Soyer BMS-10P User manual

BMS-10P
Operating Instructions
Stud Welder
GB: English Version
Read these operating instructions before starting any work!
Doc.ID: P00297 Date of issue: 06.2013 www.soyer.de


3
Operating Instructions
BMS-10P Stud Welder
Serial number *
BMS-10P Stud Welder_________________________
Please enter the serial number here, so that the data is
immediately available if you need service support.
Order No. Code designation Note
P01063 BMS-10P Mains voltage 230 V (OPTION 115 V *1)
with capacitance change-over 33,000 / 99,000 µF
*1 The BMS-10P stud welder is suitable for operation with 115 V or 230 V.
The current mains voltage is indicated on the type plate.
Heinz Soyer Bolzenschweißtechnik GmbH
Inninger Straße 14 | 82237 Wörthsee | Tel.: +49 8153 8850 | Fax: +49 8153 8030 | E-mail: [email protected] | www.soyer.de

4
Thank you!
Congratulations on purchasing the BMS-10P SOYER stud welder.
You have made an excellent choice. Your BMS-10P SOYER stud welder was specially developed for
the high-speed fastening of SOYER weld studs in compliance with DIN EN ISO 13918 on metallic,
weldable workpieces.
Our devices have been tested and proven according to current European and national
guidelines on health and safety. Proof of conformity has been established and the
manufacturer is in possession of the corresponding documents.
FOR YOUR SAFETY
Read all of these operating instructions prior to start-up. Please follow all safety
precautions as well as all chapters of these operating instructions before starting
to weld. Non-compliance with the safety precautions can result in serious
personal injuries or death.
SOYER®is a registered trade mark of Heinz Soyer Bolzenschweißtechnik GmbH.
It is prohibited to distribute or reprint this document. It is also prohibited to exploit or disclose its
contents unless permission has been expressly granted. Non-compliance with this regulation will lead
to compensation for damages. All rights reserved, particularly in the case of a patent grant or a GM
registration.
We have verified that the contents of this pamphlet correspond to the hard- and software described.
Deviations, however, cannot be excluded so that we cannot warrant for absolute compliance. The
illustrations contained in this instruction manual can vary in some details from your product. This,
however, has no influence on the handling of the machine
The data in this documentation is verified regularly and any necessary corrections incorporated in
future impressions. Any suggestions for improvement are appreciated.
Date of issue: January 01, 1998
Revision: rev. 06.2013
© Heinz Soyer Bolzenschweißtechnik GmbH 2013 · All rights reserved
Printed in the Federal Republic of Germany

5
Heinz Soyer Bolzenschweißtechnik GmbH
Inninger Straße 14
82237 Wörthsee
CE Declaration of Conformity
We herewith declare that the machine described in the following and the version available on the
market correspond in design and construction to the safety and health requirements of the listed
guidelines and standards. Any unauthorised modification to this machine automatically annuls this
declaration.
Designation of machine : Stud welding device
Machine type :BMS-10P
BMS-10PV
Machine no. : ______________________
Applicable EU directives : RoHS Directive (2011/65/EU)
Low Voltage Directive (2014/35/EU)
EMC Directive (2014/30/EU)
Applied harmonised : EN 60 974-1:2012
standards, in particular EN 60 974-10:2008
Applied national standards : DGUV Regulation 1
Date : 16 July 2015
Producer’s signature : ____________________
Signer’s function : Managing Director

6
Table of contents
1Safety instructions................................................................................................................ 8
1.1Description of reference signs in the operating instructions................................................ 10
1.2Staff qualification and training..............................................................................................11
1.3Dangers in the case of non-compliance with safety instructions......................................... 11
1.4Before starting to weld... ...................................................................................................... 11
1.5Working with the stud welding equipment............................................................................ 11
1.6Inadmissible operating methods .......................................................................................... 11
1.7Stopping the stud welding equipment.................................................................................. 11
2General................................................................................................................................. 12
2.1The following should be principally observed... ................................................................... 12
2.2Intended use ........................................................................................................................ 12
2.3Marketing and service.......................................................................................................... 12
2.4Information on the documentation ....................................................................................... 12
2.4.1Information on the operating instructions ........................................................................ 12
2.4.2Conduct in the case of malfunctions................................................................................ 13
3Description of stud welder................................................................................................. 14
3.1Description ........................................................................................................................... 14
3.2Capacitor discharge stud welding technology...................................................................... 14
3.3Technical data...................................................................................................................... 15
3.4Interfaces BMS-10P............................................................................................................. 16
4Installation of the stud welding system............................................................................ 18
5Start-up................................................................................................................................. 19
5.1View...................................................................................................................................... 19
5.1.1Main switch ...................................................................................................................... 20
5.1.2Description of function keys............................................................................................. 20
5.1.3Description of LED displays............................................................................................. 20
5.1.4Description of display....................................................................................................... 21
5.1.5Fuse element ................................................................................................................... 22
5.1.6Connecting elements ....................................................................................................... 22
5.1.7Description of symbols..................................................................................................... 23
5.2Adjustment of operating modes ........................................................................................... 24
5.2.1Starting the stud welder ................................................................................................... 24
5.2.2Operating modes / parameters........................................................................................ 24
5.3Creating a new welding program ......................................................................................... 25
5.4Copying a welding program ................................................................................................. 26
5.5Deleting welding programs................................................................................................... 26
5.6Preparation for start-up........................................................................................................ 27
5.6.1Earth connection.............................................................................................................. 27
5.6.2Connection of stud welding gun....................................................................................... 27
5.6.3Power supply ................................................................................................................... 27
5.7Welding parameters............................................................................................................. 28
6Operation ............................................................................................................................. 29
6.1Notes on the "Lifting test" operation mode........................................................................... 30

