Simplex 4100-3109 IDNet 2 User manual

579-1169 Rev E
4100-3109 IDNet 2, 4100-3110 IDNet 2+2 and 4100-3111 IDNet Loop card Installation Instructions
*05791169E*
Cautions, warnings, and regulatory information
READ AND SAVE THESE INSTRUCTIONS Follow the instructions in this installation manual. These instructions must be followed to avoid damage to
this product and associated equipment. Product operation and reliability depend upon proper installation.
DO NOT INSTALL ANY SIMPLEX™ PRODUCT THAT APPEARS DAMAGED Upon unpacking your Simplex product, inspect the contents
of the carton for shipping damage. If damage is apparent, immediately file a claim with the carrier and notify an authorized Simplex
product supplier.
ELECTRICAL HAZARD Disconnect electrical field power when making any internal adjustments or repairs. All repairs should be
performed by a representative or an authorized agent of your local Simplex product supplier.
STATIC HAZARD Static electricity can damage components. Handle as follows:
• Ground yourself before opening or installing components.
• Prior to installation, keep components wrapped in anti-static material at all times.
EYE SAFETY HAZARD Under certain fiber optic application conditions, the optical output of this device may exceed eye safety limits. Do
not use magnification (such as a microscope or other focusing equipment) when viewing the output of this device.
SULFURIC ACID WARNING Battery contains sulfuric acid, which can cause severe burns to the skin and eyes and can destroy fabric.
Replace any leaking or damaged battery while wearing appropriate protective gear. If you come in contact with sulfuric acid, immediately
flush skin or eyes with water for 15 minutes and seek immediate medical attention.
FCC RULES AND REGULATIONS – PART 15 This equipment has been tested and found to comply with the limits for a Class A digital device, pursuant
to Part 15 of the FCC Rules. These limits are designed to provide reasonable protection against harmful interference when the equipment is operated
in a commercial environment. This equipment generates, uses, and can radiate radio frequency energy and, if not installed and used in accordance
with the instruction manual, may cause harmful interference to radio communications. Operation of this equipment in a residential area is likely to
cause harmful interference in which case the user will be required to correct the interference at his own expense.
SYSTEM REACCPTANCE TEST AFTER SOFTWARE CHANGES To ensure proper system operation, this product must be tested in accordance with
NFPA-72, after any programming operation or change in site-specific software. Reacceptance testing is required after any change, addition or deletion
of system components, or after any modification, repair or adjustment to system hardware or wiring. All components, circuits, system operations, or
software functions known to be affected by a change must be 100% tested. In addition, to ensure that other operations are not inadvertently affected,
at least 10% of initiating devices that are not directly affected by the change, up to a maximum of 50 devices, must also be tested and proper system
operation verified.
NFPA 72® is a registered trademark of the National Fire Protection Association.
Introduction
The IDNet 2* card provides the Fire Alarm Control Panel (FACP) with one
isolated IDNet Signaling Line Circuit (SLC) (or channel) and with up to
four isolated loop outputs. This card is used with compatible** IDNet
and MAPNET II communicating devices and allows the system CPU to
communicate with up to 250 initiating devices, such as smoke sensors and
pull stations. Isolated IDNet communications provide overall operation
improvement, and isolated output loops allow a short circuit on one loop
to avoid impacting the other loops.
There are two available configurations for the IDNet 2 card:
• 4100-3109 IDNet 2 card: This is the basic configuration which provides
the FACP with two Class B (or Class A) loop outputs that are isolated
from each other as well.
•4100-3110 IDNet 2+2 card: In this configuration, the 4100-3109 IDNet
2 card is fitted with two 4100-3111 IDNet Loop cards and provides the
FACP with four Class B (or Class A) isolated IDNet loops. Two isolated
loops are provided by the card and one isolated loop is added per IDNet
Loop card.
*= Unless specified otherwise, the term “IDNet 2” is used in this manual to
designate both the IDNet 2 and the IDNet 2+2 cards.
IDNet 2 Card
IDNet Loop Card
IDNet 2+2 Card
Note: The 4100-3111 IDNet Loop daughter card can be purchased separately and placed on a pre-installed IDNet 2 card that is not EPS-mounted.
However, once it is added to the IDNet card, the compatibility and programming requirements will become the same as with the IDNet 2+2 card.
Important: Verify FACP system programmer, executive, and slave software compatibility when installing, or replacing system components. Refer to the
Technical Support Information and Downloads website for compatibility information.

page 2 579-1169 Rev E
4100-3109 IDNet 2, 4100-3110 IDNet 2+2 and 4100-3111 IDNet Loop card Installation Instructions
Card Layout
Compatibility
Hardware compatibility:
IDNet 2: 4100ES bays, EPS modules, 4100U bays.
IDNet 2+2: 4100ES bays, 4100U bays, ES-PS modules.
Software compatibility:
For use with revision 2.04 or higher of the ES Panel Programmer Software, and revision 12.08 of the 4100U Programmer and Master software.
** = Refer to IDNET and MAPNET II Addressable Device Communications Compatibility Chart S4090-0011
Card Layout
The IDNet 2 is a standard 4x5 card that can accommodate two IDNet Loop cards. Figure 1 highlights the feature elements of these cards.
IDNET 2
2
176543 8
LOOP A
B+ B- A+ A- B+ B- A+ A-
LOOP B
IDNet Terminal Block (TB1)
IDNET 2
21 4
35678
LOOP A
B+ B- A+ A- B+ B- A+ A-
LOOP B
A-A+
S
B-B+
A+ A-
S
B-B+
PDI Connector (P5)
(Reverse Side)
Address
Dip Switch
(SW1)
LOOP B
Class A/B
Jumper (P2)
LOOP A
Class A/B
Jumper (P1)
LEDs
IDNet Terminal
Block (TB1)
IDNet Loop Card
Connector
IDNet Loop Card
(LOOP C)
Connector
(LOOP D)
4100-3109 IDNet 2 Card
4100-3109 IDNet 2 Card
4100-3110 IDNet 2+2 Card
Class A/B
Jumper (P1)
Connector on
Reverse Side
(P2)
IDNet Loop
Card
4100-3111
Figure 1: Card Layout

