REXROTH UPE 2 User manual

1/10
Information on available spare parts:
www.boschrexroth.com/spc
Clamping and drive module
Type UPE 2
Drive power 1.1 kW / 2.2 kW
Component series 1X
Maximum operating pressure 700 bar
RE 51142/05.13
Replaces: 02.11
Table of contents
Contents Page
Features 1
Applications 1
Description 2
Symbol 2
Ordering code 2
Overview of the attachment modules 3
Technical data 4
Performance diagram 4
Electric motor
• Technical data 5
• Electromagnetic compatibility of devices (EMVG) 5
• Terminal assignment 5
Dimensions 6
Filling and removal quantity 6
Sound pressure level 7
Options
• Level switch, electrical function 7
• Temperature switch, electrical function 8
• Ventilation filter 8
• Oil tray 8
Commissioning notes 9
Features
–
Duty cycle, short-time operation S2 and intermittent operation S3
– Compact design
– Low-noise
– Broad field of application
– Large number of variants
– Complete hydraulic control possible
(in this connection see data sheet 51144)
– Ready for connection
UPE2_1X••
Applications
– Clamping, locking, releasing and indexing at machines
– Drive for hydraulic tools
– Drive for lifting and swiveling units
– Use in the general mechanical engineering sector
– Test machines and test stands

P
T
M
2/10 Bosch Rexroth AG Hydraulics UPE 2 RE 51142/05.13
Ordering code
Further details in the plain text
Seal
V = FKM seals
Mounting hydraulic control
(in this connection see data sheet 51144)
0 = without mounting
1 = with mounting
Carrying handle
no code = without carrying handle
T = with carrying handle
Filling plug
no code = Filler neck with dipstick
B = Ventilation filter
Oil monitoring
A = Oil level display
AN = Oil level display with level switch
AT = Oil level display and temperature switch
ANT = Oil level display with level and temperature switch
Nominal tank size
1.1 kW drive power
3 = 1) Filling quantity 2.4 liters
4 = Filling quantity 4.5 liters
2.2 kW drive power
5 = 1) Filling quantity 4.3 liters
7 = Filling quantity 7.2 liters
Description, symbol
The UPE 2 clamping and drive module constitutes a complete
drive system that is delivered ready for connection. It is used
for supplying hydraulic circuits with hydraulic fluid.
For reasons in connection with the thermal load, the clamp-
ing and drive module is to be operated in short-time operation
and intermittent operation. The duty cycle is to be selected
depending on the power output and the environmental condi-
tions so that the maximum admissible operating temperature
of 80 °C is not exceeded.
The clamping and drive module basically consists of the alu-
minum housing, the pump (radial piston pump or external
gear pump) and the oil-immersed motor. The stator of the
oil-immersed motor is pressed into the aluminum housing. It
transfers the heat of the winding directly to the exterior alumi-
num housing wall.
• For the installation, four through holes have been provided
in the tank bottom for the mounting screws. The clamping
and drive module is to be operated in vertical installa-
tion position.
Optionally, the UPE 2 clamping and drive module can be
equipped with an electric monitor for the oil level as well as
the oil temperature, a ventilation filter and a complete hydrau-
lic control (see 51144).
Attention!
The clamping and drive module may heat up during
operation => risk of injury!
Symbol
UPE 2 1X V *
G 3/8
Oil drain screw
1) Version with external gear pump not possible!
Component series 10 to 19 = 1X
(10 to 19: unchanged installation and
connection dimensions)
Drive power
1.1 kW = 1.1
2.2 kW = 2.2
Radial piston pump
Flow
0.49 liters/min = R0.49
0.82 liters/min = R0.82
1.00 liter/min = R1.00
1.25 liters/min = R1.25
1.70 liters/min = R1.70
1.95 liters/min = R1.95
2.55 liters/min = R2.55
2.60 liters/min = R2.60
4.00 liters/min
= R4.00
External gear pump
Flow
1.4 liters/min = G1.40
2.8 liters/min = G2.80
4.4 liters/min = G4.40
5.6 liters/min = G5.60
7.0 liters/min = G7.00
8.8 liters/min = G8.80
11.2 liters/min = G11.2
14.0 liters/min = G14.0

Hydraulics Bosch Rexroth AGRE 51142/05.13 UPE 2 3/10
Basic module "G"
– Basic module with integrated pressure relief valve for simple stroke lowering or
pressure holding functions
– If the "G" basic modules are used, no further stacking is possible.
