Wavelength Electronics LDTC2/2E User manual

ORDERING INFORMATION
PART NO DESCRIPTION
LDTC 2/2E Enclosed 2.2 A LD/TEC Controller
LDTC 2/2O Open Frame 2.2 A LD/TEC Controller
WEV-300* Thermal Washer & Heatsink
WEV-301* Thermal Washer, Heatsink, 5 V Fan
WEV-302* Thermal Washer, Heatsink, 12 V Fan
POWER & STABILITY
Combine the drive power of the WLD3343 laser driver (up
to 2.2 A) with the temperature stability of the WTC3243
temperature controller (±2.2 A available) on one small board.
Available as an open frame or in a chassis mount enclosure.
APPLICATIONS
Ideal for integrated laser driver or LED packages that include
temperature control, often utilized in medical diagnostic
equipment, remote sensing, analytical instrumentation,
military, and communications applications.
POWER YOUR APPLICATION WITH
THE RIGHT FEATURES
The WTC3243 will control temperature using thermistors,
RTDs, or linear temperature sensors such as the LM335
or the AD590. Adjust temperature using the onboard
trimpot or a remote voltage input from a panel mount
potentiometer, DAC, or other voltage source. A default
and avoids accidental damage to system components.
The WLD3343 Laser Driver maintains precision laser diode
curent (Constant Current Mode) or stable photodiode
current (Constant Power mode) using electronics
compatible with A/B Type lasers.
FEATURES AND BENEFITS
• ±2.2 A of TEC and 2.2 A of LD current (up to 3 A
with product variation)
• Small package size
• Single supply operation LD: +5 to +12 V
• Single supply operation TC: +5 to +28 V
• Slow start laser diode protection
• Constant Current or Constant Power modes
• Adjustable laser diode current limit
• Remote TTL Shutdown/Interlock
• Ultra-stable PI control loop
• Separate heat & cool current limits
• Failsafe Setpoint default for D/A remote
temperature setting
PAGE
e
Applies to Product Revisions A – B
© January 2019
A
Laser Type
B
Laser Type
LM335
AD590
RTD
RT
Pb
RoHS
Compliant
CONTENTS
QUICK CONNECT GUIDE 2
PIN DESCRIPTIONS 5
ELECTRICAL SPECIFICATIONS 7
SAFETY INFORMATION & THERMAL DESIGN
CONSIDERATIONS 9
OPERATING INSTRUCTIONS –
TEMPERATURE CONTROLLER 10
LASER DRIVER 12
ADDITIONAL TECHNICAL INFORMATION 15
TROUBLESHOOTING –
TEMPERATURE CONTROLLER 20
LASER DRIVER 21
MECHANICAL SPECIFICATIONS 23
CERTIFICATION AND WARRANTY 26
* Only for 2/2O
406-587-4910
www.teamWavelength.com
LDTC2/2E & LDTC2/2O
Laser Diode & Temperature Controllers
DATASHEET AND OPERATING GUIDE

© 2018 www.teamWavelength.com 2
LDTC2/2 LASER DIODE DRIVER AND TEMPERATURE CONTROLLER
Tset LIMA LIMB ILIM ISET
J1 J2
J3
COMmon
SENsor-
SENsor+
TEC-
TEC+
COMmon
LDAnode
PDCathode
PDAnode
LDCathode
GND
VS (5-28 V)
VDD (5-12 V)
COMmon
R TC SETpoint
SET T MONitor
ACT T MONitor
LD I MONitor
LD P MONitor
COMmon
R LDSETpoint
COMmon
LD SHD
PD MONitor
COMmon
3
2
1
10
9
8
7
6
5
4
3
2
1
12
11
10
9
8
7
6
5
4
3
2
1
LD ENABLE
TOGGLE
SWITCH
EXTERNAL
VOLTMETER
OR
VS
Bandgap
Voltage
Reference
D/A
0 V = OPEN = ENABLE
>3 V = CLOSED = DISABLE
{
AD590
THERMISTOR,
RTD, or ICs
OR
10 kΩ
OR
V
EXTERNAL
VOLTMETER
{
Like R TC SET (Pin 11)
VS
VDD
LD
ENABLE
VDD and VScan be tied together if common voltage provides
sufficient compliance for laser diode and thermoelectric loads.
Separate V
S
if higher compliance is required.
+ ++++
CC
CP
ExtTset Vset PDset
POWER
ON
CONSTANT CURRENT or
CONSTANT POWER Mode
Figure 1. Wiring Diagram for LDTC2/2.
Type A Laser Diode Type B Laser Diode Type C Laser Diode
Common
Cathode
Laser Diode Anode &
Photodiode Cathode Common Isolated Photodiode
Short the
Laser Diode Anode
to Photodiode Cathode
Common
Anode
Laser Diode Cathode &
Photodiode Anode Common
Figure 2. The LDTC2/2 is compatible with Type A and Type B lasers, but will not drive Type C lasers.
familiar with the controller operation. To pre-test or troubleshoot the temperature controller, please use the following
recommended test loads.
QUICK CONNECT GUIDE
!
Visit the Wavelength Electronics website for the most
accurate, up-to-date, and easy to use SOA calculator:
Laser Diode Drivers:
www.teamwavelength.com/support/design-tools/soa-ld-calculator/
Temperature Controllers:
www.teamwavelength.com/support/design-tools/soa-tc-calculator/

© 2018 www.teamWavelength.com 3
LDTC2/2 LASER DIODE DRIVER AND TEMPERATURE CONTROLLER
RECOMMENDED THERMOELECTRIC TEST
LOAD
For the temperature controller, recommended simulated
thermoelectric and thermistor circuits are shown in Figure 5
and Figure 6
test loads is recommended for setting the thermoelectric
controller limits or to check the temperature controller
operation.
RLOAD
TEC+
(Pin J3-6)
TEC-
(Pin J3-7)
RLOAD = 1 Ω, Rated >10 W
TEC Test Load
IMETER
Figure 5. Simulated Thermoelectric Test Load
R1
R1 = 10 kΩ, ¼ W resistor
SEN-
(Pin J3-9)
SEN+
(Pin J3-8)
Simulated Thermistor
Figure 6. Simulated Thermistor
Use the 100 µA bias current setting to create a 1 V sensor
signal. Other resistor values can be used depending on
the sensor voltage you wish to simulate. To drive cooling
current, set T SET to 1.35 V and to drive heating current, set
T SET to 0.85 V.
NOTE: To stay within the Safe Operating Area while using
the test load, VSmust not exceed 5 V.
RECOMMENDED LASER DRIVER TEST LOAD
For the laser diode driver, recommended simulated laser
loads are shown in Figure 3 and Figure 4.
1N4001
1N4001
LDC
(Pin J3-1)
LDA
(Pin J3-4)
1 Ω, 2 W
Constant Current Mode
Figure 3. Constant Current Mode Test Load
In Constant Power Mode, the setpoint correlates to the
photodiode feedback current, which represents a fraction
of the light power emitted by the laser diode. Photodiode
current is measured by monitoring LD P MON.
24 Ω
1N4001
1N4001
2N3906
0.33 µF
PDA
(Pin J3-2)
LDA
(Pin J3-4)
LDC
(Pin J3-1)
Constant Power Mode
The 24 Ω resistor typically
produces approximately 30 mA
laser driver current. Vary the
resistor value to change the
output current.
1 Ω, 2 W
Figure 4. Constant Power Mode Test Load
NOTE: To determine the actual drive current, measure
ammeter in series with the output circuit; doing so may
cause instability in the control loop. To stay within the Safe
Operating Area while using the test load, VSmust not exceed
5 V.

