S&C 5800 Series User manual

5800 Series Automatic Switch Control
April 27, 2020
© S&C Electric Company 2002-2020, all rights reserved Instruction Sheet 1041-540
Operating Instructions
Table of Contents
Section Page Section Page
Introduction
Qualified Persons ........................... 2
Read this Instruction Sheet ................... 2
Retain this Instruction Sheet. . . . . . . . . . . . . . . . . . . 2
Proper Application .......................... 2
Warranty .................................. 2
Safety Information
Understanding Safety-Alert Messages........... 3
Following Safety Instructions .................. 3
Replacement Instructions and Labels ........... 3
Safety Precautions ......................... 4
Installation
Applicable Software ......................... 5
Switch Control Components. .................. 5
Faceplate LEDs. ............................ 7
Faceplate Switches. ......................... 9
Faceplate LCD Screen.. ......................10
Power Supply/Control I/O Module. ..............13
Power Supply/Control I/O Module LEDs...........13
Battery Care and Maintenance. ................15
Switch Control Software. .....................15
Switch Control Operation
Signal Processing...........................17
RMS Ac Waveform Analysis...................17
Voltage Sensing for S&C Switches..............18
Phase Angle Measurements ..................18
Overcurrent Fault & Voltage Loss Detection ......18
Ground Overcurrent Detection. ................19
Voltage Loss Detection...................... 20
Inrush Restraint ........................... 20
Overcurrent and Voltage Loss Events .......... 20
Overcurrent Data Logging ................... 20
Automatic Operations. .......................21
Line Sectionalizing...........................21
Phase Loss Protection....................... 22
Phase Loss Protection with Automatic Reclose. .. 23
Shots-to-Lockout. .......................... 24
Local Shots-to-Lockout...................... 25
Remote Shots-to-Lockout.................... 25
Overcurrent Fault Protection
Fault Events Log ........................... 26
Fault Magnitude and Duration Log ............. 30
Ac Power Outages Log. ......................31
Routine Data-Logging Information ............. 32
Data Logging for Most Recent Week............ 33
Profile Data for One Day..................... 33
Generating Reports
Saving Settings and Data .................... 35
Saving and Loading Setup Configurations
Saving a Setup Configuration................. 36
Loading a Saved Configuration ............... 36
Using IntelliLink®Setup Software Without Data
Using Snapshots........................... 37
Saving a Snapshot ......................... 37
Viewing a Snapshot......................... 37
Creating a Configuration (CFG) File ............ 38
Updating Control Software
The Update Program. ....................... 39
Updating Control Software
with Battery Power Only................... 40

2 S&C Instruction Sheet 1041-540
Introduction
Qualified Persons WARNING
Only qualified persons who are knowledgeable in the installation, operation, and
maintenance of overhead and underground electric distribution equipment, along
with all associated hazards, may install, operate, and maintain the equipment covered
by this publication. A qualified person is someone who is trained and competent in:
• The skills and techniques necessary to distinguish exposed live parts from nonlive
parts of electrical equipment
• The skills and techniques necessary to determine the proper approach distances
corresponding to the voltages to which the qualified person will be exposed
• The proper use of special precautionary techniques, personal protective equipment,
insulated and shielding materials, and insulated tools for working on or near exposed
energized parts of electrical equipment
These instructions are intended ONLY for such qualified persons. They are not
intended to be a substitute for adequate training and experience in safety procedures
for this type of equipment.
Read this
Instruction Sheet NOTICE
Thoroughly and carefully read this instruction sheet and all materials included in
the product’s instruction handbook before installing or operating a 5800 Series
Automatic Switch Control. Familiarize yourself with the Safety Information and Safety
Precautions on pages 3 and 4. The latest version of this publication is available
online in PDF format at sandc.com/en/support/product-literature/.
Retain this
Instruction Sheet
This instruction sheet is a permanent part of your 5800 Series Automatic Switch Control.
Designate a location where you can easily retrieve and refer to this publication.
Proper Application WARNING
The equipment in this publication is only intended for a specific application. The
application must be within the ratings furnished for the equipment.
Warranty The warranty and/or obligations described in S&C’s Price Sheet 150, “Standard Conditions
of Sale–Immediate Purchasers in the United States,” (or Price Sheet 153, “Standard
Conditions of Sale–Immediate Purchasers Outside the United States,”) plus any special
warranty provisions, as set forth in the applicable product-line specication bulletin,
are exclusive. The remedies provided in the former for breach of these warranties shall
constitute the immediate purchaser’s or end user’s exclusive remedy and a fulllment of
the seller’s entire liability. In no event shall the seller’s liability to the immediate purchaser
or end user exceed the price of the specic product that gives rise to the immediate
purchaser’s or end user’s claim. All other warranties, whether express or implied or
arising by operation of law, course of dealing, usage of trade or otherwise, are excluded.
The only warranties are those stated in Price Sheet 150 (or Price Sheet 153), and THERE
ARE NO EXPRESS OR IMPLIED WARRANTIES OF MERCHANTABILITY OR FITNESS
FOR A PARTICULAR PURPOSE. ANY EXPRESS WARRANTY OR OTHER OBLIGATION
PROVIDED IN PRICE SHEET 150 (OR PRICE SHEET 153) IS GRANTED ONLY TO THE
IMMEDIATE PURCHASER AND END USER, AS DEFINED THEREIN. OTHER THAN AN
END USER, NO REMOTE PURCHASER MAY RELY ON ANY AFFIRMATION OF FACT OR
PROMISE THAT RELATES TO THE GOODS DESCRIBED HEREIN, ANY DESCRIPTION
THAT RELATES TO THE GOODS, OR ANY REMEDIAL PROMISE INCLUDED IN PRICE
SHEET 150 (or PRICE SHEET 153).

S&C Instruction Sheet 1041-540 3
Safety Information
Understanding
Safety-Alert
Messages
Several types of safety-alert messages may appear throughout this instruction sheet and
on labels and tags attached to your 5800 Series Automatic Switch Control. Familiarize
yourself with these types of messages and the importance of these various signal words:
DANGER
“DANGER” identifies the most serious and immediate hazards that will likely result in
serious personal injury or death if instructions, including recommended precautions,
are not followed.
WARNING
“WARNING” identifies hazards or unsafe practices that can result in serious personal
injury or death if instructions, including recommended precautions, are not followed.
CAUTION
“CAUTION” identifies hazards or unsafe practices that can result in minor personal
injury if instructions, including recommended precautions, are not followed.
NOTICE
“NOTICE” identifies important procedures or requirements that can result in product
or property damage if instructions are not followed.
Following Safety
Instructions
If you do not understand any portion of this instruction sheet and need assistance, contact
your nearest S&C Sales Ofce or S&C Authorized Distributor. Their telephone numbers
are listed on S&C’s website sandc.com, or call the S&C Global Support and Monitoring
Center at 1-888-762-1100.
NOTICE
Read this instruction sheet thoroughly and carefully
before installing your a 5800 Series Automatic Switch
Control.
Replacement
Instructions
and Labels
If additional copies of this instruction sheet are needed, contact your nearest S&C Sales
Ofce, S&C Authorized Distributor, S&C Headquarters, or S&C Electric Canada Ltd.
It is important that any missing, damaged, or faded labels on the equipment be replaced
immediately. Replacement labels are available by contacting your nearest S&C Sales
Office, S&C Authorized Distributor, S&C Headquarters, or S&C Electric Canada Ltd.