page 3 579-1169 Rev E
4100-3109 IDNet 2, 4100-3110 IDNet 2+2 and 4100-3111 IDNet Loop card Installation Instructions
LED Identification
The IDNet 2 Card is equipped with 8 LEDs that report the card troubles. Table 1 identifies and describes the different LEDs.
Table 1: LED Definition
LED Name LED description LED Map
Loop A
Loop B
Loop C
Loop D
When a trouble occurs on a loop, the LED corresponding to that loop
illuminates.
Earth- Normally Off. Illuminates to indicate a negative earth fault.
Earth+ Normally Off. Illuminates to indicate a positive earth fault.
IDNet Normally off. Illuminates to indicate a problem with the IDNet channel:
• Steady on indicates channel failure.
Comms Normally off. Turns on steady if the card is not communicating with the
FACP CPU.
TROUBLES
LOOP
A
B
C
D
Setting the Address
The DIP Switch SW1 is used to set the IDNet 2 card address as identified in the Panel Programmer job (see the section on Programming for more
information). From left to right, these switches are designated as SW1-1 through SW1-8. The function of these switches is as follows:
•SW1-1. This switch sets the baud rate for the internal 4100 communications line running between the card and the 4100 CPU. Set this switch
to ON.
•SW1-2 through SW1-8. These switches set the card’s address within the FACP. Refer to Figure 3 for a complete list of the switch settings for all
of the possible card addresses.
You must set these switches to the value assigned to the card by the Panel Programmer.
ON
OFF
(DIP Switch shown is set at address 31)
12345678
Most Significant Bit
Least Significant Bit
Figure 2: DIP Switch SW1

page 4 579-1169 Rev E
4100-3109 IDNet 2, 4100-3110 IDNet 2+2 and 4100-3111 IDNet Loop card Installation Instructions
SW 1-2
Address SW 1-3 SW 1-4 SW 1-5 SW 1-6 SW 1-7 SW 1-8 AddressSW 1-2 SW 1-3 SW 1-4 SW 1-5 SW 1-6 SW 1-7 SW 1-8
1 ON N O ON N O ON ON OFF 61 ON OFF OFF OFF OFF ON OFF
2 ON ON ON ON ON OFF ON 62 ON OFF OFF OFF OFF OFF ON
3 ON N O ON N O ON OFF OFF 63 ON OFF OFF OFF OFFOFF OFF
4ON ON ON ON OFF ON ON 64 OFF ON ON ON ON ON ON
5 ON N O ON N O OFF ON OFF 65 OFF ON ON N O N O ON OFF
6ON ON ON ON OFF OFF ON 66 OFF ON ON ON ON OFF ON
7 ON N O ON N O OFF OFF OFF 67 OFF ON ON N O N O OFF OFF
8ON ON ON OFF ON ON ON 68 OFF ON ON ON OFF ON ON
9 ON ON ON OFF ON OFFON 69 OFF ON ON ON ONOFF OFF
10 ON ON ON OFF ON OFF ON 70 OFF ON ON ON OFF OFF ON
ON11 ON ON OFF ON OFF OFF 71 OFF ON ON ON OFF OFFOFF
12 ON ON ON OFF OFF ON ON 72 OFF ON ON OFF ON ON ON
13 ON ONON OFF ONOFF OFF 73 OFF ON ON OFF ONON OFF
14 ON ON ON OFF OFF OFF ON 74 OFF ON ON OFF ON OFF ON
15 ON ONON OFF OFF OFF OFF 75 OFF ON ON OFF OFFON OFF
16 ON ON OFF ON ON ON ON 76 OFF ON ON OFF OFF ON ON
ON17 ON OFF ON ON ON OFF 77 OFF ON ON OFF OFF ON OFF
18 ON ON OFF ON ON OFF ON 78 OFF ON ON OFF OFF OFF ON
19 ON ON OFF ON ON OFF OFF 79 OFF ON ON OFF OFF OFF OFF
20 ON ON OFF ON OFF ON ON 80 OFF ON OFF ON ON ON ON
21 ON ON OFF ON ONOFF OFF 81 OFF ON OFF ON ON ON OFF
22 ON ON OFF ON OFF OFF ON 82 OFF ON OFF ON ON OFF ON
ON23 ON OFF ON OFF OFF OFF 83 OFF ON OFF ON OFFON OFF
24 ON ON OFF OFF ON ON ON 84 OFF ON OFF ON OFF ON ON
25 ONON OFF ONOFF ON OFF85 OFF ON ONOFF OFF ON OFF
26 ON ON OFF OFF ON OFF ON 86 OFF ON OFF ON OFF OFF ON
27 ON ON OFF OFF ON OFF OFF 87 OFF ON ONOFF OFF OFF OFF
28 ON ON OFF OFF OFF ON ON 88 OFF ON OFF OFF ON ON ON
29 ON ON OFF OFF OFF ON OFF 89 OFF ON OFF OFF ON ON OFF
30 ON ON OFF OFF OFF OFF ON 90 OFF ON OFF OFF ON OFF ON
31 ONON OFF OFF OFF OFF OFF91 OFF ON OFF OFF ON OFF OFF
32 ON OFF ON ON ON ON ON 92 OFF ON OFF OFF OFF ON ON
33 ON OFF ON ON ON ON OFF 93 OFF ON OFF OFF OFF ON OFF
34 ON OFF ON ON ON OFF ON 94 OFF ON OFF OFF OFF OFF ON
35 ON OFF ON ON ON OFF OFF95 OFF ON OFF OFF OFFOFF OFF
36 ON OFF ON ON OFF ON ON 96 OFF OFF ON ON ON ON ON
37 ON OFF ON ON OFF ON OFF97 OFF OFF ONON ON ON OFF
38 ON OFF ON ON OFF OFF ON 98 OFF OFF ON ON ON OFF ON
39 ON OFF ON ON OFF OFF OFF 99 OFF OFF ONON OFFON OFF
40 ON OFF ON OFF ON ON ON 100OFF OFF ON ON OFF ON ON
41 ON OFF ON OFF ON OFFON 101OFF OFF ONON OFF ON OFF
42 ON OFF ON OFF ON OFF ON 102OFF OFF ON ON OFF OFF ON
43 ON OFF ON ONOFF OFF OFF 103OFF OFF ON ON OFF OFF OFF
44 ON OFF ON OFF OFF ON ON 104OFF OFF ON OFF ON ON ON
45 ON OFF ON OFF OFF ON OFF 105OFF OFF ON OFF ON ON OFF
46 ON OFF ON OFF OFF OFF ON 106OFF OFF ON OFF ON OFF ON
47 ON OFF ON OFFOFF OFFOFF 107OFF OFF ON OFF ON OFFOFF
48 ON OFF OFF ON ON ON ON 108OFF OFF ON OFF OFF ON ON
49 ON OFF OFF ONON ON OFF109OFF OFF ON OFF OFF ON OFF
50 ON OFF OFF ON ON OFF ON 110OFF OFF ON OFF OFF OFF ON
ON51 OFF ONOFF ON OFF OFF 111OFF OFF ON OFF OFFOFF OFF
52 ON OFF OFF ON OFF ON ON 112OFF OFF OFF ON ON ON ON
53 ON OFF ONOFF OFF ON OFF 113 OFF OFF N OOFF N O ON OFF
54 ON OFF OFF ON OFF OFF ON 114OFF OFF OFF ON ON OFF ON
55 ON OFF OFF ON OFFOFFOFF 115 OFF OFF OFF N O N O OFF OFF
56 ON OFF OFF OFF ON ON ON 116OFF OFF OFF ON OFF ON ON
ON57 OFF OFF OFF ON ON OFF 117OFF OFF OFF ON ONOFF OFF
58 ON OFF OFF OFF ON OFF ON 118OFF OFF OFF ON OFF OFF ON
ON59 OFF OFF OFF ON OFF OFF 119OFF OFF OFF ON OFFOFF OFF
60 ON OFF OFF OFF OFF ON ON
Figure 3: 4100-3109 IDNet 2 Card Addresses

