WAGNER SprayPackE User manual

SprayPackE
Version 01/2020


3
VERSION 01/2020 ORDER NUMBER DOC2397091 SprayPackE
Table of Contents
1 ABOUT THESE INSTRUCTIONS 6
1.1 Preface 6
1.2 Warnings, Notices and Symbols in these Instructions 6
1.3 Languages 7
1.4 Abbreviations 7
1.5 Terminology for the Purpose of this Manual 8
2 CORRECT USE 9
2.1 Device Type 9
2.2 Type of Use 9
2.3 For Use in Potentially Explosive Areas 9
2.4 Processible Working Materials 9
2.5 Misuse 9
3 IDENTIFICATION 10
3.1 Identication 10
3.2 Type Plates 10
3.3 Permissible Device Combinations 11
3.4 Safety Features 11
4 BASIC SAFETY INSTRUCTIONS 13
4.1 Safety Instructions for the Operator 13
4.1.1 Electrical Devices and Equipment 13
4.1.2 A Safe Work Environment 14
4.1.3 Personnel Qualications 14
4.2 Safety Instructions for the Personnel 15
4.2.1 Personal Safety Equipment 15
4.2.2 Safe Handling of WAGNER Powder Spray Devices 15
4.2.3 Grounding the Device 16
4.2.4 Product Hoses 16
4.2.5 Electrical Connection Cables 17
4.2.6 Cleaning and Flushing 17
4.2.7 Maintenance and Repair 18
4.2.8 Protective and Monitoring Equipment 18
5 DESCRIPTION 19
5.1 Mode of Operation 19
5.2 Display and Operating Elements 19
5.2.1 Front Side of Structure 19
5.2.2 Connections on Rear Side of MCE 20
5.3 Front Side of Structure, CPE/CPE-S 22
5.4 CPE Connections on Rear Side 23
5.5 CPE-S Connections on Rear Side 24
5.6 CPE/CPE-S Connections in Housing 25
5.6.1 Terminal Assignment 26
5.7 CAN Addresses 27
5.8 CPE/CPE-S Circuit Breakers in Housing 28
5.9 Components of SprayPackE 29
5.10 Components of MCE 32
5.11 Components of pulse generator 35

4
VERSION 01/2020 ORDER NUMBER DOC2397091 SprayPackE
5.12 Components of Switching Light Curtain 36
5.13 Safety Functions 37
5.14 Scope of Delivery 38
5.15 Technical Data 38
5.15.1 Technical Data for MCE 38
5.15.2 Technical Data for CPE/CPE-S 38
5.15.3 Technical Data for Maximum SprayPackE Conguration 39
5.15.4 Rack (10 EPG S2) 40
5.15.5 EPG S2 40
5.15.6 EPG-Sprint X 41
5.15.7 Compressed Air Quality 42
6 ASSEMBLY AND COMMISSIONING 43
6.1 Training of Assembly/Commissioning Personnel 43
6.2 Storage Conditions 43
6.3 Installation Conditions 43
6.4 Connecting the Automatic Spray Guns on the EPG S2 44
6.5 Connection Diagram in the Rack 45
6.6 Connection Diagram for Entire SpraypackE System 46
6.7 Pneumatic Connections in Rack 47
6.8 Connection Diagram for CSL710 Light Curtain and Pulse Generator 48
6.8.1 Grounding of CSL710 Light Curtains 49
6.9 Description of CSL710 Light Curtains 49
6.9.1 Function Keys on the Light Curtain Display 49
6.9.2 LEDs on Receiver 50
6.9.3 LEDs on Transmitter 50
6.9.4 Meaning of Display Symbols 51
6.10 Settings on the Light Curtain 51
6.10.1 "Settings" menu 51
6.10.2 "Display" menu 53
6.10.3 "Digital IO" menu 54
6.11 Test and Diagnosis eXpertE Software 58
6.12 Grounding 59
6.12.1 Grounding of Control Units in Rack 60
6.13 Safety Checks 60
6.14 Interlocking 61
7 OPERATION 63
7.1 Training the Operating Personnel 63
7.2 Tasks 63
7.3 Controllable Spray Guns 63
7.4 Gun Cable Lengths 63
8 CLEANING AND MAINTENANCE 64
8.1 Cleaning 64
8.1.1 Cleaning Personnel 64
8.1.2 Cleaning Instructions 64
8.1.3 Cleaning Procedures 64
8.2 Maintenance 64
8.2.1 Maintenance Personnel 64
8.2.2 Maintenance Instructions 65
8.2.3 Maintenance Procedures 65
8.2.4 Safety Checks 65

5
VERSION 01/2020 ORDER NUMBER DOC2397091 SprayPackE
9 REPAIRS 66
9.1 Repair Personnel 66
9.2 Repair Notes 66
10 FUNCTION TEST AFTER REPAIR WORK 67
11 DISASSEMBLY AND DISPOSAL 67
12 ACCESSORIES 68
13 SPARE PARTS 69
13.1 How Can Spare Parts Be Ordered? 69
13.2 Spare Parts List for MCE Control Unit 69
13.3 Spare Parts List for Maintenance Unit 70
13.4 Spare Parts List for Air Diuser 70
13.5 Spare Parts List for Digital Pressure Sensor 71
14 DECLARATION OF CONFORMITY 72
14.1 EU Declaration of Conformity 72

6
VERSION 01/2020 ORDER NUMBER DOC2397091 SprayPackE
1 ABOUT THESE INSTRUCTIONS
1.1 PREFACE
The operating manual contains information about safely operating, maintaining, cleaning and
repairing the device.
The operating manual is part of the device and must be available to the operating and
service personnel.
Operating and service personnel should be instructed according to the safety instructions.
The device may only be operated in compliance with this operating manual.
This equipment can be dangerous if it is not operated according to the instructions in this
operating manual.
1.2 WARNINGS, NOTICES AND SYMBOLS IN THESE INSTRUCTIONS
Warning instructions in this manual highlight particular dangers to users and to the device
and state measures for avoiding the hazard. These warning instructions fall into the following
categories:
DANGER Immediate risk of danger.
Non-observance will result in death or serious injury.
WARNING Potential danger.
Non-observance may result in death or serious injury.
CAUTION Potentially dangerous situation.
Non-observance may result in minor injury.
NOTICE Potentially dangerous situation.
Non-observance may result in damage to property.
Note: Provides information about particular characteristics and
how to proceed.
Explanation of warning notice:
LEVEL OF DANGER
This notice warns you of a danger!
Possible consequences of not observing the warning notice.
The measures for preventing the hazard and its consequences.

