Stübbe C 110 Series User manual

Ball valve
Operating manual Series C 110
Version BA-2022.07.19 EN
Print-No. 300 876
TR MA DE Rev002
STÜBBE GmbH & Co. KG
Hollwieser Straße 5
32602 Vlotho
Germany
Phone: +49 (0) 5733-799-0
Fax: +49 (0) 5733-799-5000
E-mail: co[email protected]
Internet: www.stuebbe.com
We reserve the right to make technical changes.
Read carefully before use.
Save for future use.

Table of contents
Table of contents
1 About this document ............................... 3
1.1 Target groups ................................. 3
1.2 Other applicable documents ................ 3
1.3 Warnings and symbols ....................... 3
2 Safety instructions ................................. 4
2.1 Intended use .................................. 4
2.2 General safety instructions .................. 4
2.2.1 Obligations of the operating company ...... 4
2.2.2 Obligations of personnel ..................... 4
2.3 Specific hazards .............................. 4
2.3.1 Hazardous media ............................ 4
3 Layout and Function ............................... 4
3.1 Marking ....................................... 4
3.1.1 Type plate ..................................... 4
3.2 Layout ......................................... 5
4 Transport, Storage and Disposal ................. 6
4.1 Unpacking and inspection on delivery ...... 6
4.2 Transportation ................................ 6
4.3 Storage ....................................... 6
4.4 Disposal ....................................... 6
5 Installation and connection ....................... 7
5.1 Preparing for installation ..................... 7
5.1.1 Check operating conditions ................. 7
5.2 Planning pipelines ............................ 7
5.2.1 Designing pipelines .......................... 7
5.3 Installing fitting in pipe ....................... 7
5.3.1 Connection wafer type flange variant ... .... 7
5.3.2 Connection with flange ...................... 7
5.3.3 Connection with sockets or nozzles ........ 7
5.4 Drive and limit switch box ................... 8
5.5 Connection ................................... 8
5.5.1 Electrical connection ......................... 8
5.5.2 Pneumatic connection ....................... 9
5.5.3 Check sense of rotation of drive ............ 9
5.6 Performing the hydrostatic test .............. 9
6Operation ............................................ 9
6.1 Commissioning ............................... 9
6.2 Emergency manual operation ............... 9
6.2.1 Manual emergency operation . .......... ... . 9
7 Maintenance ......................................... 10
7.1 Servicing ...................................... 10
7.2 Maintenance .................................. 10
7.2.1 Removing fitting .............................. 10
7.2.2 Fixing leaks in the port ....................... 10
7.2.3 Fix leakage at ball valve stem ............... 10
7.3 Replacement parts and return .............. 10
8 Troubleshooting .................................... 11
9 Appendix ............................................. 11
9.1 Technical specifications ...................... 11
9.1.1 Mechanical specifications ................... 11
9.2 Flange installation ............................ 12
9.3 Tightening torques ........................... 12
9.4 Operating torques ............................ 12
List of figures
Fig. 1 Type plate (example) ........................ 4
Fig. 2 Layout ......................................... 5
Fig. 3 Attach lifting gear ............................ 6
Fig. 4 Electric drive .................................. 8
Fig. 5 Pneumatic drive .............................. 8
Fig. 6 Pneumatic actuator drive with limit
switches ....................................... 8
Fig. 7 Connect pneumatics ......................... 9
Fig. 8 Tightening torques and immersion
depth .......................................... 12
List of tables
Tab. 1 Other application documents, purpose and
where found .................................. 3
Tab. 2 Warnings and symbols ....................... 3
Tab. 3 Control pressure connections ............... 9
Tab. 4 Troubleshooting .............................. 11
Tab. 5 Mechanical specifications ................... 11
Tab. 6 Tightening torques ........................... 12
Tab. 7 Immersion depth flange screws ............. 12
Tab. 8 Tightening torques ........................... 12
Tab. 9 Operating torques ............................ 12
2 C 110 BA-2022.07.19 EN 300 876

