Trinamic TMCM-AC-840 User manual

TMCM-AC-840 Motor Control Daughter Board Kit Manual 1
Copyright © 2010 TRINAMIC Motion Control GmbH & Co. KG
TMCM-AC-840 Motor Control
Daughter Board Kit
for the Actel SmartFusion™Development Kit (A2F-DEV-KIT)
and the Actel SmartFusion™Evaluation Kit (A2F-EVAL-KIT)
Version: 1.40 / September 1st , 2011
TRINAMIC Motion Control GmbH & Co. KG
Waterloohain 5
22769 Hamburg, Germany
Phone +49-40-51 48 06 –0,
FAX: +49-40-51 48 06 –60
http://www.trinamic.com

TMCM-AC-840 Motor Control Daughter Board Kit Manual 2
Copyright © 2010 TRINAMIC Motion Control GmbH & Co. KG
Table of Contents
1INTRODUCTION.............................................................................................................................. 3
2FEATURES...................................................................................................................................... 4
3MOTOR CONTROL KIT INGREDIENTS......................................................................................... 5
4PROGRAMMING............................................................................................................................. 6
5BOARD PICTURES......................................................................................................................... 7
5.1 TOP VIEW V1.2 (LAYOUT)............................................................................................................ 7
5.2 TOP VIEW V1.2 (ASSEMBLED)....................................................................................................... 7
5.3 TOP VIEW V1.3 (LAYOUT)............................................................................................................ 8
5.4 TOP VIEW V1.3 (ASSEMBLED)....................................................................................................... 8
6INCLUDED MOTORS...................................................................................................................... 9
6.1 QMOT QSH4218-35-10-027 STEPPER MOTOR............................................................................ 9
6.2 QMOT QBL4208-41-04-006 BLDC MOTOR............................................................................... 10
7CONNECTING THE BOARD......................................................................................................... 11
7.1 ASSEMBLING THE BOARD…........................................................................................................ 11
7.2 CONNECTION TO THE ACTEL SMARTFUSION™BOARDS .............................................................. 11
7.3 CONNECTING MOTORS TO THE TMCM-AC-840.......................................................................... 12
7.4 CONNECTING THE POWER SUPPLY (TWO SEPARATE OR ONE SINGLE POWER SUPPLY)................. 13
7.5 ADDITIONAL POWER CONNECTORS FOR BOARD REVISION V1.3 AND HIGHER.................................. 14
8PINOUT LISTS............................................................................................................................... 15
8.1 MIXED SIGNAL HEADER CONNECTOR ......................................................................................... 15
8.2 TMC262 SIGNALS..................................................................................................................... 18
8.3 TMC603A SIGNALS .................................................................................................................. 18
8.4 ADDITIONAL PINS AND PIN HEADERS.......................................................................................... 19
8.5 ADDITIONAL SPI HEADER &JUMPER (ONLY REVISION V1.3 AND HIGHER)...................................... 19
8.6 BOARD LEDS............................................................................................................................ 20
9PRECAUTIONS............................................................................................................................. 22
9.1 MAXIMUM CURRENTS ................................................................................................................ 22
10 DEMO DESIGNS........................................................................................................................ 23
11 REFERENCES ........................................................................................................................... 23
12 VERSION.................................................................................................................................... 24

TMCM-AC-840 Motor Control Daughter Board Kit Manual 3
Copyright © 2010 TRINAMIC Motion Control GmbH & Co. KG
1 Introduction
SmartFusion™ FPGA fit well to motion control applications. Due to the combination of hardware,
software, and additional analog components complex systems can be integrated within a single chip.
This drastically reduces the number of required components to realize a motion control unit. Real time
critical tasks can be implemented in hardware. Complex - but less real time critical tasks - can be
realized in software. Real Time critical tasks are commutation of fast rotating BLDC motors or
processing of high resolution encoder signals. Processing of analog signals, e.g., voltage and current
measurement is a typical task in motion control applications. Therefore, the SmartFusion’s™ analog
I/Os and processing functionality can be used.
Together with Trinamic’s integrated BLDC motor gate driver TMC603A (or with the integrated stepper
motor driver TMC262), one can realize a power stage with a couple of components as demonstrated
with the TMCM-AC-840 Daughter Board Kit for direct plug to the ACTEL SmartFusion™ Evaluation Kit
boards or Development Kit boards.
The TRINAMIC TMCM-AC-840 Daughter Board Kit is a power driver for brushless DC motors (BLDC)
as well as stepper motors. The TMCM-AC-840 Daughter Board Kit incorporates one TMC603A BLDC
motor driver IC and one TMC262 coolStep™ stepper motor driver IC as well as two motors (one
BLDC and one stepper motor) and a fitting portable power supply to start right away.
The TMCM-AC-840 is designed to operate with the ACTEL SmartFusion™Development Kit (Revision
C and later) as well as the ACTEL SmartFusion™Evaluation Kit as both boards are pin-compatible
regarding their Mixed Signal Expansion Header (see the ACTEL user guides for both boards). When
using the TMCM-AC-840 in combination with an ACTEL SmartFusion™ Development Kit that is
equipped with the larger A2F500 SmartFusion™ FPGA, some additional analog I/Os are available on
the Mixed Signal Header. All signals of the Mixed Signal Expansion Header are easily accessible via
pin headers on the TMCM-AC-840 daughter board.
The TMCM-AC-840 daughter board requires at least one DC supply voltage of +VM= 12V to 40V.
We recommend driving the board with two independent DC supply voltages –one for each driver IC:
+VM262 = 12V to 40V and +VM603 = 12V to 48V!

TMCM-AC-840 Motor Control Daughter Board Kit Manual 4
Copyright © 2010 TRINAMIC Motion Control GmbH & Co. KG
2 Features
One BLDC motor pre-driver TMC603A
oIntegrated dual range high precision current measurement amplifiers
oSupports shunt less current measurement using power MOS transistor RDSon
ohallFX™ sensorless back EMF commutation emulates hall sensors
oIntegrated break-before-make logic: No special microcontroller PWM hardware
required
oSee the TMC603A datasheet for more information [2]
One stepper motor driver TMC262
oEnergy saving high resolution microstepping two phase stepper driver with step and
direction interface and external power stage
oHigh precision sensor-less motor load measurement stallGuard2™
oEnergy efficiency and coolness by automatic load dependant motor current regulation
technology coolStep™ Save up to 75% of energy!
oSee the TMC262 datasheet for more information [3]
One BLDC Motor (Qmot QBL4208-41-04-006)
oMaximum rated current 1.8A, peak current 5.4A, see motor spec/user guide for more
information on electrical and mechanical parameters [6]
One Stepper Motor (Qmot QSH4218-35-10-027)
oMaximum current 1.0A, see motor spec/user guide for more information on electrical
and mechanical parameters [5]
One portable power supply with international connectors, 24V/1A (version 1.3 and higher)
Hard top case for easy handling and safe transport (version 1.3 and higher)
The Board and the driver stages support maximum motor currents of up to 2A for stepper
driver block and up to 4A (5A with good cooling) for the BLDC driver block.
Easy plug and play solution using the freely available demo design (under BSD) for the BLDC
and stepper functionality
Hall-sensor interface for BLDC motors
ABN encoder interface for high precision position measurement
oThe encoder interface can be used with the stepper or with the BLDC motor.
Various analog signals connected to the analog blocks (Signal Conditioning Blocks, SCBs) of
the Actel SmartFusion™Device for, e.g., voltage measurement
Additional RSENSE measurement pins
All signals of the Mixed Signal Expansion Header can be accessed via additional pin headers
for test and measurement
Parallel operation of BLDC and stepper motor driver
Pin-compatible to both the Actel SmartFusion™Development Kit as well as the Actel
SmartFusion™Evaluation Kit
Each driver requires a separate DC supply voltage
oThe stepper driver block (TMC262): +VM262 = 12V to 40V
oThe BLDC driver block (TMC603A): +VM603 = 12V to 48V
oUsing jumpers, a single power supply can be used for both drivers

TMCM-AC-840 Motor Control Daughter Board Kit Manual 5
Copyright © 2010 TRINAMIC Motion Control GmbH & Co. KG
3 Motor Control Kit Ingredients

TMCM-AC-840 Motor Control Daughter Board Kit Manual 6
Copyright © 2010 TRINAMIC Motion Control GmbH & Co. KG
4 Programming
The voltage supplies (+VM262 and +VM603) of the TMCM-AC-840 daughter board must be
DISCONNECTED or SWITCHED OFF during programming of the Actel SmartFusion™
A2F200/A2F500 device.
For further help on how to program the Actel SmartFusion™ devices refer to the user guides available
on the Actel website http://www.actel.com.

