THORLABS ELL6 User manual

ELL6(K)
Dual Position Slider Kit
Operating Manual
Original Instructions

Table of Contents
Chapter 1 Introduction.......................................................................................................................... 1
Chapter 2 Safety .................................................................................................................................... 2
2.1. General Warnings and Cautions....................................................................................2
Chapter 3 Description ........................................................................................................................... 3
3.1. Environmental Conditions..............................................................................................3
3.2. Mounting ..........................................................................................................................4
Chapter 4 Operation .............................................................................................................................. 6
4.1. Introduction .....................................................................................................................6
4.2. Controlling the Stage ......................................................................................................6
4.2.1. Hand-held Controller ............................................................................................................. 7
4.2.2. Elliptec Software Control ....................................................................................................... 8
4.2.3. Communications Protocol ..................................................................................................... 9
4.2.4. Connecting Multiple Devices ................................................................................................. 9
4.2.5. Controlling the Stage without the handset ............................................................................ 9
4.3. Frequency Search .........................................................................................................11
4.3.1. Dynamic Frequency Search ................................................................................................ 11
4.4. Periodic Cycling of Devices Over Full Range of Travel.............................................12
4.5. Restoring Factory Settings ..........................................................................................12
4.6. Simultaneous Movement of Devices ...........................................................................12
Chapter 5 Troubleshooting and FAQ.................................................................................................13
5.1. Frequently Asked Questions........................................................................................13
5.2. Notes on Making a Picoflex Cable for Use when Daisy Chain Devices ...................14
Chapter 6 Specifications .....................................................................................................................16
Chapter 7 Regulatory ...........................................................................................................................17
7.1. Declarations of Conformity ..........................................................................................17
7.1.1. For Customers in Europe .................................................................................................... 17
7.1.2. For Customers In The USA ................................................................................................. 17
Chapter 8 Thorlabs Worldwide Contacts..........................................................................................18

ELL6K Dual Position Optics Slider Kit Chapter 1: Introduction
Rev. G, April 2018 Page 1
Chapter 1 Introduction
The ELL6 dual position slider for SM1 optics is part of the Thorlabs series of piezoelectric resonant motor circuits
and bare modules for OEM applications. The resonant piezo design of these motors offers fast response times and
precise positioning, and are therefore particularly useful in scanning applications. These piezo motors also do not
include magnets like traditional motors, making them ideal for applications that are sensitive to electromagnetic
interference.
The high-speed digital signal processing (DSP) architecture supports a multi-drop serial communication protocol,
and a set of digital IO lines allows the user to control the movement and state manually by switching the lines high
(5V) or low (0V).
The slider features two mounting positions for SM1 optics. It can be post-mounted using our ER series cage system
rods and a CP02(/M) Cage Plate and is also compatible with 30 mm cage systems. It offers 31 mm (1.2”) of travel
with 100 µm repeatability and a switching time of 180 to 270 ms. The module is powered via a 5V power connector
or via USB.
A hand-held controller is supplied with the ELL6K evaluation kit to allow manual switching between the two
positions. The unit can also be driven remotely via PC-based software, downloaded from www.thorlabs.com. A
compatible USB driver is included in the software download package.

ELL6K Dual Position Optics Slider Kit Chapter 2: Safety
Page 2DTN000414-D02
Chapter 2 Safety
For the continuing safety of the operators of this equipment, and the protection of the equipment itself, the operator
should take note of the Warnings, Cautions and Notes throughout this handbook and, where visible, on the product
itself.
Warning: Risk of Electrical Shock
Given when there is a risk of electrical shock.
Warning
Given when there is a risk of injury to the user.
Caution
Given when there is a possibility of damage to the product.
Note
Clarification of an instruction or additional information.
2.1. General Warnings and Cautions
Warning
If this equipment is used in a manner not specified by the manufacturer, the protection provided by the equipment
may be impaired. In particular, excessive moisture may impair operation.
The equipment is susceptible to damage from electrostatic discharge. When handling the device, anti-static
precautions must be taken and suitable discharge appliances must be worn.
Spillage of fluid, such as sample solutions, should be avoided. If spillage does occur, clean up immediately using
absorbent tissue. Do not allow spilled fluid to enter the internal mechanism.
If the device is operated over a prolonged time period, the motor housing may become hot. This does not affect
motor operation but may cause discomfort if contacted by exposed skin.
Do not bend the PCB. A bending load in excess of 500 g applied to the board may cause the PCB to deform, which
will degrade the performance of the controller.

ELL6K Dual Position Optics Slider Kit Chapter 3: Description
Rev. G, April 2018 Page 3
Chapter 3 Description
3.1. Environmental Conditions
Warning
Operation outside the following environmental limits may adversely affect operator safety.
Location Indoor use only
Maximum altitude 2000 m
Temperature range 15°C to 40°C
Maximum Humidity Less than 80% RH (non-condensing) at 31°C
To ensure reliable operation the unit should not be exposed to corrosive agents or excessive moisture, heat or dust.
Do not expose the stage to magnetic fields as this could affect the positioning and homing sensor operation.
If the unit has been stored at a low temperature or in an environment of high humidity, it must be allowed to reach
ambient conditions before being powered up.
The unit is not designed to be used in explosive environments.
The unit is not designed for continuous operation. Typical lifetime is 3.3 million switching operations, which equates
to 100 km of travel – see Chapter 5 for more details.

