Tektronix 3177 User manual




















Other Tektronix Measuring Instrument manuals

Tektronix
Tektronix 7L5 User manual
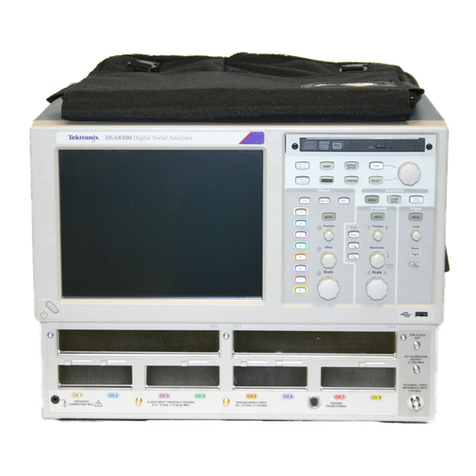
Tektronix
Tektronix DSA8300 Operating and maintenance manual
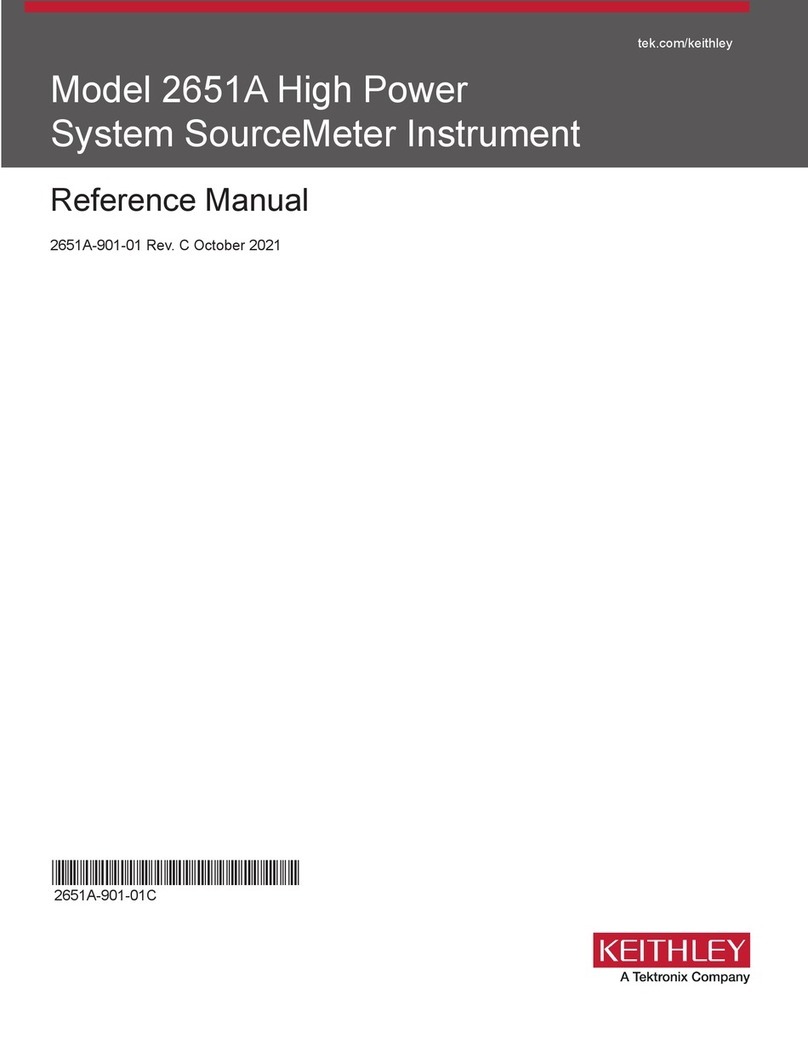
Tektronix
Tektronix Keithley 2651A User manual
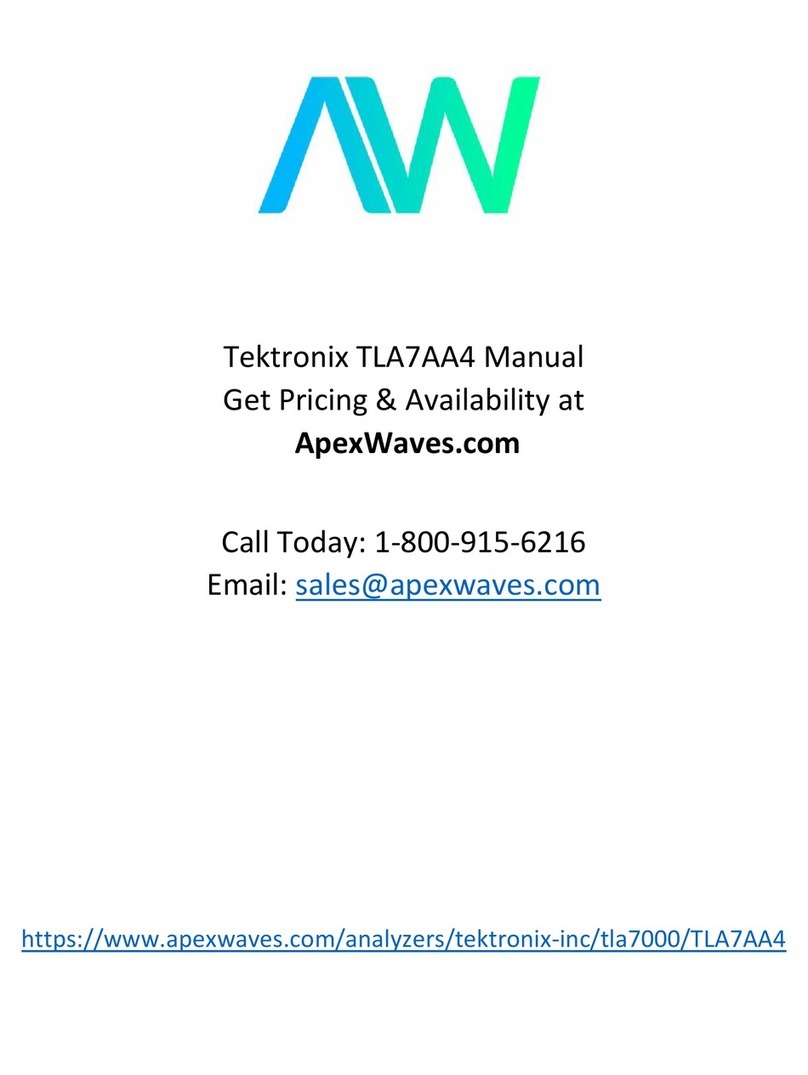
Tektronix
Tektronix TLA7AA1 User manual
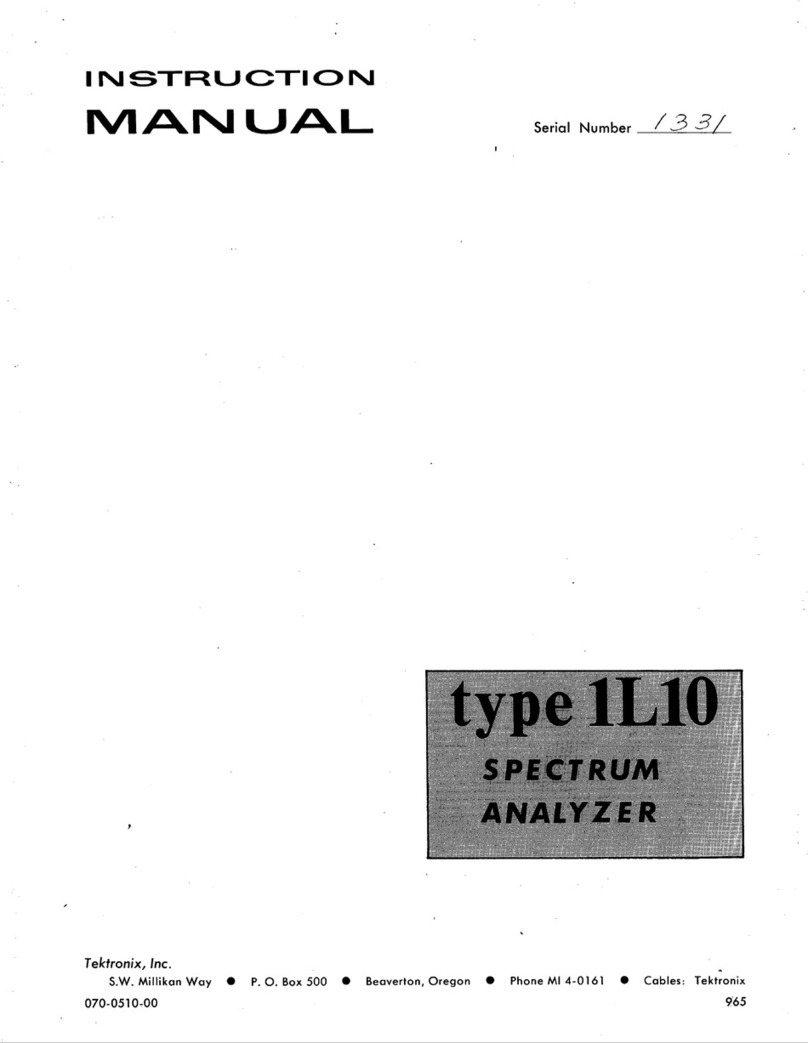
