SIP 01986 User manual

28
Ref: 180417
FOR HELP OR ADVICE ON THIS PRODUCT PLEASE CONTACT YOUR DISTRIBU-
TOR, OR SIP DIRECTLY ON:
TEL: 01509 500400
EMAIL: sales@sip-group.com or technical@sip-group.com
www.sip-group.com
Please dispose of packaging for the product in a responsible
manner. It is suitable for recycling. Help to protect the
environment, take the packaging to the local amenity tip
and place into the appropriate recycling bin.
Never dispose of electrical equipment or batteries in with
your domestic waste. If your supplier offers a disposal facili-
ty please use it or alternatively use a recognised re-cycling
agent. This will allow the recycling of raw materials and help
protect the environment.
1
10” Table Saw
With Stand
01986
Please read and fully understand the instructions in this manual
before operation. Keep this manual safe for future reference.

2
27
Declaration of Conformity
We
SIP (Industrial Products) Ltd
Gelders Hall Road
Shepshed
Loughborough
Leicestershire
LE12 9NH
England
As the manufacturer's authorised representative within the EC
declare that the
10” Table Saw - SIP Part No. 01986
Conforms to the requirements of the following directive(s), as indicated.
2006/42/EC Machinery Directive
2014/30/EU EMC Directive
2011/65/EU RoHS Directive
And the relevant harmonised standard(s), including,
EN 55014-1:2006+A2:2011
EN 55014-2:1997+A2:2008
EN 61000-3-2:2014
EN 61000-3-11:2000
Signed:
Mr P. Ippaso - Director - SIP (Industrial Products) Ltd
Date: 15/03/2017.
DECLARATION OF CONFORMITY

26
NOTES
3
CONTENTS
Page No. Description
4. Safety Symbols Used Throughout This Manual
4. Safety Instructions
8. Contents and Accessories
9. Guarantee
9. Technical Specifications
10. Electrical Connection
11. Getting To Know Your Saw
12. Assembly Instructions
16. Operating Instructions
19. Maintenance
21. Trouble Shooting
22. Exploded Drawing
23. Parts List
27. Declaration of Conformity

4
When using electric tools, basic safety precautions should always be followed to reduce
the risk of fire, electric shock and personal injury.
Read all these instructions before operating the saw and save this user manual for future
reference.
SIP recommends that this saw should not be modified or used for any application other
than that for which it was designed; This table saw is designed for the longitudinal (slitting)
and cross-cutting of most solid woods, coated woods, chip board, block board and similar
wood derived materials, commensurate with the machine’s size.
The machine is not to be used for cutting any type of round wood as they can be twisted
by the rotating saw blade.
If you are unsure of its relative applications do not hesitate to contact us and we will be
more than happy to advise you.
KNOW YOUR SAW: Read and understand the owner's manual and labels affixed to the
saw. Learn its applications and limitations, as well as the potential hazards specific to this
saw.
KEEP WORK AREA CLEAN AND WELL LIT: Cluttered work benches and dark areas invite acci-
dents. Floors must not be slippery due to oil, water or sawdust etc.
DO NOT USE THE SAW IN DANGEROUS ENVIRONMENTS: Do not use the saw in damp or wet
locations, or expose it to rain. Provide adequate space surrounding the work area. Do not
use in environments with a potentially explosive atmosphere.
KEEP CHILDREN AND UNTRAINED PERSONNEL AWAY FROM THE WORK AREA: All visitors
should be kept at a safe distance from the work area.
STORE TOOLS SAFELY WHEN THEY ARE NOT IN USE: The saw should be stored in a dry,
locked cupboard wherever possible and out of the reach of children.
Danger / Caution: Indicates risk of personal injury and/or the possibility of
damage.
SAFETY SYMBOLS USED THROUGHOUT THIS MANUAL
Warning: Risk of electrical injury or damage!
Note: Supplementary information.
SAFETY INSTRUCTIONS
IMPORTANT: Please read the following instructions carefully, failure to do
so could lead to serious personal injury and / or damage to the table
saw.
25
PARTS LIST….cont
Ref. No. Description SIP Part No. Ref. No. Description SIP Part No.
141. Safe Operation Symbols WD01-01213 152. Bevel Shaft Support (back) WD01-01224
142. Hex. Bolt WD01-01214 153. Stop rail front end cap WD01-01225
143. Cross Self Tapping Screw WD01-01215 154. Stop rail rear end cap WD01-01226
144. Overload Protection WD01-01216 155. Chain bar left end cap WD01-01227
145. Connection Lead WD01-01217 156. Chain bar right end cap WD01-01228
146. Carriage Bolt WD01-01218 157. End cap WD01-01229
147. O-ring WD01-01219 158. Hex nut WD01-01230
148. Lock Plate WD01-01220 159. Shoulder screws WD01-01231
149. Lock Nut WD01-01221 160. Washer WD01-01232
150. Screw WD01-01222 161. self tapping screws WD01-01233
151. Self Tapping Screw WD01-01223