ELL6K Dual Position Optics Slider Kit Chapter 3: Description
Page 4DTN000414-D02
3.2. Mounting
Warning
The safety of any system incorporating this equipment is the responsibility of the person performing the installation.
Caution
Although the module can tolerate up to 8kV of air discharge, it must be treated as ESD sensitive device. When
handling the device, anti-static precautions must be taken and suitable and discharge appliances must be worn.
When handling the stage, take care not to touch the wires to the motors.
Do not bend the wires over the motor spring as this affects the performance of the unit.
Do not allow the wires to contact other moving parts.
The ribbon cable connector is made of plastic and is not particularly robust. Do not use force when making
connections. Unnecessary or repeated plugging in and unplugging should be avoided or the connector may fail.
Do not move the stage by hand. Doing so will disorientate the motors and cause the unit to fail.
The recommended mounting orientation is vertically, with the motor at the bottom of the board as shown below:
Figure 1 Recommended orientation
NOTE
J1 on the reverse side of the board is reserved for future use and is not mounted at this time.

ELL6K Dual Position Optics Slider Kit Chapter 3: Description
Rev. G, April 2018 Page 5
There are several options for mounting the sliders. The ELLA1 Post Mount Adapter, which is available below, has
a 14.0 mm width and fastens directly to the back of the slider's PCB. As shown in Figure 2, the adapter can then
be used to mount the slider to a Ø1/2" post. The compact dimensions of the ELLA1 allows sliders to be placed
one behind the other while minimizing the space separating them, as shown below. The adapter can also be
integrated with Thorlabs' 30 mm Cage System components and/or SM1-threaded components, such as lens
tubes. Alternately, 30 mm cage system components alone can be used to mount the sliders. An example of this is
shown in Figure 23, in which a CP02 Cage Plate, four ER1 rods, a Ø1/2" post, and a post holder mount and
support the assembled ELL6K.
Figure 2 ELL6 mounted using ELLA1 Figure 3 ELL6 mounted using 30 mm cage rods
Figure 4 Close mounting of ELL6 and ELL9 using ELLA1

ELL6K Dual Position Optics Slider Kit Chapter 4: Operation
Page 6DTN000414-D02
Chapter 4 Operation
4.1. Introduction
Caution
Although the module can tolerate up to 8kV of air discharge, it must be treated as an ESD sensitive device. When
handling the device, anti-static precautions must be taken and suitable and discharge appliances must be worn.
Do not expose the slider to a strong infrared light (e.g. direct sunlight) as it could interfere with the operation of the
position sensor.
When power is applied, do not connect or disconnect the ribbon cable connecting the USB/PSU adapter to the Stage
PCB. Always remove power before making connections.
Do not move the stage by hand. Doing so will disorientate the motors and cause the unit to fail.
Warning
If the device is operated over a prolonged time period, the motor housing may become hot. This does not affect
motor operation but may cause discomfort if contacted by exposed skin.
1. Perform the mechanical installation as detailed in Section 3.2
2. Connect the handset to the stage.
Caution
The unit is easily damaged by connections with incorrect polarity. Pin 1 of the connector on the PCB is marked with
an arrow (see Figure 7 and section 5.2) which should be adjacent to the red wire in the connecting cable.
3. Connect the stage to a 5V supply and switch ‘ON’. (A 5V PSU is supplied with the ELL9K).
4. Connect the unit to your PC if required, and wait for the drivers to be installed.
4.2. Controlling the Stage
The stage can be controlled in three ways; via the handset, by the Elliptic software running on a PC, or by writing a
custom application using the messages described in the communications protocol document. Homing and Jogging
functionality can also be accessed by applying voltages to the digital lines on Connector J1. The modes of control
are described in the following sections.
In all modes, when the unit is mounted in the recommended orientation as shown in Figure 1, Forward moves the
stage to the right and backward moves to the left as shown in Figure 5.
Forwards Backwards and Home
Figure 5Slider direction details

ELL6K Dual Position Optics Slider Kit Chapter 4: Operation
Rev. G, April 2018 Page 7
4.2.1. Hand-held Controller
Caution
On power up the stage will move while the unit checks the sensors and then searches for the home position.
The ELL6K Evaluation Kit also contains a hand-held controller, which features two buttons (marked FW and BW)
that allow manual switching between the two slider positions. The handset also provides for connection to the
host PC and/or to an external 5V power supply. The external PSU connector allows the slider to be used in the
absence of a PC, with control being achieved via the handset buttons.
LED1 is lit when power is applied to the unit. LED2 is lit when the device being driven is in motion. Note. The JOG
button has no function and is reserved for future development.
Figure 6Handset details

ELL6K Dual Position Optics Slider Kit Chapter 4: Operation
Page 8DTN000414-D02
4.2.2. Elliptec Software Control
When connected to the host PC, the slider can be controlled remotely, via the Elliptec software.
1. Download the elliptic software from the downloads section at www.thorlabs.com. Double click the saved
.exe file and follow the on-screen instructions.
2. Connect the hand-held controller to the slider unit.
3. Connect the hand-held controller to the PC USB port.
4. Run the Elliptec software.
5. In the top left of the GUI panel displayed, select the COM port to which the device is connected, and click
‘Connect’. The software will search the comms bus and enumerate the device. It is possible to connect
multiple devices - see the helpfile supplied with the software for more information. A cable with multiple
connectors in series will be required. Contact tech support for more information.
6. The GUI and device are now ready for use. See the helpfile supplied with the software for more
information.