© 2018 www.teamWavelength.com 4
LDTC2/2 LASER DIODE DRIVER AND TEMPERATURE CONTROLLER
PIN DESCRIPTIONS
Table 1. Pin Descriptions and Wire Colors
PIN NAME CABLE
COLOR PIN DESCRIPTION
Connector J1 – WCB300
1 (VDD)
Supply Voltage to Control
Electronics and Laser
Diode
Red
Connect +5 to +12 V between Pins 1 & 3 to power the control electronics
and the output drive to the laser diode. Reference the Safe Operating
Area Calculator.
2 (VS) Supply Voltage to Output
TEC Drive White Connect +5 to +28 V between Pins 2 & 3 to drive the TEC output stage.
Reference the Safe Operating Area Calculator.
3 (GND) Power Supply Ground Black Connect power supply ground to this pin.
Connector J2 – WCB309
1 (COM) Common Tan Low current GND for monitors, DACs, External VSET, etc.
PIN 1 not available on Rev. A
2 (PD MON) PD Monitor in CC mode Pink Photodiode Monitor in Constant Current mode.
PIN 2 not available on Rev. A
3 (LD SHD) LD Shutdown/Interlock
(TTL-Compatible) Grey Float or GND = Enable Laser Diode Current
Input > 3 V = Disable Laser Diode Current
4 (COM) Common Violet Low current GND for monitors, DACs, External VSET, etc.
5 (R LD SET) Remote Laser Diode
Setpoint/Modulation Input Yellow Voltage Input range is 0 to 2 V. Transfer function is given in Table 2.
6 (COM) Common Orange Low current GND for monitors, DACs, External VSET, etc.
7 (LD P MON) Photodiode Monitor Blue
Monitor the laser diode power. This pin produces a voltage proportional
to the current produced by the laser diode monitor photodiode. See
Table 2 for the transfer function.
8 (LD I MON) LD Current Monitor Brown
Monitor the laser diode forward current. This pin produces a voltage
Table 2 for the transfer function
9 (ACT T MON) Actual Temperature
Monitor Green
Monitor the actual voltage produced by the temperature sensor. The
voltage produced and transfer function to temperature is determined
by the sensor chosen.
10 (SET T MON) Setpoint Monitor Red Monitor the temperature setpoint voltage. The voltage produced and
transfer function to temperature is determined by the sensor chosen.
11 (R TC SET) Remote Temperature
Setpoint White
Connect a voltage source between Pin 11 and Pin 12 to control the
pin drops below 0.3 V.
12 (COM) Common Black Low current GND for monitors, DACs, External VSET, etc.
Connector J3 – WCB301
1 (LDC) Laser Diode Cathode Black Laser diode cathode connection.
2 (PDA) Photodiode Anode White Photodiode anode connection.
3 (PDC) Photodiode Cathode Blue Photodiode cathode connection.
4 (LDA) Laser Diode Anode Red Laser diode anode connection.
5 (COM) Common Green Low current GND for monitors, DACs, External VSET, etc.
6 (TEC+) TEC+ Connection Red/Black
7 (TEC-) TEC- Connection Orange
8 (SEN+) [1] Temperature Sensor+ White/Black Positive side of temperature sensor. Bias current is driven from SEN+
to SEN-.
9 (SEN-) [1] Temperature Sensor- Orange/Black
table for input voltage range and damage thresholds.
10 (COM) Common Green/Black Low current GND for monitors, DACs, External VSET, etc.
[1] See page 14 for additional information regarding the use of RTDs, AD590, and LM335 sensors with the LDTC2/2.

© 2018 www.teamWavelength.com 5
LDTC2/2 LASER DIODE DRIVER AND TEMPERATURE CONTROLLER
Table 2. Monitor & Setpoint Transfer Functions
FUNCTION EQUATION DESCRIPTION
Monitor Transfer Functions
Laser Diode Forward Current
Measurement ILD = VLD I M
2·RSENSE
Converts voltage output of Laser Diode Current Monitor (Pin 8,
Connector J2) to forward current through Laser Diode.
Default RSENSE
Monitor Photodiode
Current Measurement
(Constant Power Mode)
IPD = VLD P M
2·RPD
Converts voltage output of Laser Diode Power Monitor (Pin 7,
Connector J2) to forward current through Photodiode. [2]
RPD
RPD
Monitor Photodiode
Current Measurement
(Constant Current Mode)
IPD = VPD MON
RPD
Converts voltage output of Photodiode Monitor (Pin 2, Connector J2) to
forward current through Photodiode. [2]
RPD
RPD
NOTE: Available on Rev. B and later.
Actual Temperature 1 V / V Monitors the actual temperature.
Setpoint Transfer Functions
Laser Diode Current ILD = VR LD SET
2·RSENSE
Converts Setpoint Voltage to Laser Diode current.
Default RSENSE
Photodiode Current
(Constant Power Mode) IPD = VR LD SET
2·RPD
Converts Setpoint Voltage to Photodiode current. [2]
RPD
RPD
Temperature Setpoint 1 V / V Monitors the temperature setpoint.
[2] RPD is set with the onboard PDset jumper. See page 11
Determining Revision: The product revision is indicated within the serial number. Find the serial number labeled on the
PCB. Revision is the third character. Example: 00B1730002 would be Revision B of the LDTC2/2.

© 2018 www.teamWavelength.com 6
LDTC2/2 LASER DIODE DRIVER AND TEMPERATURE CONTROLLER
ELECTRICAL SPECIFICATIONS
ABSOLUTE MAXIMUM RATINGS SYMBOL LDTC2/2E LDTC2/2O UNIT NOTE
LD Supply Voltage & Control Electronics VDD +4.75 to +12 VDC
TC Load Supply Voltage VS+4.5 to +28 VDC
Max LD Output Current ILD 2.2 A
Max TC Output Current IOUT ±2.2 A
Laser Driver Internal Power Dissipation PMAX 9 W TAMBIENT = 25ºC
Temperature Controller Internal Power
Dissipation PMAX 9 W TAMBIENT = 25ºC (with fan
and heat sink)
Case Operating Temperature [1] TOPR -40 to 85 ºC
Case Storage Temperature TSTG -65 to 150 ºC
Weight 6.5 2.4 oz 184.3 g (LDTC2/2E)
68.0 g (LDTC2/2O)
Size 4.8 × 2.7 × 1.14 4.2 × 2.5 × 1 inches 121.9 × 68.6 × 29.0 mm (2/2E)
106.7 × 63.5 × 25.4 mm (2/2O)
LASER DRIVER
SPECIFICATIONS MIN TYP MAX UNIT NOTE
CONSTANT CURRENT CONTROL
Short Term Stability, 1 hour 200 ppm TAMBIENT = 25ºC
CONSTANT POWER CONTROL
Short Term Stability, 1 hour 0.01 % TAMBIENT = 25ºC
Long Term Stability, 24 hours 0.05 % TAMBIENT = 25ºC
OUTPUT
Peak Current, IMAX 1.8 2.0 2.2 A With heat sink and fan.
Compliance Voltage, Laser Diode Load 3.0 V Full Temp. Range, ILD=2.0A, 5V
Rise Time 460 nsec ILD = 2 A
Fall Time 320 nsec ILD = 2 A
Bandwidth, Constant Current 1.6 MHz Sinewave input signal
Bandwidth, Constant Power Depends on Photodiode Bandwidth
Delayed Start 0.25 sec
Slow Start Ramp 0.01 sec
POWER SUPPLY
Voltage, VDD 5 12 V
Quiescent Current, VDD 5 10 15 mA
MODULATION INPUT
VSET Input Voltage Range 0 2 V
VSET Damage Threshold < -0.5 > 5.4 V
VSET Input Impedance 20
[1] With Revision D of the WLD3343, an internal thermostat has been added to activate Shutdown (SHD) when the internal
CAUTION: Operation higher than 5 V on VDD (i.e. 12 V) requires close evaluation of the SOA curves and current limit
settings. Damage to the WLD or WTC will occur if they are operated outside their Safe Operating Area. Contact the factory
if you plan to use higher than 5 V.

