
Can choose between two adjustment modes
responsible for stabilizing the boiler preset
temperature Standard and Fuzzy Logic. This
mode changes in the menu:
Boiler settings →Regulation mode
Operation in Standard mode.
If the boiler’s temperature reach preset one
then the controller switches off to
SUPERVISION mode. For this mode the
following parameters must be set
respectively 50% H2 hysteresis H2 and 30%
H1 hysteresis.
Hysteresis H1 and H2 of power modulation.
Operation in Fuzzy Logic mode.
In Fuzzy Logic mode the controller
automatically regulates burner power to
allow boiler operation in such a way to
maintain its temperature on preset level. The
controller uses power levels defined in
Standard mode. In this mode the parameters
H2 and H1 hysteresis do not have to be set.
The Fuzzy Logic mode unlike the Standard
mode is not faulty in respect of failing to
reach the preset boiler temperature due to
incorrect adjustment of H2 and H1. It also
allows for quicker reach the preset
temperature. In addition, you can adjust the
boiler output in FL mode by the parameters
Min. boiler output FL and Max. boiler output
FL.
Attention: If the boiler operates
without heat buffer and controller is
switched into SUMMER mode than
Standard mode operation of the
controller is recommended.
After exceeding the preset temperature by
5ºC the controller switches into
SUPERVISION mode.
8.8 SUPERVISION mode
The SUPERVISION mode is applicable either
in regulation in Standard and Fuzzy Logic
mode. The controller switches into
SUPERVISION mode automatically without
user’s intervention:
in Standard regulation mode –after
reaching the boiler preset temperature,
Feed time
operat
Feed interval
operat
Feed time
operat
Feed interval
operat
Preset temperature
T=85°
Preset temperature
T=85°
Power level
Power level

12
in Fuzzy Logic regulation mode –after
exceeding boiler preset temperature by
5ºC.
In SUPERVISION mode the controller
oversees the furnace, keeping it from
burning off. To do so, the burner operates
with very low power, what together with
properly adjusted parameters do not cause
further increase in temperature. Burner’s
power in SUPERVISION mode and other
parameters of Supervision are grouped in the
menu:
Service settings →Burner settings →
Supervision
Mode parameters must be set according to
recommendations of boiler/burner
manufacturer. They should be selected in
such a way that the furnace did not damp
out during boiler pauses (it should not be
fired up too much simultaneously as it will
cause boiler temperature to increase).
The parameters in this mode must
be so chosen as to make the boiler
temperature gradually decreasing.
Incorrect settings can cause boiler
overheating.
Maximum time of boiler’s operating in
supervision mode is defined in service
parameter Supervision time. If after this time
(in Supervision mode) there is no need to
restart the boiler then the controller starts
the process of boiler’s burning off.
For setting Supervision time = 0 the
controller omits SUPERVISION mode
and goes directly to BURNING OFF.
8.9 BURNING OUT/BURNING OFF
mode
In BURNING OUT mode the remaining fuel
burns out and the boiler is prepared for
burning off and next to enter STOP or
CLEANING mode. All parameters affecting
the burning out/burning off process are
grouped in the menu:
Service settings →
Burner settings →Burning out/Burning
off
The controller stops feeding the fuel and
performs cyclic blowing according to Blowing
time and Blowing pause settings in order to
burn the remaining fuel. After flame
brightness dropping below Burning out end
threshold value it enters into Burning off
mode where after expiry of Burning off time
the controller will shut down the boiler but
still control the CH and HUW pumps.
8.10 STOP mode
In the STOP mode the boiler is being burnt
off and awaits the signal to start operation.
The following can be a signal to start
operation:
decrease of preset boiler temperature
below preset temperature diminished by
boiler hysteresis (Boiler hysteresis),
by boiler operation configuration with the
buffer decrease of top buffer temperature
below preset value (Buffer loading start
temperature).
8.11 GRATE mode/CLEANING
Some boilers have an additional grate to
burn other fuels such as wood waste, etc. To
activate the grate, move the parameters
available in the menu:
Boiler settings → Operation mode from
"pellet" to "grate".
In the grate mode fuel feeder is turned off.
The combustion process is regulated by the
fan. Fan power, when working with grate, is
set in the parameters: Fan in grate mode,
Fan output in grate mode and Blowing power
–supervision, Blowing pause - maintaining.
The parameters affecting the grate operation
are set in the menu:
Boiler settings → Output modulation
and
Service settings →Burner settings →
Cleaning
Service settings →Burner settings →
Grate
The values of parameters such as:
Boiler settings →CH preset temperature
- grate
Service settings →Boiler settings →
Boiler hysteresis - grate
are individually adjusted for the "grate". This
allows to define different properties of boiler
operation for operation modes "grate" and
"pellets". When using the grate an alarm "No
fuel" can appear. This alarm occurs when a

13
temperature drops below the value of the
parameter:
Service settings →CH and HUW settings
→CH pump activation temperature and
then for a period of 10 minutes there has
been no growth.
