SEA SETRONIK 1 Restyling User manual

Encoder on
car roof
Cabinet at landing
(MRL)
Machine room
cabinet (MR)
Cabinet in the shaft and
at landing (MRL)
USER MANUAL
Control panel
SETRONIK 1 Restyling
SEA SYSTEMS S.r.l
Control panels, push-buttons panels and prewired systems for lifts
Via an Carlo 13 - 20010 Bareggio - Milano - ITALY
Tel: +39 02 90 36 34 99 - Fax: +39 02 90 36 35 00
Internet: www.seasystems.it - e-mail: [email protected]
TK1R-EN-95-0-A
rev0
06/04/2022

SEA SYSTEMS
INSTALLATION AND USE
STK1R control panels Setronik1 Restyling)
TK1R-EN-95-0-A
rev0
06/04/2022
INDEX
1. INTRODUCTION AND FIELD OF APPLICATION......................................5
1.1. YMBOL U ED IN THI MANUAL.................................................................................................................. 5
2. SAFETY PRECAUTIONS...........................................................................6
3. FUNCTIONAL CHARACTERISTICS..........................................................7
4. TECHNICAL CHARACTERISTICS............................................................7
5. INSTALLATION AND TESTS.....................................................................8
5.1. PRELIMINARY OPERATION .......................................................................................................................... 8
5.2. FIXING OF THE CONTROL PANEL................................................................................................................... 9
5.3. FA TENING AND CONNECTING DEVICE IN THE HAFT...................................................................................9
5.4. ATTACHING THE ‘CONNECTION BOX’ TO THE CAR ROOF..................................................................................9
5.5. ATTACHING AND CONNECTING THE FLEX CABLE IN THE HAFT........................................................................9
5.6. ATTACHING AND CONNECTING THE CAR PO ITION EN OR AND THE RELATIVE MAGNET .............................10
5.7. CONNECTING AND U ING OF THE TK2-PM PROGRAMMER.........................................................................16
5.8. PROCEDURE FOR Y TEM TART-UP.......................................................................................................... 16
5.9. IN ULATION TE T .................................................................................................................................... 17
5.10. TE T PROCEDURE OF THE UCM PROTECTION Y TEM, FOR TK1R-A3 CONTROL PANEL ........................18
5.11. TE T OF THE AFETY CIRCUIT C 4.......................................................................................................... 21
5.12. TE T OF THE LIMIT WITCHE .................................................................................................................. 22
5.13. TE T OF THE MOTOR RUN TIME LIMITER.................................................................................................... 22
5.14. TE T OF THE CAN BU ........................................................................................................................... 23
5.15. TE T OF THE CAN BU TERMINATION ..................................................................................................... 23
6. PROGRAMMING......................................................................................24
LEGEND........................................................................................................................................................... 24
0.00 LIFT TATE............................................................................................................................................... 25
0.01 ACTIVE ALARM CAU ING OUT OF ERVICE................................................................................................26
0.02 ALARM LOG............................................................................................................................................ 26
0.03 ALARM RE ET / ALARM LOG ERA ING........................................................................................................ 27
0.04 TOTAL RUN COUNT................................................................................................................................. 27
0.05 UPWARD AND DOWNWARD RUN COUNT ....................................................................................................28
0.06 EMERGENCY RUN COUNT........................................................................................................................ 28
0.07 RE-LEVELLING COUNT ............................................................................................................................ 28
0.08 DOOR TATE AND COMMAND ................................................................................................................... 29
0.09 CAR MOVEMENT COMMAND ..................................................................................................................... 30
0.10 | 0.11 ETTING THE MAINTAINER PA WORD..............................................................................................31
0.12 TORING THE PARAMETER ...................................................................................................................... 31
0.13 OPERATING TIME OF TK1R BOARD.........................................................................................................32
0.14 | 0.15 OFTWARE RELEA E...................................................................................................................... 32
0.16 LOADING A PARAMETER ET..................................................................................................................... 33
0.17 TORE A PARAMETER ET / TRAN FER PARAMETER ET FROM AND TO AN U B PEN DRIVE........................33
0.18 TK1R BOARD TEMPERATURE.................................................................................................................. 34
0.19 BATTERY VOLTAGE................................................................................................................................... 34
0.20 TK1R BOARD ERIAL NUMBER................................................................................................................ 34
0.21 RE ERVED PARAMETER............................................................................................................................ 34
0.22 | 0.23 | 0.24 UPDATING TK1R BOARD OFTWARE...................................................................................35
0.25 | 0.26 | 0.27 | 0.28 | 0.29 | 0.30 RE ERVED PARAMETER .........................................................................36
© 2022 Sea Systems Page 2 of 113