© 2018 www.teamWavelength.com 7
LDTC2/2 LASER DIODE DRIVER AND TEMPERATURE CONTROLLER
ELECTRICAL SPECIFICATIONS (CONTINUED)
TEMPERATURE CONTROLLER
SPECIFICATIONS MIN TYP MAX UNIT NOTE
TEMPERATURE CONTROL
Short Term Stability, 1 hour [2] 0.0009
Short Term Stability, 1 hour [2] 0.002
Long Term Stability, 24 hours [2] 0.002
Control Loop P PI
P (Proportional Gain) 18 20 22 A / V
I (Integrator Time Constant) 2 34 sec
Setpoint vs. Actual Temperature Accuracy <0.2%
(Rev. B)
OUTPUT
Peak Current ±1.8 ±2.0 ±2.2 A
Compliance Voltage [3],
Full Temperature Range
|VS- 0.1| V TEC, IOUT = 100 mA
|VS- 0.3| V TEC, IOUT = 1.0 A
|VS- 0.3| V TEC, IOUT = 1.5 A
|VS- 0.6| V TEC, IOUT = 2.0 A
|VS- 0.6| V Resistive Heater, IOUT = 2.2 A
POWER SUPPLY
Voltage, VDD 4.75 12 V
Quiescent Current, VDD 55 105 mA
Voltage, VS4.5 28 V
Quiescent Current, VS20 50 100 mA
TEMPERATURE SENSORS
Sensor Compatibility Thermistor, RTD, IC Sensors
Sensor Input Voltage Range [4] GND to VDD - 2.0 V
Sensor Input Damage Threshold < -0.7 > VDD+7 V
VSET
Input Impedance 500
VSET Damage Threshold < -0.7 > VDD+7 V
BIAS CURRENT
Bias Current Accuracy 1 % Include bias current resister tolerance
THERMAL
Heatspreader Temperature Rise [5] 28 30 33 No heatsink, thermal washer, or fan
Heatspreader Temperature Rise [5] 18 21.5 25 With WHS302 Heatsink and
WTW002 Thermal Washer, no fan
Heatspreader Temperature Rise [5] 3.1 3.4 3.9
With WHS302 Heatsink,
WTW002 Thermal Washer,
and 3.5 CFM fan
[2]
above ambient.
[3] Compliance voltage available between Pins 6 & 7 (TEC+ & TEC-) on J3.
[4] The bias source has a compliance up to VDD - 2 V. In normal operation this limits the sensor voltage range from 0 V to
VDD - 2 V. While voltages up to ±5 V outside this range on the VSET pin will not damage the unit, it will not provide proper
control under these conditions.
[5] TAMBIENTonly. Valid for both laser driver and temperature controller (WLD & WTC).

© 2018 www.teamWavelength.com 8
LDTC2/2 LASER DIODE DRIVER AND TEMPERATURE CONTROLLER
THEORY OF OPERATION
The LDTC2/2 Laser Diode Driver and Temperature
Controller combines the drive power of the WLD3343 with
the temperature stability of the WTC3243.
The LDTC2/2E is enclosed with a cover and base, while the
LDTC2/2O is open frame without cover or base. Accessory
heatsinking is required for LDTC2/2O. Both have the same
functionality.
LASER DIODE DRIVER CURRENT SOURCE
It may be useful to remember that you do not directly set
the laser drive current setpoint; instead, you adjust a voltage
signal that represents the output current. The setpoint
voltage is controlled by the onboard trimpot or by an an
external input.
As current is driven through the load, there is a voltage drop
across the load because of the impedance. As the current
increases, the voltage drop may increase to the point that it
reaches the Compliance Voltage limit of the current source.
Once that occurs, the current source is no longer able to
increase the current driven to the load, even if you increase
the setpoint.
TEMPERATURE CONTROLLER
thermoelectric cooler, or unidirectional current to a resistive
heater. The controller adjusts the output current in order to
change the temperature of the sensor that is connected to
the thermal load. The goal is to make the voltage across the
sensor match the setpoint voltage, and then keep them equal
in spite of changes to ambient conditions and variations in
thermal load.
FEATURES
The LDTC2/2 integrated laser driver and temperature
controller includes features that help protect your laser and
make the driver more versatile in a wide array of applications:
• The current limits (laser, heating, cooling) are set by
onboard trimpots and protect the laser from over-current
and over-/under-temperature conditions.
• Slow-start delays the laser current ramp by 250 msec,
and then ramps the current to the setpoint.
• Constant Power operation is available, where the driver
adjusts the laser forward current in order to maintain a
constant photodiode current.
• Available remote LD & TC setpoint control.
• Separate heating and cooling current limits.
SAFETY INFORMATION
& THERMAL DESIGN
CONSIDERATIONS
SAFE OPERATING AREA — DO NOT EXCEED
INTERNAL POWER DISSIPATION LIMITS
Before attempting to operate the LDTC, it is imperative that
controller will operate within the Safe Operating Area (SOA).
Operating the unit outside of the SOA may damage the
controller or the load, and will void the warranty.
Go to the Wavelength Electronics website for the most
accurate, up-to-date, and easy to use SOA calculators:
Laser Diode Drivers:
www.teamwavelength.com/support/design-tools/soa-ld-calculator/
Temperature Controllers:
www.teamwavelength.com/support/design-tools/soa-tc-calculator/
SOA charts are included in this datasheet for quick reference
(page 18), but we recommend you use the online tools
instead.
For more information on Safe Operating Area, see our
Application Note AN-LDTC01: The Principle of the Safe
Operating Area.
When you assemble and mount the TEC (or heater),
heatsink, and temperature sensor, make sure the physical
connections between the components are solid. We
recommend using thermal paste or thermal washers at the
load/TEC and TEC/heatsink interfaces. The thermistor must
reliable temperature control.
PREVENT DAMAGE FROM
ELECTROSTATIC DISCHARGE
Before proceeding, it is critical that you take precautions to
prevent electrostatic discharge (ESD) damage to the driver
and your laser. ESD damage can result from improper
handling of sensitive electronics, and is easily preventable
with simple precautions.
For more information regarding ESD, see our Application
Note AN-LDTC06: Electrostatic Discharge Basics.
We recommend that you always observe ESD precautions
when handling the LDTC controller and loads.
!

© 2018 www.teamWavelength.com 9
LDTC2/2 LASER DIODE DRIVER AND TEMPERATURE CONTROLLER
OPERATING INSTRUCTIONS –
TEMPERATURE CONTROLLER
!
WTC.
RECOMMENDED ORDER OF SETUP
simulation diode load in place until the temperature control
section is working properly. After the temperature control
section is operating according to preferences, then the
operation is recommended in order to avoid any potential
damage to an expensive laser diode.
CONFIGURING HEATING AND COOLING
CURRENT LIMITS
The LDTC2/2 has two trimpots that independently set the
heating and cooling current limits: LIM A & LIM B. These
are 12-turn trimpots. Maximum current (2.2 A) is at full CCW
position. Table 3 shows the meaning of the trimpots with
various sensors and load types. Note that PTC sensors
include RTDs, the LM335, and the AD590.
Table 3. Trimpot Function vs. Sensor & Load Type
SENSOR LOAD LIM A LIMITS LIM B LIMITS
Thermistor Thermoelectric Cool Current Heat Current
PTC Thermoelectric Heat Current Cool Current
Thermistor Resistive Heater OFF = Fully CW Heat Current
PTC Resistive Heater Heat Current OFF = Fully CW
WIRE OUTPUT CONNECTION
Use Table 4 to determine the connection from the LDTC2/2
to your thermoelectric or resistive heater.
Table 4. Wiring vs. Sensor & Load Type
SENSOR LOAD TEC+
PIN J3:6
TEC-
PIN J3:7
Thermistor Thermoelectric Thermoelectric
positive wire
Thermoelectric
negative wire
PTC Thermoelectric Thermoelectric
negative wire
Thermoelectric
positive wire
Thermistor Resistive
Heater
Quick Connect:
Connect the Resistive Heater to TEC+
& TEC- (polarity doesn’t matter). Adjust
the Cooling Current Limit A trimpot to
zero - fully CW.
Max V Connect:
Connect one side of the resistive
heater to TEC- and the other side to
the voltage source VS. LIM A trimpot
setting is then irrelevant. Allows for
approximately 1 V less internal voltage
drop across the LDTC.
PTC Resistive
Heater
Quick Connect:
Connect the Resistive Heater to TEC+
& TEC- (polarity doesn’t matter). Adjust
the Cooling Current Limit B trimpot to
zero - fully CW.
Max V Connect:
Connect one side of the resistive
heater to TEC- and the other side to
the voltage source VS. LIM B trimpot
setting is then irrelevant. Allows for
approximately 1 V less internal voltage
drop across the LDTC.
CONNECT TEMPERATURE SENSOR
Wire the thermistor between Pins 8 & 9 (SEN+ & SEN-) on
Connector J3.
!
For sensors other than thermistors, see
Alternate Temperature Sensors” on page 14.

