Precision matthews PM-727M User manual

PM-727 Manual 2015 v2.docx 1
Precision milling machine
6-speed gear head
1 HP, 110V single phase motor
DRO for precise downfeed measurement
Square column design
Heavy cast iron construction
Welded steel stand & cabinet
Total weight 485 lbs
Model PM-727M
701 Parkway View Drive
Pittsburgh, PA 15205

PM-727 Manual 2015 v2.docx 2
This manual describes PM-727M machines as shipped from January 2015. There may be detail differences
between your specific machine and the information given here (with little or no impact on functionality). If you
have questions about any aspect of the manual or your machine, please call 412-787-2876 (east coast time), or
email us at admin@machinetoolonline.com. Your feedback is welcomed!
New installation?
After uncrating the mill, please pay attention to the following:
Read the installation instructions at the BACK of this manual.
Handling the mill is at least a two-man job.
Hand-crank the headstock down until the spindle nose is just clear of the
table.
Lifting gear –sling, hoist or forklift –must be rated for at least 1000 lb.
Working location of the mill must allow:
1. Full left-right travel of the table
2. Access to the back of the column (Z axis leadscrew maintenance)
Power requirement is 110V, 60Hz, 1φ, 15A circuit protection (spindle motor
16A, full load).
Extension cord not recommended; if no alternative, use 12 AWG not longer
than 20 ft.
BEFORE connecting power be sure that:
1. The machine is on a firm footing.
2. There are no clamps or locks on moving parts.
3. The gearbox contains oil –check the sight glass at right of the headstock.
4. The gear levers are set for the lowest speed: Hi-Lo to L, 2-3-1 to 1.
5. The gears are fully engaged –hand-rotate (jiggle) the spindle forward and
back while applying light pressure on each gear lever, listening for the click
as the gears engage.
This manual contains essential safety advice on the proper setup, operation, maintenance, and
service of the PM-727M milling machine. Failure to read, understand and follow the manual may
result in property damage or serious personal injury.
There are many alternative ways to install and use a mill. As the owner of the mill you are solely
responsible for its proper installation and safe use. Consider the material contained in this manual to
be advisory only. Precision Matthews, LLC cannot be held liable for injury or property damage
during installation, or from negligence, improper training, machine modifications or misuse.

PM-727 Manual 2015 v2.docx 3
Section 1 INTRODUCTION
MODEL 727M Milling Machine features and specifications
General information
The 727M is a robust "square column" mill designed for day-in, day-out use in the model shop. With an all-up
weight of almost 500 lbs lbs it can handle far more than the typical small machine. For precise control of cutter
depth there is a worm-driven quill downfeed with graduated dial and DRO, completely independent of headstock
up/down position.
The reversible spindle runs in high-quality (ISO355) tapered-roller bearings enclosed in a 2-1/2" diameter quill
with coarse and fine downfeed options. An oil-filled gearbox provides 6 spindle speeds from 115 to 1700 rpm.
Scraped dovetailed ways for table and headstock ensure smooth, precise motion in all three axes (X= table
left/right, 15 in. Y= table front/back, 8-1/2 in. Z= headstock up/down, 16 in.). The headstock can be tilted 45o
clockwise and counter-clockwise from the vertical.
Supplied accessories
R8-JT33 drill chuck arbor
1/2" (13mm) JT33 keyed chuck (if ordered)
Spindle lock C-wrench
T-bolts for vise hold-down
Oil bottle
Floor plan
Working clearances –space requirements for full motion of the table

PM-727 Manual 2015 v2.docx 4
Approximate T-slot dimensions
Dimensions
Weight, including welded stand 485 lb net, 560 lb shipping
Size, including stand W 40 in. x D 26-1/2 in. x H 70 in.
Stand footprint W 14-1/2 in. x D 21-1/4 in.
Tray W 23-1/4 in. x D 26-1/4 in.