SEA SYSTEMS
INSTALLATION AND USE
STK1R control panels Setronik1 Restyling)
TK1R-EN-95-0-A
rev0
06/04/2022
0.31 CAB01 BOARD ETTING ......................................................................................................................... 36
0.32 RE ERVED PARAMETER............................................................................................................................ 36
0.33 M ENDING......................................................................................................................................... 37
0.34 TATE OF OME VIRTUAL INPUT DEALING WITH THE AFETY CHAIN............................................................37
0.35 W1 PU H-BUTTON FUNCTION – ALL LED IGNALLING MODE...................................................................38
0.36 HAFT EN OR TATE............................................................................................................................ 38
0.37 TATE OF OME VIRTUAL INPUT DEALING WITH THE DOOR .......................................................................39
0.38 | 0.39 | 0.40 RE ERVED PARAMETER ......................................................................................................39
0.41 COUNTED RANDOM AUTOMATIC CALL .......................................................................................................39
1.00 PROGRAMMING THE DRIVER, OPERATION, HAFT EN OR .........................................................................40
1.01 PROGRAMMING THE NUMBER OF TOP .................................................................................................... 41
1.02 PROGRAMMING THE MAIN FLOOR AND THE PARKING FLOOR........................................................................41
1.03 DE IGNATED FLOOR IN CA E OF FIRE / FIREFIGHTER ACCE FLOOR..........................................................41
1.04 OTHER ETTING FOR EN81-72 / EN81-73 OPERATION............................................................................42
1.05 | 1.06 CAR DOOR TYPE............................................................................................................................ 43
1.07 RE-LEVELLING / EARLY DOOR OPENING / ALARM 20.................................................................................46
1.08 IN PECTION OPERATION PEED AND TOP / REDUCED HEADROOM............................................................46
1.09 IN-U E IGNALLING, IN-CAR PRE ENCE EN OR, GONG, RETRACTABLE CAM................................................48
1.10 CAR PO ITION IGNAL ............................................................................................................................ 49
1.11 CAR PO ITION / CAR PEED IGNALLING DURING RE CUE OPERATION (EEO OR BRAKE RELEA E)................49
1.12 AUTOMATIC EMERGENCY OPERATION / ENABLING OF THE ELECTRICAL EMERGENCY OPERATION IN AB ENCE OF
MAIN .................................................................................................................................................... 50
1.13 CONTROL PANEL OPERATING TEMPERATURE LIMIT ....................................................................................51
1.14 MULTIPLEX (GROUP OF LIFT )................................................................................................................... 51
1.15 UNINTENDED CAR MOVEMENT (UCM) / AFETY GEAR TRIPPING DEVICE......................................................52
1.16 HAFT EN OR BEHAVIOUR / MOTOR RUN TIME LIMITER OPERATING MODE / ENABLING OF AUTOMATIC CALL
WITH HOLD-TO-RUN OPERATION / EXCLU ION OF DOOR PHOTOCELL ACCORDING TO THE CAR PO ITION.....52
1.17 LANDING / CAR CAN BU ERROR LOGGING................................................................................................53
1.18 MAX WITCHING FREQUENCY OF CONTACTOR / CONTACTORLE VVVF...................................................54
1.19 ELECTRICAL LANDING DOOR INTERLOCK / DOOR CLO ING PU H-BUTTON / DOOR TOP / RETRACTABLE CAM
.............................................................................................................................................................. 54
1.20 CAR-LIFT EMAPHORE / CAR-LIFT IDE PHOTOCELL ................................................................................55
1.21 RE ERVED OPERATION ACTIVATION - PRELIMINARY CHECK AT DEPARTURE.................................................55
1.22 “ HABBAT” OPERATION............................................................................................................................. 56
1.23 TANDARD COMPLIANCE – RE ET OF ALARM 53 (MAINTENANCE FROM THE PIT) – COMMAND ENABLED
WHEN THE DOOR AFETY CONTACT ARE BYPA ED.................................................................................56
1.24 DOOR NOT TO OPEN DURING THE EN81-72 / EN81-73 OPERATION – FUNCTION OF VIRTUAL OUTPUT
VO.58................................................................................................................................................... 57
1.25 MODE OF GENERATION AND DI TRIBUTION OF THE LOCK COMMAND ..........................................................58
1.26 VOICE ANNOUNCER V01 “CHOPIN” – ADVANCED ETTING ....................................................................59
1.27 PERIODIC TE T OF THE 12V BATTERY.......................................................................................................59
1.28 BRAKE CHECK ACCORDING TO UNI 10411-1:2021..................................................................................60
2.XX FLOOR TABLE: ENABLED DOOR , PARKING TYPE, HORT FLOOR AND ELECTIVE DOOR OPENING.................61
3.00 CALL INPUT TATE.................................................................................................................................. 61
3.XX CALL ..................................................................................................................................................... 62
4.XX TIMER .................................................................................................................................................... 64
5.XX INPUT .................................................................................................................................................... 67
6.XX OUTPUT ................................................................................................................................................. 71
7.00 RE ERVED............................................................................................................................................... 74
8.00 ENCODER TYPE / DIRECTION / MULTIPLYING FACTOR...................................................................................74
8.01 | 8.02 RE-LEVELLING DI TANCE (WITH ENCODER)......................................................................................75
8.03 | 8.04 DOOR OPENING DI TANCE (WITH ENCODER)..................................................................................75
8.05 | 8.06 LOWDOWN DI TANCE FOR PRIMARY HIGH PEED (WITH ENCODER)..................................................75
8.07 NUMBER OF PUL E /METER OF THE ENCODER...........................................................................................75
8.08 NUMBER OF IZ1 MAGNET ABOVE R MAGNET (WITH ENCODER).............................................................76
8.09 CAR PEED (WITH ENCODER)................................................................................................................... 76
8.10 CAR PO ITION (WITH ENCODER)............................................................................................................... 77
8.11 | 8.12 | 8.13 RE ERVED........................................................................................................................... 77
8.14 LOWDOWN DI TANCE FOR ECONDARY HIGH PEED.................................................................................78
8.15 RE ERVED............................................................................................................................................... 78
8.16 R MAGNET PO ITION (WITH ENCODER).................................................................................................78
© 2022 Sea Systems Page 3 of 113

SEA SYSTEMS
INSTALLATION AND USE
STK1R control panels Setronik1 Restyling)
TK1R-EN-95-0-A
rev0
06/04/2022
8.17 RD MAGNET PO ITION (WITH ENCODER).................................................................................................78
8.18 AB OLUTE REFERENCE PO ITION (WITH ENCODER)....................................................................................78
8.19 ADJU TMENT OF TOP HEIGHT IN AUTOMATIC EMERGENCY (WITH ENCODER)...............................................79
8.20 MINIMUM DI TANCE FOR THE ELECTION OF THE PRIMARY HIGH PEED (WITH ENCODER)............................79
8.21 LENGTH OF THE IZ MAGNET OF THE LOWE T FLOOR (WITH ENCODER).....................................................79
8.22 LENGTH OF THE IZ MAGNET OF THE HIGHE T FLOOR (WITH ENCODER).....................................................79
9.00 ENCODER HAFT LEARNING...................................................................................................................... 80
9.XX FLOOR TABLE: HEIGHT AND TOP DI TANCE (WITH ENCODER)...............................................................81
C.00 VOICE ANNOUNCER V01 “CHOPIN” – BA IC ETTING ...........................................................................82
C.XX VOICE ANNOUNCER V01 “CHOPIN” – ME AGE ELECTION.................................................................82
7. ELECTRONIC BOARDS DESCRIPTION.................................................85
7.1. LEGEND.................................................................................................................................................... 85
7.2. TK1R MOTHERBOARD............................................................................................................................. 86
7.3. A 01 BOARD – BATTERY CHARGER AND EMERGENCY LIGHT........................................................................88
7.4. RCF01 BOARD – UPPLY.......................................................................................................................... 89
7.5. EC02 BOARD – INPUT ANT OUTPUT EXPAN ION......................................................................................90
7.6. ER02 BOARD – RELAY OUTPUT EXPAN ION..............................................................................................92
7.7. BOX05 BOARD – CAR ROOF INPUT AND OUTPUT EXPAN ION...................................................................93
7.8. CAB01 / EC03 BOARD – CAR INPUT AND OUTPUT EXPAN ION.................................................................95
7.9. VEGA LCD581 E DI PLAY – CAR INPUT AND OUTPUT EXPAN ION..........................................................98
7.10. VOICE ANNOUNCER V01 “CHOPIN”.................................................................................................... 101
8. MAINTENANCE......................................................................................105
8.1. BATTERY MAINTENANCE........................................................................................................................... 105
8.2. HAFT EN OR MAINTENANCE (MAGNETIC EN OR AND BELT ENCODER).................................................105
8.3. TK1R BOARD MAINTENANCE................................................................................................................. 106
8.4. C 4 AFETY CIRCUIT MAINTENANCE........................................................................................................ 106
9. ANOMALIES AND SOLUTIONS............................................................107
9.1. LEGEND.................................................................................................................................................. 107
9.2. ALARM CODE DI PLAYED AT PARAMETER 0.01 AND 0.02........................................................................107
9.3. ALARM CODE DI PLAYED AT PARAMETER 9.00 ( HAFT LEARNING WITH ENCODER).....................................112
10. REMOTE CONTROL............................................................................113
11. TECHNICAL SUPPORT.......................................................................113
12. WARRANTY..........................................................................................113
List of changes from “STK1R-EN-94-0-A rev0” to “STK1R-EN-95-0-A rev0”
Page Description
5 Release software
60 New parameter 1.28
108 New alarm 31
© 2022 Sea Systems Page 4 of 113