7
VERSION 01/2020 ORDER NUMBER DOC2397091 SprayPackE
1.3 LANGUAGES
The operating manual is available in the following languages:
Original operating manual
Language Order no.
German 2397090
Translation of the original operating manual
Language Order no. Language Order no.
English 2397091 Russian 2397095
French 2397092 Chinese 2397096
Italian 2397093 Polish 2414158
Spanish 2397094 Czech 2414159
Hungarian 2414161 -- --
The software documentation is available in the following languages:
Original software documentation
Language Order no.
German 2397152
Translation of the original software documentation
Language Order no. Language Order no.
English 2397153 Russian 2397158
French 2397154 Chinese 2397159
Italian 2397156 -- --
Spanish 2397157 -- --
Additional languages on request or at: www.wagner-group.com
1.4 ABBREVIATIONS
Order no. Order number Number of pieces
Spare part OK okay
Marking in the spare parts lists IO Input/output
Position

8
VERSION 01/2020 ORDER NUMBER DOC2397091 SprayPackE
1.5 TERMINOLOGY FOR THE PURPOSE OF THIS MANUAL
Cleaning
Cleaning Manual cleaning of devices and device parts with cleaning agent
Flushing Internal ushing of paint-wetted parts with compressed air
Personnel qualications
Trained person Is instructed in the tasks assigned to him/her, the potential risks
associated with improper behavior as well as the necessary
protective devices and measures.
Electrically trained
person
Is instructed by an electrician about the tasks assigned to him/her,
the potential risks associated with improper behavior as well as
the necessary protective devices and measures.
Electrician Can assess the work assigned to him/her and detect possible
hazards based on his/her technical training, knowledge and
experience in relevant provisions.
Skilled person in
accordance with TRBS
1203
(2010/Modication 2012)
A person who, based on his/her technical training, experience and
recent vocational experience, has sucient technical knowledge in
the areas of explosion protection, protection from pressure hazards
and electric hazards (if applicable) and is familiar with the relevant
and generally accepted rules of technology so that he/she can
inspect and assess the status of devices and coating systems based
on workplace safety.

9
VERSION 01/2020 ORDER NUMBER DOC2397091 SprayPackE
2 CORRECT USE
2.1 DEVICE TYPE
Controller for automatic powder coating systems.
2.2 TYPE OF USE
The SprayPackE controller serves to control the EPG S2 control units for powder guns and
powder conveying equipment, reciprocators and sliding tables.
The device may only be operated under the following conditions:
Use the device only to work with the products recommended by WAGNER.
Only operate the device as a whole.
Do not deactivate safety xtures.
Use only WAGNER original spare parts and accessories.
The operating personnel must be trained on the basis of this operating manual.
Follow the instructions in the operating manual.
2.3 FOR USE IN POTENTIALLY EXPLOSIVE AREAS
The SprayPackE controller must not be used in the dust Ex zone (zone22).
2.4 PROCESSIBLE WORKING MATERIALS
– Types of powder which can be charged electrostatically
– Metallic powder
– Tribo powder
Note:
Contact your localWAGNER dealer and the lacquer manufacturer if you encounter application
problems.
2.5 MISUSE
Misuse can lead to physical injury and/or property damage!
Special attention must be paid that:
liquid coating products, e.g., solvents or water-based lacquers are not processed;
no food, medicine or cosmetics are processed.

10
VERSION 01/2020 ORDER NUMBER DOC2397091 SprayPackE
3 IDENTIFICATION
3.1 IDENTIFICATION
Device type: MCE/CPE control unit
Manufacturer: Wagner International AG
9450 Altstätten
Switzerland
CE European Communities
3.2 TYPE PLATES
Type / Typ:
Serie Nr.:
Serial No.:
Eingangsspannung:
Input Voltage:
Leistungsverbrauch:
Power use:
Vorsicherung:
Pre-fuse:
MCE
100-240VAC
MCE: 60W
10Amp D Type
Baujahr:
Year of manufactur:
x EPG-S2 @ 60W
Wagner International AG
CH 9450 Altstätten
Designed by WAGNER in Switzerland
50/60Hz
P_03706
1
2
4
5
6
7
3
P_03746
1
2
4
5
6
7
3
Typ / Type:
Serie Nr.:
Serial No.:
Eingangsspannung:
Input Voltage:
Eingangsleistung:
Line Power:
Vorsicherung:
Main fuse:
CPE
3P+N+PE
230/400V 50/60Hz
max. 3.0kW
max. 25 A gL/gG
Baujahr:
Year of manufactur:
Wagner International AG
CH 9450 Altstätten
Designed by WAGNER in Switzerland
1 Manufacturer 1 Manufacturer
2 Type: MCE 2 Type: CPE
3 Serial number 3 Serial number
4 Year of manufacture 4 Year of manufacture
5 Input voltage 5 Input voltage
6 Back-up fuse 6 Input power
7 Power consumption 7 Back-up fuse

11
VERSION 01/2020 ORDER NUMBER DOC2397091 SprayPackE
3.3 PERMISSIBLE DEVICE COMBINATIONS
The following control units may be connected to the MCE:
– EPG S2
– EPG S2 FM (USA Version)
– EPG Sprint X
– CPE
– CPE-S
3.4 SAFETY FEATURES
Plates bearing information for the user have been attached to the work openings of the
powder coating booth.
The plate size corresponds to the standard category Ø 100 mm; 3.94 inches.
The label plates, which must be attached, are shown below:
High voltage!
In the control cabinet:
(25 mm; 0.98 inch) voltage
upstream of main switch
Danger of crushing!
Explosive atmosphere! Risk of tripping!
Forbidden for anyone with
active implants
(e.g., a pacemaker)!
Forbidden for
unauthorized persons!
Smoking, re, and open
ames are prohibited!
Follow the instructions in
the operating manual!