Cleaning from residual of spent fuel is carried
out by operation modes of moving grate, in
accordance with the set parameters in the
menu:
Service settings → Burner settings →
Cleaning
8.12 HUW settings
The controller regulates temperature of the
HUW container, providing that the
temperature sensor is connected. When the
HUW temperature sensor is disconnected –
the information about it is displayed in the
main window.
By setting: HUW settings →HUW pump
mode user is able to:
deactivate feeding the HUW container,
parameter Off,
setting HUW priority, by parameter
Priority –then CH pump is deactivated to
feed the HUW container quicker,
set simultaneous operation of CH and
HUW pump with the parameter No
priority.
8.13 HUW preset temperature setting
Preset temperature HUW is defined by
parameter:
HUW settings →HUW preset
temperature
8.14 Hysteresis of HUW container
Below temperature HUW preset temp. minus
HUW hysteresis the HUW pump will activate
to feed the HUW container.
By small hysteresis value HUW
pump will activate faster after HUW
temperature decrease.
8.15 Activation of the SUMMER
function
To activate SUMMER function which allows
feeding the silo during summer, without
necessity to activate CH installation and
mixers periods, it is required to set the
menu: Summer/Winter → SUMMER mode
for Summer.
Attention: when boiler operates
without heating buffer and the
controller is switched into
SUMMER mode, than Standard
mode operation is
recommended.
It is not allowed to activate
function summer when HW pump
is disconnected or damaged.
Function SUMMER can be activated
automatically, on the basis of readings from
weather sensor. Use following parameters to
activate this function:
Summer/Winter → SUMMER mode →
Auto
If the automatic detection of summer mode
is switched on, you can set the parameters:
SUMMER mode act. temperature, so outdoor
temp. above which the summer mode will be
switched on and SUMMER mode deact.
temperature, so outdoor temp. below which
the SUMMER mode will be switched off).
8.16 HUW container disinfection
The controller can automatically, periodically
make HUW container warm up to 70ºC. It is
done to remove bacterial flora. Function is
activated in the menu:
HUW settings → HUW disinfection
It is absolutely important to inform
all the inmates about activating the
disinfection function. There is a
danger of scalding with hot water.
Once a week at night, in Monday at 2 a.m.
the controller increases temperature of HUW
container. After 10 minutes of keeping the
silo at 70ºC the HUW pump is deactivated
and the silo returns to its normal operation.
It is not advisable to activate disinfection
function while the service of HUW is
deactivated.
8.17 Mixer circuit settings
Settings of first mixer circle are in the menu:
Mixer 1 settings
Settings for other mixers, after connecting
additional module B and C are in the
following positions of the menu and are
identical for each circuit.

14
Mixer settings without weather sensor.
It is required to set manually desired
temperature in mixer’s heating cycle using
parameter Preset mixer temperature, e.g.
50ºC. Such should be a value to provide
required room temperature.
After connecting a room thermostat, value of
decline in preset mixer temperature from
thermostat should be set. (parameters Mixer
room thermostat, e.g. 5ºC. This value should
be chosen experimentally. A room
thermostat can be a traditional one or a
room panel. After activating the thermostat,
mixer preset temperature will be reduced.
When this value is reduced correctly then
room temperature increase will be stopped.
Mixer settings with weather sensor,
without room panel.
Set parameter Mixer weather control in
position on. Adjust weather curve according
to point 8.18. Using parameter Curve shift
set required room temperature according to
formula: Required room temperature = 20°C
+ heating curve shift. In this configuration a
thermostat can be connected. It will level
inaccuracy of heating curve adjustment in
case when its value will be too big. In such
case value of decrease of preset mixer room
temperature from thermostat should be set
i.e. for 2°C. After disconnecting thermostat
plugs preset mixer cycle temperature will be
reduced. By correct adjustment of this
reduction will stop temperature increase of
temperature in heated room.
Mixer settings with weather sensor and
room panel.
Set parameter Mixer weather control. In
position off. Adjust weather curve according
to point 8.18. Room panel automatically
moves the heating curve depending on
preset room temperature. The controller
relates adjustments to 20ºC, i.e. for preset
room temperature = 22ºC the controller will
move heating curve by 2ºC, for preset room
temperature = 18ºC the controller will move
heating curve by -2ºC. In some cases
described in point 8.18 it can be necessary to
adjust heating curve shift.
