THORLABS LD2000R User manual

LD2000R
OEM Laser Diode Driver
with Analog Modulation
User Guide

OEM Laser Diode Driver
Table of Contents
Chapter 1 Warning Symbol Definitions ...........................................1
Chapter 2 Safety.................................................................................2
Chapter 3 Description........................................................................3
Chapter 4 LD2000R Overview...........................................................4
4.1. Slow Start Circuit ..........................................................4
4.2. Limit Current Circuit ......................................................4
4.3. Constant Power Feedback Loop .....................................4
4.4. Theory of Operation......................................................6
Chapter 5 Operating the LD2000R....................................................8
5.1. Setup............................................................................8
5.2. Setting the Feedback Resistor......................................10
5.3. Operating Modes........................................................11
5.3.1. CW Operation..........................................................................11
5.3.2. Analog Modulation...................................................................11
5.3.3. External Modulation Operation.................................................12
Chapter 6 Specifications.................................................................14
Chapter 7 Mechanical Drawing.......................................................15
Chapter 8 Regulatory.......................................................................16
Chapter 9 Thorlabs Worldwide Contacts.......................................17

OEM Laser Diode Driver Chapter 1: Warning Symbol Definitions
Rev I, May 21, 2018 Page 1
Chapter 1 Warning Symbol Definitions
Below is a list of warning symbols you may encounter in this manual or on your
device.
Symbol
Description
Direct Current
Alternating Current
Both Direct and Alternating Current
Earth Ground Terminal
Protective Conductor Terminal
Frame or Chassis Terminal
Equipotentiality
On (Supply)
Off (Supply)
In Position of a Bi-Stable Push Control
Out Position of a Bi-Stable Push Control
Caution: Risk of Electric Shock
Caution: Hot Surface
Caution: Risk of Danger
Warning: Laser Radiation
Caution: Spinning Blades May Cause Harm

OEM Laser Diode Driver Chapter 2: Safety
Page 2 0187-D01
Chapter 2 Safety
All statements regarding safety of operation and technical data in this instruction
manual will only apply when the unit is operated correctly.
SHOCK WARNING
Warning is given when there is danger of injury to users.
CAUTION
Caution is given when there is a possibility of damage to the product.
WARNING
Given when there is danger of injury to users.

OEM Laser Diode Driver Chapter 3: Description
Rev I, May 21, 2018 Page 3
Chapter 3 Description
The LD2000R is a low-noise, stable laser diode current source that can be
operated with laser diodes having a common laser anode and monitor photodiode
cathode. The driver operates in an automatic power control (APC) mode using the
built-in monitor photodiode integrated in the laser diode for feedback or a constant
current (CC) mode. On board trimpots are provided for controlling the laser power
and current limit. Both functions can also be controlled via an external voltage
source. The LD2000R supports a wide range of laser diodes with drive currents up
to 100 mA and photodiode currents from 20 µA to 2 mA. The LD2000R also has
an external modulation input to support applications that require modulating the
laser output.
Figure 1 Compatible LD Pin Codes
NOTE
The Laser Diode case must remain floating with respect to both the power
supply ground, and the chassis ground.
NOTE
Read the section on Operating Modes (page 11) before attempting to operate
the LD2000R.
WARNING
The LD2000R uses CMOS circuitry to minimize power drain. Use anti-static
precautions while handling the LD2000R to prevent permanently damaging
the device.