7
6.2Adjustment of stud welding guns ......................................................................................... 31
6.2.1Basic setting of the stud chuck with set screw ................................................................ 31
6.3Start-up of PS-3 stud welding gun ....................................................................................... 32
6.4Start-up of PS-3A welding gun............................................................................................. 34
6.5Quality control...................................................................................................................... 38
6.5.1Setting up the quality control ........................................................................................... 38
6.5.2Subsequent collection or completion of reference values ............................................... 40
6.6Special functions.................................................................................................................. 41
6.6.1Special function "Deleting RAM"...................................................................................... 41
6.6.2Special functions - "Extended submenu"....................................................................... 42
6.6.3Special function "Setting the language. Display of software version number" ................ 43
6.6.4Special function "Setting the feeder times"...................................................................... 43
6.6.5Special function "Setting the feeder operation" ............................................................... 44
6.6.6Special function "Print protocol"....................................................................................... 44
7Quality control (stud welding) ........................................................................................... 47
7.1General instructions............................................................................................................. 47
8Maintenance......................................................................................................................... 48
8.1Important instructions........................................................................................................... 48
8.2Important instructions for all service works.......................................................................... 48
8.3Cleaning............................................................................................................................... 49
8.3.1Detergents for cleaning the housing................................................................................ 49
8.4Replacement of components ............................................................................................... 49
9Troubleshooting.................................................................................................................. 50
9.1Malfunctions......................................................................................................................... 50
10Transport and storage........................................................................................................ 52
11Terms of warranty............................................................................................................... 52
12List of standards and guideline......................................................................................... 53

8
1 Safety instructions
These safety precautions are for your safety.
General safety instructions
Take part in a training programme. Read and follow all safety precautions listed below
and all chapters of this manual before starting to weld.
Non-compliance with the safety precautions can result in personal injuries or
death.
Only qualified persons are allowed to operate and maintain the equipment.
Children and juveniles under the age of 16 years must be kept away from the
equipment.
WARNING
It is prohibited to open the stud welding equipment.
The service personnel are required to meet special qualifications.
Our after-sales service has adequately trained personnel, suitable service equipment
and the means to carry out all necessary works.
Warning of electromagnetic fields
Keep sufficient distance from electronic devices. When stud welding, highly intensive
electromagnetic fields are created which may permanently damage these devices (e.g.
television sets, airbags).
Ensure that the welding equipment is not operated near electronically sensitive life-
support equipment, such as in intensive care units in hospitals.
Persons with pacemakers may neither operate the stud welding equipment nor stay in
the immediate vicinity while it is running.
Electric shock can cause death
Prevent electric shock by insulating your body from the working area and the ground.
Stand on dry insulating material and wear rubber soled shoes.
Inspect all cables including power cord for damage, wear or bare wiring.
Always ensure the correct supply voltage in accordance with the type plate.
Never connect the welding equipment to a power supply network with incorrect supply
voltage.
Always disconnect the welding equipment from the mains supply before starting any
cleaning works. Only trained and appropriately qualified personnel are allowed to carry
out works at the electric mains supply and welding system.
Do not touch live electrical parts with bare hand. Wear dry, hole-free insulating gloves.
Do not wear rings, watches or electrically conductive jewellery.
Keep the work area, studs, guns, cables, energy source as well as your clothes dry.

9
Fumes and gases can cause damage to your health
Fumes and suspended/floating particles may be generated during welding. Beware of
fumes detrimental to health, particularly when using surface treated materials. Please
also observe the safety regulations applicable for your country.
Do not inhale fumes and gases. Use adequate ventilation in the work area to remove
fumes and gases.
Welding can cause fire and explosions
Welding sparks and heat from flames and arcs can cause fires. Keep a portable fire
extinguisher within reach for immediate use. Be sure you are trained to use it.
When welding, do not wear clothes soiled with easily combustible substances such as
oil, grease and paraffin oil etc.
Comply with the fire regulations and do not weld, for instance, in hazardous locations.
Pay attention to flammable objects at the welding place. All flammable materials and
liquids, such as oil, fuel, etc. must be removed prior to the start of work.
Electronic equipment (e.g. airbags) and the use of explosive substances for fuel supply
require further safety precautions when carrying out welding operations on cars.
Appropriate information can be obtained from the trade associations or the car
manufacturers.
Skin and eye protection
Arc rays and welding spatters can injure eyes and skin.
Wear safety glasses with side shields and protective goggles with correct shade of filter
to protect your eyes from welding spatters and flashes of light that are generated during
the welding process.
Wear gauntlet gloves made of leather as well as non-combustible closed working
clothes such as heavy long-sleeve shirts, cuffless pants and safety shoes.
Wear a leather apron to protect your clothes from welding spatters.
Keep sleeves and collars buttoned and remove open pockets from the front side of your
clothing.
We recommend using ear protection. Some welding and working processes may
generate loud noises.