In this configuration room thermostat is able
to:
- reduce temperature of heating cycle by a
constant value, when preset temperature in
a room will be reached. Similarly like it was
described in previous point (not
recommended), or
- automatically, constantly correct heating
cycle temperature.
It is not recommended to use both these
possibilities at the same time.
Automatic correction of room temperature is
done according to formula:
Correction = (preset room temperature –
measured room temperature) x room
temperature factor / 10
Example:
Preset temperature in heating room (set in
room panel) = 22ºC. Measured temperature
in room (using room panel) = 20ºC. Room
temperature factor = 15
Preset mixer temperature will be increased
by (22ºC –20ºC) x 15/10 = 3ºC. Correct
value of parameter must be found room
temperature factor. The bigger value of
factor the bigger correction of preset boiler
temperature factor. When set on value “0”
preset mixer temperature is not corrected.
Attention: setting too high value of room
temperature factor may cause cyclic room
temperature fluctuations.
8.18 Weather control
Depending on measured outside
temperature, automatically controlled can be
either preset boiler temperature and mixer
cycles temperatures. By correct adjustment
of heating curve temperature of heating
circuits is counted automatically depending
on value of external temperature. Thanks to
that by choosing proper heating curve for
given building, room temperature remains
approximately the same –no matter what
outside temperature. Attention: in the
process of experimental adjustment of
proper heating curve it is necessary to
temporarily exclude the influence of room
thermostat on the controller’s operation,
irrespectively if room thermostat is
connected or not, by setting parameter:
Mixer 1 settings →Mixer room

15
thermostat = 0. In case of connected room
panel, set temporarily the following
parameter: Room temp. factor = 0.
Guidelines for correct heating curve setting:
- floor heating 0,2 -0,6
- radiator heating 1,0 - 1,6
- boiler 1,8 - 4
Heating curves.
Tips for choosing proper heating curve:
If by decreasing outer temperature room
temperature is increasing, then value of
chosen heating curve is too big,
If by decreasing outer temperature, room
temperature is also decreasing, then
value of chosen heating curve is too low,
If by frosty weather room temperature is
appropriate and in warmer time is too low
–it is recommended to increase
parameter Curve shift and then choose
lower heating curve
If by frosty weather room temperature is
too low and in warmer time too high –it
is recommended to reduce parameter
Curve shift and choose higher heating
curve.
Buildings which are poorly isolated require
setting heating curve with higher values, and
for better isolated buildings heating curve
will have lower value.
Preset temperature, counted according to
heating curve can be decreased or increased
by controller when it goes beyond scope of
limits of temperatures for given cycle.
8.19 Night decrease settings
In the controller it is possible to set time
periods of silo temperature reduction,
heating cycles, HUW container, circular pump
and boiler. Time periods allow setting
temperature reduction in given time period –
i.e. at night or when user leaves the heated
room. Thanks to it preset temperature can
be reduced automatically, without loss of
heating comfort by reducing fuel
consumption. To activate time intervals, set
the parameter Night time decrease for the
given heating circuit to ON. The parameter
Decrease set the temperature reduction, one
for all time intervals. Night time decreases
can be defined separately for every day of
the week set Schedule.
Daily time schedule with periods every 30 min.
Above are examples of night-time decrease
the preset temperature lasting from 22:00
till 06:00 and the reduction from 09:00 to
15:00.
8.20 Circulation pump control
Attention: functionality of circulation pump is
available only after connecting additional
module C. Settings are in the menu:
HUW settings → Night time decrease
circul. pump
and
Service settings → CH and HUW settings
Settings of time control of circular pump are
analogical to settings of night reductions. In
defined time periods circular pump is
deactivated. In omitted periods the circular
pump is switched into position Circulating
pump operation time, what Circulating pump
standstill time.
8.21 Fuel level configuration
Fuel level indicator activating.
To activate displaying fuel level following
parameters are to be set:
Boiler settings →Fuel level →Alarm
level
on value bigger than “0”, i.e. 10%.
By pressing on the left or right window of the
main window you can select the fuel level
indicator.

16
Fuel level indicator support.
Each time when fuel silo is filled to required
level it is necessary to press and keep the
knob in main window. Following info will
appear:
Obsługa poziomu paliwa.
“Set fuel level to 100%?”. After choosing and
accepting YES fuel level will be set for 100%.
Fuel can be refilled anytime, that means it is
not needed to wait till the silo is empty.
However fuel should be filled up to the level
corresponding to 100% and set the controller
level to 100%.
Description of activity
The controller measured fuel level on the
basis of its current consumption. Factory
settings will not always correspond to actual
fuel consumption , so to work correctly this
method needs level calibration by controller’s
user. No additional fuel sensors are required.