Tektronix
Tektronix 1L10 User manual
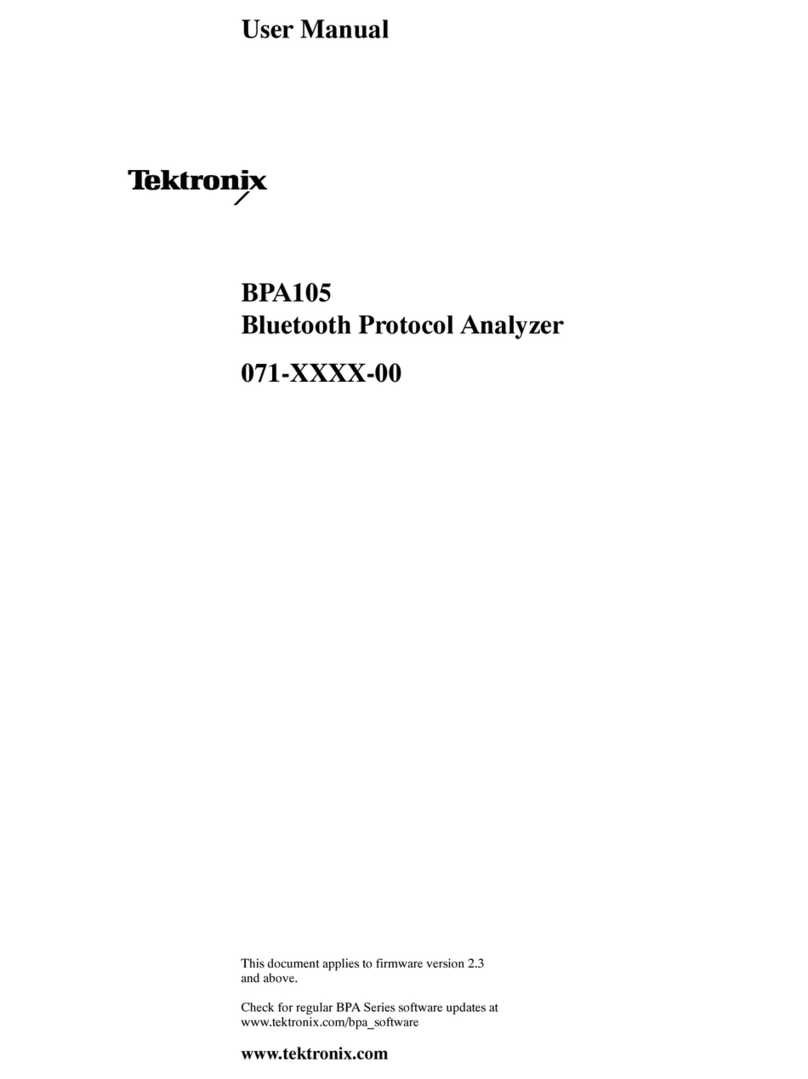
Tektronix
Tektronix BPA105 User manual
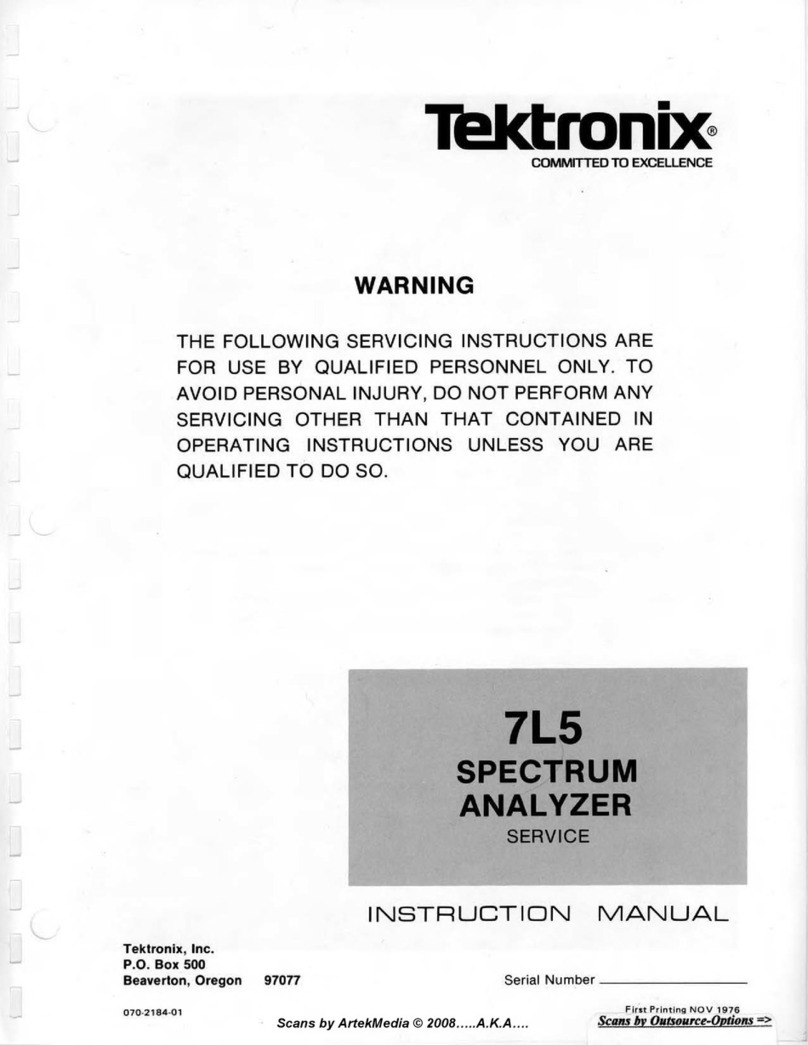
Tektronix
Tektronix 7L5 User manual