TMCM-AC-840 Motor Control Daughter Board Kit Manual 7
Copyright © 2010 TRINAMIC Motion Control GmbH & Co. KG
5 Board Pictures
5.1 Top View v1.2 (Layout)
5.2 Top View v1.2 (assembled)

TMCM-AC-840 Motor Control Daughter Board Kit Manual 8
Copyright © 2010 TRINAMIC Motion Control GmbH & Co. KG
5.3 Top View v1.3 (Layout)
5.4 Top View v1.3 (assembled)

TMCM-AC-840 Motor Control Daughter Board Kit Manual 9
Copyright © 2010 TRINAMIC Motion Control GmbH & Co. KG
6 Included Motors
The TMCM-AC-840 Daughter Board Kit includes two motors, which fit the daughter board and demo
design –one stepper motor and one BLDC motor. The picture shows how the motors will look like.
6.1 Qmot QSH4218-35-10-027 Stepper Motor
step angle: 1.8˚
optimized for microstep operation
4 wire connection
Coil current 1A RMS
0.27 Nm
Read the motor manual for more information and details on current and voltage settings for different
applications and operating conditions [5].
Wire/connector connections of the Qmot QSH4218-35-10-027 Stepper Motor. Watch the printed
information next to the motor connectors on the board. Connect the motor wires accordingly.

TMCM-AC-840 Motor Control Daughter Board Kit Manual 10
Copyright © 2010 TRINAMIC Motion Control GmbH & Co. KG
6.2 Qmot QBL4208-41-04-006 BLDC Motor
Hall effect angle: 120° electric angle
Max radial force: 28N (10mm from flange)
Max axial force: 10N
Rated phase current: 1.79A
Max peak current: 5.4A
Hall sensor outputs
Read the motor manual for more information and details on current and voltage settings for different
applications and operating conditions [6].
Wire/connector connections of the Qmot QBL4208-41-04-006 BLDC Motor. Watch the printed
information next to the motor connectors on the board. Connect the motor wires accordingly.

TMCM-AC-840 Motor Control Daughter Board Kit Manual 11
Copyright © 2010 TRINAMIC Motion Control GmbH & Co. KG
7 Connecting the Board
7.1 Assembling the board…
The board comes with different plugs, connectors and other stuff.
For the power plugs, two fitting connectors are delivered with the board. Connect them to your
laboratory power supply if you want/need to use other motor supply voltages than 24V/1A.
Take care to connect the correct wires to GND and power pins.
One 3-Wire connector is included for the BLDC UVW-Signals
One 4-Wire connector is included for the Stepper motor signals A1,A2, B1, B2.
Two 5-Wire connectors are included for the hall sensor interface and the encoder interface.
One signal is 5V and one is GND. The remaining signals are A, B, N for the encoder interface
and Hall1, Hall2, Hall3 for the hall sensor interface. See the on-board printing for which pin is
which signal.
The kit also includes 4 self-adhesive rubber feets. If using the Trinamic motor control board
with an Actel/Microsemi SmartFusion Evaluation Kit, use these feets as standoffs for the
motor control board.
The kit also comes with 6 plastic standoffs and 6 plastic screws. They have the same height
as the Actel/Microsemi SmartFusion development kit. So use these standoffs when
connecting the motor control board with a development kit. The motor control kit has 6
mounting holes for this purpose.
7.2 Connection to the Actel SmartFusion™ Boards
When using the Actel SmartFusion™Development Kit, connect the TMCM-AC-840 Daughter Board to
J21 (labeled as Mixed Signal Header) via the H3 board-to-board connector.
When using the Actel SmartFusion™Evaluation Kit, connect the TMCM-AC-840 Daughter Board to
J21 (labeled Mixed Signal Header) via the H3 board-to-board connector.
! Switch off all power supplies when connecting or disconnecting the TMCM-AC-840 Daughter board.
! Carefully connect the boards to not expose the board-to-board connector to mechanical stress.
Therefore –if not done yet –assemble the 6 plastic standoffs and screws to the board.

TMCM-AC-840 Motor Control Daughter Board Kit Manual 12
Copyright © 2010 TRINAMIC Motion Control GmbH & Co. KG
! Make sure there is no air gap remaining between the Actel board and Trinamic’s daughter board as it
is shown in the picture below.
7.3 Connecting Motors to the TMCM-AC-840
Switch off all power supplies when connecting or disconnecting any motor to/from the TMCM-AC-840
daughter board.
Connect a BLDC Motor, e.g., Qmot QBL4208-41-04-006, to the 3 pole motor connector H1 (UVW).
Additionally, Hall Sensor signals can be connected to the 5 pole hall signals connector H4 (+5V, GND,
H1, H2, H3). See the picture below for an example.
Connect a stepper motor, e.g., Qmot QSH4218-35-10-027, to the 4 pole motor connector H14 (A1,
A2, B1, B2).
Additionally, an encoder can be connected to H5 ((+5V, GND, A, B, N). When not using an encoder,
other signals can be connected to the signals A/B/N as well. See the picture below for an example.

TMCM-AC-840 Motor Control Daughter Board Kit Manual 13
Copyright © 2010 TRINAMIC Motion Control GmbH & Co. KG
Do not connect a BLDC motor to the stepper motor interface or vice versa.
If the motors are properly connected, the external power supplies can be connected to H2 and H28
respectively (GND, +VM262, +VM603). Take care to not exceed the maximum supply voltages.
When DISCONNECTING a motor, make sure that the motor is at rest and supplies are switched off
before disconnecting!
7.4 Connecting the Power Supply (two Separate or one Single Power Supply)
Two power connectors exist (H2 and H28), one for each driver block.
Each supply rail is equipped with a diode for protection against reverse polarity.
Do not exceed the maximum recommended supply voltages as printed next to each power connector.
The maximum voltages are +40V for VM262 and +48V for VM603.
! There are some boards with wrong labels saying max. 60V for VM262, but it is 40V always as
the MOSFETs are only specified for up to 40V!
Trinamic recommends using two independent supplies as seen in the picture below. Nevertheless,
when using only one power supply, the Jumpers JVM 1-4 must be connected via bridges. These 4
jumpers are NOT assembled on the board and the bridges to connect them are NOT included in the
board kit.

TMCM-AC-840 Motor Control Daughter Board Kit Manual 14
Copyright © 2010 TRINAMIC Motion Control GmbH & Co. KG
! Trinamic recommends connecting all 4 jumpers (Jumper 1-4) as high currents may occur at these
pins!
! When using only one power supply, the absolute maximum voltage is 40V.
Otherwise the TMC262 driver IC and its MOSFET stages may get damaged.
! Do not connect and switch on two power supplies at the same time while one of the jumpers 1-4 is
still connected.
7.5 Additional power connectors for board revision v1.3 and higher
TMCM-AC-840 motor control boards with board revision v1.3 and higher provide two additional power
connectors for a portable desktop power supply.
A fitting power supply is delivered together with the kit.
Dehner Elektronik SYS 1357-2424 Supply, 24 V/DC/1000 mA
manufactured by Sunny Computer Technology Europe
Input 100-240V, 1.0A max., 50Hz
Output +24VDC, 1A, 24W max.