© 2018 www.teamWavelength.com 10
LDTC2/2 LASER DIODE DRIVER AND TEMPERATURE CONTROLLER
POWER SUPPLY SELECTION
The VDD voltage supply input is common to both the WLD3343
and the WTC3243. This supply furnishes the voltage to the
control electronics of the devices as well as the compliance
voltage for the WLD3343 laser driver.
The supply should be capable of providing at least 3.0 A
of current in applications that use a separate VSsupply
in the temperature control implementation. Temperature
control applications that tie VDD and VStogether require a
VDD current capacity that equals the sum of the maximum
TEC or Resistive Heater current, plus the maximum laser
diode current, plus approximately 200 mA for the control
electronics of the WTC3243 temperature controller and the
WLD3343 laser driver, plus current to an optional fan. Using
the maximum potential of the WLD and WTC will not require
more than 6.0 A.
VSis the voltage that is applied to the TEC or Resistive
Heater. This voltage should be high enough to supply the
voltage required by the TEC or Resistive Heater plus the
compliance required by the WTC. The voltage available to
the TEC will be from between 0.5 to 1.8 V lower than VS. To
minimize power dissipation in the WTC, keep VSas low as
possible.
Calculate the maximum internal power dissipation of your
design before applying power to the LDTC2/2. There are
Safe Operating Calculators available on our website.
TEMPERATURE SETPOINT
Wavelength introduces a special setpoint circuit with the
LDTC2/2. An onboard trimpot (TSET) will adjust the voltage
from 0.3 to 2.5 V. Additionally, Pins 11 (R TC SET) &
12 (COM) of Connector J2 will accept a DAC voltage (from
0.3 to 2.5 V). The new feature - the “Failsafe Setpoint” will
the chosen signal (from the onboard trimpot or DAC) falls
below 0.3 V.
A jumper (ExtTset) lets you choose to use only the
on-board potentiometer or the external voltage, as shown in
Figure 7 below.
Use On-board
trimpot
OR
Sum ExtTset with
trimpot
CC
CP
S2
CC
CP
S2
Use External
Voltage only
ExtTset Vset PDset
ExtTset Vset PDset
Figure 7. Source of setpoint.
Setpoint choice. There is approximately 100 mV of
hysteresis built into the default voltage. The input impedance
voltage, contact Wavelength.
MONITOR ACTUAL TEMPERATURE & SETPOINT
Pins 9 & 10 of Connector J2 are ACT T MONitor
and SET T MONitor, respectively. Measure the actual
R = 10 · VJ2_PIN9
To monitor the setpoint voltage used by the WTC, use Pins
10 and 12.
ENABLE CURRENT TO TEC
Output current is supplied to the load as soon as power is
applied to the controller. The Power LED indicator will light
GREEN when power is applied.

© 2018 www.teamWavelength.com 11
LDTC2/2 LASER DIODE DRIVER AND TEMPERATURE CONTROLLER
OPERATING INSTRUCTIONS –
LASER DRIVER
!
WTC.
RECOMMENDED ORDER OF SETUP
simulation diode load in place until the temperature control
section is working properly. After the temperature control
section is operating according to preferences, then the
operation is recommended in order to avoid any potential
damage to an expensive laser diode.
CHOOSE OPERATING MODE –CONSTANT
CURRENT OR CONSTANT POWER
A sliding switch selects operating mode.
!
In Constant Current mode, Laser Diode ISET correlates
directly to the laser diode current, regardless of laser diode
power intensity.
In Constant Power mode, the LDTC2/2 controls the laser
diode using the photodiode to achieve a laser light intensity
that is directly proportional to Laser Diode ISET.
Select the mode of operation for the LDTC2/2 with the power
Current mode, or the CP position for Constant Power Mode.
SELECT THE MONITOR PHOTODIODE CURRENT
RANGE (CONSTANT POWER OPERATION)
Select between two ranges on the LDTC2/2 board:
this jumper only when power is not applied to VDD.
Setting for
2.0 mA range
Setting for
200 µA range
CC
CP
CC
CP
ExtTset Vset PDset
Vset PDset
ExtTset
Figure 8. Select the photodiode range with the PDset
jumper.
The transfer function of the setpoint voltage depends on
this setting for Constant Power Operation (see Table 2 on
page 5). If you choose the wrong setting, you could
overdrive your laser diode.
POWER SUPPLY SELECTION
!
.
The VDD voltage supply is common to both the WLD3343
and the WTC3243. This supply furnishes the voltage to the
control electronics of the devices as well as the compliance
voltage for the WLD3343 Laser Driver.
The supply should be capable of providing at least 3.0 A
of current in applications that use a separate VSsupply
in the temperature control implementation. Temperature
control applications that tie VDD and VStogether require a
VDD current capacity that equals the sum of the maximum
TEC or Resistive Heater current, plus the maximum laser
diode current, plus approximately 200 mA for the control
electronics of the WTC3243 Temperature Controller and the
WLD3343 Laser Driver. Using the maximum potential of the
WLD and WTC will not require more than 6.0 A.
Performance of the laser driver is very dependent upon
the performance of the power supply. The LDTC2/2 does
optimal performance, a power supply that can provide the
appropriate level of noise and ripple for the application at
hand should be utilized.
supplies in a range of output voltage and current capacities.

© 2018 www.teamWavelength.com 12
LDTC2/2 LASER DIODE DRIVER AND TEMPERATURE CONTROLLER
DISABLING THE OUTPUT CURRENT
The output current can be enabled and disabled as shown in
Figure 9 using the on-board toggle switch. The Enable LED
lights green when laser diode current is enabled.
ON OFF
LD ENABLE
TOGGLE
SWITCH
LD Enable
Figure 9. Use the on-board toggle switch to enable or
disable output current to the laser diode.
A remote voltage signal can be used to control the output
status of the laser driver using the laser diode shutdown
(LD SHD) pin. Float or connect a zero Volt signal to LD SHD
(Pin 3 on Connector J2) to ENABLE output current to the
laser diode. A voltage level greater than 3 V, but less than 5
V, will DISABLE output current to the laser diode. This diode
was designed for TTL inputs.
The external LD SHD signal to Pin 3 has complete control
when the on-board LD Enable switch is in the ENABLE
position.
!
!
MONITOR LASER DIODE OR PHOTODIODE
CURRENT
Equation 1 provides a transfer function for converting the
voltage output of LD I M (Laser Diode Current Monitor - Pin 8
the laser diode.
Equation 1. Laser Diode Forward Current Measurement
ILD DEFAULT = 1.25·VLD I M
Equation 2 provides a transfer function for converting the
voltage output of LD P M (Laser Diode Power Monitor - Pin 7
the photodiode.
Equation 2. Monitor Photodiode Current Measurements in
Constant Power Mode
2 mA PD Range: IPD = 0.001·VLD P M
IPD = 0.0001·VLD P M
Photodiode current can be monitored in Constant Current
Mode by monitoring J2 Pin 2 (PD MON) with a voltmeter.
(NOTE: Pin 1 & Pin 2 on J2 are not available on Rev. A.) The
photodiode current is then given by Equation 3:
Equation 3. Monitor Photodiode Current Measurements in
Constant Current Mode
2 mA PD Range: IPD = 0.002·VPD MON
IPD = 0.0002·VPD MON
NOTE: Available Rev. B and later.
NOTE: LD P MON has a gain of 2.
PD MON has a gain of 1.
Determining Revision: The product revision is indicated
within the serial number. Find the serial number labeled
on the PCB. Revision is the third character. Example:
00B1730002 would be Revision B of the LDTC2/2.

