Toshiba TOSVERT VF-PS1 User manual


E6581531
1
I
I. Safety precautions
The items described in these instructions and on the inverter itself are very important so that you can use the inverter
safely prevent injury to yourself and other people around you as well as prevent damage to property in the area.
Thoroughly familiarize yourself with the symbols and indications shown below and then continue to read the manual.
Make sure that you observe all cautions given.
Explanation of markings
Marking Meaning of marking
Indicates that errors in operation may lead to death or serious injury.
Caution Indicates that errors in operation may lead to injury (*1) to people or that these
errors may cause damage to physical property. (*2)
(*1) Such things as injury, burns or shock that will not require hospitalization or long periods of outpatient treatment.
(*2) Physical property damage refers to wide-ranging damage to assets and materials.
Meanings of symbols
Marking Meaning of marking
Indicates prohibition (Don't do it).
What is prohibited will be described in or near the symbol in either text or
picture form.
Indicates something mandatory (must be done).
What is mandatory will be described in or near the symbol in either text or
picture form.
•Indicates warning.
What is warned will be described in or near the symbol in either text or picture
form.
•Indicates caution.
What the caution should be applied to will be described in or near the symbol in
either text or picture form.
Limits in purpose
This inverter is used for controlling speeds of three-phase induction motors in general industrial use.
Safety precautions
▼The inverter cannot be used in any device that would present danger to the human
body or which a malfunction or error in operation would present a direct threat to
human life (nuclear power control device, aviation and space flight control device,
traffic device, life support or operation system, safety device, etc.). If the inverter is
to be used for any special purpose, first get in touch with the supplier.
▼When using inverters for critical equipment, even though the inverters are
manufactured under strict quality control always fit your equipment with safety
devices to prevent serious accident or loss should the inverter fail (such as failure
to issue an inverter trouble signal)
▼Do not use the inverter for loads other than those of properly applied three-phase
induction motors in general industrial use.
(Use in other than properly applied three-phase induction motors may cause an
accident.)
When the inverter is used to control the operation of a permanent magnet motor, a
combination test must be conducted in advance. For details on the test, contact
your supplier.
Warning

E6581531
2
I General Operation
Warning Reference
Disassembly
prohibited
• Never disassemble, modify or repair. This can result in electric shock, fire and injury. For
repairs, call your sales agency.
2.
Prohibited
• Never remove the front cover when power is on or open door if enclosed in a cabinet.
The unit contains many high voltage parts and contact with them will result in electric shock.
• Don't stick your fingers into openings such as cable wiring hole and cooling fan covers. This
can result in electric shock or other injury.
• Don't place or insert any kind of object into the inverter (electrical wire cuttings, rods, wires).
This can result in electric shock or fire.
• Do not allow water or any other fluid to come in contact with the inverter. This can result in
electric shock or fire.
2.
2.
2.
2.
Mandatory
• Turn power on only after attaching the front cover or closing door if enclosed in a cabinet.
If power is turned on without the front cover attached or closing door if enclosed in a cabinet,
this can result in electric shock or other injury.
• If the inverter begins to emit smoke or an unusual odor, or unusual sounds, immediately turn
power off. If the equipment is continued to operate in such a state, the result may be fire.
Call your local sales agency for repairs.
• Always turn power off if the inverter is not used for long periods of time since there is a
possibility of malfunction caused by leaks, dust and other material.
The leakage current caused by the contamination may result in fire.
2.
3.
3.
3.
Caution Reference
Prohibited
contact
• Do not touch any radiating fins or radiating resistors.
They can become very hot, and you may get burned if you touch them.
3.

E6581531
3
I
Transportation & installation
Reference
Prohibited
• Do not install or operate the inverter if it is damaged or any component is missing. This can
result in electric shock or fire. Please consult your local sales agency for repairs.
• Do not place any inflammable objects nearby. If a flame is emitted due to malfunction, it
may result in a fire.
• Do not install in any location where the inverter could come into contact with water or other
fluids. This can result in electric shock or fire.
2.
1.4.4
2.
Mandatory
• Must be used in the environmental conditions prescribed in the instruction manual. Use
under any other conditions may result in malfunction.
• Must be installed in non-inflammables such as metals.
The rear panel gets very hot. If installation is in an inflammable object, this can result in fire.
• Do not operate with the front panel cover removed. Doing so could result in electric shock.
• An emergency stop device must be installed that fits with system specifications (e.g. shut
off input power then engage mechanical brake).
Operation cannot be stopped immediately by the inverter alone, thus risking an accident or
injury.
• All options used must be those specified by Toshiba.
The use of any other option may result in an accident.
1.4.4
1.4.4
1.4.4
10.
1.4.4
1.4.4
Caution Reference
Prohibited
• When operating, do not hold by the front panel covers.
The covers may come off and the unit will drop out resulting in injury.
• Do not install in any area where the unit would be subject to large amounts of vibration.
That could result in the unit falling, resulting in injury.
• ..Do not expose the drive to halogen group disinfectants.
Failure to comply may cause damage to the electrical components in the drive.
2.
1.4.4
Mandatory
• The Inverter should be carried by 2 people more, or it could fall and cause an injury.
• Handle large capacity models using a crane.
Lifting heavy inverters can cause injury to persons.
Taking care of safety for users, handle carefully in order not to damage the inverter.
Carefully lift up the inverter, hanging wires on the hanging bolts or holes on the top or
bottom of the inverter.
Note 1: Always keep the two sling ropes in balance when lifting the inverter, and take care
that unexpected force does not apply to the inverter during lifting.
Note 2: Always protect the inverter with a cover when transporting it.
Note 3: Do not put your hand in the wiring port or do not hold it when transporting the
inverter.
• The main unit must be installed on a base that can bear the unit's weight.
If the unit is installed on a base that cannot withstand that weight, the unit may fall resulting
in injury.
• Install a mechanical brake whenever the motor requires a brake (device which retains the
motor shaft).
Failure to do so could lead to injury to persons because the inverter itself has no function of
mechanically retaining the brake shaft.
2.
1.4.4
1.4.4
Warning

E6581531
4
I Wiring
Reference
Prohibited
• Do not connect input power to the output (motor side) terminals (U/T1,V/T2,W/T3).
That will destroy the inverter and may result in fire.
• Do not connect resistors to the DC terminals (between PA/+ and PC/-, or between PO and
PC/-).
That may cause a fire.
Connect resistors as directed by the instructions for “Installing separate braking resistors.”
• Within 15 minutes after turning off input power, do not touch wires of devices (MCCB)
connected to the input side of the inverter.
That could result in electric shock.
2.2
2.2
5.19
2.2
Mandatory
• Electrical construction work must be done by a qualified expert.
Connection of input power by someone who does not have that expert knowledge may
result in fire or electric shock.
• Connect output terminals (motor side) correctly.
If the phase sequence is incorrect, the motor will operate in reverse and that may result in
injury.
• Wiring must be done after installation.
If wiring is done prior to installation that may result in injury or electric shock.
• The following steps must be performed before wiring.
(1) Turn off all input power to the inverter.
(2) Wait at least 15 minutes and check to make sure that the charge lamp is no longer lit.
(3) Use a tester that can measure DC voltage 1400VDC or more, and check to make sure
that the voltage to the DC main circuits (between PA/+ and PC/-) is 45V or less.
If these steps are not properly performed, the wiring will cause electric shock.
• Tighten the screws on the terminal board to specified torque.
If the screws are not tightened to the specified torque, it may lead to fire.
• Check to make sure that the input power voltage is +10%, -15% of the rated power voltage
written on the rating label (±10% when the load is 100% in continuous operation).
If the input power voltage is not +10%, -15% of the rated power voltage (±10% when the
load is 100% in continuous operation) this may result in fire.
2.
2.
2.
2.
2.
1.4.4
• Ground must be connected securely.
If the ground is not securely connected, it could lead to electric shock or fire when a
malfunction or current leak occurs.
2.
2.2
10.
Caution Reference
Prohibited
• Do not attach equipment (such as noise filters or surge absorbers) that have built-in
capacitors to the output (motor side) terminals.
That could result in a fire.
2.1
Mandatory
• In VFPS1-5040PM or less, Over current trip might be done by leakage current from the
motor and the wiring cable between inverter and motor.
Please take measures refer to the following conditions.
(1) When you use recommended cable size (AWG14) between inverter and motor.
When the wiring distance between the inverter and the motor exceeds 50m.
⇒Please set up the Motor end surge voltage suppression filter in order to suppress the
inverter output voltage surge.
(2) When you use a cable that is thicker than recommended cable size (AWG14) between
inverter and motor.
⇒Please set up the Motor end surge voltage suppression filter in order to suppress the
inverter output voltage surge regardless of the wiring distance between inverter and
motor.
1.5
Caution
Caution
• Charged capacitors can present a shock hazard even after source power is removed.
• Drives with EMC filters will retain a charge on the input terminals for up to 15 min. after the power has been
removed. To avoid electrical shock, don’t touch the connector terminals and uninsulated source cables at
either the main circuit disconnect or the drive until the capacitive charge has dissipated.
Be Grounded
Warning

