Precision matthews PM-727M User manual

1PM-727MV v6 2020-10 Copyright © 2020 Quality Machine Tools, LLC
Models PM-727M & PM-727V
Precision milling machines
PM-727M 6-speed gear head (6 set speeds)
PM-727V 6-speed gear head (6 speed ranges,
innitely adjustable speed in each range)
110Vac power
Quill DRO for precise downfeed measurement
Square column design, dovetail ways
Heavy cast iron construction
Optional steel stand & cabinet
Weight including stand 575 lbs
Model PM-727M (ac induction motor)
Model PM-727V (brushless dc motor)
Tachometer Speed
control
Spindle
direction:
Forward/
Reverse
Stop
spindle
(OFF)
Power
switch

2
PM-727MV v6 2020-10 Copyright © 2020 Quality Machine Tools, LLC
FAQ
This manual contains essential safety advice on the proper setup, operation, maintenance, and service
of the PM-727M and PM-727V mills. Failure to read, understand and follow the manual may result in
property damage or serious personal injury.
There are many alternative ways to install and use a milling machine. As the owner of the machine you
are solely responsible for its proper installation and safe use. Consider the material contained in this man-
ual to be advisory only. Quality Machine Tools, LLC cannot be held liable for injury or property damage
during installation or use, or from negligence, improper training, machine modications or misuse.
This manual describes PM-727 machines as shipped from January 2015. There may be detail
dierences between your specic machine and the information given here (with little or no impact
on functionality). Please email us if you have questions about any aspect of the manual or your
machine (see our website www.precisionmatthews.com for support addresses). Your feedback is
welcomed!
The collet locating screw could
be in too far. Back it out a little.
R8 collets won’t go
into the spindle
Copyright © 2020 Quality Machine Tools, LLC
This material was originated by Precision Matthews. No portion of
the manual may be reproduced or distributed in any form without
the written approval of Quality Machine Tools, LLC.
My mill doesn’t
run at all
110 Vac power connected?
Power lamp lit? (Press the
Power push-button lens)
E-Stop button in? (pop it out
by twisting rmly to the right.)
Fuse good?
PM-727M shown above.
The PM-727V panel, left,
is labeled dierently
(727V Forward = 727M
Left, Reverse = Right).

3PM-727MV v6 2020-10 Copyright © 2020 Quality Machine Tools, LLC
New installation?
These are the points to watch out for!
But read the whole manual for specics
After uncrating the mill, please pay attention to the following:
• Handling the mill is at least a two-man job.
• Read the installation instructions, Section 2 of this manual.
• Handling the mill is at least a two-man job.
• Lower the center of gravity by cranking the headstock down
until the spindle nose is just clear of the table.
• Lifting gear – sling, hoist or forklift – must be rated for at
least 1000 lb.
Working location of the mill must allow:
1. Full left-right travel of the table.
2. Access to the back of the column for Z-axis leadscrew
maintenance (if against a wall, make sure it can be moved if
access is required).
• Power requirement is 110V, 60Hz, 1φ, 20A circuit protection .
• Extension cord not recommended; if no alternative, use 12
AWG not longer than 20 ft.
Before connecting power be sure that:
1. The machine is on a rm footing.
2. No chuck or collet is installed, and the drawbar is removed.
3. There are no clamps or locks on moving parts.
4. The gearbox contains OIL – check the sight glass at right of
the headstock.
5. The gear levers are set for the lowest speed: Hi-Lo to L, 2-3-
1 to 1.
6. The gears are fully engaged – hand-rotate (jiggle) the spin-
dle forward and back while applying light pressure on each
gear lever, listening for the click as the gears engage.

4
PM-727MV v6 2020-10 Copyright © 2020 Quality Machine Tools, LLC
Section 1 FEATURES & SPECIFICATIONS
MODEL PM-727M and PM-727V MILLING MACHINES
General information
These are robust “square column” mills designed for use in the model shop. With an all-up weight of almost 600 lbs (includ-
ing the optional stand), they can handle far more than the typical small machine. For precise control of cutter depth there is a
worm-driven quill downfeed with graduated dial and DRO, completely independent of headstock up/down position.
The main dierence between M and V models is the motor — single speed ac (induction type) for PM-727M, variable speed
(brushless dc) for the PM-727V. The V model oers a signicantly wider speed range than the M model, 40-3000 rpm vs. 115-
1700 rpm.
The reversible spindle runs in high-quality tapered-roller bearings enclosed in a 2-1/2” diameter quill with coarse and ne
downfeed options. In the PM-727M an oil-lled gearbox provides 6 spindle speeds from 115 to 1700 rpm. The same gearbox
in the PM-727V provides 6 speed ranges from 40-190 to 1800-3000 rpm. Ground dovetailed ways for table and headstock en-
sure smooth, precise motion in all three axes (X = table left/right, 15 in. Y = table front/back, 8-1/2 in. Z = headstock up/down,
16 in.). The headstock can be tilted 90 degrees clockwise and counter-clockwise from the vertical.
Working clearances – space requirements
for full motion of the table
Approximate T-slot dimensions

5PM-727MV v6 2020-10 Copyright © 2020 Quality Machine Tools, LLC
Dimensions
Weight, including optional stand 575 lb net (475 lb without stand)
Size, assembled on stand W 40 in. x D 26-1/2 in. x H 70 in.
Stand footprint W 14-1/2 in. x D 21-1/4 in.
Tray W 23-1/4 in. x D 26-1/4 in.
Electrical
Power requirement 120V, 60 Hz, 1 phase
Spindle motor PM-727M Cap-start induction, 900W (1.2 HP), 1720 rpm
Spindle motor PM-727V Brushless dc, 1125W (1.5 HP), variable speed
Headstock
Vertical travel 16 in.
Left-right tilt 90° - 0° - 90°
Spindle
PM-727M Spindle speed, rpm 115, 220, 320, 600, 1120, 1700
PM-727V Spindle speed, rpm 40-190, 180-380, 350-560, 550-1000, 980-
1860, 1800-3000
Internal taper R8
Top end 6 splines, 22 mm OD
Quill travel 3 in.
Quill diameter 2-1/2 in.
Spindle nose to table 2-1/2” to 18-1/4 in.
Spindle centerline to front face of column 7-3/4 in.
Drawbar 7/16 - 20, 16 mm wrench
Table
Size W 27-1/2 in. x D 7-1/4 in.
Surface height over oor Approx 36 in.
Maximum load, centered 200 lb
Leadscrews Acme, inch pitch, 10 tpi
Left-right travel (X-axis) 15 in.
Front-back travel (Y-axis) 8-1/2 in.
T-slots (3) 12 mm wide, 63 mm centerlines
Model PM-727M and PM-727V specications
ABOUT THIS MANUAL ...
It was written before the PM-727V became available.
Unless otherwise noted, all descriptions, suggestions
and instructions apply equally to both PM-727M and
PM-727V machines. They are identical in all respects
other than the motor, single speed for the M model,
variable for the V.