12
VERSION 01/2020 ORDER NUMBER DOC2397091 SprayPackE
Wear electrostatically
conductive footwear! Wear hearing protection!
Wear respirator! Wear protective goggles!

13
VERSION 01/2020 ORDER NUMBER DOC2397091 SprayPackE
4 BASIC SAFETY INSTRUCTIONS
4.1 SAFETY INSTRUCTIONS FOR THE OPERATOR
Keep this operating manual at hand near the device at all times.
Always follow local regulations concerning occupational safety and accident prevention
regulations.
4.1.1 ELECTRICAL DEVICES AND EQUIPMENT
Danger of electric shock!
Danger to life from electric shock.
Prepare device in accordance with the local safety requirements with regard to the
operating mode and ambient inuences.
May only be maintained by skilled electricians or under their supervision. With open
housings, the mains voltage poses a danger.
Operatedevicein accordancewith thesafetyregulationsandelectrotechnicalregulations.
Must be repaired immediately in the event of problems.
Decommission if device poses a danger or is damaged.
Must be de-energized before work is commenced. Secure the device against being
switched back on without authorization. Inform personnel about planned work.
Observe electrical safety regulations.
Ground all devices to a common grounding point.
Only operate the device with a properly installed socket with a protective ground
wire connection.
Keep liquids away from electrical devices.

14
VERSION 01/2020 ORDER NUMBER DOC2397091 SprayPackE
4.1.2 A SAFE WORK ENVIRONMENT
Danger due to dust formation!
Severe or fatal injuries due to explosion danger or inhalation, swallowing or contact with
the skin or eyes.
The oor in the working area must be electrostatically conductive
(measurements according to EN 1081 and EN 61340-4-1).
Paint mist extraction systems/ventilation systems must be tted on site according
to local regulations.
Make sure that the ground connection and potential equalization of all system parts
are reliable and continuous and can withstand the expected stress (e.g., mechanical
stress, corrosion).
Ensure that personal protective equipment (see Chapter 4.2.1) is available and is used.
Ensure that all persons within the working area wear static dissipative shoes.
Footwear must comply with EN 20344. The measured insulation resistance must not
exceed 100 megohms.
Protective clothing, including gloves, must comply with EN 1149-5. The measured
insulation resistance must not exceed 100 megohms.
Ensure that there are no ignition sources such as naked ames, sparks, glowing wires,
or hot surfaces in the vicinity. No smoking.
Maintain sucient quantities of suitable re extinguishers and ensure that they are
serviceable.
The powder release must be electronically interlocked with the powder spray system
exhaust equipment.
In the event of defects, immediately bring the device or system to a stop and arrange
to have repairs carried out immediately.
Excess coating product (overspray) must be collected up safely.
The operating company must ensure that an average concentration of powder lacquer
in the air does not exceed 50% of the lower explosion limit (LEL = max. permitted
concentration of powder to air). If no reliable LEL value is available, the average
concentration must not exceed 10 g/m³.
4.1.3 PERSONNEL QUALIFICATIONS
Danger due to incorrect use of device!
Risk of death due to untrained personnel.
Ensure that the operating personnel has been instructed by the operator in accordance
with the operating manual and the operating instructions. The device must only
be operated, maintained and repaired by trained personnel. Refer to the operating
instructions for information about the required personnel qualications.

15
VERSION 01/2020 ORDER NUMBER DOC2397091 SprayPackE
4.2 SAFETY INSTRUCTIONS FOR THE PERSONNEL
Always observe the information in this manual, particularly the safety instructions
and the warning instructions.
Alwaysfollow localregulations concerning occupational safety andaccident prevention
regulations.
In electrostatics applications: Persons belonging to a risk group according to
EMF guideline 2013/35/EU (e.g., carriers of active implants), must not enter the
high-voltage area.
4.2.1 PERSONAL SAFETY EQUIPMENT
Danger due to dust formation!
Serious or fatal injuries due to inhalation, swallowing or contact with the skin or eyes.
Observe the processing regulations laid down by the manufacturer of the powder
lacquer being used, when preparing or processing the powder.
Take note of the manufacturer’s notication and the relevant environmental protection
regulations when disposing of powder lacquers.
Take the specied protective measures. In particular, wear safety goggles, protective
clothing and gloves, as well as hand protection cream if necessary.
Use a mask or breathing apparatus if necessary.
For sucient health and environmental safety: Operate the device in a powder
coating booth or on a spraying wall with the ventilation (extraction) switched on.
Danger due to noise pollution!
Hearing damage due to noise pollution.
Wear ear protection.
4.2.2 SAFE HANDLING OF WAGNER POWDER SPRAY DEVICES
Danger due to dust formation!
Do not point spray guns at people.
Do not spray device parts using electrostatic equipment.
Before any work on the device, in the event of work interruptions and malfunctions:
– Switch o the energy/compressed air supply.
– Relieve pressure on powder spray gun and device.
– Secure the powder spray gun against actuation.
– Disconnect the control unit from the mains.
– Inthe eventof functional faults:remedy thefault asdescribedin the "Troubleshooting"
chapter.