10
1.1 Description of reference signs in the operating instructions
The non-observance of safety instructions such as pictographs and warning words can cause damage
to persons. The safety instructions of this operating manual describe the following.
Safety instructions
Danger!
Warning!
Immediate hazards which could result in serious personal injuries or loss of
life.
Potential hazards which could result in serious personal injuries or loss of
life.
Caution!
Caution!
Potential hazards which could result in minor personal injuries.
Warning of damage.
Note!
Important!
Potential detrimental situation which may cause damage to the product or
to an object surrounding it.
Instructions for application and other useful information facilitating the
proper use of the product.
Safety symbols
The following pictographs for warnings, prohibitions and regulations are used in this manual:
Prohibited for persons
with pacemakers
Prohibited (only in
combination with an
additional safety symbol)
Do not touch
Housing is current-
carrying
Fire extinguisher
Warning of a danger
spot
Warning of dangerous
electric voltage
Warning of
electromagnetic field
Warning of moving
parts
General prohibition
(only in combination
with an additional
safety symbol)
Warning of inflammable
substances
Warning of explosive
substances
Eye protection
required
Protective clothing
required
Ear protection
required
Protective gloves
required
General instructions are marked with the hand symbol.

11
1.2 Staff qualification and training
The staff responsible for operation, maintenance, inspection and assembly must have the respective
qualification for carrying out these works. Field of responsibility, competence and the supervision of
staff must be carefully regulated by the user. If your personnel do not have the necessary knowledge,
they must be trained and instructed. If necessary, this can be done by the manufacturer/supplier on
behalf of the user. Furthermore, the user must ensure that the contents of the operating instructions
have been fully understood by the staff.
The society of welding institutes (GSI: Gesellschaft der Schweißtechnischen Institute mbH) offers the
appropriate training courses for your personnel.
For information on branches, please refer to website http://www.dvs-ev.de.
1.3 Dangers in the case of non-compliance with safety instructions
The non-compliance with safety instructions may not only endanger persons, but also the equipment
and its environment. Any non-compliance with safety instructions may result in a complete loss of
damage claims.
The following dangers may result if the safety instructions are not complied with:
Failure of important system functions
Failure of prescribed methods for maintenance
Danger to persons through electrical, mechanical, thermal and/or acoustic influences.
1.4 Before starting to weld...
Check the state of all cables and cable connections before starting to weld
Immediately replace defective cables and cable connections.
1.5 Working with the stud welding equipment
Comply with all accident prevention regulations applicable to the operation of your welding device.
If an accident happens,
switch off the welding device and disconnect it from the mains supply and
call a doctor
1.6 Inadmissible operating methods
Limit values
The working safety of the stud welding equipment is only guaranteed when the system is used in
accordance with its purpose. The limit values indicated in the chapter “Technical data” must never be
exceeded.
1.7 Stopping the stud welding equipment
Turn off the mains switch of the stud welding equipment.
Disconnect the mains plug from the mains socket.
In case of automatic operation, disconnect the compressed-air supply.
Disconnect the earth cable from the stud welder.
Disconnect welding gun or head from the stud welder.
Roll up the cables without buckling them.
Prevent the stud welder being operated by unauthorized personnel.
Check welding cables and connections of the stud welder for damage such as burn-off,
mechanical wear etc. and have damaged parts replaced by the SOYER customer service.

12
2 General
2.1 The following should be principally observed...
With the BMS-10P stud welder you have purchased a product which
is state-of-the-art technology
fully complies with the current safety requirements and
ensures high performance.
Before installing the stud welder, please observe the following:
Store the operating instructions in a place accessible to every operator.
Ensure that the respective operator has read and understood the operating instructions prior
to start-up. Each operator should confirm this per signature.
Prevent the stud welder being operated by unauthorized personnel.
Only trained personnel may operate the stud welder.
2.2 Intended use
The BMS-10P SOYER stud welder allows you to weld pins and threaded studs from M3 - M8 or Ø 3 -
7.1 mm and many other types of weld fasteners in accordance with DIN EN ISO 13918 (capacitor
discharge) manufactured from steel, stainless steel, aluminium and brass.
If you need consultation or assistance in solving problems, please contact either our parent company
or our field engineers.
2.3 Marketing and service
If you have any questions regarding the operation of the feeder, retrofits for special applications or if
you require service, please contact your responsible service office or the following address:
Heinz Soyer Bolzenschweißtechnik GmbH
Inninger Straße 14
D-82237 Wörthsee
Telephone: +49 8153 8850
Telefax: +49 8153 8030
www.soyer.de
2.4 Information on the documentation
The following operating instructions are supplied with the BMS-10P stud welder:
●Operating instructions for BMS-10P Order no.: P02063
2.4.1 Information on the operating instructions
Legal relationship
We point out that the contents of these operating instructions are neither part of any former or existing
arrangement, pledge or legal relationship nor have they been designed to modify the latter. All
obligations of Heinz Soyer Bolzenschweißtechnik GmbH result from the respective contract of
purchase. This contract also contains the complete and universally valid warranties. These contractual
warranty terms are neither extended nor restricted by the implementation of these operating
instructions.