ELL6K Dual Position Optics Slider Kit Chapter 4: Operation
Rev. G, April 2018 Page 9
4.2.3. Communications Protocol
Custom move applications can be written in languages such as C# and C++.
The communication bus allows multi-drop communication with speeds at 9600 baud, 8 bit data length, 1 stop bit,
no parity.
Protocol data is sent in ASCII HEX format, while module addresses and commands are mnemonic character (no
package length is sent). Modules are addressable (default address is “0”) and addresses can be changed and/or
saved using a set of commands. Lower case commands are sent by user while upper case commands are replies
by the module.
Please refer to the communications protocol manual for more detail about commands and data packet formats.
4.2.4. Connecting Multiple Devices
When a device is first connected to the PC, it is assigned the default address '0'. The software can run multiple
devices, however before more than one device can be recognised, each device must be assigned a unique
address. See below for a brief overview; detailed instructions are contained in the help file supplied with the
software.
Connect the first device to the PC USB port, then run the Elliptec software and load the device.
Change the address of the first device.
Connect the next device to the first device.
Change the address of the second device.
Multiple devices can be controlled individually, either via the Elliptec software or by a third part application written
using the messages detailed in the protocol document. Control via the handset is applied to all devices
simultaneously.
4.2.5. Controlling the Stage without the handset
Caution
During normal operation each motor is protected with a time out of 2 seconds to prevent overheating. Do not override
this protection or drive the motors continuously.
In the absence of the handset, the stage is controlled via digital lines: forward, backward and mode (J1 pins 7, 6
and 5) by shorting the corresponding line to ground (pin 1).
When the stage is moving, the open drain IN MOTION digital line (pin 4) is driven low (active low) to confirm
movement. The IN MOTION line goes high (inactive) when the move is completed or the maximum time-out (2
seconds) is reached.
Warning
Do not exceed the voltage and current ratings stated in Figure 6.
Do not reverse polarity.

ELL6K Dual Position Optics Slider Kit Chapter 4: Operation
Page 10 DTN000414-D02
Connector J2 Pin Out
PIN
TYPE
FUNCTION
1
PWR
Ground
2
OUT
ODTX - open drain transmit 3.3V TTL RS232
3
IN
RX receive - 3.3V TTL RS232
4
OUT
In Motion, open drain active low max 5mA
5
IN
JOG/Mode = normal/test demo, active low max 5V
6
IN
BW Backward , active low max 5V
7
IN
FW Forward, active low max 5V
8
PWR
VCC +5V +/-10% 600mA
Connector model number MOLEX 90814-0808 Farnell order code 1518211
Mating connector model number MOLEX 90327-0308 Farnell order code 673160
Figure 7 Connector J2 pin out details
Caution
The ribbon cable connector (J2) is made of plastic and is not particularly robust. Do not use force when making
connections. Unnecessary or repeated plugging in and unplugging should be avoided or the connector may fail.

ELL6K Dual Position Optics Slider Kit Chapter 4: Operation
Rev. G, April 2018 Page 11
4.3. Frequency Search
Due to load, build tolerances and other mechanical variances, the default resonating frequency of a particular
motor may not be that which delivers best performance. A frequency search can be performed using the Main
GUI panel in the ELLO software, or by using the serial communication line (SEARCHFREQ_MOTORX message),
which offers a way to optimize the operating frequencies for backward and forward movement.
This search can also be performed manually as follows:
With the remote handset
1. Press and hold BW button.
2. Power up the slider.
3. The slider performs a self-test by moving from one position to the other. If the slider does not move or
complete, move the slider manually from one end of travel to the other until it is no longer attempting to
move.
Note: The BW button must be held down during manual actuation.
4. Release the BW button. The red INM LED should be lit briefly.
5. A frequency search will now be performed. To avoid overheating the motor, a pause of 1 second is
programmed after each move. The red INM LED will be lit after each movement
6. Press and hold the BW button until red INM LED turns ON and then OFF, and the slider stops moving.
The optimized resonating frequency is stored until the next frequency search is requested.
7. Power down the slider.
8. Wait for the green PWR LED to turn OFF.
9. Power up the slider. The device will now complete a self test.
Without the remote handset
1. Connect Pin 6 of connector J2 to 0V.
2. With J2 Pin 6 connected to 0V, power up the slider.
3. The slider performs a self-test by moving from one position to the other. If the slider does not move or
complete, then move the slider manually from one end of travel to the other until it is no longer attempting
to move.
Note: J2 Pin6 will need to be shorted to 0V during manual actuation.
4. Connect J2 Pin 6 to 3.3V.
5. A frequency search will now be performed. To avoid overheating the motor, a pause of 1 second is
programmed after each move.
6. Connect J2 Pin 6 to 0V. The slider stops moving and the optimized resonating frequency is stored until
the next frequency search is requested.
7. Power down the slider
8. Wait for 2 seconds for power supply line to go to 0V.
9. Power up the slider. The device will now complete a self test.
4.3.1. Dynamic Frequency Search
The ELL6 unit also incorporates a dynamic frequency search. After the initial frequency search detailed above has
been performed, the ELL6 unit will search for the best mechanical performance every time the slider is moved,
tracking performance against temperature drift and changes of the load value. In this way, the frequency is
continually updated. After 60 seconds of inactivity the optimised frequencies are discarded because the motor may
have cooled down, in which case the dynamic frequency search will be performed again once motion is restarted.
In certain applications, it may be inconvenient to wait for the search to be performed each time the motor is stopped
for a time. In this case, the user should store the last frequency used before stopping the slider, and then reload
the frequencies before restarting the motion.

