ABB IRC5 Compact User guide

ROBOTICS
Safety manual for robot
Manipulator and IRC5 or OmniCore
controller

Trace back information:
Workspace 20B version a7
Checked in 2020-05-07
Skribenta version 5.3.033

Safety manual for robot
Manipulator and IRC5 or OmniCore controller
IRC5 & OmniCore
Document ID: 3HAC031045-001
Revision: Q
© Copyright 2008-2020 ABB. All rights reserved.
Specifications subject to change without notice.

The information in this manual is subject to change without notice and should not
be construed as a commitment by ABB. ABB assumes no responsibility for any errors
that may appear in this manual.
Except as may be expressly stated anywhere in this manual, nothing herein shall be
construed as any kind of guarantee or warranty by ABB for losses, damage to persons
or property, fitness for a specific purpose or the like.
In no event shall ABB be liable for incidental or consequential damages arising from
use of this manual and products described herein.
This manual and parts thereof must not be reproduced or copied without ABB's
written permission.
Keep for future reference.
Additional copies of this manual may be obtained from ABB.
Original instructions.
© Copyright 2008-2020 ABB. All rights reserved.
Specifications subject to change without notice.

Table of contents
7Overview of this manual ...................................................................................................................
91 Safety information
91.1 Limitation of liability ...........................................................................................
101.2 Requirements on personnel ................................................................................
112 Safety signals and symbols
112.1 Safety signals in the manual ................................................................................
133 Robot stopping functions
133.1 Protective stop and emergency stop .....................................................................
153.2 About emergency stops ......................................................................................
163.3 Enabling device and hold-to-run functionality .........................................................
174 Robot operating modes
174.1 About the manual mode .....................................................................................
184.2 About the automatic mode ..................................................................................
195 Installation and commissioning
216 Operation
237 Maintenance and repair
237.1 Maintenance and repair ......................................................................................
267.2 Emergency release of the robot axes ....................................................................
278 Troubleshooting
299 Decommissioning
31Index
Safety manual for robot - Manipulator and IRC5 or OmniCore controller 5
3HAC031045-001 Revision: Q
© Copyright 2008-2020 ABB. All rights reserved.
Table of contents

This page is intentionally left blank

Overview of this manual
About this manual
This manual contains safety information for the robot controllers and the
manipulators from ABB Robotics. The information applies to robot, that is, a
combination of manipulator and controller, IRC5 or OmniCore. Any deviations are
listed in the Declaration by Manufacturer and further detailed in the product
manuals.
References
The documents that are listed below describe the robot in detail, including assembly,
service, and safety instructions. All documents can be found via myABB Business
Portal, www.myportal.abb.com.
Document IDReference
3HAC027098-001Operating manual - Emergency safety information
Declaration by Manufacturer
This document is delivered together with the robot.
Product manual for the robot controller
Product manual for the manipulator
Operating manual for the robot
Revisions
DescriptionRevision
First revision.-
Changes/corrections are made for the IRC5 controller.A
Changes/corrections are made for the IRC5 controller.B
Changes/corrections are made for the IRC5 controller.C
Minor corrections.D
Minor corrections.E
Minor corrections.F
Added information about batteries.G
The manual is updated with the new main computer (DSQC1000).H
Changes/corrections are made for the IRC5 controller.J
Added information about robots for collaborative applications.K
Release 17.1.L
Changes/corrections are made for the IRC5 controller.
Release 17.2.M
Minor corrections.
Release 18.1.N
The content in the manual is partly restructured.
Continues on next page
Safety manual for robot - Manipulator and IRC5 or OmniCore controller 7
3HAC031045-001 Revision: Q
© Copyright 2008-2020 ABB. All rights reserved.
Overview of this manual

DescriptionRevision
Release 20A.
•The title is changed from Operating manual - General safety information.
• Added OmniCore robot controller.
• The content in the manual is restructured.
P
Release 20B.
• Added warning regarding unexpected movement of robot arm to con-
cerned chapters.
Q
8 Safety manual for robot - Manipulator and IRC5 or OmniCore controller
3HAC031045-001 Revision: Q
© Copyright 2008-2020 ABB. All rights reserved.
Overview of this manual
Continued

1 Safety information
1.1 Limitation of liability
Limitation of liability
Any information given in this manual regarding safety must not be construed as a
warranty by ABB that the industrial robot will not cause injury or damage even if
all safety instructions are complied with.
The information does not cover how to design, install and operate a robot system,
nor does it cover all peripheral equipment that can influence the safety of the robot
system.
In particular, liability cannot be accepted if injury or damage has been caused for
any of the following reasons:
• Use of the robot in other ways than intended.
• Incorrect operation or maintenance.
• Operation of the robot when the safety devices are defective, not in their
intended location or in any other way not working.
• When instructions for operation and maintenance are not followed.
• Non-authorized design modifications of the robot.
• Repairs on the robot and its spare parts carried out by in-experienced or
non-qualified personnel.
• Foreign objects.
• Force majeure.
Spare parts and equipment
ABB supplies original spare parts and equipment which have been tested and
approved. The installation and/or use of non-original spare parts and equipment
can negatively affect the safety, function, performance, and structural properties
of the robot. ABB is not liable for damages caused by the use of non-original spare
parts and equipment.
Safety manual for robot - Manipulator and IRC5 or OmniCore controller 9
3HAC031045-001 Revision: Q
© Copyright 2008-2020 ABB. All rights reserved.
1 Safety information
1.1 Limitation of liability