Calibration
Fill the silo to the level which corresponds to
full level of fuel, then set value of parameter:
Boiler settings →Fuel level →Fuel level
calibration →Fuel level 100%
In main window the indicator will be set to
100%. Calibration process in progress is
marked with an on screen prompt
„Calibration”. The decreasing fuel level in the
container must be under constant control. As
soon as the level drops to the desired
minimum set the following parameter to:
Boiler settings →Fuel level → Fuel level
calibration →Fuel level 0%
There is a possibility to skip the calibration
process if the parameters are set correctly.
Feeder efficiency and Capacity of tank, which
are in: Service settings →Burner
settings → Operation
8.22 Information
Menu Information enables view to
measured temperatures and allows to check
which of devices are currently activated.
After connecting extension module
of mixers information about
auxiliary mixers are displayed.
8.23 Manual control
In the controller it is possible to manual
activate devices like i.e. pumps, feeder
engine, or blower engine. It enables to
check if the device is operating correctly
and if it is connected properly.
Entering manual control is possible
only in “Boiler Off” mode, when silo
is switched off.
Manual control window view: OFF –means that the
device is turned off, ON –the device is turned on.
Attention: long lasting activation of
fan, feeder or other device may
cause danger.
8.24 Menu favorites
In the menu bar at the bottom of the screen
is visible button . After its selecting
appears quick selection menu. Elements of
this menu is added by hold for a moment the
appropriate icon in the rotary menu.
To remove an item from the menu favorites
being in the favorites menu hold the selected
icon and then confirm the deletion.
8.25 Cooperation with room
thermostat and room panel
The controller can cooperate with:
wireless, battery-powered room
thermostat eSTER_x40, via ISM
communication,
Manual control
Fan
Feeder
Boiler pump
HUW pump
Lighter

17
wireless room panel eSTER_x80 with
thermostat function via bilateral ISM
communication,
wired room panel ecoSTER200 and
ecoSTER TOUCH, with room thermostat
function.
The room thermostat and room panel
simultaneously transmit useful information,
such as: fuel level information, burner
operation status, alarms, allows to set
controller parameters and its operation
modes, it also serves as an additional panel
controlling the boiler.
8.26 Cooperation with internet module
The controller can cooperate with ecoNET300
internet module. It allows view and control of
the controller on-line via Wi-Fi or LAN
network using www.econet24.com service,
via WWW browser or ecoNET.apk,
ecoNET.app mobile application. The
application is downloadable free of charge
under:
ecoNET.apk

18

19
INSTALLATION AND SERVICE SETTINGS
ecoMAX920P1-S TOUCH

20
9Hydraulic schemes
Scheme with 4-way steering valve controlling central heating circuit
1
: 1 –boiler, 2 –burner, 3 –
controller, 4 –boiler temperature sensor, 5 –exhaust temperature sensor, 6 –servomotor of 4-way valve, 7
–mixer cycle pump, 8 –mixer cycle temperature sensor, 9 –HUW container, 10 –HUW pump, 11 –HUW
temp. sensor, 12 –weather temperature sensor, 13 –room panel with room thermostat function or
standard room panel, 14 –return temperature sensor (not necessary for system to operate).
To improve water circulation in the boiler’s gravity circuit: use large nominal cross-sections DN of
the pipe and four-way valve, avoid more elbows and constrictions of the cross-section, apply
other rules concerning construction of gravitational installations, such as keeping slopes, etc. If
the return sensor is clip-on, insulate it thermally from the surroundings and improve thermal
contact with the pipe by using thermal grease. Boiler’s preset temperature must be set high
enough to provide thermal power for the mixer circuit while heating up the water returning to the
boiler.
RECOMMENDED SETTINGS:
Parameter
Setting
MENU
CH preset temperature - grate
75-80C
Boiler settings
Min. preset boiler temperature
65C
Service settingsBoiler settings
Boiler inc. by HUW and Mixer
5-20C
Service settingsCH and HUW settings
Mixer 1 support
CH on
Service settingsMixer 1 settings
Max. mixer 1 temperature
70C
Service settingsMixer 1 settings
Mixer 1 heating curve
0.8 –1.4
Mixer 1 setting
Mixer 1 weather control
ON
Mixer 1 setting
Mixer 1 thermostat selection
ecoSTER T1
eSTER T1
Service settingsMixer 1 settings
1
The presented hydraulic diagram does not replace central heating engineering design and may be used for
information purposes only!