About this document
1 About this document
This manual
• ispartofthefitting
• applies to all series referred to
• describes safe and proper operation during all operating
phases
1.1 Target groups
Operating company
• Responsibilities:
– Keep this manual available at the place of operation,
also for future use.
– Ensure that employees read and observe this manual
and other applicable documents, especially the safety
instructions and warnings.
– Observe any additional country-specific rules and reg-
ulations that relate to the system.
Qualified personnel, fitter
• Mechanics qualification:
– Qualified employees with additional training for fitting
the respective pipework.
• Electrical qualification:
– Qualified electrician
• Responsibility:
– Read, observe and follow this manual and the other
applicable documents, especially all safety instructions
and warnings.
1.2 Other applicable documents
Resistance lists
Resistance of materialsusedtochemicals
www.stuebbe.com/pdf/300051.pdf
Data sheet
Technical specifications, conditions of
operation
www.stuebbe.com/pdf/300882.pdf
CE declaration of conformity
Conformity with standards
www.stuebbe.com/pdf/300168.pdf
Electric drive operating manual
Limit switch box operating manual
Tab. 1 Other application documents, purpose
and where found
1.3 Warnings and symbols
Symbol Meaning
• Immediate acute risk
• Death, serious bodily harm
• Potentially acute risk
• Death, serious bodily harm
• Potentially hazardous situation
• Minor injury
• Potentially hazardous situation
• Material damage
Safety warning sign
Take note of all information
highlighted by the safety warning
sign and follow the instructions to
avoid injury or death.
Instruction
1., 2., ... Multiple-step instructions
Precondition
→Cross reference
Information, notes
Tab. 2 Warnings and symbols
300 876 BA-2022.07.19 EN C 110 3

Layout and Function
2 Safety instructions
The manufacturer accepts no liability for damages caused
by disregarding any of the documentation.
2.1 Intended use
• Only use the fitting to shut off pipes for appropriate media
(→ Resistance list).
• Adhere to the operating limits (→ Data sheet).
• When using media that contains solids, the wear increases.
2.2 General safety instructions
Read and observe the following regulations before carrying
out any work.
2.2.1 Obligations of the operating company
Safety-conscious operation
• Only operate the fitting if it is in perfect technical condition
and only use it as intended, staying aware of safety and
risks, and in adherence to the instructions in this manual.
• Ensure that the following safety aspects are observed and
monitored:
– Intended use
– Statutory or other safety and accident-prevention reg-
ulations
– Safety regulations governing the handling of haz-
ardous substances
– Applicable standards and guidelines in the country
where the pump is operated
• Make personal protective equipment available.
Qualified personnel
• Make sure all personnel tasked with work on the fitting have
read and understood this manual and all other applicable
documents, especially the safety, maintenance and repair
information, before they start any work.
• Organize responsibilities, areas of competence and the
supervision of personnel.
• The following work should be carried out by specialist tech-
nicians only:
– Installation, repair and maintenance work
– Work on the electrical system
• Make sure that trainee personnel only work on the fitting
under supervision of specialist technicians.
2.2.2 Obligations of personnel
• Observe the instructions on the fitting and keep them legi-
ble, e.g. type plate, identification marking for fluid connec-
tions.
• Only carry out work on the fitting if the following require-
ments are met:
– System is empty
– System has been flushed
– System is depressurized
– System has cooled down
– System is secured against being switched back on
again
• Do not make any modifications to the device.
2.3 Specific hazards
2.3.1 Hazardous media
• When handling hazardous media (e.g. hot, flammable,
explosive, toxic, hazardous to health or the environment),
observe the safety regulations for the handling of haz-
ardous substances.
• Use personal protective equipment when carrying out any
work on the fitting.
• Collect leaking pumped liquid and residues in a safe man-
ner and dispose of in accordance with environmental reg-
ulations.
3 Layout and Function
3.1 Marking
3.1.1 Type plate
PP • PTFE
1
2
3
4
C110
PN/DN 10 / 40
Id No 145039
1407-87345 5
Hollwieser Str. 5, DE-32602 Vlotho
Fig. 1 Type plate (example)
1Type
2IDnumber
3 Nominal pressure [bar] / Nominal diameter [mm]
4 Materials (body, ball seals, other gaskets)
5 Date of manufacture - Series number
4 C 110 BA-2022.07.19 EN 300 876

Layout and Function
3.2 Layout
Manually, electrically or pneumatically driven ball valve for
shutting off pipes
• Optional flow direction
• Opening angle OPEN/CLOSE 90°
• Optional installation position
– Position electric drive laterally or over the fitting.
Fig. 2 Layout
1 Housing
2Ball
3 Hand lever
4 Bearing bush
5Use
6–
7 Hexagon socket screw (MD2)
8Ballseal
9 O-ring
10 sealing
11 O-ring
12 O-ring
13 hexagon bolt
14 Washer
15 Socket
16 Flange
300 876 BA-2022.07.19 EN C 110 5