OEM Laser Diode Driver Chapter 4: LD2000R Overview
Page 4 0187-D01
Chapter 4 LD2000R Overview
The LD2000R is composed of three independent circuits: slow start circuit, limit
current circuit, and output control circuit. Each is described below.
4.1. Slow Start Circuit
The slow start circuit is used to monitor the supply voltage and keep the laser
output off until the power supply stabilizes. The slow start circuit uses a voltage
reference and a comparator to monitor the supply voltage. An internal 2.5 V
reference is compared to the voltage at the ON/OFF pin (pin 17). When this voltage
exceeds 2.5 V, the laser is enabled. The comparator input (pin 17, ON/OFF) has
an input impedance of 20 kΩ. This resistance is used with an external resistor to
form a voltage divider that sets the LD2000R dropout voltage. For most
applications a 15 kΩ resistor tied from the 12 V power supply to the ON/OFF pin
which disables the laser when the power supply drops below 4.5 V is adequate.
Note, the ON/OFF pin can also be used to disable the laser by pulling this pin low
to 0 V.
The slow start circuit uses an internal time constant formed by a 1 MΩ and a 1 µF
capacitor to yield a 50 ms turn on delay. This can be extended by adding an
external capacitor to the SLOW_START pin.
4.2. Limit Current Circuit
The limit current circuit is a constant current source which can be set by the on-
board trim pot or an external control voltage. This determines the maximum drive
current that can be supplied to the laser. The transfer function for this control is 40
mA/V. The current limit also determines the laser current when operating in the
constant current mode.
4.3. Constant Power Feedback Loop
The constant power feedback loop circuit uses the laser monitor photodiode
current (which is proportional to the laser output power) to regulate the laser output
power. An internal transimpedance amplifier converts the photodiode current to a
voltage used by the feedback circuit. The feedback loop varies the drive current to
the laser such that the voltage derived from the photodiode monitor current
matches an adjustable setpoint voltage (described below). The laser output can
be adjusted by varying the setpoint voltage.
When the current limit is set higher than the laser current needed by the feedback
loop the laser is operating in a constant power mode. If the current needed by the
feedback loop is higher than the current limit, the laser drive current will be clipped
to the current limit and the laserwill then be operating in the constant current mode.
The photodiode transimpedance amplifier has an internal gain of 20 kΩ which
yields a 50 µA/V output. Since the maximum voltage of the feedback loop is 2.5 V,

OEM Laser Diode Driver Chapter 4: LD2000R Overview
Rev I, May 21, 2018 Page 5
this limits the maximum photodiode current to 125 µA. This upper limit can be
easily increased by adding an external resistor (see page 15).
The setpoint voltage used by the feedback loop is the difference between the PD
CURRENT SETPOINT voltage and the Analog Modulation Voltage as follows:
The control loop integrator has a time constant of approximately 16.5 µs set by a
0.033 µF integrating capacitor. The loop time constant can be extended by adding
an external capacitor across CX1 and CX2 .
Note all control signals are based on the photodiode current. The user must refer
to the manufactures spec sheets of the particular diode that will be used to
correlate this to the laser output power.

OEM Laser Diode Driver Chapter 4: LD2000R Overview
Page 6 0187-D01
4.4. Theory of Operation
The LD2000R uses the internal monitor photodiode provided on most low power
diode lasers for feedback when operating in the Constant Power Mode. The
following figure is a block diagram of the LD2000R laser driver.
Figure 2 LD2000R Simplified Block Diagram
The laser power is regulated through an integrating feedback loop. The setpoint of
the feedback is determined by the PWR LIMIT control trimpot and the OUTPUT
ADJUST knob (in external modulation mode, the external voltage is used in place
of the OUTPUT ADJUST). An internal transimpedance amplifier converts the laser
feedback current to a voltage that is used as the error signal for the feedback loop.
Since all analog signal levels are based on a 2.5 V internal reference, we will use
this to derive the feedback gain setting resistor value:

OEM Laser Diode Driver Chapter 4: LD2000R Overview
Rev I, May 21, 2018 Page 7
The LD2000R has an internal transimpedance gain of 20 k. Without a user
installed feedback resistor, the transimpedance gain is:
and VError is equal to:
where IMon is the feedback monitor photocurrent. The total transimpedance gain
should be set so that the photocurrent at the maximum laser power equals 2.5 V.
Since VError has a maximum value of 2.5 V, we can derive the value of an external
feedback resistor needed to set the transimpedance for any laser:
where RFis the transimpedance gain needed, and IMon is the monitor photocurrent
for your laser.
solving for RF EXT,

OEM Laser Diode Driver Chapter 5: Operating the LD2000R
Page 8 0187-D01
Chapter 5 Operating the LD2000R
5.1. Setup
The LD2000R is packaged as a component which, with minimal external
components, can be integrated intoa system to makea complete laserdiode driver
system. We recommend using printed circuit board construction to achieve
optimum results. The pinouts for the LD2000R are provided in Figure 1 and
described below. The LD2000R can be used with A, D, or F style diodes. The D
and F style diodes will need to be configured like an A style diode (see page 3 for
diagrams). Please note that the EK2000 is not compatible with the F Pin Style.
Figure 3 LD2000R Pin Out