Table of contents
Other Plum Controllers manuals
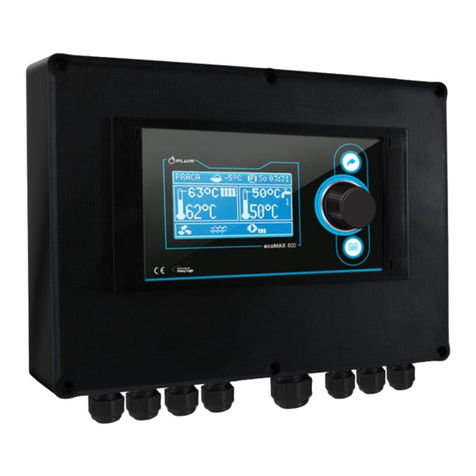
Plum
Plum ecoMAX850P1-V User manual

Plum
Plum ecoMAX360I Specification sheet
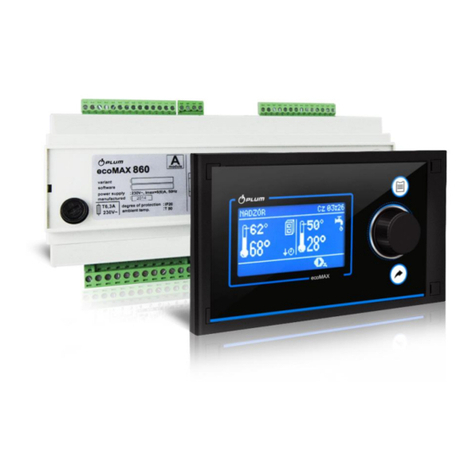
Plum
Plum ecoMAX860P3-KL User manual
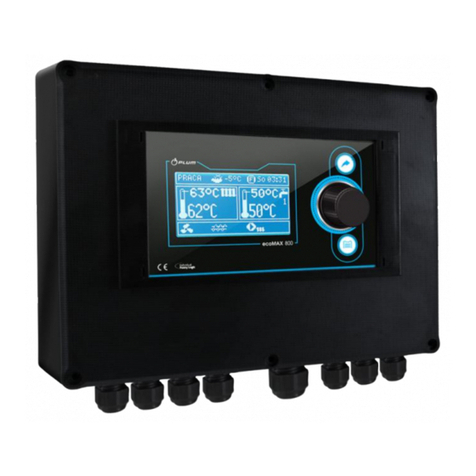
Plum
Plum Cieplo ecoMAX850P2-C User manual