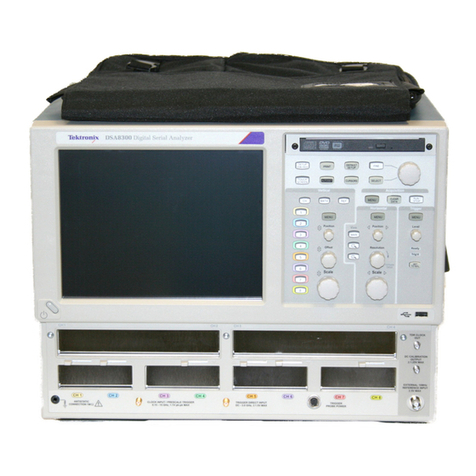
Tektronix
Tektronix DSA8300 Manual
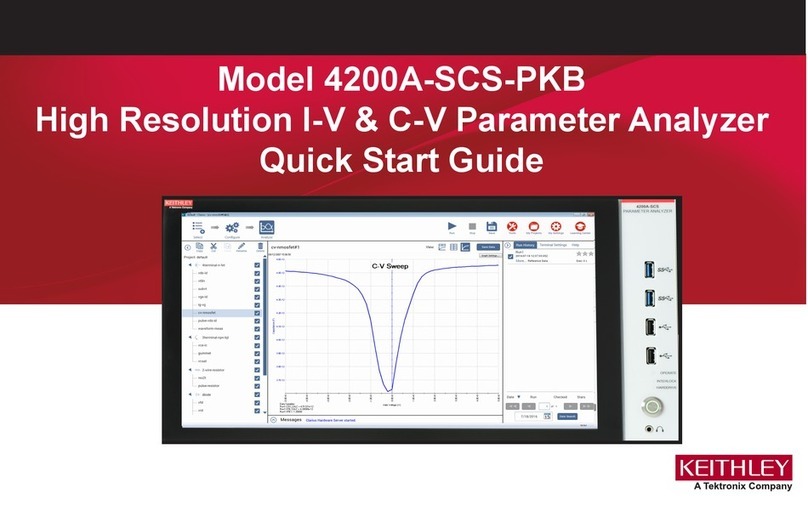
Tektronix
Tektronix KEITHLEY 4200A-SCS-PKB User manual
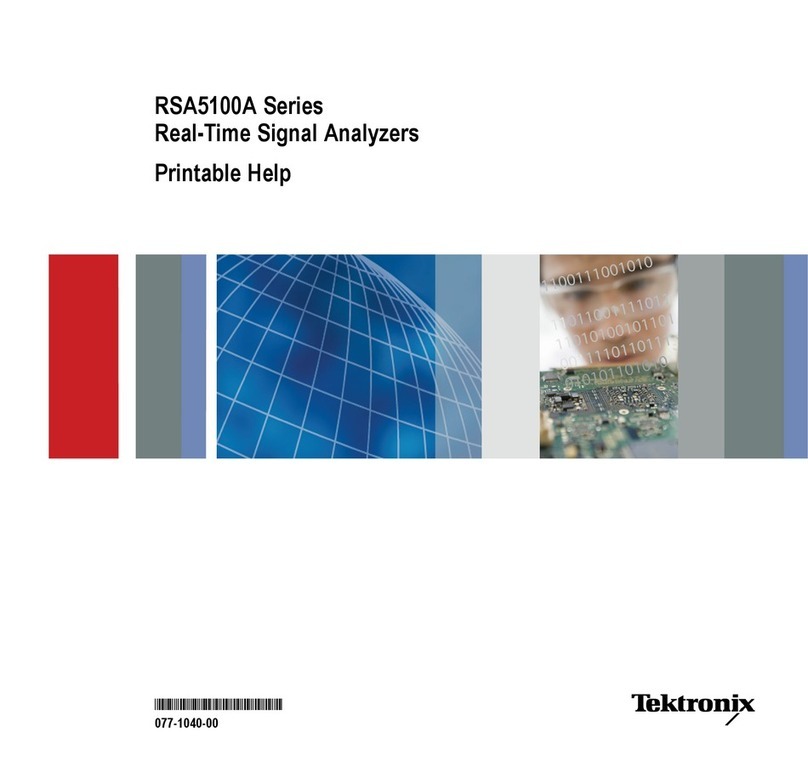
Tektronix
