Precision matthews PM-835S User manual

1Copyright © 2018 Quality Machine Tools, LLC
PM-835S 10-3-2018 v2.indd
Table size 8 x 35 in.
3 HP 220 Vac single-phase motor
Full-featured milling head with powered quill feed
Headstock tilt ± 90oleft-right, plus fore-aft tilt for tramming
Precision spindle in chrome plated and ground quill
Hardened and ground sliding surfaces and dovetails
Knee-type milling machine
Model PM-835S
The head on this machine is manufactured in Taiwan

2 Copyright © 2020 Quality Machine Tools, LLC
PM-835S v3 2020-10
FAQ
Quill auto-feed
goes the wrong
way
The collet locating screw
could be in too far. Back it out
a little, procedure in Section
4.
R8 collets won’t go
into the spindle
Rattle/clunk noise
when changing from
LOW to HIGH speed
When the motor was turned
on the step-pulley spindle
teeth were not fully meshed
with the main spindle teeth.
See “Changing Spindle
Speed” in Section 3.
The quill doesn’t move
when the ne hand-
wheel is turned
Auto feed disengaged?
Quill unlocked?
Feed direction plunger
Neutral?
Move the feed lever
(arrowed) to the left. Check the feed direction
plunger.
This manual contains essential safety advice on the proper setup, operation, maintenance, and service of the PM-835S
knee mill. Failure to read, understand and follow the manual may result in property damage or serious personal injury.
There are many alternative ways to install and use a milling machine. As the owner of the machine you are solely responsible
for its proper installation and safe use. Consider the material contained in this manual to be advisory only. Precision Matthews
cannot be held liable for injury or property damage during installation or use, or from negligence, improper training, machine
modications or misuse.
Information in this manual relates to PM-835S mills as shipped from
January 2018. There may be detail dierences between your specic
machine and the information given here (with little or no impact on func-
tionality). Please email us if you have questions about any aspect of the
manual or your machine (see our website www.precisionmatthews.com
for support addresses). Your feedback is welcomed!
This material was originated by Precision Matthews. No portion
of the manual may be reproduced or distributed in any form
without the written approval of Quality Machine Tools, LLC.
UP
DOWN
NEUTRAL

3Copyright © 2020 Quality Machine Tools, LLC
PM-835S v3 2020-10
Dimensions in inches (un-
less otherwise stated)
Table length 35
Table depth 8
Overall height 91
AOverall width (table fully L to fully R) 74
B min Depth, ram forward 46
B max Depth, ram fully retracted 58
CBase footprint: width, left to right 20
DBase footprint: depth, front to back 32
X axis travel 22.5
Y axis travel 10.0
Z axis travel 15.0
Spindle nose to table surface (min) 2.0
max 17.0
*Spindle centerline to Z ways (min) 8.75
max 18.5
Ram travel 10
Quill travel 5.0
Quill diameter 3.375
Left/right head tilt ±90º
Forward/backward head tilt ±5º
Approximate net weight (lb) 1550
Floor
plan
ref.
Section 1 FEATURES & SPECIFICATIONS
PM-835S MILLING MACHINE
PM-835S oor plan
*Z-ways means the front
surface of the vertical
(knee) dovetails
T-slot dimensions
PM-835S T-slots are 14 mm = 0.551 in.
wide, compatible with 1/2 in. diameter
threaded studs, T-bolts, etc.

4 Copyright © 2020 Quality Machine Tools, LLC
PM-835S v3 2020-10
• Full-featured head with auto (powered) quill feed
• Headstock tilt ± 90º left-right, ±5º forward-backward
• Hardened and ground ways
• High precision inch-pitch lead screws (5 TPI)
• Ground, hard chrome-plated quill, honed quill bore
• 3-step auto quill feed: 0.0015”, 0.003” and 0.008”
per spindle revolution
• Precision spindle: high quality angle-contact bear-
ings, runout less than ± 0.0002”
• Head pulleys balanced for smooth operation
• One-shot lubrication
SUMMARY OF FEATURES
1
2
11
10
9
8
7
13
3
4
5
12
6
14
15
1. Spindle HI/LO cam lever
2. Motor handle
3. Motor lock lever
4. Back gear selector
5. Quill auto feed ON/OFF
6. Quill manual feed handle
7. Quill lock
8. Micrometer depth stop
9. Quill auto feed lever
10. Quill auto feed direction plunger
11. Quill ne feed handwheel
12. Quill auto feed rate selector
13. Motor switch
14. Motor pivot
15. Spindle brake

5Copyright © 2020 Quality Machine Tools, LLC
PM-835S v3 2020-10
Section 2 INSTALLATION
Cleanup
Finished metal surfaces such as the ways and table are pro-
tected in shipping by grease and/or paper. After uncrating the
mill, clean the nished surfaces using a plastic paint scraper,
disposable rags, and a light oil such as WD-40.
Reverse the hand cranks, if they were installed inside out for
shipping (or they may have been shipped loose).
Preliminary oiling
Before cranking the table, knee, saddle and ram into position
for hoisting, apply oil to the ways using the one-shot oiler — a
couple of pump strokes should be sucient. Crank the table,
knee and saddle through at least one end-stop to end-stop
cycle. If the lube reservoir is empty, replenish with Mobil Vactra
No. 2 or equivalent (see Section 4, Maintenance).
Moving the head
If it is necessary to swivel the head for hoisting purposes, par-
tially loosen the four head mounting bolts, Figure 2-1, while
supporting the head to prevent sudden movement. Continue
supporting the head while using a wrench on hex head #1,
Figure 2-2, to crank the head to the desired position. Tighten
the bolts in the diagonal sequence, Figure 2-1, rst pass at 25
lb-ft torque, second pass at 50 lb-ft. Over-tightening can distort
the head, causing the quill to bind.
Do not move the table, saddle, knee — or any
other movable part — until everything has been
thoroughly cleaned and lubricated, see below
Figure 2-2 Head swivel & head forward/backward tilt
Use a hex wrench to crank the head clockwise/counter-clockwise (1)
— support the head manually while turning to ease pressure on
the worm. Socket head cap screw (2) bears on a ledge on the head
support casting, allowing a few degrees angular adjustment forward
and back.
Site preparation
The oor must be capable of rigidly supporting a weight of at
least 1 ton. If possible, secure the mill to the oor with anchor
bolts. Alternatively, use pads and leveling screws installed in
holes in the machine base (pads are available from Precision
Matthews).
If the machine is to be bolted down, be sure that all four cor-
ners of the base are solidly in contact with the oor after the
machine has been leveled, see below. Use metal shims to
correct if necessary.
Lifting the mill
See Figures 2-3 and 2-4 for alternatives. Go slow! Check for
balance as the mill is clearing the pallet or oor. It may be nec-
essary move the head for clearance, and/or to adjust the knee,
table and ram for balance.
Leveling
Check for clearance around the mill before settling on its nal
location. Using a precision machinist’s level check the table
lengthwise (X) and crosswise (Y), shimming as necessary un-
der the base, or adjusting the leveling screws.
Figure 2-1 Head mounting bolts
The numbers indicate the correct (diagonal) tightening sequence.
2
31
4
Head
support
casting
1
2