– For further details see data sheet 51144
"Control block for clamping and drive modules type IH15A"
Basic module "G"
Directional valve module "W" 1)
– Allows the design of controls using valves with porting pattern according to
DIN 24340 form A
– The number of directional valve modules depends on the draw-off volume and
the displacement of the pump
– For further details see data sheet 51144
"Control block for clamping and drive modules type IH15A"
Directional valve module "W"
Seat valve module "S" 1)
– Seat valves basically consist of:
• a pressure relief block
• one or several control blocks
• one end block
– The control is designed depending on the relevant application
– The number of seat valve modules depends on the draw-off volume and the
displacement of the pump
– For further details see data sheet 51144
"Control block for clamping and drive modules type IH15A"
1) The directional valve modules and the seat valve modules can be combined!
Seat valve module "S"
Overview of the attachment modules
UPE2_G•
UPE2_W•
UPE2_S•

4
3,5
3
2,5
2
1,5
1
0,5
100 200 300 400 500 600 7000
1,1 kW
2,2 kW
7,5
10
5
15
12,5
2,5
50 100 150 200 250
0
1,1 kW
2,2 kW
4/10 Bosch Rexroth AG Hydraulics UPE 2 RE 51142/05.13
Technical Data (For applications outside these parameters, please consult us!)
Operating pressure p in bar
Flow qV in l/min
5) The data is valid at a frequency of 50 Hz
Performance diagram 5)
Radial piston pump
1) See the following performance diagram
2) 60 Hz is not possible!
3) Referred to the speed at 50 Hz
Hydraulic fluid Mineral oil (HLP) according to DIN 51524, part 2
Please observe our specifications according to data sheet 07075!
Hydraulic fluid temperature range °C –20 to +80
Maximum permitted degree of contamination
of the hydraulic fluid
cleanliness class according to ISO 4406 (c)
Class 20/18/15 4)
Optimum viscosity range mm2/s 10 to 200
Direction of rotation Optional (radial piton pump), clockwise (external gear pump)
Installation position Vertical
Mode of operation
All modes of operations in which the steady-state oil temperature remains below 80 °C.
Radial piston pump
Flow 3) qV in l/min 0.49 0.82 1.00 2) 1.25 1.70 2) 1.95 2.55 2) 2.60 4.00 2)
Drive power Speed 3) n in min–1 1380 1380 2820 1380 2820 1380 2820 1380 2820
1.1 kW 1) Nominal
pressure 3) pmax in bar 700 700 700 450 310 250 200 180 140
Speed 3) n in min–1 1400 1400 2890 1400 2890 1400 2890 1400 2890
2.2 kW 1) Nominal
pressure 3) pmax in bar 700 700 700 450 700 350 450 250 280
External gear pump
Flow 3) qV in l/min 1.40 2.80 4.40 5.60 7.00 8.80 11.2 2) 14.0 2)
Drive power Speed 3) n in min–1 1380 1380 1380 1380 1380 1380 2820 2820
1.1 kW 1) Nominal
pressure 3) pmax in bar 260 180 140 110 90 70 45 37
Speed 3) n in min–1 1400 1400 1400 1400 1400 1400 2890 2890
2.2 kW 1) Nominal
pressure 3) pmax in bar 260 260 260 220 170 140 110 85
Protection class according to VDE 0530 / EN 60034 IP 54 with power unit completely mounted
Nominal tank size / type 3/R 4/R 4/G 5/R 7/R 7/G
Weight (without hydraulic fluid) kg 17.8 18.4 19.6 23.0 25.0 26.6
4) The cleanliness classes specified for the components must
be adhered to in hydraulic systems. Effective filtration pre-
vents faults and at the same time increases the service life
of the components.