ELL6K Dual Position Optics Slider Kit Chapter 4: Operation
Page 12 DTN000414-D02
4.4. Periodic Cycling of Devices Over Full Range of Travel
Caution
Periodically, devices should be moved over the full range of travel, from one end to the other. This will help minimize
the build up of debris on the track and will prevent the motors digging a groove over the most used area of contact.
Typically, a travel cycle should be performed every 10K operations.
4.5. Restoring Factory Settings
Factory settings can be restored during the start up (calibration) test as follows:
1. Remove power from the stage.
2. Press and hold the BW button (do not release until item 6).
3. POWER UP
4. WAIT for red led to switch off
5. Press and hold the FW button to request a reload of factory values (do not release until item 7 is complete).
6. Release BW to reboot
7. Continue to hold the FW button until the stage stops moving and the red LED switches off, then release.
8. Press the BW button to home the stage.
4.6. Simultaneous Movement of Devices
If more than one device is connected to the comms bus, movement of the devices can be synchronized. This can
be achieved either by using the handset, or by software. See the protocol document for details on how to use the
‘ga’ message to synchronize moves. If using the handset, synchronized movement is hard wired, so if multiple
devices are connected, pressing the FWD or BWD buttons will move all devices.

ELL6K Dual Position Optics Slider Kit Chapter 5: Troubleshooting and FAQ
Rev. G, April 2018 Page 13
Chapter 5 Troubleshooting and FAQ
5.1. Frequently Asked Questions
Bi positional slider is moving back and forth after power up
If the digital line “bw” is driven low before powering up the bi positional slider, the module will go into calibration
mode. Remove power to exit calibration mode. Keep line tight up to 3.3V or 5V rail during power up or use a serial
communication line instead.
Bi positional slider not moving
Check power supply lines ratings (polarity, voltage drop or range, available current) or reduce cable length.
Check module is not in boot loader mode (power cycle the module to exit boot loader) consumption must be higher
than 36mA at 5V.
Bi positional slider switching time increased / max load decreased
Check power supply voltage provided on J2 connector, increase voltage within specified limits if voltage drop along
cable goes below 5V during system operation.
Clean the moving surfaces. To avoid grease contamination, do not touch the moving parts.
Temperature change may affect bi positional slider performances. A frequency search procedure using provided
software will compensate frequency as needed (required current could reach 1.2A during frequency search, use an
addition 5V 2A power supply).
Integrators should search for optimal frequency on every power up sequence
(commands “s1”, “s2” see ELLx protocol document)
How do I restore the factory (default) settings
Factory settings can be restored during the start up (calibration) test – see Section 3.6.
What is the typical product life time
ELL6 product life time is restricted by the wearing of moving surfaces and the motor contact as motion is started
(due to resonance build up) and performed (due to friction). Therefore, life time is expressed both in km and millions
of operations, whichever comes first will depend on the module usage. Operation and km are related by the module
travel of 31mm, with a minimum lifetime of 100km relating to 3.3 million operations.
The unit is not designed for continuous operation. Users should aim for a duty cycle of less than 40% wherever
possible, and never exceed a duty cycle of 60% for longer than a few seconds.
Handling
The stage and interface board are robust to general handling. To ensure reliable operation, keep the surface of the
plastic track contacted by the motors free of oils, dirt, and dust. It is not necessary to wear gloves while handling
the linear stage, but avoid touching the track to keep it free of oils from fingerprints. If it is necessary to clean the
track, it may be wiped with isopropyl alcohol or mineral spirits (white spirit). Do not use acetone, as this solvent will
damage the plastic track.

ELL6K Dual Position Optics Slider Kit Chapter 5: Troubleshooting and FAQ
Page 14 DTN000414-D02
5.2. Notes on Making a Picoflex Cable for Use when Daisy Chain Devices
The multi-drop communications bus offers the option of connecting the slider to a hybrid network of up to 16 Elliptec
resonant motor products and controlling the connected units with a device such as a microprocessor. When multiple
units are connected to the same interface board, all can be controlled simultaneously using either the software or
the buttons on the interface board.
When making a cable to operate multiple devices it is important to observe the correcr pin orientation. The following
procedure offers guidance in making such a cable.
1. Gather together the parts required.
a) Ribbon cable 3M 3365/08-100 (Farnell 2064465xxxxx.
b) Female crimped connectors as required - model number MOLEX 90327-0308 (Farnell order code
673160) (Qty 1 female connector above is shipped with each stage unit).
c) Suitable screwdriver and scissors or other cutting tool.
2. Orientate the first connector correctly to mate with the connector on the stage, then arrange the ribbon
cable as shown with the red wire aligned with pin 1 (identified on the pcb by a small triangle). Slide the
connector onto the ribbon cable as shown.

ELL6K Dual Position Optics Slider Kit Chapter 5: Troubleshooting and FAQ
Rev. G, April 2018 Page 15
3. Using a screwdriver or other suitable tool, push down the crimp of each pin to make connection with the
ribbon cable.
4. If other connectors are required they should be fitted at this point. Slide each connector onto the cable,
paying attention to the orientation as shown below, then crimp as detailed in step (3).
5. Fit the terminating connector which will mate with the interface board, taking care to align the cable red
wire with pin 1 as detailed in step (2).