SEA SYSTEMS
INSTALLATION AND USE
STK1R control panels Setronik1 Restyling)
TK1R-EN-95-0-A
rev0
06/04/2022
1. INTRODUCTION AND FIELD OF APPLICATION
The control panels of the SETR NIK1 Restyling family are specially designed for the control of electric and
hydraulic lifts complying with the lift directive, and lifting platforms complying with the machinery directive.
The TK2-PM programmer allows for setting a secret access code, knowing the conditions the lift is
operating in, which and how many times alarms have occurred, controlling the lift and door motion and
modifying the operating characteristics of the lift itself.
Functional diagnostic is managed by alarm codes that are displayed on the TK2-PM terminal and by LEDs
on the TK1R board.
TK1R Restyling control panels are compliant with the following European directives:
•2014/33/UE (Lift directive), for any embedded safety component
•2014/30/UE (EMC directive)
In addition, according to customers requests, they can be made in compliance with the main
industry standards (EN81-1, EN81-2, EN 81-20 / EN81-50, EN81-21, EN81-70, EN81-72, EN
81-73, etc.)
This manual is valid only for control panels equipped with TK1R main board with software
release (see parameter 0.14.0 and 0.15.0):
1.95.x.0
In case of different software, the reader should get and read the corresponding manual.
1.1. Symbols used in this manual
NOTE
Used to indicate a very important information.
WARNING
Used to indicate an information whose content, if not observed, may cause minor injuries to
persons or damages to the lift plant.
DANGER
Used to indicate that the described operation can cause physical injuries, if not performed in
accordance with safety regulations.
© 2022 Sea Systems Page 5 of 113

SEA SYSTEMS
INSTALLATION AND USE
STK1R control panels Setronik1 Restyling)
TK1R-EN-95-0-A
rev0
06/04/2022
. SAFETY PRECAUTIONS
The control panel and all the other electrical parts supplied by ea ystems have been designed
and built in accordance with the safety and health requirements of the lift and machinery
directives. These precautions are provided to ensure safety and they must be read carefully.
•Installation and maintenance must be carried out in accordance with current regulations, according
to the manufacturer’s instructions, and only by qualified personnel.
•Improper installation or poor maintenance may cause harm to persons, animals or things, for which
the manufacturer can not be held liable.
•Before starting any cleaning or maintenance operation, disconnect the appliance from the mains
supply by turning off the main circuit breaker.
•Always wear the necessary PPE (Personal Protective Equipment).
•Do not wear loose or dangling objects (necklaces, watches, ties...) and keep long hair tied back.
•Do not carry sharp or pointed objects in shirt pockets (such as screwdrivers, scissors...).
•Do not tamper with, damage or hide the warning signs/labels and, in case of deterioration,
immediately request a substitution.
•When lifting heavy loads, use the proper equipment in order to avoid back injuries that could be
caused by manually moving them.
•The documentation provided by ea ystems must be kept by the system administrator, for the
proper and safe installation and maintenance of the lift. Remember that said documentation is
considered to be an integral part of the system and therefore it must not be damaged. If the lift is
sold or transferred to a new owner, always make sure that all of the following documentation is
transferred so that it can be consulted by the new owner and/or installer. ea ystems provides the
following documentation for each plant:
manual for installation and use (this document)
electrical diagrams
setting of the TK1R board parameters.
© 2022 Sea Systems Page 6 of 113

SEA SYSTEMS
INSTALLATION AND USE
STK1R control panels Setronik1 Restyling)
TK1R-EN-95-0-A
rev0
06/04/2022
3. FUNCTIONAL CHARACTERISTICS
LIFT TYPES - Electric : 1-2 peeds, VVVF
- Hydraulic : Direct, tar-delta, oft tarter, oft top, CC, Electronic controlled valves
OPERATIONS - Automatic Push Button
- Hold-to-run in the car and at landings or just in the car
- Collective down or Collective up-down
- Pick up
- Firefighters lifts (EN81-72), behaviour of lifts in case of fire (EN81-73)
- Multiplex (up to eight group elevators)
DOORS CONTROL - Manual, automatic, semi-automatic
- With contactors, limit switches, safety photocell, light curtain
- imultaneous or selective opening
- Open or closed doors parking at landings
- Early doors opening
CAR AND LANDINGS
SIGNALS 24V)
- present / busy / incoming (at landings)
- booking (in the car and at landings)
- display outputs for 1 wire/floor, binary, gray, bcd, 7 segments
- Next direction arrows (in the car / at landings)
- overload
- gong
- Voice synthesis
SHAFT SENSORS - Magnetic sensors (reed switches)
- Belt encoder on the car roof (with self learning)
- Encoder on the motor (with self learning)
EMERGENCIES - alarm, 12vdc emergency light
- Automatic emergencies for hydraulic lifts
- Automatic emergencies for electric lifts with brake release (only for gearless machines) or
with VVVF inverter and batteries
SERIAL / PARALLEL
CONNECTION
- Parallel at landings and in the car
- serial can bus in the car and parallel at landings
- serial can bus in the car and at landings
4. TECHNICAL CHARACTERISTICS
MAINS VOLTAGE From 110 to 440 Vac (single phase and three phases)
SAFETY CHAIN VOLTAGE 48 Vdc or 110 Vac (for lifts)
24 Vdc (for platforms)
CAM, VALVES AND DOOR OPERATORS VOLTAGES On demand
SIGNAL OUTPUTS 24 Vdc, 650mA each, 2A total
(for higher power TK1-RO board is required)
BUSY SIGNAL OUTPUT RELÈ)24 Vdc, 2A
SAFETY CHAIN MONITORING INPUTS Opto-insulated (compliant with EN81-20 EN81-50 EN81-1 EN81-
2)
OPERATING TEMPERATURE -10 ... +65 °C
CONTROL LOGIC With microcontroller
DATA STORAGE Permanent
RECHARGEABLE BATTERIES 12Vdc, 2…7Ah according to needs
© 2022 Sea Systems Page 7 of 113