OEM Laser Diode Driver Chapter 5: Operating the LD2000R
Rev I, May 21, 2018 Page 9
Pin
Name
Description
1
CX1
These pins are provided for connecting an external capacitor to
the control loop integrator to extend the integrator time constant.
This may be necessary to get maximum bandwidth when using
TTL modulation. Connect the positive terminal of the cap to CX2.
2
CX2
3
Analog
Modulation
This pin is used with an external voltage signal source to provide
analog modulation. The transfer function (referenced to the
photodiode current) is -50 µA/V with 0 V being the laser
completely on. The laser output decreases as this voltage
increases with the laser being completely off at 2.5 V. Connect
this pin to ground when not using the analog modulation.
4
Slow Start
This output pin is high during the startup period and goes low
when the laser is enabled. It can be used as a LASER
EMISSION indicator. An external capacitor can be connected
from this pin to ground to extend the slow start delay time.
Note: this output will not drive an LED directly and must be
buffered. Contact Tech Support for more details.
5
PD Current
Trimpot
This pin is connected to the wiper of the on-board PD Current
Trimpot. Connect this pin to the PD Current Setpoint to control
the PD current with the on-board trimpot.
6
PD Current
Setpoint
This pin controls the PD Current according to a transfer function
of 50 µA/V with 0 V being the laser is completely off (0 PD
current). The laser output increases as this voltage increases.
7
REF Out
This is a buffered 2.5V voltage reference.
8
PD AMP Out
This is an analog voltage proportional to the photodiode current
and referenced to one half the supply voltage as follows:
,
where RF= PD Amp Transimpedance gain (internal 20 kin
parallel with RF EXT)
9
V+
Positive supply voltage (8 to 12 VDC).
10
GND
Power supply common.
11
LD A/PD K
Common laser diode anode, photodiode cathode.
12
PD A
Photodiode anode.
13
LD K
Laser diode cathode.
14
Limit
Setpoint
This voltage determines the maximum laser drive current
according to the transfer function 40 mA/V.
15
Limit Trimpot
This is connected to the wiper of the Limit Current trimpot.
Connect this to the Limit Setpoint pin to use the on-board trimpot
to set the current limit.
16
Not used
This must be tied to ground to operate the laser.
17
ON/OFF
This pin is used to externally turn the laser on and off through
the slow start circuit and to set the low voltage dropout point. It
has an internal 20 kΩresistor to ground. Connect a 15 kΩ
resistor to the power supply voltage to set the dropout voltage to
4.5 V.
18
Limit Out
This is an output voltage proportional to the limit current with a
transfer function of 40 mA/V. Use this pin to assist in setting the
laser current limit.

OEM Laser Diode Driver Chapter 5: Operating the LD2000R
Page 10 0187-D01
5.2. Setting the Feedback Resistor
The LD2000R is configured at the factory for a maximum feedback gain. This gain
setting is appropriate for lasers that have low monitor currents in the range of 20
to 120 A.
For most lasers, the photodiode current is greater than 120 A and the feedback
gain will have to be reduced to drive the laser at full drive current. This can be done
by following the procedure below.
1. Determine the appropriate feedback gain using the following calculation:
where RF EXT is the external gain setting resistor to be added in ohms and
IMON is the monitor current for a particular laser in Amps.
2. Pick the nearest standard value resistor (0.25 W, 5% or better).
3. Connect RF EXT across pins 8 and 12 of the LD2000R.
SHOCK WARNING
The LD2000R uses CMOS circuitry to minimize power drain. Use anti-static
precautions while handling the LD2000R to prevent permanently damaging
the device.
0.1 1 10
0.1
1
10
100
1 103RFext vs. PD Monitor Current
PD Monitor Current (mA)
RFext (kohms)