Tektronix RSA5100A Series Reference guide
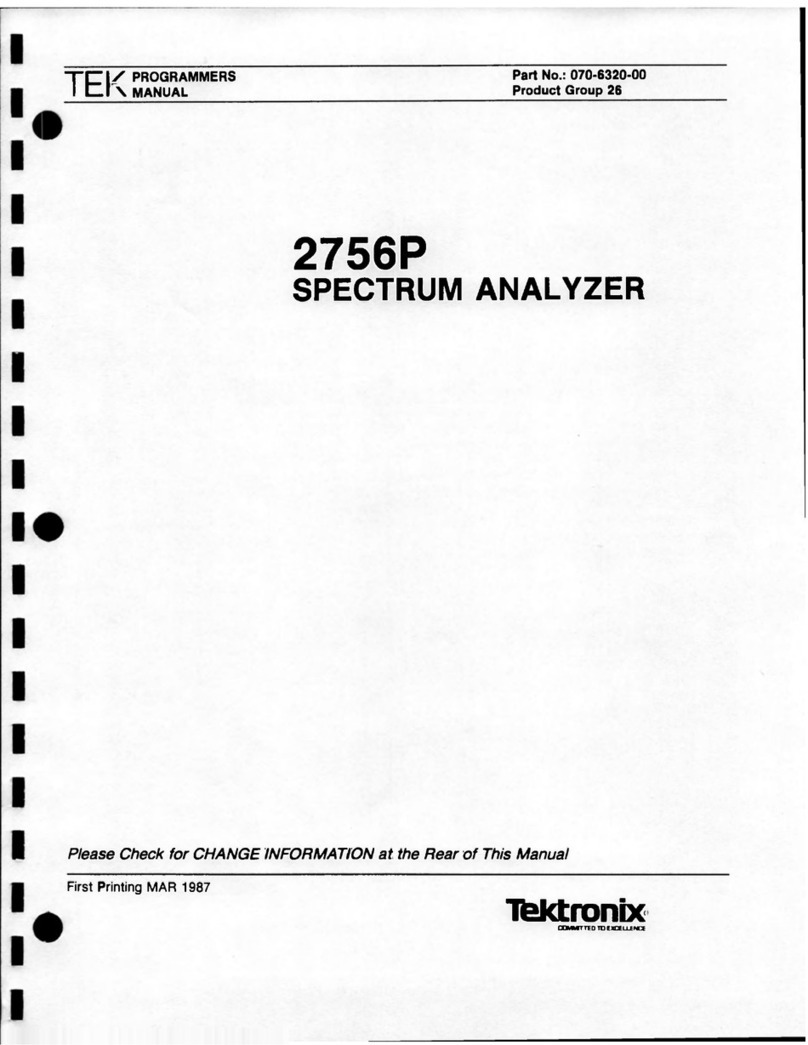
Tektronix
Tektronix 2756P Operating and maintenance manual
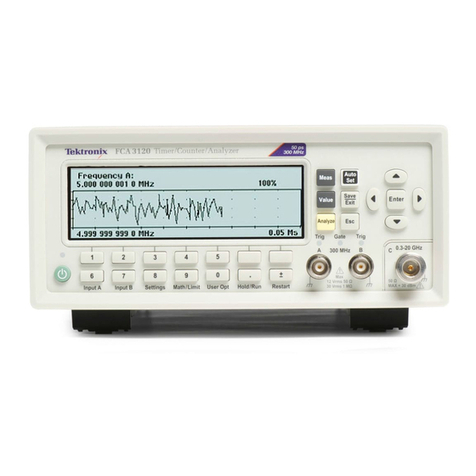
Tektronix