24
PARTS LIST….cont
Ref. No. Description SIP Part No. Ref. No. Description SIP Part No.
71. Lower Blade Guard Plate WD01-01147 106. Carriage Bolt WD01-01179
72. Spring WD01-01148 107. Bevel Scale WD01-01180
73. Washer WD01-01149 108. Nut WD01-01181
74. Bevel Indicator WD01-01150 109. Rack WD01-01182
75. Mount Plate WD01-01151 110. Screw WD01-01183
76. Washer WD01-01152 111. Capacitor WD01-01184
77. Spring WD01-01153 112. Switch WD01-01077
78. Bevel Lock Knob WD01-01154 113. Switch Box WD01-01185
79. Bracket - Driving Rod WD01-01155 114. Pad For Cord Clamp WD01-01186
80. Washer WD01-01156 115. 45° Angle Adjustment Wheel WD01-01187
81. Bevel Gear WD01-01157 116. 90° Angle Adjustment Wheel WD01-01188
82. Bushing - Driving Rod WD01-01158 117. Cord Press Plate WD01-01189
83. Actuating Arm WD01-01159 118. Cable sheath WD01-01190
84. Rating Label WD01-01160 119. Mains Lead WD01-01191
85. Crank Wheel WD01-01161 120. Cabinet WD01-01192
86. Screw WD01-01162 121. Knob Ring WD01-01193
87. Bevel Crank Wheel WD01-01163 122. Washer WD01-01194
88. Bevel Gear Wheel WD01-01164 123. Wrench A WD01-01195
89. Spring WD01-01165 124. Wrench B WD01-01196
90. Spring Pin WD01-01166 125. Hex. Bolt WD01-01197
91. Screw WD01-01167 126. Square Nut WD01-01198
92. Washer WD01-01168 127. Cross Strut B WD01-01199
93. Bevel Gear Pad WD01-01169 128. Legs A WD01-01200
94. Elevation Crank Shaft WD01-01170 129. Foot WD01-01201
95. Doublet Nut WD01-01171 130. Cross Strut C WD01-01202
96. Screw WD01-01172 131. Stability Bar WD01-01203
97. Drive Plate WD01-01173 132. Push Stick WD01-01204
98. Locknut WD01-01174 133. Table Support Strut WD01-01205
99. Hex. Bolt WD01-01175 134. Extension Table WD01-01206
100. Riving Knife Clamp WD01-01176 135. Push Stick Holder WD01-01207
101. Riving Knife WD01-01177 136. Spring Washer WD01-01208
102. Riving Knife Bracket WD01-01178 137. Washer WD01-01209
103. Right Blade Guard WD01-01076 138. Set Screw WD01-01210
104. Left Blade Guard WD01-01076 139. Blade Guard Label WD01-01211
105. Self Tapping Screw WD01-01076 140. Cabinet Logo WD01-01212
5
WEAR THE CORRECT CLOTHING: Do not wear loose clothing, neckties, rings, bracelets, or
other jewellery, which may get caught in moving parts. Non-slip footwear is recommend-
ed. Wear protective hair covering to contain long hair. Roll long sleeves up above the el-
bow.
USE SAFETY GOGGLES AND EAR PROTECTION: Wear CE approved safety goggles at all
times, normal spectacles only have impact resistant lenses, they are NOT safety glasses. A
face or dust mask should be worn if the operation is dusty and ear protectors (plugs or
muffs) should be worn, particularly during extended periods of operation.
PROTECT YOURSELF FROM ELECTRIC SHOCK: When working with power tools, avoid contact
with any earthed items (e.g. pipes, radiators, hobs and refrigerators, etc.). It is advisable
wherever possible to use an RCD (residual current device) at the mains socket.
STAY ALERT: Always watch what you are doing and use common sense. Do not operate a
power tool when you are tired or under the influence of alcohol or drugs.
DISCONNECT THE SAW FROM THE MAINS SUPPLY: When not in use, before servicing and
when changing accessories such as blades etc.
AVOID UNINTENTIONAL STARTING: Make sure the switch is in the OFF position before con-
necting the tool to the mains supply.
NEVER LEAVE THE SAW RUNNING / CONNECTED WHILST UNATTENDED: Turn off the saw and
disconnect it from the mains supply between jobs. Do not leave saw until it comes to a
complete stop.
DO NOT ABUSE THE MAINS LEAD: Never carry the saw by the mains lead or pull it to remove
the plug from the mains socket. Keep the mains lead away from heat, oil and sharp edg-
es. If the mains lead is damaged, it must be replaced by the manufacturer or its service
agent or a similarly qualified person in order to avoid unwanted hazards.
CHECK FOR DAMAGED PARTS: Before every use of the saw, a guard or other part that is
damaged should be carefully checked to determine that it will operate correctly and per-
form its intended function. Check for alignment of moving parts, free running of moving
parts, breakage of parts, and any other conditions that may affect its operation. A guard
or other part that is damaged should be correctly repaired or replaced by an authorised
service centre unless otherwise indicated in this instruction manual. Have defective switch-
es replaced by an authorised service agent. Do not attempt to operate the tool if the
switch does not turn it on and off.
KEEP ALL GUARDS IN PLACE: And in full working order.
MAINTAIN TOOLS WITH CARE: Keep tools sharp and clean for the best and safest perfor-
mance. Follow instructions for lubricating and changing accessories. All extension cables
must be checked at regular intervals and replaced if damaged.
USE ONLY RECOMMENDED ACCESSORIES: Consult this user manual for recommended ac-
cessories. Follow the instructions that accompany the accessories. The use of improper
accessories may cause hazards and will invalidate any warranty you may have.
REMOVE ADJUSTING KEYS AND WRENCHES: Form a habit of checking to see that keys and
adjusting wrenches etc. are removed from the saw before every use.
DO NOT OVERREACH: Keep proper footing and balance at all times.
USE THE RIGHT TOOL: Do not use the saw or an attachment to do a job for which it was not
designed.
DO NOT FORCE THE SAW: It will do the job better and more safely at the rate which it was
SAFETY INSTRUCTIONS...cont