1.2 Requirements on personnel
General
Only personnel with appropriate training are allowed to install, maintain, service,
repair, and use the robot. This includes electrical, mechanical, hydraulics,
pneumatics, and other hazards identified in the risk assessment.
Persons who are under the influence of alcohol, drugs or any other intoxicating
substances are not allowed to install, maintain, service, repair, or use the robot.
The plant liable must make sure that the personnel is trained on the robot, and on
responding to emergency or abnormal situations.
Personal protective equipment
Use personal protective equipment, as stated in the product manual.
10 Safety manual for robot - Manipulator and IRC5 or OmniCore controller
3HAC031045-001 Revision: Q
© Copyright 2008-2020 ABB. All rights reserved.
1 Safety information
1.2 Requirements on personnel

2 Safety signals and symbols
2.1 Safety signals in the manual
Introduction to safety signals
This section specifies all safety signals used in the user manuals. Each signal
consists of:
• A caption specifying the hazard level (DANGER, WARNING, or CAUTION)
and the type of hazard.
• Instruction about how to reduce the hazard to an acceptable level.
• A brief description of remaining hazards, if not adequately reduced.
Hazard levels
The table below defines the captions specifying the hazard levels used throughout
this manual.
For more information, see standard ISO 13849.
SignificanceDesignationSymbol
Signal word used to indicate an imminently hazard-
ous situation which, if not avoided, will result in ser-
ious injury.
DANGER
Signal word used to indicate a potentially hazardous
situation which, if not avoided, could result in serious
injury.
WARNING
Signal word used to indicate a potentially hazardous
situation related to electrical hazards which, if not
avoided, could result in serious injury.
ELECTRICAL
SHOCK
Signal word used to indicate a potentially hazardous
situation which, if not avoided, could result in slight
injury.
CAUTION
Signal word used to indicate a potentially hazardous
situation which, if not avoided, could result in severe
damage to the product.
ELECTROSTATIC
DISCHARGE (ESD)
Signal word used to indicate important facts and
conditions.
NOTE
Safety manual for robot - Manipulator and IRC5 or OmniCore controller 11
3HAC031045-001 Revision: Q
© Copyright 2008-2020 ABB. All rights reserved.
2 Safety signals and symbols
2.1 Safety signals in the manual

This page is intentionally left blank

3 Robot stopping functions
3.1 Protective stop and emergency stop
Robot stopping functions
The robot has an emergency stop function and at least one protective stop function.
These functions have provision for the connection of external emergency stops
and protective devices.
The emergency stop function is a complementary protective measure and shall
not be applied as a substitute for safeguarding measures or safety functions.
The stop categories can be re-configured as defined by standards EN ISO
10218-1:2011 and IEC 60204-1:2016.
Emergency stop and protective stop functions are activated through dedicated
safety inputs or safety protocols.
For example, an output from a safety rated presence sensing device output can
be connected to a safety input on the robot controller. This is to initiate a protective
stop of the robot.
Stop categories
As defined in IEC 60204-1, stopping by immediate removal of
power to the machine actuators.
Stop category 0
As defined in IEC 60204-1, a controlled stop with power avail-
able to the machine actuators to achieve the stop and then re-
moval of power when the stop is achieved.
Stop category 1
As defined in IEC 60204-1, a controlled stop with power remain-
ing available to the machine actuators.
Stop category 2
(Only available for certain manipulators with OmniCore, see
the product manual for the manipulator.)
Safety inputs to initiate a protective stop or an emergency stop
Protective stop and emergency stop inputs will initiate a stop, selectable of category
0 or category 1.
DescriptionSafety inputs to initiate a
stop
The Emergency Stop is operational in both automatic and
manual mode.
Emergency stop (ES)
The default configuration is stop category 0. For deviations,
see the product manual for the manipulator.
The safety input Automatic Stop is only operational in automatic
mode.
Automatic stop (AS)
The default configuration is stop category 1.
The safety input General Stop is operational in both manual
mode and automatic mode.
General stop (GS)
The default configuration is stop category 1.
Continues on next page
Safety manual for robot - Manipulator and IRC5 or OmniCore controller 13
3HAC031045-001 Revision: Q
© Copyright 2008-2020 ABB. All rights reserved.
3 Robot stopping functions
3.1 Protective stop and emergency stop

DescriptionSafety inputs to initiate a
stop
The safety input Superior Stop is operational in both manual
mode and automatic mode.
Superior stop (SS)
The default configuration is stop category 1.
(Superior stop is only available for IRC5.)
Note
For IRC5, a safety input on the panel board that is initiated, must remain active
for at least 1.5 s.
Note
For OmniCore, a safety input that is initiated must remain active for at least 100
ms.
The stop category configuration is detailed in the product manual for the controller.
14 Safety manual for robot - Manipulator and IRC5 or OmniCore controller
3HAC031045-001 Revision: Q
© Copyright 2008-2020 ABB. All rights reserved.
3 Robot stopping functions
3.1 Protective stop and emergency stop
Continued

3.2 About emergency stops
The emergency stops
The purpose of the emergency stop function is to avert actual or impending
emergency situations arising from the behavior of persons or from an unexpected
hazardous event.
The emergency stop function is to be initiated by a single human action.
The emergency stop function is a complementary protective measure and shall
not be applied as a substitute for safeguarding measures and other functions or
safety functions.
The effect of an activated emergency stop device is sustained until the actuator
of the emergency stop device has been disengaged. This disengagement is only
possible by an intentional human action on the device where the command has
been initiated. The disengagement of the device shall not restart the machinery
but only permit restarting.
After actuation and before disengaging the emergency stop device, the machinery
shall be inspected in order to detect the reason for actuation.
Safety manual for robot - Manipulator and IRC5 or OmniCore controller 15
3HAC031045-001 Revision: Q
© Copyright 2008-2020 ABB. All rights reserved.
3 Robot stopping functions
3.2 About emergency stops