6
PM-727MV v6 2020-10 Copyright © 2020 Quality Machine Tools, LLC
Everyday precautions
• This machine is designed for milling and drilling operations by
experienced users familiar with metal-working hazards.
• Untrained or unsupervised operators risk serious injury.
• Wear ANSI-approved full-face or eye protection at all times
when using the machine (everyday eyeglasses are not reliable
protection against ying particles).
• Wear proper apparel and non-slip footwear – be sure to pre-
vent hair, clothing or jewelry from becoming entangled in mov-
ing parts. Gloves – including tight-tting disposables – can be
hazardous!
• Be sure the work area is properly lit.
• Never leave chuck keys, wrenches or other loose tools on the
machine.
• Be sure the workpiece and machine ways are secure before
commencing milling or drilling – hold-downs and/or vise fully
tightened, X-Y-Z axes locked, cutting tool secured.
• Use moderation: light cuts, low spindle speeds, slow table mo-
tion give better, safer results than “hogging”.
• Don’t try to stop a moving spindle by hand – allow it to stop on
its own.
• Disconnect 110V power from the mill before maintenance op-
erations such as oiling or adjustments.
• Maintain the machine with care – check lubrication and adjust-
ments daily before use.
• Clean the machine routinely – remove chips by brush or
vacuum, not compressed air (which can force debris into the
ways).
No list of precautions can cover ev-
erything. You cannot be too careful!

7PM-727MV v6 2020-10 Copyright © 2020 Quality Machine Tools, LLC
Section 2 INSTALLATION
SETTING UP THE MILL
The PM-727M is shipped in two packing cases, one
for the machine, one for the optional stand. The follow-
ing procedure makes use of an engine hoist, minimum
weight rating 1000 lb.
If this is a stand installation, move the stand to the mill’s
working location. Make sure the back of the column will
be accessible for lubrication (working clearances, Sec-
tion 1).
1. Un-crate the mill. Remove the drill chuck, if tted.
2. Lower the center of gravity by cranking the head-
stock down.
3. Tape cloth padding to the underside of the tilt col-
lar.
4. Run a sling under the padding.
5. Hook the sling to the hoist, but do not lift before
completing the next step.
6. Place a wood stretcher under the headstock to hold
the sling away from the capacitor housing, Figure
2-1.
7. Slowly lift the mill, controlling any tendency for it to
swing as it clears the pallet.
8. Roll the mill to its working location, then lower it into
place, Figure 2-2.
9. Secure the mill to the bench or stand. If this is a
stand installation, use the four bolts supplied. The
front two bolt locations are threaded. Use lock
washers and nuts for the back two.
10. Level the mill using the table surface for reference,
shimming as necessary.
Assembly & cleanup
Unnished metal surfaces may be protected in shipping
by thick grease and/or paper. Carefully remove these
using a plastic paint scraper, disposable rags and a
light-oil such as WD-40.
Oil the ways and leadscrews. Check the headstock sight
glass for oil level.
If necessary, install the X-axis handwheels.
Initial checks
Read Section 3 if unsure about any item
1. Connect 110 Vac power.
2. Be sure the E-Stop (Emergency) button is not
pushed in (it pops out when twisted clockwise).
3. If the power lamp is unlit, press the Power button.
Figure 2-2 Lower the mill onto stand or bench
Figure 2-1 Protect the capacitor housing
An 18 inch length of 2 x 4 will reduce pressure on the plastic
case

8
PM-727MV v6 2020-10 Copyright © 2020 Quality Machine Tools, LLC
The power lamp should light.
4. Check the emergency function by pressing the E-
Stop button. The power lamp should go out, de-en-
ergizing the contactor circuit, disabling all electrics.
5. Restore power by twisting the E-Stop button rmly
clockwise.
Test run procedure
DO NOT LEAVE THE MACHINE UNATTENDED DUR-
ING THIS PROCEDURE
1. Gear levers set to L and 1 (115 rpm)? Gears fully
engaged? Speed control fully counter clockwise,
PM-727V only.
2. Test the spindle motor by pressing the Left and Right
motor switches in turn.
3. Run the spindle at 115 rpm for a few minutes, then
stop.
4. Select each of the available speeds in turn (L-2, L-3,
H-1, etc.). Check gear engagement each time, then
run for a few minutes.
The machine should now be ready for normal opera-
tions.
Optional
After a few hours of run time you may wish to drain the
gearbox to ush out any residue from the manufacturing
process. Rell the gearbox with the oil recommended in
Section 4.
Allow the spindle to stop com-
pletely before shifting gears
If this doesn’t happen, the E-stop func-
tion is defective, and needs attention
SPEED RANGES (rpm)
L1 40-190
L2 180-380
L3 350-560
H1 550-1000
H2 980-1860
H3 1800-3000
PM-727V USERS PLEASE NOTE ...
Not shown in Section 5:
• Spindle speed is transmitted to the tachom-
eter on the control panel by a sensor locat-
ed adjacent to spindle.
• The electrical schematic does not show the
PM-727V variable speed drive. This replac-
es entirely the motor and motor witching
circuit shown in the schematic.