6 Copyright © 2020 Quality Machine Tools, LLC
PM-835S v3 2020-10
Figure 2-4 Hoisting by slings
Move the ram in or out as necessary. Protect the ram ways with
padding.
Figure 2-3 Hoisting by eyebolt
The head is shown here swiveled 90º counter-clockwise.
Power hook-up
• Before running the machine, be sure that the spindle and
quill are properly lubricated, see Section 4.
• Remove any clamps or other temporary items that might
interfere with normal operation of the machine.
• Check the available power supply for compatibility with
the motor.
• Check for correct spindle rotation. With the motor switch
set to FWD and the SPEED RANGE selector set to HI,
the spindle should rotate clockwise when viewed from the
top of the machine (single-phase motors are pre-wired
that way). Three-phase motors can be reversed by phase
swapping.
• Some users prefer the FWD rotation to be clockwise when
the back gear selector is set to LO. This calls for re-wiring
if the motor is single-phase.
Tighten all bolts
and lock levers
before lifting
Tighten all bolts
and lock levers
before lifting
Eyebolt
thread
M20 x 2.5

7Copyright © 2020 Quality Machine Tools, LLC
PM-835S v3 2020-10
Everyday precautions
• This machine is intended for use by experienced users familiar with metal-
working hazards.
• Untrained or unsupervised operators risk serious injury.
• Wear ANSI-approved full-face or eye protection at all times when using the
machine (everyday eyeglasses are not reliable protection against ying par-
ticles).
• Wear proper apparel and non-slip footwear – be sure to prevent hair, clothing
or jewelry from becoming entangled in moving parts. Gloves – including tight-
tting disposables – can be hazardous!
• Be sure the work area is properly lit.
• Never leave chuck keys, wrenches or other loose tools on the machine.
• Be sure the workpiece, toolholder(s) and machine ways are secure before
commencing operations.
• Use moderation: light cuts, low spindle speeds and slow table motion give
better, safer results than “hogging”.
• Don’t try to stop a moving spindle by hand – allow it to stop on its own.
• Disconnect 220 Vac power from the mill before maintenance operations such
as oiling or adjustments.
• Maintain the machine with care – check lubrication and adjustments daily
before use.
• Clean the machine routinely – remove chips by brush or vacuum, not com-
pressed air (which can force debris into the ways).
No list of precautions can cover everything.
You cannot be too careful!

8 Copyright © 2020 Quality Machine Tools, LLC
PM-835S v3 2020-10
Section 3 USING THE MILL
MOVING THE TABLE
Left-right movement of the table is said to be the X-axis (a.k.a.
“longitudinal” or “traverse”). Front-back movement is the Y-
axis, sometimes called “cross travel”.
Each axis has a leadscrew with handwheel and micrometer
collar with 0.001” divisions, 0.1” per revolution, Figure 3-1. If
the mill is not equipped with digital readouts (DROs), the table
can be accurately positioned by counting whole turns and divi-
sions, keeping leadscrew backlash in mind. This means that
table motion must always be in the same direction when ap-
proaching the point of reference, then onward by a specied
amount to the desired location, see “X & Y axis positioning”,
later in this section.
Figure 3-3 Knee locking levers (arrows)
Figure 3-1 Example leadscrew handle & micrometer dial
The micrometer dial is resettable. It is locked to the leadscrew by a
knurled collar. Loosen the collar to rotate the dial to a desired setting,
then re-tighten.
Be sure to loosen the lock levers before moving
the table, especially under power (if so equipped)
POSITIONING THE KNEE
A micrometer collar graduated in 0.001" divisions allows the
knee elevation to be accurately set when cranked by hand,
Figure 3-2 (5).
If the mill is not equipped with a Z-axis digital readout (DRO),
the knee can be accurately positioned by counting whole turns
and divisions. To eliminate the eect of backlash, motion of the
knee must always be in the same direction when approaching
the point of reference, then onward by a specied amount to
the desired location.
Figure 3-2 Table stops & locking levers
The center bracket (1) and adjustable stops (2) allow the table to be
traversed to exact end points in repetitive operations (hand-powered
only). Two locking levers (3) are provided for the X axis, either side of
the center bracket, one lever only for the Y axis (4). Crank handle (5)
adjusts the vertical position of the knee, Z axis.
TILTING THE HEAD
The PM-835S mill has a two-way adjustable head. It can be
swiveled ±90º clockwise/counter-clockwise, also tilted ±5º
Figure 3-4 Head swivel
Support the head manually while turning to ease pressure
on the worm drive. Use a standard wrench to crank the head.
1
22
3
3
4
5
One-shot lube
reservoir

9Copyright © 2020 Quality Machine Tools, LLC
PM-835S v3 2020-10
2
31
4
Figure 3-5 Head mounting bolts
The numbers indicate the correct (diagonal) tightening sequence.
MOVING THE RAM & TURRET
In everyday use the turret is usually set with the ram at right
angles to the X-axis table, Figure 3-7. Angular adjustment is
approximately ± 5o(arrows).
The adjustable ram allows great flexibility in dealing with vari-
ous workpiece sizes and shapes. Make sure that the gib strip
is tight, and that the dovetails are properly lubricated (the one-
shot lube system does not supply the ram).
Figure 3-7 Ram and turret adjustments
To move the ram forward or backward, release the clamp screws, then
turn the pinion shaft. Adjust the gib screws for tight but smooth move-
ment of the ram.
The headstock is top heavy, so test for moveability as you
carefully loosen the bolts. To prevent damage when cranking
the swivel axis worm, or the front-to-back adjusting screw, the
head should be supported manually until the bolts are re-tight-
ened. Be especially careful if the head has not been moved
before. The paint seal may let go without warning.
Set the headstock to the desired angle then re-tighten the
bolts. For the clockwise/counter-clockwise axis, re-tighten in
a diagonal sequence, Figure 3-5, rst pass at 25 lb-ft torque,
second pass at 50 lb-ft. (Over-tightening can distort the head,
causing the quill to bind.) Use the same torque settings on the
other tilt axis.
The tilt scales are good only to approximately ± 0.25o, so a
more accurate means of angle measurement will be needed if
the project calls for a precise oset or, for everyday milling and
drilling, true vertical in both axes. This is done by tramming the
head, described later in this section. [Because tramming is a
time consuming process, most machinists look rst for other
ways to handle the project instead of moving the head.]
front-to-back for head tramming (described later in this sec-
tion). A worm drive adjuster is provided for the swivel axis
(only), Figure 3-4. Clamping bolts for the swivel axis are shown
in Figure 3-5.
Figure 3-6 Forward tilt adjustment
The head can be adjusted front-to-back approximately ±5º. Loosen
the clamp screws on both sides, white arrows, then adjust using a hex
key, black arrow.
Ram
clamp
screws
Pinion
shaft
Gib
screw
Gib
screw
Check lubrication, clamping bolts, locking
levers, tooling before powering up
FORWARD spindle rotation is usually said to be clock-
wise, looking down on the workpiece.
Spindle speed is determined by the combination of pulley ratio
between motor and spindle (four choices), and spindle-to-mo-
tor coupling (two choices). For high speeds the 4-step driven
pulley is directly coupled to the spindle. For low speeds the
driven pulley is connected to the spindle through a back gear.
Key fact ...
The back gear reverses the direction of spindle rotation. If
the spindle turns clockwise in the high range when the motor
switch is set to FWD, it will turn counter-clockwise in the low
range. For clockwise rotation in the low range, set the motor
Spindle
speed
(rpm)
LO
Back gear
engaged
80
135
210
325
HI
Back gear
disen-
gaged
660
1110
1750
2720
RUNNING THE SPINDLE
SPINDLE SPEED