Transport, Storage and Disposal
4 Transport, Storage and
Disposal
4.1 Unpacking and inspection on delivery
1. Unpack the fitting when received and inspect it for transport
damage.
2. Report any transport damage to the manufacturer immedi-
ately.
3. Ensure that the information on the type plate agrees with
the order/design data.
4. For immediate installation, dispose of packaging material
according to local regulations.
– For later installation, leave the fitting in the original
packaging.
4.2 Transportation
DANGER
Death or limbs crushed as a result transported items
falling over or tilting.
Do not stand under suspended loads.
Use lifting gear appropriate for the total weight to be trans-
ported. Weight specification (→ data sheet).
Attach lifting gear in accordance with the following diagram.
Fig. 3 Attach lifting gear
Lift the fitting with properly installed lifting gear and position
it at the place of installation.
4.3 Storage
NOTE
Material damage due to inappropriate storage!
Store the fitting properly.
1. Make sure the storage room meets the following condi-
tions:
–Dry
– Frost-free
– Vibration-free
– Not in direct sunlight
– Storage temperature +10 °C to +60 °C
2. Store fitting in “Valve open” state, if possible in the original
packaging.
4.4 Disposal
Plastic parts can be contaminated by poisonous or radioac-
tive media to such an extent that cleaning will not be suffi-
cient.
WARNING
Risk of poisoning and environmental damage from
medium.
Use personal protective equipment when carrying out any
work on the fitting.
Before disposing of the fitting:
– Collect escaping medium and dispose separately
according to local regulations.
– Neutralize residues of medium in the fitting.
Remove plastic parts and dispose of them in accordance
with local regulations.
Dispose of fitting in accordance with local regulations.
6 C 110 BA-2022.07.19 EN 300 876

Installation and connection
5 Installation and connection
5.1 Preparing for installation
5.1.1 Check operating conditions
1. Ensure the design of the fitting is consistent with the pur-
pose intended:
– Materials used (→ type plate).
– Medium (→ order and design data).
2. Ensure the required operating conditions are met:
– Resistance of body and seal material to the medium
(→ resistance lists).
– Media temperature (→ Data sheet).
– Operating pressure (→ Data sheet).
3. Consult with the manufacturer regarding any other use of
the device.
5.2 Planning pipelines
5.2.1 Designing pipelines
WARNING
Risk of poisoning and environmental damage from
medium.
Leaks due to impermissible pipework forces.
Ensure that the fitting is not subject to any pulling or thrust-
ing forces or bending moments.
1. Plan pipes safely:
– No pulling or thrusting forces
– No bending moments
– Adjust for changes in length due to temperature
changes (compensators, expansion shanks)
– Optional flow direction
– Optional installation position and direction
2. Dimensions (→ Data sheet).
5.3 Installing fitting in pipe
WARNING
Risk of poisoning and environmental damage from
medium.
Leak due to faulty installation.
Installation work on the pipes should only be performed
by technicians who have been specially trained for the
pipework in question.
NOTE
Material damage due to contamination of the fitting!
Make sure no contamination reaches the fitting.
Flush the pipe with a neutral medium.
The fitting is installed according to the connection type of
the pipes.
Any position of the compressed air drive.
Position electric drive laterally or over the fitting.
5.3.1 Connection wafer type flange variant
For installation of the fitting with O-ring, only use flange
adapters or welding stubs with smooth sealing surfaces.
1. Open fitting completely.
2. Prepare pipe ends according to connection type.
3. Screw fitting (→ manufacturers' instructions).
– Observe the maximum screw-in depth
(→ Tab. 7 Immersion depth flange screws, Page 12).
– Observe tightening torques (→ 9.3 Tightening torques,
Page 12).
5.3.2 Connection with flange
1. Open fitting completely.
2. Prepare pipe ends according to connection type.
3. Radially position the fitting and flat seal between the flange
ends.
4. Screw fitting (flange screws, nuts and
washers).
– Observe tightening torques (→ 9.3 Tightening torques,
Page 12).
5.3.3 Connection with sockets or nozzles
1. Open fitting completely.
2. Prepare pipe ends according to connection type.
3. Loosen the screws on the socket or nozzle flange.
4. Connect socket or nozzle flange to pipe ends.
5. Radially position the fitting between the flange ends.
6. Screw fitting (flange screws, nuts and
washers).
– Observe the maximum screw-in depth
(→ Tab. 7 Immersion depth flange screws, Page 12).
– Observe tightening torques (→ 9.3 Tightening torques,
Page 12).
300 876 BA-2022.07.19 EN C 110 7