9PM-727MV v6 2020-10 Copyright © 2020 Quality Machine Tools, LLC
Section 3 USING THE MILL
Allow the spindle to stop com-
pletely before shifting gears
L-1 115
L-2 220
L-3 320
H-1 600
H-2 1120
H-3 1700
FRONT PANEL CONTROLS
Connect the mill to a 110Vac outlet. Press the Power
lamp switch, top center Figure 3-1, to energize the
control circuit (the lamp should light). This is a latching
switch – press once to energize, press again to de-en-
ergize.
The E-stop button, bottom right, is in series with the
Power switch. Like the Power switch, it de-energizes
the control circuit completely, but it should be used only
for its intended purpose – emergency disconnect. Once
the E-stop button is pushed in, it stays in until twisted
clockwise to release.
The spindle drive motor is controlled by the three push
buttons:
Left = Forward (cw, looking down, used for
most milling/drilling operations)
Right = Reverse (ccw, looking down)
O = Stop
SPINDLE SPEEDS
This is a gear-head machine with a constant speed mo-
tor and a two-stage gearbox providing a choice of six
spindle speeds. The rst stage (L-H) selects the speed
range, high or low; the second stage (1-3-2) selects a
specic speed within that range.
Before switching on the spindle motor be sure that
Excessive cutter noise, chatter, poor
nish and tool wear are often the result
of too high a feed rate, and/or too high a
spindle speed. If unsure, go slow!
Spindle speeds (rpm)
INSTALLING & REMOVING TOOLING
The spindle and drawbar are designed for R-8 taper
collets, drill chucks and other arbors with the standard
7/16”-20 internal thread.
When installing or removing R8 tooling, set the spindle
speed to L1 for the best braking action. Alternatively, an
adjustable wrench can be used to grip the ats on the
bottom end of the spindle.
To install: Hand-thread the drawbar into the R-8 device
until the washer, arrowed in Figure 3-2, is seated on the
Figure 3-1 Motor controls, gear shifters & DRO
both stages are properly engaged. Hand-rotate (jiggle)
the spindle forward and back while applying light pres-
sure on each gear-shift knob, listening for the click as
the gears engage.
Figure 3-2 Spindle & drawbar (arrowed)

10
PM-727MV v6 2020-10 Copyright © 2020 Quality Machine Tools, LLC
MOVING THE TABLE
Left-right movement of the table is usually said to be
on the X-axis (a.k.a. “longitudinal travel” or “traversing”).
Front-back movement is on the Y-axis, sometimes called
“cross travel”.
Each axis has a leadscrew with handwheel and gradu-
ated dial with 0.001” divisions, 0.1” per revolution, Fig-
ure 3-3. If the mill is not equipped with digital readouts
(DROs), the table can be accurately positioned by count-
ing whole turns and divisions, keeping leadscrew back-
lash in mind. This means that table motion must always
be in the same direction up to the point of reference,
then on to the desired location, see “Spindle Positioning
by Counting Divisions” later in this section.
Replace the drawbar cap to
protect bearings and spline
Figure 3-3 Y-axis handwheel, X-axis clamp levers
Figure 3-4 Y-axis clamp levers
QUILL DOWNFEED
The quill is controlled in two dierent ways, coarse and
ne.
In the drilling mode, coarse feed, the mill functions like a
standard drill press – pull the upper lever toward you to
lower the quill. For milling operations the 3-lever hub is
disengaged, and the quill is controlled by the ne down-
feed handwheel. The quill is locked by a lever on the left
of the headstock, Figure 3-1.
Figure 3-5 Quill downfeed controls
The quill pinion is driven by the lever hub (1). The ne con-
trol handwheel (2) is connected by a worm gear to sleeve (3),
which is free to rotate — doing nothing to the quill — if it is not
meshed with the lever hub. Do this by tightening knob (4).
Always lock the quill when milling
splined spindle. Fully tighten the drawbar.
To remove: Protect the table under the spindle with
rags or scrap wood. Loosen the drawbar one half turn
or less — holding the spindle with a wrench if necessary
— then tap the top of the drawbar with a brass or dead-
blow hammer to unseat the taper. Unscrew the drawbar
with one hand while supporting the R-8 device with the
other hand.
Why support the R-8 item? Because the table, vises
and workpiece can be damaged by falling tools and drill
chucks. The cutting tool itself can also be damaged in
the same way.

11PM-727MV v6 2020-10 Copyright © 2020 Quality Machine Tools, LLC
including the heavier knee mills, locking the quill may
oset the spindle by a few thousandths of an inch. If
the edge of the workpiece has been “found” in the quill-
locked condition, this will aect placement of holes
drilled thereafter. Instead, lower the quill with the ne
downfeed control. This is worm driven, so it stays where
it’s put without locking.
NOTE: This does not apply to operations calling for pre-
cise depth control, such as milling. For such operations
the quill is locked to maintain a given depth of cut.
In Figure 3-6 a hole is to be drilled 0.25” on the Y-axis
relative to the front edge of a workpiece in a vise, or
otherwise clamped to the table.
1. Install an edge-nder in collet or chuck (a tip diam-
eter of 0.2” is assumed).
2. Clamp the X-axis by tightening both levers, Figure
3-3.
3. If the reference edge is already to the back the spin-
dle centerline, do nothing; if not, rotate the Y-axis
handwheel clockwise to send the workpiece back-
wards (toward the column).
4. Engage the ne downfeed, Figure 3-5.
5. With the spindle running, lower the quill as neces-
sary using the ne downfeed handwheel; bring the
table forward (counter-clockwise), stopping at the
point where the edge-nder just makes contact (the
tip jumps out of line). Stop the spindle.
6. While holding the Y-axis handwheel to prevent move-
ment, zero the dial.
7. Raise the quill, then rotate the handwheel one exact
full turn counter-clockwise (0.1”) to bring the refer-
ence edge to the spindle centerline.
8. Rotate the handwheel 2-1/2 turns counter-clockwise
to bring 50 on the dial opposite the datum; the spin-
dle is now exactly 0.25” behind the reference edge.
QUILL DOWNFEED
The quill is controlled in two dierent ways, coarse and
ne.
In the drilling mode, coarse feed, the mill functions like a
standard drill press – pull the upper lever toward you to
lower the quill. For milling operations the 3-lever hub is
disengaged, and the quill is controlled by the ne down-
feed handwheel. The quill is locked by a lever on the left
of the headstock, Figure 3-1.
Coarse feed (Figure 3-5)
For drilling operations, loosen knob (4), allowing the le-
ver hub to rotate independently of sleeve (3).
Fine feed (Figure 3-5)
For milling operations calling for precise, repeatable
control of tool depth, tighten knob (4) to engage hub (1)
with the internal taper on sleeve (3). Tighten the Z-axis
clamps, Figure 3-7.
Rotate the ne control knob (2) to raise or lower the quill.
Lower the quill by rotating the ne control knob clock-
wise, positioning it precisely either by counting divisions
on the graduated dial, or by reference to the digital read-
out (DRO), Figure 3-1. Use the locking lever left of the
headstock to hold the quill rmly in position.
If you are counting downfeed divisions be aware of
backlash in the worm drive.
This means that the handwheel must always be turning
in the same direction throughout the entire process,
from setting a reference level to subsequent cutting
passes at specic depths – see the backlash discussion
in “Moving the Table”, above.
Using the DRO – which has no backlash issues – is less
laborious, but remember that the quill is spring-loaded.
This calls for care when releasing the quill locking le-
ver prior to repositioning the quill downward. If the ne
control knob has been allowed to disengage (backed
o counter clockwise), the quill will jump up by 0.01” or
more. To avoid this, make sure the ne control is rmly
clockwise, lightly loading the quill rack, before releasing
the locking lever.
For all spindle positioning op-
erations, with or without DROs,
avoid using the quill lock.
Figure 3-6 Spindle positioning example
Why not use the lock? On vertical mills of this type,
X & Y-AXIS POSITIONING BY COUNTING
DIVISIONS