ELL6K Dual Position Optics Slider Kit Chapter 6: Specifications
Page 16 DTN000414-D02
Chapter 6 Specifications
General Specifications
Switching Time
Unloaded: 180 to 270 ms
100g Load: <600 ms
Travel
31 mm (1.22")
Endstop Repeatability a
<100 µm (30 µm Typical)
Maximum Load (Vertically Mounted) b
150 g (5.29 oz)
Minimum Lifetime c
100 km (3.3 Million Operations)
Rated Voltage
4.5 to 5.5 V
Typical Current Consumption, During Movement
<600 mA
Typical Current Consumption, During Standby
38 mA
Typical Current Consumption, During Frequency
Search d
1.2 A
Bus e
Multi-Drop 3.3V/5V TTL RS232
Speed
9600 baud/s
Data Length f
8 bit
Protocol Data Format
ASCII HEX
Module Address and Command Format
Mnemonic Character
Ribbon Cable Length (Supplied)
250 mm
Ribbon Cable Length (Maximum)
3 m
Optic Thread Type
SM1
Dimensions of the Slider (Mount Centered)
64.0 mm x 77.7 mm x 10.3 mm
(2.52" x 3.06" x 0.41")
Dimensions of the Slider (Mount at Full Extension)
79.0 mm x 77.7 mm x 10.3 mm
(3.11" x 3.06" x 0.41")
Dimensions of the Control Board
32 mm x 65 mm x 12.5 mm
(1.26" x 2.56" x 0.49")
Weight: Slider unit only, (no cables or handset).
44 g (1.55 oz)
Weight: Handset
10.3 g (0.36 oz)
Notes
a.Low power infrared photo-sensor technology aligns the slider at each position.
b.Vertically Mounted so that Movement is Side-to-Side and not Up-and-Down
c.Lifetime is measured in terms of distance traveled by the optics mount.
d.Additional Power Supply May Be Required
e.Use two 10 kΩ pull-up resistors in multi-drop mode for RX/TX.
f.1 Stop Bit, No Parity

ELL6K Dual Position Optics Slider Kit Chapter 7: Regulatory
Rev. G, April 2018 Page 17
Chapter 7 Regulatory
7.1. Declarations of Conformity
7.1.1. For Customers in Europe
7.1.2. For Customers In The USA
This equipment has been tested and found to comply with the limits for a Class A digital device, persuant to part 15 of the FCC
rules. These limits are designed to provide reasonable protection against harmful interference when the equipment is operated
in a commercial environment. This equipment generates, uses and can radiate radio frequency energy and, if not installed and
used in accordance with the instruction manual, may cause harmful interference to radio communications. Operation of this
equipment in a residential area is likely to cause harmful interference in which case the user will be required to correct the
interference at his own expense.
Changes or modifications not expressly approved by the company could void the user’s authority to operate the equipment.

ELL6K Dual Position Optics Slider Kit Chapter 8: Thorlabs Worldwide Contacts
Page 18 DTN000414-D02
Thorlabs verifies our compliance with the WEEE (Waste Electrical and Electronic Equipment)
directive of the European Community and the corresponding national laws. Accordingly, all end
users in the EC may return “end of life” Annex I category electrical and electronic equipment
sold after August 13, 2005 to Thorlabs, without incurring disposal charges. Eligible units are
marked with the crossed out “wheelie bin” logo (see right), were sold to and are currently owned
by a company or institute within the EC, and are not dissembled or contaminated. Contact
Thorlabs for more information. Waste treatment is your own responsibility. “End of life” units
must be returned to Thorlabs or handed to a company specializing in waste recovery. Do not
dispose of the unit in a litter bin or at a public waste disposal site.
Chapter 8 Thorlabs Worldwide Contacts
For technical support or sales inquiries, please visit us at www.thorlabs.com/contact for our most up-to-
date contact information.
USA, Canada, and South America
Thorlabs, Inc.
techsupport@thorlabs.com
Europe
Thorlabs GmbH
France
Thorlabs SAS
Japan
Thorlabs Japan, Inc.
UK and Ireland
Thorlabs Ltd.
techsupport.uk@thorlabs.com
Scandinavia
Thorlabs Sweden AB
Brazil
Thorlabs Vendas de Fotônicos Ltda.
China
Thorlabs China
Other manuals for ELL6
1
This manual suits for next models
1
Table of contents
Other THORLABS Control Unit manuals
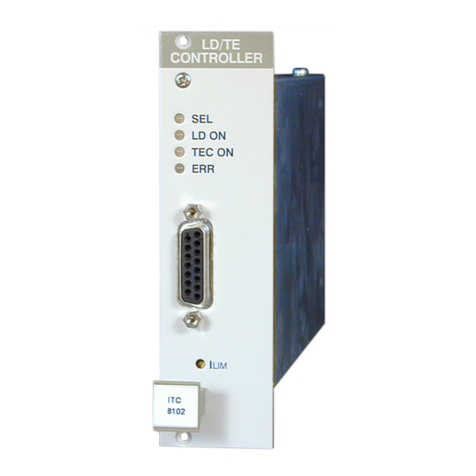
THORLABS
THORLABS ITC8 Series User manual