16
VERSION 01/2020 ORDER NUMBER DOC2397091 SprayPackE
4.2.3 GROUNDING THE DEVICE
Danger due to electrostatic charge!
Explosion hazard and damage to the device.
The electrostatic charge may, in certain cases, give rise to electrostatic charges on the
device. Flames or sparks can form during discharge.
Correct grounding of the entire coating system prevents electrostatic charges:
Ensure that all devices and tanks are grounded before each coating process.
All of the system's conductive elements, such as oors, walls, ceilings, protective
grating, transport equipment, work pieces, powder tanks, automatic moving devices
or construction parts etc. in the spray area, with the exception of parts which carry
high voltage during operation, must be connected to the grounding system.
Parts of the booth must be grounded in accordance with EN 12981.
Ensure that all persons inside the working area are grounded, e.g., that they are wearing
static dissipative shoes.
Grounding cables must be checked regularly to ensure that they are serviceable
(see EN 60204).
4.2.4 PRODUCT HOSES
Danger due to damaged product hoses!
The product hose may cause dangerous injuries.
Use only an original WAGNER powder hose.
Make sure that the hoses are laid only in suitable places. Hoses should not be laid in the
following places under any circumstances:
– in high-traffic areas,
– on sharp edges,
– on moving parts or
– on hot surfaces.
Ensure that the hoses are never run over by vehicles (e.g., fork lifts), or that the hoses
are never put under pressure from the outside in any other way.
Ensure that the hoses are never kinked. Observe maximum bending radii.
Ensure that no work is ever performed with a damaged hose.
Make sure that the hoses are never used to pull or move the device.

17
VERSION 01/2020 ORDER NUMBER DOC2397091 SprayPackE
4.2.5 ELECTRICAL CONNECTION CABLES
Risk caused by improperly laid cables!
Risk of injury and damage to the device.
Properly lay connection cables and check them regularly.
Immediately replace damaged connection cables.
Ensure that no work is ever performed with a damaged connection cable.
Do not lay connection cables on routes used by product handling vehicles and not
through doors/gates.
Do not route connection cables near aisles or walkways in order to avoid tripping.
4.2.6 CLEANING AND FLUSHING
Danger due to cleaning and ushing!
Explosion hazard and damage to the device.
Before starting cleaning or any other manual work, the high voltage in the spray area
must be shut down and locked to prevent it from being switched back on.
Lock the compressed air supply and decompress the device.
Secure the device against being switched back on without authorization.
Use only electrically conducting and grounded tanks for cleaning uids.
Preference should be given to non-ignitable cleaning uids.
If ignitable cleaning uids are used, all parts carrying high voltage must be discharged
to a discharge energy of less than 0.24 mJ, once the high voltage has been switched
o, before they can be reached. Most ignitable solvents have an ignition energy of
around 0.24 mJ or 60 nC.
The cleaning agent's ash point must be at least 15 K above the ambient temperature.
Note the details provided by the powder lacquer manufacturer.
Only mobile industrial vacuum cleaners of design 1 (see EN 60335-2) may be used
for getting rid of dust build-up.
Take measures for workplace safety (see Chapter 4.1.2).

18
VERSION 01/2020 ORDER NUMBER DOC2397091 SprayPackE
4.2.7 MAINTENANCE AND REPAIR
Danger due to improper maintenance and repair!
Danger to life and equipment damage.
Only a WAGNER service center or a suitably trained person may carry out repairs and
replace parts.
Repair or replacement of devices or parts of devices are only allowed to be
performed outside the hazard area by qualied personnel.
Do not change or modify the device; if change is necessary, contact WAGNER.
Only repair and replace parts that are listed in Chapter 12 and Chapter 13 that are
assigned to the device.
Do not use any defective components.
Exclusively use accessories listed in Chapter 12 and that are assigned to the unit.
Before all work on the device and in the event of work interruptions:
– Switch o the energy and compressed air supply.
– Relieve pressure on powder spray gun and device.
– Secure the powder spray gun against actuation.
Observe the operating and service manual for all work.
4.2.8 PROTECTIVE AND MONITORING EQUIPMENT
Danger due to removal of protective and monitoring equipment!
Danger to life and equipment damage.
Protective and monitoring equipment must not be removed, modied or rendered
unusable.
Regularly check for perfect functioning.
If defects are detected on protective and monitoring equipment, the system must
not be operated until these defects are remedied.

19
VERSION 01/2020 ORDER NUMBER DOC2397091 SprayPackE
5 DESCRIPTION
5.1 MODE OF OPERATION
The MCE control unit is the superordinate controller for small to mid-sized power coating
systems. The modular concept permits maximum exibility in the development stages,
types and number of powder spray guns, gap control for saving powder and exact control
of movements for optimum coating results.
An easy-to-use user interface allows all parameters to be quickly modied with the option
of storing and loading them for reproducible results.
A maximum of 20 powder spray guns can be controlled.
5.2 DISPLAY AND OPERATING ELEMENTS
5.2.1 FRONT SIDE OF STRUCTURE
1
6 2345
P_03707
Designation
1 PC controller with screen and touch operation
2 Emergency stop button
– system's safety stop button
3 "System release" illuminated button
– lights up white when the system is ON
– button for system O and resetting the emergency stop safety circuit
4 Display: "Fault"
– lights up in the event of a malfunction
5 Key switch for system release
– rotary movement to the right, with spring return
– start of the safety circuit
6 ON/OFF switch for the SprayPackE controller and EPG S2