page 5 579-1169 Rev E
4100-3109 IDNet 2, 4100-3110 IDNet 2+2 and 4100-3111 IDNet Loop card Installation Instructions
Installation
Mounting
The IDNet 2 card and the IDNet 2+2 card mount onto the Power Distribution Interface (PDI) in an FACP expansion cabinet. The IDNet 2 card can also
be installed in the expansion slot of an ES Power Supply Card (ES-PS) card.
To mount the IDNet 2 and IDNet 2+2 card:
1. Select an empty PDI connector. Insert the washer and the metal standoffs into the corresponding installation holes.
2. Insert the PDI connector on the back of the card into the PDI connector.
3. Use the provided hardware to secure the card.
PDI Connector
(Reverse Side)
#6 Screws
Standoffs
Washers
PDI
Figure 4: Mounting an IDNet 2 or IDNet 2+2 card (IDNet 2 card shown)
To add IDNet Loop cards to an IDNet 2 card:
1. Remove the screws that attach the IDNet 2 card to the panel.
2. Insert the metal standoffs and the plastic standoffs into the corresponding installation holes.
3. Insert the connector on the back of the IDNet Loop card into the connector on the IDNet 2 card and snap it in place with the plastic standoff.
4. Use the provided hardware to secure the card.
Note: When adding IDNet Loop cards to a pre-installed IDNet 2 card, it is important to remember that the properties of the IDNet 2 card must be
updated in the FACP programmer.
IDNet Loop Card IDNet 2 Card
Plastic Snap-In
Standoff
Metal
#6 Screw
Standoffs
Connector
(Reverse Side)
IDNet Loop Card IDNet 2 Card
Figure 5: Adding an IDNet Loop Card to an IDNet 2 Card

page 6 579-1169 Rev E
4100-3109 IDNet 2, 4100-3110 IDNet 2+2 and 4100-3111 IDNet Loop card Installation Instructions
Wiring Overview
Each IDNet output from the IDNet 2 or IDNet Loop cards can be wired as a either an isolated Class A circuit or as two isolated Class B circuits.
Class A wiring provides an alternate communication path that allows communication to all devices to be maintained when a single open circuit
fault occurs. Class A wiring requires two wires to be routed from the IDNet 2 Primary Terminals (B+, B-) to each device, and then back to the IDNet
Secondary Terminals (A+, A-). Wiring is in/out, “T” tapping is not allowed.
Class B wiring allows “T” tapping. IDNet wiring is inherently supervised due to individual device level communications. End-of-line resistors are not
required.
Wiring Parameters
Table 2 identifies the card wiring parameters that must be considered when installing these cards.
Table 2: Card Wiring Parameters
Wiring Capacitance Parameters
Parameter Value
Maximum Supported Channel Capacitance; Total of all four Isolated
Outputs.
The sum of line-to-line capacitance, plus the capacitance of either line-to-shield
(if shield is present) = 0.6 μF (600 nF).
Capacitance between IDNet SLC wiring (between wires of the same
polarity; plus to plus, minus to minus).
1 μF maximum (this is for multiple IDNet loops).
Wiring Distance Limits (see note below).
Class B Wiring, Total Channel Wiring Parameters,
Including T-Taps
Class A Wiring, Total Channel Wiring
Parameters
Channel Loading
Up to 125 devices 126 to 250 devices Up to 125 devices 126 to 250 devices
Total Loop Resistance 50 Ω maximum 35 Ω maximum 50 Ω maximum 35 Ω maximum
18 AWG (0.82 mm2) 4000 ft (1219 m) per run,
12,500 ft (3810 m) total
2500 ft (762 m) per run,
10,000 ft (3048 m) total
4000 ft (1219 m) per loop,
12,500 ft (3810 m) total
2500 ft (762 m) per loop,
10,000 ft (3048 m) total
16 AWG (1.31 mm2)
14 AWG (2.08 mm2)
12 AWG (3.31mm2)
5000 ft (1524 m) per run,
12,500 ft (3810 m) total
2500 ft (762 m) per run,
10,000 ft (3048 m) total
5000 ft (1524 m) per loop,
12,500 ft (3810 m) total
2500 ft (762 m) per loop,
10,000 ft (3048 m) total
Note: Maximum wiring distance is determined by either reaching the maximum resistance, the maximum capacitance, or the stated maximum dis-
tance, whichever occurs first. Class A maximum distances are to the farthest device on the loop from either “B” or “A” terminals. For Class B wiring, the
maximum distance to the farthest device is limited to the stated Class A wiring distances.
Note: External wiring must be shielded (for lightning suppression) and 2081-9044 Overvoltage Protectors
must be installed at building exit and entrance locations.
Capacitance: Each protector adds 0.006 μF across the connected line.
Resistance: Each protector adds 3 Ω per line of series resistance; both IDNet lines are protected; 6 Ω per
protector will be added to total loop resistance.
Maximum distance of a single protected wiring run is 3270 ft (1 km).
Wiring Considerations using 2081-9044
Overvoltage Protectors.
(2081-9044 is UL listed to Standard
1459, Standard for Telephone
Equipment).
Refer to document number 574-832: 2081-9044 Overvoltage Protector Installation Instructions for additional
information.
Class A Wiring
To wire the Loop terminals as a Class A circuit:
1. Set the jumper assigned to the loop to the “A” position, as shown in Figure 6.
- Loop A= Jumper P1 on the IDNet 2 card
- Loop B= Jumper P2 on the IDNet 2 card
- Loop C= Jumper P1 on the first IDNet Loop cards
- Loop D= Jumper P1 on the second IDNet Loop card
2. Shielded wire is not recommended. If shielded wires are present, cut and tape off the shield to
prevent it from coming in contact with other components. Metallic continuity of the shield must be
maintained and insulated throughout the entire length of the cable.
3. Route the wiring from the Primary Terminals (B+, B-) to the corresponding inputs on the first device.
4. Route wiring from the first device to the next as in/out. See Figure 7. Repeat for each device.
5. Route the wiring from the last device to the panel.
6. Connect the wiring to the corresponding Secondary Terminals (A+, A-).
Figure 6: Class A Jumper Setting