SEA SYSTEMS
INSTALLATION AND USE
STK1R control panels Setronik1 Restyling)
TK1R-EN-95-0-A
rev0
06/04/2022
5. INSTALLATION AND TESTS
Follow the ‘safety precautions’ listed in chapter 2 during installation.
Under no circumstances EA Y TEM .r.l. will be held liable for any damage arising from
failure to comply with the instructions below, or for any unauthorized modification of the original
equipment.
INSTALLATION MODE
At some point during the installation operations you probably need to move the car frame by
rotating the motor. You can do this without having completed yet the placement and wiring of
shaft sensors and of other devices by using the “installation mode” (see parameter 1.08.0).
5.1. Preliminary operations
Before starting the installation, proceed to the following checks and arrangements.
5.1.1. PREPARING OF THE INSTALLATION SITE
•Check whether there is sufficient lighting in the shaft.
•Check the cleanliness of the shaft and the pit.
•Check whether the grounding system is effective (if not, immediately stop installation until a suitable
grounding system has been provided).
•Make sure that the shaft entrances are properly closed.
•Organise a storage area for materials next to the shaft, which is easily accessible and protected from
any possible adverse weather conditions.
•Make sure that all of the electrical cable ducts and wire passages are free, examinable and well-
finished.
5.1. . UNLOADING AND STORING THE MATERIALS
•Make sure that the TK1R control panel specifications (control panel type, contactors, starter…)
comply with the order specifications listed on the order confirmation.
•Check the bill of materials to verify the availability of all the materials required for installation.
•Check the status of all the components and materials upon delivery to the site, in order to verify any
possible damages which may have occurred during transportation. Immediately notify EA
Y TEM .r.l. in the case of missing or damaged components.
•tore electric and electronic components in their original packaging, in a dry and cool location.
•If for any reason it is not possible to immediately install the unit, periodically check the stored
components to prevent any damages which could be caused by long-term storage in unfavourable
conditions.
© 2022 Sea Systems Page 8 of 113

SEA SYSTEMS
INSTALLATION AND USE
STK1R control panels Setronik1 Restyling)
TK1R-EN-95-0-A
rev0
06/04/2022
5. . Fixing of the control panel
Depending on the version supplied, follow one of the following instructions:
5. .1. CONTROL PANEL IN THE MACHINE ROOM STK1R-MR (FOR ELECTRIC AND HYDRAULIC LIFTS)
Attach the panel in the machine room as close as possible to the motor, using the angle bracket provided.
5. . . CONTROL PANEL AT LANDING STK1R-MRLP (FOR ELECTRIC LIFTS)
Place the control panel as close as possible to the motor.
5. .3. POWER CONTROL PANEL IN THE SHAFT AND MAINTENANCE CONTROL PANEL IN THE DOOR JAMB OF THE UPPERMOST
LANDING STK1R-MRLV (FOR ELECTRIC LIFTS)
1. Attach the ‘main panel’ with the two angle brackets provided in the headroom of the shaft, above the
operator of the uppermost landing, so that it does not interfere with car movement and so that it is
accessible from the car roof.
2. Put the ‘maintenance panel’ in the door jamb on the uppermost landing and attach it according to the
instructions supplied by the door manufacturer.
5.3. Fastening and connecting devices in the shaft
1. Attach the provided cable duct in the shaft near the push-button panel with the provided plugs.
2. Attach the bundle of cables to the cable duct with the provided tie-wraps, starting from the top.
3. Connect the bundle of cables to the control panel as shown on the installation diagram.
4. Connect the various devices for the landings (limit switches, siren, pit emergency stop, landing door
locking devices, car operating panel) as shown on the installation diagram.
5.4. Attaching the ‘connection box’ to the car roof
1. Place the ‘connections box’ on the car roof in such a way that it is easy to connect the flexible cables that
come from the panel, the car operating panel, the door operator and the shaft sensors.
2. Attach the connections box to the car roof with the provided screws.
5.5. Attaching and connecting the flex cable in the shaft
1. Connect the flexible cable (ground side with eyelet terminal) to the connectors of the connection box on
the car roof according to the installation diagram. Attach them to the box using the supplied cable ties.
2. Attach the flexible cable on the car roof and under the car with the supplied cable brackets and plugs.
3. Connect the flexible cable (ground side without eyelet terminal) to the control panel according to the
installation diagram.
4. Attach the provided wedge bracket approximately in the middle of the shaft using the provided plugs.
5. Attach the flexible cables to the wedge bracket at such a point that when the car is at the lowest point,
the flexible cable bag does not touch the bottom of the pit.
© 2022 Sea Systems Page 9 of 113

SEA SYSTEMS
INSTALLATION AND USE
STK1R control panels Setronik1 Restyling)
TK1R-EN-95-0-A
rev0
06/04/2022
EXCESSIVE FLEXIBLE CABLE LENGTH
To solve the problem of excessive length of flexible cables in the pit, move the wedge bracket
upward. Please note that a raising of 1 meter of the wedge bracket corresponds to approximately
0.5 meter of raising of the cable bag under the car.
6. Make sure that the flexible cables are not twisted in the pit. If they are, disconnect the connectors from
the control panel, untwist, and reconnect them.
7. Attach the provided fastening bracket to the wall of the pit at the point where the flexible cables begin to
rise vertically along the shaft.
5.6. Attaching and connecting the car position sensors and the relative magnets
EA Y TEM .r.l. provides various types of shaft sensors depending on the application. Each solution is
outlined by one of the following installation diagrams.
1. Attach the shaft sensors and the relative magnets according to the indications on the relative diagram.
2. Connect the shaft sensors according to the installation diagram.
© 2022 Sea Systems Page 10 of 113

SEA SYSTEMS
INSTALLATION AND USE
STK1R control panels Setronik1 Restyling)
TK1R-EN-95-0-A
rev0
06/04/2022
5.6.1. SHAFT SYSTEM VC01
ystem made up of magnetic sensors (reed switches). Used for electric and hydraulic lifts.
KD, KS = SLOWDOWN DISTANCES
These distances depend on the speed of the lift and the technical characteristics of the motor or
the hydraulic unit installed.
If KD + KS + 5CM > minimum distance between adjacent floors, it is necessary to install the
VEN01 encoder shaft system.
© 2022 Sea Systems Page 11 of 113
FRONT VIEW CAR ROOF VIEW
Sensor Function
I
Monostable reed switch for
ascending stop control and
ascending speed change
control
ID
Monostable reed switch for
descending stop control and
descending speed change
control
R
Bistable reed switch for
speed change control at
uppermost landing
RD
Bistable reed switch for
speed change control at
lowest floor and position reset
IZ1, IZ2
Monostable reed switches for
controlling C 4 safety circuit
(*)
(*) The C 4 safety circuit is necessary in
the following cases:
- amendment A3
- hydraulic/electric relevelling
- early door opening