TMCM-AC-840 Motor Control Daughter Board Kit Manual 15
Copyright © 2010 TRINAMIC Motion Control GmbH & Co. KG
8 Pinout Lists
All Pins of the Mixed Signal Header are connected to the TMCM-AC-840 daughter board and are
either used for motor control, analog and/or digital signal measurement, or are free to be used for
other purpose.
H3 connector type to Actel board: Samtec CLP-150-02-L-DH
K1 pin header type: standard 2.54mm pitch pins
The picture below shows the header K1 and the connector H3.
8.1 Mixed Signal Header Connector
Connector H3 connects to the Mixed Signal Expansion Header of the SmartFusion™ Development Kit
or Evaluation Kit and provides access to analog and digital I/Os of the SmartFusion device. All signals
are connected to and accessible at the TMCM-AC-840 pin header K1 for test and measurement. It’s
pin numbering and signal assignment are identical to connector H3 and thus identical to the Actel
Mixed Signal Header.
The table below lists all pins of the Mixed Signal Header and their connection/purpose on the TMCM-
AC-840 daughter board.
I/O Pins/Signals with grey background are only available when connecting the TMCM-AC-840 to a
SmartFusion™ Development Kit with an S2F500 SmartFusion™ device.
Mixed Signal Header (J21) of the Actel SmartFusion™
Development Kits and Evaluation Kits
TMCM-AC-840 H3/K1 signal
J21 Pin
Net Name
FPGA PIN
Description
1
5V
Power
Power
+5V
2
5V
Power
Power
+5V
3
5V
Power
Power
+5V
4
5V
Power
Power
+5V
5
DGND
DGND
Digital ground
GND
6
DGND
DGND
Digital ground
GND
7
MSS_GP_IO_0
V1
MSS I/Os
ENC_A (Encoder Output to SmartFusion)
8
MSS_GP_IO_1
R3
MSS I/Os
DIR (TMC262 Input)
9
MSS_GP_IO_2
W1
MSS I/Os
ENC_B (Encoder Output to SmartFusion)
10
MSS_GP_IO_3
Y1
MSS I/Os
STEP (TMC262 Input)
11
MSS_GP_IO_4
AA1
MSS I/Os
ENC_N (Encoder Output to SmartFusion)

TMCM-AC-840 Motor Control Daughter Board Kit Manual 16
Copyright © 2010 TRINAMIC Motion Control GmbH & Co. KG
12
DGND
DGND
Digital ground
GND
13
MSS_GP_IO_5
U2
MSS I/Os
CSN (TMC262 SPI Input)
14
MSS_GP_IO_6
V2
MSS I/Os
SG_TST (TMC262 Output to SmartFusion)
15
DGND
DGND
Digital ground
GND
16
MSS_GP_IO_7
W2
MSS I/Os
CLK (TMC262 Input)
17
MSS_GP_IO_8
T3
MSS I/Os
ENN (TMC262 Input)
18
MSS_GP_IO_9
V3
MSS I/Os
SCK (TMC262 SPI Input)
19
MSS_GP_IO_10
U3
MSS I/Os
SDI (TMC262 SPI Input)
20
DGND
DGND
Digital ground
GND
21
MSS_GP_IO_11
T4
MSS I/Os
SCCLK (TMC603A Input)
22
MSS_GP_IO_12
AA2
MSS I/Os
SAMPLEx (TMC603A Input)
23
DGND
DGND
Digital ground
GND
24
MSS_GP_IO_13
AB2
MSS I/Os
SENSE_HI (TMC603A Input)
25
MSS_GP_IO_14
AB3
MSS I/Os
ENABLE (TMC603A Input)
26
MSS_GP_IO_15
Y3
MSS I/Os
CLR_ERR (TMC603A Input)
27
F2-200-IO_0
E3
FPGA I/Os
BL1 (TMC603A Input)
28
DGND
DGND
Digital ground
GND
29
F2-200-IO_1
F3
FPGA I/Os
BH1 (TMC603A Input)
30
F2-200-IO_2
G4
FPGA I/Os
BH2 (TMC603A Input)
31
DGND
DGND
Digital ground
GND
32
F2-200-IO_3
H5
FPGA I/Os
BL2 (TMC603A Input)
33
F2-200-IO_4
H6
FPGA I/Os
H1 (BLDC Motor Output to SmartFusion)
34
F2-200-IO_5
J6
FPGA I/Os
BH3 (TMC603A Input)
35
F2-200-IO_6
B22
FPGA I/Os
H2 (BLDC Motor Output SmartFusion)
36
DGND
Digital ground
GND
37
F2-200-IO_7
C22
FPGA I/Os
H3 (BLDC Motor Output SmartFusion)
38
F2-200-IO_8
F1
FPGA I/Os
BL3 (TMC603A Input)
39
PWM0
E22
unused
40
PWM1
F22
unused
41
DGND
DGND
Digital ground
GND
42
DGND
DGND
Digital ground
GND
43
AGND
AGND
Analog ground
GND
44
AGND
AGND
Analog ground
GND
45
DACOUT0
V7
SDD0
unused
46
DACOUT1
Y17
SDD1
unused
47
AGND
AGND
Analog ground
GND
48
AGND
AGND
Analog ground
GND
49
AC2
AB13
CM2
unused
50
AT2
AB12
TM2
unused
51
AGND
AGND
Analog ground
GND
52
ATGND1
GNDTM1
GND

TMCM-AC-840 Motor Control Daughter Board Kit Manual 17
Copyright © 2010 TRINAMIC Motion Control GmbH & Co. KG
53
AC3
AA11
CM3
unused
54
AT3
Y12
TM3
unused
55
AGND
AGND
Analog ground
GND
56
AGND
Analog ground
GND
57
AC4
W13
CM4
unused
58
AT4
T13
TM4
unused
59
AGND
AGND
Analog ground
GND
60
ATGND2
GNDTM2
unused
61
AV1_1
W9
ABPS2
CUR1 (TMC603A Output to SmartFusion)
62
AV2_1
AB7
ABPS3
CUR2 (TMC603A Output to SmartFusion)
63
AGND
AGND
Analog ground
GND
64
AGND
AGND
Analog ground
GND
65
AV1_3
W12
ABPS6
CUR3 (TMC603A Output SmartFusion)
66
AV2_3
Y11
ABPS7
VM603_FPGA (SmartFusion analog input, 21:1
voltage divider used to fit into 2.56V range)
67
AGND
AGND
Analog ground
GND
68
AGND
AGND
Analog ground
GND
69
AV2_4
W14
ABPS9
unused
70
AV1_4
Y13
ABPS8
unused
71
AGND
AGND
Analog ground
GND
72
AGND
AGND
Analog ground
GND
73
ADC2
V9
ADC2
HallFX1 (TMC603A Output to SmartFusion), used as
LVTTL
74
ADC3
AB8
ADC3
SDO (TMC262 SPI Output to SmartFusion), used as
LVTTL
75
AGND
AGND
Analog ground
GND
76
AGND
AGND
Analog ground
GND
77
ADC4
U12
ADC4
HallFX2 (TMC603A Output to SmartFusion), used as
LVTTL
78
ADC5
V12
ADC5
VM262_FPGA (SmartFusion analog input, 21:1
voltage divider used to fit into 2.56V range)
79
AGND
AGND
Analog ground
GND
80
AGND
AGND
Analog ground
GND
81
ADC6
V11
ADC6
HallFX3 (TMC603A Output to SmartFusion), used as
LVTTL
82
ADC7
T12
ADC7
unused
83
AGND
AGND
Analog ground
GND
84
AGND
AGND
Analog ground
GND
85
ADC8
V14
ADC8
unused
86
ADC9
AA14
ADC9
unused
87
AGND
AGND
Analog ground
GND
88
AGND
AGND
Analog ground
GND
89
ADC10
AA13
ADC10
unused
90
ADC11
U14
ADC11
unused
91
AC1
U9
CM1
unused