page 7 579-1169 Rev E
4100-3109 IDNet 2, 4100-3110 IDNet 2+2 and 4100-3111 IDNet Loop card Installation Instructions
+
12
1 2 1 2
IDNet 2 Card
Devices
18 to 12 AWG
Figure 7: IDNet Loop Class A Wiring
Class A wiring notes:
1. If no remote isolators or isolator bases are on the loops, device addressing can be assigned without concern for sequence.
2. If remote isolators or isolator bases are on the loops, the required addressing approach is to start from the “B” side and assign each
successive isolator a higher address than the isolator it proceeds.
Class B Wiring
When wiring the loop for Class B circuits, both the B+, B- and A+, A- terminals are available for parallel connections. Within the IDNet circuitry, A+ is
connected to B+, and A- is connected to B- so circuits can stem from either one. Additionally, two wires can be connected to each screw terminal.
To wire the Loop terminals as a Class B circuit:
1. Set the jumper assigned to the loop to the “B” position, as shown in Figure 8.
- Loop 1 = Jumper P1 on the IDNet 2 card
- Loop 2 = Jumper P2 on the IDNet 2 card
- Loop 3 = Jumper P1 on the left IDNet Loop card
- Loop 4 = Jumper P1 on the right IDNet Loop card
2. Route wiring from the Primary Terminals (B+, B-) to the corresponding inputs on the first device.
It is possible to add up to 4 circuits per IDNet loop on the terminal block when using Class B wiring. See
Figure 9 for the diagram.
3. Route wiring from the first device to the next as in/out as shown in Figure 9. Repeat for each device.
4. Shielded wire is not recommended. If shielded wires are present, cut and tape off the shield at each
end (in the panel and at the last device in each run) to prevent it from coming in contact with other
components. Metallic continuity of the shield must be maintained and insulated throughout the entire
length of the cable.
Figure 8: Class B Jumper Setting

page 8 579-1169 Rev E
4100-3109 IDNet 2, 4100-3110 IDNet 2+2 and 4100-3111 IDNet Loop card Installation Instructions
B+
TB1
IDNet CIRCUIT A
1
B- A+ A-
Devices
B+, B-
Terminals
2
1
4
3
Note: For Class B wiring only, upto4 parallel wiring “T”
taps may be made at the output terminal blocks
2
1Different Circuit Configurations
B+ B- A+ A-
2Circuit Configuration
B+ B- A+ A-
4Circuit Configuration
Figure 9: IDNet Loop Class B Wiring
Class B wiring Notes:
1. If no remote isolators or isolator bases are on the loops, device addressing can be assigned without concern for sequence.
2. If remote isolators or isolator bases are on the loops, the required addressing approach is to start at the output and assign each successive
isolator a higher address than the isolator it proceeds. For Class B wiring only, the “A” output and “B” output per loop are connected together
in parallel for wiring convenience.

page 9 579-1169 Rev E
4100-3109 IDNet 2, 4100-3110 IDNet 2+2 and 4100-3111 IDNet Loop card Installation Instructions
Programming
Adding the IDNet 2 to the Programmer
The IDNet 2 card must be added to the FACP through the ES Panel Programmer. For information on general programming instructions consult the
579-849 ES Panel Programmer.
Note:
The IDNet 2+2 card can be added to the programmer using the same steps as shown below. The difference is in selecting the 4100-3110/4100-3112
IDNet 2+2 card from the Available Hardware window instead of the 4100-3109 IDNet 2 card.
To add the IDNet 2 card to the programmer:
1. Start the programmer software.
2. Open an existing job or create a new one.
3. Select the Hardware tab.
4. Open the Box and the Bay in which you want to place the card.
5. Select the 4100-3109 IDNet 2 card from the Available Hardware window under the “Interface” menu and drag it to the bay. The card has now
been added to your FACP.
6. Double click on the card’s icon to access the Card Properties, Point Editing and Loop Editing tabs. See the “Configuring the Card
Properties Tab” section for more information.
Figure 10: Adding the IDNet 2 Card to the FACP
Configuring the Card Properties Tab
The first tab that require configuring is the Card Properties tab.
To configure the Car Properties tab enter the following information:
•Card Address.*
•Card Description.
•Card Default label.
•Card Custom Label: This field can be used to describe the card's
function, location, or other descriptive information.
•Card Alternate Custom Label: This field is used to have an
alternative description of the card.
•Annunciator: This field indicates which annunciator the card is
associated with.
•Number of units, bays, and boxes.*
•Location.*
•Only activate TrueAlarm device LEDs**: Select this option to only
activate the LEDs corresponding to TrueAlarm devices in a state of alarm (up
to 20 devices at any given time).
•Activate Signal IAM LEDs**: Select this option to only activate the LEDs
corresponding to Signal IAM devices that are in a state of alarm (up to 20
devices at any given time).
•24 V Alarm and Standby current (Amps).
* It is possible to modify the default data manually, however, an error will be triggered if the information entered does not correspond with the FACP
data.
** These options are independent of each other, either one or both can be selected.