Installation and connection
5.4 Drive and limit switch box
Limit switch box can only be used with pneumatic drive.
1
3
2
Fig. 4 Electric drive
1 Electric drive
2 Mounting set
3 Housing with ball
3
2
1
Fig. 5 Pneumatic drive
1 Pneumatic drive
2 Mounting set
3 Housing with ball
2
1
3
Fig. 6 Pneumatic actuator drive with limit switches
1 Limit switch box
2 Cable gland
3 Pneumatic drive
5.5 Connection
5.5.1 Electrical connection
DANGER
Risk of electrocution!
All electrical work must be carried out by qualified electri-
cians only.
1. Connect limit switch in electric drive
(→ electric drive operating manual).
2. Connect electric drive (→ Operation instructions for electric
drive).
3. Connect limit switch in limit switch box (→ limit switch box
operating manual).
8 C 110 BA-2022.07.19 EN 300 876

Operation
5.5.2 Pneumatic connection
Solenoid pilot valves are available for control of the pneu-
matic drive (→ Operating instructions for pilot valve):
– 3/2-way valve for single-acting drives
– 5/2-way valve for double-acting drives
CAUTION
Risk of injury from compressed air!
All work on the pneumatic system must be carried out by
qualified technicians.
Fig. 7 Connect pneumatics
A Connection A
B Connection B
Connect compressed air lines to the pneumatic drive
(→ Fig. 7 Connect pneumatics, Page 9 ).
Control pressure to
connection
Function A B
Normally closed (NC) – open
Normally open (NO) –close
Doubleacting(DA) close open
Tab. 3 Control pressure connections
5.5.3 Check sense of rotation of drive
1. Open and close fitting once via drive.
2. Check position of the fitting at the flow indicator:
– Position indicator along the pipe: Fitting opened
5.6 Performing the hydrostatic test
Pressure test using neutral medium, e.g. water.
1. Pressurize the fitting, ensuring
– Test pressure < permissible system pressure
– Test pressure < 1.5 PN
– Test pressure < PN + 5 bar
2. Check the fitting for leaks.
6 Operation
6.1 Commissioning
Fitting correctly installed and connected
WARNING
Risk of injury and poisoning due to medium spraying out.
Use personal protective equipment when carrying out any
work on the fitting.
1. Opening and closing the fitting:
– Hand lever along the pipe: Fitting opened
– Hand lever perpendicular to the pipe: Fitting closed
2. After the initial stresses due to pressure and operating tem-
perature, check if the fitting is sealed.
6.2 Emergency manual operation
Only with electrically driven ball valve.
6.2.1 Manual emergency operation
1
2
1. Ensure that the electricity supply is interrupted for the elec-
tric drive.
2. Set the clutch switch (2) from AUTO to MAN and hold it.
3. Remove the protective cap (1).
4. Turn the actuator shaft with the aid of an adjustable span-
ner until the fitting is in the desired position.
5. Put the protective cap back on.
6. Set the clutch switch back to AUTO.
300 876 BA-2022.07.19 EN C 110 9