OEM Laser Diode Driver Chapter 5: Operating the LD2000R
Rev I, May 21, 2018 Page 11
5.3. Operating Modes
NOTE
For all modes of operation, we recommend using a linear DC power supply or
battery. Although the LD2000R provides over -60 dB of power supply
suppression, switch-mode power supplies should be avoided due to the
inherent transients in their output.
5.3.1. CW Operation
To operate the LD2000R in a CW mode, follow the steps below.
1. Connect your laser diode to the appropriate pins (11, 12, 13)
2. Attach a suitable DC voltage supply to pins 9 and 10. The power supply
should be bypassed near the LD2000R with a 10 µF tantalum capacitor
and a 0.1 µF ceramic capacitor.
3. Short pins 5 and 6 to use the on-board PD Current Trimpot.
4. Short pins 14 and 15 to use the on-board Current Limit Trimpot.
5. Short pin 3 to ground to set analog modulation to FULL ON.
6. Short pin 16 to ground.
7. Turn both the PD Current Trimpot and the Current Limit Trimpot
counterclockwise 20 turns each to set these at their minimum operating
points.
8. Turn the DC power supply on and use a voltmeter to monitor the LIMIT
OUT on pin 18.
9. Adjust the Current Limit Trimpot clockwise slowly while observing the
LIMIT OUT to set the maximum operating current for your laser (refer to
laser manufacturer's data sheets). Note, this output is 40 mA/V.
10. Using a calibrated power meter to monitor the diode laser output, slowly
adjust the PD Current Setpoint trimpot clockwise to obtain the desired
operating power level. The laser will begin to emit upon reaching the drive
current threshold.
5.3.2. Analog Modulation
To operate the LD2000R analog modulation feature, follow the setup procedures
for CW Operation to establish the laser operating conditions. Once the LD2000R
has been setup for your laser, remove the short from pin 3 to ground and apply a
positive voltage to pin 3 to modulate the laser.

OEM Laser Diode Driver Chapter 5: Operating the LD2000R
Page 12 0187-D01
1. The analog modulation voltage has a negative transfer function
characteristic. That is, at 0 V, the laser is fully on, at 2.5 Vthe laser should
be completely off.
2. The linear operating range of the analog modulation is determined by the
transimpedance gain of the PD Amplifier, RF. The appropriate
transimpedance gain for your laser can be calculated as follows:
Where IMON is the PD current specified by the laser manufacturer for the
maximum operating output power.
Note, the LD2000R includes an internal 20 kΩ resistor. RFis the net
resistance of the internal 20 kΩ resistor with any external resistance
added in parallel on pins 8 and 12. To calculate the external resistance
(RF EXT) needed to operate at a particular monitor current (IMON), use the
following equation:
5.3.3. External Modulation Operation
The laser output power can be controlled via an external modulation voltage while
operating in the Constant Power Mode. The laser output is inversely proportional
to the modulating voltage with 0 V being the laser fully on and 2.5 V turning the
laser fully off.
1. To use the external modulation, perform the following steps:
2. Set up the LD2000R for Constant Power.
3. Attach an external modulation source (e.g. function generator, D/A
converter, etc.) to the Analog Modulation Input (pin 3).
4. Apply power to the LD2000R and adjust the modulation input amplitude
and frequency for the desired output.
5. The laser output will now be controlled by the external modulation
voltage.
The graph above describes the characteristic of the modulation voltage. If the
LD2000R is set up to match a particular laser, the solid curve would represent the
output power of the laser as a function of the modulation voltage. A couple of notes
of interest:

OEM Laser Diode Driver Chapter 5: Operating the LD2000R
Rev I, May 21, 2018 Page 13
1. If the PWR Limit control is set below the maximum output power, the laser
output will plateau (clip) at the PWR Limit level for modulations below the
PWR limit.
2. If the total feedback gain, RF, is not optimized for the operating laser, the
laser turn off point of the output will be different than 2.5V (usually
somewhere below 2.5V since the default feedback gain is usually too high
for most lasers).
3. If the feedback gain is too low for a laser (i.e. the maximum laser power
can be reached at a point somewhere below the maximum setting of
PWR Limit, than use care to set the PWR Limit control to the maximum
desired operating power before applying the modulating voltage.
The turn-off
voltage is
dependent on
matching Rfext to
the laser. If the
feedback gain is
too high, the laser
will turn off at a
lower voltage
(Voff = RF(IMon),
where RF=RF EXT
in parallel with
20 kΩ).
Clipping due to
Current Limit
being set too
low.

OEM Laser Diode Driver Chapter 6: Specifications
Page 14 0187-D01
Chapter 6 Specifications
Specification
Value
Current Output
Limit Current Control
Trimpot or External Analog Voltage
Limit Current Range
0 to 100 mA
Limit Accuracy
±1%
Compliance Voltage
Power Output
Photodiode Current Control
Trimpot or External Analog Voltage
Photodiode Current Range
20 to 125 A (Factory Configured1)
Long Term Drift (24 hrs)
<0.1%
Temperature Coefficient
<100 ppm/°C
Analog Bandwidth
3 db Bandwidth (Nominal)
10 kHz2
Power Supply
Supply Voltage (V+)
8 to 12 VDC
Supply Current
30 mA Plus Laser Current
General
Dimensions
2" x 1.3" x 0.5"
Operating Temperature
0 to 40 °C
Storage Temperature
0 to 70 °C
Packaging
PCB DIP, Plastic Encapsulated
1
Higher photodiode currents are easily supported by adding a single external resistor.
2
The actual bandwidth is laser dependent.