12
PM-727MV v6 2020-10 Copyright © 2020 Quality Machine Tools, LLC
Figure 3-7 Headstock clamp levers
HEADSTOCK ELEVATION (Z-AXIS)
The headstock is elevated by a hand crank on the left
side of the column, Figure 3-1. For milling operations the
headstock is usually locked in position by tightening the
clamp levers, Figure 3-7.
The spindle must come to a
stop before reversing
Figure 3-8 Headstock nuts (2 of 3)
TAPPING OPERATIONS
When threading a drilled hole it is essential to align the
threading tap properly in the bore. The mill is often used
for this purpose, ideally with a dedicated (non-slip) tap
holder or, for production work, an auto-reverse tapping
TILTING THE HEADSTOCK
In routine operations the user relies on squareness of
the spindle relative to both axes of the table. Front-to-
back squareness set at the factory, and is not adjust-
able (by everyday methods), but in the other plane the
headstock can be set to any angle up to 90 degrees
either side of the normal vertical position. Because re-
establishing true vertical (tramming) on any mill is a time
consuming process, most machinists look rst for other
ways of handling a project instead of tilting the head.
The headstock is secured by three nuts spaced 120 de-
grees apart, one underneath and one either side, Figure
3-8. The headstock is top-heavy, and may swing sud-
denly to either side unless a helper is on hand to restrain
it. Using an 18 mm wrench, testing for moveability as
you go, carefully loosen the nuts by degrees. Be es-
pecially careful if the head has not been moved before
QUILL DRO
The quill DRO is in metric mode when switched on.
Press the mm/in button to display inches. By pressing
and holding the Up arrow (incrementing) or Down ar-
row (decrementing) the display can be set to a chosen
value. To activate the Up/Down function press and hold
the ZERO button until the letter ‘S’ is displayed at right
(about 3 seconds). The longer the Up or Down buttons
are held down, the faster the change in displayed val-
ue. Press the ZERO button briey to exit the Up/Down
mode.
Switch o the DRO when not in use!
Replace the battery by removing the small molded cover
on the face of the DRO unit. Check the type number and
voltage of the installed battery. Replace with an equiva-
lent silver oxide cell available from local retailers.
attachment. The drill chuck can be used instead for siz-
es up to (say) M6 or 1/4”, beyond which the chuck may
not grip tightly enough to avoid slippage. Tapping can
be done under power, or by hand turning the chuck (see
below). For either method, it is essential to use a tapping
uid. Any cutting oil is better than none, but most users
nd Castrol’s Moly Dee the most reliable for threading
in steel. If power tapping bear in mind that reversing is
not instantaneous, so be careful tapping blind holes. Be
sure the quill locking lever is free, and start trial work
with the lowest spindle speed, L-1.

13PM-727MV v6 2020-10 Copyright © 2020 Quality Machine Tools, LLC
Figure 3-9 Headstock tilted 45ocounter clockwise
TRAMMING THE HEADSTOCK
As shipped, the mill is set to zero tilt, squared accurately
enough for initial “out of the box” test drillings, etc. For
more demanding project work thereafter, the spindle
needs to be set at precisely 90 degrees relative to the
table, in other words trammed. “Out of tram” may show
up as an oset of a few thousandths between entry and
exit of a deep hole, or as a scalloped eect when surfac-
ing a workpiece with a large-radius y cutter, exagger-
ated in Figure 3-10.
Figure 3-11 Sweep holder for dial indicator
The holder is a rectangular section aluminum bar with thread-
ed holes allowing the choice of two sweep diameters, 6” and
10”, measured from spindle centerline to indicator tip. The
smaller sweep can be used for front-to-back tramming, also
left-to-right as here. For more sensitive left-to-right tramming,
use the larger sweep.
Figure 3-10 Head tilt can aect surface atness
Tramming is the process of ne-tuning the headstock tilt
angle. Start by attaching a dial indicator to some form
of “sweepable” holder installed in the spindle, the aim
being to adjust tilt for the same reading on either side
of the X axis. The longer the radius arm, the greater the
sensitivity.
Figure 3-11 shows a typical shop-made holder; it has a
threaded arbor allowing the choice of two radius arms,
6 and 10 inches measured from spindle centerline to
indicator tip. A collet is used to hold the arbor, in this
example 5/8” diameter. The dimensions are arbitrary,
but note that the indicator must be rmly attached, and
the arm rock-solid relative to the indicator spring force
(which can be considerable on plunger-type indicators).
A suggested procedure for establishing tram:
1. Disconnect power.
2. Install the dial indicator.
3. Set the spindle drive to H-3 (this will allow the indi-
cator holder to sweep easily from side to side).
4. If the headstock has been tilted, reset it to the ap-
proximate zero degree position on the tilt scale, then
tighten the three nuts enough to avoid unexpected
headstock movement.
Tramming is done by ne-tuning the headstock tilt an-
gle. Tram is typically checked by attaching a dial indica-
tor to some form of “sweepable” holder installed in the
spindle, the aim being to adjust tilt for the same reading
on either side of the X axis. The longer the radius arm,
the greater the sensitivity.
– the paint seal may let go without warning. (First-time
tilting may also call for unusual eort on the wrench.)
Set the headstock to the desired angle by reference to
the tilt scale on the headstock base casting, then re-
tighten the nuts. The tilt scale was carefully installed in
manufacture, and is good to within ± 1 degree. A more
accurate means of angle measurement will be needed if
the project calls for greater precision.