Maintenance
7 Maintenance
WARNING
Risk of injury and poisoning due to hazardous media liq-
uids!
Use personal protective equipment when carrying out any
work on the fitting.
7.1 Servicing
1. Visual and function check (every three months):
– Normal operating conditions unchanged
–Noleaks
– No unusual operating noises or vibrations
2. Ensure that fitting functions properly (opening, closing)
3. Clean fitting with a moist cloth if necessary.
4. Fail safe version:
– Open and close the fitting once in emergency operation
(battery operation without supply voltage)
– in the case of safety-related applications, replace the
battery yearly
– otherwise replace the batteries every 3 years
7.2 Maintenance
DANGER
Risk of electrocution!
All electrical work must be carried out by qualified electri-
cians only.
WARNING
Risk of injury and poisoning due to hazardous or hot
media.
Use personal protective equipment when carrying out any
work on the fitting.
Safely collect the media and dispose of it in accordance
with environmental regulations.
WARNING
Risk of injury during disassembly!
Wear protective gloves, components can be very sharp-
edged due to wear or damage.
Remove components with springs (e.g. pneumatic drive)
carefully, since spring tension can cause components to
be ejected.
7.2.1 Removing fitting
1. Ensure that:
– System is empty
– System has been flushed
– System is depressurized
– System has cooled down
– System is secured against being switched back on
again
2. Remove fitting from the pipe.
3. Decontaminate fitting if required.
– Dead space in the fitting may still contain medium.
7.2.2 Fixing leaks in the port
1. Removing fitting (→ 7.2.1 Removing fitting, Page 10).
2. Replace ball seals and/or ball.
3. Install fitting (→ 5.3 Installing fitting in pipe, Page 7 ).
7.2.3 Fix leakage at ball valve stem
1. Removing fitting (→ 7.2.1 Removing fitting, Page 10).
2. Replace the O-rings on the ball valve stem.
3. Install fitting (→ 5.3 Installing fitting in pipe, Page 7 ).
7.3 Replacement parts and return
1. Have the following information ready to hand when order-
ing spare parts (→ type plate).
– Fitting type
– ID number
– Nominal pressure and diameter
– Body and seal material
2. Please complete and enclose the document of compliance
for returns (→ www.stuebbe.com/en/service/downloads).
3. Only use spare parts from STÜBBE.
10 C 110 BA-2022.07.19 EN 300 876

Appendix
8 Troubleshooting
WARNING
Risk of injury and poisoning due to hazardous or hot
media.
Use personal protective equipment when carrying out any
work on the fitting.
Safely collect the media and dispose of it in accordance
with environmental regulations.
Consult with the manufacturer regarding faults which are not
identified in the following table, or which cannot be traced to
the indicated causes.
Error Possible cause Corrective action
Medium is leaking out of the flange Pre-tension of the O-ring too small Retighten flange fittings
(→ 9.2 Flange installation, Page 12).
Medium leakage at the stem O-ring worn Replace fitting.
Fitting does not close completely Ball seals worn
Ball worn
(→ 7.2.3 Fix leakage at ball valve
stem, Page 10).
Tab. 4 Troubleshooting
9 Appendix
9.1 Technical specifications
Technical data (→ data sheet).
9.1.1 Mechanical specifications
Size Value
Process conditions (medium)
Pressure and temperature → Data sheet
Pressure loss curve → Data sheet
Flow characteristic → Data sheet
Materials in contact with medium
Ball PVC-U, PP, PVDF
Ball seal PTFE
Seals FPM, EDPM
Housing PVC-U, PP, PVDF
Tab. 5 Mechanical specifications
300 876 BA-2022.07.19 EN C 110 11