13
CAUTION
Do not carry out any actions on the stud welding equipment without specifically
knowing the operating instructions or the respective part. Ensure that only qualified
and trained personnel familiar with the operating instructions operate the system.
2.4.2 Conduct in the case of malfunctions
If malfunctions occur, first try to detect and eliminate the causes according to the list in the
"Troubleshooting" chapter of these operating instructions. In all other cases, contact our service
department.
If you require our service, please make sure that you supply us with the following information:
Customer number
Product designation / options
Serial number
Year of construction
Material of stud and workpiece
Stud dimensions
This information helps us save time and unnecessary costs, e.g. incurred by delivering the wrong
spare parts.

14
3 Description of stud welder
3.1 Description
The BMS-10P SOYER stud welder is universally applicable for both manual and automatic operation.
Control via a serial CNC interface is possible.
The BMS-10P stud welder enables the storage of parameters for various welding tasks as welding
programs. These parameters can be recalled at any time. To simplify operation, it is possible to store
programs for different stud diameters. This allows a more rapid and simpler interchange of different
welding tasks. The integrated quality control allows the most important parameters of the weld to be
monitored and any welding faults to be reported when inadmissible deviations occur.
The stud welder is equipped with eight keys, eight light-emitting diodes (LED) and a two-lined text
display at the front panel. The stud welder is adjusted via the keys. The operating state during welding
is shown by the light-emitting diodes and on the display.
3.2 Capacitor discharge stud welding technology
The BMS-10P SOYER stud welder runs according to the principle of capacitor discharge with tip
ignition as defined in DVS Leaflet 0903 (DVS = German Welding Society).
This system uses the sudden discharge of a capacitor battery to generate arc energy.
Stud tip touches workpiece. Ignited arc generates a fusion
zone on stud and workpiece.
Stud is plunged into the
welding pool. Material solidifies
and stud is welded.
For further information, please refer to www.soyer.de
IMPORTANT INFORMATION
Ensure that the surface is electroconductive.
Grind coated parts.

15
3.3 Technical data
Designation BMS-10P
Welding process Capacitor discharge stud welding
Standard gun PS-3
Welding range
M3 - M8 or Ø 3 - 8 mm with steel, stainless steel, aluminium and
brass (M8 or Ø 8 in aluminium and brass conditionally, depending on
the respective requirements)
Power source Capacitor bank with capacitance change-over 33,000 / 99,000 µF
Charging voltage 60 - 200 V infinitely variable up/down
Welding sequence Up to 20 studs/min (depending on stud diameter and type of feed)
Power supply 230 V, 50/60 Hz, 10 A (*2 OPTION 115 V )
Fuse T 10 A (5 x 20 mm time-lag fuse)
Type of cooling F
System of protection IP 21
Dimensions 430 x 220 x 560 mm (w x h x d)
Weight *1 26 kg *1
Colour RAL 5009 azure blue
Technical specifications are subject to change without notice
WARNING
The "S" symbol is the symbol for welding current sources permitted for operation with
increased electrical danger. The "S" symbol on our stud welders refers exclusively to
the welding current circuit and not to the complete stud welding equipment.
*1 Slight deviations are possible depending on accessories.
*2 The BMS-10P stud welder is suitable for operation with 115 V or 230 V. Please refer to the type plate for the current
mains supply.

16
3.4 Interfaces BMS-10P
CNC interface
The CNC interface serves for the control and communication e.g. in conjunction with a CNC stud welding
machine.
PIN Description of 9-pole D-Sub female connector (CNC interface)
1 + 6 Start external Contact releases the welding process.
2 + 7 Signal 1 Weld is OK: Contact is present during operation. It is interrupted in case
of a faulty weld.
Power Contact load: max. 24 V, 200 mA
3 + 8 Signal 2
Stud onto workpiece
Contact is made when stud touches the workpiece.
4 + 9 Signal 3
Charge is ready
Contact is made after the set charging voltage has been reached.
6 + 5 Reset external Error reset, external
Contact resets error messages.
RS 232-interface (bidirectional communication interface)
The RS 232 interface serves as a "printer interface" or as "remote control" e.g. in conjunction with a
CNC stud welding machine. A complete device configuration for the central control via a PC is
possible via the interface. Operation via the eight function keys is therefore no longer necessary.
Technical data of interface: 9-pin plug - Connector pin assignment
PIN Signal Adjustment: 9600 baud
2 RxD 8 Data bits
3 TxD 1 Stop bit
5 Ground no Parity