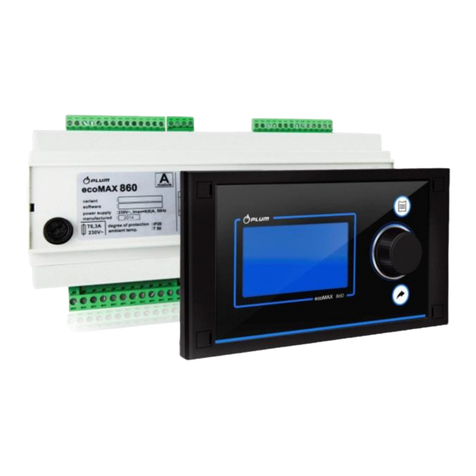
Plum
Plum ecoMAX860P1-K STANDARD User manual
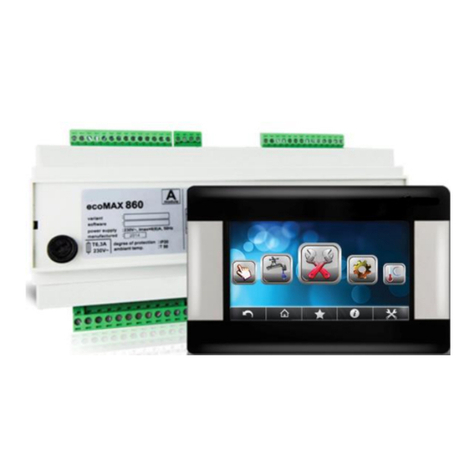
Plum
Plum ecoMAX860P3-C TOUCH User manual
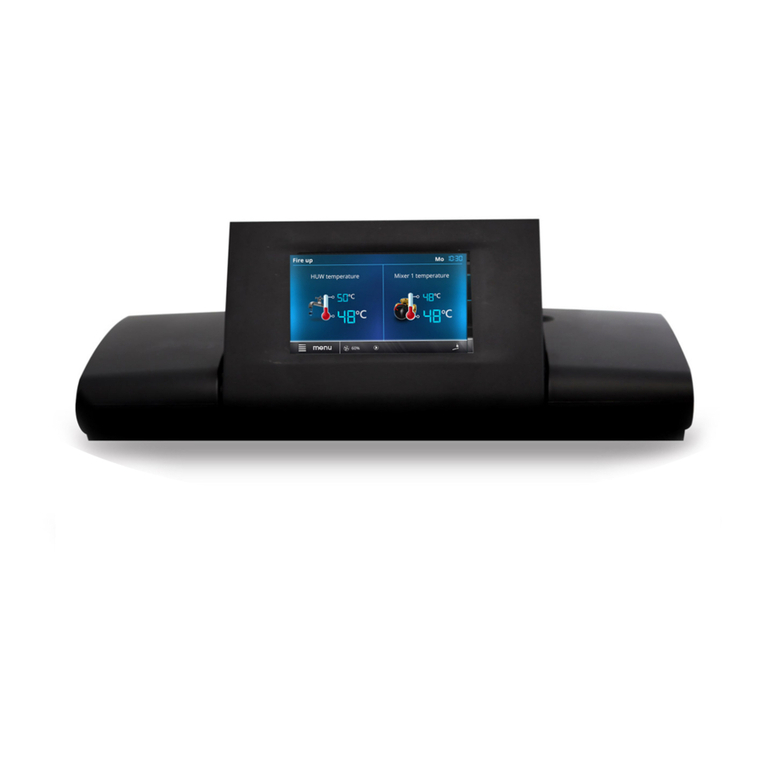
Plum
Plum ecoMAX920P1-K User manual
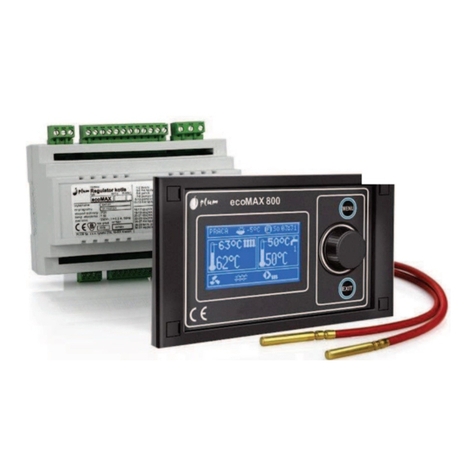
Plum
Plum ecoMAX 80 R1 User manual
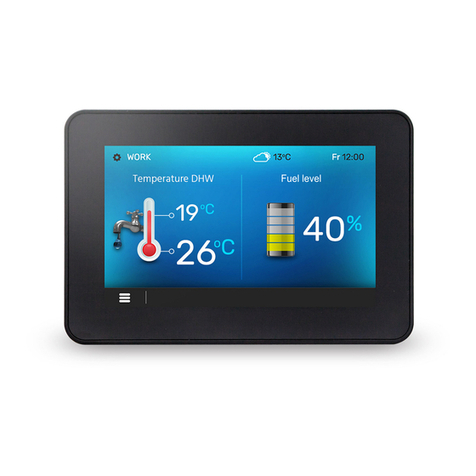