OEM Laser Diode Driver Chapter 7: Mechanical Drawing
Rev I, May 21, 2018 Page 15
Chapter 7 Mechanical Drawing
Figure 4 LD2000R Mechanical Drawing

OEM Laser Diode Driver Chapter 8: Regulatory
Page 16 0187-D01
Chapter 8 Regulatory
As required by the WEEE (Waste Electrical and Electronic Equipment Directive)
of the European Community and the corresponding national laws, Thorlabs offers
all end users in the EC the possibility to return “end of life” units without incurring
disposal charges.
This offer is valid for Thorlabs electrical and electronic equipment:
Sold after August 13, 2005
Marked correspondingly with the crossed out
“wheelie bin” logo (see right)
Sold to a company or institute within the EC
Currently owned by a company or institute
within the EC
Still complete, not disassembled and not
contaminated
As the WEEE directive applies to self-contained
operational electrical and electronic products, this end of
life take back service does not refer to other Thorlabs products, such as:
Pure OEM products, that means assemblies to be built into a unit by the
user (e.g. OEM laser driver cards)
Components
Mechanics and optics
Left over parts of units disassembled by the user (PCB’s, housings etc.).
If you wish to return a Thorlabs unit for waste recovery, please contact Thorlabs or
your nearest dealer for further information.
Waste Treatment is Your Own Responsibility
If you do not return an “end of life” unit to Thorlabs, you must hand it to a company
specialized in waste recovery. Do not dispose of the unit in a litter bin or at a public
waste disposal site.
Ecological Background
It is well known that WEEE pollutes the environment by releasing toxic products
during decomposition. The aim of the European RoHS directive is to reduce the
content of toxic substances in electronic products in the future.
The intent of the WEEE directive is to enforce the recycling of WEEE. A controlled
recycling of end of life products will thereby avoid negative impacts on the
environment.
Wheelie Bin Logo

2(0/DVHU'LRGH'ULYHU&hapter : Thorlabs Worldwide Contacts
Rev ,, 0D\ , 2018 Page
USA, Canada, and South America
Thorlabs, Inc.
Europe
Thorlabs GmbH
France
Thorlabs SAS
Japan
Thorlabs Japan, Inc
UK and Ireland
Thorlabs Ltd.
Scandinavia
Thorlabs Sweden AB
Brazil
Thorlabs Vendas de Fotônicos Ltda.
China
Thorlabs China
Chapter Thorlabs Worldwide Contacts
For technical support or sales inquiries, please visit us at
www.thorlabs.com/contact for our most up-to-date contact information.