3.3 Enabling device and hold-to-run functionality
Three-position enabling device
CAUTION
The person using the three-position enabling device is responsible to observe
the safeguarded area for hazards due to robot motion and any other hazards
controlled by the robot.
The three-position enabling device is a manually operated, constant pressure
push-button which, when in center-enabled position, allows potentially hazardous
functions.
The three-position enabling device will when continuously held in center-enabled
position permit robot motion and any hazards controlled by the robot. Release of
or compression past the center-enabled position will stop the hazard, for example,
robot motion.
CAUTION
For safe use of the three-position enabling device, the following must be
implemented:
• The three-position enabling device must never be rendered inoperational
in any way.
•If there is a need to enter safeguarded space, always bring the three-position
enabling device. This is to enforce single point of control.
Hold-to-run function in manual full speed mode
The hold-to-run function for manual full speed allows movement in conjunction
with the three-position enabling device when the button connected to the function
is actuated manually. This hold-to-run function can only be used in manual full
speed mode. In case of hazard, release or compress the three-position enabling
device.
How to use the hold-to-run function for manual full speed mode is described in the
operating manual for the controller.
Note
The manual full speed mode is not available in all markets.
Deviations are listed in the product manual for the manipulator.
16 Safety manual for robot - Manipulator and IRC5 or OmniCore controller
3HAC031045-001 Revision: Q
© Copyright 2008-2020 ABB. All rights reserved.
3 Robot stopping functions
3.3 Enabling device and hold-to-run functionality

4 Robot operating modes
4.1 About the manual mode
The manual mode
Manual mode is a control state that allows for the direct control by an operator.
The operator will through positioning the three-position enabling switch to the
center-position allow for movement of the manipulator.
There are two manual modes:
• Manual reduced speed mode
• Manual high speed mode (optional)
Safeguard mechanisms
• Protective stops through
- Three-position enabling switch
- General Stop, GS
Deviations are listed in the product manual for the controller.
Safety manual for robot - Manipulator and IRC5 or OmniCore controller 17
3HAC031045-001 Revision: Q
© Copyright 2008-2020 ABB. All rights reserved.
4 Robot operating modes
4.1 About the manual mode

4.2 About the automatic mode
The automatic mode
Automatic mode is an operating mode in which the robot control system operates
in accordance with the task program(s) and therefore not in direct control by an
operator.
Safeguard mechanisms
• Protective stop through
- Automatic Stop, AS
- General Stop, GS
- Superior Stop, SS (not available for OmniCore)
Deviations are listed in the product manual for the controller.
18 Safety manual for robot - Manipulator and IRC5 or OmniCore controller
3HAC031045-001 Revision: Q
© Copyright 2008-2020 ABB. All rights reserved.
4 Robot operating modes
4.2 About the automatic mode

5 Installation and commissioning
National or regional regulations
The integrator of the robot system is responsible for the safety of the robot system.
The integrator is responsible that the robot system is designed and installed in
accordance with the safety requirements set forth in the applicable national and
regional standards and regulations.
The integrator of the robot system is required to perform an assessment of the
hazards and risks.
Layout
The robot integrated to a robot system shall be designed to allow safe access to
all areas during installation, operation, maintenance, and repair.
If robot movement can be initiated from an external control panel then an emergency
stop must also be available.
If the manipulator is delivered with mechanical stops, these can be used for reducing
the working area.
A perimeter safeguarding, for example a fence, shall be dimensioned to withstand
the following:
• The force of the manipulator.
•The force of the load handled by the robot if dropped or released at maximum
speed.
• The maximum possible impact caused by a breaking or malfunctioning
rotating tool or other device fitted to the robot.
The maximum TCP speed and the maximum velocity of the robot axes are detailed
in the section Robot motion in the product specification for the respective
manipulator.
Consider exposure to hazards, such as slipping, tripping, and falling.
Consider hazards from other equipment in the robot system, for example, that
guards remain active until identified hazards are reduced to an acceptable level.
Allergenic material
See the respective product manual for specification of allergenic materials in the
product, if any.
Securing the robot to the foundation
The robot must be properly fixed to its foundation/support, as described in the
product manual.
When the robot is installed at a height, hanging, or other than mounted directly on
the floor, there will be additional hazards.
Electrical safety
The mains power must be installed to fulfill national regulations.
Continues on next page
Safety manual for robot - Manipulator and IRC5 or OmniCore controller 19
3HAC031045-001 Revision: Q
© Copyright 2008-2020 ABB. All rights reserved.
5 Installation and commissioning