page 10 579-1169 Rev E
4100-3109 IDNet 2, 4100-3110 IDNet 2+2 and 4100-3111 IDNet Loop card Installation Instructions
Figure 11: Card Properties Tab

page 11 579-1169 Rev E
4100-3109 IDNet 2, 4100-3110 IDNet 2+2 and 4100-3111 IDNet Loop card Installation Instructions
Configuring the Point Editing Tab
The next tab is the Point Editing tab. This tab is used to manage and edit the point types that correspond to the devices on the IDNet loop.
Refer to the 579-849 ES Panel Programmer manual for information and instructions on how to proceed.
Figure 12: Point Editing Tab
Configuring the Loop Editing Tab
The Loop Editing tab determines the configuration of the loops.
When the IDNet 2 card is added to the ES Programmer, the programmer automatically reserves four specific addresses for the four potential loops.
• Loop 1: Point 251
• Loop 2: Point 252
• Loop 3: Point 253
• Loop 4: Point 254
The device type for both Loop 1 and Loop 2 is set to ISO and cannot be edited.
The device type for Loop 3 and Loop 4 is set to UNUSED by default and must be set to ISO for those loops to be activated.
Once the device type has been determined the following fields may be completed:
• Custom Label
• Alternate Custom Label
• Primary Action Message
• Trouble Action Message

page 12 579-1169 Rev E
4100-3109 IDNet 2, 4100-3110 IDNet 2+2 and 4100-3111 IDNet Loop card Installation Instructions
Figure 13: Loop Editing Tab
Troubleshooting
Troubleshooting
Refer to the tables below for a list of error messages that may appear on the FACP display when using the IDNet 2 card:
Table 3: Trouble Messages
Trouble Message Possible Cause
Extra Device Appears if one or more extra devices (i.e., devices that have not been configured for the IDNet channel) are found on
the system, or if a device is at an incorrect address.
Note: An extra device on address 253 or 254 indicates that a Loop Module has been detected but not programmed.
Only one trouble message appears, regardless of the number of extra devices found. Viewing the trouble log reveals
the extra device address. Devices with LEDs will light their LED steady to indicate the trouble as long as no alarms are
present in the system.
Wrong Device Appears when the device detected at the address does not match what is programmed in the system.
Earth Fault Search Appears while the IDNet 2 card is searching for earth faults on the IDNet channel. When this message is displayed, the
IDNet1+ card cannot show any alarms or other statuses.
Channel Fail Appears when devices have been configured, but none of the devices are communicating on the channel. This
message does not appear if there are no configured devices on the IDNet channel.
No Answer Appears when a device is missing, damaged, improperly configured,
or duplicate devices are present.
Note: A No Answer trouble on address 253 or 254 indicates a loop module has been programmed but not detected.
Bad Answer Appears when there is a faulty device, a noisy communications channel, or duplicate devices are present.
Output Abnormal Occurs during any of these conditions:
• When 24 V is not present on IDNet devices (MBZAM and MAZAM devices for example).
• When TrueAlarm sensor bases with relay driver outputs are not properly supervised.
• When isolator devices are in isolation mode.
Note: Additional troubleshooting information about duplicate devices, weak answers and other problems may be obtained through panel diagnostics.

page 13 579-1169 Rev E
4100-3109 IDNet 2, 4100-3110 IDNet 2+2 and 4100-3111 IDNet Loop card Installation Instructions
Table 4: Loop Troubles
All loop statuses report on the isolator points (unlike the IDNet+ card where card status points are used to report the short and open statuses of the
loops).
Supported Loop Statuses: Loop Connected OFF
Loop Isolated ON
Break in loop wiring OPEN CKT TROUBLE
Short circuit SHORT CKT TROUBLE
The isolator devices may be made Public to the network so that loop status is readily available at external nodes instead of reporting in the common
trouble point.
• If expansion loop cards are programmed but not connected, No Answer troubles are indicated for those devices.
• If the loop card is present but not programmed, an Extra Device card status trouble is indicated for the card and the appropriate address (253, 254,
or both) is logged in the trouble log.
Card Specifications
Card Specifications
Table 5: IDNet 2 Card Specifications
Operating Conditions:
Operating Temperature Range 32oF - 120oF (0oC-49oC).
Operating Humidity Range Up to 93% relative humidity at 90oF (32oC), non-condensing.
Electrical Specifications:
Channel Voltage
to Remote Devices
30 VDC (normal); 35 VDC maximum.
During an alarm or when activating large quantity of device outputs, the channel output voltage is
increased to 35 VDC.
Data rate is 3333 bps.
Output circuits are supervised and power-limited.
Earth Detection Threshold 10k ohms minimum from either positive or negative terminals.
Card Supply Requirements 19.5 V - 32 V / 350 mA maximum. 100 mA for the first device,
0.8 mA for each additional IDNet device.
Comm Wiring Distance See Table 2.
Table 6: IDNet Loop Card Specifications
Operating Conditions:
Operating Temperature Range 32oF - 120oF (0oC-49oC).
Operating Humidity Range Up to 93% relative humidity at 90oF (32oC), non-condensing.
Electrical Specifications:
Channel Voltage
to Remote Devices
30 VDC (normal); 35 VDC maximum.
During an alarm or when activating large quantity of device outputs, the channel output voltage is
increased to 35 VDC.
Data rate is 3333 bps.
Output circuits are supervised and power-limited.
Earth Detection Threshold 10k ohms minimum from either positive or negative terminals.
Card Supply Requirements 19.5 V - 32 V.
Comm Wiring Distance See Table 2.

579-1169 Rev E
© 2019 Johnson Controls. All rights reserved. All specifications and other information shown were current as of document revision and are subject to change without notice. Additional listings may be applicable, contact your local Simplex®
product supplier for the latest status. Listings and approvals under Simplex Time Recorder Co. Simplex, and the product names listed in this material are marks and/or registered marks. Unauthorized use is strictly prohibited. NFPA 72 and
National Fire Alarm Code are registered trademarks of the National Fire Protection Association (NFPA).
This manual suits for next models
2
Table of contents
Other Simplex Computer Hardware manuals