20
VERSION 01/2020 ORDER NUMBER DOC2397091 SprayPackE
5.2.2 CONNECTIONS ON REAR SIDE OF MCE
1
2
3
4
5
6
7
8
20
19
18
17
16
15
14
13
12
11
10
9
P_03708
Signal Description
1 USB 2.0 connection USB 2.0 connection for USB storage medium for
software updates and saving data
Close connection with cover when not in use.
2 Ethernet LAN connection Connect the MCE controller to a network
Normal MCE version, direct LAN connection
MCE version, remote service link from remote router
Various cablelengthsavailable,seelist ofcomponents
3 Network option Plastic cover in the basic version
If necessary, another data interface can be added.
4 Fuse, AC internal Fuse, 2 AT AC/DC supply (internal)
9951116 = Spare fuse 2AT, type FST 5 x 20 mm
5 Mains output terminal #1 Mains supply for EPG S2, group 1
6 Mains output terminal #2 Mains supply for EPG S2, group 2
7 Mains input terminal Universal mains input terminal 100-240 VAC,
50/60 Hz, 10Amp D
8 Grounding point Connection for grounding cable green/yellow
(4 mm²)
9 In/Out EPG Sprint X no. 2 Release signal for high voltage and powder
Signal for cleaning mode
Fault message from EPG-Sprint X no. 2
Table of contents
Other WAGNER Measuring Instrument manuals
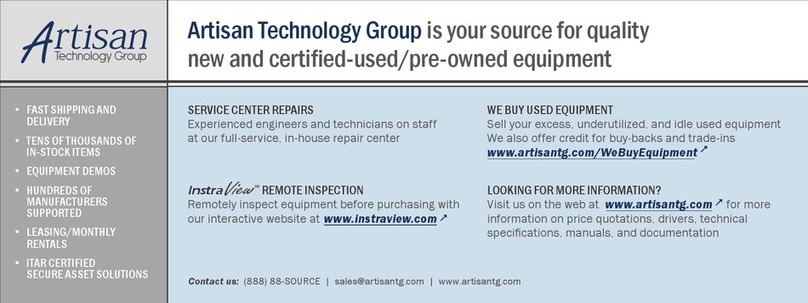
WAGNER
WAGNER FORCE DIAL FDL Series User manual
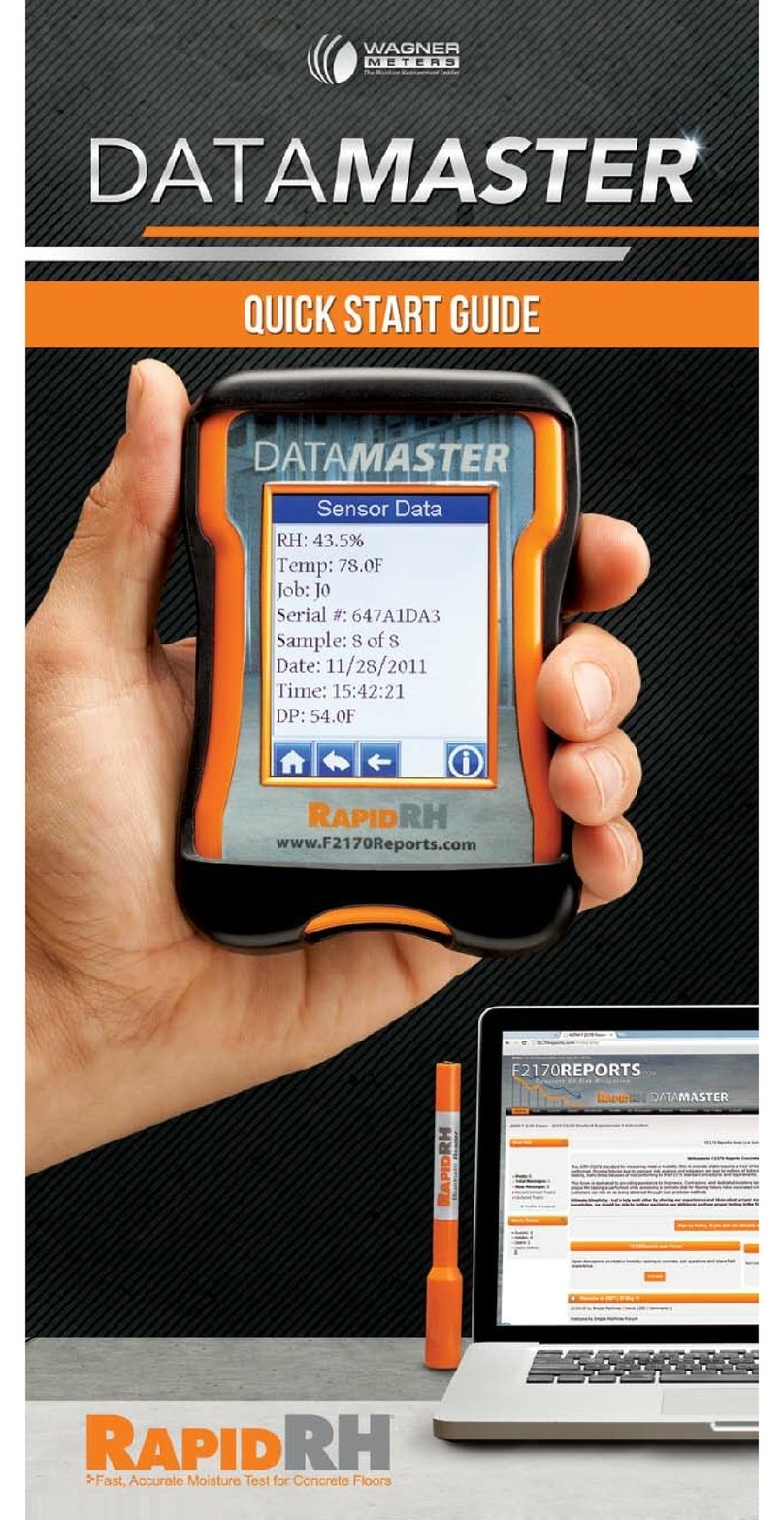
WAGNER
WAGNER Datamaster User manual
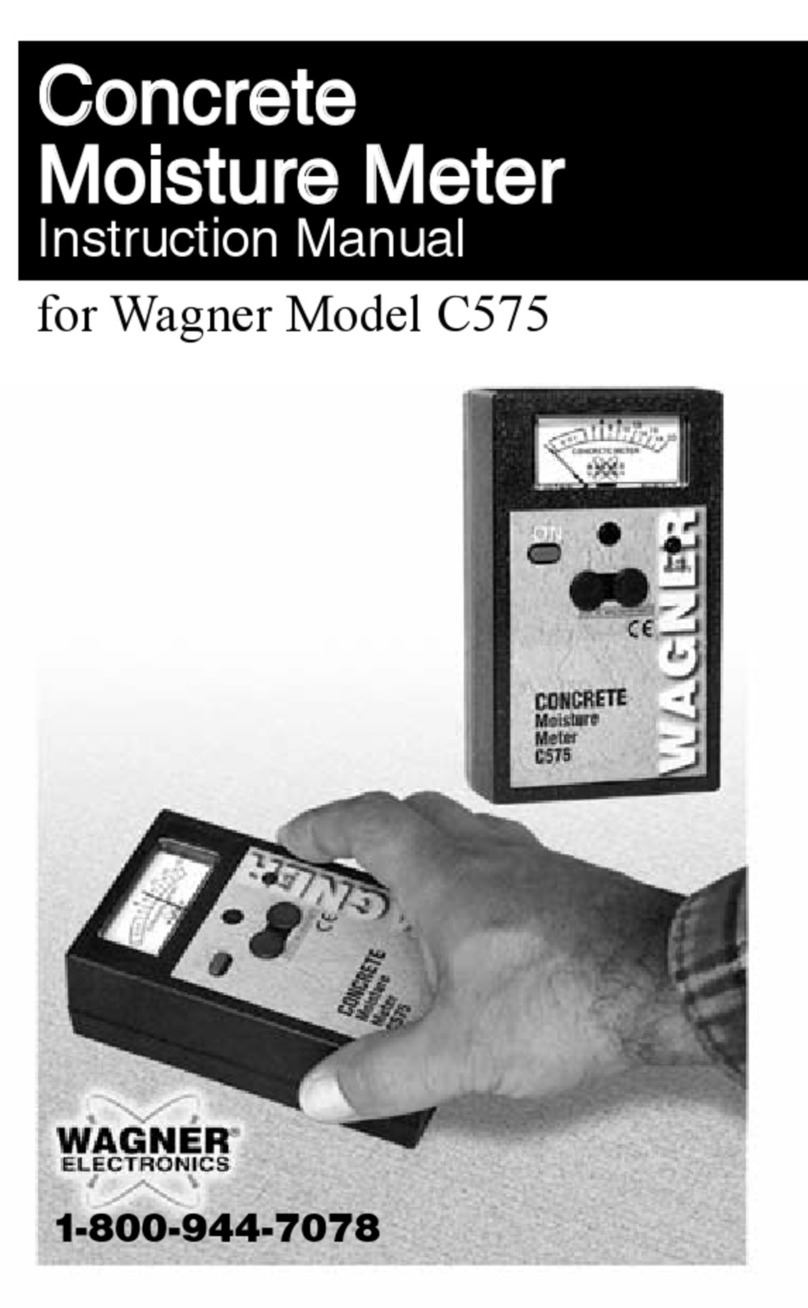
WAGNER
WAGNER C575 User manual
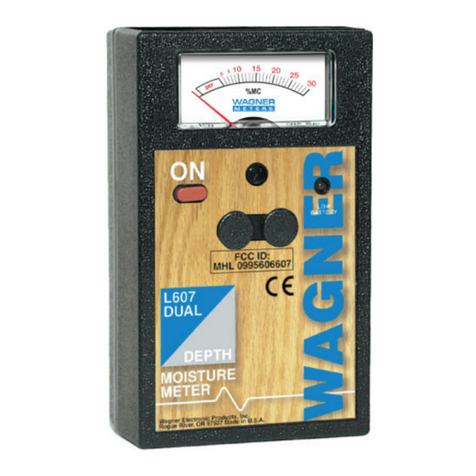
WAGNER
WAGNER L606 User manual
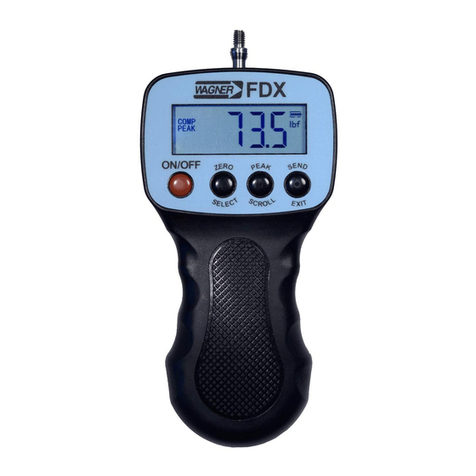
WAGNER
WAGNER Force Ten FDX User manual
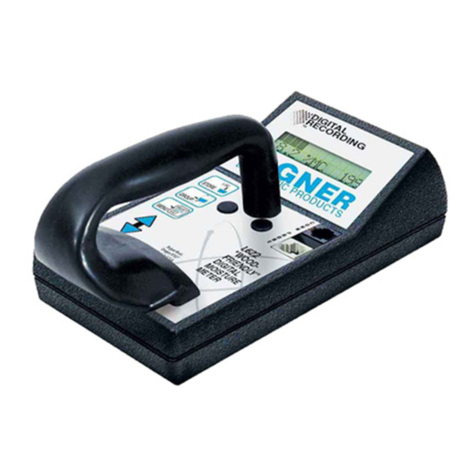
WAGNER
WAGNER L622 User manual