© 2018 www.teamWavelength.com 13
LDTC2/2 LASER DIODE DRIVER AND TEMPERATURE CONTROLLER
CONFIGURE THE LASER DIODE CURRENT LIMIT
to adjust the Current Limit. The trimpot is labeled ILIM (as
opposed to LIM A or LIM B for the temperature control limit
current trimpots). Fully CCW sets the limit current to the
maximum. A simulated laser diode load is recommended to
set the limit current. To set the laser diode current limit:
•
jumper to the lower position (see Figure 10).
• Set ILIM to zero by turning the trimpot 12 full turns CW.
• Set ISET to maximum by turning the trimpot 12 full turns
CW.
• Monitor the voltage between LD I MON and COM.
• Increase ILIM (turning CCW) until the desired voltage is
reached.
• Decrease ISET (turning CCW) until the voltmeter is
The LD current limit is now set and the current can be
adjusted within the limit range.
LASER DIODE SETPOINT AND MODULATION
The laser diode setpoint voltage determines the amount of
current that is delivered to the laser. In Constant Current
mode, the setpoint is directly proportional to the laser diode
current. In Constant Power mode, the setpoint is directly
proportional to the photodiode current, allowing for control
of the optical power of the light emitted by the laser diode.
The setpoint voltage can be adjusted either by using the on-
board ISET trimpot, by applying an external setpoint voltage,
or by summing an external setpoint voltage with the setpoint
voltage created by adjustment of the ISET trimpot. The sum
of the external setpoint voltage and the voltage created with
the on-board ISET trimpot can be from zero to 2.5 V.
To use only the on-board ISET trimpot, place the VSET
jumper in the lower position (as shown below in Figure 10),
and do not connect an external voltage source to the R LD
SET input. The ISET trimpot provides a setpoint adjustment
of between zero to 2.5 V.
Use On-board
trimpot
OR
Sum ExtTset with
trimpot
CC
CP
CC
CP
Use External
Voltage only
ExtTset Vset PDset
ExtTset Vset PDset
Figure 10.
To use an external voltage source summed with the voltage
supplied by the ISET trimpot, place the VSET jumper in the
lower position (as shown in Figure 10). Connect the external
voltage, or DAC output, to the R LD SET input (Pin 5 on
the external voltage being supplied plus any setpoint voltage
created with the on-board SET trimpot.
To use only an external voltage source for the setpoint
voltage, place the VSET jumper in the upper position (see
Figure 10) and connect the external setpoint voltage via the
setpoint voltage which is applied to the laser driver.
Equation 4 illustrates the relationship between setpoint
voltage (VR LD SET) and the current that will be applied to the
laser diode.
Equation 4. Current Applied to the Laser Diode
ILD = 1.25 · VR LDSET
Equation 5 and Equation 6 illustrate the relationship
between setpoint voltage (VR LD SET) and the resulting
photodiode current while operating in Constant Power
mode for the two standard photodiode ranges that can be
Equation 5. Photodiode Current in Constant Power Mode
(2 mA PD Range)
IPD = 0.001 ·VR LDSET
Equation 6. Photodiode Current in Constant Power Mode
IPD = 0.0001 ·VR LDSET
OPERATION NOTES
!
!

© 2018 www.teamWavelength.com 14
LDTC2/2 LASER DIODE DRIVER AND TEMPERATURE CONTROLLER
ADDITIONAL TECHNICAL
INFORMATION
This section includes useful technical information on the
following topics:
• Steps For Replacing The WTC/WLD
• Proportional Gain & Integrator Time Constant – PI
Terms
•
• Changing The Laser Diode Output Current Range
• Laser Driver Block Diagram
• Temperature Controller Block Diagram
• Safe Operating Area Calculation
STEPS FOR REPLACING THE WTC/WLD
Disassemble the LDTC2/2:
1. Remove cables from the unit.
2. Remove screw from top of unit holding the cover down.
3. Lift straight up on the cover to remove it from the base.
4. Remove PCB from the base plate by carefully pulling it
PCB.
5. Remove the eight screws on the bottom of the baseplate
that attach the WLD and WTC to the baseplate.
6. Use a small screwdriver to separate the WLD and WTC
from the baseplate.
Reassemble the LDTC2/2:
1. Plug the new part(s) into the PCB before attaching it to
the base to ensure that the pins do not get bent.
2. Make sure that the thermal sil pad or thermal paste is in
good shape in order to tightly couple the WLD/WTC heat
spreader to the mounting plate or heat sinking surface.
Replace a questionable sil pad or spread a new thin coat
of thermal paste.
3. Seat the holes on the PCB onto the corner posts and
press PCB into seated position. Install the eight screws
in the WLD and WTC.
4. Install the cover and cables.
PROPORTIONAL GAIN & INTEGRATOR TIME
CONSTANT – PI TERMS
appropriate for most laser diode loads. To adjust these
parameters to optimize the temperature control system time
to temperature or stability, contact Wavelength.
CONFIGURATION FOR ALTERNATE
TEMPERATURE SENSORS
LM335
To use a National Semiconductor LM335 temperature sensor
with the LDTC2/2, attach the LM335 cathode to SENSOR+
and the LM335 anode to SENSOR-. RBIAS, shown in
Figure 11
1mA through the sensor.
The voltage output of the LM335 is 10 mV/K.
NOTE: The ExtTset must be used for setting the temperature
when using the LM335.
AD590
To use an Analog Devices AD590 temperature sensor with
BIAS shown in Figure 11.
Connect the positive lead of the AD590 to a VDD voltage
connected between SENSOR+ and ground (Pins 8 & 9 on
J3).
RTD
To use an RTD, the bias current resistor RBIAS (see Figure 11)
must be changed to yield either 1 mA (RBIAS
(RBIAS
range required. Additionally, reverse the connections to
TEC+ and TEC-.
1
1 1
CC
CP
+
ON
OFF
Tset LIMA LIMB
ILIM
ISET
+
+
J1 J2
J3
ExtTset Vset PDset
3
2
1
10
9
8
7
6
5
4
3
2
1
12
11
10
9
8
7
6
5
4
3
2
1
R
BIAS
R
35
+ ++++
Figure 11. Location of Sensor Bias Resistor (RBIAS).

© 2018 www.teamWavelength.com 15
LDTC2/2 LASER DIODE DRIVER AND TEMPERATURE CONTROLLER
CHANGING THE LASER DIODE OUTPUT
CURRENT RANGE
The output current range of the WLD3343 depends on
the selection of resistor RSENSE. Two 2520-sized resistors
combine in series to produce this total RSENSE resistance
(R14 & R15). See Figure 12 for their location.
RSENSE = R14 + R15
The LDTC2/2 defaults the maximum range to 2.2 A. To
change the range, and the sensitivity of the setpoint voltage,
use Table 5, Equation 7, or Equation 8, and install the
appropriate RSENSE resistance.
Table 5. Laser Diode Current Sense Resistor RSENSE vs.
Maximum Laser Diode Current ILDMAX
MAXIMUM OUTPUT
CURRENT
ILDMAX
CONSTANT
POWER
RSENSE
CONSTANT
CURRENT
RSENSE
50 mA
125 mA
250 mA
500 mA
1.25 Amps
2.2 Amps
Equation 7. Calculating RSENSE for Constant Power Mode.
RSENSE = 1.25
ILDMAX
Equation 8. Calculating RSENSE for Constant Current Mode.
RSENSE = 1.00
ILDMAX
Helpful hints for choosing RSENSE:
• SENSE.
• Avoid resistors with high parasitic inductance.
•
• Use Equation 9 for determining the power rating of
RSENSE.
Equation 9. Calculating the Power Rating for RSENSE.
RATING = 1.25 · (ILDMAX)2· RSENSE
1
J2
12
11
10
9
8
7
6
5
4
3
2
1
R SENSE = R14 + R15
R14
R15
Figure 12. Location of RSENSE

© 2018 www.teamWavelength.com 16
LDTC2/2 LASER DIODE DRIVER AND TEMPERATURE CONTROLLER
LASER DRIVER BLOCK DIAGRAM
SHD
1
VSET
2
IMON
3
PMON
4
MODE
5
LIM
6
GND
7RS+ 8
B9
RS- 10
A11
PD+ 12
PD- 13
VDD 14
U2
WLD3343
R15
0.20 2512 1.5W
R14
0.20 2512 1.5W
+1
-- 2
3
VR2
LM4040AIM3-2.5
IMON 2
1
3S1
GT11MCKE
PMON
VDD
D1
LED
Remote Enable
CW 3
W
2
CCW
1
R5
500
1
2
3
JP3
HEADER 3
Shown in CC
LDC
PDA
PDC
LDA
VDD
VDD
Ext Vset
LIM
S2
EG2211
R17
1.00K 1%
R7
1.00K
R19
1.00K
R18
150
R16
10K
2
3
1
411
U6A
5
6
7
411
U6B
9
10
8
411
U6C
13
12
14
411
U6D
R11
1.00K
R10
1.00K
R12
1.00K
R9
1.00K
R8
10K
1
2
3
JP2
HEADER 3
VDD
VDD
VDD
R13
1.00K
MOD
1
2
J4
Fan Power
VDD
VDD
1
2
3
4
5
6
7
8
9
10
J3
CON10
VDD
Common
Common
TEC+
TEC-
Sensor+
TEC+
TEC-
Sensor+
Sensor-
CW 3
W2
CCW
1
R6
5K
+
C15
4.7UF 16V
C18
0.1UF
C16
0.1UF 50V
+
C14
4.7UF 16V
C7
0.1UF 50V
OFF
ON
ISET
PDMON
R42 1.00M
R41
1.00M
R40
1.00M
R39
1.00M
R21
4.99K
R20
499
VDD
Figure 13. Block Diagram for WLD3343 Connections