17
p-Select – interface
Communication interface for the P3-Select/S gun distribution system. This interface serves for the
automatic selection of programs (for further information, please refer to the operating instructions of the
P3-Select gun distribution system).
Feeder – interface
The feeder interface serves as the control and communication of our systems for the automatic stud
reload of e.g. UVR-300 SOYER universal feeders.
Isolated ground receptacle 3.15 A
The isolated ground receptacle exclusively serves as power supply for our universal feeders or
additional accessories such as welding heads.
NOTE
The operating voltage of the isolated ground receptacle corresponds to the current
mains voltage.
CAUTION
The isolated ground receptacle is protected by 3.15 A. Never connect any additional
"appliances" such as stud welders.
Setting the mains voltage for 115 V or 230 V
The BMS-10P stud welder is suitable for two power supply voltages: 115 V or 230 V.
The factory-set mains connection values are indicated on the type plate of the welding equipment.
The mains voltage can be changed by reconnecting the corresponding connection terminals at the
mains transformer.
For further information, please contact your responsible SOYER service office.
CAUTION
If the operating voltage is changed by reconnecting the connection terminals at the
mains transformer, the specifications on the type plate have to be changed
accordingly.
CAUTION
Only authorized specialist electricians are allowed to carry out works at the electric
mains supply!

18
4 Installation of the stud welding system
Only install the stud welder on an even surface. The pads located on the bottom of the
welding equipment guarantee its anti-skid position and serve as vibration dampers.
Although the stud welder is resistant to environmental influences, it should be protected
against dampness and dust.
Please pay particular attention to the bearing strength of the workshop furniture and ensure a
safe and stable position for the welding equipment.
Make sure there is sufficient free space around the air apertures, otherwise the device safety
mechanism will respond and interrupt the welding process.
Install the stud welder close to the welding location.
Ensure sufficient ventilation of the working room when operating the welding system.
NOTE
The casing of the stud welder corresponds to safety class IP 21. Please note that this
system of protection is not suitable for operation or transportation in the rain.
Ensure correct connected loads for electrical connections as indicated on the type
plate.

19
5 Start-up
5.1 View
Front view
1. No function
2. Main switch
3. Fuse element F 1 with
fuse 10 AT
4. LCD display
5. LED displays
6. Function keys
7. Air function "forward"
8. Air function "back"
9. Control cable socket
10. Test jack GUN
11. Test jack EARTH
12. Gun cable socket
13. Earth cable connectors
14. Mains cable
Rear view
15. CNC interface
16. Feeder interface
17. Interface RS 232
18. Interface p-Select
19. Fuse element with fuse
3.15 AT
20. Schuko plug socket 230
V ~ 3.15 A
21. Type plate
22. Compressed-air supply
23. Connection sockets for
the compressed-air
control of the feeder