14
PM-727MV v6 2020-10 Copyright © 2020 Quality Machine Tools, LLC
Tramming calls for patience! Expect to tighten
and re-check at least three times (simply tight-
ening the bolts can itself aect the tram).
Figure 3-14 Indicating the vise
The tip of a standard dial indicator, arrowed, rides along the
face of a ground reference bar
5. Remove the vise, if installed, and clean the table
surface. If there are noticeable grooves or dings,
atten the surface with a diamond lap or ne-grit
stone.
6. Set a 1-2-3 block (or other precision-ground block)
on the table under the indicator probe.
7. Switch on the DRO.
8. Using the ne downfeed lower the spindle to give an
indicator reading of about half-scale.
9. Note both the dial indicator and DRO readings, then
back o the ne downfeed at least a couple of turns
to avoid collision when sweeping.
10. Reposition the 1-2-3 block to the opposite location
on the table.
11. Swing the indicator holder to the new location, then
lower the spindle – ne downfeed again – to give
the same dial indicator reading as in step (7).
If the headstock is perfectly trammed – highly unlikely
at the rst shot – the DRO reading should be as in step
(9). If not, loosen the nuts just enough to allow the head-
stock to be tapped a fraction of a degree in the direc-
tion called for, then re-tighten the nuts. The “tap” can be
anything from a gentle slap of the hand to a rap with a
dead-blow mallet.
Repeat steps (8) through (11) until satised with the
tram, tightening the nuts as you go. This will likely call
for several iterations. There is no “right” tram; the ac-
ceptable dierence in side-to-side readings depends on
project specs. As a starting point, aim for ± 0.001” on a
sweep radius of 5 or 6 inches.
A similar procedure may be used to check tram in the
Y-axis, front to back. The dierence here is that there is
that Y-axis tram is established in manufacture, and can
be adjusted by one of two methods:
1. Shimming between the dovetailed base casting and
the headstock itself. It is more likely that the head-
stock is nodding forward rather than leaning back-
ward, so start with (say) a 2 mil shim in line with the
underside (central) headstock nut. This is a tempo-
rary x that will need to be checked if the headstock
is tilted again.
2. Shimming between the underside of the column and
the main base casting. This is a long-term x. It is a
two-person procedure, requiring an engine hoist or
some other means of un-weighting the headstock
(see Section 2, Installation).
INSTALLING & INDICATING A VISE
For routine milling operations the workpiece is held in a
precision vise. For the PM 727M a 4” vise is most suit-
able. “Indicating” means checking the alignment of the
xed (back) vise jaw relative to the axis of table motion.
Install the T-bolts and align the vise by eye. With one of
the clamp nuts snug, but not tight, tighten the other one
just short of fully-tight (but tight enough so the vise won’t
budge without a denite tap from a dead-blow mallet).
A typical setup for indicating is shown in Figure 3-14.
There is no spindle lock, but you need to make sure
that the spindle does not rotate throughout the pro-
cedure. It helps to set the gears for the lowest spindle
speed (L-1). Take up any backlash by pushing against
the indicator holder. Set the indicator tip against the up-
per edge of a precision reference bar or, if not available,
use the front face of the xed jaw of the vise instead
(check for dings, hone if necessary). Adjust the Y-axis to
pre-load the indicator to mid range at the tightly-clamped
side of the vise, then lock the Y-axis.
Note the indicator reading, then watch the indicator as
you traverse the table slowly toward the loosely clamped
side. Ideally, there should be no discrepancy between
the indicator readings at the two ends — unlikely at the
rst attempt. Return the table to the starting point, then
repeat the process, tapping the vise in as you go. Re-
peat the process as often as necessary for the desired
accuracy, progressively tightening the “looser” nut. Now
fully tighten both nuts, and re-check again (tightening a
nut can itself introduce signicant error). An established
routine like this – tight to loose – can save a lot of time.

15PM-727MV v6 2020-10 Copyright © 2020 Quality Machine Tools, LLC
Figure 3-16 Shop-made vise key
Dimensions in millimeters
Figure 3-15 Keys installed on X-axis of vise
On most vises the keys can also be installed on the long axis
VISE KEYS
Most precision vises come with key slots on the un-
derside machined exactly parallel to the xed jaw. Key
slots, Figure 3-15, can be a great time saver. Properly
installed they allow the vise to be removed and replaced
routinely, accurately enough for general machining with-
out the need for indicating every time.
Most 4” vises have either 14 mm or 16 mm slots, calling
for shop-made T-shape adapter keys as Figure 3-16. It
is well worth the eort to make these precisely.
Aim for a snug t in both vise and table, but not so tight
that it takes more than reasonable eort to lift the vise
clear. The objective is allow the vise to be removed and
replaced routinely, accurately enough for general ma-
chining without the need for indicating every time.
Case hardening of the keys is recommended, with nal
tting using a ne stone or diamond stone.
There is no “right” setup for a vise, but as a starting point
aim for an indicator dierence of no more than ± 0.001”
over the width of the jaw.

16
PM-727MV v6 2020-10 Copyright © 2020 Quality Machine Tools, LLC
Section 4 MAINTENANCE
Unplug the 110V power cord before any
maintenance operation!
LUBRICATION
ISO and SAE are the main indexes of viscosity. ISO has
a “one number” scale, but SAE uses dierent indexes for
engine and gear oils (there is also the sux W, mean-
ing multigrade). SAE 20 engine oil has about the same
viscosity as SAE 80 gear oil, both roughly equivalent to
ISO 68.
Recommended lubricants
Gearbox: ISO 68, such as SAE 80W90 auto gear oil, or
Mobil DTE Heavy/Medium circulating oil (about 2 qts.)
Ball oilers: ISO 68 oil, such as Mobil Vactra No. 2, or
equivalent
X, Y and Z axis ways (dovetails): ISO 68 oil, such as
Mobil Vactra No. 2
Quill rack and pinion, Z-axis gears: light general pur-
pose grease, NLGI No. 2, or equivalent
X and Y leadscrews: ISO 68 oil, such as Mobil Vactra
No. 2, or equivalent
Z leadscrew: ISO 68 oil or NLGI No. 2 grease
GENERAL OILING
Assuming a clean environment – free from abrasive par-
ticles and machining debris – lack of proper lubrication
is the main cause of premature wear. Rotating parts are
easy to lubricate, sliding parts are not. Gibs are tight-
ened for the best compromise between rigidity and slid-
eability, which means practically zero gap between the
ways. Take time to understand exactly which are the
bearing surfaces on the various dovetail surfaces; this
is not obvious – some of the interfaces look like bearing
surfaces, but are simply narrow gaps.
Every few hours of operation:
1. Apply the recommended way-oil with a dedicated
short-bristle brush such as the type used for apply-
ing ux.
2. Use a similar brush to apply oil or grease to the
leadscrews
3. Apply oil to the ball oilers, see below.
BALL OILERS
Use a pump-type oil can with tip large enough to more
than span the oiler’s spring-loaded steel ball. Oil pres-
sure will displace the ball, allowing oil to ow, provided
the oil can tip is rmly pressed onto the brass seating.
Before oiling check that the ball is not stuck – press it
lightly with a probe.
GEARBOX DRAIN & REFILL
1. Run the mill a few minutes to warm the oil if neces-
sary.
2. Remove the ll plug on the top surface of he head-
stock.
3. Place a 1-gallon or larger drain pan under the head-
stock.
4. Using a 6 mm hex wrench remove the drain plug,
Figure 4-1.
5. Allow the oil to drain completely, then replace the
drain plug.
6. Remove the ll plug, then add just a few ounces of
oil.
7. When satised that the headstock is oil-tight, add
oil to the halfway mark on the sight glass (about 2
qts total).
8. Replace the ll plug.
Figure 4-1 Gearbox oiling
Drain plug (1), sight glass (2)
QUILL RACK & PINION
Lower and lock the quill, Figure 4-2. Using a sti ux
brush, clean the visible portions of the rack and pinion.
Remove all machining debris and foreign ob-
jects before lubricating ANYTHING! If need be,
any oil is better than no oil – but use the recom-
mended lubricants when you can.