SEA SYSTEMS
INSTALLATION AND USE
STK1R control panels Setronik1 Restyling)
TK1R-EN-95-0-A
rev0
06/04/2022
5.6. . SHAFT SYSTEM VC0
A system made up of magnetic sensors (reed switches). Used for elevator platforms.
*) The orientation of these magnets depends on the sensor manufacturer / model. The figure shows the correct orientation
with CARL GAVAZZI model FMPB2 sensor.
© 2022 Sea Systems Page 12 of 113
FRONT VIEW CAR ROOF VIEW
Sensor Function
I
Monostable reed switch for
ascending stop control and
ascending speed change
control
ID
Monostable reed switch for
descending stop control and
descending speed change
control
DR Bistable reed switch for
position reset
IZ1
Monostable reed sensor for
controlling the C 4 safety
circuit. (*)
(*) The C 4 safety circuit is necessary in
the following cases:
- amendment A3
- hydraulic/electric relevelling
- early door opening

SEA SYSTEMS
INSTALLATION AND USE
STK1R control panels Setronik1 Restyling)
TK1R-EN-95-0-A
rev0
06/04/2022
5.6.3. SHAFT SYSTEMS VC03
ystem made up of bistable magnetic sensors (reed switches), used for electric lifts without a C 4 safety
circuit.
KD, KS = SLOWDOWN DISTANCES
These distances depend on the speed of the system and the technical characteristics of the
motor or the hydraulic unit installed.
If KD + KS + 5CM > minimum distance between adjacent floors, it is necessary to install the
VEN01 encoder shaft system.
© 2022 Sea Systems Page 13 of 113
FRONT VIEW CAR VIEW VIEW
Adjustable spacings by moving the
magnets)
Zp Door unlocking zone (around
35 cm)
Zf topping zone (around 5 cm)
h10 cm
Sensor Function
I
Bistable reed sensor for
ascending stop control and
ascending speed change
control
ID
Bistable reed sensor for
descending stop control and
descending speed change
control
R
Bistable reed sensor for speed
change control at uppermost
landing
RD
Bistable reed sensor for speed
change control at lowest floor
and position reset

SEA SYSTEMS
INSTALLATION AND USE
STK1R control panels Setronik1 Restyling)
TK1R-EN-95-0-A
rev0
06/04/2022
5.6.4. SHAFT SYSTEM VEN01
ystem made up of magnetic sensors (reed switches) and an encoder on the car or on the motor shaft. Used
for electric/hydraulic lifts and elevator platforms.
KRS, KRD
These distances must be about 10 cm smaller than the slowdown distances set in parameters
8.05.0 and 8.06.0
SELF LEARNING OF FLOOR HEIGHTS AND STOP DISTANCES
For automatic acquisition of floor heights and stop distances, see parameter 9.00.
© 2022 Sea Systems Page 14 of 113
FRONT VIEW CAR ROOF VIEW
Sensor Function
ENC01
Encoder for the control of
stopping and speed change.
The one on the motor can
also be used.
R
Bistable reed switch for
speed change control at
uppermost landing during
acquisition and rephrasing of
the encoder
RD
Bistable reed switch for
speed change control at
lowest landing during
acquisition
IZ1
Monostable reed switch for
controlling C 4 safety circuit
(*)
(*) The C 4 safety circuit is necessary in
the following cases:
- amendment A3
- hydraulic/electric relevelling
- early door opening

SEA SYSTEMS
INSTALLATION AND USE
STK1R control panels Setronik1 Restyling)
TK1R-EN-95-0-A
rev0
06/04/2022
5.6.5. SHAFT SYSTEM VEN01: ATTACHING THE ENC01 ENCODER TO THE CAR ROOF
ENCODER POSITIONING
To avoid excessive noise, it is absolutely necessary to attach the pulleys bracket of the encoder
ECN01 on the arch of the car, and not on covering plates.
ADJUSTING THE TENSION OF THE TOOTHED BELT
Extend the spring until it has a length of 17 cm
© 2022 Sea Systems Page 15 of 113

SEA SYSTEMS
INSTALLATION AND USE
STK1R control panels Setronik1 Restyling)
TK1R-EN-95-0-A
rev0
06/04/2022
5.7. Connecting and using of the STK -PM programmer
Connect the TK2-PM programmer to the FC3 connector on the TK1R board and turn it on (on/off switch).
On the display, one of the following three parameters will appear:
DG0 DG1 DG2 DG3 DG4 DG5 DG6
F 0 0 0 0 0 0 A password as been entered
ee parameters 0.10. 0 e 0.11. 0
0 0 0 X X X X There is no password. XXXX indicates the system
status. ee parameter 0.00
F 0 1 X X X X A standard programmer has been connected to a
customized board. Contact technical assistance
ee chapter 6 for more informations about the TK2-PM programmer and for an exhaustive guide to all
parameters and functions of the TK1R board.
5.8. Procedure for system start-up
To put the lift into normal service follows this steps:
1. et the parameter 1.08.0 to a value different from 4 (i.e remove the installation mode)
2. Make sure that maintenance switch on the car roof is set to NORMAL.
3. Make sure that there are no active alarms (see parameter 0.01). In case of alarms refer to the chapter
“9. Anomalies and olutions”.
4. Cancel any old alarms that were recorded during installation / maintenance operations (see parameter
0.03.0)
© 2022 Sea Systems Page 16 of 113