The power supply wiring to the robot must be sufficiently fused and if necessary,
it must be possible to disconnect it manually from the mains power.
The power to the robot must be turned off with the main switch and the mains
power disconnected when performing work inside the controller cabinet. Lock and
tag shall be considered.
Harnesses between controller and manipulator shall be fixed and protected to
avoid tripping and wear.
Note
Use a CARBON DIOXIDE (CO2) extinguisher in the event of a fire in the robot.
Safety devices
The integrator is responsible for that the safety devices necessary to protect people
working with the robot system are designed and installed correctly.
When integrating the robot with external devices to a robot system:
•The integrator of the robot system must ensure that emergency stop functions
are interlocked in accordance with applicable standards.
• The integrator of the robot system must ensure that safety functions are
interlocked in accordance with applicable standards.
Other hazards
WARNING
Never stay beneath a robot arm. Gravity and the release of braking devices can
create additional hazards.
A robot may perform unexpected limited movement.
WARNING
Manipulator movements can cause serious injuries on users and may damage
equipment.
The risk assessment should also consider other hazards, such as, but not limited
to:
• Water
• Compressed air
• Hydraulics
Verify the safety functions
Before the robot system is put into operation, verify that the safety functions are
working as intended and that any remaining hazards identified in the risk
assessment are mitigated to an acceptable level.
20 Safety manual for robot - Manipulator and IRC5 or OmniCore controller
3HAC031045-001 Revision: Q
© Copyright 2008-2020 ABB. All rights reserved.
5 Installation and commissioning
Continued
Other manuals for IRC5 Compact
17
This manual suits for next models
1
Table of contents
Other ABB Robotics manuals
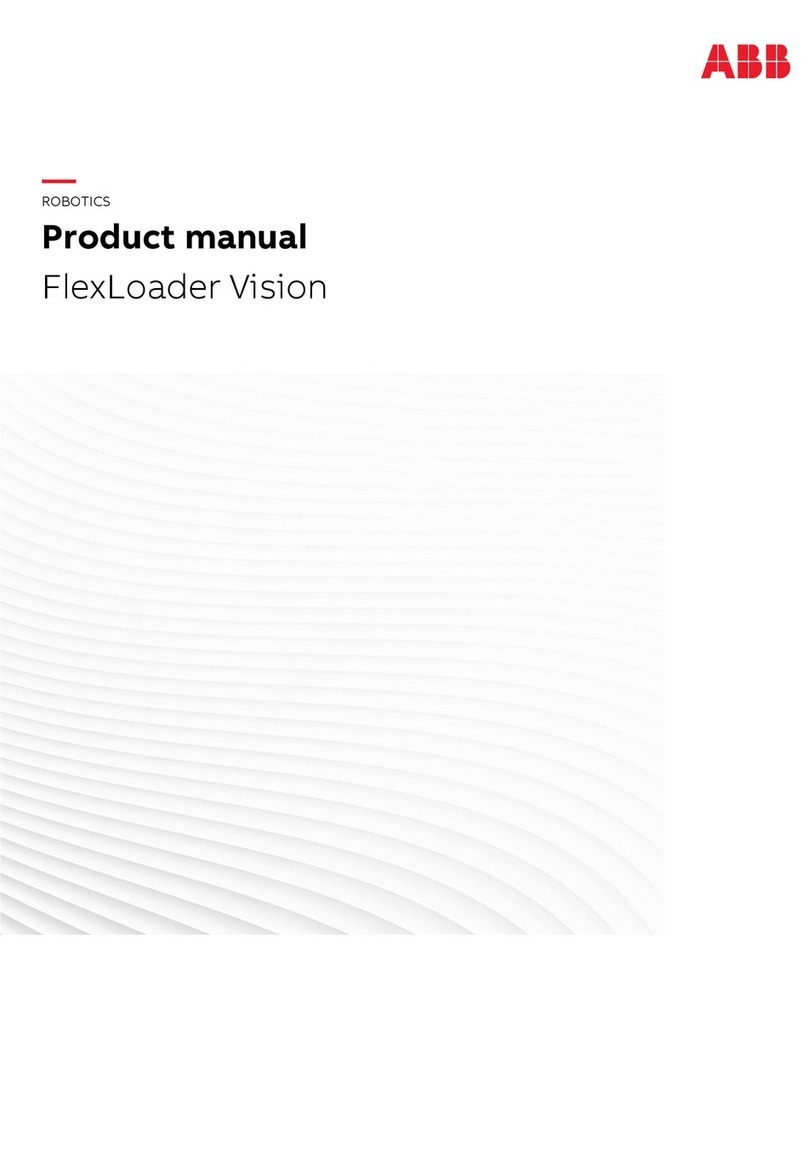
ABB
ABB FlexLoader Vision User manual
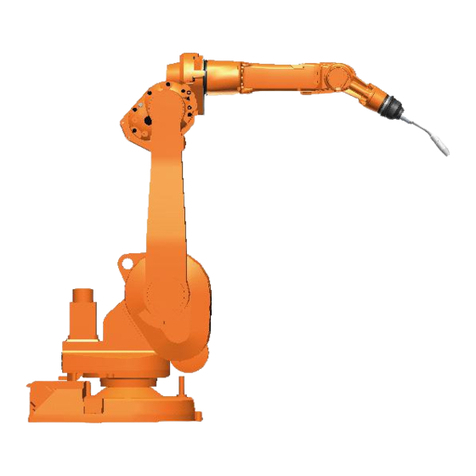
ABB
ABB IRBP User manual
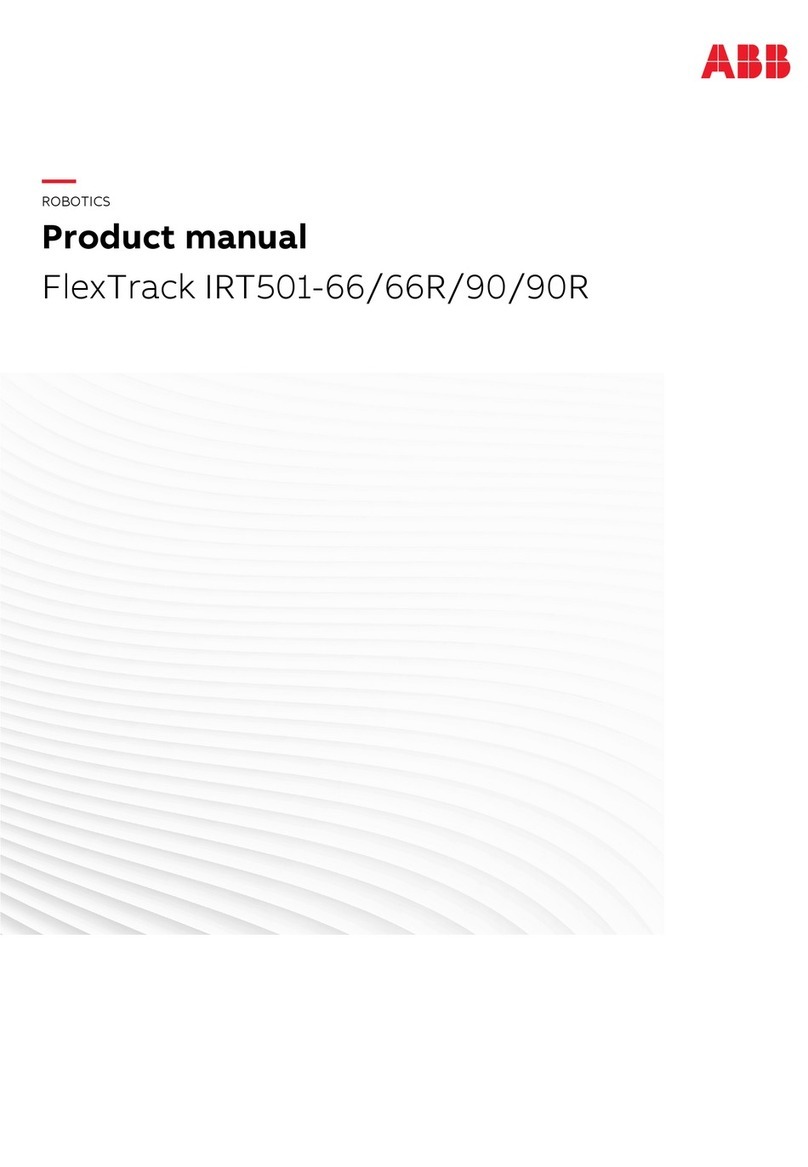
ABB
ABB FlexTrack IRT501 Series User manual
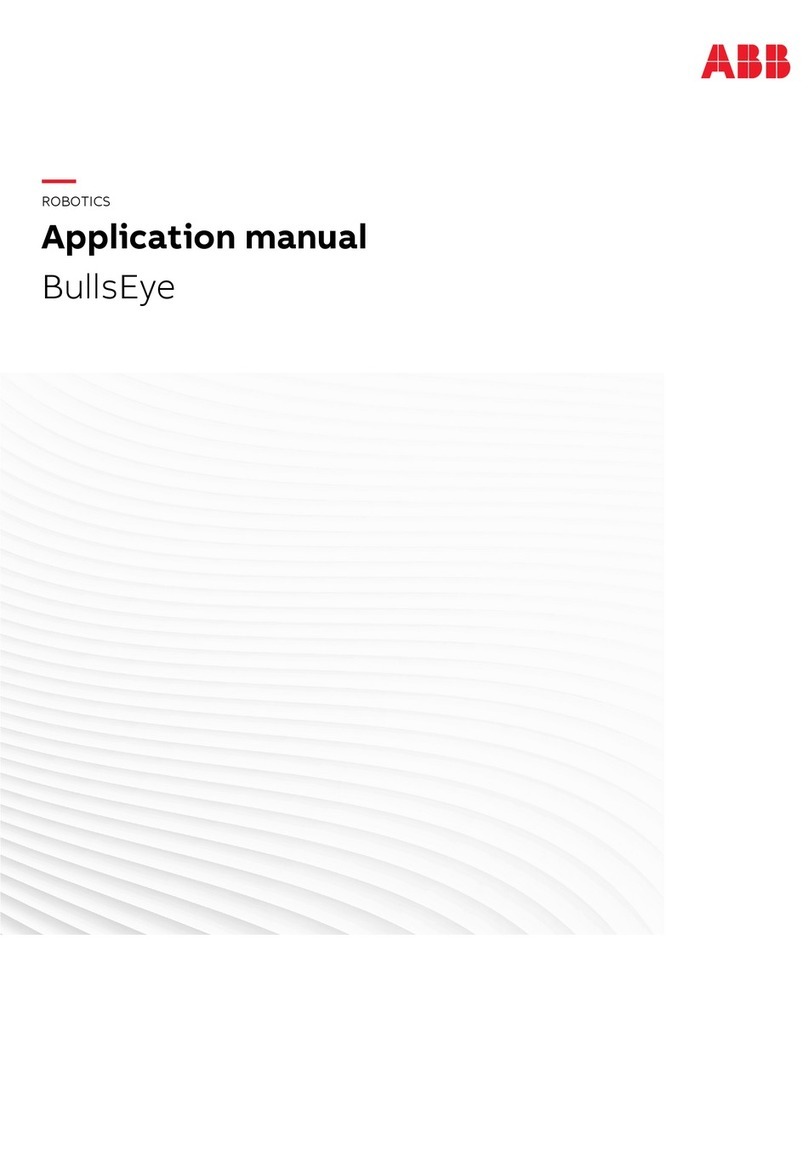
ABB
ABB BullsEye Instructions for use
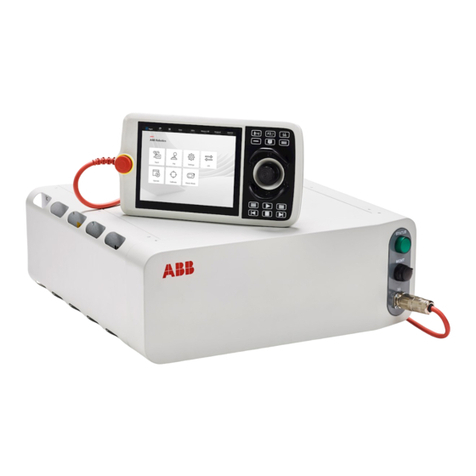
ABB
ABB OmniCore User manual
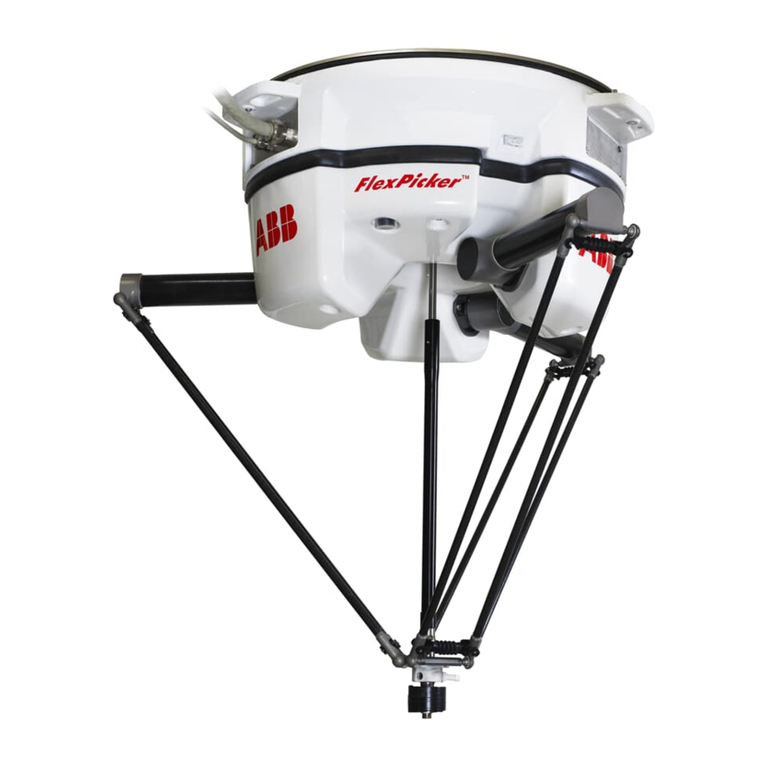
ABB
ABB IRB 360 User manual