17PM-727MV v6 2020-10 Copyright © 2020 Quality Machine Tools, LLC
Figure 4-2 Quill rack
QUILL RACK & PINION
Lower and lock the quill, Figure 4-2. Using a sti ux
brush, clean the visible portions of the rack and pinion.
Raise and lower the quill to expose the remainder of the
working surfaces, locking and cleaning at each setting.
SPINDLE BEARINGS
The spindle runs on grease-lubricated tapered roller
bearings. These should be serviced every 500 hours
of running time. Thoroughly clean each bearing assem-
bly then repack with a grease such as Kluber Isoex
(auto shop wheel bearing grease can be substituted in
low-load, low rpm operations). Do not over-pack the
bearings! Bearing manufacturers recommend that the
free volume between inner and outer should be no more
than 30% lled with grease. (If smothered with grease,
bearings are subject to overheating.)
BOTH screw heads must be tight against the
gib ends. If you loosen one, tighten the other.
Remove the way covers for access to the back
of the Y gib and bottom of the Z gib.
GIB ADJUSTMENT
Gibs on the X, Y and Z axes control the t of the mating
dovetailed surfaces. They are gently-tapered lengths of
Figure 4-3 X and Y-axis gib adjustment
The back adjustment screw for the Y axis gib
is under the solid way cover
Figure 4-4 Z-axis gib adjustment (top)
The lower adjustment screw is under the
pleated way cover
LEADSCREW BACKLASH CORRECTION
When alternating between clockwise and counter clock-
wise rotation of the X or Y leadscrews, the handwheel
moves freely a few degrees but the table stays put. This
is backlash, a feature of all leadscrews other than the
precision variety found on CNC machines. The accept-
able amount of lost motion depends on the user, but
0.005” is generally a good compromise. Smaller num-
bers are possible, but overdoing it can lead to premature
wear of leadscrew and nut.
Excessive backlash can be corrected by compressing
the leadscrew nut. For the X-axis this is done by tighten-
ing the socket head screw in Figure 4-5. A long-handled
4 mm hex wrench is required, ideally one with an ex-
tra-thick shank to minimize exing. The corresponding
adjustment for the Y-axis, Figure 4-6, is concealed by
the solid way cover. It is more dicult to get to because
access to the screw is partly blocked by the leadscrew
itself.
ground cast iron located by opposing screws at each
end. Adjusting them is a trial and error process that
takes time and patience. Aim for the best compromise
of rigidity and reasonably free table movement. Too tight
means accelerated wear on the ways and leadscrews.
Too free means workpiece instability, inaccuracies and
chatter.
Especially during the rst 10 hours of running time
check that the spindle runs smoothly, without ex-
cessive heat build up (the spindle will run warm
when used at high speeds over long periods, but
should not be uncomfortably hot). Overheating can
be due to excessive grease, see above, or an over-
tight spanner nut at the upper end of the spindle.
Call Precision Matthews for guidance.

18
PM-727MV v6 2020-10 Copyright © 2020 Quality Machine Tools, LLC
Figure 4-5 X-axis backlash adjustment
Figure 4-6 Y-axis backlash adjustment
DOWNFEED RETURN SPRING TENSION
The quill should automatically retract when the coarse
downfeed levers are released following a drilling opera-
tion. If not, the return spring may need to be re-tensioned
– but rst check for other issues such as obstructions or
lack of lubrication.
A pin in the headstock casting engages in one of 6
notches on the rim of the cup-shaped spring housing.
Spring tension is adjusted by disengaging the housing,
see below, then rotating and re-engaging it at the de-
sired tension – clockwise to reduce, counter-clockwise
to increase.
To adjust the tension:
1. Wear heavy-duty leather gloves for hand protection
2. Loosen one half turn, but do not remove, the knob
holding the spring housing in place.
3. While holding the housing rmly to stop rotation,
continue to loosen the knob to the point where the
housing can just be disengaged from the pin.
4. Step the housing round to the next notch, then tight-
en the knob to secure the housing. Test for tension.
5. Repeat as necessary, then fully tighten the knob.
Take extra care when working on the spring — it
can unwind violently if not controlled
Figure 4-7 Return spring housing
Notches in the rim, arrowed, allow 6 radial settings

19PM-727MV v6 2020-10 Copyright © 2020 Quality Machine Tools, LLC
Section 5 PARTS
MOTOR CONTROLS
Power Press once to energize, press
again to de-energize.
Left = Spindle Forward = clockwise
looking down on mill table
Right = Spindle Reverse = counter-
clockwise
O = Stop motor
E-Stop Emergency disconnect (stays
in until turned counter-clockwise to
release)