6
Use only the blades specified for this saw.
Before each use; Ensure that the blade is fully secure.
For your safety; remove the chippings and work debris etc. from the table top and from
inside the extraction port before each operation.
Make sure that all keys and wrenches are removed before switching on the saw.
Keep hands out of path of the saw blade.
Make sure the blade is clear of the workpiece before the switch is turned on.
Allow the saw to run up to full speed before starting a cut.
Stop operation immediately if you notice anything abnormal.
Wait for the saw blade to stop completely and remove from mains supply before ser-
vicing or adjusting the saw.
Be alert at all times, especially during repetitive, monotonous operations. Don't be lulled
into a false sense of security. Blades are extremely unforgiving.
Use of improper accessories may cause damage to the saw and surrounding area as
well as increasing the risk of injury.
Do not modify the saw to do tasks other than those intended.
Do not cut workpieces too small to hold by hand outside the blade guard.
Maintain a steady grip, avoid awkward positions and do not allow your hand to be in
direct line of the cut.
Make sure the blade is installed with the teeth pointing downward at the front of the saw
to avoid lifting of the workpiece.
Hold the workpiece firmly against the table.
Do not feed the work too quickly while cutting, only feed at a rate so that the blade
can perform the cut without overloading the saw.
Be very cautious when cutting material of uneven cross section such as mouldings,
ensure the material is laying flat and firmly on the table.
This table saw is for indoor use only.
Clear the work table of all objects (tools, scraps, rulers etc.) except the workpiece be-
fore turning the saw on.
When cutting a large piece of material, support it at the height of the table with rollers
or similar.
Make sure there are no nails or foreign objects in the part of the workpiece to be sawn.
Use the push stick to the side of the blade line to push the workpiece securely through
SAFETY INSTRUCTIONS...cont
designed.
DO NOT OPERATE THE SAW IN EXPLOSIVE ATMOSPHERES: Do not use the saw in the pres-
ence of flammable liquids, gases, dust or other combustible sources. The saw may create
sparks which can ignite the dust or fumes.
DO NOT EXPOSE THE SAW TO RAIN OR USE IT IN WET CONDITIONS: Water entering the saw
will greatly increase the risk of electric shock.
WARNING: The dust generated by certain wood or wood derived products can be danger-
ous to the operator, as well as anyone in the area. Always operate The saw in well ventilat-
ed areas and provide dust removal where possible.
23
Ref. No. Description SIP Part No. Ref. No. Description SIP Part No.
1. Table Insert WD01-01078 36. Brush Holder WD01-01113
2. Screw WD01-01079 37. Carbon Brush WD01-01075
3. Screw WD01-01080 38. Screw WD01-01114
4. Table WD01-01081 39. Spring Washer WD01-01115
5. Nut WD01-01082 40. Washer WD01-01116
6. Carriage Bolt WD01-01083 41. Motor House WD01-01117
7. Chain Bar WD01-01084 42. Strain Relief WD01-01118
8. Scale WD01-01085 43. Motor Connect Line WD01-01119
9. C-ring WD01-01086 44. Bearing Sleeve WD01-01120
10. Bevel Shaft WD01-01087 45. Bearing WD01-01121
11. Bevel Shaft Support WD01-01088 46. Motor Housing Field Assembly WD01-01122
12. Press Plate WD01-01089 47. Self Tapping Screw WD01-01123
13. Pin WD01-01090 48. Armature Assembly WD01-01124
14. End Cap WD01-01091 49. Bearing WD01-01125
15. Socket Screw WD01-01092 50. Baffle WD01-01126
16. Wing Nut WD01-01093 51. Gear Housing WD01-01127
17. Parallel Stop WD01-01094 52. C-ring WD01-01128
18. Carriage Bolt WD01-01095 53. Gear WD01-01129
19. Stop Rail WD01-01096 54. Screw WD01-01130
20. Self Tapping Screw WD01-01097 55. Bearing WD01-01131
21. Rip Fence Indicator WD01-01098 56. Bearing Cover Plate WD01-01132
22. Parallel Stop WD01-01099 57. Arbor WD01-01133
23. Eccentric Lever WD01-01100 58. Flat key WD01-01134
24. End Cap WD01-01101 59. Spring Washer WD01-01135
25. Mitre Gauge Stop Rail WD01-01102 60. Screw WD01-01136
26. Carriage Bolt WD01-01103 61. Motor Bracket WD01-01137
27. Self Tapping Screw WD01-01104 62. Lower Blade Guard WD01-01138
28. Mitre Handle WD01-01105 63. Inner Blade Flange WD01-01139
29. Mitre Gauge WD01-01106 64. Washer WD01-01140
30. Self Tapping Screw WD01-01107 65. Blade WD01-01141
31. Mitre Gauge Indicator WD01-01108 66. Outer Blade Flange WD01-01142
32. Rod - Mitre Gauge WD01-01109 67. Hex. Bolt (L) WD01-01143
33. Hex bolt WD01-01110 68. Dust Chute WD01-01144
34. Motor End Cap WD01-01111 69. Screw WD01-01145
35. Self Tapping Screw WD01-01112 70. Extraction Hose WD01-01146
PARTS LIST