Electrical
Power requirement 110V, 60 Hz, 1 phase
Spindle motor Cap-start induction, 900W (1 HP), 1720 rpm
Full load current 15.6A
Headstock
Vertical travel 16 in.
Left-right tilt
45° - 0° - 45°
Spindle
Speeds (rpm) 115, 220, 320, 600, 1120, 1700
Internal taper R8
Top end 6 splines, 22 mm OD
Quill travel 3 in.
Quill diameter 2.45 in.
Spindle nose to table 2-1/2" to 18-1/4 in.
Spindle centerline to front face of column 7-3/4 in.
Drawbar 7/16 - 20, 16 mm wrench
Table
Size W 27-1/2 in. x D 7-1/4 in.
Surface height over floor Approx 36 in.
Maximum load 200 lb
Leadscrews Acme, inch pitch, 10 tpi
Left-right travel (X-axis) 15 in.
Front-back travel (Y-axis) 8-1/2 in.
T-slots (3) 12 mm wide, 63 mm centerlines

PM-727 Manual 2015 v2.docx 5
No list of precautions can cover every-
thing. You cannot be too careful!
Everyday precautions
This machine is designed for milling and drilling operations by experienced
users familiar with metal-working hazards.
Untrained or unsupervised operators risk serious injury.
Wear ANSI-approved full-face or eye protection at all times when using the
machine (everyday eyeglasses are not reliable protection against flying
particles).
Wear proper apparel and non-slip footwear –be sure to prevent hair, clothing or
jewelry from becoming entangled in moving parts. Gloves –including tight-fitting
disposables –can be hazardous!
Be sure the work area is properly lit.
Never leave chuck keys, wrenches or other loose tools on the machine.
Be sure the workpiece and machine ways are secure before commencing milling
or drilling –hold-downs and/or vise fully tightened, X-Y-Z axes locked, cutting
tool secured.
Use moderation: light cuts, low spindle speeds, slow table motion give better,
safer results than "hogging".
Don't try to stop a moving spindle by hand –allow it to stop on its own.
Disconnect 110V power from the mill before maintenance operations such as
oiling or adjustments.
Maintain the machine with care –check lubrication and adjustments daily before
use.
Clean the machine routinely –remove chips by brush or vacuum, not
compressed air (which can force debris into the ways).

PM-727 Manual 2015 v2.docx 6
Section 2 USING THE MILL
FRONT PANEL CONTROLS
Connect the mill to a 110Vac outlet. The Power
lamp, top center, should light indicating that the
control circuit is energized.
The E-stop button, bottom right, disconnects the
control circuit completely, but it should be used only
for its intended purpose –emergency disconnect.
The E-stop button is not momentary. Once in, it
stays in until twisted clockwise.
The spindle drive motor is controlled by the three
push buttons:
Left = Forward (cw, looking down, used for
most milling/drilling operations)
Right = Reverse (ccw, looking down)
Off = Stop
SPINDLE SPEEDS
This is a gear-head machine with a constant speed
motor and a two-stage gearbox providing a choice of
six spindle speeds. The first stage (L-H) selects the
speed range, high or low, and the second stage (1-3-
2) selects a specific speed within that range.
Before switching on the spindle motor, be sure that both stages are properly engaged. Hand-rotate
(jiggle) the spindle forward and back while applying light pressure on each gear-shift knob, listening for the
click as the gears engage.
Allow the spindle to stop completely before shifting gears
Spindle speeds (rpm)
L-1
115
L-2
220
L-3
320
H-1
600
H-2
1120
H-3
1700
Excessive cutter noise, chatter, poor finish and tool wear are often the result of too high a
feed rate, and/or too high a spindle speed. If unsure, go slow!
Figure 2-1 Motor controls, gear-shift knobs and DRO

PM-727 Manual 2015 v2.docx 7
INSTALLING AND REMOVING TOOLING
The spindle and drawbar are designed for R-8 taper
collets, drill chucks and other arbors with the standard
7/16"-20 internal thread. Two tools are required to
install or remove R8 tooling: a 16 mm wrench for the
drawbar nut, and the supplied C-wrench which engages
in a slot at the bottom end of the spindle.