20
PM-727MV v6 2020-10 Copyright © 2020 Quality Machine Tools, LLC
PM-727M ELECTRICAL SCHEMATIC Fig 1
This schematic is representational.
Point-to-point wiring may dier.
Other manuals for PM-727M
1
This manual suits for next models
1
Table of contents
Other Precision matthews Power Tools manuals
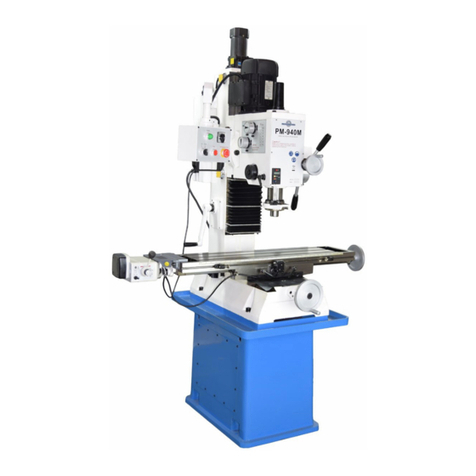
Precision matthews
Precision matthews PM-940M User manual
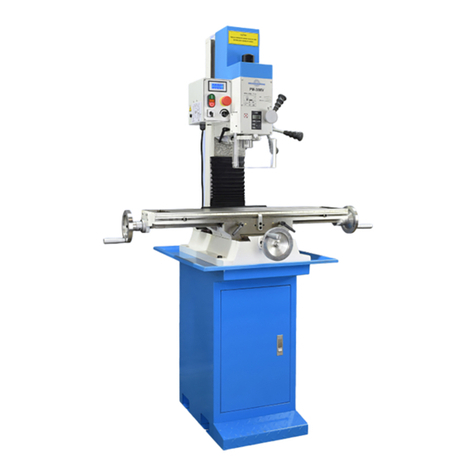
Precision matthews
Precision matthews PM-30MV User manual
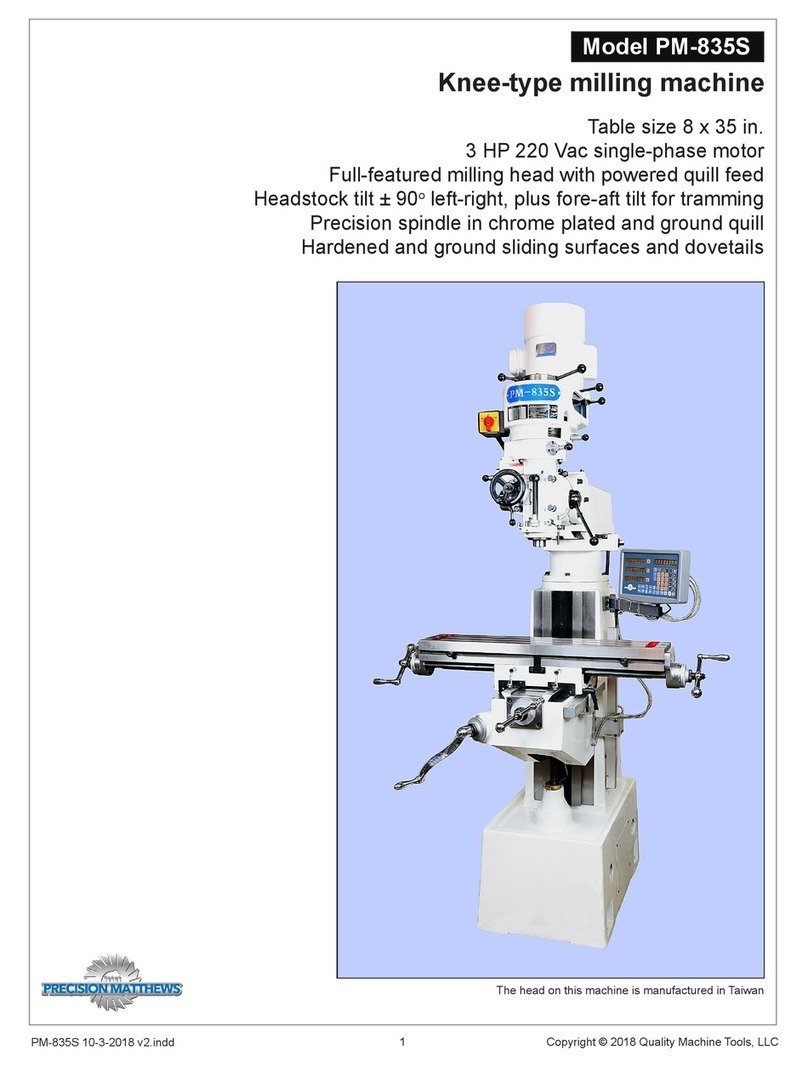
Precision matthews
Precision matthews PM-835S User manual
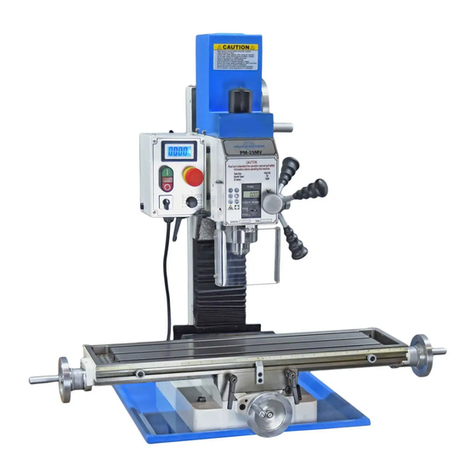