22
EXPLODED DRAWING
7
Some wood and wood composites have the potential to be highly
toxic; always wear a face mask when operating saw.
When using the saw always ensure the operator as well as those in
the area wear ear protection.
When using the saw always ensure the operator as well as those in
the area wear eye protection.
SAFETY INSTRUCTIONS...cont
Caution: The warnings and cautions mentioned in this user manual can not
cover all possible conditions and situations that may occur. It must be under-
stood by the operator that common sense and caution are factors which can-
not be built into this product, but must be applied.
the saw blade.
Make sure that the riving knife is always used, and set up is correctly.
Use the upper blade guard and set it to the correct position.
Only use saw blades for which the maximum permissible speed is not lower than the
maximum spindle speed of the saw and which are suitable for the material to be cut.
The saw must not be used for slotting jobs (cutting grooves which end in the workpiece).
Ensure that the upper part of the saw blade is covered during transport, e.g. by the
guard.
Before each use; Ensure that the blade guard is fitted and in full working order.
Understand the operating environment; Before each use the operator should assess,
understand and where possible reduce the specific risks and dangers associated with
the operating environment. Bystanders should also be made aware of any risks associ-
ated with the operating environment.

8
CONTENTS AND ACCESSORIES
Note: If any parts are missing, contact your distributor for the missing parts
to be replaced.
Ref. No. Description Ref. No. Description
N/A Main Saw Body 17. Leg Brace - Long (2)
4. Saw blade guard 18. Leg Brace - Short (2)
5. Suction hose 19. Fixing Kit
7. Mitre Gauge 20. Fixing Kit
8. Extension Tables (2) 20a. Fixing Kit
9. Push Stick 20b. Fixing Kit
15. Rip fence 21a. Blade Wrench
16. Legs (4) 21b. Blade Wrench
16a. Rubber Feet (4) 22. Support Strut
16b. Stability Brackets (2)
21
TROUBLE SHOOTING
Problem Possible cause Possible solution
Motor is slow or weak:
Voltage from source is low.
Windings are burned out or
open.
NVR Switch is defective.
Circuit is overloaded with
appliances lights or other
electrically powered equip-
ment
Request a voltage check
from local power company.
Have the Motor checked,
repaired or replaced.
Have the NVR switch
checked, repaired or re-
placed.
Do not use other appliances
or electrically powered
equipment on the same
circuit when using the Table
Saw.
Motor regularly overheats:
Voltage from source is low.
Dull saw blade.
Sawdust inside table saw is
blocking airflow.
Request a voltage check
from the local power com-
pany.
Replace the saw blade.
Clean out the saw base.
When ripping, the cut
burns the workpiece, or
stalls the motor:
Blade teeth are dull.
Workpiece is warped.
Rip fence is not parallel with
the saw blade.
Sharpen or replace the
blade.
Replace the workpiece.
Re-align the rip fence, and
lock it in position.
Rip Fence does not move
smoothly:
Rip Fence is mounted incor-
rectly.
Remove, and reposition the
Rip Fence and lock it in posi-
tion.
Bevel & Height Handles are
hard to turn:
Sawdust has collected on
the mechanisms inside the
saw.
Clean and lubricate the
mechanisms inside the
base.
Table saw vibrates exces-
sively:
Floor surface is uneven.
Saw blade is damaged.
Loose bolt, Screws, Nuts.
Sit the saw on a level sur-
face.
Replace the Saw Blade.
Tighten all Hardware.

20
Note: Ensure that the blade is fitted in the correct direction; The teeth
should point downward at the front of the blade.
MAINTENANCE….cont
Remove the outer flange and the old saw blade from the inner flange.
Clean the blade flange thoroughly before fitting the new blade.
Mount and fasten the new saw blade in reverse order.
Refit the table insert (2).
Check to make sure that all safety devices are properly mounted and in good
working condition before you begin working with the saw again.
9
This SIP table saw is covered by a 12 month parts and labour warranty covering failure
due to manufacturers defects. This does not cover failure due to misuse or operating
the saw outside the scope of this manual - any claims deemed to be outside the
scope of the warranty may be subject to charges Including, but not limited to parts,
labour and carriage costs. Consumable items such as fuses, blades and motor brush-
es are not covered by the warranty.
Consumable items such as blades, table inserts & carbon brushes etc. are not cov-
ered by the warranty.
This saw is designed to ONLY cut wood or wood derived products.
In the unlikely event of warranty claims, contact your distributor as soon as possible.
TECHNICAL SPECIFICATIONS
Note: Proof of purchase will be required before any warranty can be hon-
oured.
GUARANTEE
Part number 01986
Input voltage 230v ~ 50hz
Input Fuse Rating 13 amps
Motor 1800W
No Load Speed 5000 r/min
Blade Size Ø 250 x 30 x 2.8 mm
Blade Tilt 0° - 45°
Main Table Dimensions 487mm x 640mm
Table Dimensions inc. 2 Extensions 940mm x 640mm
Cutting capacity @ 0° 85mm
Cutting capacity @ 45° 65mm
Blade Height Adjustment 0mm - 85mm
Extraction Port Ø 35mm
Sound Pressure (LpA)* 91.0 dB(A)
Sound Power (LWA)* 104.0 dB(A)
* Tested According to: EN 61029.3 dB(A) uncertainty