20
5.1.1 Main switch
Main switch
The main switch is used to switch the stud welder on and off.
5.1.2 Description of function keys
The BMS-10P stud welder has eight function keys at the front panel which allow different types of
functions to be carried out.
Key Description
6.1 "Arrow up" Modification of selected parameters (flashing symbol in display)
6.2 " Arrow down" Modification of selected parameters (flashing symbol in display)
6.3 " Arrow left" Selection of parameters to be modified (shifting of the flashing symbol to the left)
6.4 " Arrow right" Selection of parameters to be modified (shifting of the flashing symbol to the right)
6.5 "ENTER" Creating a new program or copying an existing program
6.6 "DELETE/CLEAR" Deletion of a program
6.7 "HELP" Explanation of the parameters shown in the display
6.8 "LIFT" Activating the lifting magnet of the welding gun
5.1.3 Description of LED displays
The respective operating states may be read via the LED displays.
LED Description
5.1 LED "Ready" LED lights up when capacitor battery has been charged to the set value.
5.2 LED "SOW" LED lights up as soon as the stud touches the workpiece provided the workpiece is
connected to the earth pole of the stud welder.
5.3 LED "Release" LED lights up when pressing the trigger switch of the gun or when the start signal at
the external interface has been activated.
5.4 LED "Lift" LED lights up as soon as the lifting magnet of the gun has been activated.
5.5 LED "Ignition" LED lights up when stud is ignited (welding process).
5.6 LED "Error" LED blinks when the welding parameters are outside the tolerance limit with the
quality control being switched on.
5.7 LED "Quako" LED lights up when the stud welder is equipped with a quality control and when the
quality control works faultlessly.
5.8 LED "External" LED only lights up during internal quality test run (service mode).
Table of contents
Other Soyer Welding System manuals
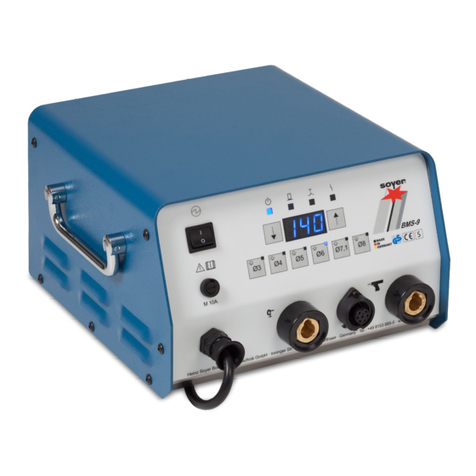
Soyer
Soyer BMS-9 ACCU User manual
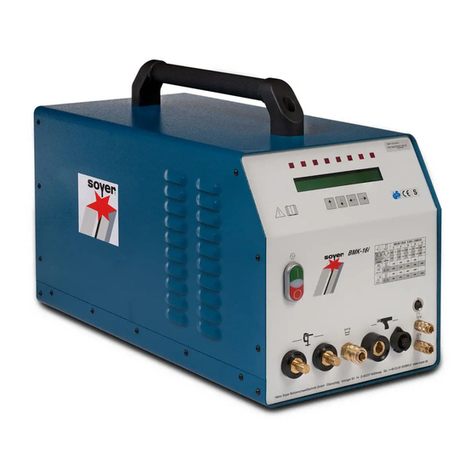
Soyer
Soyer BMK-16i User manual
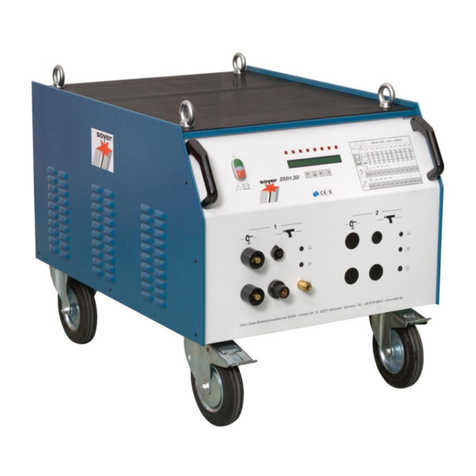
Soyer
Soyer BMH-30i User manual
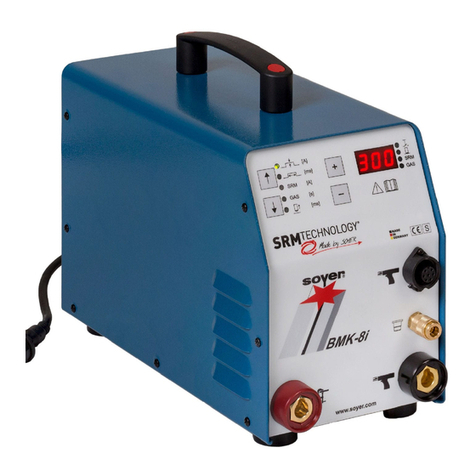
Soyer
Soyer BMK-8i User manual