For selecting the filters, see data sheet 51144.
Operating pressure p in bar
Flow qV in l/min
External gear pump

W2
V1 W1U1
U2 V2
L1 L2 L3PE
W2
V1 W1U1
U2 V2
L1 L2 L3PE
W2 U2 V2
W1
U1 V1
Hydraulics Bosch Rexroth AGRE 51142/05.13 UPE 2 5/10
Electric motor
Terminal assignment
The clamping and drive module is designed for the mode of
operation according to VDE 0530 (EN 60034) for short-time
operation S2 and intermittent operation S3 in the area of the
nominal power. The electric motor complies with insulation
Electromagnetic compatibility of devices (EMVG)
According to the "Act on the electromagnetic compatibility of
devices (§2, subsection 4)" of the EEC directive, the clamp-
ing and drive module is no device that is ready-for-use. In or-
der to avoid electromagnetic interference that might occur, we
recommend using the interference suppression elements by
the company Murr-Elektronik in 71570 Oppenweiler.
e.g. type 23050, 3 x400 VAC, 50-60 Hz
1) Other voltages on request 2) Number of poles 4 3) Number of poles 2
class F and the complete clamping and drive module with
protection class IP 54.
The electric motor's direction of rotation depends on the
pump installed (in this connection see Technical data page 4).
Technical Data (For applications outside these parameters, please consult us!)
Voltage 1) UV 230 / 400 ±6 % Y
Frequency fHz 50 / 60
Mode of operation S2 short-time operation, S3 intermittent operation
Insulation class F (winding)
Protection class IP 54
Number of poles 2 / 4
Customer side: ∆ triangle U = 230 V Customer side: Y star U = 400 V
Terminal assignment in the terminal box at the clamping and drive module
Factory side:
Temperature switch
(optional)
Frequency 50 Hz
Power Speed Power Nom. current at
kW min-1 factor cos 230 V Y 400 V
1.1 2) 1380 0.80 4.70 A 2.70 A
1.1 3) 2820 0.85 4.45 A 2.55 A
2.2 2) 1400 0.82 9.20 A 5.30 A
2.2 3) 2890 0.85 8.35 A 4.80 A
Frequency 60 Hz
Power Speed Power Nom. current at
kW min-1 factor cos 230 V Y 400 V
1.1 2) 1670 0.84 4.45 A 2.55 A
1.1 3) 3380 0.88 4.10 A 2.35 A
2.2 2) 1690 0.83 8.70 A 5.00 A
2.2 3) 3420 0.88 7.80 A 4.50 A

A
B
C
D
B
A
Ø9
E
ca.25
G
F
15
54
34
1
2
6/10 Bosch Rexroth AG Hydraulics UPE 2 RE 51142/05.13
X, Y and Z are reference axes for de-
termining the installation dimensions
when control blocks are mounted.
1 Control connection surface
2 Oil drain screw G 3/8
3Ventilation filter
4Carrying handle
Dimensions (dimensions in mm)
Filling and removal quantity
max
min.
Tank Size in liters
Size Radial piston
pump
External gear
pump
Filling quantity
32.4
44.5 4.1
54.3
77.2 6.8
Removal quantity
31.0
43.0 2.6
52.3
75.1 4.7
Removal quan-
tity up to switch-
ing point of level
switch
30.8
42.8 2.4
52.0
74.8 4.4
"X" reference axis
"Y" reference axis
"Z" reference axis
Tank size A B C D E F G
3164 125 85 40 105 280 295
4164 125 85 40 105 390 405
5190 156 98 50 118 320 335
7190 156 98 50 118 450 465
Not possible

1212
75
70
65
60
55
50
0 100 200 300 400 500 600 700
45
R1,70
R0,82
R1,00
R0,49
R1,25
80
75
70
65
60
55
R4,00
50
0 100 200 300 400 450
50 150 250 350
R2,60 R2,55
R1,95
65
60
55
50
45
400 40 80 120 160 200 240 280
G1,40
G5,60 G4,40
G2,80
75
70
65
60
55
50
G14,0
G11,2 G8,00
G7,00
04080 120 160 180
20 60 100 140
Hydraulics Bosch Rexroth AGRE 51142/05.13 UPE 2 7/10
Sound pressure level (measured at
= 41 mm2/s and
= 50 °C)
Operating pressure in bar
Level switch (option)
Description
The level switch provides for the electric monitoring of the hy-
draulic fluid level. If the minimum oil level is reached, the con-
tact opens and thus outputs a signal to the control.