Simplex
Simplex 4001-9813 User manual
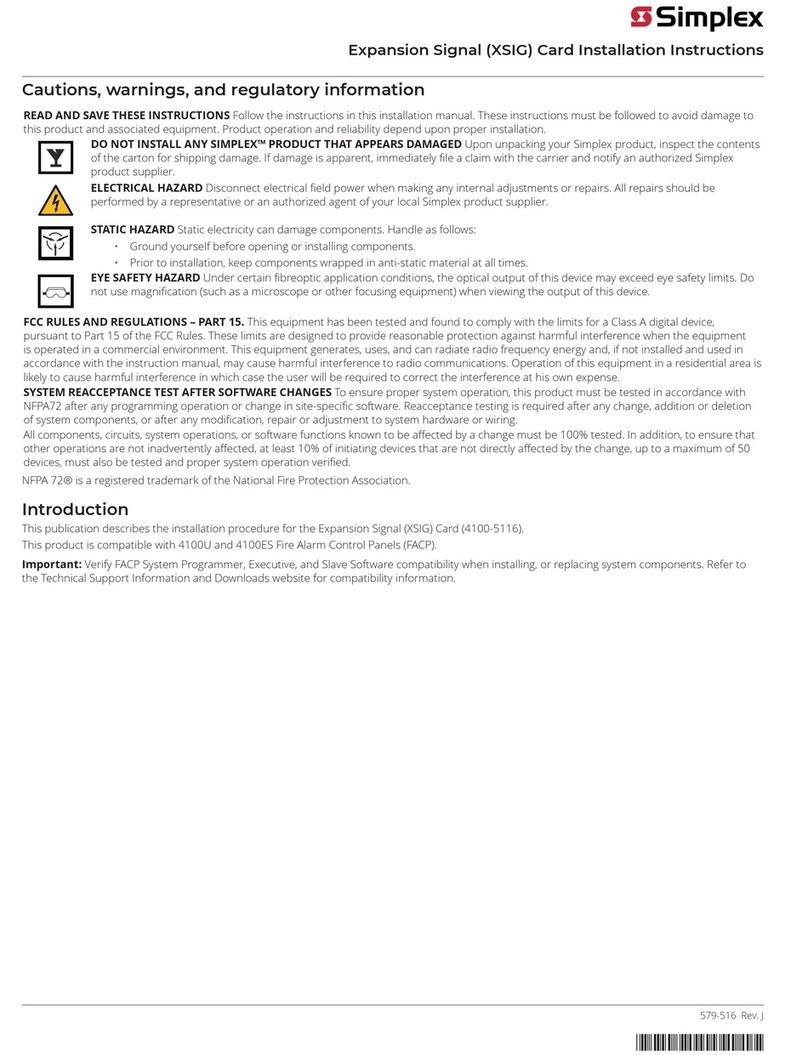
Simplex
Simplex XSIG User manual
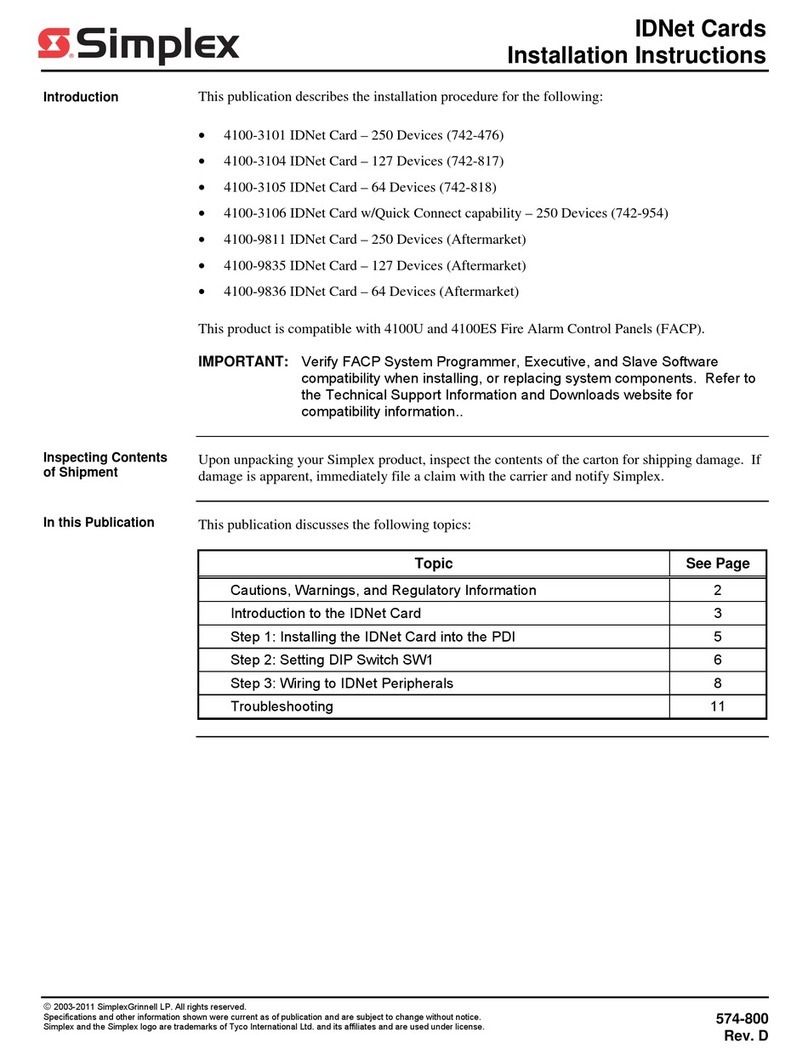
Simplex
Simplex 4100-3101 User manual
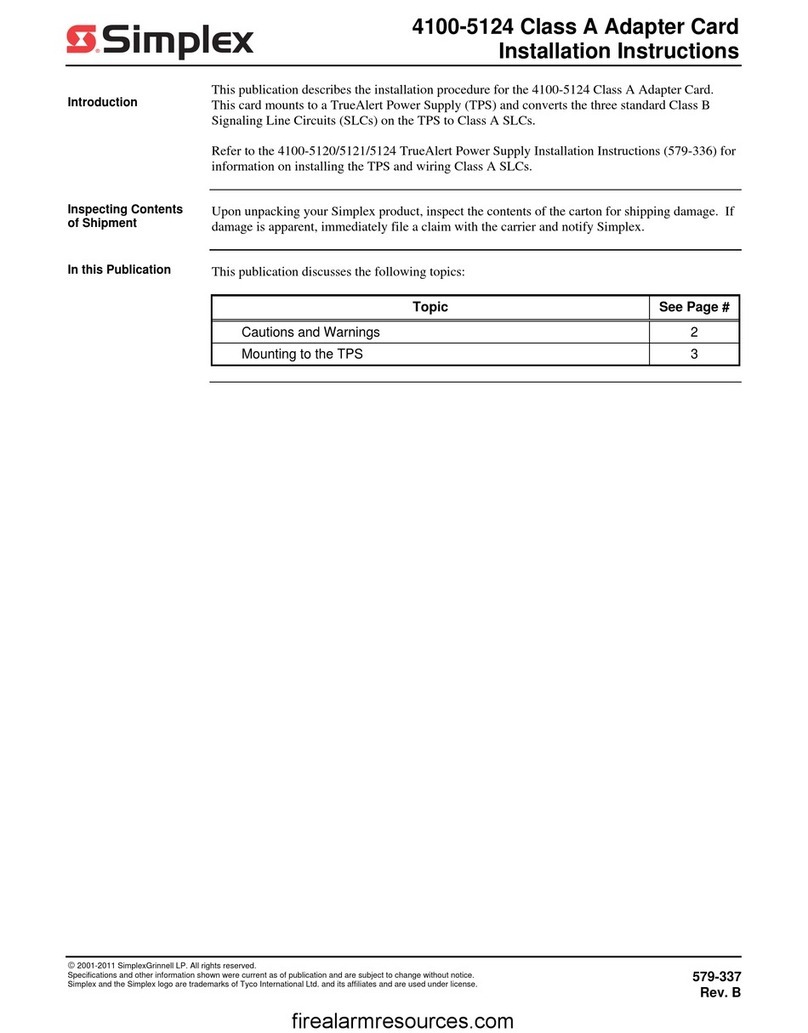
Simplex
Simplex 4100-5124 User manual