10 Copyright © 2020 Quality Machine Tools, LLC
PM-835S v3 2020-10
Figure 3-8 Drive components
To engage/disengage the back gear, pull on the black knob then swing
the crank handle. Back gear IN = LOW speed, back gear OUT = HIGH
speed. Take extra care when changing from LOW to HIGH.
CHANGING SPINDLE SPEED
Make sure the spindle is
stopped — POWER OFF —
before touching the Vee belt
for ANY REASON
Repositioning the Vee belt
Figure 3-8 shows one of the two motor clamp levers, one on
each side. Loosen both levers, then swing the motor forward
to de-tension the belt. Reposition the belt, then reverse the
procedure.
Engaging/de-engaging the back gear
HIGH to LOW
1. Move the spindle cam lever to the right (this raises the
driven pulley).
2. Move the SPEED RANGE crank to the LOW detent posi-
tion, Figure 3-1. (LOW = back gear IN)
3. Run the spindle. Rotation OK? Switch FWD/REV if not.
Going from LOW to HIGH is not simply the reverse of
HIGH to LOW!
LOW to HIGH
1. Move the spindle cam lever to the front.
2. Push on the Vee belt, Figure 3-9, until you hear the clutch
dogs engage (signifying that the driven pulley has dropped
into position). Until that happens don’t apply power!
3. Move the SPEED RANGE lever to the HIGH detent posi-
tion. (HIGH = back gear OUT)
4. Run the spindle. Rotation OK? Switch FWD/REV if not.
INSTALLING & REMOVING TOOLING
The spindle and drawbar are designed for R-8 taper collets,
drill chucks and other arbors with the standard 7/16”-20 inter-
nal thread. When installing or removing tooling, pull the spindle
brake handle toward you to stop the spindle rotating, Figure
3-10.
To install a tool, install the R-8 device (collet or arbor) in the
spindle bore, then thread the drawbar into it by as many turns
as it takes to bottom-out the drawbar head on top of the spin-
dle. (Washers may be required if the device's internal thread
is too short, or damaged.) Tighten the drawbar with a 19 mm
(or 3/4″) wrench.
To remove R-8 tooling, loosen the drawbar then tap it with a
brass or dead-blow hammer to unseat the taper. Unscrew the
drawbar by turning the upper nut with one hand while sup-
porting the R-8 device with the other.
Keep in mind that the table, vise and work-
piece can be damaged by falling tools and drill
chucks. The cutting tool itself can also be dam-
aged in the same way.
Figure 3-9 Switching from LOW to HIGH range
One way to make sure the drive system is properly set before
switching on the motor is to turn the spindle by hand. Another way,
inset photo, is to push back on the outer surface of the belt with
ngertips until you hear the clutch engage.
switch to REV.
Some users prefer the alternate choice of FWD = clockwise
rotation in low speed. This will require rewiring of the motor
switch.
Clamp
lever
Motor
handle
Back gear
IN/OUT
Cam
lever
DrawbarSpindle
brake
Auto quill feed
OFF ON
Figure 3-10 Spindle brake
Spindle
brake
Cam
lever
POWER OFF... Take care
when doing either of these!
Keep ngers away from
cutters and from the inner
surface of the belt.

11 Copyright © 2020 Quality Machine Tools, LLC
PM-835S v3 2020-10
QUILL DOWNFEED
The quill is moved in three dierent ways: manual coarse,
manual ne, and powered (auto quill feed).
Coarse manual downfeed
In this mode the mill functions like a standard drill press —
lower the quill using the quill manual feed handle, Figure 3-11.
Before operating the manual feed handle, unlock the quill.
Stop the spindle and disengage the quill auto feed (crank at
right of the head).
The feed handle hub, Figure 3-12, is held on the quill pinion
shaft by a spring-loaded ball and a detent groove on the outer
end of the shaft. A pin on the hub locates in one of 12 holes in
an index plate keyed to the shaft.
To reposition the manual feed handle relative to the index
plate, pull the hub about 1/4” away o the plate, then re-index
the hub to a dierent location.
Figure 3-12 Quill manual feed handle and index plate
Quill manual
feed handle
Quill auto
feed ON/OFF
(engaged/dis-
engaged)
Feed rate
selector
ON OFF
Figure 3-11 Quill controls
Fine feed handwheel
Quill lock
Micrometer
depth stop
Quill auto
feed lever
Fine manual downfeed
For milling operations calling for better control of tool depth,
use the ne feed handwheel.
1. With the spindle stationary, disengage the quill auto feed
(crank at right of the head).
2. Unlock the quill.
3. Set the quill auto feed direction plunger to neutral (mid
position), Figure 3-13.
4. Swing the quill auto feed lever to the left.
The quill is now under handwheel control.
NOTE 1: Clockwise rotation of the handwheel causes the quill
to descend.
NOTE 2: The handwheel is often removed for better visibility
of the micrometer scale.
NOTE 3: In common with other knee mills there is no indica-
tion of down feed amount unless a DRO is installed on the
quill. Most users control cutting depth by locking the quill then
raising the knee in precise increments.
Figure 3-13 Auto feed direction plunger
Moving the plunger from fully in to fully out reverses feed direction.
The center position is neutral, no down feed. UP and DOWN direc-
tions here apply to clockwise spindle rotation — vice-versa for count-
er-clockwise rotation.
UP
DOWN
NEUTRAL
QUILL AUTO FEED
The auto feed system can be set to drive the quill either up or
down at a choice of three speeds, Figure 3-14. A clutch mech-
anism disables the drive when overloaded (as shipped, the
clutch is adjusted for a drilling capacity of about 3/8” in mild
steel).
Be sure the quill is unlocked before auto feeding