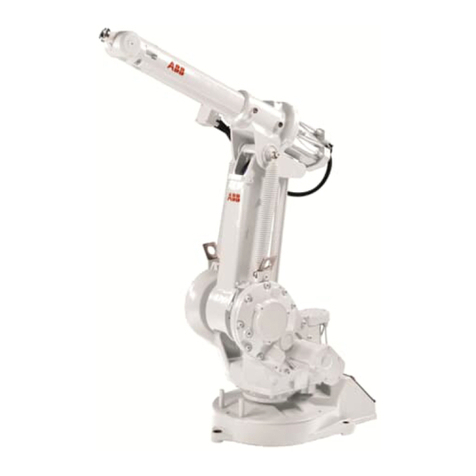
ABB
ABB IRB1410 User manual
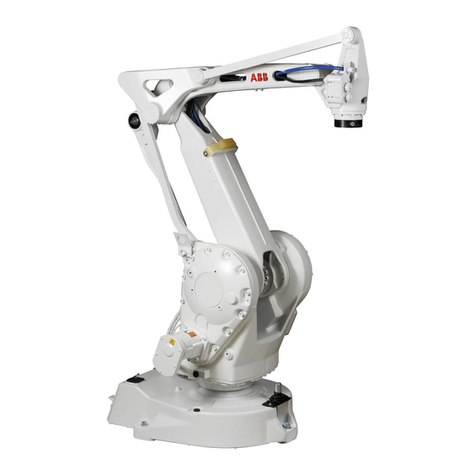
ABB
ABB IRB 260 User manual
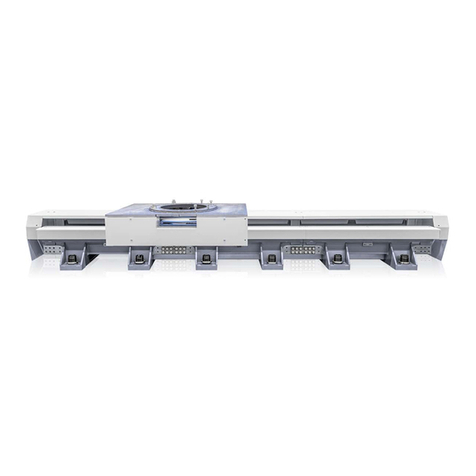
ABB
ABB IRBT 2005 User manual
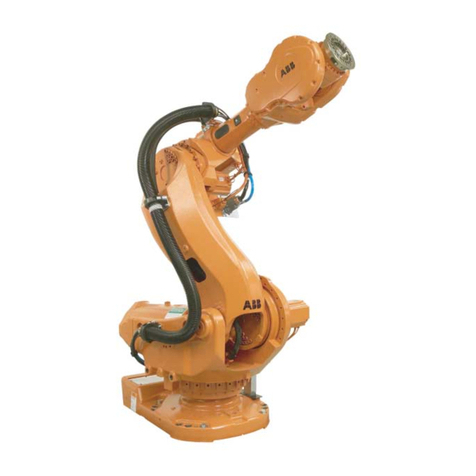
ABB
ABB IRB 7600 Series User manual
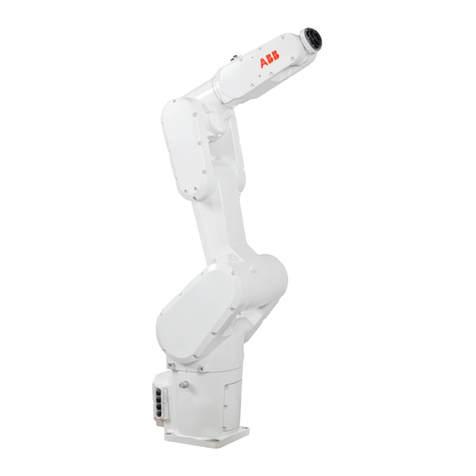
ABB
ABB IRB 1300 User manual
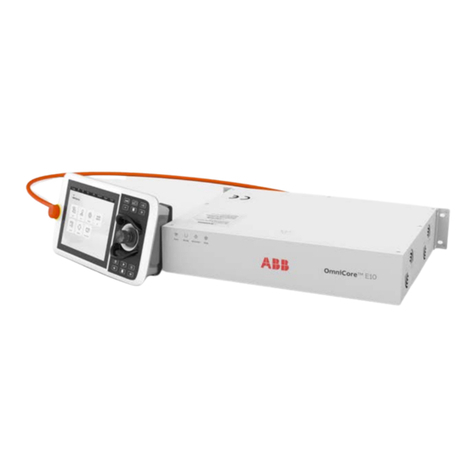
ABB
ABB OmniCore E10 User manual
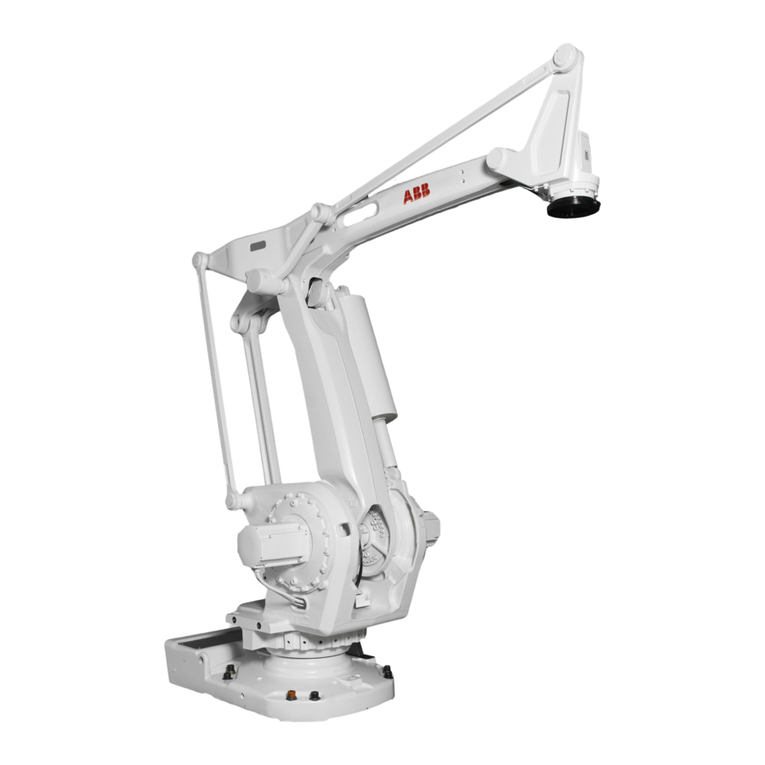
ABB
ABB IRB 660 Owner's manual
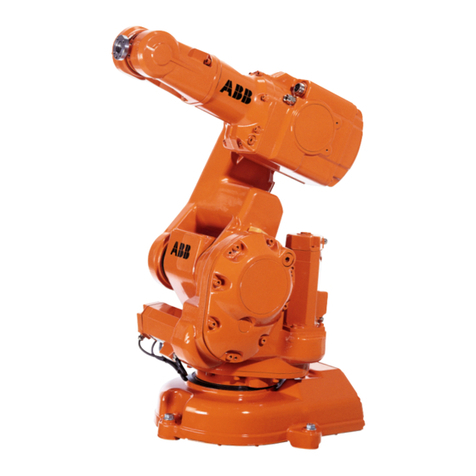
ABB
ABB IRB 140 User manual
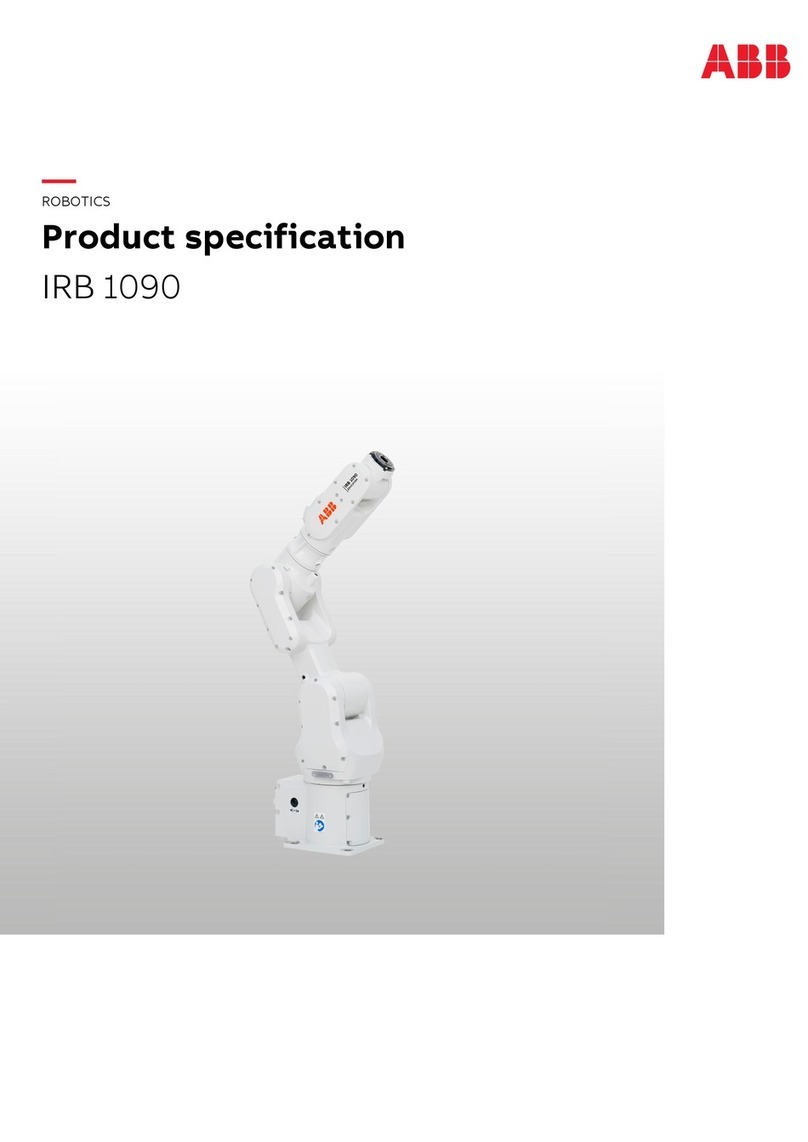
ABB
ABB IRB 1090 Owner's manual
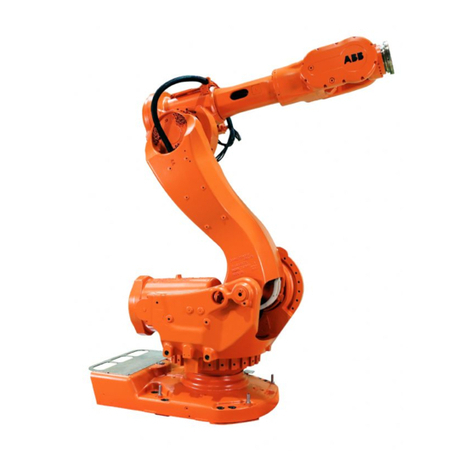
ABB
ABB IRB 6600 - 225/2.55 type B User manual
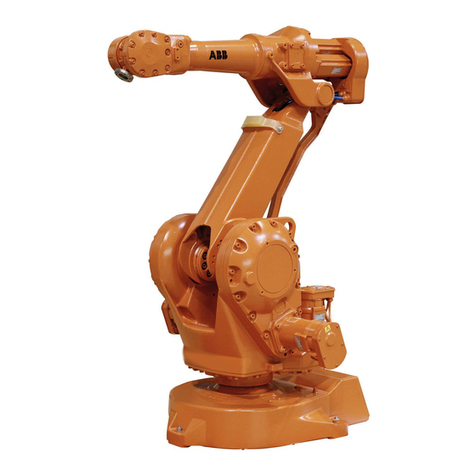
ABB
ABB M2004 User instructions