Simplex
Simplex Aval PKW1100 User manual
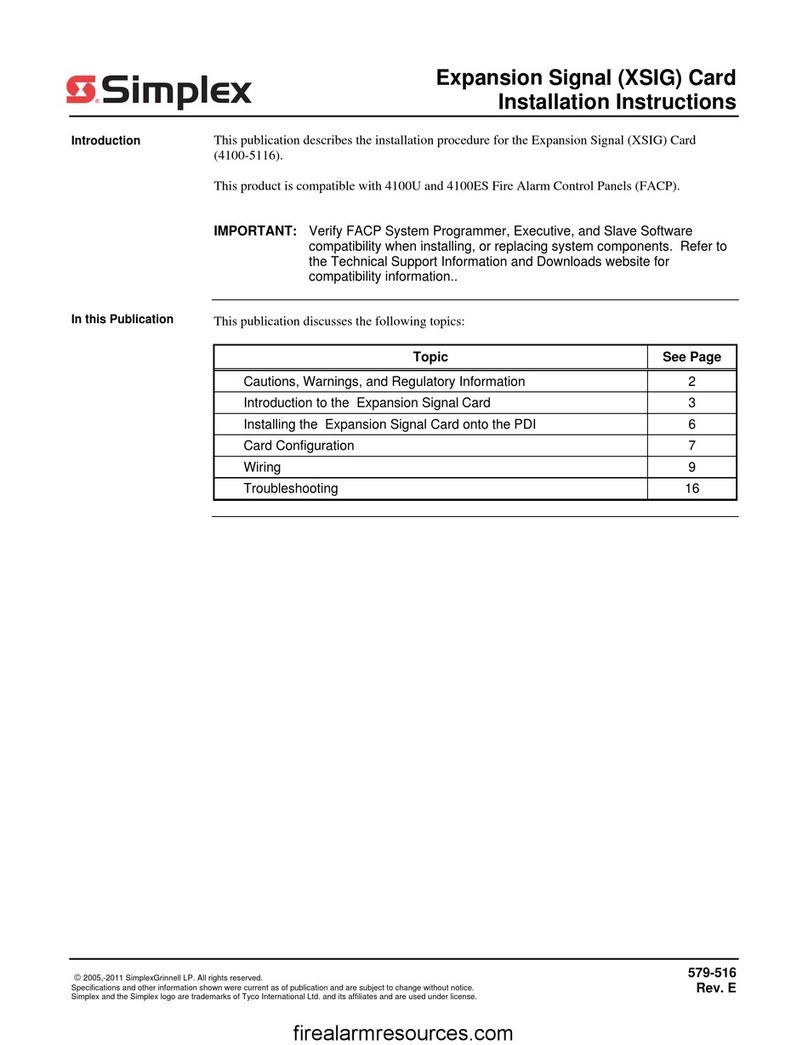
Simplex
Simplex 4100-5116 User manual
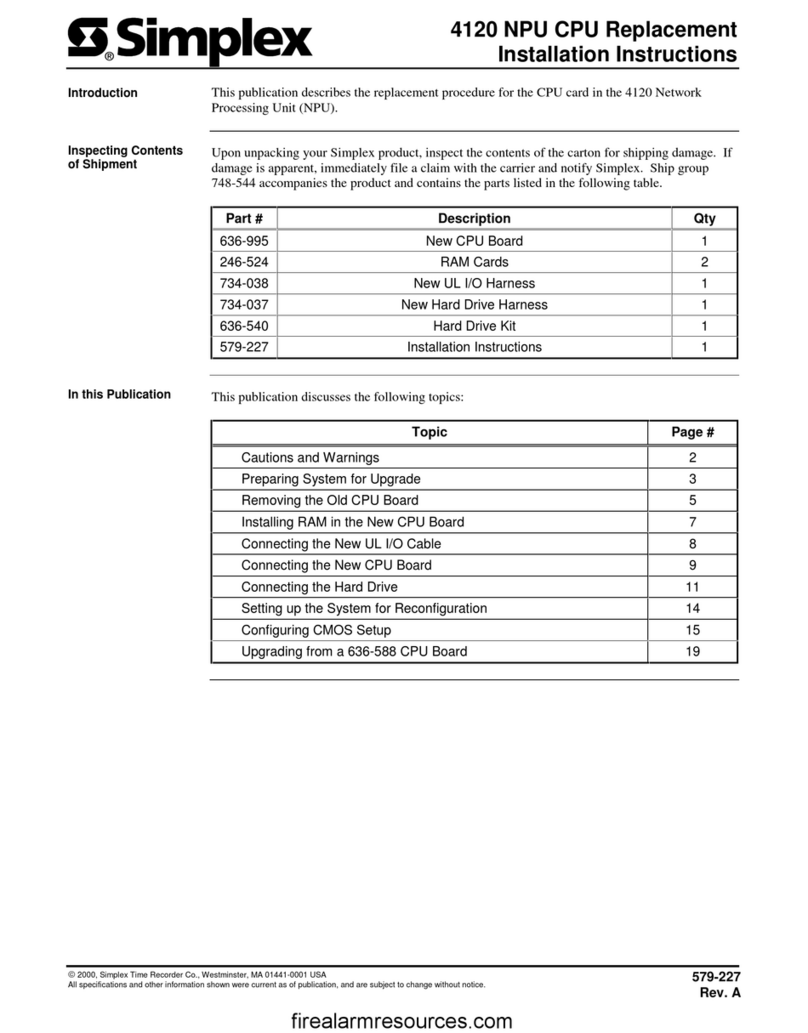
Simplex