4 S&C Instruction Sheet 1041-540
Safety Precautions
DANGER
The 5800 Series Automatic Switch Control line voltage input range is 93 to
276 Vac. Failure to observe the precautions below will result in serious per-
sonal injury or death.
Some of these precautions may differ from your company’s operating procedures
and rules. Where a discrepancy exists, follow your company’s operating procedures
and rules.
1. QUALIFIED PERSONS. Access to the 5800 Series
Automatic Switch Control must be restricted only to
qualified persons. See the “Qualified Persons”
section on page 2.
2. SAFETY PROCEDURES. Always follow safe
operating procedures and rules.
3. PERSONAL PROTECTIVE EQUIPMENT. Always
use suitable protective equipment, such as rubber
gloves, rubber mats, hard hats, safety glasses, and
flash clothing, in accordance with safe operating
procedures and rules.
4. SAFETY LABELS. Do not remove or obscure any
of the “DANGER,” “WARNING,” “CAUTION,” or
“NOTICE” labels.
5. MAINTAINING PROPER CLEARANCE. Always
maintain proper clearance from energized
components.

S&C Instruction Sheet 1041-540 5
Installation
This instruction sheet was prepared for use with all stand-alone 5800 Series control
software available as of September 2004:
SNCD2S0X Rev. 2.37, SNCD2S0V Rev. 2.31, PADD2S0X Rev. 2.37, USBD2S0X Rev.
2.30, and UDSD2S0X Rev. 2.26.
The revision number is on the setup disk label and on the IntelliLink® Setup Software
TROUBLESHOOTING: Control & Switch Information screen. For questions regarding
the applicability of information in this instruction sheet to future product releases, please
contact S&C.
Applicable
Software
This section describes various switch control components. The following “Overview of
Switch Control Operations” section explains how these components work together to
monitor the distribution feeder and manage switch operation.
The Switch Control Modules
The switch control electronics modules are described in this section and are shown in
Figure 1.
Switch Control
Components
Faceplate
processor board
Power supply
control I/O
module
ASP module
(behind the PS/IO
module
Sensor
conditioning
module (behind
the PS/IO and
ASP modules)
Figure 1. Location of the switch control modules (front view).
Faceplate/5800 control module. This printed circuit board is attached to the back of
the faceplate. It includes all the electronics and toggle switches for the faceplate and the
5800 control microprocessor.
Power Supply/Control I/O module (PS/IO).This is the source for all low-voltage
power the switch control uses and any associated communications equipment. It is also
responsible for all digital interfacing. The PS/IO module performs all data-acquisition,
control, and basic communication interfacing functions. For more about the power
management system, see the “Power Supply/Control I/O Module” section on page 13.
ASP module.This module is responsible for waveform processing. It is located behind
the Power Supply/Control I/O module.
Sensor Conditioning module.This module conditions ac waveforms to standard low-
voltage AC levels and provides analog I/O interfacing. The module is located behind PS/
IO and ASP modules.

6 S&C Instruction Sheet 1041-540
Installation
The Faceplate
The 5800 Series control faceplate includes LEDs and switches for monitoring and
controlling the line switches and the switch control. It also includes an LCD screen and
two DATA SCROLL switches. See Figure 2.
Figure 2. The 5801 Series control faceplate.
Note: To extend battery carryover time, the switch control turns off power to the face-
plate (including the LEDs and the LCD screen) when the enclosure door or low-voltage
cabinet door is closed.

S&C Instruction Sheet 1041-540 7
Installation
The faceplate includes the following LEDs:
Overcurrent Fault LED
This LED becomes lit when the switch control detects an Overcurrent condition. For a
normally closed switch, the LED turns off when all of the following are true:
• Three-phase line voltage has been sensed.
• The switch is closed.
• Forty-ve minutes have elapsed.
The LED also turns OFF when the switch is closed and someone toggles the switch
on the faceplate The REMOTE/LOCAL switch or clears the LED via SCADA.
For the normally open switch, the LED turns off when doing one of the following:
• Toggle the REMOTE/LOCAL switch or clear the LED via SCADA. (The line switch can
be open or closed.)
• Close the switch from the faceplate or via SCADA.
Note: The LED cannot be cleared via SCADA if the REMOTE/LOCAL switch is in the
Local position.
Note: When reinitializing the switch control using the IntelliLink software, the LED
turns off regardless of whether the conditions above are met.
Remote Communication RCV/XMT LEDs
These LEDs blink when the switch control sends or receives signals through remote-
communication equipment installed in the control enclosure. There are separate sets of
LEDs for Port A and Port B.
RCV LED – Blinks when the switch control detects an incoming character
XMT LED – Blinks when the switch control sends one or more characters
Note: Activity on both of these LEDs will be seen only if remote-communications
equipment is installed, properly connected, and receiving power. The XMT LED blinks
any time a transmit is attempted, regardless of whether communications equipment is
properly installed.
Error Detected LED
This LED lights up if the switch control detects any of the following conditions:
• Battery charger overvoltage. If the charger attempts to overcharge the battery, the
switch control turns the charger off and turns on the LED.
• Open/close contacts are not mutually exclusive. The switch position contacts are
either both open or both closed.
• Temperature sensor failure. The temperature sensor (on the PS/IO) reads abnormally
high or low (generally caused by an open/shorted circuit).
• Switch error (5801 control). There is an error with the switch, such as open visual
disconnect contacts (Scada-Mate) or low pressure (Joslyn).
• Switch in Local mode (5802/5803 controls). The switch control senses that one
of the switches is in Local mode (a manual mode for the switch, selected at the low
voltage cabinet).
Processor Status LED
This LED blinks once per second when the switch control has power and the control’s
software is running normally.
Faceplate LEDs