E6581531
5
I
Operations
Warning Reference
Prohibited
• Do not touch inverter terminals when electrical power is applied to the inverter even if the
motor is stopped.
Touching the inverter terminals while power is connected to it may result in electric shock.
• Do not touch switches when thands are wet and do not try to clean the inverter with a
damp cloth.
Such practices may result in electric shock.
• Do not go near the motor in alarm-stop status when the retry function is selected.
The motor may suddenly restart and that could result in injury.
Take measures for safety, e.g. attaching a cover to the motor, against accidents when the
motor unexpectedly restarts.
• The inverter is tuned automatically (auto-tuning H=, ) when the inverter is started
for the first time after setup.
During auto-tuning, which takes about several seconds to three minute, it is not error that
the tuning time is long.
Do not touch a motor, wiring equipment and so on during the tuning because the motor
doesn't rotate but the electrical power is applied.
Do not approach near the motor and the machine because the motor rotates after the
tuning.
The motor may produce noise during auto-tuning, which, however, does not indicate that
something is wrong with the inverter or the motor.
• Do not set the stall prevention level (H) extremely low.
If the stall prevention level parameter (H) is set at or below the no-load current of the
motor, the stall preventive function will always be active and increase the frequency when it
judges that regenerative braking is taking place.
Do not set the stall prevention level parameter (H) below 30% under normal use
conditions.
3.
3.
3.
6.22
6.33.1
Mandatory
• Do not turn on the power before attaching the front cover.
When storing inside the cabinet and using with the front cover removed, always close the
cabinet doors first and then turn power on. If the power is turned on with the front cover or
the cabinet doors open, it may result in electric shock.
• Make sure that operation signals are off before resetting the inverter after malfunction.
If the inverter is reset before turning off the operating signal, the motor may restart
suddenly causing injury.
• Provide cranes and hoists with sufficient circuit protection such as mechanical braking.
Without sufficient circuit protection, the resulting insufficient motor torque during tuning
could create a risk of machine stalling/falling.
3.
10.
3.
6.22
Caution Reference
Mandatory
• Observe all permissible operating ranges of motors and mechanical equipment. (Refer to
the motor's instruction manual)
Not observing these ranges may result in injury.
3.
When sequence for restart after a momentary failure is selected
Caution Reference
Mandatory
• Stand clear of motors and mechanical equipment.
If the motor stops due to a momentary power failure, the equipment will start suddenly
when power is restored.
This could result in unexpected injury.
• Attach cautions about sudden restart after a momentary power failure on inverters, motors
and equipment for prevention of accidents in advance.
5.18.1
When retry function is selected
Caution Reference
Mandatory
• Stand clear of motors and equipment.
If the motor and equipment stop when the alarm is given, selection of the retry function will
restart them suddenly after the specified time has elapsed and alarm condition has
disappeared. This could result in unexpected injury.
• To prevent accidents, stick caution notices that the inverter has a retry function to the
inverter, the motor and the machine.
6.14.1

E6581531
6
I Maintenance and inspection
Warning Reference
Prohibited
• Never replace any part by yourself.
This could be a cause of electric shock, fire and bodily injury. To replace parts, call the local
sales agency.
14.2
Mandatory
• The equipment must be inspected frequently.
If the equipment is not inspected and maintained, errors and malfunctions may not be
discovered which could lead to accidents.
• Before inspection, perform the following steps.
(1) Turn off all input power to the inverter.
(2) Wait at least 15 minutes and check to make sure that the charge lamp is no longer lit.
(3) Use a tester that can measure DC voltage 1400VDC or more, and check to make sure
that the voltage to the DC main circuits (between PA/+ and PC/-) is 45V or less.
If inspection is performed without performing these steps first, it could lead to electric
shock.
14.
14.
14.2
Disposal
Caution Reference
Mandatory
• If you throw away the inverter, have it done by a specialist in industry waste disposal*.
If you throw away the inverter by yourself, this can result in explosion of capacitor or
produce noxious gases, resulting in injury.
(*) Persons who specialize in the processing of waste and known as “industrial waste product
collectors and transporters” or “industrial waste disposal persons.” If the collection,
transport and disposal of industrial waste is done by someone who is not licensed for that
job, it is a punishable violation of the law. (Laws in regard to cleaning and processing of
waste materials)
16.
Attach caution labels
Shown here are examples of caution labels to prevent, in advance, accidents in relation to inverters, motors and
other equipment.
If the inverter has been programmed for auto-restart function after momentary power failure or retry function, place
caution labels in a place where they can be easily seen and read.
If the inverter has been programmed for restart
sequence of momentary power failure, place
caution labels in a place where they can be easily
seen and read.
(Example of caution label)
If the retry function has been selected, place
caution labels in a location where they can be
easily seen and read.
(Example of caution label)
Caution
(Functions programmed for restart) Caution
(Functions programmed for retry)
Do not go near motors and equipment.
Motors and equipment that have stopped
temporarily after momentary power failure
will restart suddenly after recovery.
Do not go near motors and equipment.
Motors and equipment that have stopped
temporarily after an alarm will restart
suddenly after the specified time has elapsed
and alarm condition has disappeared.

E6581531
7
II
II. Introduction
Thank you for your purchase of the Toshiba “TOSVERT VF-PS1” industrial inverter.
This instruction manual is intended for inverters with CPU version 650 or later for VFPS1-5*** and
CPU version 650 or later for VFPS1-6***. The CPU version will be frequently upgraded.