Plum
Plum ecoMAX860P3-LZ User manual
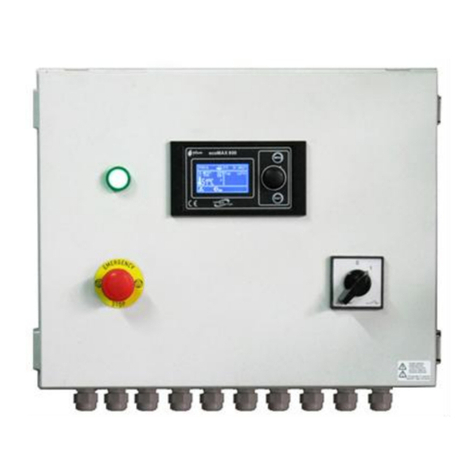
Plum
Plum ZAB-14 User manual
Popular Controllers manuals by other brands
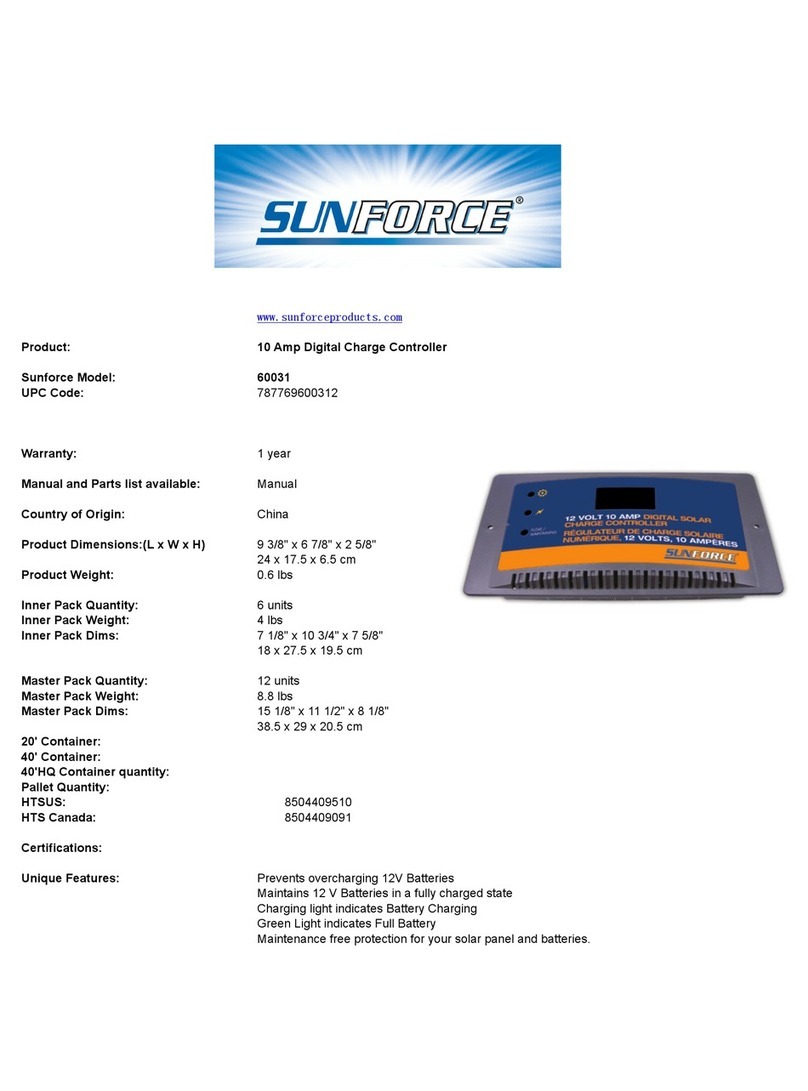
Sunforce
Sunforce 60031 manual
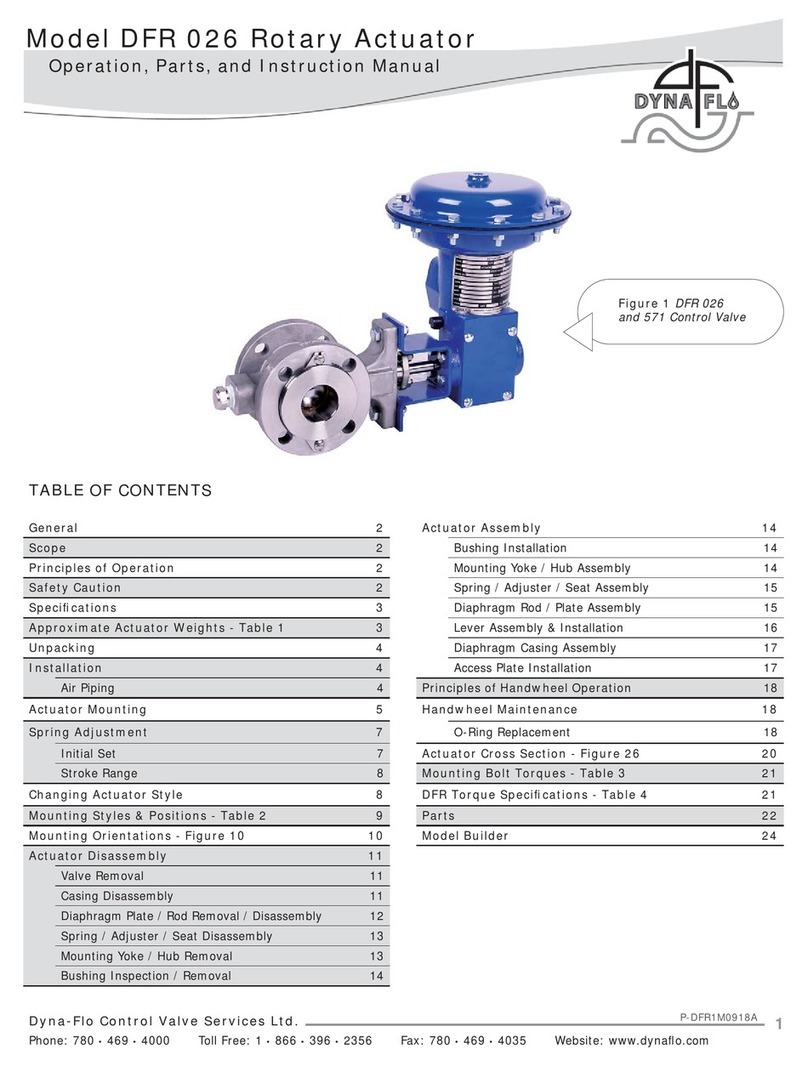
Dyna-Flo
Dyna-Flo DFR 026 Operation, Parts, and Instruction Manual