8 S&C Instruction Sheet 1041-540
Installation
Battery Low LED
This LED is off when the battery system is working normally and the battery is charged.
The LED becomes lit when the battery power level drops below the Battery Voltage
Low value on the TROUBLESHOOTING: Battery System screen. It is normal for this LED
to be ON when the switch control is operating on battery power and the normal battery
carryover period is nearly over. If this LED is lit when ac power is on and the battery
normally would contain an adequate charge, the battery may be defective.
The LED blinks during any battery test. The switch control automatically runs the
battery test at scheduled intervals. In addition, a SCADA command or the faceplate
BATTERY TEST/LAMP TEST switch can be used to start a battery test at any time. See
the Battery Test/Lamp Test switch” section on page 9 for more details.
Note: When replacing a defective battery, initiate a battery test immediately to update
the battery status.
Closed LED
This red LED lights up when the line switch is closed. The LED indicates the sensed
position of the line switch based on the state of the Closed status input from the switch.
It also blinks while Shots-to-Lockout mode is enabled. Each CLOSED LED provides
information about one line switch.
Trip LED
This yellow LED becomes lit when the switch control trips open the line switch using
automatic logic (Sectionalizing, Phase Loss Protection, etc.). It turns off when the
switch is closed. For the normally open switch, the LED also turns off when toggling the
REMOTE/LOCAL switch. Each TRIP LED provides information about one line switch.
If the switch tripped because of phase-loss protection and Phase Loss Protection
with Automatic Reclose mode is enabled, the LED blinks while waiting to reclose the
switch. For the normally open switch, the LED also turns off when toggling the REMOTE/
LOCAL switch.
Note: When reinitializing the switch control using the IntelliLink software, the LED
turns off regardless of whether the switch is closed.
Open LED
This green LED becomes lit when the line switch is open. The LED indicates the sensed
position of the line switch based on the state of the Open status input from the switch.
Each OPEN LED provides information about one line switch.
Local LED
This LED is lit when remote (SCADA) operation of the switch control is blocked and
local operation is allowed. The LED is off when local operation is blocked and remote
operation is allowed.
Automatic Operation Enabled LED
This LED is lit when automatic operation of the switch control is enabled.
CAUTION
If automatic operation is enabled, the Automatic Control logic may trip the switch
regardless of the state of the REMOTE/LOCAL switch.
Automatic Operation Disabled LED
This LED is lit when automatic operation of the switch control is disabled.

S&C Instruction Sheet 1041-540 9
Installation
The faceplate includes the following switches:
Data Scroll Switches
Use these switches to scroll the LCD screen data into view. For more details, see “The
Faceplate LCD Screen” section on page 10, Figure 3 on page 11, and Figure 4 on page 12.
Battery Test/Lamp Test switch
Toggle this switch to the Up position to start a battery test. The test lasts approximately
30 seconds if the control is operating on battery power or approximately 3 minutes if the
control is operating on ac power. The BATTERY LOW LED blinks during the test. See the
“Power Supply/Control I/O Module” section on page 13 for more details.
Hold this switch in the Down position to test the LEDs on the faceplate (all LEDs should
blink).
Close/Open switch
Toggle this switch to the Up position to transmit a “Close” pulse to the line switch. Toggle
this switch to the Down position to transmit an “Open” pulse to the switch. It is also used
to enable Shots-to-Lockout mode. See the “Automatic Operations” section on page 21.
Each CLOSE/OPEN switch operates one line switch.
Note: If the REMOTE/LOCAL switch is in the Remote position, toggling a CLOSE/
OPEN switch has no effect.
Remote/Local switch
Toggle this switch to the Up position to enable remote (SCADA) control of the line
switch(es) and disable commands from the faceplate CLOSE/OPEN switches and
automatic operation ENABLE/DISABLE switch.
Toggle this switch to the Down position to disable remote (SCADA) operation of the
line switch(es) and enable commands from the faceplate CLOSE/OPEN switch(es) and
automatic operation ENABLE/DISABLE switch. (The LOCAL LED becomes lit when this
switch is set to Local mode.)
Note: To disable local automatic operation and have full control of the switch(es),
the faceplate ENABLE/DISABLE switch must be toggled to the Disable position. If
automatic operation is disabled on the SETUP: Automatic Operation screen (for both
switches, if applicable), toggling the ENABLE/DISABLE switch has no effect.
Enable/Disable switch
Toggle this switch to the Up position to enable automatic switch operation of the control.
Toggle this switch to the Down position to disable automatic operation. This switch
affects automatic operation of both line switches, if applicable. It is also used in enabling
Shots-to-Lockout mode. See the “Automatic Operations” section on page 21.
Note: If automatic operation is disabled on the SETUP: Automatic Operation screen
(for both switches, if applicable), toggling this switch has no effect.
Faceplate
Switches

10 S&C Instruction Sheet 1041-540
Installation
The LCD screen enables quick access to key information while at the switch control
installation site. The LCD screen displays several categories of information:
Real-time Data. Displays the total operation count, and the present phase and ground
current levels, line voltage, reverse current conditions, phase angles, and total kvar
ows, for both feeders if applicable (This information is also displayed on the SETUP:
Site- Related screen.)
Auto Operation (Switch 1 and Switch 2, if applicable). Displays the automatic operation
features that are enabled, and the present value for the automatic operations setpoints
(These values are also displayed on the SETUP: Automatic Operation screens.)
Fault Events. Displays the date, time, event, switch control interpretation, and action
for the 62 most recent protection-related fault events. These fault messages are coded
versions of the messages displayed on the OVERCURRENT FAULT: Fault Events screen
(See “Fault Events Log” section on page 26 for an explanation of each code.)
Fault Magnitudes. Displays the date, time, phase, peak magnitude, and duration for the
16 (5801 control) or 32 (5802/5803 controls) most recent overcurrent fault events (This
information is also displayed on the OVERCURRENT FAULT: Fault Magnitudes screen.)
Maintenance. Displays the software version installed in the switch control, assorted
battery status information, and the present cabinet temperature (The software version
is also displayed on the TROUBLESHOOTING: Control & Switch Information screen.
The battery and temperature information is also displayed on the TROUBLESHOOTING:
Battery System screen.)
Fault Settings. Displays the present value for each of the fault-detection setpoints,
for Switch 1 and Switch 2 if applicable (These values are also displayed on the SETUP:
Fault Detection screen.)
The 2 x 40 character LCD screen always displays one eld from a large data page. See
Figure 3 on page 11 and Figure 4 on page 12.
Use the DATA SCROLL switches to scroll each eld into view.
• To move left or right across the page (from one category to another category), toggle
the LEFT/RIGHT switch.
• To move up or down between elds within a category, toggle the UP/DOWN switch.
• The Fault Events and Fault Magnitude logs are circular buffers. The most recent event
is normally displayed on the LCD screen. To see the second-most-recent event, toggle
the switch to the Up position.
For an explanation of the codes used in the Fault Events column, see “Fault Events Log”
section on page 30.
Faceplate LCD Screen