Simplex SafeLINC 4120 User manual
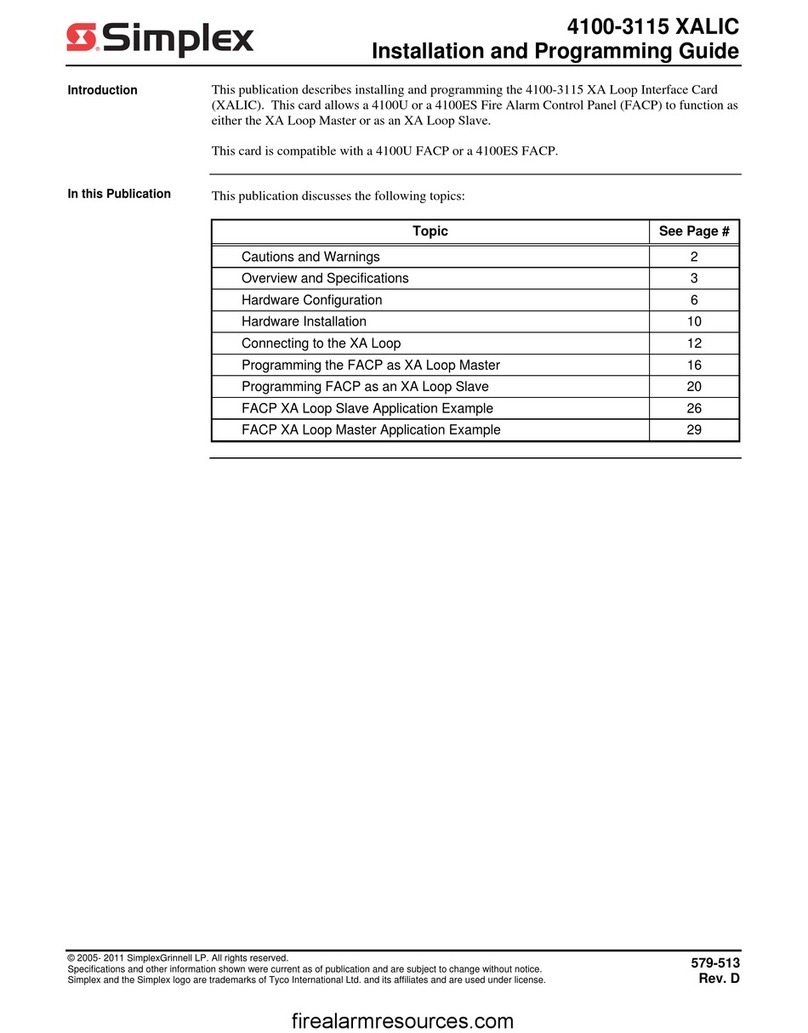
Simplex
Simplex 4100-3115 XALIC Installation guide
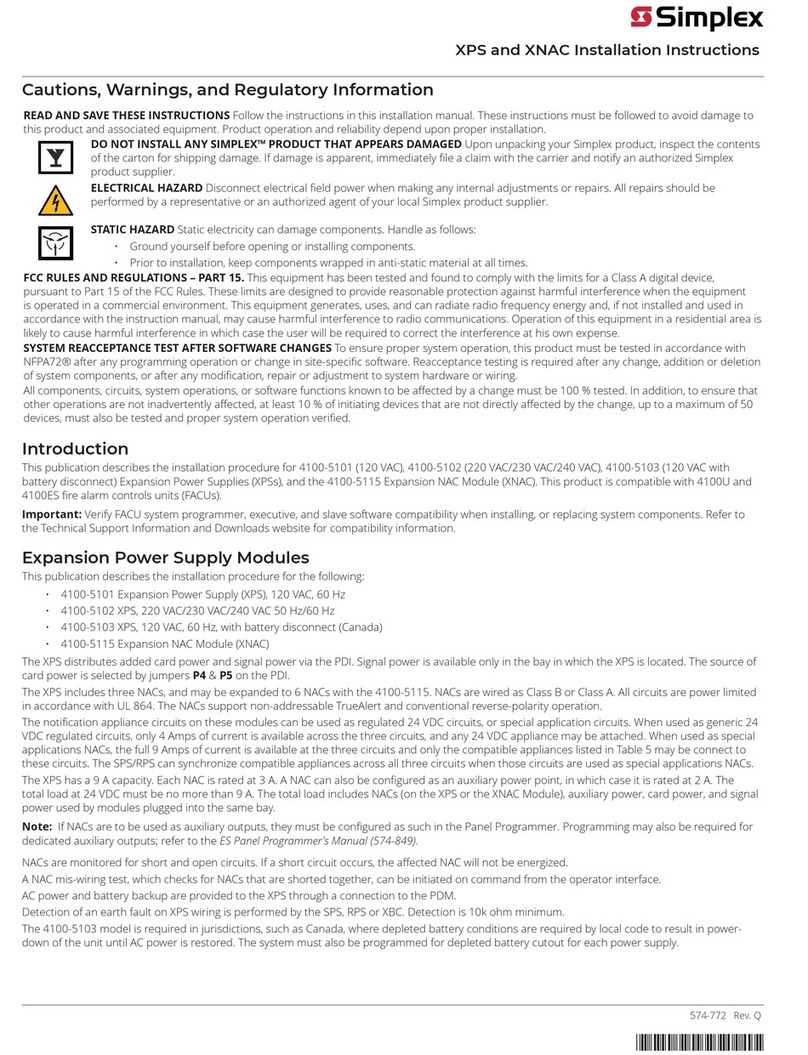
Simplex
Simplex XPS User manual