SEA SYSTEMS
INSTALLATION AND USE
STK1R control panels Setronik1 Restyling)
TK1R-EN-95-0-A
rev0
06/04/2022
5.9. Insulation tests
Before executing the insulation tests required by standards (EN81-20 item 5.10.1.3, EN81-20 item 6.3.2 c),
EN81-1 and EN81-2 item 13.1.3), you have to:
1. place the car out of floors
2. open mains switches
3. check that the automatic switch FA is closed
4. disconnect green-yellow wire from the RCF01 device
5. disconnect from the earth collector on the control panel any other conductor that has not protective function or equipotentiality
function (i.e. which is not green-yellow). Conductors with protective function are, for example, any connection to metal plates,
frames or enclosure of any electrical equipment, while conductors with equipotentiality function are connections to foreign
metallic parts, such as a metal pipe coming from the outside
6. if a VVVF drive or a soft starter device is used, please follow the instruction for insulation tests supplied by the manufacturer.
Generally, a short-circuit between the power terminals (all together) is required. With ZIEHL-ABEGG Zadyn4C VVVF drive,
please disconnect the wiring on the inverter X-ENCO connector (otherwise the "electronic" circuit is not isolated from the
ground)
7. disconnect the phone line from the automatic phone dialer
8. disconnect the control panel from any other control panel belonging to an array of lifts
9. for any device not supplied by EA Y TEM , always follow the manufacturer instructions. For example, if you use VEGA B-
LIFT series 8120 evo light curtain along with the CPB12/24 control unit supplied by 0/24V coming from the TK1R control
panel, you have to disconnect the supply conductors of CBP12/24 (DC IN terminals) before performing any test, because its
electrical circuits are not insulated from the ground (G terminal) and from the metallic frame of the light curtains.
The circuits that must be isolated from each other and the tests to be performed are summarized in the
following tables.
Circuit Signals / terminals
Motive power, motors R, , T, U, V, W, U1, V1, W1, U2, V2, W2
Car light L1, L, N
AC door motor MPA, MPB, MPC, MPD, MPE, MPF
DC door motor +, -, 30, 32, MPA, MPB
afety chain, brake, cam 1 … 10, F1+, F1-, F2+, F2-, PR+, PR-, VALVE
Electronic 0, +24, OCC, F , FD, P 1 … P 6, AL+, AL-, AL, I , ID, R, DR, IZ, CAN+, CAN-, GG, GE,
FF , encoder, inverter commands, sensors, ….
To simplify the measure, it is possible to perform the insulation test of this circuit only on the signal
“0”, which is available, for example, on terminals A0.1, A0.2 of the TK1R board. All other signals
are kept almost at the same voltage (within a few volt) by protective electronic devices provided on
all inputs and outputs.
TO
FROM
Motive power,
Motors
Car light AC door
motor
DC door
motor
Safety chain,
brake, cam
Electronic
Earth XXXXXX
Motive power,
Motors NO OOOOO
Car light -NO OOOO
AC door motor - - NO OOO
DC door motor ---NO O O
Safety chain, brake,
cam ----NO O
Electronic -----NO
Legend
X : test to be performed (500Vcc, Riso >= 1Mohm) O : optional test (not required by standards) NO : test not to be executed
- : test already executed
© 2022 Sea Systems Page 17 of 113

SEA SYSTEMS
INSTALLATION AND USE
STK1R control panels Setronik1 Restyling)
TK1R-EN-95-0-A
rev0
06/04/2022
5.10. Test procedure of the UCM protection system, for STK1R-A3 contro
pane s
TK1R control panels designed for lifts equipped with UCM protection means are called TK1-A3. Below
you will find the relative tests to be performed before putting the lift into service.
5.10.1. STK1R-UCM PROCEDURE – TEST OF INDIVIDUATION AND INTERRUPTION OF UNINTENDED CAR MOVEMENTS WITH
DOORS NOT CLOSED AND LOCKED (WITH THE EXCEPTION OF HYDRAULIC LIFTS WITH MORIS KMI DEVICE, SEE
PARAGRAPH 5.10.7)
1. Call the car to the second floor, leave it with doors closed
2. Open the safety chain just after the door safety contacts (terminal 10 of the CM4 connector, on the
control panel terminals block)
3. Lower the car using the parameter 0.09.0=4
4. When the car exits from the door unlocking zone, lift is put out of service. Check that alarm 88 is
active (see parameter 0.01)
5. Restore the safety chain (undo point 2)
6. Reset the alarm (by using the W1 push-button on the TK1R board or the parameter 0.03)
7. Call the car to the second to last floor, leave it with doors closed
8. Repeat points 2 through 6 (at point 3 raise the car instead of lowering it)
5.10. . STK1R-SMA1 PROCEDURE – TEST OF THE SELF MONITORING FUNCTION OF TWO HYDRAULIC VALVES IN SERIES
1. Turn the power switch off and on again (QFM switch)
2. et the delay before return to the lowest floor to 1 minute (parameter 4.09=0600)
3. Call the car to the second floor
4. When the time 4.09 is elapsed, the car begins to move toward the lowest floor. As soon as it starts,
keep the first hydraulic valve open
5. Two consecutive re-levelling operations will be executed. After the second one, the lift is put out of
service. Check that alarm 81 is active (see parameter 0.01)
6. Reset the alarm (by using the W1 push-button on the TK1R board or the parameter 0.03)
7. Repeats steps 2 through 6 (at step 4 keep open the second hydraulic valve)
8. Turn the power switch off and on again (QFM switch)
For machine-roomless plants, the valve referred to in step 4 must be kept open electrically, temporarily modifying its
wiring. Pay close attention to remove completely these changes at the end of the procedure!
5.10.3. STK1R-SMA PROCEDURE – TEST OF THE SELF MONITORING FUNCTION OF TWO BRAKES
1. Call the car to an intermediate floor
2. Disconnect the wire under the P T terminal on the TK1R board (state sensor of the first brake)
3. Move the car by making a call. Check that the lift is put out of service and that the alarm 81 is active
(see parameter 0.01)
4. Reset the alarm (by using the W1 push-button on the TK1R board or the parameter 0.03)
5. Reconnect the wire under the P T terminal (undo step 2)
6. Disconnect the wire under the TC terminal on the TK1R board (state sensor of the second brake)
7. Move the car by making a call. Check that the lift is put out of service and that the alarm 81 is active
(see parameter 0.01)
8. Reset the alarm (by using the W1 push-button on the TK1R board or the parameter 0.03)
9. Reconnect the wire under the TC terminal (undo step 6)
© 2022 Sea Systems Page 18 of 113

SEA SYSTEMS
INSTALLATION AND USE
STK1R control panels Setronik1 Restyling)
TK1R-EN-95-0-A
rev0
06/04/2022
5.10.4. STK1R-SMA3 PROCEDURE – TEST OF THE SELF MONITORING FUNCTION OF THE BUCHER IVALVE
1. Force to 0 the virtual input VI.13 (for example disconnecting the wire under the MA terminal of the
iValve and connecting it to 0V)
2. Move the car by making a call
3. 1.5s after the car stops at the floor of destination check the activation of alarm 81 (see parameter
0.01), and the consequent out of service state
4. Force to 1 the virtual input VI.13 (same wire of step 1 now connected to +24V)
5. Reset the alarm (by using the W1 push-button on the TK1R board or the parameter 0.03)
6. Move the car by making a call
7. 0.2 seconds after the movement commands are given to the iValve, check the activation of the alarm
81 (see parameter 0.01) and the consequent out of service state
8. Reconnect the wire of point 1 to the MA terminal of the iValve
9. Reset the alarm (by using the W1 push-button on the TK1R board or the parameter 0.03)
5.10.5. STK1R-SMA4 PROCEDURE – TEST OF THE SELF MONITORING FUNCTION OF THE GMV NGV-A3 VALVE
The test of the self monitoring function of the GMV NGV-A3 valve involves simulating the malfunction of the
RUN and READY signals and checking for the activation of the alarm 81. To this end, see the manufacturer's
user manual of the NGV-A3 valve.
© 2022 Sea Systems Page 19 of 113