S&C Instruction Sheet 1041-540 11
Installation
Categories
Fields 1. Real-
Time Data
2. Auto Operation 3. Fault
Events
4. Fault
Magnitude
5. Maintenance 6. Fault Settings
Operations
Counter
Line Current
(Amps)
Ground
Current
(Amps)
Line Voltage
(Volts)
Phase Angle
(Degrees)
Reverse
Current
(Active or
None)
Line kVARs
Automatic Operation
Features Enabled
Transfer Process
Time Limit
Return to Normal
Delay Time
Sectionalizer Reset
and Extended
Voltage Loss Time
Successful Reclose
Rest Time
Fault Current
Required before
First/ All Voltage
Loss(es)
Recloser Counts
to Trip, w/Fault
(Minimum)
Recloser Counts
to Trip, w/Fault
(Maximum)
Recloser Counts
to Trip, Voltage
Loss Only
Number of
Shots Required
for Lockout
Shots-To-Lockout
Time Threshold
(Tenths)
Phase Loss
Protection
Voltage Loss
Threshold
Phase Loss
Protection Time
Threshold
Phase Loss
Protection Current
Threshold
Automatic Reclose
Time Threshold
Present Transfer
Capacity, Left Feeder
Present Transfer
Capacity, Right
Feeder
Software Version
AC Power/Battery
Status
Battery
Low/Bad Setpoints
Battery Voltage w/o
Surface Charge
Predicted Voltage
Under Load
Power Supply
Voltage/ Battery
Impedance
Cabinet Temperature
Phase Fault Detected
Current Level (Amps)
Ground Fault Detected
Current Level (Amps)
Phase Fault Duration
Time Threshold
(msec)
Ground Fault Duration
Time Threshold
(msec)
Phase Current Inrush
Restraint Time (msec)
Ground Current Inrush
Restraint Time (msec)
Phase Current Inrush
Restraint Multiplier
Ground Current Inrush
Restraint Multiplier
Figure 3. LCD screen data page for the 5801 control.

12 S&C Instruction Sheet 1041-540
Installation
Categories
Fields 1. Real-
Time Data
2. Auto Operation 3. Sw. 2 Auto
Operation
4. Fault
Events
5. Fault
Magnitude
6.
Maintenance
7. Fault
Settings
Cloose/Open
Status
[Sw. 1, 2, 3]
Operations
Counter
[Sw. 1, 2, 3]
Switch 1 Line
Current (Amps)
Switch 2 Line
Current (Amps)
Switch 3 Line
Current (Amps)
Ground Current
(Amps)
[Sw. 1, 2, 3]
Switch 1 Line
Voltage (Volts)
Switch 2 Line
Voltage (Volts)
Switch 1 Phase
Angle (Degrees)
Switch 2 Phase
Angle (Degrees)
Switch 1 Reverse
Current (Active or
None)
Switch 2 Reverse
Current (Active or
None)
Switch 1 Line
kVARs Switch 2
Automatic
Operation Features
Enabled
Transfer Process
Time Limit
Return to Normal
Delay Time
Sectionalizer Reset
+ Extended Voltage
Loss Time
Successful Reclose
Rest Time
Fault Current
before First/All
Voltage Loss(es)
Recloser Counts to
Trip, w/Fault
Recloser Counts to
Trip, Voltage loss
Only
Number of Shots
Required for
Lockout
Shots-To-Lockout
Time Threshold
(Tenths)
Phase Loss
Protection Voltage
Loss Threshold
Phase Loss
Protection Time
Threshold
Phase Loss
Protection Current
Threshold
Automatic Reclose
Time Threshold
Present Transfer
Capacity, Left
Feeder
Present Transfer
Capacity, Right
Feeder
Automatic
Operation Features
Enabled
Transfer Process
Time Limit
Return to Normal
Delay Time
Sectionalizer
Reset + Extended
Voltage
Loss Time
Successful
Reclose
Rest Time
Fault Current
before First/All
Voltage Loss(es)
Recloser Counts to
Trip, w/Fault
Recloser Counts to
Trip, Voltage loss
Only
Number of Shots
Required for
Lockout
Shots-To-Lockout
Time Threshold
(Tenths)
Phase Loss
Protection Voltage
Loss Threshold
Phase Loss
Protection Time
Threshold
Phase Loss
Protection Current
Threshold
Automatic Reclose
Time Threshold
Present Transfer
Capacity, Left
Feeder
Present Transfer
Capacity, Right
Feeder
Software
Version
AC Power/
Battery
Status
Battery
Low/Bad
Setpoints
Battery
Voltage w/o
Surface
Charge
Predicted
Voltage
Under Load
Power
Supply
Voltage/
Battery
Impedance
Cabinet
Temperature
Phase Fault
Detected
Current Level
(Amps) [Sw.
1, 2]
Ground Fault
Detected
Current Level
(Amps)
[Sw. 1, 2]
Phase Fault
Duration Time
Threshold
(msec)
[Sw. 1, 2]
Ground Fault
Duration Time
Threshold
(msec)
[Sw. 1, 2]
Phase
Current
Inrush
Restraint
Time (msec)
[Sw. 1, 2]
Ground
Current
Inrush
Restraint
Time (msec)
[Sw. 1, 2]
Phase
Current
Inrush
Restraint
Multiplier
[Sw. 1, 2]
Ground
Current
Inrush
Restraint
Multiplier
[Sw. 1, 2]
Figure 4. LCD screen data page for 5802/5803 controls.

S&C Instruction Sheet 1041-540 13
Installation
The Power Supply/Control I/O (PS/IO) module is a highly efcient, computer-controlled,
uninterrupted power supply system specically designed to meet the specialized power
requirements of automated electric power distribution equipment.
The PS/IO module provides steady-state current flow for switch control operation,
pulsed current flow for communications equipment, and occasional large current surges
for line switch operation. It also provides 12 Vdc, battery charging (24 or 36 Vdc) and other
dc voltages from a single 24- or 36-Vdc source. (This design provides superior battery
lifetime and carryover compared to systems that “center tap” a 24- or 36-Vdc system to
supply their 12-Vdc requirements or that use multiple, non-interchangeable batteries.)
The PS/IO module supplies accurate, temperature-compensated charging voltages,
with current-limiting and other safety mechanisms to maximize battery carryover and
to minimize the possibility of battery off-gassing or explosion. This system meets or
exceeds ANSI surge-withstand and dielectric specifications (including ANSI C62.41
-1992 6KV3KA surge and C37.90a 2.5-kV 125-MHz ring wave and 5-kV “Fast Transient”
waveform specifications).
The power-management system consists of the PS/IO module, and a Hawker/Gates
24- Vdc or 36-Vdc battery. When ac power is available, the PS/IO converts the ac power to
dc, and then uses the dc power to run the switch control, charge the battery, and operate
the communications equipment. It draws on the battery only for the current needed to
operate the switch. When external ac power is not available, the PS/IO uses power from
the sensors instead (if applicable). When neither external ac power nor power from the
sensors is available, the PS/IO draws on the stored battery power for all switch control
operations.
Users can monitor and control the power management system from the switch control
faceplate, with the IntelliLink software, or from a SCADA master station.
Power Supply/ Control
I/O Module
The PS/IO module LEDs provide information about the state of the battery and ac power.
Ac On
This LED comes becomes lit when the switch control has a power source (either external
AC or sensor power). It is located on the middle left of the module.
NOTE: The Ac Line fuse is not intended for field replacement. Replacing a blown fuse
may result in further damage.
CHG ON
This LED becomes lit when the battery charger is connected to the battery, the AC
ON LED is lit, and the battery charger and battery are within the proper voltage range
(20- 30.5 Volts for 24-Vdc batteries, 30-45.75 Volts for 36-Vdc batteries). It is located on
the middle left of the module.
BAT ON
This LED becomes lit when the battery is connected to the 24- or 36-Vdc power supply
bus. It is located on the bottom right of the module.
ANALOG PWR
This LED becomes lit when power is being supplied to the analog processors. It is located
on the top middle of the module.
Battery Management
The purpose of the S&C battery-management system is to ensure the switch control
can operate the line switch with the available battery capacity and to provide advanced
warning of a weak battery. Battery capacity is affected by several variables, including
age, temperature, load cycling, and loading.
Power Supply/Control
I/O Module LEDs