E6581531
i
- Contents -
I. Safety precautions ······················································································································································ 1
I I. Introduction ······························································································································································· 7
1. Read first····························································································································································· A-1
1.1 Check the product········································································································································ A-1
1.2 Contents of the product code ······················································································································· A-1
1.3 The product classes for input voltage··········································································································· A-2
1.4 Structure of the main body ··························································································································· A-4
1.4.1 Names and functions ···························································································································· A-4
1.4.2 Detaching the cover······························································································································ A-9
1.4.3 Grounding capacitor switching method ································································································· A-12
1.4.4 Installing the transformers on VFPS1···································································································· A-14
1.5 Notes on the application······························································································································· A-19
1.5.1 Motors··················································································································································· A-19
1.5.2 Inverters················································································································································ A-21
1.5.3 What to do about the leak current········································································································· A-22
1.5.4 Installation············································································································································· A-24
2. Connection equipment ········································································································································ B-1
2.1 Cautions on wiring········································································································································ B-1
2.2 Standard connections··································································································································· B-3
2.3 Description of terminals································································································································ B-10
2.3.1 Main circuit terminals ···························································································································· B-10
2.3.2 Control circuit terminal block················································································································· B-11
2.3.3 Serial RS485 communication connector······························································································· B-16
3. Operations··························································································································································· C-1
3.1 Setting/monitor modes ································································································································· C-2
3.2 Simplified operation of the VF-PS1 ·············································································································· C-3
3.2.1 Terminal board operation ······················································································································ C-3
3.2.2 Panel operation····································································································································· C-7
4. Searching and setting parameters······················································································································· D-1
4.1 How to set parameters ································································································································· D-2
4.1.1 Setting parameters in the selected quick mode ···················································································· D-2
4.1.2 Setting parameters in the standard setting mode·················································································· D-3
4.2 Functions useful in searching for a parameter or changing a parameter setting·········································· D-4
5. Basic parameters ················································································································································ E-1
5.1 History function ············································································································································ E-1
5.2 Setting acceleration/deceleration time ········································································································· E-2
5.2.1 Automatic acceleration/deceleration ····································································································· E-2
5.2.2 Manually setting acceleration/deceleration time ··················································································· E-3
5.3 Increasing starting torque····························································································································· E-3
5.4 Setting parameters by operating method ····································································································· E-5
5.5 Selection of operation mode ························································································································ E-6
5.6 Selecting control mode································································································································· E-11
5.7 Manual torque boost–increasing torque boost at low speeds ······································································ E-16
5.8 Base frequency ············································································································································ E-16
5.9 Maximum frequency····································································································································· E-17
5.10 Upper limit and lower limit frequencies········································································································· E-17
5.11 Setting frequency command characteristics································································································· E-18
5.12 Preset speed operation (speeds in 15 steps))··························································································· E-18
5.13 Selecting forward and reverse runs (operation panel only) ·········································································· E-20
5.14 Setting the electronic thermal······················································································································· E-21
5.15 Changing the display unit % to A (ampere)/V (volt)······················································································ E-25

E6581531
ii
5.16 Meter setting and adjustment························································································································ E-26
5.17 PWM carrier frequency ································································································································· E-30
5.18 Trip-less intensification ································································································································· E-31
5.18.1 Auto-restart (Restart during coasting)···································································································· E-31
5.18.2
Regenerative power ride-through control/
Deceleration stop during power failure ········································ E-32
5.19 Dynamic (regenerative) braking - For abrupt motor stop ·············································································· E-34
5.20 Standard default setting ································································································································ E-39
5.21 Searching for all reset parameters and changing their settings ···································································· E-42
5.22 EASY key function ········································································································································ E-43
6. Extended parameters··········································································································································· F-1
6.1 Input/output parameters································································································································ F-1
6.1.1 Low-speed signal··································································································································· F-1
6.1.2 Putting out signals of arbitrary frequencies···························································································· F-2
6.2 Input signal selection ···································································································································· F-3
6.2.1 Priority when forward/reverse run commands are entered simultaneously············································ F-3
6.2.2 Assigning priority to the terminal board in the operation panel and operation mode ····························· F-4
6.2.3 Analog input signal switching················································································································· F-5
6.3 Terminal function selection···························································································································· F-6
6.3.1 Keeping an input terminal function always active (ON)·········································································· F-6
6.3.2 Modifying input terminal functions ········································································································· F-6
6.3.3 Modifying output terminal functions ······································································································· F-8
6.4 Basic parameters 2······································································································································· F-8
6.4.1 Switching among V/f characteristics 1 and 2 from input terminal··························································· F-8
6.5 V/f 5-point setting·········································································································································· F-10
6.6 Speed command switching ··························································································································· F-10
6.6.1 Using two types of frequency (speed)commands ················································································· F-10
6.7 Operation frequency ····································································································································· F-12
6.7.1 Start frequency/Stop frequency·············································································································· F-12
6.7.2 Run/Stop control with frequency setting signals ···················································································· F-12
6.7.3 Frequency setting signal 0Hz dead zone handling function··································································· F-13
6.8 DC braking···················································································································································· F-13
6.8.1 DC braking············································································································································· F-13
6.8.2 Motor shaft fixing control························································································································ F-15
6.8.3 Function of issuing a 0Hz command during a halt ················································································· F-16
6.9 Auto-stop in case of lower-limit frequency continuous operation ·································································· F-17
6.10 Jog run mode················································································································································ F-18
6.11 Setting frequency via external contact input (Up/Down frequency setting) ··················································· F-19
6.12 Jump frequency - jumping resonant frequencies ·························································································· F-21
6.13 Preset speed operation frequencies ············································································································· F-22
6.13.1 Preset speed operation frequency 8 to 15····························································································· F-22
6.13.2 Forced oeration control·························································································································· F-22
6.14 Bumpless operation ······································································································································ F-23
6.15 Trip-less intensification ································································································································· F-24
6.15.1 Retry function ········································································································································ F-24
6.15.2 Avoiding overvoltage tripping················································································································· F-25
6.15.3 Output voltage adjustment/Supply voltage correction············································································ F-25
6.15.4 Reverse run prohibition·························································································································· F-27
6.16 Drooping control ··········································································································································· F-27
6.17 Commercial power/inverter switching ··········································································································· F-29
6.18 PID control ···················································································································································· F-31
6.19 Setting motor constants ································································································································ F-35
6.20 Increasing the motor output torque further in low speed range····································································· F-39
6.21 Torque limit ··················································································································································· F-40
6.22 Speed control gain ········································································································································ F-41
6.23 Fine adjustment of frequency setting signal·································································································· F-42
6.24 Operating a synchronous motor···················································································································· F-43

E6581531
iii
6.25 Acceleration/deceleration 2·························································································································· F-43
6.25.1 Setting acceleration/deceleration patterns and switching acceleration/deceleration patterns 1 and 2 ·· F-43
6.26 Protection functions······································································································································ F-46
6.26.1 Setting of stall prevention level ············································································································· F-46
6.26.2 Stall prevention control switching·········································································································· F-46
6.26.3 Inverter trip record retention·················································································································· F-46
6.26.4 Emergency stop···································································································································· F-47
6.26.5 Output phase failure detection ·············································································································· F-48
6.26.6 OL reduction starting frequency ············································································································ F-48
6.26.7 Input phase failure detections ··············································································································· F-48
6.26.8 Control mode for low current················································································································· F-49
6.26.9 Detection of output short circuit ············································································································ F-50
6.26.10 Overtorque trip······································································································································ F-50
6.26.11 Cooling fan control selection················································································································· F-51
6.26.12 Cumulative operation time alarm setting······························································································· F-51
6.26.13 Abnormal speed detection ···················································································································· F-52
6.26.14 Overvoltage limit operation ··················································································································· F-52
6.26.15 Undervoltage trip··································································································································· F-52
6.26.16 Regenerative power ride through control level······················································································ F-53
6.26.17 VI/II analog input wire breakage detection level···················································································· F-53
6.26.18 Guide to time of replacement················································································································ F-54
6.26.19 Rush current suppression relay activation time ···················································································· F-54
6.26.20 Motor thermal protection ······················································································································· F-54
6.26.21 Braking resistance overload curve ········································································································ F-54
6.26.22 Selection of a restart condition for the motor stopped with a mechanical brake ··································· F-55
6.26.23 Motor PTC thermal protection··············································································································· F-56
6.26.24 Protection against a failure of the control power backup device (optional CPS002Z)··························· F-56
6.27 Forced fire-speed control function················································································································ F-58
6.28 Low torque detection signals························································································································ F-59
6.29 Override ······················································································································································· F-60
6.30 Adjustment parameters ································································································································ F-62
6.30.1 Pulse train output for meters················································································································· F-62
6.30.2 Setting of optional meter outputs ·········································································································· F-63
6.30.3 Calibration of analog outputs ················································································································ F-63
6.31 Operation panel parameter ·························································································································· F-64
6.31.1 Prohibition of key operations and parameter settings ··········································································· F-64
6.31.2 Displaying the rotational speed of the motor or the line speed ····························································· F-65
6.31.3 Changing the steps in which the value displayed changes ··································································· F-66
6.31.4 Changing the standard monitor display································································································· F-67
6.31.5 Selection of operation panel stop pattern······························································································ F-67
6.32 Tracing functions·········································································································································· F-67
6.33 Integrating wattmeter ··································································································································· F-71
6.34 Communication function······························································································································· F-72
6.34.1 2-wire RS485/4-wire RS485 ················································································································· F-72
6.34.2 Open network option····························································································································· F-79
6.35 My function··················································································································································· F-79
6.36 Instruction manuals for optionally available devices and special functions ·················································· F-80
7. Operation with external signal ····························································································································· G-1
7.1 External operation········································································································································ G-1
7.2 Applied operation with input and output signals (operation by terminal board) ············································ G-2
7.2.1 Functions of input terminals (in case of sink logic)················································································ G-2
7.2.2 Functions of output terminals (in case of sink logic)·············································································· G-5
7.2.3 Analog input filter ·································································································································· G-9
7.3 Setup of external speed command (analog signal) ······················································································ G-10
7.3.1 Setup by analog input signals (RR/S4 terminal) ··················································································· G-11
7.3.2 Setup by analog input signals (VI/II terminal)························································································ G-12
7.3.3 Setup by analog input signals (RX terminal) ························································································· G-13