12 Copyright © 2020 Quality Machine Tools, LLC
PM-835S v3 2020-10
Figure 3-14 Quill feed components
Overload
clutch trip
lever Quill auto
feed lever
Quill manual
feed handle
Fine feed
handwheel
Auto feed ON Auto feed OFF
Figure 3-15 Activating the quill auto feed
* Feed direction and rate can be changed at any time while
the spindle is running.
Auto feed will terminate when the stop collar reaches the mi-
crometer depth stop, tripping the quill auto feed lever to the
right.
The tripping point is accurate only to within ± 0.01”. For a more
precise end point (± 0.001”), hand feed to a dead stop.
Feed rate
selector
1. Set the micrometer depth as required, Figure 3-11.
2. With the spindle stationary, engage the quill auto feed
(crank at right of the head).
3. Select* a feed direction, Figure 3-13. The directions given
in this gure apply to the usual spindle direction for drill-
ing, clockwise looking down.
4. Select* a feed rate, Figure 3-14: 0.0015”, 0.003” and
0.008” per spindle revolution.
5. Start the auto feed action by pushing the quill auto feed
lever to the left, Figure 3-15.

13 Copyright © 2020 Quality Machine Tools, LLC
PM-835S v3 2020-10
Figure 3-16
Auto feed schematic
The auto feed system’s many
inter-dependent parts are ad-
justed in manufacture for trip-
ping action and clutch torque.
They will not normally need
attention. If you are consider-
ing any adjustments, please
contact Precision Matthews
for guidance.

14 Copyright © 2020 Quality Machine Tools, LLC
PM-835S v3 2020-10
Figure 3-17 is an example of Y-axis positioning. A hole is to be
drilled 0.25” on the Y-axis relative to the front edge of a work-
piece in a vise, or otherwise clamped to the table:
1. Install an edge-nder in collet or chuck (a tip diameter of
0.2” is assumed).
2. Lock the X-axis by tightening both levers.
3. If the reference edge is already to the back the spindle
centerline, do nothing; if not, rotate the Y-axis handwheel
clockwise to send the workpiece backwards (toward the
column).
4. Engage the ne downfeed.
5. With the spindle running, lower the quill with the downfeed
handwheel to bring the tip of the edge-nder just below the
top of the workpiece.
6. Bring the table forward (counter-clockwise), stopping at
the point where the edge-nder just makes contact (the tip
jumps out of line). Stop the spindle.
7. While holding the Y-axis handwheel to prevent movement,
zero the dial.
8. Raise the quill, then rotate the Y-axis handwheel one ex-
act full turn counter-clockwise (0.1”) to bring the reference
edge to the spindle centerline.
9. Rotate the handwheel 2-1/2 turns counter-clockwise to
bring 50 on the dial opposite the datum; the spindle is now
exactly 0.25” behind the reference edge.
Figure 3-17 Spindle positioning example
both axes, in other words trammed.
“Out of tram” may show up as an oset of a few thousandths
between entry and exit of a deep hole, or as a scalloped eect
when surfacing a workpiece with a large-radius y cutter, high-
ly exaggerated in Figure 3-18.
Figure 3-18 Head tilt can aect workpiece surface atness
This shows the eect when y-cutting if the head is tilted left or right
(clockwise/counter-clockwise). Front to back tilt causes a similar scal-
loping eect in the other axis of the workpiece.
Figure 3-19 Sweeping holder for dial indicator
This example shows a rectangular section aluminum bar with threaded
holes allowing the choice of two sweep diameters, 6” and 10”, mea-
sured from spindle centerline to indicator tip. The smaller sweep can
be used for front-to-back tramming, also left-to-right as here. For more
sensitive left-to-right tramming, use the larger sweep.
X & Y-AXIS POSITIONING BY COUNTING
DIVISIONS
Note: The following procedure shows how to eliminate the
leadscrew backlash factor when dead reckoning. This also ap-
plies to the knee: when counting divisions on the knee dial, the
knee must be traveling in the same direction when approach-
ing a point of reference, then onward by a specic number of
divisions to the desired location.
TRAMMING THE HEADSTOCK
“Tram”, short for trammel, means accurate alignment — in
this case adjusting the headstock tilt to bring the spindle to a
known angle — usually 90 degrees — relative to the table. This
is essential for routine operations in which the user relies on
squareness of the spindle relative to both axes of the table.
Unless it was swiveled 90 degrees for compactness in ship-
ping, the head is usually installed accurately enough for initial
out-of-the-box test drillings, etc. If the head was swiveled, it
can be zeroed with ± 0.25oaccuracy by reference to the at-
tached scale. For more demanding project work thereafter, the
spindle needs to be precisely set at 90 degrees to the table in
Tramming is the process of ne-tuning the headstock tilt angle.
Tram is typically checked by attaching a dial indicator to some
form of “sweepable” holder installed in the spindle, the aim
being to adjust tilt for the same reading on either side of the X
axis. The longer the radius arm, the greater the sensitivity.
Figure 3-19 shows a typical shop-made holder; it has a thread-
ed arbor allowing the choice of two radius arms, 6 and 10 inch-
es measured from spindle centerline to indicator tip. A collet is
used to hold the arbor, in this case 5/8” diameter. The dimen-
sions are arbitrary, but note that the indicator must be rmly
attached, and the arm rock-solid relative to the indicator spring
force (which can be a factor with plunger-type indicators).
A suggested procedure for establishing tram in the X axis:
1. Disconnect power.
2. Set the headstock to the approximate zero degree posi-
tion on the tilt scale, then tighten the three nuts enough to
avoid unexpected headstock movement.
3. Remove the vise and clean the table surface.