Tektronix FCA3000 Series Operating and maintenance manual
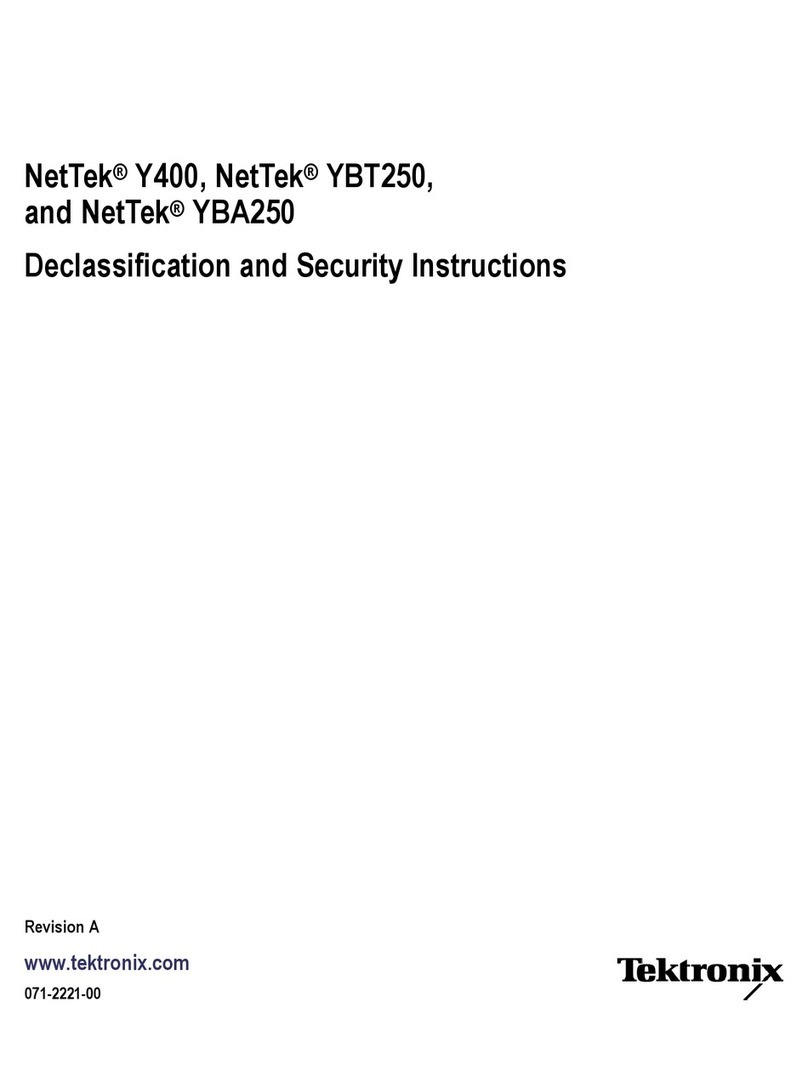
Tektronix
Tektronix NetTek Y400 Installation and maintenance instructions
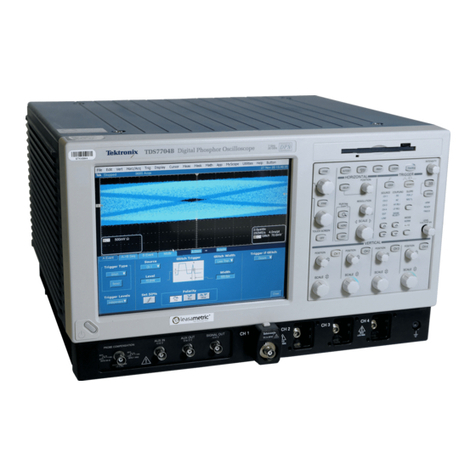
Tektronix