14 S&C Instruction Sheet 1041-540
Installation
The switch control continuously monitors the battery voltage. In addition, it tests the
battery at regular, scheduled intervals. The interval depends on the power conditions:
• During battery discharge, the test is run hourly.
• After a power outage, the test is run every two hours for 24 hours to monitor the bat-
tery status while the battery is recharged.
• After 24 hours of continuous operation on ac power (or power from the sensors, if
applicable), the test is run once a day.
Note: The BATTERY TEST/LAMP TEST switch or a SCADA command can be used to
manually test the battery at any time.
During the battery test, the switch control applies various loads to the battery to
determine how it will perform under load. These tests include:
Actual battery voltage. Determines the true open circuit battery voltage
Battery impedance. Determines the internal impedance of the battery
Calculated voltage under load. Determines the minimum voltage predicted during
switch operation (When the switch control is operating on battery power, the control
reevaluates this “calculated voltage under load” continuously. Otherwise, it evaluates
this value only during battery test cycles.)
Based on the results of the above monitoring and tests, the switch control may take
the following actions:
• If the battery “calculated voltage under load” drops below the Battery Low value,
the switch control displays a “Battery Low” message and turns on the faceplate
BATTERY LOW LED. (At voltages below this value, switch operation is still possible
but only for a limited time.)
• If the “calculated voltage under load” drops below the Battery Bad value, the
switch control sets the Battery Bad status indication for the SCADA operator and
displays a “Battery Bad” message on certain IntelliLink software screens. (The
switch will not reliably operate at voltages below this value.)
• If the battery steady-state voltage drops below 22 Volts (for a 24-Vdc battery) or 33
volts (for a 36-Vdc battery) while the switch control is operating on battery power,
the switch control automatically disconnects all loads to prevent deep discharge.
Power is restored to loads once ac power (or sensor power, if applicable) is restored
or the battery is replaced.
• If the battery voltage falls outside the proper range (20-30.5 Volts for 24-Vdc batter-
ies, 30-45.75 Volts for 36-Vdc batteries) while the switch control is operating on ac
power (or sensor power, if applicable), the switch control disconnects the battery
from the system and turns off the BAT ON LED on the Power Supply/Control I/O
module.
Because the battery is used for the wetting voltage of certain switch status contacts,
disconnecting the battery will also generate alarms.
Based on field experience, a weak battery may fail the battery test in very cold tem-
peratures but pass when the ambient temperature rises. If a Battery Low or Battery
Bad alarm occurs, schedule the battery for replacement. In warmer climates or seasons,
if a battery test indicates a Battery Low condition, the battery may last 1-2 weeks longer.

S&C Instruction Sheet 1041-540 15
Installation
Typical battery life for 5800 Series controls is ve to seven years. The battery should be
replaced when capacity is reduced to 80% of capacity when new. Increased temperature
accelerates battery aging, so installations in warmer climates will have a shorter battery
life.
5800 Series controls automatically test and record battery capacity, and the only
routine maintenance they require is battery replacement. Yearly site inspection of the
BATTERY LOW LED and the physical condition of the battery is recommended for
noncommunicating controls. More frequent inspection should be scheduled for older
batteries. Batteries should be replaced every five years. Communicating controls report
“Battery Low” to SCADA when capacity is near 80%, and the battery will still power the
switch operator.
The following suggestions can help with battery maintenance:
• Store batteries at room temperature. To maximize battery life, store all gel-cell bat-
teries at or below room temperature. Once in service, the battery will probably be
exposed to higher temperatures that will affect its life. However, proper storage can
avoid accelerating the process.
• Keep stored batteries charged. Gel-cell batteries are generally designed with a 6-month
maximum shelf life. This means they can survive sitting on the shelf without being
recharged and without incurring substantial damage for 6 months. If having to store
them longer, it is critical to recharge them periodically. If recharging them every month,
they can sit on the shelf for years without signicant damage. To recharge a battery,
connect it to a switch control or to an independent battery charger. See Table 8 in S&C
Specication Bulletin 1045-33 for available charger options.
• The best approach to storing batteries is to maintain the smallest inventory possible.
Make sure a procedure is in place for rotating the inventory, removing the oldest bat-
teries rst.
• Use batteries known to be good. Do not install used batteries in battery-backed
equipment unless they have been properly tested. The cost of a service call to replace a
bad battery is usually higher than the cost of a new battery. Although a battery might be
good enough to provide temporary standby power, the line switch has a brief but large
power requirement that may exceed a weak battery’s ability to deliver charge rapidly.
• Avoid installing the enclosure in a sunny location. If at all possible, install the switch
control enclosure in a shady area. Because batteries do not do as well in warm/hot
environments, do everything possible to minimize the peak operating temperature.
Battery Care and
Maintenance
5800 Series switch controls are entirely software-driven. Each switch control is shipped
with control and IntelliLink software.
The Control Software
The control software is preloaded into the switch control in the factory. This software
manages the minute-by-minute functioning of the switch control. It continually monitors:
• Voltage and current on the feeder
• Incoming SCADA commands
• The position of the faceplate switches
• The condition of the battery
• Ambient air temperature inside the control enclosure
• The internal switch control clock/calendar
• The software setpoint values
• Fault and voltage loss information already stored in the control
• Various other setpoints and data values as needed
Switch Control
Software