Appendix
9.2 Flange installation
I
F
MD
MD1
MD1
Fig. 8 Tightening torques and immersion depth
Tightening *1) MD [Nm]
for the versions
d
[mm]
DN
[mm]
Flat sealing
ring
max. 10 bar
max. 40 °C
Profile seal
max. 16 bar
O-ring
max. 16 bar
75 65 35 20 20
90 80 35 20 20
110 100 35 20 20
140 125 45 30 25
160 150 55 35 30
Tightening*1) MD1 [Nm]
for the version O-ring
max. 16 bar
Wafer type flange,
all sizes 20
Tab. 6 Tightening torques
1) Use torque wrench
Max. immersion depth flange screws
[mm] for the sizes
Description
75
(M16)
90
(M16)
110
(M16)
140
(M16)
160
(M20)
Immersion depth
(l) 20 20 20 20 30
Tab. 7 Immersion depth flange screws
9.3 Tightening torques
Description Size Tightening
torque [Nm]
Hexagon socket
screws (MD2)
(→ Fig. 2 Layout, Page 5 ).
DN75
DN90
DN110
DN140
DN150
20
Tab. 8 Tightening torques
9.4 Operating torques
The specified values are standard values for a manually
operated ball valve under the following conditions:
– Water (H2O)
– Media temperature 20 ºC
Torque [Nm] for size DN
Materials
75 90 110 140 150
PVC-U /
PP / PVDF 25 40 50 50 80
Tab. 9 Operating torques
12 C 110 BA-2022.07.19 EN 300 876
Table of contents
Other Stübbe Control Unit manuals
Popular Control Unit manuals by other brands
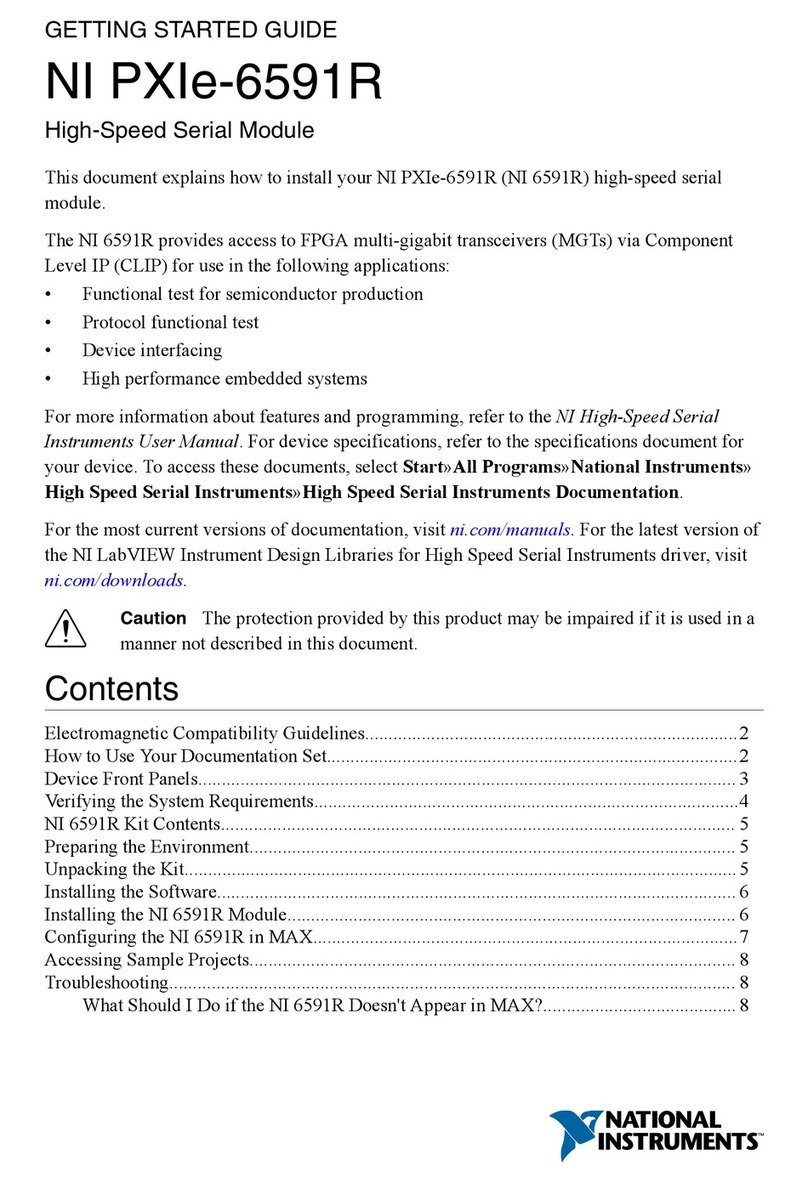
National Instruments
National Instruments PXIe-6591R Getting started guide
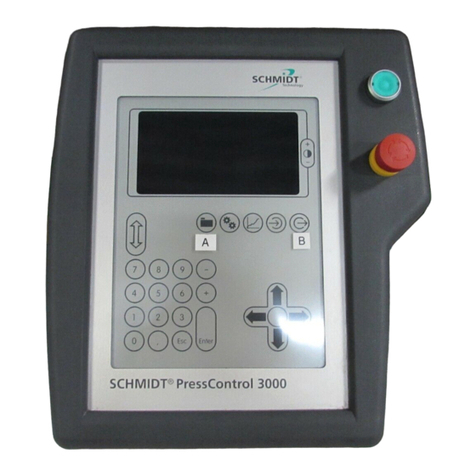
Schmidt
Schmidt PressControl 3000 Operator's manual

Nice
Nice TTPRO BD Instructions and warnings for installation and use

Cree
Cree CR Series installation instructions

HORNER
HORNER HE800PCU100 Configuration

Regulus
Regulus TVMIX 3/4F instruction manual