15 Copyright © 2020 Quality Machine Tools, LLC
PM-835S v3 2020-10
Tramming calls for patience on any mill! Expect to
tighten and re-check at least three times (simply
tightening the bolts can aect the tram).
INSTALLING & INDICATING A VISE
For routine milling operations the workpiece is usually held in
a precision vise. “Indicating” means checking the alignment of
the xed (back) vise jaw relative to the axis of table motion.
Install the T-bolts and align the vise by eye. With one of the
clamp nuts snug, but not tight, tighten the other one just short
of fully-tight (but tight enough so the vise won’t budge without
a denite tap from a dead-blow mallet).
Figure 3-20 Indicating the vise
The tip of a standard dial indicator, arrowed, rides on the face of a at
(ground) reference bar.
VISE KEYS
Most precision vises come with key slots on the underside ma-
chined exactly parallel to the xed jaw. Shop-made vise keys
can be a great time saver. Properly installed they allow the vise
to be removed and replaced routinely, accurately enough for
most jobs without the need for indicating every time.
Many precision vises have 14 mm slots. This is an exact match
for the PM-835S T-slots, in which case the keys will have par-
allel sides as in Figure 3-21 (wider slots in the vise will call for
T-shape keys). It is well worth the eort to make these pre-
cisely.
Aim for a snug t in both vise and table, but not so tight that
it takes more than reasonable eort to lift the vise clear. The
objective is allow the vise to be removed and replaced without
eort.
Case hardening of the keys is recommended, with nal tting
using a ne stone or diamond stone.
Figure 3-21 Keys installed on X-axis of vise
On most vises the keys can also be installed on the long axis
4. Set a 1-2-3 block (or other precision-ground block) on the
table under the indicator probe.
5. Raise the knee, or lower the spindle using ne downfeed,
to give an approximate half-scale indicator reading.
6. Record the exact readings on both the dial indicator and
the downfeed micrometer collar.
7. Lower the knee or back o the ne downfeed to avoid col-
lision when sweeping.
8. Select the highest spindle speed (this will allow you to
sweep the indicator holder easier from side to side).
9. Reposition the 1-2-3 block to the opposite location on the
table.
10. Swing the indicator holder to the new location, then lower
the spindle – ne downfeed again – to give the same dial
indicator and micrometer collar readings as in step (6).
If the headstock is perfectly trammed – highly unlikely at the
rst shot – the readings should be as in step (6). If not, loos-
en the 4 head bolts just enough to allow the headstock to be
worm-driven a fraction of a degree in the direction called for,
then re-tighten the bolts, Figure 3-5.
Repeat steps (5) through (10) until satised with the tram,
tightening the bolts as you go. This will likely call for several
iterations. There is no “right” tram; the acceptable dierence in
side-to-side readings depends on project specs. As a starting
point, aim for ± 0.001” on a radius of 5 or 6 inches.
A similar procedure is used to check tram in the Y-axis, front
to back.
A typical setup for indicating is shown in Figure 3-20. Use the
spindle lock to make sure that the spindle does not rotate
throughout the procedure. The tendency to rotate can also be
minimized by selecting the lowest spindle speed, taking up
any backlash by pushing against the indicator holder. Set the
indicator tip against the upper edge of a precision reference
bar or, if not available, use the front face of the xed jaw of
the vise instead (check for dings, hone if necessary). Adjust
the Y-axis to pre-load the indicator to mid range at the tight-
ly-clamped side of the vise, then lock the Y-axis.
Note the indicator reading, then watch the indicator as you tra-
verse the table slowly toward the loosely clamped side. Ideally,
there should be no discrepancy between the indicator read-
ings at the two ends — unlikely at the rst attempt. Return the
table to the starting point, then repeat the process, tapping the
vise in as you go. Repeat the process as often as necessary
for the desired accuracy, progressively tightening the “looser”
nut each time. Now fully tighten both nuts, and re-check again
(tightening a nut can itself introduce signicant error). An es-
tablished routine like this – tight to loose – can save a lot of
time.
There is no “right” setup for a vise, but as a starting point aim
for an indicator dierence of no more than ± 0.001” over the
width of the jaw.

16 Copyright © 2020 Quality Machine Tools, LLC
PM-835S v3 2020-10
Section 4 MAINTENANCE
Disconnect 220V power before any
maintenance operation!
Remove all machining debris and foreign ob-
jects before lubricating ANYTHING! If need
be, any oil is better than no oil – but use the
recommended lubricants when you can.
OILING PROCEDURE
Assuming a clean environment – no abrasive particles or ma-
chining debris – lack of proper lubrication is the main cause of
premature wear.
Figure 4-1 One-shot lube reservoir
The one-shot system oils the X, Y and Z dovetails. Inset is the left
end of the table, bearing bracket removed.
Before starting a work session, lubricate the X and Y dovetails
by operating the one-shot lube system, Figure 4-1. The recom-
mended oil for this is ISO68, Mobil Vactra No. 2 or equivalent.
(Don't overdo the lube action — one or two pump strokes will
usually be enough.) Distribute the oil evenly by running the
table full travel in both axes. Also check the following:
1. X & Y axis leadscrews: ISO68 oil, Vactra No. 2 or equiva-
lent. Apply by brush. Distribute the oil evenly by running
the table full travel in both axes.
2. Z axis leadscrew, Figure 4-2: NLGI No. 2 grease. Apply
by brush. Distribute the grease evenly by running the
knee up/down full travel.
3. Ram dovetails, Figure 4-3 (not lubricated by the one-shot
system): ISO68 oil, Vactra No. 2 or equivalent. Apply by
brush.
4. Quill: A few drops of ISO 32 (10W oil) in the oil cup,
Figure 4-4.
5. Quill rack and pinion, Figure 4-5. Fully lower and lock the
quill. Using a sti ux brush, clean the visible portions of
the rack. Apply by brush NLGI No. 2 grease. Raise and
lower the quill a few times to distribute the grease.
6. Back gear, Figures 4-6: Use a grease gun to apply NLGI
No. 2.
Figure 4-2 Z-axis leadscrew
Figure 4-3 Quill oilcup
Figure 4-4 Quill rack
Figure 4-5 Ram dovetails

17 Copyright © 2020 Quality Machine Tools, LLC
PM-835S v3 2020-10
DOWNFEED RETURN SPRING TENSION
The quill should automatically retract when the manual feed le-
ver is released following a drilling operation. If it fails to retract,
the return spring may need to be re-tensioned — but rst check
for other issued such as obstructions or lack of lubrication.
Fully raise the quill. Remove the feed handle, lock the quill,
then remove the two screws securing the pinion shaft index
plate, Figure 4-10. (Some pressure should be felt when the
second screw is loosened; if not, the spring may be broken, or
detached from the shaft — call Precision Matthews for guid-
ance.)
Allow the index plate to rotate to its neutral setting — spring
fully relieved. Using a pin wrench or needle-nosed pliers, ro-
tate the index plate clockwise 90ofrom neutral, then re-attach.
With the feed handle in place, check the return spring force. If
insucient, try one or two additional 45orotations.
GIB ADJUSTMENT
Gibs on the X, Y and Z axes control the t of the mating dove-
tailed surfaces. They are gently-tapered lengths of steel or
cast iron held in place by opposing screws at each end. Ad-
justing them is a trial and error process that takes time and
patience. Aim for the best compromise between rmness and
reasonably free table movement. Too tight means accelerated
wear on the ways, leadscrews and feed motors, if installed.
Too free means workpiece instability, inaccuracies and chatter.
BOTH gib screw heads must be tight against
the gib ends. If you loosen one, tighten the oth-
er. Remove the way covers for access to the
back of the Y gib and bottom of the Z gib.
COLLET LOCATING SCREW
R8 devices are located in the spindle by a special set screw
that protrudes less than 3/32" beyond the inner wall of the quill.
This may or may not be locked in place by a second, outer,
set screw. If your R8 devices meet spec, but consistently bind
when inserted, the inner screw may be in too far.
For access to the set screw(s), lock the quill, then loosen the
locking set screw in Figure 4-7. With a pin wrench or needle-
nosed pliers, Figure 4-8, remove the spindle nose-piece —
LEFT HAND thread. The collet locating screw should now be
visible below the quill, Figure 4-9. Adjust the screw depth using
a ball-end hex wrench (the screw may be too close to the quill
rim for a standard wrench).
Figure 4-8 Removing the nose-piece
Figure 4-7 Spindle nose-piece lock screw
Figure 4-9 Collet locating screw(s)
Figure 4-6 Back gear grease nipple
Figure 4-10 Quill index shaft index plate
Figure 4-11 Table (X axis) gib screw, left side