© 2018 www.teamWavelength.com 17
LDTC2/2 LASER DIODE DRIVER AND TEMPERATURE CONTROLLER
TEMPERATURE CONTROLLER BLOCK DIAGRAM
VDD
1
VSET
2
LIMA
3
LIMB
4
P
5
+1V
6
I
7SG 8
S+ 9
BIAS 10
OUTA 11
OUTB 12
GND 13
VS 14
U1
WTC3243
+1
-- 2
3
VR1
LM4040AIM3-2.5
VDD
Set T
ACT T
CW 3
W
2
CCW
1
R3
5K
CW 3
W2
CCW
1
R4
5K
VDD
VDD
VDD
LIMA LIMB
VDD
VS
VDD VS
100uA
VDD
VS
VCC
D2 power
R24
1.00K
R25
1.00K 1%
R34
1.00K
R29
1.5K
R28
1.5K
VIN
2
GND
3
3.3V 1
U8
LM3480IM3-3.3
VCC
Vset/DAC
VDD
VDD
VDD
VCC
VCC
VCC
R35
20.0K
1
2
3
4
5
6
7
8
9
10
11
12
J2
CON12
ACT T
SET T GND
ACT T
SET T
Common
Common
TEC+
TEC-
Sensor+
R33
10.0K
R32
100K
1
2
3
J1
CON3
VDD
PMON
IMON
Ext Vset
Remote Enable
PMON
IMON
Ext Vset
Rem En
Common
PD MON
Common
NO 6
COM 5
NC 4
IN
1
V+
2
GND
3
U7
ISL84544
R1
1.00K 1%
74
3
2
6
+
_ U3
OP777AR
2
3
1
84
U5A
OP727ARU OS
5
6
7
84
U5B
OP727ARU OS
1
2
3
JP1
HEADER 3
R36
348K 1%
R26
10.0K
R27
4.99K
CW 3
W2
CCW
1
R2
5K
+
C5
68UF 16V
+
C2
4.7UF 50V
+
C1
4.7UF 16V
+
C8
4.7UF 50V
+
C9
4.7UF 50V
C11
0.1UF 50V
C10
0.1UF 50V
C6
0.1UF
C12
0.1UF 50V C13
0.1UF 50V
C3
0.1UF
C4
0.1UF
R30
24.9K
R31
31.6K
R23
150
2
3
1
84
U4A
OP727ARU
5
6
7
84
U4B
OP727ARU
C17
0.1UF
TSET
R37
1.00K
C19
0.1UF
R38
1.00M
PDMON
Rbias
VDD
VDD
* PIN 1 & 2 NOT AVAILABLE ON Rev. A
Figure 14. Block Diagram for WTC3243 Connections

© 2018 www.teamWavelength.com 18
LDTC2/2 LASER DIODE DRIVER AND TEMPERATURE CONTROLLER
SAFE OPERATING AREA CALCULATION
To determine if the LDTC controller is suitable for your
application and if it will be operating in the safe range,
consult the instructions for calculating the Safe Operating
Area online at:
Laser Diode Drivers:
www.teamwavelength.com/support/design-tools/soa-ld-calculator/
Temperature Controllers:
www.teamwavelength.com/support/design-tools/soa-tc-calculator/
If you have any questions about the Safe Operating Area
calculator, call the factory for free and prompt technical
assistance.
!
LOADS.
We recommend using the online SOA calculators rather than
the charts provided here. The online calculators take into
Follow these steps to use the SOA Chart to determine if the
LDTC will be operating safely. SOA charts for the LDTC2/2
Series are shown in Figure 15 and Figure 16.
• Determine the VDD supply voltage for the laser driver.
•
(VMAX) and current (IMAX
• Calculate the voltage drop across the controller:
VDROP = VDD – VMAX
• Mark VDROP on the X-axis, and extend a line upward.
• Mark IMAX on the Y-axis, and extend a line to the right
until it intersects the VDROP line.
• On the X-axis, mark the supply voltage (VDD).
• Extend a diagonal line from VDD to the intersection of the
VDROP and IMAX lines; this is the Load Line.
• If the Load Line crosses the Safe Operating Area line at
If the SOA calculator indicates the LDTC will be outside of the
Safe Operating Area, the system must be changed so that
less power is dissipated within the driver. See Application
Note AN-LDTC01: The Principle of the Safe Operating Area
for information on shifting the Load Line.
After changing any of the parameters, recalculate the SOA
to make sure the controller will operate safely. If you have
Wavelength Electronics for assistance.
The SOA chart must be examined for both the laser driver
and for the temperature controller.
12108642
2.2
2.0
1.8
1.6
1.4
1.2
1.0
0.8
0.6
0.4
0.2
0
0
Voltage Across LDTC2/2 (V)
Current (A)
Figure 15. Laser Driver SOA Chart, LDTC2/2.
With heatsink and fan.
2520151050
2.2
2.0
1.8
1.6
1.4
1.2
1.0
0.8
0.6
0.4
0.2
0
Voltage Across LDTC2/2 (V)
Current (A)
Figure 16. Temperature Controller SOA Chart, LDTC2/2.
With heatsink and fan.

© 2018 www.teamWavelength.com 19
LDTC2/2 LASER DIODE DRIVER AND TEMPERATURE CONTROLLER
TROUBLESHOOTING –
TEMPERATURE CONTROLLER
PROBLEM POTENTIAL CAUSES SOLUTIONS
Temperature is decreasing
when it should be increasing.
–OR–
Temperature is increasing when
it should be decreasing.
The TEC may be connected
backwards to the LDTC.
The convention is that the red wire on the TEC module connects to
TEC+ (pin 6) and the black wire to TEC- (pin 5). If your TEC is connected in
this manner and the problem persists, the TEC module itself may be wired in
and then try again to operate the system.
TEC wiring polarity is dependent on temperature sensor type (NTC vs. PTC).
Verify that the polarity is correct for the sensor type you are using (Table 4).
Temperature increases beyond
the setpoint and will not come
down.
The heatsink may be inadequately
sized to dissipate the heat from the
load and TEC module, and now
the system is in a condition called
thermal runaway.
Increase the size of the heatsink, add a fan to blow air over the heatsink,
and/or reduce the ambient air temperature around the heatsink.
Apply a thin layer of thermal paste or use thermal washers between the load,
the TEC surfaces, and the heatsink.
The TEC is not adequately sized for
the thermal load.
The heat being generated by the load may be too great for the TEC to pump
to the heatsink; a larger TEC may be needed. Consult our technical note
TN-TC01: Optimizing Thermoelectric Temperature Control Systems at
www.teamwavelength.com/download/applicationtechnotes/tn-tc01.pdf
The temperature of my heater-
based system increases without
stopping.
The current limits might not be
When using a heater the current limit trimpots LIM A and LIM B must be
set according to the temperature sensor type you are using. If the load
temperature increases past the setpoint and continues to increase, one of
the current limit trimpots may have been improperly set. Refer to Table 3 and
for more
information.
Temperature does not stabilize
very well at the setpoint.
Poor thermal contact between
components of the thermal load.
Use thermal paste or washers between the load/TEC and TEC/heatsink
interfaces. Make sure the temperature sensor is in good thermal contact with
the load.
Operating outside of the ideal
region of the temperature sensor.
The sensor type and bias current should be selected to maximize sensitivity at
the target temperature. Thermistors provide the best performance, particularly
for applications where a single setpoint temperature must be accurately
Proportional control term is set too
high.
Reduce the value of the proportional term. For more information, contact the
factory.
Temperature does not reach the
setpoint.
TEC or Heater.
or heater.
The controller does not have
drive the TEC or heater.
Increase the power supply voltage; be certain to verify that the controller is
within the Safe Operating Area; the SOA calculator is found at:
www.teamwavelength.com/support/design-tools/soa-tc-calculator/
LDTC does not respond to
external temperature setpoint
input.
The EXT T SET signal is below the
minimum signal value of 0.3 V.
If the R TC SET signal falls below 0.3 V, the LDTC defaults to a “safe
setpoint voltage can be changed at the factory if your application requires it.
To reset the safety circuit, the R TC SET signal must be greater than 0.4 V.
Temperature is slow to
stabilize and is not within the
Setpoint temperature is set close to
the ambient temperature.
heater. A resistive heater is unable to precisely maintain temperature near
ambient because once the temperature overshoots the setpoint, the controller
thermoelectric cooler, which can alternately heat and cool the load to maintain
a more precise setpoint temperature.
Setpoint is 1 V even when the
Tset trimpot is fully OFF.
Failsafe circuit has been activated
due to low setpoint.
Increase the temperature setpoint to a value above 0.3 V. Once the Tset
value becomes greater than 0.3 V, the failsafe circuit will be disabled and the
setpoint will be at the set value.