E6581531
iv
8. Monitoring the operation status···························································································································· H-1
8.1 Screen composition in the status monitor mode ··························································································· H-1
8.2 Monitoring the status····································································································································· H-2
8.2.1 Status monitor under normal conditions································································································· H-2
8.2.2 Display of detailed information on a past trip ························································································· H-5
8.3 Changing status monitor function·················································································································· H-6
8.4 Display of trip information ····························································································································· H-9
8.4.1 Trip code display···································································································································· H-9
8.4.2 Monitor display at tripping······················································································································ H-11
8.5 Display of alarm, pre-alarm, etc. ··················································································································· H-13
9. Measures to satisfy the standards························································································································ I-1
9.1 How to cope with the CE standard················································································································ I-1
9.1.1 EMC directive ········································································································································ I-1
9.1.2 Measures to satisfy the EMC directive ·································································································· I-2
9.1.3 Low-voltage directive ····························································································································· I-3
9.1.4 Measures to be taken to satisfy the low-voltage directive······································································ I-4
9.2 Measures to be taken to satisfy the UL/CSA standards················································································ I-4
9.2.1 Caution in installing the inverter············································································································· I-4
9.2.2 Caution in wiring and rated current········································································································ I-4
9.2.3 Caution as to peripheral devices ··········································································································· I-5
9.2.4 Caution as to the protection of motors from overload ············································································ I-5
9.3 Compliance with safety standards ················································································································ I-6
10. Selection of peripheral devices ···························································································································· J-1
10.1 Selection of wiring materials and devices ····································································································· J-1
10.2 Installation of a magnetic contactor··············································································································· J-5
10.3 Installation of an overload relay ···················································································································· J-5
10.4 Application and functions of options ············································································································· J-6
10.5 Optional internal devices······························································································································· J-9
10.6 Connection of a DC power terminals ············································································································ J-12
11. Table of parameters ············································································································································· K-1
12. Specifications ······················································································································································· L-1
12.1 Models and their standard specifications ······································································································ L-1
12.2 Outside dimensions and mass······················································································································ L-6
13. Before making a service call- Trip information and remedies··············································································· M-1
13.1 Trip causes/warnings and remedies ············································································································· M-1
13.2 Method of resetting causes of trip················································································································· M-7
13.3 If the motor does not run while no trip message is displayed…···································································· M-8
13.4 How to check other troubles ························································································································· M-9
14. Inspection and maintenance ································································································································ N-1
14.1 Regular inspection ········································································································································ N-1
14.2 Periodical inspection····································································································································· N-2
14.3 Making a call for servicing····························································································································· N-4
14.4 Keeping the inverter in storage ····················································································································· N-4
15. Warranty······························································································································································· O-1
16. Disposal of the inverter ········································································································································ P-1

E6581531
A-1
1
1. Read first
1.1 Check the product
Before using the product you have purchased, check to make sure that it is exactly what you ordered.
Caution
Mandatory
Use an inverter that conforms to the specifications of the power supply and three-phase induction
motor being used. If the inverter being used does not conform to those specifications, not only will
the three-phase induction motor not rotate correctly, but it may cause serious accidents through
overheating and fire.
Type indication
label
Series name
Power supply
Motor capacity
Inverter Type
Applicable motor
Invert rated output capacity
Power supply
Related input current
Related output current
Serial No.
Type indication Inverter main unit
Carton box
Name plate
Warning label
VF-PS1 3PH-500/600/690V
11kW/ 15HP/15kW
Type indication
Name plate
Warning label
Instruction manual
This manual
Risk of injury, electric shock or fire.
・
Read the Instr uction Manual.
・
Do not open the cover while power is applied o
r
for 15 minutes after power has been removed.
・
Ensure proper ear th connection.
DANGER
1. 2 Contents of the product code
Explanation of the type and form written on the label.
Type Form
V F P S 1 - 6 1 5 0 P L Y - WN - A 2 2
Model name
TOSVERT
VF-PS1 series
Operation panel
P: Provided
Additional functions II
Y: Others
(non-standard)
Applicable motor capacity
for 690V Power supply
030:3.0kW
055:5.5kW
075:7.5kW
110:11kW
150:15kW
185:18.5kW
220:22kW
300:30kW
370:37kW
450:45kW
550:55kW
750:75kW
900:90kW
110K:110kW
132K:132kW
160K:160kW
200K:200kW
250K:250kW
315K:315kW
400K:400kW
500K:500kW
630K:630kW
Voltage class
5: 500V~600V
6: 500V~690V
Special
specification code
A: Special
specification code
(is a number)
Additional functions I
L: Built-in EMC filter
+
basic filter
M: Built-in basic filter
C: Built-in EMC filter
S
p
ecial s
p
ecification code
Default interface logic
WN: Negative
HN: US Negative
*1)
*1): Applicable motor capacity changes with power supply. ⇒For more details, refer to Section 1.3 or Section 12.

E6581531
A-2
1
1.3 The product classes for input voltage
The 600V series of VFPS1 has the following three kinds of voltage classes. There are 500V, 575V and 690V class.
Note
★ VFPS1-5*** : Applied power source voltage 500V to 600V.
★ VFPS1-6*** : A
pp
lied
p
ower source volta
g
e 500V to 690V.
Power supply 500V ( 500V class) and
Power supply 600V
(
575V class
)
A
pplicable Moto
r
Power supply 690V (690V class)
A
pplicable Moto
r
132kW / -
18.5kW / 25HP
30kW / 40HP
45kW / 60HP
75kW / 100HP
VFPS1-6110PL
11kW / 15HP
15kW / 20HP
55kW / 75HP
37kW / 50HP
22kW / 30HP
110kW / 150HP
90kW / 125HP
315kW / 450HP
250kW / 350HP
200kW / 250HP
160kW / 200HP
500kW / 700HP
VFPS1
-
5022PM
2.2kW / 3HP
VFPS1
-
5030PM
VFPS1-6030PL
VFPS1
-
5040PM
VFPS1-6055PL
4.0kW / 5HP
VFPS1
-
5055PM
VFPS1-6055PL
5.5kW / 7.5HP
VFPS1
-
5075PM
VFPS1-6075PL7.5kW / 10HP
400kW / 550HP
VFPS1-6132KPC
VFPS1-6185PL
VFPS1-6300PL
VFPS1-6450PL
VFPS1-6750PL
VFPS1-6150PL
VFPS1-6550PL
VFPS1-6370PL
VFPS1-6220PL
VFPS1-6110KPC
VFPS1-6900PL
VFPS1-6315KPC
VFPS1-6250KPC
VFPS1-6200KPC
VFPS1-6160KPC
VFPS1-6500KPC
VFPS1-6400KPC
VFPS1-6630KPC
VFPS1-6132KPC
VFPS1-6185PL
VFPS1-6300PL
VFPS1-6450PL
VFPS1-6750PL
VFPS1-6150PL
VFPS1-6550PL
VFPS1-6370PL
VFPS1-6220PL
VFPS1-6110KPC
VFPS1-6900PL
VFPS1-6315KPC
VFPS1-6250KPC
VFPS1-6200KPC
VFPS1-6160KPC
VFPS1-6500KPC
VFPS1-6400KPC
VFPS1-6630KPC
132kW
18.5kW
30kW
45kW
75kW
11kW
15kW
55kW
37kW
22kW
110kW
90kW
315kW
250kW
200kW
160kW
500kW
3.0kW
4.0kW
5.5kW
7.5kW
400kW
630kW
3.0kW / -