www.thorlabs.com
Table of contents
Other THORLABS Control Unit manuals
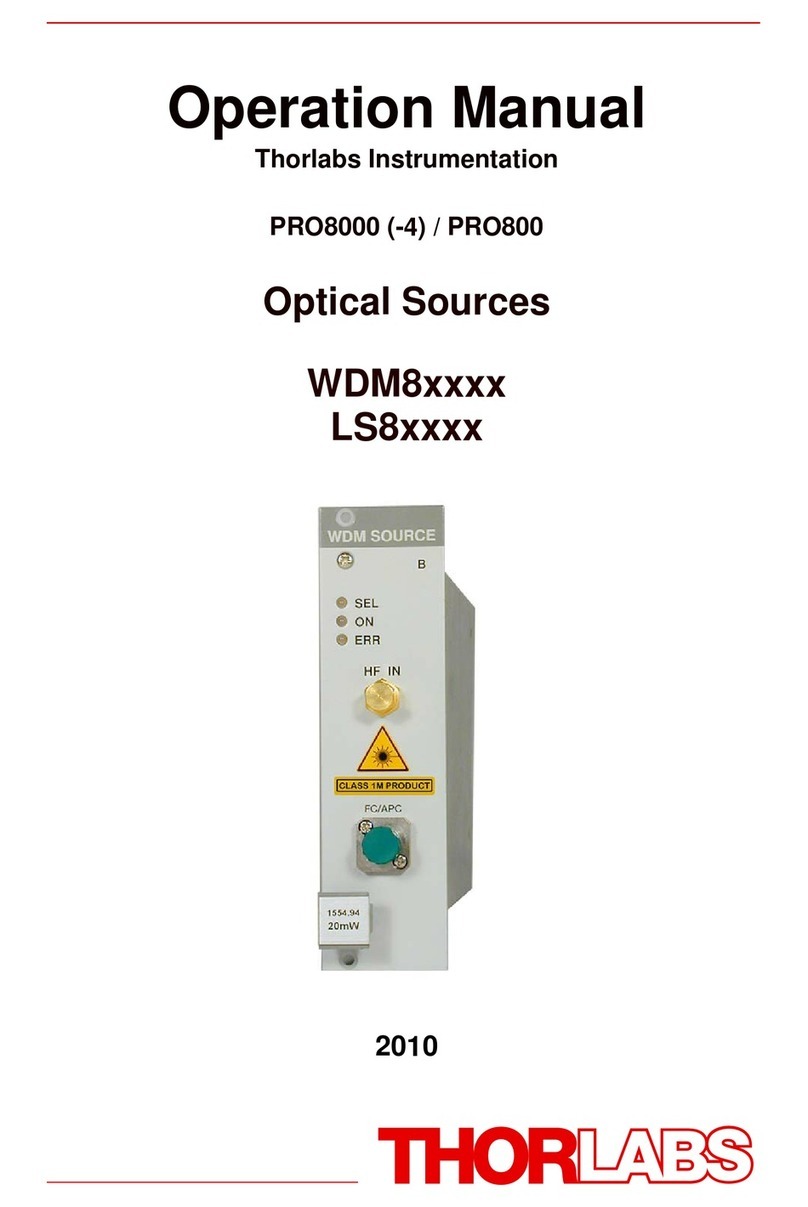
THORLABS
THORLABS WDM8 Series User manual
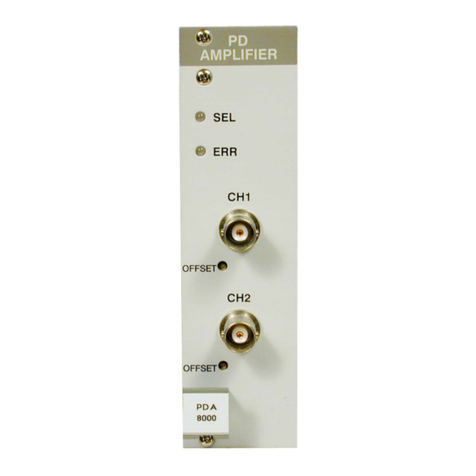
THORLABS