10
ELECTRICAL CONNECTION
Note: Always make sure the mains supply is of the correct voltage and the
correct fuse protection is used. In the event of replacing the fuse always
replace the fuse with the same value as the original.
Warning: Never connect live or neutral wires to the earth terminal of the
plug. Only fit an approved plug with the correct rated fuse. If in doubt
consult a qualified electrician.
Note: If an extension lead is required in order to reach the mains supply;
ensure that this too is rated for the correct voltage and fuse rating.
Note: The cross section of the extension lead should be checked so that it
is of sufficient size so as to reduce the chances of voltage drops.
This table saw is double insulated; This means the operator is separated from
the tool's electrical system by two complete sets of electrical insulation.
This table saw is fitted with a standard UK type 230V ~ plug. Before using the tool in-
spect the cable and plug to ensure that neither are damaged. If any damage is visi-
ble have the tool inspected / repaired by a suitably qualified person. If it is necessary
to replace the plug a heavy duty impact resistant plug would be preferable.
The wires for the plug are coloured in the following way:
Blue Neutral
Brown Live
As the colours of the wires may not correspond with the markings in your plug, pro-
ceed as follows:
The wire which is coloured blue, must be connected to the terminal marked with N
or coloured black.
The wire which is coloured brown, must be connected to the terminal, which is
marked L or coloured red.
Always secure the wires in the plug terminal carefully and tightly. Secure the cable
in the cord grip carefully.
19
Warning! Always ensure that the saw is turned off and that the plug is disconnected
from the mains supply before carrying out any adjustments, repairs or maintenance.
MAINTENANCE
CHANGING / INSTALLING THE BLADE
GENERAL CLEANING
Remove dust and dirt regularly from the machine. Cleaning is best carried out with
a fine brush or a cloth.
Never use caustic agents to clean plastic parts.
Keep all safety devices, air vents and the motor housing free of dirt and dust as far
as possible.
Wipe the equipment with a clean cloth or blow it with compressed air at low pres-
sure.
We recommend that you clean the device immediately each time you have fin-
ished using it.
Clean the saw regularly with a moist, not wet, cloth and some soft soap.
Do not use cleaning agents or solvents; these could attack the plastic parts of the
equipment.
Ensure that no water can seep into the electric parts of the saw.
Ensure the blade guard is kept clean with a damp cloth (do not clean the guard or
any part of the saw with a corrosive solvent) to reduce the risk of injury.
Do not allow pitch to accumulate on the saw table; Clean it with gum/pitch remov-
er.
Raise the blade to its highest point.
Detach the saw blade guard (6).
Remove the table insert by loosening the countersunk screw.
Loosen the nut; Turn the nut in the direction in which the saw blade rotates by using
a wrench on the nut and another wrench on the motor shaft to apply counter-
pressure.

18
OPERATING INSTRUCTIONS….cont
Insert the mitre gauge (7) into the slot (31) of the saw table (Fig.17).
Loosen locking knob (32).
Turn the mitre gauge (7) until the arrow points to the angle required.