WAGNER
WAGNER FORCE DIAL FDL Series User manual
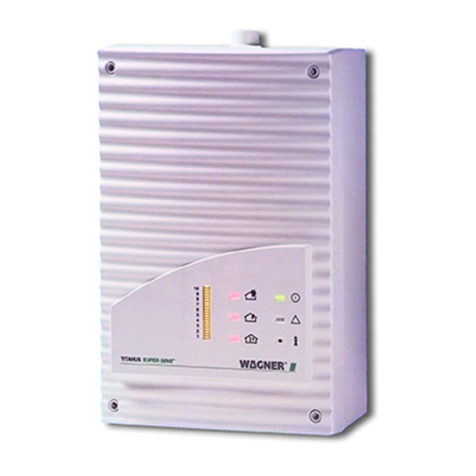
WAGNER
WAGNER TITANUS SUPER-SENS User manual

WAGNER
WAGNER RAPID RH User manual
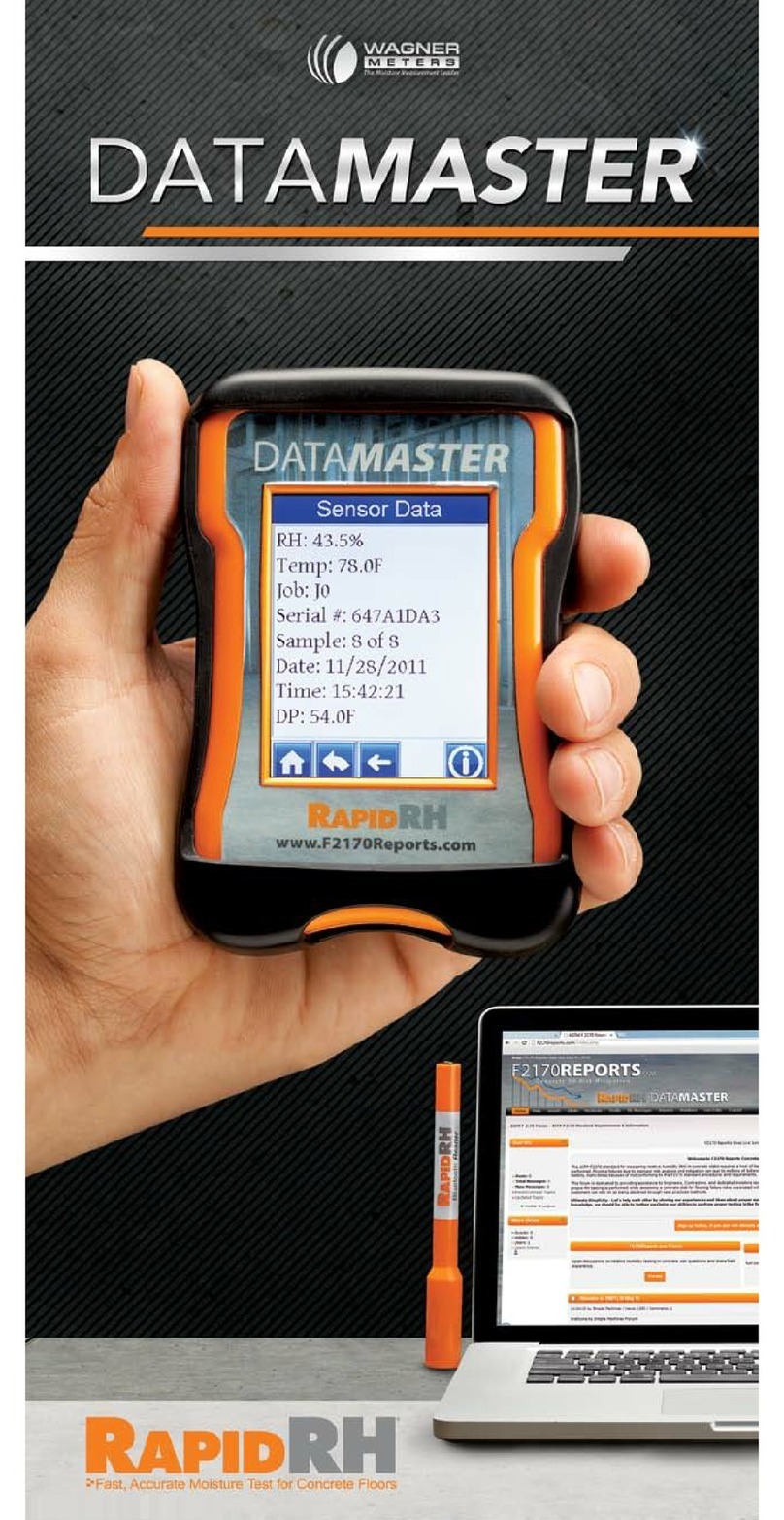
WAGNER
WAGNER Datamaster User manual
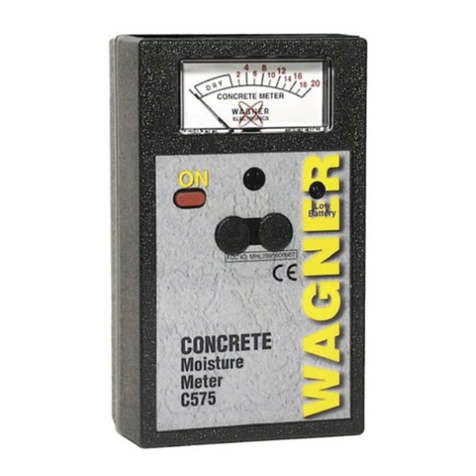
WAGNER
WAGNER C575 User manual
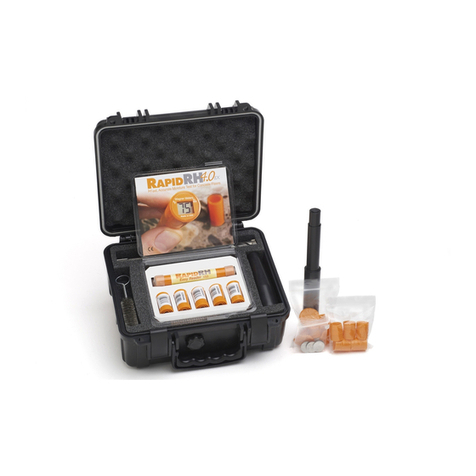
WAGNER
WAGNER Rapid RH 4.0 EX User manual
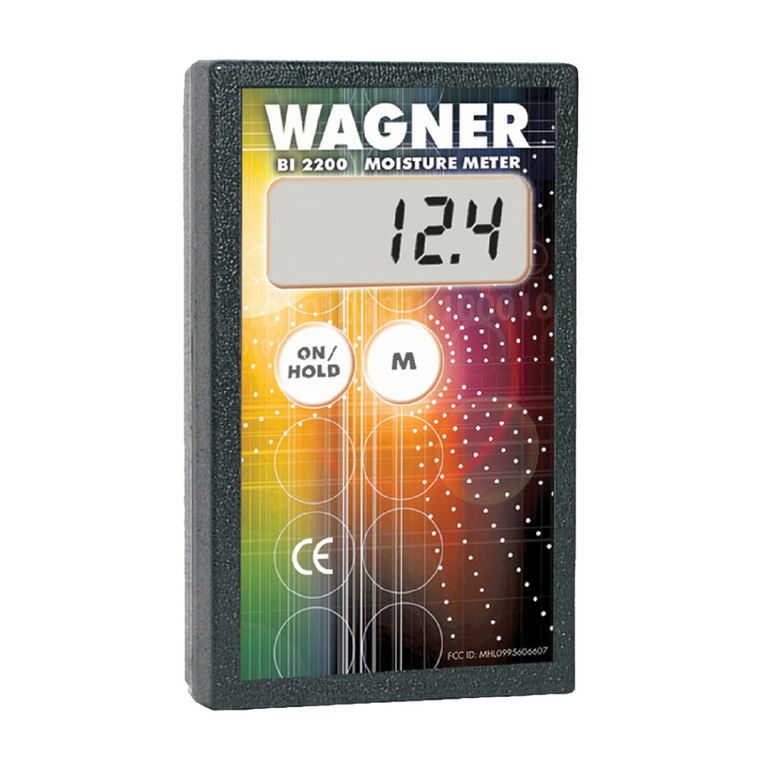