Tektronix CSA7404B User manual

Tektronix
Tektronix 7D01 Reference manual

Tektronix
Tektronix MTS4000 MPEG Manual
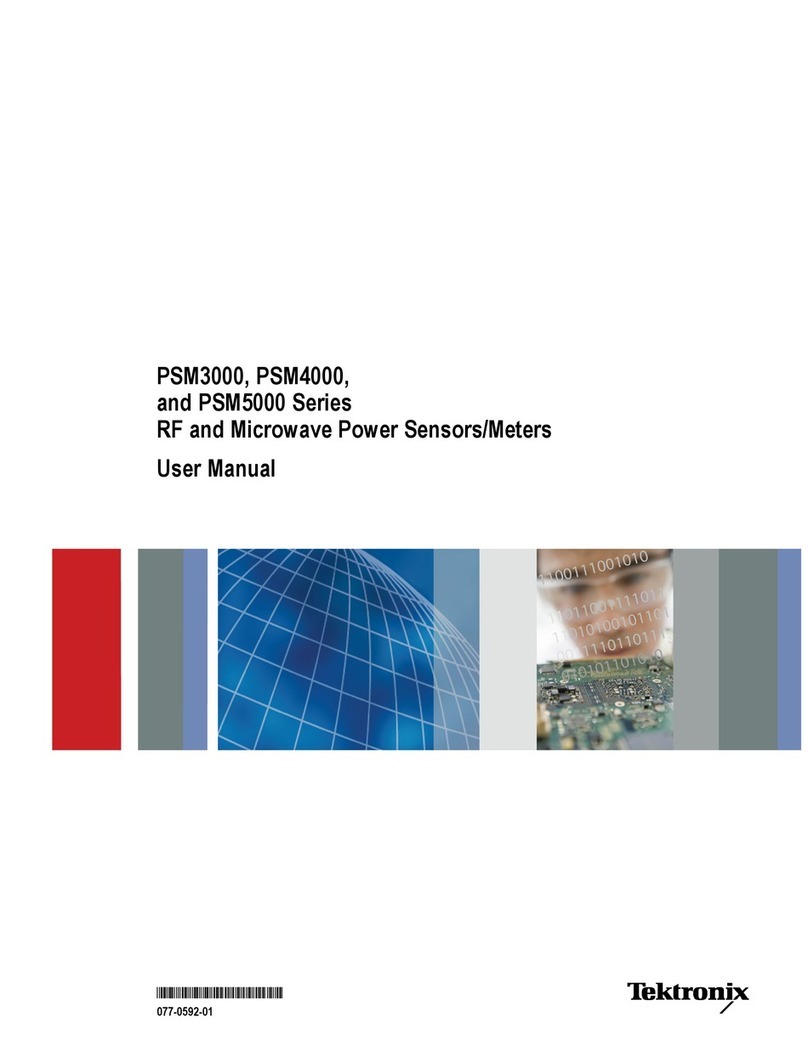
Tektronix
Tektronix PSM3000 Series User manual
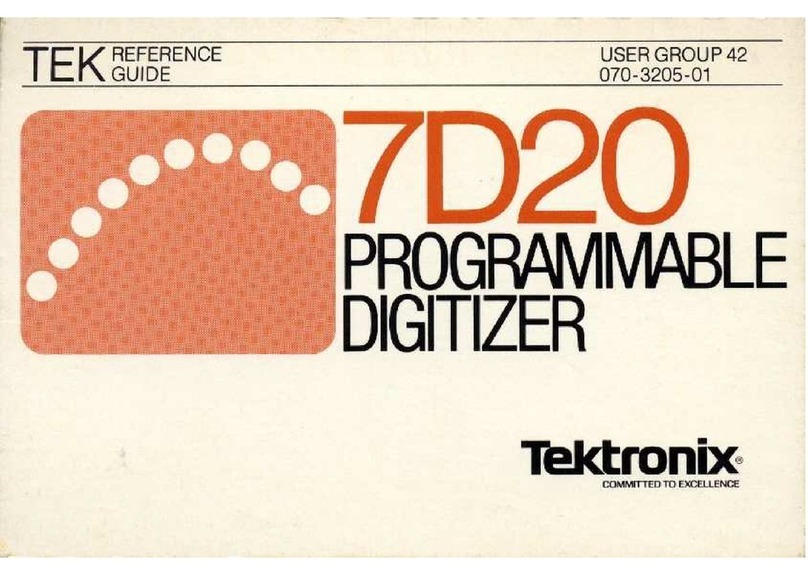