Re-tighten locking knob (32).
When cutting larger workpieces, the mitre gauge (7) can be lengthened with the aux-
iliary extrusion (34) (Fig. 17).
USING THE MITRE GAUGE
Caution: Do not allow the auxiliary extrusion to come into contact with the
saw blade; The distance between the extrusion and the saw blade should
be at least 2 cm.
Slacken the thumb screws (28) and push the extrusion (27) forward until it touches
the imaginary 45° line.
Re-tighten the wing nuts (28).
Once set in the correct position and orientation, ensure that the rip-fence is locked in
position by pressing down on the locking handle (30).
11
GETTING TO KNOW YOUR SAW
Ref. No. Description Ref. No. Description
1. Main Table 9. Push Stick
2. Table Insert 10. Saw Stand
3. Blade 11. On/Off (NVR) Switch
4. Blade Guard 12. Height/Angle Adjust Hand Wheel
5. Extraction Hose 13. Angle Lock
6. Riving Knife 14. Rip Fence Guide Rail
7. Mitre Gauge 15. Rip Fence
8. Table Extension

12
ASSEMBLY INSTRUCTIONS
FITTING THE EXTENSION TABLES
Line up one of the extension tables (8) with the main saw table (1) (Fig.5).
Fit the bolts (19), spring washers (20a), washers (20b) and nuts (20) hand tight to
hold the table in place.
Line up the support struts (22) as shown, and secure one end to the table exten-
sion (8) with the bolts (19), spring washers (20a), washers (20b) and nuts (20).
The opposite end should be secured once the leg set has been fitted.
Repeat this process for the opposite table extension.
DANGER! Always ensure that the saw is turned off and that the plug is disconnect-
ed from the mains supply before carrying out any adjustments, repairs or mainte-
nance.
Unpack the table saw and check it for damage which may have occurred in
transit.
The saw should be set up where it can stand firmly on a flat level surface.
All covers and safety devices have to be correctly fitted and in full working order
before the machine is switched on.
The saw blade should run freely.
Place the main saw assembly, table face down, onto a flat level surface.
Note: Place the saw onto cardboard, or similar, to reduce the risk of dam-
age and ensure that the blade is in its lowest position.
Note: The bolts should not be tightened fully at this point as some adjust-
ments will be required.
17
USING THE RIP-FENCE
OPERATING INSTRUCTIONS….cont
The Rip-Fence (15) has an auxiliary extrusion (27) which has two different guide faces
which should be set according to the thickness of the material to be cut.
The extrusion (27) should be used according to Fig.14 for thin material (under 25mm
workpiece thickness), and according to Fig.15 for thick material (over 25mm work-
piece thickness).
Loosen the wing nuts (28) in order to turn the extrusion.
The extrusion can be removed and replaced in the correct orientation on either the
left or right side of the rip-fence depending on the type of cut and size of workpiece.
There are 2 scales on the rip-fence guide rail (14) depending on which orientation the
extrusion is set to.
In order to avoid “jamming” of the workpiece; the auxiliary extrusion (27) is longitudinal-
ly adjustable.
A Rule of thumb: The rear end of the extrusion is connected to an imaginary line,
which begins approximately at the middle of the saw blade, and runs towards the rear
of the saw at an angle of 45°.
Set the rip-fence to the required cutting width.