16 S&C Instruction Sheet 1041-540
Installation
Based on this information, the Control software decides how to respond to a possible
overcurrent fault, a change in voltage, a command from the faceplate or SCADA master
station, and other conditions.
The control software, the setpoint values, and historical data are all stored in non-volatile
switch control memory. This memory survives power interruptions, including complete
loss of the battery system.
Battery Backed Non-volatile SRAM
The memory and perpetual calender are implemented with battery-backed non-volatile
SRAM with a 10-year battery life in the non-powered state; this is no battery draw when
control power is connected. The real time clock IC is battery-backed as well which
counts seconds, minutes, hours, days, day of the week, date, month and year with leap
year compensation up to 2100.
The IntelliLink software
The IntelliLink software is supplied on the Setup disk and runs on IBM/PC-compatible
computers. This software enables communication with the control software while at the
switch control site. Using the IntelliLink software, users can:
• Enter installation-dependent operating parameters (setpoints), such as a network
address, automatic operation features, etc.
• Monitor real-time data, such as the present line voltage and current
• Examine the performance and operating history of an installed switch control
• Transfer all conguration, operating, and historical data from the switch control to
a “report” le on your computer
• Download new control software into the switch control
• Troubleshoot assorted types of switch control installation problems
SCADA Communications Equipment
5800 Series switch controls include two remote communications access ports. When
combined with suitable communications equipment and protocols, this permits users
to remotely monitor, control, and change setpoints for the switch control installation.
S&C supports the 5800 Series controls with a variety of communications hardware
options and software protocols, including:
• DNP 3.0 (default protocol)
• PG&E SCADA (Cooper 2179)
• Landis & Gyr Telegyr 8979
• Schlumberger’s UtiliNet®
• Schlumberger’s CellNet®
• Cellular telephones
• Fiber optics
• Phone lines
The communications hardware (radio, modem, etc.) is mounted inside the switch
control enclosure on the universal communications mounting plate on the back of the
faceplate. This eliminates clutter and provides a higher level of reliability for the overall
installation.
For more details, see the manufacturer’s documentation or contact S&C.

S&C Instruction Sheet 1041-540 17
Switch Control Operation
The switch control includes separate electronic paths to accommodate the different
requirements for peak versus normal operating current measurements. For normal
operating current measurements, full scale is 800 amps RMS. For peak measurements,
full scale varies with the switch type. For S&C switches, the value is approximately
4000 amps RMS and depends on the switch model. See Table 1 on page 18 for details.
Peak detection focuses on speed, with several samplings taken for each sinusoidal
peak and instantaneous analysis of the incoming data. Measurement of normal operating
current is slower and includes a finer degree of accuracy.
The switch control reports current, voltage, and phase-related data in units of amperes,
volts, and kvars. The rated accuracy of these measurements is based on the combined
accuracy of all the control components (exclusive of the sensor and sensor cable but
inclusive of all sensor conditioning components). The switch control uses the switch
calibration data and the phase angle offset values to correct all ac waveform data sampled
from the switch sensors.
Using the jumpers that come with the switch control, users can configure it in the field
for wye or delta distribution line applications. Based on the selected configuration and
certain setpoint values, the control normalizes voltages to nominal 120- or 240-Vac values.
Signal Processing
The switch control uses RMS detectors (with accuracy to the 100th 60 Hz harmonic) to
produce true RMS amplitude data for current, neutral current, and voltage waveforms.
This is particularly important when measuring neutral current because the effects of
harmonic distortion of any single phase are multiplied in the summing of the phases.
Because there is some response latency associated with this circuitry, voltage and
current changes that occur within a few tenths of a second are sensed as a single, steady
value.
For real-time, steady state monitoring and data logging, the switch control collects
data at 0.2-second intervals. It then averages eight samples and reports the “1.6-second
averaged” value. This results in a net response time of 1.6 seconds.
The switch control uses these “1.6-second averaged” values for the real-time display,
reporting via SCADA communication, and data logging. Daily high and low values are
kept for the current day and the preceding 7 days.
Waveform Analysis for Power System with Delta-Connected Customer
Transformers
The switch control treats power systems with delta-connected customer transformers
as a special case.
When the line switch has three voltage sensors and the Sensor Conditioning module
is configured with a “delta” jumper, the switch control reproduces the delta voltage wave-
form before any transducer functions are performed. This is useful for comparing the
measured voltage against that seen by customers served by phase-to-phase connected
transformers. For S&C voltage sensors, this configuration is necessary for accurate
phase-to-phase voltage measurements because these sensors measure phase-to-neutral
voltages even in a delta distribution system.
For switches with one voltage transformer for voltage sensing and control power and
three CVMI current sensors, the Sensor Conditioning module must always be configured
with a “wye” jumper. Voltage sensing and reporting are determined by the way the voltage
transformer is connected: phase to phase (delta) or phase to neutral (wye).
RMS Ac Waveform
Analysis
This section explains how the switch control components work together to detect and
respond to “faults” and voltage outages.

18 S&C Instruction Sheet 1041-540
Switch Control Operation
The 5800 Series control software supports 15-kV, 25-kV, and 34.5-kV S&C switches.
The nominal voltage sensor ratios for the line switch(es), with corresponding maximum
voltage levels, are shown in the Table 1.
Table 1. Maximum Voltage Levels Supported in S&C Switches
S&C Switch Model S&C Nominal Voltage
Sensor Ratio
Maximum Phase-to-
Phase Voltage (Delta
Jumper)
Maximum Phase-to-
Ground Voltage (Wye
Jumper)
15 kV 1386:1 20.0 kV 15.0 kV
25 kV 2440:1 27.3 kV 20.4 kV
34.5 kV 3389:1 38.7 kV 29.0 kV
The Maximum Voltage levels represent the highest voltage measurements supported
by the control software. The maximum voltage levels in Table 1 are based on nominal
sensor ratios. Actual maximum voltages may vary slightly based on the S&C factory-
supplied sensor calibration data (supplied with each switch). (For information on the
physical and electrical specifications for each switch, see the applicable S&C literature.
If support for higher voltage levels is required, contact S&C.)
The third column in Table 1 shows the maximum voltage levels supported for installa-
tions configured for phase-to-phase (delta) voltage reporting. These installations require
the presence of a delta-configured Sensor Conditioning module.
The fourth column in Table 1 shows the maximum voltage levels supported for installa-
tions configured for phase-to-ground (wye) voltage reporting. These installations require
the presence of a wye-configured Sensor Conditioning module.
Accurate voltage reporting requires proper configuration of the setpoints. This includes
entering the actual sensor ratios (as supplied by S&C) for each sensor. It also includes
selection of a voltage-reporting method (phase to phase or phase to neutral) consistent
with customer transformers on the feeder and their associated step-down ratios.
Voltage Sensing for
S&C Switches
The switch control uses a highly accurate, proprietary, zero-crossing detection scheme
(that is not tricked by multiple zero-crossings of noisy or harmonic-contaminated signals)
to measure the phase angles between the voltage and current waveforms on each phase.
The switch control samples the phase angle reading every 0.2 seconds and then
averages eight samples and reports the “1.6-second averaged” value. Phase-angle
measurements are on a 0-360 degree range.
As part of the switch control setup, users can enter Phase Angle Offset values to
compensate for both sensor-dependent and installation-dependent phase-angle charac-
teristics.
Phase Angle
Measurements
Overcurrent faults are measured with a combination of peak current detection hardware
for phase faults and true RMS amplitude detection hardware for harmonic-sensitive,
neutral current faults.
To determine whether an overcurrent fault exists, the switch control compares the
sensed current to setpoint values for current level and fault duration. The Current Level
setpoint value can be specified in 10-amp RMS increments for phase faults and one-amp
RMS increments for ground faults.
The Fault Duration Time Threshold value can be specified in 6.25-millisecond
(approximately ⅓-cycle) increments for phase faults and 50-millisecond increments for
ground faults.
This scheme allows the software to measure fault currents with a scaling appropriate
to the higher amplitude signals encountered with faults and to detect the peaks of narrow
spikes caused by CT saturation that trick many digital sampling schemes.
Overcurrent Fault
& Voltage Loss
Detection