E6581531
A-3
1
The default setting of all products is 575V-60Hz.
You can change it to other voltage class Inverter(500V-50Hz or 690V-50Hz) by changing the "V[R" parameter.
Title Function Adjustment range Default setting
V[R Factory default setting
: -
: 500V-50Hz default setting
: 575V-60Hz default setting
: 690V-50Hz default setting
Please refer to Chapter 11 Table of parameters for the changed parameters by the V[R setting.
[ Instance setting : Set to 690V-50Hz ]
Key operated LED display Operation
Displays the operation frequency. (Perform during operation stopped.)
(When standard monitor display selection H=[Output
frequency])
CWJ Displays the first basic parameter “History function (CWJ).”
V[R Press either the or key to select “V[R.”
Q Press the ENTER key to display the parameter setting (Default
setting:).
Press the key to change the parameter to.
PV
The parameter value is written. After set it, “PV” is displayed
for a while and the display disappears momentarily, it becomes
“” displays.
MODE
ENT
ENT

E6581531
A-4
1
1. 4 Structure of the main body
1.4.1 Names and functions
1) Outside view
Be sure to close the
cover before starting the
operation to prevent
persons from touching
the terminal in error.
Control circuit
terminal cover
Be sure to attach the
cover before starting the
operation to prevent
persons from touching
the terminal in error.
Main circuit terminal
cover
Operation panel
Inverter type and
production No. are on
the back side of the
control circuit terminal
cover.
[Front panel]
Cooling fan
Wiring port
Protective cover on the top [Note]
Name plate
[Bottom view] [Side view]
Note: Remove this cover when installing the inverter side by side with other inverters where the ambient temperature will rise
above 40°C. ⇒For more details, refer to Section 1.5.4.

E6581531
A-5
1
Operation panel
RUN key lamp
Lights when the RUN
key is enabled.
RUN key
Pressing this key while
the RUN key lamp is lit
starts the operation.
Pressing this key while the
RUN key lamp is lit
causes the motor to make
a deceleration stop. Press
the key twice to reset the
inverter after a trip.
STOP key
Up/Down key lamp
With these keys, you
can set the operation
frequency while the
Up/Down key lamp is
lit. [Note 2]
2-wire RS485 connector. This
connector is used to connect an
optional device, such as an
extended control panel.
Up key
Down key
RUN lamp
Lights when an ON
command is issued but no
frequency signal is sent
out. It blinks when
operation is started.
MODE key
Displays the operation
frequency, a
parameter, the cause
of a failure
,
and so on.
MON lamp
Lights when the inverte
r
is in monitor mode.
Blinks when the inverte
r
is placed in trip record
display mode.
PRG lamp
Lights when the
inverter is in parameter
setting mode.
ENTER key
EASY key lamp
Lights when the EASY
key is enabled.
EASY key [Note 1]
Press this key to control
the function assigned
with a parameter.
% lamp
Lights when the unit
is %.
Hz lamp
Lights when the unit is
Hz.
Serial RS485 connector/cover
Note 1: ⇒For details EASY Key functions, refer to Section 5.22.
Note 2: When parameter H is set to , the operation frequency cannot be set even if this lamp is lit.

E6581531
A-6
1
2) Main circuit terminal
M5 screw
Shorting-bar
Grounding terminal
(M5 screw)
Screw hole for EMC plate
VFPS1-5022PM-5075PM
VFPS1-6030PL-6300PL