16
ON/OFF (NVR) SWITCH
OPERATING INSTRUCTIONS
SETTING THE CUTTING HEIGHT
Once fully assembled and adjusted, and all safety precautions have been followed;
the saw is ready to be run.
Connect the mains plug to an appropriate power supply.
To start the saw; press the green (I) button.
To stop the saw; press the red (0) button.
Your SIP 10” Table Saw is fitted with a safety NVR (No Volt Release) switch (11). This
means that if power is cut to the saw (such as in a power failure); the motor will not
start to run once the power is returned without the operator following the above in-
structions to restart the saw.
Turn the height adjust handle (12) to set the blade (3) to the required cutting height.
- Anticlockwise: Lower cutting height.
- Clockwise: Higher cutting height.
SETTING THE CUTTING ANGLE
Loosen the angle lock (13) by turning it anti-clockwise.
Push the angle/height adjust hand-wheel (12) in so that the gears mesh and turn
the hand-wheel (12) until the desired angle is achieved.
Release the hand-wheel (12) and retighten the angle lock (13).
Note: After each new adjustment it is advisable to carry out a trial cut in
order to check the set settings are correct.
13
FITTING THE LEG SET
ASSEMBLY INSTRUCTIONS….cont
Line up the square holes on each leg (16) with the square tabs on the main saw.
Fit and loosely tighten the bolts (19), spring washers (20a) and the washers (20b)
together with the opposite end of the support struts (22) onto the side of the main
saw (Fig.6).
Fit and loosely tighten the bolts (19), spring washers (20a) and the washers (20b) to
the front and rear of the main saw.
Repeat this process for the opposite side of the saw.
Push the 4 rubber feet (16a) onto the bottom of each leg (Fig.6.1).
Fit the long braces (17) to the left and right sides of the leg set (Fig.7) and secure in
place using the bolts (19), spring washers (20a), washers (20b) and the nuts (20).
Repeat the operation with the short braces (18) to the front and rear of the leg set.
Fit the 2 stability brackets (16b) to the back of each rear leg (Fig7.1) and secure in
place using the bolts (19), spring washers (20a), washers (20b) and nuts (20).

14
ASSEMBLY INSTRUCTIONS….cont
Once the side extensions and the leg set are loosely fitted; Turn the saw over onto
a firm level surface.
Ensure that the main saw table is as level as possible.
With a straight edge, or similar, set the extension tables level with the main saw bed
and proceed to tighten all of the nuts and bolts etc.
SETTING THE RIVING KNIFE
The riving knife (6) is a safety device that sits behind, and moves relative to the saw
blade to, when set correctly, help eliminate kickback. To set the riving knife:
Set the saw blade (3) to the max. cutting depth, bring it to the 0° position and lock
it (see operating instructions).
Loosen and remove the screw (23) from the table insert (2) using a Phillips screw-
driver, and remove the table insert.
The distance between the saw blade (3) and the riving knife (6) must be between
3mm & 5mm (Fig. 9).
Loosen the mounting bolt (24) in order to adjust the riving knife (6) until the right dis-
tance is achieved.
Retighten the mounting screw (24) and refit and secure the table insert (2).
Slot
15
Note: Do not over tighten the wing-nut; the guard should move freely and
drop over the blade under its own weight.
ASSEMBLY INSTRUCTIONS….cont
FITTING THE BLADE GUARD
Loosely fit the bolt (25) & wing-nut to the blade guard (4).
Slide the bolt (25) into the slot on the riving knife (6) and push back (Fig.10 & 11).
Tighten the wing-nut to hold in place.
Push one end of the suction hose (5) onto the suction adapter (26) and the oppo-
site end to the connecting piece of the blade guard (4) (Fig.12).
Table of contents
Other SIP Saw manuals
Popular Saw manuals by other brands