18 Copyright © 2020 Quality Machine Tools, LLC
PM-835S v3 2020-10
Figure 4-13 Saddle gib (Y axis), front
Figure 4-14 Saddle gib (Y axis), rear
Figure 4-15 Knee gib (Z axis), topside
Figure 4-16 Knee gib (Z axis), underside
LEADSCREW BACKLASH CORRECTION
When alternating between clockwise and counter clockwise
rotation of the X or Y leadscrews, the handwheel moves freely
a few degrees but the table stays put. This is backlash, a fea-
ture of all standard leadscrews. The acceptable amount of lost
motion depends on the user, but 0.005” is generally a good
compromise. Smaller numbers are possible, but overdoing it
can lead to premature wear of leadscrew and nut.
Each leadscrew nut comprises two internally-threaded com-
ponents, one xed, the other adjustable. Backlash is corrected
by rotating the adjustable nut shown in Figures 4-17 and 4-18.
Clockwise or counter-clockwise rotation of the nut has a simi-
lar eect in reducing backlash. Adjust backlash by rotating the
nut nger tight, then re-tighten the two socket head screws.
Figure 4-17 Table (X axis) backlash adjuster
Figure 4-18 Saddle (Y axis) backlash adjuster
Figure 4-12 Table (X axis) gib screw, right side

19 Copyright © 2020 Quality Machine Tools, LLC
PM-835S v3 2020-10
MILLING HEAD COMPONENTS Fig 1
There may be detail dierences
between this representative draw-
ing and the machine as supplied.
O-the-shelf hardware may not
be shown in all instances (some
locations call for US threads, some
Metric). To order replacement parts
from Precision Matthews, give the
Model number, Serial number, and
reference number on this drawing.

20 Copyright © 2020 Quality Machine Tools, LLC
PM-835S v3 2020-10
MILLING HEAD COMPONENTS Fig 1
Standard off-the-shelf hardware is omitted from this list. Items listed are unique fabricated or critical parts specic to the PM-835S mill.
Ref Description Part
3 Bevel gear Z7137
4 Worm gearshaft sleeve Z7138
5 Worm cradle bushing Z7139
8 Worm gear Z7140
9 Worm gearshaft Z7141
15 Bevel gear Z7142
16 Feed engage pin Z7143
17 Worm gear cradle Z7144
18 Cradle actuator Z7145
19 Flange Z7146
20 Shift plunger Z7147
21 Compression spring Z7148
23 Shift crank Z7149
27 Cluster gearshft bearing Z7150
28 Cluster gear assembly Z7151
31 Cluster gearshaft Z7152
32 Retaining ring Z7153
33 Bevel gear bearing Z7154
34 Spacer Z7155
35 Bevel gear Z7156
36 Feed drive gear Z7157
38 Cluster gear input shaft Z7158
40 Feed drive gear Z7159
41 Needle bearing Z7160
42 Bushing Z7161
43 Worm Z7162
44 Worm shaft bushing Z7163
48 Oilite bearing Z7164
49 Bevel gear Z7165
50 Dog clutch Z7166
51 Bevel gear Z7167
52 Oilite bearing Z7168
55 Feed dir. clutch rod Z7169
57 Feed worm shaft Z7170
60 Feed shift rod Z7171
63 Feed gear shift fork Z7172
64 Cluster gear shift crank Z7173
66 Cluster gear cover plate Z7174
Ref Description Part
68 Gear shift plunger Z7175
69 Compression spring Z7176
70 Shift crank Z7177
75 Clutch ring Z7178
77 Brass plug Z7179
78 Overload clutch locknut Z7180
79 Clutch spring Z7181
80 Overload clutch A Z7182
81 Overload clutch shaft Z7183
82 Spring washer Z7184
88 Compression spring Z7185
89 Overload clutch plunger Z7186
90 Quill pinion shft bshing Z7187
91 Spacer Z7188
92 Feed worm gear Z7189
93 Overload clutch B Z7190
96 Ovrload clutch trip lever Z7191
99 Clutch cover Z7192
103 Cam rod Z7193
104 Trip handle Z7194
106 Feed trip base Z7195
110 Feed direction stud Z7196
111 Feed direction plunger Z7197
113 Handwheel boss Z7198
115 Compression spring Z7199
116 Clutch spring screw Z7200
118 Sleeve assembly Z7201
120 Compression spring Z7202
121 Trip plunger sleeve Z7203
122 Plunger bushing Z7204
123 Plunger bushing Z7205
124 Trip plunger Z7206
125 Handwheel Z7207
126 Handwheel handle Z7208
127 Spindle Z7209
128 Quill skirt Z7210
129 Locknut Z7211
130 Tabbed washer Z7212
Ref Description Part
131 Ball bearing Z7213
132 Spindle sleeve Z7214
133 Spindle nose piece Z7215
134 Spindle shield Z7216
135 Ball bearing Z7217
136 Bearing spacer - large Z7218
137 Bearing spacer - small Z7219
138 Ball bearing Z7220
140 Set screw, special Z7221
141 Set screw, special Z7222
142 Quill Z7223
145 Feed trip lever Z7224
146 Trip lever pin Z7225
148 Quill lock sleeve A Z7226
149 Quill lock lever Z7227
152 Quill lock bolt Z7228
153 Quill lock sleeve B Z7229
155 Tee bolt Z7230
156 Tee bolt spacer Z7231
159 Scale Z7232
161 Quill stop nut Z6971
162 Micromemter nut Z6972
163 Quill stop knob Z6973
164 Quill stop screw Z6974
166 Quill pinion shaft Z6975
168 Spring pin Z7238
174 Compression spring Z7239
175 Handle hub Z7240
176 Index plate Z7241
177 Spring housing Z7242
178 Clock spring Z7243
180 Quill pinion Z7244
183 Reverse trip ball lever Z7245
184 Reverse trip plunger Z7246
185 Reverse trip lever screw Z7247
186 Head swivel worm Z7248
189 Worm shaft Z7249
192 Quill housing Z7250
Table of contents
Other Precision matthews Power Tools manuals
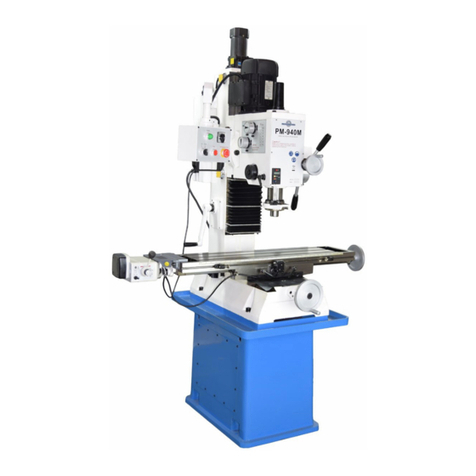
Precision matthews
Precision matthews PM-940M User manual
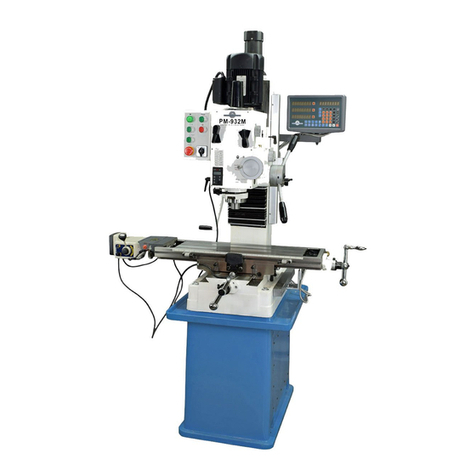
Precision matthews
Precision matthews PM-932M User manual
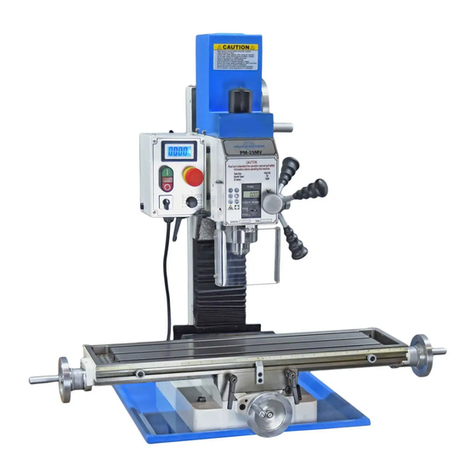
Precision matthews
Precision matthews PM-25MV User manual
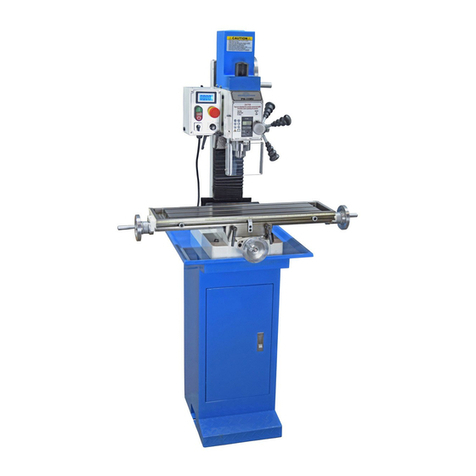
Precision matthews
Precision matthews PM 25MV-BD User manual