THORLABS
THORLABS LS5000 Series User manual
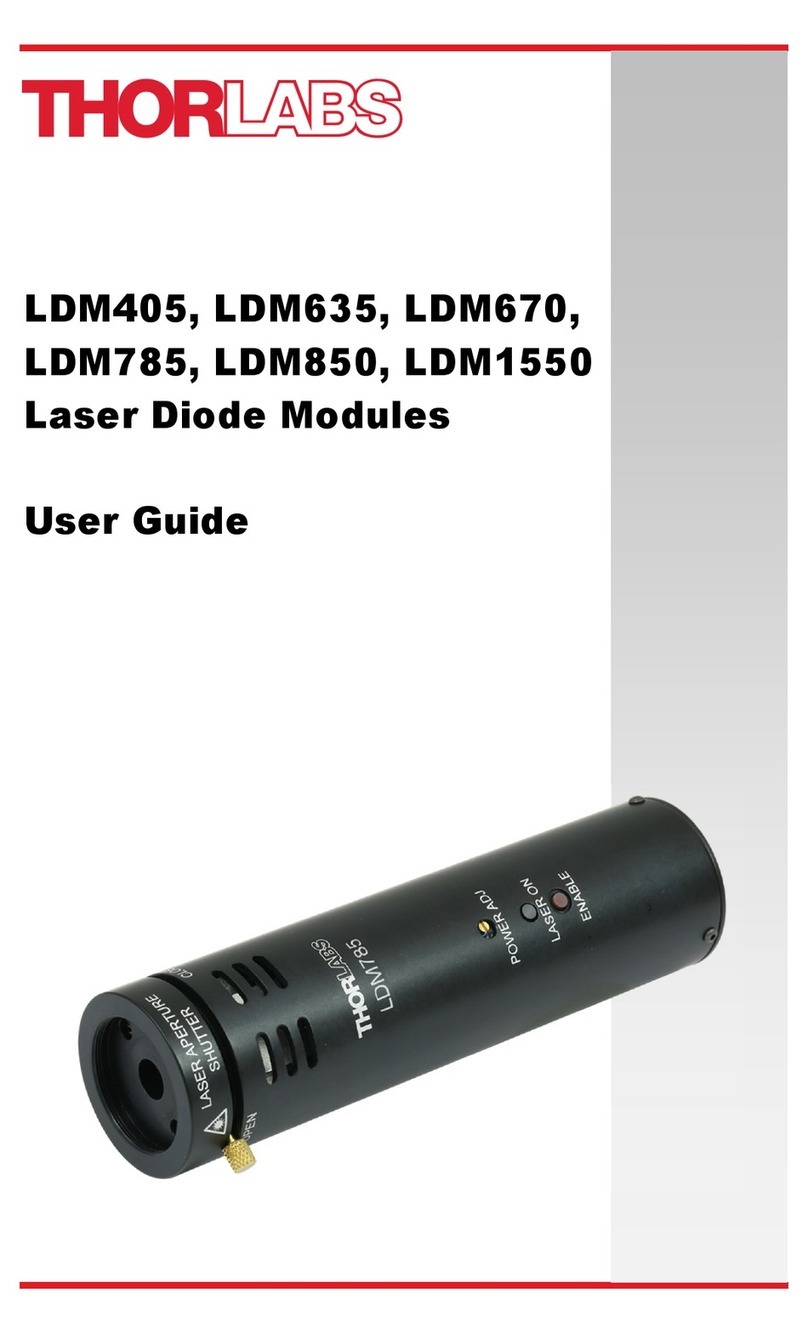
THORLABS
THORLABS LDM405 User manual
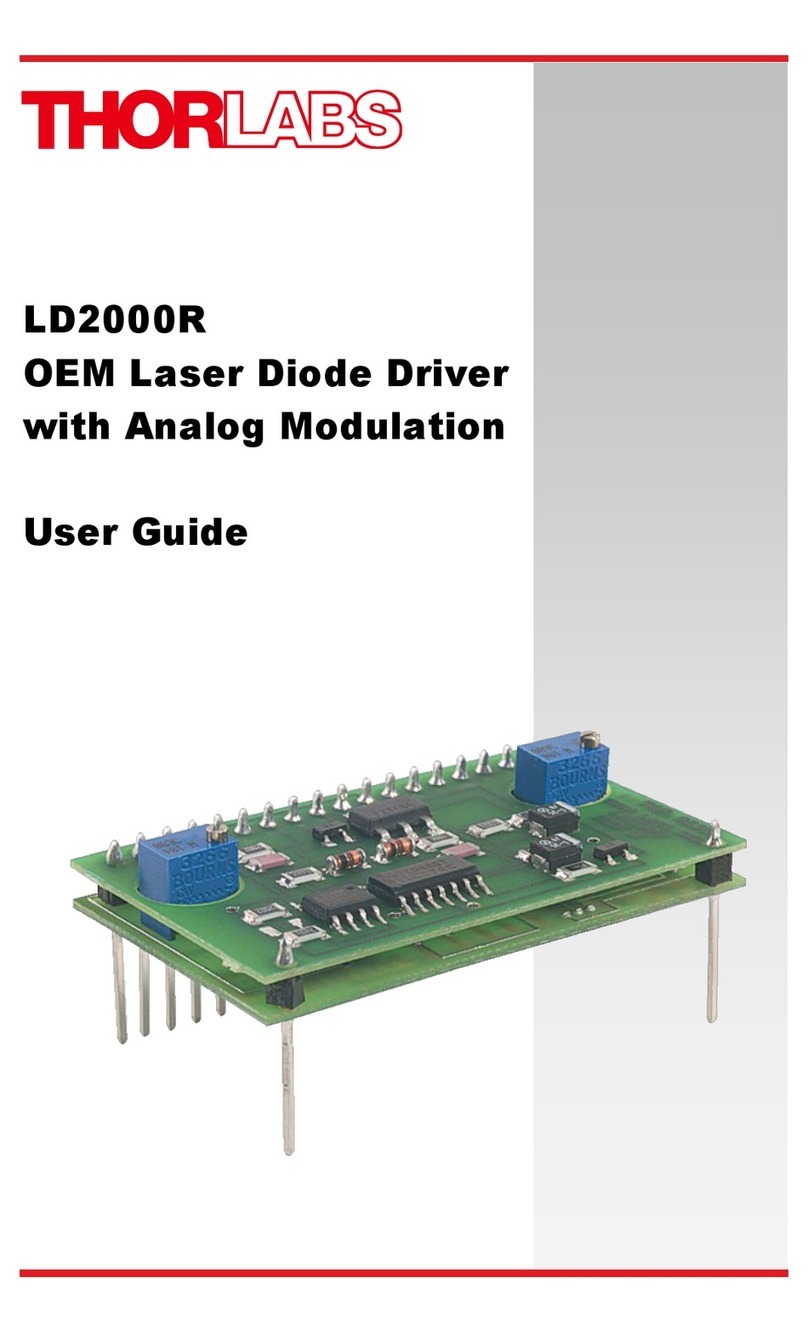
THORLABS
THORLABS LD2000R User manual
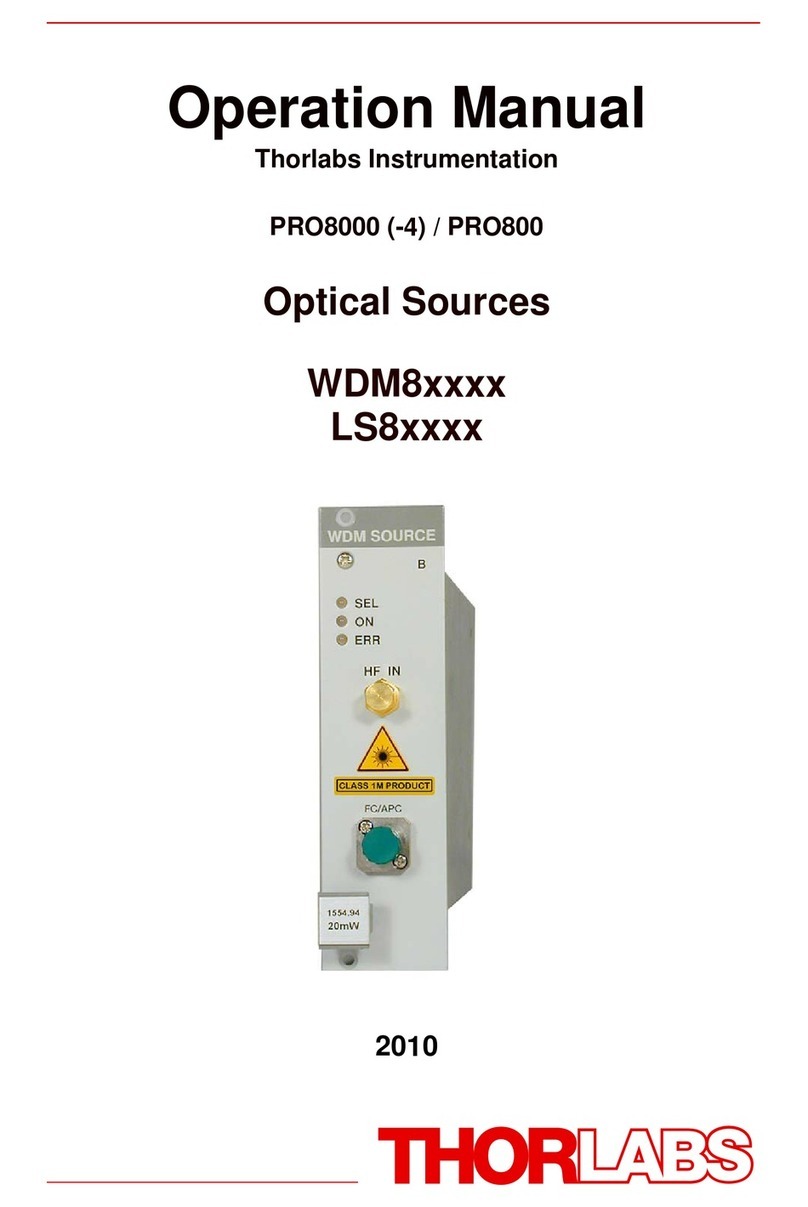