Altrad
Altrad BELLE BC 350 Operator's manual

Chicago Electric
Chicago Electric 65570 Owner's manual & safety instructions
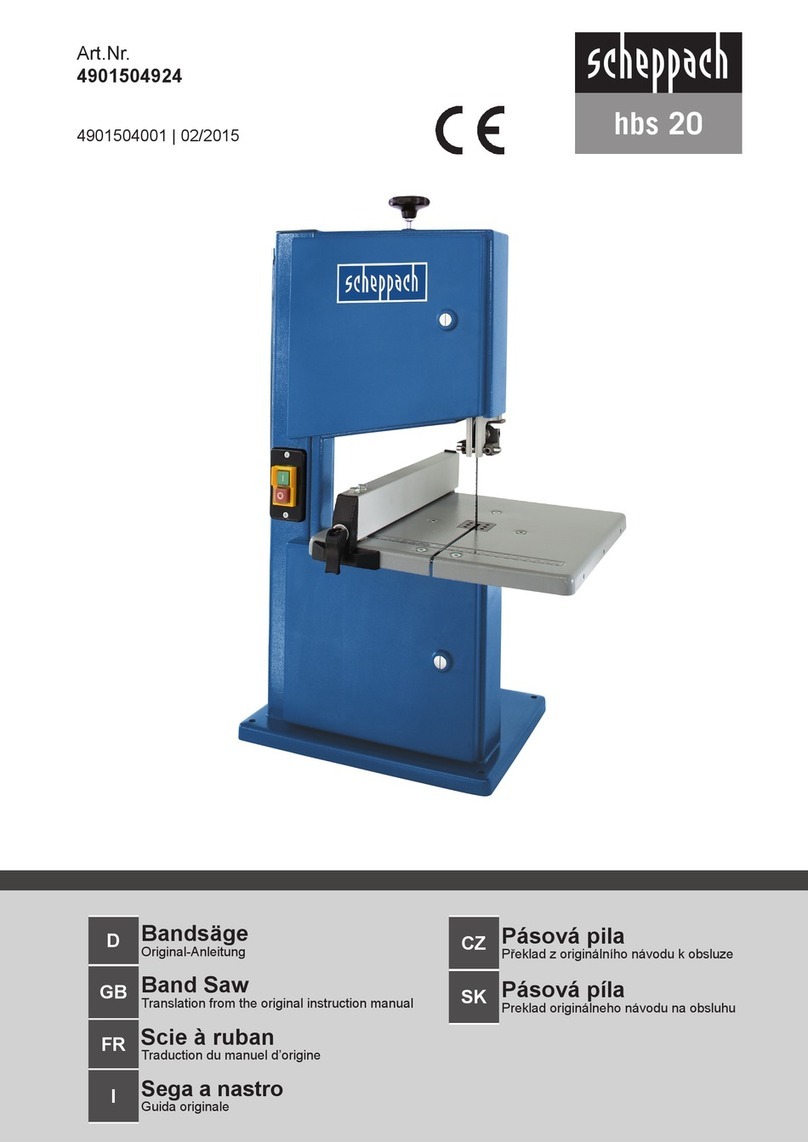
Scheppach
Scheppach HBS20 Translation from the original instruction manual
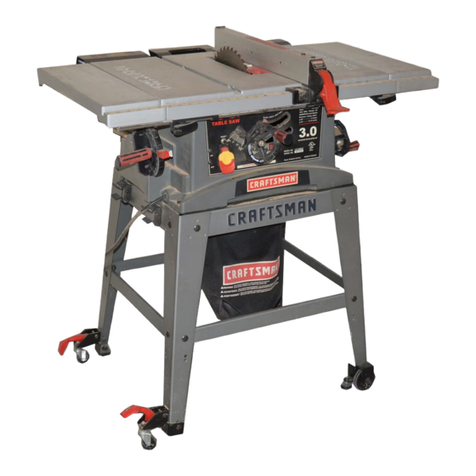
Craftsman
Craftsman 137.248830 Operator's manual

GreenWorks
GreenWorks CRD401 Operator's manual
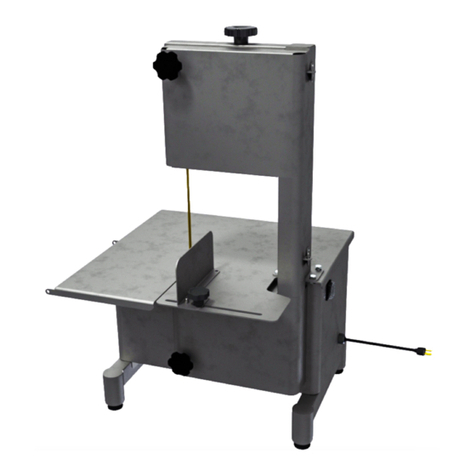
Skymsen
Skymsen MSL instruction manual