THORLABS PDA8000-1 User manual
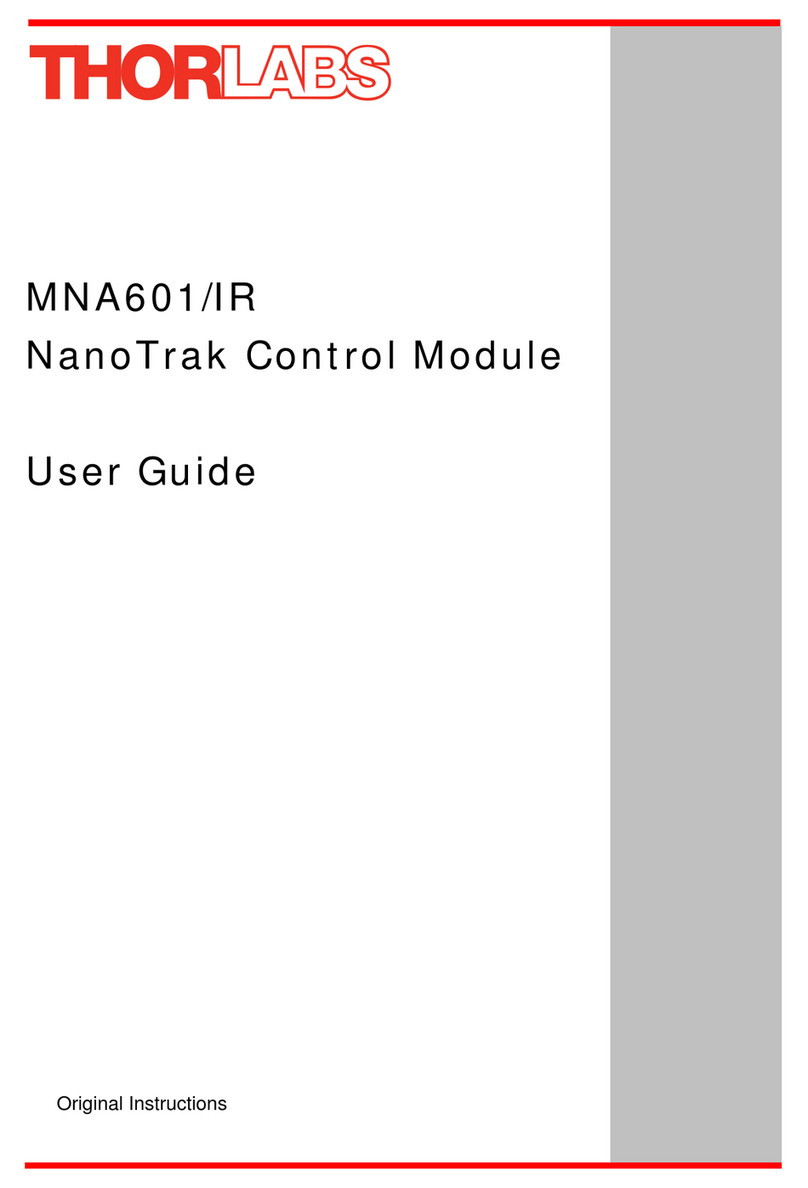
THORLABS
THORLABS MNA601/IR User manual
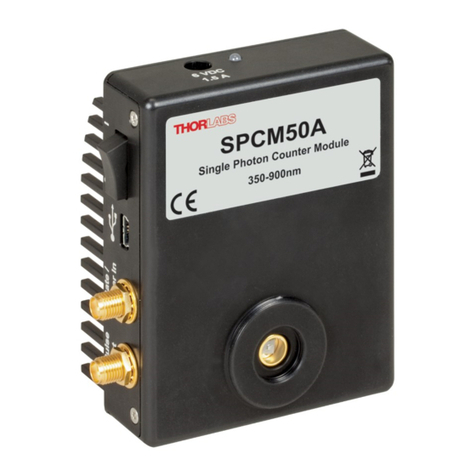
THORLABS
THORLABS SPCM A Series User manual