Electrical function
Maximum level Minimum level
Sound pressure level in dB(A)
Radial piston pump
External gear pump
Sound pressure level in dB(A)
Sound pressure level in dB(A)
Technical data
Maximum voltage V 50 AC / DC
Maximum current consumption A 0.25
Maximum power consumption W 3.0
Protection class IP 65
Contact type Normally closed contact
Sound pressure level in dB(A)
Operating pressure in bar
Operating pressure in bar Operating pressure in bar

67
280
300
20
156
425
445
20
156
45
M8 Ø9
40
30
30
Ø40
8/10 Bosch Rexroth AG Hydraulics UPE 2 RE 51142/05.13
Ventilation filter (option)
When the clamping and drive module is used in a heavily
contaminated environment, we recommend using a ventila-
tion filter.
Technical data
Nominal current with 250 V AC 50/60 Hz
(cos 0.95 / 0.60) A 2.5 / 1.6
Nominal current with 50 V DC A 0.25
Contact type Normally closed contact
Tripping temperature °C 80 ±3 K
The ventilation filter has a filter rating of 10 m.
Oil tray (option) (dimensions in mm)
Size 3 and size 4 Material no. R901109231
Size 5 and size 7 Material no. R901109235
Color: RAL 7035 "Light gray"
By means of the temperature switch, the clamping and drive
module is protected from inadmissibly high hydraulic flu-
id temperatures. The temperature switch has a fixedly set
switching point switching at a hydraulic fluid temperature
of 80 °C.
The switch-back hysteresis is ca. 10 K.
Temperature < 80 °C Temperature ≥ 80 °C
Electrical function
Temperature switch (option)

Hydraulics Bosch Rexroth AGRE 51142/05.13 UPE 2 9/10
Commissioning notes
– Check whether the clamping and drive module has been
connected to the machine to be operated in a professional
form (hydraulically and electrically).
– For the electrical connections of the motor, the washers
and connection bridges that are included in the scope of
delivery must be used.
– The electric motor must be protected by means of equip-
ment with an overload relay.
The later must be set to the nominal current that is speci-
fied on the name / rating plate.
– When installing the clamping and drive module at an exter-
nal gear pump, you must imperatively observe the direction
of rotation of the motor; see arrow indicating the direction
of rotation.
(Practical check: Switch on the motor briefly and check
whether the pump delivery fluid.)
(Optical check: Remove the ventilation filter at the tank
cover, switch on the electric motor briefly and check the
direction of rotation of the rotor shaft.)
– Only fill in the hydraulic fluid through a filter with the re-
quired minimum retention rate.
– The clamping and drive module must maximally be filled
with hydraulic fluid until the dipstick is reached and/or to the
lower edge of the cover.
– The clamping and drive module must in no case be oper-
ated without hydraulic fluid.
– Start up the clamping and drive module without load and
allow it to run at zero pressure for some seconds in order to
provide for sufficient lubrication.
– After bleeding the hydraulic control as well as the actuators
by moving them back and forth several times or by opening
available bleeding points, the hydraulic fluid in the clamping
and drive module is to be refilled to the correct level.
– The clamping and drive module may only be operated
within the permitted limits. It may moreover only be oper-
ated if it is in an unobjectionable condition.