Tektronix
Tektronix 7D20 User manual
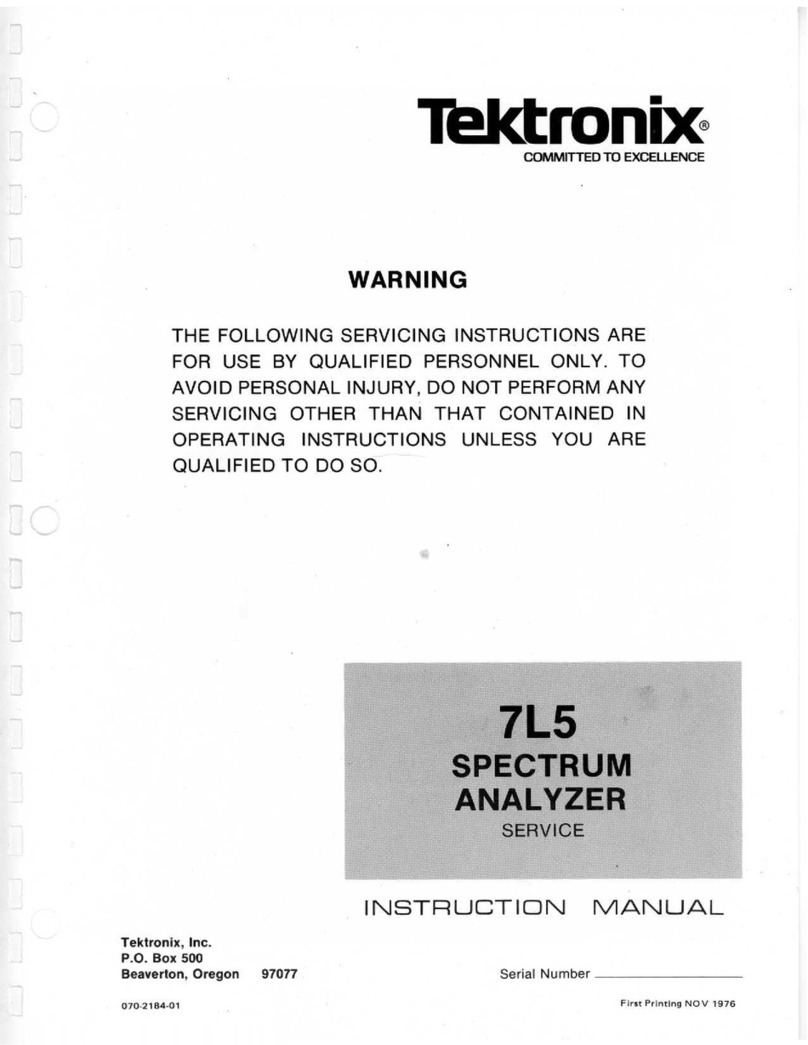
Tektronix
Tektronix 7L5 User manual
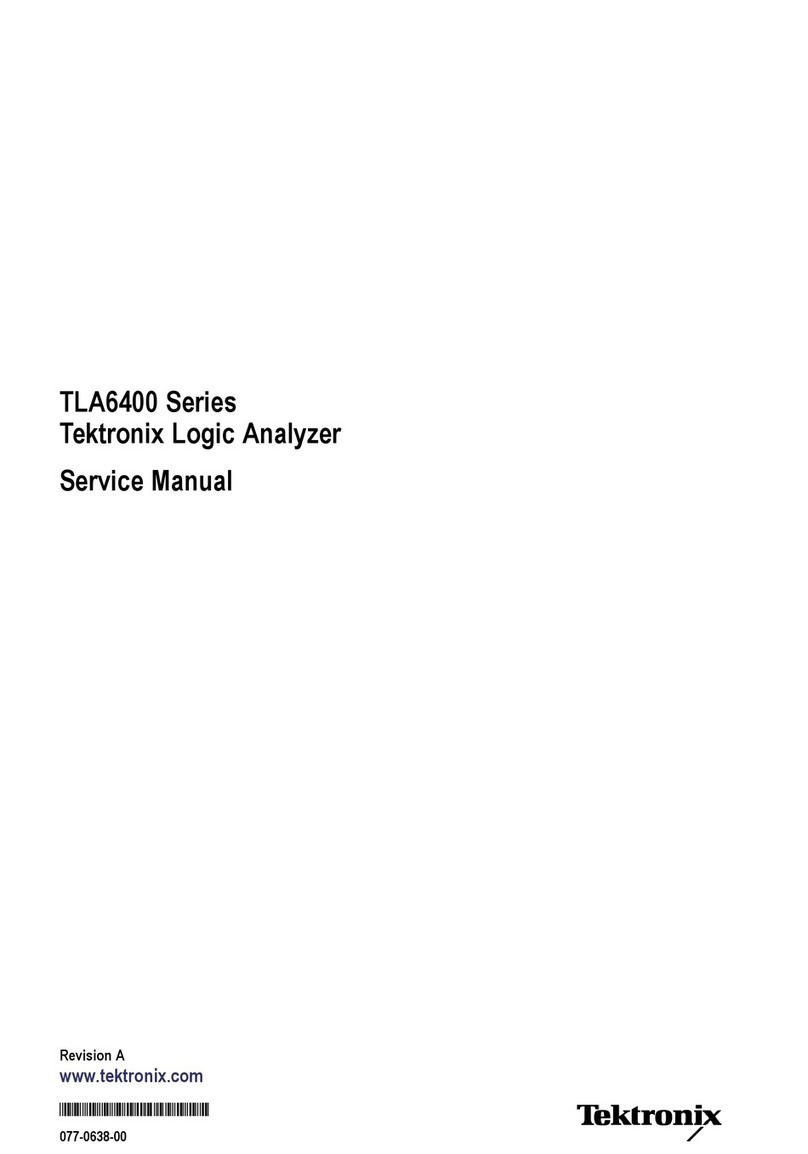
Tektronix
Tektronix TLA6400 Series User manual