S&C Instruction Sheet 1041-540 19
Switch Control Operation
Phase Overcurrent Detection
Phase overcurrent conditions are sensed using a combination of analog and digital
techniques. The switch control provides fault detection with a resolution of 1/3-cycle
and peak values of approximately 4000 amps RMS. Overcurrent measurements are
accurate to 0.5% of full scale, excluding sensors. (For information about scaling beyond
4000 amps, contact S&C.)
Note: In the 5802/5803 controls, the control monitors each feeder (or branch) indepen-
dently and responds to changes on that feeder regardless of the condition of the other
pad-mounted switch and feeder.
To detect phase overcurrent faults:
STEP 1. The switch control monitors the current on all three phases and compares it to
the Phase Fault Detection Current Level setpoint.
STEP 2. When at least one peak overcurrent sample is above the setpoint every
18.75 milliseconds (a window of time slightly longer than one cycle), the switch
control registers an overcurrent condition (a potential, or pending, “fault”)
on that phase.
STEP 3. Once the overcurrent condition is registered, the switch control starts the
Phase Fault Duration Time Threshold timer.
STEP 4. If the overcurrent condition is present continuously for the duration of the
timer, the switch control labels it a “phase overcurrent fault” and responds
accordingly. If during any 18.75-millisecond window overcurrent is not
detected, the switch control considers the “fault” (or the overcurrent condition)
to be no longer present and takes appropriate action.
STEP 5. When a recognized “phase overcurrent fault” ends (after the timer has expired),
the software records the maximum RMS current measured during the fault
and the fault duration. Any fault lasting longer than 6.82 minutes is recorded as
6.82 minutes (409.6 seconds).
The switch control hardware measures ground current as an analog vector sum of the
three individually sensed phase currents. This analog signal is presented to a true RMS-
detecting circuit, yielding a very accurate, harmonic-independent measure of the true
RMS current integrated over several cycles. Because of this multi-cycle integration,
there is some delay in the response time through the hardware. This delay is inversely
proportional to the magnitude of the change in ground current. The larger the change
in ground current, the faster the circuit responds. The net result is very similar to the
time-current characteristics of a protective relay.
The control software samples the true RMS detection hardware on 50-millisecond
intervals. On each interval, the current is compared to the Ground Fault Detection
Current Level setpoint. If the current exceeds the setpoint and this condition persists
continuously for a period of time specified by the Ground Fault Duration Time Thresh-
old setpoint, an Overcurrent Fault condition is indicated and appropriate action taken.
Because the registration of Overcurrent Fault conditions is affected by the rela-
tionship between the minimum fault current detection level and RMS detector rise and
fall times, a family of time-current characteristic curves is generated. See the graph
under the “Ground Fault Detection Current Level (RMS Amps)” section in Instruction
Sheet 1041-530.” Each of these curves corresponds to a single Ground Fault Detection
Current Level setting.
The points on each curve represent the minimum amount of time the ground current
must be present to register a fault. For example, when the Ground Fault Detection
Current Level setting is set to 150 amps, a 500-amp ground current must be present for
approximately 42 milliseconds before the switch control registers a fault.
Ground Overcurrent
Detection

20 S&C Instruction Sheet 1041-540
Switch Control Operation
The switch control keeps a record of each recognized event, the assumed cause of the
event, and any action taken. The switch control logs all events, regardless of the position
of the automatic operation ENABLE/DISABLE switch and REMOTE/LOCAL switch.
The switch control maintains three separate, chronological logs of event data. Infor-
mation is stored in these logs in a circular fashion; the newest entry always overwrites
the oldest. (The switch control logs each event with millisecond timestamping and 6.25
millisecond resolution.)
The first log is a “sequence of events” buffer. Each record in this log represents one
fault event (for example, an Overcurrent condition followed by voltage loss) and/or a
fault-related action taken by the switch control (for example, the line switch opened
because of a Phase Imbalance condition). The information in this log is displayed on the
IntelliLink software OVERCURRENT FAULT:Fault Events screen and the LCD screen.
Overcurrent Data
Logging
The switch control checks the voltage on all three phases at 50-millisecond intervals.
Any voltage drop below the Loss of Voltage Threshold setpoint is considered a voltage
outage.
Voltage Loss
Detection
The Inrush Restraint feature prevents phase or ground overcurrent conditions, which
can occur during outage restoration (hot or cold load pickup) from falsely indicating a
“fault.” It also applies when the switch is closed from the faceplate or via SCADA while
power is present. The Current Inrush Restraint Multiplier feature enables the switch
control to differentiate between moderate overcurrents (caused by cold load pickup) and
large overcurrents (caused by a fault condition) during the Inrush Restraint period. See
S&C Instruction Sheet 1041-572 for additional information.
The Inrush Restraint feature is applied as follows:
(a) During a voltage outage, the switch control continuously monitors the switch
status, the RMS voltage sensors, and the phase overcurrent detectors for any
indication that the outage has ended
(b) When voltage rises above the Loss of Voltage Threshold setpoint on any phase
or overcurrent is detected on any phase, the switch control checks the switch
position
(c) If the switch is closed, the switch control starts the Phase Current Inrush
Restraint timer and the Ground Current Inrush Restraint timer
(d) If both Current Inrush Restraint Multiplier values are set to TimeBlock
mode, the switch control ignores all overcurrent conditions until the Inrush
Restraint timers expire
IfoneorbothCurrentInrush RestraintMultipliervaluesaresettosomething
other than Time Block mode, the switch control considers any overcurrent
condition that exceeds the specied multiplier value to be a “fault.” See the “Phase
Overcurrent Detection” and the “Ground Overcurrent Detection” sections on page
19 for details.
(e) After the inrush restraint timers expire, the switch control responds to
overcurrent conditions in the normal manner (See the “Phase Overcurrent
Detection” and the “Ground Overcurrent Detection” sections on page 19 for
details.)
Note: If the “Inrush Restraint” times are set to “0”, no inrush restraint occurs.
Inrush Restraint
The switch control’s response to an overcurrent condition or voltage loss depends on
the settings in effect when the event occurs. For example, the values selected for the
Fault Detection Current Level and Fault Duration Time Threshold setpoints
determine whether the switch control recognizes an overcurrent event as a “fault.” The
Automatic Operation features enabled, and the position of the faceplate automatic
operation ENABLE/DISABLE switch, determine what the switch control will do when a
recognized “fault” occurs.
Overcurrent and
Voltage Loss Events
Other manuals for 5800 Series
2
Table of contents
Other S&C Control Unit manuals
Popular Control Unit manuals by other brands