TMCM-AC-840 Motor Control Daughter Board Kit Manual 18
Copyright © 2010 TRINAMIC Motion Control GmbH & Co. KG
92
AGND
AGND
Analog ground
GND
93
AGND
AGND
Analog ground
GND
94
AGND
AGND
Analog ground
GND
95
DGND
DGND
Digital ground
GND
96
DGND
DGND
Digital ground
GND
97
3.3V
Power
Power
+3.3V
98
3.3V
Power
Power
+3.3V
99
3.3V
Power
Power
+3.3V
100
3.3V
Power
Power
+3.3V
8.1 : Mixed Signal Header Pin Connections
8.2 TMC262 Signals
The following table contains all signals/pins of the stepper motor driver TMC262 that are accessible
via the pin header K1.
Package Pin TMC262
J21 Pin
SmartFusion IO type
Comments
SDO
74
Analog IO ADC5 used as LVTTL
SPI from TMC262
SDI
19
MSS IO
SPI to TMC262
CSN
13
MSS IO
SPI to TMC262
SCK
18
MSS IO
SPI to TMC262
SG_TST
14
MSS IO
Stallguard™ signal
STEP
10
MSS IO
Step input
DIR
8
MSS IO
Direction input
CLK
16
MSS IO
TMC262 external clock input
ENN
17
MSS IO
Enable not MOSFET bridges of TMC262
8.2 : TMC262 related pins of the mixed signal header connector
8.3 TMC603A Signals
The following table contains all signals/pins of the BLDC motor driver TMC603A that are accessible
via the pin header K1.
Package Pin TMC603A
J21 Pin
SmartFusion IO type
Comments
CUR1
61
Analog IO ABPS2
CURx signals have a range of 0 to 3.3V. They need
to be connected to the Active Bipolar Prescaler IOs
(ABPS2,3,6) of the SmartFusion. These IOs must be
correctly configured inside the ACTEL tool chain
(MSS Configurator) to handle voltages over 2.56V.
CUR2
62
Analog IO ABPS3
CUR3
65
Analog IO ABPS6
BL1
27
FPGA IO
Low side gate control
BL2
32
FPGA IO
BL3
38
FPGA IO
BH1
29
FPGA IO
High side gate control
BH2
30
FPGA IO
BH3
34
FPGA IO
HallFX1
73
Analog IO ADC2 used as LVTTL
HallFX signals generated inside the TMC603A when
HallFX is enabled. These signals are generated
using the back EMF of the motor.
HallFX2
77
Analog IO ADC4 used as LVTTL
HallFX3
81
Analog IO ADC6 used as LVTTL
SENS_HIGH
24
MSS IO
Switches current amplifiers to high sensitivity.
SSCLK
21
MSS IO
Switched capacitor filter clock input for hallFX™.
SAMPLEx
22
MSS IO
Sample & Hold input for the CURx signals
CLR_ERR
26
MSS IO
Clears the error-latch after /error_out has
signalized an error.
ENABLE
25
MSS IO
Connected to /ERR_OUT of TMC603A. Needs to be
declared as Tristate IO inside the MSS Configurator
to also enable/disable the MOSFET bridges by hand
from the SmartFusion.
8.3 : TMC603A related pins of the mixed signal connector

TMCM-AC-840 Motor Control Daughter Board Kit Manual 19
Copyright © 2010 TRINAMIC Motion Control GmbH & Co. KG
8.4 Additional Pins and Pin Headers
The TMCM-AC-840 provides various additional pins and pin headers for measurement and testing.
These are listed below:
Diverse Ground pins (labeled GND)
All signals of the stepper motor connector (H14), BLDC motor connector (H1), hall sensors
connector (H4) and encoder connector (H5) are available via pin headers for measurement
and testing. These pin headers are located directly next to the respective main connector.
oK2 = stepper motor driver signals GND, B2, B1, A2, A1
oK3 = stepper motor encoder signals +5V, GND, A, B, N
oK4 = BLDC motor hall sensors +5V, GND, H1, H2, H3
oH12 = BLDC motor driver signals U, V, W, GND
Pin TST_ANA of the TMC262
Header H5 for the ABN-Encoder can be used for other signals as well, if no encoder is used in
your application.
Sense resistor measurement pins
oTMC262 block: SRA, SRB
oTMC603A block: RSENSE U, RSENSE V, RSENSE W
Measurement pins for the supply voltages +VM262 and +VM603 behind the voltage divider
(scaled to approximately 2.56V) labeled “VM262/” and “VM603/”
oThe voltage divider to scale the VMs down to a healthy FPGA-IO level uses a ratio of
21:1 with two resistors 20K Ohms and 1K Ohms.
8.5 Additional SPI Header & Jumper (only revision v1.3 and higher)
The TMCM-AC-840 board has an additional header (“J9 – SPI Select”) for choosing an alternative SPI
source for configuration and control of the TMC262 stepper drive IC.
One can choose between an SPI source coming directly from the board-to-board connector pins (see
tables 7.1 and 7.2) or an external SPI source using a 4-wire cable connection (SDO, SDI, SCK, SS).
For example, one can connect the external SPI pins of the SmartFusion Development Kit directly to
this pin header or another SPI master from an own custom board using wires.
If the signals ABCD are connected with pin rows 1-2 using the jumpers delivered with the kit,
the SPI signals coming from the mixed signal header are used (this is the default jumper
setup).
If an external SPI source is used, e.g., the external SPI header from the SmartFusion
Development Kit, these signals must be directly connected to pin row 2 of J9 using wires.
Pin row 3 of J9 is not used.
Pin/Signal of J9
SPI-Interface Signal
A
SPI Chip Select / Slave Select, goes to CSN pin of TMC262
B
SPI Clock, goes to SCK pin of TMC262
C
SPI Serial Data In, goes to SDI pin of TMC262
D
SPI Serial Data Out, goes to SDO pin of TMC262