THORLABS
THORLABS WDM8 Series User manual
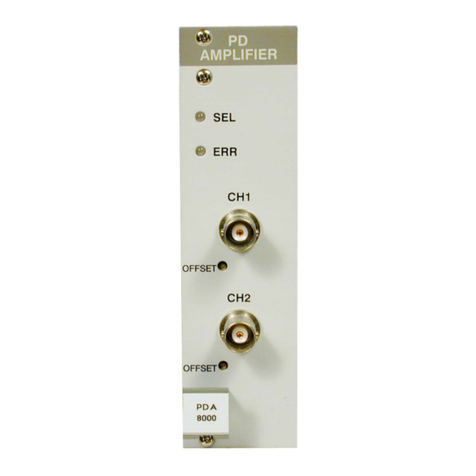
THORLABS
THORLABS PDA8000-1 User manual
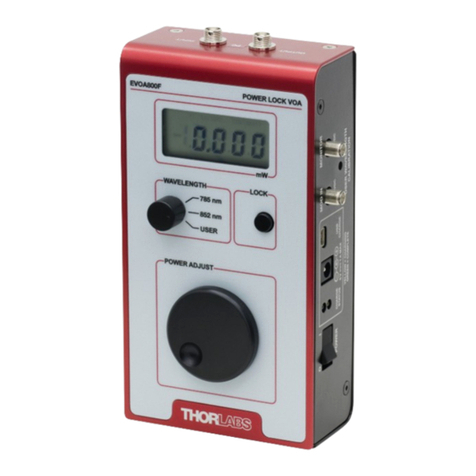
THORLABS
THORLABS EVOA800F User manual
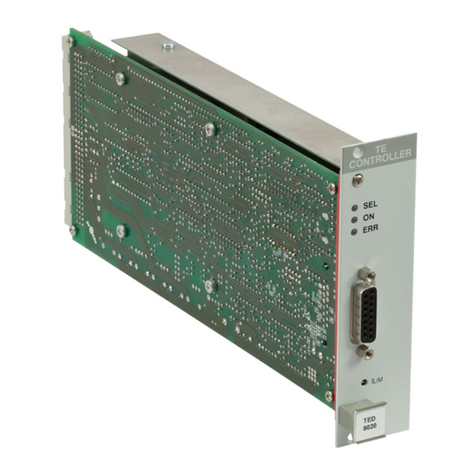