To install: Hand-thread the drawbar into the R-8 device
until the washer, arrowed in Figure 2-2, is seated on the
splined spindle. Lock the spindle with the C-wrench
while at the same fully tightening the drawbar.
To remove: Protect the table under the spindle with
rags or scrap wood. Lock the spindle with the C-
wrench, loosen the drawbar one half turn or less, then
tap the top of the drawbar with a brass or dead-blow
hammer to unseat the taper. Unscrew the drawbar with
one hand while supporting the R-8 device with the other
hand. Keep in mind that the table, vises and workpiece
can be damaged by falling tools and drill chucks. The
cutting tool itself can also be damaged in the same way.
Replace the drawbar cap to protect
bearings and spline.
MOVING THE TABLE
Conventionally, left-right movement of the
table is said to be along the X-axis (also
called "longitudinal travel" or "traversing").
Front-back movement is on the Y-axis,
sometimes called "cross travel".
Each axis has a leadscrew with handwheel
and graduated dial with 0.001" divisions,
Figure 2-3. If the mill is not equipped with
digital readouts (DROs), the table can be
accurately positioned by counting whole
turns and divisions, keeping leadscrew
backlash in mind. This means that table
motion must always be in the same
direction up to the point of reference, then
on to the desired location. For example:
A hole is to be drilled exactly 0.25" on the Y-axis
relative to the front edge of a workpiece in a
Figure 2-2 Spindle and drawbar
Figure 2-3 Y-axis handwheel, X-axis locks

PM-727 Manual 2015 v2.docx 8
Figure 2-5 Spindle positioning example
Figure 2-4 Y-axis locks
vise, or otherwise clamped to the table,
Figure 2-5.
.
1. Install an edge-finder in collet or chuck
(a tip diameter of 0.2" is assumed).
2. Lock the X-axis by tightening both
screws, Figure 2-3.
3. If the reference edge is to the back the
spindle centerline, do nothing; if not,
rotate the Y-axis handwheel clockwise
to send the workpiece backwards
(toward the column).
4. With the spindle running, lower the quill
as necessary, then bring the table
forward (counter-clockwise), stopping
at the point where the edge-finder just
makes contact (the tip jumps out of line).
Stop the spindle.
5. While holding the Y-axis handwheel to
prevent movement, zero the dial.
6. Raise the quill, then rotate the
handwheel one exact full turn counter-
clockwise (0.1") to bring the reference
edge to the spindle centerline.
7. Rotate the handwheel 2-1/2 turns
counter-clockwise to bring 50 on the dial
opposite the datum; the spindle is now
0.25" to the back of the reference edge.

PM-727 Manual 2015 v2.docx 9
Figure 2-6 Quill downfeed controls
The quill pinion is driven by the lever hub (1). The fine control
knob (2) is connected by a worm gear to the sleeve (3), which
is free to rotate –doing nothing to the quill –if it is not meshed
with the lever hub. Do this by tightening knob (4).
QUILL DOWNFEED
The quill is controlled in two different ways, coarse and
fine.
In the drilling mode, coarse feed , the mill functions like
a standard drill press –pull the upper lever toward you
to lower the quill. For milling operations the lever hub is
disengaged, and the quill is controlled by the fine
downfeed handwheel. The quill is locked by a lever on
the left of the headstock, see page 1.
Coarse feed (Figure 2-6)
For drilling operations, loosen knob (4), allowing the
lever hub to rotate independently of sleeve (3).
Fine feed (Figure 2-6)
For milling operations calling for precise, repeatable
control of tool depth, tighten knob (4) to engage hub (1)
with the internal taper on sleeve (3). Tighten the Z-axis
locks, Figure 2-8.