Precision matthews
Precision matthews PM-833TV User manual
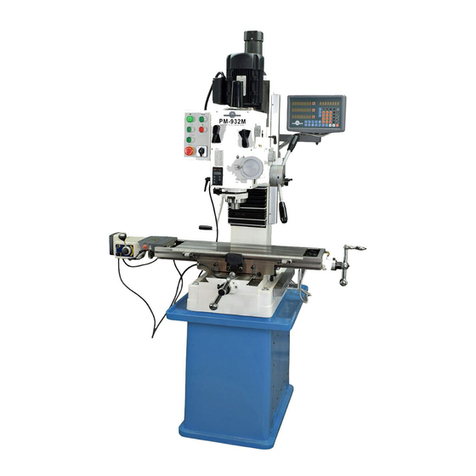
Precision matthews
Precision matthews PM-932M User manual
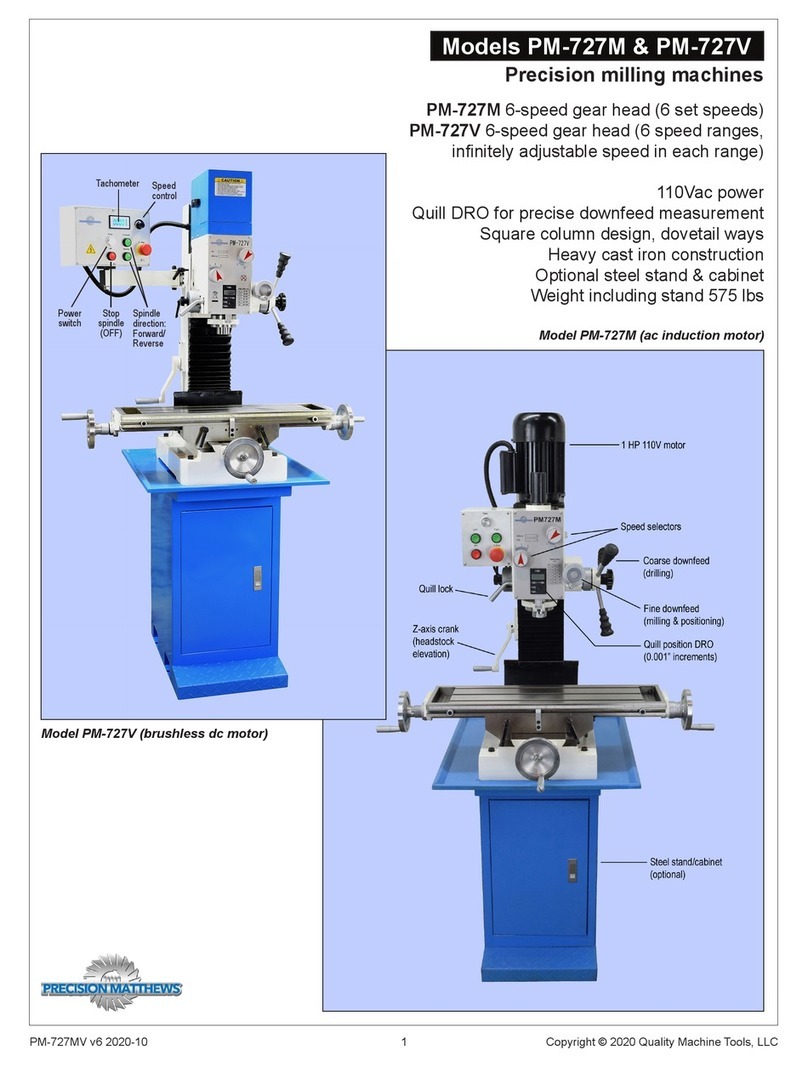
Precision matthews
Precision matthews PM-727M User manual