Soyer
Soyer BMK-16i User manual
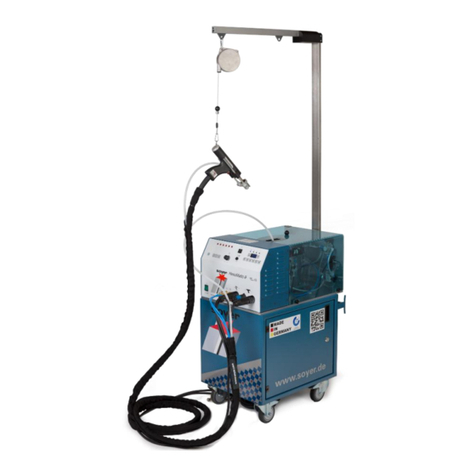
Soyer
Soyer HesoMatic-9 User manual
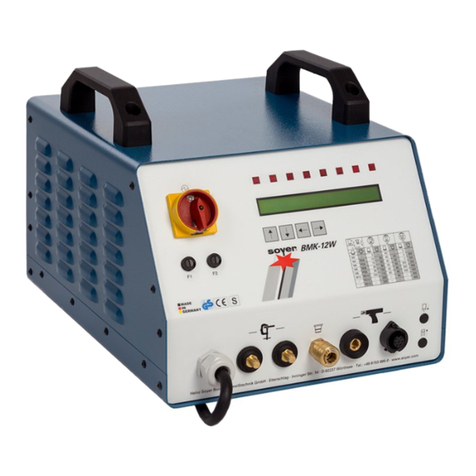
Soyer
Soyer BMK-12 W User manual
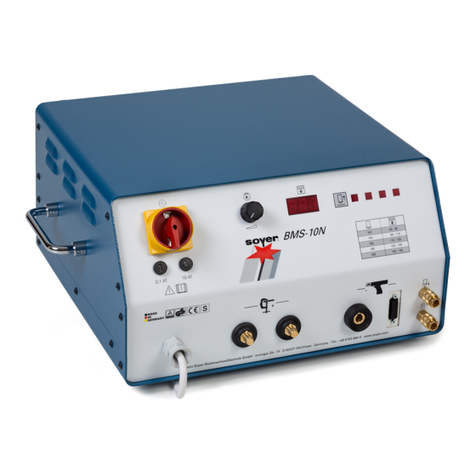
Soyer
Soyer BMS-10N User manual
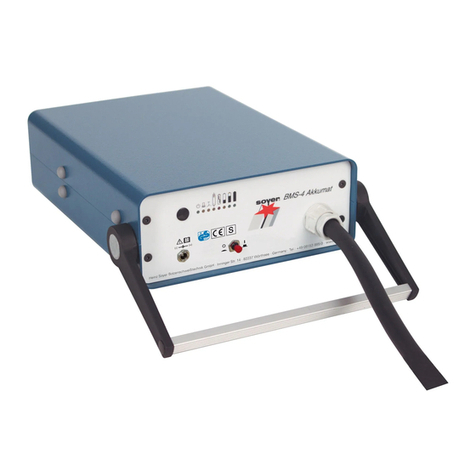
Soyer
Soyer BMS-4 Akkumat User manual
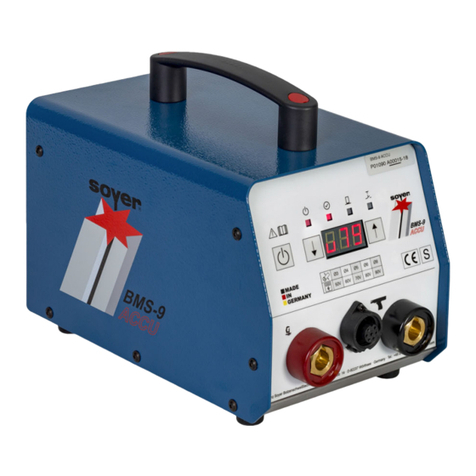
Soyer
Soyer BMS-9 ACCU User manual
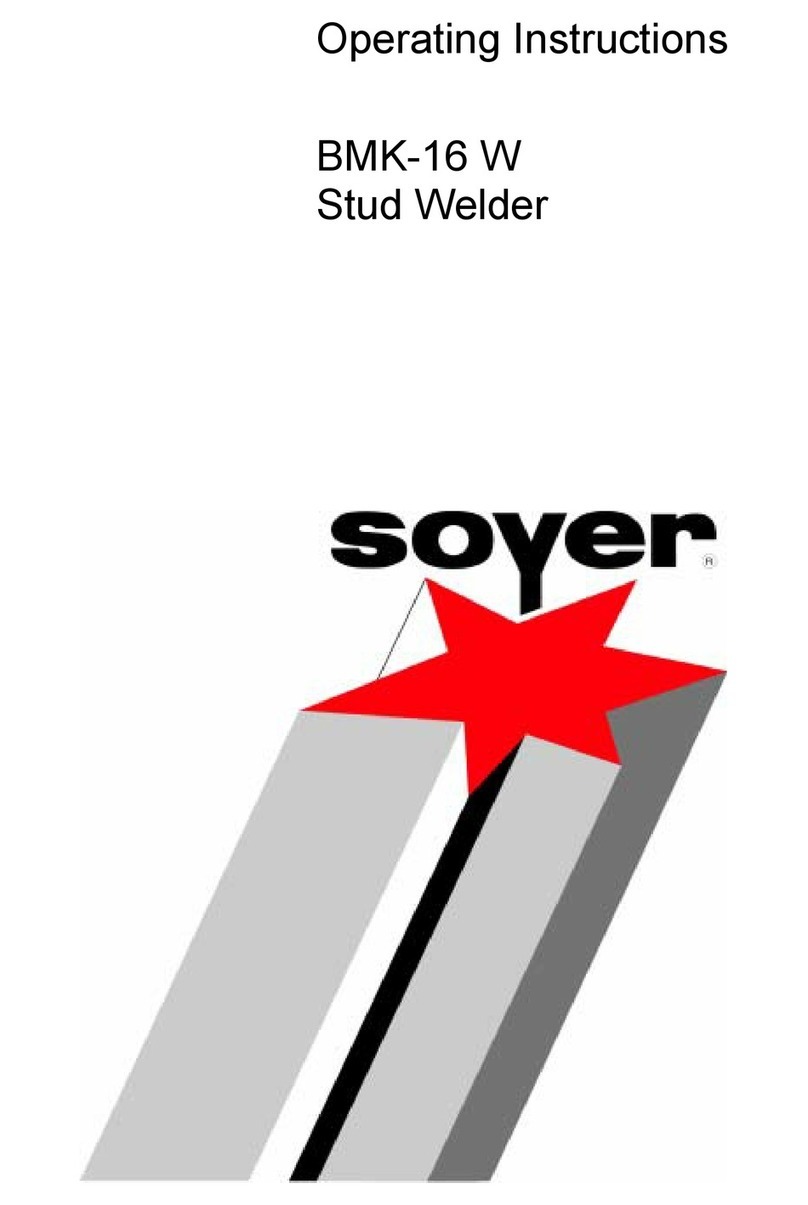
Soyer
Soyer BMK-16 W User manual
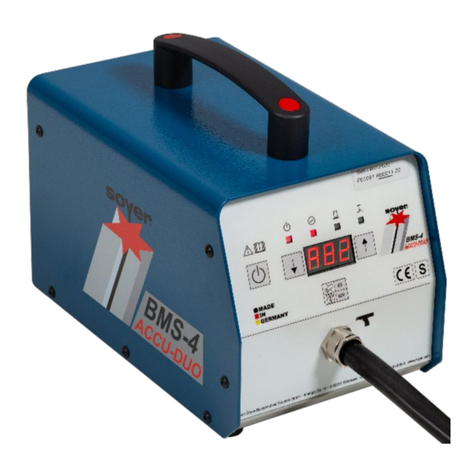
Soyer
Soyer BMS-4 ACCU-DUO User manual
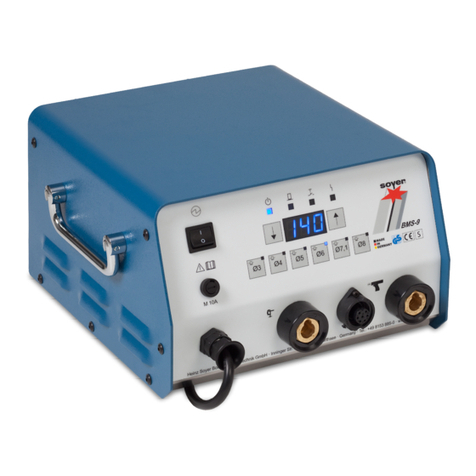
Soyer
Soyer BMS-9 ACCU User manual
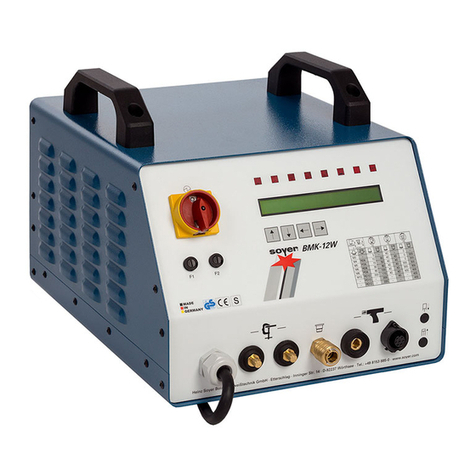
Soyer
Soyer BMK-12 W User manual
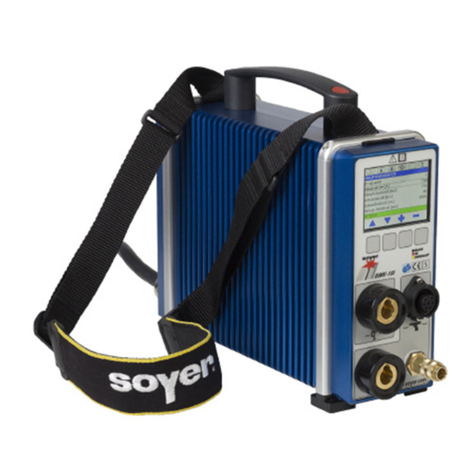
Soyer
Soyer BMK-12i User manual
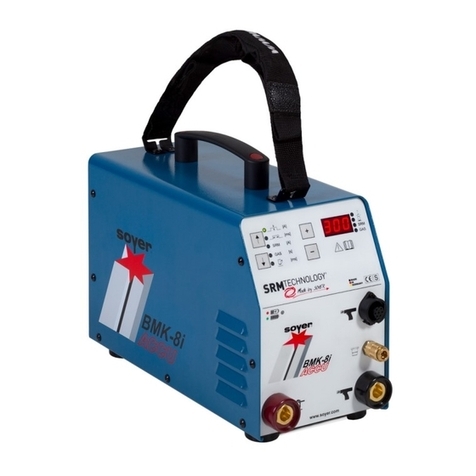
Soyer
Soyer BMK-8i User manual