E6581531
A-7
1
VFPS1-6370PL-6900PL
VFPS1-6110KPC-6200KPC

E6581531
A-8
1
VFPS1-6250KPC~6400KPC
VFPS1-6500KPC-6630KPC
Other manuals for TOSVERT VF-PS1
6
Table of contents
Other Toshiba Power Supply manuals
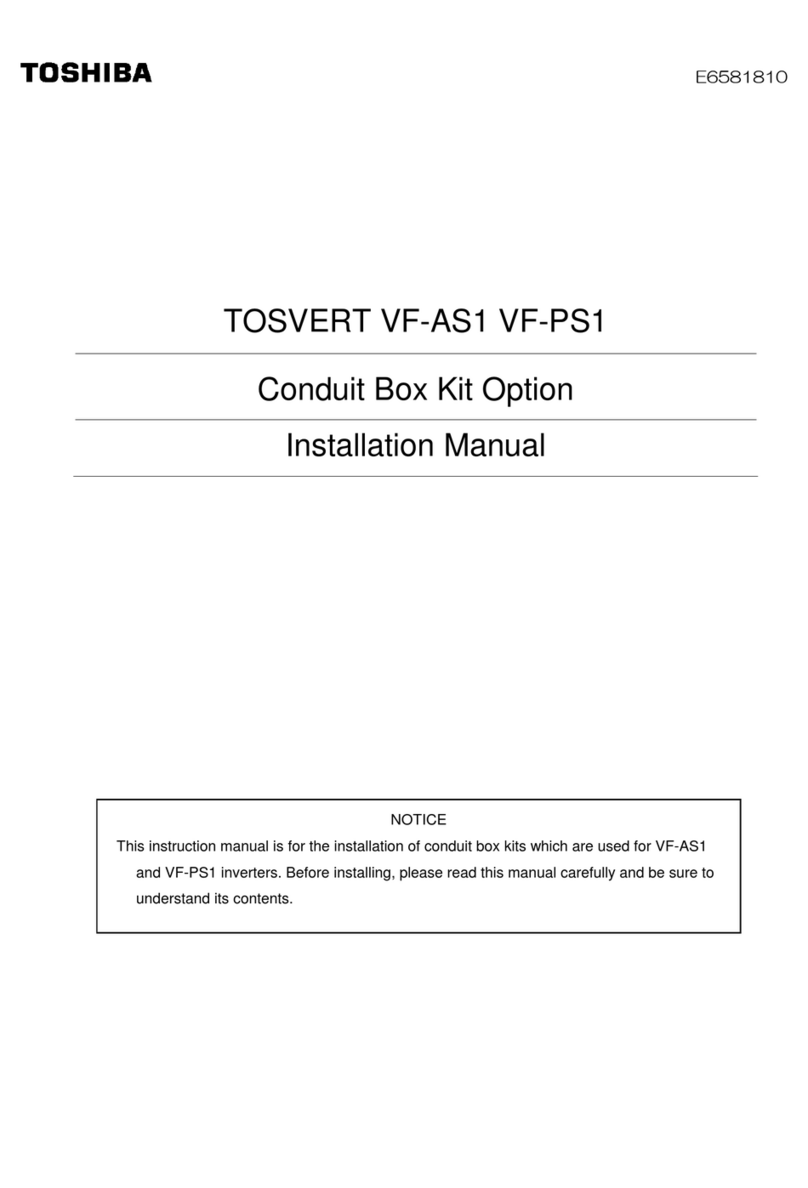
Toshiba
Toshiba TOSVERT VF-AS1 Series User manual