– When carrying out any work at the clamping and drive mod-
ule, the system must be depressurized and de-energized.
– Unauthorized conversions or modifications, which affect
safety and function are not permitted.
–
Existing protective devices must not be removed.
– The generally valid safety and accident prevention regula-
tions must be observed and complied with.
Attention!
The clamping and drive module may heat up during operation
=> risk of injury!
The clamping and drive module may only be set, maintained
and serviced by authorized, trained and instructed personnel.
In repairs, only original spare parts may be used!

Bosch Rexroth AG
Hydraulics
Zum Eisengießer 1
97816 Lohr am Main, Germany
Phone +49 (0) 93 52 / 18-0
www.boschrexroth.de
© This document, as well as the data, specifications and other informa-
tion set forth in it, are the exclusive property of Bosch Rexroth AG. It
may not be reproduced or given to third parties without its consent.
The data specified above only serve to describe the product. No state-
ments concerning a certain condition or suitability for a certain applica-
tion can be derived from our information. The information given does not
release the user from the obligation of own judgment and verification. It
must be remembered that our products are subject to a natural process
of wear and aging.
10/10 Bosch Rexroth AG Hydraulics UPE 2 RE 51142/05.13
Notes

Bosch Rexroth AG
Hydraulics
Zum Eisengießer 1
97816 Lohr am Main, Germany
Phone +49 (0) 93 52 / 18-0
www.boschrexroth.de
© This document, as well as the data, specifications and other informa-
tion set forth in it, are the exclusive property of Bosch Rexroth AG. It
may not be reproduced or given to third parties without its consent.
The data specified above only serve to describe the product. No state-
ments concerning a certain condition or suitability for a certain applica-
tion can be derived from our information. The information given does not
release the user from the obligation of own judgment and verification. It
must be remembered that our products are subject to a natural process
of wear and aging.
Hydraulics Bosch Rexroth AGRE 51142/05.13 UPE 2 11/10
Notes

Bosch Rexroth AG
Hydraulics
Zum Eisengießer 1
97816 Lohr am Main, Germany
Phone +49 (0) 93 52 / 18-0
www.boschrexroth.de
© This document, as well as the data, specifications and other informa-
tion set forth in it, are the exclusive property of Bosch Rexroth AG. It