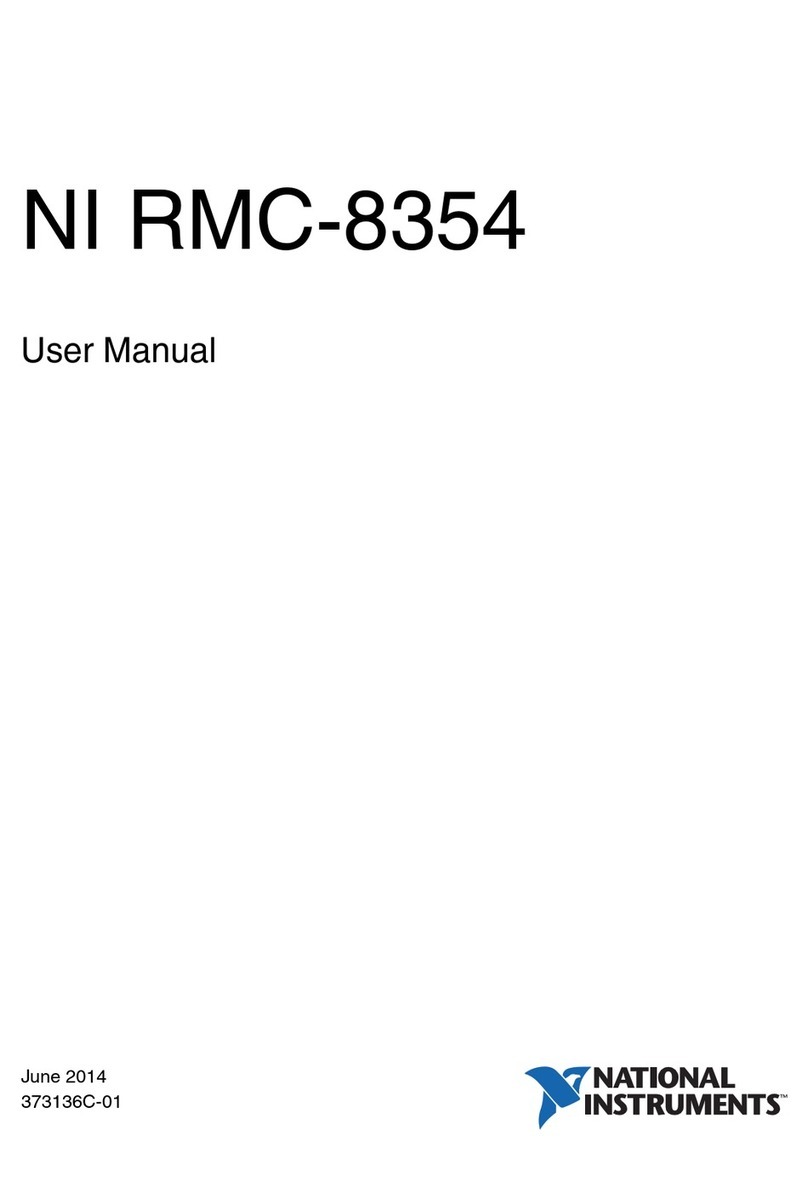
National Instruments
National Instruments RMC-8354 user manual
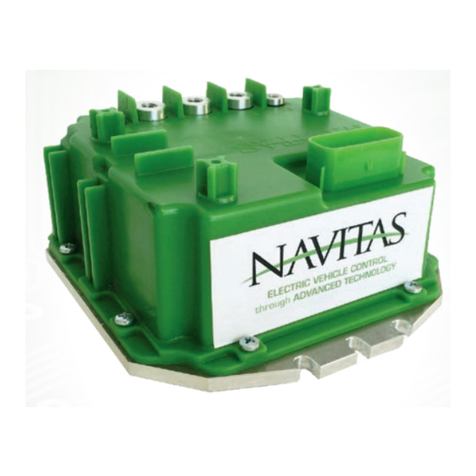
NAVITAS
NAVITAS 440A Installation & service manual
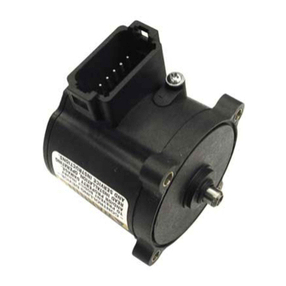
Woodward
Woodward L-Series Installation and operation manual

Renesas
Renesas RA6T2 Application note