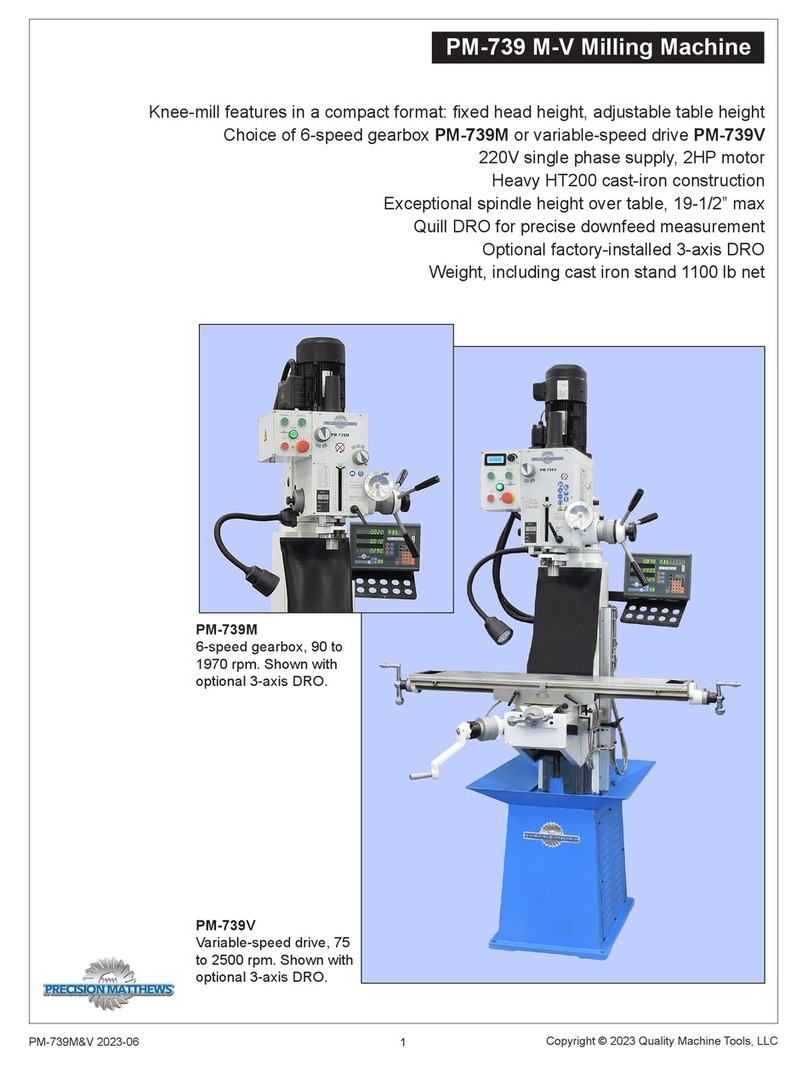
Precision matthews
Precision matthews PM-739M User manual
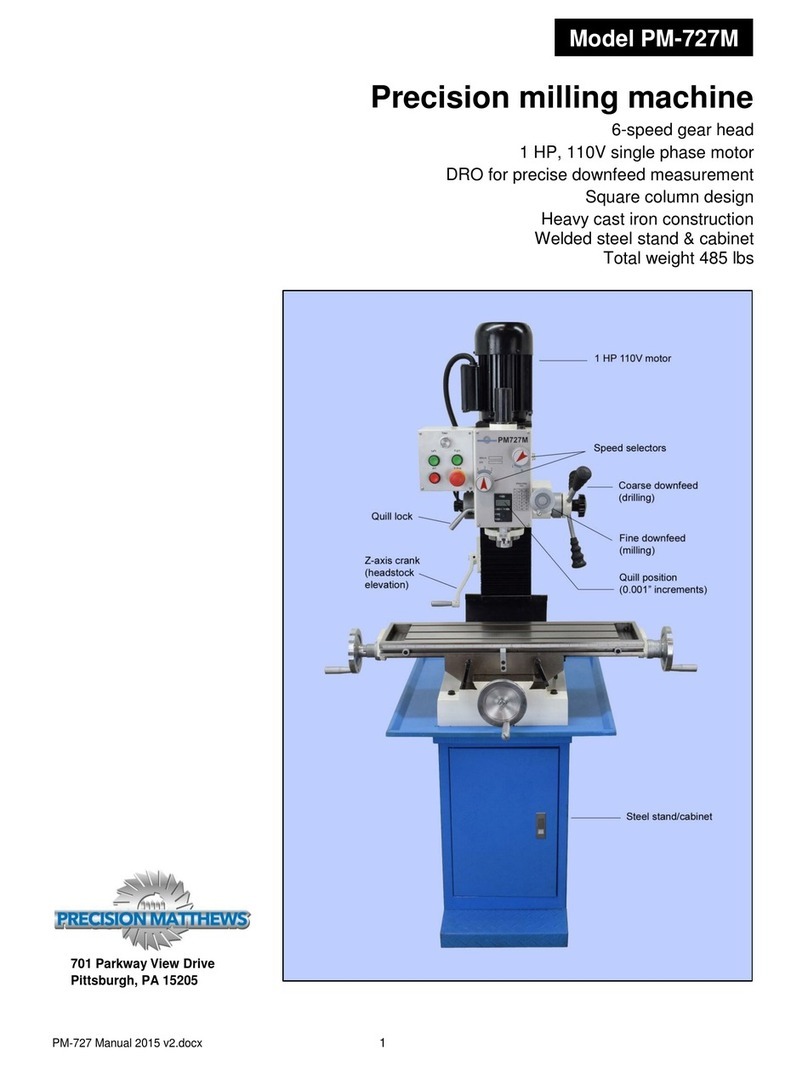
Precision matthews
Precision matthews PM-727M User manual
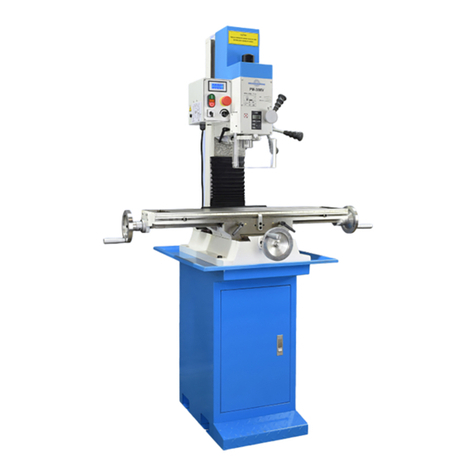
Precision matthews
Precision matthews PM-30MV User manual