may not be reproduced or given to third parties without its consent.
The data specified above only serve to describe the product. No state-
ments concerning a certain condition or suitability for a certain applica-
tion can be derived from our information. The information given does not
release the user from the obligation of own judgment and verification. It
must be remembered that our products are subject to a natural process
of wear and aging.
12/10 Bosch Rexroth AG Hydraulics UPE 2 RE 51142/05.13
Notes
Table of contents
Other REXROTH Control Unit manuals
Popular Control Unit manuals by other brands
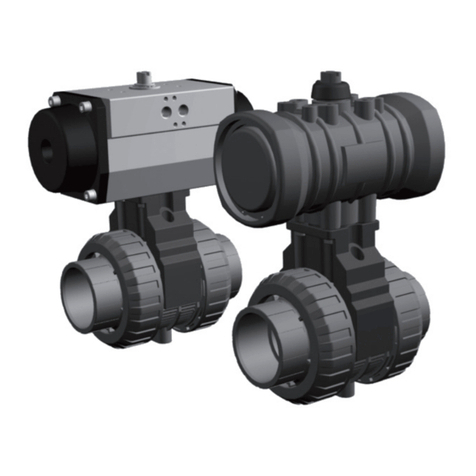
Cepex
Cepex EXTREME Series Installation and maintenance manual
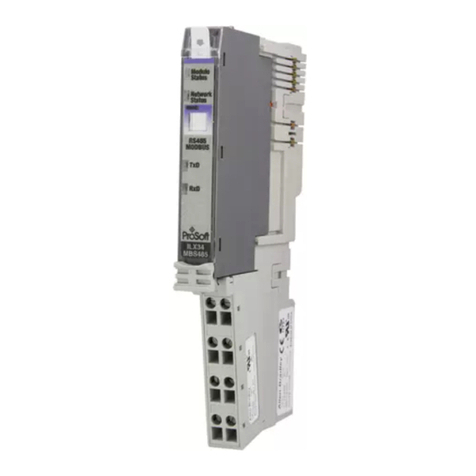
ProSoft Technology
ProSoft Technology ILX34-MBS485 user manual
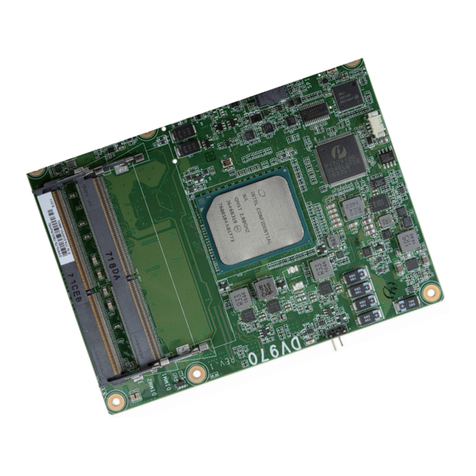
DFI
DFI DV970 user manual
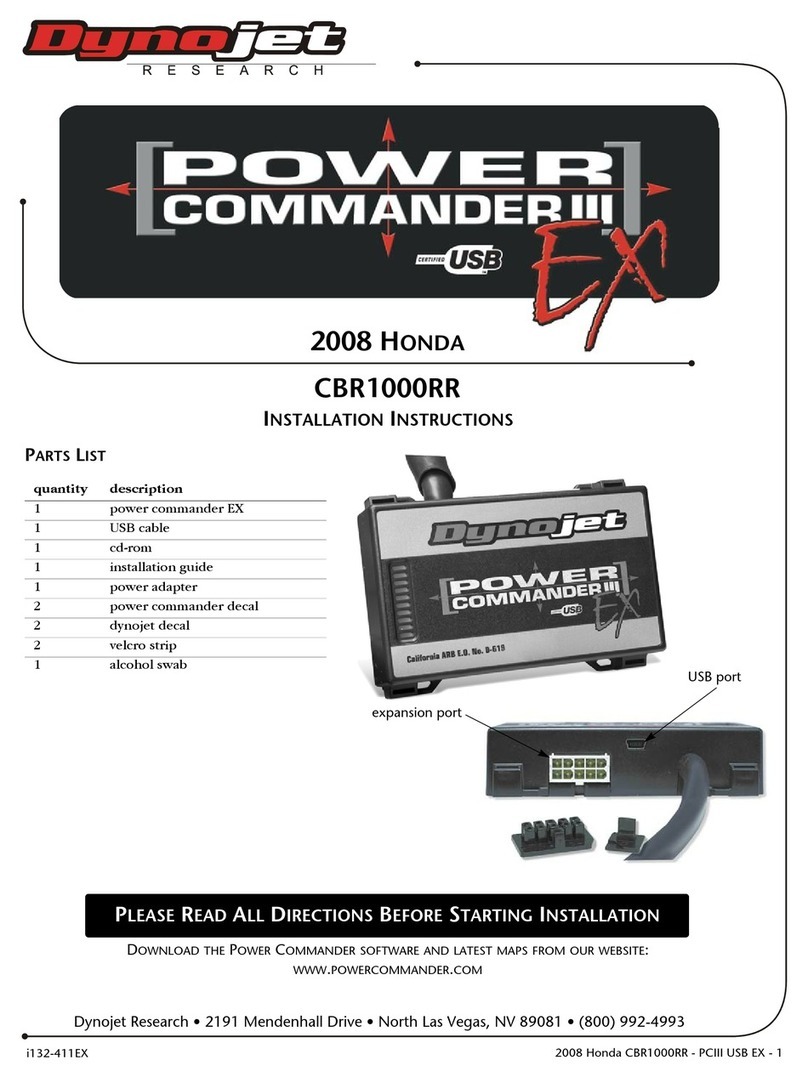
Dynojet
Dynojet Power Commander III USB EX installation instructions
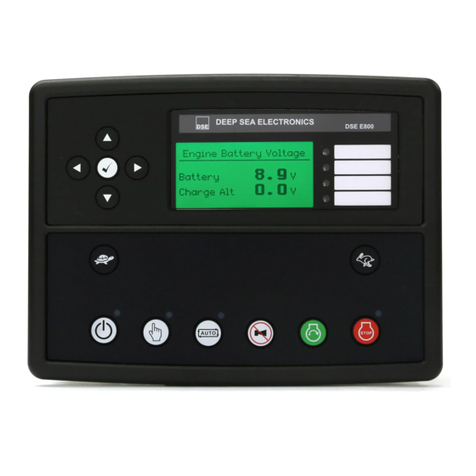
DEEP SEA ELECTRONICS
DEEP SEA ELECTRONICS DSEE800 installation instructions
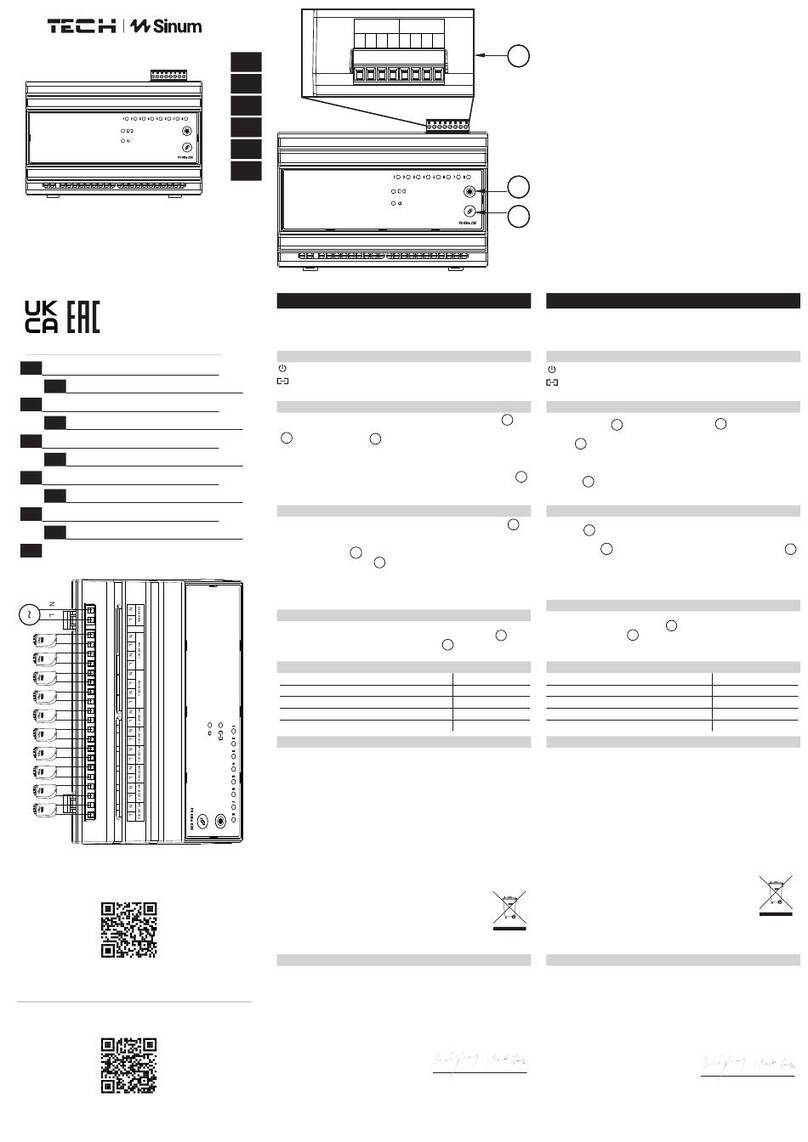
TECH
TECH Sinum PS-08m 230 quick start guide