© 2018 www.teamWavelength.com 20
LDTC2/2 LASER DIODE DRIVER AND TEMPERATURE CONTROLLER
TROUBLESHOOTING –
LASER DRIVER
PROBLEM POTENTIAL CAUSES SOLUTIONS
Driver will not switch on. Carefully check the wiring diagram on page 2. Make sure the power
supply polarity is not reversed.
Output will not enable.
on the LDTC.
onboard LD Enable toggle switch must be set to ON (enable). Make sure
this switch is properly set.
Remote Enable signal is not correct.
Input a 3 to 5 V signal to disable the output.
Laser output power too low in
Constant Current mode.
Laser current setpoint too low. Increase the setpoint either by adjusting the I SET trimpot counter-
clockwise, or by increasing the signal voltage on the R LD SET input
(Pin 5 on Connector J2).
Laser current limit too low. Refer to page 12 for instructions on setting the laser driver current limit.
Laser driver is compliance limited.
(VF). Make sure that the LDTC2/2 is not compliance limited. Refer to the
page 6. If the driver is compliance
limited, VDD may need to be increased. Verify that the LDTC2/2 will be
operating within the Safe Operating Area if VDD is increased.
Laser does not reach desired
output in Constant Power mode.
Laser current limit too low. Check the laser diode datasheet to determine the approximate laser
drive current at the desired optical power output level. Then verify that
the current limit is set slightly higher than that. Refer to page 12 for
instructions on setting the laser driver current limit. Do not exceed the
maximum current for the laser diode.
Photodiode feedback current is out
of range for the LDTC.
Refer to the laser diode datasheet to determine the approximate
photodiode (PD) current at the desired output power level. If the PD
current exceeds the LDTC PD current range, the LDTC will require
assistance.
This manual suits for next models
1
Table of contents
Other Wavelength Electronics Temperature Controllers manuals
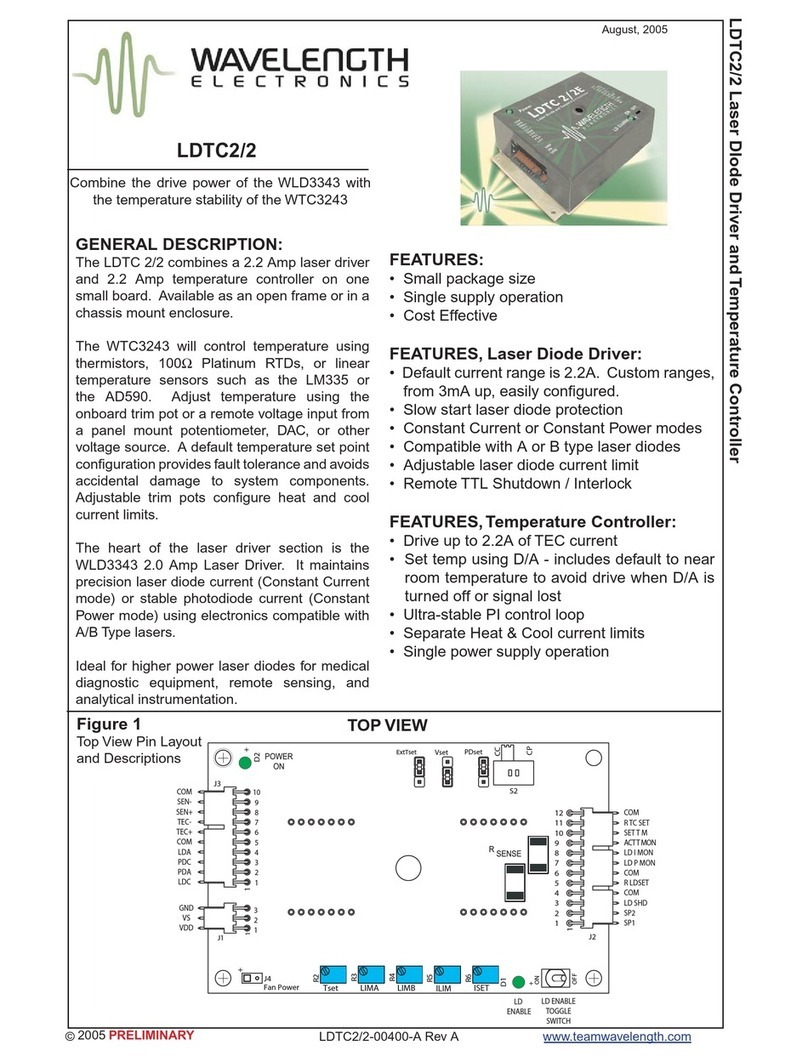
Wavelength Electronics
Wavelength Electronics LDTC2/2 User manual
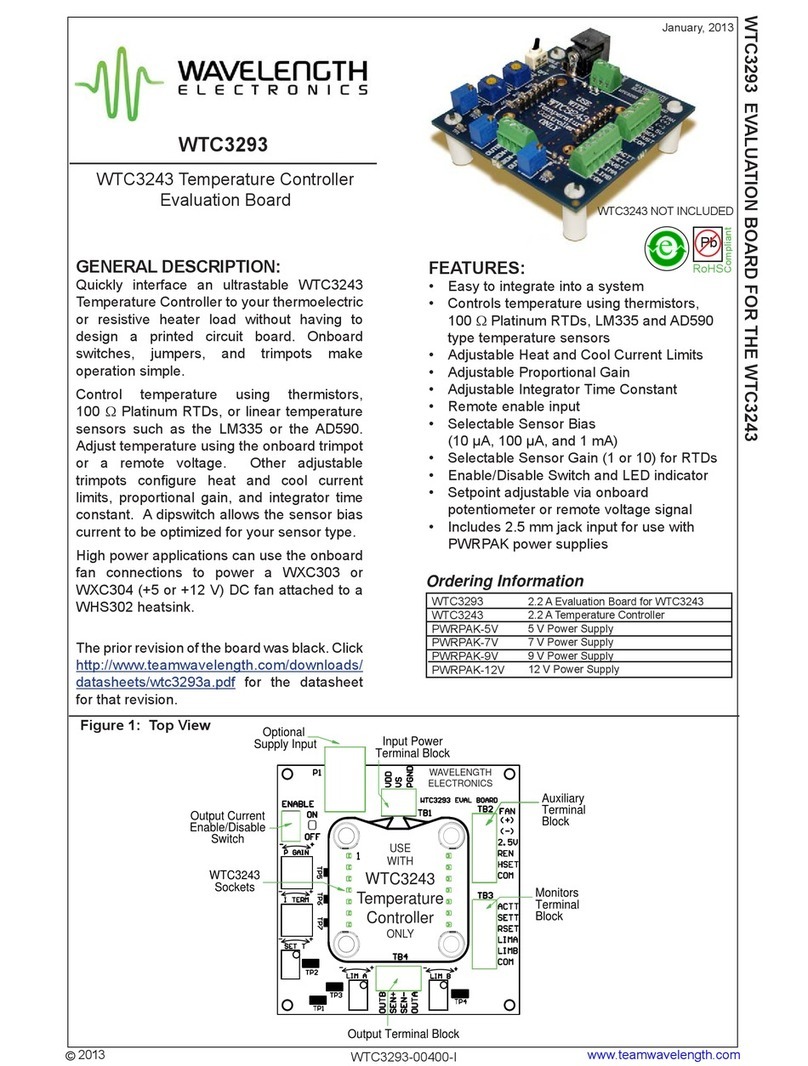
Wavelength Electronics
Wavelength Electronics WTC3293 User manual
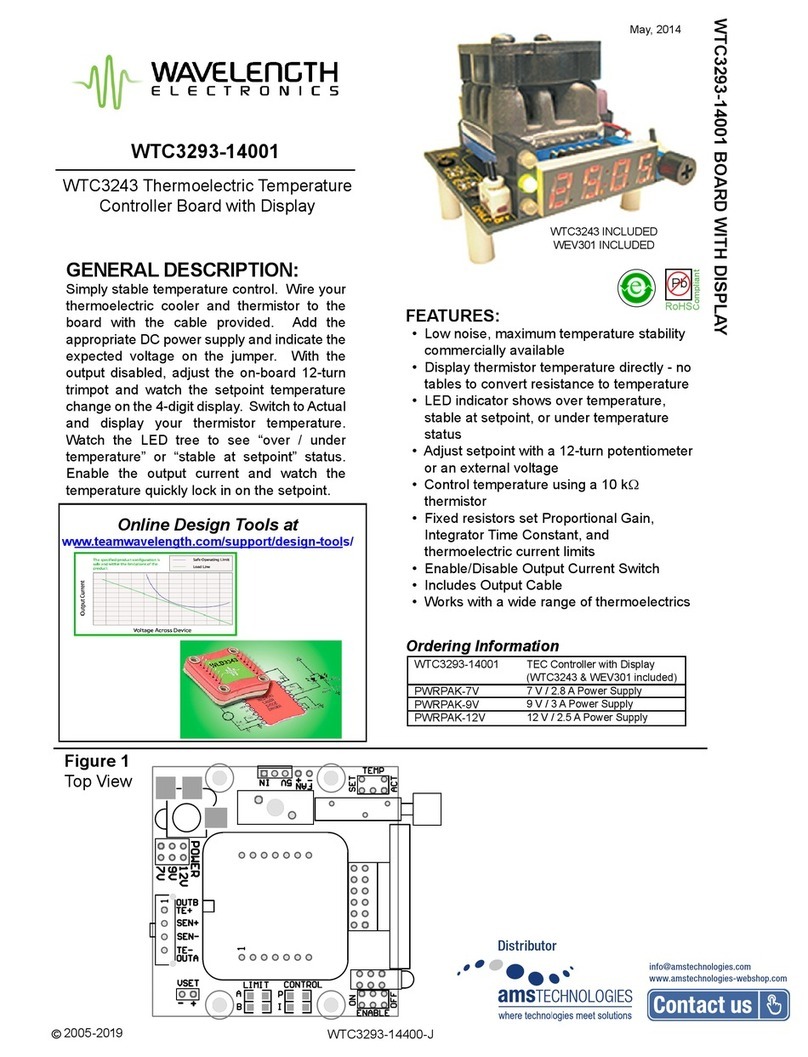
Wavelength Electronics
Wavelength Electronics WTC3293-14001 User manual
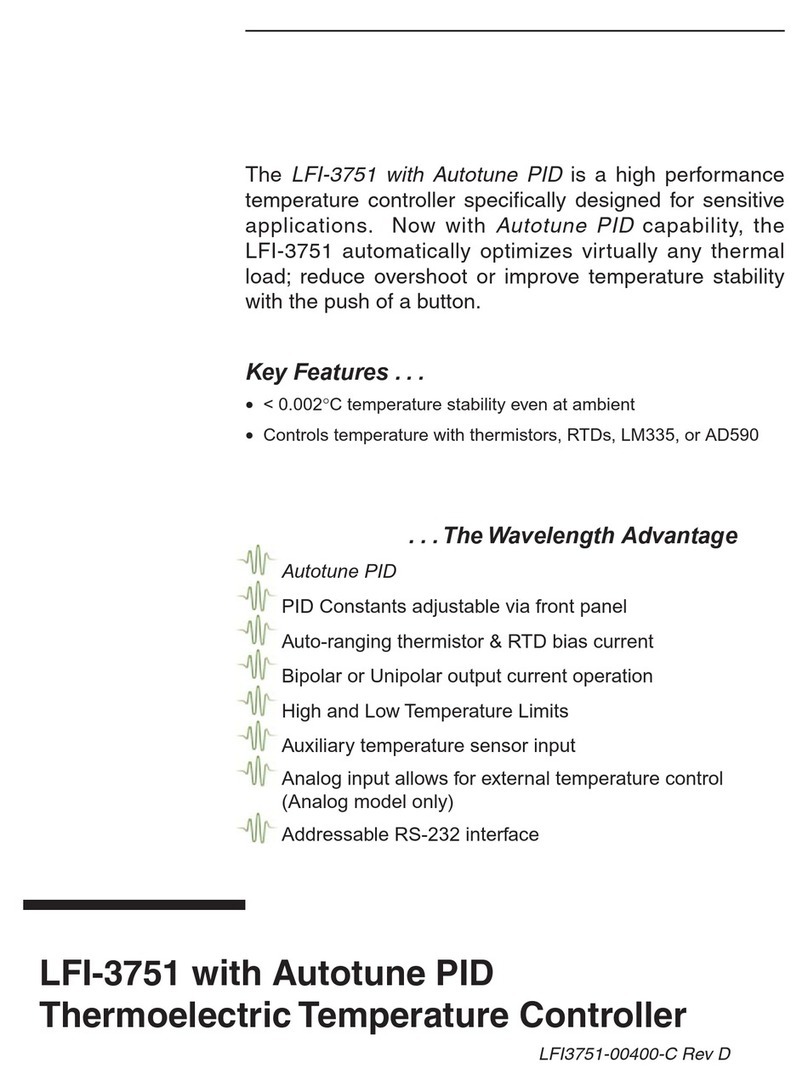
Wavelength Electronics
Wavelength Electronics LFI-3751 User manual
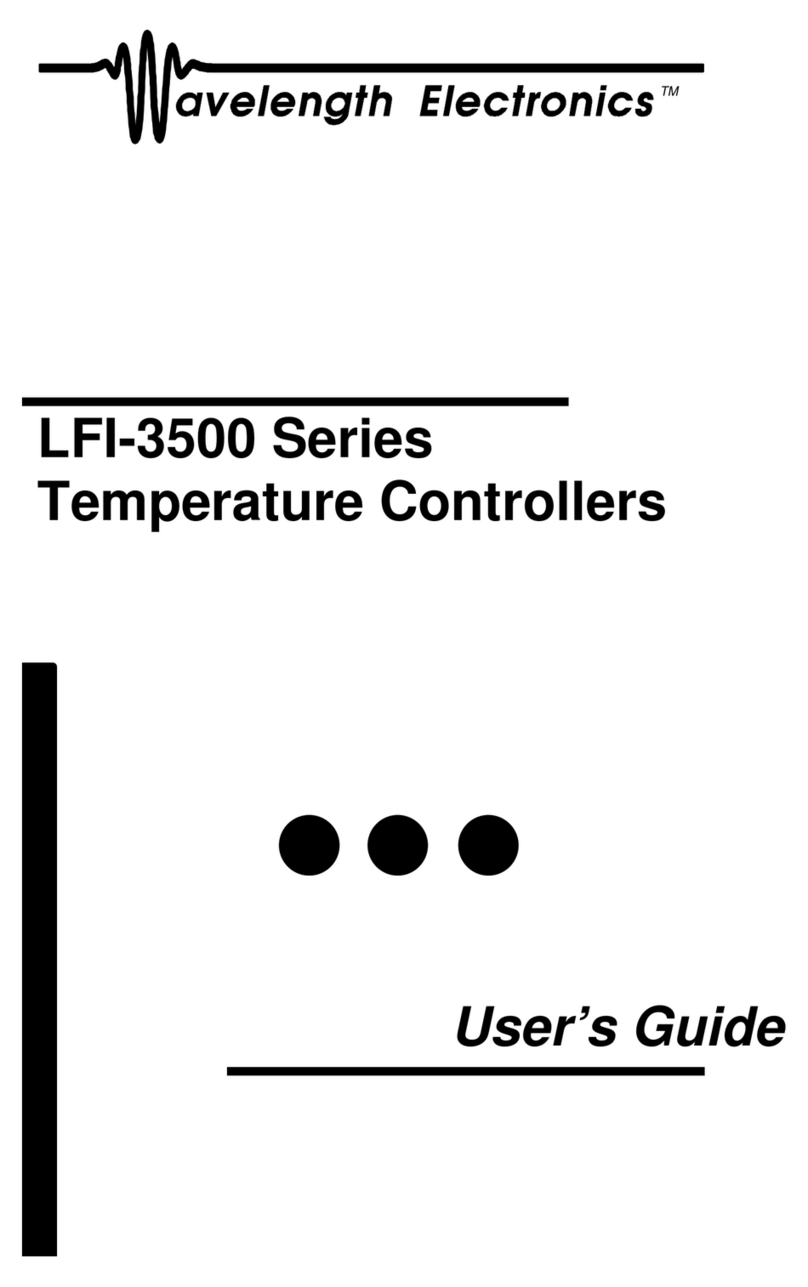
Wavelength Electronics
Wavelength Electronics LFI-3500 Series User manual