TMCM-AC-840 Motor Control Daughter Board Kit Manual 20
Copyright © 2010 TRINAMIC Motion Control GmbH & Co. KG
8.6 Board LEDs
The TMCM-AC-840 has several LEDs indicating different operating conditions of the daughter board.
LED SG: This LED is placed next to the stallGuard™ logo. It is on when the TMC262
stallGuard functionality detects and signals a motor stall.
LED ENN: This is the enable-LED of the MOSFET stages of the TMC262 driver IC. It is on
when the MOSFET bridges are enabled and running. It is off when the MOSFET bridges are
disabled. The ENN-signal is routed to the SmartFusion device and can be controlled via
software (Cortex M3) or from the FPGA fabric. Furthermore the TMC262 MOSFET bridges
can be switched off via SPI as well.
LED VLS: This LED is connected to the TMC603A’s voltage regulator stage and indicates a
“good” low side driver supply voltage of TMC603A driver IC for driving the low side gates. The
LED shines the brighter with increasing VLS/+VM603.
LED ENABLE /ERR_OUT: This LED is similar to LED ENN. It is connected to the ENABLE
and /ERR_OUT signals of the TMC603A driver IC. ENABLE can be controlled via the
SmartFusion device and switches on/off the MOSFET bridges of the TMC603A block. As a
self-protection mechanism, the /ERR_OUT signal of the TMC603A is directly connected to the
ENABLE pin of the TMC603A to switch off the MOSFETs upon errors. The ENABLE signal
that is routed to the SmartFusion device must be configured as a tristate pin/signal inside the
SmartFusion to override the /ERR_OUT signal and manually set/reset ENABLE. Alternatively,