Soyer
Soyer PH-9 SRM12 User manual

Soyer
Soyer BMK-8 U User manual
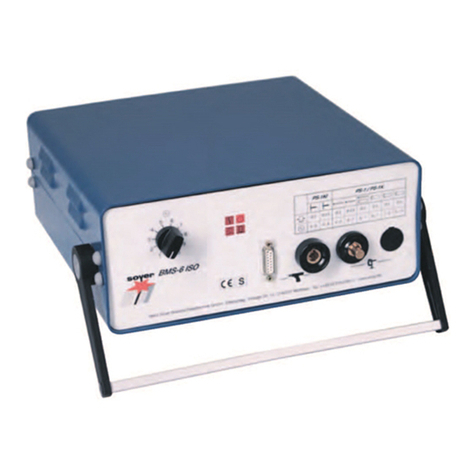
Soyer
Soyer BMS-6 User manual
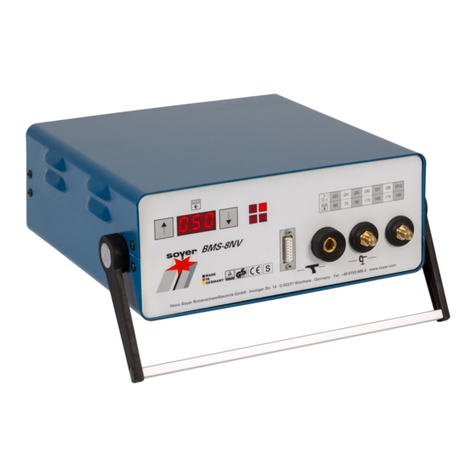
Soyer
Soyer BMS-8N User manual