Precision matthews
Precision matthews PM-25MV User manual
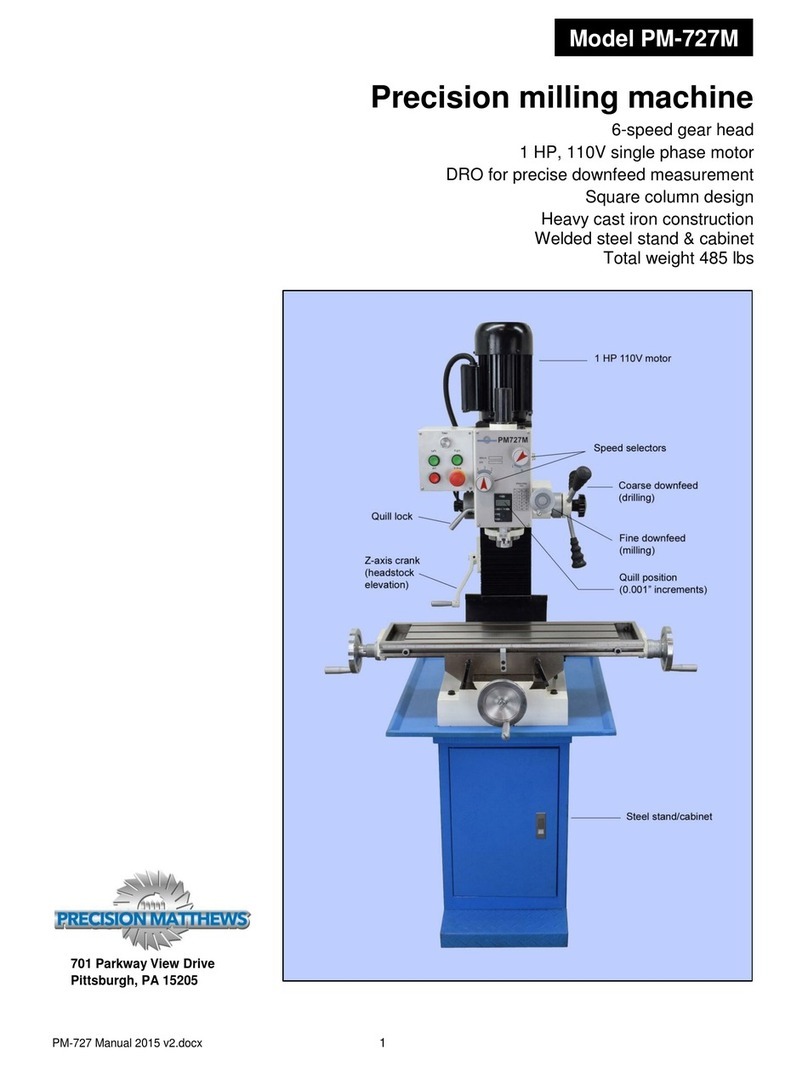
Precision matthews
Precision matthews PM-727M User manual
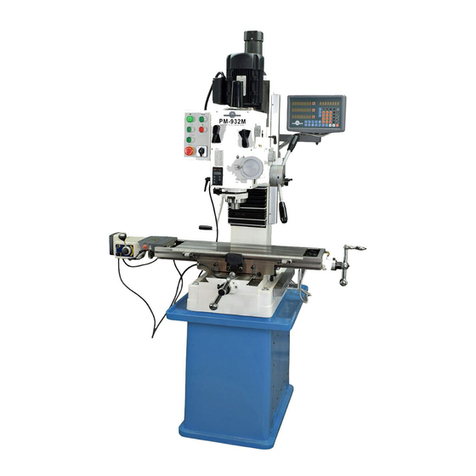
Precision matthews
Precision matthews PM-932M User manual
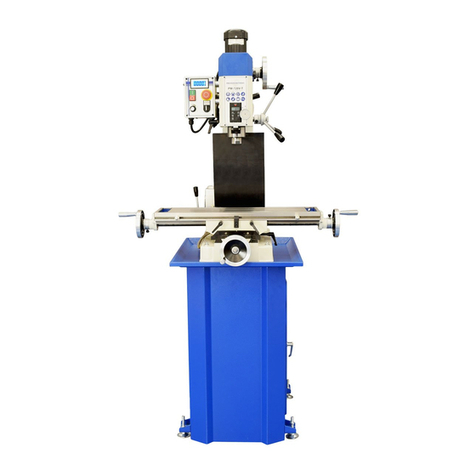
Precision matthews
Precision matthews PM 728V-T User manual
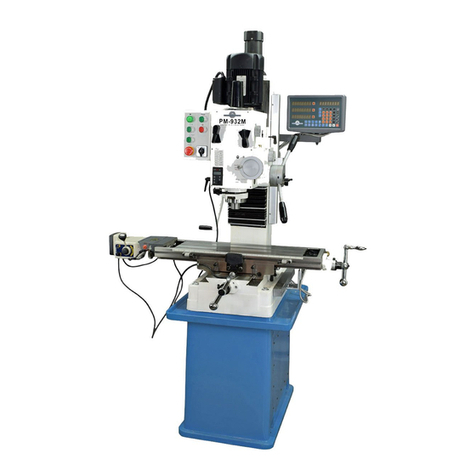
Precision matthews
Precision matthews PM-932M User manual
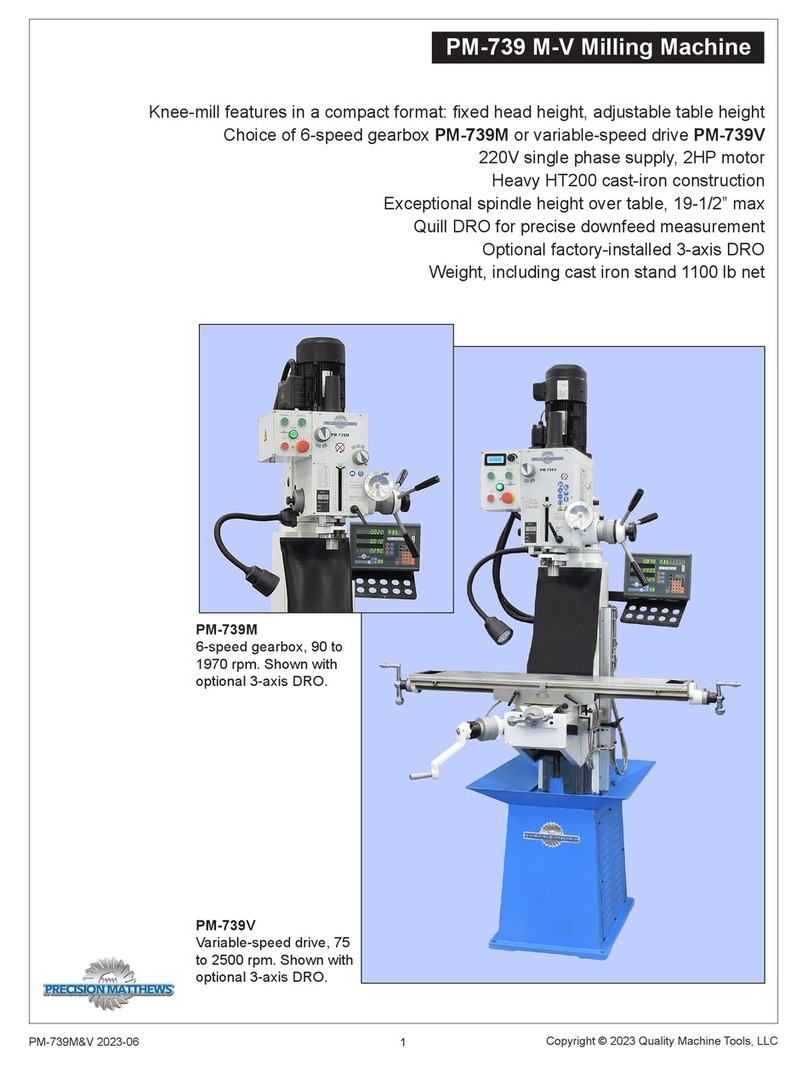
Precision matthews
Precision matthews PM-739M User manual

Precision matthews
Precision matthews PM-833TV User manual