THORLABS
THORLABS TED8000 Series User manual
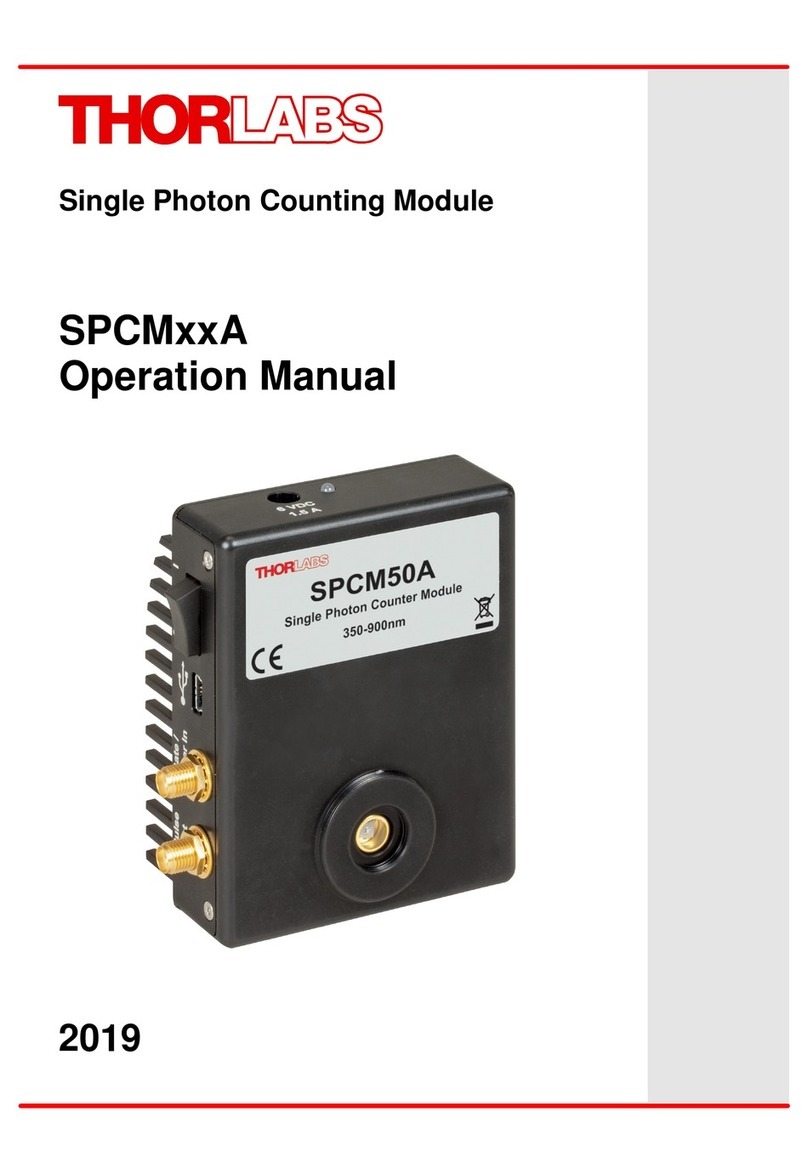
THORLABS
THORLABS SPCM A Series User manual
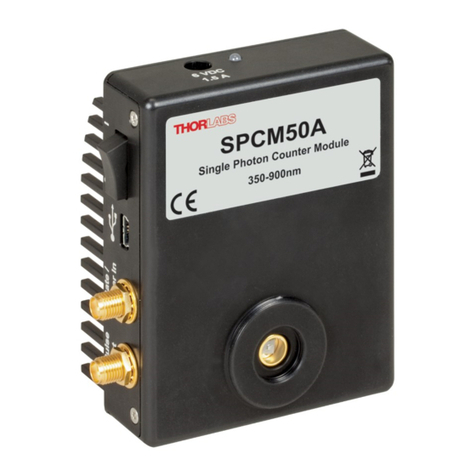
THORLABS
THORLABS SPCM A Series User manual