the CLR_ERR signal can be used to reset the error condition that keeps the TMC603A’s
MOSFET bridges switched off. Thus, LED ENABLE /ERR_OUT is on when the MOSFET
bridges are enabled, otherwise it is off.
The following picture shows the LEDs of the daughter board during operation. The blue LEDs (LED
ENN & LED ENABLE /ERR_OUT) indicate that the MOSFETs driver stages of both driver ICs are
enabled and the motor coils are powered. The green LED (LED VLS) indicates that the power
converter circuit for the TMC603A BLDC driver is operating correctly. The higher VM603, the brighter
this LED shines, especially at low voltage, which indicates a correct/good power supply.
Table of contents
Other Trinamic Computer Hardware manuals
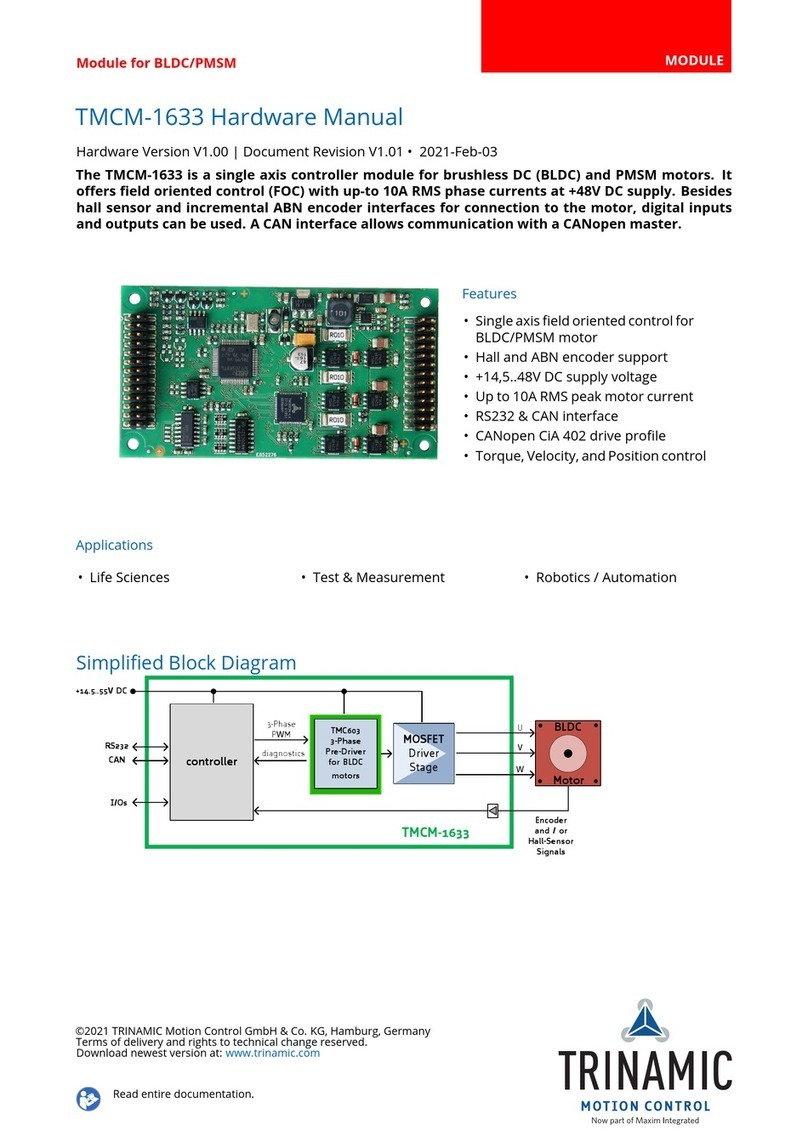
Trinamic