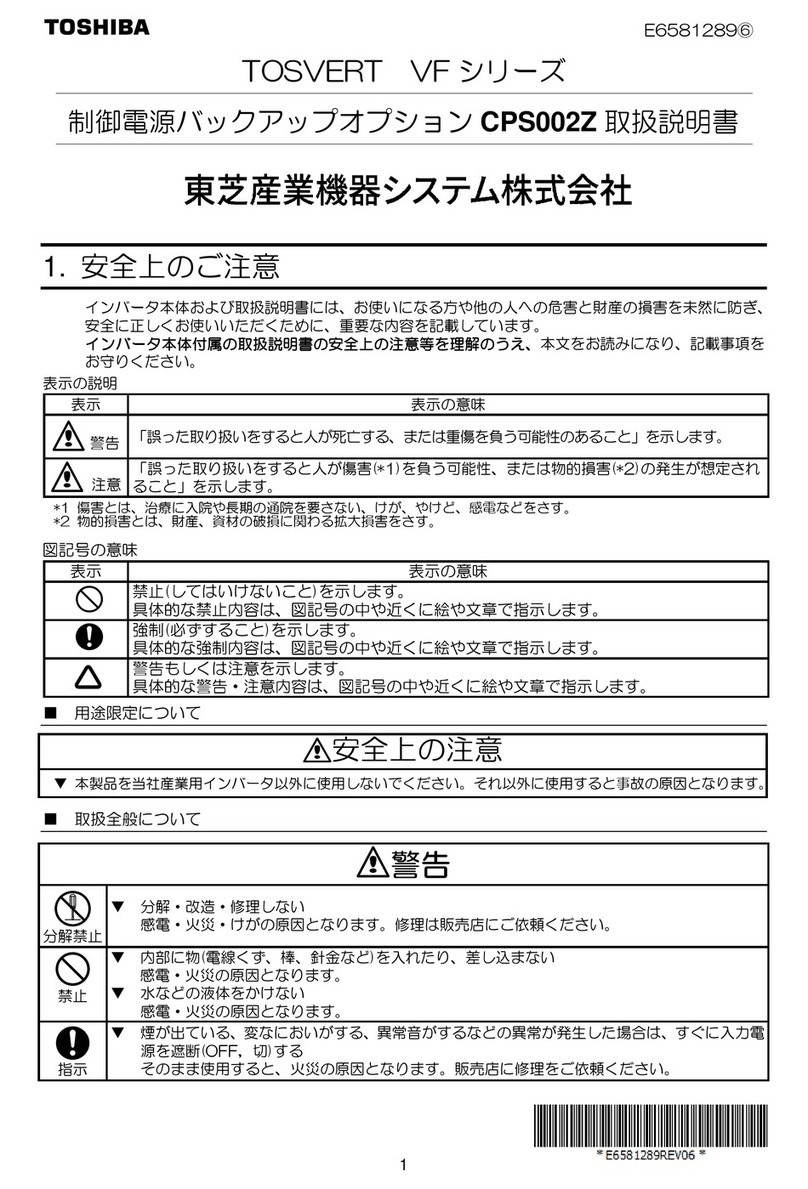
Toshiba
Toshiba CPS002Z User manual
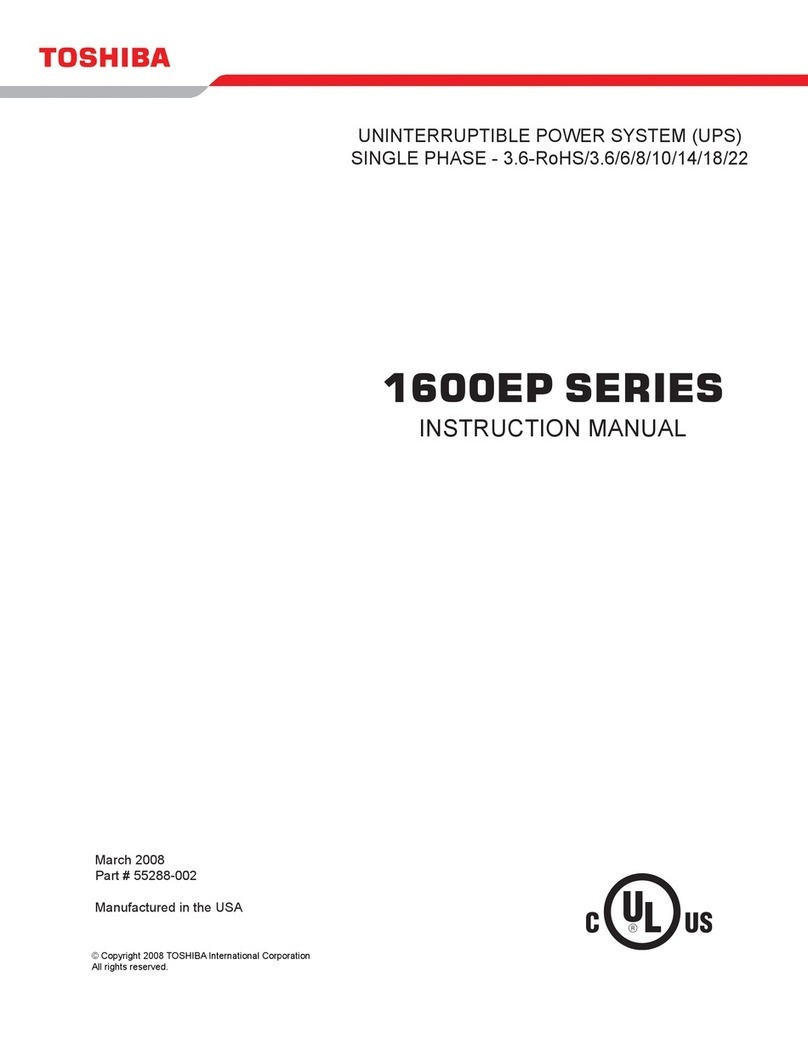
Toshiba
Toshiba 1600EP Series User manual
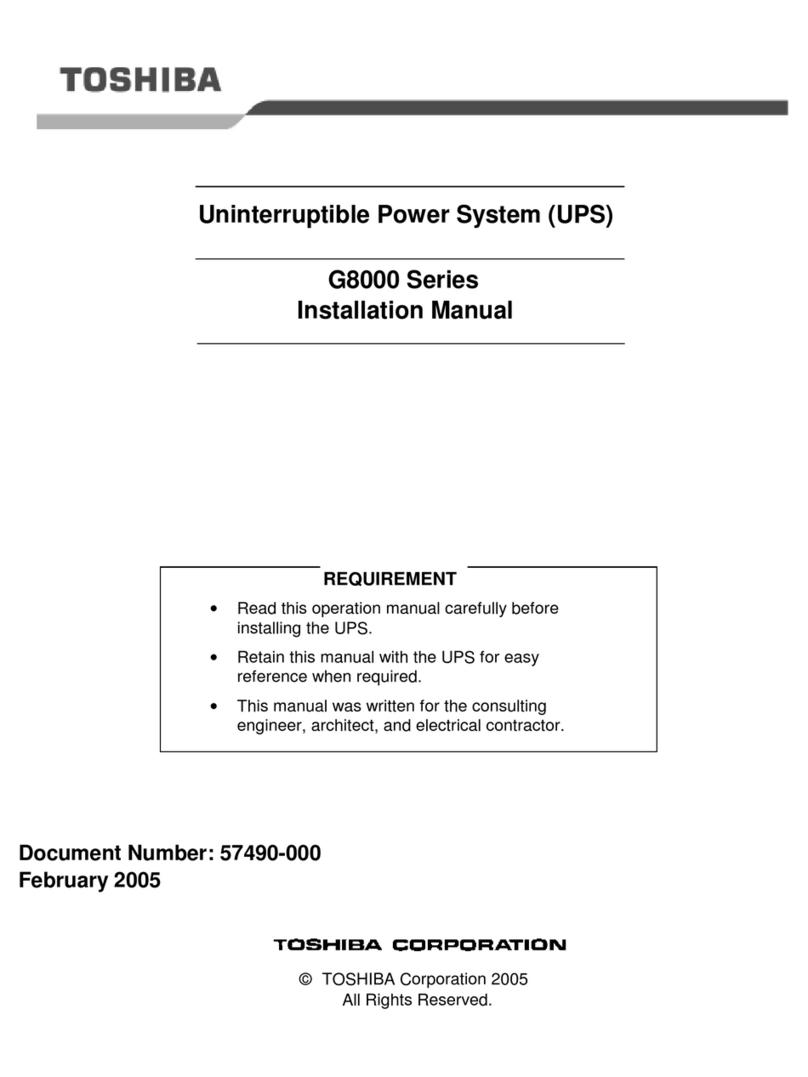
Toshiba
Toshiba G8000 Series User manual
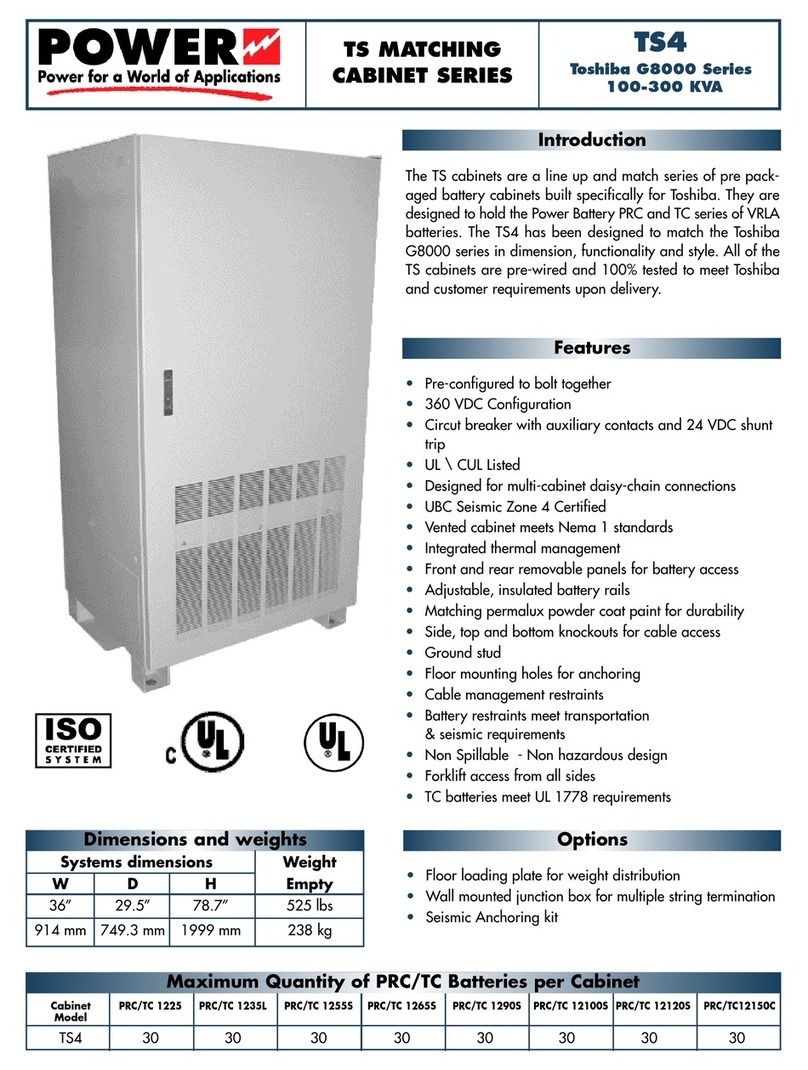
Toshiba
Toshiba Power TS4 User manual