Rotate the fine control knob (2) to raise or lower the
quill. Lower the quill by rotating the fine control knob
clockwise ??, positioning it precisely either by
counting divisions on the graduated dial, or by
reference to the digital readout (DRO), Figure 2-1. Use
the locking lever left of the headstock to hold the quill
firmly in position.
If division-counting, be aware of backlash in the worm drive. This means that the handwheel must always be
turning in the same direction throughout the entire process, from setting a reference level to subsequent
cutting passes at specific depths –see the backlash discussion in "Moving the table", above. Using the DRO –
which has no backlash issues –is less laborious, but remember that the quill is spring-loaded. This calls for
care when releasing the quill locking lever prior to repositioning the quill downward. If the fine control knob has
been allowed to disengage (backed off counter clockwise ??), the quill will jump up by 0.01" or more. To avoid
this, make sure the fine control is firmly clockwise, lightly loading the quill rack, before releasing the locking
lever.
DRO
The DRO is in metric mode when switched on. Press the mm/in button to display inches. By pressing and
holding the Up arrow (incrementing) or Down arrow (decrementing) the display can be set to a chosen value.
The longer the buttons are held down, the faster the change in displayed value. Zero the display at any time by
pressing the ON/O button.
Switch off the DRO when not in use!
Replace the battery by sliding the cover (small arrow) to the right. For longer battery life use a 1.5V silver
oxide battery, SR44 or equivalent.
Other manuals for PM-727M
1
Table of contents
Other Precision matthews Power Tools manuals
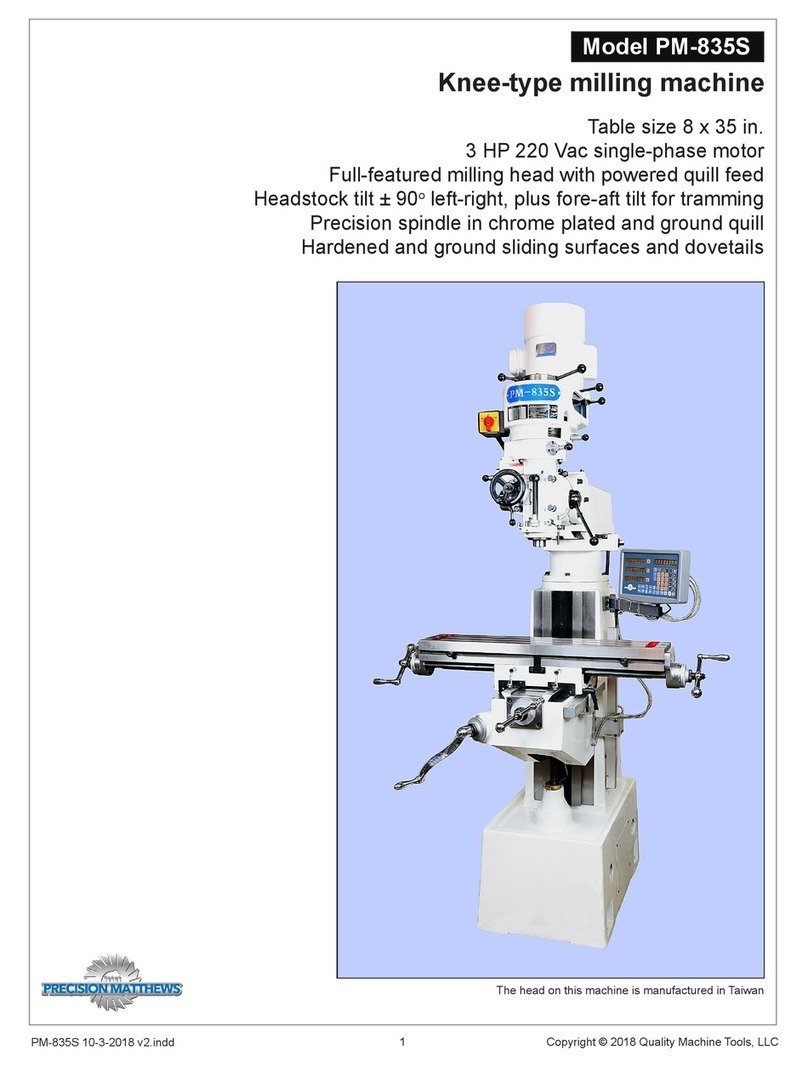
Precision matthews
Precision matthews PM-835S User manual
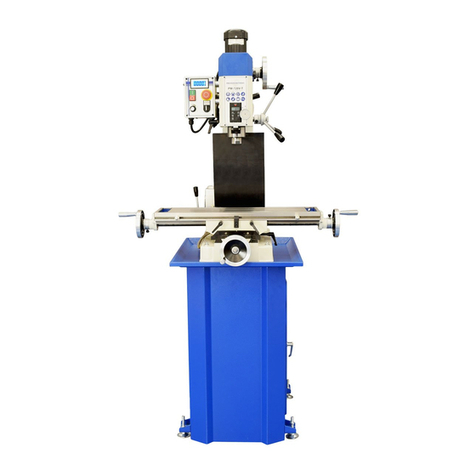
Precision matthews
Precision matthews PM 728V-T User manual
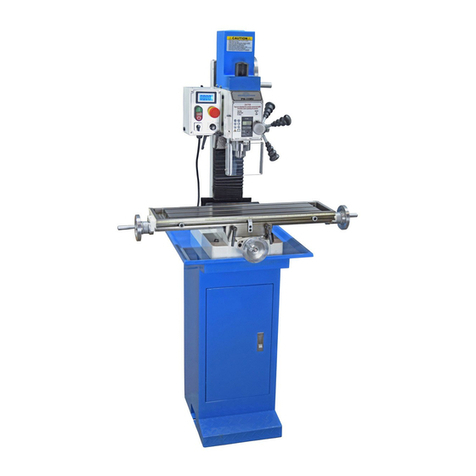
Precision matthews
Precision matthews PM 25MV-BD User manual