Trinamic TMCM-1633 User manual
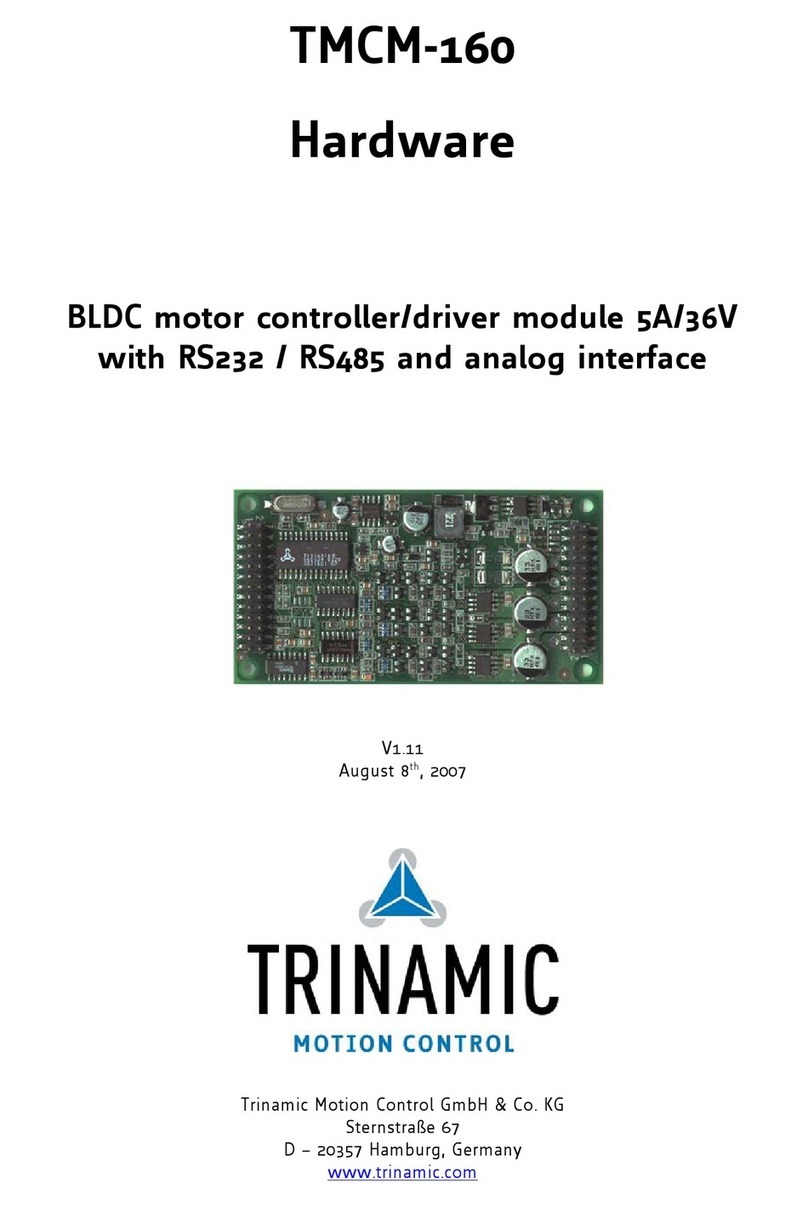
Trinamic
Trinamic TMCM-160 User manual
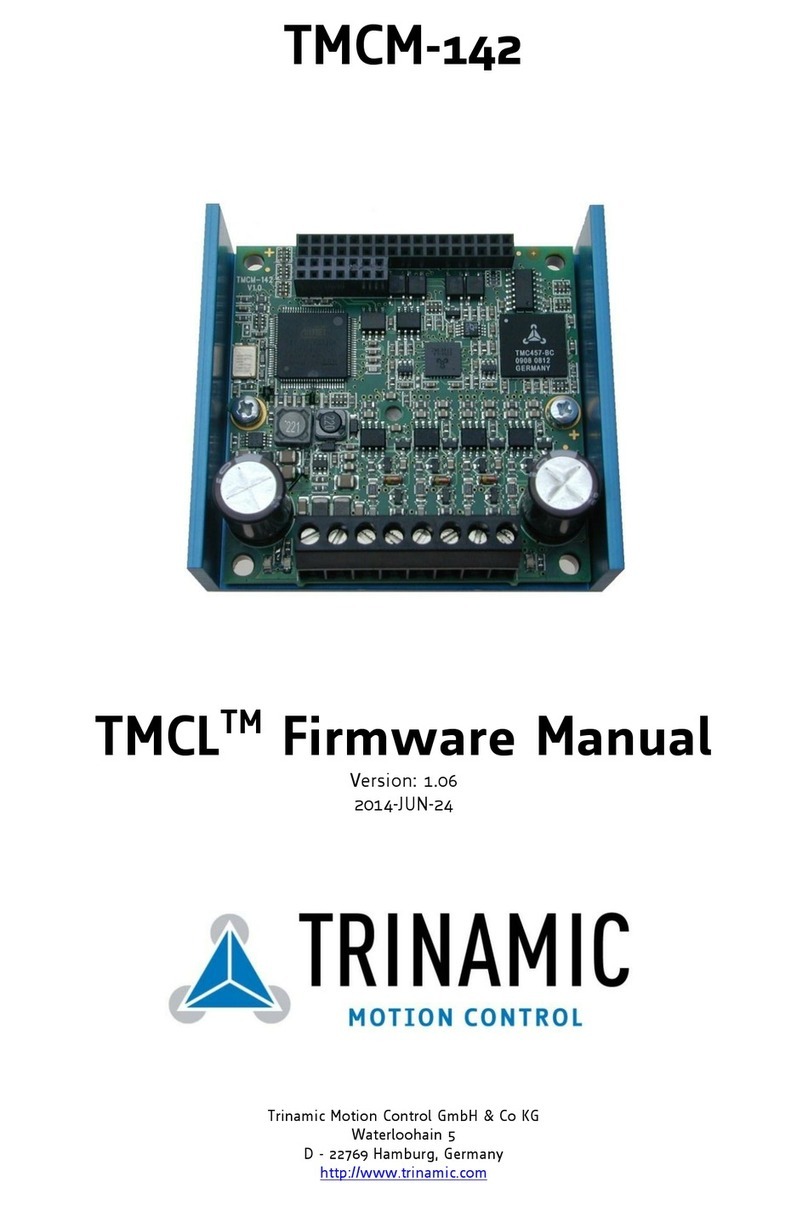
Trinamic
Trinamic TMCL TMCM-142 Use and care manual
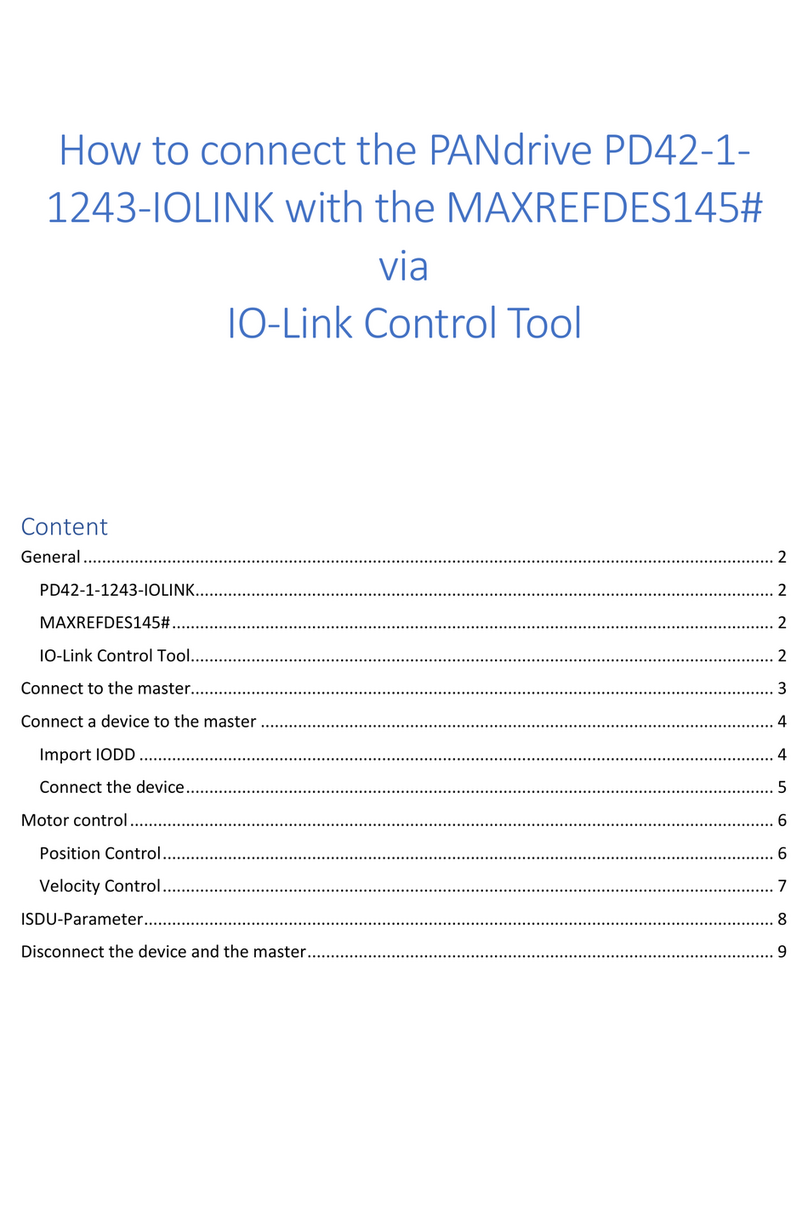
Trinamic
Trinamic PANdrive PD42-1- 1243-IOLINK Safety guide
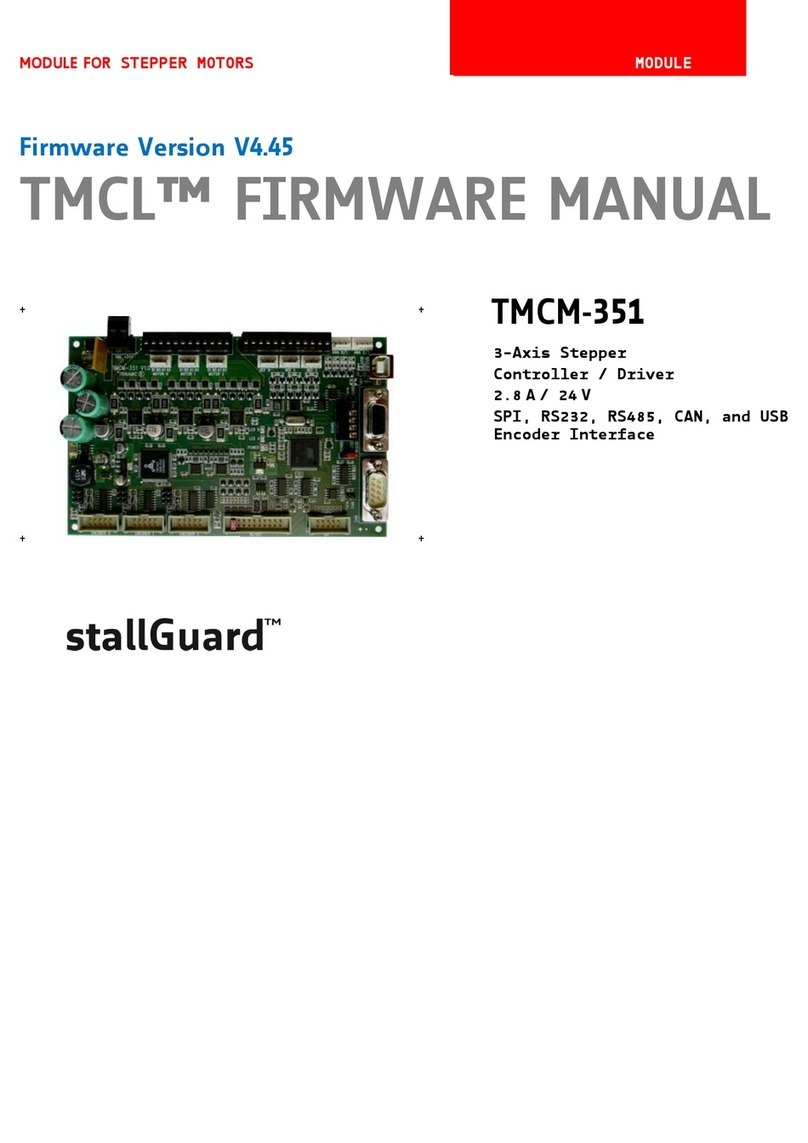
Trinamic
Trinamic TMCM-351 Use and care manual
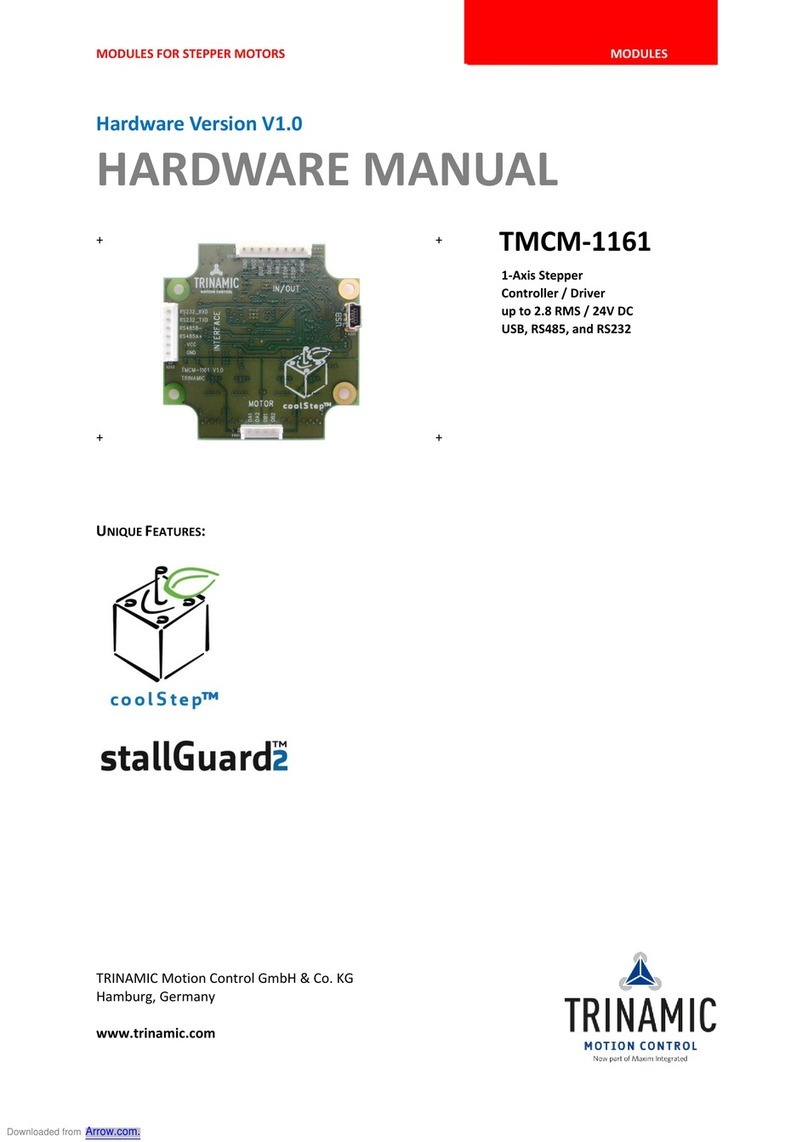
Trinamic
Trinamic TMCM-1161 User manual
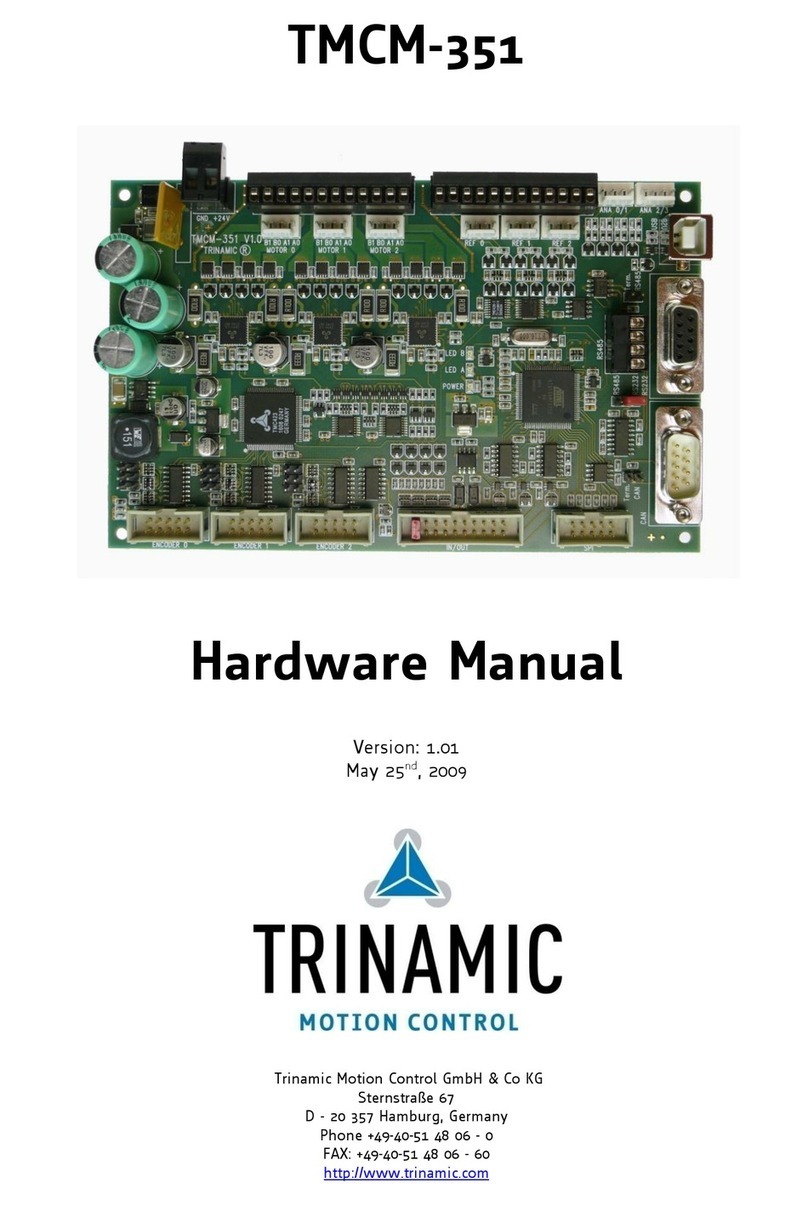
Trinamic
Trinamic TMCM-351 User manual
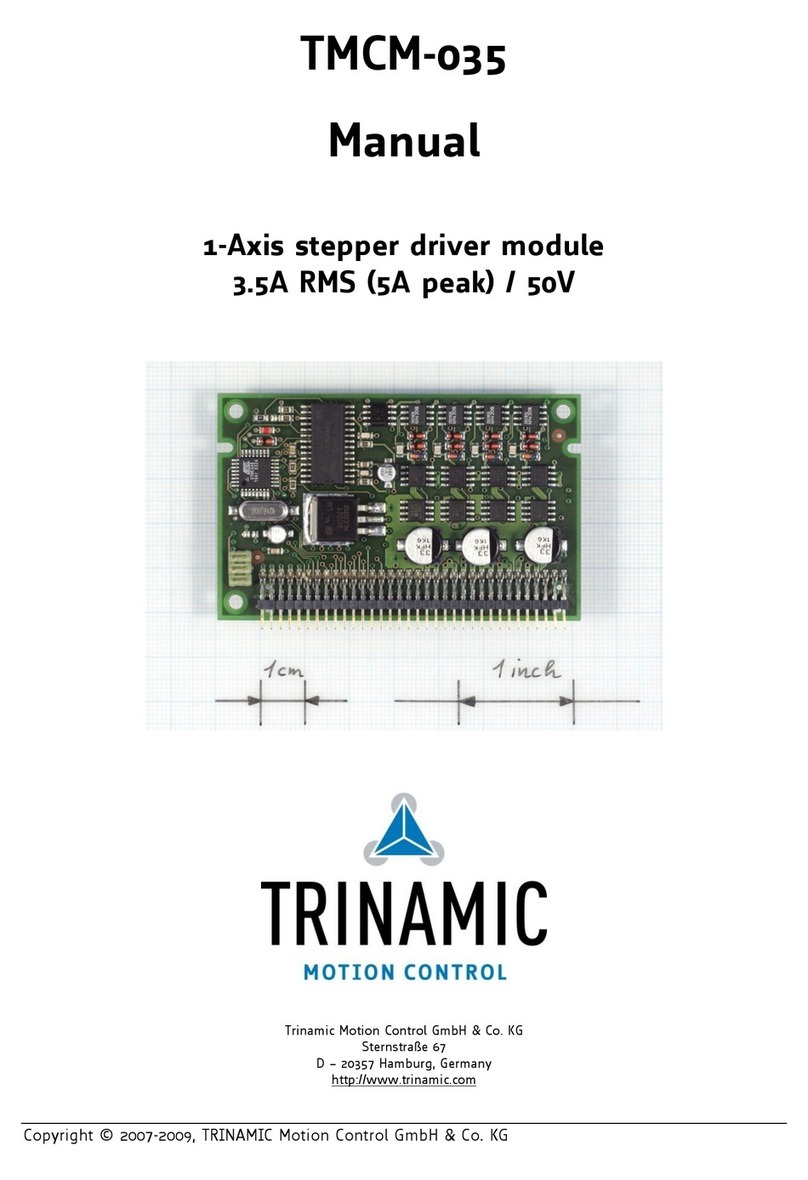
Trinamic
Trinamic TMCM-035 User manual
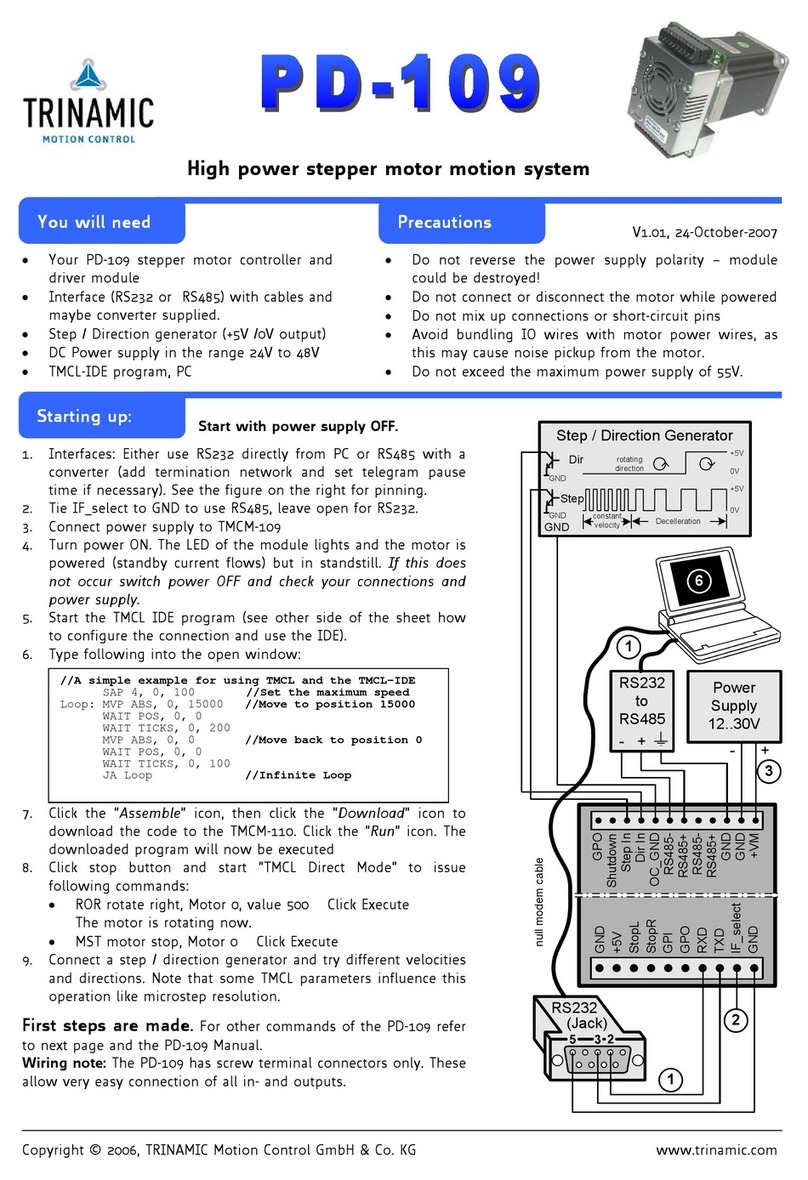
Trinamic
Trinamic PD-109 User manual
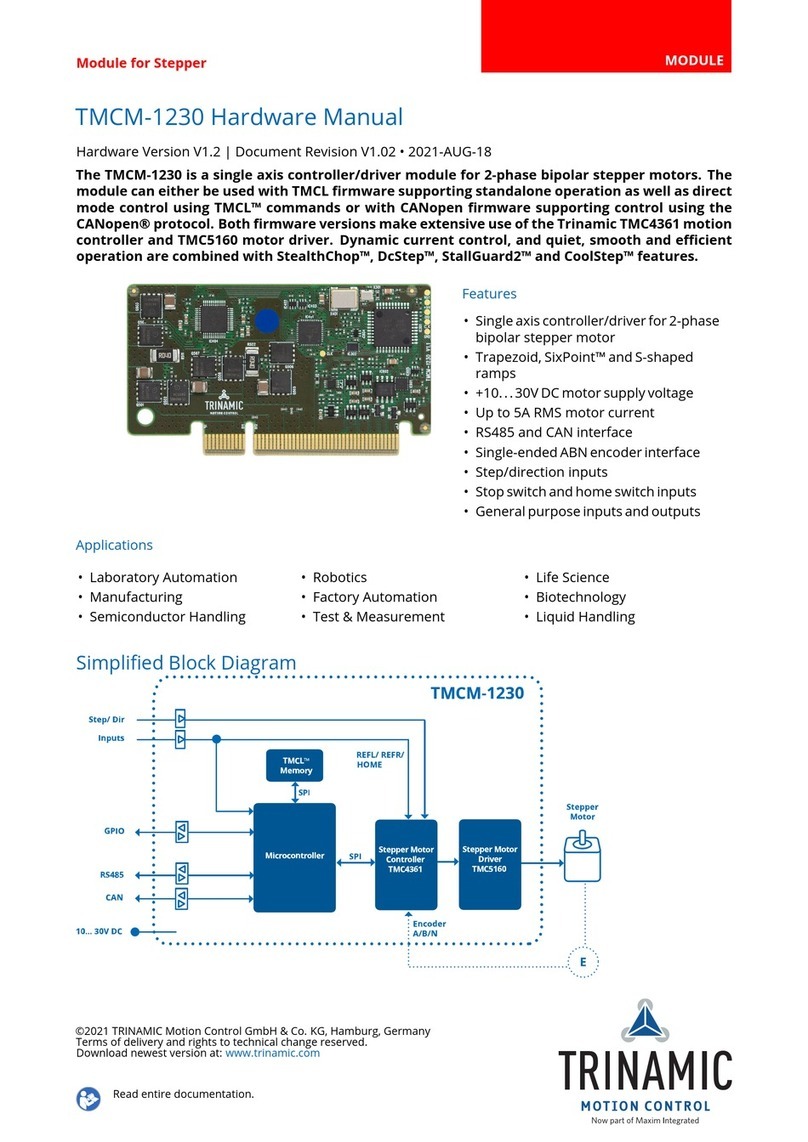
Trinamic
Trinamic TMCM-1230 User manual