Toshiba
Toshiba Black Gold TB Series User manual
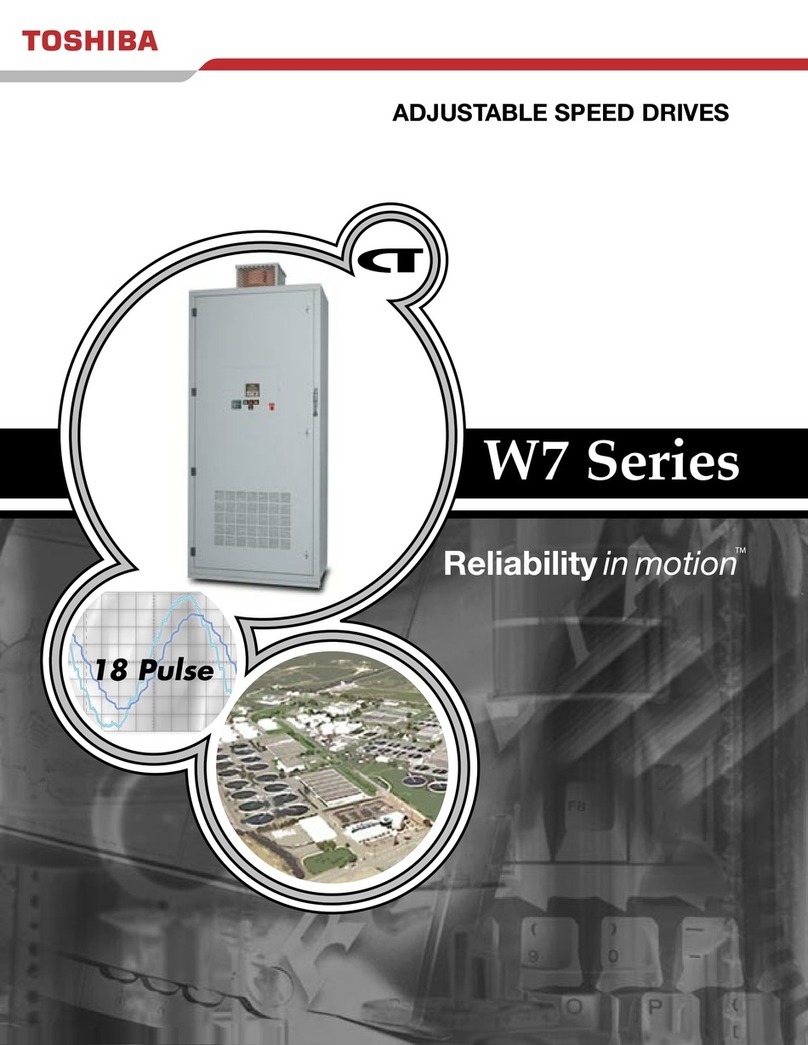
Toshiba
Toshiba W7 Series User manual
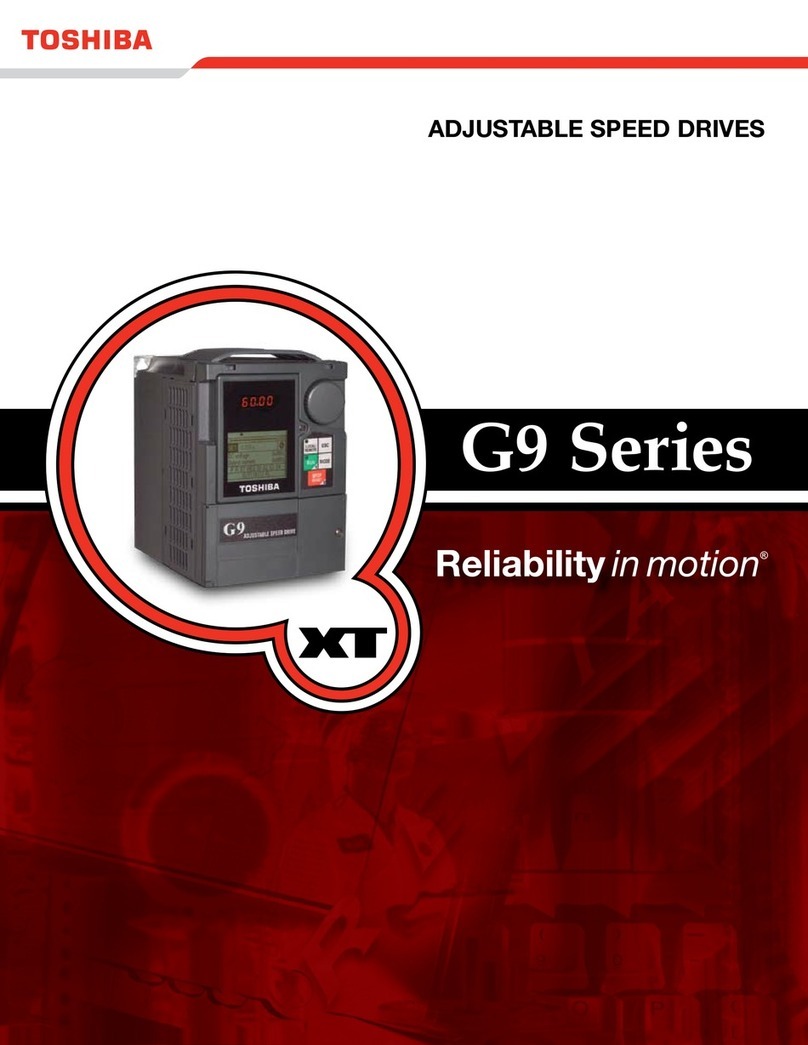
Toshiba
Toshiba RAS-S10CX User manual
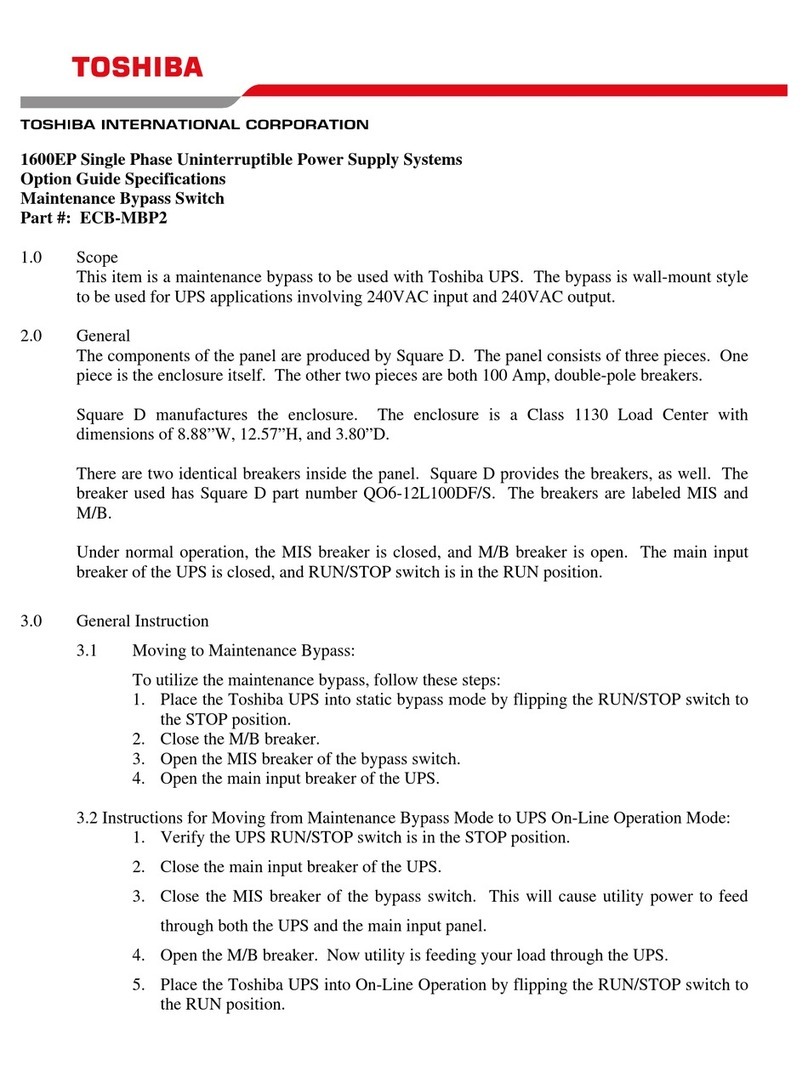
Toshiba
Toshiba 1600EP Series User manual
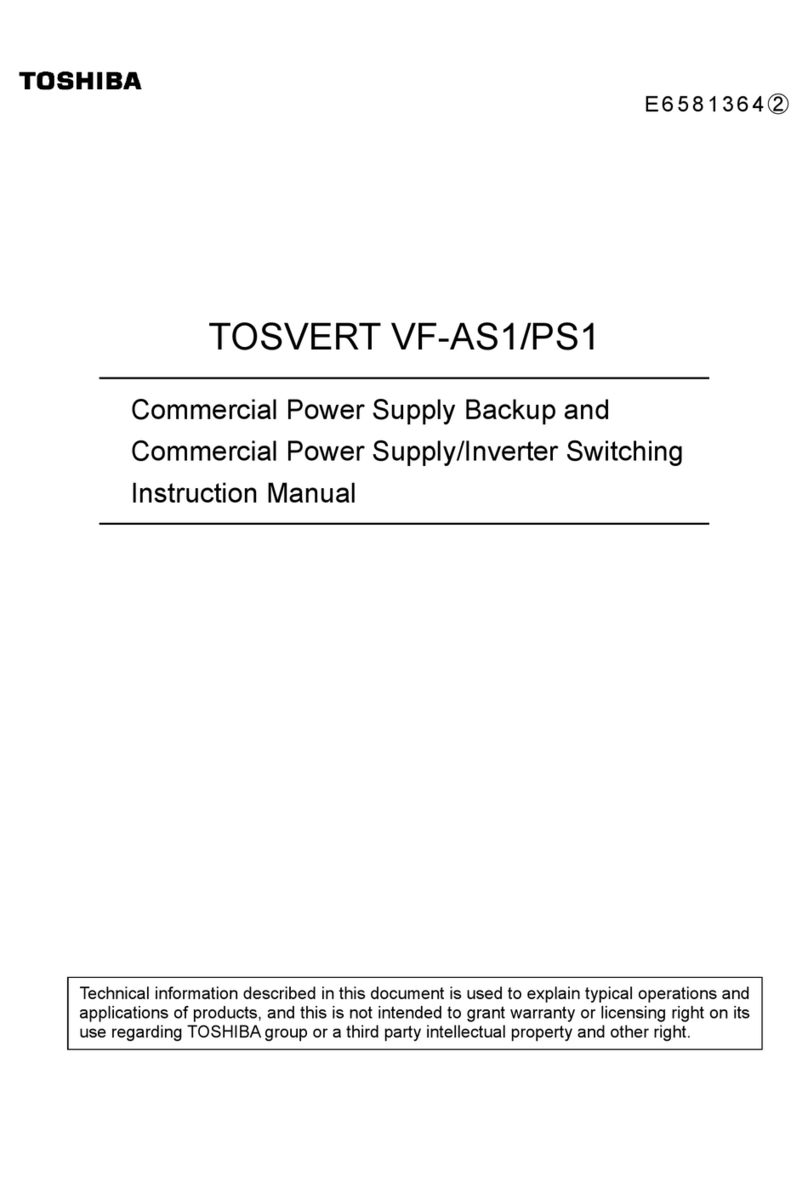
Toshiba
Toshiba TOSVERT VF-AS1 Series User manual