WAGNER
WAGNER BI 2200 User manual
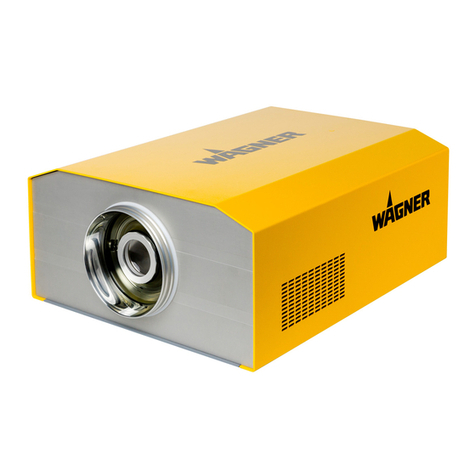
WAGNER
WAGNER Layer Check LC 1000 User manual
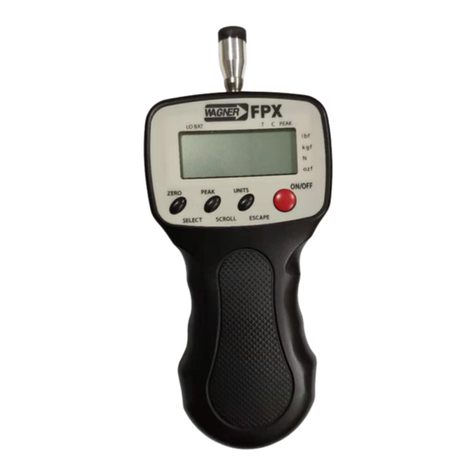
WAGNER
WAGNER FORCE TEN User manual
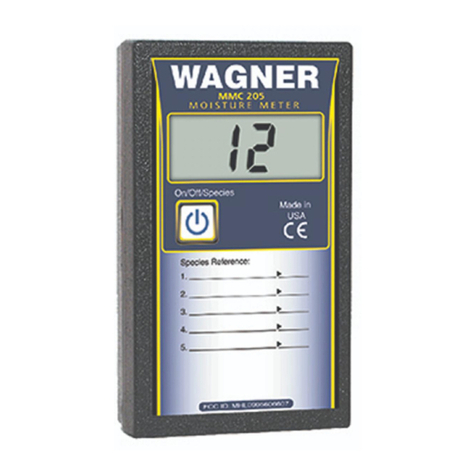
WAGNER
WAGNER MMC 205 User manual
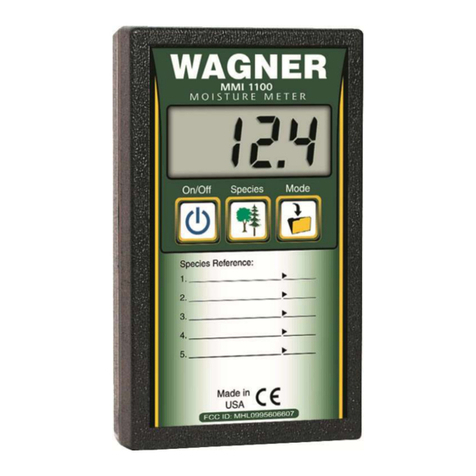
WAGNER
WAGNER MMI 1100 User manual

WAGNER
WAGNER RS 500 Operational manual

WAGNER
WAGNER L601-3 User manual