ABB
ABB IRB 6600 - 175/2.55 User manual
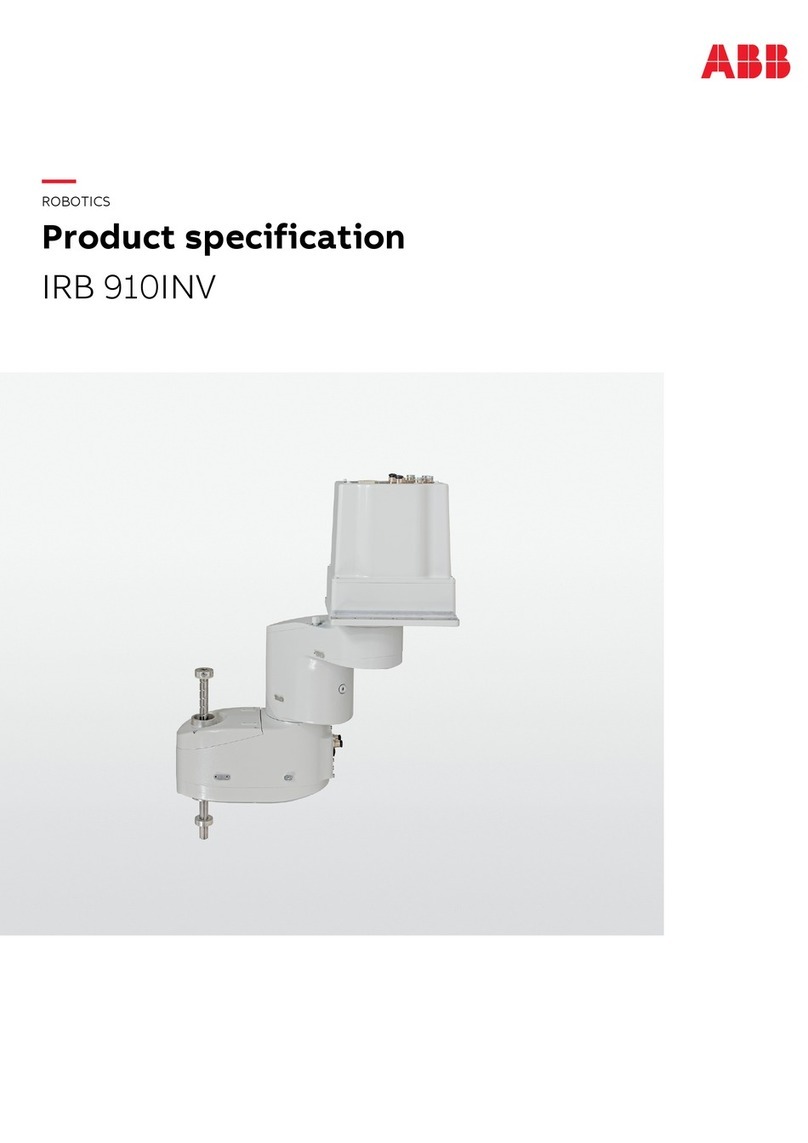
ABB
ABB IRB 910INV Owner's manual

ABB
ABB IRB 760 Series User manual