SEA SYSTEMS
INSTALLATION AND USE
STK1R control panels Setronik1 Restyling)
TK1R-EN-95-0-A
rev0
06/04/2022
5.10.6. STK1R-SMA5 PROCEDURE – TEST OF THE UCM SELF MONITORING FUNCTION OF THE GMV 3010- CH-A3 AND
3100- CH-A3 VALVES
The test the UCM self-monitoring function, as part of the tests and checks to be performed before the lift is
put into service (EN81-20 point 6.3.13), naturally consists of simulating the failure of the e1 and e2 signals
and checking the onset of error 81. It is possible to proceed in this way:
1. With the car stationary, disconnect the e1 sensor. After the time programmed by parameter 4.16 has elapsed,
verify the activation of error 81 and that the lift is put out-of-service
2. Reconnect the e1 sensor
3. Reset the error with the W1 push-button on the TK1R board, or with the programmer (see parameter 0.03)
4. With the car stationary, disconnect the e2 sensor. After the time programmed by parameter 4.16 has elapsed,
verify the activation of error 81 and that the lift is put out-of-service
5. Reconnect the e2 sensor
6. Reset the error with the W1 push-button on the TK1R board, or with the programmer (see parameter 0.03)
7. Make an upward and a downward run and check that e1 and e2 sensors switch during the run as specified
by the manufacturer (see fig. 1), checking the status of the relative LEDs on the TK1R board (in the example
of fig. 2, LEDs X11 and X12).
Figure 1
Figure 2
5.10.7. STK1R-KMI PROCEDURE - TEST OF INDIVIDUATION AND INTERRUPTION OF UNINTENDED CAR MOVEMENTS WITH
DOORS NOT CLOSED AND LOCKED (ONLY FOR HYDRAULIC LIFTS EQUIPPED WITH THE MORIS KMI DEVICE)
Please follow the specific instructions provided by the manufacturer (MORI Italia). ee, for example, the
"Use and maintenance manual" of the KMI device, page 13.
In case of block following a UCM event identified by the KMI device, the TK1R control board signals the
alarm 94.
© 2022 Sea Systems Page 20 of 113
Table of contents
Other SEA Control Panel manuals
Popular Control Panel manuals by other brands
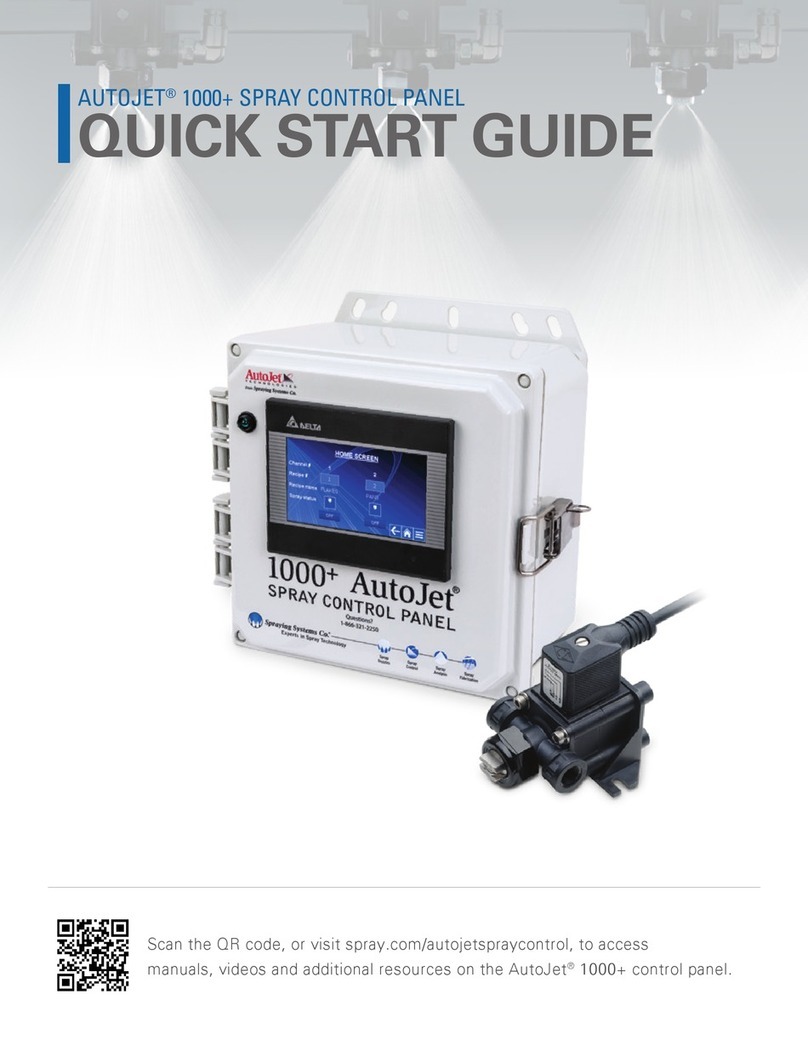
Spraying Systems
Spraying Systems AutoJet 1000+ quick start guide
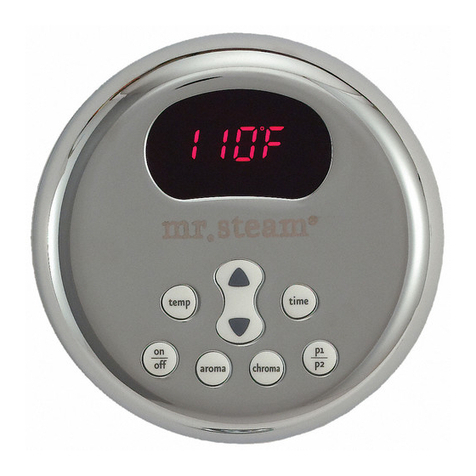
mr. steam
mr. steam TEMPO/PLUS owner's manual