THORLABS
THORLABS LS5000 Series User manual
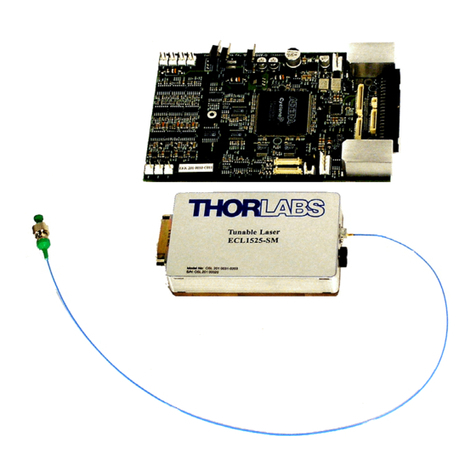
THORLABS
THORLABS ECL1525M-PM User manual
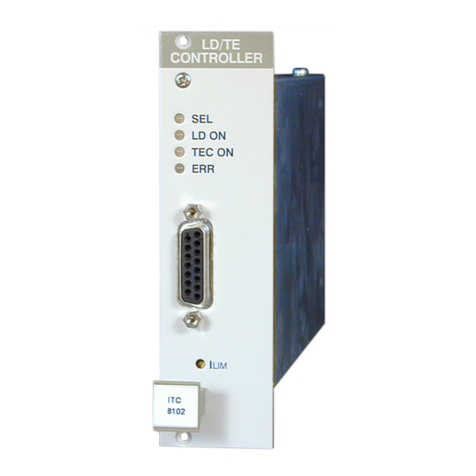
THORLABS
THORLABS ITC8 Series User manual
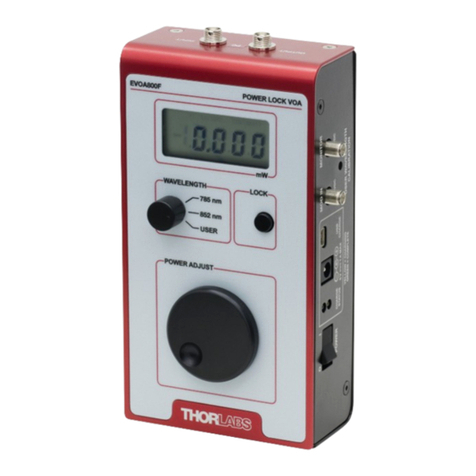
THORLABS
THORLABS EVOA800F User manual
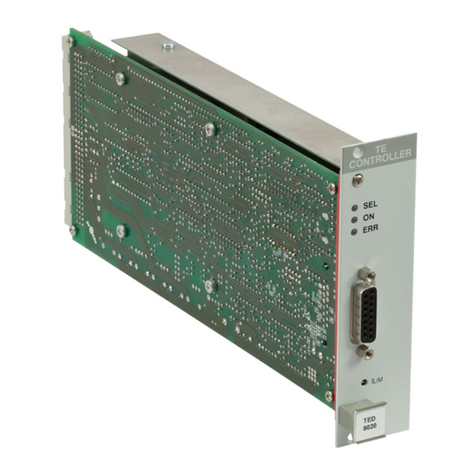
THORLABS
THORLABS TED8000 Series User manual
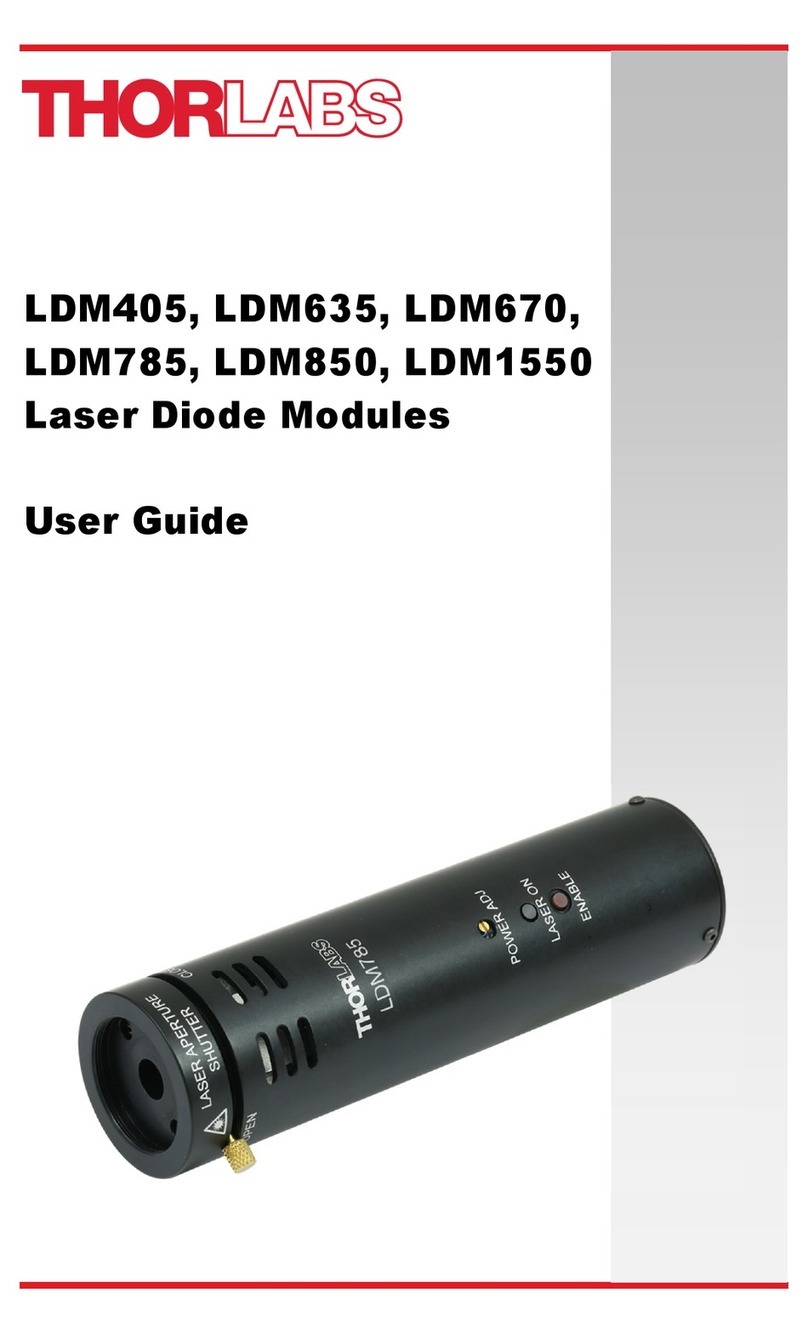
THORLABS
THORLABS LDM405 User manual