Genebre
Genebre 5985 Installation, operation and maintenance manual
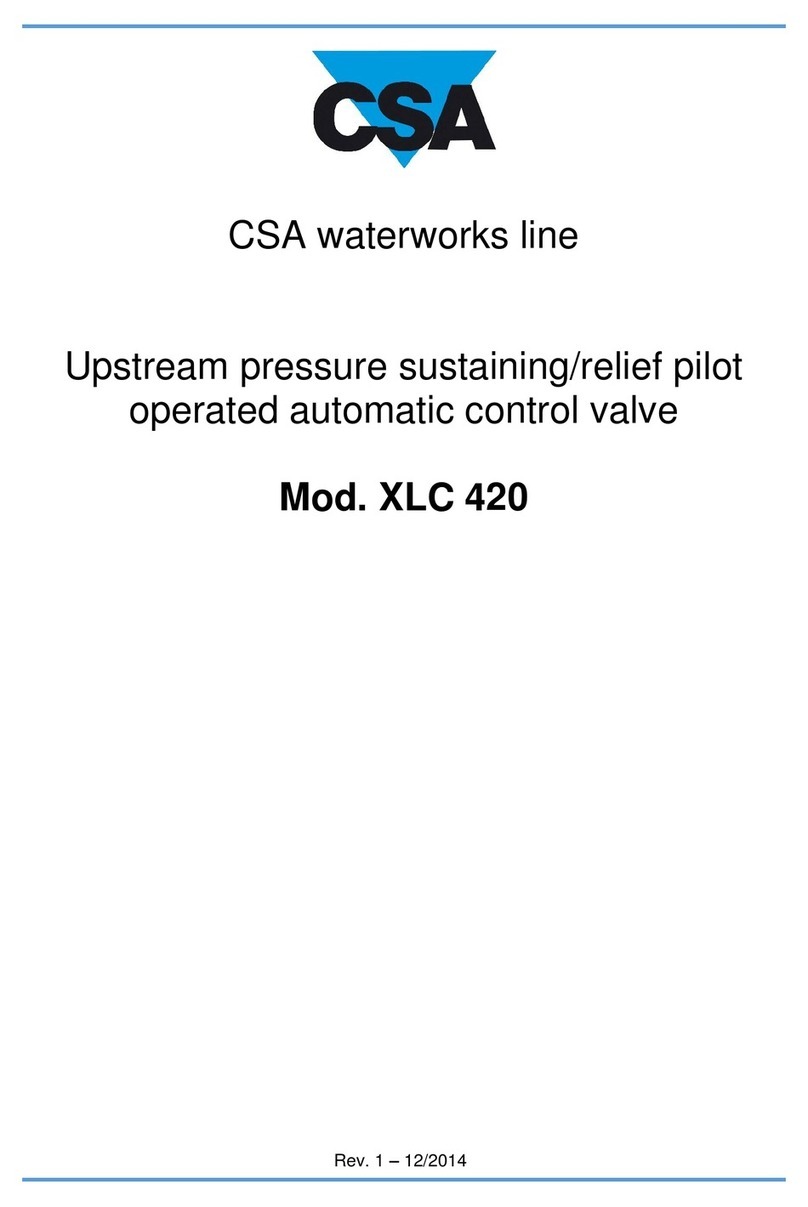
CSA
CSA XLC 420 manual
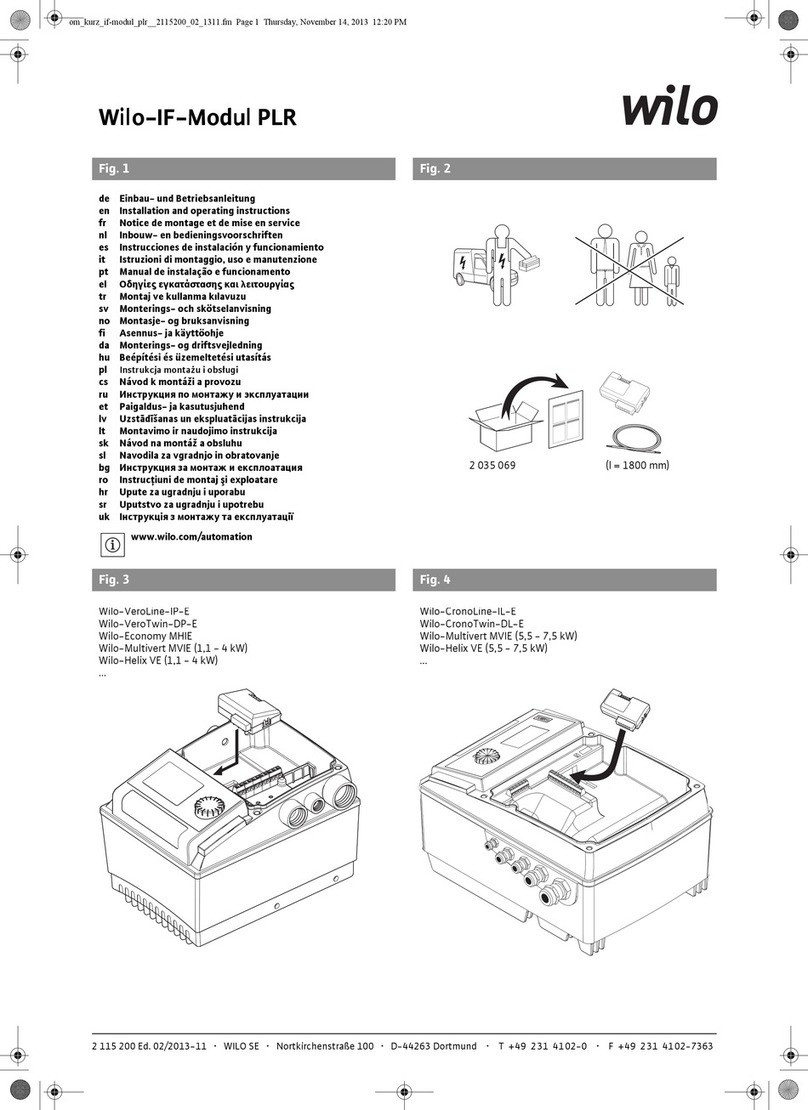
Wilo
Wilo PLR Installation and operating instructions
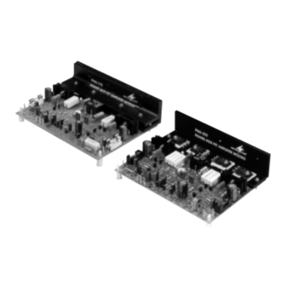
Monacor
Monacor PMA-102 Mounting instructions

Allen-Bradley
Allen-Bradley 1762-OF4 installation instructions

American Standard
American Standard R127 installation instructions