Paradox
Paradox Digiplex DGP-848 Reference and installation manual
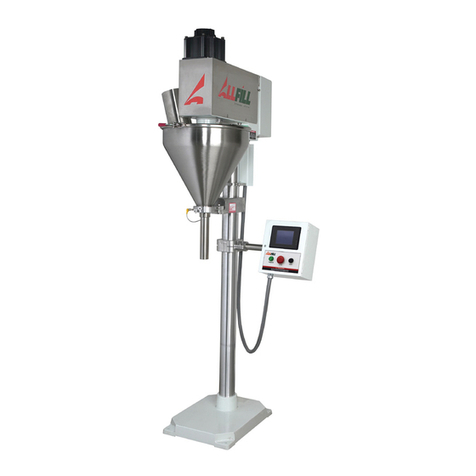
ALL-FILL
ALL-FILL B-SV-600 user manual
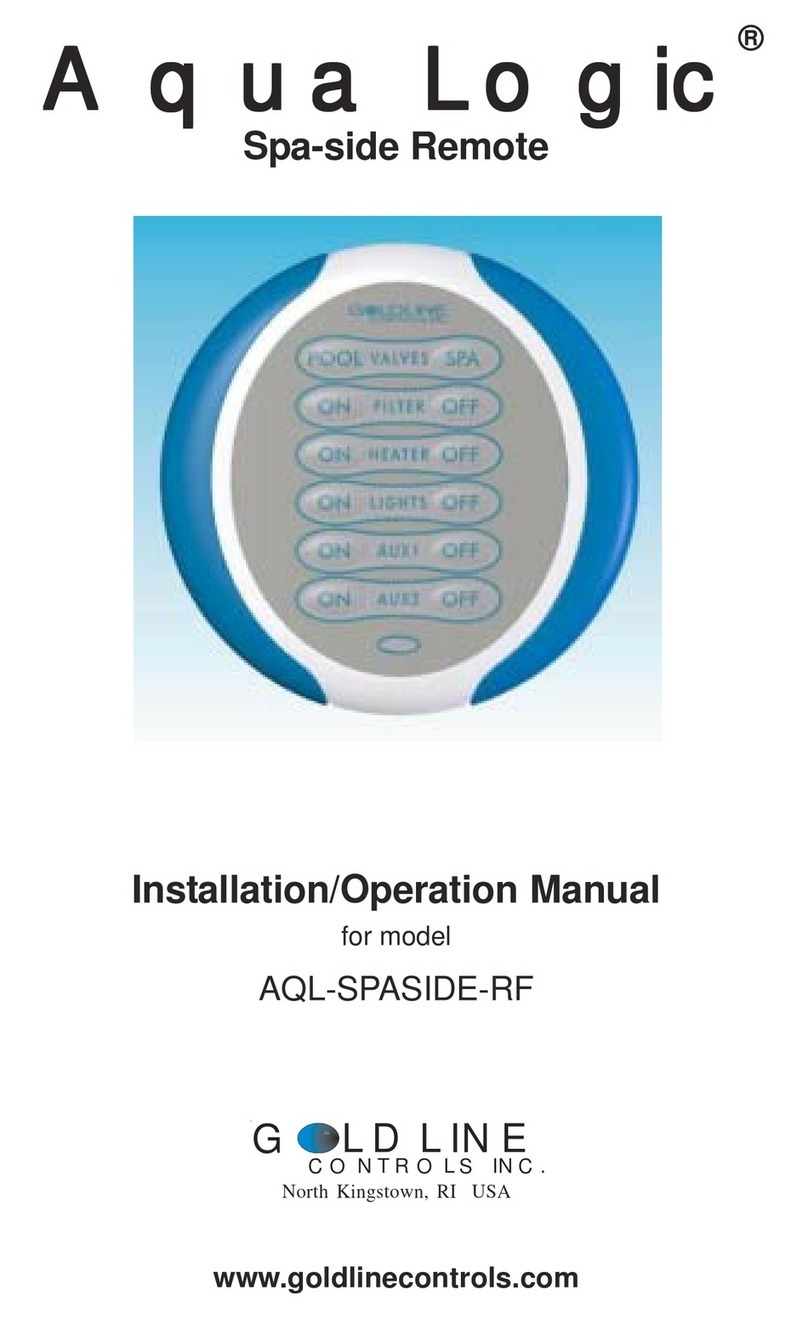
Goldline
Goldline AQL-SPASIDE-RF Installation and operation manual
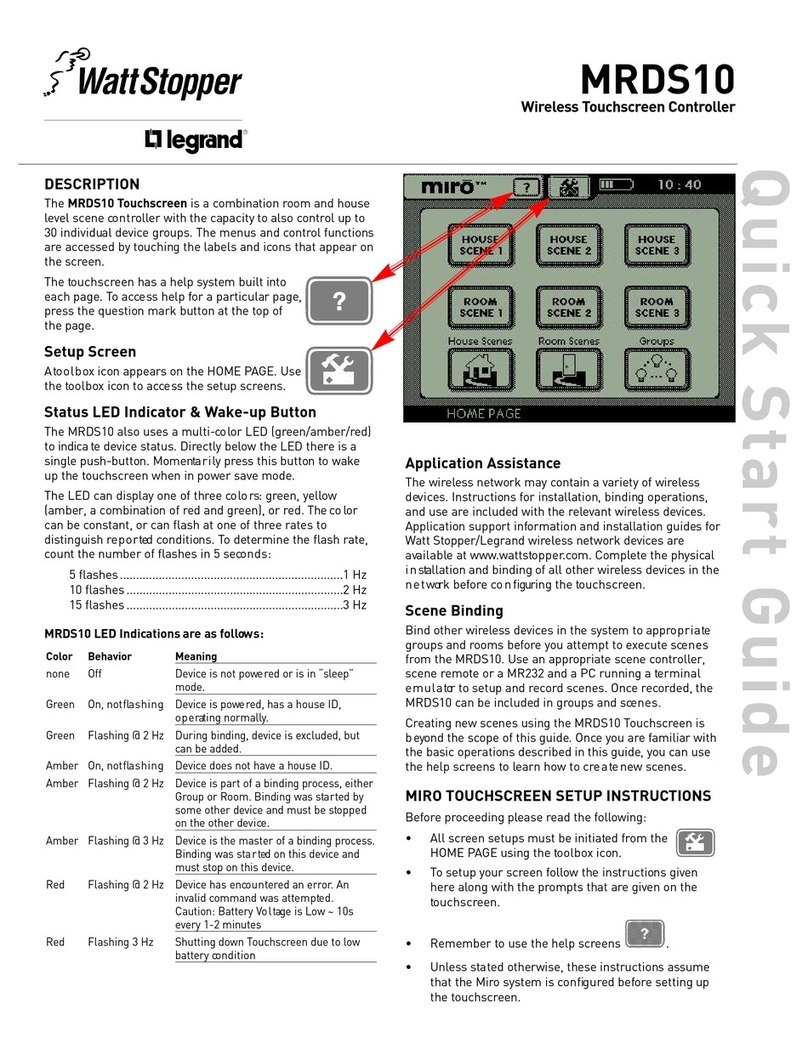
wattstopper
wattstopper Legrand Miro MRDS10 quick start guide