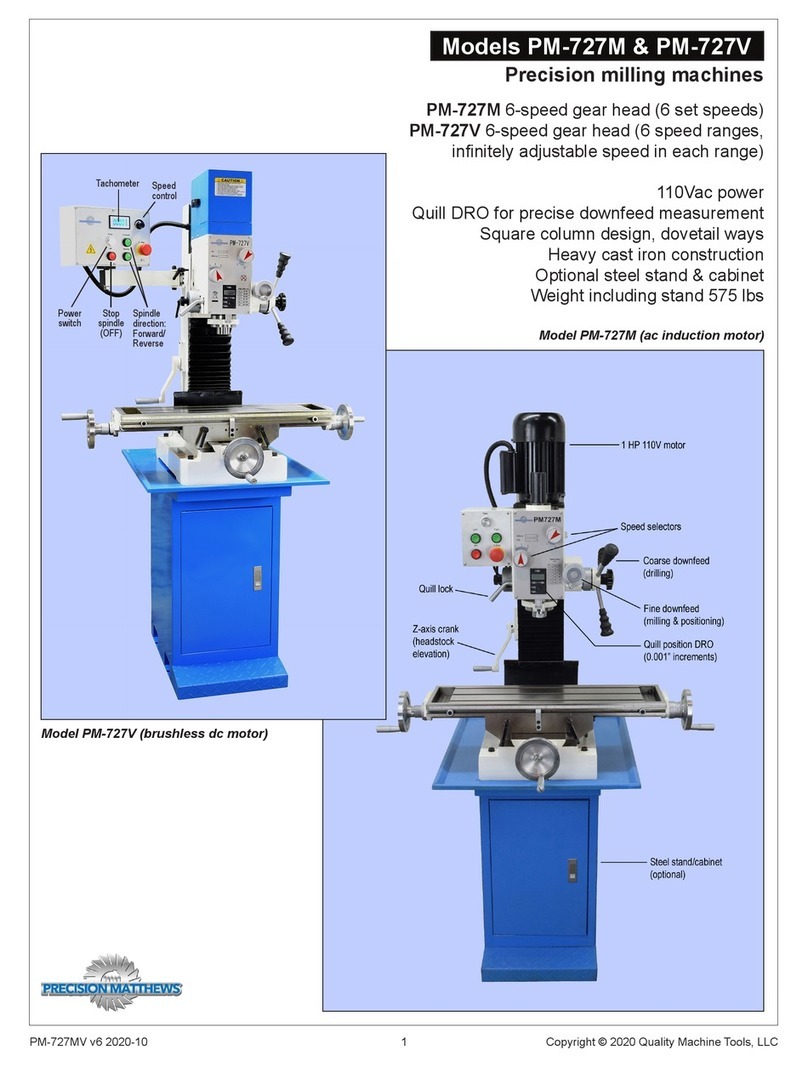
Precision matthews
Precision matthews PM-727M User manual
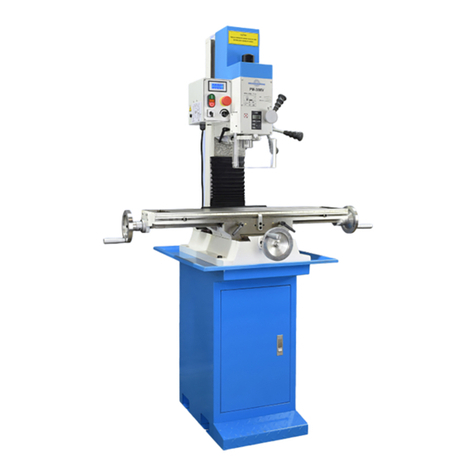
Precision matthews
Precision matthews PM-30MV User manual
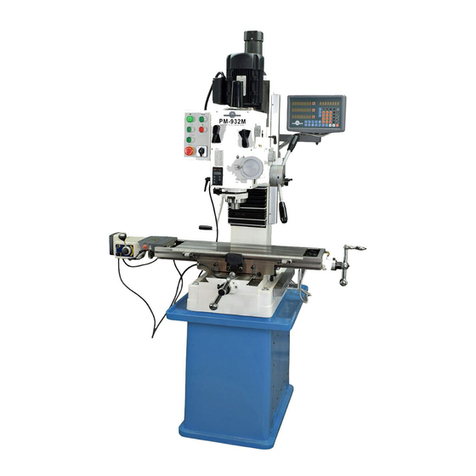
Precision matthews
Precision matthews PM-932M User manual
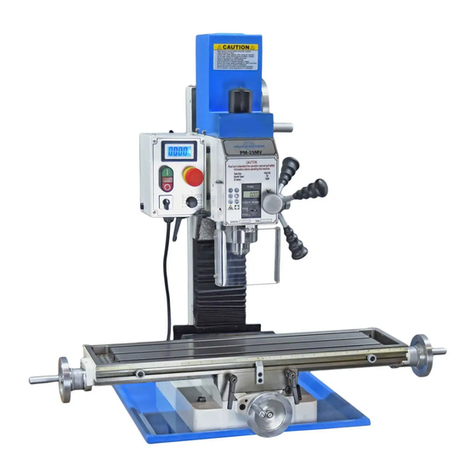
Precision matthews
Precision matthews PM-25MV User manual
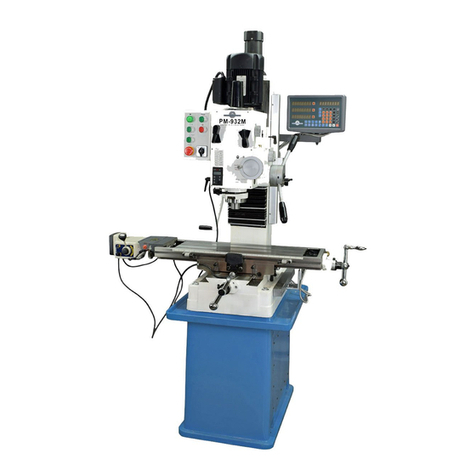
Precision matthews
Precision matthews PM-932M User manual
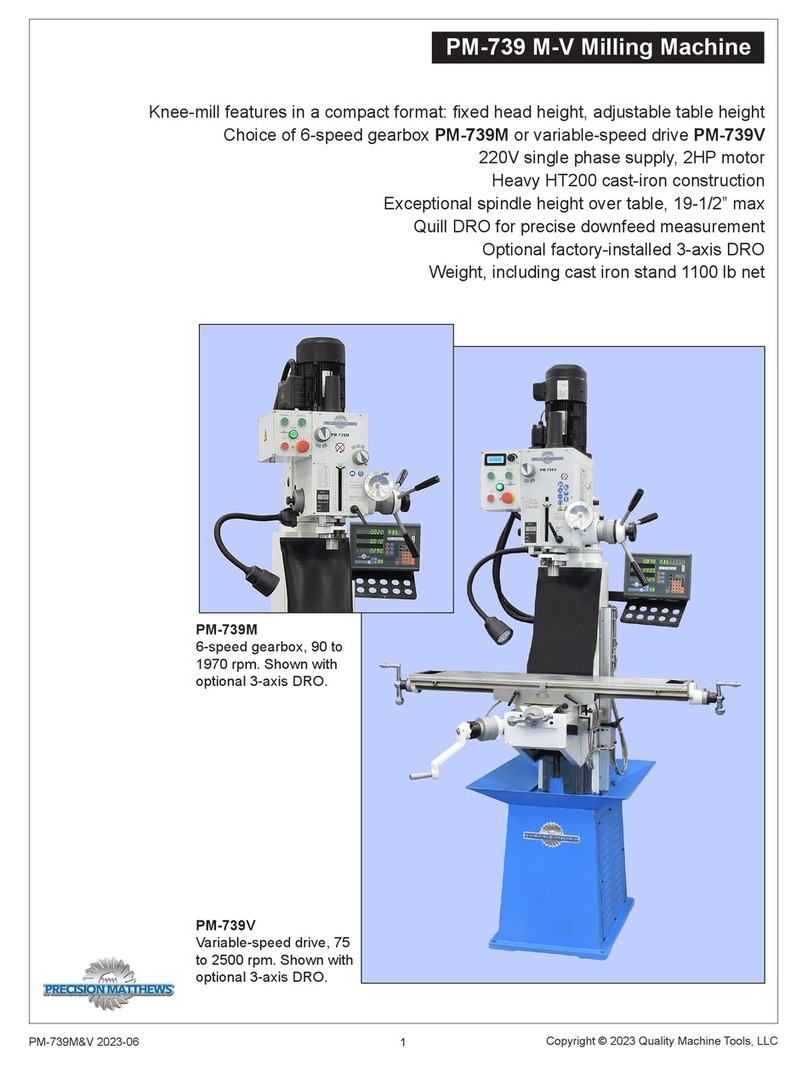
Precision matthews
Precision matthews PM-739M User manual
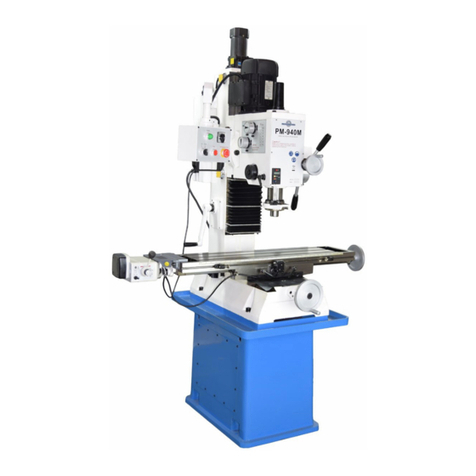
Precision matthews
Precision matthews PM-940M User manual